Физика металлов и металловедение, 2021, T. 122, № 10, стр. 1065-1074
Влияние дефектности поверхности образцов титанового сплава Ti–10V–2Fe–3Al на его поведение при испытаниях на высокоцикловую усталость
a Главная государственная лаборатория по механике и контролю качества механических структур,
Институт аэрокосмической инженерии, Нанкинский университет аэронавтики и космонавтики
210016 Нанкин, Китай
* E-mail: zcw@nuaa.edu.cn
Поступила в редакцию 17.11.2020
После доработки 05.04.2021
Принята к публикации 10.06.2021
Аннотация
Высокоцикловые усталостные испытания образцов титанового сплава Ti–10V–2Fe–3Al с поверхностными дефектами – царапинами и выбоинами, проводили при различной амплитуде циклических напряжений и различном размере дефектов. Для анализа морфологии усталостного разрушения был использован метод растровой электронной микроскопии (РЭМ). Экспериментальные результаты показали, что присутствие дефектов на поверхности образцов, таких как выбоина или царапина, приводит к снижению усталостной долговечности сплава Ti–10V–2Fe–3Al, а ухудшение сопротивления усталости материала напрямую связано с увеличением глубины дефекта. Места зарождения усталостных трещин были определены с помощью РЭМ-анализа, который локально проводили на краю выбоины и на дне царапины. Кроме того, модели прогнозирования сопротивления усталости для случаев выбоины и царапины соответственно были предложены на основе эмпирической формулы Мураками, и прогнозируемые результаты новых моделей хорошо согласуются с данными испытаний на усталость.
ВВЕДЕНИЕ
Усталостное разрушение – это основной тип разрушения конструкций, которые при эксплуатации подвергаются циклическим нагрузкам. Усталостное поведение металлических материалов является постоянной темой обсуждения в научной и технической литературе, поскольку оно в значительной степени связано с безопасностью техники и экономичностью ее производства [1–3].
Усталостная долговечность конструкции не только напрямую связана с такими факторами, как материал, тип конструкции и спектр нагрузок, но и зависит от дефектов поверхности, таких как выбоины и царапины, вызванных ударами или царапанием посторонних предметов в процессе производства или обслуживания. Эти дефекты, безусловно, приводят к снижению усталостной долговечности конструкции [4, 5]. Например, на динамические компоненты деталей вертолета легко воздействовать инструментами в процессе изготовления, что приводит к очевидному снижению усталостной долговечности [6]. Посторонние предметы, такие как птицы или мелкие твердые предметы, засасываемые в авиационный двигатель, могут повредить поверхность лопасти двигателя и впоследствии снизить срок службы лопасти двигателя [7–9]. Таким образом, необходимо исследовать влияние вышеупомянутых поверхностных дефектов на усталостную долговечность металлических материалов, чтобы избежать авиационных аварий и в полной мере использовать остаточный ресурс поврежденных конструкций или деталей.
Проектирование с учетом усталостной долговечности является важной технической работой в авиационной промышленности и еще более важной и насущной задачей при проектировании динамических компонентов вертолета [10]. В течение длительного времени для определения усталостной долговечности основных конструкций вертолета используется метод прогнозирования безопасного срока службы, который основан на идеальной ситуации, когда конструкция совершенна [11]. Вместе с тем структурные сбои иногда происходят до истечения расчетного срока службы из-за наличия неожиданных дефектов или повреждений, которые не учитываются в методе прогнозирования безопасного срока службы. В этом смысле данный метод в действительности не является надежным для предотвращения незапланированных аварийных ситуаций. Другой широко используемой методикой расчета усталости является определение устойчивости к повреждениям, основанное на теории механики разрушения [12‒14]. Этот метод предполагает, что начальные небольшие трещиноподобные дефекты неизбежно выходят из материала наружу, и время, когда небольшая трещина вырастает до критической, определяется как усталостная долговечность конструкции. Проверка состояния материала конструкции в этом случае обычно назначается до достижения момента прогнозируемого усталостного разрушения. Метод устойчивости к повреждениям в настоящее время широко используется при оценке усталости материала деталей самолетов с неподвижным крылом, однако этот метод неприменим в случаях, отвечающих динамическим компонентам деталей вертолета, где усталостная трещина будет быстро расти после зарождения под высокочастотной циклической нагрузкой, и это приведет к необходимости установления довольно коротких интервалов проверки или к сложным процедурам проверки [15]. В 1989 г. была предложена более рациональная схема оценки усталости деталей вертолета под названием метод допуска по дефектам, которая постепенно была принята гражданским вертолетным сообществом. Этот метод основан на предположении–допущении, что дефекты возникают в опасной части динамических компонентов деталей вертолета. Впервые метод был применен при проектировании вертолета S-92, и некоторые динамические компоненты вертолета марки NH-90 также были разработаны на основе этого метода [16, 17].
Для динамических компонентов деталей вертолета выбоина и царапина – это часто встречающиеся дефекты поверхности, возникшие в результате авиационного происшествия. Для оценки допуска по дефектам динамического компонента конструкции важной процедурой является испытание материала на усталость. Усталостная прочность и кривая S–N всегда служат объектами исследования многоцикловой усталости (МЦУ) [18, 19]. Связь между амплитудой возникающего напряжения и усталостной долговечностью может быть проиллюстрирована некоторыми специальными функциональными формами, такими как экспоненциальная, соотношение Баскина (Basquin), формы, использующие закон распределения случайных величин по Вейбуллу (Weibull)–Гнеденко и др. [20]. Зависимость усталостных свойств от факторов окружающей среды может быть непосредственно отражена с помощью некоторых параметров в этих функциях. Возьмем в качестве примера соотношение Баскина: коэффициент усталостной прочности и показатель степени усталостной прочности изменяются в зависимости от температуры немонотонно, но демонстрируют различные тенденции изменения. А именно, при повышении температуры коэффициент усталостной прочности сначала уменьшается, а затем повышается, однако величина показателя усталостной прочности сначала увеличивается, а затем падает [21]. Это означает, что эти параметры могут проиллюстрировать, как сказывается величина температуры на ходе кривой S–N. Усталостная прочность всегда является ключевым показателем для выбора и оценки конструкционных материалов, ее обычно измеряют ступенчатым методом и методом групповых испытаний [22, 23].
Титановые сплавы широко применяются в аэрокосмической технике из-за их превосходных механических характеристик при низкой удельной плотности [24]. Например, титановый сплав Ti–10V–2Fe–3Al часто используется в основных деталях роторных систем вертолетов и их шасси [25, 26]. Поэтому были проведены МЦУ испытания титанового сплава, и на образцах были нанесены два типичных дефекта (выбоина и царапина) различных размеров. По этим экспериментальным результатам были построены S–N-кривые для образцов титанового сплава Ti–10V–2Fe–3Al с дефектами различных размеров и получены эмпирические формулы пределов выносливости. Морфология поверхности излома была изучена с использованием метода РЭМ, и для двух указанных дефектов расчетным путем были установлены соответствующие источники зарождения трещин.
МАТЕРИАЛ И ПОДРОБНОСТИ ЭКСПЕРИМЕНТА
Материалом исследования был титановый сплав Ti–10V–2Fe–3Al, типичный металлический материал, часто используемый для изготовления динамических компонентов деталей вертолета. Это сплав близок к Ti сплавам β-типа, его химический состав приведен в табл. 1.
Таблица 1.
Химический состав титанового сплава Ti–10V–2Fe–3Al
Элемент | Содержание, вес. % | Элемент | Содержание, вес. % | Элемент | Содержание, вес. % |
---|---|---|---|---|---|
Ti | >84.57 | Al | 3.30 | V | 10.00 |
Y | <0.001 | Fe | 1.70 | C | <0.01 |
N | <0.01 | H | 0.001 | O | 0.10 |
Rest | <0.30 | – | – | – | – |
Статические и усталостные испытания гладких образцов
Размеры гладких (т.е. без дефектов на поверхности) усталостного образца и образца для статического растяжения из сплава Ti–10V–2Fe–3Al одинаковы, размеры показаны на рис. 1. Все образцы были изготовлены методом фрезерования, чтобы обеспечить шероховатость поверхности, в соответствии с требованиями, предписанные стандартом Ra = 3.2 мкм, а фактически измеренные значения шероховатости поверхности образцов составляли Ra = 1.6~0.2 мкм. Боковые грани образцов были дополнительно отполированы до Ra = 0.8 мкм. Статические испытания на растяжение проводили на электромеханической универсальной испытательной машине (МТS CMT5504) со скоростью деформации 5 × 10–4 с–1. Испытания на усталость под механическим напряжением с постоянной амплитудой проводили на автоматически регулируемом гидравлическом испытательном стенде (МТS Landmark 370-50) и высокочастотном тестере-устройстве, испытывающем на механическую усталость QBG-200. Волнообразное нагружение синусоидальной формы осуществляли при отношении напряжений R = –1. Частота нагружения в 5 Гц была использована для образцов, подвергавшихся воздействию высокого уровня напряжений ~600 МПа, а частота нагружения в 80 Гц для всех остальных образцов, с учетом временных затрат на их усталостные испытания. Как статические, так и усталостные испытания проводили на открытом воздухе при комнатной температуре около 25°С.
Испытания на усталость образцов с дефектами поверхности
Форма и размеры образцов с выбоиной и царапиной такие же, как и гладких. Дефект царапина располагался на центральной линии образца (линия AB на рис. 1), а дефект выбоина находился в его центральной точке (точка С на рис. 1). Рисунки 2 и 3 иллюстрируют формы дефектов двух типов соответственно. Обработка поверхности дефектных образцов была такой же, как и для гладких образцов. Выбоина была нанесена на поверхность образцов с помощью копровой бабы (CEAST 9350), а нанесение царапины производили с помощью поперечно-строгального станка (BC6063). Образец при нанесении выбоины закрепляли с обоих концов стальной пластиной, проложенной под ним, чтобы избежать его изгиба при создании дефекта. Размеры исследованных дефектов приведены в табл. 2, в которой перечислено по три глубины для обоих дефектов, поскольку считается, что именно глубина является главной размерной составляющей дефекта, определяющей величину сопротивления усталости. Оборудование и условия нагружения при испытаниях на усталость дефектных образцов были такими же, как при испытании гладких образцов.
Таблица 2.
Размеры исследованных дефектов
Тип дефекта | Радиус у дна дефекта, мм | Глубина дефекта, мм |
---|---|---|
Выбоина | 3 | 0.15 |
0.25 | ||
0.4 | ||
Царапина | 0.2 | 0.15 |
0.25 | ||
0.4 |
Усталостные испытания образцов, к которым предъявляются самые жесткие и менее жесткие требования по срокам безаварийной эксплуатации, проводили как на гладких, так и на дефектных образцах. Метод групповых испытаний применяли для тестирования на долговечность образцов, к которым предъявляются менее жесткие требования. Были использованы три группы амплитуд напряжений с соответствующими требуемыми сроками службы около 5 × 104, 1 × 105 и 5 × 105 циклов, причем было выполнено требование 95%-ной достоверности полученных результатов. Испытания – в случае тестирования на усталостную долговечность образцов, к которым предъявляются самые жесткие требования по срокам безаварийной эксплуатации, проводили с использованием метода испытаний “вверх–вниз”. Было испытано сопротивление усталости при 107 циклах, при 4-х уровнях амплитуды напряжений и для 5-ти пар деталей узлов, задействованных в режиме “подъем”.
РЕЗУЛЬТАТЫ ИСПЫТАНИЙ И ОБСУЖДЕНИЕ
Механические свойства на растяжение. Инженерная кривая “напряжение–деформация” при статическом растяжении образцов титанового сплава Ti–10V–2Fe–3Al показана на рис. 4, из нее не видно, как можно извлечь явную информацию о величине предела текучести и составить представление о протекании деформационного упрочнения в процессе пластического течения материала. Преобразуем инженерную кривую в кривую “истинное напряжение–деформация” (см. рис. 4), и в качестве предела текучести исследуемого материала Ti–10V–2Fe–3Al выберем истинное напряжение, соответствующее остаточной деформации 0.2%. Ряд основополагающих механических свойств на растяжение перечислен в табл. 3.
Рис. 4.
Инженерная кривая и кривая “истинное напряжения–деформация” для сплава Ti–10V–2Fe–3Al, где Sa – амплитуда напряжения циклического нагружения; Se – предел выносливости; N – количество циклов до разрушения, т.е. усталостная долговечность; C и α – постоянные материала, причем α > 0. Для подгонки параметров в уравнении (1) по данным о многоцикловой усталости, приведенным на рис. 5а–5в, использовался метод наименьших квадратов, причем, подогнанные кривые также изображены на указанных рисунках, а подогнанные параметры перечислены в табл. 4.
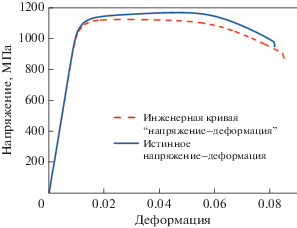
Таблица 3.
Статические механические свойства титанового сплава Ti–10V–2Fe–3Al
Модуль Юнга E, MПa | Коэффициент Пуассона ν | Предел текучести ${{\sigma }_{{\text{y}}}},$ MПa | Предел прочности ${{\sigma }_{{\text{u}}}},$ MПa |
---|---|---|---|
106 000 | 0.34 | 1098 | 1170 |
Таблица 4.
Подгоночные параметры S–N кривых для гладких и дефектных образцов сплава Ti–10V–2Fe–3Al
Тип образца | Глубина дефекта, мм | Se, MПa | C | α |
---|---|---|---|---|
Гладкий | – | 416.4 | 8144 | 0.9025 |
C выбоиной | 0.15 | 382.8 | 142.7 | 0.5393 |
0.25 | 361.9 | 39.61 | 0.4212 | |
0.40 | 294.0 | 4 131 289 | 1.4990 | |
C царапиной | 0.15 | 367.7 | 21.71 | 0.4428 |
0.25 | 319.0 | 8 598 8115 | 1.8266 | |
0.40 | 279.0 | 3 085 029 | 1.4965 |
S–N кривая и циклическая прочность. S–N кривые гладких, а также дефектных образцов сплава Ti–10V–2Fe–3Al приведены на рис. 5, на котором вертикальные координаты обозначают амплитуды напряжений циклических нагрузок, а горизонтальные координаты – величины усталостной долговечности. S–N кривые металлических материалов могут быть выражены трехпараметрической формулой, как показано ниже:
Рис. 5.
Экспериментальная величина усталостной долговечности и установленные подгонкой S–N кривые для образцов сплава Ti–10V–2Fe–3Al. (а) гладкие образцы; (б) образцы с выбоиной, (в) образцы с царапиной.
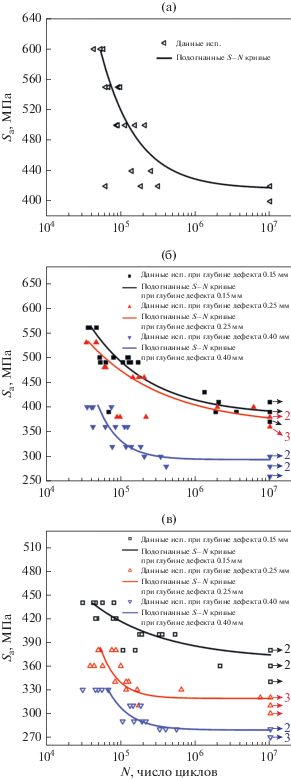
где Sa – амплитуда напряжения циклического нагружения; Se – предел выносливости; N – количество циклов до разрушения, т.е. усталостная долговечность; C и α – постоянные материала, причем α > 0. Для подгонки параметров в уравнении (1) по данным о многоцикловой усталости, приведенным на рис. 5а–5в, использовался метод наименьших квадратов, причем, подогнанные кривые также изображены на указанных рисунках, а подогнанные параметры перечислены в табл. 4.
Сопротивление усталости образцов с выбоинами и царапинами в зависимости от глубины дефекта показано на рис. 6. Оба этих дефекта усиливают снижение сопротивления усталости с увеличением глубины дефекта, и даже самые маленькие дефекты, глубиной 0.15 мм, изученные в данной работе, могут вызвать очевидное снижение сопротивления усталости. Кроме того, образец с царапиной вызывает большее снижение сопротивления усталости, чем образец с выбоиной при одинаковой глубине дефекта. Источники усталостного разрушения, как правило, выявляются на дне царапины и на краю выбоины. На дне царапины возникает более высокая концентрация напряжений, когда два дефекта имеют одинаковую глубину. Таким образом, это может быть объяснением того, что царапина приводит к большему снижению сопротивления усталостни, чем выбоина, как показано на рис. 6. Более подробное обсуждение источников усталостного разрушения будет представлено в следующем разделе настоящей статьи.
Рис. 6.
Зависимость сопротивления усталости от глубины дефекта поверхности образца титанового сплава Ti–10V–2Fe–3Al.
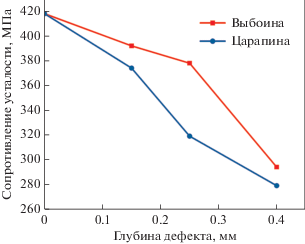
Морфология поверхности усталостного излома
Поверхность разрушения дефектных образцов после усталостных испытаний наблюдали РЭМ методом. В образцах для РЭМ исследований дефекты в виде выбоины имели размеры: радиус R = 3 мм и глубина D = 0.25 мм, в то время как дефекты в виде царапины имели размеры R = 0.2 мм и глубиной D = 0.25 мм. Эти два размера дефектов определяются как стандартные размеры для дефектов типа выбоина и царапина, которые могут статистически покрывать 90% размеров этих двух дефектов, обнаруженных в динамических компонентах деталей вертолета [27]. Общий вид поверхности усталостного разрушения образца сплава Ti–10V–2Fe–3Al с выбоиной показан на рис. 7, из которого видно, что поверхность усталостного разрушения проходит через дефект. Участок разрушения можно разделить на три области, как показано на рис. 7, первая область является областью зарождения трещины, вторая – область распространения трещины, а третья – область долома. Наблюдаются расходящиеся линии, сходящиеся к источнику инициирования трещины в первой области, и четко идентифицируемая демаркационная линия существует между второй областью распространения трещины и третьей областью окончательного разрушения (долома). Источник инициации усталостного разрушения находится на краю дефекта. Этот факт интерпретируется так, что дно выбоины несет остаточное сжимающее напряжение, которое повышает сопротивление материала усталости. Напротив, на краю выбоины существует остаточное растягивающее напряжение, которое усиливает там локальное растягивающее напряжение под усталостной нагрузкой, что способствует возникновению усталостной трещины. Две области, отмеченные на рис. 7а литерами А и В, были выбраны для дальнейшего наблюдения с большим увеличением. Область А (рис. 7б) демонстрирует тонкую текстуру, указывающую на область А как источник усталостной трещины, а область В (рис. 7в) определяет границу между поверхностью мелкозернистого излома и поверхностью крупнозернистого разрушения, которые являются типичной зоной распространения трещины и областью долома.
Рис. 7.
Морфология поверхности усталостного разрушения образца сплава Ti–10V–2Fe–3Al с выбоиной: (а) общий вид; (б) область инициации усталостной трещины; (в) граница между зоной распространения усталостной трещины и зоной долома.
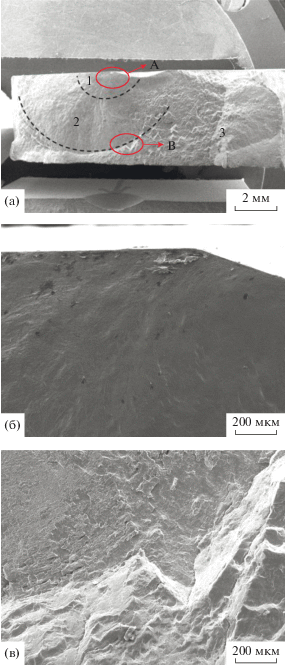
На рис. 8 показана морфология поверхности усталостного разрушения образца сплава Ti–10V–2Fe–3Al с царапиной. На РЭМ изображении рис. 8а, 8б линии расходятся от дна царапины вблизи боковой стороны образца, где, как полагают, находился источник усталостной трещины. Для царапины локальное остаточное напряжение и пластическая деформация незначительны по сравнению с этими же характеристиками для выбоины. Максимальной величины локальное растягивающее напряжение локализовано действовало в нижней части канавки царапины, являвшейся концентратором напряжений. Итак, усталостная трещина инициируется в указанном месте по вполне понятным причинам.
Рис. 8.
Морфология поверхности усталостного разрушения образца сплава Ti–10V–2Fe–3Al с царапиной: (а) общий вид; (б) увеличенное изображение области инициации усталостной трещины; (в) увеличенное изображение границы между зоной распространения усталостной трещины и зоной долома.
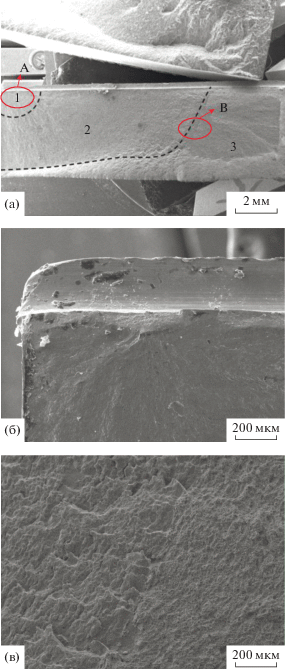
Увеличенные РЭМ-изображения области источника усталостной трещины (область А) и границы между зоной распространения трещины и областью долома (область В) показаны на рис. 8б и в соответственно. При наблюдении поверности разрушения образцов сплава Ti–10V–2Fe–3Al с выбоиной и царапиной можно обнаружить сходство между изломами. Каждую из поверхностей усталостного излома дефектных образцов с выбоиной и царапиной можно разделить на три области: область зарождения усталостной трещины, область распространения трещины и область окончательного разрушения. Кроме того, усталостные трещины возникают на дефектах обоего вида, нанесенных на поверхность изучаемых образцов.
С другой стороны, различие особенностей морфологии поверхностей усталостного разрушения в этих двух случаях очевидно. Для дефекта типа выбоины источник усталостного разрушения локализован, как правило, на краю дефекта, тогда как в случае царапины источник находится у дна дефекта.
Эмпирическая формула сопротивления усталости образцов сплава Ti–10V–2Fe–3Al с дефектами
Размер и форма являются двумя ключевыми параметрами дефекта при оценке сопротивления усталости металлической конструкции, содержащей дефект. Конфигурация дефекта на практике может быть сложной, поэтому иногда трудно эффективно определить его размер, который является определяющим для зарождения усталостной трещины. Мураками [28] предложил эмпирическую модель прогнозирования сопротивления усталости металлической конструкции. В его модели размер дефекта обобщается как некий эквивалент размера дефекта – это квадратный корень из площади дефекта, проецирующейся на плоскость, параллельную направлению глубины дефекта. Сопротивление усталости металла считается возрастающим с его твердостью, поскольку усталостное разрушение металлического материала считается связанным с локальной пластичностью, а металл с более высокой твердостью обычно имеет более высокий предел текучести. Модель прогнозирования сопротивления усталости Мураками представлена в следующем виде:
(2)
${{\sigma }_{{\text{f}}}} = \frac{{{{c}_{1}}\left( {{{H}_{{\text{V}}}} + {{c}_{2}}} \right)}}{{{{{\left( {\sqrt {area} } \right)}}^{{{{c}_{3}}}}}}},$Таблица 5.
Значения подгоночных параметров прогностической модели Мураками усталостной долговечности материалов
Материал | Тип дефекта | c1 | c2 | c3 |
---|---|---|---|---|
Мартенситная сталь | Искусственно-привнесенный дефект | 1.43 | 120 | 1/6 |
Сплав Ti–10V–2Fe–3Al | Выбоина | 1.43 | 2156 | 0.361 |
Царапина | 1.43 | 2824 | 0.469 |
Они являются подстраиваемыми параметрами, когда эта модель используется для других металлических материалов. В этом исследовании значения сопротивления усталости образцов титанового сплава Ti–10V–2Fe–3Al с дефектами в виде выбоины и царапины на поверхности также были рассчитаны по формуле Мураками, а эквивалентные размеры дефектов для выбоины и царапины, как показано на рис. 2 и 3 , рассчитаны из следующих соображений.
Для выбоины:
Для царапины:
(4)
$\begin{gathered} area = {\text{tg}}{\kern 1pt} 10^\circ {{D}^{2}} + 2RD(1 - {\text{tg}}{\kern 1pt} 10^\circ ) + \\ + \,\,\left( {\frac{\pi }{2} + {\text{tg}}{\kern 1pt} 10^\circ - 2} \right){{R}^{2}}. \\ \end{gathered} $Непосредственное использование значений параметров Мураками в этом исследовании привело бы к значительной недооценке сопротивления усталости, как можно видеть из табл. 6. Расхождения можно интерпретировать как то, что модель Мураками была обобщена на основе серии усталостных испытаний мартенситной стали с дефектами обработанной поверхности. Отметим, что у нас и материал, и тип дефектных образцов были отличны от того, что изучал Мураками. “Отфрезерованные” дефекты влияют на сопротивление усталости металлического материала просто через введение концентрации напряжений в области дефекта. Однако для дефектов типа выбоины или царапины, помимо локальной концентрации напряжений при циклических нагрузках, местные остаточные напряжения и локальная пластичность и локальное начальное повреждение могут играть значительную роль в достигаемом уровне сопротивления усталости. Дефекты, изученные в этой статье, приводят к необходимости учета более сложных факторов, влияющих на поведение характеристики усталости материала.
Таблица 6.
Сравнение прогнозируемых значений сопротивления усталости с использованием оригинальной модели Мураками и модифицированной модели с экспериментальными данными, полученными на дефектных образцах титанового сплава Ti–10V–2Fe–3Al
Тип дефекта | Глубина, мм | $\sqrt {area} ,$ мкм | ${{\sigma }_{{\text{f}}}},$ MПa испытан. |
${{\sigma }_{{\text{f}}}}$, MПa с параметрами из [23] | Ошибка, % | ${{\sigma }_{{\text{f}}}},$ MПa с модифицированными параметрами | Ошибка, % |
---|---|---|---|---|---|---|---|
Выбоина | 0.15 | 434 | 392 | 255 | 34.9 | 403 | 2.8 |
0.25 | 635 | 378 | 239 | 36.8 | 352 | 7.4 | |
0.4 | 900 | 294 | 226 | 23.1 | 310 | 5.4 | |
Царапина | 0.15 | 207 | 374 | 288 | 23.0 | 374 | 0.0 |
0.25 | 289 | 319 | 272 | 14.7 | 320 | 0.3 | |
0.4 | 387 | 279 | 260 | 6.8 | 279 | 0.0 |
Кроме того, особенности состояния локального остаточного напряжения, пластичности, а также локального начального повреждения весьма различны для дефектов типа выбоины и типа царапины, поэтому нельзя использовать один и тот же набор эмпирических параметров, соответствующих сопротивлению усталости для этих двух дефектов одновременно. Здесь значения параметров модели были установлены с использованием экспериментальных данных отдельно для дефектов типа выбоины и типа царапины (как указано в табл. 5), причем, во всех случаях величина коэффициента c1 была одинакова.
В табл. 6 проведено сравнение значений сопротивления усталости, предсказанных модифицированными моделями, с результатами испытаний на усталость. Проведенное сравнение указывает на особенно хорошее совпадение для случая дефекта, представленного поверхностной царапиной. Таким образом, приведенные выше формулы с модифицированными значениями параметров могут быть использованы для прогнозирования сопротивления усталости титанового сплава Ti–10V–2Fe–3Al с часто возникающими дефектами (типа выбоины или поверхностной царапины). Отметим, что эти два набора значений параметров для дефектов типа выбоины и царапины экстраполированы из экспериментальных данных, отвечавших дефектам с размерами в определенном диапазоне. Эти наборы следует использовать с осторожностью, когда размер дефекта или его конфигурация выходят за эти пределы.
ВЫВОДЫ
В настоящем исследовании были проведены усталостные испытания для изучения влияния дефектов – выбоины или царапины поверхности образца титанового сплава Ti–10V–2Fe–3Al, на его усталостные свойства. Трехпараметрические формулы для S–N-зависимостей были получены по результатам испытаний на высокоцикловую усталость. РЭМ была использована для наблюдения морфологии поверхностей усталостного разрушения дефектных образцов для выявления источников усталостных трещин. Эмпирическое предсказание Мураками относительно сопротивления усталости, примененное для мартенситной стали, было использовано для расчета сопротивления усталости образцов сплава Ti–10V–2Fe–3Al с дефектами, а параметры модели были откалиброваны с учетом экспериментальных результатов испытаний на высокоцикловую усталость образцов исследованного материала. По результатам проведенных исследований сделаны следующие выводы.
1. Небольшие дефекты, такие как выбоина и поверхностная царапина, действительно оказывают негативное влияние на высокие усталостные характеристики титанового сплава Ti–10V–2Fe–3Al, и его сопротивление усталости будет уменьшаться с увеличением глубины дефекта образца. Царапина, по-видимому, оказывает большее влияние на сопротивление усталости сплава по сравнению с выбоиной при той же глубине дефекта и стандартном радиусе.
2. РЭМ-наблюдения поверхностей усталостного разрушения дефектных образцов сплава Ti–10V–2Fe–3Al показывают, что поверхностные дефекты, как правило, являются источниками возникновения усталостных трещин. Источник трещины находится на краю выбоины, где существует локальное остаточное растягивающее напряжение, возникающее при ударе, в то время как для дефекта типа царапины трещина, как доказано, зарождается на дне дефекта, где концентрация локальных напряжений является самой высокой при циклической нагрузке.
3. Величины сопротивления усталости, предсказанные моделью Мураками, которая первоначально использовалась для мартенситной стали, имеют большое отклонение от результатов испытаний на усталость образцов сплава Ti–10V–2Fe–3Al с дефектами типа выбоина и царапина, если используются непосредственно параметры модели Мураками. На основе результатов испытаний на высокоцикловую усталость было откалибровано два набора значений параметров модели для прогнозирования сопротивления усталости образцов сплава Ti–10V–2Fe–3Al с выбоиной и царапиной, соответственно.
Данная работа была спонсирована Национальным Естественно-Научным Фондом Китая (гранты 11872205, 11272147), Общедоступным Фондом Главной Государственной Лаборатории по механике и контролю качества механических структур (грант MCMS-0218G01), а также профинансирована в рамках Программы Развития приоритетных академических исследований для высших учебных заведений провинции Цзянсу.
Список литературы
Huang C., Zhao Y., Xin S., Zhou W., Tan C. High cycle fatigue behavior of Ti–5Al–5Mo–5V–3Cr–1Zr titanium alloy with bimodal microstructure // J. Alloy. Compd. 2016. V. 695. P. 1966–1975.
Glode S., Klemenc J., Zupani F., Vesenjak M. High-cycle fatigue and fracture behaviours of SLM AlSi10Mg alloy // Trans. Nonferrous Met. Soc. China. 2020. V. 30. № 10. P. 2577–2589.
Singh J., Arora K.S., Shukla D.K. High cycle fatigue performance of cold metal transfer (CMT) brazed C–Mn–440 steel joints // Int. J. Fatigue. 2020. V. 137. P. 105663.
Zhan Z., Hu W., Shen F., Meng Q., Pu J., Guan Z. Fatigue life calculation for a specimen with an impact pit considering impact damage, residual stress relaxation and elastic-plastic fatigue damage // Int. J. Fatigue. 2016. V. 96. P. 208–223.
Nishimura Y., Yanase K., Ikeda Y., Tanaka Y., Miyamoto N., Miyakawa S., Endo M. Fatigue strength of spring steel with small scratches // Fatigue Fract. Eng. Mater. Struct. 2018. V. 41. P. 1514–1528.
Tiong U.H., Jones R. Damage tolerance analysis of a helicopter component // Int. J. Fatigue. 2009. V. 31. № 6. P. 1046–1053.
Peters J.O., Boyce B.L., Chen X., McNaney J.M., Hutchinson J.W., Ritchie R.O. On the application of the Kitagawa-Takahashi diagram to foreign-object damage and high-cycle fatigue // Eng. Fract. Mech. 2002. V. 69. № 13. P. 1425–1446.
Nowell D., Dini D., Duo P. Stress analysis of V-notches with and without cracks, with application to foreign object damage // J. Strain Anal. Eng. Des. 2003. V. 38. № 5. P. 429–441.
Zhao Z., Wang L., Zhang J., Liu L., Chen W. Prediction of high-cycle fatigue strength in a ti-17 alloy blade after foreign object damage // Eng. Fract. Mech. 2020. V. 241. P. 107385.
Krasnowski B.R., Rotenberger K.M., Spence W.W. A Damage Tolerance Method for Helicopter Dynamic Components // J. Am. Helicopter Soc. 1991. V. 36. № 2. P. 52–60.
Lazzeri L., Mariani U. Application of Damage Tolerance principles to the design of helicopters // Int. J. Fatigue. 2009. V. 31. № 6. P. 1039–1045.
Jones R. Fatigue crack growth and damage tolerance // Fatigue Fract. Eng. Mater. Struct. 2014. V. 37. № 5. P. 463–483.
Tavares S.M.O., de Castro P.M.S.T. An overview of fatigue in aircraft structures // Fatigue Fract. Eng. Mater. Struct. 2017. V. 40. № 10. P. 1510–1529.
Ramesh Talreja, Nam Phan. Assessment of damage tolerance approaches for composite aircraft with focus on barely visible impact damage // Compos. Struct. 2019. V. 219. P. 1–7.
Giglio M., Beretta S., Mariani U., Ratti G. Defect tolerance assessment of a helicopter component subjected to multi-axial load // Eng. Fract. Mech. 2010. V. 77. № 13. P. 2479–2490.
Adams D.O., Tritsch D.E. Flaw tolerance substantiation test results for S-92 dynamic components/The 28th European Rotorcraft Forum, Bristol, UK, 2002.
Struzik A. NH90 Qualification According to Damage Tolerance// Icaf Structural Integrity Influence of Efficiency & Green Imperatives. 2011. P. 877–897.
Wang B., Zhang Z., Shao C., Duan Q., Pang J., Yang H., Li X., Zhang Z.F. Improving the high-cycle fatigue lives of Fe–30Mn–0.9C twinning-induced plasticity steel through pre-straining // Metall. Mater. Trans. A. 2015. V. 46. № 8. P. 3317–3323.
Shiozawa K., Lu L., Ishihara S. S-N curve characteristics and subsurface crack initiation behavior in ultra-long life fatigue of a high carbon-chromium bearing steel // Fatigue Fract. Eng. Mater. Struct. 2001. V. 24. № 12. P. 781–790.
Yao W.X. Fatigue life prediction of structures. National Defence Industry Press, 2003.
Qiu Y., Pang J.C., Zhang M.X., Zou C.L., Li S.X., Zhang Z.F. Influence of temperature on the high-cycle fatigue properties of compacted graphite iron // Int. J. Fatigue. 2018. V. 112. P. 84–93.
Pollak R., Palazotto A., Nicholas T. A simulation-based investigation of the staircase method for fatigue strength testing// Mech. Mater. 2006. V. 38. № 12. P. 1170–1181.
Zhang X.P., Zhang C.C., Xing H.N. Test Study on Fatigue Property for Forging and Casting Steels of Grade E // Adv. Mater. Res. 2013. V. 712–715. № 1. P. 82–86.
Kumar R.K., Sampathkumaran P., Seetharamu S., Kumar S.A., Pramod T., Naveen G.J. Investigation of shot peening effect on titanium alloy affecting surface residual stress and roughness for aerospace applications // Second Structural Integrity Conference & Exhibition. 2018. Procedia Structural Integrity. 2019. V. 14. P. 134–141.
Liu Y., Qu N. Obtaining high surface quality in electrolyte jet machining tb6 titanium alloy via enhanced product transport // J. Mater. Process. Technol. 2020. V. 276. P. 116381–116381.
Liu J., Sun J., Zaman U.K.U., Chen W. Influence of wear and tool geometry on the chatter, cutting force, and surface integrity of tb6 titanium alloy with solid carbide cutters of different geometry // Strojniski Vestn. J. Mech. Eng. 2020. V. 66. № 12. P. 709–723.
van der Walt J.P., Nurick A. Static pressure distribution in the inlet of a helicopter turbine compressor // J. Aircr. 1994. V. 31. № 6. P. 1411–1413.
Murakami Y. Metal Fatigue: Effects of small defects and non-metallic inclusions // Mater. Corros. 2003. V. 54. № 3. P. 198. Elsevier Science, 2002. 369 p.
Дополнительные материалы отсутствуют.
Инструменты
Физика металлов и металловедение