Физика металлов и металловедение, 2021, T. 122, № 11, стр. 1171-1178
Влияние золь-гель-метода герметизации на коррозионную стойкость плазменно напыленных покрытий WC–12% Co
М. А. Ашраф a, А. Салман a, М. У. Манзур a, *, А. Фарук a
a Институт металлургии и материаловедения, Университет Пенджаба
54590 Лахор, Пакистан
* E-mail: umar.imme@pu.edu.pk
Поступила в редакцию 06.02.2019
После доработки 14.06.2021
Принята к публикации 24.06.2021
Аннотация
Покрытия WC–12% Co, полученные плазменным напылением, благодаря своим превосходным механическим свойствам находят применение, например, в износостойких соплах, а также, в режущих инструментах и сверлах. Однако коррозионные свойства этих покрытий ухудшаются из-за их пористости, что позволяет агентам агрессивных сред проникать сквозь покрытие и достигать металлической подложки. Цель данной работы – повышение коррозионной стойкости покрытий WC–12% Co, получаемых плазменным напылением, посредством герметизации их пор золь-гель методом. Степень пористости в напыленных и герметизированных покрытиях оценивали по стандартному методу Международной организации стандартов (ASTM). При этом наличие герметика в порах было подтверждено методами растровой электронной микроскопии и энерго-дисперсионной рентгеновской спектроскопии. Электрохимические испытания в 3.5 вес. % растворе NaCl были использованы для изучения коррозионной стойкости напыленных и герметизированных покрытий. Результаты оценки пористости показали значительное снижение (на 75%) пористости покрытия после герметизирующей обработки. Электрохимические испытания показали, что покрытие после герметизации обладает отличным антикоррозионным потенциалом (–452 мВ) по сравнению с Ag/AgCl, демонстрирует более низкую плотность тока коррозии (3.07 мкА/см2) и более высокое сопротивление поляризации (162.649 кОм см2) по сравнению с напыленным покрытием, следовательно, герметизация повышает коррозионную стойкость покрытия.
ВВЕДЕНИЕ
WC–Co-покрытия обладают сочетанием высокой твердости и хорошей ударной вязкости благодаря твердым частицам карбида вольфрама WC и пластичной кобальтовой (Co) матрице [1]. Эти покрытия были нанесены на различные металлические материалы, чтобы повысить их износостойкость и твердость поверхности. Для нанесения этих покрытий используются такие методы термического напыления как воздушно-плазменное напыление (ВПН), высокоскоростное газоплазменное (ВСГП) напыление и детонационное напыление [2, 3]. В процессах термического напыления распыляемый материал получает тепло от источника тепла, и расплавленные или полурасплавленные частицы генерируются и направляются на поверхность подложки для образования покрытия заметной толщины. ВПН-процесс напыления обеспечивает высокотемпературную стабильность покрытий и их улучшенное межфазное сцепление (30–70 МПа) с подложкой. Однако наличие трещин и высокая пористость (2–5%) покрытий плазменного напыления ухудшают их коррозионные свойства, позволяя агентам агрессивных сред проходить через поверхность покрытия и достигать подложки [4, 5].
Для уменьшения микроструктурных дефектов в покрытиях, полученных термическим напылением, были разработаны методы последующей обработки, такие как переплавка, термообработка и герметизация [6–8]. Процессы переплавки и термообработки позволяют значительно улучшить свойства покрытий [9]. Однако тепловые воздействия во время этих процессов могут вызвать термические напряжения и в конечном итоге привести к образованию трещин в покрытиях [10]. Процесс герметизации является удобным и широко используемым методом обработки покрытий, полученных термическим напылением. В этом процессе жидкие герметики проникают в несплошности покрытий, такие как поры и трещины, а последующая термическая обработка приводит к затвердеванию герметика с последующим запечатыванием приповерхностных пор и трещин [11].
Растворы герметиков должны обладать определенными характеристиками, такими как хорошее смачивание, низкая вязкость и высокое поверхностное натяжение, чтобы эффективно проникать в пористые структуры [12]. Различные растворы герметиков были использованы для запечатывания пор в покрытиях, полученных термическим напылением, чтобы повысить их коррозионные свойства. Ваном с соавт. изучено влияние использования герметиков из ортосиликата натрия, фосфата алюминия и соли церия на коррозионную стойкость покрытий на основе Fe и установлено, что герметики эффективно закрывают поры в покрытиях и повышают коррозионную стойкость этих покрытий [13]. Шао и др. обнаружили, что герметизация плазмонапыленных покрытий Cr2O3–Al2O3 посредством фосфата алюминия повышает их коррозионные свойства [14]. Чжан с соавт. герметизировали ВСГП напыленные наноструктурированные металлокерамические покрытия WC–CoCr фосфатом алюминия методом уплотнения с ультразвуковым возбуждением. Их исследование показало, что герметичные покрытия демонстрируют превосходную коррозионную стойкость в двух различных электролитах [15].
Растворы золь-гель-герметиков также привлекли внимание для герметизации из-за их низкой вязкости. Amousoltani и др. исследовали применение раствора золь-гель герметика, содержащего смесь триизопропилата алюминия и 1,2-пропандиола, для герметизации ВСГП напыленных покрытий WC–Co. Их результаты показали, что коррозионные и износостойкие свойства покрытий улучшились после герметизирующей обработки [16]. Раствор герметика, содержащий изопропоксид алюминия Al (OC3H7)3 и изопропиловый спирт (C3H8O), был использован для герметизации покрытий YSZ, полученных плазменным напылением, и покрытий WC–CoCr, полученных ВСГП напылением, для улучшения их защитных характеристик [17, 18]. Предыдущие исследования доказали, что исходный золь-гель-реагент пропитывает термически напыленные покрытия, образуя мелкий порошок после гидролиза и конденсации in situ.
Из приведенного выше обзора литературы видно, что герметизирующая обработка проводилась на термически напыленных покрытиях различных типов. Вместе с тем герметизация может оказаться более эффективной в плазменно напыленных покрытиях из-за их более высокой пористости и присутствия структурных дефектов. Было установлено, что очень мало исследований проводится для улучшения коррозионных свойств плазмо-напыляемых покрытий методом герметизации. Кроме того, отсутствует литература о влиянии золь-гель герметизации на коррозионную стойкость покрытий WC–12% Co, полученных плазменным напылением. Поэтому целью данной работы было запечатать поры в покрытии WC–12% Co, полученном плазменным напылением, золь-гель герметиком для повышения коррозионной стойкости этого покрытия. Покрытие насыщали раствором золь-гель-герметика с последующей обработкой его отвердителем. Изучены и сопоставлены микроструктурные особенности и коррозионные свойства свеженапыленных покрытий и герметизированных покрытий.
МЕТОДИКА ЭКСПЕРИМЕНТА
Порошок WC–12% Co с размером частиц 15–75 мкм распыляли на подложки из нержавеющей стали AISI 321 (∅ = 25.4 × 3 мм) методом воздушно-плазменного напыления. Перед напылением, подложки подвергали пескоструйной обработке (с использованием корунда дисперсностью 60 меш (60 частиц одинакового линейного размера на 1 линейный дюйм) при давлении 0.7–0.8 МПа и “прицельном” расстоянии 5–10 мм. После пескоструйной обработки подложки очищали ацетоном и этанолом с последующей сушкой в печи. Средняя шероховатость (Ra) поверхности подложки составила 4.6 мкм. Покрытия WC–12% Co были нанесены на подложки с помощью оборудования (модели SX-80) для атмосферного плазменного напыления; аргон использовался в качестве первичного газа, а водород – в качестве вторичного.
Подробная информация о параметрах плазменного напыления приведена в табл. 1.
Таблица 1.
Параметры плазменного напыления
Параметр | Значение |
---|---|
Электр. напряжение | 40 В |
Эл. ток | 650 А |
Скорость подачи порошка | 50 г/мин |
Расстояние до поверхности напыления | 120 мм |
Скорость подачи первичного газа (Ar) | 30 л/мин |
Скорость подачи вторичного газ (H2) | 4 л/мин |
Герметик был приготовлен посредством дефлегмирования смеси оптимизированных количеств изопропоксида алюминия и изопропанола при 90°C в течение 4 ч на нагревательной бане. Напыленные покрытия обезжиривали путем промывки в ацетоне и этаноле с последующей сушкой в печи. После этого образцы покрытий погружали в раствор герметика на 10 мин. Затем образцы погружали в 0.1 молярный раствор HCl для катализа образования геля с последующим отвердением при 120°C в течение 24 ч для увеличения плотности геля оксида алюминия. Образцы покрытий после герметизации были слегка обработаны наждачной бумагой SiC (1200 зернистости), чтобы удалить излишки герметика с поверхности покрытия во избежание каких-либо ошибок в расчетах пористости и результатах электрохимических испытаний.
Пористость свеженапыленных и герметизированных покрытий измеряли стандартным методом ASTM (C20-00) для оценки эффективности герметизации [19].
В основе оценки пористости покрытий лежали следующие уравнения:
(1)
${\text{Объем пор}} = V = {{(M--S)} \mathord{\left/ {\vphantom {{(M--S)} {{{\rho }_{{{\text{воды}}}}}}}} \right. \kern-0em} {{{\rho }_{{{\text{воды}}}}}}};$Фазовый состав напыленного покрытия исследовали с помощью рентгеновского дифрактометра (D8 Advance, Bruker, США) с изменением угла 2θ от 20° до 90°. Изменения морфологии и микроструктуры покрытий до и после герметизации исследовали с помощью растрового электронного микроскопа (РЭМ), работавшего при 20 кВ (SU8230, Hitachi, Япония). Наличие герметика в герметизированных покрытиях было подтверждено методом энерго-дисперсионной рентгеновской спектроскопии (ЭДС). Коррозионные свойства свеженапыленных и герметизированных покрытий оценивали в процессе электрохимических испытаний в 3.5-вес. % растворе NaCl при комнатной температуре (35 ± 1°C). Эти испытания проводили в трехэлектродной ячейке, соединенной с потенциостатом (Interface 1000E, Gamry Instruments, США), в которой Ag/AgCl электрод (насыщенный KCl) использовали в качестве электрода сравнения, графитовый стержень в качестве вспомогательного электрода, а напыленные покрытия с открытой площадью 1 см2 в качестве рабочих электродов. Перед каждым испытанием рабочий электрод погружали в электролит на 1 час для стабилизации потенциала. Потенциал разомкнутой цепи (ПРЦ) измеряли в течение 1000 с, а графики потенциодинамической поляризации получали путем поляризации поверхности покрытия со скоростью сканирования 1 мВ/с в диапазоне сканирования – 0.5–1.5 В относительно ПРЦ. Кривые спектроскопии электрохимического импеданса (СЭИ) всех образцов покрытия были получены в диапазоне частот от 100 кГц до 0.01 Гц с пульсирующим потенциалом переменного тока ±5 мВ. Софт “Echem Analys” версии 6.03 использовали при измерении кинетических параметров и при подгонке модели эквивалентной электрической цепи (ЭЭЦ) для понимания механизма коррозии по кривым частотного разряда и СЭИ кривых соответственно.
РЕЗУЛЬТАТЫ И ОБСУЖДЕНИЕ
На рис. 1 представлена рентгенограмма, полученная со свеженапыленного покрытия WC–12% Co, подтверждающая присутствие в нем фаз WC, W2C, W и W3Co3C. Образование фаз, не содержащих WC, указывает на значительное окисление и обезуглероживание покрытия во время его напыления. В процессе напыления, обезуглероживание (потеря углерода) частиц WC происходит в условиях высоких температур и в присутствии кислорода с образованием газа CO. Обезуглероживание приводит к образованию углерододефицитных фаз, таких как W2C и чистый W, за счет карбида WC [20].
На рис. 2 показаны РЭМ микроизображения структуры плазмо-напыленного покрытия WC–12% Co перед его герметизацией. Микроструктура покрытий отражает типичные особенности плазмо-напыляемых покрытий, с определенными дефектами. Более того, “топография” покрытий указывает на шероховатую поверхность, содержащую открытые и полузакрытые поры. Пористость играет решающую роль в определении коррозионной стойкости покрытий, наносимых термическим напылением.
Рис. 2.
РЭМ-изображения микроструктуры свеженапыленного покрытия: (а) поверхность, (б) поперечное сечение.
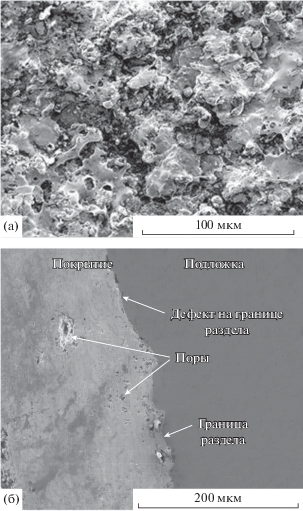
Соединенные между собой поры позволяют ионам электролита проникать до подложки и вступать во взаимодействие с ней [21]. Наличие пористости (диаметр пор ≤10 мкм) в покрытиях обусловлено захватом воздуха или газов в процессе затвердевания покрытий и реакцией частиц осаждаемого материала с воздухом [22]. Средняя пористость свеженапыленного покрытия, измеренная по стандарту ASTM C20-00, составляет 3.51%. Толщина нанесенного покрытия составляет приблизительно 220 ± 10 мкм, и покрытие демонстрирует хорошую адгезию с подложкой, как показано на микрофотографии поперечного сечения образца (рис. 2б).
На рис. 3 показана морфология поверхности герметизированного покрытия WC–12% Co. По-видимому, никаких видимых изменений в структуре покрытия после герметизирующей обработки не наблюдается. Однако на изображении при большем увеличении (рис. 3б) видно, что герметик присутствует в открытых порах поверхности покрытия, подвергшейся процедуре “герметизации”.
На микроизображениях видно, что поры не полностью заполнены частицами герметика. Основная причина этого явления заключается в том, что первоначально, проникая в поры, герметик был жидким, и обработка, приводящая к отвердеванию герметика, вызвала чрезмерное испарение растворителя. Следовательно, герметик испытывает “декомпозицию” с образованием твердых частиц внутри пор [23]. Средняя пористость герметизированного покрытия, измеренная по методу ASTM C20-00, составляла 0.75%. Снижение пористости герметизированных покрытий подтверждает эффективность золь-гель-метода герметизации. Ожидается, что уменьшенная открытая пористость покрытия, прошедшего процедуру герметизации, повысит его коррозионную стойкость.
Присутствие включений герметика в порах герметизированного покрытия также подтверждается ЭДС-анализом. Точечный ЭДС анализ пористых областей (точка А) указывает на присутствие Al (25.90 вес. %) и O (36.16 вес. %) наряду с первичными элементами покрытий, такими как W, C и Co. В то время как в “плотной” области (точка В) присутствуют только первичные элементы, включая W (75.51 вес. %), C (13.01 вес. %) и Co (11.48 вес. %).
На рис. 4 изображены ПРЦ-кривые для свеженапыленных и для герметизированных покрытий WC–12% Co, погруженных в 3.5-вес. % раствор NaCl в течение 1000 с. Видно, что значения потенциала обоих покрытий оставались стабильными на протяжении всего испытания. В конце испытания значения ПРЦ потенциала свеженапыленных и герметизированных покрытий относительно Ag/AgCl электрода составляли: ‒539 и –229 мВ соответственно. Замечательный потенциал герметизированного покрытия был связан с его плотной микроструктурой, которая препятствовала проникновению электролита. Это означает, что поры внутри покрытия закрываются после герметизирующей обработки, и открытая пористость становится меньше, чем у свеженапыленного покрытия, благодаря чему герметизированное покрытие обладает лучшим барьерным эффектом [21].
Потенциодинамические поляризационные кривые свеженапыленных и герметизированных покрытий показаны на рис. 5. Катодная ветвь поляризационных кривых почти одинакова для обоих покрытий. Поскольку 3.5-вес. % раствор NaCl нейтрален по своей природе, то восстановление при катодной поляризации на поверхности покрытия будет реакцией восстановления кислорода в соответствии с реакцией, описываемой уравнением (3) [24].
(3)
${{{\text{O}}}_{2}} + 2{{{\text{H}}}_{{\text{2}}}}{\text{O}} + 4{{{\text{e}}}^{ - }} \to ~4{\text{OH}}.$Соответствующая анодная ветвь для обоих образцов покрытия показывает область растворения или активации при низком потенциале и область поляризации эл. сопротивления при высоком потенциале. Кинетические параметры, такие как потенциал коррозии (Ecorr), плотность тока коррозии (Icorr) и скорость коррозии свеженапыленных и герметизированных покрытий, рассчитываются по поляризационным кривым с помощью процедуры подгонки Тафеля в области активации анодной и катодной ветвей, их значения проиллюстрированы в табл. 2. Согласно результатам поляризации, можно наблюдать положительный сдвиг в значениях Ecorr в случае герметизированного покрытия (–452 мВ отн. Ag/AgCl) относительно случая свеженапыленного покрытия (–771 мВ отн. Ag/AgCl). Как правило, характеристика Ecorr описает термодинамические свойства, и более высокое значение Ecorr указывает на низкую склонность к коррозии [25]. Очевидно, что герметизированное покрытие имеет более высокое значение Ecorr по сравнению со свеженапыленным покрытием, что связано с герметизацией пор, которая повысила барьерные характеристики покрытия, сделав его менее проницаемым для электролита [26]. Более низкое значение Ecorr свеженапыленного покрытия связано с его относительно более пористой и дефектной микроструктурой, которая обеспечивает проход химически активных ионов, таких как Cl, через покрытие. Icorr является важным параметром для оценки кинетики коррозионной реакции, и более низкое значение Icorr указывает на более высокую коррозионную стойкость [27]. Значения Icorr для свеженапыленных и герметизированных покрытий составляют 35.40 и 3.07 мкА/см2 соответственно. Очевидно, что величина Icorr герметизированного покрытия намного ниже, чем у свеженапыленного покрытия. Это подтверждает снижение скорости коррозии более чем в десять раз после герметизирующей обработки. На основании полученных результатов можно предположить, что герметизирующая обработка повысила плотность микроструктуры покрытия и, следовательно, его коррозионную стойкость.
Таблица 2.
Значения кинетических параметров свеженапыленных и герметизированных покрытий в 3.5‑вес. % NaCl
Образец покрытия | Ecorr, мВ | Icorr, мкA/cм2 | Скорость коррозии, м/год |
---|---|---|---|
Свеженапыленный | –771 | 35.40 | 15.30 |
Герметизированный | –452 | 3.07 | 1.31 |
На рис. 6 показаны спектры импеданса (графики Найквиста) свеженапыленных и герметизированных покрытий после выдержки в 3.5-вес. % растворе NaCl. Можно видеть, что емкостная дуга для герметизированного покрытия выглядит как полукруг, в то время как дуга для свеженапыленного покрытия представляет собой “сплющенную” дугу. Эта особенность свидетельствует о том, что характеристики защитных пленок были различными в соответствующих покрытиях [15]. Кроме того, график Найквиста позволяет сравнивать емкостную дугу для покрытий обоих типов. Хорошо известно, что больший радиус емкостной дуги соответствует более высокой коррозионной стойкости или большему сопротивлению переноса заряда из-за двойного слоя [28]. Из рис. 6 можно сделать вывод, что герметизированное покрытие обладает более высокой коррозионной стойкостью по сравнению со свеженапыленным покрытием.
Для расчета количественных параметров механизма деградации покрытия результаты импеданса, представленные на графиках Найквиста, прошли предварительную подгонку для приведения их в соответствие с результатами конкретной модели эквивалентной электрической цепи (ЭЭЦ).
Модели ЭЭЦ показаны на рис. 7, а полученные значения проиллюстрированы в табл. 3. В выбранной нами модели ЭЭЦ параметры Rs, Rp, Yc и Yd представляют сопротивление раствора (Rs) между покрытием (рабочим электродом) и электродом сравнения, поляризационное сопротивление (Rp), обеспечиваемое покрытием, неидеальная емкостная составляющая (Yc) реактивного сопротивления границы раздела “покрытие/подложка” и неидеальная емкостная составляющая (Yd) реактивного сопротивления диэлектрического материала, присутствующего в покрытии. Видно, что значение Rp герметизированного покрытия (162.649 кОм см2) выше, чем у свеженапыленного (0.326 кОм см2) покрытия. Это означает, что герметизированное покрытие имеет наименьшую пористость среди всех покрытий, поэтому оно является наиболее коррозионностойким [29]. Величина Rp определяется значением поляризации, поскольку герметизированное покрытие имеет более низкую скорость коррозии (1.31 м/год) по сравнению со свеженапыленным покрытием. Значение Rs почти то же, потому что раствор остается одинаковым для всех покрытий. Все покрытия демонстрируют неидеальное емкостное поведение из-за неоднородной морфологии поверхностей покрытий, из-за чего значение n лежит между 0 и 1 (0 < n <1). Уменьшение величины Yc указывает на хороший неидеальный емкостный слой на границе покрытия и электролита. Модель ЭЭЦ герметизированного покрытия несколько отличается от модели ЭЭЦ свеженапыленного покрытия. Это показано на рис. 7б. Дополнительный компонент – Yd обусловлен диэлектрическим характером герметика, заполняющего поры напыляемого покрытия, что делает механизм его коррозии отличным от других покрытий.
Рис. 7.
Модели эквивалентной электрической цепи: (а) свеженапыленного покрытия и (б) герметизированного покрытия.

Таблица 3.
Параметры импеданса свеженапыленных и герметизированных покрытий, полученных с помощью подгонки (модель ЭЭЦ)
Образец покрытия | Rs Ом cм2 |
Rp кОм cм2 |
Yc (См сn/cм2) |
nc | Yd (См сn/cм2) |
nd |
---|---|---|---|---|---|---|
Свеженапыленный | 5.375 | 0.326 | 9.831 × 10–3 | 0.595 | – | – |
Герметизированный | 8.137 | 162.649 | 6.843 × 10–6 | 0.398 | 3.764 × 10–3 | 0.634 |
ВЫВОДЫ
Плазменно напыленное WC–Co-покрытие было герметизировано золь-гель методом для повышения его коррозионной стойкости. После герметизации пористость была значительно снижена, с 3.51 до 0.75%. Электрохимические испытания показали, что коррозионно-барьерные свойства герметизированного покрытия улучшились за счет уменьшения его пористости. Герметизированное покрытие показало более низкий ток коррозии, более высокий потенциал коррозии и улучшенную поляризационную стойкость по сравнению со свеженапыленным покрытием, что подтверждает превосходную коррозионную стойкость герметизированного покрытия.
Список литературы
Liu X., Song X., Wang H., Liu X., Tang F., Lu H. Complexions in WC–Co cemented carbides// Acta Mater. 2018. V. 149. P. 164–178.
Tillmann W., Hagen L., Stangier D., Paulus M., Tolan M., Sakrowski R., Biermann D., Freiburg D. Microstructural characteristics of high-feed milled HVOF sprayed WC–Co coatings// Surf. Coatings Technol. 2019. V. 374. P. 448–459.
Myalska H., Lusvarghi L., Bolelli G., Sassatelli P., Moskal G. Tribological behavior of WC-Co HVAF-sprayed composite coatings modified by nano-sized TiC addition// Surf. Coatings Technol. 2019. V. 371. P. 401–416.
Pawlowski L. The Science and Engineering of Thermal Spray Coatings: Second Edition, 2008.
Ivannikov A.Y., Kalita V.I., Komlev D.I., Radyuk A.A., Bagmutov V.P., Zakharov I.N., Parshev S.N. The effect of electromechanical treatment on structure and properties of plasma sprayed Ni–20Cr coating // J. Alloys Compd. 2016. V. 655. P. 11–20.
Zhang L.M., Zhang S.D., Ma A.L., Hu H.X., Zheng Y.G., Yang B.J., Wang J.Q. Influence of sealing treatment on the corrosion behavior of HVAF sprayed Al-based amorphous/nanocrystalline coating// Surf. Coatings Technol. 2018. V. 353. P. 263–273.
Deen K.M., Afzal M., Liu Y., Farooq A., Ahmad A., Asselin E. Improved corrosion resistance of air plasma sprayed WC–12% Co cermet coating by laser re-melting process // Mater. Lett. 2017. V. 191. P. 34–37.
Zheng Z.B., Zheng Y.G., Sun W.H., Wang J.Q. Effect of heat treatment on the structure, cavitation erosion and erosion–corrosion behavior of Fe-based amorphous coatings // Tribol. Int. 2015. V. 90. P. 393–403.
Ciubotariu C.-R., Frunzăverde D., Mărginean G., Șerban V.-A., Bîrdeanu A.-V. Optimization of the laser remelting process for HVOF-sprayed Stellite 6 wear resistant coatings // Opt. Laser Technol. 2016. V. 77. P. 98–103.
Batista C., Portinha A., Ribeiro R.M., Teixeira V., Costa M.F., Oliveira C.R. Morphological and microstructural characterization of laser-glazed plasma-sprayed thermal barrier coatings // Surf. Coatings Technol. 2006. V. 200. P. 2929–2937.
Wang Q., Ramachandran C.S., Smith G.M., Sampath S. Sliding wear behavior of air plasma sprayed Al2O3 coatings sealed with aluminum phosphate // Tribol. Int. 2017. V. 116. P. 431–439.
Smith G.M., Resnick M., Flynn K., Dwivedi G., Sampath S. Nature inspired, multi-functional, damage tolerant thermal spray coatings// Surf. Coatings Technol. 2016. V. 297. P. 43–50.
Wang Y., Jiang S.L., Zheng Y.G., Ke W., Sun W.H., Wang J.Q. Effect of porosity sealing treatments on the corrosion resistance of high-velocity oxy-fuel (HVOF)-sprayed Fe-based amorphous metallic coatings // Surf. Coatings Technol. 2011. V. 206. P. 1307–1318.
Shao F., Yang K., Zhao H., Liu C., Wang L., Tao S. Effects of inorganic sealant and brief heat treatments on corrosion behavior of plasma sprayed Cr2O3–Al2O3 composite ceramic coatings // Surf. Coatings Technol. 2015. V. 276. P. 8–15.
Zhang Y., Hong S., Lin J., Zheng Y. Influence of ultrasonic excitation sealing on the corrosion resistance of HVOF-sprayed nanostructured WC–CoCr coatings under different corrosive environments // Coatings. 2019. V. 9. P. 724–732.
Amousoltani N., Salimijazi H., Golozar M. Study of alumina sealing of HVOF thermally sprayed WC–Co coatings by sol-gel method // Mater. Res. Express 2019. V. 7. P. 016410–016421.
Troczynski T., Yang Q., John G. Post-deposition treatment of zirconia thermal barrier coatings using sol-gel alumina // J. Therm. Spray Technol. 1999. V. 8. P. 229–234.
Armada S., Tilset B.G., Pilz M., Liltvedt R., Bratland H., Espallargas N. Sealing HVOF thermally sprayed WC–CoCr coatings by sol-gel methods // J. Therm. Spray Technol. 2011. V. 20. P. 918–926.
ASTM C20-00, Standard Test Methods for Apparent Porosity, Water Absorption, Apparent Specific Gravity, and Bulk Density of Burned Refractory Brick and Shapes by Boiling Water, Am. Soc. Test. Mater. 00, 1–3 2015.
Jafari M., Enayati M.H., Salehi M., Nahvi S.M., Park C.G. Comparison between oxidation kinetics of HVOF sprayed WC–12Co and WC–10Co–4Cr coatings // Int. J. Refract. Met. Hard Mater. 2013. V. 41. P. 78–84.
Sadeghimeresht E., Markocsan N., Nylén P. A comparative study of corrosion resistance for HVAF-sprayed Fe- and Co-based coatings // Coatings. 2016. V. 6. P. 26–28.
Zhou S., Dai X., Zheng H. Microstructure and wear resistance of Fe-based WC coating by multi-track overlapping laser induction hybrid rapid cladding // Opt. Laser Technol. 2012. V. 44. P. 190–197.
Kathikeyan J., Berndt C.C., Ristorucci A., Herman H. Ceramic impregnation of plasma sprayed thermal barrier coatings / in Therm. Spray: Pract. Solut. Eng. Probl. by ed. C.C. Berndt. ASM International, 1996. P. 477–482.
Pourbaix M. Atlas of Electrochemical Equilibria in Aqueous Solution. NACE, 1974. 644 p.
Chen J., Song Y., Shan D., Han E.-H. Modifications of the hydrotalcite film on AZ31 Mg alloy by phytic acid: The effects on morphology, composition and corrosion resistance // Corros. Sci. 2013. V. 74. P. 130–138.
Aw P.K., Tan A.L.K., Tan T.P., Qiu J. Corrosion resistance of tungsten carbide based cermet coatings deposited by High Velocity Oxy-Fuel spray process // Thin Solid Films. 2008. V. 516. P. 5710–5715.
Ding J.-H., Zhao H.-R., Zheng Y., Zhao X., Yu H.-B. A long-term anticorrsive coating through graphene passivation // Carbon. 2018. V. 138. P. 197–206.
Xu Z., Eduok U., Szpunar J. Effect of annealing temperature on the corrosion resistance of MgO coatings on Mg alloy // Surf. Coatings Technol. 2019. V. 357. P. 691–697.
Ammar S., Ramesh K., Ma I.A.W., Farah Z., Vengadaesvaran B., Ramesh S., Arof A.K. Studies on SiO2-hybrid polymeric nanocomposite coatings with superior corrosion protection and hydrophobicity // Surf. Coatings Technol. 2017. V. 324. P. 536–545.
Дополнительные материалы отсутствуют.
Инструменты
Физика металлов и металловедение