Физика металлов и металловедение, 2020, T. 121, № 8, стр. 892-898
Влияние отжига на механические и термомеханические характеристики сплава Ti50Pd40Ni10 с высокотемпературным эффектом памяти формы, исследованные на заготовке в виде прутка
Н. Н. Попов a, *, Д. В. Пресняков a, В. Ф. Ларькин a, И. С. Рыжов a, А. А. Костылева a
a ФГУП “РФЯЦ-ВНИИЭФ”
607188 Нижегородская обл., Саров, пр. Мира, 37, Россия
* E-mail: NNPopov@vniief.ru
Поступила в редакцию 19.09.2019
После доработки 21.01.2020
Принята к публикации 24.03.2020
Аннотация
Проведены комплексные исследования свойств сплава Ti50Pd40Ni10 (ат. %) с высокотемпературным эффектом памяти формы на образцах, изготовленных из прутка 5.86 мм, после различных режимов отжига и условий наведения деформации. Получены сведения о температурах фазовых превращений, механических и термомеханических характеристиках сплава. Диапазон фазовых превращений находится в интервале от Mf = 360°С до Af = 439°С. Это приемлемые величины для создания требуемого устройства безопасности. Максимальные величины эффекта памяти формы и степени восстановления формы равны 2.4 и 43% соответственно. Этого недостаточно для создания работоспособного устройства безопасности. Таким образом, существенно увеличить термомеханические характеристики за счет выбора режимов отжига и условий наведения деформации не удалось. Более высокие значения термомеханических характеристик получены нами ранее на образцах, вырезанных из полосы толщиной 2.04 мм. Поэтому в дальнейшем изготовление рабочих элементов устройств безопасности, предназначенных для объектов атомной энергетики, будет производиться из полосы.
ВВЕДЕНИЕ
Ранее мы выбрали сплав Ti50Pd40Ni10 (ат. %) с высокотемпературным эффектом памяти формы для изготовления термочувствительных элементов устройства безопасности, предназначенного для реакторных установок на быстрых нейтронах.
В работе [1] мы изучили свойства данного сплава в исходном состоянии, на образцах, изготовленных из полосы толщиной 2.04 мм, а в [2] – на образцах из прутка диаметром 5.86 мм. Однако для прутка было получено, что максимальные величины эффекта памяти формы и степени восстановления формы равны 1.5 и 21% соответственно. Этого недостаточно для создания работоспособного устройства безопасности. Увеличение этих характеристик было намечено провести за счет выбора оптимальных режимов термообработки и режимов наведения деформации исследуемым объектам. Результаты этих исследований приведены в данной работе.
МАТЕРИАЛЫ И МЕТОДИКА ЭКСПЕРИМЕНТА
Исследования проводили на сплаве состава 33.1Ti–58.8Pd–8.1Ni, мас. доля по шихте, %, или Ti50Pd40Ni10 (ат. %) поставленном в виде прутка, маркированного изготовителем обозначением L. Пруток после изготовления был отожжен в вакууме при температуре 850°С в течение 1 ч в вакуумной печи сопротивления СШВЭ-1.2,5/25И4.
Исследование элементного и локального фазового состава проводили на сканирующем автоэмиссионном электронном микроскопе MIRA LMU, укомплектованном аналитической приставкой INCA с детектором X-MAX, методом электронно-зондового микрорентгеноспектрального анализа (EPMA).
Для измерения температур мартенситных превращений (МП) и температуры плавления сплава использовали термоанализатор “SETARAM” (Франция) в режиме дифференциально-термического анализа (ДТА) на образцах в виде параллелепипеда с размерами 2 × 2 × 4 мм. Механические свойства сплава исследовали на образцах цилиндрической формы с резьбовыми головками М4, общей длиной 26 мм, длиной и диаметром рабочей части 13 и 2 мм соответственно, на универсальной испытательной машине UTS-100К (Германия). Наведение деформации для определения термомеханических характеристик осуществляли на этой же машине с помощью специально разработанного приспособления. Нагрев образцов производили с использованием вертикальной раздвижной трубчатой печи VST 12/200. Исследование термомеханических характеристик (ТМХ) при проявлении эффекта памяти формы (ЭПФ) проводили с помощью разработанного стенда. Более подробно методики исследований описаны в [1, 3].
Термическую обработку (ТО) образцов сплава Ti50Pd40Ni10 выполняли по следующим режимам:
– отжиг при 400°С в течение 1 ч, охлаждение с печью (ТО № 1);
– отжиг при 600°С в течение 1 ч, охлаждение с печью (ТО № 2);
– отжиг при 850°С в течение 1 ч, охлаждение с печью (ТО № 3);
– отжиг в вакууме при 850°С в течение 1 ч, охлаждение с печью (ТО № 4).
Отжиг образцов по режимам ТО №№ 1–3 проводили в лабораторной печи сопротивления А07-Р722.01.010, а отжиг по режиму ТО № 4 в шахтной вакуумной печи СШВ 1.2,5/25И1.
Статистическую обработку значений полученных характеристик проводили на персональном компьютере с помощью универсального программного статистического пакета STADIA и критериев, приведенных в [4–6].
РЕЗУЛЬТАТЫ И ИХ ОБСУЖДЕНИЕ
1. Исследование элементного и локального фазового состава. Результаты исследований концентрации элементов приведены в табл. 1. Установлено, что основная матрица сплава Ti50Pd40Ni10 (ат. %) после различных видов и режимов термообработки имеет одинаковый состав и образована твердым раствором элементов Ti, Pd, Ni. В матрице сплава после отжига по режимам ТО № 1, ТО № 2 и ТО № 3 расположены включения микронного и субмикронного размера, представляющие собой нитрид титана TiN0.6 и соединения элементов Ti, Pd, Ni, О (вероятно, оксиды) с различным атомным соотношением элементов в них. После отжига по режиму ТО № 4 вблизи поверхности образца расположены включения в виде оксида TiO2. В режиме вторичных электронов (топографический контраст) в структуре сплава обнаружены поры размером до нескольких микрон. Подобные явления в образцах, вырезанных из полосы и исследованных нами ранее, отсутствовали. Поэтому можно предположить, что характеристики пластичности, и как следствие, величина эффекта памяти формы у образцов, изготовленных из прутка, будет ниже, чем у образцов, изготовленных из полосы.
Таблица 1.
Результаты статистической обработки значений концентраций элементов, полученных в различных участках поверхности образцов сплава Ti50Pd40Ni10 (ат. %), в исходном состоянии и после различных режимов термообработки
Параметры статистической обработки | Концентрации элементов | |||||
---|---|---|---|---|---|---|
мас. % | ат. % | |||||
Ti | Pd | Ni | Ti | Pd | Ni | |
Исходное состояние | ||||||
Приведенное среднее значение | 32.9 | 59.2 | 7.9 | 49.8 | 40.5 | 9.7 |
СКО | 0.12 | 0.13 | 0.10 | 0.13 | 0.12 | 0.12 |
Квар, % | 0.4 | 0.2 | 1 | 0.3 | 0.3 | 1 |
n | 25 | 25 | 25 | 25 | 25 | 25 |
ТО № 1 (отжиг при 400°С 1 ч, охлаждение с печью) | ||||||
Среднее значение | 33.2 | 58.8 | 8.1 | 50.1 | 39.95 | 9.95 |
Приведенное среднее значение | 33.2 | 58.7 | 8.1 | 50.0 | 40.0 | 10.0 |
СКО | 0.15 | 0.14 | 0.08 | 0.15 | 0.14 | 0.10 |
Квар, % | 0.5 | 0.2 | 1 | 0.3 | 0.4 | 1 |
n | 24 | 24 | 24 | 24 | 24 | 24 |
ТО № 2 (отжиг при 600°С 1 ч, охлаждение с печью) | ||||||
Среднее значение | 33.2 | 58.9 | 7.9 | 50.1 | 40.1 | 9.8 |
СКО | 0.16 | 0.14 | 0.11 | 0.25 | 0.17 | 0.14 |
Квар, % | 0.5 | 0.2 | 1 | 0.5 | 0.4 | 1 |
n | 24 | 24 | 24 | 24 | 24 | 24 |
ТО № 4 (отжиг в вакууме при 850°С 1 ч, охлаждение с печью) | ||||||
Среднее значение | 33.9 | 58.1 | 8.0 | 50.9 | 39.3 | 9.8 |
СКО | 0.11 | 0.10 | 0.09 | 0.14 | 0.09 | 0.11 |
Квар, % | 0.3 | 0.2 | 1 | 0.3 | 0.2 | 1 |
n | 23 | 23 | 23 | 23 | 23 | 23 |
2. Определение температур фазовых превращений сплава Ti50Pd40Ni10 методом дифференциального термического анализа. Исследуемый образец сплава сначала нагревался со скоростью 20°С/мин от температуры окружающей среды, равной 20–25°С, до 800°С, а затем охлаждался со скоростью 10°С/мин от 800°С до температуры 75–85°С.
Полученные термограммы мартенситно-аустенитных фазовых превращений в сплаве Ti50Pd40Ni10, ат. % подобны термограммам, полученным нами для полосы [1]. По термограммам определяли температуру начала As и окончания Af МП, протекающего в сплаве при нагревании. Аналогичным образом находили температуры начала Ms и окончания Mf прямого МП, протекающего в сплаве при охлаждении [1].
Значения температур МП As, Af, Ms, Mf, их интервалов |As–Аf| и |Мs–Мf|, гистерезиса температур фазового превращения (As–Mf) в образцах сплава в исходном состоянии и после отжига по различным режимам, а также результаты их статистической обработки с учетом инструментальной погрешности (±0.5)°С представлены в табл. 2. Анализ табл. 2 показывает различие между собой соответствующих значений температур фазовых превращений As, Af (до 12.0°С) и Ms, Mf (до 20.5°С), интервалов температур |As–Аf| (до 7.5°С) и |Мs–Мf| (до 16.5°С) и гистерезиса (As–Mf) (до 13.0°С) в сплаве Ti50Pd40Ni10 (ат. %) в исходном состоянии (средние значения) и после различных режимов отжига, хотя это сравнение нельзя подтвердить статистическим анализом из-за единичных значений температур, определенных в сплаве после ТО. Можно также отметить, что для данного сплава в исходном состоянии и после различных режимов ТО обратное МП при нагревании и прямое МП при охлаждении осуществляются в достаточно узких интервалах температур |As–Аf| (не более 36.0°С) и |Мs–Мf| (не более 31.0°С), соответственно; гистерезис температур фазового превращения (As–Mf) небольшой (не более 45.5°С).
Таблица 2.
Значения определенных методом ДТА на термоанализаторе “SETARAM” температур фазовых превращений в образцах сплава Ti50Pd40Ni10, ат. % в исходном состоянии и после различных режимов отжига
Термо-обработка | Масса образца, мг | Обратное МП (при нагревании сплава) | Прямое МП (при охлаждении сплава) | Гистерезис As–Mf, °С | ||||
---|---|---|---|---|---|---|---|---|
As, °С | Af, °С | |As–Аf|, °С | Ms, °С | Mf, °С | |Мs–Мf|, °С | |||
Исходное состояние (средние значения) | – | 397.5 | 433.5 | 36.0 | 386.0 | 363.5 | 23.0 | 35.5 |
ТО № 1 | 207.4 | 409.5 | 439.0 | 29.5 | 395.0 | 364.0 | 31.0 | 45.5 |
ТО № 2 | 209.2 | 398.0 | 429.0 | 31.0 | 395.0 | 365.5 | 29.5 | 32.5 |
ТО № 4 | 209.4 | 399.5 | 428.0 | 28.5 | 374.5 | 360.0 | 14.5 | 39.5 |
3. Исследование механических свойств. Испытания на растяжение проводили на машине UTS-100К с использованием приспособления Л351 в диапазоне температур от 23°С до 380°С со скоростью деформации $\dot {\varepsilon }$ ≈ 1.2 × 10–3 с–1.
В результате механических испытаний получали диаграммы растяжения в координатах “напряжение σ–деформация ε”. По данным диаграммам определяли фазовый предел текучести σф, предел прочности σв, максимальную деформацию образца перед разрывом (под нагрузкой) $\varepsilon _{{\text{о}}}^{{{\text{max}}}},$ соответствующую напряжению предела прочности. Относительное остаточное удлинение δост определяли при комнатной температуре. Предел текучести σт, обусловленный дислокационным пластическим течением, определить не удалось в связи с отсутствием на диаграммах второго участка упругого деформирования. Типичные диаграммы растяжения приведены на рис. 1.
Рис. 1.
Диаграммы растяжения в координатах (σ–ε) образцов сплава Ti50Pd40Ni10, ат. % после ТО № 1 (1) и ТО № 3 (2), полученные по результатам испытаний при температуре 325°С со скоростью деформации $\dot {\varepsilon }$ ≈ ≈ 1.2 × 10–3 с–1.
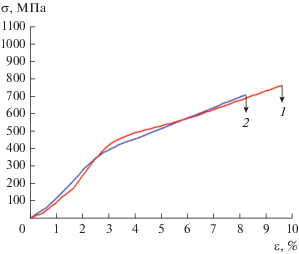
Значения основных механических характеристик, округленные с учетом инструментальных погрешностей, представлены в табл. 3.
Таблица 3.
Основные механические характеристики, полученные при испытании на растяжение со скоростью деформации $\dot {\varepsilon }$ ≈ 1.2 × 10–3 с–1 при различных температурах, образцов сплава Ti50Pd40Ni10, ат. % в исходном состоянии и после различных режимов отжига
Температура испытаний, °С | № образца | Термообработка | σф, МПа | σв, МПа | $\varepsilon _{{\text{o}}}^{{\max }},$ % | δост, % |
---|---|---|---|---|---|---|
23 | 1 | Исходное состояние | 380 | 1010 | 11.0 | 5 |
2 | ТО № 1 | 470 | 830 | 8.0 | 3 | |
3 | ТО № 3 | 380 | 790 | 7.5 | 2 | |
170–175 | 1 | Исходное состояние | 390 | 920 | 13.5 | 6 |
2 | ТО № 1 | 500 | 830 | 10.5 | 4 | |
3 | ТО № 3 | 380 | 710 | 10.5 | 5 | |
325 | 1 | ТО № 1 | 460 | 760 | 9.5 | 3 |
2 | ТО № 3 | 380 | 710 | 8.0 | 4 | |
375–380 | 1 | ТО № 4 | 290 | 610 | 8.0 | 5 |
Нагрев до 450 и охлаждение до 380–370 | 2 | 210 | 550 | 7.5 | 5 | |
Нагрев до 450 и охлаждение до 170–175 | 3 | 310 | 800 | 8.5 | 6 |
Выявлено (см. табл. 3), что в исходном состоянии получены максимальные значения предела прочности σв = 1010 МПа при температуре испытания Tисп = 23°С и относительного удлинения δост = 6% при Tисп = 170–175°С. Варьирование температурами отжига и испытания образцов привело только к уменьшению (в ряде случаев – к резкому) σв и δост. Исключение составили испытания образца после вакуумного отжига при 850°С и предварительно нагретого до температуры 450°С, а затем охлажденного до Tисп = 170–175°С. При этих условиях получено значение δост = 6%.
Отметим, что по результатам дюраметрических исследований установлено, что наименьшую микротвердость сплав имеет после отжига по режиму ТО № 4 и, следовательно, можно было ожидать, что при этом режиме будет наибольшая δост. Этот факт мы и зарегистрировали после испытаний на растяжение.
4. Исследование термомеханических свойств. На испытательной машине UTS-100K образцам сплава Ti50Pd40Ni10, ат. % после различных режимов отжига наводили деформацию растяжением при различных температурах ТД и при различных величинах общей наводимой деформации εо со скоростью деформации $\dot {\varepsilon }$ ≈ 1.2 × 10–3 с–1. Нагрев образцов проводили со скоростью 7°С/мин. По полученным диаграммам определяли величину наведенной растяжением деформации εр (остаточной деформации после разгрузки). После наведения деформации образцы сплава поочередно устанавливали в термокамеру стенда Р1288 для определения термомеханических характеристик. Затем проводили нагрев образцов от Т = 23°С до Т ~ 500°С (соответствующей ожиданию стабильного окончания проявления ЭПФ) со средним темпом нагрева 10°С/мин. При нагреве образцы укорачивались – наблюдалось проявление ЭПФ. При охлаждении проявление эффекта обратимой памяти формы не обнаружено. По полученным диаграммам формовосстановления образцов определяли характеристические температуры $А_{{{\text{s}}{{\,}_{{{\text{ЭПФ}}}}}}}^{{\text{н}}},$ $А_{{{\text{f}}{{\,}_{{{\text{ЭПФ}}}}}}}^{{\text{к}}}$ соответственно, на начальной и конечной стадиях всего этапа формовосстановления при проявлении ЭПФ (характеризуют весь диапазон формовосстановления). Методом касательных определяли характеристические температуры АsЭПФ, АfЭПФ, (характеризуют основное формовосстановление внутри диапазона температур $А_{{{\text{s}}{{\,}_{{{\text{ЭПФ}}}}}}}^{{\text{н}}},$ $А_{{{\text{f}}{{\,}_{{{\text{ЭПФ}}}}}}}^{{\text{к}}}$). Затем рассчитывали температурные интервалы |$А_{{{\text{s}}{{\,}_{{{\text{ЭПФ}}}}}}}^{{\text{н}}}$–$А_{{{\text{f}}{{\,}_{{{\text{ЭПФ}}}}}}}^{{\text{к}}}$|, |АsЭПФ–АfЭПФ|. По диаграммам также определяли величину термически обратимой деформации εЭПФ при проявлении ЭПФ и степень восстановления формы ηЭПФ [7]. Диаграммы формовосстановления в координатах “температура Т–деформация ε” образцов сплава в исходном состоянии и после различных режимов отжига и условий наведения деформации, полученные по результатам исследований на стенде Р1288, представлены на рис. 2.
Рис. 2.
Диаграммы формовосстановления образцов сплава Ti50Pd40Ni10, ат. % в исходном состоянии и после различных режимов отжига, полученные при нагреве до Т = 445–480°С (стабильного окончания проявления ЭПФ) после предварительно наведенной деформации растяжением при различных ТД и εо со скоростью $\dot {\varepsilon }$ ≈ 1.2 × 10–3 с–1: 1 – исходное состояние, ТД = 23°С, εо = 9%; 2 – исходное состояние, ТД = 170‒175°С, εо = 11%; 3 – ТО № 1, ТД = 23°С, εо = 8%; 4 –ТО № 1, ТД = 170–175°С, εо = 9%; 5 – ТО № 3, ТД = 170–175°С, εо = 9%; 6 – ТО № 4, ТД = 380–370°С, εо = 7.5%.
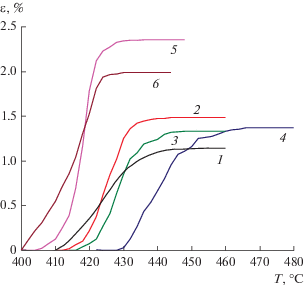
Значения основных ТМХ, полученные при проявлении ЭПФ в исследуемых образцах и округленные с учетом инструментальных погрешностей для характеристических температур – (±1)°С, для величин εр, εЭПФ – (±0.1)%, для степени ηЭПФ – (±1)%, приведены в табл. 4.
Таблица 4.
Термомеханические характеристики образцов сплаваTi50Pd40Ni10, ат. % в исходном состоянии и после различных режимов отжига, полученные при нагреве до Т = 445–480°С (стабильного окончания проявления ЭПФ) после предварительно наведенной деформации растяжением при различных ТД и εо со скоростью $\dot {\varepsilon }$ ≈ 1.2 × 10–3 с–1
Термомеханические характеристики | Температура наведения деформации, °С | |||||
---|---|---|---|---|---|---|
Исходное состояние | ТО № 1 | ТО № 3 | ТО № 4 | |||
23 | 170–175 | 23 | 170–175 | 170–175 | 380–370 (после нагрева до 450°С) |
|
εо, % | 9 | 11 | 8 | 9 | 9 | 7.5 |
εр, % | 5.4 | 7.3 | 4.2 | 6.0 | 5.6 | 5.3 |
$А_{{{\text{s}}\,{\text{ЭПФ}}}}^{{\text{н}}},$ °С | 408 | 411 | 417 | 428 | 405 | 400 |
Аs ЭПФ, °С | 412 | 418 | 421 | 430 | 414 | 408 |
Аf ЭПФ, °С | 436 | 432 | 436 | 451 | 422 | 423 |
$А_{{{\text{f}}\,{\text{ЭПФ}}}}^{{\text{к}}},$ °С | 457 | 443 | 448 | 467 | 436 | 430 |
Интервал |$А_{{{\text{s}}\,{\text{ЭПФ}}}}^{{\text{н}}}$ – $А_{{{\text{f}}\,{\text{ЭПФ}}}}^{{\text{к}}}$|, °С |
49 | 32 | 31 | 39 | 31 | 30 |
Интервал |Аs ЭПФ–Аf ЭПФ|, °С | 24 | 14 | 15 | 21 | 8 | 15 |
εЭПФ, % | 1.1 | 1.5 | 1.3 | 1.4 | 2.4 | 2.0 |
ηЭПФ, % | 20 | 21 | 31 | 23 | 43 | 38 |
В результате проведенных экспериментов установлено (см. табл. 4), что при нагреве до Т = 480°С (стабильного окончания проявлении ЭПФ) после предварительно наведенной деформации растяжением при различных температурах ТД и величинах общей наводимой деформации εо со скоростью $\dot {\varepsilon }$ ≈ 1.2 × 10–3 с–1 для образцов сплава Ti50Pd40Ni10 (ат. %) максимальные (но все равно не очень большие) значения характеристик памяти формы εЭПФ = 2.4%, ηЭПФ = 43% получены после ТО № 3 (что в 1.6–2.2 раза превышает эти характеристики в исходном состоянии и после ТО № 1 после предварительной деформации растяжением при ТД = 23°С и (170–175)°С); при этом температуры обратного МП, характеризующие основное формовосстановление, составляют Аs ЭПФ = 414°С, Аf ЭПФ = = 422°С, и это превращение происходит в узком интервале температур |Аs ЭПФ–Аf ЭПФ| = 8°С. Для образцов, подвергнутых вакуумному отжигу по режиму ТО № 4, после предварительно наведенной деформации растяжением при температуре ТД = = 380–370°С (после нагрева до 450°С) со скоростью $\dot {\varepsilon }$ ≈ 1.2 × 10–3 с–1 при величине εо = 7.5% получены также не очень большие значения εЭПФ = 2.0%, ηЭПФ = 38%; при этом температуры обратного МП составляют Аs ЭПФ = 408°С, Аf ЭПФ = = 423°С, и это превращение также происходит в узком интервале температур |Аs ЭПФ–Аf ЭПФ| = 15°С. Необходимо отметить, что по причине дороговизны и, следовательно, ограниченного количества материала для определения ТМХ при каждом режиме ТО и условии наведения деформации (ТД и εо) использовали только по одному образцу. Сравнивая значения температур начала и конца обратного МП ($А_{{{\text{s}}\,{\text{ЭПФ}}}}^{{\text{н}}},$ $А_{{{\text{f}}\,{\text{ЭПФ}}}}^{{\text{к}}}$), полученные деформационным методом [7] (см. табл. 4), со значениями температур (As, Af), полученными методом ДТА (см. табл. 2), отметим, что $А_{{{\text{s}}\,{\text{ЭПФ}}}}^{{\text{н}}},$ $А_{{{\text{f}}\,{\text{ЭПФ}}}}^{{\text{к}}}$ увеличены чуть более, чем на 5%. При сравнении четырех температур МП, полученных ранее в [8, 9] для сплава Ti50Pd40Ni10 методом дифференциальной сканирующей калориметрии (ДСК), и результатов, полученных нами методом ДТА (см. табл. 2), отмечено, что отличие не превышает 7%. Это неожиданно, поскольку технологии получения заготовок, способы термообработки, методы определения температур отличались. При этом заготовка в нашем случае была в виде прутка, а в [8] – в виде листа толщиной 1 мм. Также хорошее совпадение наблюдается при сравнении температур превращения сплава Ti50Pd40Ni10, полученных нами, с данными, приведенными в [10].
В заключение можно отметить, что за счет варьирования температур отжига и условий наведения деформации образцам, вырезанным из прутка сплава Ti50Pd40Ni10, удалось увеличить в 1.6 раза εЭПФ и в 2 раза ηЭПФ по сравнению с данными, полученными для прутка в исходном состоянии [2]. Вместе с тем отметим, что максимальные значения величин εЭПФ = 2.4%, ηЭПФ = 43%, полученные нами в данной работе, недостаточны для создания работоспособного устройства безопасности.
Однако результаты, полученные на образцах, изготовленных из полосы в исходном состоянии [1], имеют приемлемые значения (εЭПФ = 3.9%, ηЭПФ = 49%) и будут использованы нами для создания устройств безопасности применительно к объектам атомной энергетики. Более низкие значения характеристик механических и термомеханических свойств, полученные для заготовки в виде прутка, связаны, видимо с несовершенной (по сравнению с полосой) технологией изготовления прутка.
ВЫВОДЫ
1. Проведены комплексные исследования свойств сплава Ti50Pd40Ni10 с высокотемпературным эффектом памяти формы на образцах, изготовленных из прутка диаметром 5.86 мм, после различных режимов отжига и условий наведения деформации. Получены сведения о температурах фазовых превращений, механических и термомеханических характеристиках сплава.
2. Диапазон фазовых превращений находится в интервале от Mf = 360°С до Af = 439°С. Это приемлемые величины для создания требуемого устройства безопасности.
3. Максимальные величины εЭПФ и ηЭПФ равны 2.4 и 43% соответственно. Этого недостаточно для создания работоспособного устройства безопасности. Таким образом, попытки существенно увеличить эти характеристики за счет выбора режимов отжига и условий наведения деформации не привели к желаемому результату.
4. Более высокие значения термомеханических характеристик получены нами ранее на образцах, вырезанных из полосы толщиной 2.04 мм. По-видимому, технология изготовления прутка менее совершенна, чем полосы.
Поэтому в дальнейшем изготовление рабочих элементов устройств безопасности, предназначенных для объектов атомной энергетики, будет производиться из полосы.
Список литературы
Попов Н.Н., Ларькин В.Ф., Пресняков Д.В., Гришин Е.Н., Сысоева Т.И., Морозова Т.А., Потемкин Г.А., Костылева А.А. Исследование свойств сплава 50Ti–40Pd–10Ni с высокотемпературным эффектом памяти формы // ФММ. 2018. Т. 119. № 3. С. 303–316.
Попов Н.Н., Пресняков Д.В., Ларькин В.Ф., Суворова Е.Б., Костылева А.А. Механические и термомеханические свойства сплава Ti50Pd40Ni10, ат. % с высокотемпературным эффектом памяти формы, исследованные на заготовке в виде прутка в отожженном состоянии // ФММ. 2019. Т. 120. № 10. С. 1096–1100.
Попов Н.Н., Пресняков Д.В., Гришин Е.Н., Сысоева Т.И., Морозова Т.А., Костылева А.А. Исследование свойств высокотемпературного сплава с памятью формы 49Ni–36Ti–15Hf в литом состоянии // Металлы. 2019. № 2. С. 43–53.
Кулаичев А.П. Универсальный программный статистический пакет STADIA (версия 7.0) для Windows. М.: НПО “Информатика и компьютеры”, 2007.
Кулаичев А.П. Методы и средства комплексного анализа данных. М.: Форум: Инфра-М, 2006. 512 с.
Степнов М.Н. Статистические методы обработки результатов механических испытаний. М: Машиностроение, 1985. 232 с.
Попов Н.Н. Способ определения термомеханических характеристик материалов с памятью формы. Патент РФ № 2478928, МПК G 01N 3/18. Опубл. 10.04.2013.
Golberg D., Xu Y., Murakami Y., Otsuka K., Ueki T., Horikawa H. High-temperature shape memory effect in Ti50Pd50 – xNix (x = 10, 15, 20) alloys // Mater. Letters. 1995. V. 22. P. 241–246.
Kumar P., Lagoudas D.C. Experimental and microstructural characterization of simultaneous creep, plasticity and phase transformation in Ti50Pd40Ni10 high-temperature shape memory alloy // Acta Mater. 2010. V. 58. P. 1618–1628.
Сплавы никелида титана с памятью формы. Ч. I. Структура, фазовые превращения и свойства. Под науч. ред. В.Г. Пушина. Екатеринбург: УрО РАН, 2006. С. 96–112.
Дополнительные материалы отсутствуют.
Инструменты
Физика металлов и металловедение