Физика металлов и металловедение, 2021, T. 122, № 10, стр. 1054-1064
Влияние всесторонней ковки в условиях кратковременной ползучести на структуру и механические свойства алюмоматричного композита Al7075/10SiCp
Д. И. Крючков a, *, А. В. Нестеренко a, С. В. Смирнов a, Н. Б. Пугачева a, Д. И. Вичужанин a, Т. М. Быкова a
a Институт машиноведения УрО РАН
620049 Екатеринбург, ул. Комсомольская, 34, Россия
* E-mail: kru4koff@bk.ru
Поступила в редакцию 05.11.2020
После доработки 16.06.2021
Принята к публикации 18.06.2021
Аннотация
Исследовано влияние предварительной деформационно-термической обработки в виде всесторонней ковки в условиях кратковременной высокотемпературной ползучести на микроструктуру и механические свойства композиционного материала на основе высокопрочного алюминиевого сплава системы Al–Cu–Mg–Zn (Al7075), упрочненного частицами SiC (10 мас. %). Экспериментально установлен наиболее эффективный режим кратковременной высокотемпературной ползучести. Определено, что при нагреве выше 500°С возникает лавинообразный рост значений скорости относительной деформации. Это обусловлено локальным появление жидкой фазы на границах между игольчатыми частицами S-фазы и твердым раствором на основе Al в матрице композита по эвтектическому превращению α-Al + S(Al2CuMg) → L. После деформационно-термической обработки произошло перераспределение армирующих частиц SiC, структура композита преобразовалась из ячеистой в равномерную. При этом выровнялись микромеханические свойства по объему композита. Увеличилось максимальное значение сопротивления деформации при испытании на осевое сжатие.
ВВЕДЕНИЕ
Алюмоматричные композитные материалы, дискретно армированные карбидом кремния, применяют в транспортном машиностроении, авиакосмической технике и других областях благодаря высоким показателям удельной прочности, износостойкости, теплопроводности [1–5]. При этом алюмоматричные композитные материалы, изготовленные методом порошковой металлургии, как правило, имеют неоднородную, ячеистую, крупнозернистую структуру с наличием микронесплошностей [6]. Для улучшения их структуры применяют предварительную обработку посредством интенсивной пластической деформации при высокой температуре. При использовании только термообработки принципиально не меняется структура материала и не улучшается деформируемость [7]. Часто применяют горячее выдавливание, после которого материал уже может иметь мелкозеренную структуру, что показано в работе Курбаткиной и др. [8]. При этом частицы карбида кремния наблюдаются как на границах, так и в объеме зерен. Однако для каждого конкретного материала оптимальный режим предварительной деформационно-термической обработки характеризуется специфическими условиями, и оказывает существенное влияние на комплекс механических свойств. Так, композит Al8009/15SiCp (p – означает “particles”, т.е. армирующая фаза используется в виде частиц карбид кремния) изготовленный по порошковой технологии, в исследовании Čadek J. и др. [9, 10], после консолидации и выдавливания при 557°С оказался значительно устойчивее к ползучести, чем такой же материал в исследовании Ma Z.Y. и Tjong S.C. [11], полученный прессованием при 450°С с последующим выдавливанием с коэффициентом вытяжки 20 при 460°С.
Отметим, что предварительная обработка не ограничена горячим выдавливанием, при котором происходит существенное уменьшение поперечного сечения заготовки. Более предпочтительным, по сравнению с выдавливанием, на наш взгляд, является процесс всесторонней ковки. Это эффективный способ деформационно-термической обработки, приводящей к формированию однородной микроструктуры с использованием относительно дешевого деформирующего инструмента и способствующей повышению эксплуатационных свойств изделия/полуфабриката. Процесс эффективно может применяться как для алюминиевых сплавов [12, 13], так и для алюмоматричных композитов. Например, Božić D. и др. в своей работе [14] получили параметры оптимальной области деформации алюмоматричного композитного материала Al6061/20SiCp, изготовленного по технологии “литье под давлением” (squeeze-cast). При 485°С и скорости деформации 0.16 с–1 проведена термо-деформационная обработка, включающая одноосную осадку и кантовку, после которой было отмечено улучшение микроструктуры и механических свойства композитов. В процессе такой обработки происходило затекание расплава в микропоры между частицами наполнителя SiC и снижение пористости. Более того, режим ковки дает возможность при завершающих кантовках уже получить заготовку, приближенную по форме к готовой детали. Последнее обстоятельство важно, поскольку при производстве готовых деталей из таких материалов необходимо минимизировать финишную обработку, при которой происходит быстрый износ режущего инструмента.
Однако стоит учитывать, что для эффективного протекания процесса всесторонней ковки необходимо обеспечивать достаточную степень деформации материала без разрушения. Известно, что горячее деформирование с низкой скоростью деформирования, в условиях мягкого нагружения, может благоприятно влить на формоизменение материалов склонных к хрупкому разрушению. Например, в работах [15, 16] описан механизм многоступенчатой термодеформационной обработки, при котором поэтапно достигается высокая степень деформации. Авторы, применив термоциклирование за 150 циклов (нагрев от 100 до 450°С за 200 с и принудительное охлаждение конвекцией за то же время) под давлением 6 Мпа, достигли значения относительного удлинения 325%, при этом средняя скорость деформации составила 2.5 × 10–6 с–1. Однако такой процесс достаточно сложный. На наш взгляд, проще проводить обработку в условиях высокотемпературной ползучести [17]. В зарубежной литературе такой процесс называется сreep age forming (CAF) [18]. В литературе широко представлены исследования на ползучесть композиционных материалов на основе деформируемых алюминиевых сплавов систем: Al–Mg–Cu (за рубежом – Al2124), Al–Mg–Si (Al6061), Al–Fe–V–Si (Al8009). В тоже время исследования материалов на основе высокопрочных алюминиевых сплавов системы Al–Cu–Mg–Zn (7000 серии) ограничены, в основном, результатами стандартных испытаний на растяжение при разных температурах [19–21]. Но наибольший интерес, с точки зрения практического применения, представляет кратковременная ползучесть. К сожалению, изучению деформируемости алюмоматричных композитов в условиях кратковременной высокотемпературной ползучести в литературе уделяется крайне мало внимания [22].
Из вышесказанного можно сделать вывод, что актуальной задачей является разработка способов получения заготовок из алюмоматричных композитов на основе высокопрочных алюминиевых сплавов, обладающих мелкозернистой структурой с равномерно распределенными по объему частицами. Поэтому была поставлена цель работы – оценить влияние всесторонней ковки в режиме кратковременной высокотемпературной ползучести на изменения микроструктуры и механических свойств алюмоматричного композиционного материала на основе высокопрочного алюминиевого сплава системы Al–Cu–Mg–Zn (Al7075), упрочненного частицами SiC.
МАТЕРИАЛ И МЕТОДИКА ИССЛЕДОВАНИЯ
Исследован алюмоматричный композиционный материал, изготовленный по порошковой технологии из гранулированного высокопрочного алюминиевого сплава 7075 и порошка карбида кремния SiC в количестве 10 мас. %. Гранулированный высокопрочный алюминиевый сплав системы Al–Zn–Mg–Cu имеет следующий химический состав, в мас. %: 5–7 Zn, 1.8–2.8 Mg, 1.4–2 Cu, до 0.5 Fe, до 0.5 Si, 0.2–0.6 Mn, 0.1–0.25 Сr, до 0.05 Ni до 0.05 Ti.
Поскольку на каждом проходе всесторонней ковки образцы из композита должны подвергаться высокой степени деформации без разрушения использовали режим кратковременной ползучести и предварительно определяли его наиболее эффективные параметры. При выборе эффективного режима кратковременной высокотемпературной ползучести опирались на результаты исследования, проведенного в работе [23], из которой следует, что при начальном давлении 5 МПа на образец (с размерами 3 мм в диаметре и 3 мм в высоту) наиболее эффективный режим деформации реализуется при нагреве до температуры 540–560°С. При этом деформация протекает за 80 мин и более, в зависимости от скорости нагрева. Поэтому для исследования был выбран нагрев именно до этого интервала температур. Для сокращения времени протекания процесса пробовали более высокие значения начального давления.
Определение эффективных параметров режима кратковременной ползучести проводили на цилиндрических образцах из Al7075/10SiC при начальных давлениях на образец 5, 8, 10 и 15 МПа на испытательной сервогидравлической установке INSTRON 8801 с нагревательной печью, имеющейся в комплекте. При испытании каждый образец помещался в холодную печь и нагревался до фиксированной температуры. Детальный режим нагрева при испытаниях представлен на рис. 1. При этом за все время нагрева на образец действовало давление, которое задавалось усилием на плунжер испытательной установки. Усилие, задаваемое на плунжер, не менялось, поэтому по мере деформации происходило увеличение площади контакта образца с инструментом, что приводило к уменьшению давления на образец. Во время испытаний отслеживали перемещение плунжера, время и температуру образца. После обработки данных рассчитывали скорость относительной деформации по формуле:
где Δε = εi+ 1 – εi – относительная деформация за промежуток времени Δt = ti + 1 – ti, при этом εi= = (h0 – hi)/h0, εi+ 1 = (h0 – hi + 1)/h0.После того, как были определены наиболее эффективные параметры режима кратковременной ползучести, они были использованы при обработке методом всесторонней ковки. Образец подвергали деформации в 3 прохода. В каждом проходе нагрев начинался в холодной печи и продолжался до 550°С, начальное давление на образец составляло 8 МПа. На рис. 2 приведена схема всесторонней ковки по проходам и фотография полученных образцов для испытаний механических свойств. В соответствии с принятой прямоугольной системой координат, деформация образца по проходам осуществлялась по осям 3 → 1 → 2. Поскольку при деформации использовали плоские бойки, то для устойчивости образцов, а также исследования микроструктуры после каждого прохода отрезали часть образца. Кантовку образца осуществляли на 90°, для последующей деформации в направлении перпендикулярном к плоскости реза.
Рис. 2.
Схема всесторонней ковки образца из алюмоматричного композитного материала Al7075/10SiCp по проходам (красным выделены плоскости реза): (а) I проход, (б) II проход, (в) III проход, (г) фотография вырезанных цилиндрических образцов для оценки механических свойств после трех проходов.
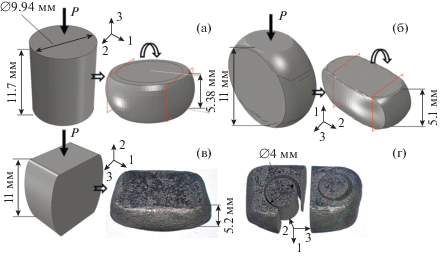
Для образца после всесторонней ковки исследована микроструктура с использованием оптического микроскопа NEOPHOT-21 и сканирующего электронного микроскопа Tescan Vega II XMU, а также проведен микрорентгеноспектральный анализ с использованием рентгеновского энергодисперсионного микроанализатора INCA ENERGY 450.
Из заготовки после трех проходов изготовлены цилиндрические образцы для оценки механических свойств на сжатие при температурах 20 и ‒50°С. Поверхность разрушения исследовали на сканирующем электронном микроскопе Tescan Vega II XMU. Микромеханические характеристики композита после всесторонней ковки определяли на инструментированном микротвердомере FISHERSCOPE 2000xym с системой кинетического микроиндентирования. Определяли микротвердость и приведенный модуль упругости (Е), из которого рассчитывали нормальный модуль упругости (Еупр) по формуле:
где μ – коэффициент Пуассона (в данной работе принят μ = 0.34 [24]). Нагрузки на индентор составляли от 0.05 до 1.96 Н.Кроме того, были определены полная работа вдавливания индентора (А), работа сил релаксации (Арел) и остаточного формоизменения (Ао.ф). (рис. 3). Условный показатель запаса пластичности (φ) оценивали по формуле:
Рис. 3.
Кривая индентирования: Р – нагрузка на индентор; h – глубина внедрения индентора; Ао.ф – работа сил остаточного формоизменения; Арел – работа сил релаксации; горизонтальный участок кривой от h1 до h2 – участок ползучести.
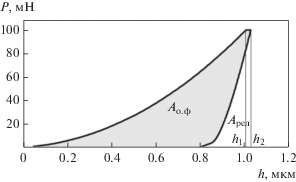
Ползучесть при вдавливании (indentation creep) [24] рассчитывали по формуле
где СIT – ползучесть, характеризующая способность материала к формоизменению при постоянно действующей нагрузке; h1 – глубина внедрения индентора, соответствующая начальной точке горизонтального участка на кривой нагружения (рис. 3); h2 – глубина внедрения индентора, соответствующая конечной точке кривой. Время выдержки при максимальной нагрузке – 20 с.РЕЗУЛЬТАТЫ ИССЛЕДОВАНИЙ И ИХ ОБСУЖДЕНИЕ
В структуре композита после спекания частицы карбида кремния SiC сосредоточены по границам гранул алюминиевого сплава (рис. 4). Гранулы матрицы, в свою очередь, имеют зеренную структуру, характерную для сплава Al7075. По границам зерен расположены частицы S-фазы (Al2CuMg) игольчатой формы, как показано в работе [24]. Как и в сплаве Al7075, в матрице исследованного композита очевидно присутствуют частицы η-фазы MgZn2 и T-фазы Mg3Zn3Al2 размерами 20–50 нм.
Рис. 4.
Исходная микроструктура (a) композита после спекания (светлые частицы – S-фаза, гранула алюминиевого сплава – М) и поверхность разрушения (б) после испытаний на сжатие при 20°С.
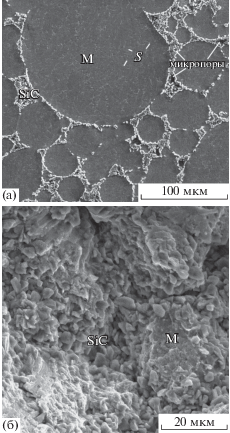
Такое строение композита не обеспечивает его прочность. Скопление частиц карбида кремния приводит к образованию микропустот между тремя и более соседними частицами SiC. Также отсутствует прочная связь на интерфейсе “SiC–SiC”. В ходе испытаний на сжатие образцов из спеченного композита с исходной структурой, разрушение происходит путем скалывания по скоплениям частиц SiC (рис. 4б). Очевидно, что для повышения прочности композита необходимо разбить скопления армирующих частиц, получить их равномерное распределение в алюминиевой матрице. При этом желательно создать условия не только для адгезионного, но и для диффузионного взаимодействия армирующих частиц с матрицей. В этом случае прочная связь на интерфейсах “матрица–SiC” обеспечит высокую прочность композита. Диффузионное взаимодействие между матрицей и частицами наполнителя возможны только при повышенных температурах [25, 26]. Именно поэтому для разбиения скоплений армирующих частиц проведено исследование возможности применения всесторонней ковки при повышенной температуре.
В ходе определения эффективных параметров режима кратковременной ползучести были получены следующие результаты. При испытании образца с нагревом до температуры 550°С и начальном давлении 5 МПа деформирование происходило в течении 129 мин, при этом наблюдали образование трещин на боковой поверхности (рис. 5а), а относительная деформация ε достигла значения 0.64. Небольшая корректировка режима нагрева и увеличение давления с 5 до 8 МПа позволили сократить время протекания процесса деформации (до ε = 0.54) практически в 2 раза, со 114 до 54 мин.
Рис. 5.
Вид образцов из Al7075/10SiCp, сжатых при начальных давлениях: (а) 5, (б) 8, (в) 10 и (г) 15 МПа в режиме кратковременной ползучести.
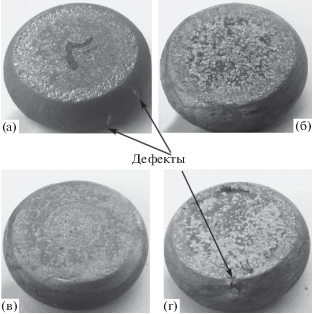
При начальном давлении 15 МПа и нагреве до температуры 520°С относительная деформация ε составляла 0.54 за 46 мин, однако при этом произошло образование дефекта (рис. 5г). Наиболее благоприятными условиями для деформации без разрушения в условиях кратковременной ползучести были режимы при давлении на образец 8 МПа и нагреве за 54 мин до температуры 544°С (рис. 5б) и при давлении 10 МПа и нагреве за 50 мин до 537°С (рис. 5в). Относительная деформация ε при этом составила 0.54 и 0.56 соответственно. Режим обработки методом всесторонней ковки с начальным давлением 5 МПа в дальнейшем не рассматривался ввиду более длительного протекания процесса. Наиболее эффективным режимом деформации для осуществления обработки композита методом всесторонней ковки в данном случае был выбран режим при минимальном давлении, т. е. 8 МПа, обеспечивающий формоизменение за приемлемое время.
При начальном давлении на образец 8 МПа деформация начинается после 40-ой минуты нагрева, температура при этом достигла 485°С. Резкое возрастание скорости деформации происходит через 45 мин при достижении температуры 516°С, при этом давление на образец снизилось до 6.5 МПа, а деформация достигла 0.2. На рис. 6 показано, что максимальная скорость относительной деформации составила 0.0014–0.0016 c–1 при нагреве от 530 до 540°С. Затем следует падение скорости деформации до 0.0007–0.0008 c–1, которое, скорее всего связано со снижением давления на образец до 5.4 МПа, и достижения деформации 0.38.
Рис. 6.
Значения скорости относительной деформации от достигнутой температуры в диапазоне 470–550°С.
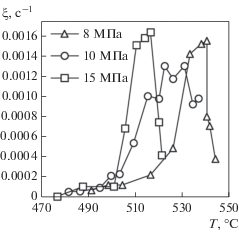
В случае одноосного сжатия при начальном давлении на образец 10 МПа деформация начинается после 35-ой минуты нагрева, когда температура достигла 469°С. На рис. 6 видно, что лавинообразный рост скорости деформации произошел при достижении температуры 503°С, и сохранялся до 522°С и относительной деформации 0.28. Максимальные скорости относительной деформации составляли 0.0012–0.0013 c–1 в диапазоне температуры нагрева от 522 до 531°С. После того как давление на образец снизилось до 6.2 МПа, а деформация достигла значения 0.43 последовало снижение скорости относительной деформации до 0.0009 c–1.
При начальном давлении на образец 15 МПа деформация зафиксирована на 30 минуте при достижении температуры нагрева 407°С. Скачок роста скорости относительной деформации произошел при достижении температуры 501°С и продолжался до температуры 511°С (рис. 6) и накоплении относительной деформации до 0.27 (рис. 7). Затем в диапазоне температуры нагрева от 511 до 517°С установилась максимальная скорость относительной деформации, которая составляла 0.0015–0.0016 c–1. После того как деформация достигла значения 0.46 давление на образец снизилось до 8.9 МПа и скорость деформации резко упала до 0.0004 c–1. Вероятнее всего, образование дефектов при данном начальном давлении связано с тем, что не произошло образование достаточного количества жидкой фазы, которое возникает в диапазоне 530–540°С и часть деформации пошла по скоплениям частиц наполнителя.
Рис. 7.
Значения скорости относительной деформации от относительной деформации при испытании образцов в режиме кратковременной ползучести с начальными давлениями 8, 10 и 15 МПа.
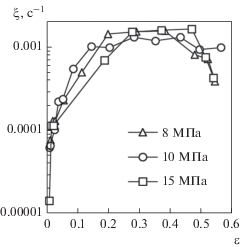
Во всех рассмотренных случаях, лавинообразный рост скорости относительной деформации продолжается в среднем до накопления относительной деформации 0.2, далее следует деформация в среднем до 0.43 с максимальной скоростью относительной деформации. Падение скорости относительной деформации происходит при снижении давления на образец до уровня в 61–67.5% от начального давления.
При увеличении начального давления на образец с 8 до 10 МПа уменьшается время начала деформации на 5 мин (или на 12.5%). При этом деформация начинается при меньшей температуре, с разницей в 16°С (или 3.2%). При меньшей температуре на 13°С (или 2.5%) начинается резкий рост скорости деформации. Температурный интервал протекания формоизменения образца с максимальными значениями скорости деформации ниже на 10°С (или на 1.9%). Однако сами максимальные значения скорости относительной деформации ниже на 0.0003 c–1 (или на 21.4%). При увеличении начального давления на образец с 8 до 15 МПа время начала деформации сокращается на 10 мин (или на 25%). Деформация при этом начинается при меньшей на 78°С (или на 16%) температуре. Резкий рост скорости относительной деформации начинается на 10 мин (или на 21%) раньше при меньшей на 15°С (или на 1.9%) температуре. Температурный интервал протекания формоизменения образца с максимальными значениями скорости относительной деформации ниже на 23°С (или на 2.4%), при этом сами значения скорости относительной деформации выше на 0.0001 c–1 (или на 6.7%).
При обработке методом всесторонней ковки образца в условиях кратковременной ползучести относительная деформация ε составляла 0.54, 0.54 и 0.53, по I, II и III проходу соответственно. На каждом проходе средняя за процесс скорость деформации составляла 0.00017 c–1. Режим нагрева образцов в интервале от 450 до 550°С немного отличается. При этом общее время, по сравнению с I проходом (54 мин) изменилось на 1 минуту во II проходе (53 мин) и на 2 мин в III проходе (52 мин). Максимальные значения скорости относительной деформации в каждом проходе находилось в диапазоне 0.00145–0.00164 с–1.
На рис. 8а на разрезе образца показаны участки анализа микроструктуры композита в плоскости 1–2 (в соответствии с принятой на рис. 2 системой координат), в той же плоскости, где изначально располагался торец образца до деформации. Установлено, что частицы наполнителя SiC проникают внутрь гранул алюминиевой матрицы, а скопления частиц SiC разбиваются. В результате формируется композит с равномерным распределением частиц SiC (рис. 8б–8г). Каждая частица SiC окружена металлической матрицей, т.е. присутствуют только межфазные связи “матрица–SiC”.
Рис. 8.
Образец в разрезе (а) после III прохода (давление 8 МПа, температура 540°С) с обозначенными участками микроанализа в плоскости 1–2, распределение частиц наполнителя по сечению образца: (б) участок D; (в) участок E; (г) участок A.
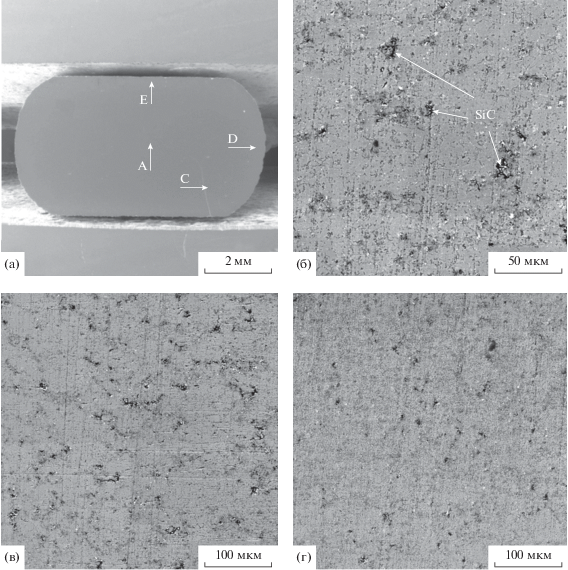
При нагреве в алюминиевой матрице происходит эвтектическое превращение L ↔ α + + S(Al2CuMg). Оно локализуется по межфазным границам частиц S-фазы и твердого раствора на основе алюминия. Образование жидкой фазы в данном композите подтверждается выполненными ранее в работе [24] калориметрическими исследованиями, показавшими наличие эндотермического превращения в исследуемом композите при температуре 534°С. Появление жидкой фазы можно констатировать по образованию характерной скелетообразной структуры, которая наблюдается после закалки от температур 530–540°С [26]. Действующие при всесторонней ковке нагрузки подавляют образование эвтектических структур. Косвенным подтверждением локального оплавления являются, во-первых, отсутствие трековых следов в твердом растворе на основе алюминия, неизбежно возникающих при перемещении частиц SiC, во-вторых, заполнение микропустот между армирующими частицами
Перераспределение частиц наполнителя по объему композита привело к однородному распределению микромеханических свойств (рис. 9). После спекания кривые нагружения, полученные с разных участков поперечного шлифа, были смещены друг относительно друга, как показано ранее в работе [24]. А после всесторонней ковки, кривые нагружения накладывались друг на друга, что означает выравнивание микромеханических свойств. Конкретные значения величин показаны в табл. 1.
Рис. 9.
Кривые микроиндентирования композита после всесторонней ковки при температуре 540°С и давлении 8 МПа (III прохода); цифрами указаны участки на поверхности шлифа, в которых проводили индентирование, участки расположены на одной линии на расстоянии 50 мкм друг от друга.
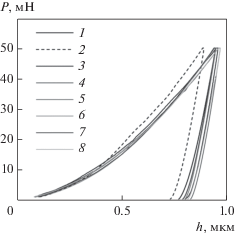
Таблица 1.
Микромеханические свойства композита при индентировании с нагрузкой 50 мН после всесторонней ковки при 540°С (давление 8 МПа, III прохода)
№ отпечатка | HV 0.05 | hmax, мкм | Е, ГПа | Еупр, ГПа | φ, % | CIT |
---|---|---|---|---|---|---|
1 | 226 | 0.94 | 76 | 67 | 78 | 0.05 |
2 | 252 | 0.89 | 88 | 78 | 79 | 0.14 |
3 | 213 | 0.95 | 88 | 78 | 82 | 0.14 |
4 | 208 | 0.96 | 88 | 78 | 83 | 0.21 |
5 | 224 | 0.94 | 80 | 71 | 81 | 0.10 |
6 | 220 | 0.94 | 84 | 74 | 80 | 0.09 |
7 | 221 | 0.94 | 85 | 75 | 80 | 0.11 |
8 | 217 | 0.96 | 71 | 63 | 81 | 0.11 |
Из заготовки после трех проходов были изготовлены цилиндрические образцы для оценки механических свойств на сжатие при температурах 20 и –50°С. Образцы вырезаны из заготовки таким образом, что их ось симметрии проходила параллельно оси 2. Полученные зависимости сопротивления деформации σS от степени деформации εC при испытании по осевому сжатию образцов, полученных после всесторонней ковки, представлены на рис. 10. По сравнению с результатом по испытанию образца при 20°С в исходном состоянии, образцы после всесторонней ковки обладают повышенными механическими свойствами. Так, испытание показало, что степень деформации до разрушения образца из материала в исходном состоянии (кривая 1) составила 0.28 при сопротивлении деформации 428 МПа. Ступеньки на кривой обусловлены микросколами по границам “SiC–SiC”. Максимальное значение сопротивления деформации образца из материала после обработки (кривая 2) выросло на 32% и составило 570 МПа, при этом значение степени деформации до разрушения выросло на 40% и составило 0.38. В испытании при температуре –50°С (кривая 3) максимальное значение сопротивления деформации выросло до 650 МПа (выше на 52%), но значение степени деформации до разрушения уменьшилось до 0.24 (ниже на 14%). Приведенные данные о сопротивлении деформации полученных образцов из композитного материала не только дают представление, что после обработки механические характеристики повышаются по сравнению с исходным состоянием, но и дают возможность для сравнения с характеристиками матричного сплава. Так, максимальное значение сопротивления деформации образца из алюмоматричного композитного материала после обработки находится на уровне временного сопротивления разрушению σв для сплава В95 (Al7075 является аналогом), приведенного в справочнике по конструкционным материалам [27]. При отрицательных температурах, поведение композита соответствует поведению матричного сплава. С понижением температуры испытания сплав В95 в закаленном и искусственно состаренном состоянии имеет тенденцию к увеличению прочности с понижением пластичности.
Рис. 10.
Зависимость сопротивления деформации от степени деформации при испытании на сжатие цилиндрических образцов Al7075/10SiCp: 1 – при комнатной температуре в исходном состоянии, 2 – при комнатной температуре после обработки, 3 – при –50°С после обработки.
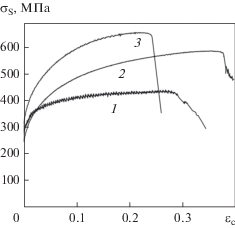
Всесторонняя ковка изменила вид излома при испытании на сжатие: излом образца стал однородным (рис. 11а), на микроуровне, соответствующим вязкому разрушению с характерными мелкими ямками (рис. 11б). Частицы наполнителя не оказывают никакого влияния на характер разрушения. Прочность композита увеличивается за счет залечивания микропустот, а также диффузионного взаимодействия матрицы и армирующих частиц в условиях деформационно-термической обработки. При температуре 540°С и выше происходит диффузионное проникновение алюминия в тонкий поверхностный слой частиц SiC. Микрорентгеноспектральный анализ показал, что в поверхностном слое частиц SiC толщиной 2 мкм содержится около 5 мас. % Al.
ЗАКЛЮЧЕНИЕ
Показано положительное влияние деформационно-термической обработки методом всесторонней ковки в режиме высокотемпературной кратковременной ползучести на структуру и свойства композита Al7075/10SiCp. При нагреве выше 500°С происходит локальное появление жидкой фазы на межфазных границах по эвтектическому превращению α + S(Al2CuMg) ↔ L. При этом возникает лавинообразный рост значений скорости относительной деформации, который продолжается в среднем до накопления относительной деформации 0.2. Деформация образцов происходит с максимальной скоростью до деформации 0.46.
Интенсивная деформация композита происходит за счет передвижения частиц SiC в расплаве и заполнения жидкой фазой микропустот между армирующими частицами. Поскольку количество жидкой фазы ограничено количеством S-фазы, дальнейшая деформация происходит с меньшей скоростью и определяется только свойствами алюминиевой матрицы.
Эффективным режимом деформационно-термической обработки является 3 прохода, где осуществляется осадка с кантовкой при нагреве за 54 мин до температуры 544°С с начальным давлением 8 МПа на образец. В результате формируется композит с равномерным распределением частиц SiC, каждая из которых окружена металлической матрицей.
Равномерное распределение армирующих частиц обеспечивает выравнивание микромеханических свойств. Прочность композита при одноосном сжатии увеличивается. Разрушение происходит по вязкому механизму.
Представленный способ предварительной деформационно-термической обработки может быть применен совместно с операциями штамповки, что дает возможность при завершающих кантовках получить заготовку, приближенную по форме к готовой детали с высокими механическими характеристиками.
Работа выполнена в рамках программы ФНИ государственных академий наук по темам АААА-А18-118020790145-0. При проведении испытаний использовалось оборудование ЦКП “Пластометрия” ИМАШ УрО РАН. Выражаем благодарность в проведении экспериментов к.т.н. А.С. Смирнову.
Список литературы
Каблов Е.Н., Щетанов Б.В., Гращенков Д.В., Шавнев А.А., Няфкин А.Н. Металломатричные композиционные материалы на основе Al–SiC // АМИТ. 2012. № S. С. 373–380.
Шавнев А.А., Березовский В.В., Курганова Ю.А. Особенности применения конструкционного металлического композиционного материала на основе алюминиевого сплава, армированного частицами SiC. Ч. 1 (обзор) // Новости материаловедения. Наука и техника. 2015. № 3(15). С. 3–10.
Шавнев А.А., Березовский В.В., Курганова Ю.А. Особенности применения конструкционного металлического композиционного материала на основе алюминиевого сплава, армированного частицами SiC. Ч. 2 (обзор) // Новости материаловедения. Наука и техника. 2015. № 3(15). С. 11–17.
Стоякина Е.А., Курбаткина Е.И., Симонов В.Н., Косолапов Д.В., Гололобов А.В. Механические свойства алюмоматричных композиционных материалов, упрочненных частицами SiC, в зависимости от матричного сплава (обзор) // Труды ВИАМ. 2018. № 2(62). С. 62–73.
Miracle D.B. Metal matrix composites – From science to technological significance // Compos. Sci. Technol. 2005. V. 65. № 15–16. P. 2526–2540. https://doi.org/10.1016/j.compscitech.2005.05.027
Vani V.V., Chak S.K. The effect of process parameters in Aluminum Metal Matrix Composites with Powder Metallurgy // Manufacturing Rev. 2018. V. 5. Ar. N. 7 (13).
Курбаткина Е.И., Шавнев А.А., Косолапов Д.В., Гололобов А.В. Особенности термической обработки композиционных материалов с алюминиевой матрицей (обзор) // Труды ВИАМ. 2017. № 11(59). С. 82–97.
Курбаткина Е.И., Косолапов Д.В., Гололобов А.В., Шавнев А.А. Исследование структуры и свойств металлического композиционного материала системы Al–Zn–Mg Cu/SiC // Цветные металлы. 2019. № 1. С. 40–45.
Čadek J., Kuchařová K., Zhu S.J. High temperature creep behaviour of an Al–8.5Fe–1.3V–1.7Si alloy reinforced with silicon carbide particulates // Mater. Sci. Eng. A. 2000. V. 283. № 1–2. P. 172–180.
Čadek J., Kuchařová K., Zhu S.J. Transition from athermal to thermally activated detachment of dislocations from small incoherent particles in creep of an Al–8.5Fe–1.3V–1.7Si alloy reinforced with silicon carbide particulates // Mater. Sci. Eng. A. 2001. V. 297. № 1–2. P. 176–184.
Ma Z.Y., Tjong S.C. High-temperature creep behaviour of SiC particulate reinforced Al–Fe–V–Si alloy composite // Mater. Sci. Eng. A. 2000. V. 278. № 1–2. P. 5–15.
Кищик М.С., Котов А.Д., Демин Д.О., Кищик А.А., Аксенов С.А., Михайловская А.В. Влияние режимов всесторонней изотермической ковки на деформационное поведение и микроструктуру сплава на основе системы Al–Mg // ФММ. 2020. Т. 121. № 6. С. 659–666.
Кищик А.А., Кищик М.С., Котов А.Д., Михайловская А.В. Влияние всесторонней ковки на микроструктуру и механические свойства сплава системы Al–Mg–Mn–Cr // ФММ. 2020. Т. 121. № 5. С. 543–549.
Božić D., Vilotijević M., Rajković V., Gnjidić Ž. Mechanical and Fracture Behaviour of a SiC-Particle-Reinforced Aluminum Alloy at High Temperature // Mater. Sci. Forum. 2005. V. 494. P. 487–492.
Wu M.Y., Sherby O.D. Superplasticity in a silicon carbide whisker reinforced aluminum alloy // Scripta Metal. 1984. V. 18. № 8. P. 773–776.
González-Doncel G., Sherby O.D. Tensile ductility and fracture of superplastic Aluminum-SiC composites under thermal cycling conditions // Metall. Mater. Trans. A. 1996. V. 27. № 9. P. 2837–2842.
Ларичкин А.Ю., Захарченко К.В., Горев Б.В., Капустин В.И. Физическое моделирование технологического процесса формообразования элементов конструкций из алюминиевого сплава В95 в условиях ползучести // Обработка металлов (технология, оборудование, инструменты). 2016. № 1(70). С. 6–15.
Luo H., Li W., Li C., Wan M. Investigation of creep-age forming of aluminum lithium alloy stiffened panel with complex structures and variable curvature // Intern. J. Adv. Manufactur. Techn. 2017. V. 91. № 9–12. P. 3265–3271.
Pickens J.R., Langan T. J., England R.O., Liebson M. A study of the hot-working behavior of SiC−Al alloy composites and their matrix alloys by hot torsion testing // Metall. Mater. Trans. A. 1987. V. 18. № 2. P. 303–312.
Razaghian A., Yu D., Chandra T. Fracture behaviour of a SiC-particle-reinforced aluminium alloy at high temperature // Compos. Sci. Technol. 1998. V. 58. № 2. P. 293–298.
Azpen Q.M., Baharudin B.T.H.T., Shamsuddin S., Mustapha F. Reinforcement and hot workability of aluminium alloy 7075 particulate composites: A review // J. of Eng. Sci. Techn. 2018. V. 13. № 4. P. 1034–1057.
Крючков Д.И., Нестеренко А.В. Обзор экспериментальных исследований деформационного поведения алюмо-матричных композиционных материалов, дискретно упрочненных карбидом кремния, в состоянии высокотемпературной сверхпластичности и при ползучести // Обработка металлов (технология, оборудование, инструменты). 2020. Т. 22. № 2. С. 130–157.
Смирнов С.В., Крючков Д.И., Нестеренко А.В., Березин И.М., Вичужанин Д.И. Экспериментальное исследование кратковременной неустановившейся ползучести алюмоматричного композита в условиях одноосного сжатия // ВПНИПУ. Механика. 2018. № 4. С. 98–105.
Пугачева Н.Б., Мичуров Н.С., Сенаева Е.И., Быкова Т.М. Структура и теплофизические свойства алмоматричных композитов //ФММ. 2016. Т. 117. № 11. С. 1188–1195.
Пугачева Н.Б., Мичуров Н.С., Быкова Т.М. Структура и свойства композиционного материала Al/SiC // ФММ. 2016. Т. 117. № 6. С. 654–660.
Pugacheva N.B., Malygina I.Yu., Michurov N.S., Senaeva E.I., Antenorova N.P. Effect of Heat Treatment on the Structure and Phase Composition of Aluminum Matrix Composites Containing Silicon Carbide [Electronic resource] [In Russian] // Diagnostics, Resource and Mechanics of materials and structures. 2017. № 6. P. 28–36.
Арзамасов Б.Н., Соловьев Т.В. Справочник по конструкционным материалам. М.: Изд-во МГТУ им. Н.Э. Баумана, 2005. 640 с.
Дополнительные материалы отсутствуют.
Инструменты
Физика металлов и металловедение