Физика металлов и металловедение, 2020, T. 121, № 12, стр. 1324-1330
Трансформация структуры, параметров фаз при старении сплава титана Ti–10V–2Fe–3Al и их связь упрочнением
А. В. Желнина a, *, М. С. Калиенко a, b, А. Г. Илларионов b, c, Н. В. Щетников a
a ПАО “Корпорация ВСМПО-АВИСМА”
Верхняя Салда, Россия
b ФГАОУ ВО Уральский федеральный университет имени первого Президента России Б.Н. Ельцина
620002 Екатеринбург, ул. Мира, 19, Россия
c Институт физики металлов УрО РАН
620108 Екатеринбург, ул. С. Ковалевской, 18, Россия
* E-mail: illarionovag@mail.ru
Поступила в редакцию 28.07.2020
После доработки 04.08.2020
Принята к публикации 19.08.2020
Аннотация
Методами растровой электронной сканирующей микроскопии, микрорентгеноспектрального, рентгеноструктурного фазового анализа и дюрометрии рассмотрено изменение структуры, фазового состава и твердости в закаленном титановом сплаве Ti–10V–2Fe–3Al в ходе старения в течение 2–32 ч при температуре 500°С. Впервые с использованием метода полнопрофильного РСФА осуществлен комплексный анализ изменения параметров кристаллической решетки первичной и вторичной α-фазы, формируемых при старении в сплаве. Показано, что изменение твердости сплава при старении определяется как размером образующихся частиц вторичной α-фазы, так и изменением легированности матричного β-твердого раствора.
ВВЕДЕНИЕ
Высокопрочные сплавы титана на основе β‑фазы, к которым относится сплав Ti–10V–2Fe–3Al (далее по тексту Ti–10–2–3), являются основными конструкционными авиационными материалами для получения высоконагруженных элементов планера и узлов шасси [1], благодаря сочетанию высокой удельной и усталостной прочности, вязкости разрушения, прокаливаемости и ряда других свойств. Комплекс свойств сплава Ti‒10–2–3 формируется в ходе проведения операций закалки из (α + β)-области и последующего старения (упрочняющей термической обработки – УТО) или термомеханических обработок, связанных с процессами распада метастабильного β‑твердого раствора [1–6]. При этом свойства сплава достаточно чувствительны к колебанию химического состава сплава в пределах марки и параметров УТО, которые определяют характерные изменения, происходящие при старении [1, 6]. В этом аспекте представляют интерес идущее в ходе распада метастабильной β-фазы диффузионное перераспределение легирующих элементов между α-, β‑фазами при старении сплава.
Известно [7], что легирующие элементы имеют различную максимальную растворимость в фазах, и присутствующий в сплаве α-стабилизатор – Al имеет большую растворимость в α-твердом растворе, а V и Fe, являющиеся β-стабилизаторами, растворяются в основном в β-матрице. Концентрация легирующих элементов в фазах также зависит от пути получения структурно-фазового состояния [8], однако в литературе не удалось найти комплексного анализа закономерностей данных изменений при старении сплава Ti–10–2–3. Происходящее при старении перераспределение легирующих элементов между фазами определяет физико-механические свойства элементов структуры, влияет на уровень упрочнения α-, β-фаз, критические напряжения начала пластической деформации, проницаемость межфазных границ [9–11]. В связи с этим изучение указанных явлений помогает прояснить закономерности превращений, протекающих в (α + β)-титановых сплавах при термической обработке, и найти их взаимосвязь с комплексом механических свойств. Следует отметить, что прямое измерение концентрации легирующих элементов с высокой локальностью, сопоставимой с типичными размерами вторичной α‑фазы (30–60 нм), весьма затруднительно и требует наличия дорогостоящего оборудования, например, атомного-силового томографа или электронного просвечивающего микроскопа со специальными аналитическими приставками [12, 13]. Однако такой широкодоступный метод РСФА также позволяет качественно, а в ряде случаев и количественно, анализировать динамику происходящих диффузионных процессов на основании изменения периодов кристаллической решетки фаз [5]. Исходя из вышесказанного, цель работы – провести анализ изменения структуры, фазового состава, включая эволюцию параметров и легированности фаз, и их влияние на упрочнение при старении закаленного сплава Ti–10–2–3.
МАТЕРИАЛ И МЕТОДИКИ
Материалом исследования служил пруток диаметром 20 мм из сплава состава Ti–9.3V–1.8Fe–3.0Al (вес. %), после горячей деформации в (α + + β)-области, произведенный на ПАО “Корпорация ВСМПО-АВИСМА”. Пруток был подвергнут УТО, включающей закалку в воду из (α + β)-области от температуры нагрева 753°С, а затем старение с выдержками 2, 4, 8, 16, 32 ч при 500°С.
Анализ микроструктуры и локального химического состава термообработанных образцов проводили на микрошлифах с продольного сечения прутка методом растровой электронной микроскопии (РЭМ) c использованием детектора обратно-отраженных электронов (BSED) на приборе Quanta 3D FEG с приставкой для микрорентгеноспектрального анализа (МРСА) EDAX Genesis 2000. Рентгеноструктурный фазовый анализ (РСФА) с расчетом параметров фиксируемых фаз осуществляли на дифрактометре Bruker D8 Advance с детектором LynxEye в CuKα-излучении в диапазоне углов 2Θ = 34°–105° с шагом 0.02° и экспозицией в точке 1 с. В программе TOPAS 3 [14] проводили полнопрофильный анализ полученных дифрактограмм с использованием для подгонки профильной функции уточненных параметров модели, состоящей из трех фаз: две α‑фазы первичная (αI), вторичная (αII), имеющие ГПУ-решетку, и матричная β-фаза с ОЦК-решеткой. Твердость по Виккерсу закаленных и состаренных образцов измеряли на приборе DuraScan50 при нагрузке 9.8 Н.
РЕЗУЛЬТАТЫ И ОБСУЖДЕНИЕ
На дифрактограмме, снятой с закаленного сплава (рис. 1) фиксируются интенсивные линии от матричной β- и первичной αI-фаз, которые имеют периоды решеток – аβ = 3.2410 A, aαI = = 2.93201 A, cαI = 4.67843 A, (с/аαI = 1.5956).
Линии αI-фазы имеют разделение на Кα1–Кα2 дублет (рис. 1), что обычно фиксируется при минимальной плотности дислокаций в фазе [15] и в данном случае связано с протеканием в ней в ходе нагрева и выдержки при температуре закалки процессов сфероидизации и рекристаллизации.
Анализ структуры закаленного сплава (рис. 2а) показал, что первичная αI-фаза действительно имеет форму глобулей размером 2–3 мкм и располагается преимущественно по границам β-субзерен.
Следует отметить, что мы не обнаружили в закаленном сплаве Ti–10–2–3 α"-мартенсита, часто фиксируемого при охлаждении в воде [2, 16]. Очевидно, это связано с тем, что легированность β-твердого раствора при закалке из двухфазной (α + β)-области обеспечивает снижение ниже комнатной температуры начала мартенситного превращения (Mн).
Оценка температуры Мн по формуле из [17]: Мн = Тпп–80Moэкв–7Alэкв, где Тпп – температура полиморфного (α + β)–β-превращения сплава (в данном случае была определена методом пробных закалок и составила 798°C), Moэкв, Alэкв – так называемые молибденовый и алюминиевый эквиваленты сплава [1], учитывающие с определенными коэффициентами содержание β- и α-стабилизаторов в сплаве соответственно. Исходя из рассчитанного в программном пакете JMatPro среднего химического состава β-фазы при температуре закалки (в мас. %) – Ti–10.967V–2.12Fe–2.86Al получено:
т.е. действительно ниже комнатной температуры.
Твердость закаленного из (α + β)-области сплава составила 287 ± 2 ед. HV (рис. 3). Это выше, чем указанная в работах [5, 18] (260–275 ед. HV) после закалки из β-области. Более высокую твердость сплава в нашем случае мы связываем с фиксацией мелкого β-субзерна размером около 4 мкм (150 мкм в работе [5]) вследствие торможения его роста частицами αI-фазы, которая отсутствовала в работах [5, 18].
Структура сплава Ti–10–2–3 после старения представлена на рис. 4а, 4б. В отличие от закаленного состояния в структуре кроме αI-фазы в β‑матрице фиксируются дисперсные пластинчатые выделения αII-фазы, склонные к росту с увеличением времени старения.
Рис. 4.
Структура сплава Ti–10–2–3 после старения при 500°С с выдержками 2 (а) и 32 ч (б) и данные изменения химического состава фаз (в) после времени старения 32 ч.
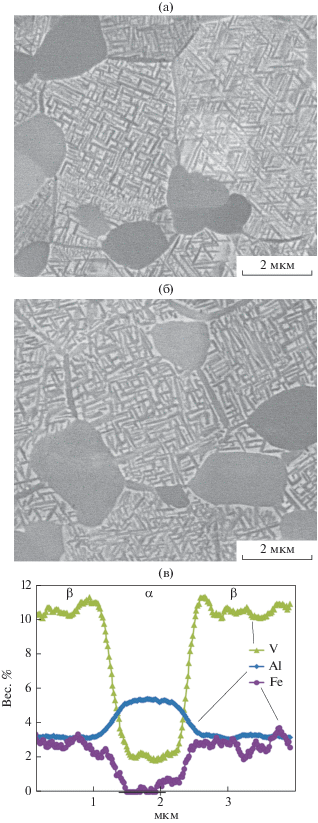
Выделение αII-фазы при старении способствует дисперсионному упрочнению сплава, обеспечивая ему более высокую твердость по сравнению с закаленным состоянием (рис. 3). В то же время по мере увеличения времени старения от 2 до 32 ч происходит снижение твердости сплава (рис. 3), наблюдавшееся так же в работе [3] и в нашем случае связанное с отмеченным выше укрупнением частиц αII-фазы (рис. 4а, 4б).
На рентгенограммах состаренных сплавов наблюдается наложение линии αI- и αII-фаз (рис. 1). Для разделения этих линий применили метод полнопрофильного анализа. На рис. 5 представлены рентгенограммы состаренных образцов с наложением смоделированных при полнопрофильном анализе линий αI- и αII-фаз.
После полнопрофильного анализа сплава, состаренного в течение 32-х ч, фиксируется разделение на Кα1–Кα2 дуплет дифракционных линии αII-фазы. Это дает основание говорить о достижении порогового уровня размера ее кристаллитов, при котором размерный фактор перестает вносить существенный вклад в уширение линий [19]. По полученным методом РСФА данным рассчитано изменение при старении размера области когерентного рассеяния (ОКР) αII-фазы, напрямую связанной с ее размерами [20]. ОКР αII-фазы и соответственно ее размер закономерно растет по мере увеличения времени старения (рис. 6а), что согласуется с данными микроструктуры (рис. 4а, 4б).
Рис. 6.
Изменение с временем выдержки при старении сплава Ti–10–2–3 параметров α-фазы (а, в–е) и β-фазы (б).
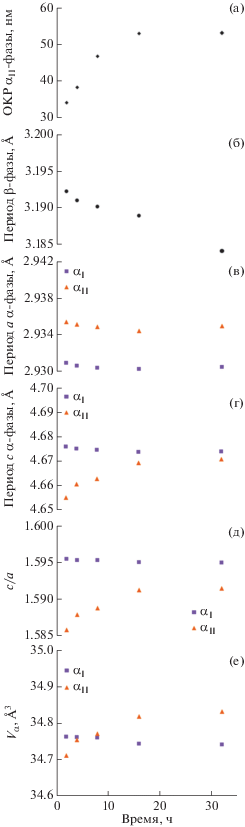
С увеличением времени старения фиксируется изменение положения дифракционных линий фаз и соответственно периодов решеток α- и β-фаз в сплаве (рис. 6б–6г). Как известно [8, 21], это связано с перераспределением между α- и β-фазами легирующих элементов замещения (Al, V и Fe) [7, 10], имеющих меньшие атомные размеры по сравнению с титаном [22]. По данным работ [22, 23], период ОЦК-решетки β-фазы зависит от содержания в ней Al, V, Fe (в ат. %) следующим образом:
(1)
$\begin{gathered} {{а}_{\beta }} = 3.282--(0.154\% {\text{ Al}}--0.236\% {\text{V}}-- \\ - \,\,0.5445\% {\text{ Fe}}) \times {{10}^{{--2}}}\left( {\text{{\AA}}} \right). \\ \end{gathered} $Растворяясь в α-фазе, Al, V и Fe также уменьшают периоды “а”, “с” ее кристаллической решетки, но при этом алюминий увеличивает параметр “с/а” [22], а ванадий и железо его уменьшают [22–24].
Анализ полученных зависимостей параметров и объемов элементарных ячеек кристаллических решеток αI, αΙΙ, β-фаз в зависимости от времени старения (рис. 5) показал, что с увеличением времени старения от 2 до 32 ч наблюдается преимущественное уменьшение периодов решеток аβ, aαI, cαΙ, параметра (с/a)αI,Vβ, VαI, рост периодов aαII,cαII, VαII и практически не меняется параметр (с/a) αΙΙ. Уменьшение периода aβ и соответственно объема элементарной ячейки Vβ вызвано обогащением β-фазы β-стабилизаторами – ванадием и железом в результате их перехода в β-твердый раствор из образующейся в ходе старения αII-фазы, которая обедняется этими элементами все в большей степени с увеличением времени старения за счет образования более крупных и соответственно более равновесных выделений с меньшим содержанием β-стабилизаторов. Постепенное с увеличением времени старения уменьшение содержания ванадия и железа в αII-фазе обеспечивает закономерный рост периодов aαII, cαII и объема ее элементарной ячейки VαII, так как αII‑фаза обедняется по элементам (V, Fe) с минимальным атомным радиусом. Близкое в течение старения к постоянному значение параметра (с/a)αII, по-видимому, связано с близкой скоростью роста периодов aαII, cαII в результате изменения ее легирования.
Незначительное снижение в ходе старения всех параметров αΙ-фазы (aαI, cαΙ, с/a αI, VαI), объясняется ее постепенным обогащением ванадием и железом при незначительном снижении содержания алюминия в ходе старения по сравнению с закаленным состоянием (рис. 2б, 4в).
В целом параметры αΙ и αΙΙ-фаз с увеличением продолжительности старения меняются в разных направлениях: для αΙ -фазы они уменьшаются, а для αΙΙ-фазы – увеличиваются. Причина этого – разный химический состав фаз, которые участвуют в трансформации αΙ- и αΙΙ-фаз в ходе старения. Для αΙ-фазы – это непосредственно она сама, обогащенная по алюминию и обедненная по ванадию и железу после закалки по отношению к состаренному состоянию, а для αΙΙ-фазы – это матричный β-твердый раствор, который по отношению к αΙΙ-фазе обогащен по ванадию, железу и обеднен по алюминию. Одним из интересных результатов, связанных с этим, является то, что после старения в течение более 10-ти ч (рис. 6е) объем элементарной ячейки VαII оказывается больше, чем объем элементарной ячейки VαI, хотя при менее длительных временах старения было наоборот (VαI > VαII). Из этого можно заключить, что при старении с выдержками более 10 ч содержание легирующих элементов в αΙΙ-фазе оказывается меньше, чем в αΙ-фазе, а на начальных стадиях старения было наоборот. По нашему мнению, данный эффект связан с различным размером αΙ, αΙΙ-фаз (рис. 2). Размер αΙ-фазы на 2 порядка больше αΙΙ-фазы и выравнивание ее состава до состояния, близкого к равновесному, происходит значительно медленнее, чем в αΙΙ-фазе, так как известно [25], что диффузионный путь, проходимый элементом при постоянной температуре, пропорционален квадратному корню из времени выдержки при этой температуре.
Как было отмечено выше (рис. 3), в ходе старения наблюдается повышение дюрометрических характеристик, которое можно связать с выделением дисперсных частиц αΙΙ-фазы. Эффект упрочнения снижается при длительных выдержках, и одной из причин этого является укрупнение αΙΙ-частиц (рис. 4а, 4б). Оценка величины упрочнения при старении за счет роста αΙΙ-частиц показала, что, если учитывать только дисперсионное упрочнение, снижение твердости должно быть больше, чем фиксируется в эксперименте. Так после двухчасового старения разница в твердости между состаренным и закаленным состоянием, то есть упрочнение, составляет 89 ед. HV (377-288), а после 32-х часового старения – 70 ед. HV (358–288). В то же время, согласно данным РСФА (рис. 6а), по ОКР, связанным с размером частиц αΙΙ-фазы, увеличение продолжительности старения от 2-х до 32 ч приводит к росту ОКР в 1.56 раза (53 нм/34 нм). Как известно [25], эффект дисперсионного упрочнения обратно пропорционален размеру выделяющихся частиц (τ ≈ Gb√f/r, где τ – критическое сдвиговое напряжение, G – модуль сдвига в β-матрице, b – вектор Бюргерса в β-матрице, f – объемная доля частиц αΙΙ-фазы, r – размер частиц αΙΙ-фазы). Минимальное в работе время старения при 500°C 2 ч превышает, согласно данным [2], время условного конца распада в сплаве Ti–10–2–3, поэтому f-объемная доля частиц αΙΙ-фазы практически постоянна в интервале выдержек 2–32 ч. Близкие значения будут иметь значения G, b. Из этого следует, что на величину τ главным образом влияет параметр r – размер частиц αΙΙ-фазы. Поэтому, если эффект упрочнения связан только с дисперсностью αΙΙ- частиц, то после 32‑часового старения его величина не должна была превышать 57 ед. HV (89 ед. HV/1.56), а она оказалась на 13 единиц больше – 70 ед. HV. Т.е. кроме дисперсионного упрочнения при увеличении времени старения в сплаве происходит дополнительное упрочнение, которое, исходя из результатов работы [18], можно связать с твердорастворным упрочнением β-матрицы в результате отмеченного выше ее обогащения по ванадию и железу в ходе старения. Оценим возможный порядок такого упрочнения, опираясь на изменение периода решетки β-фазы.
Выше отмечено, что, зная содержание легирующих элементов Al, Fe, V, период решетки β-фазы в сплаве Ti–10–2–3 можно оценить по формуле (1). Для оценки равновесного содержания алюминия, ванадия, железа в α- и β-фазе в исследуемом сплаве при температуре старения 500°С произведен расчет в программном пакете JMatPro (табл. 1).
Таблица 1.
Расчетное равновесное содержание легирующих элементов в α, β-фазах в сплаве Ti–10–2–3 (мас. %) при температуре 500°С
Фазы | V | Fe | Al |
---|---|---|---|
αI,II-фаза | 1.35 | 0.02 | 3.38 |
β-фаза | 31.12 | 6.46 | 1.99 |
Расчетное содержание легирующих элементов в β-фазе при температуре 500°С хорошо соотносится с экспериментально определенным в сплаве в работе [26] при 500°С – Ti–2Al–16V–6.4Fe. Исключение составляет содержание ванадия, которого при 500°С согласно расчетам в β-фазе должно быть в 2 раза больше, чем получено в работе [26]. В то же время, по полученным (рис. 4в) нами данным МРСА, в αΙ-фазе после старения содержание ванадия около 1.8%, а в αΙΙ-фазе, исходя из анализа данных на рис. 6е, еще ниже. Согласно данным работы [16], объемная доля β-фазы при 500°С в сплаве составляет около 30%. Расчет в этом случае показывает, что при содержании в сплаве 9.3 мас. % ванадия в β-матрице должно содержаться ванадия не менее 25% (9.3–1.8)/0.3. В пределах 20% погрешности сопоставимо с расчетными данными.
По сравнению со средним химическим составом сплава по расчетам наиболее сильно после старения в β-фазе изменяется содержание ванадия и железа (в 3 и более раз), и менее значительно содержание алюминия (не более, чем в 1.5 раза). Кроме того, алюминий, исходя из коэффициентов в формуле (1), вносит наименьший вклад в изменение периода решетки β-фазы. Перевод расчетного содержания ванадия и железа в сплаве в атомные проценты показал, что при температуре 500°С расчетное отношение %V/%Fe составляет 5.28/1. В связи с этим для простоты расчетов было решено считать содержание алюминия в β‑фазе при увеличении времени старения постоянным и расчет вести исходно только через условное содержание железа. Сделав такие допущения, оценено изменение содержания ванадия и железа в β-фазе при увеличении времени старения от 2 до 32 ч по следующей формуле:
Получили Δa = –0.84 нм и тогда ΔFe = 0.487 ат. % (0.575 мас. %), ΔV = 5.28ΔFe = 2.572 ат. %. (2.77 мас. %).
В результате обогащения β-матрицы ванадием и железом при увеличении времени старения от 2 до 32 ч, происходит увеличение прочностного молибденового эквивалента [27] β-твердого раствора на ΔMo = 2.77%V/1.7 + 0.575%Fe/0.7 = 2.45, что дает вклад в увеличение прочности Δσ = 50ΔMo = = 50 × 2.45 = 122.5 МПа. Для титановых сплавов известна связь между σ и HV [7, 18]: σ = 9.81/3 × HV, из которой ΔΗV = 3Δσ/9.81. С учетом объемной доли β-фазы в структуре (≈30%) прирост твердости по расчету составил ΔΗV = (3 × 122.5 МПа/9.81м/с2) × 0.3 = 11 ед. НV. Произведенный расчет вклада твердорастворного упрочнения β-фазы за счет обогащения ванадием и железом при увеличении времени старения дал величину 11 ед. HV, что в пределах ошибки 15% дает необходимые 13 ед. HV, чтобы компенсировать разупрочнение за счет роста αΙΙ-частиц.
ВЫВОДЫ
1. Фиксируемое при закалке фазовое состояние в сплаве Ti–10–2–3 определяется распределением легирующих элементов в β- и αΙ-фазах и характеризуется более высокой твердостью по сравнению с имеющимися в литературе данными при закалке из β-области.
2. Старение сплава при 500°С в течение 2–32 ч приводит к выделению из β-матрицы дисперсных частиц αΙΙ-фазы, которые склонны к росту по мере увеличения продолжительности выдержки.
3. Показано, что упрочнение сплава при увеличении времени выдержки при старении зависит по крайней мере, от двух составляющих – дисперсионного упрочнения за счет αΙΙ-фазы, уровень которого снижается из-за роста ее размеров, и твердорастворного упрочнения β-матрицы, которое растет за счет ее обогащения ванадием и железом.
4. Установлено, что перераспределение легирующих элементов (Al, V, Fe) в ходе старения между β, αΙ, αΙΙ обеспечивает закономерное изменение параметров кристаллических решеток этих структурных составляющих.
Авторы признательны программе поддержки ведущих университетов РФ в целях повышения их конкурентоспособности № 211 Правительства РФ № 02.А03.21.0006.
Список литературы
Cotton J.D., Briggs R.D., Boyer R.R., Tamirisakandala S., Russo P., Shchetnikov N., Fanning J.C. State of the Art in Beta Titanium Alloys for Airframe Applications // JOM. 2015. V. 67. № 6. P. 1281–1303.
Duerig T.W., Terlinde G.T., Williams J.C. Phase transformations and tensile properties of Ti–10V–2Fe–3Al // Met.Trans. A. 1980. V. 11A. P. 1980–1987.
Илларионов А.Г., Корелин А.В., Попов А.А., Илларионова С.М., Елкина О.А. Формирование структуры, фазового состава и свойств в титановом сплаве ВТ22И при изотермической и термомеханической обработке // ФММ. 2018. Т. 119. № 8. С. 827–835.
Шаболдо О.П., Виторский Я.М., Сагарадзе В.В., Печеркина Н.Л., Скотникова М.А. Формирование структуры и свойств β-титанового сплава при термомеханической обработке // ФММ. 2017. Т. 118. № 1. С. 79–84.
Илларионов А.Г., Трубочкин А.В., Шалаев А.М., Илларионова С.М., Попов А. А. Изотермический распад β-твердого раствора в титановом сплаве Ti–10V–2Fe–3Al // МиТОМ. 2016. № 11. С. 36–41.
Boyer R.R., Kuhlman G.W. Processing properties relationships of Ti–10V–2Fe–3Al // J. Metall. Trans. A. 1987. V. 18. P. 2095–2103.
Collings E.W. The Physical Metallurgy of Titanium Alloys, Park, Ohio, 1984. 261 p.
Li T., Ahmed M., Sha G. Shi R., Casillas G., Yen H.-W., Wang Y., Pereloma E.V., Cairney J.M. The influence of partitioning on the growth of intragranular α in near-β Ti alloys // J. Alloys Compd. 2015. V. 643. P. 212–222.
Wang C.Y., Yang L.W., Cui Y.W., Pérez-Prado M.T. High throughput analysis of solute effects on the mechanical behavior and slip activity of beta titanium alloys // Materials & Design. 2018. V. 137. P. 371–383.
Zou C., Li J., Wang W.Y. Zhang Y., Tang B., Kou H., Wang H., Wang J., Xu D., Lin D. Revealing the local lattice strains and strengthening mechanisms of Ti alloys // Comput. Mater. Sci. 2018. V. 152. P. 169–177.
Pan Y., Sun Q., Xiao L. Ding X. Juan L. Plastic deformation behavior and microscopic mechanism of metastable Ti–10V–2Fe–3Al alloy single crystal pillars orientated to 〈011〉β in submicron scales Part II: Phase transformation dependence of size effect and deformation mechanism // Mater. Sci. Eng. A. 2019. V. 743. P. 804–810.
Gault B., Moody M.P., Cairney S.P., Ringer S.P. Atom probe microscopy. Springer Science & Business Media, 2012. V. 160. 396 p.
Williams D.B., Carter C.B. Transmission Electron Microscopy: Spectrometry. IV. N.Y.: Plenum Press, 1996. 610 p.
TOPAS. v3, General Profile and Structure Analysis Software for Powder Diffraction Data. User’s manual. Karlsruhe, Germany: Bruker AXS, 2005.
Dragomir I.C., Li D.S., Castello-Branco G.A., Garmestani, Snyder R.L., Ribarikd G., Ungar T. Evolution of dislocation density and character in hot rolled titanium determined by X-ray diffraction // Mater. Charact. 2005. V. 55. P. 66–74.
Barriobero-Vita P, Requena G., Warchomicka F., Stark A., Shell N., Buslaps T. Phase transformation kinetics during continuous heating of a β-quenched Ti–10V–2Fe–3Al alloy // J. Mater. Sci. 2015. V. 50. P. 1412–1426.
Водолазский Ф.В., Илларионов А.Г., Попов А.А., Ледер М.О., Жлоба А.В., Скидан А.В. Исследование процессов изотермического распада β-твердого раствора в титановом сплаве VST2 // МиТОМ, 2015. № 8. С. 11–16.
Li P., Zhang T. Sun X., Zhang H., Wang D., Sun Q, Xiao L., Sun J. Secondary hardening behavior in Ti alloy // Mater. Sci. Eng. A. 2019. V. 759. P. 640–647.
Uvarov V., Popov I. Metrological characterization of X‑ray diffraction methods at different acquisition geometries for determination of crystallite size in nano-scale materials // Mater. Charact. 2013. V. 85. P. 111–123.
Kalienko M.S., Volkov A.V., Zhelnina A.V. Use of Full-Profile X-ray Analysis for Estimation of the Dispersity of the Secondary Alpha Phase in High-Strength Titanium Alloys // Crystallogr. Rep. 2020. V. 65. P. 412–416.
Chen F. W., Xu G, Zhang X.Y., Zhou K.-C., Cui Y. Effect of α morphology on the diffusional β ↔ α transformation in Ti–55531 during continuous heating: Dissection by dilatometer test, microstructure observation and calculation // J. Alloys Compd. 2017. V. 702. P. 352–365.
Цвиккер У. Титан и его сплавы. М.Мир, 1979. 512 с.
Shao G., Miodownik A.P., Tsakiropoulos P. ω-phase formation in V–Al and Ti–Al–V alloys // Philosophical Magazine A. 1995. V. 71. № 6. P. 1389–1408.
Kilmametov A. Ivanisenko Yu, Straumal B., Mazilkin A.A., Hahn H. Gomakova A.S., Kriegel M.J., Fabrichnaya O.B., Rafaia D. Transformations of α' martensite in Ti–Fe alloys under high pressure torsion // Scr. Mater. 2017. V. 136. P. 46–49.
Готтштайн Г. Физико-химические основы материаловедения, М.: Бином, 2014. 402 с.
Ahmed M. Wexler D., Casillas G., Ivasishin O.M., Peraloma E. The influence of β phase stability on deformation mode and compressive mechanical properties of Ti–10V–2Fe–3Al alloy // Acta Mat. 2015. V. 84. P. 124–154.
Ильин А.А., Колачев Б.А., Полькин И.С. Титановые сплавы. Состав, структура, свойства. Справочник. М.: ВИЛС. 2009. 520 с.
Дополнительные материалы отсутствуют.
Инструменты
Физика металлов и металловедение