Физика металлов и металловедение, 2020, T. 121, № 3, стр. 314-321
Структура и деформационные свойства аустенитной нержавеющей стали
Н. С. Сурикова a, *, И. В. Власов a, Н. А. Наркевич a, А. И. Гордиенко a, П. В. Кузнецов a, b
a Институт физики прочности и материаловедения СО РАН
634055 Томск, пр. Академический, 2/4, Россия
b Томский политехнический университет
634050 Томск, пр. Ленина, 30, Россия
* E-mail: surikova@ispms.tsc.ru
Поступила в редакцию 14.06.2019
После доработки 11.07.2019
Принята к публикации 28.08.2019
Аннотация
В работе методами механических испытаний, оптической металлографии, электронной просвечивающей и растровой микроскопии, рентгеноструктурного и ESBD-анализа исследованы структура и механические характеристики нержавеющей аустенитной стали 12Х15Г9НД (в вес. %: основа Fe–0.12C–(14.0–16.5)Cr–(8.5–10.5)Mn–(1.0–1.5)Ni–2.0Cu–0.060P–0.030S–0.2N) после высокотемпературной поперечно-винтовой и холодной продольной прокатки. Проанализированы механизмы пластической деформации.
ВВЕДЕНИЕ
Аустенитные нержавеющие стали широко используются в медицине, нефтехимической и пищевой промышленности, машиностроении, т.е. относятся к классу важнейших конструкционных материалов. Сталь 12Х15Г9НД, выбранная для исследования, метастабильна [1], мало изучена, является недорогим заменителем коррозионно-стойких хромоникелевых сталей марок 12Х18Н10Т, 10Х18Н8Д3БР, 08Х18Н10 и др. Она оптимально легирована хромом, никелем, марганцем, медью и азотом. У нее нет порога хладноломкости, что позволяет использовать ее при низких температурах. В данном исследовании ставилась задача поиска оптимальных режимов упрочнения стали путем интенсивной пластической деформации прокаткой и отжигом, которые позволят расширить сферы ее применения, в том числе в условиях отрицательных климатических температур.
1. МАТЕРИАЛ И МЕТОДИКИ ЭКСПЕРИМЕНТА
Исследуемая сталь 12Х15Г9НД в состоянии поставки имела следующий состав: Fe–0.12C–(14.0–16.5)Cr–(8.5–10.5)Mn–(10–1.5)Ni–2.0Cu–0.060P–0.030S–0.2N (вес. %).
В работе изучали механические свойства и структуру стали в исходном состоянии, после высокотемпературной поперечно-винтовой и холодной прокатки и после отжигов.
Поперечно-винтовую прокатку (ПВП) стали осуществляли на трехвалковом министане винтовой прокатки РСП “14-40” мощностью 33 кН по нескольким режимам. Угловая скорость вращения валков составляла 3.7 с–1, скорость подачи заготовки 10 мм/c. Перед прокаткой заготовку прогревали в течение 30 мин при заданной температуре в печи ПКМ-612. Суммарную истинную логарифмическую деформацию стали (е) и коэффициент вытяжки (Кв) оценивали по формулам: е = ln(D/d) и Кв = (D/d)2 соответственно. Здесь D – исходный, а d – конечный диаметр заготовки.
ПВП по режиму I в интервале температур 950–700°С сопровождалась понижением температуры прокатки на 50°С на каждом следующем проходе. Процедуру понижения температуры прокатки применяли для снижения скорости роста зерен в процессе динамической рекристаллизации. Суммарная истинная логарифмическая деформация стали после 7 проходов такой прокатки составила 0.7–0.8, коэффициент вытяжки 5.0.
Прокатку по режиму II выполняли в четыре прохода при температуре 900°С до е ~ 0.7, коэффициент вытяжки составил 4.16. После прокатки заготовку закаливали в холодной воде или охлаждали на воздухе.
Холодную продольную прокатку на гладких валках проводили на прокатном стане Арт. 01002 “Вальцы ВЭМ-3 с автоматической системой смазки”, прокатывали только образцы стали после ПВП по режиму I до величины деформации 1.8–2.0.
Механические испытания на одноосное растяжение выполняли на универсальной испытательной машине “Instron-5582” при комнатной температуре и на установке типа Поляни в интервале температур от +20°С до –90°С со скоростью 5 × × 10–4 с–1. Охлаждение исследуемых образцов осуществляли в смесях жидкого азота и этилового спирта. Образцы для растяжения вырезали в форме двойных лопаток с площадью поперечного сечения 2 × 1 мм2 и длиной рабочей части 15 мм. Для удаления воздействий искровой резки все поверхности образцов шлифовали на абразивном материале различной зернистости и подвергали электролитической полировке в смеси ортофосфорной кислоты и окиси хрома в соотношении 8 : 1.
Показатели твердости стали определяли методом локального нагружения материала жестким индентором [2] с записью кривой индентирования в координатах: “нагрузка на индентор F”–“глубина внедрения индентора h”. При этом использовали пирамидальный индентор Берковича при нагрузке 200 мН.
Трибологические исследования проводили при комнатной температуре на высокотемпературном трибометре TMT фирмы CST Instrument при нормальной нагрузке 2 Н и влажности 50%. В качестве контртела использовали сапфировый шар диаметром 6 мм, линейная скорость шарика составляла 5.0 см/с, длина пути ~100 м.
Профилометрию поверхности при определении величины износа осуществляли с помощью оптического интерферометра белого света NewView 6200. Коэффициент интенсивности износа К (мм3/Н м) определяли по формуле
где V – объем изношенного материала, Р – приложенная нагрузка, L – путь, пройденный контртелом.Структурные исследования выполняли методами оптической, растровой и просвечивающей электронной микроскопии и рентгеноструктурного анализа. При этом использовали: световой микроскоп марки Zeiss Axiovert 25, растровый электронный микроскоп Philips SEM 515, систему с электронным и сфокусированным ионным пучком Quanta 200 3D, оснащенную приставкой NORDLYS Oxford Instruments HKL Technology для автоматического анализа дифракции обратно рассеянных электронов (EBSD), электронный просвечивающий микроскоп JEM-2100 при ускоряющем напряжении 200 кВ и рентгеновскую установку ДРОН-7 из ЦКП “НАНОТЕХ” ИФПМ СО РАН.
Фольги для электронной микроскопии готовили методом струйной электрополировки на приборе ПТФ в охлажденном растворе уксусной и хлорной кислот в соотношении 5 : 1 при напряжении на электродах 50 В.
2. РЕЗУЛЬТАТЫ ИССЛЕДОВАНИЙ И ИХ ОБСУЖДЕНИЕ
При аттестации исходного состояния (состояния поставки) методом рентгеноструктурного анализа и исследования температурной зависимости электросопротивления было установлено, что при закалке в холодную воду от высоких температур и при медленном охлаждении до температуры жидкого азота в стали 12Х15Г9НД не происходит мартенситных превращений, она сохраняет свое аустенитное состояние. На дифрактограммах (рис. 1а), полученных от исходных образцов стали присутствуют только отражения γ-фазы.
Рис. 1.
Фрагменты рентгенограмм, полученных от образцов стали в различных состояниях: а – исходное состояние, б – после ПВП по режиму I, в – после ПВП по режиму I и последующей холодной прокатки.
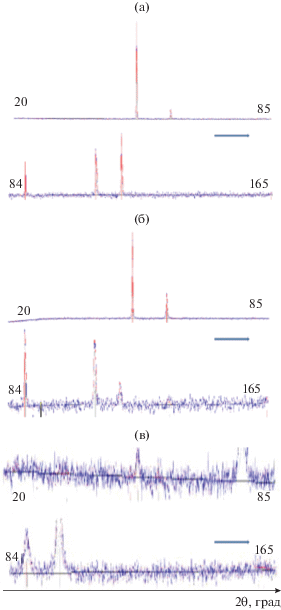
Эксперименты на растяжение и измерение твердости показали (рис. 2а, кривая 1), что в исходном состоянии при комнатной температуре сталь 12Х15Г9НД имеет пластичность до разрушения δ ~ 90%, предел текучести σ0.1 ~ 400 МПа, предел прочности σВ ~ 850 МПа, твердость по Виккерсу 372 кГ/мм2 (табл. 1). Средний размер аустенитных зерен составляет ~20 мкм, согласно металлографическим и ESBD-исследованиям (рис. 3а, 4а). В материале наблюдается высокая доля (96.9%) большеугловых границ зерен (рис. 4б), половина из которых (46.8%) имеет двойниковую разориентировку 60° с Σ = 3. Наличие таких границ связано с низкой энергией дефекта упаковки, а также может быть связано с присутствием в составе стали примеси азота [3].
Рис. 2.
а – Кривые деформации стали: 1 – состояние поставки; 2 – после ПВП по режиму I (е ∼ 0.7); 3 – после ПВП по режиму I с последующей холодной прокаткой до е ∼ 1.8; 4 – после ПВП по режиму II c закалкой в воде; 5 – после ПВП по режиму II с охлаждением на воздухе. б – Зависимость предела текучести (1) и предела прочности (2) стали после ПВП по режиму I от времени отжига при Т = 650°С, 5 ч.
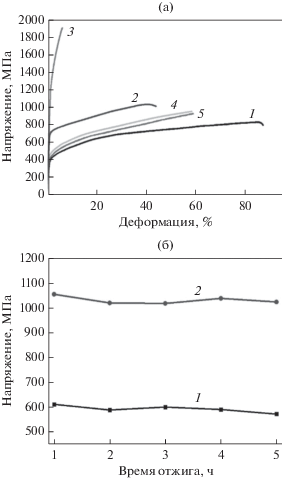
Таблица 1.
Механические показатели стали, полученные при наноиндентировании
Состояние стали | H, МПа | HV, кГ/мм2 | Е, ГПа | hmax, нм | Аупр, пДж | Апл, пДж | Аобщ, пДж | ηупр, % |
---|---|---|---|---|---|---|---|---|
Исходное | 4011 | 372 | 150 | 1661 | 19 773 | 101 655 | 121 428 | 16 |
ПВП, режим I | 4240 | 393 | 171 | 1613 | 20 367 | 99 274 | 119 641 | 17 |
ПВП, режим I + холодная прокатка | 8277 | 767 | 210 | 1214 | 21 837 | 65 059 | 86 896 | 25 |
ПВП, режим I + холодная прокатка + отжиг 600°С | 6113 | 566 | 204 | 1361 | 19 446 | 78 260 | 97 706 | 20 |
Здесь H =Fmax/Sp – твердость по Мейеру (Fmax – максимальное усилие, Sp – проекция области контакта на поверхность образца), HV – твердость по Виккерсу, Е – модуль Юнга, hmax – максимальная глубина внедрения индентора, Аобщ=Аупр+Апл – общая работа индентирования, Аупр – упругая составляющая работы индентирования, Апл – пластическая составляющая работы индентирования, ηупр – доля упругой составляющей в общей работе индентирования.
Рис. 3.
Металлографическая картина зеренной структуры стали в исходном состоянии (а), после ПВП по режиму I, периферийная зона (б) и после ПВП по режиму I (центральная зона прутка) (в).
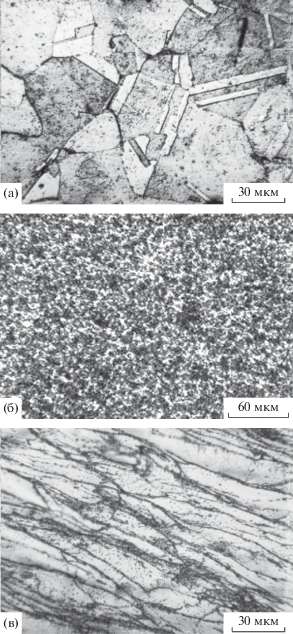
Рис. 4.
Результаты EBSD-анализа структуры стали в исходном состоянии (а–в) и после ПВП, режим I (продольное сечение, периферийная зона) (г–е) при сканировании поверхности с шагом 0.5 мкм; шаг 1.6 мкм [4](а–в).
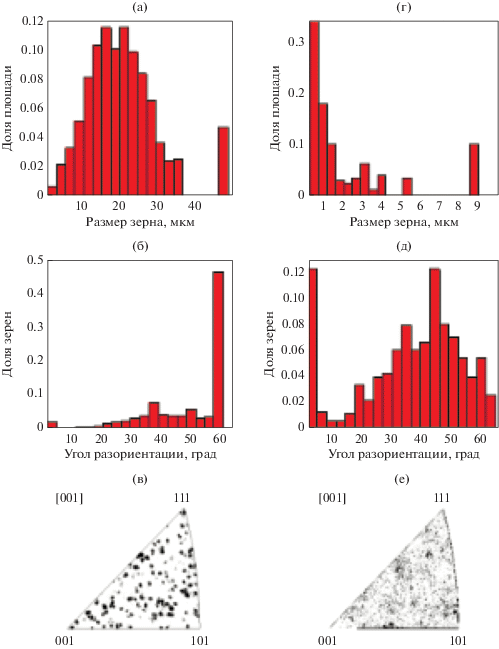
Электронная микроскопия показала, что изначально в зернах аустенита практически не содержится дислокаций, это, наряду с отсутствием текстуры (рис. 4в), является показателем высокотемпературной рекристаллизации. На металлографической картине (см. рис. 3а) наблюдаются дисперсные включения вторичных фаз, отдельные частицы достигают больших размеров ~5–6 мкм и располагаются как на границах, так и в объеме зерен. Основным включением, как установлено с помощью электронной микроскопии, является фаза – Cr23C6 (рис. 5).
Рис. 5.
Включения основной карбидной фазы Cr23С6: а – темнопольное изображение частиц фазы Cr23С6 в рефлексе 860, ось зоны ${{[3\bar {4}7]}_{{{\text{C}}{{{\text{r}}}_{{23}}}{{{\text{C}}}_{6}}}}}$; б – микродифракционная картина от частиц и матрицы к (а), наблюдаются несколько зон карбидной фазы, рефлексы обозначены в зонах ${{[3\bar {4}7]}_{{{\text{C}}{{{\text{r}}}_{{23}}}{{{\text{C}}}_{6}}}}}$ и ${{[6\bar {7}13]}_{{{\text{C}}{{{\text{r}}}_{{23}}}{{{\text{C}}}_{6}}}}}$, угол между осями зон 2.17°.
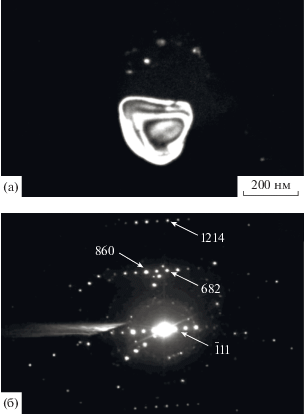
После ПВП по режиму I наблюдается упрочнение стали, предел текучести увеличивается до ~620 МПа, предел прочности до ∼1050 МПа при сохранении достаточно высокой пластичности до разрушения δ ~ 50% (см. рис. 2а, кривая 2). Показатели твердости – H и Hv, модуль Юнга и доля упругой составляющей в общей работе индентирования при этом возрастают всего на 6–10%. Сталь остается в аустенитном состоянии (рис. 1б). После прокати пруток имеет слоистое строение [4] – в периферийных объемах прутка наблюдаются зерна глобулярной формы, а в центральной зоне – вытянутой (см. рис. 3б, 3в).
На рис. 4 представлены результаты ESBD-анализа, показывающие изменения в зеренной структуре стали после ПВП по режиму I. Произошло измельчение зерна, средний размер зерна согласно рис. 4г составил 0.57 мкм. Из сравнения областей, соответствующих большеугловым границам на гистограмме распределения границ по углам разориентации (углы 15° и более), на рис. 4б и 4д видно, что в результате интенсивной пластической деформации доля специальных двойниковых границ аустенита с разориентацией 60° значительно уменьшилась. Они превратились в границы общего типа [5], которые оказывают большее сопротивление деформационным сдвигам, чем когерентные двойниковые границы зерен. Доля малоугловых разориентаций, наоборот, возросла, что свидетельствует об интенсивном формировании зеренно-субзеренной структуры.
Таким образом, после ПВП по режиму I в стали формируется субмикрокристаллическое состояние, которое имеет более высокие прочностные свойства по сравнению с исходным состоянием и в области отрицательных температур (рис. 6а). Одним из факторов упрочнения [4] является измельчение карбидной подсистемы, после поперечно-винтовой прокатки размер крупных частиц не превышал 0.5 мкм. Кроме основной карбидной фазы Cr23С6, в структуре проката наблюдаются мелкие (до 100 нм) включения карбидов (Fe, Mn)3C и (Fe, Mn)2C (рис. 7) и карбонитрида хрома Cr2C0.61N0.3.9 [4].
Рис. 6.
Кривые деформации стали при различных температурах: а – 1, 2, 3 – состояние поставки, 4, 5 ,6 – после ПВП по режиму I е ~ 0.7); б – после ПВП по режиму I с последующей холодной прокаткой до е ~ 1.8 и старением, 600°С, 3 ч.
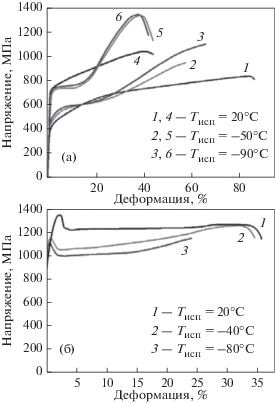
Рис. 7.
а – Темнопольное изображение частиц карбидной фазы (Fe, Mn)2C в рефлексе 501; б – микродифракционная картина к (а), обозначены рефлексы в зоне ${{[3\overline {11} \overline {15} ]}_{{{\text{FeM}}{{{\text{n}}}_{2}}{\text{C}}}}}$. Размер более крупной частицы ~50 нм, меньших ~15 нм.
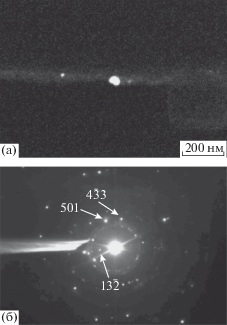
Материал, полученный ПВП по режиму I, обладает хорошей стабильностью структуры и механических характеристик в температурном интервале 600–700°С, в котором традиционно эксплуатируются нержавеющие аустенитные стали. Из рис. 2б видно, что после отжига прокатанного материала при температуре 650°С в течение 5 часов прочностные характеристики – σ0.1 и σВ, практически не изменяются.
Прокатка по режиму II c закалкой в воде и с охлаждением на воздухе приводит к незначительному упрочнению (рис. 2а, кривые 4 и 5), что связано с быстрым ростом аустенитного зерна при высокой температуре прокатки.
В результате ПВП по режиму I и последующей холодной прокатки до е ~ 1.8 в материале формируется двухфазное (рис. 1в) нанокристаллическое состояние с присутствием зерен α-феррита и аустенита. Такое состояние является высокопрочным, поскольку его предел прочности (рис. 2а, кривая 3) близок к σB ~ Е/100 (табл. 1), и имеет невысокую до 10% пластичность до разрушения. Основными механизмами пластической деформации и фрагментации стали 12Х15Г9НД при холодной деформации, также как в других метастабильных сталях [1, 6–8] являются деформационные мартенситные превращения.
На рис. 8 показано формирование зародышей ε-мартенситной фазы, имеющей ГПУ-решетку, на тонких дефектах упаковки в аустенитной матрице на начальных стадиях (е ~ 0.07) холодной прокатки. В других зернах материала при этом наблюдаются только отдельные ламели α'-мартенсита.
Рис. 8.
а – Темнопольное изображение дефектов упаковки и зародышей ε-мартенсита в рефлексе 0$\bar {1}$1ε; б – микродифракционная картина к (а), обозначены рефлексы в двух зонах, параллельных друг другу, [001]-зоне аустенита и [$\bar {1}$11]‑зоне ε-мартенсита, слева и внизу снимка показаны расположение и форма рефлексов при большем увеличении.
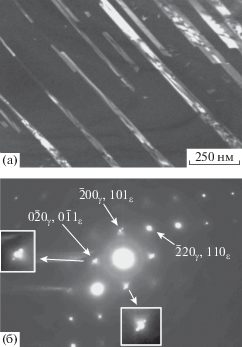
В соответствии с выводами работы [8], ориентация зерен относительно приложенной нагрузки в поликристалле метастабильной стали определяет последовательность образования и объемную долю мартенситных ε- и α'-фаз. После холодной прокатки до е ~ 1.8 материал находится в двух фазном (γ + α')-состоянии, объемная доля α'-мартенсита по рентгеноструктурным оценкам составляет ≈85.6%, размер областей когерентного рассеяния – 40 нм, ε-фаза не фиксируется (возможно ее доля меньше 5%). Это свидетельствует о том, что при деформации происходят мартенситные превращения γ → ε → α'. Холодная прокатка формирует неоднородную структуру, в зонах материала, которые испытали большие степени пластической деформации, размер зерен составляет 40–100 нм (рис. 9а, 9б). В зонах с меньшей 30–400 нм. В структуре проката присутствуют нанокарбиды и нитриды хрома (рис. 9в, 9г).
Рис. 9.
Структура стали 12Х15Г9НД после ПВП по режиму I (е ~ 0.7) и холодной прокатки (е ~ 1.8): а – светлоепольное изображение; б – микродифракция к (а), наблюдаются только отражения α'-мартенситной фазы; в – микродифракционная картина, наблюдаются две зоны с азимутальным размытием рефлексов – [110]-зона аустенита и [111]-зона α'‑мартенсита, а так же зона ${{[2\bar {1}1]}_{{{\text{C}}{{{\text{r}}}_{{\text{3}}}}{{{\text{C}}}_{{\text{2}}}}}}}$ карбида хрома Cr3C2 (орторомбическая структура) и зона [001] нитрида хрома Cr2N (ГПУ-решетка), рефлексы в этой зоне указаны маленькими стрелками; г – темнопольное изображение в рефлексе ${{[011]}_{{{\text{C}}{{{\text{r}}}_{{\text{3}}}}{{{\text{C}}}_{{\text{2}}}}}}}$, видны нанокарбиды хрома размером ~5–15 нм.
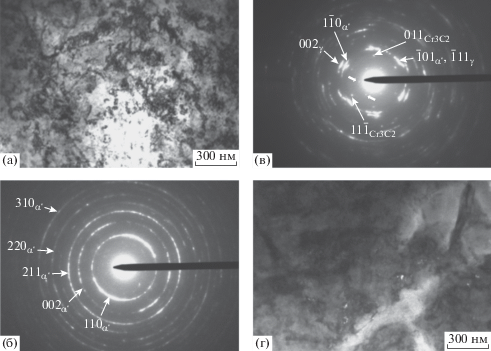
Важным свойством полученного нанокристаллического состояния является его высокая сопротивляемость износу. В наших экспериментах (см. раздел 1) коэффициент интенсивности износа стали после ПВП по режиму I с последующей холодной прокаткой уменьшился в 6.6 раза по сравнению со значением в исходном состоянии и имел величину 1.30 × 10–5 мм3/Н⋅
Для увеличения пластичности материал с нанокристаллической структурой был отожжен, на рис. 6б приведены кривые растяжения образцов стали после ПВП по режиму I с последующей холодной прокаткой до е ~ 1.8 и отжигом при 600°С в течении 3 ч. Видно, что в температурном интервале от 20 до – 80°С предел текучести и предел прочности снизились, но остались достаточно высокими – ~1050 и ~1200 МПа соответственно, пластичность стали до разрушения возросла до ~25%.
После отжига материал остается в двухфазном состоянии с преобладанием аустенитной фазы. По рентгеноструктурным оценкам, доля α'-мартенситной (ферритной) фазы составляет всего ~6%. Размер крупных зерен аустенита увеличился, часто встречаются зерна шириной 200–400 нм. В них наблюдается дефектная субструктура, унаследованная от мартенсита при обратном α' → γ-превращении – дефекты упаковки, малоугловые границы и дислокации. Среди дисперсных частиц преобладают карбиды и карбонитриды хрома. Мелкий размер зерна, остаточный мартенсит, наличие дефектной подсистемы и дисперсных фаз обусловили после отжига более высокие прочностные свойства стали, чем в исходном состоянии.
ВЫВОДЫ
Подводя итоги, можно сделать следующие выводы.
1. Показано, что в результате высокотемпературной поперечно-винтовой прокатки в стали 12Х15Г9НД формируется субмикрокристаллическая структура аустенита со средним размером зерна ~0.6 мкм, которая характеризуется более высокой твердостью и прочностью, достаточной пластичностью и хорошей стабильностью.
2. Комбинация методов высокотемпературной ПВП и интенсивной холодной прокатки
позволяет получить в стали высокопрочное нанокристаллическое состояние с σв ~ Е/100 ≈ ≈ 2000 МПа и высокой износостойкостью при комнатной температуре. Пластичность до разрушения при этом находится в пределах 6%.
3. Методами электронной просвечивающей микроскопии и рентгеноструктурного анализа показано, что основными механизмами пластической деформации стали при холодной прокатке являются деформационные мартенситные превращения γ → ε + α' → α'.
4. Определены режимы температурно-деформационной обработки стали 12Х15Г9НД, которые позволяют получить стабильный материал с хорошим сочетанием прочностных и пластических характеристик в интервале отрицательных климатических температур.
Работа выполнена при финансовой поддержке гранта РФФИ № 18-08-00221 и частично в рамках ПФНИ ГАН на 2013–2020 годы, направление III.23.
Список литературы
Филиппов М.А., Литвинов В.С., Немировский Ю.Р. Стали с метастабильным аустенитом. М.: Металлургия, 1988. 256 с.
Головин Ю.И. Наноиндентирование и его возможности. М.: Машиностроение, 2009. 312 с.
Свяжин А.Г., Капуткина Л.М. Стали, легированные азотом // Изв. Вузов. Черная металлургия. 2005. № 10. С. 36–46.
Сурикова Н.С., Панин В.Е., Наркевич Н.А., Мишин И.П., Гордиенко А.И. Создание поперечно-винтовой прокаткой многоуровневой иерархической мезосубструктуры и ее влияние на механическое поведение аустенитной стали // Физическая мезомеханика. 2018. Т. 21. № 3. С. 36–47.
Ефименко С.П., Козлов Э.В., Теплякова Л.А., Гаврилюк В.Г., Игнатенко Л.Н., Гирсова Н.В., Попова Н.А., Лешкевич Г.Г., Конева Н.А. Эволюция субструктуры при горячей прокатке высокоазотистой аустенитной стали Х18АГ15 // Металлы. 1995. № 5. С. 30–36.
Немировский Ю.Р., Хадыев М.С., Филлипов М.А. Особенности упрочнения аустенита ε-мартенситом в малоуглеродистых марганцевых сталях. // ФММ. 1998. Т. 85. № 1. С. 118–126.
Немировский Ю.Р., Хадыев М.С., Филлипов М.А. О взаимосвязи деформационных процессов двойникования ε-мартенсита и образования α'-мартенсита в метастабильных сталях с низкой энергией дефектов упаковки аустенита. // ФММ. 2004. Т. 99. № 1. С. 76–82.
Киреева И.В., Чумляков Ю.И. Пластическая деформация монокристаллов аустенитных нержавеющих сталей и ГЦК-высокоэнтропийных сплавов. Томск: Изд-во НТЛ, 2018. 200 с.
Дополнительные материалы отсутствуют.
Инструменты
Физика металлов и металловедение