Физика металлов и металловедение, 2021, T. 122, № 2, стр. 173-180
Влияние малых добавок Zr и Er на фазовый состав и механические свойства сплава Al–5Si–1.3Cu–0.5Mg
Р. Ю. Барков a, *, А. Г. Мочуговский a, М. Г. Хомутов a, А. В. Поздняков a
a НИТУ “МИСиС”
119049 Москва, Ленинский пр., 4, Россия
* E-mail: barkov@misis.ru
Поступила в редакцию 03.08.2020
После доработки 22.09.2020
Принята к публикации 09.10.2020
Аннотация
Исследовано влияние малых добавок эрбия и циркония на микроструктуру, фазовый состав, кинетику упрочнения при старении и разупрочнения в процессе отжига после прокатки сплава Al–5Si–1.3Cu–0.5Mg. Эрбий и цирконий образуют с алюминием, кремнием, медью и магнием фазу кристаллизационного происхождения, которая не растворяется и не изменяет своей морфологии в процессе гомогенизации перед закалкой. Эрбий и цирконий увеличивают эффект старения после закалки, особенно при 210°С, повышают предел текучести при повышенной температуре, снижают склонность к разупрочнению в процессе отжига после прокатки, уменьшают размер рекристаллизованного зерна за счет дисперсоидов, сформированных в процессе гомогенизации. Закалка деформированных листов с последующим старением приводит к достижению несколько меньшего предела текучести, чем низкотемпературный отжиг после прокатки. При этом достигается существенно больший предел прочности в 344–375 МПа и пластичность 11.0–14.7%. Сплав с малыми добавками циркония и эрбия имеет более высокие характеристики как прочности, так и пластичности.
ВВЕДЕНИЕ
Легирование алюминия и сплавов на его основе переходными и редкоземельными металлами позволяет повышать прочностные характеристики как при комнатной, так и при повышенных температурах за счет формирования дисперсоидов в процессе отжига слитков. Цирконий является эффективным упрочнителем и антирекристаллизатором как в чистом алюминии [1–5], так и в деформируемых алюминиевых сплавах в основном на основе системы Al–Mg [6–8]. Наиболее эффективен цирконий совместно со скандием [9–11]. Однако последний является самым дорогим легирующим элементом в алюминиевых сплавах. Одной из альтернативных замен скандию является эрбий [12–31]. Эрбий с цирконием способны образовывать L12-дисперсоиды в процессе отжига слитков, повышая прочность и температуру начала рекристаллизации как чистого алюминия [12–17], так и сплавов на основе систем Al–Mg [18–23], Al–Cu [24–27]. Влияние же циркония и эрбия на структуру и свойства литейных алюминиевых сплавов, в частности силуминов, изучено в меньшей степени [28–31]. Малые добавки эрбия и циркония приводят к образованию сложных фаз кристаллизационного происхождения, повышают механические свойства сплава Al–7Si–0.4Mg (A356) как при комнатной, так и при повышенной температурах [28–31].
Настоящее исследование посвящено анализу влияния малых добавок эрбия и циркония на фазовый состав и механические свойства сплава Al‒5Si–1.3Cu–0.5Mg (типа АК5М). Силумины с содержание кремния более 4% отличаются хорошей технологичностью при литье [32–35]. При этом невысокое содержание кремния должно обеспечить хорошую технологичность при обработке давлением, а добавки циркония и эрбия – снизить склонность к разупрочнению в процессе отжига после деформации.
МЕТОДИКА ЭКСПЕРИМЕНТОВ
Сплавы составов Al–5Si–1.3Cu–0.5Mg (далее AlSi) и Al–5Si–1.3Cu–0.5Mg–0.1Zr–0.1Er (AlSiErZr) выплавлены в печи сопротивления из Al (99.99%), магния (99.9%), лигатур Al–53.5% Cu, Al–12% Si, Al–5% Zr и Al–8% Er (в мас. %). Разливку проводили в графитовую изложницу с внутренней полостью шириной 30 мм, толщиной 15 мм и высотой 150 мм. Скорость охлаждения составила примерно 15 K/с.
Термическую обработку проводили в печах “Nabertherm” и “SNOL” с принудительной циркуляцией воздуха и точностью поддержания температуры 1°С. Слитки после термической обработки подвергнуты горячей прокатке до толщины 8 мм при температуре 460–480°С с последующей прокаткой до 1 мм при при комнатной температуре.
Подготовку шлифов для микроструктурных исследований производили на шлифовально-полировальной установке Struers Labopol-5. Микроструктурные исследования и идентификацию фаз проводили на световом микроскопе (СМ) Neophot 30, на сканирующем электронном микроскопе (СЭМ) TESCAN VEGA 3LMH с использованием энерго-дисперсионного детектора X-Max 80 и рентгеновском дифрактометре Bruker D8 Advance. Расчет неравновесной кристаллизации проведен с использованием модели Sheil в программе Thermo-Calc.
Твердость измеряли стандартным методом Виккерса, ошибка в определении не превышала 3 HV. Испытания на растяжение образцов, полученных из листов толщиной 1 мм, проводили на универсальной испытательной машине Zwick/Roll Z250 серии Allround в комплексе с автоматическим датчиком продольной деформации. Испытания на сжатие при комнатной и повышенной температурах проводили на установке Gleeble-3800.
Измерение электропроводности производили при помощи установки INSTEK GOM-802 на образцах размером 1 мм × 70 мм × 5 мм с использованием метода “двойной мост”.
РЕЗУЛЬТАТЫ ЭКСПЕРИМЕНТОВ И ОБСУЖДЕНИЕ
Литая микроструктура сплавов и распределение легирующих элементов между фазами в выделенной области представлено на рис. 1. Литая микроструктура состоит из алюминиевого твердого раствора (Al), эвтектики ((Al) + Si) и светлых включений. Согласно расчету неравновесной кристаллизации (рис. 2а) в литой структуре сплава AlSi так же должны присутствовать включения фаз θ(Al2Cu) и Q (Al5Cu2Mg8Si6), что подтверждено результатами анализа структуры в СЭМ (рис. 1а) и рентгенофазовым анализом (РФА) (рис. 2б). Распределение элементов между двумя светлыми фазами показывает, что одна обогащена медью, вторая медью, магнием и кремнием (рис. 1а). По результатам РФА выявлены пики, соответствующие фазам θ и Q (рис. 2б).
Рис. 1.
Литая микроструктура (СЭМ) сплавов AlSi (а) и AlSiErZr (б) и распределение легирующих элементов между фазами в выделенной области (белый прямоугольник).
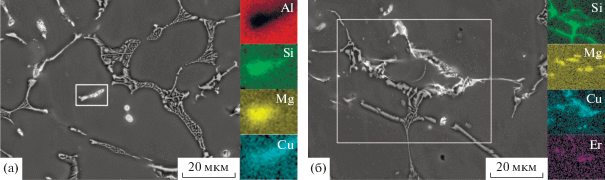
Рис. 2.
Неравновесная кривая охлаждения сплава AlSi (а) (пунктир – равновесная кривая) и рентгенограммы сплавов AlSi (б), AlSiErZr (в) (черная линия – литое состояние, темно-серая – отжиг 495°С, 1 ч и светло-серая – отжиг 495°С, 3 ч).
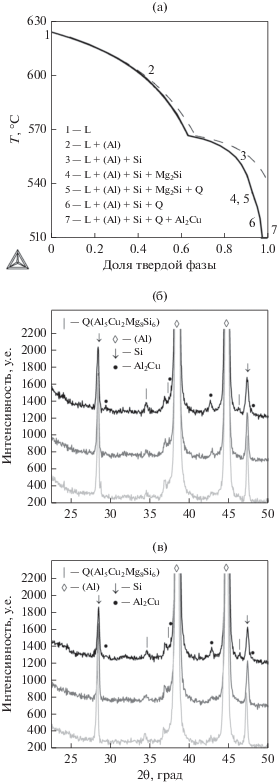
В сплаве AlSiErZr присутствуют светлые включения, обогащенные кремнием, магнием, медью и эрбием (рис. 1б), в которых растворяется до 1 ат. % Zr. На рентгенограмме сплава AlSiErZr присутствуют не идентифицированные пики, вероятно, соответствующие этой фазе. Ввиду ее малого количества пики имеют небольшую интенсивность. В процессе гомогенизации перед закалкой при 495°С происходит фрагментация и сфероидизация кремния и растворение неравновесного избытка фаз θ и Q (рентгенограммы на рис. 2б, 2в и эволюция микроструктуры на рис. 3), в результате которого концентрация легирующих элементов в твердом растворе увеличивается (табл. 1). Максимальное содержание добавок в твердом растворе достигнуто после трех часов гомогенизации и в дальнейшем не изменяется (табл. 1). Светлые включения в сплаве AlSiErZr, обогащенные эрбием, не изменяют морфологии и не растворяются в процессе гомогенизации (рис. 3б, 3г). Концентрация Er и Zr в твердом растворе находится на уровне разрешающей способности СЭМ и составляет около 0.1 мас. %.
Рис. 3.
Эволюция микроструктуры (СЭМ) сплавов AlSi (а, в), AlSiErZr (б, г) в процессе гомогенизации в течение 1 (а, б) и 3 (в, г) часов выдержки перед закалкой с 495°С.
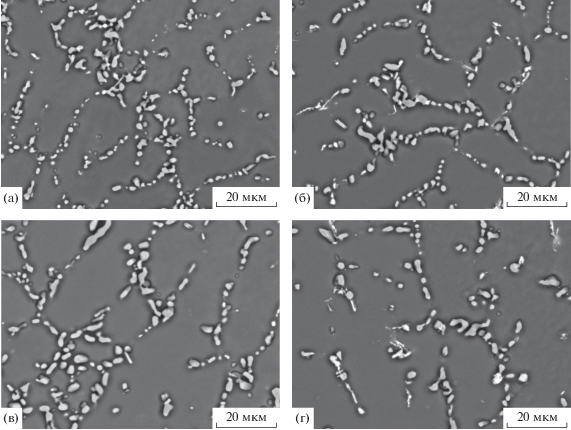
Таблица 1.
Изменение концентрации легирующих элементов в алюминиевом твердом растворе в зависимости от времени гомогенизации перед закалкой
Элемент | Равновесное расчетное содержание в сплаве AlSi | AlSi | AlSiErZr | ||||||
---|---|---|---|---|---|---|---|---|---|
литой | 1 час | 3 часа | 5 часов | литой | 1 час | 3 часа | 5 часов | ||
Cu | 1.4 | 0.5 | 1.3 | 1.5 | 1.5 | 0.4 | 1.4 | 1.5 | 1.5 |
Si | 0.46 | 0.6 | 0.6 | 0.6 | 0.6 | 0.4 | 0.4 | 0.4 | 0.4 |
Mg | 0.77 | 0.2 | 0.3 | 0.4 | 0.4 | 0.3 | 0.3 | 0.4 | 0.4 |
Er | – | – | – | – | – | 0.1 | 0.1 | 0.1 | 0.1 |
Zr | – | – | – | – | – | 0.1 | 0.1 | 0.1 | 0.1 |
После трех часов гомогенизации при 495°С сплавы подвергнуты закалке и старению в течение разного времени при температурах 150, 180 и 210°С. Кинетика старения носит обычный характер: с увеличением температуры уменьшается время достижения пика твердости, максимальная твердость достигнута после старения при 150 и 180°С (рис. 4).
Рис. 4.
Кинетические зависимости твердости сплавов AlSi (а) и AlSiErZr (б) для различных температур старения.
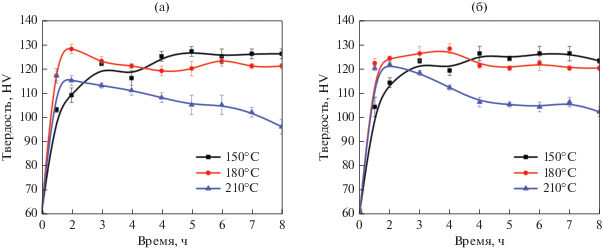
Некоторые особенности кинетики старения и эффекта упрочнения присутствуют в сплаве AlSiErZr и обусловлены влиянием дисперсоидов фазы Al3(Er,Zr), образованной в процессе гомогенизации.
Похожие результаты получены в работах [26, 27]. В сплаве AlSiErZr отмечен больший прирост твердости при старении при 210°С и в среднем прирост твердости больше на 3–5 HV. В табл. 2 представлены результаты испытаний на сжатие при комнатной и повышенной температурах. Предел текучести исследуемых сплавов при комнатной температуре примерно одинаков, а при 200°С предел текучести сплава AlSiErZr на 10 МПа выше.
Таблица 2.
Предел текучести на сжатие (МПа) при комнатной и повышенной температурах
Сплав | 20°С | 200°С |
---|---|---|
AlSi | 240 ± 1 | 178 ± 1 |
AlSiErZr | 238 ± 3 | 188 ± 2 |
Закаленные сплавы после прокатки отжигали по двум режимам: 1 – сразу после прокатки и 2 – после закалки с 495°С с выдержкой 10 мин. Сразу после прокатки (режим 1) разупрочнение в сплаве AlSiErZr в процессе отжига проходит в меньшей степени (рис. 5а, 5б), что связано с наличием сдерживающего полигонизацию фактора – дисперсоидов.
Рис. 5.
Кинетические зависимости твердости сплавов AlSi (а, в), AlSiErZr (б, г) после прокатки (а, б) и после прокатки и закалки с 495°С после выдержки 10 мин (в, г).
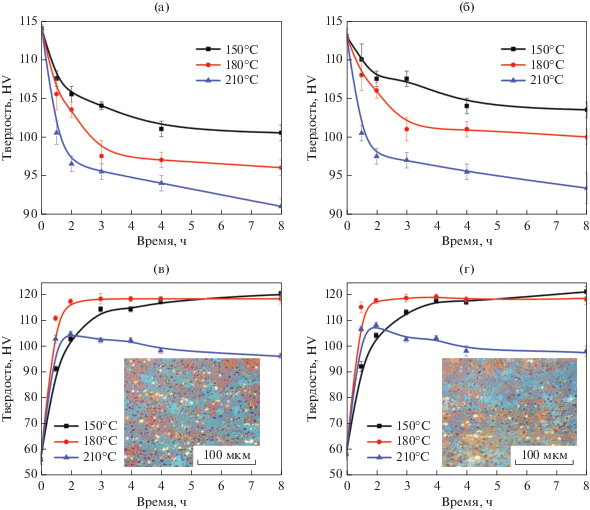
Рекристаллизация в обоих сплавах начинается в интервале 300–350°С. После одного часа отжига при 300°С сплавы имеют нерекристаллизованную структуру (вставки на рис. 6), а твердость сплава AlSiErZr примерно на 10 HV больше. Рекристаллизация в ходе отжига при 350°С приводит к резкому снижению твердости обоих сплавов (рис. 6).
Рис. 6.
Зависимости твердости от температуры отжига сплавов AlSi (черная линия) и AlSiErZr (серая линия) в течение 1 ч и зеренная структура после отжига при 300 и 350°С.
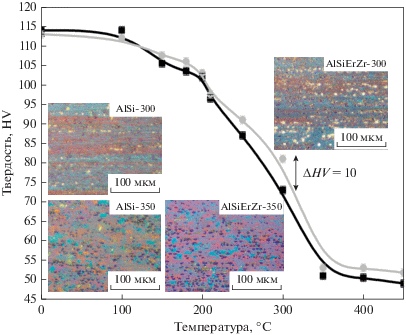
Отжиг при 495°С в течение 10 мин приводит к рекристаллизации, при этом в сплаве AlSiErZr размер рекристаллизованного зерна существенно меньше и составляет в среднем 12 мкм, в то время как в сплаве AlSi – более 20 мкм (вставки микроструктур на рис. 5в, 5г). Старение же после закалки деформированных листов (рис. 5в, 5г) проходит примерно так же, как и старение после закалки слитков (рис. 4). При этом твердость сплава AlSiErZr несколько выше.
Отжиг деформированных листов при температурах 150–210°С приводит к снижению предела текучести примерно с 330 до 270–300 МПа в обоих сплавах, при этом предел прочности обоих сплавов составляет 308–335 МПа при удлинении в 4.5–6.2% (табл. 3). Существенной разницы в свойствах сплавов не отмечено. Закалка деформированных листов с 495°С с последующим старением приводят к достижению несколько меньшего предела текучести 271–289 МПа, но к существенно большему пределу прочности в 344–375 МПа и пластичности в 11.0–14.7%. При этом сплав с малыми добавками циркония и эрбия имеет более высокие характеристики как прочности, так и пластичности (табл. 3).
Таблица 3.
Характеристики механических свойств после испытаний на растяжение в деформированном и отожженном состояниях
Состояние | σ0.2, МПа | σв, МПа | δ, % | σ0.2, МПа | σв, МПа | δ, % |
---|---|---|---|---|---|---|
AlSi | AlSiErZr | |||||
После прокатки | ||||||
Деформированное | 331 ± 1 | 357 ± 2 | 3.5 ± 0.5 | 334 ± 1 | 360 ± 3 | 3.2 ± 0.6 |
Отжиг 150°С, 4 часа | 294 ± 2 | 334 ± 1 | 5.1 ± 0.8 | 300 ± 2 | 335 ± 1 | 5.5 ± 0.3 |
Отжиг 180°С, 2 часа | 292 ± 2 | 328 ± 1 | 6.0 ± 0.5 | 293 ± 1 | 331 ± 1 | 5.6 ± 0.5 |
Отжиг 180°С, 4 часа | 280 ± 2 | 313 ± 1 | 4.5 ± 0.9 | 282 ± 2 | 318 ± 2 | 6.4 ± 0.2 |
Отжиг 210°С, 1 час | 272 ± 1 | 308 ± 1 | 6.1 ± 0.6 | 273 ± 1 | 308 ± 1 | 6.2 ± 0.8 |
После закалки с 495°С | ||||||
Отжиг 150°С, 4 часа | 243 ± 2 | 370 ± 4 | 18.5 ± 1.2 | 254 ± 2 | 374 ± 3 | 16.8 ± 0.4 |
Отжиг 180°С, 4 часа | 278 ± 1 | 371 ± 1 | 13.5 ± 1.5 | 282 ± 2 | 375 ± 1 | 14.7 ± 0.5 |
Отжиг 180°С, 8 часов | 282 ± 4 | 365 ± 2 | 11.0 ± 1.8 | 289 ± 1 | 369 ± 2 | 12.7 ± 1.1 |
Отжиг 210°С, 1 час | 271 ± 2 | 344 ± 2 | 12.0 ± 0.9 | 275 ± 1 | 346 ± 4 | 11.4 ± 0.8 |
В табл. 4 представлены результаты определения электропроводности в процентах по международному стандарту на отожженную медь (IACS). В деформированном состоянии сплав AlSiErZr имеет большую электропроводность, что связано вероятнее всего с меньшей степенью легирования алюминиевой матрицы медью, магнием и кремнием, которые частично идут на образование нерастворимых при гомогенизации фаз кристаллизационного происхождения с эрбием (табл. 1, рис. 1–3).
Таблица 4.
Электропроводность сплава в деформированном и отожженном состояниях
Состояние | IACS, % | |
---|---|---|
AlSi | AlSiErZr | |
После прокатки | ||
Деформированное | 41.3 | 45.6 |
Отжиг 180°С, 1 час | 47.1 | 46.3 |
Отжиг 180°С, 2 часа | 47.5 | 47.0 |
Отжиг 180°С, 4 часа | 48.2 | 47.5 |
Отжиг 210°С, 1 час | 48.8 | 48.2 |
Отжиг 210°С, 2 часа | 48.9 | 48.2 |
Отжиг 210°С, 4 часа | 49.3 | 48.5 |
После закалки с 495°С | ||
Закаленное | 37.6 | 38.6 |
Отжиг 180°С, 1 час | 39.9 | 39.9 |
Отжиг 180°С, 2 часа | 40.2 | 40.1 |
Отжиг 180°С, 4 часа | 40.4 | 40.4 |
Отжиг 210°С, 1 час | 41.1 | 41.3 |
Отжиг 210°С, 2 часа | 40.9 | 41.6 |
Отжиг 210°С, 4 часа | 40.9 | 41.8 |
Отжиг при 180–210°С приводит к увеличению электропроводности, что связано со снижением концентрации точечных дефектов и прохождением процессов полигонизации. При этом электропроводность в сплаве AlSi увеличивается на большую величину (с 41.3 до 49.3%IACS) в сравнение со сплавом AlSiErZr (с 45.6 до 48.5% IACS), что подтверждает меньшую склонность последнего к разупрочнению в процессе отжига. Более высокая электропроводность сплава с добавками в закаленном состоянии после прокатки также может быть объяснена наличием предположительно когерентных выделений дисперсоидов фазы Al3(Er,Zr), образованной в процессе гомогенизации еще перед прокаткой (табл. 4). При этом последующее старение приводит к небольшому приросту электропроводности, связанному с обеднением матрицы легирующими элементами.
ВЫВОДЫ
Исследовано влияние малых добавок эрбия (0.1 мас. %) и циркония (0.1 мас. %) на микроструктуру, фазовый состав, кинетику упрочнения при старении и разупрочнения в процессе отжига после прокатки. Часть эрбия и циркония идет на образование фазы кристаллизационного происхождения с алюминием, кремнием, медью и магнием, которая не растворяется и не изменяет своей морфологии в процессе гомогенизации перед закалкой.
Эрбий и цирконий, растворенные в алюминиевой матрице, увеличивают эффект старения после закалки, снижают склонность к разупрочнению в процессе отжига после прокатки, уменьшают размер рекристаллизованного зерна за счет дисперсоидов, сформированных в процессе гомогенизации. При этом отмечено следующее влияние на механические свойства:
– сплав с добавками в состаренном состоянии обладает пределом текучести на сжатие при 200°С равным 188 МПа, в то время как в сплаве без добавок – 178 МПа;
– твердость сплава с добавками после отжига деформированных листов на 5–10 HV больше;
– закалка деформированных листов с последующим старением приводят к достижению меньшего (с отличием до 10 МПа) предела текучести, чем низкотемпературный отжиг после прокатки. Однако, при этом достигается существенно больший предел прочности в 344–375 МПа и пластичность в 11.0–14.7%;
– сплав с малыми добавками циркония и эрбия имеет более высокие характеристики как прочности, так и пластичности.
Работа выполнена при поддержке Минобрнауки России в рамках государственного задания (код проекта 0718-2020-0030).
Список литературы
Zariff A., Chaudhury C., Suryanarayana A. TEM study of decomposition behavior of a melt-quenched A1–Zr alloy // Metallography. 1984. V. 17. P. 231–250.
Nes E. Precipitation of the metastable cubic Al3Zr-phase in subperitectic Al–Zr alloys // Acta Metall. 1972. V. 20. P. 499–506.
Xin-yu Ü., Er-jun G., Rometsch P., Li-juan W. Effect of one-step and two-step homogenization treatments on distribution of Al3Zr dispersoids in commercial AA7150 aluminium alloy // Trans. Nonferrous Metals Soc. China. 2012. V. 22. P. 2645–2651.
Knipling K.E., Dunand D.C., Seidman D.N. Precipitation evolution in Al–Zr and Al–Zr–Ti alloys during aging at 450–600°C // Acta Mater. 2008. V. 56. P. 1182–1195.
Knipling K.E., Dunand D.C., Seidman D.N. Precipitation evolution in Al–Zr and Al–Zr–Ti alloys during isothermal aging at 375–425°C // Acta Mater. 2008. V. 56. P. 114–127.
Mikhaylovskaya A.V., Portnoy V.K., Mochugovskiy A.G., Zadorozhnyy M.Yu., Tabachkova N.Yu., Golovin I.S. Effect of homogenisation treatment on precipitation, recrystallisation and properties of Al–3%Mg–TM alloys (TM = Mn, Cr, Zr) // Mater. Des. 2016. V. 109. P. 197–208.
Mikhaylovskaya A.V., Mochugovskiy A.G., Levchenko V.S., Tabachkova N.Yu., Mufalo W., Portnoy V.K. Precipitation behavior of L12 Al3Zr phase in Al–Mg–Zr alloy // Mat. Char. 2018. V. 139. P. 30–37.
Ma Y., Mishra R.S. Development of ultrafine-grained microstructure and low temperature (0.48 Tm) superplasticity in friction stir processed Al–Mg–Zr // Scr. Mater. 2005. V. 53. P. 75–80.
Fuller C.B., Seidman D.N. Temporal evolution of the nanostructure of Al3(Sc,Zr) alloys: Part II-coarsening of Al3(Sc1 –xZrx) precipitates // Acta Mater. 2005. V. 53. № 20. P. 5415–5428.
Zolotorevskiy V.S., Dobrojinskaja R.I., Cheverikin V.V., Khamnagdaeva E.A., Pozdniakov A.V., Levchenko V.S., Besogonova E.S. Evolution of structure and mechanical properties of Al–4.7Mg–0.32Mn–0.21Sc–0.09Zr alloy sheets after accumulated deformation during rolling // Phys of Met and Metall. 2016. V. 117. № 11. P. 1163–1169.
Zolotorevskiy V.S., Dobrojinskaja R.I., Cheverikin V.V., Khamnagdaeva E.A., Pozdniakov A.V., Levchenko V.S., Besogonova E.S. Strength and Substructure of Al–4.7Mg–0.32Mn–0.21Sc–0.09Zr Alloy Sheets // Phys of Met and Metall. 2017. V. 118. № 4. P. 407–414.
Zhang Y., Gao K., Wen S., Huang H., Nie Z., Zhou D. The study on the coarsening process and precipitation strengthening of Al3Er precipitate in Al–Er binary alloy // J. Alloys Compd. 2014. V. 610. P. 27–34.
Wen S.P., Gao K.Y., Li Y., Huang H., Nie Z.R. Synergetic effect of Er and Zr on the precipitation hardening of Al–Er–Zr alloy // Scr. Mater. 2011. V. 65. P. 592–595.
Wen S.P., Gao K.Y., Huang H., Wang W., Nie Z.R. Precipitation evolution in Al–Er–Zr alloys during aging at elevated temperature // J. Alloys Compd. 2013. V. 574. P. 92–97.
Pozdniakov A.V., Barkov R.Yu., Prosviryakov A.S., Churyumov A.Yu., Golovin I.S., Zolotorevskiy V.S. Effect of Zr on the microstructure, recrystallization behavior, mechanical properties and electrical conductivity of the novel Al–Er–Y alloy // J. Alloys Compd. 2018. V. 765. P. 1–6.
Pozdnyakov A.V., Osipenkova A.A., Popov D.A., Makhov S.V., Napalkov V.I. Effect of Low Additions of Y, Sm, Gd, Hf and Er on the Structure and Hardness of Alloy Al – 0.2% Zr – 0.1% Sc // Met. Sci. Heat Treat. 2017. V. 58. № 9–10. P. 537–542.
Pozdnyakov A.V., Barkov R.Yu. Effect of impurities on the phase composition and properties of a new alloy of the Al–Y–Er–Zr–Sc system // Metallurgist. 2019. V. 63. № 1–2. P. 79–86.
Song M., Du K., Huang Z.Y., Huang H., Z.R. Nie, Ye H.Q. Deformation-induced dissolution and growth of precipitates in an Al–Mg–Er alloy during high-cycle fatigue // Acta Mater. 2014. V. 81. P. 409–419.
Hao H.L., Ni D.R., Zhang Z., Wang D., Xiao B.L., Ma Z.Y. Microstructure and mechanical properties of Al–Mg–Er sheets jointed by friction stir welding // Mater. and Des. 2013. V. 52. P. 706–712.
Wen S.P., Wang W., Zhao W.H., Wu X.L., Gao K.Y., Huang H., Nie Z.R. Precipitation hardening and recrystallization behavior of Al–Mg–Er–Zr alloys // J. Alloys Compd. 2016. V. 687. P. 143–151.
Yang dongxi, Li xiaoyan, He dingyong, Huang hui. Effect of minor Er and Zr on microstructure and mechanical properties of Al–Mg–Mn alloy (5083) welded joints // Mater. Sci. & Eng. A. 2013. V. 561. P. 226–231.
Pozdniakov A.V., Yarasu V., Barkov R.Yu., Yakovtseva O.A., Makhov S.V., Napalkov V.I. Microstructure and mechanical properties of novel Al–Mg–Mn–Zr–Sc–Er alloy // Mat. Let. 2017. V. 202. P. 116–119.
Mochugovskiy A.G., Mikhaylovskaya A.V., Tabachkova N.Yu., Portnoy V.K. The mechanism of L12 phase precipitation, microstructure and tensile properties of Al–Mg–Er–Zr alloy // Mater. Sci. & Eng. A. 2019. V. 744. P. 195–205.
Pozdnyakov A.V., Barkov R.Yu., Sarsenbaev Zh., Amer S.M., Prosviryakov A.S. Evolution of Microstructure and Mechanical Properties of a New Al–Cu–Er Wrought Alloy // Phys. Met. Metallogr. 2019. V. 120. № 6. P. 614–619.
Amer S.M., Barkov R.Yu., Yakovtseva O.A., Pozdniakov A.V. Comparative analysis of structure and properties of quasi-binary Al–6.5Cu–2.3Y and Al–6Cu–4.05Er alloys // Phys. Met. Metallogr. 2020. V. 121. № 5. P. 476–482.
Amer S.M., Barkov R.Yu., Yakovtseva O.A., Loginova I.S., Pozdniakov A.V. Effect of Zr on microstructure and mechanical properties of the Al–Cu–Er alloy // Mater. Sci. and Techn. 2020. V.36. № 4. P. 453–459.
Amer S.M., Yakovtseva O.A., Loginova I.S., Medvedeva S.V., Prosviryakov A.S., Bazlov A.I., Barkov R.Yu., Pozdniakov A.V. Phase composition and mechanical properties of a novel precipitation strengthening Al–Cu–Er–Mn–Zr alloy // Appl. Sci. 2020. V. 10. № 15. P. 5345–5353.
Hu X., Jiang F., Ai F., Yan H. Effects of rare earth Er additions on microstructure development and mechanical properties of die-cast ADC12 aluminum alloy // J. Alloys Compd. 2012. V. 538. P. 21–27.
Shi Z.M., Wang Q., Zhao G., Zhang R.Y. Effects of erbium modification on the microstructure and mechanical properties of A356 aluminum alloys // Mater. Sci. Eng. A. 2015. V. 626. P. 102–107
Colombo M., Gariboldi E., Morri A. Er addition to Al–Si–Mg-based casting alloy: effects on microstructure, room and high temperature mechanical properties // J. Alloys Compd. 2017. V. 708. P. 1234–1244.
Colombo M., Gariboldi E., Morri A. Influences of different Zr additions on the microstructure, room and high temperature mechanical properties of an Al–7Si–0.4Mg alloy modified with 0.25% Er // Mater. Sci. Eng. A. 2018. V. 713. P. 151–160.
Новиков И.И. Горячеломкость цветных металлов и сплавов. М.: Наука, 1966. 299 с.
Eskin D.G, Suyitno, Katgerman L. Mechanical properties in the semi-solid state and hot tearing of aluminium alloys // Prog. in Mat. Sci. 2004. V. 49. P. 629–711.
Zolotorevskiy V.S., Pozdniakov A.V. Determining the hot cracking index of Al–Si–Cu–Mg casting alloys calculated using the effective solidification range // Int. J. of Cast Met. Res. 2014. V. 27. № 4. P. 193–198.
Zolotorevskiy V.S., Pozdniakov A.V., Churyumov A.Yu. Search for promising compositions for developing new multiphase casting alloys based on Al–Cu–Mg matrix using thermodynamic calculations and mathematic simulation // Phys. of Met. and Metall. 2012. V. 113. № 11. P. 1052–1060.
Дополнительные материалы отсутствуют.
Инструменты
Физика металлов и металловедение