Физика металлов и металловедение, 2021, T. 122, № 11, стр. 1205-1217
Влияние параметров индукционной закалки сплава DIN 42CrMo4 на его микротвердость, коррозионную стойкость и микроструктуру
Мухаммад Самиутдин a, b, c, Ли Цзинлон a, b, *, Мухаммад Музамил d, Мухаммад Али Сиддики c, Суфян Насеем c, Сён Цзиантао b, **
a Ведущая государственная лаборатория обработки направленным затвердеванием,
Северо-Западный политехнический университет
710072 Сиань, Китайская Народная Республика
b Ведущая лаборатория технологий сварки трением в Шаньси, Северо-Западный политехнический университет
710072 Сиань, Китайская Народная Республика
c Кафедра металлургии, Химико-технологический факультет,
Инженерно-технологический университет им. Н.Е. Диншоу
75270 Карачи, Пакистан
d Кафедра машиноведения, Факультет технологии машиностроения,
Инженерно-технологический университет им. Н.Е. Диншоу
75270 Карачи, Пакистан
* E-mail: ijinglg@nwpu.edu.cn
** E-mail: xiongjiangtao@nwpu.edu.cn
Поступила в редакцию 03.05.2021
После доработки 20.05.2021
Принята к публикации 22.06.2021
Аннотация
Исследовательская работа сосредоточена на микроструктурных изменениях, которые происходили в сплаве DIN 42CrMo4 в процессе его индукционной закалки, с акцентом на изменениях коррозионных свойств и микротвердости сплава. Проведены эксперименты с постепенным увеличением мощности, подаваемой на индуктор, и времени обработки исследуемого сплава. Для изучения микроструктуры обработанного сплава использовали оптическую и растровую электронную микроскопию. Механические характеристики индукционно закаленного сплава были объяснены на основе результатов исследования его микротвердости. Установлено, что процентное содержание доли мартенситной фазы увеличивалось с ростом мощности, подаваемой на индуктор: 10, 14, 18 и 22 кВт. Аналогичная тенденция наблюдалась и при увеличении продолжительности индукционного нагрева с 3 до 9 с. Также наблюдалась характерная трансформация морфологии мартенсита при изменении параметров индукционной обработки, что оказало существенное влияние на коррозионные характеристики и величину твердости исследуемого сплава. Твердость сплава прогрессивно возрастала с увеличением мощности и времени индукционного нагрева и стабилизировалась при более высоких входных значениях параметров обработки в результате достижения мартенситной структурой своей равновесной формы. Исследование электрохимических свойств показало, что морфология мартенсита играет определяющую роль в коррозионных характеристиках сплава. Было обнаружено, что структура реечного мартенсита обладала большей коррозионной стойкостью по сравнению с огрубленным мартенситом, при незначительном отличие в величине твердости. Таким образом, для оптимизации свойств необходимо использовать надлежащие параметры индукции.
ВВЕДЕНИЕ
Индукционный нагрев является одним из наиболее востребованных технологических процессов в промышленности, позволяющим избежать огромных затрат природных ресурсов и финансов на дорогостоящие печи, которые используются для многочисленных процессов термообработки. Индукционный нагрев может быть использован для различных целей, в том числе для объемного нагрева, локального нагрева при соединении отдельных частей и нагрева поверхности материала для его упрочнения [1]. Типичными промышленными применениями индукционного нагрева являются нагрев металлов для ковки, непрерывный нагрев пруткового материала и рельсов, а также нагрев материалов из цветных металлов для экструзии [2]. Такие специальные типы сварочного процесса как фальцевое соединение труб и сварка давлением чаще всего сочетаются с индукционным нагревом для “ускорения” процесса. Кроме того, высоколокализованный нагрев на небольшую глубину, поверхностное упрочнение зубьев зубчатых колес, роликов, лопастей, осевых валов редких конфигураций и различных автомобильных деталей являются примерами применения на производстве индукционной закалки (ИЗ).
Многие исследователи изучали механические свойства и микроструктуру индукционно закаленных деталей [3–5]. Но, насколько известно автору, не было опубликовано ни одной работы по коррозионному поведению стали DIN 42CrMo4, подвергнутой ИЗ. Авторы работы [6] провели экспериментальное исследование индукционной закалки стали 55CrMo и осветили эффекты и проблемы аустенитизации при различных температурах. Разница температур между поверхностями при аустенитизации может привести к возникновению в материале неоднородно упрочненного слоя, причем формирование мартенсита требует обеспечения правильных значений таких параметров, как скорость нагрева и время превращения мартенсита из предшествующих фаз. Кроме того, в [7] скорость индукционного нагрева варьировали линейным образом в зависимости от температуры аустенитизации. ИЗ стали GCr15 оказала значительное влияние на ее трибологическое поведение [8]. Основной причиной такой реакции материала явилось образование упомянутого развитого слоя при индукционном нагреве, что привело к высокой объемной доле мартенсита и следам остаточного аустенита в соответствующей микроструктуре. Сравнительное экспериментальное исследование среднеуглеродистой (AISI 1045) и низколегированной (AISI 5140) сталей было проведено с использованием процесса ИЗ. Микроструктуры указывали на впечатляющее различие между этими двумя сталями: среднеуглеродистая сталь содержала смесь мартенсита и перлита в упрочненном слое, в то время как низколегированная сталь демонстрировала только мартенсит [9]. Также была предпринята попытка на примере стали SUP9 (AISI 5160) изучить процентное содержание в ней мартенсита после индукционной закалки стали путем отпуска [10]. Результаты показали, что повышение температуры отпуска приводит к снижению процентного содержания мартенсита. Однако эта тенденция выгодна с точки зрения трибологических свойств материала. Также сообщалось о наличии небольших объемных долей феррита в микроструктурах после отпуска [11].
Микроструктурные изменения также оказывают непосредственное влияние на электрохимические свойства исследуемой стали. Многие исследователи изучали коррозионное поведение различных сталей в различных агрессивных средах. Коррозионное поведение высокопрочной низколегированной стали (HSLA) с различной микроструктурой было изучено в 3.5%-ном растворе NaCl [12], и установлено, что микроструктурные изменения сопровождаются значительным улучшением коррозионной стойкости данного сплава. Авторы [12] пришли к выводу, что игольчатый феррит обладает большей коррозионной стойкостью, в то время как мартенсит демонстрирует плохую коррозионную стойкость из-за увеличенной катодной площади карбидов, внедренных в мартенсит. Коррозионные свойства сталей также зависят от количества, природы и распределения фазовых составляющих, присутствующих в микроструктуре [13]. Было установлено, что арматурная сталь, полученная с принудительным воздушным охлаждением, обладает превосходной коррозионной стойкостью по сравнению с арматурной сталью, охлажденной с печью, а также закаленной и отпущенной сталью. Отпущенный мартенсит проявляет высокую скорость коррозии из-за высокой энергии активации, которая усиливается присутствием карбидов. Кроме того, высокая концентрация хлорида значительно повышает скорость коррозии.
При разработке микроструктуры коррозионная стойкость и твердость углеродистой стали могут быть улучшены за счет формирования многофазной структуры [14]. Различные термические обработки были применены для оптимизации двухфазной структуры феррит–перлит и двух вариантов трехфазных структур бейнит–мартенсит–ферритной и бейнит–перлит–ферритной. Результаты показали, что благодаря многофазности твердость и коррозионные характеристики улучшались по мере увеличения объемной доли бейнита при низком содержании мартенсита. Аналогичные исследования [15, 16] на высокоуглеродистой низколегированной стали также проводили при различной температуре аустенитизации с контролируемыми временем выдержки в печи и скоростью закалки. Результаты показали, что твердость увеличивается при использовании более низкой температуры аустенитизации, при этом коррозионная стойкость снижается. С другой стороны, коррозионная стойкость улучшается при более высокой температуре аустенитизации в ущерб твердости стали из-за укрупнения зерна. Был исследован также эффект от ИЗ [16] стали SPCC и установлено, что скорость коррозии значительно увеличивается после закалки и затем снижается после отпуска. Высокопрочную легированную (HSLA) сталь исследовали при различных температурах закалки из межкритического интервала. В результате исследования был сделан вывод, что большая доля мартенсита образуется при более высокой температуре, что приводит к улучшению механических свойств стали. Но в этом случае возрастает скорость коррозии из-за того, что гальваническая пара между ферритом и мартенситом оказывается парой меньшей “эффективности” в сравнении с ферритом и перлитом. Высокое содержание мартенсита в двухфазной стали делает ее восприимчивой к общей коррозии [17]. Результаты электрохимических опытов показали, что при высоком содержании мартенсита сопротивление питтингу (точечной коррозии) резко возрастает из-за индуцирования большого числа центров защитных сжимающих напряжений на поверхности стали. В результате, наилучший компромисс между этими тенденциями был достигнут, когда структура содержала от 40 до 60% объемной доли мартенсита.
Имеется обширная литература по низкоуглеродистым и среднеуглеродистым сталям, но информация по индукционной закалке среднеуглеродистой и низколегированной стали, такой как DIN 42CrMo4, и о ее коррозионных свойствах крайне малочисленна. В данной работе представлены экспериментальные результаты комплексного исследования и анализа влияния мощности и времени индукционного нагрева на преобразование микроструктуры стали при различных параметрах ИЗ. Коррозионное поведение изучаемой стали также исследовали с помощью потенциодинамического поляризационного (ПДП) сканирования в 1-мольном растворе HCl. Для экспериментов были выбраны четыре уровня мощности, подаваемой на индуктор, при трех значениях продолжительности индукционного нагрева. Таким образом, было получено двенадцать комбинаций режимов ИЗ. На цилиндрических образцах диаметром 9 мм для исследований был создан качественный упрочненный слой, и поперечные сечения обработанных образцов были проанализированы с использованием различных методов исследования.
МЕТОДИКА ЭКСПЕРИМЕНТА
Материал и метод
Выбранным материалом для экспериментов являлась сталь марки DIN 42CrMo4 (1.7225); в табл. 1 приведен ее химический состав.
Таблица 1.
Номинальный химический состав стали DIN 42CrMo4 (1.7225)
Содержание химического элемента, мас. % | |||||
---|---|---|---|---|---|
C | Si | Mn | Ni | Cr | Mo |
0.45–0.49 | 0.30–0.40 | 0.50–0.70 | 0.15–0.18 | 1.00–1.30 | 0.16–0.18 |
В этом исследовании были проведены контролируемые по времени температурные циклы индукционного нагрева на образцах малых размеров. Управляемые по времени циклы оказывают непосредственное влияние на фазовые превращения, которые происходят в условиях интенсивного подвода внешней энергии. Из-за плохого управления скоростью охлаждения возникают неоднородности свойств обрабатываемого материала, причем именно за счет образования проэвтектоидных фаз. При сквозном нагреве передача тепла к центру заготовки без перегрева затруднена, и для контроля нагрева образца требуется проведение многочисленных экспериментальных работ. В связи с этим было проведено предварительное исследование для расчета проникновения тока в металл, чтобы смоделировать параметры полного проникновения тепла и получить отклик по толщине образца выбранного сплава. В процессе индукционной закалки проникновение тока в материал зависит от его свойств и параметров индукции, которые были определены с помощью процедур, упомянутых в литературе [2, 18, 19]. При индукционном нагреве проводящий металл помещают в переменное магнитное поле, где индуцируемый в металле электрический ток создает тепло, которое приводит к фазовому превращению.
Образцы стали DIN 42CrMo4 подвергали термической обработке (ТО) в следующем порядке. Сначала все образцы отжигали при температуре 850°C в течение 2 ч в печи электрического сопротивления и медленно охлаждали до комнатной температуры. На втором этапе ТО проводили индукционную закалку с помощью устройства, изображенного на рис. 1.
Рис. 1.
Экспериментальное устройство для ИЗ и микроструктура стали после первого этапа ТО: а – микроструктура; б – вид образца и его размеры; в – блок устройства для ИЗ.
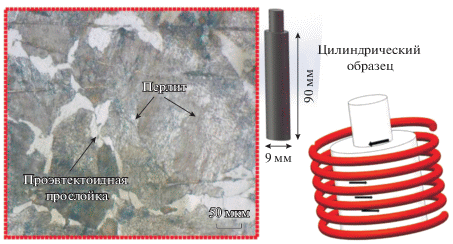
В верхней части устройства расположен автоматически срабатывающий фиксатор, освобождающий цилиндрический образец после завершения цикла. В результате образец оказывается в камере масляной закалки.
Моделирование процесса индукционной закалки
Выбор режимов индукционного теплового цикла часто оказывается на ложном пути при моделировании процесса, который влияет на микроструктуру и дает оптимизированные результаты. Чтобы не упускать из виду, насколько важен процесс ИЗ для желаемого конечного результата, в экспериментах использовали циклы с контролем времени. Управляемые по времени циклы нагрева использовали в сочетании с выбранной мощностью, подаваемой на индуктор. Заготовки загружались в систему и выбрасывались по завершении цикла. Все эксперименты проводили в соответствии с картой режимов ИЗ, представленной на рис. 2.
Микроструктурный анализ
Опытный образец с размерами представлен на рис. 1, на котором также показана микроструктура, предварительно термообработанного образца, демонстрирующая перлит с проэвтектоидной фазой, являющейся одной из составляющих. Двенадцать образцов были получены для исследований, в соответствии с экспериментальной картой, представленной на рис. 2. Для анализа влияния параметров процесса на микроструктуру образцов они были разрезаны на электроискровом станке по своему поперечному сечению на три части. Центральную часть каждого из образцов устанавливали на предметном столике (при температуре 150°C) с помощью фенольной смолы и подвергали полированию алмазной пастой до получения отражающей поверхности. Далее, эти образцы для металлографических исследований травили в свежеприготовленном травителе “Пикраль” (1–2 г пикриновой кислоты и 10 мл этанола) и в Нитале (100 мл этанола 99%, плюс 10 мл азотной кислоты 65%) [20]. Образцы исследовали с помощью металлографического микроскопа (IMM 901, Турция) и растрового электронного микроскопа (Quanta 200S).
Электрохимический тест
Для оценки коррозионной стойкости ИЗ-образцов были использованы количественные данные, полученные с помощью Потенциостата (Camry, США). Испытуемые образцы длиной 10 мм разрезали вдоль по всей длине образца, как показано на рис. 1б, припаивали проволоку для получения электрического соединения и фиксировали одну из поверхностей образца эпоксидной смолой. Шлифовка и полировка были осуществлены с использованием алмазной суспензии (0.5 мкм) для получения поверхности без царапин. Ультразвуковую обработку поверхностей проводили в этаноле для исключения их загрязнения. Все измерения были сделаны на поперечных сечениях (диаметром ∅ ≈ 9 мм) с использованием 1-мольного раствора HCl, относительно потенциала насыщенного хлоридом ртути (HgCl) электрода, выступавшего в качестве электрода сравнения. После стабилизации потенциала открытой цепи до –420 мВ применяли потенциодинамическую поляризацию, в положительном направлении от –0.8 мВ, со скоростью сканирования 1 мВ/с.
РЕЗУЛЬТАТЫ И ОБСУЖДЕНИЕ
Влияние мощности, подводимой к индуктору, и времени ИЗ на микроструктуру
Термообработка позволяет управлять фазовыми превращениями в стали, и точная информация об оценке количества фазы, ее распределении, размере зерна, частицах выделившихся фаз и других характеристиках структуры образцов, прошедших ТО, зависит от нескольких параметров, которые включают скорость нагрева, температуру, время выдержки, скорость охлаждения и среду закалки [21]. В контексте процесса индукционной закалки наиболее важными параметрами являются мощность и продолжительность индукционного нагрева, обеспечивающие формирование полностью мартенситной структуры для получения высокого значения твердости. Если сталь быстро закаливается до температуры окружающей среды от температуры аустенитизации, ее исходная аустенитная фаза полностью превращается в мартенсит путем бездиффузионного превращения при высоких скоростях охлаждения [22].
Перед проведением упрочняющей обработки важно обеспечить трансформацию всех фаз, образовавшихся в производственном процессе изготовления/деформации изделия, т.е. перлита, избыточного феррита и цементита, в аустенитную фазу за счет надлежащей величины индукционного нагрева. Для отожженного образца, если температура материала поддерживается вблизи Ac1, только небольшой процент фазы, потенциально способной к превращению, превращается в аустенит, и при закалке фиксируется пропорциональная доля мартенсита вместе с непревращенными областями [6]. Поэтому в этой работе были выбраны четыре различные мощности индукционного воздействия на материал (10, 14, 18 и 22 кВт) и три различных временных режима (выдержки 3, 6 и 9 с) для изучения их влияния на образование мартенситной фазы. Как ясно из рис. 3а, при мощности 10 кВт и времени воздействия 3 и 6 с никаких заметных изменений с точки зрения мартенситного превращения не наблюдалось, что показало, что эти параметры не подходят для эффективной ИЗ. Было отмечено, что после индукционной обработки конечная микроструктура все еще содержала мягкую перлитную фазу, которая вызывает снижение эксплуатационных характеристик сплава. Из рис. 3а также очевидно, что, несмотря на присутствие непревращенных перлитных колоний, можно было одновременно наблюдать нерастворенные карбиды, что свидетельствовало о том, что при выбранной мощности в 10 кВт не произошло превращения этих фаз в аустенит; поэтому при закалке были зафиксированы перлит и нерастворенные карбиды. Однако при увеличении времени нагрева до 9 с появлялась и мартенситная фаза, как показано на рис. 3в.
Рис. 3.
Микроструктура индукционно упрочненных образцов при различных параметрах обработки. Оптическая металлография.
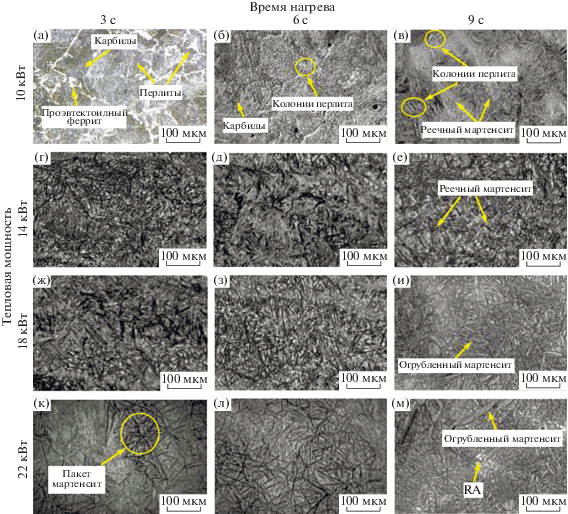
На рис. 3г–3е показана микроструктура стали, которая возникала в результате обработки при мощности в 14 кВт и продолжительности индукционного воздействия 3, 6 и 9 с. В ней выявлено образование иглообразной структуры, которую можно охарактеризовать как реечный мартенсит. Перлитная фаза преобразуется в мартенситную структуру. На рис. 3ж–3и показано, что при использовании мощности 18 кВт области первичной фазы испытывали превращение и замещались мартенситной фракцией, которая постепенно увеличивалась по мере увеличения времени нагрева. При 9 с воздействия была получена полностью мартенситная структура, как видно на рис. 3и, со значительной долей грубого мартенсита, как также видно на рис. 3и. В конце концов при мощности в 22 кВт грубая мартенситная структура стала более заметной с увеличением времени нагрева, как показано на рис. 3к–м, что подтверждает полную трансформацию микроструктуры в мартенситную фазу при этой мощности, феррит и цементит не обнаружены. Однако идентификация доли цементита, оставшегося от предыдущей структуры, затруднена, поскольку карбиды очень малы и замаскированы мартенситом. Микроструктура, которая при некотором увеличении выглядит как мартенсит, при более высоких увеличениях может выявить нерастворенные карбиды. После увеличения времени аустенитизации (т.е., при 9 с) структура после закалки продемонстрировала присутствие блоков мартенсита. Помимо мартенсита на рис. 3к–3м можно увидеть остаточный аустенит в виде белых прослоек межу огрубленными мартенситными блоками, сохранившегося из-за недостаточного времени превращения и наличия легирующих элементов, которые стабилизировали аустенитную фазу (т.е. Ni, C и т.д.).
Количественная металлография также была выполнена на всех образцах для определения доли мартенсита с помощью программного обеспечения для анализа изображений Olympus GX51. Результаты приведены на рис. 4. Результаты подтверждают, что мартенситная структура начала формироваться при индукционной обработке при 10 кВт, и ее доля возрастала с ростом значений параметров ИЗ. При 10 кВт было получено до 6% мартенсита; около 70% объема претерпело превращение при 14 кВт, и до 80–90% мартенсита образовалось при 18 и 22 кВт, соответственно. Кроме того, для мартенситной структуры оказались характерны два варианта морфологии, а именно, наблюдались реечный и огрубленный мартенсит. При мощности 14 кВт нестабильный аустенит трансформировался в структуру реечного мартенсита, а огрубление мартенситной структуры произошло при мощности 18 кВт и времени индукционного нагрева 9 с. Это огрубление еще больше усилилось при мощности 22 кВт, как показано на рис. 3м.
Для тщательного анализа микроструктурных составляющих, были проведены исследования с помощью растровой электронной микроскопии (РЭМ), чтобы получить подробную информацию о характерныех особенностиях микроструктуры. Энерго-дисперсионная рентгеновская спектроскопия (ЭДС) также была проведена для определения природы карбидов, присутствующих в стали. На рис. 5 показаны РЭМ-изображения структуры отдельных образцов, прошедших индукционную обработку; эти снимки указывают на очевидные микроструктурные изменения при критических параметрах обработки. На рис. 5а представлена структура образца, обработанного при мощности в 10 кВт и времени нагрева 6 с. Присутствие карбидов на основе хрома можно установить по изображению на рис. 5а, что подтверждается результатами, полученными с помощью ЭДС-анализа (см. рис. 5б). Перлитные колонии, как не превращенная фаза из-за неправильно выбранной температуры аустенитизации, также были распознаны вместе с реечным мартенситом. По мере увеличения тепловой мощности до 14 кВт наблюдается резкое изменение микроструктуры, сопровождающееся образованием реечного мартенсита, который можно видеть в виде игл, отмеченных на рис. 5в. Аналогичным образом при тепловой мощности 22 кВт, но с увеличением времени нагрева (т.е. при 9 с), наблюдалось заметное огрубление реечного мартенсита, как показано на рис. 5г. Присутствие остаточного аустенита также видно на рис. 5в и 5г, как прослойки. Результаты, полученные с помощью РЭМ, подтверждают предположения, выдвинутые на основании оптической металлографии.
Рис. 5.
РЭМ изображения структуры образцов, прошедших ИЗ при различных параметрах: а, б – 10 кВт, 6 с, в – 14 кВт, г – 22 кВт, 9 с.
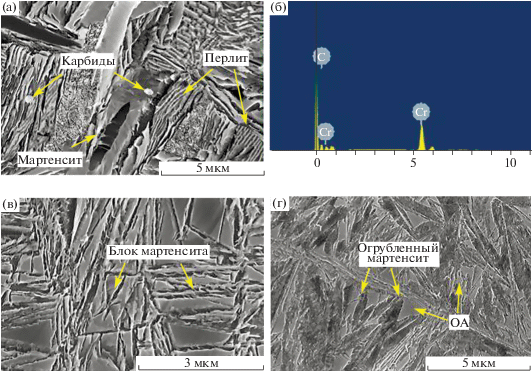
Как сообщалось ранее, в легированной стали этого типа превращение фазы в аустенит зависит от растворения карбидов и от присутствия других легирующих элементов, таких как C, Cr, Ni и Mo, указанных в табл. 1. Таким образом, в выбранной стали полная аустенитизация может быть достигнута при высоких значениях мощности и времени нагрева. При низкой мощности углерод и другие легирующие элементы не могут раствориться и в матрице сохраняются остатки не превращенных фаз (например, перлит, феррит и т.д.). Поэтому для полной аустенитизации требуется более высокая температура за счет соответствующего увеличения количества тепла, которое пропорционально мощности, подводимой к индуктору, и времени обработки. Кроме того, наблюдалось характерное изменение морфологии мартенсита при изменении мощности и времени нагрева, что также показано на рис. 5.
Из приведенного выше обсуждения следует, что по мере увеличения значений параметров индукционной закалки, т.е. тепловой мощности и времени индукционной обработки, количество мартенсита в микроструктуре увеличивается. Исследование показало, что оптимальными параметрами процесса для достижения полностью мартенситной структуры в подвергнутой ИЗ стали являются использование мощности более 14 кВт и времени нагрева от 6 до 9 с.
Взаимосвязь между микротвердостью, мощностью и временем нагрева
Из предыдущих исследований видно, что тепловая мощность оказывает значительное влияние на образование аустенита, который, посредством фазового превращения оказывает влияние на мартенситное превращение. Для достижения однородной структуры вся сталь должна пройти цикл двойной оптимизации значений параметров ИЗ – мощности и продолжительности воздействия. В этом исследовании влияние времени нагрева и тепловой мощности на микротвердость кратко представлено на рис. 6а, 6б. Все измерения микротвердости были сделаны в центральной части поперечных сечений ИЗ-образцов, чтобы сделать заключение о глубине индукционной обработки. Как общий вывод из обоих рисунков, значение твердости увеличивается за счет увеличения тепловой мощности и времени индукционного воздействия. На начальных этапах значение твердости резко возрастало с ростом мощности и времени, однако при более высоких значениях параметров ИЗ была зафиксирована тенденция к стабилизации твердости.
Рис. 6.
Изменение микротвердости (а) в зависимости от мощности, подводимой к индуктору, и (б) от времени нагрева в процессе индукционной закалки.
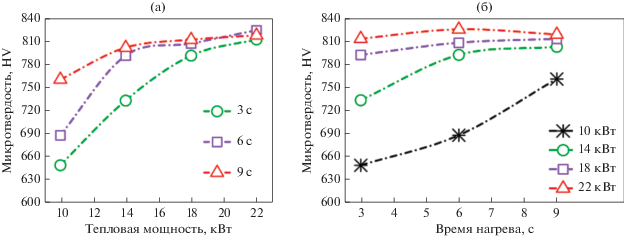
На рис. 6а показано изменение микротвердости при различных значениях тепловой мощности. На рис. 6а хорошо видно значительное смещение трех графиков друг относительно друга при мощности 10 кВт и различном времени ИЗ. По мере увеличения мощности все зависимости сближались и в конечном итоге перекрывались при мощности 22 кВт. Это может быть легко объяснено результатами исследования микроструктуры: при высокой тепловой мощности достигается надлежащая температура аустенитизации, и в образцах образуется однородная аустенитная фаза, которая при охлаждении превращается в мартенсит, повышающий твердость стали.
Аналогичная тенденция также прослеживается на рис. 6б. Самая низкая твердость достигается при тепловой мощности 10 кВт из-за “недостаточной” температуры аустенитизации, при которой заметных изменений в микроструктуре не произошло, поэтому образцы сохранили перлитные колонии с некоторым количеством нерастворенных карбидов. Однако при большем времени нагрева, т.е. 9 с, образуется небольшое количество мартенсита, присутствие которого в структуре приводит к повышению значений твердости (рис. 6б). Таким образом, нами сделан вывод, что при использовании времени нагрева 3 с и мощности от 10 до 14 кВт образцы достигли уровня, отвечавшего наименьшим значениям твердости, из-за наличия мягких фаз – перлита и феррита [23, 24]. При высокой мощности (от 18 до 22 кВт) и времени ИЗ (от 6 до 9 с) достигается стабилизация значений микротвердости.
Электрохимический анализ
На рис. 7а–7в показаны потенцио-динамические поляризационные кривые, полученные при различных параметрах ИЗ. Из полученных данных видно, что в разных образцах, обработанных при наименьшем времени индукционной закалки (3 с) с различной мощностью, подводимой к индуктору, наблюдался существенно различный ход ПДП кривых (см. рис. 7а). Поведение ПДП кривых изменялось, когда образцы подвергались ИЗ при более продолжительном времени нагрева; в этом случае ПДП кривые сближаются, как это показано на рис. 7б и 7в. На рис. 7а показано, что для времени обработки 3 с, когда мощность, подводимая к индуктору, увеличилась с 10 до 22 кВт, катодная ветвь потенциодинамической кривой переместилась в сторону более отрицательных значений плотности тока, что соответственно повлияло на ее анодную ветвь, а также изменило значения плотности тока коррозии (Icorr) и потенциала коррозии (Ecorr). Подобные изменения поведения катодной и анодной ветвей также имели место и в случае образцов, обработанных в течение 6 и 9 с (рис. 7б в соответственно). Изменение поведения анодной и катодной ветвей было обусловлено электрохимической реакцией в исследуемой стали в среде HCl. Было надежно установлено, что при погружении Fe или его сплавов в среду HCl происходит следующая химическая реакция (1):
(1)
${\text{Fe}} + 2{\text{HCl}} \to {\text{FeC}}{{{\text{l}}}_{2}} + {{{\text{H}}}_{{\text{2}}}}\left( {\text{g}} \right).$Рис. 7.
Потенциодинамические поляризационные кривые при различных параметрах процесса индукционной закалки: а – 3 с, б – 6 с, в – 9 с, и г – поляризационные кривые Тафеля.
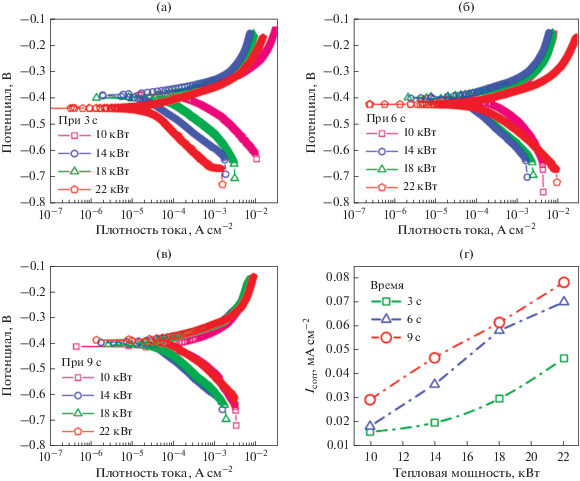
Более того, с позиций электрохимии эта реакция (1) может быть представлена как
(2)
${\text{Fe}} + 2{{{\text{H}}}^{ + }} + {\text{C}}{{{\text{l}}}^{{2 - }}} \to {\text{F}}{{{\text{e}}}^{{2 + }}} + {\text{C}}{{{\text{l}}}^{{2 - }}} + {{{\text{H}}}_{{\text{2}}}}\left( {\text{g}} \right).$Окисление Fe → Fe2+ происходило на анодной ветви при стандартном восстановительном потенциале –0.440 В, что также наблюдалось в значениях потенциала при разомкнутой цепи в текущих исследованиях, тогда как 2H+ + 2e → H2(g) происходило на катодной ветви электрода. Таким образом, изменение этих окислительно-восстановительных реакций из-за изменения параметров индукционной закалки привело к изменению значений Icorr, полученных и рассчитанных по поляризационным кривым Тафеля, которые представлены на рис. 7г.
На рис. 7г представлена плотность тока коррозии (Icorr) индукционно закаленных образцов, обработанных при выбранных экспериментальных параметрах ИЗ. Данные извлечены из результатов потенциодинамического сканирования. Легко заметить, что плотность тока коррозии постепенно возрастает с увеличением мощности, подводимой к индуктору. Образцы, обработанные в течение 3 с, показали самые низкие значения плотности тока коррозии при всех мощностях, что свидетельствует о высокой стойкости к коррозии. Аналогичным образом, образцы, обработанные в течение 6 и 9 с, показали постепенное снижение коррозионных характеристик. Это поведение можно понять, соотнеся его с соответствующими микроструктурами. Образцы после обработки при мощности 10 кВт обладали высокой коррозионной стойкостью благодаря наличию “мягких” фаз (например, перлита), содержание которых уменьшается с увеличением времени ИЗ и образованием мартенситной структуры. (Поскольку перлит при коррозии материала ведет себя как катодная область, а мартенсит как анодная [15].) Многофазная микроструктура в стали всегда вызывает гальваническую коррозию из-за существования микроячеек. В случае сталей в качестве составляющих фаз выступают перлит и мартенсит, перлит наиболее предпочтителен из-за его высокой способности противостоять коррозии.
Недавние исследования показали, что на коррозионную стойкость влияют природа фаз, их распределение и частицы второй фазы [14, 25, 26]. Во время индукционного нагрева по мере увеличения времени обработки остаточный аустенит стабилизируется, при этом реечный мартенсит обедняется по углероду, и развивается структура огрубленного мартенсита с островками остаточного аустенита (см. рис. 5г). Полученный в результате огрубленный мартенсит и сохраненный аустенит снижали коррозионную стойкость стали [12, 14, 27–29]. Таким образом, высокое значение коррозионного тока (Icorr), создаваемого “гальваническими элементами” этого типа, и снижение коррозионной стойкости сохранялись из-за возникновения огрубленной мартенситной фазы с увеличением мощности и времени индукционного нагрева. Поэтому для образцов, обработанных при высокой мощности, т.е. 22 кВт, с увеличенным временем обработки, т.е. при 9 с, можно выдвинуть предположение, что тенденция к увеличению значений Icorr указывает на наличие грубого мартенсита. При этом образцы, обработанные при мощности от 14 до 18 кВт, показали неизменность морфологии реечного мартенсита без заметного количества остаточного аустенита, что привело к повышению коррозионной стойкости стали при отсутствии или наличии незначительной доли микроячеек. Хотя в этом случае наблюдалось небольшое снижение твердости из-за более низкой объемной доли мартенсита [14–16, 25]. Кроме того, содержание углерода также влияет на скорость коррозии, поскольку в различных коррозионно-активных средах высокоуглеродистые фазы более стабильны и устойчивы, чем низкоуглеродистые фазы [14, 30]. Таким образом, грубая мартенситная структура менее устойчива, чем реечный мартенсит, из-за диффузии атомов углерода при высокой мощности, подводимой к индуктору, и при увеличении времени обработки.
Микроструктурный анализ после проведения коррозионных тестов
Микроструктуры корродированных образцов после испытания на потенциодинамическую поляризацию также анализировали для получения подробной информации о коррозионных характеристиках сплава при выбранных параметрах обработки. На рис. 8а–8м показаны микроструктуры корродированных образцов сразу после поляризационных испытаний Тафеля. На рис. 8а–8е представлено образование ямок от питтинговой коррозии при тепловой мощности 10 и 14 кВт и времени нагрева от 3 до 9 с. Интенсивность коррозии можно легко оценить по соответствующим микроструктурам. По мере увеличения мощности и времени индукционного нагрева коррозионные ямки начинают зарождаться, и их размер постепенно увеличивается. После ИЗ при более высоких мощности и времени, образование коррозионных ямок становилось более интенсивным, происходило слияние небольших ямок, что приводило к их расширению, как показано на рис. 8к–8м.
Рис. 8.
Изменение интенсивности образования коррозионных ямок при изменении параметров индукционного упрочнения: а–в – 10 кВт, г–е – 14 кВт, ж–и – 18 кВт, к–м – 22 кВт; а, г, ж, к – 3 с, б, д, з, л – 6 с, в, е, и, м – 9 с.
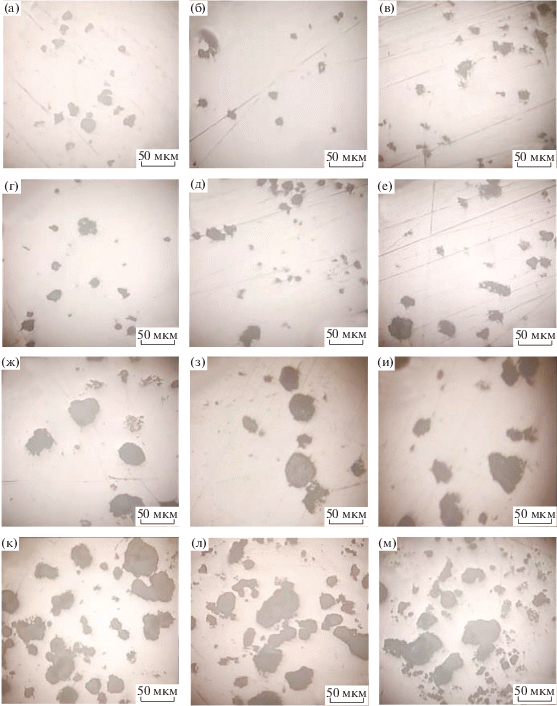
Следовательно, можно сделать вывод, что доля мартенсита увеличивается с постепенным увеличением значений параметров ИЗ, и в конечном итоге коррозионные характеристики сплава ухудшаются. Кроме того, также интересно отметить, что коррозионная стойкость сплава ухудшалась, когда в сплаве формировалась грубая мартенситная структура (см. рис. 3м и рис. 5г), а при образовании структуры реечного мартенсита коррозионные характеристики сплава значительно улучшались благодаря более низкой величине плотности тока коррозии, что видно из рис. 7г. Кроме того, высокая твердость была также достигнута при мощности 14 кВт и времени нагрева 9 с (см. рис. 6а и 6б). Это указывает на то, что лучшие коррозионные характеристики, а также оптимальные механические свойства могут быть получены при использовании мощности, подводимой к индуктору, 14 кВт и времени индукционного нагрева 6–9 с.
ВЫВОДЫ
Мощность, подводимая к индуктору, и продолжительность нагрева являются очень эффективными параметрами, знание которых необходимо при моделировании процесса индукционной закалки материала и для получения требуемых свойств. Варьированием уровня мощности и времени индукционного нагрева можно достичь надлежащей температуры аустенитизации. Таким образом, данное экспериментальное исследование изучает вопросы реакции стали DIN 42CrMo4 (1.7225) на индукционную закалку при разных значениях параметров воздействия на материал и отвечает на следующие основные вопросы:
1. Микротвердость индукционно закаленных образцов постепенно повышалась с увеличением мощности и времени индукционной обработки. Однако резкое возрастание значений твердости наблюдается при более высоких мощности и времени нагрева за счет образования максимальной объемной доли мартенсита. Поэтому при использовании мощности, подводимой к индуктору, в диапазоне 18–22 кВт и времени нагрева от 6 до 9 с, было получено большое количество мартенсита в стали DIN 42CrMo4 и достигнуто высокое значение твердости материала.
2. Образование коррозионных ямок стало серьезным отличием материала после ИЗ при высоких экспериментальных значениях, что указывало на ухудшение коррозионных характеристик сплава. При изменении мощности от 14 до 18 кВт, произошло изменение в характере формирования ямок.
3. В целом коррозионная стойкость индукционно закаленных образцов снижалась по мере того, как микроструктура трансформировалась в структуру с высокой объемной долей мартенсита. Но исследование показало, что морфология мартенсита сыграла решающую роль в коррозионных характеристиках сплава; было обнаружено, что структура реечного мартенсита обладает большей коррозионной стойкостью по сравнению с огрубленным мартенситом, с незначительным различием в величине твердости в пользу последнего.
4. Высокая твердость и лучшая коррозионная стойкость были получены при мощности 14 кВт и времени нагрева от 6 до 9 с, что указывает на оптимальные параметры обработки для стали DIN 42CrMo4 (1.7225).
Список литературы
Rudnev V., Loveless D., Cook R.L. Handbook of induction heating. CRC press, 2017.
Semiatin S. Elements of induction heating: design, control, and applications. ASM International, 1988.
Revilla C., López B., Rodriguez-Ibabe J. Carbide size refinement by controlling the heating rate during induction tempering in a low alloy steel // Mater. & Design. 2014. V. 62. P. 296–304.
Prisco U. Case microstructure in induction surface hardening of steels: an overview. // Intern. J. Advan. Manufact. Techn. 2018. V. 98. № 9–12. P. 2619–2637.
Akinay Y., Hayat F. The influence of the heat treatment on mechanical and microstructure properties of Fe–Mn–C high-manganese steel // Kovove Mater. 2016. V. 54. P. 91–96.
Li H., He L., Gai K., Jiang R., Zhang C., Li M. Numerical simulation and experimental investigation on the induction hardening of a ball screw // Mater. & Design. 2015. V. 87. P. 863–876.
Yin F., Hua L., Mao H., Han X. Constitutive modeling for flow behavior of GCr15 steel under hot compression experiments // Mater. & Design. 2013. V. 43. P. 393–401.
Cao Y.J., Sun J.Q., Ma F., Chen Y.Y., Cheng X.Z., Gao X., Xie K. Effect of the microstructure and residual stress on tribological behavior of induction hardened GCr15 steel // Tribology International, 2017. V. 115. P. 108–115.
Gao K., Qin X., Wang Z., Zhu S. Effect of spot continual induction hardening on the microstructure of steels: Comparison between AISI 1045 and 5140 steels // Materials Science and Engineering: A. 2016. V. 651. P. 535–547.
Kim M., Rhee K.Y., Paik Y.N., Hong J.S., Ham Y.S. Experimental investigation on the mechanical behavior of high-frequency induction-hardened mild carbon, SPS5 steel // Mater. Sci. Eng.: A. 2008.V. 485. № 1–2. P. 31–38.
Coupard D., Palin-luc T., Bristiel P., Ji V., Dumas C. Residual stresses in surface induction hardening of steels: Comparison between experiment and simulation // Mater. Sci. Eng.: A. 2008. V. 487. № 1–2. P. 328–339.
Guo Y.-B., Li C., Liu Y.-C., Yu L.-M., Ma Z.-Q., Liu C.-X., Li H.-J. Effect of microstructure variation on the corrosion behavior of high-strength low-alloy steel in 3.5 wt % NaCl solution // Intern. J. Minerals, Metal., Mater. 2015. V. 22. № 6. P. 604–612.
Katiyar P.K., Behera P.K., Misra S., Mondal K. Comparative Corrosion Behavior of Five Different Microstructures of Rebar Steels in Simulated Concrete Pore Solution with and Without Chloride Addition // J. Mater. Eng. Perform. 2019. V. 28. № 10. P. 6275–6286.
Handoko W., Pahlevani F., Sahajwalla V. Enhancing Corrosion Resistance and Hardness Properties of Carbon Steel through Modification of Microstructure // Materials. 2018. V. 11. № 12. P. 2404.
Handoko W., Anurag A., Pahlevani F., Hossain R., Sahajwalla V., Privat K. Effect of selective-precipitations process on the corrosion resistance and hardness of dual-phase high-carbon steel // Sci. Rep. 2019. V. 9(1). P. 15631.
Lin C.-H., Lee J.-R., Sheu H.-H., Tsai S.-Y. Corrosion Resistance and Mechanical Property Enhancement of SPCC Steel Using an Induction Heat Treatment // Intern. J. Electrochemical Sci. 2017. V. 12. P. 7965–7976.
Van Bennekom A., Matihews L.M., Tarboton J.N., Robinson F.P.A. The Effect of Martensite Content on the Corrosion and Mechanical Properties of Dual-phase 12 per cent Cr Steels. /in INFACON 6. Proceedings oj the 1st Imen/arional Chromium Steel and Alloys Congress. Cape Town, Johannesburg, 1992. V. 2. P. 157–163.
Bui H.-T., Hwang S.-J. Development of barrel heating system in injection molding machine via induction heating // Rapid Prototyping J. 2015. V. 21. № 3. P. 244–249.
Simpson P.G. Induction heating: coil and system design. London: McGraw-Hill, 1960.
ASTM E407-07(2015)e1, Standard Practice for Microetching Metals and Alloys. West Conshohocken, PA, 2015.
Clarke K.D., Van Tyne C.J., Vigil C.J., Hackenberg R.E. Induction Hardening 5150 Steel: Effects of Initial Microstructure and Heating Rate // J. Mater. Eng. and Performance. 2011. V. 20. № 2. P. 161–168.
Fuhrmann J., Hömberg D., Uhle M. Numerical simulation of induction hardening of stee // COMPEL: Int J. for Computation and Maths. in Electrical and Electronic Eng. 1999. V. 18. № 3. P. 482–493.
Onan M., Baynal K., Ünal H.İ. Determining the influence of process parameters on the induction hardening of AISI 1040 steel by an experimental design method // Indian J. Engineering & Materials Sciences. 2015. V. 22. P. 513–520.
Onan M., Baynal K., Ünal H.İ., Katre F. Optimization of induction hardened AISI 1040 steel by experimental design method and material characterization analysis / in ASME International Mechanical Engineering Congress and Exposition American Society of Mechanical Engineers. 2012. P. 1219–1222.
Hafeez M.A., Inam A., Farooq A. Mechanical and corrosion properties of medium carbon low alloy steel after cyclic quenching and tempering heat–treatments // Mater. Research Express. 2020. V. 7. № 1. P. 016553.
Park I.-J., Kim S.-T., Lee I.-S., Park Y.-S., Moon M.B. A Study on Corrosion Behavior of DP-Type and TRIP-Type Cold Rolled Steel Sheet // Mater. Trans. 2009. V. 50. № 6. P. 1440–1447.
Dalmau A., Richard C., Igual–Muñoz A. Degradation mechanisms in martensitic stainless steels: Wear, corrosion and tribocorrosion appraisal // Tribology International. 2018. V. 121. P. 167–179.
Nice P.I., Ueda M. The Effect of Microstructure and Chromium Alloying Content to the Corrosion Resistance of Low-Alloy Steel Well Tubing in Seawater Injection Service /in CORROSION 98. NACE International: San Diego, California, 1998 p. 11.
Monrrabal G., Bautista A., Guzman S., Gutierrez C., Velasco F. Influence of the cold working induced martensite on the electrochemical behavior of AISI 304 stainless steel surfaces // J. Mater. Research and Technology. 2019. V. 8. № 1. P. 1335–1346.
Hao X., Dong J., Nabuk Etim I.-I., Wei J., Ke W. Sustained effect of remaining cementite on the corrosion behavior of ferrite-pearlite steel under the simulated bottom plate environment of cargo oil tank // Corrosion Sci. 2016. V. 110. P. 296–304.
Дополнительные материалы отсутствуют.
Инструменты
Физика металлов и металловедение