Физика металлов и металловедение, 2020, T. 121, № 11, стр. 1206-1212
Влияние условий термомеханической обработки на структуру и свойства MgB2
Е. И. Кузнецова a, *, Т. П. Криницина a, Ю. В. Блинова a, М. В. Дегтярев a
a Институт физики металлов УрО РАН
620108 Екатеринбург, ул. С. Ковалевской, 18, Россия
* E-mail: monocrist@imp.uran.ru
Поступила в редакцию 27.05.2020
После доработки 19.07.2020
Принята к публикации 21.07.2020
Аннотация
Проведено исследование влияния спекания под давлением и предварительного уплотнения гидростатическим давлением коммерческого порошка на микроструктуру и сверхпроводящие свойства керамики MgB2. Показано, что различные способы термомеханического воздействия приводят к формированию разного рода дефектов структуры, которые можно рассматривать как вероятные центры закрепления магнитного потока.
ВВЕДЕНИЕ
При создании проводников на основе соединения MgB2 в качестве исходного материала используется синтезированный порошок (ex-situ) или смесь порошков магния и бора (in-situ). Слабые межгранулярные связи и высокая пористость, снижающие критический ток, являются общим недостатком поликристаллического диборида магния [1]. Полученная методом ex-situ керамика MgB2 трудно поддается спеканию с образованием эффективного межзеренного контакта. Присутствующий на поверхности порошка слой MgO не способствует хорошему спеканию, хоть и действует как диффузионный барьер, препятствуя дальнейшему окислению. Кроме того, любая термическая обработка приводит к росту зерна. Для получения плотной, с хорошей межзеренной связностью керамики MgB2 успешно применяется метод горячего изостатического прессования [2], длительное спекание при атмосферном давлении [1, 3], спекание под высоким давлением [4]. Применение высоких давлений приводит к диспергированию оксида магния и внесению структурных дефектов, которые могут выступать в качестве центров пиннинга [5]. К сожалению, установки высокого квазигидростатического давления позволяют получить керамику, пригодную только для научных исследований из-за ограниченных размеров образцов.
Одной из важных является проблема консолидации порошка и достижения хорошего уплотнения материала перед спеканием. При обычном спекании и горячем изостатическом прессовании порошковых материалов относительная плотность выше 80% достигается при высокой температуре и длительном спекании. Но в этих условиях происходит рост зерна, поэтому в настоящее время многочисленные исследования сосредоточены на поиске способов подавить процесс роста зерна и тем самым улучшить сверхпроводящие свойства MgB2. В ряде работ отмечается, что на механизм спекания, кроме температуры, давления и времени спекания влияет качество и морфология порошка [6].
Проблема пористости становится особенно существенной в случае синтеза MgB2 из смеси порошков магния и бора. В процессе in-situ реализуется хороший межзеренный контакт, поскольку зерна MgB2 образуются в результате химической реакции,но сам продукт синтеза имеет высокую пористость [7]. Применение холодной деформации под высоким давлением приводит к уплотнению керамики, при этом разрушаются сформированные в процессе синтеза межзеренные связи. Требуется восстановительный отжиг, во время которого происходит некоторое увеличение размера зерна [8]. Для лучшего контроля размера зерна эффективен метод обработки, который включает в себя синтез и двустадийную деформацию с последующим спеканием [9]. Такая обработка может способствовать повышению критической плотности тока jc, благодаря улучшению связности границ зерен, уменьшению размера зерна и увеличению количества кристаллических дефектов.
Целью данного исследования является установление взаимосвязи структуры и свойств соединения MgB2, полученного из коммерческого порошка методами спекания под давлением и спекания скомпактированной под гидростатическим давлением заготовки.
МЕТОДИКА ЭКСПЕРИМЕНТА
Использован коммерческий порошок MgB2 субмикронного размера частиц. Фазовый состав порошка изучен с помощью рентгеноструктурного анализа. Скомпонованную из порошка таблетку диаметром 12 мм и высотой 5 мм спекали под давлением 0.4 ГПа при 800°С в течение 4 ч. Давление создавали одноосным нагружением до начала нагрева. Снятие давления проводили после остывания образца. Скорость нагрева составляла 15°C/мин, скорость охлаждения – 30°C/мин. Второй тип керамики получили нагружением порошка MgB2 в силиконовом чехле гидростатическим давлением 0.5 ГПа. От полученной в форме стержня диаметром 15 мм и длиной 40 мм заготовки отрезали шайбы высотой 10 мм и отжигали в атмосфере аргона при 650°С в течение 8 ч и при 750°С в течение 20 ч.
Объемную плотность образцов оценивали геометрическим методом. Микроструктурный анализ проведен с помощью рентгеновской дифракции (XRD), сканирующей и просвечивающей электронной микроскопии (SEM и TEM). Критическую плотность тока определяли по кривой намагниченности при 30 К в нулевом магнитном поле. Измерение магнитных характеристик проводили на магнитометрической установке MPMS-XL-5.
РЕЗУЛЬТАТЫ И ОБСУЖДЕНИЕ
Результаты рентгенографического исследования приведены на рис. 1. Анализ показал, что основной фазой коммерческого порошка (рис. 1а) является MgB2 (90%), кроме этого присутствуют примесные фазы MgB4 и MgO (5 и 5% соответственно). Недостатком порошка является наличие агломератов частиц, что приводит к неоднородной плотности компактируемой заготовки. Это, в свою очередь, вызывает неравномерное уплотнение и создание пор во время спекания. На рис. 2 приведено изображение частиц исходного коммерческого порошка диборида магния. Видно, что мелкие порошинки субмикронного размера налипают друг на друга и образуют агломераты размером 2–3 мкм, состоящие из множества частиц. Следующий уровень составляют крупные глобулы 5–15 мкм. После спекания можно выделить поры двух размерных уровней. Поры нанометрового размера наблюдаются среди субмикронных частиц с самой низкой плотностью упаковки. При спекании агломератов формируются более крупные поры – микронного размера и больше.
Рис. 1.
Рентгеновские дифрактограммы керамики MgB2: а – исходного коммерческого порошка; б – керамики, спеченной под давлением; в – керамики, спеченной после предварительного компактирования под гидростатическим давлением.
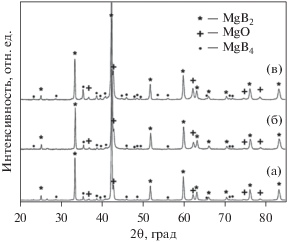
Влияние температуры спекания на уплотнение неоднозначно. С увеличением температуры спекания плотность керамики повышается, но высокие температуры провоцируют процесс роста зерна, скорость которого, в свою очередь, зависит от размера частиц исходного порошка. Следовательно, особенно важно быть осторожным с выбором температуры спекания. Спекание при 800°С под давлением 0.4 ГПа не привело к значительному росту зерен, их размеры в основном составляют около 1 мкм, в некоторых местах образуются сплошные пластины размером до 3 мкм (рис. 3а). Фазовый состав спеченной керамики такой же, как исходного порошка (рис. 1б), плотность довольно низкая, около 1.0 г/см3.
Рис. 3.
SEM-изображение структуры керамики MgB2, спеченной под давлением: а – зеренная структура; б – монокристаллическая область; в – EDX-спектры с области (б).
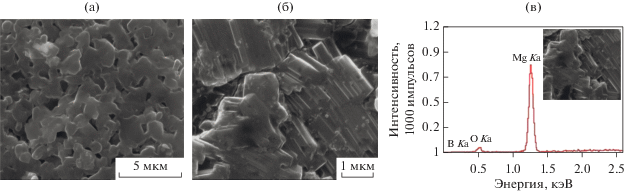
В структуре также наблюдаются более крупные (3–5 мкм) ограненные кристаллы (рис. 3б). По данным микроанализа соотношение элементов в этих кристаллах составляет Mg : B : O = 31 : : 59 : 10 (рис. 3в). Правильная огранка этих крупных монокристаллов свидетельствует о согласованном срастании нескольких мелких кристаллов MgB2 при спекании. В процессе роста крупных кристаллов произойдет вытеснение примесных фаз на поверхность. Действительно, на поверхности кристаллов наблюдается большое количество кубической формы частиц размером ~50–100 нм (рис. 3б). Необычно, что наблюдаемые на микрофотографиях монокристаллические включения образовались при твердофазном спекании без присутствия жидкой фазы. Основная окружающая ограненные кристаллы структура из пластинчатых зерен (рис. 3а) образуется в соответствии с обычным твердофазным спеканием [3].
Размер зерна спеченной под давлением керамики (1–5 мкм) дает возможность исследовать с помощью ТEM морфологию зерен, дефекты кристаллического строения и выделения примесных фаз. В основном наблюдаются тонкие и ровные границы зерен, свободные от вторичных фаз. На рис. 4а, 4б показаны гексагонально ограненные зерна, имеющие чистые прямые границы (отмечены стрелками). На рис. 4в показана граница зерна с дислокациями (указаны стрелкой, на вставке при большем увеличении). Равноосные зерна округлой формы имеют на границе аморфный слой толщиной ~7 нм (рис. 4б). В ряде работ показано, что на границах зерен керамики, полученной спеканием под давлением, всегда присутствует аморфный слой толщиной ~10 нм и более [10, 11]. Аморфные границы зерен, безусловно, подавляют критический ток, а тонкие и чистые границы зерен, напротив, способствуют усилению связи между зернами, даже при невысокой плотности керамики.
Рис. 4.
TEM-изображение структуры керамики MgB2, спеченной под давлением. Светлопольное изображение структуры разных (а, б, в) участков керамики (на вставке – электронограммы).
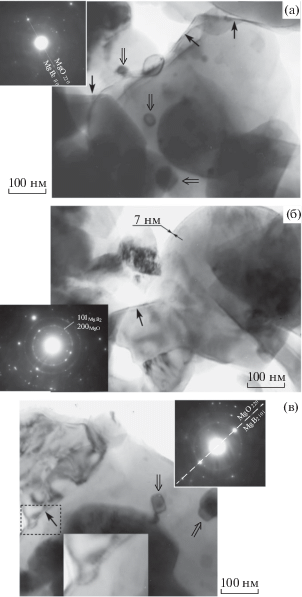
ТЕМ исследование выявило наличие включений размером 10–50 нм, распределенных в объеме зерен (рис. 4а, 4в, отмечены двойными стрелками). Эти частицы прямоугольной огранки, соответствующие по форме и размерам частицам, наблюдаемым в SEM (рис. 3б), могут принадлежать MgO как примесной фазе, определенной рентгеноструктурным анализом. Это согласуется с данными SEM-EDX спектров включений оксида магния, имеющих подобную форму и размеры 50–200 нм [8]. Неоднократно отмечалось, что довольно сложно однозначно идентифицировать фазу MgO в керамике MgB2, поскольку наиболее сильные рефлексы MgB2 совпадают с рефлексами MgO. На соответствующих электронограммах, кроме совпадающих рефлексов MgB2/MgO, присутствуют отдельные рефлексы, принадлежащие только 111MgO, поэтому наблюдаемые на микрофотографиях частицы, вероятнее всего, принадлежат фазе MgO. Отсутствие дислокаций вокруг выделений и их огранка свидетельствуют о том, что они когерентны матрице.
Таким образом, метод ex-situ с применением одноосного нагружения с нагревом является эффективным при условии умеренных температур спекания, что в свою очередь приводит к подавлению роста зерна. В этом случае керамика имеет высокую плотность границ зерен вследствие мелкого размера зерна, а включения вторых фаз имеют нанометровые размеры.
На рис. 5 показана структура керамики, полученной из порошка MgB2, который предварительно компактировали под гидростатическим давлением 0.5 ГПа и затем отжигали при 750°С в течение 20 ч. Керамике присуща характерная структура, в которой выделяются сильно контрастирующие по плотности области, состоящие из рыхлой фракции и почти монолитных участков, где зерна очень плотно прилегают друг к другу [12]. Плотность полученной керамики ~1.4 г/см3, размер зерен составляет ~2 мкм. Данные рентгеноструктурного анализа приведены на рис. 1в. Основной фазой является MgB2 (78%), кроме этого присутствуют фазы MgB4 и MgO (15 и 7% соответственно). Рентгеноструктурный анализ показал наличие большего, чем в исходном порошке, количества MgB4 в качестве примесной фазы, что указывает на разложение MgB2 во время спекания, несмотря на то, что температура спекания 750°С довольно низкая для разложения фазы MgB2 по реакции: 2MgB2 → MgB4 + Mg [13]. Интересно отметить, что более низкая температура и меньшее время (650°С, 8 ч) оказались недостаточными для хорошего спекания, и образец рассыпался после отжига, однако его фазовый анализ все равно показал наличие фазы MgB4, но в меньшем количестве (82% MgB2, 11% MgB4 и 7% MgO). Видимо, основным фактором распада MgB2 и появления MgB4, в данном случае, является длительное время спекания в открытой системе. Вопреки общепринятому мнению, что присутствие MgB4 ухудшает сверхпроводящие свойства, мелкодисперсные включения этой фазы, создающие локальные области искажений в матрице, могут служить эффективными центрами пиннинга [14].
Рис. 5.
SEM-изображение структуры керамики MgB2, спеченной после предварительного компактирования под гидростатическим давлением.
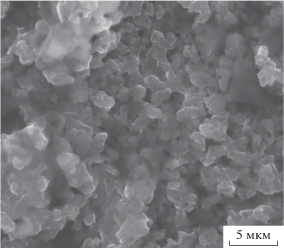
ТЕМ-исследование выявило высокую плотность наноразмерных включений в зернах спеченной после предварительного гидростатического компактирования керамики (рис. 6–8). На рис. 6а показана область керамики MgB2, содержащая округлые, размером ~50 нм частицы (отмечены стрелками) и связанные с ними дислокации (отмечены двойными стрелками), которые появляются в результате релаксации упругих напряжений около частиц. На соответствующей электронограмме присутствуют рефлексы только матричной фазы и MgO, а на темнопольном изображении этого участка в выделенном рефлексе, принадлежащем ${{{{{101}}_{{{\text{Mg}}{{{\text{B}}}_{{\text{2}}}}}}}} \mathord{\left/ {\vphantom {{{{{101}}_{{{\text{Mg}}{{{\text{B}}}_{{\text{2}}}}}}}} {{{{200}}_{{{\text{MgO}}}}}}}} \right. \kern-0em} {{{{200}}_{{{\text{MgO}}}}}}}$ наблюдаются эти частицы (рис. 6б, показаны стрелками). Можно с достаточной уверенностью предположить, что это частицы MgO, и межфазные границы проявляют себя как центры зарождения дислокаций.
Рис. 6.
TEM-изображение структуры керамики MgB2, спеченной после предварительного компактирования под гидростатическим давлением: а – светлопольное изображение (на вставке – элетронограмма); б – темнопольное изображение в рефлексах ${{\left( {{\text{1}}0{\text{1}}} \right)}_{{{\text{Mg}}{{{\text{B}}}_{{\text{2}}}}}}}$ и (200)MgО (на вставке – увеличенное изображение выделенного участка).
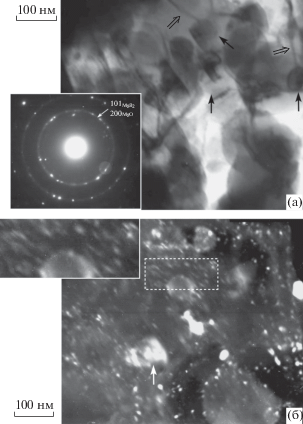
Рис. 7.
TEM-изображение структуры керамики MgB2, спеченной после предварительного компактирования под гидростатическим давлением: а – светлопольное изображение; б – темнопольное изображение в рефлексах ${{\left( {{\text{1}}0{\text{1}}} \right)}_{{{\text{Mg}}{{{\text{B}}}_{{\text{2}}}}}}}$ и (200)MgО (на вставке – электронограмма).
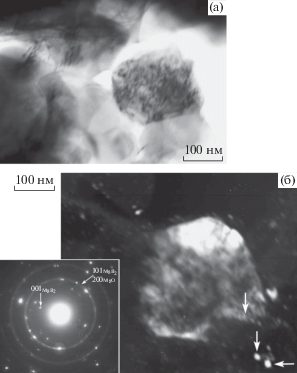
Рис. 8.
Tемнопольное изображение в рефлексе ${{\left( {{\text{1}}00} \right)}_{{{\text{Mg}}{{{\text{B}}}_{{\text{2}}}}}}}$ (на вставке – электронограмма) керамики MgB2, спеченной после предварительного компактирования под гидростатическим давлением.
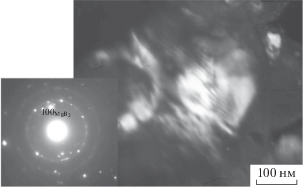
На темнопольном изображении этого участка (рис. 6б) наблюдаются еще два типа включений: очень мелкие, до 10 нм, округлые частицы и другие – вытянутые в виде тонких штрихов (на вставке при большем увеличении). Первые, в основном, декорируют границы зерен, а вторые равномерно распределены в теле зерна. Невысокая температура и большая длительность спекания исследуемой керамики, а также высокая дисперсность этих включений указывают на то, что их образование может происходить по спинодальному механизму. Наличие упругих напряжений около таких частиц должно приводить к искажению решетки матрицы и появлению в связи с этим характерного контраста, наблюдаемого электронномикроскопически. На рис. 7а представлено светлопольное изображение зерен матричной фазы MgB2. Внутри зерен наблюдается созданный полями напряжений вокруг частиц черно-белый контраст, свидетельствующий о локальных искажениях решетки MgB2. На темнопольном изображении другого участка в рефлексе, принадлежащем ${{{{{101}}_{{{\text{Mg}}{{{\text{B}}}_{{\text{2}}}}}}}} \mathord{\left/ {\vphantom {{{{{101}}_{{{\text{Mg}}{{{\text{B}}}_{{\text{2}}}}}}}} {{{{200}}_{{{\text{MgO}}}}}}}} \right. \kern-0em} {{{{200}}_{{{\text{MgO}}}}}}}$ видны частицы (рис. 7б, указаны стрелками), и наблюдается черно-белый контраст – результат наличия упругих напряжений около частиц. На темнопольном изображении (рис. 8), полученном в принадлежащем только матричной фазе рефлексе 100MgB2, наблюдается классическая модулированная структура концентрационного типа.
Наличие эффектов, связанных с присутствием наноразмерных выделений внутри зерен MgB2, указывает на расслоение, происходящее в самой матричной фазе. Подобные выделения пластинчатой формы размером 5–10 нм и предполагаемым составом Mg(BО)х наблюдали в работе [15]. Авторы работы считают, что наличие таких выделений является общей структурной особенностью поликристаллической керамики MgB2. Учитывая то, что включения такого типа, наблюдаемые на рис. 6б, располагаются вдоль определенного направления, можно предположить, что частицы имеют некоторую когерентность с матрицей. В работе [14] рассматриваются когерентные и полукогерентные матрице включения фазы MgB4 размером 5–20 нм, вызывающие искажения решетки MgB2. В работе [16] фаза MgB4, определяемая методом EBSD, образует вкрапления размером 20–100 нм, в основном расположенные на границах зерен MgB2. Результаты рентгеноструктурного анализа показывают присутствие значительного количества фазы MgB4 (15%). Образование выделений этой фазы внутри зерен MgB2, несомненно, более предпочтительно для обеспечения сверхпроводящих свойств, чем выделение частиц по границам зерен.
Оба типа полученной в работе керамики имеют температуру начала перехода в сверхпроводящее состояние ~38.5 К, типичную для нелегированной керамики MgB2. Наблюдается значительная ширина перехода, что объясняется наличием наноразмерных включений вторых фаз, создающих локальные искаженные области в матрице MgB2.
При использовании модели Бина [17] для определения jc поликристаллических сверхпроводников возникает проблема установления циркуляционного радиуса. Использование размеров всего образца, имеющего высокую пористость (низкую плотность), может привести к значительной недооценке величины jc, так как в этом случае характер распределения циркулирующих токов не соответствует полностью плотной, однородной с хорошо связанными зернами керамике [18]. Суммарная внутригранульная плотность критического тока, рассчитанная из уравнения Бина, использующего размеры образца, будет значительно меньше. В табл. 1 показаны результаты оценки сверхпроводящих свойств исследованных керамик с использованием формулы для определения внутригранульной плотности критического тока сверхпроводников, имеющих слабосвязанные зерна [18].
где ∆M – ширина петли намагниченности, d0.5 – средний размер частиц, определенный с помощью SEM.ВЫВОДЫ
Небольшой размер кристаллитов исходного коммерческого порошка MgB2 и пониженная температура спекания позволили получить керамику с зерном микронного размера. Определен температурный интервал спекания 750–800°С, при котором не происходит значительный рост зерна. Показано, что примесными фазами являются MgO, частицы которой имеют размеры в диапазоне от 10 до 50 нм, и MgB4, количество которой больше в керамике, предварительно скомпактированной под гидростатическим давлением. В керамике, спеченной под давлением, наблюдается два типа границ зерен. Плохо связанные зерна имеют границы, содержащие аморфный слой, в то время как хорошо связанные зерна имеют структурно неповрежденные границы. Керамика, спеченная после предварительного компактирования гидростатическим давлением, содержит высокую плотность дефектов и показывает широкий сверхпроводящий переход, но немного более высокие значения jc, что может быть связано как с закреплением на этих дефектах магнитного потока, так и с более высокой плотностью синтезированного материала.
Работа выполнена в рамках госзадания Минобрнауки (тема “Давление”, Г.р. № АААА-А18-118020190104-3. Электронно-микроскопические исследования проведены в отделе электронной микроскопии ЦКП ИФМ УрО РАН.
Список литературы
Yamamoto A., Tanaka H., Shimoyama J., Ogino H., Kishio K., Matsushita T. Towards the Realization of Higher Connectivity in MgB2 Conductors: In-situ or Sintered Ex-situ? // Jap. J. Appl. Phys. 2012. V. 51. 010105-1-6.
Shields T.C., Kawano K., Holdom D., Abell J.S. Microstructure and superconducting properties of hot isostatically pressed MgB2 // Supercond. Sci. Technol. 2001. V. 15. P. 202–205.
Tanaka H., Yamamoto A., Shimoyama J., Ogino H., Kishio K. Strongly connected ex-situ MgB2 polycrystalline bulks fabricated by solid-state self-sintering // Supercond. Sci. Technol. 2012. V. 25. P. 115022-7.
Ma H.A., Jia X.P., Chen L.X., Zhu P.W., Ren G.Z., Guo W.L., Fu X.Q., Zou G.T., Ren Z.A., Che G.C., Zhao Z.X. Superhard MgB2 bulk material prepared by high-pressure sintering // J. Phys. Cond. Matter. 2002. V. 14. P. 11181–11184.
Liao X.Z., Serquis A.C., Zhu Y.T., Huang J.Y., Peterson D.E., Mueller F.M., Xu H.F. Controlling flux pinning precipitates during MgB2 synthesis // Appl. Phys. Lett. 2002. V. 80. P. 4396–4400.
Zhou S., Pan A.V., Horvat J., Qin M.J., Liu H.K. Effects of precursor powders and sintering processes on the superconducting properties of MgB2 // Supercond. Sci. Technol. 2004. V. 17. P. 528–532.
Кузнецова Е.И., Акшенцев Ю.Н., Есин В.О., Сударева С.В., Блинова Ю.В., Дегтярев М.В., Новожонов В.И., Романов Е.П. Механизмы образования массивной сверхпроводящей фазы MgB2 при высоких температурах // ФТТ. 2015. Т. 57. С. 859–865.
Кузнецова Е.И., Криницина Т.П., Блинова Ю.В., Дегтярев М.В., Сударева С.В. Тонкая структура массивного сверхпроводника MgB2 после деформации и термической обработки // ФММ. 2017. Т. 118. № 4. С. 364–371.
Кузнецова Е.И., Криницина Т.П., Дегтярев М.В., Блинова Ю.В. Механизмы холодной деформации под высоким давлением сверхпроводящей керамики MgB2 // ФММ. 2018. Т. 119. С. 850–857.
Li Q., Wu L., Zhu Y., Moodenbaugh A.R., Gu G.D., Suenaga M., Ye Z.X., Fischer D.A. Comparative Studies of MgB2/Mg Nano-Composites and Press-Sintered MgB2 Pellets // IEEE Trans. Appl. Supercond. 2003. V. 13. № 2. P. 3051–3055.
Zhu Y., Wu L., Volkov V., Li Q., Gu G.D., Moodenbaugh A.R., Malac M., Suenaga M., Tranquada J. Microstructure and structural defecs in MgB superconductor // Physica C. 2001. V. 356. P. 239–253.
Кузнецова Е.И., Сударева С.В., Криницина Т.П., Блинова Ю.В., Романов Е.П., Акшенцев Ю.Н., Дегтярев М.В., Тихоновский М.А., Кисляк И.Ф. Механизм образования и особенности структуры массивных образцов соединения MgB2 // ФММ. 2014. Т. 115. С. 186–197.
Zhigadlo N.D., Katrych S., Karpinski J., Batlogg B., Bernardini F., Massidda S., Puzniak R. Influence of Mg deficiency on crystal structure and superconducting properties in MgB2 single crystals // Phys. Rev. B. 2010. V. 81. P. 0545201-7.
Cai Q., Liu Y., Ma Z.Q., Li H.J., Yu L.M. Variation of pinning mechanism and enhancement of critical current density in MgB2 bulk containing self-generated coherent MgB4 impurity // Appl. Phys. Lett. 2013. V. 103. P. 132601-4.
Song X. Atomic structure and chemistry of dense nano-precipitates in MgB2 ceramic // Ceramics International. 2013. V. 39. P. 4299–4305.
Koblischka-Veneva A., Koblischka M.R., Schmauch J., Noudem J., Murakami M. Analysis of the microstructure of bulk MgB2 using TEM, EBSD and t-EBSD // J. Microscopy. 2019. V. 274. P. 123–131.
Bean C.P. Magnetization of hard superconductors // Phys. Rev. Lett. 1962. V. 8. P. 250–253.
Matthews G.A.B., Santra S., Ma R., Grovenor C.R.M., Grant P.S., Speller S.C. Effect of the sintering temperature on the microstructure and superconducting properties of MgB2 bulks manufactured by the field assisted sintering technique // Supercond. Sci. Technol. 2020. V. 33. P. 054003-11.
Дополнительные материалы отсутствуют.
Инструменты
Физика металлов и металловедение