Физика металлов и металловедение, 2021, T. 122, № 12, стр. 1309-1316
Структура и механические свойства сплава Al–Cu–Mg–Si, полученного селективным лазерным сплавлением
И. Г. Бродова a, *, А. Н. Кленов b, И. Г. Ширинкина a, Е. Б. Смирнов b, Н. Ю. Орлова c
a Институт физики металлов УрО РАН им. М.Н. Михеева
620108 Екатеринбург, ул. С. Ковалевской, 18, Россия
b ФГУП “РФЯЦ-ВНИИТФ им. академ. Е.И. Забабахина”
456770 Снежинск, ул. Васильева, 13, а/я 245, Россия
c СФТИ НИЯУ МИФИ
456776 Снежинск, ул. Комсомольская, 8, Россия
* E-mail: brodova@imp.uran.ru
Поступила в редакцию 06.07.2021
После доработки 23.08.2021
Принята к публикации 24.08.2021
Аннотация
Рассмотрено влияние физических и технологических характеристик 3D-печати на структуру и твердость монолитных и сетчатых деталей из Al–Cu–Mg–Si-сплава, полученных методом селективного лазерного сплавления. Сравнивали структуру и твердость монолитных образцов, синтезированных при мощности лазера (P = 100–200 Вт) и скорости сканирования (V = 400–950 мм/с) при постоянных диаметре пучка лазера (60 и 75 мкм) и толщине слоя порошка (0.05 мм). Установлено, что твердость 50HB10/250 имели образцы, синтезированные при Р = 200 Вт и V = 750–900 мм/с, а наименьшей твердостью (менее 28HB10/250) обладали образцы, полученные при V = 400 мм/с и Р = 100 Вт. Металлографические исследования структуры образцов выявили наличие дефектов, таких, как усадочные пустоты, горячие трещины и нерасплавленные частицы порошка. Получены экспериментальные данные, показывающие взаимосвязь геометрии построения сетчатых образцов с разным уровнем заполнения (количеством и конфигурацией отверстий) с их динамическими свойствами, измеренными при сжатии методом Гопкинсона–Кольского. Установлено, что уменьшение плотности (ρ = 2.44 – 1.19 г/см3) и повышение суммарной доли площади отверстий в плоскости построения и в перпендикулярной ей плоскости от 4 до 86% приводит к снижению динамических механических свойств: предела текучести в 3 раза, а предела прочности в 4.7 раза.
ВВЕДЕНИЕ
Разработки аддитивных способов получения Al сплавов являются приоритетными направлениями исследований в России и за рубежом [1‒4]. Изготовления по компьютерным моделям деталей сложной формы, обладающих высокими механическими свойствами, имеют хорошие перспективы для развития современных технологий в аэрокосмической и машиностроительной отрасли.
Среди материалов, для которых разрабатываются аддитивные технологии, Al сплавы занимают одно из первых мест. Наиболее известны и доведены до практического использования способы селективного лазерного сплавления (СЛС) Al–Si-сплавов с применением 3D принтеров [5‒9]. Полученные результаты доказали, что СЛС технология имеет большие преимущества перед традиционными способами производства отливок из силуминов, позволяя не только экономить материал, но и за счет высоких скоростей охлаждения расплава получать изделия с дисперсной структурой и повышенными эксплуатационными характеристиками.
Сплавы системы Al–Cu–Mg, относящиеся к классу 2ххх-сплавов, являются широко распространенными легкими сплавами, обладающими высокими свойствами, такими как прочность, коррозионная стойкость, пластичность, хорошая свариваемость. Сплавы относятся к термически упрочняемым сплавам, поэтому их свойства можно регулировать в широких пределах за счет подбора режимов термической обработки. Все это явилось причиной для быстрого развития новых аддитивных технологий получения этих сплавов, включая селективное лазерное сплавление [10‒12]. Большинство исследований посвящено описанию особенностей структурообразования при подборе параметров принтера для получения качественных деталей и аттестации их свойств. В частности, в [10] предложены режимы 3D-печати, позволяющие получить качественные образцы из Al–Cu–Mg-сплава типа АА2024 с плотностью 99.8%. Авторы [10] описывают влияние режимов термической обработки на свойства СЛС Al–Cu–Mg-сплава и доказывают, что оптимальным режимом гомогенизации является нагрев до температуры 540°С с выдержкой 1 ч, а высокие механические свойства σВ = 532 МПа, σ0.2 = 338 МПа, δ = 13% – обусловлены выделением вторичной AlCuMg фазы.
Недостатком Al–Mg композиций является их склонность к образованию трещин при горячей пластической деформации, для устранения этого дефекта в сплавы добавляют скандий [11, 12]. К более стойким к трещинообразованию сплавам относятся сплавы системы Al–Mg–Si–Cu типа АК6 (АА1360), которые применяются для изготовления сложных штамповок для нагруженных деталей, работающих в том числе и в условиях криогенных температур.
Метод СЛС позволяет создавать детали сложной формы с внутренними отверстиями и перегородками из конструкционных материалов, подвергающихся экстремальным нагрузкам [13, 14]. Такие объекты, сочетающие низкую массу и высокие удельные механические характеристики, имеют преимущества перед монолитными аналогами и находят применение в оборонной и космической технике. Использование сплава АК6 для изготовления деталей сложной формы является перспективным, а применение метода 3D печати позволит значительно сократить затраты на их производство. Целью данной работы является изучение структуры монолитных и сетчатых образцов из сплава АК6, полученных СЛС, и определение их динамических свойств.
Отсутствие таких данных в научной литературе делает эти исследования интересными и актуальными, а полученные результаты будут использованы для совершенствование практики 3D-печати деталей из алюминиевых сплавов.
МАТЕРИАЛ И МЕТОДЫ ИССЛЕДОВАНИЯ
Объектами исследования служили монолитные и сетчатые образцы из Al сплава АК6, синтезированные на 3D-принтере по металлу Realizer SLM100. Образцы получены селективным лазерным сплавлением порошка, изготовленного на предприятии ФГУН ВИАМ. Гранулометрический состав порошка удовлетворял стандартным условиям синтеза – половина частиц имела размеры от 20 до 60 мкм, а доля частиц размером 80 мкм не превышала 5%.
Содержание основных компонентов в алюминиевой матрице порошка и сплава после СЛС проверяли на спектрометре ICPE-9000 SHIMADZU с индуктивно-связанной плазмой (погрешность ±0.01 мас. %).
Результаты анализа показали хорошее совпадение химических составов порошка и синтезированного сплава со стандартным составом сплава АК6 (табл. 1).
Таблица 1.
Химический состав сплава АК6
Элемент, мас. % | Mg | Cu | Mn | Si | Al |
---|---|---|---|---|---|
Порошок | 0.64 | 2.25 | 0.51 | 0.99 | Oснова |
СЛС сплав | 0.61 | 2.25 | 0.50 | 0.98 | Oснова |
ГОСТ 4784–97 | 0.4–0.8 | 1.8–2.6 | 0.4–0.8 | 0.7–1.2 | Oснова |
Режимы работы принтера при синтезе монолитных деталей указаны в таблице 2. Варьировали такие параметры, как мощность лазера (P), скорость сканирования (V), диаметр пучка (d) и межтрековое расстояние (S) при толщине слоя порошка t = 0.05 мм.
СЛС-детали имели форму дисков толщиной 9 мм и диаметром 80 мм. Сетчатые детали специального назначения были синтезированы при одинаковых СЛС параметрах: P = 200 Вт, V = 500 мм/c, d = 60 мкм, S = 12 мм, и разделены на 4 группы в зависимости от их плотности и топологии внутреннего строения (размера, количества и формы отверстий).
Образцы для анализа структуры изготавливали с использованием механического полирования на алмазной суспензии. Финишную полировку проводили на суспензии коллоидного диоксида кремния. Для выявления макро и микроструктуры применяли электрохимическую полировку в электролите (430 мл H3PO4, 50 г CrO3) и химическое травление в реактиве Келлера (0.5 мл HF, 2.5 мл HNO3, 1.5 мл HCl, 100 мл H2O).
Структуру изучали на поперечных и продольных шлифах, соответствующих плоскости построения образцов и перпендикулярной ей плоскости, с помощью световых оптических микроскопов (ОМ) Neophot-32 и Микромед МС2 Zoom 2CR и сканирующего электронного микроскопа (СЭМ) “Quanta-200” с приставкой для автоматического индексирования карт дифракции обратно-отраженных электронов (EBSD анализ). На основании этих данных построены гистограммы распределения зерен-субзерен по размерам и по углам разориентировки. Твердость образцов измеряли на приборе Бринелль (диаметр шарика 10 мм, нагрузка 250 кг) согласно ГОСТ 9012–59. Значения твердости усредняли по 3–5 отпечаткам, измеренным с погрешностью ±0.25%. (погрешность определения экспериментальных значений твердости не превышала ±1.5%). Микротвердость структурных составляющих определяли на приборе ПМТ-3 (нагрузка 20 г). Усреднение результатов проводили по 10 измерениям. Погрешности измерений микротвердости рассчитывали методом Стъюдента. При доверительной вероятности 0.95 относительная погрешность среднего значения микротвердости составила 5%.
Динамические механические свойства на сжатие сетчатых образцов определяли по методу Гопкинсона–Кольского. Размеры образцов до сжатия: ∅ – 14–16 мм; толщина 7–8 мм. В каждой группе было испытано 6 образцов. Скорость деформации варьировали в интервале (8–31) × × 102 с–1 путем изменения скорости ударника от 9.61 до 22.72 м/с. Относительная деформация ε образцов не превышала 43%. По результатам динамических испытаний построены графики зависимостей напряжения и скорости деформации от относительной деформации (σ(ε) и έ (ε)), и установлены значения условных пределов текучести и прочности в зависимости от скорости деформации. Далее в каждой группе определяли средние значения механических характеристик шести образцов, нагруженных во всем интервале скоростей деформации (8–31) × 102 с–1. Подробно построение графиков и обработка результатов эксперимента описаны в [15, 16].
РЕЗУЛЬТАТЫ И ИХ ОБСУЖДЕНИЕ
Структура и твердость монолитных образцов. Для определения оптимальных параметров для 3D-печати монолитных образцов проведено сравнение их структуры и свойств при варьировании параметров синтеза согласно табл. 2. В частности, сравнивали образцы, синтезированные при диаметре лазерного пучка (d = 60 и 75 мкм) и одинаковой толщине слоя порошка (t = 0.05 мм) и разных мощности лазера (P = 100–200 Вт) и скорости сканирования (V = 400–950 мм/с). В качестве характеристики свойств материала использовали твердость СЛС образцов. Полученные зависимости твердости от мощности лазера при d = 60 мм и 75 мм и V = 700 мм/с показаны на рис. 1. Рисунок 2 иллюстрирует зависимость твердости от скорости сканирования при P = 200 и 100 Вт и d = 60 мкм.
Из приведенных зависимостей видно, что твердость меняется при варьировании технологических параметров синтеза. Наибольшую твердость более 50 HB10/250 имели образцы, полученные при P = 200 Вт и V = 750–950 мм/с. Наименьшую твердость менее 29HB10/250 имели образцы, синтезированные при P = 100 Вт и V = 450 мм/с. Для объяснения такой разницы твердости представляло интерес проанализировать эволюцию структуры СЛС образцов и оценить их качество. На рис. 3а показана структура в поперечном сечении СЛС образца с типичной эллиптической формой ванны расплава (треками). Внутри треков выявляется неравномерная структура, образованная столбчатыми и равноосными зернами.
Рис. 3.
Структура СЛС-образцов в поперечном сечении: а – зерна внутри трека; б – ячеистая субструктура (ОМ); в – эвтектические алюминиды Al (Cu, Mg) по границам ячеек (СЭМ).
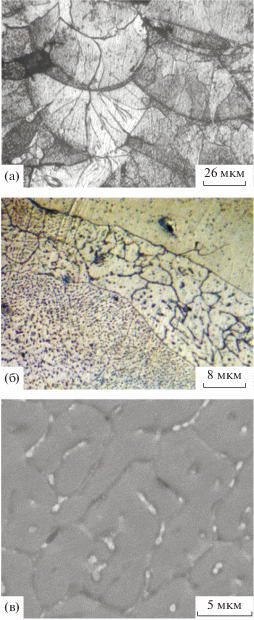
С увеличением мощности лазера глубина зоны проплавления увеличивается, а количество столбчатых зерен, растущих по направлению теплоотвода, сокращается, появляются области равноосных зерен. Подавление роста столбчатых зерен связано с уменьшением температурного градиента в объеме ванны расплава.
Смешанная структура, присущая технологии получения СЛС образцов, четко прослеживается при EBSD-анализе (рис. 4). Сопоставляя ориентационную карту (рис. 4а) с картой распределения границ зерен-субзерен по углам разориентировки (рис. 4б) и с гистограммами распределения зерен-субзерен по размерам (рис. 4в) и по углам разориентировки (рис. 4г), видно, что в данной области структуры доля большеугловых границ зерен с разориентировкой >15° (БУГ) составляет 25%, а преобладающую долю (~70%) имеют малоугловые границы (МУГ) субзерен с углом разориентировки менее 5°. Наличие таких границ дислокационного происхождения свидетельствует о неравновесной кристаллизации сплава с образованием внутренней ячеистой субструктуры внутри зерен. Средний размер зерен-субзерен равен 22 мкм, а размер зерен не превышает 100 мкм. Для сравнения размер зерна в слитках из сплава АК6 составляет не менее 500 мкм, что указывает на измельчение структуры при СЛС.
Рис. 4.
EBSD-анализ: а – ориентационная карта; б – карта распределения границ зерен-субзерен по углам разориентировки (БУГ обозначены черным цветом, МУГ-серым цветом); в – гистограмма распределения зерен–субзерен по размерам; г – спектр углов разориентировок зерен–субзерен.
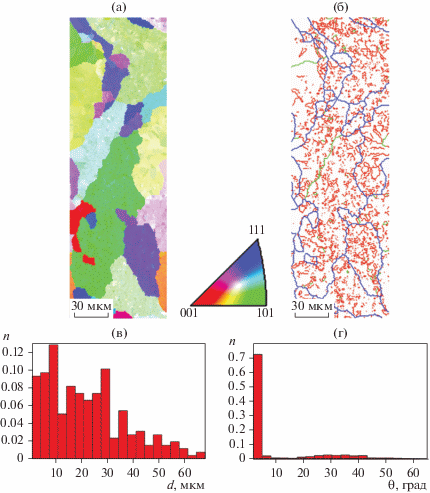
На рис. 3б показана область равноосных зерен с ячеистой субструктурой. В центральной части трека ячейки меньше ~2 мкм, а по границам, вследствие переплава при повторном прохождении лазерного пучка, они крупнее в 2–2.5 раза. Ячеистый тип кристаллизации часто наблюдается при быстрой закалке Al сплавов из расплава и свидетельствует о высоком значении параметра G/R (где G – температурный градиент на межфазной границе кристалл–расплав, а R – скорость кристаллизации) [17].
На рис. 3в дано изображение структуры трека, полученное во вторичных электронах (СЭМ), на котором видно, что эвтектические алюминиды Al (Cu, Mg), элементный состав которых подтвержден ЕDS-анализом, образуют дискретную тонкую сетку по границам ячеек, толщина которой составляет 150–900 нм. Смена формы роста эвтектики с пластинчатой в литом сплаве на глобулярную в СЛС сплаве также обусловлена высокими скоростями охлаждения расплава при синтезе. Микротвердость СЛС сплава HV = 650–750 МПа. Все вышеперечисленные факты подтверждают идентичность структурообразования Al сплавов при СЛС и быстрой закалке из расплава, что неоднократно отмечалось ранее [9, 17, 18].
При анализе качества СЛС образцов, не зависимо от режима их синтеза, было обнаружено большое количество дефектов – усадочных пустот (рис. 5а), не растворившихся частиц исходного порошка и кристаллизационных трещин (рис. 5б), что не могло не сказаться на результатах измерения твердости.
Известно, что [4, 19, 20] при использовании низкой мощности лазерного излучения совместно с высокой скоростью сканирования не происходит полного расплавления порошка из-за недостатка энергии, что не позволяет получить хорошую зону перекрытия между слоями и приводит к пористости. При использовании режимов с высокой мощностью лазерного излучения и низкой скоростью сканирования создаются температурные условия, достаточные для испарения материала, что также приводит к высокой пористости. Газовая пористость является одним из наиболее распространенных дефектов в СЛС-алюминиевых сплавах и может оказывать сильное влияние на усталостную прочность. Установлено, что газовые поры, объемная доля которой составляет 0.2–1.6%, и средний размер – 20–55 мкм, инициируют разрушение образцов при испытании на усталость [20].
Наличие кристаллизационных трещин в СЛС-образцах в первую очередь [21–23] связано с большими термическими напряжениями, возникающими вследствие цикличности быстрых процессов нагрева и охлаждения. Так, в [22, 23] путем измерения внутренних напряжений в Ti и Co сплавах установлено, что при СЛС возникают упругие напряжения растяжения, снижающие пластичность материала и приводящие к его разрушению. В Al сплавах причиной кристаллизационных трещин является также широкий эффективный интервал кристаллизации [24].
Можно заключить, что все исследованные образцы, содержат макродефекты, и для их устранения требуется корректировка режимов синтеза. В целях дальнейшей оптимизации технологии синтеза образцов из сплава АК6, были проанализированы результаты качественной 3D печати Al сплавов других составов. Согласно [7, 25], основным параметром синтеза, влияющим на теплофизические условия на межфазной границе расплав-кристалл и, тем самым, контролирующим структуру и дефектность СЛС сплавов, является плотность энергии Ψ, которую можно рассчитать по формуле:
Практика получения качественных бездефектных образцов из Al-сплавов показала, что плотность энергии должна быть не менее 180–340 Вт с/мм3 [7, 25]. Из этих результатов следует, что при предельной мощности лазера 200 Вт и заданных параметрах S и t (см. табл. 2), скорость сканирования, для случая получения качественных образцов из сплава АК6, должна быть снижена до 200 мм/с. Данные рекомендации требуют практической проверки в дальнейших экспериментах.
Структура и динамические свойства сетчатых образцов. Сетчатые образцы из сплава АК6, отличающиеся плотностью, разным уровнем заполнения, конфигурацией и количеством внутренних отверстий, были разделены на 4 группы по 6 штук в каждой (группы 1–4). На рис. 6а, 6б в качестве примера представлены фотографии двух сечений образцов, входящих в первую группу. Тонкая структура каркаса из сплава АК6 идентична описанной выше структуре монолитных образцов.
В задачу эксперимента входило определение связи топологии внутреннего строения образцов с их динамическими свойствами.
В качестве условной характеристики, описывающей топологию внутреннего строения сетчатых образцов каждой группы, была выбрана суммарная доля площади, занятой отверстиями в плоскости построения и перпендикулярной ей плоскости (Σ S1 + S2), где S1 – отношение суммы площадей всех отверстий в поперечном сечении к его площади, а S2 – отношение суммы площадей всех отверстий в продольном сечении к его площади.
Для расчета этой характеристики использовали программный комплекс “FIJI” – расширенную версию программы ImageJ, позволяющий обрабатывать оптические изображения объектов любой формы и определять их количество, размеры, площади и т.д. [26]. Оптические изображения поперечных и продольных сечений сетчатых образцов, на которых проводили расчеты площади отверстий, были получены на микроскопе “Микромед MC2 Zoom 2CR” при одном увеличении (погрешность измерения ±5%).
В табл. 3 приведены результаты этих расчетов для образцов, входящих в разные группы. Образцы каждой группы подвергались динамическому сжатию при одинаковых режимах нагружения έ = = (8–31) × 102 с–1. Для сравнения свойств сетчатых образцов в зависимости от уровня их заполнения были посчитаны средние значения механических характеристик в пределах каждой группы.
Таблица 3.
Характеристика сетчатых образцов до испытаний
№№ группы |
Плотность, г/см3 |
Доля площади, занятой отверстиями в поперечном сечении, S1, % | Доля площади, занятой отверстиями в продольном сечении, S2, % | ΣS1 + S2 |
---|---|---|---|---|
1 | 1.24 | 44 | 42 | 86 |
2 | 1.19 | 32 | 46 | 78 |
3 | 1.79 | 17 | 11 | 28 |
4 | 2.44 | 3 | 1 | 4 |
В табл. 4 представлены средние значения механических характеристик четырех групп образцов (по 6 образцов в каждой группе), определенные при динамическом сжатии во всем интервале έ = (8–31) × 102 с–1. Исходя из приведенных данных, видно, как изменяются динамические свойства в зависимости от топологии внутреннего строения сетчатых образцов. Эти данные позволяют ориентировочно оценить потерю прочностных характеристик деталей с ростом объема, занятого отверстиями.
Таблица 4.
Динамические свойства СЛС образцов с разным уровнем заполнения (έ = (8–31) × 102 с–1)
№№ группы |
ΣS1+S2, % | Средние значения, МПа | |
---|---|---|---|
σТ | σВ | ||
1 | 86 | 28 | 52 |
2 | 78 | 30 | 52 |
3 | 28 | 42 | 110 |
4 | 4 | 87 | 244 |
После испытаний внешняя форма отверстий и их площади меняются (рис. 6в, 6г). Например, Σ S1 + S2 в образце первой группы, продеформированном на 43% с έ = 24 × 102 с–1, уменьшается с 86 до 58% (S1 = 32%, а S2 = 26%). В результате динамического сжатия алюминиевый каркас сетчатых образцов дополнительно упрочняется, его микротвердость возрастает с 750 до 1050 МПа. Дополнительное упрочнение материала достигается за счет увеличения плотности дислокаций, что неоднократно доказано при анализе деформированной структуры Al-сплавов [16, 27], а также стали [28] после динамического сжатия по методу Гопкинсона–Кольского.
ЗАКЛЮЧЕНИЕ
Методом СЛС получены монолитные и сетчатые детали из Al–Mg–Cu–Si-сплава. Изучено влияние режимов 3D-печати на структуру, твердость и дефектность деталей. Показано, что при мощности лазера P = 100–200 Вт и скорости сканирования более 400 мм/с в структуре сохраняются не проплавленные частицы порошка и присутствуют горячие трещины и поры. Для устранения этих дефектов и повышения качества деталей предложено изменение режима печати за счет снижения скорости сканирования лазерного пучка. Установлено, что СЛС-образцы из сплава АК6 имеют смешанную структуру, состоящую из столбчатых и равноосных зерен, средний размер которых на порядок ниже, чем в сплаве, полученном традиционными методами литья. Определено, что многократный нагрев и высокая скорость охлаждения расплава вызывают формирование дисперсной ячеистой структуры Al-твердого раствора и интерметаллидных фаз эвтектического происхождения субмикронных размеров. Исследована структура и динамические свойства сетчатых деталей с разным уровнем заполнения. Показано, что снижение суммарной доли площади отверстий в плоскости построения и перпендикулярной ей плоскости от 86 до 4% приводит к трехкратному повышению динамического предела текучести и к росту предела прочности в 4.7 раза.
Авторы выражают благодарность за участие в проведении металлографических исследований Т.И. Яблонских и В.В. Астафьеву.
Работа выполнена в рамках государственного задания МИНОБРНАУКИ России (тема “Структура”, № АААА-А18-118020190116-6. Электронно-микроскопические исследования проведены в ЦКП “Испытательный центр нанотехнологий и перспективных материалов” ИФМ УрО РАН.
Список литературы
Каблов Е.Н. Аддитивные технологии – доминанта национальной технологической инициативы // Интеллект и технологии. 2015. № 2(11). С. 52–55.
Попкова И.С., Золоторевский В.С., Солонин А.Н. Производство изделий из алюминия и его сплавов методом селективного лазерного плавления // Технология легких сплавов. 2014. № 4. С. 14–24.
Louvis E., Fox P., Sutcliffe C.J. Selective laser melting of aluminium components. // J. Mater. Proces. Techn. 2011. V. 211. P. 275–84.
DebRoy T., Wei H.L., Zuback J.S., Mukherjee T., Elmer J.W., Milewski J.O., Beese A.M., Wilson-Heid A., Ded A., Zhang W. Additive manufacturing of metallic components – Process, structure and properties // Progress in Mater. Sci. 2018. V. 92. P. 112–224.
Рябов Д.К., Антипов В.В., Королев В.А., Медведев П.Н. Влияние технологических факторов на структуру и свойства силумина, полученного с использованием технологии селективного лазерного синтеза // Авиационные материалы и технологии. 2016. № S1. С. 44–51.
Olakanmi E.O. Selective laser sintering/melting (SLS/SLM) of pure Al, Al–Mg, and Al–Si powders: effect of processing conditions and powder properties // J. Mater. Proces. Techn. 2013. V. 213. P. 1387–1405.
Read N., Wang W., Essa K., Attallah M.M. Selective laser melting of AlSi10Mg alloy: Process optimization and mechanical properties development. // Mater. Design. 2015. V. 64. P. 417–424.
Zhao J., Easton M., Qian M., Leary M., Brandt M. Effect of building direction on porosity and fatigue life of selective laser melted AlSi12Mg alloy // Mater. Sci. Eng. A. 2018.V. 729. P. 76–85.
Бродова И.Г., Чикова О.А., Петрова А.Н., Меркушев А.Г. Структурообразование и свойства эвтектического силумина, полученного селективным лазерным сплавлением // ФММ. 2019. Т. 120. № 11. С. 1204–1209.
Zhang H., Zhu H., Qi T., Hu Z., Zeng X. Selective laser melting of high strength Al–Cu–Mg alloys: Processing, microstructure and mechanical properties // Mater. Sci. Eng. A. 2016. V. 656. P. 47–54.
Spierings A.B., Dawson K., Voegtlin M., Palm F., Uggowitzer P.J. Microstructure and mechanical properties of as-processed scandium modified aluminium using selective laser melting // Manufacturing Technology. 2016. V. 65. P. 213–216.
Spierings A.B., Dawson K., Heeling T., Uggowitzer P.J., Schäublind R., Palme F., Wegener K. Microstructural features of Sc- and Zr-modified Al–Mg alloys processed by selective laser melting // Mater. Design. 2017. V. 115. P. 52–63.
Savio G., Rosso S., Meneghello R., Concheri G. Geometric modeling of cellular materials for additive manufacturing in biomedical field: a review // Applied Bionics and Biomechanics. 2018. № 3. P. 1–14.
Дьяченко С.В., Лебедев Л.А., Сычев М.М. Нефедова Л.А. Физико-механические свойства модельного материала с топологией трижды периодических поверхностей минимальной энергии типа гироид в форме куба // Журн. техн. физики. 2018. Т. 88. В. 7. С. 1014–1017.
Петрова А.Н., Бродова И.Г., Разоренов С.В., Шорохов, Е.В., Акопян Т.К. Механические свойствf Al–Zn–Mg–Fe–Ni сплава эвтектического типа при разных скоростях деформации // ФММ. 2019. Т. 120. № 12. С. 1322–1328
Ширинкина И.Г., Бродова И.Г., Распосиенко Д.Ю., Мурадымов Р.В., Елшина Л.А., Шорохов Е.В., Разоренов С.В., Гаркушин Г.В. Влияние добавки графена на структуру и свойства алюминия // ФММ. 2020. Т. 121. № 12. С. 1297–1306.
Бродова И.Г., Попель П.С., Барбин Н.М., Ватолин Н.А. Расплавы как основа формирования структуры и свойств алюминиевых сплавов. Екатеринбург: УрО РАН, 2005. 369 с.
Aboulkhai N.T., Maskery I., Tuck C. The microstructure and mechanical properties of selectively laser melted AlSi10Mg: The effect of a conventional T6-like heat treatment // Mater. Sci. Eng.: A. 2016. V. 667. P. 139–146.
Carter L.N., Martin C., Withers P.J., Attallah M.M. The influence of the laser scan strategy on grain structure and cracking behaviour in SLM powder-bed fabricated nickel superalloy // J. Alloy Comp. 2014. V. 615. P. 338–47.
Galy C., Le Guen E., Lacoste E., Arvieu C. Main defects observed in aluminum alloy parts produced by SLM: From causes to consequences // Additive Manufacturing. 2018. V. 22. P. 165–175.
Khairallah S.A., Anderson A.T., Rubenchik A., King W.E. Laser powder-bed fusion additive manufacturing: Physics of complex melt flow and formation mechanisms of pores, spatter, and denudation zones // Acta Mater. 2016. V. 108. P. 36–45.
Казанцева Н.В., Ежов И.В., Виноградова Н.И., Ильиных М.В., Фефелов А.С., Давыдов Д.И., Оленева О.А., Карабаналов М.С. Влияние геометрии построения образца в методе селективного лазерного сплавления на микроструктуру и прочностные характеристики сплава Ti–6Al–4V // ФММ. 2018. Т. 119. № 11. С. 1138–1164.
Казанцева Н.В., Ежов И.В., Давыдов Д.И., Меркушев А.Г. Анализ структуры и механических свойств сплава CoCrMo, полученного методом 3D печати // ФММ. 2019. Т. 120. С. 1271–1278.
Maskery I., Aboulkhair N.T., Aremu A.O., Tuck C.J., Ashcroft I.A., Wildman R.D., Hague R.J.M. A mechanical property evaluation of graded density Al–Si10–Mg lattice structures manufactured by selective laser melting // Mater. Sci. Eng. A. 2016. V. 670. P. 264–274.
Патент № 272/2728450. Способ получения деталей из алюминиевых сплавов методом селективного лазерного сплавления.
Abramoff M.D., Magalhaes P.J., Ram S.J. Image Processing with ImageJ // Biophotonics International. 2004. V. 11. № 7. P. 36–42.
Петрова А.Н., Бродова И.Г., Разоренов С.В. Особенности разрушения субмикрокристаллического Al–Mg–Mn-сплава в условиях ударного сжатия // Письма в ЖТФ. 2017. Т. 43. № 10. С. 34–41.
Зельдович В.И., Хомская И.В., Фролова Н.Ю, Хейфец А.Э., Абдуллина Д.Н., Петухов Е.А., Смирнов Е.Б., Шорохов Е.В., Кленов А.И., Пильщиков А.А. Структура и механические свойства аустенитной нержавеющей стали, полученной методом селективного лазерного сплавления // ФММ. 2021. Т. 122. № 5. С. 527–534.
Дополнительные материалы отсутствуют.
Инструменты
Физика металлов и металловедение