Физика металлов и металловедение, 2021, T. 122, № 12, стр. 1302-1308
Особенности формирования поверхностных слоев нержавеющей стали и титанового сплава имплантацией ионов N+
В. Л. Воробьев a, *, П. В. Быков a, А. А. Колотов a, Ф. З. Гильмутдинов a, И. К. Аверкиев a, В. Я. Баянкин a
a Удмуртский федеральный исследовательский центр УрО РАН
426067 Ижевск, ул. им. Т. Барамзиной, 34, Россия
* E-mail: vasily_l.84@mail.ru
Поступила в редакцию 28.05.2021
После доработки 13.08.2021
Принята к публикации 18.08.2021
Аннотация
Исследовано влияние имплантации ионов N+ на морфологию поверхности, накопление азота, формирование химических соединений и структурно-фазовое состояние поверхностных слоев нержавеющей стали 03Х17Н12М2Т и титанового сплава ВТ6. Облучение ионами N+ приводит к накоплению азота в нержавеющей стали до 17 ат. %, формированию химических соединений CrN, Cr2N, MoN, TiN и Fe4N в виде кластеров небольших размеров и кратерообразной морфологии поверхности. В случае титанового сплава накопление азота осуществляется до 32 ат. % и сопровождается образованием нитридов титана, в частности, TiN в виде фазовых включений по всей поверхности. Показано, что формирование морфологии поверхности нержавеющей стали определяется процессами распыления, а титанового сплава – образованием множества включений из нитридов титана.
ВВЕДЕНИЕ
Формирование поверхностных слоев металлических материалов с улучшенными механическими и эксплуатационными свойствами посредством внедрения в них ускоренных ионов относится к одному из перспективных направлений современной науки и техники [1–4]. Несмотря на исследования в этом направлении, до сих пор остается невыясненным влияние компонентов металлических сплавов на формирование морфологии поверхности, элементного и структурно-фазового состава поверхностных слоев в результате ионного облучения. Поэтому целью данной работы является исследование морфологии поверхности, накопления азота, формирования химических соединений и структурно-фазового состояния поверхностных слоев нержавеющей стали 03Х17Н12М2Т и титанового сплава ВТ6 при имплантации ионов N+. Выбор данных металлических материалов обусловлен разной химической активностью их компонентов к азоту. Химическая активность компонентов возрастает от железа к титану. Кроме того, данные сплавы находят широкое применение в качестве конструкционных материалов в химической промышленности, авиа- и судостроении. Сталь 03Х17Н12М2Т является незакаливаемой, поэтому азотирование такого типа сталей является одним из способов повышения твердости, износостойкости и коррозионной стойкости [5].
МАТЕРИАЛЫ И МЕТОДИКА ИССЛЕДОВАНИЯ
Образцы нержавеющей стали 03Х17Н12М2Т и титанового сплава ВТ6 представляли собой пластины длиной 30 мм, сечением 8 × 2 мм2, вырезанные электроискровой резкой из листа в состоянии поставки. Состав образцов в исходном состоянии: нержавеющая сталь – Fe – основа, C – 0.03%, Cr – 17%, Ni – 12%, Mo – 2%, Ti – 0.6%; титановый сплав ВТ6 — Ti – основа, Al – 6%, V – 4%. Образцы подвергали механической шлифовке, полировке и очистке в органических растворителях. После этого осуществляли их рекристаллизационный отжиг в вакууме ~10–4 Па (безмасленная атмосфера) при температуре 750°С для нержавеющей стали, 800°С для титанового сплава, время выдержки 30 мин. После отжига производили финишную полировку поверхности на войлоке с использованием полирующих паст. Ее цель – очистка от адсорбированных примесей, осаждаемых на поверхность из остаточной атмосферы вакуума в процессе отжига.
Имплантацию ионов N+ проводили с использованием источника на основе импульсной вакуумной дуги в импульсно-периодическом режиме (f = 100 Гц, t = 1 мс) при энергии ионов 30 кэВ, дозе облучения 1018 ион/см2 и средней плотности тока ионного пучка 100 мкА/см2. Вакуум в камере имплантера в процессе облучения составлял ~10–2 Па. Температура образцов контролировалась с помощью термопары и не превышала 300°С.
Исследования морфологии поверхности и элементный анализ проводили на сканирующем электронном микроскопе Termo Fisher Scientific Quattro S, оснащенном системой энергодисперсионного микроанализа на основе спектрометра EDAX “Octane Elect Plus EDS System”. Съемки проводили при ускоряющем напряжении 20 кВ и токе пучка 64 пА. Глубина анализа – 2 мкм.
Исследования состава и химического состояния элементов на поверхности образцов выполнены методом рентгеновской фотоэлектронной спектроскопии (РФЭС) на спектрометрах SPECS и ЭС-2401 с Mg Kα-возбуждением спектра фотоэлектронов (Е = 1253.6 эВ). Разрешение энергетической шкалы спектрометра 0.1 эВ. Относительная погрешность определения концентрации элементов 3 ат. %. Послойный РФЭС-анализ проведен с помощью распыления поверхности ионами аргона со скоростью травления ~1 нм/мин. Разложение спектра Cr 2p3/2 проводили с использованием параметров FWHM (≈1.8 эВ), функции Гаусс–Лоренц и асимметрии спектра, полученных для спектра Cr 2p3/2 с поверхности исходного образца. Для разложения спектра N 1s использовали параметры FWHM (≈1–1.2 эВ) и симметричную функцию Гаусс–Лоренц для спектра N 1s с поверхности эталонного нитрида титана TiN. Положения максимумов линий N 1s и Ti 2p3/2 в TiN соответствуют значениям энергий 397.2 и 455 эВ соответственно.
Рентгеновские дифрактограммы снимали в CoKα-излучении на дифрактометре MINIFLEX-600. Рентгенофазовый анализ проводили в пакете программ, предложенном авторами [6].
РЕЗУЛЬТАТЫ И ОБСУЖДЕНИЕ
Растровое электронно-микроскопическое изображение поверхности образца нержавеющей стали в исходном состоянии и после имплантации ионов N+ представлено на рис. 1. Исходная поверхность представляет собой типичный пример металлической поверхности после шлифовки и полировки. Обращает на себя внимание наличие темных точек, распределенных по поверхности образца. Энергодисперсионный анализ этих участков показывает, что они состоят из титана и углерода. По всей видимости, эти частицы представляют собой карбиды титана. Известно, что в хромоникелевые стали целенаправленно вводится титан для связывания углерода в карбиды титана, с целью уменьшения склонности стали к межкристаллитной коррозии [5]. После имплантации ионов N+ микрорельеф поверхности становится более развитым (рис. 1б). Более выраженными становятся микротрещины и различные особенности микрорельефа. Кроме того, на облученной поверхности имеются небольшие частички с более выраженными границами раздела. Следует отметить, что это не частички, сформировавшиеся в процессе ионной имплантации, а те, что имелись на исходной поверхности (рис. 1а). Это следует из того, что они состоят из титана и углерода, но из-за имплантации добавляется азот, а морфология их поверхности имеет кратерообразный характер (рис. 1б – изображение с меньшим масштабом). В принципе, по всей поверхности в большей или меньшей степени проявляются подобные кратеры (рис. 1б). Предполагается, что это обусловлено распылением поверхности в ходе ионного облучения. Одной из особенностей этого процесса является преимущественное распыление атомов вдоль плотноупакованных направлений [7].
Рис. 1.
РЭМ-изображение поверхности нержавеющая сталь в исходном состоянии (а) и после имплантации ионов N+ (б).
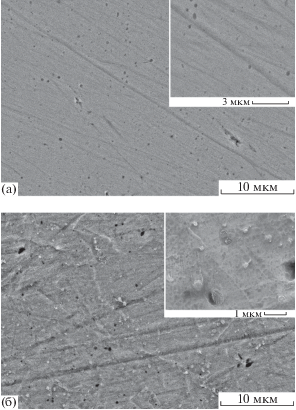
Энергодисперсионный анализ показывает, что элементный состав нержавеющей стали в исходном состоянии представлен железом 67 ат. %, хромом 19 ат. %, никелем 10 ат. % и с концентрацией менее 1 ат. % титаном и молибденом (табл. 1). После имплантации ионов N+ элементный состав дополняется азотом 17 ат. %. Проникновение азота в поверхностные слои происходит непосредственно при ионной имплантации.
Таблица 1.
Элементный состав нержавеющей стали
Эле-мент | В исходном состоянии | После имплантации ионов N+ | ||
---|---|---|---|---|
вес. % | ат. % | вес. % | ат. % | |
Fe | 68 | 67 | 60 | 57 |
Cr | 18 | 19 | 17 | 16 |
Ni | 11 | 10 | 11 | 9 |
Ti | менее 1 | менее 1 | менее 1 | менее 1 |
Mo | менее 2 | менее 1 | менее 2 | менее 1 |
N | – | – | 5 | 17 |
Исследования, проведенные методом РФЭС, позволили выявить элементный состав тонких поверхностных слоев глубиной ~40 нм (рис. 2). Исходная поверхность характеризуется адсорбированным слоем глубиной ~5 нм, после которого концентрация железа, хрома и никеля возрастает до значений 60, 17 и 14 ат. % соответственно и с глубиной не изменяется. Концентрация молибдена и титана не превышает 2 ат. %. После имплантации ионов N+ наблюдаются изменения в распределении элементов нержавеющей стали. Добавляется профиль распределения азота, уменьшается приповерхностная концентрация железа, а вблизи поверхности сегрегирует никель (рис. 2б). Концентрация как титана, так и молибдена остается неизменной и не превышает 2 ат. %.
Рис. 2.
Профили распределения элементов нержавеющей стали в исходном состоянии (а) и после имплантации ионов N+ (б).
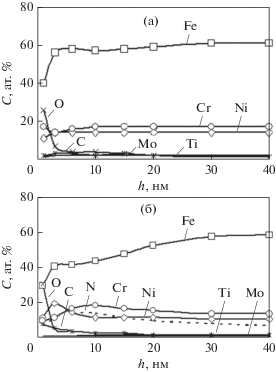
Сравнительный анализ наиболее информативных РФЭ спектров компонентов нержавеющей стали до (спектры 1) и после облучения (спектры 2) показывает, что фактически для всех, за исключением Ni 2p3/2, после облучения наблюдается сдвиг положений их максимумов в сторону больших энергий связи и уширение (увеличение параметра FWHM) (рис. 3). Наиболее явно это проявляется для спектров Ti 2p, Mo 3d и в меньшей степени для Cr 2p3/2 и Fe 2p3/2. Химический сдвиг спектра Fe 2p3/2 составляет примерно 0.1 эВ, что соответствует экспериментальной точности определения положения пиков, но наблюдается уширение спектра (рис. 3). РФЭ-спектры Ni 2p3/2 как для исходной поверхности, так и после облучения повторяют друг друга (рис. 3). Это свидетельствует о том, что химическое состояние атомов никеля после имплантации ионов N+ не изменяется. Положение максимума спектров Ni 2p3/2 приходится на 853 эВ и соответствует металлическому состоянию никеля в узлах кристаллической решетки твердого раствора [8]. Наблюдаемый химический сдвиг спектров остальных элементов и их уширение свидетельствует об образовании химических соединений. Анализируя как литературные данные [8–12], так и распределения элементов (рис. 2) можно сделать предположение о формировании химических соединений с азотом. Например, возможно образование нитридов CrN [9], Cr2N [10], MoN [11], TiN и Fe4N [12]. По всей видимости, ионы азота, внедряясь в приповерхностные слои, вступают во взаимодействие с компонентами сплава с образованием химических соединений, что приводит к сегрегации никеля вблизи поверхности.
Рис. 3.
РФЭ-спектры Fe 2p3/3, Cr 2p3/2, Ni 2p3/2, Ti 2p и Mo 3d, полученные на поверхности нержавеющей стали с глубины ~10 нм, исходного образца (1) и после облучения ионами N+ (2).
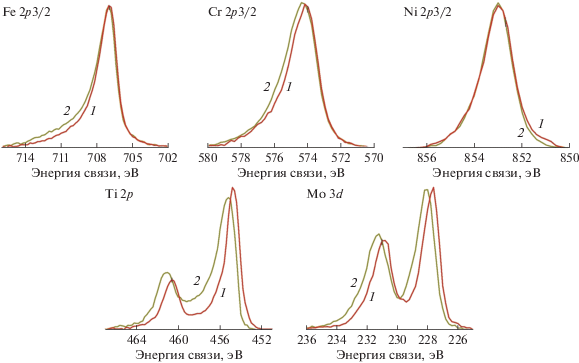
Далее более подробно был проанализирован спектр Cr 2p3/2 ввиду того, что хром является одним из основных компонентов сплава и обладает большей химической активностью к азоту, чем железо и никель. Проведенный анализ позволяет предположить, что хром находится в основном либо в металлическом состоянии в узлах кристаллической решетки твердого раствора Cr0 (Есв = = 574 эВ), либо в виде нитридов Cr2N (Есв = 574.4 эВ) и CrN (Есв = 575.6 эВ) (рис. 4а). Присутствует также соединения со связями Cr–О (Есв = 576.8 эВ), но их концентрация не превышает 1–2 ат. % (рис. 4а).
Рис. 4.
РФЭ-спектры Cr 2p3/2 (а) и N 1s (б) с поверхности нержавеющей стали после имплантации ионов N+.
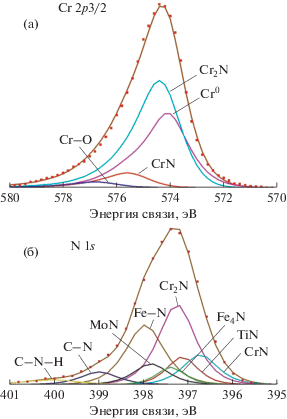
Более детально также был разобран спектр N 1s (рис. 4б). Он является многокомпонентным, поскольку многокомпонентной является сама сталь и, как было показано выше, каждый компонент стали, кроме Ni, взаимодействует с азотом. Для разложения спектра N 1s использовали параметры спектра N 1s от эталонного нитрида титана TiN. Положения максимума линии N 1s в TiN составляет 397.2 эВ, что позволяет зафиксировать положение составляющей для TiN на N 1s-спектре исследуемой стали. Кроме этого, интенсивность составляющих от TiN и MoN на спектре N 1s задавали с учетом концентрации молибдена и титана в сплаве. Поскольку их концентрации не превышают 1–2 ат. %, а соединения TiN и MoN имеют близкие соотношения компонентов, то интенсивности линий для TiN и MoN должны соответствовать концентрации азота 1–2 ат. %. Таким образом, задавали их интенсивность. Положения составляющих для Cr2N, CrN, MoN и Fe4N были выбраны из литературных источников [8‒12]. Возникали сомнения в интерпретации составляющей Fe–N, без которой результирующий спектр N 1s не удавалось описать. Однако сравнение со спектром N 1s для армко-железа, облученного ионами N+, позволило выявить, что данное состояние соответствует связи железа с азотом – Fe–N [13]. Возможно, это вклад от атомов азота из междоузельного пространства (октаэдрических пор) ГЦК кристаллической структуры аустенита исследуемой стали – твердый раствор внедрения.
Таким образом, данные РФЭС дают основание позволяют предположить, что имплантация ионов N+ в нержавеющую сталь приводит к накоплению азота до 17 ат. %, формированию химических соединений азота с компонентами сплава, за исключением никеля и, возможно, образованию твердого раствора внедрения.
Рентгеноструктурный анализ облученного образца не выявляет линий большого числа составляющих, регистрируемых методом спектроскопии (рис. 5). Дифрактограммы как исходного, так и облученного образца представлены альфа-линиями аустенита. Вероятнее всего, формируемые химические соединения находятся в микроструктуре сплава в виде кластеров или наноразмерных частиц, размеры которых недостаточны для формирования областей когерентного рассеяния рентгеновских лучей. Тем не менее, сравнивая положения отдельных пиков дифрактограмм, можно видеть, что, например, положение линии (111) после имплантации ионов N+ оказывается сдвинутой в сторону больших углов (рис. 6). Это свидетельствует об увеличении параметра кристаллической решетки аустенита. Предполагается, что это связано с формированием указанных выше химических соединений, а также твердого раствора внедрения азота в решетке аустенита.
Рис. 6.
Фрагмент дифрактограмм нержавеющей стали в исходном состоянии (1) и после облучения ионами N+ (2).
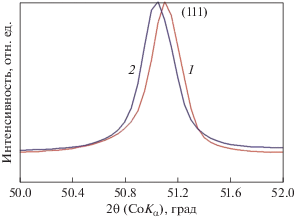
Далее аналогичным образом был проанализирован титановый сплав ВТ6. Морфология поверхности титанового сплава в исходном состоянии подобно нержавеющей стали не имеет каких-то особенностей и представляет собой следы предшествующей механической обработки (рис. 7а). После имплантации ионов N+ поверхность образца становится более развитой (рис. 7б). Однако это связано не с особенностями микрорельефа из-за распыления, как в случае нержавеющей стали, а с формированием множества наноразмерных включений по всей поверхности. Это особенно отчетливо проявляется на изображениях меньшего масштаба. Как будет показано ниже, данные включения представляют собой нитриды титана, в частности, нитрид титана TiN. Это позволяет предположить, что формирование морфологии поверхности титанового сплава при имплантации ионов N+ определяется не столько процессами распыления, сколько образованием наноразмерных включений из нитридов титана.
Элементный анализ, проведенный энергодисперсионным способом, выявляет, что в исходном состоянии титановый сплав ВТ6 представлен титаном, алюминием и ванадием – 86, 10 и 4 ат. % соответственно (табл. 2). После облучения ионами N+ добавляется азот, причем существенно, до 32 ат. %.
Таблица 2.
Элементный состав титанового сплава ВТ6
Эле-мент | В исходном состоянии | После имплантации ионов N+ | ||
---|---|---|---|---|
вес. % | ат. % | вес. % | ат. % | |
Ti | 90 | 86 | 73 | 53 |
Al | 6 | 10 | 4 | 5 |
V | 4 | 4 | 9 | 6 |
C | – | – | 3 | 8 |
N | – | – | 11 | 28 |
Значительное накопление азота на поверхности титанового сплава после облучения ионами N+ подтверждается исследованиями методом РФЭС (рис. 8). Накопление азота в тонких поверхностных слоях осуществляется до концентраций более 30 ат. % (рис. 8б), что примерно в 2 раза выше, чем в случае нержавеющей стали. При этом ход распределения титана и азота по глубине образца совпадает. Это свидетельствует о том, что накопление азота и формирование профиля его распределения определяется взаимодействием с атомами титана.
Анализ РФЭ-спектров, в частности, N 1s и Ti 2p подтверждает данное предположение: в основном, весь азот расходуется на образование нитрида титана TiN (рис. 9). Об этом свидетельствует пик с наибольшей интенсивностью на N 1s-спектре с энергией связи 397.2 эВ (рис. 9а). Кроме того, проявляется химическое состояние азота с энергией связи 397.5 эВ, которое, вероятнее всего, также, связано со связями титана с азотом – Ti–N-связями [8] (рис. 9а). Возможно, это соединения с нестехиометрическим соотношением азота и титана. На спектре Ti 2p образование нитридов проявляется в виде химического сдвига на 1 эВ в сторону больших энергий связи максимумов линий спектра (рис. 9б). Например, энергия связи линий Ti 2p3/2 для образца в исходном состоянии составляет 454 эВ, а после облучения 455 эВ.
Рис. 9.
РФЭ-спектр N 1s (а) с поверхности облученного титанового сплава и РФЭ спектры Ti 2p (б) с поверхности исходного титанового сплава (1) и после облучения (2). Спектры получены с глубины ~10 нм.
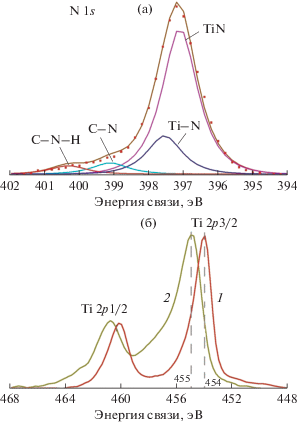
Исследования, проведенные методом РСА, позволяют предположить, что химические соединения азота с титаном на поверхности образца ВТ6 после имплантации ионов N+ выделяются в виде фазовых включений. Об этом свидетельствует слабоинтенсивный пик на дифрактограмме образца после облучения от фазы TiN (рис. 10, обведен красным овалом). Основное же структурное состояние сплава как в исходном состоянии, так и после облучения представляется α-Ti с ГПУ-кристаллической решеткой.
Таким образом, имплантация ионов N+ в титановый сплав ВТ6 приводит к накоплению азота до концентраций ~32 ат. % и образованию на поверхности множества включений, представляющих собой нитриды титана и, в частности, нитрид титана TiN. По всей видимости, азот, внедряясь в структуру сплава, из-за высокой химической активности к титану вступает во взаимодействие с ближайшими атомами титана, и образуются соединения с прочной химической связью. Это сопровождается накоплением азота, перестраиванием атомной структуры сплава и формированием включений со структурами, характерными для нитридов титана. Процесс формирования нитридных включений преобладает над процессами распыления, сопровождающими облучение, и определяет формирование морфологии поверхности.
ВЫВОДЫ
Имплантация ионов N+ в нержавеющую сталь приводит к накоплению азота до 17 ат. %, образованию химических соединений азота с компонентами сплава, за исключением никеля, в виде кластеров или нанормазмерных частиц и формированию кратерообразной морфологии поверхности.
Предполагается, что формирование морфологии поверхности определяют процессы распыления, сопровождающие облучение.
Накопление азота до 32 ат. % в поверхностных слоях титанового сплава ВТ6 при имплантации ионов N+ сопровождается одновременным образованием множества включений на поверхности сплава из нитридов титана, в частности, TiN.
Показано, что формирование морфологии поверхности в этом случае определяется процессами образования нитридов титана в виде включений по всей поверхности.
Работа выполнена в рамках государственного задания Министерства науки и высшего образования РФ ГЗ N 121030100002-0.
Исследования выполняли с использованием оборудования ЦКП “Центр физических и физико-химических методов анализа, исследования свойств и характеристик поверхности, наноструктур, материалов и изделий” УдмФИЦ УрО РАН.
Список литературы
Козлов Д.А., Крит Б.А., Столяров В.В., Овчинников В.В. Ионно-лучевое модифицирование трибологических свойств хромистой стали // ФизХОМ. 2010. № 1. С. 50–53.
Сунгатулин А.Р., Сергеев В.П., Федорищева М.В., Сергеев О.В. Влияние обработки пучками ионов (Cr + B) поверхностного слоя стали 38ХН3МФА на износостойкость // Изв. Томского политехнического ун-та. 2009. Т. 315. № 2. С. 134–137.
Братушка С.Н., Маликов Л.В. Ионно-плазменная модификация титановых сплавов // Вопросы атомной науки и техники. 2011. № 6. С. 126–140.
Овчинников В.В., Макаров Е.В., Гущина Н.В. Образование аустенита в α-сплаве Fe–Mn после холодной пластической деформации в условиях быстрого нагрева пучком ионов Ar+ до 299°С // ФММ. 2019. Т. 120. № 12. С. 1307–1313.
Гуляев А.П. Материаловедение. М.: Металлургия, 1986. 544 с.
Шелехов E.В., Свиридова Т.А. Программы для рентгеновского анализа поликристаллов // Металловедение и термическая обр. металлов. 2000. № 8. С. 16–19.
Бериш Р. Распыление твердых тел ионной бомбардировкой. М.: Мир, 1984. 336 с.
https://srdata.nist.gov/xps/EnergyTypeValSrch.aspx
Yongjing Shi, Siyuan Long, Liang Fang, Fusheng Pan, Huimin Liao Effects of N2 content and thickness on CrNx coatings on Mg alloy by the planar DC reactive magnetron sputtering // Applied Surface Science. 2009. V. 255. P. 6515–6524.
Hongming Dong, Shuai He, Xinzhu Wang, Caizhi Zhang, Deen Sun. Study on conductivity and corrosion resistance of N-doped and Cr/N co-doped DLC films on bipolar plates for PEMFC // Diamond & Related Materials. 2020. V. 110. P. 108156(9).
Zainab N. Jaf, Zhong-Tao Jiang, Hussein A. Miran, Mohammednoor Altarawneh, Jean-Pierre Veder, Manickam Minakshi, Zhi-feng Zhou, H.N. Lim, N.M. Huang, Bogdan Z. Dlugogorski Physico-chemical properties of CrMoN coatings—combined experimental and computational studies // Thin Solid Films. 2020. V. 693. P. 137671(14).
Yanfeng Jiang, Xiaowei Zhang, Aminul Al Mehedi, Meiyin Yang and Jian-Ping Wang A method to evaluate α"-Fe16N2 volume ratio in FeN bulk material by XPS // Mater. Res. Express. 2015. V. 2. Article 116103. P. 1–8.
Решетников С.М., Бакиева О.Р., Борисова Е.М., Воробьев В.Л., Гильмутдинов Ф.З., Картапова Т.С., Баянкин В.Я. Влияние имплантации ионов азота на коррозионно-электрохимические и другие свойства армко-железа. Ч. II. Коррозионно-электрохимическое поведение образцов армко-железа, подвергнутых имплантации ионами азота // Коррозия: материалы, защита. 2018. № 4. С. 1–8.
Дополнительные материалы отсутствуют.
Инструменты
Физика металлов и металловедение