Физика металлов и металловедение, 2021, T. 122, № 10, стр. 1033-1041
Влияние скандия на микроструктуру сплава системы Al–Cu–Mn–Mg–Hf–Nb
В. В. Яшин a, *, Е. В. Арышенский b, А. М. Дриц a, Ф. В. Гречников b, c, А. А. Рагазин a, В. Е. Баженов a
a АО “Арконик СМЗ”
443051 Самара, Россия
b Самарский национальный исследовательский университет имени академика С.П. Королева
443086 Самара, Россия
c Федеральное государственное бюджетное учреждение науки
Самарский федеральный исследовательский центр Российской академии наук
443001 Самара, Россия
d Национальный исследовательский технологический университет “МИСиС”
119049 Москва, Россия
* E-mail: Vasiliy.Yashin@arconic.com
Поступила в редакцию 24.09.2020
После доработки 16.06.2021
Принята к публикации 18.06.2021
Аннотация
Проведено исследование влияния добавок скандия, на микроструктуру и механические свойства сплава системы Al–Cu–Mn–Mg–Nb–Hf. Проведен теоретический расчет фазового состава сплава при помощи программного продукта Thermo-Calc. Отлиты опытные слитки сплава со скандием и без, которые затем прошли гомогенизацию, отжиг на распад пересыщенного твердого раствора, прокатку на лабораторном стане и отжиг на рекристаллизацию. На каждом этапе образцы изучали методами оптической и электронной микроскопии (при помощи просвечивающего микроскопа). Показано, что фазовый состав сплава без скандия включает наличие вторичных частиц Al12Mn, Al2CuMg4 и Al20Cu2Mn3 размерами от 10 до 200 нм, сплав со скандием отличается наличием частиц Al3(ScxHf1 –x). Массовая доля этой фазы после гомогенизации составляет 0.5%, далее при температуре отжига 300°С она увеличивается до 1.9%. Благодаря наличию этих частиц, процесс деформации при температуре 380–400°С идет без признаков рекристаллизации, а разупрочнение происходит только за счет процессов возврата. Отжиг при повышенных температурах (540°С) запускает процесс статической рекристаллизации, в ходе которой происходит формирование микроструктуры с условным средним диаметром зерна 8 мкм. На сплаве без скандия количество блокирующих частиц недостаточно для того, чтобы сдерживать миграцию границ при отжиге, и размер зерна при тех же параметрах обработки остается более 26 мкм.
ВВЕДЕНИЕ
В настоящее время востребованы новые сплавы, имеющие существенно более высокие прочностные характеристики в сочетании с высокой технологичностью [1–9]. Один из способов улучшения прочностных свойств алюминиевых сплавов – это легирование их переходными металлами. При распаде пересыщенных твердых растворов переходных металлов в алюминии образуются частицы структурного типа L12, которые обладают очень полезным свойством – сдерживать миграцию зеренных границ [10–14]. В настоящей работе проведено исследование влияния добавки скандия на микроструктуру и механические свойства сплава системы Al–Cu–Mn–Mg–Nb–Hf с низким содержанием легирующих элементов. Такая композиция позволит вести высокотемпературную гомогенизацию (≈600°С), с сохранением высокой степени пресыщенности твердого раствора по переходным металлам. После отжига такого сплава (≈300°С) будет получаться гетерофазная структура с интерметаллидами размерами около 1–10 мкм, содержащими Cu, Mn и Mg и с дисперсоидами структуры L12 размерами менее 250 нм. В процессе деформации вокруг крупных интерметаллидов происходит накопление дополнительных напряжений, которые релаксируют с разворотом областей решетки, что приводит к появлению дополнительных мест образования зародышей при рекристаллизации [15–17]. Новые зерна не увеличиваются в размерах за счет блокировки роста границ зерен дисперсоидами структуры L12. Благодаря сочетанию этих двух факторов, в полуфабрикате получается мелкозернистая структура, которая, в свою очередь, является необходимым условием для получения сверхпластичного состояния. Полученная мелкозернистая структура служит для заготовок под интенсивную пластическую деформацию, в ходе которой получают ультрамелкозернистую структуру [18–20].
Предельная растворимость ниобия (Nb), гафния (Hf) и скандия (Sc) в твердом алюминии при температуре 662–665°С составляет 0.22% (здесь и далее по тексту статьи все концентрации указаны в массовом соотношении), 1.2 и 0.55% соответственно. При снижении температуры предельная растворимость снижается: ниобия до 0.1% (при 327°С) [22, 24–27], гафния до 0.43% (при 427°С) [21, 28, 29], скандия до 0.01% (при 300°С) [23, 30]. Совместное же легирование этими элементами снижает предельную растворимость в разы, в результате чего можно добиться двойного эффекта, первый – модифицирование литой структуры сразу после литья, и второй – получение мелкозернистой структуры за счет контролируемой рекристаллизации.
Поэтому цель данной работы – изучение влияния скандия на зеренную структуру и формирование упрочняющих наночастиц в сплаве Аl–1.75% Cu–1.15% Mn–1.04% Mg–0.3% Nb–0.5% Hf при литье, высокотемпературной гомогенизации, низкотемпературном отжиге, горячей деформации и отжиге на рекристаллизацию.
МЕТОДИКА ПРОВЕДЕНИЯ ЭКСПЕРИМЕНТА
Опытные плавки проводили в индукционной печи средней частоты, с графитовым тиглем, масса плавки 10 кг. Масса отливаемого слитка составляла 3 кг.
В качестве шихты для приготовления сплавов использовали следующие материалы: первичный алюминий высокой чистоты марки А95, чушковый магний первичный марки Мг90, дробленная медь марки М1, лигатура в виде слитка Al–Sc2, лигатура марки Al–Mn10, лигатура собственного производства Al–Nb2, Аl–Hf2.
При производстве лигатуры марок Al–Hf2, Al–Nb2 использовали следующие материалы: первичный алюминий марки A85, гафний марки ГФИ1, ниобий марки НбШ0.
После расплавления алюминия и достижения температуры 730°С производили снятие шлака с поверхности расплава. Далее расплав нагревали до температуры 780–800°С и производили присадку лигатур Al–Sc2, Al–Nb2, Аl–Hf2 порциями по 300 г с последующим перемешиванием и выдержкой расплава в течение 5 мин и нагревом расплава до температуры присадки следующей порции. После присадки всей рассчитанной лигатуры расплав охлаждали до температуры 740°С и производили присадку легирующих компонентов (Cu, Mg, Mn) по расчету. Далее производили перемешивание расплава в течение 3-х мин с последующим нагревом расплава до температуры 740°С и отбор пробы на экспресс-анализ химического состава плавки. Температура литья 720–740°С.
Химический состава определяли методом спектрального анализа. Результаты анализа опытных плавок представлены в табл. 1.
Таблица 1.
Результаты химического анализа состава опытных плавок
Маркировка плавки | Массовая доля элемента, % | ||||||||
---|---|---|---|---|---|---|---|---|---|
Si | Fe | Cu | Mn | Mg | Nb | Hf | Sc | Al | |
А | 0.01 | 0.01 | 1.62 | 1.08 | 1.06 | 0.3 | 0.5 | – | Остальное |
А + Sc | 0.01 | 0.01 | 1.75 | 1.15 | 1.04 | 0.3 | 0.5 | 0.31 | Остальное |
Перед сливом расплава в кокиль его рафинировали карналлитовым флюсом из расчета 5 г на 1 кг загруженной шихты. Далее с поверхности расплава снимали шлак и сливали металл в кокиль из конструкционной стали. Разливку металла производили равномерной струей в течение 40 с. После затвердевания слиток извлекали из кокиля, охлаждали в воде и отправляли на гомогенизацию. Гомогенизацию проводили при 590°С в течение 4 ч в муфельной печи THERM CONCEPT KM 70/06/A. После гомогенизации проводили гетерогенизационный отжиг при 300°С в течение 4 ч для выделения частиц структуры L12.
Прокатку вели при температуре 380–400°С, в несколько проходов с суммарной степенью относительной деформации 60%. После прокатки полосу подвергали высокотемпературному отжигу для прохождения рекристаллизации и проводили очередной цикл проката (ε = 60%). Параметры прокатки представлены в табл. 2 . Данная процедура была повторена 3 раза.
Деформационную обработку проводили на лабораторном стане К220-75/300 (диаметр рабочих валков 220 мм). На каждом этапе от заготовки отбирали образцы на всестороннее исследование, включая:
Таблица 2.
Параметры прокатки
№ прохода | h0, мм | hк, мм | ε | $\varepsilon \cdot $ |
---|---|---|---|---|
1 | 40 | 16 | 0.92 | 2.75 |
2 | 16 | 6.4 | 0.92 | 4.35 |
3 | 6.4 | 2.56 | 0.92 | 6.88 |
4 | 2.56 | 1.02 | 0.92 | 10.88 |
– измерение электропроводности портативным прибором ВЭ-17НЦ, п/я Р-6409, г. Екатеринбург (погрешность измерения не более 2%);
– измерение твердости микротвердомером HV-1000, “Time Group Inc.”, Китай;
– размер зерна определяли на оптическом микроскопе Axiovert-40 МАТ, Carl Zeiss, Германия, в поляризованном свете (образцы перед изучением были подготовлены электрополированием в фтороборном электролите) с подсчетом среднего размера зерна методом секущих по ГОСТ 21073;
– определение интерметаллидов и дисперсоидов методом просвечивающей микроскопии (Tecnai G2 F20 S-TWIN TMP с термополевым катодом при ускоряющем напряжении 200 кВ);
– изучение химического состава структурных составляющих методом энергодисперсионной спектроскопии при помощи детектора X-Max 80T в диапазоне энергий 0–10 кэВ (энергетическое разрешение детектора составляет 122 эВ);
– исследование механических свойств при растяжении на универсальной испытательной машине (Zwick/Roell Z050).
Расчет фазового состава проводили с использованием программы Thermo-Calc 2016a [31]. Использовали термодинамическую базу TCAL4 (TCS Al-based alloy database, Version 4.0) [32]. Ввиду отсутствия в базе возможности ведения расчета по Nb, количество фаз с ниобием пересчитывали, исходя из диаграммы Al–Nb [21, 24].
РЕЗУЛЬТАТЫ ИССЛЕДОВАНИЯ И ОБСУЖДЕНИЕ
Сырое состояние. Изучение микроструктуры слитков в сыром состоянии показывает, что зеренное строение сплава со скандием значительно отличается от сплава без скандия. Структура сплава А имеет дендритное строение с условным диаметром зерна 290 мкм (см. рис. 1а). Микроструктура сплава А + Sc в исходном литом состоянии показана на рис. 1б. Сплав А + Sc имеет зеренное строение со средним размером зерна 70 мкм. На периферии отливки, где скорость охлаждения значительно выше, размер зерна 45 мкм.
Средние значения механических характеристик сплава в литом состоянии и после прокатки представлены в табл. 3. Из табл. 3 видно, что добавление скандия приводит к увеличению предела текучести на ≈30 МПа, а предела прочности на 107 МПа.
Таблица 3.
Механические свойства образцов исследуемых сплавов
Характеристики | Слиток | После проката № 4 | |
---|---|---|---|
А | А + Sc | А + Sc | |
σ0.2, МПа | 129 | 161 | 352 |
σв, МПа | 169 | 276 | 362 |
δ, % | 10 | 12.8 | 1.45 |
Для исследования эволюции частиц образцы были изучены посредством электронного просвечивающего микроскопа. По границам зерен в обоих сплавах располагаются частицы, содержащие в основном медь (см. рис. 2б) и в меньшем количестве марганец, железо и магний. Ниобий и гафний располагаются в объеме материала более однородно (см. рис. 2г, 2д), области, обогащенные данными элементами, не выявляются. По результатам исследования частиц в темном поле можно предположить, что на границе зерна располагаются сравнительно крупные (40 нм) частицы Al2CuMg и фазы Al20Cu2Mn3. В структуре образца сплава А + Sc в литом состоянии выявляются частицы со скандием, расположенные в объеме зерна, размеры которых изменяются в пределах 3–5 нм.
Рис. 2.
Микрорентгеноспектральный анализ сплава А + Sc: (а) изображение в светлом поле, (б) распределение меди, (в) гафния, (г) скандия, (д) ниобия.

Гомогенизация
Первый этап обработки — это гомогенизация, термообработка слитков при максимально возможной температуре. Исходя из результатов расчета в программном продукте Thermo-Calc, построен график изменения доли фаз сплава А + Sc (см. рис. 3), в зависимости от температуры (фазы с марганцем объединены на одной кривой, так же, как и фазы Al3Sc, Al3Nb и Al3Hf), который показывает, что при температуре 590°С в равновесном состоянии будут находиться фазы Al6Mn и Al28Cu4Mn7 в количестве около 2%, Al3(ScxHf1 –x) и Al3(NbyHf1 –y) в количестве до 0.5%.
Важно длительностью выдержки при гомогенизации не допустить коагуляции и потери их когерентности с матрицей. После гомогенизации выравнивание концентраций скандия в структуре металла не наблюдается. Выделение скандия происходит преимущественно на элементах дислокационной субструктуры с образованием фазы Al3Sc размерами (10–17 нм, см. рис. 4), с кристаллической решеткой L12, когерентной с матрицей.
Отжиг на распад пересыщенного твердого раствора
После гомогенизации низкотемпературный отжиг при температуре Т ≈ 300°С (см. рис. 1) приводит к выходу из твердого раствора магния, марганца и меди с образованием фаз Al12Mn и Al2CuMg4 и идет интенсивное образование частиц со скандием, ниобием и гафнием в количестве, близком к максимальному (≈0.83%). На протяжении термодеформационной обработки фазовая структура металла постоянно меняется, об этом свидетельствуют изменения таких свойств, как электропроводность и твердость (см. рис. 5). Очень показателен рост электропроводности от 13 до 17 МСм/м и твердости от 64.5 до 86 HV после отжига при 300°С, который свидетельствует о процессе распада пересыщенного твердого раствора с образованием упрочняющих дисперсоидов.
Исследования на микроскопе показывают, что после 4-х часов выдержки при температуре 300°С объем зерна сплава А и сплава А + Sc заполнен пластинчатой фазой Al20Cu2Mn3 (см. рис. 6б). Размеры пластин этой фазы достигают 200 нм, толщина не превышает 50 нм. В сплаве А + Sc часть пластин фазы Al20Cu2Mn3 образуется в областях с повышенной плотностью дислокаций рядом со сферическими частицами, богатыми Sc. На границах зерен также присутствуют вытянутые частицы неправильной формы с размерами до 2.5 мкм. Согласно ЭДС-анализу, химический состав близок к составу фазы Al2CuMg4. В сплаве А + Sc количество частиц Al3Sc значительно увеличивается как по границам зерен, так и внутри зерна, размеры их составляют 20 нм (рис. 6).
Рис. 6.
Структура образца сплава А + Sc в темном поле после гетерогенизационного отжига, полученные в рефлексах: (а) [111]Al + [111]Al3Sc + [041]Al3Hf; (б) [113]Al + [113]Al3Sc + [440] Al20Cu2Mn3 + [260]AlHf. Частицы, указанные белыми стрелками, являются Al3Sc или Al3Hf; указанные красными стрелками – Al20Cu2Mn3.
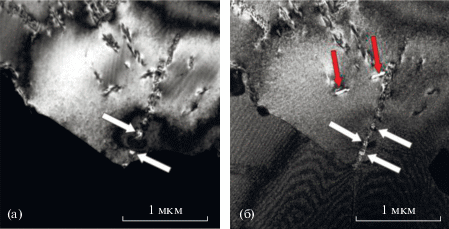
Прокатка и высокотемпературный отжиг
После первого цикла прокатки и последующего высокотемпературного отжига размер зерна соответствует величине 53–56 мкм (см. рис. 7, 8). После второго цикла обработки размер зерна уменьшается еще в два раза до 27–28 мкм. Дальнейшие циклы обработки не приводят к уменьшению размеров зерен на базовом сплаве (минимальный размер 26 мкм), но на сплаве с Sc продолжается измельчение микроструктуры, средний условный диаметр зерна после четвертого цикла соответствует величине 8 мкм. Частицы со скандием блокируют рост границ новых рекристаллизованных зерен, благодаря чему стало возможным получение столь мелкозернистой структуры. Нагрев до температуры 540°С переводит часть компонентов снова в твердый раствор, это видно по обратному изменению контролируемых свойств (электропроводность снова снижается до 13 МСм/м, а твердость до 71 HV). После третьего и четвертого высокотемпературного отжига электропроводность уже не возвращается на минимальный уровень (13 МСм/м) и соответствует 15 и 17 МСм/м соответственно, твердость постепенно снижается до начального уровня 64.5 HV. Предел текучести листов из сплава А + Sc после 4‑х циклов обработки увеличился более чем в два раза (см. таблицу 3).
Рис. 7.
Микроструктура в поляризованном свете: (а) после проката (первый проход); (б) первый проход + отжиг при 540°С – 2 ч; (в) после третьего прохода; г) третий проход + отжиг при 540°С – 2 ч.
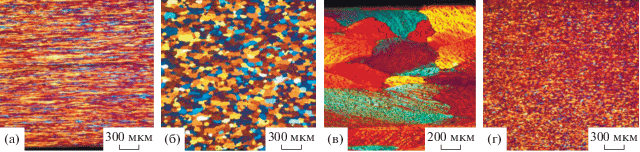
После первой прокатки (ε = 60%) при температуре 380–400°С образцы сплава А + Sc отличаются от образцов без скандия тем, что имеют развитую субзеренную структуру с относительно низкой дислокационной плотностью. Субзерна имеют как вытянутую форму, так и равноосную. Размеры субзерен варьируются в пределах 0.1–1.5 мкм. В объеме зерна равномерно распределены: агломераты фазы Al3Sc размером не более 50 нм и отдельные сферические частицы Al3Sc размером не более 10 нм. С меньшей степенью однородности в объеме зерна присутствуют: пластины фазы Al2CuMg4 с размерами, не превышающими 100 нм, и пластины фазы Al20Cu2Mn3 с размерами не более 300 нм (см. рис. 9). Замечена повышенная плотность выделений как фазы Al2CuMg4, так и фазы Al20Cu2Mn3 вблизи границ зерен. Также присутствуют строчечные выделения частиц с повышенным содержанием скандия и незначительным количеством Hf (до 0.1 ат. %). Частицы располагаются как на границах, так и в объеме субзерен. Частицы имеют вытянутую неправильную форму, толщину 30 нм, длину не более 300 нм.
Рис. 9.
ЭДС-профили через частицы Al2CuMg4 (S) и Al20Cu2Mn3 (T). Образец после первой прокатки ε = = 60%.
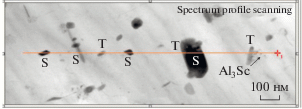
После второго и третьего этапов деформации на образцах со скандием происходит увеличение степени наклепа, отдельные дислокации не различаются (см. рис. 10). Размеры видимых субзерен составляют 0.1–1 мкм. В сплаве А + Sc в объеме зерен присутствуют сферические частицы Al3Sc размерами 100–250 нм. В составе частиц Al3Sc также имеется Hf (до 2–3 ат. %).
При помощи сканирующего электронного микроскопа произведена оценка удельного объема (f) дисперсоидов (частиц размером менее 1 мкм) и их средний диаметр (d). Изменение величины f/d для исследуемых сплавов представлены на графике рис. 11.
Отношение f/d показывает, насколько эффективно работает эффект торможения миграции границ [12]. Из рис. 11 видно, что максимальный эффект будет после отжига при 300°C, и на сплаве со скандием он почти в два раза выше, чем на сплаве без скандия.
ВЫВОДЫ
В работе проведено исследование влияния малой добавки скандия на эволюцию микроструктуры в экспериментальном сплаве системы Аl–Cu–Mn–Mg–Nb–Hf при его термомеханической обработке.
По мере обработки исследуемых сплавов, выявлены отличия в процессе эволюции зеренной микроструктуры, а именно показано, что с увеличением скорости деформации на сплаве со скандием удается зафиксировать структуру с размером зерна до 8 мкм, в сплаве без скандия снизить средний условный диаметр зерна на величину менее 26 мкм не получилось. Такой эффект объясняется повышенным количеством частиц структуры L12 в сплаве со скандием, которые эффективно тормозят миграцию границ в процессе рекристаллизационного отжига и не дают расти вновь образованным зернам. Исследование методом электронной сканирующей микроскопии показали, что такие частицы практически отсутствуют в сыром состоянии, часть выпадает уже при гомогенизации, наибольшее количество выделяется при отжиге 300°C, при последующем отжиге 540°C дисперсоиды увеличиваются в размерах и их эффективность снижается.
В сплаве без скандия выделенных частиц фаз Al12Mn, Al2CuMg4 и Al20Cu2Mn3 недостаточно, чтобы блокировать рост границ зерен.
Список литературы
Арышенский Е.В., Гук С.В., Галиев Э.Э., Дриц А.М., Кавалла Р. Оценка возможности применения сплава 1565ч в автомобильной промышленности // Деформация и разрушение материалов. 2018. № 9. С. 40–46.
Захаров В.В. Фисенко И.А. К вопросу о легировании алюминиевых сплавов скандием // Металловедение и термическая обработка металлов. 2017. № 5. С. 15–22.
Захаров В.В. О легировании алюминиевых сплавов переходными металлами // Металловедение и термическая обработка металлов. 2017. №. 2. С. 3–8.
Сизяков В.М., Бажин В.Ю., Власов А.А. Состояние и перспективы развития производства алюминия // Металлург. 2010. № 7. С. 4–7.
Акопян Т.К., Летягин Н.В., Белов Н.А., Кошмин А.Н., Гизатулин Д.Ш. Анализ микроструктуры и механических свойств нового деформируемого сплава на основе ((Al) + Al4 (Ca, La)) эвтектики // Физика металлов и металловедение. 2020. V. 121. № 9. P. 1003–1008.
Belov N.A., Korotkova N.O., Akopyan T.K., Timofeev V.N., Structure and Properties of Al–0.6% Zr–0.4% Fe–0.4% Si (wt %) Wire Alloy Manufactured by Electromagnetic Casting // Journal of the minerals metals and materials society (JOM). 2020. V. 72. № 4. P. 1561–1570.
Saitov A.V., Bazhin V.Y., Povarov V.G. On the application of lithium additives in the electrolytic production of primary aluminum // Russian Metallurgy (Metally). 2017. V. 2017. № 12. P. 1018–1024.
Косов Я.И., Бажин В.Ю. Особенности фазообразования при алюминотермическом получении лигатуры алюминий-эрбий // Металлург. 2018. № 5. С. 39–44.
Bazhin V.Y., Savchenkov S.A., Kosov Y.I. Specificity of the titanium-powder alloying tablets usage in aluminium alloys // non-ferrous metals. 2016. № 2. P. 52–56.
Колачев, Б.А., Ливанов В.А., Елагин В.И. Металловедение и термическая обработка цветных металлов и сплавов // Учеб. для вузов 3-е изд., перераб. и доп. М.: МИСИС, 2001. 416 с.
Belov N.A., Alabin A.N., Matveeva L.A. Optimization of phase composition of Al–Cu–Mn–Zr–Sc alloys for rolled products without requirement for solution treatment and quenching // J. alloys and compounds. 2014. T. 583. P. 206–213.
Яковлев А.А. Исследование и разработка технологии получения слитков алюминиевых сплавов системы Al–Cu–Mn–Zr–Sc с целью изготовления из них деформированных полуфабрикатов без использования операций гомогенизации и закалки // Дис. Нац. исслед. технол. ун-т, 2015. С. 211.
Chen B.A., Pan L., Wang R.H., Liu G., Cheng P.M., Xiao L., Sun J. Effect of solution treatment on precipitation behaviors and age hardening response of Al–Cu alloys with Sc addition // Materials Science and Engineering: A. 2011. T. 530. C. 607–617.
Захаров В.В., Филатов Ю.А., Фисенко И.А. Легирование алюминиевых сплавов скандием // Металловедение и термическая обработка металлов. 2020. № 8. С. 31–36.
Кищик М.С., Михайловская А.В., Котов А.Д., Дриц А.М., Портной В.К. Влияние режимов гетерогенизационного отжига перед холодной прокаткой на структуру и свойства листов из сплава 1565ч // Металловедение и термическая обработка металлов. 2019. № 4. С. 25–31.
Humphreys F., Rollett A., Rohrer G.S., Hatherly M. Recrystallization and related annealing phenomena // B.: Elsevier Science. 2012. P. 658.
Тептерев М.С. Арышенский Е.В., Гук С.В., Баженов В.Е., Дриц А.М., Кавалла Р. Исследование влияния режимов отжига на эволюцию зеренной структуры и интерметаллидных фаз в холоднокатаной ленте из алюминиево-магниевого сплава // Физика металлов и металловедение. 2020. № 121(9). С. 995–1002.
Бродова И.Г. Ширинкина И.Г., Распосиенко Д.Ю., Акопян Т.К. Эволюция структуры закаленого Al–Zn–Mg–Fe–Ni-сплава в процессе интенсивной пластической деформации и отжига // Физика металлов и металловедение. 2020. Т. 121. № 4. С. 987–994.
Ширинкина И.Г., Бродова И.Г. Структурно-фазовые превращения при отжиге Al–Zn–Mg–Fe–Ni-сплава после кручения при высоком давлении // Физика металлов и металловедение. 2020. Т. 121. № 4. С. 388–395.
Кайгородова Л.И., Распосиенко Д.Ю., Пушин В.Г., Пилюгин В.П., Смирнов С.В. Влияние отжига на структуру и свойства стареющего сплава Al–Li–Cu–Mg–Zr–Sc–Zn, подвергнутого мегапластической деформации // Физика металлов и материаловедение. 2019. Т. 120. № 1. С. 169–175.
Арышенский Е.В., Арышенский В.Ю., Яшин В.В., Дриц А.М., Гречников Ф.В. Высокопрочный термостойкий мелкозернистый сплав на основе системы Al–Cu–Mn–Mg–Sc–Nb–Hf и изделие из него. Заявка № 2020130600 от 17.09.2020.
Мондольфо Л.Ф. Структура и свойства алюминиевых сплавов М.: Металлургия. 1979. С. 640.
Røyset, J., Ryun N. Scandium in aluminium alloys // International Materials Reviews. 2013. № 50(1). P. 19–44.
Elliott R.P., Shunk F.A. The Al−Nb system (Aluminum–Niobium) // Bulletin of Alloy Phase Diagrams. 1981. № 2. P. 75–81.
Латушкин И.А., Яшин В.В., Рагазин А.А., Арышенский В.Ю., Арышенский Е.В. Влияния микролегирования алюминиевых сплавов редкоземельными элементами на структуру литейной заготовки // Наследственность в литейно-металлургических процессах. 2018. С. 374–386.
Яшин В.В., Кабанов А.С., Арышенский Е.В., Латушкин И.А. Влияние микролегирования алюминиевого сплава АМг5 переходными металлами (Sc, Zr, Nb) на структуру литой заготовки // Цветные металлы. 2019. № 2. С. 56–61.
Казакова Е.Ф., Дмитриева Н.Е., Дунаев С.Ф. Взаимодействие алюминия с ниобием и скандием в равновесных и неравновесных состояниях // Вестник Московского университета. 2015. Т. 56. № 1. С. 41–47.
Hallem H. Lefebvre W., Forbord B., Danoix F., Mathinsen K. The formation of Al3(ScxZryHf1 – x − y)-dispersoids in aluminium alloys // Materials Science and Engineering: A. 2006. T. 421. № 1–2. C. 154–160.
Rokhlin, L.L., Bochvar N.R., Dobatkina T.V., Leont’ev V.G. Al-rich portion of the Al–Hf phase diagram // Russian Metallurgy (Metally). 2009. № 3. P. 258–262.
Fuller, Christian B. David N. Seidman, David C. Dumand Mechanical properties of Al(Sc,Zr) alloys at ambient and elevated temperatures // Materials Science and Engineering. 2003. V. 51. P. 4803–4814.
Andersson J.O., Helander T., Höglund L., Shi P.F., Sundman B. Thermo-Calc and DICTRA, Computational tools for materials science // CALPHAD. 2002. № 26. P. 273–312.
Thermo-Calc Software TCAL4 Al-based alloy database, Version 4.0 (accessed 1 August 2020).
Дополнительные материалы отсутствуют.
Инструменты
Физика металлов и металловедение