Физика металлов и металловедение, 2021, T. 122, № 1, стр. 74-80
Влияние теплого равноканального углового прессования на структуру и механические свойства сплава Al–Mg–Ca–Mn–Fe–Zr
С. О. Рогачев a, *, Е. А. Наумова a, b, Р. Д. Карелин a, c, В. А. Андреев c, d, М. М. Перкас c, В. С. Юсупов c, В. М. Хаткевич a
a Национальный исследовательский технологический университет “МИСиС”
119049 Москва, Ленинский просп., 4, Россия
b МГТУ “Станкин”
127994 Москва, Вадковский пер., 1, Россия
c Институт металлургии и материаловедения имени А.А. Байкова РАН
119334 Москва, Ленинский просп., 49, Россия
d ООО “Промышленный центр МАТЭК-СПФ”
117449 Москва, ул. Карьер, 2А/1, Россия
* E-mail: csaap@mail.ru
Поступила в редакцию 11.08.2020
После доработки 09.09.2020
Принята к публикации 14.09.2020
Аннотация
Изучено влияние равноканального углового прессования (РКУП) на структуру, механические свойства и термическую стабильность сплава Al–5% Mg–1% Ca–0.9% Mn–0.5% Fe–0.1% Zr. РКУП проводили на образцах сплава в отожженном состоянии по режиму: температура 400°С, маршрут BC, угол пересечения каналов 110° и число проходов N = 8. В результате РКУП в сплаве формируется субструктура с высокой плотностью дислокаций, содержащая выделения наноразмерных частиц Al6(Mn, Fe) и Al3Zr. РКУП приводит к повышению как прочности, так и пластичности сплава: прочностные свойства сплава после РКУП увеличились в 1.3–1.5 раза, а относительное удлинение – в 2.0–2.5 раза по сравнению с исходным состоянием.
ВВЕДЕНИЕ
Алюминиевые сплавы широко применяются в качестве конструкционного материала в таких сферах, как авиа-, автомобиле- и приборостроение, космическая техника и др. Это связано с уникальным комплексом свойств алюминиевых сплавов – малой плотностью, коррозионной стойкостью, пластичностью, высокой электропроводностью [1, 2].
Сплавы системы Al–Mg относятся к термически неупрочняемым и характеризуются сочетанием удовлетворительной прочности и пластичности, хорошей свариваемости и коррозионной стойкости, в т.ч. в морской воде и морской атмосфере [3]. Кроме того, эти сплавы отличаются повышенной усталостной прочностью. Увеличение концентрации магния на каждый процент содержания повышает предел прочности сплава на ~30 МПа, а предел текучести – на ~20 МПа. В то же время увеличение содержания магния свыше 6% приводит к ухудшению коррозионной стойкости сплава. Поэтому наиболее широкое распространение в промышленности получили сплавы с содержанием магния от 1 до 5%.
Для улучшения прочностных характеристик сплавы системы Al–Mg легируют. Добавка марганца дополнительно упрочняет алюминиевый твердый раствор. Железо и кальций образуют с алюминием тройное соединение эвтектического происхождения, состав которого отвечает формуле Al10CaFe2, кристаллизующееся в компактной форме, что положительно влияет на механические свойства [4]. Добавление малых количеств Zr или Sc в сплав Al–Mg может значительно улучшить прочность при сохранении высокой коррозионной стойкости и свариваемости [5, 6]. Выделившиеся при старении частицы Al3Zr или Al3Sc могут сильно закреплять дислокации и границы зерен, улучшая механические свойства сплава, и в то же время препятствовать разупрочнению при рекристаллизации [7–9]. Однако даже дисперсно-упрочненные Al–Mg сплавы обладают средним уровнем прочности. Расширение применимости Al–Mg сплавов возможно за счет улучшения их механических свойств.
Известно, что получение в алюминиевых сплавах ультрамелкозернистого состояния методами больших пластических деформаций (англ. Severe Plastic Deformations) существенно улучшает комплекс их механических свойств [10–13]. Перспективным методом, позволяющим получать ультрамелкозернистую структуру в массивных образцах алюминиевых сплавов, является равноканальное угловое прессование (РКУП) [14–18]. Большая доля этих работ посвящена исследованию сплавов Al–Mg и Al–Mg–Sc. В то же время влияние добавок кальция, железа и циркония в Al–Mg сплавах на их поведение при больших пластических деформациях практически не изучали.
В данной работе изучено влияние теплого равноканального углового прессования на структуру и механические свойства сплава Al–Mg–Ca–Mn–Fe–Zr.
МАТЕРИАЛЫ И МЕТОДИКИ ИССЛЕДОВАНИЯ
В качестве материала для исследования использовали литой алюминиевый сплав следующего химического состава: Al–5% Mg–1% Ca–0.9% Mn–0.5% Fe–0.1% Zr. Сплав перед РКУП подвергали отжигу (Т = 400°С, 1 ч).
РКУП проводили на образцах сплава диаметром 20 мм и длиной 100 мм в изотермических условиях при температуре 400°С, используя маршрут BC, угол пересечения каналов 110° и число проходов N = 8. Температуру РКУП выбирали, исходя из известной температуры прокатки Al‒Mg-сплавов, которая составляет 400–450°С.
Образцы после РКУП электроискровым методом резали на пластины толщиной 1 мм в направлениях, нормальном и продольном направлению прессования.
Металлографический анализ структуры проводили на оптическом микроскопе AxioObserver D1m CarlZeiss и сканирующем микроскопе JSM-IT500 (JEOL) с ЭДС.
Электронно-микроскопические исследования структуры сплава после РКУП проводили в сечении, продольном направлению прессования, на тонких фольгах с помощью электронного микроскопа JEM-2100 (JEOL) с ЭДС. Размер структурных элементов (частиц вторых фаз) рассчитывали по светлопольным ПЭМ-фотографиям с использованием программы ImageExpert.
Измерения микротвердости сплава в исходном состоянии и после РКУП осуществляли методом Виккерса (нагрузка 1 N, время выдержки 10 с) с помощью микротвердомера MICROMET 5101 с цифровой камерой и программы “ImageExpert MicroHardness 2”. Микротвердость сплава после РКУП измеряли в сечениях, нормальном и продольном направлению прессования. В нормальном сечении измерения проводили с шагом 1 мм на двух взаимно-перпендикулярных диаметрах (по 3 измерения на точку), а в продольном сечении – с шагом 5 мм на расстоянии 1 мм от края и в середине прутка (по 3 измерения на точку). Схема измерения микротвердости приведена на рис. 1.
Рис. 1.
Схема измерения микротвердости на образце алюминиевого сплава после РКУП (сверху – нормальное сечение, снизу – продольное сечение).
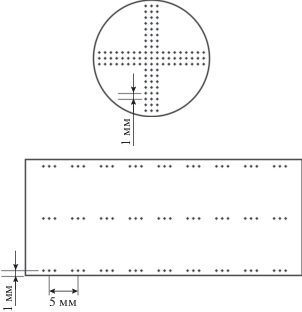
Испытания на одноосное растяжение образцов сплава в исходном отожженном состоянии, после РКУП, а также после постдеформационного отжига проводили на универсальной испытательной машине INSTRON-5966 при комнатной температуре со скоростью растяжения 1 и 20 мм/мин. Разрывные образцы после РКУП вырезали в направлениях, нормальном и продольном направлению прессования. Использовали плоские образцы в форме “лопаток” общей длиной 40 мм, толщиной 1.0 мм, размерами рабочей части 20 × × 3.5 мм, полученные методом электроэрозионной резки с последующей механической шлифовкой поверхности. Ввиду ограниченного размера нормального сечения (20 мм) прутка после РКУП, для растяжения использовали миниатюрные образцы общей длиной 12 мм и размерами рабочей части 5 × 1.45 мм. Испытывали не менее трех образцов на точку.
Анализ изломов образцов после испытания на растяжение проводили на сканирующем микроскопе JSM-IT500 (JEOL) при увеличениях ×30–3000.
Для изучения термической стабильности упрочнения образцы после РКУП нагревали в камерной электропечи в интервале температур от 100 до 450°С (с шагом в 50°С и выдержкой 1 ч). Термическую стабильность оценивали по изменению микротвердости (по 6 измерений на точку).
РЕЗУЛЬТАТЫ И ОБСУЖДЕНИЕ.
Влияние РКУП на структуру сплава Al–Mg–Ca–Mn–Fe–Zr. По данным оптической микроскопии структура сплава в исходном отожженном состоянии состояла из твердого раствора (Al) и крупных выделений размером до 20 мкм (рис. 2а). По данным СЭМ и ЭДС в структуре сплава присутствуют крупные выделения типа Al6(Mn,Fe), Al10CaFe2 и Al4Ca. После РКУП наблюдается формирование деформированной структуры и дробление исходных крупных частиц (рис. 2б).
Рис. 2.
Структура сплава Al–Mg–Ca–Mn–Fe–Zr в исходном отожженном состоянии (после отжига) (а) и после РКУП (б) (ОП).
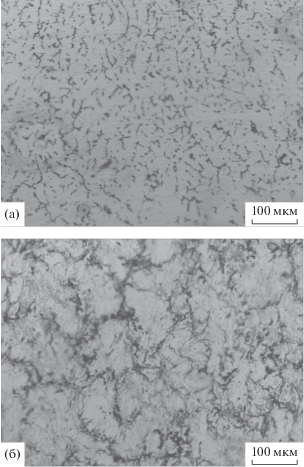
Согласно данным просвечивающей микроскопии, в результате РКУП в сплаве сформировалась субструктура с высокой плотностью дислокаций, в т. ч. с образованием дислокационных стенок (рис. 3а, 3б). Электронограмма соответствует крупнокристаллической структуре (рис. 3а). В структуре также выявлены выделения наноразмерных частиц Al6(Mn,Fe) размером ~20 нм, а также малое количество наноразмерных частиц Al3Zr (рис. 3б, 3в). Наличие указанных частиц в структуре сплава после РКУП может быть связано с их выделением при предварительном (перед РКУП) отжиге, а также с самим процессом теплого РКУП.
Влияние РКУП на механические свойства сплава Al–Mg–Ca–Mn–Fe–Zr. Микротвердость сплава отожженного состояния составила 0.84 ± 0.04 ГПа (86 ± 4 HV). Известно, что при деформировании заготовки методом РКУП распределение напряжений и деформаций в объеме заготовки может быть неоднородным. Поэтому для изучения однородности деформации заготовки после РКУП были измерены значения микротвердости в сечениях, нормальном и продольном направлению прессования. Результаты измерения микротвердости показали ее однородное распределение в объеме заготовки (рис. 4). Усредненные значения микротвердости составили 1.01 ± 0.04 ГПа (103 ± ± 4 HV) в нормальном сечении и 1.11 ± 0.04 ГПа (113 ± 4 HV) в продольном сечении. Таким образом, в результате РКУП значения микротвердости сплава увеличились в 1.2–1.3 раза.
Рис. 4.
Распределение значений микротвердости в продольном (а) и нормальном (б) сечениях образца сплава Al–Mg–Ca–Mn–Fe–Zr после РКУП.
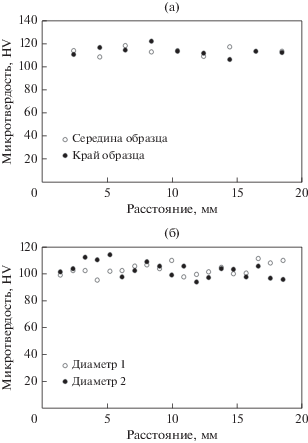
Диаграммы деформации сплава в различных состояниях в координатах “условное напряжение – условная деформация” приведены на рис. 5, а значения механических характеристик – в табл. 1. Пределы текучести и прочности сплава исходного отожженного состояния составили 177 ± 2 и 238 ± 1 МПа, соответственно, при относительном удлинении 7 ± 1%. В результате РКУП наблюдается существенное повышение как прочности, так и пластичности сплава. Пределы текучести и прочности сплава после РКУП в продольном направлении составили 242 ± 2 и 350 ± 3 МПа, соответственно, при относительном удлинении 14 ± 1%. Пределы текучести и прочности сплава после РКУП в поперечном направлении составили 240 ± 2 и 325 ± 3 МПа, соответственно, при относительном удлинении 18 ± 2%. Таким образом, прочностные характеристики сплава после РКУП увеличились в 1.3–1.5 раза, а относительное удлинение – в 2.0–2.5 раза по сравнению с отожженным состоянием. Увеличение скорости растяжения с 1 до 20 мм/мин слабо влияет на прочностные свойства сплава, но понижает его пластичность на ~30%.
Рис. 5.
Диаграммы деформации сплава Al–Mg–Ca–Mn–Fe–Zr в различных состояниях (скорость растяжения 1 мм/мин): 1 – в исходном отожженном состоянии; 2 – после РКУП в продольном направлении; 3 – после РКУП в поперечном направлении.
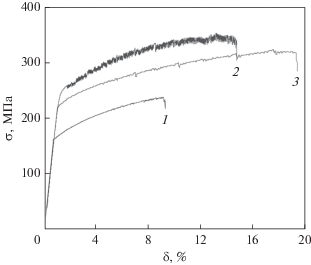
Таблица 1.
Механические характеристики сплава Al–Mg–Ca–Mn–Fe–Zr в различных состояниях (для скоростей растяжения 1 и 20 мм/мин)
Обработка | σ0.2, МПа | σB, МПа | δ, % |
---|---|---|---|
Исходное отожженное состояние | 177 ± 2/– | 238 ± 1/– | 7 ± 1/– |
РКУП (продольное направление) | 242 ± 2/238 ± 2 | 350 ± 3/339 ± 2 | 14 ± 1/10 ± 1 |
РКУП (поперечное направление) | 240 ± 2/246 ± 2 | 325 ± 3/317 ± 2 | 18 ± 2/12 ± 1 |
РКУП (продольное направление) + отжиг 400°С, 1 ч | 227 ± 2/– | 332 ± 3/– | 12 ± 1/– |
РКУП (поперечное направление) + отжиг 400°С, 1 ч | 245 ± 2/– | 327 ± 3/– | 8 ± 1/– |
Можно заключить, что сплав после РКУП обладает наилучшим сочетанием прочности и пластичности.
Следует отметить наличие на кривых “напряжения–деформация” эффекта Портвена–Ле Шателье, проявляющегося в виде скачкообразной деформации на стадии равномерной пластической деформации, характерного для Al–Mg-сплавов и характеризующего нестабильность пластического течения [19–23].
Эффект Портвена–Ле Шателье слабо проявляется для образцов в отожженном состоянии и для поперечных образцов после РКУП и значительно усиливается для продольных образцов после РКУП. При увеличении скорости растяжения с 1 до 20 мм/мин эффект сохраняется, при этом размах скачков увеличивается, а их количество уменьшается (рис. 6). Считается, что основным механизмом возникновения эффекта Портвена–Ле Шателье является динамическое старение под напряжением – блокировка дислокаций из-за их взаимодействия с атмосферами вторых фаз и растворенных атомов [24]. В результате РКУП плотность дислокаций в сплаве существенно повышается, следовательно, для их движения требуется большее напряжение.
Рис. 6.
Диаграмма деформации сплава Al–Mg–Ca–Mn–Fe–Zr после РКУП в продольном направлении (скорость растяжения 20 мм/мин).
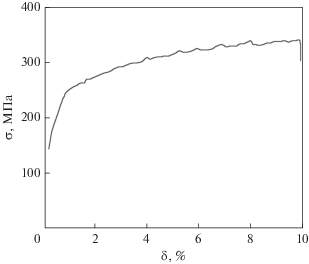
Как только дислокации освобождаются, происходит быстрое падение напряжения до тех пор, пока дислокации снова не будут заблокированы, что отображается на диаграммах деформации в виде “зубьев”. Видимо, в продольных образцах движение дислокаций более затруднено, чем в поперечных (это подтверждается меньшей пластичностью продольных образцов по сравнению с поперечными), что приводит к усилению эффекта Портвена–Ле Шателье. Ранее усиление эффекта Портвена–Ле Шателье в алюминиевых сплавах наблюдали при измельчении зерна, например, в результате легирования цирконием [24].
Поверхности изломов образцов сплава Al–Mg–Ca–Mn–Fe–Zr после испытания на растяжение показаны на рис. 7. Поверхность излома сплава исходного отожженного состояния на макроуровне плоская, однако на микроуровне рельеф более развитый. Микростроение излома преимущественно хрупкое, основной механизм разрушения квазискол (рис. 7а, 7б). В то же время присутствуют области вязкого разрушения в виде вязких перемычек и плоских ямок.
Рис. 7.
Поверхности изломов разрывных образцов сплава Al–Mg–Ca–Mn–Fe–Zr в исходном отожженном состоянии (а, б) и после РКУП (в, г) (СЭМ).
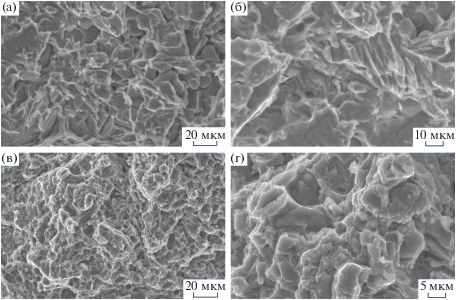
Рельеф поверхности излома образцов сплава в состоянии после РКУП значительно более развитый, что говорит о повышении энергоемкости разрушения. Излом имеет преимущественно ямочное строение (рис. 7в, 7г). Присутствуют как более крупные (3–5 мкм в диаметре) ямки, так и более мелкие (менее 1 мкм в диаметре). В то же время в изломе сохраняются области хрупкого разрушения в виде фасеток квазискола.
Таким образом, наиболее предпочтительный характер разрушения наблюдается для сплава после РКУП.
Влияние нагрева после РКУП на механические свойства сплава Al–Mg–Ca–Mn–Fe–Zr. При постдеформационном отжиге в интервале температур от 100 до 450°С сплава, подвергнутого РКУП, наблюдается слабая тенденция к снижению микротвердости, однако в целом влияние отжига на твердость невелико (рис. 8). Не исключено, что в процессе нагрева в структуре сплава могут одновременно протекать несколько процессов: аннигиляция дефектов кристаллической решетки, приводящая к разупрочнению сплава, и дополнительное выделение частиц вторых фаз (Al3Zr), приводящее к упрочнению сплава. Колебания значений микротвердости сплава после отжигов могут быть связаны с конкуренцией вышеуказанных процессов.
Были дополнительно проведены испытания на растяжение образцов сплава после РКУП и последующего отжига при температуре 400°С. Значения механических свойств приведены в табл. 1.
Пределы текучести и прочности сплава после РКУП и постдеформационного отжига при температуре 400°С (1 ч) составили 227 ± 2 и 332 ± 3 МПа, соответственно, для образцов продольного направления, при относительном удлинении 12 ± 1%. Для образцов поперечного направления пределы текучести и прочности составили 245 ± 2 и 327 ± 3 МПа, соответственно, при относительном удлинении 8 ± 1%. При этом на диаграммах растяжения сохраняется проявление эффекта Портвена–Ле Шателье.
Таким образом, постдеформационный отжиг слабо влияет на прочностные свойства сплава, но приводит к снижению пластичности, что особенно заметно для поперечных образцов.
ВЫВОДЫ
1. В результате РКУП (400°С; N = 8) сплава Al–5% Mg–1% Ca–0.9% Mn–0.5% Fe–0.1% Zr формируется субструктура с высокой плотностью дислокаций, содержащая выделения наноразмерных частиц Al6(Mn,Fe) и Al3Zr;
2. РКУП приводит к повышению как прочности, так и пластичности сплава при формировании преимущественно вязкого ямочного излома: прочностные характеристики сплава после РКУП увеличились в 1.3–1.5 раза, а относительное удлинение – в 2.0–2.5 раза по сравнению с исходным состоянием;
3. Постдеформационный отжиг (400°С, 1 ч) после РКУП слабо влияет на прочностные свойства сплава, но приводит к снижению пластичности, особенно для поперечных образцов.
Работа выполнена в рамках государственного задания ИМЕТ РАН № 075-00947-20-00.
Список литературы
Polmear I. Light alloys. From traditional alloys to nanocrystals. Elsevier, 2006. 421 p.
Glazoff M., Zolotorevsky V., Belov N. Casting Aluminum Alloys, 1st Edition. Elsevier Science, 2007. 544 p.
Kaufman J.G., Rooy E.L. Aluminum alloy castings: properties, processes and applications. ASM International, Materials Park, USA, 2004
Шуркин П.К., Долбачев А.П., Наумова Е.А., Дорошенко В.В. Влияние железа на структуру, упрочнение и физические свойства сплавов системы Al–Zn–Mg–Ca // Цветные металлы. 2018. № 5. С. 69–76.
Alil A., Popović M., Radetić T., Zrilić M., Romhanji E. Influence of annealing temperature on the baking response and corrosion properties of an Al–4.6 wt. % Mg alloy with 0.54 wt. % Cu // J. Alloys Compd. 2015. V. 625. P. 76–84.
Zhou S., Zhang Z., Li M., Pan D., Su H., Du X., Wu Y. Effect of Sc on microstructure and mechanical properties of as-cast Al–Mg alloys // Mater. Des. 2016. V. 90. P. 1077–1084.
Li M.J., Pan Q.L., Shi Y.J., Wang Y. Microstructure dependent fatigue crack growth in Al–Mg–Sc alloy // Mater. Sci. Eng. A. 2014. V. 611. P. 142–151.
Kumar N., Mishra R.S. Additivity of strengthening mechanisms in ultrafine grained Al–Mg–Sc alloy // Mater. Sci. Eng. A. 2013. V. 580. P. 175–183.
Liu F.C., Xue P., Ma Z.Y. Microstructural evolution in recrystallized and unrecrystallized Al–Mg–Sc alloys during superplastic deformation // Mater. Sci. Eng. A. 2012. V. 547. P. 55–63.
Orlov D., Beygelzimer Y., Synkov S., Varyukhin V., Tsuji N., Horita Z. Plastic flow, structure and mechanical properties in pure Al deformed by twist extrusion // Mater. Sci. Eng. A. 2009. V. 519. P. 105–111.
Leo P., Cerri E., De Marco P.P., Roven H.J. Properties and deformation behaviour of severe plastic deformed aluminium alloys // J. Mater. Proces. Techn. 2007. V. 182. P. 207–214.
Khmelevskaya I.Yu., Karelin R.D., Prokoshkin S.D., Andreev V.A., Yusupov V.S., Perkas M.M., Prosvirnin V.V., Shelest A.E., Komarov V.S. Effect of the quasi-continuous equal-channel angular pressing on the structure and functional properties of Ti–Ni-based shape-memory alloys // Phys. Met. Metallogr. 2017. V. 118. P. 279–287.
Andreev V.A., Yusupov V.S., Perkas M.M., Prosvirnin V.V., Shelest A.E., Prokoshkin S.D., Khmelevskaya I.Yu., Korotitskii A.V., Bondareva S.A., Karelin R.D. Mechanical and runctional properties of commercial alloy TN-1 semiproducts fabricated by warm rotary forging and ECAP // Russ. Metall. 2017. V. 2017. P. 890–894.
Shaeri M.H., Shaeri M., Ebrahimi M., Salehi M.T., Seyyedein S.H. Effect of ECAP temperature on microstructure and mechanical properties of Al–Zn–Mg–Cu alloy // Progr. Natural Sci.: Mater. Intern. 2016. V. 26. P. 182–191.
Nikulin S.A., Dobatkin S.V., Khanzhin V.G., Rogachev S.O., Chakushin S.A. Effect of submicrocrystalline structure and inclusions on the deformation and failure of aluminum alloys and titanium // Metal Science and Heat Treatment. 2009. V. 51. P. 208–217.
Angella G., Bassani P., Tuissi A., Ripamonti D., Vedani M. Microstructure evolution and aging kinetics of Al–Mg–Si and Al–Mg–Si–Sc alloys processed by ECAP // Mater. Sci. Forum. 2006. V. 503–504. P. 493–498.
Маркушев М.В., Мурашкин М.Ю. Прочность и трещиностойкость промышленных алюминиевых сплавов 1560 и 5083 системы Al–Mg–Mn после интенсивной пластической деформации угловым прессованием // ФММ. 2004. Т. 98. № 2. С. 116–128.
Лежнев С.Н., Волокитина И.Е., Куис Д.В. Эволюция микроструктуры и механических свойств композиционного сплава на основе алюминия при РКУП // ФММ. 2018. Т. 119. № 8. С. 858–864.
Cho C.-H., Son H.-W., Lee J.-C., Son K.-T., Lee J.-W., Hyun S.-K. Effects of high Mg content and processing parameters on Portevin-Le Chatelier and negative strain rate sensitivity effects in Al–Mg alloys // Mater. Sci. Eng. A. 2020. V. 779. Article 139151.
Cai Y., Yang S., Fu S., Zhang D. Qingchuan Zhang. Investigation of Portevin–Le Chatelier Band Strain and Elastic Shrinkage in Al-Based Alloys Associated with Mg Contents // J. Mater. Sci. Techn. 2017. V. 33. P. 580–586.
Thevenet D., Mliha-Touati M., Zeghloul A. Characteristics of the propagating deformation bands associated with the Portevin–Le Chatelier effect in an Al–Zn–Mg–Cu alloy // Mater. Sci. Eng. A. 2000. V. 291. P. 110–117.
Hu Q., Zhang Q., Fu S., Cao P., Gong M. Influence of precipitation on the Portevin-Le Chatelier effect in Al-Mg alloys // Theor. Appl. Mechan. Letters. 2011. V. 1. Article. 011007.
Jiang H., Zhang Q., Chen X., Chen Z., Jiang Z., Wu X., Fan J. Three types of Portevin–Le Chatelier effects: Experiment and modelling // Acta Materialia. 2007. V. 55. P. 2219–2228.
Nie X., Zhang H., Zhu H., Hu Z., Qi Y., Zeng X. On the role of Zr content into Portevin-Le Chatelier (PLC) effect of selective laser melted high strength Al–Cu–Mg–Mn alloy // Mater. Letters. 2019. V. 248. P. 5–7.
Дополнительные материалы отсутствуют.
Инструменты
Физика металлов и металловедение