Физика металлов и металловедение, 2020, T. 121, № 2, стр. 207-215
Влияние условий механоактивации и ПАВ на фазовый состав и свойства композитов на основе карбогидрида титана и меди
М. А. Еремина a, *, С. Ф. Ломаева a, С. Н. Паранин b, В. В. Тарасов a
a УдмФИЦ УрО РАН
426067 Ижевск, ул. Т. Барамзиной, 34, Россия
b Институт электрофизики УрО РАН
620016 Екатеринбург, ул. Амундсена, 106, Россия
* E-mail: mrere@mail.ru
Поступила в редакцию 13.08.2019
После доработки 19.09.2019
Принята к публикации 26.09.2019
Аннотация
Изучена возможность получения композитов на основе гексагонального карбогидрида титана и меди с помощью двух- и трехстадийной механоактивации порошков титана и меди в жидком углеводороде с последующим магнитно-импульсным прессованием. Применение ПАВ при трехстадийном способе получения позволяет сдержать формирование интерметаллидов в процессе механоактивации и снизить долю интерметаллидов в компактных образцах. Проведена оценка плотности, микротвердости, абразивной износостойкости и параметров износа в условиях сухого трения со стальным шариком. Показано, что двух- и трехстадийный способы получения порошков предпочтительнее, поскольку коэффициенты трения и величины износа в парах трения оказались существенно ниже, чем для композитов, полученных одностадийным способом.
ВВЕДЕНИЕ
Карбогидриды титана получают в условиях высоких температур и давлений [1, 2], а также механоактивацией (МА) порошков Ti в жидких углеводородах с последующей термообработкой [3–5]. Последний способ имеет преимущество, поскольку дисперсные и однородные по размерам частиц порошки карбогидрида можно получить при механоактивации в течение 3‑4 ч и отжиге при температурах 500–600°С, 1 ч. Синтезированы карбогидриды титана с гранецентрированной кубической (ГЦК) и гексагональной плотноупакованной (ГПУ) решетками. Последние наиболее термически стабильны – температура начала их распада превышает 900°С. Карбогидриды титана содержат до 2.3 мас. % водорода [5], обладают высокой термической стабильностью. Они перспективны в качестве материалов для биологической защиты в ядерной энергетике [6], могут использоваться как прекурсоры для создания покрытий из карбида титана [7], в виде композиционных твердых и износостойких сплавов [4], могут служить в качестве упрочняющей добавки для электроконтактных материалов. Несмотря на широкие возможности применения данных материалов, они остаются мало изученными.
В данной работе рассмотрены возможности получения композитов на основе карбогидридов титана и меди. В предыдущих работах [4, 8] магнитно-импульсным прессованием механоактивированных порошков получены композиты на основе ГПУ и ГЦК-карбогидридов титана, карбида титана и интерметаллидов Cu–Ti с плотностью 4.28–4.90 г/см3, микротвердостью 4–6 ГПа и абразивной износостойкостью в десять раз выше, чем для стали У13. Образование фаз интерметаллидов является характерной особенностью совместной механоактивации порошков титана и меди [9–11]. Появление дисперсных хрупких и твердых интерметаллидов обычно способствует повышению твердости и износостойкости, но при этом прочность, электропроводность и антифрикционные характеристики снижаются. Это особенно актуально при получении электроконтактных материалов на основе меди. Для снижения доли интерметаллидов, во-первых, можно уменьшить длительность совместной механоактивации титана и меди, например, применив измельчение в два и более этапа [12] с предварительным синтезом карбогидрида на начальном этапе. Во-вторых, можно ускорить формирование карбогидрида, использовав поверхностно-активные вещества (ПАВ) [13]. ПАВ препятствует холодной сварке частиц порошка при механоактивации, позволяет существенно снизить размер частиц порошка и, помимо этого, способен формировать адсорбционный барьерный слой на поверхности частиц, который в нашем случае может предотвратить взаимную диффузию титана и меди при механоактивации и при последующем низкотемпературном компактировании. Целью работы было исследование влияния различных способов механоактивации Ti и Cu (многостадийность, использование ПАВ) на фазовый состав и свойства полученных компактных образцов.
ОБРАЗЦЫ И МЕТОДЫ
Синтез исходных порошковых прекурсоров проведен в шаровой планетарной мельнице “Fritsch P-7” с использованием измельчающих контейнеров (45 см3) и шаров (20 шт., ∅8 мм) из закаленной стали (С – 1 мас. %, Сr – 1.5 мас. %). Исходные порошки титана (99.02 мас. %, ~40 мкм) и меди (99.72 мас. %, ~18 мкм) взяты в весовом соотношении 80 : 20. В качестве среды измельчения выбран петролейный эфир (ч. д. а.). Схематически условия синтеза показаны на рис. 1. Полученные порошки промаркированы литерой “P”. Образец P1 получен без меди в качестве эталонного для оценки свойств карбогидрида титана. Образец P2 подготовлен одностадийным способом – совместной механоактивацией порошков титана и меди. Критерием окончания процесса механоактивации служит исчезновение линий α-Ti на дифрактограммах полученных порошков, что означало полное взаимодействие исходного титана со средой измельчения и медью. Образец P3 получен двухстадийным способом – введением меди в предварительно механоактивированный титан, после чего смесь обрабатывали еще в течение tМА= 0.5 ч. Образец P4 получен трехстадийным способом: на первом этапе – механоактивация порошка титана, на втором – введение ПАВ – 3 мас. % пленкобразующего амина (октадециламина C18H39N) – и механоактивация в течение 0.5 ч, на третьем – введение порошка меди и обработка еще в течение 0.5 ч. Полученные порошки скомпактированы методом динамического магнитно-импульсного прессования [14] при T = = 500°С в вакууме (остаточное давление 5–10 Па), с предварительной дегазацией в течение 4 ч при той же температуре. Амплитуда импульсов давления составляет ~1.5 ГПа, длительность – 300 мкс. Полученные компактные образцы в виде дисков диаметром 10 мм и высотой 3–5 мм обозначены далее как С1–С4, соответственно.
Анализ структурно-фазового состояния образцов проведен с использованием рентгеновского дифрактометра MiniFlex (Rigaku) в Co Kα-излучении в интервале углов 20°–140°. Микроструктура и распределение основных компонентов в компактных образцах исследованы на сканирующем электронном микроскопе VEGA 3 LMN (TESCAN). Поверхность образцов предварительно отшлифована, отполирована и потравлена.
Оценка плотности образцов проведена гидростатическим методом, микротвердость по Виккерсу – на приборе ПМТ 3 по десяти измерениям при нагрузке 100 г. Абразивная износостойкость оценена методом, описанным в [15], с использованием электрокорундовых шкурок на тканевой основе КК19XW с разным размером частиц абразива – М40 (28–40 мкм), 5-Н (50–63 мкм) и 40-Н (400–500 мкм). Массовый износ определен как среднее значение по трем измерениям на аналитических весах ВЛА-200г-М. Оценка фрикционных характеристик проведена при комнатной температуре и влажности 30% на многофункциональной машине трения SRV–III Test System (Германия) с использованием вибромодуля при возвратно-поступательном движении образцов в режиме фреттинг-изнашивания. В качестве контртела использован шарик из углеродистой закаленной стали (диаметр – 9.4 мм, твердость – 55–57 HRC, параметр шероховатости Ra = 0.02). Ход контртела при испытаниях составлял 2 мм, частота его перемещения – 20 Гц, длительность испытания – 20 мин, нагрузка – 10 Н. Параметры шероховатости образцов на исходной поверхности и на пятнах износа измерены профилографом Perthometer M2 (Mahr GmbH, Германия). Поверхность образцов перед испытаниями отшлифована и отполирована. Параметр шероховатости поверхности полированных образцов Ra = 0.03.
РЕЗУЛЬТАТЫ И ОБСУЖДЕНИЕ
На рис. 2а показаны дифрактограммы порошков Р1–Р4. Фазовый состав образца Р1 представлен метастабильным ГЦК-твердым раствором Ti(C, H) [16]. В составе образца Р2 также присутствует ГЦК фаза Ti(C, H). Медь при совместном измельчении титана и меди полностью перешла в состав рентгеноаморфных интерметаллидов. Двухстадийный способ получения (образец Р3) дает смесь фаз Ti(C, H) и Cu с параметром решетки меди 0.3613(1) нм, близким к эталонному (0.3615 нм). Однако объемная доля меди снижена до 4% по сравнению с исходной (10%), что указывает на то, что половина меди за tМА = 0.5 ч успела перейти в интерметаллидную фазу. Образец Р4 является двухфазным – Ti(C, H) + Cu. Объемное содержание меди равно изначально заложенным 10%. Таким образом, формирование адсорбционного слоя из длинных углеводородных цепочек [13], ориентированных аминной группой к поверхности частиц титана и меди, сдерживает взаимодействие последних и предотвращает образование интерметаллидов в процессе МА.
Рентгеновские дифрактограммы компактных образцов С1‑С4 показаны на рис. 2б. В табл. 1 приведены результаты количественного фазового анализа. Основными фазами в компактных образцах являются ГПУ-карбогидрид титана с параметрами решетки, близкими параметрам решетки фазы Ti2CH0.6, и интерметаллиды CuTi2 и СuTi. На дифрактограмме образца С1 фиксируется набор линий от α-Ti, наиболее интенсивная из которых – вблизи угла 47°. На дифрактограмме образца С2 наиболее интенсивные линии титана также сохраняются, а в случае образцов С3 и С4 однозначно выделить вклад от α-Ti сложно. Результаты полнопрофильной подгонки дифрактограмм показали, что если вклад от α-Ti и присутствует, то он очень мал. В образцах С1 и С4 обнаружено заметное количество гидрида титана. Появление гидрида в образце С1 обусловлено недостатком углерода в метастабильном ГЦК-твердом растворе Ti(C, H). При нагревании порошков перед компактированием метастабильный твердый раствор распадается с формированием ГПУ-карбогидрида. Согласно [17], однофазные ГПУ-карбогидриды титана можно получить только при концентрации углерода не ниже 0.3 от стехиометрического для TiC и при равной или большей концентрации водорода. В нашем случае в образцах имеет место недостаток углерода, избыточные титан и водород вступают во взаимодействие друг с другом с формированием гидрида и α-титана. В случае образцов Р2 и Р3 титан взаимодействует с медью еще в процессе механообработки, формируя интерметаллиды.
Таблица 1.
Объемная доля фаз в компактных образцах (±3%)
Фаза | Образец | |||
---|---|---|---|---|
С1 | С2 | С3 | С4 | |
Ti2CH0.6 | 60 | 53 | 67 | 72 |
α-Ti | 31 | 17 | 0 | 0 |
TiH2 | 9 | 0 | 1 | 9 |
CuTi2 | 0 | 30 | 23 | 7 |
CuTi | 0 | 0 | 9 | 11 |
Cu | 0 | 0 | 0 | 1 |
В образцах Р3 и Р4 в процессе механоактивации до момента введения ПАВ и меди формируется фаза твердого раствора Ti(C, H) с таким же составом, что и в Р1, поскольку условия обработки одинаковы. В образце Р3 после введения меди при последующей механообработке начинают формироваться рентгеноаморфные интерметаллиды с участием титана из твердого раствора и меди. В случае образца Р4 созданный адсорбционный слой из ПАВ позволяет “законсервировать” состав Ti(C,H) и сдержать взаимодействие титана с медью. Поэтому при последующей термической обработке при распаде твердого раствора Ti(C,H) в образце С4 образуется такое же количество титана и гидрида титана, что и в С1.
Барьерный органический слой разрушается при достаточно низких температурах (температура кипения ктадециламина составляет 349°С), свободный титан взаимодействует с медью с формированием интерметаллидов. Однако часть меди в образце С4 сохраняется. Для данного образца характерны наименьшая суммарная доля интерметаллидов и наибольшая доля карбогидрида титана.
Полученные результаты свидетельствуют об эффективности использования выбранного ПАВ: даже при четырехчасовом отжиге механоактивированных порошков при 500°С удается сохранить часть меди. Меньшее время термообработки позволит существенно повысить долю меди. Пленка из углеводородных цепочек при нагревании превращается в слой аморфного углерода [18], который участвует в формировании карбида титана при более высоких температурах [19].
Условия механоактивации порошков влияют и на микроструктурное состояние полученных компактов. На рис. 3 представлены электронно-микроскопические изображения структуры компактных образцов С2–С4. Микроструктура образца С2 (рис. 3а, 3б) однородная, слоистая: светлые слои интерметаллида CuTi2 чередуются с более темными слоями карбогидрида титана. Толщина слоев – около 50–100 нм.
В образце С3 (см. рис. 3в, 3г, рис. 4 и табл. 2) компоненты распределены менее однородно. Слоистость микроструктуры сохраняется, но толщина слоев заметно больше. Видны области трех типов – I светлые зоны, содержащие равные доли меди и титана, II темные зоны, не содержащие меди, и III серые зоны, которые являются переходными зонами между I и II. Зоны III содержат и интерметаллиды (CuTi, CuTi2) и карбогидрид (см. табл. 1), часть указанных фаз присутствует в виде высокодисперсных включений (см. рис. 4).
Рис. 4.
Электронно-микроскопические изображения поверхности скола образца C3 при разных увеличениях.
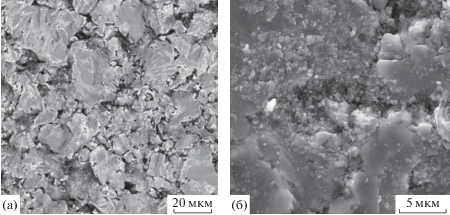
Таблица 2.
Результаты энергодисперсионного анализа содержания основных элементов в компактах С2–С4 (±1 мас. %). Обозначения см. на рис. 3а–3е
Образец | Ti | Cu | C | O | Ti : Cu | |
---|---|---|---|---|---|---|
С2 | Общее | 73 | 18 | 7 | 1 | 80 : 20 |
С3 | Общее | 73 | 18 | 8 | – | 80 : 20 |
I | 45 | 46 | 8 | – | 50 : 50 | |
II | 90 | 2 | 7 | – | 98 : 2 | |
III | 69 | 22 | 8 | – | 76 : 24 | |
С4 | Общее | 77 | 11 | 8 | 1 | 88 : 12 |
I | 61 | 26 | 10 | 1 | 70 : 30 | |
II | 91 | 1 | 7 | – | 99 : 1 |
Для образца С4 (рис. 3д, 3е) разделение на титановую и медную компоненты еще более выражено: светлые зоны I интерметаллидов также располагаются вдоль границ исходных частиц, толщина их местами достигает 1–2 мкм. В объеме частиц – в зонах II – медь практически отсутствует. Для данного образца характерна наибольшая пористость. Поры размером от нескольких до десятка микрометров располагаются преимущественно по стыкам спеченных частиц. Поскольку после введения меди механообработка проводится уже в присутствии ПАВ, то на поверхности меди также формируется адсорбционный слой из углеводородных цепочек. При последующем нагревании этот слой разрушается до аморфного углерода. Растворимость и скорость диффузии углерода в меди очень малы, и он остается на поверхности частиц. Мы предполагаем, что слой аморфного углерода на поверхности частиц и продукты его окисления при нагревании приводят к ухудшению спекаемости и появлению пор.
Свойства компактных образцов
В табл. 3 приведены плотность, микротвердость и износостойкость компактных образцов. Присутствие интерметаллидов обеспечивает повышенные значения плотности и микротвердости образцов С2–С4 по сравнению с образцом С1. Твердость интерметаллида CuTi может достигать 8–8.5 ГПа [20], CuTi2 – 7.5 ГПа [21]. Сниженная доля интерметаллидов в образце С4 по сравнению с образцом С3 при равных долях карбогидрида приводит к уменьшению микротвердости С4. Абразивная износостойкость у образца С4 ниже, чем у образцов С1–С3, что возможно обусловлено большим количеством пор в его микроструктуре (см. рис. 3д, 3е).
Таблица 3.
Свойства компактных образцов
Образец | Плотность, г/см3 (±0.05) | HV, ГПа | kтр (±0.01) | Износ при сухом трении в паре “образец–контртело”, мкм (±5) | Приведенный абразивный износ образцов для разных шкурок, мг/мм2 (±0.002) | ||
---|---|---|---|---|---|---|---|
М40 | 5‑Н | 40‑Н | |||||
С1 | 4.0 | 4.1 ± 0.5 | 1.5–2 | 125 | 0.009 | 0.017 | 0.049 |
С2 | 4.6 | 5.1 ± 0.8 | 1.2 | 44 | 0.010 | 0.021 | – |
С3 | 4.5 | 5.1 ± 0.8 | 0.6 | 34 | 0.008 | 0.015 | 0.050 |
С4 | 4.3 | 4.5 ± 0.5 | 0.6–0.8 | 30 | 0.017 | 0.030 | 0.084 |
При сухом трении в паре со стальным шариком характер поведения образца С1 и медьсодержащих образцов существенно отличается. Зависимости коэффициента трения (kтр) пары “образец–контртело” и их общего износа от времени испытаний показаны на рис. 5. Процесс приработки для всех исследованных образцов завершается к 1–3 мин испытаний. Коэффициент трения в случае образца С1 растет от 0.2 до максимального значения 2 в первую минуту испытания. Характер изменения kтр нестационарный, скачкообразный. Износ трущейся пары после 20 мин испытаний достигает значения около 125 мкм. Вероятно, это обусловлено достаточно сильным адгезионным взаимодействием образца и контртела. В фазовом составе образца С1 содержится около 30 об. % α-Ti, для которого характерны склонность к адгезионному износу и высокие значения коэффициента трения. Поверхность контртела в этой паре истирается менее значительно, в то время как след износа поверхности образца С1 четко виден (рис. 6). Определить глубину следа на поверхности образца с помощью профилометра не удалось – диапазон измерения профилометра оказался недостаточным. Оценка микрометром толщины слепка со следа износа дает значение 155 ± 25 мкм. Это означает, что в общую величину износа основной вклад дает износ поверхности образца.
По сравнению с С1 образцы С2–С4 изнашиваются существенно меньше и характеризуются меньшими коэффициентами трения. В [20, 22] показано, что появление интерметаллидов снижает коэффициент трения до 0.15 и улучшает стойкость к истиранию. Начальное значение коэффициента трения для образца С2 соответствует 0.7, максимальное – ~1.2. Повышенный коэффициент трения для образца С2, как и для образца C1, может быть обусловлен присутствием α-Ti в его составе. Для образцов С3 и С4 начальное значение коэффициента трения – 0.2, после чего он увеличивается до значения ~0.6 (образец С3) или ~0.6–0.8 (образец С4).
Профилограммы следов изнашивания, приведенные на рис. 7, свидетельствуют о незначительном износе поверхности образцов. Общий износ в парах трения в случае образцов С2–С4 составляет 44, 34 и 30 мкм, соответственно. Оценка величины линейного износа контртела, рассчитанной из диаметра следа изношенного сегмента (рис. 7), дает значения 48, 38 и 31 мкм соответственно. В пределах ошибки эти величины близки к полученным значениям общего износа. Таким образом, основной вклад в общий износ трущейся пары для данных образцов вносит износ контртела, хотя его твердость выше, чем твердость исследованных компактных образцов. Причинами износа контртела наиболее вероятно являются абразивный износ с участием частиц интерметаллидов, вырванных из поверхностных слоев композита, а также окислительное разрушение поверхности стального контртела. В пользу абразивного изнашивания свидетельствует то, что со снижением доли интерметаллидов величина износа уменьшается. Абразивный характер износа также подтверждают канавки в области следов износа на поверхностях образца и контртела, образованные попаданием крупного твердого агломерата частиц в зону контакта при трении и показанные в правой части рис. 7. Таким образом, использование ПАВ позволяет ограничить взаимную диффузию титана и меди в процессе механоактивации и частично сдержать ее при последующей термообработке. Применение ПАВ приводит к снижению доли интерметаллидов в компактных образцах, увеличению доли карбогидридов титана и меди, что, в свою очередь, приводит к снижению величины износа в паре трения “образец–контртело”.
Рис. 7.
(а) Поперечные профили следов износа на поверхности образцов C2–C4 и вид следов износа поверхности (б) образцов и (в) контртела.
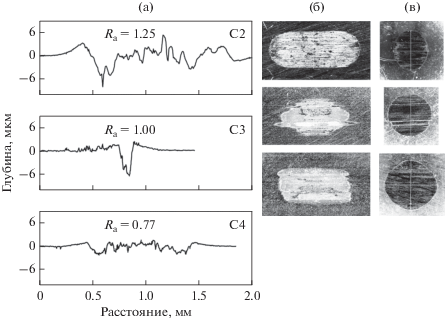
Предложенный способ механосинтеза может быть использован для получения других композитов в случаях, когда необходимо избежать формирования интерметаллидных фаз или твердых растворов металлов. В данной работе в качестве ПАВ был взят 3% раствор октадециламина в петролейном эфире, в составе которого присутствуют только углерод, водород и азот. Возможными причинами сдерживания межфазного взаимодействия металлов при повышении температуры являются формирование на границах слоя аморфного углерода и/или тонкого слоя карбонитридов титана. В связи с этим представляет интерес изучение влияния соединений с большей концентрацией азота в составе. Целесообразно также исследовать взаимосвязь структурно-фазового состояния и концентрации введенного ПАВ, особенно в сторону уменьшения последней, что, возможно, позволит снизить пористость компактных образцов.
ЗАКЛЮЧЕНИЕ
Одно- и двухстадийной механоактивацией порошков титана и меди в жидком углеводороде и последующим магнитно-импульсным прессованием при 500°С получены композиты на основе гексагонального карбогидрида титана и интерметаллидов CuTi и CuTi2. Трехстадийная механообработка в присутствии ПАВ дает возможность сдержать формирование интерметаллидной фазы в процессе механоактивации, а также снизить долю интерметаллидов и частично сохранить медь в компактных образцах.
Оценка уровня свойств показала, что микротвердость полученных композитов составляет 4–5 ГПа, она повышается с ростом доли интерметаллидов. Полученные композиты характеризуются высокой абразивной износостойкостью, причем она не зависит от присутствия в их составе интерметаллидов, TiH2 и α-Ti.
Коэффициент трения в условиях сухого трения полученных композитов по стали зависит от условий механоактивации порошков: наименьшее его значение 0.6 достигается при двух- и трехстадийной механоактивации, наибольшее ~1.2 – при одностадийной механоактивации. Наибольшие величины коэффициента трения обусловлены заметным количеством α-Ti в составе композитов. Наименьшая величина износа в паре “образец–контртело” достигается при использовании ПАВ в процессе механоактивации (трехстадийный способ получения) благодаря увеличению доли карбогидрида и уменьшению доли интерметаллидов в составе композита.
Работа выполнена в рамках гос. задания, № гос. регистрации НИР АААА-А17-117022250038-7, частично поддержана проектом РФФИ № 18-48-180003.
Список литературы
Renaudin G., Yvon K., Dolukhanyan S.K., Aghajanyan N.N., Shekhtman V.Sh. Crystal structures and thermal properties of titanium carbo-deuterides as prepared by combustion synthesis // J. Alloys Compnd. 2003. V. 356–357. P. 120–127.
Khidirov I. Neutron diffraction study of dehydrogenation of titanium carbohydrides TiCxHy // Russ. J. Inorg. Chem. 2017. V. 62. № 4. P. 498–502.
Eremina M.A., Lomaeva S.F., Burnyshev I.N., Kalyuzhnyi D.G. Mechanosynthesis of precursors for TiC–Cu cermets // Russ. Phys. J. 2018. V. 60. № 12. P. 2155–2163.
Eryomina M.A., Lomayeva S.F., Paranin S.N., Zayatz S.V., Tarasov V.V., Trifonov I.S. Properties of the Ti–C–H–Cu composites obtained by mechanosynthesis using organic media // Letters on materials. 2017. V. 7. № 3. P. 323–326.
Eremina M.A., Lomaeva S.F., Burnyshev I.N., Kalyuzhnyi D.G., Konygin G.N. Titanium carbohydride synthesis by mechanical activation in liquid hydrocarbon // Russ. J. Inorgan. Chem. 2018. V. 63. № 10. P. 1274–1282.
Aghajanyan N.N., Dolukhanyan S.K., Ter-Galstyan O.P. The combustion processes in system Ti–V–Cr–C–H and synthesis of complex carbohydrides // Int. J. Hydrogen Energy. 2011. V. 36. № 1. P. 1306–1308.
Eryomina M.A., Lomayeva S.F., Kharanzhevskiy E.V., Burnyshev I.N. Peculiarities of phase formation in the mechanosynthesized titanium carbohydride powders under short pulse selective laser alloying // Europ. Phys. J. Spec. Topics 228, 2429–2439 (2019).
Eryomina M.A., Lomayeva S.F. Mechanosynthesis of TiC(NbC)–Cu composites using liquid hydrocarbons // Materials Today: Proceedings. 2019. V. 12. P. 151–154.
Oanh N.T.H., Viet N.H., Kim J.-S., Jorge Junior A.M. Characterization of in-situ Cu–TiH2–C and Cu–Ti–C nanocomposites produced by mechanical milling and spark plasma sintering // Metals. 2017. V. 7. № 117. P. 1–12.
Wang F., Li Y., Wang X., Koizumi Y., Kenta Y., Chiba A. In-situ fabrication and characterization of ultrafine structured Cu-TiC composites with high strength and high conductivity by mechanical milling // J. Alloys Compnd. 2016. V. 657. P. 122–132.
Zhuang J., Yu Sh., Liu Y., Cao Zh. Microstructure of graphite and Cu–Ti–C composites fabricated by mechanical alloying and spark plasma sintering // Adv. Mater. Res. 2012. V. 509. P. 121–124.
Wang F., Li Y., Yamanaka K., Wakon K., Harata K., Chiba A. Influence of two-step ball-milling condition on electrical and mechanical properties of TiC-dispersion-strengthened Cu alloys // Mater. Design. 2014. V. 64. P. 441–449.
Nouri A., Wen C. Surfactants in mechanical alloying/milling: A Catch-22 situation // Critical reviews in solid state and materials sciences. 2013. V. 39. № 2. P. 81–108.
Boltachev G.Sh., Nagayev K.A., Paranin S.N., Spirin A.V., Volkov N.B. Theory of the magnetic pulsed compaction of nanosized powders / In “Nanomaterials: properties, preparation and processes”. Nova Science Publishers, Inc., 2011. P. 1–58.
Тарасов В.В., Лоханина С.Ю., Чуркин А.В. Испытание материалов на относительную износостойкость на машине трения SRV-III // Заводская лаборатория. Диагностика материалов. 2010. Т. 76. № 4. С. 57–60.
Nagumo M., Suzuki T., Tsuchida K. Metastable states during reaction milling of hcp transition metals with hydrocarbon // Mater. Sci. Forum. 1996. V. 225–227. P. 581–586.
Khidirov I.G., Mukhtarova N.N., Mirzaev B.B., Getmanskiy V.V., Serikbaev B.T., Kholmedov Kh.M., Zaginaichenko S.Yu., Schur D.V., Pishuk V.K., Kuzmenko L.V., Garbuz V.V., Nuzhda S.V., Pishuk O.V. Determination of homogeneity range of Ti2C1 –x'H2 –y' solid solution by neutron diffraction // Al’tern. Energ. Ekol. 2007. № 5. P. 49–55.
Акользин А.П., Жуков А.П. Кислородная коррозия оборудования химических производств. М.: Химия, 1985. 240 с.
Eryomina M.A., Lomayeva S.F., Demakov S.L., Yurovskikh A.S. SPS of “Titanium Carbide/Carbohydride–Copper” composites / XIX International scientific-technical conference “The Ural school-seminar of metal scientists-young researchers”, KnE Engineering, 2019. P. 246–252.
Reza Bateni M., Szpunar J.A., Ashrafizadeh F., Zandrahimi M. The effect of novel Ti-Cu intermetallic compound coatings on tribological properties of copper / National Tribology conference. The annals of University “Dunarea de Jos” of galati fascicle VIII. Tribology, 2003. P. 55–62.
Concustell A., Sort J., Fornell J., Rossinyol E., Surinach S., Gebert A., Eckert J., Baro M.D. Work-hardening mechanisms of the Ti60Cu14Ni12Sn4Nb10 nanocomposite alloy // J. Mater. Res. 2009. V. 24. № 10. P. 3146–3154.
Wang S., Ma Z., Liao Z., Song J., Yang K., Liu W. Study on improved tribological properties by alloying copper to CP-Ti and Ti–6Al–4V alloy // Mater. Sci. Eng. C. 2015. V. 57. P. 123–132.
Дополнительные материалы отсутствуют.
Инструменты
Физика металлов и металловедение