Физика металлов и металловедение, 2021, T. 122, № 1, стр. 67-73
Влияние температуры деформации на формирование ультрамелкозернистой структуры в термоупрочняемом Cu–Cr–Zr сплаве
А. И. Морозова a, b, *, А. Н. Беляков a, Р. О. Кайбышев a
a ФГАОУ ВО НИУ “БелГУ”
308015 Белгород, ул. Победы, 85, Россия
b НИТУ “МИСиС”
119049 Москва, Ленинский просп., 4, Россия
* E-mail: morozova_ai@bsu.edu.ru
Поступила в редакцию 27.03.2020
После доработки 18.08.2020
Принята к публикации 04.09.2020
Аннотация
Изучено влияние температуры пластической деформации методом равноканального углового прессования на микроструктуру и физико-механические свойства термоупрочняемого сплава Cu–0.3% Cr–0.5% Zr. Пластическая деформация приводит к формированию областей ультрамелкозернистой структуры со средним размером зерен менее 1 мкм, распаду пересыщенного твердого раствора и выделению дисперсных частиц. Показано, что с ростом температуры деформации доля распада пересыщенного твердого раствора увеличивается. С повышением объемной доли дисперсных частиц растет плотность полос микросдвига, увеличивается плотность дислокаций, доля большеугловых границ и ультрамелкозернистой структуры.
ВВЕДЕНИЕ
Перспективными материалами для электротехнической промышленности являются термоупрочняемые Cu–Cr–Zr сплавы, в которых может быть достигнута высокая электрическая проводимость и прочность за счет формирования ультрамелкозернистой (УМЗ) структуры, стабилизированной дисперсными частицами [1–3]. Такая микроструктура может быть сформирована в результате воздействия больших пластических деформаций в сочетании с термической обработкой (ТО) [4]. Роль одного из основных упрочняющих компонентов в Cu–Cr–Zr сплавах выполняют дисперсные частицы. В литературе упоминают зоны Гинье-Престона, частицы ГЦК и ОЦК Cr, Cu5Zr, Cu4Zr, Cu2CrZr, выделяющиеся в Cu–Cr–Zr-сплавах [5–7]. Из-за малой объемной доли (менее 1%) и размера частиц вторых фаз (2–4 нм) точное определение их химического состава затруднено. Установлено, что дисперсные частицы, выделяющиеся в Cu–Cr–Zr-сплавах, комплексно повышают эксплуатационные характеристики [8]. С одной стороны, дисперсные частицы обеспечивают существенное дисперсионное упрочнение (100–150 МПа) [9], с другой стороны, обеднение пересыщенного твердого раствора (ПТР) медной матрицы легирующими элементами способствует значительному улучшению проводящих свойств [10]. Известно, что дисперсные частицы существенно влияют на эволюцию микроструктуры и физико-механических свойств сплавов в процессе деформации [11]. Однако большинство работ, посвящeнных воздействую больших пластических деформаций, были проведены в Cu–Cr–Zr-сплавах после обработки на получение пересыщенного твердого раствора, причем деформация осуществлялась при комнатной температуре [1, 3, 4, 8]. Поэтому влияние дисперсных частиц, формирующихся в ходе предварительной ТО и в процессе деформации, на микроструктуру и свойства сплавов не было исследовано.
Цель настоящей работы – изучить влияние дисперсных частиц и температуры деформации на формирование ультрамелкозернистой структуры Cu–Cr–Zr-сплава, установить влияние микроструктурных изменений на физико-механические характеристики сплава.
МАТЕРИАЛ И МЕТОДИКИ
В качестве материала исследования был выбран сплав Cu–0.3% Cr–0.5% Zr (мас. %). Сплав был подвергнут обработке на получение пересыщенного твердого раствора при температуре 920°С в течение 0.5 ч с охлаждением в воде (закалка). После закалки в структуре наблюдали крупные частицы Cr и частицы обогащенные цирконием, которые не растворились при 920°С. Размер зерен составлял 120 мкм. Часть образцов была дополнительно подвергнута старению при температуре 450°С в течение 1 ч с охлаждением в воде. После старения в структуре наблюдали дисперсные частицы Cr размером 2–4 нм. Более подробно с исходной микроструктурой можно ознакомиться в работе [12]. Образцы размером 14 × 14 × 900 мм после закалки или закалки с последующим старением (старение) деформировали методом равноканального углового прессования (РКУП) в оснастке с углом пересечения каналов матрицы 90° при температурах 473, 573, 673 К. Осуществляли 4 прохода РКУП по маршруту Вс (после каждого прохода образец поворачивали на 90° относительно оси прессования).
Испытания на растяжение проводили при комнатной температуре со скоростью деформирования 2 мм/мин на испытательной машине Instron 5882. Плоские образцы (длина рабочей части – 6 мм, поперечное сечение 1.5 × 3 мм) для механических испытаний были вырезаны вдоль направления прессования. Твердость оценивали методом Виккерса на микротвердомере WOLPERT 420 MVD при нагрузке 100 г и времени выдержки 15 с, количество измерений составляло не менее 10, погрешность измерения находилась в интервале 3–7%. В отличие от предыдущих работ, электрическая проводимость была измерена вихретоковым методом с помощью прибора Константа К–6, который обеспечивал относительную погрешность 1–3%, количество измерений составляло не менее 10.
Исследования микроструктуры проводили в сечении образцов параллельном направлению прессования с помощью растрового электронного микроскопа Nova NanoSem 450 FEI с детектором дифракции обратно-рассеянных электронов и просвечивающего электронного микроскопа (ПЭМ) Jeol Jem 2100. Образцы готовили с использованием электролита 25% HNO3 и 75% CH3OH методом электролитической полировки с помощью установки TenuPol-5 при температуре –20°С и напряжении 10 В. Средний размер зерен D определяли по картинам дифракции обратно-рассеянных электронов методом эквивалентных диаметров, долю большеугловых границ (БУГ) FБУГ, величину микронапряжений θKAM (Kernel Average Misorientation) и долю УМЗ-структуры (доля зерен, средний размер которых составляет менее 2 мкм) FУМЗ оценивали с использованием программного обеспечения OIM Analysis (шаг сканирования 50 нм), размер субзерен d оценивали по данным ПЭМ методом случайных секущих, плотность дислокаций ρ определяли по числу выходов линий дислокаций на поверхность фольги, объемную долю частиц fчаст оценивали по картинам ПЭМ, используя следующее соотношение [13]:
где Ns – число частиц на единицу площади, а r – средний радиус частиц.РЕЗУЛЬТАТЫ И ИХ ОБСУЖДЕНИЕ
1. Микроструктура Cu–Cr–Zr-сплава после РКУП при повышенной температуре
Микроструктура Cu–Cr–Zr-сплава после РКУП при исследованных температурах представлена на рис. 1. Пластическая деформация приводит к формированию плотной сетки малоугловых границ (МУГ) деформационного происхождения. Образуются кристаллиты размером 0.3–0.5 мкм, которые окружены только БУГ, т.е. формируются новые ультрамелкие зерна. Формирование УМЗ структуры происходит в основном внутри деформационных полос – областей, образованных длинными параллельными БУГ. В предварительно закаленных образцах данный процесс менее выражен. С ростом температуры деформации в Cu–Cr–Zr-сплаве после старения толщина деформационных полос увеличивается. Средний размер зерен составляет около 1 мкм (рис. 2). В образцах после старения средний размер структурных элементов ниже, чем после закалки. Доля БУГ и УМЗ-структуры составляет примерно 0.4 и 0.3, соответственно, причем предварительное старение обеспечивает увеличение этих параметров на ≈0.1 вне зависимости от температуры деформации.
Рис. 1.
Распределение границ кристаллитов в Cu–Cr–Zr сплаве после закалки и старения с последующим РКУП при температуре 473 K, 573 K, 673 K. Серыми линиями обозначены малоугловые границы (<15°), черными – большеугловые границы (>15°).
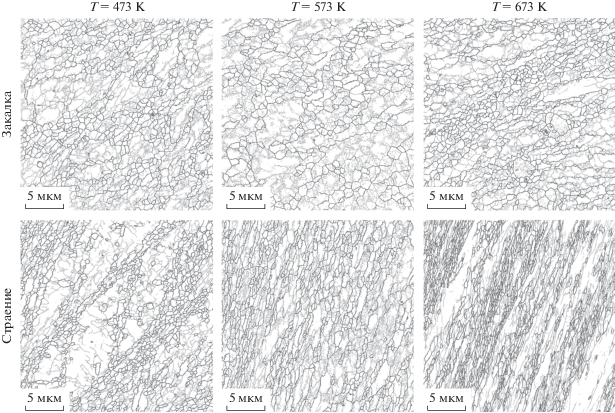
Рис. 2.
Влияние температуры РКУП на средний размер зерен (D), субзерен (d), плотность дислокаций (ρ), долю большеугловых границ (FБУГ) и ультрамелкозернистой структуры (FУМЗ), внутренние микронапряжения (θKAM) и объемную долю дисперсных частиц fчаст в Cu–Cr–Zr сплаве. Заполненные значки – закалка, прозрачные – старение.
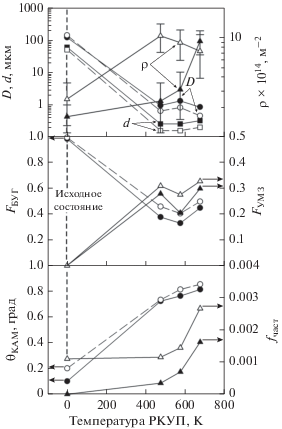
После РКУП в образцах наблюдали высокую плотность дислокаций (рис. 3). В закаленном сплаве с повышением температуры деформации с 473 до 673 K плотность дислокаций увеличивается с 2 × 1014 до 9 × 1014 м–2, в то же время в состаренном сплаве плотность дислокаций незначительно снижается с ростом температуры деформации с 1 × 1015 до 7 × 1014 м–2. С ростом температуры деформации происходит небольшой рост внутренних микронапряжений вне зависимости от исходного состояния в пределах 0.70°–0.85°. Деформация при повышенных температурах приводит к распаду ПТР и (до)выделению дисперсных частиц в сплаве вне зависимости от предварительной ТО. Объемная доля частиц в сплаве после старения в 1.5–3 раза выше, чем в сплаве после закалки. С увеличением температуры деформации это различие уменьшается.
2. Физико-механические свойства Cu–Cr–Zr-сплава
После закалки сплав характеризуется относительно низким пределом текучести и высоким удлинением. Старение увеличивает предел текучести на 100 МПа и уменьшает относительное удлинение на 25% (рис. 4). Деформация при повышенной температуре приводит к росту предела текучести, предела прочности и снижению относительного удлинения. В сплавах после предварительной закалки предел текучести и предел прочности увеличиваются с ростом температуры деформации и составляют 465–490 и 475–530 МПа соответственно. Предел текучести в Cu–Cr–Zr-сплаве после старения не изменяется с ростом температуры деформации. Предел прочности после деформации при температуре 473–573 K составляет 550 МПа. Наибольший предел прочности наблюдается после деформации при температуре 673 К и составляет 570 МПа. Относительное удлинение после деформации при температурах 473–573 K составляет 7–9% вне зависимости от предварительной ТО. Увеличение температуры деформации до 673 K приводит к росту пластичности до 20 и 22% для закаленных и состаренных образцов, соответственно.
Рис. 4.
а – Кривые “Напряжение – деформация” Cu–Cr–Zr сплава после закалки и старения с последующим РКУП при температуре 473, 573, 673 K. б – Влияние температуры РКУП на твердость (⚫, ⚪) и электропроводность (△, ▲) Cu–Cr–Zr сплава. Заполненные значки – закалка, прозрачные – старение.
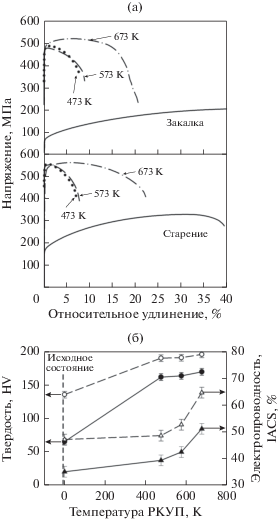
Твердость незначительно увеличивается с увеличением температуры деформации с 161 до 169 HV в предварительно закаленном сплаве и с 189 до 195 HV в состаренном сплаве. Отметим, что изменение данных значений находится в пределах погрешности измерений твердости. Электрическая проводимость в исходном состоянии сплава после закалки составляет 35% IACS (процент от электрической проводимости чистой отожженной меди), а после старения – 47% IACS. РКУП при повышенной температуре приводит к росту проводящих характеристик в Cu–Cr–Zr-сплаве вне зависимости от предварительной ТО, причем с ростом температуры деформации наблюдается рост проводящих характеристик. Максимальная проводимость Cu–Cr–Zr-сплава после закалки и деформации составляет 51% IACS, после старения и деформации – 65% IACS.
3. Влияние деформационного старения на структуру и свойства Cu–Cr–Zr сплава
Повышение электрической проводимости Cu–Cr–Zr-сплава свидетельствует о распаде ПТР в процессе деформации и выделении дисперсных частиц, т.е. деформационном старение, что подтверждается данными ПЭМ. Доля распада пересыщенного твердого раствора fрасп может быть выражена с использованием текущих значений удельного электрического сопротивления Ω (величина, обратная удельной электрической проводимости) следующим образом [14]:
(2)
${{f}_{{{\text{расп}}}}} = \frac{{\Omega - {{\Omega }_{0}}}}{{{{\Omega }_{{\max }}} - {{\Omega }_{0}}}},$(3)
$\Delta g = - \frac{{kT}}{{{{\nu }_{{{\text{at}}}}}}}\ln \left( {\frac{C}{{{{C}_{{{\text{eq}}}}}}}} \right),$Рис. 5.
а – Влияние температуры деформации на распад пересыщенного твердого раствора. б – Зависимость объемной доли частиц (fчаст), размера зерен (D), микронапряжений (θKAM) и плотности дислокаций (ρ) от распада пересыщенного твердого раствора. Заполненные значки – закалка, прозрачные – старение.
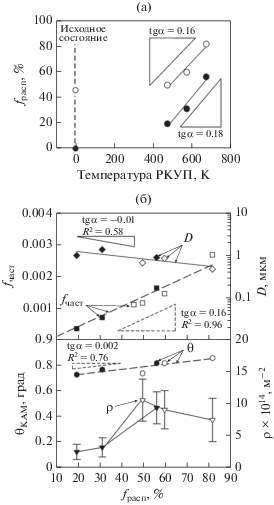
Если предположить, что в закаленном сплаве концентрация Cr в матрице составляет 0.003, а циркония 0.002 (соответствует предельной растворимости Zr в медной матрице [9]), а в состаренном сплаве согласно рассчитанной доли распада ПТР концентрация Cr в матрице составляет 0.00093, а циркония 0.00062, то движущая сила выделения дисперсных частиц в соответствии с уравнением (3) в 1.7 раза больше для предварительно закаленного сплава.
Отметим, что объемная доля выделившихся частиц, наблюдаемых в ПЭМ, хорошо коррелирует с долей распада пересыщенного твердого раствора (коэффициент достоверности аппроксимации R2 = 0.96). С повышением доли распада ПТР наблюдается тенденция к усилению локализации деформации внутри деформационных полос (рис. 1), а также увеличению плотности дислокаций, уровня микронапряжений и снижению среднего размера зерен (рис. 5) в Cu–Cr–Zr-сплаве. Выделение дисперсных частиц из ПТР в процессе деформации может приводить к замедлению динамического возврата и способствовать повышению плотности дислокаций, что соответствует увеличению микронапряжений в сплаве. Частицы, как дополнительные препятствия, могут проявлять себя в качестве эффективных точек закрепления дислокаций и снижать их подвижность, способствуя выгибанию дислокаций и формированию новых дислокационных петель. Увеличение плотности дислокаций и соответствующий рост микронапряжений способствуют фрагментации микроструктуры – формированию границ зерен деформационного происхождения. В то же время с повышением температуры деформации активизируются процессы динамического возврата, которые, с одной стороны, уменьшают плотность дислокаций, а с другой – способствуют непрерывной динамической рекристаллизации. Дисперсионное упрочнение из-за выделяющихся частиц и динамический возврат, как два конкурирующих процесса, контролируют скорость развития динамической рекристаллизации, размер зерен и плотность дислокаций, что может быть причиной разной тенденции изменения плотности дислокаций в предварительно закаленном и состаренном сплаве с ростом температуры деформации. Размер зерен и плотность дислокаций оказывают влияния на прочностные свойства сплава в соответствии с известными соотношениями Холла–Петча и Тейлора, соответственно [8]. Выделение дисперсных частиц в процессе деформации обеспечивает повышение прочностных свойств медных сплавов не только за счет дисперсионного упрочнения, но и опосредованно влияет на увеличение дислокационного и зернограничного упрочнения.
Деформационное старение приводит к увеличению числа структурных дефектов, формирующихся в процессе деформации, таких как частицы, дислокации, границы зерен, на которых может происходить рассеяние электронов в процессе их движения при приложении разности потенциалов. Однако в эксперименте наблюдается увеличение электропроводности с увеличением доли распада ПТР и с ростом плотности дислокаций и границ зерен (величина обратная размеру зерна). Полученные экспериментальные данные могут быть объяснены разной степенью влияния дислокаций, границ кристаллитов и атомов замещения на проводимость металлических материалов. Именно атомы замещения оказывают основное влияние на проводящие характеристики медных сплавов [1, 9]. Повышение проводимости за счет уменьшения концентрации легирующих элементов в твердом растворе в значительной степени превосходит снижение проводящих свойств из-за рассеяния электронов на остальных структурных дефектах. Поэтому выделение дисперсных частиц до или в процессе деформации принципиально необходимо для формирования оптимальной структуры, обеспечивающей высокую прочность и электропроводность Cu–Cr–Zr-сплавов.
На основании полученных результатов была разработана графическая модель влияния температуры деформации на структуру Cu–Cr–Zr-сплава, проиллюстрированная на рис. 6. Повышение температуры деформации способствует распаду пересыщенного твердого раствора и выделению дисперсных частиц, которые обеспечивают локализацию деформации в деформационных полосах и способствуют накоплению повышенной плотности дислокаций, что приводит к формированию структуры с меньшим размером кристаллитов, большей долей БУГ и УМЗ-структуры.
ЗАКЛЮЧЕНИЕ
РКУП сплава Cu–0.3% Cr–0.5% Zr при повышенной температуре приводит к формированию густой сетки МУГ деформационного происхождения и областей УМЗ-структуры, что обеспечивает значительное увеличение прочностных свойств.
Деформация при повышенных температурах способствует распаду ПТР и выделению дисперсных частиц, причем с ростом температуры деформации доля распада ПТР увеличивается.
Выделение дисперсных частиц в процессе деформации способствует ее локализации в деформационных полосах, снижению размера зерна, повышению плотности дислокаций, доли БУГ и УМЗ-структуры.
Предварительное старение сплава повышает эффективность РКУП с точки зрения улучшения прочности и электропроводности. Прочность сплава после старения и РКУП при 673 К составляет 570 МПа при электропроводности 65% IACS.
Работа выполнена при финансовой поддержке Министерства Образования и Науки РФ в рамках программы Грант Президента для государственной поддержки молодых российских ученых (Соглашение № 075-15-2020-407 от 18.03.2020).
Список литературы
Murashkin M.Y., Sabirov I., Sauvage X., Valiev R.Z. Nanostructured Al and Cu alloys with superior strength and electrical conductivity // J. Mater. Sci. 2016. V. 51. № 1. P. 33–49.
Zel’dovich V.I., Dobatkin S.V., Frolova N.Y., Khomskaya I.V., Kheifets A.E., Shorokhov E.V., Nasonov P.A. Mechanical properties and the structure of chromium–zirconium bronze after dynamic channel-angular pressing and subsequent aging // Phys. Met. Metal. 2016. V. 117. № 1. P. 74–82.
Liang N., Liu J., Lin S., Wang Y., Wang J. T., Zhao Y., Zhu Y. A multiscale architectured CuCrZr alloy with high strength, electrical conductivity and thermal stability // J. Alloys Compd. 2018. V. 735. P. 1389–1394.
Vinogradov A., Suzuki Y., Ishida T., Kitagawa K., Kopylov V. I. Effect of Chemical Composition on Structure and Properties of Ultrafine Grained Cu–Cr–Zr Alloys Produced by Equal-Channel Angular Pressing // Mater. Trans. 2004. V. 45. № 7. P. 2187–2191.
Мелёхин Н.В., Чувильдеев В.Н. Влияние равноканально–углового прессования на процесс выделения частиц в сплаве Cu–Cr–Zr // ФТТ. Вестник Нижегородского университета им. Лобачевскогою. 2011. № 5. С. 55–61.
Chbihi A., Sauvage X., Blavette D. Atomic scale investigation of Cr precipitation in copper // Acta Mater. 2012. V. 60. № 11. P. 4575–4585.
Fuxiang H., Jusheng M., Honglong N., Zhiting G., Chao L., Shumei G., Xuetao Y., Tao W., Hong L., Huafen L. Analysis of phases in a Cu–Cr–Zr alloy // Scr. Mater. 2003. V. 48. № 1. P. 97–102.
Shangina D.V., Terent’ev V.F., Prosvirnin D.V., Antonova O.V., Bochvar N.R., Gorshenkov M.V., Raab G.I., Dobatkin S.V. Mechanical Properties, Fatigue Life, and Electrical Conductivity of Cu–Cr–Hf Alloy after Equal Channel Angular Pressing // Adv. Eng. Mater. 2018. V. 20. № 1. P. 1700536.
Morozova A., Mishnev R., Belyakov A., Kaibyshev R. Microstructure and properties of fine grained Cu–Cr–Zr alloys after termo-mechanical treatments // Rev. Adv. Mater. Sci. 2018. V. 54. № 1. P. 56–92.
Исламгалиев Р.К., Нестеров К.Н., Валиев Р.З. Структура, прочность и электропроводность медного сплава Cu–Cr подвергнутого интенсивной пластической деформации // ФММ. 2015. Т. 116. № 2. С. 219–228.
Murayama M., Belyakov A., Hara T., Sakai Y., Tsuzaki K., Okubo M., Eto M., Kimura T. Development of a high-strength high-conductivity Cu–Ni–P alloy. Part I: Characterization of precipitation products // J. Electron. Mater. 2006. V. 35. № 10. P. 1787–1792.
Zhilyaev A. P., Shakhova I., Morozova A., Belyakov A., Kaibyshev R. Grain refinement kinetics and strengthening mechanisms in Cu–0.3Cr–0.5Zr alloy subjected to intense plastic deformation // Mater. Sci. Eng. A. 2016. V. 654. P. 131–142.
Humphreys F.J., Hatherly M. Recrystallization and related annealing phenomena. Elsevier, 2012. 635 p.
Zhang Y., Volinsky A.A., Tran H.T., Chai Z., Liu P., Tian B., Liu Y. Aging behavior and precipitates analysis of the Cu–Cr–Zr–Ce alloy // Mater. Sci. Eng. A. 2016. V. 650. P. 248–253.
Aaronson H.I., Kinsman K.R., Russell K.C. The volume free energy change associated with precipitate nucleation // Scripta Metall. 1970. V. 4. № 2. P. 101–106.
Дополнительные материалы отсутствуют.
Инструменты
Физика металлов и металловедение