Физика металлов и металловедение, 2020, T. 121, № 12, стр. 1331-1337
Влияние Mn на фазовый состав и свойства сплава Al–Cu–Y–Zr
С. М. Амер a, Р. Ю. Барков a, А. В. Поздняков a, *
a НИТУ “МИСиС”
119049 Москва, Ленинский просп., 4, Россия
* E-mail: pozdniakov@misis.ru
Поступила в редакцию 03.08.2020
После доработки 11.08.2020
Принята к публикации 18.08.2020
Аннотация
Исследовано влияние марганца на микроструктуру, фазовый состав и механические свойства термически упрочняемого деформируемого сплава Al–5.5Cu–2.0Y–0.3Zr. В литой структуре сплава идентифицирована четверная фаза на основе алюминия с соотношением Cu/Mn/Y равным 4/2/1, которой предположительно соответствует химическое соединение Al25Cu4Mn2Y. Максимальное упрочнение в процессе старения слитка после закалки достигнуто через 5 ч отжига при 210°С. В процессе термической обработки в сплаве образуется 3 типа выделений. Выделения фаз Al20Cu2Mn3 и Al3(Zr,Y) образуются в процессе гомогенизации при температуре 605°С. Частицы фазы Al3(Zr,Y) имеют размер 30–50 нм, а фазы Al20Cu2Mn3 – 200–250 нм в длину и 150–200 нм в ширину. Диаметр дискообразных выделений метастабильной фазы θ''(Al2Cu), образованной при старении, составляет 80–200 нм при толщине около 5 нм. После прокатки и отжига в течение 1 и 2 ч наблюдается максимум твердости при температуре 150°С, связанный с тем, что старение превалирует над разупрочнением, которое сдерживают дисперсоиды фаз Al20Cu2Mn3 и Al3(Zr,Y) и достаточно дисперсные частицы фаз Al8Cu4Y и (Al,Cu)11Y3 кристаллизационного происхождения. При 210°С разупрочнение деформированного сплава перекрывает эффект от старения, и твердость незначительно снижается. Добавка марганца позволяет сохранить существенно более высокий уровень твердости в исследуемом сплаве при температурах отжига вплоть до 550°С и повысить температуру начала рекристаллизации до 350–400°С. По результатам испытаний на одноосное растяжение исследуемый сплав демонстрирует высокий уровень характеристик механических свойств после отжига прокатанных листов при 150°С: σ0.2 = 330–334 МПа, σв = 374 МПа при δ = 3.6–5.5%.
ВВЕДЕНИЕ
Литейные и деформируемые сплавы на основе системы Al–Cu отличаются высокими характеристиками механических свойств и самой низкой среди всех алюминиевых сплавов технологичностью при литье [1–6]. Составы практически всех промышленных сплавов на основе системы Al‒Cu соответствуют области твердых растворов на диаграмме состояния [1–3], в результате они имеют матричный тип структуры и высокую склонность к образованию трещин кристаллизационного происхождения [3–6]. Легирование алюминиевомедных сплавов эвтектикообразующими элементами позволяет сформировать сложную многофазную структуру и повысить литейные и прочностные характеристики [5, 6]. Малые добавки редкоземельных металлов (РЗМ) позволяют улучшить механические и технологические свойства [7–16]. Упрочнение при этом достигается в основном за счет выделения в процессе гомогенизации слитков дисперсоидов L12-фазы Al3M [10–16]. Снижения горячеломкости можно добиться за счет модифицирования зеренной структуры [14, 16, 17]. С другой стороны, квазибинарные сплавы некоторых тройных систем Al–Cu–РЗМ, в частности с Ce [18, 19], Y [20, 21] и Er [21–23], представляют большой интерес благодаря узкому интервалу кристаллизации и высокой термической стабильности фаз кристаллизационного происхождения. Легирование цирконием тройных сплавов систем Al–Cu–Y и Al–Cu–Er позволяет существенно повысить характеристики механических свойств прокатанных листов за счет выделения дисперсоидов Al3(Zr,Y) [24] и Al3(Zr,Er) [25]. Настоящее исследование направлено на определение влияния добавки марганца на микроструктуру, фазовый состав и механические свойства сплава Al–5.5Cu–2.0Y–0.3Zr.
МЕТОДИКА ЭКСПЕРИМЕНТОВ
Сплав Al–5.5Cu–2.0Y–0.8Mn–0.3Zr (мас. %) выплавлен в печи сопротивления из чистого алюминия А99 и лигатур Al–51.7Cu, Al–10Y, Al–10Mn, Al–5Zr при температуре 750°С и разлит в медную водоохлаждаемую изложницу с размером внутренней полости 20 × 40 × 120 мм. Дифференциальный сканирующий калориметр (ДСК) Labsys Setaram использован для определения температуры солидуса. Гомогенизационный отжиг проводили при 605°С в течение 1 и 3 ч. После отжига 605°С, 1 ч сплав закаливали и проводили старение в интервале температур 150–225°С. Слиток после закалки был прокатан до толщины 10 мм при температуре 440°С и до 1 мм при комнатной температуре. После прокатки сплав отжигали при 150–550°С в течение 1–10 ч. Микроструктурные исследования и идентификацию фаз проводили на световом микроскопе (СМ) Zeiss, сканирующем (СЭМ) TESCAN VEGA 3LMH, просвечивающем электронном микроскопе (ПЭМ) JEM 2100 и рентгеновском дифрактометре Bruker D8 Advance. Твердость измеряли стандартным методом Виккерса (HV) при нагрузке 5 кг. Испытания на растяжение проводили на универсальной испытательной машине Zwick/Roll Z250.
РЕЗУЛЬТАТЫ ЭКСПЕРИМЕНТОВ И ОБСУЖДЕНИЕ
На рис. 1 представлена микроструктура и фазовый состав исследуемого сплава в литом и термообработанном состоянии. В литой структуре (согласно СЭМ и рентгенограммы) помимо алюминиевого твердого раствора (Al) присутствует дисперсная эвтектика ((Al) + Al8Cu4Y), фазы (Al,Cu)11Y3 и AlCu, расположенные на границах дендритных ячеек (Al) (рис. 1а, 1б). Также согласно результатам рентгеновского анализа в сплаве присутствует небольшое количество фазы Al2Cu (рис. 1б). На основании распределения легирующих элементов между фазами (белый прямоугольник на рис. 1а) в сплаве выявлена четверная фаза, обогащенная медью, марганцем и иттрием (рис. 1а), а на рентгенограмме (рис. 1б) присутствует несколько неидентифицированных пиков обозначенных знаком “?”. Точечный анализ в СЭМ показывает, что атомное соотношение Cu/Mn/Y в этой фазе равно 4/2/1. Химическое соединение Al25Cu4Mn2Y может соответствовать найденной четверной фазе. Практически такая же фаза, но содержащая эрбий обнаружена в сплаве системы Al–Cu–Er–Mn–Zr [26]. Морфология четверной фазы напоминает “китайский шрифт”, свойственный эвтектической фазе Al15(Fe,Mn)3Si2 [3, 5, 6]. Примерно 1.6% Cu, 0.7% Mn, 0.3% Zr и 0.1–0.2% Y растворено в (Al) после кристаллизации. Согласно данным ДСК-анализа температура солидуса сплава составляет 613°С. На рис. 1в, 1г представлены микроструктуры сплава после 1 и 3 ч отжига при 605°С. В процессе гомогенизации перед закалкой при температуре 605°С происходит фрагментация, сфероидизация и рост эвтектической фазы Al8Cu4Y. В результате растворение неравновесного избытка медьсодержащих фаз концентрация меди в твердом растворе повышается до 2.5% после 1 ч отжига и не изменяется с увеличением времени до 3 чв. После 1 ч отжига произведена закалка сплава с температуры 605°С и последующее старение в интервале температур 150–225°С.
Рис. 1.
Микроструктура (а, в, г) (СЭМ) и рентгенограмма (серая линия – тот же сплав без марганца) (б) исследуемого сплава: а, б – литое состояние (на изображении а показано распределение легирующих элементов между фазами в белом прямоугольнике); в – отжиг при 605°С в течение 1 ч; г – отжиг при 605°С в течение 3 ч.
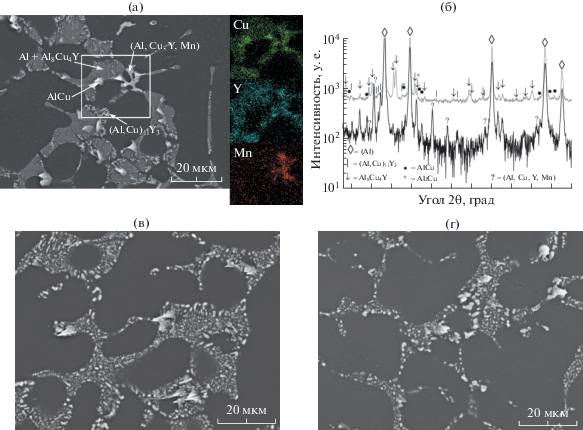
На рис. 2 представлены зависимости HV от времени старения. Увеличение температуры старения со 150 до 210°С приводит к повышению упрочняющего эффекта, а максимальное упрочнение достигнуто после 5 ч отжига при 210°С.
Повышение температуры отжига до 225°С приводит к перестариванию, однако твердость при этом выше чем после отжига при более низких температурах (рис. 2).
На рис. 3 представлена тонкая структура исследуемого сплава в состаренном при 210°С после закалки состоянии. В структуре найдено 3 типа выделений. Выделения фаз Al20Cu2Mn3 и Al3(Zr,Y) образуются в процессе гомогенизации при температуре 605°С. Округлые выделения дисперсоидов фазы Al3(Zr,Y) имеют размер 30–50 нм. Такие же выделения, но несколько меньшего размера, были выявлены в сплаве Al–Cu–Y–Zr после отжига при 590°С [24]. Фаза Al20Cu2Mn3 имеет размер 200–250 нм в длину и 150–200 нм в ширину. Внутри выделений фазы Al20Cu2Mn3 выявлены двойниковые границы и муаровый эффект (правое изображение на рис. 3), свойственный марганцовистым выделениям в алюминиевых сплавах [27‒29]. Дискообразные выделения метастабильной фазы θ''(Al2Cu), образованные при старении, имеют диаметр 80–200 нм при толщине около 5 нм.
Рис. 3.
Микроструктура исследуемого сплава после 1 ч выдержки при 605°С и 5 ч старения при 210°С (ПЭМ).
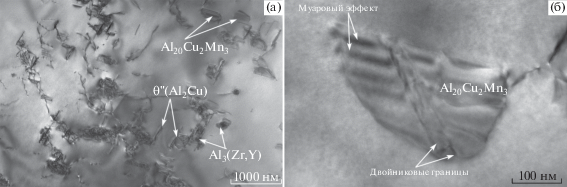
Закаленный от 605°С после часовой выдержки слиток был прокатан до 1 мм листа. На рис. 4 представлены зависимости твердости HV от температуры и времени отжига. В процессе отжига при низких температурах (до 250°С) в сплаве протекают два конкурирующих процесса. Процесс разупрочнения, связанный с уменьшением концентрации дефектов и полигонизацией, конкурирует с процессом упрочнения, обусловленным выделением метастабильной фазы θ”(Al2Cu) или старением. При температуре 150°С наблюдается пик твердости после 1 и 2 ч отжига (см. рис. 4б). В данном случае процесс старения превалирует над разупрочнением, которое в свою очередь, сдерживают дисперсоиды фаз Al20Cu2Mn3 и Al3(Zr,Y) и достаточно дисперсные частицы фаз Al8Cu4Y и (Al,Cu)11Y3 кристаллизационного происхождения. С повышением температуры отжига до 180°С обнаруживается уже слабый максимум твердости при меньших временах отжига, а при 210°С разупрочнение перекрывает эффект от старения (см. рис. 4б). На рис. 4а для сравнения приведены аналогичные зависимости твердости от температуры отжига для сплавов Al–6.5Cu–2.3Y [21] и Al–4.5Cu–1.6Y–0.3Zr [24]. Можно отметить, что добавка марганца позволяет сохранить существенно более высокий уровень твердости в исследуемом сплаве при температурах отжига вплоть до 550°С. Рекристаллизация в исследуемом сплаве начинается в интервале температур 350–400°С (рис. 5а, 5б). При 400°С наблюдается частично рекристаллизованная структура (см. рис. 5б), для сравнения в сплаве Al–4.5Cu–1.6Y–0.3Zr без добавки марганца после отжига при 350°С структура была полностью рекристаллизована. С увеличением температуры отжига размер зерна незначительно увеличивается и составляет в среднем 11 мкм после отжига при 550°С.
Рис. 4.
Зависимость твердости деформированного сплава от температуры отжига в течение 1 ч (а) и времени отжига при 100, 180 и 210°С (б).
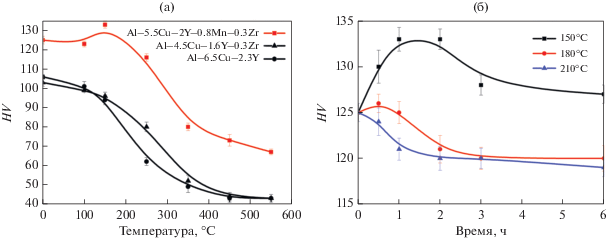
Рис. 5.
Зеренная структура исследуемого сплава после прокатки и последующего отжига при 350, 400, 450 и 550°С в течение 1 ч.
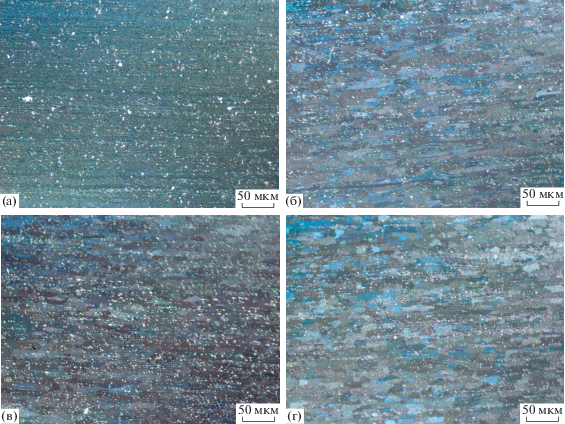
Результаты испытаний на одноосное растяжение представлены в табл. 1. В деформированном состоянии условный предел текучести составляет 346 МПа при удлинении 2.4%. В процессе отжига при 150°С происходит незначительное снижение σ0.2 менее, чем на 15 МПа, удлинение при этом возрастает более, чем вдвое. При увеличении температуры отжига до 210°С предел текучести снижается до 308–313 МПа. При этом стоит отметить, что при времени отжига до 10 ч σ0.2 практически не изменяется, оставаясь на уровне, полученном после одночасового отжига. Для сравнения сплав близкого состава без марганца Al–4.5Cu–1.6Y–0.3Zr имеет σ0.2 = 270 МПа после отжига при 150°С [24]. Согласно ГОСТ в листах из сплава Д16 системы Al–Cu–Mg предел текучести составляет 230–360 МПа [30]. А в отожженных магналиях условный предел текучести составляет 260–409 МПа [31, 32].
Таблица 1.
Характеристики механических свойств после испытаний на одноосное растяжение в деформированном и отожженном состояниях
Состояние | σ0.2, МПа | σв, МПа | δ, % |
---|---|---|---|
Деформированное | 346 ± 2 | 378 ± 3 | 2.4 ± 0.1 |
Отжиг при 150°С в течение 2 ч | 330 ± 4 | 374 ± 4 | 3.9 ± 0.1 |
Отжиг при 150°С в течение 6 ч | 334 ± 1 | 374 ± 1 | 3.6 ± 0.5 |
Отжиг при 150°С в течение 10 ч | 333 ± 2 | 375 ± 1 | 5.5 ± 0.3 |
Отжиг при 180°С в течение 3 ч | 310 ± 10 | 357 ± 8 | 5.2 ± 0.3 |
Отжиг при 180°С в течение 6 ч | 321 ± 2 | 365 ± 1 | 4.4 ± 0.8 |
Отжиг при 180°С в течение 10 ч | 317 ± 3 | 362 ± 1 | 4.9 ± 0.3 |
Отжиг при 210°С в течение 1 ч | 313 ± 1 | 361 ± 2 | 5.1 ± 0.5 |
Отжиг при 210°С в течение 6 ч | 308 ± 2 | 354 ± 1 | 4.0 ± 0.3 |
Отжиг при 210°С в течение 10 ч | 311 ± 2 | 354 ± 1 | 5.5 ± 0.5 |
ЗАКЛЮЧЕНИЕ
Исследовано влияние марганца на микроструктуру, фазовый состав и механические свойства термически упрочняемого деформируемого сплава Al–5.5Cu–2.0Y–0.3Zr. В литой структуре сплава выявлена четверная фаза, обогащенная медью, марганцем и иттрием с соотношением Cu/Mn/Y равным 4/2/1, которой предположительно соответствует химическое соединение Al25Cu4Mn2Y.
После закалки старение в интервале температур от 150 до 225°С показывает максимальное упрочнение после 5 ч отжига при 210°С. В процессе отжига перед закалкой и старения в сплаве выделяются 3 типа дисперсоидов. Выделения фаз Al20Cu2Mn3 и Al3(Zr,Y) образуются в процессе гомогенизации при температуре 605°С. Округлые выделения дисперсоидов фазы Al3(Zr,Y) имеют размер 30–50 нм. Фаза Al20Cu2Mn3 имеет размер 200–250 нм в длину и 150–200 нм в ширину. Дискообразные выделения метастабильной фазы θ''(Al2Cu), образованные при старении, имеют диаметр 80–200 нм при толщине около 5 нм.
Отжиг прокатанных листов в течение 1 и 2 ч при температуре 150°С приводит к росту твердости, т.е. старение превалирует над разупрочнением, которое сдерживают дисперсоиды фаз Al20Cu2Mn3 и Al3(Zr,Y) и достаточно дисперсные частицы фаз Al8Cu4Y и (Al,Cu)11Y3 кристаллизационного происхождения. При 210°С разупрочнение перекрывает эффект от старения, и твердость незначительно снижается. Добавка марганца позволяет сохранить существенно более высокий уровень твердости в исследуемом сплаве при температурах отжига вплоть до 550°С и повысить температуру начала рекристаллизации до 350–400°С. По результатам испытаний на одноосное растяжение исследуемый сплав демонстрирует высокий уровень характеристик механических свойств после отжига прокатанных листов при 150°С: σ0.2 = 330–334 МПа, σв = 374 МПа при δ = 3.6–5.5%.
Работа выполнена при финансовой поддержке Российского Научного Фонда (проект № 19-79-10242).
Список литературы
ГОСТ 1583–93. Сплавы алюминиевые литейные ТУ-Минск: ИПК Изд-во стандартов, 2000.
ГОСТ 4784–2019. Алюминий и сплавы алюминиевые деформируемые. Марки: ИПК Изд-во стандартов, 2019
Zolotorevsky V.S., Belov N.A., Glazoff M.V. Casting Aluminum Alloys, Alcoa Technical Center, Alcoa Center, PA, United States, 2007. 530 p.
Новиков И.И. Горячеломкость цветных металлов и сплавов. М.: Наука, 1966. 299 с.
Zolotorevskiy V.S., Pozdniakov A.V. Determining the hot cracking index of Al–Si–Cu–Mg casting alloys calculated using the effective solidification range // Int. J. Cast Met. Res. 2014. V. 27. № 4. P. 193–198.
Zolotorevskiy V.S., Pozdniakov A.V., Churyumov A.Yu. Search for promising compositions for developing new multiphase casting alloys based on Al–Cu–Mg matrix using thermodynamic calculations and mathematic simulation // Phys. Met. Metall. 2012. V. 113. № 11. P. 1052–1060.
Pozdnyakov A.V., Osipenkova A.A., Popov D.A., Makhov S.V., Napalkov V.I. Effect of Low Additions of Y, Sm, Gd, Hf and Er on the Structure and Hardness of Alloy Al–0.2% Zr–0.1% Sc // Met. Sci. Heat Treat. 2017. V. 58. № 9–10. P. 537–542.
Pozdniakov A.V., Aytmagambetov A.A., Makhov S.V., Napalkov V.I. Effect of impurities of Fe and Si on the structure and strengthening upon annealing of the Al–0.2% Zr–0.1% Sc alloys with and without Y additive // Phys. Met. Metall. 2017. V. 118. № 5. P. 479–484.
Pozdnyakov A.V., Barkov R.Yu. Effect of impurities on the phase composition and properties of a new alloy of the Al–Y–Er–Zr–Sc system // Metallurgist 2019. V. 63. № 1–2. P. 79–86.
Pozdniakov A.V., Barkov R.Yu., Prosviryakov A.S., Churyumov A.Yu., Golovin I.S., Zolotorevskiy V.S. Effect of Zr on the microstructure, recrystallization behavior, mechanical properties and electrical conductivity of the novel Al–Er–Y alloy // J. Alloys Compd. 2018. V. 765. P. 1–6.
Pozdniakov A.V., Barkov R.Yu. Microstructure and mechanical properties of novel Al–Y–Sc alloys with high thermal stability and electrical conductivity // J. Mater. Sci. Technol. 2020. V. 36. P. 1–6.
Pozdniakov A.V., Yarasu V., Barkov R.Yu., Yakovtseva O.A., Makhov S.V., Napalkov V.I. Microstructure and mechanical properties of novel Al–Mg–Mn–Zr–Sc–Er alloy // Mat. Let. 2017. V. 202. P. 116–119.
Song M., Du K., Huang Z.Y., Huang H., Nie Z.R., Ye H.Q. Deformation-induced dissolution and growth of precipitates in an Al–Mg–Er alloy during high-cycle fatigue // Acta Mater. 2014. V. 81. P. 409–419.
Hao H.L., Ni D.R., Zhang Z., Wang D., Xiao B.L., Ma Z.Y. Microstructure and mechanical properties of Al–Mg–Er sheets jointed by friction stir welding // Mater. Des. 2013. V. 52. P. 706–712.
Wen S.P., Wang W., Zhao W.H., Wu X.L., Gao K.Y., Huang H., Nie Z.R. Precipitation hardening and recrystallization behavior of Al–Mg–Er–Zr alloys // J. All. Comp. 2016. V. 687. P. 143–151.
Barkov R.Yu., Pozdniakov A.V., Tkachuk E., Zolotorevskiy V.S. Effect of Y on microstructure and mechanical properties of Al–Mg–Mn–Zr–Sc alloy with low Sc content // Mater. Lett. 2018. V. 217. P. 135–138.
Li M., Wang H., Wei Z., Zhu Z. The effect of Y on the hot-tearing resistance of Al–5 wt % Cu based alloy // Mat. and Des. 2010. V. 31. P. 2483–2487.
Belov N.A., Khvan A.V., Alabin A.N. Microstructure and phase composition of Al–Ce–Cu alloys in the Al-rich corner // Mater. Sci. Forum. 2006. V. 519–521(PART 1). P. 395–400.
Belov N.A., Khvan A.V. The ternary Al–Ce–Cu phase diagram in the aluminum-rich corner // Acta Mater. 2007. V. 55. P. 5473–5482.
Pozdniakov A.V., Barkov R.Y. Microstructure and materials characterisation of the novel Al–Cu–Y alloy // Mater. Sci. Tech. 2018. V. 34. № 12. P. 1489–1496.
Amer S.M., Barkov R.Y., Yakovtseva O.A., Pozdniakov, A.V. Comparative Analysis of Structure and Properties of Quasibinary Al–6.5Cu–2.3Y and Al–6Cu–4.05Er Alloys // Phys. Met. Metall. 2020. V. 121. № 5. P. 476–482.
Pozdnyakov A.V., Barkov R.Yu., Sarsenbaev Zh., Amer S.M., Prosviryakov A.S. Evolution of Microstructure and Mechanical Properties of a New Al–Cu–Er Wrought Alloy // Phys. Met. Metall. 2019. V. 120. № 6. P. 614–619.
Amer S.M., Barkov R.Y., Pozdniakov A.V. Effect of Impurities on the Phase Composition and Properties of a Wrought Al–6% Cu–4.05% Er Alloy // Phys. of Met. and Metall. 2020. V. 121. № 5. P. 495–499.
Pozdniakov A.V., Barkov R.Yu., Amer S.M., Levchenko V.S., Kotov A.D., Mikhaylovskaya A.V. Microstructure, mechanical properties and superplasticity of the Al–Cu–Y–Zr alloy // Mater. Sci. Eng. A. 2019. V. 758. P. 28–35.
Amer S.M., Barkov R. Yu., Yakovtseva O.A., Loginova I.S., Pozdniakov A.V. Effect of Zr on microstructure and mechanical properties of the Al–Cu–Er alloy // Mater. Sci. Tech. 2020. V. 36. № 4. P. 453–459.
Amer S.M., Yakovtseva O.A., Loginova I.S., Medvedeva S.V., Prosviryakov A.S., Bazlov A.I., Barkov R.Yu. and Pozdniakov A.V. The Phase Composition and Mechanical Properties of the Novel Precipitation-Strengthening Al–Cu–Er–Mn–Zr Alloy // Appl. Sci. 2020. V. 10. № 15. P. 5345–5353.
Mikhaylovskaya A.V., Kishchik A.A., Kotov A.D., Rofman O.V., Tabachkova N.Yu. Precipitation behavior and high strain rate superplasticity in a novel fine-grained aluminum based alloy // Mater. Sci. Eng. A. 2019. V. 760. P. 37–46.
Mochugovskiy A.G., Tabachkova N.Yu., Mikhaylovskaya A.V. Annealing induced precipitation of nanoscale icosahedral quasicrystals in aluminum based alloy // Mat. Lett. 2019. V. 247. P. 200–203.
Kishchik A.A., Mikhaylovskaya A.V., Levchenko V.S., Portnoy V.K. Formation of microstructure and the superplasticity of Al–Mg-based alloys // Phys. Met. Metall. 2017. V. 118. № 1. P. 96–103.
ГОСТ 21631–76. Листы из алюминия и алюминиевых сплавов. Технические условия. Стандартинформ, 2008.
Zolotorevskiy V.S., Dobrojinskaja R.I., Cheverikin V.V., Khamnagdaeva E.A., Pozdniakov A.V., Levchenko V.S., Besogonova E.S. Evolution of structure and mechanical properties of Al–4.7Mg–0.32Mn–0.21Sc–0.09Zr alloy sheets after accumulated deformation during rolling // Phys. Met. Metall. 2016. V. 117. № 11. P. 1163–1169.
Zolotorevskiy V.S., Dobrojinskaja R.I., Cheverikin V.V., Khamnagdaeva E.A., Pozdniakov A.V., Levchenko V.S., Besogonova E.S. Strength and Substructure of Al–4.7Mg–0.32Mn–0.21Sc–0.09Zr Alloy Sheets // Phys. Met. Metall. 2017. V. 118. № 4. P. 407–414.
Дополнительные материалы отсутствуют.
Инструменты
Физика металлов и металловедение