Физика металлов и металловедение, 2021, T. 122, № 12, стр. 1332-1338
Влияние газовой среды на механические, трибологические и антикоррозионные свойства покрытий Cr–Ni–Al–C–N, полученных методом импульсного катодно-дугового испарения
Ф. В. Кирюханцев-Корнеев a, *, А. Д. Сытченко a, А. Н. Шевейко a, В. А. Горшков b, Е. А. Левашов a
a Национальный исследовательский технологический университет “МИСиС”
119049 Москва, Ленинский пр., 4, Россия
b Институт структурной макрокинетики и проблем материаловедения им. А.Г. Мержанова РАН
142432 Московская обл., Черноголовка, ул. Академика Осипьяна, 8, Россия
* E-mail: kiruhancev-korneev@yandex.ru
Поступила в редакцию 13.04.2021
После доработки 04.08.2021
Принята к публикации 05.08.2021
Аннотация
Покрытия Cr–Ni–Al–C–N наносили методом импульсного катодно-дугового испарения (PCAE) в среде аргона, азота и этилена с использованием катода Cr3C2–NiAl, полученного с помощью самораспространяющегося высокотемпературного синтеза. Структура покрытий исследована методами сканирующей электронной микроскопии, рентгенофазового анализа, оптической эмиссионной спектроскопии тлеющего разряда и рамановской спектроскопии. Механические и трибологические свойства были исследованы методами наноиндентирования и трибологического тестирования по схеме “pin-on-disk”. Антикоррозионные свойства оценивали методом вольтамперометрии в среде 1 N H2SO4. Нереакционное покрытие, осажденное в инертной среде Ar, содержало ГЦК-фазу Cr3C2 с размером кристаллитов <20 нм. Осаждение в реакционных средах C2H4 и N2 привело к аморфизации покрытий. Образцы, осажденные в аргоне и азоте, показали высокую твердость 24–25 ГПа. Осаждение покрытий в C2H4 привело к снижению твердости на 40%. Однако углеродсодержащий образец характеризовался относительно низким коэффициентом трения на уровне 0.28, а также лучшей износо- и коррозионной стойкостью, благодаря положительному влиянию фазы DLC.
ВВЕДЕНИЕ
Для нанесения защитных покрытий различного назначения (износо-, жаро- и коррозионностойких) в настоящее время активно применяют высокоточные технологии, такие как высокомощное импульсное магнетронное напыление [1], электроискровое легирование (electospark alloying, ESA) и импульсное катодно-дуговое испарение (pulsed cathodic arc evaporation, PCAE) [2] с использованием керамических или композитных электродных материалов, изготовленных методом самораспространяющегося высокотемпературного синтеза. Применение импульсного питания позволяет предотвратить интенсивное разрушение керамики вследствие термоудара [2–4]. Нанесение тонкого поверхностного слоя позволяет модифицировать широкий спектр подложек и придать им повышенные твердость, износостойкость и коррозионную стойкость, характерные для объемных керамических, металлокерамических и композитных материалов [5–7]. К основным преимуществам данных технологий следует отнести высокую производительность и высокую адгезионную прочность получаемых покрытий [8]. Высокая прочность сцепления покрытия с подложкой обусловлена либо протеканием металлургических реакций на межфазной границе (ESA) [9], либо бомбардировкой подложки высокоэнергетическими ионами и образованием протяженных псевдодиффузионных слоев между подложкой и растущим покрытием (PCAE) [10]. Ключевыми параметрами процесса осаждения для управления свойствами покрытий являются частота и длительность импульсов, средняя и пиковая мощность, энергия разряда и другие электрические характеристики [11, 12]. Дополнительный контроль структуры и свойств достигается за счет использования различных газовых сред при нанесении покрытий [13, 14].
Одним из перспективных материалов для нанесения защитных покрытий является карбид хрома. Широко известны покрытия в системе Cr3C2–NiCr [15–17], также разрабатываются новые составы с улучшенными характеристиками: Cr3C2–ZrO2 [18], Cr3C2–NiCr–CeO2 [19], Cr3C2–NiMo [20], Cr3C2–NiCrCoMo [21]. Ранее нами были исследованы покрытия на основе системы Cr3C2–NiAl, осажденные методом ESA в токе аргона или воздуха при нормальных условиях [22]. Проведены работы по осаждению покрытий методами магнетронного напыления и электроискрового легирования в вакууме [23]. Было показано, что покрытия, полученные по оптимальным режимам, обладают высокой износостойкостью и низким коэффициентом трения на уровне 0.18. Образцы, нанесенные ионно-плазменными методами при распылении катодов Cr3C2–NiAl в аргоне, характеризуются высокой плотностью и сплошностью [22]. Известно, что улучшить технологические характеристики покрытий можно путем введения дополнительных компонентов посредством осаждения в реакционной атмосфере. Отметим, что покрытия Сr–Ni–Al–C–N, полученные методом PCAE в реакционной среде, ранее изучены не были.
Настоящая работа посвящена получению покрытий методом PCAE при испарении катода Cr3C2–NiAl в различных газовых средах, таких как аргон, азот и этилен, а также исследованию влияния рабочей среды на свойства получаемых покрытий.
МАТЕРИАЛЫ И МЕТОДЫ
В данной работе для испарения использовали катод Сr3C2–NiAl, полученный методом самораспространяющегося высокотемпературного синтеза (СВС). По сравнению с традиционными методами порошковой металлургии СВС обладает лучшими технико-экономическими показателями, такими как высокая производительность, относительная дешевизна, достигаемая за счет использования более дешевого сырья, и чистота получаемых продуктов. В качестве подложек использовали диски из стали 5140 (40Х, состав, вес. %: Fe – 97.0, C – 0.36–0.44, Si – 0.17–0.37, Mn – 0.5–0.8, Cr – 0.8–1.1, Cu – 0.3) размером ∅30 × 5 мм. Покрытия синтезировали на установке на базе откачивающей системы УВМ‑2М, в камере которой установлен узел PCAE, оснащенный катодом из наносимого материала, анодами в форме металлического кольца и спирали, а также электродом поджига (рис. 1).
Катод помещают в специальный держатель, изолированный от электрических пробоев с помощью тефлоновой трубки и кварцевой колбы. Поджиг осуществляется через металлическую проволоку. Анодное напряжение подается на водоохлаждаемые спираль и диск, изготовленные из меди. Подложка закрепляется на удерживающем кольце и располагается в пространстве между спиралью и диском на расстоянии 20 мм от катода. Энергия дугового разряда накапливается в батарее конденсаторов емкостью 2000 мкФ. Для реализации этой энергии в дуговом разряде используется высоковольтный инициирующий импульс напряжения, подводимый вблизи катода. Напряжение и частота поджига составляли 15 кВ и 10 Гц соответственно. Напряжение, подаваемое на анод, находилось вблизи значения 110 В, ток при этом достигал 1 кА. Давление рабочих газов, Ar (99.9995%), N2 (99.999%) и C2H4 (99.95%) составляло 0.4 Па, остаточное давление 4 × 10–3 Па. Подложки подвергали ультразвуковой очистке в изопропиловом спирте. Затем после помещения в вакуумную камеру, на подложку в первые 2–3 мин подавали анодное напряжение для нагрева за счет электронной бомбардировки. Далее в течение 5 мин проводили формирование псевдодиффузионного слоя при плавном понижении от –2 до 0 кВ отрицательного напряжения смещения, подаваемого на подложку. Перед осаждением покрытий в реакционных средах проводили нанесение подслоя при испарении катода в аргоне в течение 1–2 мин.
Для структурного анализа использовали сканирующий электронный микроскоп Hitachi S-3400N c системой энергодисперсионного анализа NORAN System 7. Профили распределения элементов получали с помощью оптического эмиссионного спектрометра тлеющего разряда Profiler-2 HORIBA-JY согласно методике [24]. Рентгенофазовый анализ (РФА) проводили на дифрактометре D8 ADVANCE компании Bruker с использованием CuKα-излучения. Расчет размера кристаллитов проводили с использованием формулы Дебая–Шеррера. Исследования методом Рамановской спектроскопии проводили на приборе NTEGRA NT-MDT с использованием красного лазера (длина волны 633 нм). Механические характеристики, такие как твердость (Н), модуль упругости (Е), упругое восстановление (W), исследовали на нанотвердомере Nanohardness Tester (CSM Instruments) при нагрузке 4 мН. Расчет параметров проводили по методу Оливера–Фарра. Значения твердости рассчитывали как отношение максимальной нагрузки к площади проекции восстановленного отпечатка, модуль упругости определяли исходя из площади проекции отпечатка, контактной жесткости, рассчитываемой по наклону верхней трети кривой разгружения, коэффициента Пуассона и параметров индентора. Трибологические испытания проводили на автоматизированной машине трения Tribometer (CSM Instruments) по схеме “pin-on-disk” с помощью контртела из Al2O3 при линейной скорости 10 см/с и нагрузке 1 Н. Фрактографические исследования канавок износа с последующим вычислением величины приведенного износа проводили на оптическом профилометре Veeco WYKO NT1100. Для экспериментов по определению коррозионной стойкости использовали трехэлектродную ячейку с потенциостатом “Voltalab PST050”. Испытания проводили в 1 N H2SO4 при температуре 25°C.
РЕЗУЛЬТАТЫ И ОБСУЖДЕНИЕ
Состав покрытий, определенный методом оптической эмиссионной спектроскопии тлеющего разряда (ОЭСТР), может быть записан следующим образом: Cr47.0Ni5.2Al1.3C46.5 (покрытие 1), Cr37.8Ni7.8Al1.4C10.3N42.7 (покрытие 2), и Cr20.8Ni6.0Al3.0C70.2 (покрытие 3). На поверхности всех покрытий наблюдаются выраженные включения конденсированной капельной фазы, появившейся в результате плавления и испарения катодного материала (рис. 2а). Данный поверхностный дефект является особенностью катодно-дуговых покрытий [25]. Для всех покрытий концентрация капель преимущественно сферической формы находилась в пределах 13–15% от площади покрытий.
Рис. 2.
Типичные СЭМ-изображения поверхности (а) и поперечного сечения (б) покрытия 3, рентгенограммы (в) и спектры комбинационного рассеяния (г) покрытий 1–3.
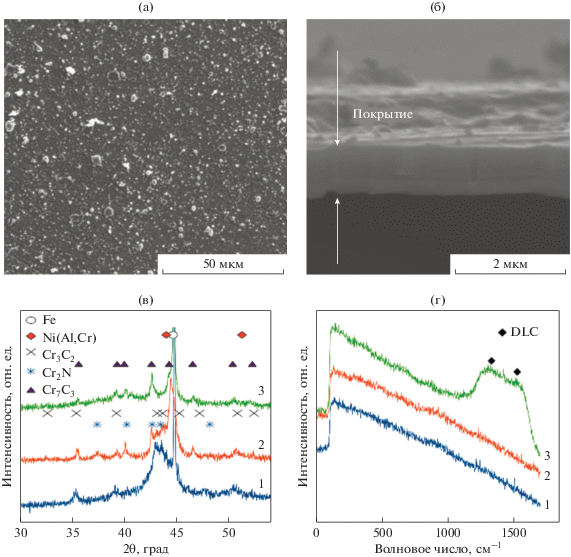
Отметим, что толщина покрытий 1, 2 и 3, определенная из профилей ОЭСТР, составила 1.0, 0.6 и 2.3 мкм соответственно.
Согласно СЭМ-изображениям поперечных изломов, все покрытия показали схожую плотную однородную структуру. На поверхности покрытий заметна капельная фаза; дефектов внутри покрытий не наблюдали. Для реакционных покрытий четко прослеживается подслой, осажденный в среде Ar (рис. 2б).
Согласно данным РФА, на дифрактограммах всех покрытий были выявлены пики подложки Fe (JCPDS 06-0696) и твердого раствора Ni(Al,Cr) (JCPDS 16-17228) (рис. 2в). Для покрытий, полученных в Ar и N2, были найдены пики, связанные с отражениями от плоскостей (201), (211) и (121) ГЦК-фазы на основе Cr3C2 (JCPDS 89–2723). Размер кристаллитов Cr3C2 не превышал 25 нм для образцов 1 и 2. Осаждение в реакционной среде N2 дополнительно привело к образованию фазы Сr2N (JCPDS 35-0803). При переходе к распылению в среде C2H4 выявлялись пики от фазы Cr7C3 (JCPDS 071–3789), при этом размер кристаллитов составлял 30–50 нм. В диапазоне 2Θ = = 35°–50° наблюдали уширенный пик, который, вероятно, связан с образованием аморфного углерода.
Спектры комбинационного рассеяния покрытий Cr–Ni–Al–C–N, полученных в атмосфере Ar, N2 и C2H4, показаны на рис. 2г. Для покрытий, нанесенных в Ar и N2, не было выявлено характерных пиков. В то время как на спектрах комбинационного рассеяния покрытия, полученного в среде C2H4, наблюдаются пики 1330 и 1520 см–1, форма и положение которых аналогичны фазе алмазоподобного углерода DLC [26].
Исследование механических характеристик показало, что покрытие, осажденное в аргоне, обладает твердостью Н = 24 ± 5 ГПа, максимальным модулем упругости Е = 305 ± 37 ГПа и упругим восстановлением W = 59% (табл. 1).
Таблица 1.
Механические свойства покрытий и подложки
№ | Атмосфера | H, ГПа | E, ГПа | W, % | H/E | H3/E2, ГПа |
---|---|---|---|---|---|---|
1 | Ar | 24 ± 5 | 305 ± 37 | 59 | 0.079 | 0.149 |
2 | N2 | 25 ± 5 | 281 ± 24 | 70 | 0.089 | 0.198 |
3 | C2H4 | 15 ± 3 | 185 ± 36 | 66 | 0.081 | 0.099 |
Подложка | – | 4 | 223 | 12 | 0.018 | 0.001 |
При осаждении покрытий в среде N2 значение твердости практически не изменилось и составило 25 ± 5 ГПа, однако наблюдалось снижение модуля упругости на 8%. При этом образец 2 обладал максимальным упругим восстановлением W = 70%. Похожие результаты, такие как незначительный рост твердости и снижение модуля упругости при увеличении концентрации азота, были получены для катодно-дуговых покрытий Al–Cr–B–N в работе [27]. Осаждение в среде этилена привело к снижению твердости на ~40% и модуля упругости на ~35–40%. В то же время упругое восстановление покрытия 3 составило 66%, что на 12% выше значений, полученных для нереакционного покрытия. Снижение твердости при осаждении покрытий в углеродсодержащей среде может быть связано с образованием фазы графита. Подобное явление наблюдали в работах [28, 29]. На основании результатов наноиндентирования были также определены характеристики H/E и H3/E2 (табл. 2), которые могут служить показателями износостойкости и характера разрушения покрытий [30].
Таблица 2.
Трибологические характеристики и коррозионная стойкость покрытий
№ | f | VW × 10–5, мм3 Н–1 м–1 | φ, мВ | icor, мкА/см2 |
---|---|---|---|---|
1 | 0.71 | 19.9 | –198 | 88 |
2 | 0.97 | 4.8 | –203 | 189 |
3 | 0.28 | 1.5 | –210 | 35 |
График зависимости коэффициента трения f от дистанции и средние значения f покрытий 1–3 показаны на рис. 3 и в табл. 2. Характерным для покрытия 1 является наличие этапа приработки на пробеге 0–14 м, после которого f плавно возрастает до значений 0.70–0.76 и сохраняется постоянным до конца испытания. Коэффициент трения азотсодержащего покрытия за 40 м испытания возрос до ~1 и сохранился постоянным на оставшейся дистанции испытания.
В случае покрытия 3 наблюдали скачок f до 0.44 на пробеге 0–25 м, связанный с этапом приработки покрытия. Углеродсодержащее покрытие показало низкий и стабильный коэффициент трения на уровне ~0.28. Снижение коэффициента трения при осаждении в этилене может быть связано с образованием графита на поверхности покрытия, что подтверждается данными спектроскопии комбинационного рассеяния (рис. 2г). В работах [31, 32] показано, что графит в зоне трибоконтакта на изношенной поверхности способствует снижению коэффициента трения за счет смазывающего эффекта.
Согласно 2D- и 3D-профилям, глубина дорожки износа (hw) покрытия 1, полученного в Ar, составила 5 мкм при толщине 1 мкм, что говорит о полном износе образца 1. Для образца 2 hw = 1.5 мкм, что превышает толщину покрытия и свидетельствует о его износе. Покрытие, полученное в C2H4, характеризовалось hw = 0.3 мкм при толщине 2.3 мкм. Можно сделать вывод, что образец 3 не износился до подложки.
Отметим, что скорость износа покрытий (Vw), определенная по 3D-профилям дорожек трения (рис. 4), снижалась в ~13 и ~3 раза при переходе от Ar и N2 к распылению в среде C2H4 (табл. 2).
Поляризационные кривые покрытий 1–3 представлены на рис. 5.
Потенциал свободной коррозии (φ) и плотность тока коррозии (icor), рассчитанная с использованием уравнения Тафеля, сведены в табл. 2. Близкие значения потенциалов коррозии всех испытанных образцов указывают на то, что плотности тока покрытий в основном определяются растворением материала подложки (железа). Для нереакционного покрытия значение плотности тока коррозии составило 88 мкА/см2. При переходе к реакционному распылению в среде N2 для покрытия 2 плотность тока коррозии возросла в ~2 раза и составила 189 мкА/см2. Минимальной плотностью тока коррозии 35 мкА/см2 характеризовался образец, осажденный в среде C2H4. Таким образом, покрытие, полученное в С2Н4, показало стойкость к коррозионному воздействию в 2.5 и 5.4 раза выше, чем образцы, осажденные в среде Ar и N2.
ЗАКЛЮЧЕНИЕ
Методом импульсного катодно-дугового испарения электрода Сr3C2–NiAl были получены покрытия в атмосфере Ar, N2 и C2H4. Покрытие, осажденное в Ar, содержало фазы Cr3C2 и Ni(Al,Cr). Переход к распылению в реакционной среде N2 способствовал образованию в покрытии дополнительной фазы Cr2N. Осаждение в C2H4 привело к изменению доминирующей фазы Cr3C2 на Cr7C3; тогда как избыточный углерод выделялся в виде фазы DLC. Образцы, полученные в Ar и N2, показали близкие значения твердости 24 и 25 ГПа соответственно. При осаждении в углеродсодержащей среде твердость покрытия снизилась на 40% в результате образования относительно мягкой фазы графита. Однако образование свободного углерода привело к снижению коэффициента трения и росту износостойкости покрытия по сравнению с образцами, осажденными в аргоне и азоте. Покрытие, осажденное в C2H4, характеризовалось низкой плотностью тока коррозии на уровне 35 мкА/см2, что в 2.5 и 5.4 раза меньше данных, полученных для образцов, осажденных в Ar и N2, соответственно.
Таким образом, покрытия, осажденные в Ar и N2, показали лучшие механические характеристики. В то же время углеродсодержащий образец обладал низким коэффициентом трения, высокой износо- и коррозионной стойкостью.
Работа выполнена при финансовой поддержке Российского научного фонда (договор № 20-79-10104) в части электрохимических исследований.
Список литературы
Kiryukhantsev-Korneev Ph.V., Sheveyko A.N., Vorotilo S.A., Levashov E.A. Wear-resistant Ti–Al–Ni–C–N coatings produced by magnetron sputtering of SHS-targets in the DC and HIPIMS modes // Ceramics International. 2019. V. 46(2). P. 1775–1783.
Kiryukhantsev-Korneev Ph., Sytchenko A., Sheveyko A., Moskovskikh D., Vorotylo S. Two-Layer Nanocomposite TiC-Based Coatings Produced by a Combination of Pulsed Cathodic Arc Evaporation and Vacuum Electro-Spark Alloying // Materials. 2020. V. 13. № 547.
Zhao X., Chen Z., Wang H., Zhang Z., Shao G., Zhang R., Fan B., Lu H., Xu H., Chen D. The influence of additive and temperature on thermal shock resistance of ZrB2 based composites fabricated by Spark Plasma Sintering // Materials Chemistry and Physics. 2020. V. 240. № 122061.
Antonov M., Hussainova I. Thermophysical properties and thermal shock resistance of chromium carbide based cermets // Proc. Estonian Acad. Sci. Eng. 2006. V. 12. P. 358–367.
Almandoz E., Fernández de Ara J., Martínez de Bujanda J., Fernández Palacio J., José Rodríguez R., Zhang Z., Dong H., Qin Y. García Fuentes G. CrAlON CAE-PVD coatings for oxidation and wear protection of TZM alloys in FAST sintering applications // Mater. Chem. Phys. 2018. V. 208. P. 189–197.
Goncharov V.S., Vasil’ev E.V., Goncharov M.V. Effect of technological parameters of applying yttrium-containing coatings on their structure and properties // Phys. Metals. Metallogr. 2014. V. 115. P. 169–174.
Krause-Rehberg R., Pogrebnyak A.D., Borisyuk V.N., Kaverin M.V., Ponomarev A.G., Bilokur M.A., Oyoshi K., Takeda Y., Beresnev V.M., Sobol’ O.V. Analysis of local regions near interfaces in nanostructured multicomponent (Ti–Zr–Hf–V–Nb)N coatings produced by the cathodic-arc-vapor-deposition from an arc of an evaporating cathode // Phys. Metals Metallogr. 2013. V. 114. P. 672–680.
Kiryukhantsev-Korneev Ph.V., Kuptsov K.A. Impact wear-resistance of Ti–Cr–B–N coatings produced by pulsed CAE of ceramic target // J. Phys.: Conf. Ser. 2019. V. 1238. № 012003.
Shafyei H., Salehi M., Bahrami A. Fabrication, microstructural characterization and mechanical properties evaluation of Ti/TiB/TiB2 composite coatings deposited on Ti6Al4V alloy by electro-spark deposition method // Ceramics International. 2020. V. 46. P. 15276–15284.
Hovsepian P.E., Ehiasarian A.P. Six strategies to produce application tailored nanoscale multilayer structured PVD coatings by conventional and High Power Impulse Magnetron Sputtering (HIPIMS) // Thin Solid Films. 2019. V. 688. № 137409.
Mei H., Ding J.C., Xiao X., Luo Q., Wang R., Zhang Q., Gong W., Wang Q. Influence of pulse frequency on microstructure and mechanical properties of Al–Ti–V–Cu–N coatings deposited by HIPIMS // Surface and Coatings Technology. 2021. V. 405. № 126514.
Ferreira F., Serra R., Oliveira J.C., Cavaleiro A. Effect of peak target power on the properties of Cr thin films sputtered by HiPIMS in deep oscillation magnetron sputtering (DOMS) mode // Surface and Coatings Technology. 2014. V. 258. P. 249–256.
Kiryukhantsev-Korneev Ph.V., Pierson J.F., Kuptsov K.A. and Shtansky D.V., Hard Cr–Al–Si–B–(N) coatings deposited by reactive and non-reactive magnetron sputtering of CrAlSiB target // Appl. Surface Sci. 2014. V. 314. P. 104-111.
Shtansky D.V., Gloushankova N.A., Sheveiko A.N., Kiryukhantsev-Korneev P.V., Bashkova I.A., Mavrin B.N., Ignatov S.G., Filippovich S.Y., Rojas C. Si-doped multifunctional bioactive nanostructured films // Surf. Coat Technol. 2010. V. 205. P. 728–739.
Shi M., Xue Z., Liang H., Yan Z., Liu X., Zhang S. High velocity oxygen fuel sprayed Cr3C2–NiCr coatings against Na2SO4 hot corrosion at different temperatures // Ceramics International. 2020. V. 46. P. 23629–23635.
Zhang Y., Chong K., Liu Q., Bai Y., Zhang Z., Wu D., Zou Y. High-temperature tribological behavior of thermally-treated supersonic plasma sprayed Cr3C2–NiCr coatings // Intern. J. Refractory Metals Hard Mater. 2021. V. 95. № 105456.
Lu H., Shang J., Jia X., Li Y., Li F., Li J., Nie Y. Erosion and corrosion behavior of shrouded plasma sprayed Cr3C2–NiCr coating // Surface and Coatings Technology. 2020. V. 388. № 125534.
Suresh V., Jegan A., Kumar S.L. Microstructure, mechanical and tribological characteristics of plasma and HVOF sprayed Cr3C2–PS.ZrO2 coatings // Mater. Today: Proceedings. 2020. V. 33. P. 1137–1143.
Kumar S., Mudgal D., Singh S., Prakash S. Effect of CeO2 in Cr3C2–NiCr Coating on Superni 600 at High Temperature // Procedia Mater. Sci. 2014. V. 6. P. 939–949.
Zhai W., Pu B., Sun L., Wang Y., Dong H., Gao Q., He L., Gao Y. Influence of molybdenum content and load on the tribological behaviors of in-situ Cr3C2–20 wt % Ni composites // J. Alloys and Compounds. 2020. V. 826. P. 154180.
Du J.-Y., Li Y.-L., Li F.-Y., Ran X.-J., Zhang X.-Y., Qi X.-X. Research on the high temperature oxidation mechanism of Cr3C2–NiCrCoMo coating for surface remanufacturing // J. Materials Research and Technology. 2021. V. 10. P. 565–579.
Kiryukhantsev-Korneev Ph.V., Sytchenko A.D., Gorshkov V.A., Levashov E.A. Mass-transfer kinetics, structure, and tribological properties of coatings deposited on steel in Ar or N2 + O2 by electro-spark alloying using Cr3C2–NiAl electrodes // IOP Conf. Ser.: Mater. Sci. Eng. 2020. V. 848. № 012087.
Kiryukhantsev-Korneev Ph.V., Shvyndina N.V., Sytchenko A.D., Shtansky D.V., Gorshkov V.A., Levashov E.A. Healing effect in coatings deposited by hybrid technology of vacuum electro-spark alloying, pulsed cathodic arc evaporation, and magnetron sputtering using Cr3C2–NiAl electrodes // J. Physics: Conference Series. 2020. V. 1431. № 012027.
Kiryukhantsev-Korneev F.V. Possibilities of glow discharge optical emission spectroscopy in the investigation of coatings // Russian J. Non-Ferrous Metals. 2014. V. 55. P. 494–504.
Martin P.J., Bendavid A. Review of the filtered vacuum arc process and materials deposition // Thin Solid Films. 2001. V. 394. P. 1–14.
Laumer J., Schmidt K., O’Leary S.K. The relationship between the Raman spectral form and the location of the corresponding sample within the overall thin-film carbon genome // Solid State Comm. 2020. V. 322. № 114059.
Warcholinski B., Gilewicz A., Myslinski P., Dobruchowska E., Murzynski D., Kochmanski P., Rokosz K., Raaen S. Effect of nitrogen pressure and substrate bias voltage on the properties of Al–Cr–B–N coatings deposited using cathodic arc evaporation // Tribology International. 2021. V. 154. № 106744.
Кирюханцев-Корнеев Ф.В., Бондарев A.В. Структура и свойства антифрикционных покрытий Cu, Cu–C и DLC // ФММ. 2019. V. 120. P. 764–770.
Хрущев M.M., Марченко E.A., Левин И.С., Авдюхина В.M., Рэйляну M.Д., Образцова E.A., Атаманов M.В. Особенности структуры и трибологическое поведение хромуглеродных покрытий, полученных магнетронным распылением // Физика металлов и металловедение. 2019. V. 120. P. 219–224.
Musil J., Kunc F., Zeman H., Polakova H. Relationships between hardness, Young’s modulus and elastic recovery in hard nanocomposite coatings // Surface and Coatings Technology. 2002. V. 154. P. 304–313.
Guo Z., Zhang A., Han J., Meng J. Microstructure, mechanical and tribological properties of CoCrFeNiMn high entropy alloy matrix composites with addition of Cr3C2 // Tribology International. 2020. V. 151. № 106436.
Staia M.H., Valente T., Bartuli C., Lewis D.B., Constable C.P., Roman A., Lesage J., Chicot D., Mesmacque G. Part II: tribological performance of Cr3C2–25% NiCr reactive plasma sprayed coatings deposited at different pressures // Surface and Coatings Technology. 2001. V. 146–147. P. 563–570.
Дополнительные материалы отсутствуют.
Инструменты
Физика металлов и металловедение