Физика металлов и металловедение, 2021, T. 122, № 12, стр. 1339-1346
Механические и триботехнические свойства спеченных алюмоматричных композитов Al–Sn, упрочненных частицами Al3Fe
Н. М. Русин a, А. Л. Скоренцев a, *
a Институт физики прочности и материаловедения СО РАН
634055 Томск, пр. Академический, 4/2, Россия
* E-mail: skoralexan@mail.ru
Поступила в редакцию 04.06.2021
После доработки 03.08.2021
Принята к публикации 18.08.2021
Аннотация
Исследованы триботехнические свойства композитов Al–Fe–Sn при сухом трении по стальному диску при скорости скольжения 0.6 м/с и давлении 1–5 МПа. Образцы для исследований получали методом жидкофазного спекания смеси элементарных порошков. Установлено, что с повышением температуры спекания образцов сопротивление их изнашиванию улучшается и повышается дополнительно при устранении остаточной пористости материала допрессовкой в закрытом штампе. Прочность композитов после допрессовки достигала постоянного высокого значения, величина которого практически не зависела от температуры спекания.
ВВЕДЕНИЕ
Существенным недостатком подшипников скольжения из алюминия является их склонность к схватыванию со стальным валом в случае дефицита жидкой смазки на поверхности трения. Вероятность зарождения очага схватывания снижается, а давление схватывания повышается, если в состав Al матрицы вводят вещества типа олова, способные размазываться по поверхности трения в виде тонких разделительных пленок [1‒3]. Композиционные материалы (КМ) с большой долей мягких фаз используются обычно в виде антифрикционных покрытий твердых подшипниковых вкладышей (ГОСТ 14113–78).
Для повышения твердости Al-сплавов в них вводят твердые керамические частицы [4–6]. Однако их поверхность плохо смачивается оловом, и при кристаллизации расплава образуются слабые межфазные границы. С целью сохранения высокой прочности антифрикционного КМ площадь таких границ стремятся минимизировать путем снижения объемной доли олова или его замены частицами материала типа графита [7–9].
С целью увеличения прочности межфазных границ твердые керамические частицы в композитах Al–Sn можно заместить алюминидами, хорошо смачиваемыми и жидким Sn, и Al. Причем, твердые частицы необязательно вводить в расплав готовыми, они могут быть получены “in situ” вследствие реакции между алюминиевой основой и железом [10]. Во избежание проблемы однородного перемешивания расплава с большим содержанием частиц твердой фазы, такие КМ можно получать методами порошковой металлургии. Например, в ходе спекания прессовок из элементарных порошков были получены двухфазные КМ “Al–Al3Fe”, обладающие повышенной износостойкостью по сравнению с обычными алюминиевыми сплавами и не уступающие по триботехническим свойствам оловянистым бронзам [11].
Поскольку алюминид Al3Fe частично растворим в жидком алюминии [12], он хорошо им смачивается и образует с матрицей прочную адгезионную границу при кристаллизации расплава. Растворимость железа в жидком олове также растет с температурой [13]. Отсюда следует, что можно не опасаться формирования в композите Al–Fe–Sn слабых адгезионных границ между добавками и смело увеличивать содержание олова до высокой оптимальной концентрации 35–40 мас. %, определенной в работе [14]. Однако ранее такие композиционные материалы спеканием не получали и не исследовали. Поэтому основной целью настоящей работы является исследование триботехнических свойств указанных КМ при сухом трении, с тем чтобы установить целесообразность введения большого количества олова в алюмоматричный КМ, упрочненный частицами интерметаллидов.
МАТЕРИАЛЫ И МЕТОДИКА ЭКСПЕРИМЕНТА
Для формирования композитов со сложным фазовым составом использовали смеси порошков алюминия марки АСД-4, железа марки ПЖ-4 и олова марки ПО 2. Так в смесь, обозначаемую далее КМ20, помимо алюминия входили 8 мас. % (5 ат. %) Fe и 21 мас. % (6 ат. %) Sn, а в смесь, обозначаемую КМ40, входили 7 мас. % (5 ат. %) железа и 38 мас. % (13 ат. %) олова. После смешивания порошки прессовали в плотные брикеты с пористостью ∼5% и подвергали спеканию в вакуумной печи марки СНВЭ, при остаточном давлении атмосферных газов не выше 10–2 Па. Спекание проводили при температурах ниже и выше точки плавления алюминия с выдержкой 1 ч. Спеченные брикеты подвергали дополнительному уплотнению при 250°С в закрытой пресс-форме под давлением, трехкратно превышающем предел текучести Al. Плотность образцов определяли по методу Архимеда, путем гидростатического взвешивания.
Шлифы для металлографических исследований готовили по следующей методике: поверхность образца шлифовали на наждачных бумагах с убывающим размером абразивных частиц, а затем на сукне с нанесенной на него алмазной пастой, содержащей частицы менее 1 мкм. Полированные поверхности дополнительно протравливали в 4%-ном растворе азотной кислоты в этиловом спирте. Для анализа структуры и состава поверхности шлифов использовали оптический и сканирующий электронный LEO EVO 50 (Zeiss, Германия) микроскопы, предоставленные ЦКП “НАНОТЕХ” ИФПМ СО РАН (ЦКП ТНЦ СО РАН).
Данные для рентгенофазового анализа были получены с помощью дифрактометра ДРОН-7, с использованием CoKα-излучения без монохроматора при симметричной схеме отражения. Съемку проводили в интервале углов 25° ≤ 2θ ≤ 165° с шагом 0.05°. Для обработки результатов использовали программный комплекс PDWin (Буревестник, Россия).
Триботехнические свойства композитов определяли при сухом трении по стальному контртелу по схеме “палец–диск” на установке фирмы “Tribotechnic” (Франция). Коэффициент трения µ рассчитывался автоматически встроенным компьютером. Линейную интенсивность изнашивания Ih образцов сечением 2 × 2 мм определяли по формуле: Ih = Δ/L [мкм/м], где Δ – толщина изношенного слоя при прохождении пути трения длиной L, измеренная с помощью микрометра. Точность значения Ih составила ±0.02 [мкм/м]. Поверхности контртел перед началом трибологических испытаний готовили по методике, используемой для приготовления шлифов. Давление на поверхность трения P составляло 1–5 МПа, скорость скольжения V – 0.6 м/с, путь трения L – 1000 м. Механические характеристики материалов определяли при сжатии прямоугольных образцов на универсальной испытательной машине Instron-1185 при скорости осаживания 0.5 мм/мин.
РЕЗУЛЬТАТЫ
В спекаемых двухкомпонентных порошковых смесях твердое соединение Al3Fe интенсивно образуется при температуре ∼650°С, близкой к плавлению эвтектики Al–Fe [15]. Однако олово плавится при 231°С. Его расплав проникает по границам зерен алюминиевых порошинок и насыщается алюминием. Достигнув порошинок железа, он хорошо их смачивает и фрагментирует на отдельные зерна, в которые диффундирует растворенный в олове алюминий, образуя интерметаллид Al3Fe. Увеличение площади поверхности реакции приводит к быстрому сплавообразованию, и свободное железо в образцах полностью замещается указанным соединением уже при 490°С спекания (рис. 1). Данные результаты согласуются с [13], где сообщается, что равновесный фазовый состав сплавов Al–Fe–Sn в алюминиевом углу диаграммы при 320 и 700°С образуют олово, алюминий и соединение Al3Fe.
За счет растворения атомов Al в порошках железа объем последних возрастает почти в 4 раза, и на их месте формируются кластеры, состоящие из тугоплавких частиц Al3Fe, разделенных тонкими прослойками Sn. Ввиду завершения реакции сплавообразования при низкой температуре спекания (Тсп), дальнейший ее подъем на фазовый состав КМ40 и КМ20 не влияет, хотя частицы Al3Fe при этом укрупняются, а среднее расстояние между ними увеличивается (рис. 2).
Рис. 2.
Структура спеченного композита КМ40. Тсп, °С: 620 (а); 650 (б); 680 (в); 710 (г). Темные области – алюминиевая матрица, светлые – оловянные включения, серые – частицы Al3Fe.
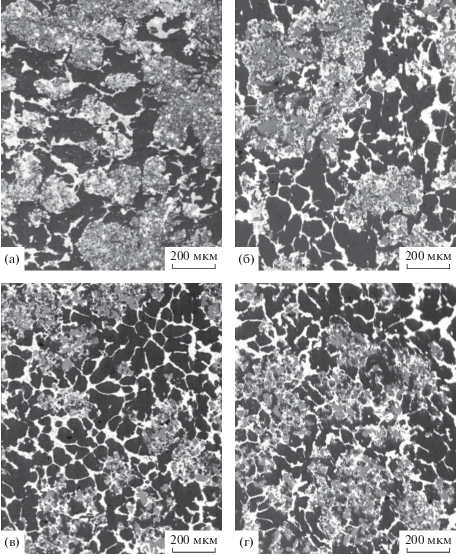
Условный предел текучести композитов σ0.2 также не зависел от температуры спекания и имел практически постоянную величину ∼60 МПа (табл. 1). Низкое ее значение указывает, что поры, как непременные элементы структуры спеченных материалов, также вносят свой вклад в их прочность. Двустороннее обжатие спеченных образцов при 250°С в закрытой пресс-форме с целью их доуплотнения привело к заметному уменьшению объемной доли пор и росту σ0.2 композитов КМ40 и КМ20 от 60 до ∼100 МПа и до ∼122–130 МПа предела прочности (σВ). Полученные значения указанных величин практически не зависели от температуры спекания КМ (табл. 1), что также указывает на постоянство их фазового состава.
Таблица 1.
Влияние температуры спекания Тсп и последующего доуплотнения на механические свойства (предел текучести σ0.2, предел прочности σB, относительное укорочение δ) КМ Al–Fe–Sn при сжатии
Состав | Фазовый состав | Тсп, °С | σ0.2, МПа | σB, МПа | δ, % |
---|---|---|---|---|---|
КМ40 | Al, Sn, Al3Fe | 570 | 101/61* | 126/81* | 18/9.4* |
Al, Sn, Al3Fe | 595 | 100 | 128 | 18.5 | |
Al, Sn, Al3Fe | 620 | 97/61* | 123/95* | >30/>30* | |
Al, Sn, Al3Fe | 680 | 90 | 123 | >30 | |
Al, Sn, Al3Fe | 710 | 98 | 122 | >30 | |
КМ20 | Al, Sn, Al3Fe | 620 | 97 | 129 | >30 |
**Al–40Sn [14] | Al, Sn | 600 | 102/43* | 110/80* | >30 |
**Al–20Sn [14] | Al, Sn | 600 | 103/45* | 119/91* | >30 |
Включения олова, в отличие от пор, являются несжимаемыми элементами структуры КМ с пределом упругости немного ниже, чем у Al и, значит, поддерживают уровень действующего гидростатического давления в деформируемом образце. Поэтому при изменении концентрации олова аддитивная величина σ0.2 у доуплотненных двухфазных композитов Al–Sn меняется мало. Алюминиды же гораздо тверже Al-матрицы, и при их добавлении в композит величина σ0.2 растет. В нашем случае объемная доля твердых частиц Al3Fe, образующихся при спекании смесей Al–Fe–Sn, составляла 14–17%, в результате чего предел текучести КМ после их допрессовки имел такую же величину, как σ0.2 у упрочненных методом равноканального углового прессования (РКУП) соответствующих двухфазных композитов Al–Sn [14]. При сжатии на 30% прочность дисперсно-упрочненных КМ20 и КМ40 дополнительно возрастала на 25–30 МПа (табл. 1).
Сравнительные испытания спеченных пар композитов с малым (Al–20Sn и КМ20) и большим (КМ40 и Al–40Sn) содержанием олова показали, что интенсивность изнашивания спеченных при низкой температуре (570°С) легированных железом КМ была выше, чем у двухфазных КМ, и стала сравнимой только при повышении температуры спекания до 620°С (табл. 2). Т.е. повышение износостойкости композитов Al–Sn за счет легирования их железом было незначительным.
Таблица 2.
Зависимость интенсивности изнашивания Ih и коэффициента трения μ композитов Al–Fe–Sn в спеченном и доуплотненном (ГП) состоянии от давления при сухом трении по стали. V = 0.6 м/с
Состав | Тсп, °С | Ih, мкм/м | μ | ||||||
---|---|---|---|---|---|---|---|---|---|
1 МПа | 3 МПа | 4 МПа | 5 МПа | 1 МПа | 3 МПа | 4 МПа | 5 МПа | ||
Al–10Fe | 680 + ГП | 0.21 | 0.51 | 0.66 | 0.97 | 0.42 | 0.29 | 0.27 | 0.26 |
КМ20 | 570 | 0.16 | 0.35 | 0.52 | 0.59 | 0.47 | 0.40 | 0.39 | 0.32 |
570 + ГП | 0.16 | 0.28 | 0.40 | 0.46 | – | – | – | – | |
620 + ГП | 0.13 | 0.22 | 0.33 | 0.36 | – | – | – | – | |
КМ40 | 570 | 0.14 | 0.33 | 0.42 | 0.55 | 0.45 | 0.39 | 0.38 | 0.29 |
570 + ГП | 0.13 | 0.22 | 0.25 | 0.28 | 0.43 | 0.37 | 0.38 | 0.30 | |
620 | 0.15 | 0.26 | 0.28 | 0.33 | – | – | – | – | |
620 + ГП | 0.13 | 0.19 | 0.23 | 0.25 | – | – | – | – | |
680 + ГП | 0.14 | 0.20 | 0.26 | 0.28 | – | – | – | – | |
710 | 0.17 | 0.24 | 0.25 | 0.28 | – | – | – | – | |
710 + ГП | 0.12 | 0.17 | 0.21 | 0.22 | 0.45 | 0.36 | 0.34 | 0.32 | |
Al–20Sn | 600 + ГП | 0.13 | 0.24 | – | 0.36 | – | – | – | – |
Al–40Sn | 600 + ГП | 0.13 | 0.20 | 0.23 | 0.25 | – | – | – | 0.31 |
АВЧ | Литой | 0.10 | 0.23 | 0.30 | 0.32 | 0.34 | – | 0.30 | 0.29 |
АСД-4 | 640 + 2 РКУП | 0.08 | 0.23 | 0.37 | 0.40 | 0.56 | – | 0.32 | 0.31 |
Максимальная температура спекания двухфазных композитов Al–Sn ограничивается из-за потери порошковыми прессовками формы вследствие растворения алюминия в олове и образования большого количества жидкой фазы. Однако образцы КМ40 и КМ20 благодаря присутствию в них тугоплавких частиц Al3Fe можно было нагревать до температуры выше точки плавления Al-матрицы. В результате после спекания при 710°С и допрессовки интенсивность изнашивания композита КМ40 при сухом трении по стальному диску стала на 10–15% ниже, чем у базового КМ Al–40Sn (табл. 2). Износостойкость КМ20 с меньшим содержанием олова была заметно хуже, а спеченный при 680°С безоловянистый композит Al–10Fe (5 ат. % Fe) истирался еще быстрее, несмотря на более высокое содержание в нем твердых алюминидов.
ОБСУЖДЕНИЕ РЕЗУЛЬТАТОВ
Из представленных в табл. 2 данных следует, что при сухом трении по стальному контртелу износостойкость литого (АВЧ) алюминия выше, чем у мелкозернистого спеченного алюминиевого образца. Объяснить слабое сопротивление спеченных образцов истиранию только отрицательным влиянием остаточной пористости нельзя, поскольку даже после уплотнения и упрочнения спеченных образцов двукратным РКУП износостойкость их при повышенных давлениях оставалась ниже, чем у литого сплава. Т.е. при сухом трении интенсивность изнашивания алюминиевого образца зависит в основном от величины приложенной нагрузки, и в малой степени от его прочности.
Однако величину Ih у спеченного алюминия можно существенно снизить, если в его состав добавить около 40 мас. % (20 об. %) мягкого олова. Указанная концентрация Sn вдвое больше, чем в стандартных литых сплавах марки АО, но при меньших его концентрациях эффект олова на износостойкость спеченного Al незначителен [14].
Исследования структуры подповерхностного слоя трущихся по стали образцов Al–Sn показали [10, 14], что улучшение износостойкости алюминия при добавлении в него большого количества олова обусловлено не смазыванием им поверхности трения, а облегчением относительного смещения соседних зерен, которое имеет место при наличии на разделяющей их границе тонкой прослойки из мягкого пластичного материала. Проскальзывание Al-зерен вдоль Sn прослоек позволяет подвергнуть материал большим деформациям, не повышая существенно плотность дислокаций внутри зерен [16]. Весовая концентрация олова 35–45% является оптимальной, поскольку позволяет сохранить мостики спекания между Al-зернами и в то же время существенно облегчает их относительное смещение. Поскольку при сухом трении деформирующему воздействию в первую очередь подлежит верхний слой зерен, то при наличии прочных связей между зернами деформация не локализуется только в верхнем их слое, а распространяется и на нижележащие слои. Рост толщины вовлеченного в деформацию слоя материала приводит к снижению ее градиента, и расположенные в деформируемом слое зерна могут испытывать большие деформации до отслоения, которое происходит вследствие исчерпания ресурса пластичности разделяющих их тонких оловянных прослоек.
Сдерживать взаимное проскальзывание деформируемых зерен могут и присутствующие на границах твердые частицы, и тем самым способствовать вовлечению в пластическое течение подповерхностные слои зерен, т.е. увеличивать толщину вовлеченного в деформацию силами трения слоя и снижать интенсивность образования частиц износа в виде отслоившихся зерен матрицы. Однако если частицы хрупкие и слабо связаны с окружающим их оловом, то их присутствие ускорит разрушение оловянных прослоек, и влияние частиц на износостойкость композиционного материала будет обратным.
Межзеренные поры также способствуют локализации пластического течения и ускоренному изнашиванию спеченных образцов при сухом трении. При повышении температуры спекания их объемная доля убывает, а износостойкость КМ растет. Однако устранить поры полностью удается лишь посредством горячей допрессовки спеченных образцов, что способствует дальнейшему улучшению их износостойкости (табл. 2). Устранение пор привело к росту у допрессованных образцов σ0.2 на 30–40 МПа, но примерно на эту же величину вырос и предел их прочности σВ. Т.е. прочность исследуемых композитов является величиной аддитивной концентрации составляющих их фаз, объемное соотношение которых постоянно и не зависит от Тсп композита.
Во время непосредственно спекания объемное соотношение фаз не является величиной постоянной и зависит от температуры процесса, влияющей на растворимость атомов алюминия в олове и атомов железа в расплаве Sn–Al. Их растворимость растет при повышении Тсп и таким образом влияет на размеры частиц фаз и образуемую ими структуру КМ. В результате ускоренной растворимости мелкие частицы алюминидов исчезали, а крупные подрастали, и удельная поверхность частиц фазы Al3Fe снижалась. Часть защемленного между частицами олова высвобождалась и расходовалась на фрагментацию матрицы и утолщение прослоек между ее зернами (рис. 1). С ростом толщины прослоек ресурс их пластичности увеличивался, и это способствовало повышению износостойкости композитов (табл. 2).
Растворимость олова в жидком алюминии неограниченна, и при расплавлении матрицы КМ образуется расплав Al–Sn. При его кристаллизации растворенное в нем олово выпадает на границах растущих алюминиевых зерен в виде прослоек (рис. 2в, 2г). Ввиду высокой скорости кристаллизации расплава размер новых Al зерен становится меньше, чем до расплавления матрицы, и это благоприятно сказывается на пластичности КМ [14]. При расплавлении матрицы значительная часть олова продолжает удерживаться в кластерах капиллярными силами и высвобождается только при укрупнении частиц алюминидов. С уходом избыточного олова в расплав размеры кластеров снижаются (рис. 2). В результате указанных структурных изменений износостойкость композитов возросла, величина Ih у КМ40 стала на 10–15% ниже, чем у базового двухфазного композита Al–40Sn при прочих равных условиях.
Эволюцию размеров и формы частиц Al3Fe при температуре выше плавления Al-матрицы можно видеть на рис. 3. До расплавления матрицы в оловянных прослойках оставалось много мелких частиц алюминидов (показаны стрелками на рис. 3а), которые снижали их пластичность. Крупные частицы имели неравновесную форму и содержали поры и трещины, что также плохо сказывалось на износостойкости КМ. При расплавлении Al начинает действовать как поверхностно-активная жидкость, проникает на границы зерен больших частиц алюминидов железа и фрагментирует их (рис. 3б). Увеличение площади межфазной поверхности способствует интенсификации процессов растворения–осаждения и приводит к практическому исчезновению мелких частиц Al3Fe. Размер оставшихся алюминидов выравнивается, а количество в них трещин и других дефектов снижается (рис. 3в). Снижение числа частиц приводит к утолщению прослоек олова, ресурс их пластичности повышается, и они могут выдержать большие деформации до его исчерпания.
Таким образом, из рассмотренного выше материала следует, что основным фактором, способствующим повышению износостойкости КМ Al–Fe–Sn, является улучшение их пластичности за счет снижения пористости и утолщения оловянных прослоек, при условии сохранения связанности зерен матрицы. Об улучшении пластичности КМ с ростом температуры спекания свидетельствуют не только данные испытаний на сжатие (табл. 1), но и характер структуры материала под поверхностью трения (рис. 4).
Рис. 4.
Структура доуплотненных образцов КМ40 под поверхностью трения. V = 0.6 м/с, P = 5 МПа. Температура спекания, °С: 570 (а), 620 (б), 710 (в, г). Образец (г) не доуплотнялся.
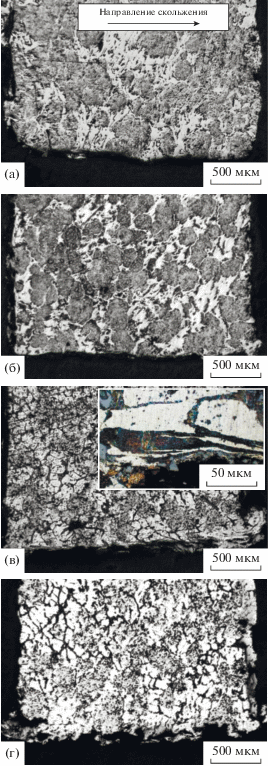
На представленных фотографиях видно, что в случае низкой пластичности спеченного при 570 С КМ40 зерна матрицы под поверхностью трения практически не деформированы. Т.е. частицы износа образуются вследствие разрушения кластеров с мелкими частицами алюминидов и абразивного истирания больших зерен матрицы поверхностными неровностями твердого стального контртела.
Однако, как только пластичность материала повышалась за счет утолщения прослоек Sn, высвободившегося вследствие укрупнения интерметаллических частиц, так под поверхностью трения стали наблюдаться сильнодеформированные Al-зерна, а износостойкость КМ возросла (табл. 2). Явными признаками возросшей пластичности спеченного при 710°С КМ40 является появление заусенца с задней стороны трущегося образца (рис. 4в).
Отметим важность такой операции как допрессовка спеченных образцов. В результате ее применения устраняются охрупчивающие материал межчастичные поры. В противном случае они облегчают распространение подповерхностных трещин и преждевременное образование частиц износа. На месте таких частиц образуются большие углубления (рис. 4г), которые хорошо видны и на фотографиях поверхности трения образца (рис. 5а). На поверхности трения допрессованного образца также присутствуют углубления на месте отслоившихся зерен (рис. 5б), но из сравнения рис. 4в и 4г следует, что они гораздо мельче, чем у спеченных образцов.
ЗАКЛЮЧЕНИЕ
Из полученных результатов следует, что посредством спекания смеси элементарных порошков Al, Fe и Sn можно получать композиты на основе алюминия с большим содержанием мягкого олова и твердой интерметаллидной фазы Al3Fe, объединенной в кластеры из мелких частиц, разделенных тонкими оловянными прослойками. С повышением температуры спекания размер частиц увеличивается, прочность композитов несколько снижается, но заметно возрастает их пластичность и становится сравнимой с пластичностью двухфазных КМ Al–Sn. Спекание при температуре выше точки плавления Al матрицы огрубляет структуру частиц в железосодержащих кластерах, что приводит к увеличению толщины разделяющих их оловянных прослоек и повышению износостойкости КМ. Горячая допрессовка спеченных КМ Al–Fe–Sn эффективно способствует улучшению их механических и триботехнических свойств. Увеличение содержания олова с 20 до 40 мас. % также способствует существенному повышению износостойкости исследуемых КМ тройного состава.
Работа выполнена в рамках государственного задания ИФПМ СО РАН, тема № FWRW-2021-0006.
Список литературы
Stolyarova O.O., Muravyeva T.I., Zagorskiy D.L., Gubenko M.M. Investigation of the surface of antifriction Al–Cu–Si–Sn–Pb aluminum alloys // J. Synch. Investig. 2017. V. 11. P. 832–839.
Bushe N.A., Goryacheva I.G., Makhovskaya Yu.Yu. Effect of aluminum alloy composition on self-lubrication of frictional surfaces // Wear. 2003. V. 254. P. 1276–1280.
Миронов А.Е., Белов Н.А., Столярова О.О. Алюминиевые сплавы антифрикционного назначения. М.: Изд. дом МИСиС, 2016, 222 с.
Cree D., Pugh M. Dry wear and friction properties of an A356/SiC foam interpenetrating phase composite // Wear. 2011. V. 272 P. 88–96.
Марукович Е.И., Кукареко В.А., Стеценко В.Ю., Чекулаев В., Сухоцкий П.Г. Исследование триботехнических свойств литейного силумина АК15М3 // Литье и металлургия. 2018. Т. 1. № 90. С. 7–11.
Vencl A., Bobic I., Jovanovic M.T., Bobic M., Mitrovic S. Microstructural and tribological properties of A356 Al–Si alloy reinforced with Al2O3 particles // Tribol. Lett. 2008. V. 32. P. 159–170.
Goudar D.M., Srivastava V.C., Rudrakshi G.B., Raju K., Ojha S.N. Effect of tin on the wear properties of spray formed Al–17Si alloy // Trans. Indian Inst. Met. 2015. V. 68. P. 3–7.
Ayyanar S., Gnanavelbabu A., Rajkumar K., Loganathan P. Studies on high temperature wear and friction behaviour of AA6061/B4C/hBN hybrid composites // Met. Mater. Int. 2020. https://doi.org/10.1007/s12540-020-00710-z
Basavarsjappa S., Chandramohan G., Mukund K., Ashwin M., Prabu M. Dry sliding wear behavior of Al 2219/SiC–Gr hybrid metal matrix composites // J. Mater. Eng. Perf. 2006. V. 15(6). P. 668–674.
Щербакова О.О., Муравьева Т.И., Загорский Д.Л. Исследование антифрикционных алюминиевых сплавов, содержащих железо, до и после трибологических испытаний // Письма о материалах. 2018. Т. 8. № 2. С. 123–128.
Русин Н.М. Триботехнические свойства спеченных композиционных материалов с алюминиевой матрицей // Трение и смазка в машинах и механизмах. 2010. № 9. С. 7–15.
Диаграммы состояния двойных и многокомпонентных систем на основе железа: Справ. изд./ Банных О.А., Будберг П.Б., Алисова С.П. и др. М: Металлургия, 1986. 440 с.
Liu Y., Yin F., Hu J., Li Z., Cheng S. Phase equilibria of Al–Fe–Sn ternary system // Trans. Nonferrous Met. Soc. China. 2018. V. 28. P. 282–289.
Rusin N.M., Skorentsev A.L., Kolubaev E.A. Effect of severe plastic deformation on wear resistance of sintered Al–Sn alloys under dry friction against steel // J. Frict. Wear. 2020. V. 41(3). P. 259–266.
Русин Н.М., Савицкий А.П. Жидкофазное реакционное спекание порошковых смесей в системе алюминий–железо // Порошковая металлургия. 1993. № 1. С. 28–32.
Иванов К.В., Найденкин Е.В. Особенности структуры и механических свойств чистого алюминия и сплава 1420 после воздействия интенсивной пластической деформации // Изв. Томского политехнического ун-та. 2009. Т. 315. № 2. С. 118–122.
Дополнительные материалы отсутствуют.
Инструменты
Физика металлов и металловедение