Физика металлов и металловедение, 2020, T. 121, № 7, стр. 696-730
Фазово-структурные превращения и свойства цветных металлов и сплавов при экстремальных воздействиях
И. Г. Бродова a, *, В. И. Зельдович a, И. В. Хомская a
a Институт физики металлов им. М.Н. Михеева УрО РАН
620108 Екатеринбург, ул. С. Ковалевской, 18, Россия
* E-mail: brodova@imp.uran.ru
Поступила в редакцию 25.02.2020
После доработки 03.03.2020
Принята к публикации 03.03.2020
Аннотация
В обзоре приведены оригинальные экспериментальные данные о структурообразовании и свойствах титана, алюминия, меди и их сплавов при интенсивных деформационных и ударно-волновых воздействиях. Основной объем статьи посвящен получению субмикрокристаллических и нанокристаллических цветных металлов и сплавов методом динамического канально-углового прессования. Определены оптимальные для каждого материала режимы ДКУП, позволяющие получать качественные объемные образцы без поверхностных дефектов. Подробно, с привлечением комплексных аналитических методов, изучено изменение морфологических и размерных характеристик структуры разных материалов в зависимости от режима деформирования. Рассмотрены механизмы деформации и деформационного упрочнения металлов и сплавов в широком интервале скоростей деформации. Представлены новые данные о термической устойчивости СМК- и НК-материалов, полученных динамическим прессованиям. Проведен анализ изменения динамических характеристик при ударно-волновом сжатии в зависимости от природы сплавов. Установлена взаимосвязь состава и структуры СМК-алюминия, меди и их сплавов, полученных ДКУП, с механическими свойствами в широком диапазоне скоростей деформации 3 × 10–3–6 × 105 с–1. В заключение с единых позиций описаны принципы создания методами интенсивной пластической деформации СМК- и НК- ГЦК-материалов с разной энергией дефекта упаковки – алюминия, меди, их сплавов и титана.
ВВЕДЕНИЕ
Современные инновационные технологии требуют создания новых материалов с возможностью их эксплуатации в экстремальных условиях. Титан, алюминий, медь и их сплавы являются важными и широко применяемыми конструкционными и функциональными материалами во многих отраслях промышленности. Благодаря большому разнообразию составов, известных к настоящему времени, они обладают очень широким комплексом физических и механических характеристик. Для сохранения лидирующих позиций в разряде перспективных материалов для наиболее востребованных к настоящему времени отраслей промышленности – авиационной, космической, автомобильной, совершенствуются способы получения и обработки металлов и сплавов. В последние годы широкое применение получили методы, основанные на воздействии интенсивных пластических деформаций (ИПД), позволившие резко измельчить структуру металлов и сплавов и качественно улучшить их свойства, такие как прочность, пластичность, жаростойкость, вязкость разрушения. Проведенные к настоящему времени многочисленные экспериментальные и теоретические исследования деформационного поведения металлов и сплавов наглядно продемонстрировали положительную роль такого подхода [1–6]. Согласно представленным результатам, одним из наиболее распространенных способов формирования субмикрокристаллического (СМК) состояния в металлах и сплавах является способ равноканального углового прессования – РКУП.
С целью дальнейшего совершенствования способов диспергирования структуры металлов и сплавов, в РФЯЦ-ВНИИТФ на основе схемы РКУП разработан новый и более эффективный способ динамического канально-углового прессования (ДКУП), использующий в качестве источника внешней нагрузки энергию пороховых газов, что обеспечило повышение скорости деформации на 4–5 порядков, до 104–105 с–1, по сравнению с РКУП [7]. Принципиальное преимущество предложенного метода состоит в том, что к деформации простого сдвига, реализуемого при РКУП, добавляется ударно-волновая деформация, которая усиливает общий результат воздействия. Теоретические и экспериментальные данные о комплексном воздействии импульсного давления и простого сдвига на структурообразование в цветных металлах и их сплавах подробно изложены в [8–12]. Результаты экспериментальных исследований структуры и свойств различных металлов и сплавов, полученных методом ДКУП, продемонстрировали возможность создания объемных материалов с субмикро- и нанокристаллической структурой [11–18]. Изучение физических свойств этих материалов выявило ряд особенностей, связанных со структурным состоянием, обусловленным одновременным воздействием ударной волны и механического простого сдвига, в частности, повышенную диссипативную способность, высокие прочностные характеристики и термическую устойчивость [15–17].
Учитывая сферы применения таких материалов и для обеспечения безопасности их эксплуатации, необходимы знания их механического поведения в условиях более интенсивных воздействий, т.е., при переходе от статической к динамической деформации [19–22]. В настоящее время с развитием нанотехнологий важным направлением исследований ученых становится изучение механизмов пластических деформаций, в частности, развитие дислокационной и дисклинационной моделей. Учитывая особенности структурного состояния и разную природу (тип кристаллической решетки, величину энергии дефектов упаковки) титана, меди и алюминия, изучение механизмов деформации и деформационного упрочнения таких металлов и их сплавов в условиях интенсивных воздействий является особенно актуальным.
Цель данного обзора состоит в кратком описании наиболее новых и важных экспериментальных результатов, полученных при исследовании структурно-фазовых превращений и деформационного поведения титана, меди, алюминия и сплавов алюминия и меди при высокоскоростном и ударно-волновом нагружениях.
МЕТОДИКА ЭКСПЕРИМЕНТА
На рис. 1 представлена схема ДКУП. С помощью специальной пушки образцы разгоняли до скоростей V = 215–500 м/с и направляли в матрицу, содержащую, как правило, два канала разного диаметра, пересекающиеся под углом 90°. Источником энергии для разгона образцов служили пороховые газы. Прессование образцов выполняли с использованием двух схем: инерционной (рис. 1а) и поршневой (рис. 1б). Число циклов прессования (проходов) варьировали от 1 до 4. Для того, чтобы задействовать несколько плоскостей сдвига при многократном прессовании реализовывали схему маршрута Вс, при которой между проходами образец поворачивается вокруг своей продольной оси по часовой стрелке на угол 90°, скорость деформации материала 104–105 с–1. Исходные размеры образцов из материалов разного химического состава, характеристики матриц (D – диаметр входного канала; R – радиус закругления внутреннего угла каналов) и параметры прессования (V – начальная скорость разгона образца; P – давление в образце в области угла поворота) указаны в разделе “Результаты”.
Рис. 1.
Установки динамического канально-углового прессования: а – инерционная и б – поршневая схемы; 1 – пороховой заряд, 2 – образец, 3 – ствол, 4 – матрица, 5 – поршень.
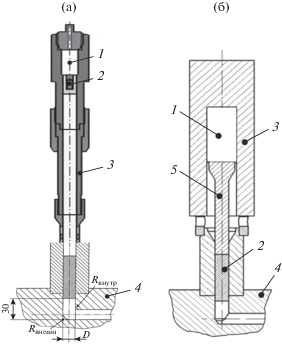
Структуру материалов изучали с помощью световых микроскопов Neophot-32, электронных просвечивающих микроскопов (ПЭМ) JEM-200CX, Philips CM30, TecnaiG2-30, JEM-2100CX, сканирующего электронного микроскопа (СЭМ) Quanta-200 с приставками для EBSD- и EDS-анализов. Средний размер кристаллитов определяли по темнопольным ПЭМ снимкам с помощью программно-аппаратного комплекса анализа изображений SIAMS-700 и по светлопольным ПЭМ-снимкам, полученным на микроскопе TecnaiG2-30. Рентгеноструктурный анализ (РСА) проводили на дифрактометре ДРОН-3 в CoKα- и СuKα-излучениях. Обработка дифрактограм, полученных для образцов до и после деформации, проводили с помощью программ PROFILE, OUTSET. По данным РСА рассчитывали параметр кристаллической решетки алюминия, плотность решеточных дислокаций, размеры областей когерентного рассеяния и значения среднеквадратичной микродеформации кристаллической решетки алюминия (${{\left\langle {{{\varepsilon }^{2}}} \right\rangle }^{{1/2}}}$). Микротвердость материалов HV измеряли методом индентирования на приборе ПMT-3 при нагрузке 0.49 Н. Твердость по Бринеллю Al сплавов определяли при нагрузке 250 кг и диаметре шарика 10 мм.
Механические испытания на одноосное растяжение проводили на разрывной машине ZWICK/ RoellZ050 при скорости деформирования 10–2 м/с и комнатной температуре (ГОСТ 1497-84). Плоские образцы для испытаний с расчетной длиной l0 = 20.0 мм, шириной w0 = 7.0 мм и толщиной t0 = = 1.5–2.0 мм вырезали параллельно продольному сечению деформированных ДКУП-образцов и исходных прутков крупнокристаллических металлов и сплавов. Погрешность измерений σB и σ0.2 составляла ±10 МПа; δ − ±1%.
Свойства СМК Al сплавов в условиях более интенсивных нагрузок, в диапазоне ɛ̇ = (3.3–6.6) × × 103 с–1, определены при динамическом сжатии по методу Кольского с использованием разрезного стержня Гопкинсона [23, 24]. В процессе динамического сжатия распределение температуры на поверхности образца регистрировали инфракрасной камерой FLIR SC 5000 (спектральный диапазон 3–5 мкм, температурная чувствительность 0.025 К, частота съемки 3 кГц, пространственное разрешение 0.2 мм).
Динамические свойства Al и Cu сплавов изучены при ударно-волновых экспериментах. Исследовали образцы в форме дисков толщиной 2 мм, вырезанные из КК прутков и СМК-сплавов после ДКУП. Образцы были нагружены ударом алюминиевой пластины толщиной 0.4 мм, которая разгонялась до скорости 630 ± 30 м/с взрывными устройствами, давление составляло 4.0–6.8 ГПа, а ɛ̇ = (0.9–2.0) × 105 с–1 [20–22, 25–27]. Скорость тыльной поверхности образца регистрировалась с помощью лазерного доплеровского измерителя VISAR, имеющего временное разрешение ~1 нс [28]. Точность измерения скорости составляла ±3 м/с.
РЕЗУЛЬТАТЫ И ИХ ОБСУЖДЕНИЕ
1.1. Структурно-фазовые превращения при ИПД Al сплавов
Учитывая широкую палитру алюминиевых сплавов и сильное влияние состава на их структуру и свойства, были изучены сплавы, относящиеся к разным системам легирования. При выборе материалов исследования ставилась цель – сравнить деформационное поведение алюминиевых сплавов с разной подвижностью дислокационного ансамбля при разных схемах нагружения и разных скоростях деформирования. Были продеформированы: алюминий технической чистоты марки А7, сплавы систем Al–Mn и Al–Mg–Mn со слабым твердорастворным упрочнением А3003 и А5083 и сплав системы Al–Zn–Mg–Cu с сильным твердорастворным и дисперсионным упрочнением А 7075 [29]. Алюминий был взят в качестве модельного материала для описания особенностей формирования СМК-состояний в ГЦК-металлах с высокой энергией дефекта упаковки γ = = 200 мДж/м2.
Химический состав и специальная термическая обработка исследованных материалов (низкотемпературный отжиг для сплавов А3003 и А5083 и высокотемпературный гетерогенизирующий отжиг для сплава А7075) обеспечили разную степень легированности Al-твердого раствора, характер распределения вторичных фаз и твердость этих материалов (табл. 1). Учитывая, что на подвижность ансамбля дислокаций оказывает влияние не только величина энергии дефекта упаковки (которая понижается при легировании алюминиевого твердого раствора), но и наличие дисперсных интерметаллидов, можно условно считать, что сплавы А3003 и А5083 являются материалами, в которых процессы дислокационной перестройки облегчены, а сплав А7075 – материалом с более низкой подвижностью дислокационного ансамбля.
Таблица 1.
Характеристики исследованных Al-сплавов
Марка сплава | Термическая обработка | Фазовый состав | Подвижность дислокаций (условно) |
---|---|---|---|
А7 | – | Однофазный Al-твердый раствор (HB = 15) | Высокая |
А3003 Al–Mn | Низкотемпературный отжиг | Слаболегированный однофазный Al-твердый раствор (HB = 30) | Средняя |
А5083Al–Mn–Mg | Низкотемпературный отжиг | Слаболегированный однофазный Al-твердый раствор (НВ = 75) | Средняя |
А7075 Al–Zn–Mg–Cu | Гетерогенизирующий отжиг | Пересыщенный Al-твердый раствор, дисперсоиды тугоплавких металлов, упрочняющая фаза MgZn2 (НВ = 68) | Низкая |
Цилиндрические образцы диаметром 14 мм и длиной 70 мм были продеформированы методом ДКУП с использованием поршневой схемы с V = = 150–400 м/с. Число циклов прессования N варьировали от 1 до 4. Закономерности измельчения структуры и упрочнения алюминиевых сплавов методом ДКУП подробно изложены в [12, 31].
На примере сплавов А3003 и А 5083 установлены особенности структурообразования в термически неупрочняемых Al сплавах при ДКУП. После одного цикла прессования тонкая структура в продольном сечении представляет собой мезополосы сдвига, внутри которых формируются слабо разориентированные субзерна (сплав А5083, V ≤ ≤ 300 м/с, рис. 2а, 2б). Параллельные между собой мезополосы сдвига объединяются в пакеты, которые образуют полосовую макроструктуру, состоящую из волокон шириной несколько микрометров.
Рис. 2.
Микроструктура сплавов А5083 (а, б) и А3003 (в, г) после ДКУП: а–в – N = 1, V ≤ 300 м/с, г – N = 4, V ≥ 300 м/с; а, в, г – светлопольное изображение, б – темнопольное изображение в рефлексе Al.

В поперечном сечении формируется фрагментированная СМК-структура с высокой долей малоугловых границ (МУГ), высокой плотностью дислокаций (5 × 1014 м–2) и средним размером зерен-субзерен 300–600 нм (сплав А3003, V ≤ 300 м/с, N = 1, рис. 2в).
При увеличении скорости деформации и числа циклов ДКУП (V ≥ 300 м/с, N = 4) наблюдается незначительное укрупнение кристаллитов до 800 нм, и типичной становится рекристаллизованная структура с большой долей большеугловых границ (БУГ) до 65%, т.е. с ростом величины деформации сдвига происходит смена механизма образования СМК-структуры (рис. 2г).
Иная картина наблюдается при деформировании многофазного термически упрочняемого сплава А7075. Уже после однопроходного прессования (V = 150 м/с) происходит резкое измельчение структуры, и средний размер зерен-субзерен становится равным 200 нм (рис. 3а). На ПЭМ снимках наблюдаются кристаллиты с неоднородным внутренним контрастом, разделенные размытыми БУГ, которые декорируются дисперсными вторичными фазами. С ростом накопленной деформации (числа циклов ДКУП) при высокоскоростном деформировании, средний размер структурных составляющих в сплаве А 7075 существенно не изменяется, также сохраняются дисперсные вторичные фазы, располагающиеся по границам зерен-субзерен. Повышение величины деформации сдвига приводит к росту внутренних микронапряжений второго рода. Плотность решеточных дислокаций достигает 2 × 1015 м–2, а доля БУГ – 60–65%. Все выше перечисленные признаки свидетельствуют об образовании СМК-структуры в результате фрагментации и ее стабилизации при повторных циклах ДКУП. Одной из причин стабилизации фрагментированной структуры с ростом накопленной деформации является блокировка дислокаций выделениями вторичных фаз.
Для объяснения эффективного измельчения структуры сплавов уже после 1–2 циклов ДКУП, в отличие от РКУП , где для получения такого же результата требуется 6–8 циклов [3, 32, 33], можно привести три аргумента: высокоскоростная деформация в ударной волне осуществляется при более значительном уровне сдвиговых напряжений [34, 35]; в условиях высокоскоростных и высокоэнергетических воздействий в материалах активизируются дополнительные системы скольжения и увеличивается плотность дислокаций [36]; при высокоинтенсивных методах нагружения меняется динамика движения дислокаций, и они, согласно соотношению Орована, становятся подвижнее. Так как при ДКУП скорость деформации на 5 порядков выше, чем при РКУП, то дополнительное увеличение подвижности структурных дефектов в этом случае очевидно.
Для сравнения эти же материалы были подвержены квазистатическому деформированию (ɛ̇ = = 10–1 с–1) методом кручения в наковальнях Бриджмена при высоком квазигидростатическом давлении (КВД) P = 4–8 ГПа и варьировании числа оборотов наковальни от 0.5 до 15, что соответствовало изменению истинной деформации e = 3.9–6.9 [30]. При КВД сплава А3003 обнаружена более богатая палитра структур. При е = = 4.1–5.5 субзеренная структура, преобладающая при е = 3.9, заменяется смешанной структурой, в которой с ростом деформации увеличивается доля рекристаллизованной составляющей. При е = = 6.4–6.9 снова активизируются процессы пластической деформации, и формируется структура, в которой основной объем занимают вторично фрагментированные зерна с развитой внутренней субструктурой и размером 150 нм. В тройных стыках таких кристаллитов возникают единичные, свободные от дислокаций рекристаллизованные зерна. Таким образом, в сплаве А3003 при квазистатическом методе деформации обнаружен циклический характер формирования СМК-состояний. При этом в материале понижается уровень внутренних напряжений и степень упрочнения. Установленная для СМК-сплава А3003 последовательность структурообразования, ранее обнаруженная в меди [37], сейчас находит подтверждение для других СМК-материалов [1].
Природа физических процессов, протекающих при КВД сплава А7075, изменяется в зависимости от режима деформации. Преобладающим механизмом релаксации внутренних напряжений в широком интервале истинных деформаций е ≤ 6.4 является фрагментация, при этом, структура измельчается до наноуровня. Средний размер зерна при е = 6.4 равен 55 нм (рис. 3б). При е ≥ 6.9 в сплаве начинает действовать другой канал диссипации упругой энергии – низкотемпературная динамическая рекристаллизация. В этом случае в смешанной структуре, состоящей преимущественно из фрагментированных зерен, появляются менее дефектные зерна с четкими границами.
Установлено, что смена одного вида структуры другим в сплаве А7075 происходит на фоне двух индуцированных пластической деформацией и конкурирующих между собой фазовых превращений: деформационного растворения дисперсоидов алюминидов тугоплавких металлов и фазы MnZn2 (4.1 < е < 4.8) и деформационного кинетического старения с выделением метастабильной упрочняющей η'-фазы (е > 5.5). Таким образом, переход от фрагментированной структуры к рекристаллизованной структуре происходит через дополнительный канал релаксации упругой энергии – фазовые превращения [1]. Подводя итог проведенным экспериментам, можно считать установленным, что в процессе кручения под высоким давлением при больших степенях деформации (е = 5.5–6.4) в сплаве А7075 достигается наноструктурное состояние. Все описанные выше характеристики такой структуры свидетельствуют о том, что она образуется путем фрагментации субзерен, т.е. за счет изгиба кристаллической решетки и ротационных мод деформации. Изгиб кристаллической решетки осуществляется в результате развития кристаллографического скольжения решеточных дислокаций, а ротационные моды деформации реализуются посредством зернограничного проскальзывания, обусловленного перемещением частичных дисклинаций [2, 3, 38]. Такой же механизм релаксации подводимой извне упругой энергии наблюдался в этом сплаве и в процессе его высокоскоростного деформирования методом ДКУП. Переход к другому механизму релаксации упругой энергии – динамической рекристаллизации, в исследованном сплаве реализуется только при очень большой величине накопленной деформации (е = 6.9), достигаемой при КВД.
Приведенные выше данные свидетельствуют о том, что структуру и фазовые превращения в Al сплавах можно варьировать в широких пределах, меняя режимы ИПД.
Известно, что СМК-структура Al сплавов, полученных разными методами ИПД, чувствительна к нагревам и при отжигах происходит ее деградация [39–41]. Для выяснения механизма перехода деформированной ДКУП структуры в ультрамелкозернистую (УМЗ) равновесную структуру, подробно изучена термическая стабильность СМК-состояния в сплаве А3003 [16]. Изохронные отжиги деформированных образцов, полученных при V = 300 м/с и N = 4, проводили в интервале температур 200–400°С с шагом 100°С в течение одного и двух часов с охлаждением на воздухе. Согласно температурным зависимостям микротвердости при разных временах отжига, можно выделить две стадии изменения этой характеристики материала (рис. 4а).
Рис. 4.
Температурные зависимости микротвердости при разных временах отжига при 400°С: ◼ – 1 ч, ⚫ – 2 ч (а) и микроструктура сплава А3003 после отжига, 2 ч: б – светлопольное изображение, в – темнопольные изображения в рефлексах матрицы (002)Al.
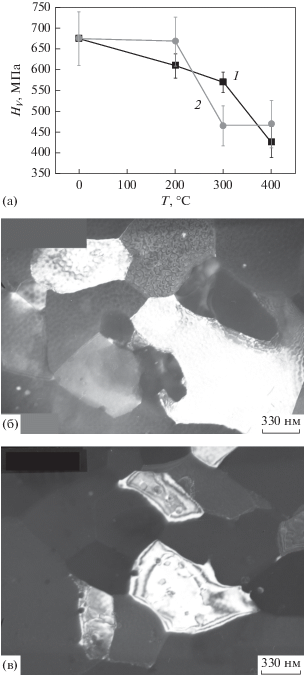
На первой стадии при нагреве до 200°С наблюдается незначительное снижение твердости, и фактически сохраняется деформационное упрочнение от ДКУП. При отжиге 300°С, 1 ч наблюдается падение значений твердости на 100 МПа, а увеличение времени выдержки усиливает процессы разупрочнения, и HV продолжает снижаться до 470 МПа. Дальнейшее повышение температуры и времени отжига стабилизируют низкие значения HV на уровне 450–425 МПа. Подобный характер изменения твердости наблюдали при изохронном одночасовом отжиге сплава А1560, полученного методом равноканально-угловой экструзии [33].
Эволюция деформационной структуры после изохронного отжига была исследована на двух масштабных уровнях, применяя СЭМ и ПЭМ. Анализ EBSD-карт разориентировок фрагментов структуры показал, что, несмотря на высокую температуру отжига (400°С), при одночасовой обработке сохраняется субмикронный масштаб структуры, а большинство зерен-субзерен (90%) имеют размеры менее 1 мкм. В структуре преимущественно формируются большеугловые границы, их доля составляет ~70%, средний угол разориентировки – 31°. С ростом времени отжига размерная стабильность нарушается, формируется структура, состоящая из достаточно крупных зерен, размером 3–5 мкм, и равноосных зерен, окруженных БУГ, размер которых не превышает 1 мкм (рис. 5а). Доля последних при данной продолжительности отжига сокращается до 50%, а растет до 30% число зерен, размером более 2 мкм.
Рис. 5.
Ориентационная карта структуры сплава А3003 после отжига при 400°С, 2 ч (а), спектры изменения размеров субзерен-зерен (б), углов разориентировки границ зерен (в).
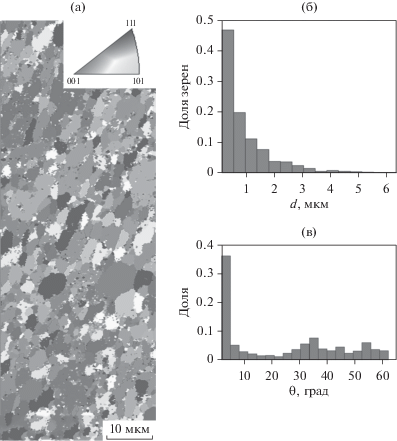
Средний размер элементов структуры, согласно представленной на рис. 5б гистограмме – 1.4 мкм.
Крупные зерна характеризуются развитой субструктурой, внутри них формируются малоугловые границы. Такую структуру можно охарактеризовать как частично рекристаллизованную, причем более мелкие и несодержащие МУГ зерна могли сформироваться в результате процесса статической рекристаллизации. В спектре углов разориентировки границ зерен доля БУГ составляет 53%, а средний угол равен 28° (рис. 5в). Неоднородность структуры, выявленная при анализе EBSD-карт, сохраняется и на микроуровне.
Так, на фоне мелких зерен с неоднородным внутренним контрастом, разделенных БУГ (рис. 4б), встречаются более крупные образования, состоящие из субзерен с МУГ (рис. 4в). Границы и тройные стыки зерен, окруженных БУГ, являются наиболее вероятными местами для зарождения центров постдинамической прерывистой рекристаллизации.
Таким образом, установлено, что в интервале температур 100–300°С сплав А3003, полученный динамическим прессованием, сохраняет СМК-состояние и повышенное упрочнение за счет высокой зернограничной составляющей, компенсирующей частичную релаксацию напряжений при нагреве. Нагрев до 400°С активизирует процессы разупрочнения деформированного ДКУП- сплава, уменьшая его твердость в 2 раза. При нагреве переход от СМК-деформированной структуры к УМЗ-структуре осуществляется путем одновременного протекания нескольких релаксационных процессов: “возврата” БУГ, непрерывной и прерывистой рекристаллизации. При повышении температуры отжига до 400°С формируется размерно-неоднородная зеренная структура с неуравновешенными тройными стыками (средний размер зерна 1.4 мкм), дальнейшее совершенствование которой осуществляется механизмом собирательной рекристаллизации.
1.2. Механические свойства СМК Al сплавов
Как показано выше, применение нового способа ИПД–ДКУП позволило получить широкую палитру алюминиевых сплавов в СМК-состоянии. Рассмотрим, как влияет формирование СМК-структуры на механические свойства и механизмы разрушения алюминиевых сплавов в широком диапазоне нагрузок – от статических испытаний до ударно-волнового нагружения, т.е.при ɛ̇ = 10–3–105 с–1.
Исследование закономерностей деформационного поведения СМК-сплава А 3003 при статическом растяжении проведены на образцах, полученных при разных параметрах ДКУП. Рисунок 6 демонстрирует инженерные кривые “напряжение–деформация”, построенные для СМК-образцов (V = 80 м/c, N = 2–4) и их крупнокристаллического (КК) аналога. Сравнение данных кривых указывает на существенное различие прочностных характеристик материала в зависимости от его структурного состояния. В СМК-состоянии значения условного предела текучести σ0.2 и временного сопротивления при растяжении σВ возрастают в 1.5–1.7 раз, при этом уменьшаются протяженность стадии деформационного упрочнения и коэффициент упрочнения. Отмеченные выше особенности подтверждают многочисленные экспериментальные данные, полученные для различных материалов в СМК-состоянии [38–41], а снижение коэффициента упрочнения свидетельствует в пользу преобладания механизма зернограничного проскальзывания над механизмом внутризеренного скольжения [5].
Рис. 6.
Кривые “напряжение–деформация” СМК-сплава А3003 после ДКУП (1 – N = 2, 2 – N = 4) в сравнении с КК аналогом (3).
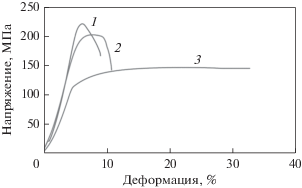
В то время как значения прочностных характеристик повышаются, пластичность сплава при переходе в СМК-состояние падает. Значение относительного удлинения до разрушения уменьшается в 2–3 раза, по сравнению с КК-состоянием. Сравнение механических свойств ДКУП-образцов, полученных при разном числе циклов динамического прессования, позволяет оценить их изменение с ростом величины накопленной деформации. При N = 1 σВ = 185 МПа, при N = 2 наблюдается небольшой рост прочностных характеристик до 215 МПа, обусловленный увеличением дефектности зерен-субзерен и количества МУГ. После четырехкратного прессования в смешанной структуре появляются рекристаллизованные зерна, при этом пластичность материала повышается до 10% при сохранении высокой прочности на уровне 200 МПа (рис. 6).
Наилучшим сочетанием прочностных и пластических свойств обладают образцы с бимодальной смешанной структурой, образованной СМК-зернами-субзернами и большой долей рекристаллизованных зерен, полученные методом ДКУП при V = 300 м/с, N = 4. Их сравнение со свойствами КК-сплава после традиционных методов обработки свидетельствует, что СМК-материал имеет более высокую прочность (σВ = 255 МПа), чем в нагартованном состоянии (σB = 200 МПа), и в два раза пластичнее (δ = 14%). Эти результаты подтверждают выводы авторов [42], о том, что сосуществование мелких и крупных фрагментов обеспечивает наилучшее сочетание механических свойств.
В условиях более интенсивных нагрузок, в диапазоне ɛ̇ = (4–8) × 103 с–1 [23], были исследованы термодинамические характеристики процесса пластической деформации, эволюции структуры и закономерности диссипации приложенной упругой энергии в упрочненных ДКУП Al сплавах разного состава [43, 44]. Методика измерения доли диссипированной энергии при динамическом сжатии образцов подробно описана в [24]. Суммируя полученные результаты, можно констатировать, что величина диссипированной энергии β- в Al-сплавах является структурно-чувствительным свойством. Если все данные, полученные при динамическом сжатии с разной скоростью, нанести на один график, то для каждого состава сплава получим набор значений, очерченных эллипсом (рис. 7). При сравнении величин диссипированной энергии в СМК- и КК-состояниях, видно, что в зависимости от состава сплава эти соотношения меняются. Так, в сплаве А3003 переход в СМК-состояние вызывает понижение β, а в сплаве А7075, наоборот, повышение.
Противоречивые, на первый взгляд, результаты можно объяснить, если сопоставить исходные до сжатия структурные состояния исследованных сплавов и проследить эволюцию структуры в процессе динамического сжатия. В частности, сплав А7075 до динамического сжатия имел неравновесную фрагментированную структуру с размером зерен-субзурен 200 нм, высокой плотностью дислокаций (2 × 1015 м–2), большой долей МУГ и БУГ и высоким уровнем внутренних напряжений, а сплав А3003 – менее дефектную СМК-рекристаллизованную структуру (размер зерна 600 нм) с высокой долей БУГ и плотностью решеточных дислокаций на порядок меньше. Так как главными источниками внутренних напряжений является дислокационные МУГ и дисклинации в тройных стыках, то после ДКУП уровень запасенной энергии в сплаве А7075 был выше, чем в сплаве А3003. Эволюция структуры при последующем деформировании (динамическом сжатии) зависит от величины запасенной энергии и связана с релаксацией внутренних напряжений.
Именно разный уровень запасенной при ДКУП энергии и диктует разный сценарий эволюции структуры двух рассматриваемых сплавов при динамическом сжатии в интервале ɛ̇ = (4–8) × 103 с–1. По данным ПЭМ определено, что после динамического сжатия в СМК-сплаве А3003, при сохранении среднего размера зерен 600 нм, формируется развитая дислокационная субструктура и появляются новые МУГ, т.е. подводимая энергия сжатия расходуется на накопление дефектов и рост внутренней запасенной энергии.
В СМК-сплаве А7075, наоборот, происходит трансформация неравновесных границ зерен-субзерен, аннигиляция граничных дефектов (возврат неравновесных границ) и уменьшение общей плотности дислокаций. Подобная эволюция структуры свидетельствует об активизации процессов релаксации внутренних напряжений и понижении внутренней энергии. Эти данные подтверждены результатами РСА об уменьшении среднеквадратичной микродеформации кристаллической решетки Al-твердого раствора (рис. 8а), а также понижением твердости сплава А7075 после сжатия (рис. 8б).
Рис. 8.
Среднеквадратичная микродеформация кристаллической решетки Al в КК (⚫) и СМК (◼) сплаве А7075 (а) и их твердость (б) до (◻) и после (◼) динамического сжатия.
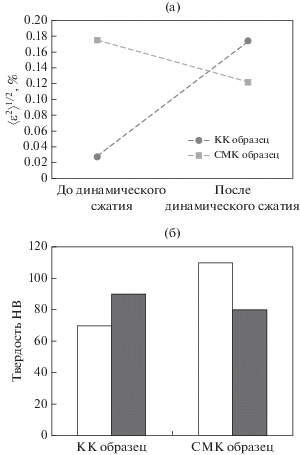
В КК-сплавах А3003 и A7075 при динамическом сжатии формируется ячеистая деформационная структура, при этом увеличиваются микронапряжения и твердость материалов (рис. 8а, 8б). Плотность дислокаций возрастает, часть энергии сжатия расходуется на образование дефектов, и доля накопленной энергии растет.
Таким образом, при динамическом сжатии уровень накопленной энергии в КК-сплавах и в СМК-сплаве А3003 повышается, а в СМК-сплаве А7075 понижается. Чем выше скорость деформации, тем больше эти изменения. Так как величина энергии динамического сжатия при постоянной скорости одинакова для обоих сплавов, то, чем меньше доля накопленной энергии в общем балансе энергии, тем большая ее часть переходит в тепло. Примером служит СМК-сплав А7075, когда в тепло (по результатам инфракрасного сканирования процесса динамического сжатия) переходит до 80% всей энергии деформации.
Исследования механического поведения СМК Al сплавов, полученных ДКУП, в условиях динамического сжатия выполнены на сплавах А7075 с фрагментированной структурой и А3003 со смешанной, с преобладанием рекристаллизованной, структурой. Динамическое сжатие по методу Гопкинсона–Кольского осуществляли при различных ɛ̇ = (3.3–6.6) × 103 с–1, что дало возможность получить результаты о скоростной чувствительности механических характеристик этих материалов [17]. Полученные в процессе динамического сжатия деформационные кривые ДКУП-образцов из сплава А3003 показаны на рис. 9а, а КК-образцов на рис. 9в. В обоих случаях наблюдается прямая скоростная зависимость предела текучести, т.е. чем выше ɛ̇, тем больше этот параметр. Сравнение рис. 9а и 9в показывает, что для СМК-сплава характерен рост прочностных характеристик, а именно, на 47% при ɛ̇ = 4.0 ×103 и на 28% при ɛ̇ = 6.0 × 103 c–1.
Рис. 9.
Деформационные кривые СМК-сплавов А3003 (а) и А 7075 (б) и КК сплава А3003 (в), полученные при динамическом сжатии с разными скоростями (1 – ɛ̇ = 4 × 103 с–1; 2 – ɛ̇ = 6.0 × 103 c–1; 3 – ɛ̇ = 6.6 × × 103 c–1).
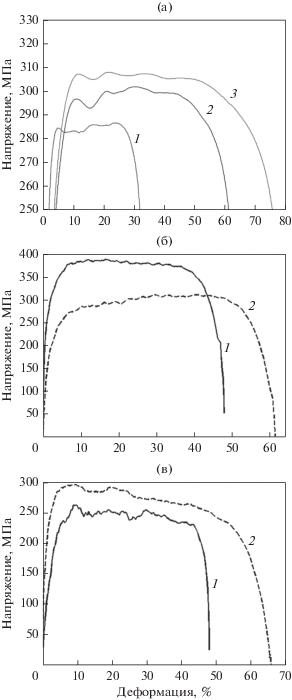
Механическое поведение сплава А7075 в СМК-состоянии наглядно демонстрируется на рис. 9б. При увеличении ɛ̇, динамические механические характеристики СМК-сплава А7075 проявляют обратную скоростную чувствительность: предел текучести снижается на 27%, и при этом уменьшается деформационное упрочнение на стадии пластического течения. Такие изменения механических характеристик с ростом скорости динамического сжатия могут быть обусловлены изменением структурного состояния, снижением дефектности границ зерен и сменой механизма внутризеренного дислокационного скольжения на механизм зернограничного проскальзывания. О подобном влиянии границ зерен на прочностные свойства наноструктурной меди отмечалось в [45].
Механические характеристики СМК Al сплавов, полученных ДКУП, при ɛ̇ ≥ 105 с–1 определяли при ударно-волновом нагружении [44, 46, 47]. Учитывая доказанную зависимость механического поведения СМК-сплавов от их структурных характеристик при менее интенсивных воздействиях, эксперименты по измерению прочностных характеристик при ударно-волновом нагружении были выполнены на алюминиевых сплавах, отличающихся химическим составом, размером структурных составляющих, количеством МУГ и БУГ зерен, а также плотностью дефектов. Для выявления особенностей деформационного поведения и разрушения СМК-образцов было проведено сравнение с поведением сплавов в КК-состоянии.
На волновых профилях (рис. 10а) регистрируется выход на поверхность образцов упругого предвестника (HEL), пластической волны сжатия (показана стрелкой A) и части следующей за ней волны разрежения (обозначена стрелкой Б). Сразу за фронтом упругой волны наблюдается плавный рост скорости свободной поверхности до резкого скачка в пластической волне сжатия вследствие деформационного упрочнения материала. Время нарастания параметров в пластической ударной волне определяется вязкостью материала или временем релаксации напряжений [20, 21]. После отражения импульса сжатия от свободной поверхности внутри образца генерируются растягивающие напряжения, в результате чего инициируется его разрушение-откол (момент формирования откола отмечен стрелкой В на рис. 10а). При этом происходит быстрая релаксация растягивающих напряжений, и формируется слабая волна сжатия (откольный импульс), выход которой на поверхность образца вызывает второй подъем скорости. Последующие затухающие колебания скорости вызваны многократными отражениями волн между поверхностью образца и откольной пластиной.
Рис. 10.
Профили скорости свободной поверхности образов с различными структурами: а – обобщенный волновой профиль; стрелками показаны: HEL – упругий предвестник волны сжатия; А – фронт пластической волны сжатия; Б – волна разрежения; В – момент формирования откола; Δufs – величина спада скорости от максимума до минимума в момент откола; б–г – волновые профили образцов алюминиевых сплавов А7 (б), А7075 (в) и А3003 (г) в КК (1) и СМК (2) состояниях.
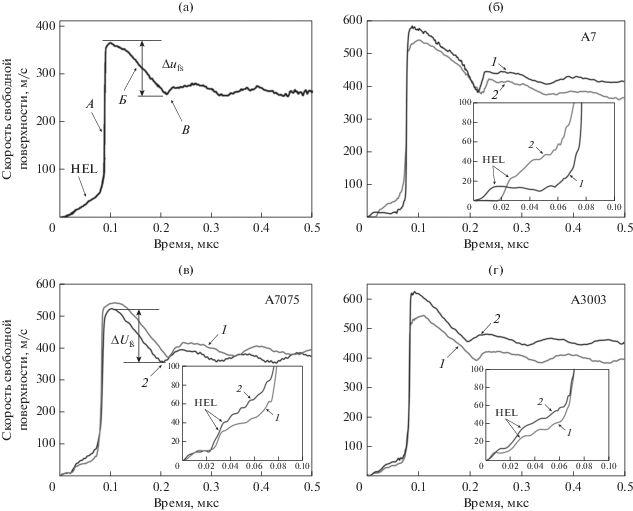
По измеренной из волновых профилей амплитуде фронта упругого предвестника рассчитывали значения динамического предела упругости σHEL и предела текучести, а для расчета критических разрушающих напряжений при отколе (откольной прочности) из экспериментальных профилей скорости свободной поверхности определяли величину спада скорости от максимума до первого минимума в момент откола [26, 48]. Кроме того, волновые профили позволяют получать данные по толщине откольной пластины hsp, которая формируется при откольном разрушении. По описанной выше методике были испытаны образцы технического алюминия с рекристаллизованной структурой (V = 300 м/c, N = 4), сплава А3003 со смешанной структурой, состоящей из зерен-субзерен с МУГ и БУГ (V = 300 м/c, N = 1, рис. 2в), сплава А5083 со структурой, образованной мезополосами сдвига (V = 150 м/c, N = 1, рис. 2а), и сплава А7075 с развитой фрагментированной структурой (V = 150 м/c, N = 2). Полученные волновые профили показаны на (рис. 10б–10г).
На основании полученных данных можно оценить влияние состава материала, величины зерна и степени дефектности структуры на динамические механические свойства исследованных сплавов. Сопоставление двух волновых профилей, полученных в одинаковых условиях нагружения, для КК- и СМ-К образцов одного состава (рис. 10б–10г), свидетельствует о том, что для всех сплавов перевод материала в СМК-состояние сопровождается повышением динамического предела упругости. Сравнение амплитуды и формы упругого предвестника, распространяющегося при нагружении КК- и СМК-сплавов, показывает, как меняется динамический предел упругости σHEL, который пропорционален напряжению сжатия за фронтом упругого предвестника. В СМК-состоянии σHEL всегда в среднем в 1.5 раза выше, чем соответствующий σHEL КК-аналогов. Наибольший рост σHEL отмечен в алюминии А7, наименьший – в сплаве А 3003.
Аналогичным образом изменяется и динамический предел текучести (Y) материалов (рис. 11). В СМК-алюминии А7 по сравнению с КК-аналогом происходит увеличение Y в 1.7 раза, в СМК-сплавах А3003 и А7075, А5083 в 1.4 и 1.5 раза соответственно.
Следовательно, все СМК Al сплавы, полученные методом ДКУП, при ɛ̇ = (1.2–3.3) × 105 с–1 демонстрируют увеличение характеристик упруго-пластического перехода по сравнению с КК-сплавами. Это отличает их поведение от СМК-материалов, полученных квазистатическими методами ИПД. Например, для СМК-тантала после всесторонней изотермической ковки (ВИК) динамический предел упругости снижается по сравнению с σHEL КК-тантала на 35% [48], а в СМК-алюминиевом сплаве 1421, полученном РКУП, и в СМК-титане, полученном всесторонней ковкой, наблюдается слабое снижение динамического предела текучести [49].
Другой важной характеристикой, рассчитываемой из профиля скорости движения свободной поверхности нагружаемых образцов, является их откольная прочность σsp. Имеющиеся литературные данные по влиянию масштаба структуры и степени ее дефектности на сопротивление откольному разрушению неоднозначны, и их корректное сравнение возможно только при одинаковой скорости деформирования. Так, в тантале уменьшение размера зерна до СМК-уровня привело к 5% возрастанию откольной прочности [48], а в сплаве Д16 [50] и меди [51] авторы не выявили различий в процессе динамического разрушения. Оцененные значения откольной прочности СМК Al сплавов, полученных ДКУП, также не столь однозначны. Согласно проведенным измерениям абсолютные значения σsp СМК-материалов практически одинаковы для всех составов и изменяются от 1.32 до 1.36 ГПа. Сравнение значений критических разрушающих напряжений при отколе СМК- и КК-образцов показало, что переход в СМК-состояние сплава А7075 и алюминия А7 сопровождается уменьшением σsp. В легированном сплаве разница составляет всего 7%, а в алюминии А7 – существенно выше – 25%. Если считать, что высокоскоростное разрушение при отколе представляет собой кинетический процесс зарождения и роста дефектов, которые концентрируются на границах зерен и на поверхности хрупких интерметаллических фаз, то понижение σsp СМК-материалов является вполне закономерным. В отличие от этих двух сплавов, СМК-сплав А3003, наоборот, демонстрирует незначительное повышение откольной прочности.
Если сравнить значения откольной прочности КК Al сплавов и КК- алюминия, то последний демонстрирует более высокие значения (1.80 вместо 1.34–1.38 ГПа), что также отмечалось в [52]. Т.е. полученные данные соответствуют утверждению этих авторов, что разница в откольной прочности поликристаллического алюминия различной чистоты и его сплавов (например, А 5083) существует и исчезает только с ɛ̇ > 106 с–1. Толщина откола во всех СМК-материалах равна 0.33–0.39 мм, это на ~10% меньше, чем в аналогичных КК-сплавах.
Таким образом, проведенные измерения динамического предела упругости и критических разрушающих напряжений при отколе, показали, что при скоростях деформирования, соответствующих условиям ударной нагрузки, алюминий и его сплавы с СМК-структурой, полученной ДКУП, остаются в упрочненном состоянии, в отличие от СМК-материалов, полученных методами ИПД. Это обусловлено повышенным начальным уровнем запасенной в результате ДКУП упругой энергии деформации, вследствие суммарного действия механического простого сдвига и ударной волны. Откольная прочность исследованных СМК-алюминиевых сплавов колеблется в пределах 7% по отношению к ее значениям в КК аналогах.
Для исследования эволюции СМК-структуры Al сплавов при ударно-волновом сжатии были выполнены специальные эксперименты с сохранением образцов сплава А5083 с зеренно-субзеренной смешанной структурой (V = 250–300 м/с, N = 2). Сохраненный образец с внутренним отколом исследовали в трех сечениях – у поверхности нагружения, в области разрушения и у свободной поверхности. В сравнении с состоянием после ДКУП, структура образцов после ударного сжатия характеризуются повышенными в 1.5–2 раза значениями плотности дислокаций и увеличенной на 200 MПa микротвердостью. Учитывая незначительное увеличение этих параметров относительно исходного состояния сплава, нельзя исключить, что при динамическом сжатии наблюдается конкуренция двух механизмов пластической деформации, а именно, дислокационного скольжения и зернограничного проскальзования. Тем не менее дополнительное упрочнение сплава свидетельствует в пользу того, что преобладающим механизмом пластической деформации при ударном сжатии является дислокационное скольжение. Можно предположить, что дополнительное упрочнение материала происходит за счет образования эффективных структурных барьеров (например, наноразмерных выделений) на пути распространения деформации вблизи границ зерен, которые затрудняют низкотемпературное зернограничное проскальзывание. При отсутствии таких выделений в СМК-сплаве А5083, их роль, вероятно, играют зернограничные дефекты – дислокации и частичные дисклинации, образующиеся в результате процесса интенсивной фрагментации, инициированной сложной деформационной модой.
Проведен эксперимент по сравнению динамических свойств СМК-сплава А5083, полученного разными методами ИПД–ДКУП и КВД. Относительно КК-аналога, все динамические свойства СМК-образца после КВД, структура которого сформирована деформированными зернами со средним размером 200 нм, окруженных большим количеством размытых БУГ, в 2 раза выше, а именно, σHEL = 0.77 ГПа, Y = 0.41 ГПа .Как показано ранее, характеристики упруго-пластического перехода СМК-сплава (структура которого показана на рис. 2а, 2б) также обладает повышенными относительно КК аналога динамическими свойствами, но прирост этих характеристик меньше, только в 1.5 раза. Следовательно, по сравнению с образцами, деформированными КВД, образцы после ДКУП демонстрируют более низкие динамические свойства. Для объяснения этих результатов проанализируем отличия в СМК-структуре после ДКУП и КВД. Если не принимать во внимание незначительную разницу в среднем размере структурных составляющих, то основными факторами различия становятся соотношение МУГ и БУГ и плотность дислокаций (8.7 × 1014 и 7.8 × 1013 м–2 соответственно). Оба эти фактора вносят свой вклад в суммарное упрочнение сплава и регулируют величину Y. Исходя из определенных значений Y, следует, что, несмотря на меньшую плотность дислокаций в СМК структуре после КВД, более высокие значения предела текучести (на 80 МПа) достигаются за счет зернограничного упрочнения, вызванного формированием большого количества зерен с БУГ. Таким образом, при оценке динамических свойств СМК-сплавов помимо размера зерна важно учитывать плотность дефектов и соотношение МУГ и БУГ.
2. Титан
Исследование возможностей использования ИПД, таких как квазистатическое РКУП, для создания в титане и его сплавах СМК и нанокристаллических (НК) структур с высокими свойствами и улучшенной биосовместимостью имеет важное практическое значение, поскольку указанные материалы находят широкое применение в биомедицинских технологиях [53, 54]. Первые измерения показали, что высокоскоростное ДКУП повышает прочностные характеристики титана почти в два раза при относительно небольшом снижении пластичности [55]. Цель исследования заключалась в подборе оптимальных режимов ДКУП, анализе геометрии ДКУП и изучении особенностей деформационного поведения, эволюции микроструктуры и механических свойств титана при высокоскоростном прессовании по различным режимам. Цилиндрические образцы титана марки ВТ1-00 и ВТ1-0 диаметром 16 либо 14 мм, длиной 60 мм подвергали ДКУП по различным схемам (рис. 1), при этом варьировали начальную скорость разгона образцов, количество проходов и температуру прессования.
2.1. Деформационное поведение титана при ДКУП
Эффекты локализованного разрушения. После одного прохода прессования (ДКУП, N = 1) при комнатной температуре в деформированном образце возникла система трещин, которые разделили его на шесть соединенных фрагментов. Форма и расположение трещин позволяют выяснить некоторые особенности высокоскоростной деформации при данном методе нагружения.
На рис. 12 представлена макроструктура образца в продольном сечении. Видно, что трещины (стрелка 1) расположены периодически, примерно через равные интервалы, и имеют почти одинаковую криволинейную форму. Сопоставление вида трещин в продольном и поперечном сечении образца показало, что в пространстве трещины имеют форму изогнутых желобов. Похожая картина нарушения сплошности образцов и образования трещин наблюдалась на магниевом сплаве при РКУП с малой скоростью деформации [56]. Тонкие светлые полоски, простирающиеся вдоль образца (стрелка 2), как будет показано ниже, являются следами локализации высокоскоростной деформации.
Рис. 12.
Макроструктура титанового образца после ДКУП, N = 1. 1 – трещины, 2 – следы локадизации деформации.
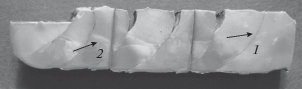
Равномерная деформация при ДКУП. “Геометрический” метод расчета деформации сдвига. Основная микроструктура, сформированная при равномерной деформации, представляет собой дисперсные удлиненные зерна-волокна (рис. 13а). Их длина составляет 15–20 мкм, ширина – около 2 мкм. Зерна вытянуты в одном направлении, составляющем с продольной осью образца (направлением прессования) угол α близкий к 30°. .Электронно-микроскопическое исследование показало, что удлиненные зерна состоят из субзерен (рис. 13б). Субзерна также имеют удлиненную форму. Субзеренная структура весьма неоднородна как по размерам субзерен, так и по их разориентации. Поперечный размер субзерен изменяется от 0.3 до 1 мкм. Разориентировка может составлять несколько градусов. В субзернах наблюдается чередующийся контраст, свидетельствующий о высоком уровне внутренних напряжений. Наблюдаются также деформационные двойники (рис. 13в).
Рис. 13.
Структура титана в области равномерной деформации при ДКУП, N = 1. Металлографическое (а) и электронно-микроскопические (б, в) изображения; в – темнопольное изображение.
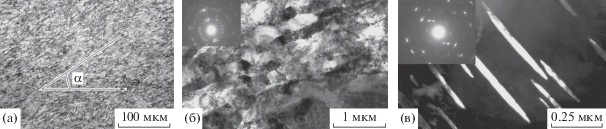
Зная характеристики микроструктуры, а именно угол α, можно рассчитать величину деформации сдвига. Рассмотрим геометрию деформации при РКУП для двух значений внутреннего угла между двумя каналами: Ф = π/2 и π > Ф > π/2 (рис. 14).
Рис. 14.
Схемы, поясняющие метод определения деформации сдвига при ДКУП-прессовании для угла пересечения каналов Ф = π/2 (а) и произвольного угла π > Ф > π/2 (б).
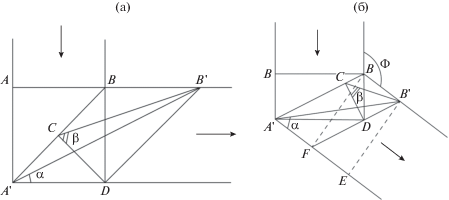
Считаем, что трение о стенки каналов отсутствует, сопротивление сдвигу мало по сравнению с действующим напряжением, течение материала в каналах ламинарное. В результате деформации точка А, расположенная на внешней стороне канала, займет положение А' (рис. 14). Точка В, расположенная на внутренней стороне канала, займет положение В', при этом АА' = BB '. В результате деформации линия АВ преобразуется в линию А'В ', которая соответствует ориентации волокон относительно направления деформирования. Треугольник ΔА'ВD, характеризующий недеформированное состояние, преобразуется после деформации в ΔА'ВB '. Деформация сдвига описывается перемещением отрезка СD (СD ⊥ А'В) в положение СВ ', угол сдвига β (рис. 14а). Относительный сдвиг γ = tg β. Из подобия треугольников ΔА'ВB ' ~ ΔB 'ВС следует, что α + β = π/2. Отсюда
Соотношение (1) позволяет определить деформацию сдвига по углу между направлением волокнистой структуры и продольной осью образца.
Установим взаимосвязь между внутренним углом Ф и углом α. Для этого рассмотрим два треугольника: ΔА'ВF и ΔА'B 'E (рис. 14б). В этих треугольниках сtg(Ф/2) = А'F/ВF и сtg α = А'E/B 'E. Отсюда
(2)
$2{\text{сtg}}\left( {{\Phi \mathord{\left/ {\vphantom {\Phi 2}} \right. \kern-0em} 2}} \right) = {\text{сtg}}\alpha .$Таким образом, соотношения (1) и (2) связывают геометрию канального прессования (угол Ф), деформацию сдвига (γ) и характеристику микроструктуры (угол α).
В работе [57] подобные соотношения были получены с использованием методов математической теории пластичности. При этом не было обращено внимание на то, что угол α можно определить из металлографических наблюдений. Описанный вывод этих соотношений существенно проще и нагляднее, и использует только геометрию деформирования.
Сравним результаты металлографического исследования титанового образца с анализом геометрии деформирования. При Ф = π/2, учитывая, что АА' = BB ' = AB, получаем ∠В 'А'D = α = 26.5° (рис. 14а). Эта величина неплохо согласуется с микроструктурой, где α ≈ 30 град. (рис. 13а). При α = 26.5° γ = 2.0, при α = 30 град γ = 1.7. Таким образом, действительная деформация сдвига в данном эксперименте составляет около 1.7.
Движение металла во втором канале описывается перемещением фронта А'В '. В идеальном случае фронт будет прямолинейным и перемещается поступательно. В действительности процесс происходит сложнее.
В данном эксперименте о распространении фронта можно судить по форме трещин. Криволинейная форма трещин, показанная на рис. 12, свидетельствует, что скорость течения металла в поперечном сечении неодинакова при переходе из первого канала во второй, а именно, в верхней половине канала он течет медленнее, чем в нижней. Как будет показано ниже, это подтверждено результатами моделирования. Разная скорость течения приводит к сдвигам в горизонтальной плоскости. Такие сдвиги вызывают эффекты локализации сдвиговой деформации.
На рис. 12 видно, что на верхней поверхности образца трещины “раскрыты” и образуют клинообразные пустоты. Это указывает на то, что в верхней половине образца действуют растягивающие напряжения, происхождение которых также связано с разной скоростью течения. Неравномерность деформации по сечению обусловлена динамическими эффектами при большой скорости течения и, возможно, трением о стенки канала.
Локализованная деформация. Полосы адиабатического сдвига. Микроструктурное исследование показало, что тонкие светлые полоски на изображении макроструктуры (рис. 12) представляют собой протяженные участки рекристаллизованных зерен на фоне деформированной структуры. На рис. 15а представлен снимок микроструктуры с участком динамически рекристаллизованных зерен. Температура рекристаллизации α-титана зависит от многих факторов: степени предварительной деформации, времени выдержки, наличия примесей. Она расположена в интервале температур 500–600°С [58]. Поэтому тонкие слабо травящиеся полоски представляют собой участки, в которых произошло значительное повышение температуры (до температур рекристаллизации) вследствие локализации сдвиговой деформации, то есть это полосы адиабатического сдвига (ПАС). В отличие от известных работ [59, 60], в которых ПАС в титане имели ширину от 1 до 10 мкм, ширина ПАС в исследованном образце была на порядок больше и составляла 50–100 мкм.
Рис. 15.
Микроструктура титанового образца после ДКУП, N = 1 в участках локализованной деформации. Продольная полоса адиабатического сдвига (а), участок полосы при большом увеличении (б), полоса сдвига без рекристаллизации (в).
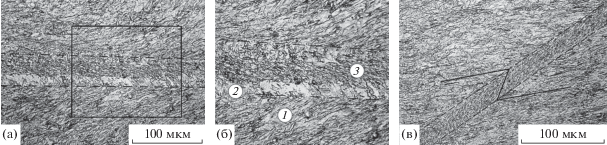
Представленная на рис. 15а полоса очерчена штриховыми линиями. Видно, что структура полосы неоднородна по ширине, и полоса состоит из трех слоев. По ее краям располагаются слои из более крупных зерен, что свидетельствует о более высокой температуре нагрева. В среднем слое размер зерен меньше, и структура сохраняет направленность.
На рис. 15б представлен при большом увеличении участок микроструктуры, выделенный прямоугольником на рис. 15а. Цифрой 1 указана деформированная структура, цифрой 2 – крайний слой полосы адиабатического сдвига с более крупными зернами, цифрой 3 – средний слой. В среднем слое на фоне деформированной структуры видны мелкие рекристаллизованные зерна, т.е. произошла частичная рекристаллизация. Направление волокон в этом слое образует угол ~120 град с направлением волокон в деформированном слое 1.
Этот факт служит подтверждением сдвигового механизма образования полосы. Относительный сдвиг материала в среднем слое полосы составляет приблизительно 3.5. Можно заключить, что подобная трехслойная структура полосы свидетельствует о том, что степень сдвиговой деформации на краях полосы больше, чем в ее средней части.
Микроструктурное исследование показало, что вдоль трещин, как и в тонких светлых полосках, располагались участки рекристаллизованной структуры.
Иногда в отдельных участках полосы сдвига можно наблюдать, что рекристаллизация не произошла, но сама полоса четко выявляется по изгибу структурных составляющих (рис. 15в). Изменение направления вытянутости структуры позволяет выполнить оценку деформации сдвига в полосе. Относительный сдвиг в разных участках полосы, показанной на рис. 15в, составляет 3.5–4.0.
Наблюдение рекристаллизации вдоль трещин свидетельствует о том, что локализованная сдвиговая деформация сопутствовала распространению трещины, препятствуя окончательному разрушению за счет локального повышения температуры. В некоторых, более крупных рекристаллизованных зернах в ПАС наблюдались пластинчатые структуры. Пластинки могут иметь двоякое происхождение. Это либо деформационные двойники в α-фазе, либо пластинчатые кристаллы α'-мартенсита, возникшие в результате превращения высокотемпературной β-фазы в низкотемпературную α-фазу. В последнем случае температура в таких участках должна была бы повыситься до температуры α → β-перехода (885°С). В работах [59, 60] было расчитано, что температура внутри ПАС в титане не превышала 800°С, а в работе [61] в сплаве Ti–6% Al–4% V она оценивалась как 1000°С. Поэтому данный вопрос требует дальнейшего исследования.
Таким образом, кроме равномерной деформации, ДКУП титана при комнатной температуре сопровождается сильными эффектами локализованной деформации в виде поперечных и продольных полос адиабатического сдвига и трещин вдоль поперечных ПАС [8, 62]. Для устранения таких нежелательных эффектов необходимо создать условия, обеспечивающие релаксацию возникающих напряжений.
Одним из общеизвестных методов повышения способности к релаксации напряжений является повышение температуры деформации. Известно [58, 63, 64], что при комнатной и низкой температурах деформация титана осуществляется преимущественно двойникованием, затем включается призматическое скольжение. При повышении температуры титан деформируется преимущественно скольжением, причем кроме призматического скольжения, включается пирамидальное по нескольким плоскостям. Множественное скольжение способствует повышению релаксационной способности и деформируемости.
2.2. Структура титана после ДКУП при повышенной температуре
В исходном состоянии титан марки ВТ1-0 имел крупнозернистую структуру, сформировавшуюся в результате β → α превращения. Зерна размером в несколько десятых долей миллиметра содержали хорошо очерченные пластины и субзерна со слабо травящимися границами. Как обсуждалось выше, в титане при ДКУП при комнатной температуре наблюдаются эффекты локализации деформации: образуются наклонные и продольные полосы адиабатического сдвига (ПАС) и закономерно расположенные трещины (рис. 12, 15). С целью устранения таких нежелательных эффектов ДКУП титана было выполнено при температурах 390–530°С. В продольных сечениях деформированных при повышенной температуре образцов при визуальном рассмотрении не было найдено ни раскрытых трещин, ни поперечных и продольных ПАС, которые наблюдались в образцах титана, подвергнутых ДКУП при комнатной температуре. (рис. 12). Следовательно, повышение температуры ДКУП до 500°С предотвращает разрушение образцов титана. На рис.16 видны периодически расположенные наклонные полосы, происхождение которых обусловлено деформацией сдвига. Угол наклона полос сдвига к продольной оси образцов составляет около 30°, что согласуется с результатами РКУП [3, 4, 56, 57] и геометрией деформации при ДКУП [8] (рис. 14).
Среднее расстояние между полосами локализованного сдвига в образцах титана уменьшается при увеличении температуры и интенсивности прессования. Так, для ДКУП при 500°С среднее расстояние между полосами составляет 0.3 мм (рис. 16), для ДКУП в два прохода при 530°С – 0.05 мм. Расстояние между наклонными ПАС в титане, подвергнутом ДКУП при комнатной температуре, составляло 7–10 мм (рис. 15).
В процессе ДКУП при прохождении зоны пересечения каналов в образце накапливаются упругие напряжения, которые релаксируют периодически повторяющейся сдвиговой деформацией. Так как критическое напряжение сдвига уменьшается при повышении температуры, релаксация происходит чаще, и расстояние между полосами сдвига уменьшается, разрушения не происходит. Изменение расстояния между полосами на два порядка (от 7 мм до 50 мкм) свидетельствует о значительном уменьшении критического напряжения сдвига при повышении температуры до 530°С. Это обусловлено не столько влиянием собственно температуры на прочностные характеристики титана, как и любого другого металла, сколько изменением механизма деформации. Как обсуждалось выше, деформация титана при повышенной температуре происходит множественным скольжением (призматическим и пирамидальным), в то время как при комнатной и низкой температурах преобладает двойникование. Смена механизма деформации при повышении температуры приводит к повышению характеристик пластичности и деформируемости титана [58, 65]. При ДКУП титана при комнатной температуре, в условиях низкой деформируемости, возникают продольные и поперечные ПАС и трещины. Внутри ПАС температура резко возрастает, и происходит рекристаллизация, которая препятствует полному разрушению образцов [8]. При ДКУП при повышенной температуре напряжения релаксируют за счет частого образования наклонных полос сдвига, поэтому ПАС и трещины не возникают [66]. Такая релаксация напряжений была названа поперечной крупномасштабной [66].
После ДКУП при 500°С (рис. 16) между наклонными полосами сдвига видны многочисленные короткие цепочки, расположенные в продольном направлении, состоящие из мелких рекристаллизованных зерен. Расположение цепочек и их внутренняя структура позволяют считать, что они имеют такое же происхождение, как продольные ПАС в образцах, подвергнутых ДКУП при комнатной температуре. Цепочки, как и наклонные полосы сдвига, являются результатом релаксации напряжений. Эта релаксация названа продольной мелкомасштабной [66]. Заметим, что после ДКУП при 530°С в два прохода цепочки рекристаллизованных зерен не наблюдаются.
Микроструктура полос локализованного сдвига изменяется в зависимости от температуры ДКУП. На рис. 17 представлена микроструктура анализируемых образцов. Видно, что в образце, подвергнутом ДКУП, N = 1 при 500°С полосы сдвига шириной 10–15 мкм состоят из мелких рекристаллизованных зерен размером 2–3 мкм (рис. 17а, 17б). Между полосами сдвига структура представляет собой дисперсную смесь рекристаллизованных зерен, группирующихся в короткие изогнутые цепочки, и деформированных нерекристаллизованных участков (дуплексная структура). Длина цепочек равна 150 мкм, ширина 10–15 мкм. Форма цепочек (радиус изгиба) определяется размером областей, испытывающих вращение при деформации. В процессе вращения, вследствие сдвига одних областей металла относительно соседних, происходит локализация деформации, приводящая к дополнительному нагреву. Локальное повышение температуры вызывает динамическую рекристаллизацию, которая является механизмом релаксации напряжений. После ДКУП, N = 2 при 530°С цепочки рекристаллизованных зерен не наблюдали (рис. 17в). Микроструктурное исследование показало, что отсутствие цепочек связано с общим измельчением структуры. Полосы сдвига имеют дуплексную структуру: они состоят из рекристаллизованных зерен размером 1.0–1.5 мкм и участков деформированной структуры в виде вытянутых изогнутых зерен. Между полосами располагаются деформированные участки и мелкие (1.0–1.5 мкм) рекристаллизованные зерна. Очевидно, что ДКУП, N = 2 приводит к уменьшению эффектов локализации деформации и получению более однородной структуры.
Рис. 17.
Металлографические снимки и схемы структур титана ВТ1-0 после: ДКУП, N = 1 при 500°С (а, б) и ДКУП, N = 2 при 530°С (в, г): 1 – протяженная полоса локализованной деформации, 2 – короткие изогнутые цепочки-кластеры рекристаллизованных зерен, 3 – участки деформированной структуры.
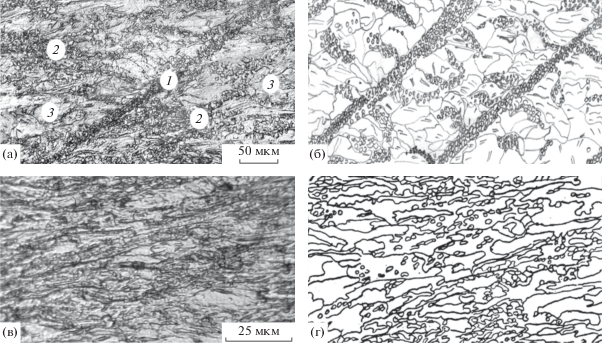
Деформированная часть структуры состоит, как правило, из удлиненных субзерен с поперечным размером 200–300 нм (рис. 18а). Субзерна содержат дислокации, что указывает на динамический характер полигонизации.
Рис. 18.
Электронно-микроскопические снимки титана ВТ1-0 после различных обработок: ДКУП, N = 1. при 500°С (а); ДКУП, N = 2 при 530°С (б) и ДКУП, N = 2 при 530°С, прокатки при 300°С и отжига при 210°С (в).
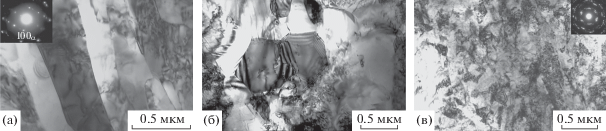
После ДКУП, N = 2 при 530°С, в структуре наряду с удлиненными, наблюдаются равноосные субзерна размером 150–200 нм и рекристаллизованные зерна (рис. 18б). Границы равноосных субзерен нечеткие, что характерно для субзерен деформационного происхождения.
Известно [67, 68], что дополнительная прокатка повышает прочностные характеристики титана. Исследования показали, что прокатка существенно (на 2–3 порядка) повышает плотность свободных дислокаций в субзернах, но практически не изменяет размеры субзерен, полученных при ДКУП (рис. 18в). После прокатки в структуре наблюдается высокая плотность контуров экстинкции деформационного происхождения, что свидетельствует о высоком уровне внутренних напряжений. Таким образом, микроструктура, сформированная при комбинированной обработке: ДКУП, N = 2 при 530°С, прокатке и отжиге, является наиболее благоприятной для получения наилучших прочностных свойств.
Металлографические исследования и измерения микротвердости образцов показали [13], что интервал температур рекристаллизации титана, упрочненного комбинированной обработкой, совпадает с температурным интервалом рекристаллизации холоднодеформированного титана (400–600°С), то есть полученная структура термически устойчива при нагреве до 400°С.
2.3. Механические свойства титана после ДКУП, прокатки и отжига
Результаты испытаний на растяжение представлены на рис. 19 и в табл. 2. ДКУП, N = 1 при 500°С увеличивает предел прочности в 1.2 раза, при этом важно, что относительное удлинение почти не уменьшается. ДКУП при 390°С приводит к повышению предела прочности в 1.4 раза, однако относительное удлинение уменьшается в 1.7 раза [13]. Несмотря на то, что при ДКУП, N = 2 температура деформации (530°С) была немного выше, чем при ДКУП, N = 1, предел прочности возрос в 1.5 раза по сравнению с σВ в недеформированном состоянии (650 против 430 МПа). Относительное удлинение уменьшилось в 1.6 раза, однако осталось на высоком уровне (19%). Прокатка образцов, подвергнутых ДКУП (кривые 4 на рис. 19), привела к существенному дополнительному упрочнению [13]. При этом упрочнение, полученное за счет ДКУП и за счет прокатки, складывается. Упрочнение, достигнутое за счет ДКУП при повышенных температурах, обусловлено, диспергированием структуры и субструктуры. Дополнительное упрочнение при прокатке связано с повышением плотности дислокаций и высоким уровнем внутренних напряжений. Наибольшее полученное значение предела прочности составляет 790 МПа, при относительном удлинении 15%.
Рис. 19.
Влияние прокатки и низкотемпературного отжига после ДКУП, N = 1 при 500°С (а) и ДКУП, N = 2 при 530°С (б). Диаграммы растяжения титана ВТ1-0 после обработок: 1 – исходный титан, 2 – прокатка и отжиг, 3 – ДКУП, 4 – ДКУП + прокатка и отжиг.
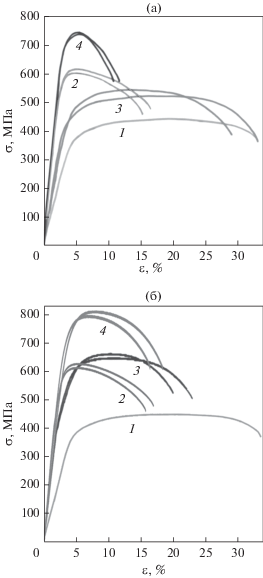
Таблица 2.
Механические свойства титана ВТ1-0 после различных обработок
Обработка | σ0.2, МПа | σВ, МПа | δ, % |
---|---|---|---|
Исходное состояние | 325 | 430 | 31 |
ДКУП, N = 1 при 390°С | 530 | 610 | 18 |
ДКУП, N = 1, при 500°С | 375 | 520 | 29 |
ДКУП, N = 2 при 530°С | 380 | 650 | 19 |
Прокатка и отжиг* | 490 | 620 | 17 |
ДКУП, N = 1 при 500°С + прокатка + отжиг* | 670 | 750 | 9 |
ДКУП, N = 2 при 530°С + прокатка + отжиг* | 630 | 790 | 15 |
По данным [69] РКУП, N = 8 титана при 450°С повышает предел прочности до 710 МПа при относительном удлинении 14%, что близко к результатам, полученным после ДКУП, N = 2 при 530°С Дополнительная (после РКУП) прокатка или экструзия повышает предел прочности до 1050 МПа при относительном удлинении 6–8%. Наибольшее значение предела прочности титана ВТ1-0, приведенное в [69], 1265 МПа при относительном удлинении 8.8%, получено в результате сложной обработки: многократной всесторонней изотермической ковки и последующей прокатки.
Таким образом, структура титана, подвергнутого ДКУП при 500–530°С представляет собой дисперсную смесь мелких рекристаллизованных зерен (1–3 мкм) и деформированных нерекристаллизованных участков. После одного прохода ДКУП рекристаллизованные зерна группируются в протяженные наклонные полосы и короткие продольные цепочки. Деформированные участки имеют субзеренное строение, поперечный размер субзерен составляет 200–300 мкм. При увеличении числа проходов до двух размер рекристаллизованных зерен уменьшается вдвое, субзерна в деформированных участках приобретают более равноосную форму, и микроструктура становится более однородной. Прокатка на 50% при 300°С и отжиг при 210°С образцов, подвергнутых ДКУП, повышает общую плотность дислокаций и создает высокий уровень внутренних напряжений. ДКУП, N = 2 при 530°С позволяет повысить предел прочности титана до 650 МПа, относительное удлинение уменьшается от 31 до 19%. Дополнительная прокатка и отжиг повышает предел прочности до 790 МПа при сохранении относительного удлинения на уровне 15%. Таким образом, предел прочности титана, подвергнутого ДКУП при повышенной температуре, можно существенно повысить за счет увеличения числа проходов и увеличения степени деформации при последующей прокатке.
3. Медь и ее сплавы
3.1. Эволюция структуры меди при ДКУП
Для определения влияния параметров высокоскоростного прессования на деформационное поведение меди в процессе ДКУП была проведена оценка напряженно-деформированного состояния нагружаемых образцов. Численное моделирование процесса высокоскоростного прессования выполняли для образца диаметром 16 мм и длиной 60–65 мм при его движении по двум пересекающимся каналам с закруглением внутреннего угла по радиусу (R) 7 мм. То есть постановка численного эксперимента соответствовала первоначально выбранной схеме ДКУП в матрице с R = 7 мм. Учитывали, что прохождение образца по каналам происходит за счет запасенной образцом кинетической энергии (см. инерционная схема нагружения, рис. 1а). Начальную скорость образца варьировали от 100 до 250 м/c. Расчеты проводили методом конечных элементов. Использовали упруго-пластическую модель Джонсона–Кука и уравнение состояния меди в форме Ми–Грюнайзена [70]. Определено, что нижний порог скорости, при которой медный образец полностью проходит зону пересечения каналов составляет 230 м/с [18]. Этот вывод согласуется с полученными [71–73] экспериментальными данными исследования эволюции структуры и свойств образцов меди при ДКУП по различным режимам и оценки их напряженно-деформированного состояния.
На рис. 20 приведены результаты расчетов сдвиговых напряжений в образце при начальной скорости 250 м/с [18]. Распределение сдвиговых напряжений в образце на момент времени, соответствующий прохождению половины длины образца в матрице с R = 7 мм, показано на рис. 20а. Согласно этим данным, наибольшие напряжения развиваются в области пересечения каналов. Таким образом, То, изменив геометрию каналов матрицы (например, уменьшив радиус внутреннего угла закругления каналов R с 7 мм до 0), можно существенно повлиять на картину гидродинамического течения материала при ДКУП [18, 73], как будет показано ниже. Сдвиговые напряжения и скорость оценивали в трех точках А, В, С, выбранных в среднем сечении образца (см. рис. 20б), точка А – ближайшая к внутреннему углу закругления каналов матрицы. На рис. 20б представлены зависимости сдвиговых напряжений от времени в исследуемых точках образца. Видно, что в верхней части образца (см. кривая А, рис. 20б) имеют место всплески напряжений с последующей крупномасштабной (на расстояниях 5−10 мм) релаксацией. В экспериментах эта релаксация проявилась в формировании в структуре меди и сплавов на основе меди системы периодически расположенных полос локализованного сдвига (см. рис. 21а, 21в). При ДКУП более хрупких материалов – латуни и титана такая релаксация происходит за счет образования не только полос сдвига, но и периодически расположенных областей разрушения - наклонных трещин (см. рис. 12) [8, 18]. Анализ экспериментальных результатов, полученных на образцах меди, показал, что при оптимальной скорости разгона образцов 230–250 м/с наибольшее влияние на дисперсность и однородность формирующейся структуры оказывает величина деформации, зависящая от количества проходов (N = 1–4) и изменение геометрии каналов матрицы, а именно радиуса закругления внутреннего угла каналов (R) от 7 мм до 0 (см. рис. 1).
Рис. 20.
Результаты моделирования процесса ДКУП на примере образца меди, подвергнутого ДКУП, N = 1 в матрице R = 7 мм: а – распределение сдвиговых напряжений на момент времени, соответствующий прохождению половины длины образца; б – зависимость сдвиговых напряжений от времени движения в исследуемых точках образца (А, В, С).
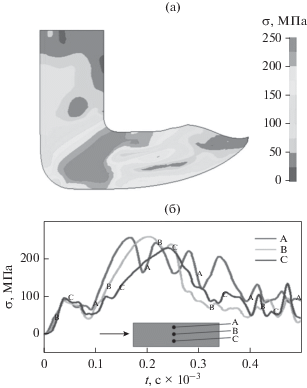
Рис. 21.
Структура образцов меди после ДКУП, N = 4 с использованием матриц с R = 7 мм (а, б) и R = 0 (в, г): а –волокнисто-полосовая и в – волокнистая структуры; б, г – зерна-субзерна внутри волокон меди; на а: 1 – волокнистая структура; 2 – широкие полосы локализованного сдвига; 3 – тонкая полосчатость; на в: стрелками белого цвета показаны гребни волн, стрелками на схеме – направления локализованных сдвигов.
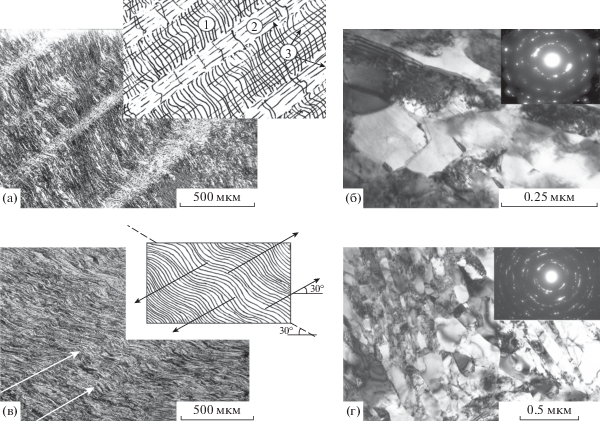
В исходном состоянии (после отжига при 450°С) средний размер зерна меди составлял 100 мкм, микротвердость – 780 МПа. После ДКУП, N = 4 в матрице с R = 7 мм, возникает волокнисто-полосовая структура (рис. 21а). Внутри полос локализованного сдвига (2) шириной 50–150 мкм и волокон (1) шириной 0.5–5.0 мкм обнаружена тонкая (1–5 мкм) полосчатость (3). Волокнистая структура (1) образовалась при 3-м проходе; полосы (2) и тонкая полосчатость (3), возникшие при 4-м проходе, располагаются под углом 30°–35° к продольной оси образца, что согласуется с результатами РКУП [3] и соответствует геометрии деформации при ДКУП [8]. Полосы (2) разделяют волокна (1) на крупные фрагменты, тонкие полосы (3) – на более дисперсные. Внутри дисперсных фрагментов волокон обнаружили зерна-субзерна размерами от 0.10 до 0.45 мкм (рис. 21б).
После ДКУП, N = 4 с R = 0, практически по всей длине образца сформировалась тонкая (0.5–1.0 мкм) волокнистая структура с необычной волнообразной формой волокон (рис. 21в). “Гребни” волн (см. стрелки) расположены под углом 30°‒35° к продольной оси образца. Внутри волокон обнаружена неравновесная смешанная СМК + НК структура, состоящая из зерен-субзерен размерами от 0.05 до 0.35 мкм (рис. 21г). Сложный дислокационный контраст в субзернах и изгибные контуры экстинкции в зернах свидетельствуют о высоком уровне внутренних напряжений, а присутствие зерен с небольшой плотностью дислокаций указывает на частичное протекание релаксационных процессов в ходе ДКУП, в том числе динамической полигонизации и динамической рекристаллизации.
Для объяснения влияния геометрии каналов на эффект измельчения структуры, был проведен анализ напряженно-деформированного состояния нагружаемых образцов [73, 74] и выполнена оценка изменения величины сдвига вдоль поперечного сечения образца при ДКУП [73]. Показано, что при нулевом значении радиуса происходит наиболее частая релаксация накапливаемых напряжений при деформировании, что может способствовать получению однородной и дисперсной структуры по всей длине образца. На основании анализа картины гидродинамического течения материала вдоль поперечного сечения образца при ДКУП, полученной на образце латуни Л63 с естественными реперными линиями – продольными цепочкам неметаллических включений, определено, что величина сдвига вдоль поперечного сечения образца при ДКУП в матрице с R = 0 составляет 1.8–2.0; и не превышает 1.6 в случае матрицы с R = 7 мм [73]. Микроструктура материалов, формирующаяся как реакция на внешнее воздействие, различается [8–18, 66, 73], но картина течения одинакова для всех материалов. Поскольку напряжения, возникающие при деформировании методом ДКУП, существенно превышают динамический предел текучести, роль материала становится незначительной, и динамика процесса определяется геометрией нагружения и энергией воздействия, то есть материал течет через каналы.
Границы зерен в образцах, полученных ДКУП, N = 4 при R = 0 (рис. 21г) были изучены методом высокоразрешающей электронной микроскопии (ВРЭМ). На рис. 22а приведено изображение участка одной из типичных неравновесных межзеренных границ и фурье-изображение, полученное с правого зерна. По данным дифракционного анализа, ориентировка правого зерна [110 ] ГЦК, левого зерна − [112 ] ГЦК. В правом зерне удалось разрешить отдельные атомные плоскости {111}ГЦК, межплоскостное расстояние составляет 0.210 нм (рис. 22а). Граница и прилегающие к ней области, в которых наблюдается искажение кристаллической решетки, содержат 5−6 атомных слоев (рис. 22а). Ранее подобные границы, содержащие высокую плотность различных дефектов: ступенек, фасеток, дислокаций, обнаружили в СМК-меди и других металлах и сплавах, полученных методами КВД и РКУП. Именно с присутствием этих дефектов связаны упругие искажения вблизи границ [3, 75]. Необходимо отметить, что неравновесные границы, сформировавшиеся при ДКУП, менее дефектны, а наблюдаемые на границах фасетки и ступеньки более упорядочены и равномерно распределены (рис. 22а), чем границы, образовавшиеся в СМК-меди при КВД и РКУП [3, 75]. Это обусловлено частичным протеканием релаксационных процессов уже в ходе ДКУП [73]. Вблизи границ и внутри зерен обнаружены участки размером 5–7 нм (показаны стрелками на рис. 22б). Одной из возможных причин их возникновения в процессе ДКУП может быть образование частиц вторых фаз либо из исходно присутствующих примесей, либо вследствие “захвата” примесей из окружающей атмосферы, как это обнаружили в технической меди 99.7 мас. % с СМК-структурой, полученной РКУП и КВД [1]. С образованием таких наночастиц вторых фаз может быть связано дополнительное упрочнение СМК + + НК-меди при статических и динамических испытаниях.
Рис. 22.
Участок межзеренной границы в СМК + НК-меди и Фурье-изображение, полученное с правого зерна (а); и внутризеренные наноучастки показаны стрелками (б); ВРЭМ.
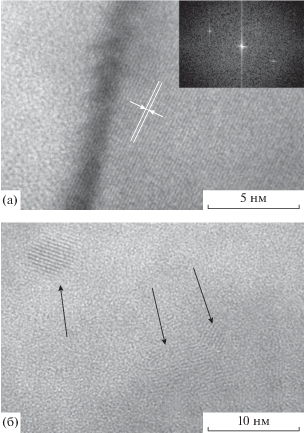
Для оценки степени однородности структур, сформированных при ДКУП, по темнопольным снимкам методом секущих был выполнен статистический анализ распределения зерен-субзерен по размерам [73]. Результаты анализа показали, что СМК-структура представляет собой субзерна размерами от 0.5 до 1.0 мкм. СМК + НК-структура состоит из зерен-субзерен размером от 0.05 до 0.40 мкм; количество кристаллитов размером 0.05–0.10 и 0.11–0.40 мкм составляет 35 и 65% соответственно, средний размер − 0.15 мкм. Кроме того, полученные структуры были изучены методом дифракции обратно рассеянных электронов. На рис. 23 а и 23г представлены EBSD-карты СМК- и СМК + НК-меди. Все зерна-субзерна окрашены согласно шкале ориентаций, соседние зерна имеют различные кристаллографические ориентировки. На рис. 23б, 23д и 23в, 23е показаны гистограммы распределения границ по углам разориентировки и зерен-субзерен по размерам.
Рис. 23.
Ориентационные EBSD-карты (а, г) и гистограммы распределения границ по углам разориентировки (б, д) и зерен по размеру (в, е) в образцах меди, после ДКУП, N = 1(а−в) и N = 4 (г−е).
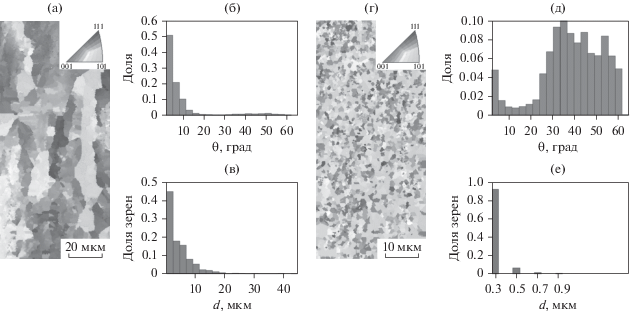
Анализ приведенных данных показал, что СМК-структура (рис. 23а), на 90–95% состоит из субзерен с МУГ (рис. 23б). Смешанная СМК + + НК-структура (рис. 23г) − на 90% из зерен с БУГ и на 10% из субзерен с МУГ (рис. 23д). Более 95% зерен-субзерен имеет размеры от 0.05 до 0.30 мкм (рис. 23е), что согласуется с результатами статистического анализа, приведенными выше.
Таким образом, при ДКУП, N = 4 в меди формируется смешанная СМК + НК-структура с неравновесными преимущественно с большеугловыми границами и средним размером зерна 0.15 мкм. Для сравнения при РКУП, N = 16 формируется СМК-структура со средним размером зерна 0.25 мкм [3].
3.2. Механические свойства СМК- и НК-меди
В табл. 3 представлены результаты измерения микротвердости и механических свойств меди с различными структурами при испытании в условиях одноосного растяжения при ɛ̇ = 10–2 с–1. Измерения выполнены на плоских образцах толщиной 2 мм и длиной 65 мм, с использованием клиновых захватов. Видно, что измельчение зерна от КК (100 мкм) до СМК (0.5−1.0 мкм)- и СМК + НК (0.05−0.40 мкм)-состояний при ДКУП приводит к увеличению микротвердости (НV) от 780 МПа до 1450 и 1560 МПа, предела текучести (σ0.2) от 304 до 362 и 414 МПа и предельного сопротивления разрушению (σB) − от 312 до 369 и 440 МПа при сохранении удовлетворительной пластичности. Для сравнения измельчение зерна меди чистотой 99.98% от КК (30 мкм) до СМК (0.2−0.3 мкм) состояния методом РКУП, N = 16 увеличивает НV от 550 до 1700 МПа, σ0.2 от 140 до 380 МПа и σB от 160 до 440 МПа [3]. Сопоставив полученные результаты с данными [3], можно заключить, что, несмотря на существенное (в 2 раза) различие прочностных характеристик КК чистой (99.98%) меди [3] и исследуемой технической (99.8%), диспергирование структуры до СМК- и СМК + НК-состояния методами РКУП и ДКУП приводит к достижению близких значений прочности.
Таблица 3.
Механические свойства меди
№ п/п | Режимы обработки и структура | НV, МПа | σ0.2, МПа | σB, МПа | δ, % |
---|---|---|---|---|---|
1 | Отжиг 450°С; КК | 780 | 304 | 312 | 37 |
2 | ДКУП, N = 1; СМК | 1450 | 362 | 369 | 22 |
3 | ДКУП, N = 4; СМК + НК | 1560 | 414 | 440 | 19 |
Исследования динамических свойств материалов в субмикросекундном диапазоне длительностей нагрузки основаны на том факте, что процессы упруго-пластического деформирования и разрушения сопряжены с изменением сжимаемости материала и проявляются в структуре плоских волн сжатия и разрежения [19]. Динамическая (откольная) прочность материалов исследуется путем регистрации так называемых “откольных явлений” при отражении импульсов одномерного ударного сжатия от свободной поверхности тела [20, 21, 51]. Для получения информации о количественных характеристиках процессов высокоскоростного деформирования и разрушения анализируемой меди было проведено ударное сжатие серии образцов размером 12 × 12 мм и толщиной ~2 мм. Максимальное давление ударного сжатия составляло 6.8ГПа, максимальная скорость деформирования в разгрузочной части волны сжатия перед откольным разрушением ɛ̇ = 2.0 × × 105 с–1. На рис. 24 приведены волновые профили образцов меди с исходной КК- (кривая 1) и СМК- и СМК + НК-структурами, полученными при ДКУП (кривые 2 и 3). На основании анализа полученных волновых профилей были определены и рассчитаны по формулам, приведенным в [20, 21, 44, 46, 51], параметры ударно-волнового нагружения: давление ударного сжатия − Pmax, скорость свободной поверхности на фронте упругого предвестника − ufsHEL, максимальная скорость свободной поверхности − ufsmax, скорость деформации перед откольным разрушением − V/V0; и характеристики прочности меди: динамический предел упругости − σHEL, динамический предел текучести − Y, откольная прочность − σsp. Значения основных параметров и характеристик представлены в табл. 4.
Рис. 24.
Профили скорости свободной поверхности образцов меди с различными кристаллическими структурами: 1 – КК, 2 – СМК и 3 – СМК + НК.
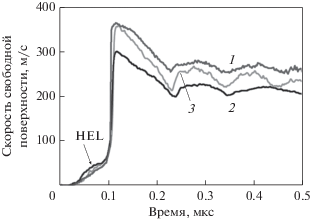
Таблица 4.
Динамические свойства меди
№ п/п | Режимы обработки и структура | σHEL, ГПа | Y, ГПа | σsp, ГПа |
---|---|---|---|---|
1 | Отжиг 450°С; КК | <0.10 | <0.05 | 1.86 |
2 | ДКУП, N = 1; СМК | 0.62 | 0.30 | 1.79 |
3 | ДКУП, N = 4; СМК + НК | 0.69 | 0.30 | 2.51 |
Из сравнения волновых профилей (рис. 24) и данных, приведенных в табл. 4, видно, что преобразование КК-структуры в СМК- и СМК + НК при ДКУП приводит к существенному изменению динамических свойств исследуемой меди. Так, динамический предел упругости увеличивается от 0.10 ГПа в КК-состоянии до 0.62 и 0.69 ГПа в СМК- и СМК + НК-состояниях, поскольку структура, сформированная при ДКУП, характеризуется наличием большого числа микродефектов, которые препятствуют движению дислокаций [76]. Динамический предел текучести возрастает от 0.05 ГПа в КК-состоянии до 0.30 ГПа в СМК- и СМК + НК-состояниях. Увеличение Y меди с СМК- и СМК + НК-структурами показывает, что упрочняющий эффект ДКУП сохраняется при скорости деформирования, соответствующей условиям ударного сжатия, как это было установлено для СМК-алюминиевых сплавов, полученных ДКУП [44, 46]. Это связано с повышенным начальным уровнем запасенной упругой энергии деформации, вследствие комбинированного действия на материалы в процессе ДКУП высокоскоростной деформации простого сдвига и ударно-волновой деформации сжатия [31, 46, 73].
Таким образом, медь с СМК- и СМК + НК-структурами, полученными ДКУП, при ɛ̇ = = (0.9−2.0) × 105 с–1 демонстрирует увеличение характеристик упруго-пластического перехода в 6 раз, по сравнению с КК медью (табл. 4). Для сравнения аналогичные характеристики меди М1 (99.9%) с СМК-структурой, полученной квазистатическими методами ВИК и РКУП, увеличиваются в 2.2 и 2.5 раза [21, 51]. Такое различие обусловлено специфическим неравновесным СМК + НК-состоянием, сформированным в меди при ДКУП в результате высокоскоростных процессов фрагментации, динамической полигонизации и динамической рекристаллизации [73, 76].
К настоящему времени надежно установлено, что все известные методы ИПД: КВД, РКУП, ВИК и др. [1, 3, 6, 38, 45, 77–81], и ДКУП [8–16] позволяют значительно увеличить статическую прочность металлов и сплавов вследствие существенного измельчения структуры до СМК- и НК-состояний. Имеющиеся в литературе сведения о влиянии размера зерна и степени дефектности структуры на динамическую (откольную) прочность и сопротивление откольному разрушению не так многочисленны и как показано ранее не столь однозначны [20, 21, 44, 46, 51].
Откольная прочность исследуемой меди изменяется немонотонно: сначала при переходе от КК- к СМК-состоянию σsp уменьшается от 1.86 до 1.79 ГПа, а затем при дальнейшем диспергировании структуры увеличивается до 2.51 ГПа (табл. 4). Незначительное уменьшение σsp связано с формированием СМК-структуры со значительной долей малоугловых границ (рис. 23а–23в) и расположением вытянутых субзерен в образце преимущественно под углом 30°–35° к направлению приложения ударной нагрузки [76]. Рост откольной прочности в 1.4 раза обусловлен образованием неравновесной смешанной СМК + НК-структуры, состоящей из сильно разориентированных зерен размерами 0.05−0.40 мкм со значительной долей БУГ (рис. 21г, рис. 23г–23е), что, по-видимому, способствует затруднению роста микротрещин.
О характере откольного разрушения нагружаемых образцов можно судить на основании анализа волновых профилей (рис. 24). Так, вид профиля КК-образца (кривая 1) свидетельствует о том, что откольное разрушение КК-меди, как и ожидалось, имеет затянутый характер, − откалывающийся поверхностный слой еще в течение длительного времени после начала разрушения остается связанным с образцом [21, 51]. Из сопоставления волновых профилей образцов с различными структурами (рис. 24) видно, что уменьшение размера зерна до субмикронного уровня не изменяет характер откольного разрушения (кривая 2). Дальнейшее измельчение до СМК + НК-состояния способствует более медленному затуханию колебаний скорости свободной поверхности образцов после начала разрушения (см. кривые 1 и 3). Для сравнения измельчение структуры меди М1 от КК- до СМК-состояния методами ВИК и РКУП либо не влияет на характер высокоскоростного разрушения [51], либо приводит к ускорению процесса разрушения [21].
Таким образом, можно отметить следующие особенности деформационного поведении меди с СМК + НК структурой, полученной ДКУП, при субмикросекундных длительностях нагрузки: возрастание характеристик упруго-пластического перехода, увеличение критического разрушающего напряжения при отколе и затягивание процесса откольного разрушения, по сравнению с КК состоянием.
3.3. Структурно-фазовые превращения в сплавах меди при ДКУП и отжигах
Известно, что легирование меди хромом и цирконием в количестве 0.5–1.0%* (здесь и далее концентрации Cr и Zr указаны в мас. %) незначительно снижая электропроводность меди, деформированной прокаткой, повышают ее прочностные свойства и увеличивают температуру рекристаллизации [82]. В последнее время появилось большое количество работ, посвященных изучению закономерностей формирования СМК-структуры при таких способах ИПД как КВД и РКУП в дисперсионно-твердеющих сплавах меди, используемых в электротехнической и атомной промышленности [78–80, 83–85]. Известно, что дополнительно прочностные и эксплуатационные характеристики этих сплавов можно повысить, выбрав оптимальные температурно-временные параметры следующего после ИПД-отжига [78, 82, 83]. Представляло интерес сравнить упрочнение и структуру меди и сплавов меди, легированных микродобавками (0.09−0.14%) хрома и (0.04−0.08%) циркония, подвергнутых ДКУП и отжигам. В исходном КК-состоянии (после закалки от 990–1000°С) размер зерна исследованных сплавов Сu−0.06% Zr, Cu−0.09% Cr−0.08% Zr и Cu−0.14% Cr−0.04% Zr составлял 200–400 мкм. После ДКУП N = 3–4 в сплавах формируется волокнисто-полосовая структура (рис. 25а), подобная наблюдаемой в меди (см. рис. 21а).
Рис. 25.
Микроструктура сплавов Cu−0.09% Cr−0.08% Zr (а–в), Cu−0.14% Cr−0.04% Zr (г) и Сu−0.06% Zr (д) после ДКУП, N = 3−4; а – металлографическое и б–д – электронно-микроскопические изображения; б, д – светлопольные и в, г– темнопольные изображения в рефлексах (002)α (в) и (111)α (г).
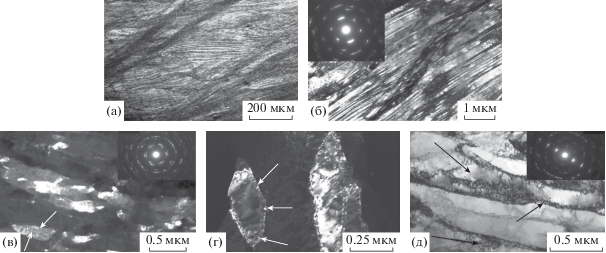
Полосы локализованного сдвига располагаются под углом ~30° к продольной оси образцов, что согласуется с данными, полученными при РКУП [3] и схемой деформации при ДКУП [8] (рис. 14). В большинстве случаев полосы локализованного сдвига содержат двойники деформации толщиной 0.05–0.10 мкм (рис. 25б), что приводит к дополнительному диспергированию структуры сплавов при ДКУП. Следует отметить, что ДКУП меди не приводило к такому развитию двойникования [73, 76].
Между полосами сдвига шириной 50–100 мкм выявлены тонкие (0.5–5 мкм) волокна (рис. 25а). Внутри тонких волокон при последовательных проходах ДКУП формируется фрагментированная СМК-структура, состоящая из субзерен с поперечным размером 0.2–0.5 мкм и внутренней дислокационной структурой (рис. 25в−25д), что свидетельствует о прохождении динамической полигонизации в процессе ДКУП. При большом увеличении на границах и внутри отдельных субзерен видны выделения частиц вторых фаз размерами до 5 нм (показаны стрелками на рис. 25в–25д), что указывает на протекание начальных стадий распада пересыщенного α-твердого раствора меди уже в процессе ДКУП. Т.е. при ДКУП исходная КК-структура сплавов преобразуется в СМК в результате высокоскоростных процессов фрагментации, динамической полигонизации и деформационного старения. В меди, как обсуждалось выше, установлен циклический характер структурообразования, обусловленный чередованием высокоскоростных процессов фрагментации, динамической полигонизации и динамической рекристаллизации [73].
Таким образом, легирование меди микродобавками Cr и Zr приводит к смене механизма формирования СМК-структуры и релаксации упругой энергии при ДКУП, что связано с процессом распада пересыщенного α-твердого раствора меди.
Отжиг при температурах 250−300°С не вызывает изменений СМК-структуры, сформированной при ДКУП. Повышение температуры отжига до 350–500°С приводит к дальнейшему распаду пересыщенного твердого раствора. Анализ данных темнопольного и дифракционного исследований микролегированного Cu–Zr [86, 87] и низколегированных Cu–Cr–Zr [15, 88] сплавов показал, что при ДКУП и ДКУП + отжигах при 350–400°С в сплавах происходит выделение наноразмерных (5−10 нм) частиц Cu5Zr. Наночастицы Cu5Zr (показаны стрелками на рис. 25в−25д, рис. 26а), выделяясь на дислокациях и границах субзерен, способствуют их закреплению и уменьшению подвижности. В результате замедляется процесс образования центров рекристаллизации, требующий перестройки дислокационной структуры.
Рис. 26.
Микроструктура сплавов Сu−0.06% Zr (а) и Cu−0.09% Cr−0.08% Zr (б, в), после ДКУП и отжига (старения) при 400 (а), 600 (б) и 700°С (в).
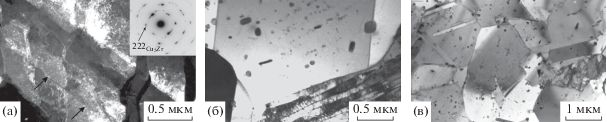
Увеличение температуры отжига (старения) до 450−500°С вызывает более полный распад твердого раствора, при этом в сплавах Cu−Cr–Zr кроме Cu5Zr выделяются частицы Cr [88, 89]. Рекристаллизация сплавов начинается при 500°С и заканчивается при 600−650°С. При повышении температуры нагрева до 600−700°С частицы Cr увеличиваются в размерах до 100 нм и зачастую приобретают вытянутую форму [15, 88, 89], глобулярные частицы Cu5Zr практически не растут – их размер не превышает 10 нм (рис. 26б). В результате в сплавах Cu−Cr–Zr формируется микроструктура с размером зерна 1−5 мкм, содержащая большое количество наночастиц Cr и Cu5Zr (рис. 26в).
3.4. Микротвердость, механические свойства и электропроводность СМК Cu сплавов
Микротвердость сплавов Cu–Zr и Cu–Cr–Zr в исходном закаленном КК-состоянии равна 600 и 680 МПа соответственно. После ДКУП микротвердость повысилась до 1430 и 1600 МПа (рис. 27, кривые 1–3), т.е., увеличилась в 2.3–2.4 раза по сравнению с исходной, что связано с существенным, на три порядка, измельчением структуры и деформационным старением сплавов уже в процессе ДКУП (рис. 25в–25д). Заметим, что микротвердость меди в результате ДКУП увеличилась в 1.8–2.0 раза (см. табл. 3).
Рис. 27.
Зависимости микротвердости меди и сплавов меди, подвергнутых ДКУП, от температуры отжига (старения), выдержка 1 ч: 1 – Cu–0.09% Cr–0.08% Zr; 2 – Cu–0.14% Cr–0.04% Zr; 3 – Сu–0.06% Zr; 4 – Cu (99.8%).
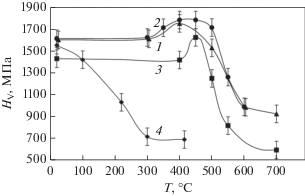
Отжиг СМК-сплавов Cu–Cr–Zr при 300°С, 1 ч (а сплава Cu–Zr и при 400°С, 1 ч) не приводит к изменению микротвердости. Ее рост отмечен при температурах отжига 400 и 450°С, 1 ч: так для сплавов Cu–Cr–Zr на 150–180 МПа и для сплава Cu–Zr на 200 МПа по сравнению с микротвердость в деформированном состоянии (рис. 27, кривые 1, 2 и 3). Это связано, как обсуждалось выше, с процессами распада пересыщенного α‑твердого раствора меди.
Отжиг при температурах 500–600°С приводит к снижению микротвердости (рис. 27, кривые 1–3) что обусловлено развитием процесса рекристаллизации (рис. 26б, 26в). Заметим, что СМК + НК медь разупрочняется при нагреве весьма существенно уже в интервале 100–300°С (рис. 27, кривая 4). Это обусловлено развитием релаксационных процессов возврата (при 100–150°С), рекристаллизации (150–220°С) и переходу меди в крупнозернистое состояние (300–400°С) [15].
Увеличение времени выдержки при 400–450°С до 4 ч, согласно данным [82], может повысить упрочнение сплавов меди, деформированных прокаткой. Действительно, изменение длительности отжига (старения) при 400°С с 1 до 4 ч увеличило микротвердость СМК сплава Cu–0.14% Cr–0.04% Zr от 1780 до 1880 МПа. Таким образом, комбинированная обработка: ДКУП + + отжиг 400–450°C,1 и 4 ч существенно (в 2.7–2.8 раза) увеличивает микротвердость исследованных микро- и низколегированных сплавов, по сравнению с исходным закаленным состоянием.
В табл. 5 представлены механические свойства сплава Cu–0.14% Cr–0.04% Zr после различных обработок. Как и ожидалось, высокоскоростное деформирование методом ДКУП существенно (в 2.6–3.3 раза) повышает прочностные характеристики сплава: предел прочности увеличивается от 196 МПа в исходном КК до 507 МПа после ДКУП; предел текучести возрастает от 94 МПа до 312 МПа, при этом относительное удлинение составляет 10%. Для сравнения, прочностные характеритики меди после аналогичной обработки увеличились в 1.2–1.4 раза (см. табл. 3).
Таблица 5.
Механические свойства сплава Cu–Cr–Zr
№ п/п | Режимы обработки | σ0.2, МПа | σВ, МПа | δ, % |
---|---|---|---|---|
1 | Закалка 1000°С | 94 | 196 | 37 |
2 | Закалка + 450°С, 1 ч | 139 | 237 | 18 |
3 | Закалка + ДКУП, N = 4 | 312 | 507 | 10 |
4 | ДКУП + 400°С, 1 ч | 464 | 542 | 10 |
5 | ДКУП + 400°С, 4 ч | 464 | 536 | 13 |
6 | ДКУП + 450°С, 1 ч | 477 | 520 | 11 |
Еще более существенно, в 2.8–5.1 раз, возрастают прочностные свойства СМК-сплава после старения при 400–450°С (табл. 5). Таким образом, за счет комбинированной обработки: ДКУП, N = 4 + 400°С, 4 ч можно получить образец сплава с высокой твердостью – 1880 МПа и характеристиками прочности (σB = 536 МПа, σ0.2 = 464 МПа) при сохранении удовлетворительной пластичности – δ = 13% (табл. 5), подобные результаты невозможно достичь при деформации прокаткой [82]. Заметим, что для достижения такого уровня свойств в более легированном сплаве Cu–0.50% Cr–0.12% Ag понадобилось 8 проходов РКУП [84].
Электропроводность сплава Cu–0.14.% Cr–0.04.% Zr в закаленном состоянии составляет 40% IACS (рис. 28а, кривая 1). Снижение электропроводности меди, легированной микродобавками хрома и циркония, в закаленном КК состоянии связано с тем, что при образовании α-твердого раствора, то есть размещении в пространственной решетке меди атомов хрома и циркония, электрическое поле решетки растворителя-меди искажается, и рассеяние электронов проводимости увеличивается [82, 90].
Рис. 28.
Влияние температуры старения на электропроводность (а) и микротвердость (б) сплава Cu–0.14% Cr–0.04% Zr после закалки от 1000°С (1) и ДКУП (2).
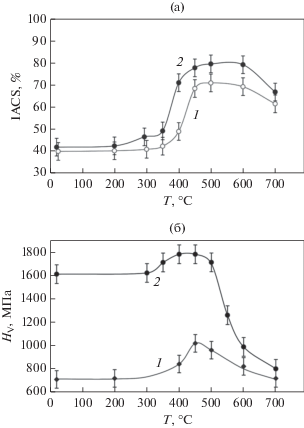
Высокоскоростная деформация несколько повышает электропроводность сплава по сравнению с закаленным состоянием (см. кривые 1 и 2 на рис. 28а). Это связано с распадом пересыщенного α-твердого раствора меди уже в процессе ДКУП, что подтверждается структурными наблюдениями, а также результатами механических испытаний.
Электропроводность закаленного сплава практически не изменяется при нагреве до 300°С и возрастает от 43 до 70% IACS при отжиге в интервале температур 350–500°С (рис. 28а, кривая 1), что обусловлено распадом пересыщенного α-твердого раствора. Электропроводность СМК-сплава, полученного ДКУП, не изменяется до 200°С, а затем в интервале 200–350°С начинает увеличиваться (рис. 28а, кривая 2), что связано с процессами возврата, и существенно увеличивается от 48 до 80% IACS в интервале температур 350–500°С (рис. 28а, кривая 2), что обусловлено распадом твердого раствора с выделением наноразмерных частиц вторых фаз, как обсуждалось выше. Следует отметить, что рост электропроводности СМК-сплава начинается при более низкой температуре отжига, чем сплава в КК состоянии, поскольку процесс распада пересыщенного твердого раствора после ДКУП происходит интенсивнее. Увеличение электропроводности происходит при более низкой температуре, чем температура, при которой начинается рост микротвердости. Это означает, что обеднение твердого раствора легирующими элементами происходит раньше, чем формируются частицы вторых фаз оптимального размера, необходимые для повышения микротвердости.
Поскольку низколегированные сплавы Cu–Cr–Zr используются для электродов машин контактной сварки, представляло интерес методами микродюрометрии и кинетического микроиндентирования провести измерения твердости, удельной контактной твердости и величины упругого восстановления СМК-сплавов, а также сравнить полученные результаты с аналогичными характеристиками СМК + НК-меди [15]. Показано, что деформирование меди методом ДКУП обеспечивает увеличение твердости по Виккерсу, Мартенсу и твердости вдавливания в 1.4–1.5 раза по сравнению с твердостью в исходном крупнокристаллическом состоянии. Более значительный рост указанных характеристик прочности (в 2.4–2.8 раза) достигается в СМК сплавах, полученных ДКУП [15]. Как уже обсуждалось выше, исследование структуры показало, что существенное упрочнение СМК-сплавов, по сравнению с СМК + НК- медью, обусловлено выделением в сплавах наноразмерных (≤5 нм) частиц вторых фаз уже в процессе ДКУП (см. рис. 25в–25д).
Таким образом, установлена повышенная способность СМК + НК-меди и, особенно, СМК-дисперсионно-твердеющих низколегированных сплавов выдерживать механические контактные нагрузки без пластического деформирования по сравнению с исходным крупнокристаллическим состоянием.
В [91] показано, что повышенное сопротивление деформированных материалов с НК поверхностью пластическому деформированию при контактном нагружении обеспечивает высокое сопротивление таких материалов различным видам изнашивания. Следовательно, можно ожидать положительного влияния обработки ДКУП не только на прочностные характеристики материалов, но и на их износостойкость, что важно для практического применения исследуемых материалов.
3.5. Формирование НК структуры трения в СМК сплаве меди
Сведения о влиянии ИПД и старения на эксплуатационные, в том числе и трибологические, свойства СМК Cu–Cr–Zr сплавов немногочисленны [78–80]. Известно, что достигаемая при ИПД трением степень деформации материала поверхностного слоя сталей и сплавов существенно выше, чем в случае применения методов объемного деформирования. При этом в материалах формируется НК- структура трения, возникновение которой свидетельствует о том, что в условиях фрикционного воздействия в тонком (толщиной до 10 мкм) поверхностном слое металлических материалов реализуются экстремально большие величины пластической деформации [91, 92].
Трибологические испытания проводили в условиях трения скольжения по схеме – пластина (образец) – цилиндрический индентор из сплава ВК-8 диаметром 4 мм, высотой 4 мм на экспериментальной установке [91, 92]. Трение осуществлялось в воздушной среде без смазки при нагрузке 196 Н и скорости скольжения 0.014 м/с; число циклов (двойных ходов индентора) составляло 1000, путь трения – 9 м. В процессе истирания непрерывно измеряли и регистрировали силу трения. Коэффициент трения f определяли, как отношение средних (за время испытания) интегральных значений силы трения к нормальной нагрузке. Погрешность измерений f составляла ±5%. Интенсивность изнашивания Ih рассчитывали по формуле
где ΔQ – потеря массы образца, ρ – плотность, s – геометрическая площадь контакта, l – путь трения.В исходном закаленном КК-состоянии значения интенсивности изнашивания и коэффициента трения сплава Cu–0.09% Cr–0.08% Zr составляли 3.1 × 10–7 и 0.5, соответственно. После ДКУП, N = 3 значение Ih СМК-сплава понизилось до 2.3 × 10–7, что в 1.4 раза меньше интенсивности изнашивания сплава в КК-состоянии, а f – увеличилось до 0.62. Старение при 400°С, 1ч приводит к незначительному повышению Ih СМК-сплава по сравнению с ДКУП состоянием. При этом f понижается и достигает своего минимального значения – 0.35 [93].
Дифракционный и темнопольный анализ структуры поверхностного слоя показал, что ИПД трением сплава с объемной СМК-структурой, сформированной методом ДКУП, приводит к образованию в материале поверхностного слоя НК структуры с размером кристаллитов 40–50 нм (рис. 29а). О формировании НК-структуры свидетельствует наличие на электронограмме колец с большим количеством точечных рефлексов, принадлежащих ГЦК-медной матрице (рис. 29a). Такое диспергирование структуры закономерно приводит к увеличению микротвердости сплава (до 3200 МПа), т.е. к упрочнению в 2 раза материала поверхностного слоя, по сравнению с упрочнением, достигнутым при ДКУП (1600 МПа) [93].
Рис. 29.
НК структура, полученная при ИПД трением скольжения в сплаве Cu–0.09% Cr–0.08% Zr, подвергнутом ДКУП (a) и ДКУП и старению при 400°С, 1 ч (б); темнопольные изображения в рефлексе (111)α.
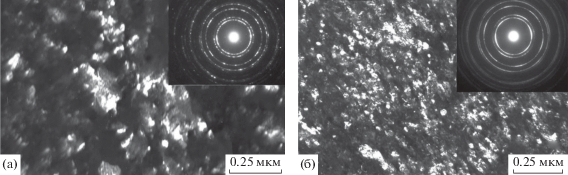
Таким образом, СМК-структура, сформировавшаяся при ДКУП, после ИПД трением преобразуется в НК-структуру с высокой твердостью [94]. На рис. 29б представлена структура материала поверхностного слоя, полученная в сплаве после комбинированной обработки: ДКУП + старение при 400°С + ИПД трением. Видно, что такая обработка приводит к еще большему диспергированию структуры поверхностного слоя по сравнению с обработкой ДКУП+ИПД трением. Размер кристаллитов уменьшается от 40–50 до 15–30 нм [94]. Микротвердость сплава после ДКУП и отжига при 400° составляет 1800 МПа (см. рис. 27, кривая 1). После ИПД трением микротвердость повышается до 3350 МПа. Т.е. комбинированная обработка ДКУП + 400°С + ИПД трением приводит к дополнительному упрочнению материала поверхностного слоя – микротвердость увеличивается в 5 раз по сравнению с микротвердостью сплава в исходном КК-состоянии.
Интенсивность изнашивания образцов с СМК-структурой, полученной при ДКУП, понижается в 1.4 раза по сравнению с КК-состоянием [93].
Таким образом, изучено влияние высокоскоростной (105 с–1) деформации методом ДКУП и комбинированной обработки, включающей ДКУП, отжиг при 400°С и ИПД трением скольжения на эволюцию структуры и свойств дисперсионно-твердеющих сплавов на основе системы Cu–Cr–Zr.
Показано, что легирование меди микродобавками хрома (0.09–0.14%) и циркония (0.04–0.08%) приводит к смене механизма формирования СМК-структуры и релаксации упругой энергии при ДКУП: циклический характер структурообразования, обусловленный чередованием высокоскоростных процессов фрагментации и динамической рекристаллизации, сменяется процессами фрагментации и деформационного старения с выделением наноразмерных частиц вторых фаз.
Определен температурно-временной режим отжига (старения) сплавов Cu–Cr–Zr с СМК-структурой, сформированной методом ДКУП, для улучшения механических свойств и повышения электропроводности. В частности, для СМК-сплава Cu–0.14% Cr–0.04% Zr, показано, что оптимальное сочетание микротвердости (HV = 1880 МПа), электропроводности (80%IACS), прочности (σ0.2 = = 464 МПа, σB = 542 МПа) и пластичности, было получено при обработке, включающей ДКУП и отжиг при 400°С, 1 ч. Повышенный по сравнению с медью уровень механических свойств сплавов связан с дополнительным упрочнением, обусловленным выделением наноразмерных (5–10 нм) частиц Cu5Zr и Cr в процессе ДКУП и старения.
Определено, что экономно-легированные сплавы Cu–Cr–Zr обладают высокой способностью к упрочнению методами ДКУП и ИПД трением скольжения. На примере сплава Cu–0.09% Cr–0.08% Zr определено, что интенсивность изнашивания образцов с СМК структурой, полученной при ДКУП, понижается в 1.4 раза по сравнению с КК состоянием.
Установлено, что комбинированная обработка по схеме: ДКУП + отжиг при 400°С + ИПД трением скольжения приводит к формированию в материале поверхностного слоя НК структуры трения с размером кристаллитов 15–30 нм, что обеспечивает высокий уровень твердости (HV = = 3350 МПа) и низкое значение коэффициента трения (f = 0.35) при сохранении удовлетворительной интенсивности изнашивания.
ЗАКЛЮЧЕНИЕ
Изучена эволюция структуры и физико-механических характеристик конструкционных цветных металлов и сплавов при ударно-волновом нагружении и высокоскоростной деформации. Определены механизмы измельчения структуры и деформационного упрочнения сплавов при комплексном воздействии ударно-волнового нагружения и высокоскоростной (105 с–1) сдвиговой деформации в процессе ДКУП. Подробно описаны экспериментальные данные о формировании методом ДКУП СМК-алюминиевых сплавов разного состава. Выделены две группы сплавов в зависимости от степени легирования матрицы: термически неупрочняемые Al–Mg–Mn (А 5083) и Al–Mn (А3003) сплавы со слабым твердорастворным упрочнением и термически упрочняемый Al–Zn–Mg–Cu (А7075) сплав c дисперсионным и сильным твердорастворным упрочнением. Установлено, что уже после однопроходного прессования происходит резкое измельчение структуры до 200–600 нм, а преимущественным механизмом формирования СМК-структуры является фрагментация. Основными характеристиками фрагментированной структуры в многокомпонентных термически упрочняемых сплавах являются кристаллиты, окруженные размытыми БУГ, высокий уровень внутренних напряжений, плотность дислокаций >1015 м–2 и высокая твердость. По мере увеличения накопленной деформации дислокационный ансамбль претерпевает эволюцию, активизируются коллективные моды деформации, в результате образуются устойчивые мезодефекты – дисклинации, и фрагментированная структура с БУГ стабилизируется. В менее легированных Al сплавах иерархия эволюции структуры по мере накопления деформации более сложная, важную роль приобретают релаксационные процессы, и образуется смешанная структура, в которой сосуществуют деформационные фрагменты с МУГ и БУГ и динамически рекристаллизованные зерна. Плотность дислокаций в такой структуре на порядок меньше, а распределение зерен по размерам часто носит бимодальный характер. На примере сплава А3003 установлено, что именно такая модель структурообразования обеспечивает наилучшее соотношение прочностных и пластических свойств.
Представлены результаты исследования деформационного поведения, микроструктуры и свойств титана при ДКУП по различным режимам. В частности, рассмотрено влияние температуры на эффекты локализации деформации и структурные изменения в титане. Установлено, что после ДКУП при комнатной температуре в материале образуются трещины, и формируется неравномерная деформированная структура с полосами адиабатического сдвига, состоящими из рекристаллизованных зерен. Механизмами деформации являются двойникование и призматическое скольжение. С ростом температуры ДКУП до 450–500°С трещины и полосы адиабатического сдвига отсутствуют, а структура состоит из деформированных и рекристаллизованных зерен. Механизм деформации – множественное скольжение (призматическое и пирамидальное). Получены результаты о влиянии комбинированной деформационной обработки (ДКУП и последующей прокатки) на структуру и механические свойства титана. Установлено, что после комбинированной обработки и отжига для снятия напряжений материал имеет высокие прочностные и пластические свойства: σ0.2 = 630 МПа, σВ = 790 МПа, δ = 15%.
Показано, что структурообразование в меди при высокоскоростном деформировании происходит за счет закономерно повторяющихся процессов фрагментации, динамической полигонизации и динамической рекристаллизации, в сплавах на основе меди протекают процессы фрагментации, динамической полигонизации и частичного деформационного старения с выделением наноразмерных (~5 нм) частиц вторых фаз. Обнаружено, что измельчение структуры этих материалов на три порядка (от 100–200 до 0.1–0.2 мкм), и повышение характеристик прочности в 1.4 и 2.8 раза при сохранении удовлетворительной пластичности может быть достигнуто уже при трех–четырех проходах ДКУП. Определено, что медь и сплавы меди с СМК- и НК-структурой, полученной методом ДКУП, обладают повышенной по сравнению с КК-состоянием способностью выдерживать контактные механические нагрузки без пластического деформирования.
На основании сравнения экспериментальных данных, полученных для Al, Cu и их сплавов, выявлено влияние энергии дефектов упаковки ГЦК-материалов на механизмы деформации и сценарии формирования СМК-структур при ДКУП, а на примере титана показано их отличие от материалов с ГПУ-кристаллической решеткой. Так в Al и его сплавах с высокой энергией дефекта упаковки (135–200 мДж/м2) основным механизмом высокоскоростной деформации является множественное скольжение, а в Cu и в Сu сплавах с низкой энергией дефекта упаковки (60–70 мДж/м2) к скольжению добавляется двойникование, роль которого повышается при деформировании сплавов. Важно подчеркнуть, что более интенсивные процессы деформирования ГЦК-материалов и измельчения их структуры при ДКУП (относительно квазистатических методов ИПД) обусловлены повышением количества вакансий и ускорением кинетики движения дислокаций при ударно-волновом нагружении. Сценарии формирования разнообразных СМК- и НК-структур зависят от структурно-фазовых превращений, протекающих в сплавах до и в процессе ДКУП.
Исследованы механические свойства алюминиевых и медных сплавов при статических и динамических нагрузках в широком интервале скоростей деформации ɛ̇ = 10–3–105 с–1. Приведены сравнительные результаты исследования механического поведения СМК сплавов при статических испытаниях, динамическом сжатии по методу Гопкинсона–Кольского и при воздействии плоских ударных волн. Показано, что предел прочности и условный предел текучести СМК-меди и термически неупрочняемых алюминиевых сплавов, полученных ДКУП, возрастают в 1.5–2.0 раза. Прочностные характеристики СМК сплавов меди с хромом и цирконием после ДКУП и термической обработки увеличиваются в 2.8 и 5.1 раза, по сравнению с КК-аналогами, при сохранении удовлетворительной пластичности.
Впервые измерены динамические прочностные характеристики (динамический предел упругости σHEL, динамический предел текучести Y, откольная прочность σsp) СМК-металлов и сплавов, полученных ДКУП, при нагружении плоскими ударными волнами со скоростью 105 с–1. Так, σHEL и Y СМК- и НК-меди в 6 раз, а СМК-сплавов меди в 1.9–2.8 раза выше, чем у КК аналогов. Динамические свойства СМК-алюминиевых сплавов увеличиваются в 1.5–2.0 раза. Откольная прочность Al сплавов сохраняется на уровне свойств КК-аналогов (1.32–1.36 ГПа), а σsp СМК-Cu и сплавов – в 1.3–1.4 раз выше.
Полученные экспериментальные данные о прочностных свойствах и характере откольного разрушения СМК-металлов и сплавов при ударно-волновом сжатии и выявленные особенности эволюции структуры и свойств при ДКУП позволяют прогнозировать поведение конструкционных материалов в экстремальных условиях эксплуатации.
Авторы выражают признательность за проведение экспериментов и участие в исследованиях Е.В. Шорохову, А.Н. Петровой, Н.Ю. Фроловой, А.Э. Хейфецу, И.Г. Ширинкиной, С.В. Разоренову, О.А. Плехову, Л.Г. Коршунову, Д.Н. Абдуллиной, Т.И. Яблонских и В.В. Астафьеву.
Электронно-микроскопические исследования проведены на оборудовании ЦКП “Испытательный центр нанотехнологий и перспективных материалов” ИФМ УрО РАН”.
Работа выполнена в рамках государственного задания МИНОБРНАУКИ России по теме “Структура”, № АААА-А18-118020190116-6.
Список литературы
Козлов Э.В., Глезер А.М., Конева Н.А., Попова Н.А., Курзина И.А. Основы пластической деформации наноструктурных материалов. М.: Физматлит, 2016. 304 с.
Рыбин В.В. Большие пластические деформации и разрушение металлов. М.: Металлургия, 1986. 224 с.
Валиев Р.З., Александров И.В. Объемные наноструктурные металлические материалы: получение, структура, свойства М.: ИКЦ Академкнига, 2007. 398 с.
Langdon T.G. The principles of grain refinement in equal-channel angular pressing // Mater. Sci. Eng. A. 2007. V. 462. P. 3–11.
Zehetbauer M.J., Valiev R.Z. Nanomaterials by severe plastic deformation. Weinheim, Germany: Wiely-VCH, 2004. 875 p.
Estrin Y., Vinogradov A. Extreme grain refinement by severe plastic deformation: a wealth of challenging science // Acta Mater. 2013. V. 61. P. 782–817.
Шорохов Е.В., Жгилев И.Н., Валиев Р.З. Способ динамической обработки материалов. Пат. 2283717 Российская Федерация, МПК51 B 21 J 5/04, B 21 C 23/18, C 21 D 7/02. Опубл. 27.04.06, Бюл. № 26. 64 с.
Зельдович В.И., Шорохов Е.В., Фролова Н.Ю., Жгилев И.Н., Хейфец А.Э., Хомская И.В., Гундырев В.М. Высокоскоростная деформация титана при динамическом канально-угловом прессовании // ФММ 2008. Т. 105. № 4. С. 431–437.
Brodova I.G., Shirinkina I.G., Antonova O.V., Shorokhov E.V., Zhgilev I.I. Formation of a submicro-crystalline structure upon dynamic deformation of aluminum alloys // Mater. Sci. Eng. A. 2009. V. 503. P. 103–105.
Хомская И.В., Зельдович В.И., Фролова Н.Ю., Шорохов Е.В., Жгилев И.Н., Хейфец А.Э. Электронно-микроскопическое исследование деформационного поведения и структуры меди после динамического канально-углового прессования // Хим. физика. 2007. Т. 26. № 12. С. 64–68.
Шоpохов Е.В., Жгилев И.Н., Хомская И.В., Бpодова И.Г., Зельдович В.И., Гундеpов Д.В., Фpолова Н.Ю., Гуpов А.А., Оглезнева Н.П., Шиpинкина И.Г., Хейфец А.Э., Астафьев В.В. Высокоскоростное деформирование металлических материалов методом канально-углового прессования для получения ультрамелкозернистой структуры // Деформация и разрушение материалов. 2009. № 2. С. 36–41.
Brodova I.G., Shorokhov E.V., Petrova A.N., Shirinkina I.G., Minaev I.V., Zhgilev I.N., Abramov A.V. Fragmentation of the structure in Al-based alloys upon high speed effect // Rev. on Adv. Mater. Sci. 2010. V. 25. P. 128–135.
Зельдович В.И., Шорохов Е.В., Добаткин С.В., Фролова Н.Ю., Хейфец А.Э., Хомская И.В., Насонов П.А., Ушаков А.А. Структура и механические свойства титана, подвергнутого высокоскоростному канально-угловому прессованию и деформации прокаткой // ФММ. 2011. Т. 111. № 4. С. 439–447.
Зельдович В.И., Добаткин С.В., Фролова Н.Ю., Хомская И.В., Хейфец А.Э., Шорохов Е.В., Насонов П.А. Механические свойства и структура хромоциркониевой бронзы после динамического канально-углового прессования и последующего старения // ФММ. 2016. Т. 117. № 1. С. 79–87.
Хомская И.В., Зельдович В.И., Макаров А.В., Хейфец А.Э., Фролова Н.Ю., Шорохов Е.В. Исследование структуры, физико-механических свойств и термической стабильности наноструктурированных меди и бронзы, полученных методом ДКУП // Письма о материалах. 2013. Т. 3. № 2. С. 150–154.
Ширинкина И.Г., Бродова И.Г. Исследование термической стабильности субмикрокристаллического алюминиевого сплава, полученного высокоскоростным деформированием // Деформация и разрушение материалов. 2016. № 12. С. 27–33.
Brodova I.G., Petrova A.N., Naimark O.B., Plekhov O.A., Razorenov S.V., Shorokhov E.V. The influence of the structure of ultrafine-grained aluminium alloys on their mechanical properties under dynamic compression and shock-wave loading // J. Phys.: Conf. Series. 2017. V. 894. P. 12016–12025.
Хомская И.В., Шорохов Е.В., Зельдович В.И., Хейфец А.Э., Фролова Н.Ю., Минаев И.В., Абрамов А.В. Применение динамического канально-углового прессования для получения наноструктурированных меди и латуни // Деформация и разрушение материалов. 2012. № 1. С. 17–24.
Канель Г.И., Разоренов С.В., Уткин А.В., Фортов В.Е. Ударно-волновые явления в конденсированных средах. М.: Янус-К, 1996. 408 с.
Канель Г.И., Разоренов С.В., Фортов В.Е. Субмикросекундная прочность материалов // Изв. РАН. МТТ. 2005. № 4. С. 86–111.
Гаркушин Г.В., Игнатова О.Н., Канель Г.И., Мейер Л., Разоренов С.В. Субмикросекундная прочность ультрамелкозернистых материалов // МТТ. 2010. № 4. С. 155−163.
Разоренов С.В., Гаркушин Г.Н. Упрочнение металлов и сплавов при ударном сжатии // ЖТФ. 2015. Т. 85. № 7. С. 77−82.
Kolsky H. An investigation of the mechanical properties of material at very high rates of loading //Proceed. Phys. Society (London). 1949. V. 62B. P. 676–700.
Плехов О.А., Чудинов В., Леонтьев В., Наймарк О.Б. Экспериментальное исследование закономерностей диссипации энергии при динамическом деформировании нанокристаллического титана // Письма в ЖТФ. 2009. Т. 35. № 2. С. 82–89.
Marsh S.P. LASL Shock Hugoniot Data. Berkeley: University of California Press, 1980. 658 p.
Antoun T., Seaman L., Curran D.R., Kanel G.I., Razorenov S.V., Utkin A.V. Spall Fracture. New York: Springer, 2003. 404 p.
Razorenov S.V. Influence of structural factors on the strength properties of aluminum alloys under shock wave loading // Matter and Radiation at Exstremes. 2018. V. 3. № 145. P. 1–54.
Barker L.M., Hollenbach R.E. Laser interferometry for measuring high velocities of any reflecting surface // J. Appl. Phys. 1972. V. 43. № 11. P. 4669–4675.
Альтман М.Б., Амбарцумян С.М., Аристова Н.А. Арчакова З.Н. Промышленные деформируемые, спеченные и литейные алюминиевые сплавы. М.: Металлургия, 1972. 552 с.
Бродова И.Г., Ширинкина И.Г., Петрова А.Н., Антонова О.В., Пилюгин В.П. Эволюция структуры алюминиевого сплава В95 при сдвиге под давлением // ФММ. 2011. Т. 111. № 6. С. 659–667.
Петрова А.Н., Бродова И.Г., Шорохов Е.В. Измельчение структуры Al–Mg–Mn сплава методом динамического канально-углового прессования // Перспективные материалы. 2015. № 12. С. 72–77.
Valiev R.Z., Murashkin M.Y., Bobruk E.V., Raab G.I. Grain refinement and mechanical behavior of the Al alloy, subjected to the new SPD technique // Mater. Trans. 2009. V. 50. P. 87–91.
Markushev M.V., Murashkin M.Yu. Structure and mechanical properties of commercial Al–Mg 1560 alloy after equal-channel angular extrusion and annealing // Mater. Sci. Eng. A. 2004. V. 367. P. 234–242.
Фортов В.Е. Экстремальные состояния вещества. М.: Физмат, 2009. 303 с.
Зельдович Я.Б., Райзер Ю.П. Физика ударных волн и высокотемпературных гидродинамических явлений. М.: Наука, 1966. 600 с.
Иванова В.С., Гордиенко Л.К., Геминов В.Н. Роль дислокаций в упрочнении и разрушении металлов. М.: Наука. 1965. 180 с.
Быков В.М., Лихачев В.А., Никонов Ю.А. Сербина Л.Л. Шибалова Л.И. Фрагментирование и динамическая рекристаллизиция в меди при больших и очень больших пластических деформациях. // ФММ. 1978. Т. 45. № 1. С. 163–169.
Valiev R.Z., Estrin Y., Horita Z., Langdon T.G., Zehetbauer M.J., Zhu Y.T. Producing bulk ultrafine-grained materials by severe plastic deformation // J. The Minerals Met. and Mater. Society. 2006. V. 58. № 4. P. 33–38.
Zhao Y.H., Jin Z., Liao X.Z., Valiev R.Z., Zhu Y.T. Microstructures and mechanical properties of ultrafine grained 7075 Al alloy processed by ECAP and their evolutions during annealing // Acta Mater. 2004. V. 52. P. 4589–4599.
Islamgaliev R.K., Yanusova N.F., Sabirov I.N., Sergueeva A.V., Valiev R.Z. Deformation behavior of nanosrructured aluminum alloy processed by severe plastic deformation // Mater. Sci. Eng. A. 2001. V. 319–321. P. 874–878.
Park Y.S., Chung K.H., Kim N.J. Lavernia E.J. Microstructural investigation of nanocrystalline bulk Al–Mg alloy fabricated by cryomilling and extrusion // Mater. Sci. Eng. A. 2004. V. 374. P. 211–216.
Wang Y., Chen M., Zhou F. et al. High tensile ductility in a nanostructured metal // Acta Mater. 2004. V. 52. P. 1699–1709.
Петрова А.Н., Бродова И.Г., Плехов О.А., Наймарк О.Б., Шорохов Е.В. Механические свойства и особенности диссипации энергии в ультрамелкозернистых алюминиевых сплавах АМЦ и В 95 при динамическом сжатии // ЖТФ. 2014. Т. 84. № 7. С. 44–51.
Brodova I.G., Petrova A.N. Dynamic properties of submicrocrystallinealuminum alloys // Phys. Met. Metallogr.2018. V. 119. P. 1342–1345.
Valiev R.Z., Kozlov E.V., Ivanov Yu.F., Lian J., Nazarov A.A., Baudelet B. Deformation behavior of ultra-fine-grained copper // Acta Metallur. Mater. 1994. V. 42. P. 2467–2475.
Бродова И.Г., Петрова А.Н., Разоренов С.В., Шорохов Е.В. Сопротивление высокоскоростному деформированию и разрушению субмикрокристаллических алюминиевых сплавов после динамического канально-углового прессования // ФММ. 2015. Т. 116. № 5. С. 548–556.
Петрова А.Н., Бродова И.Г., Разоренов С.В. Прочностные свойства и структура субмикрокристаллического Al–Mg–Mn сплава в условиях ударного сжатия // ФММ. 2017. Т. 118. № 6. С. 632–638.
Разоренов С.В., Канель Г.И., Гаркушин Г.Н. Сопротивление динамическому деформированию и разрушению тантала с различной зеренной и дефектной структурой // ФТТ. 2012. Т. 54. № 4. С. 742–749.
Канель Г.И., Разоренов С.В., Савиных В.С., Зарецкий Е.Б., Колобов Ю.Р. Исследование структурных уровней, определяющих сопротивление деформированию и разрушению металлов и сплавов. М.: ОИВТ РАН, 2004. 31 с.
Гаркушин Г.В., Разоренов С.В., Канель Г.И. Влияние структурных факторов на субмикросекундную прочность алюминиевого сплава Д16Т // ЖТФ. 2008. Т. 78. № 11. С. 53–59.
Гаркушин Г.В., Иванчихина Г.Е., Игнатова О.Н., Каганова И.И., Малышев А.Н., Подурец А.М., Раевский В.А., Разоренов С.В., Скоков В.И., Тюпанова О.А. Механические свойства меди М1 до и после ударного сжатия в широком диапазоне длительности нагрузки // ФММ. 2011. Т. 111. № 2. С. 203–212.
Разоренов С.В., Канель Г.И., Фортов В.Е. Субмикросекундная прочность алюминия и сплава АМг6М при нормальной и повышенных температурах // ФММ. 2003. Т. 95. № 1. С. 91–96.
Валиев Р.З., Семенова И.П., Латыш В.В., Щербаков А.В. Наноструктурный титан для биомедицинских применений: новые разработки и перспективы коммерциализации // Российские нанотехнологии. 2008. Т. 3. № 9–10. С. 80–89.
Якушина Е.Б., Семенова И.П., Валиев Р.З. Наноструктурный титан для биомедицинских применений // Цветные металлы. 2010. № 7. С. 81–83.
Shorokhov E.V., Zhgiliev I.N., Gunderov D.V., Gurov A.A. Dynamic deformation of titanium for producing ultrafine-grained structure // Proceeding of Intern. conference “Shock waves in condensed matter”. St-Petersburg, 2006. P. 281–283.
Agnew S.R., Mehrotra P., Lillo T.M., Stoica G.M., Liaw P.K. Texture evolution of five wrought magnesium alloys during route A equal channel angular extrusion: Experiments and simulations // Acta Mater. 2005. V. 53. P. 3135–3146.
Сегал В.М., Резников В.И., Дробышевский А.Е., Копылов В.И. Пластическая обработка металлов простым сдвигом // Изв. АН СССР, Металлы.1981. № 1. С. 115–123.
Цвиккер У. Титан и его сплавы. М.: Металлургия, 1979. 511 с. (Springer-Verlag, 1974).
Meyers M.A., Pak H-r. Observation of an adiabatic shear band in titanium by high-voltage transmission electron microscopy // Acta Metall. 1986. V. 34. P. 2493–2499.
Yang Y., Xinming Z., Zhenghua L., Qingyun L. Adiabatic shear band on the titanium side in the Ti/mild steel explosive cladding interface // Acta Mater. 1996. V. 44. P. 561–565.
Timothy S.P., Hutchings I.M. The structure of adiabatic shear bands in a titanium alloy // Acta Metall. 1985. V. 33. P. 667–676.
Шорохов Е.В., Зельдович В.И., Жгилев И.Н. Фролова Н.Ю., Хейфец А.Э., Хомская И.В. Динамическая деформация титана простым сдвигом // Фундаментальные проблемы современного материаловедения. 2007. Т. 4. № 1. С. 24–29.
Paton N.E., Backofen W.A. Plastic Deformation of Titanium at Elevated Temperatures // Metall. Trans. A. 1970. V. 1. P. 2839–2847.
Rosi F.D., Perkins F.C., Seigle L.L. Mechanism of plastic flow in titanium at low and high temperatures // J. of Metals. 1956. V. 8. № 2. P. 115–122.
Колачев Б.А., Ливанов А.А., Буханова А.А. Механические свойства титана и его сплавов. М.: Металлургия, 1974. 543 с.
Зельдович В.И, Шорохов Е.В., Фролова Н.Ю., Жгилев И.Н., Хейфец А.Э., Хомская И.В., Насонов П.А., Ушаков А.А. Структура титана после динамического канально-углового прессования при повышенной температуре // ФММ. 2009. Т. 108. № 4. С. 365–370.
Шаркеев Ю.П., Ерошенко А.Ю., Братчиков А.Д. Структура и механические свойства наноструктурного титана после дорекристаллизационных отжигов // Физическая мезомеханика. 2005. Т. 8. Спец. выпуск. С. 91–94.
Малышева С.П., Салищев Г.А., Якушина Е.Б. Влияние холодной прокатки на структуру и механические свойства листов из технического титана // МиТОМ. 2008. № 4. С. 34–40.
Семенова И.П., Салимгареева Г.Х., Латыш В.В., Кунавин С.А., Валиев Р.З. Исследование сопротивления усталости титана с ультрамелкозернистой структурой // МиТОМ. 2009. № 2. С. 34–39.
Минаев И.В., Абрамов А.В., Шорохов Е.В., Жгилев И.Н. Моделирование процесса интенсивной пластической деформации при высокоскоростном нагружении металлов // Деформация и разрушение материалов. 2009. № 3. С. 17–20.
Хомская И.В., Зельдович В.И., Шорохов Е.В., Жгилев И.Н., Фролова Н.Ю., Жгилев И.Н. Хейфец А.Э. Особенности формирования структуры в меди при динамическом канально-угловом прессовании // ФММ. 2008. Т. 105. № 6. С. 621–629.
Хомская И.В., Зельдович В.И., Шорохов Е.В., Фролова Н.Ю., Жгилев. И.Н. Структура меди после динамического канально–углового прессования // Металловедение и термическая обработка металлов. 2008. № 5. С. 38–43.
Хомская И.В., Шорохов Е.В., Зельдович В.И., Хейфец А.Э., Фролова Н.Ю., Насонов П.А. Жгилев И.Н. Исследование структуры и свойств субмикрокристаллической и нанокристаллической меди, полученной высокоскоростным прессованием // ФММ. 2011. Т. 111. № 6. С. 639–650.
Khomskaya I.V., Zel’dovich V., Kheifets A.E., Purygin N.P. Structure and properties of a Cu–37 wt % Zn alloy subjected to quasi–spherical explosive loading // Letters on materials 2015. V. 5. № 4 P. 454–458.
Валиев Р.З., Мусалимов Р.Ш. Электронная микроскопия высокого разрешения нанокристаллических материалов // ФММ. 1994. Т. 78. № 6. С. 114−121.
Хомская И.В., Шорохов Е.В., Зельдович В.И., Хейфец А.Э., Фролова Н.Ю. Структура и свойства субмикрокристаллической и нанокристаллической меди, полученной методом канально-углового прессования // Металлы. 2012. № 6. С. 56–62.
Mulyukov R.R., Imayev R.M., Nazarov A.A. Production, properties and application prospects of bulk nanostructured materials // J. Materials Science. 2008. V. 43. P. 7257–7263.
Dobatkin S.V., Shangina D.V., Bochvar N.R., Janeček M. Effect of deformation schedules and initial states on structure and properties of Cu–0.18% Zr alloy after high-pressure torsion and heating // Mater. Sci. Eng. A. 2014. V. 598. P. 288–292.
Zhilyaev A.P., Morozova A., Cabrera J.M., Kaibyshev R., Langdon T.G. Wear resistance and electroconductivity in a Cu–0.3Cr–0.5Zr alloy processed by ECAP // J. Materials Science. 2017. V. 52. P. 305–313.
Purcek G., Yanar H., Shangina D.V., Demirtas M., Bochvar N.R., Dobatkin S.V. Influence of high pressure torsion-induced grain refinement and subsequent aging on tribological properties of Cu–Cr–Zr alloy // J. Alloys and Compounds. 2018. V. 742. P. 325–333.
Попов В.В., Столбовский А.В., Попова Е.Н., Фалахутдинов Р.М., Шорохов Е.В. Эволюция структуры оловянистой бронзы при динамическом канально-угловом прессовании // ФММ. 2017. Т. 118. № 9. С. 909–916.
Осинцев О.Е., Федоров В.Н. Медь и медные сплавы. Отечественные и зарубежные марки / Справочник. М. “Машиностроение”, 2004. 336 с.
Vinogradov A., Patlan V., Suzuki Y., Kitagawa K., Kopylov V.I. Structure and properties of ultra-fine grain Cu–Cr–Zr alloy produced by equal-channel angular pressing // Acta Materialia. 2002. V. 50. P. 1639–1651.
Исламгалиев Р.К., Нестеров К.М., Валиев Р.З. Структура, прочность и электропроводность медного сплава системы Cu–Cr, подвергнутого интенсивной пластической деформации // ФММ. 2015. Т. 116. № 2. С. 219–228.
Беляева А.И., Коленов И.В., Савченко А.А., Галуза А.А., Аксенов Д.А., Рааб Г.И., Фаизова С.Н., Войценя В.С., Коновалов В.Г., Рыжков И.В., Скорик О.А., Солодовченко С.И., Бардамид А.Ф. Влияние размера зерна на стойкость к ионному распылению зеркал из низколегированного медного сплава системы Cu–Cr–Zr // Вопр. атомной науки и техники. Сер. Термоядерный синтез. 2011. Вып. 4. С. 50–59.
Зельдович В.И., Фролова Н.Ю., Хомская И.В., Хейфец А.Э. Электронно–микроскопическое исследование старения в сплаве Cu–0.06% Zr // ФММ. 2016. Т. 117. № 7. С. 732–741.
Khomskaya I.V., Zel’dovich V.I., Frolova N.Yu., Abdullina D.N., Kheifets A.E. Investigation of Cu5Zr particles precipitation in Cu–Zr and Cu–Cr–Zr alloys subjected to quenching and high strain rate deformation // Letters on Materials. 2019. V. 9. № 4. P. 400–404.
Зельдович В.И., Хомская И.В., Фролова Н.Ю., Хейфец А.Э., Шорохов Е.В., Насонов П.А. Структура хромоциркониевой бронзы, подвергнутой динамическому канально-угловому прессованию и старению // ФММ. 2013. Т. 114. № 5. С. 449–456.
Khomskaya I.V., Zel’dovich V.I., Frolova N.Yu., Kheifets A.E., Shorokhov E.V., Abdullina D.N. Effect of high-speed dynamic channel angular pressing and aging on the microstructure and properties of Cu–Cr–Zr alloys // IOP Conference Series: Materials Science and Engineering. 2018. V. 447. P. 12007–12012.
Хомская И.В., Зельдович В.И., Шорохов Е.В., Фролова Н.Ю., Хейфец А.Э., Дякина В.П. Влияние высокоскоростной деформации на структуру, свойства и термическую стабильность меди, легированной хромом и цирконием // Деформация и разрушение материалов. 2017. № 4. С. 22–29.
Makarov A.V., Skorynina P.A., Yurovskikh A.S., Osintseva A.L. Effect of the Technological Conditions of Frictional Treatment on the Structure, Phase Composition and Hardening of Metastable Austenitic Steel // AIP Conference Proceedings. 2016. V. 1785. P. 40035–40035.
Коршунов Л.Г., Корзников А.В., Черненко Н.Л. Влияние интенсивной пластической деформации и температуры старения на упрочнение, структуру и износостойкость бериллиевой бронзы // Физика металлов и металловедение. 2011. Т. 111. № 4. С. 413–420.
Хейфец А.Э., Хомская И.В., Коршунов Л.Г., Зельдович В.И., Фролова Н.Ю. Влияние высокоскоростной деформации и температуры старения на эволюцию структуры, микротвердость и износостойкость низколегированного сплава Cu–Cr–Zr // Физика металлов и металловедение. 2018. Т. 119. № 4. С. 423–432.
Khomskaya I.V., Kheifets A.E., Zel’dovich V.I., Korshu-nov L.G., Frolova N.Yu., Abdullina D.N. The formation of friction-induced nanocrystalline structure in submicrocrystalline Cu–Cr–Zr alloy processed by DCAP // Letters on Materials. 2018. V. 8. № 4. P. 410–414.
Дополнительные материалы отсутствуют.
Инструменты
Физика металлов и металловедение