Физика металлов и металловедение, 2021, T. 122, № 11, стр. 1179-1186
Влияние железа и кремния на фазовый состав и микроструктуру деформируемого сплава Al–2% Cu–2% Mn (мас. %)
Н. А. Белов a, *, С. О. Черкасов a, Н. О. Короткова a, А. О. Яковлева a, К. А. Цыденов a
a НИТУ “МИСиС”
119049 Москва, Ленинский проспект, 4, Россия
* E-mail: nikolay-belov@yandex.ru
Поступила в редакцию 07.04.2021
После доработки 17.05.2021
Принята к публикации 05.07.2021
Аннотация
С использованием экспериментальных и расчетных методов изучено влияние Fe и Si, как вероятных примесей, на фазовый состав и микроструктуру деформируемого сплава Al–2% Cu–2% Mn (мас. %). Установлено, что при совместном введении этих элементов в количестве до 0.4% они в основном связываются в эвтектические включения фазы Al15(Fe,Mn)2Si5, которые не оказывают отрицательного влияния на технологичность при холодной прокатке. При этом значения твердости и удельной электропроводности отожженных холоднокатаных листов практически не снижаются по сравнению с соответствующими значениями базового сплава, приготовленного на основе высокочистого алюминия.
ВВЕДЕНИЕ
Среди стандартных деформируемых сплавов наиболее высокой термостойкостью обладают алюминиевые сплавы 2xxx серии, легированные медью, например, АА2219 (1201) [1–3]. Рабочие температуры таких сплавов составляют около 250°С, причем значительно повысить этот уровень в рамках традиционного легирования вряд ли возможно [4–6]. Существенным недостатком сплавов 2ххх серии является необходимость проведения операций гомогенизации для слитков и закалки для деформированных полуфабрикатов [7–11].
В работах [10, 12] на примере модельного сплава Al–2% Cu–2% Mn (мас. %) было показано, что он обладает преимуществами по сравнению с марочными сплавами типа АА2219, как по технологичности, так и по термической стабильности. В частности, после отжига при 400°С модельный сплав в виде холоднокатаных листов обладает существенно более высокими прочностными характеристиками: по временному сопротивлению – более, чем на 20%, по пределу текучести – более, чем в 2 раза. Сделан вывод о его перспективности в качестве основы для разработки высокотехнологичных термостойких алюминиевых сплавов как альтернативы существующим сплавам 2ххх серии.
Поскольку данный модельный сплав был приготовлен на основе алюминия высокой чистоты, то остается открытым вопрос о влиянии примесей Fe и Si, которые неизбежно присутствуют в подавляющем большинстве промышленных сплавов. В частности, наличие даже небольших количеств Fe и Si существенно усложняет фазовый состав сплавов на основе системы Al–Cu–Mn [10]. Если в базовой тройной системе кроме алюминиевого твердого раствора (далее (Al)) возможно образование только трех фаз (Al6Mn, Al20Cu2Mn3 и Al2Cu), то в присутствии Fe и Si к ним добавляется еще 7: Al3Fe, (Al,Cu)6(Fe,Mn,Cu), Al7Cu2Fe, Al15(Fe,Mn)2Si3, Al5FeSi, Al8Fe2Si и (Si). Особо следует отметить то, что железо, обладая очень низкой растворимостью в (Al) [13], практически полностью находится в тех или иных фазах кристаллизационного происхождения. Известно, что влияние Fe-содержащих фаз на механические свойства в значительной мере определяется их морфологией. Наиболее вредными являются иглообразные частицы (например, фазы Al7Cu2Fe и Al5FeSi) [13]. Фаза Al15(Fe,Mn)2Si3, эвтектические включения которой имеют компактную скелетообразную морфологию, представляется наиболее предпочтительной. Однако ее образование приводит к неизбежному снижению концентрации Mn в (Al), что соответственно уменьшает количество дисперсоидов Al20Cu3Mn2, от которых зависят механические свойства сплавов предложенного типа [14, 15]. Из этого вытекает необходимость оценки такой потери марганца и ее влияния на прочностные свойства.
Именно на решение данной задачи и была направлена настоящая работа, сфокусированная, прежде всего, на анализе влияния железа и кремния на фазовый состав деформируемого модельного сплава Al–2% Cu–2% Mn на различных стадиях технологического процесса.
АНАЛИЗ ФАЗОВОГО СОСТАВА СИСТЕМЫ Al–Cu–Mn–Fe–Si
Раздельное влияние железа и кремния на фазовый состав сплавов системы Al–Mn–Cu вытекает из строения соответствующих четверных диаграмм состояния. Согласно имеющимся данным [3, 11, 13] добавление железа к сплавам, легированным медью и марганцем, имеющм фазовый состав (Al) + Al2Cu + Al20Cu2Mn3, приводит к появлению фазы Al7Cu2Fe. Однако при значительной концентрации этого элемента возможно образование фазы (Al,Cu)6(Fe,Cu,Mn). Хотя данная фаза и не находится в равновесии с Al2Cu, она может присутствовать в структуре из-за неполного протекания перитектических реакций. В алюминиевом углу системы Al–Cu–Mn–Si новых фаз по сравнению с тройными системами (Al–Si–Cu и Al–Si–Mn) не образуется [3, 11, 13]. Добавление небольших количеств кремния к сплавам системы Al–Cu–Mn должно приводить к образованию только фазы Al15Mn3Si2. В условиях неравновесной кристаллизации возможно появление и свободного кремния по эвтектической реакции L → → (Al) + Al2Cu + (Si) + Al15Mn3Si2 [16].
Строение системы Al–Cu–Mn–Fe–Si было предложено в работе [16] на основе анализа соответствующих четверных диаграмм. Из него следует, что совместное наличие примесей Fe и Si в сплавах системы Al–Mn–Cu должно привести в равновесных условиях только к образованию фазы Al15(Fe,Mn)2Si3. Появление фаз Al7Cu2Fe и (Si) возможно при явном избытке одной и этих примесей.
Для количественного анализа влияния Fe и Si на фазовый состав базового сплава Al–2% Mn–2% Cu проводили расчет с помощью программы “Thermo-Calc” (термодинамическая база TTAL5), что отражено на рис. 1, 2 и в табл. 1. Как видно из политермического разреза, рассчитанного при 2% Cu и 2% Mn (рис. 1а), в отсутствие железа добавление кремния в базовый сплав в количестве до 1% включительно приводит к образованию только одной фазы Al15Mn2Si3. При этом кремний незначительно снижает ликвидус и достаточно сильно солидус. При увеличении концентрации кремния в сплаве количество фазы Al20Cu2Mn3, определяющей свойства базового сплава [12], должно уменьшаться. Как видно из табл. 1 (см. сплавы 1 и 3), при 0.5% Si ее объемная доля по расчету более, чем в 2 раза меньше по сравнению с долей фазы Al15Mn2Si3. Дисперсоиды фазы Al15Mn2Si3 играют существенную роль в структуре некоторых сплавов 3ххх и 2ххх серий [17–21]. Следует учесть, что табл. 1 отражает равновесный фазовый состав, установление которого требует длительной выдержки. Кроме того, данный расчет не позволяет определить происхождение фазы (кристаллизационное или вторичное).
Рис. 1.
Фрагменты политермических разрезов систем Al–Cu–Mn–Si (а) и Al–Cu–Mn–Fe–Si (б) при 2% Cu и 2% Mn: (б) при 0.5% Si, где Al20–Al20Cu2Mn3; Al6 – (Al,Cu)6(Fe,Cu,Mn); Al2–Al2Cu; Al15–Al15(Fe,Mn)2Si3.
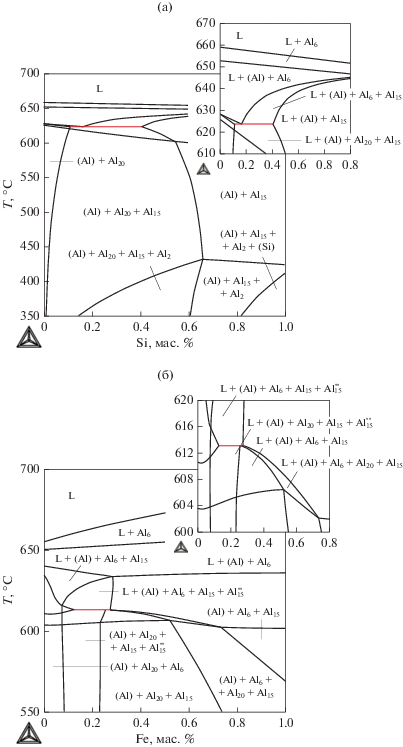
Рис. 2.
Расчетные зависимости массовой доли твердых фаз (Q) от температуры (T) по модели неравновесной кристаллизации (Sheil–Gulliver) для сплавов Al–2% Cu–2% Mn–0.5% Fe (а) и Al–2% Cu–2% Mn–0.5% Fe–0.5% Si (б).
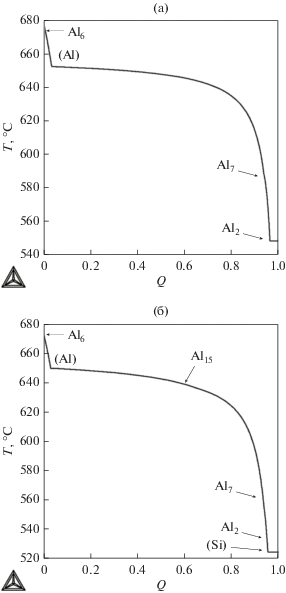
Таблица 1.
Расчетные данные фазового состава сплавов системы Al–Cu–Mn–Fe–Si, содержащих 2% Cu и 2% Mn, при 400°С
№ п/п | Концентрация в сплаве, мас. % | Доля фаз, об. % | Концентрация в (Al), мас. % | |||||||||
---|---|---|---|---|---|---|---|---|---|---|---|---|
Fe | Si | Al6 | Al20 | Al15 | Al2 | Al7 | (Al) | Cu | Mn | Si | Fe | |
1 | – | – | 9.71 | – | – | 90.29 | 0.57 | 0.08 | – | – | ||
2 | 0.50 | – | 4.35 | 6.37 | – | – | 0.70 | 88.56 | 0.84 | 0.07 | – | <0.01 |
3 | – | 0.50 | – | 2.23 | 5.33 | 0.41 | – | 92.03 | 1.47 | 0.05 | 0.05 | – |
4 | 0.50 | 0.50 | – | 3.74 | 5.92 | 0.63 | – | 90.27 | 1.47 | 0.05 | 0.03 | <0.01 |
При добавлении железа к сплаву Al–2% Mn–2% Cu–0.5% Si (т.е. в пятикомпонентных сплавах) фазовый состав существенно усложняется, что отражает политермический разрез, показанный на рис. 1б.
Железо в отличие от кремния повышает температуру ликвидуса, но мало влияет на солидус.
При концентрации железа до 0.5% включительно данный элемент должен быть полностью
связан в фазу Al15(FeMn)3Si2, которая согласно расчету может присутствовать в виде двух составов (на разрезе Al15 и ).
Для анализа влияния Fe и Si на формирование литой структуры базового сплава использовали модель Шейля–Гулливера (Sheil–Gulliver). О влиянии 0.5% Fe можно судить по рис. 2а, согласно которому кристаллизация начинается с образования фазы (Al,Cu)6(Fe,Cu,Mn), а заканчивается при 547°С по эвтектической реакции, в которой основными фазами являются (Al) и Al2Cu. При добавлении 0.5% Si к четверному сплаву кристаллизация заканчивается при 525°С (рис. 2б), что отвечает эвтектической реакции L → (Al) + + Al2Cu + (Si) + Al5FeSi + Al15(FeMn)3Si2 [8, 11]. Данная реакция является неравновесной, поскольку для ее протекания в равновесных условиях концентрация кремния должна быть существенно выше (по расчету ~1.5%).
МЕТОДИКА ЭКСПЕРИМЕНТА
Объектами исследования были слитки и холоднокатаные листы 4 сплавов системы Al–Cu–Mn, содержащих по ~2 мас. % Mn и Cu и различное количество Fe и Si. Все сплавы готовили на основе первичного алюминия марки А85 (ГОСТ 11069–2001). Медь марки М1 (ГОСТ 859–2001) вводили в чистом виде, марганец и железо в виде двойных лигатур (Al–10% Mn и Al–10% Fe по ГОСТ 53777–2010), а кремний в виде силумина АК12пч (ГОСТ 1583–83). Плавку проводили в электрической печи сопротивления (GRAFICARBO) в графитном тигле при 740–760°С. Плоские слитки с размерами 10 × 40 × 180 мм получали литьем в графитовую изложницу (скорость охлаждения составляла около 20 К/с). Фактический химический состав экспериментальных сплавов приведен в табл. 2.
Таблица 2.
Химический состав экспериментальных сплавов
Обозначение сплава | Концентрация, мас. % | ||||
---|---|---|---|---|---|
Cu | Mn | Fe | Si | Al | |
0.3Fe | 1.94 | 1.85 | 0.33 | <0.01 | Основа |
0.1Fe0.5Si | 2.02 | 1.97 | 0.11 | 0.47 | |
0.4Fe0.4Si | 1.91 | 1.90 | 0.41 | 0.42 | |
0.7Fe0.4Si | 1.92 | 1.68 | 0.68 | 0.41 |
Нижние половины слитков отрезали и подвергали холодной прокатке на вальцах ВЭМ 3М до толщины 2 мм (степень обжатия ε = 80%), что позволяло оценить деформационную технологичность литых сплавов.
Отжиг слитков и листов проводили по многоступенчатым режимам в муфельной электропечи SNOL 8,2/1100 в интервале температур от 300 до 600°С (с шагом 50°С) с 3-часовой выдержкой на каждой ступени и последующим охлаждением на воздухе.
После каждого режима отжига на слитках и листах измеряли удельную электрическую проводимость (УЭП) и твердость (НV). Таким образом, все измерения для каждого сплава (как для слитка, так и для листа) проводили на одном образце. Значения УЭП определяли методом вихревых токов на приборе ВЭ-26НП, используя в качестве эталона чистый алюминий (А99). Твердость по Виккерсу определяли на твердомере DUROLINE MH-6 при нагрузке 1 кГс. Микроструктуру слитков и листов изучали на световом (СМ) и электронном сканирующем (СЭМ) микроскопах: соответственно Axio Observer MAT и TESCAN VEGA 3, укомплектованном энергодисперсионной приставкой-микроанализатором OXFORD (МРСА). Для приготовления шлифов использовали как механическую, так и электролитическую полировку.
ЭКСПЕРИМЕНТАЛЬНЫЕ РЕЗУЛЬТАТЫ И ИХ ОБСУЖДЕНИЕ
Микроструктуры экспериментальных сплавов в литом состоянии приведены на рис. 3. Их общей особенностью является наличие эвтектических колоний, обогащенных фазой Al2Cu. Они имеют преимущественно компактную форму, а их размер не превышает 5 мкм. В сплаве 0.3Fe выявляются прожилки фазы (Al,Cu)6(Fe,Cu,Mn) (рис. 3а), а в сплаве 0.1Fe0.5Si – скелетообразные частицы фазы Al15(FeMn)3Si2 (рис. 3б) [21]. Идентификация этих фаз подтверждается результатами МРСА, а их морфология и расположение свидетельствуют об эвтектическом происхождении. Согласно приведенному в [11, 13, 16] анализу фазовых диаграмм Al–Cu–Mn–Fe и Al–Cu–Mn–Fe–Si и с учетом неравновесной кристаллизации (рис. 2) можно предположить последовательность образования фаз. В сплаве 0.3Fe после первичной кристаллизации (Al) формируется двойная эвтектика по реакции L → (Al) + (Al,Cu)6(Fe,Cu,Mn), а затем тройная по реакции L → (Al) + Al2Cu + + (Al,Cu)6(Fe,Cu,Mn). Поскольку иглообразные частицы фазы Al7Cu2Fe не выявляются, то можно считать, что перитектическая реакция L + + (AlCu)6(CuFeMn) → (Al) + Al7Cu2Fe + Al20Cu2Mn3 [16] не протекает из-за слишком быстрого охлаждения.
Рис. 3.
Микроструктуры сплавов 0.3Fe (а), 0.1Fe0.5Si (б), 0.4Fe0.4Si (в) и 0.7Fe0.4Si (г) в литом состоянии, СЭМ.
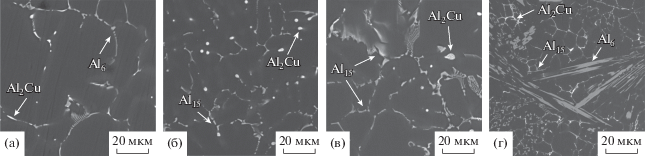
Наличие скелетообразных частиц фазы Al15(FeMn)3Si2 (т.е. двойной эвтектики) и отдельных включений кремниевой фазы в многофазных конгломератах в литой структуре сплава 0.1Fe0.5Si (рис. 3б) согласуется со строением политермической диаграммы пятерной системы [16]. Увеличение концентрации железа до 0.4% (сплав 0.4Fe0.4Si) мало меняет структуру, отмечается лишь увеличение количества Fe- и Si-содержащих частиц (рис. 3в) Следует отметить отсутствие в этом сплаве первичных кристаллов фазы (Al,Cu)6(Fe,Cu,Mn), образование которых вытекает из рис. 1б. Это можно объяснить влиянием скорости охлаждения. С другой стороны, в сплаве 0.7Fe0.4Si концентрация железа уже достаточно высока, чтобы первичные кристаллы этой фазы образовались и в малоразмерных слитках. Некоторые кристаллы имеют иглообразную морфологию длиной до 100 мкм (рис. 3г). Очевидно, что такая структура, в отличие от остальных экспериментальных сплавов, является заведомо неблагоприятной для деформационной обработки, что подтвердилось экспериментально. При попытке прокатать слиток данного сплава произошло его разрушение при обжатии менее 30%.
Для оценки влияния скорости охлаждения на формирование литой структуры был проведен металлографический анализ медленно закристаллизованных сплавов. Как видно из рис. 4, снижение скорости охлаждения привело к ожидаемому огрублению микроструктуры, а именно увеличению размеров дендритной ячейки (Al) и расположенных по их границам избыточных фаз. Это свидетельствует об эвтектическом происхождении последних. В сплавах 0.3Fe и 0.4Fe0.4Si было также выявлено небольшое количество первичных кристаллов фазы (Al,Cu)6(Fe,Cu,Mn).
Рис. 4.
Микроструктуры сплавов 0.3Fe (а) 0.1Fe0.5Si (б) и 0.4Fe0.4Si (в), после переплава и охлаждения в печи, СЭМ.
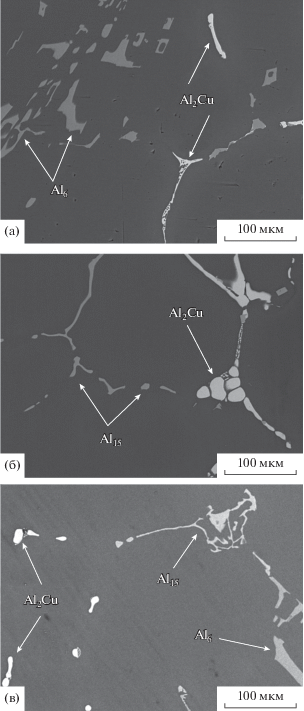
Как было показано в предыдущих работах по сплавам системы Al–Cu–Mn [8–10], состав (Al), сформировавшийся при литье, в значительной мере, определяет количество дисперсоидов, образующихся при отжиге [22, 23]. Поэтому для всех экспериментальных сплавов был проведен соответствующий анализ методом МРСА. Как видно из табл. 3, концентрация марганца в (Al) во всех сплавах кроме 0.7Fe0.4Si составляет не менее ~1.5% (т.е. не менее 75% от его общего количества в сплаве). Концентрация меди составляет 0.6–0.8%, т.е. примерно такая же, как и в сплаве без Fe и Si [10]. В сплаве 0.1Fe0.5Si алюминиевый твердый раствор содержит также 0.15% Si, что предполагает формирование при отжиге дисперсоидов Al15Mn2Si3 в достаточно большом количестве [16].
Таблица 3.
Состав алюминиевого твердого раствора экспериментальных сплавов в литом состоянии
Обозначение сплава | Концентрация, мас. % | ||||
---|---|---|---|---|---|
Cu | Mn | Si | Fe | Al | |
0.3Fe | 0.79 | 1.69 | <0.01 | <0.01 | Основа |
0.1Fe0.5Si | 0.77 | 1.74 | 0.15 | <0.01 | |
0.4Fe0.4Si | 0.57 | 1.46 | 0.02 | <0.01 | |
0.7Fe0.4Si | 0.70 | 1.05 | 0.06 | <0.01 |
Компактная морфология и относительно равномерное распределение эвтектических фаз в слитках сплавов, содержащих до 0.4% Fe (рис. 3а–3в), позволили обеспечить достаточную деформационную технологичность при холодной прокатке. Из них были получены 2-мм листы без видимых дефектов. Более того, деформационная обработка привела к улучшению структуры, поскольку произошла фрагментация эвтектических частиц, а их распределение стало еще более равномерным. В первую очередь это относится к сплавам 0.1Fe0.5Si (рис. 5а) и 0.3Fe (рис. 5б), в которых средний размер частиц не превышает 2 мкм. Несколько хуже выглядит структура сплава 0.4Fe0.4Si, поскольку в нем в процессе прокатки сформировались строчки по границам дендритных ячеек (Al), вытянутых в направлении прокатки (рис. 5в). Это можно объяснить повышенным количеством интерметаллидов в исходной литой структуре (рис. 3в).
Рис. 5.
Микроструктуры холоднокатаных листов сплавов 0.1Fe0.5Si (а), 0.3Fe (б) и 0.4Fe0.4Si (в, г) в исходном состоянии (а–в) и после отжига при 450°С (г), СЭМ.
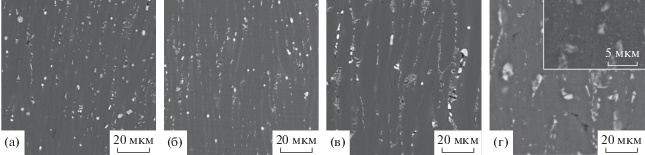
Как было показано в работе [12], при отжиге холоднокатаного листа тройного сплава с 2% Mn и 2% Cu, протекают несколько процессов: растворение эвтектических включений Al2Cu в (Al), формирование дисперсоидов при распаде последнего, а также рекристаллизация при температурах выше 400°С. Те же процессы были выявлены и в экспериментальных сплавах, содержащих железо и кремний. В качестве примера на рис. 5г приведена типичная структура после отжига при 450°С. Она показывает, что частицы Al2Cu полностью отсутствуют, в то время как Fe-содержащие частицы сохраняются практически такими же, как и в исходном состоянии (рис. 5а–5в).
В отожженных листах также выявляются Mn-дисперсоиды размером около 200 нм, а зеренная структура полностью рекристаллизованная.
Анализ зависимостей твердости и электропроводности холоднокатаных листов от температуры отжига позволяет оценить структурные изменения, протекающие при более низких температурах. Из рис. 6а видно, что при температуре отжига до 400°С наблюдается слабое разупрочнение всех трех сплавов.
Рис. 6.
Влияние температуры последней ступени отжига на твердость (а) и удельную электропроводность (б) холоднокатаных листов экспериментальных сплавов.
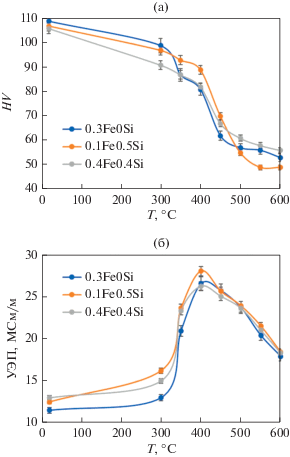
Как было показано в работе [13], в которой рассматривался модельный сплав, содержащий по 2% Cu и 2% Mn, при таких температурах размер дисперсоидов Al20Cu2Mn3 не превышает 100 нм, что делает их эффективными антирекристаллизаторами. При этом значения УЭП достигают максимума при 400°С (рис. 6б). Это можно объяснить снижением концентраций Cu и Mn в (Al) до минимальных значений, близких к равновесным, как это было показано в [24] При более высоких температурах отжига происходит одновременное снижение, как твердости (рис. 6а), так и УЭП (рис. 6б). Это объясняется укрупнением Mn-содержащих дисперсоидов и увеличением концентраций Cu и Mn в (Al) [25, 26]. В целом зависимости, приведенные на рис. 6, очень близки зависимостям, полученным на модельном сплаве, приготовленном на основе высокочистого алюминия [12]. Весьма близки к свойствам базового сплава и абсолютные значения HV и УЭП. В частности, после отжига при 400°С они составляют 82–89 НV и 27–28 МСм/м соответственно. Из этого следует, что при содержании примесей железа и кремния до 0.4% включительно (это отвечает типичным концентрациям в промышленных сплавах), можно достигать такого же комплекса механических свойств, которой был достигнут на модельном сплаве [12]. Это позволяет рассчитывать на возможность использования дешевых шихтовых материалов для приготовления сплавов предложенного типа.
ВЫВОДЫ
1. Расчетным методом проанализировано раздельное и совместное влияние железа и кремния на фазовый состав сплава Al–2% Mn–2% Cu (мас. %). Показано, что при совместном введении этих элементов они в основном связываются в фазу Al15(Fe,Mn)2Si3, эвтектического происхождения. Также возможно появления первичных кристаллов фазы (Al,Cu)6(Fe,Mn,Cu).
2. Показано, что при получении слитков co скоростью охлаждения ~20 K/с формирование первичных кристаллов (Al,Cu)6(Fe,Mn,Cu) подавляется, если концентрация железа не превышает 0.4%. Это позволяет получать в литых сплавах структуру, которая обеспечивает их способность к холодной прокатке со степенью обжатия до 80%. Это обусловлено относительно компактной морфологией эвтектических включений фаз Al15(Fe,Mn)2Si3 и Al6(Fe,Mn,Cu), которые способны к фрагментации на субмикронные частицы в процессе холодной прокатки.
3. Установлено, что значения твердости и удельной электропроводности отожженных холоднокатаных листов сплавов-экспериментального состава при наличии до 0.4% Fe и Si практически не снижаются по сравнению со свойствами базового сплава, приготовленного на основе высокочистого алюминия. Это позволяет рассчитывать на возможность использования дешевых шихтовых материалов для приготовления сплавов предложенного типа.
Работа выполнена при поддержке гранта РНФ № 20-19-00249.
Список литературы
Hatch J.E. (ed.) Aluminum: Properties and Physical Metallurgy. ASM Metals. Park, Ohio, 1984. 424 p.
International alloy designations and chemical composition limits for wrought aluminum and wrought aluminum alloys. The Aluminum Association Publications. Arlington, 2015.
Mondolfo L.F. Aluminium alloys: Structure and properties. 1st ed., Butterworths, London, 1976. 218 p.
Tiryakioglu M., Shuey R.T. Quench sensitivity of 2219-T87 aluminum alloy plate // Mater. Sci. Eng. A. 2010. V. 527. № 18–19. P. 5033–5037. https://doi.org/10.1016/j.msea.2010.04.060
Chen Zh., Pei Ch., Ma C. Microstructures and mechanical properties of Al–Cu–Mn alloy with La and Sm addition // Rare Metals. 2012. № 31. P. 332–335. https://doi.org/10.1007/s12598-012-0515-6
Bakavos D., Prangnell P.B., Bes B., Eberl F. The Effect of silver on microstructural evolution in two 2xxx-series Al alloys with a high Cu: Mg ratio during ageing to a T8 temper // Mater. Sci. Eng. A. 2008. V. 491. P. 214–223. https://doi.org/10.1016/j.msea.2008.03.014
Polmear I., StJohn D., Nie J.F., Qian M., Physical metallurgy of aluminium alloys/ In: Light Alloys, 5th ed. Elseiver, London, 2017. pp. 31–107. https://doi.org/10.1016/B978-0-08-099431-4.00002-6
Belov N.A., Korotkova N.O., Akopyan T.K., Pesin A.M. Phase Composition and Mechanical Properties of Al–1.5% Cu–1.5% Mn–0.35% Zr(Fe,Si) Wire Alloy // J. Alloys Compd. 2019. V. 782. P. 735–746. https://doi.org/10.1016/j.jallcom.2018.12.240
Belov N., Korotkova N., Akopyan T., Tsydenov K. Simultaneous increase of electrical conductivity and hardness of Al–1.5 wt % Mn alloy by addition of 1.5 wt % Cu and 0.5 wt % Zr // Metals. 2019. V. 9. P. 1246. https://doi.org/10.3390/met9121246
Белов Н.А., Короткова Н.О., Шуркин П.К., Аксенов А.А. Обоснование концентрации меди в термостойких деформируемых алюминиевых сплавах, содержащих 2 мас. % Mn // ФММ. 2020. Т. 121. № 12. С. 1315–1323. https://doi.org/10.31857/S0015323020120037
Белов Н.А. Фазовый состав промышленных и перспективных алюминиевых сплавов. М.: Издательский дом МИСиС, 2010. 511 с.
Belov N.A., Akopyan T.K., Shurkin P.K., Korotkova N.O. Comparative analysis of structure evolution and thermal stability of experimental AA2219 and model Al–2 wt % Mn–2 wt % Cu cold rolled alloys // J. Alloys Compd. 2021. V. 864. P. 158823. https://doi.org/10.1016/j.jallcom.2021.158823
Glazoff M., Khvan A. Zolotorevsky V., Belov N., Dinsdale A. Casting aluminum alloys: Their physical and mechanical metallurgy. 2nd ed., Butterworth-Heinemann, London, 2018. 562 p.
Chen Z., Chen P.P., Li S. Effect of Ce addition on microstructure of Al20Cu2Mn3 twin phase in an Al–Cu–Mn casting alloy // Mater. Sci. Eng. A. 2012. V. 532. P. 606–609. https://doi.org/10.1016/j.msea.2011.11.025
Rios P.R., Fonseca G.S. Grain boundary pinning by Al6Mn precipitates in an Al–1 wt % Mn alloy // Scripta Mater. 2004. V. 50. № 1. P. 71–75. https://doi.org/10.1016/j.scriptamat.2003.09.031
Belov N.A., Eskin D.G., Aksenov A.A. Multicomponent phase diagrams: Applications for commercial aluminum alloys. Elsevier, London, 2005. 393 p. https://doi.org/10.1016/B978-0-08-044537-3.X5000-8
Chen S.P., Kuijpers N.C.W., van der Zwaag S. Effect of microsegregation and dislocations on the nucleation kinetics of precipitation in aluminium alloy AA3003 // Mater. Sci. Eng. A. 2003. V. 341. P. 296–306. https://doi.org/10.1016/S0921-5093(02)00245-9
Robson J.D., Hill T., Kamp N. The effect of hot deformation on dispersoid evolution in a model 3xxx alloy // Mater. Sci. Forum. 2014. V. 794–796. P. 697–703. https://doi.org/10.4028/www.scientific.net/MSF.794-796.697
Mondol S., Alam T., Banerjee R., Kumar S. Chattopadhyay K. Development of a high temperature high strength Al alloy by addition of small amounts of Sc and Mg to 2219 alloy // Mater. Sci. Eng. A. 2017. V. 687. P. 221–231. https://doi.org/10.1016/J.MSEA.2017.01.037
Zhen K.K., Fung, Y.Q. Direct observation of the transformation of the icosahedral phase in (Al6Mn)1–xSix, into α(AlMnSi) // Philos. Mag. B. 1986. V. 54. P. 27–31.
Flattum Muggerud A.M., Li Y., Holmestad R. Orientation studies of α-Al(Fe,Mn)Si dispersoids in 3xxx Al alloys // Mater. Sci. Forum. 2014. V. 794–796. P. 39–44. https://doi.org/10.4028/www.scientific.net/MSF.794-796.39
Dar S.M., Liao H., Xu A. Effect of Cu and Mn content on solidification microstructure, T-phase formation and mechanical property of AlCuMn alloys // J. Alloys Compd. 2018. V. 774. P. 758–767. https://doi.org/10.1016/j.jallcom.2018.09.362
Zupanič F., Wang D., Gspan C., Bončina T. Precipitates in a quasicrystal strengthened Al–Mn–Be–Cu alloy // Mater. Charact. 2015. V. 106. P. 93–99. https://doi.org/10.1016/j.matchar.2015.05.013
Zupanič F., Gspan C., Burja J., Bončina T. Quasicrystalline and L12 precipitates in a microalloyed Al–Mn–Cu alloy // Mater. Today Commun. 2020. V. 22. P. 100809. https://doi.org/10.1016/j.mtcomm.2019.100809
Feng Z.Q., Yang Y.Q., Huang B., Li M.H., Chen Y.X., Ru J.G. Crystal substructures of the rotation-twinned T (Al20Cu2Mn3) phase in 2024 aluminum alloy // J. Alloys Compd. 2014. V. 583. P. 445–451. https://doi.org/10.1016/j.jallcom.2013.08.200
Vlach M., Stulikova I., Smola B., Piesova J., Cisarova H., Danis S., Plasek J., Gemma R., Tanprayoon D., Neuber V. Effect of cold rolling on precipitation processes in Al–Mn–Sc–Zr alloy // Mat. Sci. Eng. A. 2012. V. 548. P. 27–32. https://doi.org/10.1016/j.msea.2012.03.06
Дополнительные материалы отсутствуют.
Инструменты
Физика металлов и металловедение