Физика металлов и металловедение, 2021, T. 122, № 2, стр. 166-172
Исследование влияния углерода на деформационное поведение и микроструктуру сплава Ti–10V–2Fe–3Al
А. В. Желнина a, *, М. С. Калиенко a, b, Н. В. Щетников a
a ПАО “Корпорация ВСМПО-АВИСМА”
624760 Верхняя Салда, ул. Парковая, 1, Россия
b ФГАОУ ВО “УрФУ им. первого Президента России Б.Н. Ельцина”
620002 Екатеринбург, ул. Мира, 19, Россия
* E-mail: avzhelnina@gmail.com
Поступила в редакцию 22.03.2020
После доработки 18.09.2020
Принята к публикации 22.09.2020
Аннотация
Исследование структуры, фазового состава и деформационного поведения титанового сплава Ti–10V–2Fe–3Al с различным содержанием углерода проведено методами растровой электронной сканирующей микроскопии (РЭМ), рентгеноструктурного фазового анализа (РФА). Показано, что по мере повышения содержания углерода в сплаве до предела его максимальной растворимости происходит увеличение дисперсности вторичной α-фазы и, как следствие, прочности сплава. После достижения предела растворимости углерода в структуре сплава наблюдаются частицы карбида титана, морфология и размеры которых аналогичны первичной α-фазе. Установлено, что частицы карбида титана не оказывают влияние на характеристики прочности и пластичности сплава при испытании на растяжение и сохраняют после деформации первоначальную форму. На этапе локализации деформации частицы карбида титана служат местами зарождения микропор.
ВВЕДЕНИЕ
Титановые (α + β)-сплавы переходного класса, к которым относится сплав Ti–10V–2Fe–3Al благодаря комбинации механических свойств (удельной прочности, вязкости разрушения и усталостной прочности) широко используются в авиастроении для изготовления высокопрочных конструкционных элементов планера и узлов шасси [1, 2]. Технические требования к химическому составу сплава строго ограничивают содержание в сплаве легких элементов, а именно: не более 0.13 мас. % кислорода, 0.05 мас. % азота, 0.05 мас. % углерода, 0.015 мас. % водорода [3]. Атомы легких элементов имеют следующие размеры: кислород 60 пм, азот 71 пм, углерод 77 пм, водород 46 пм, и поэтому располагаются в междоузлиях кристаллической решетки титана (радиус октаэдрических пор в α-Ti 61 пм, тетраэдрических 33 пм в α-Ti и 44 пм в β-Ti). Углерод в титановых сплавах, как кислород и азот, является α-стабилизатором и расширяет температурную область стабильности α-фазы [4, 5]. Растворимость углерода в титане существенно меньше, чем азота и кислорода, предел растворимости углерода в α‑фазе порядка 0.48 мас. % (2 ат. %). Растворимость углерода в титановых сплавах зависит от химического и фазового состава сплава [6], так, например, предел растворимости углерода в широко используемом сплаве Ti6Al4V порядка 0.35 мас. %, в β-титановых сплавах предел растворимости существенно меньше, в сплаве Ti15Mo – 0.006 мас. %, в сплаве Ti16Nb – 0.023 мас. % [7]. Когда концентрация углерода в кристаллической решетке превышает предел растворимости, углерод с титаном образуют новую фазу – карбид титана [8]. Данная фаза TiXCY может иметь различную стехиометрию и, как следствие, различные физико-механические свойства. Карбид титана TiC имеет высокую температуру плавления (3140°С) и существенно больший модуль упругости (440 ГПа), чем у конструкционных титановых сплавов (115 ГПа).
Одни из первых данных по влиянию углерода на свойства титана были представлены в 1955 г. в работе [4], где было установлено, что углерод оказывает на свойства меньшее влияние, чем кислород и азот, хотя имеет больший атомный радиус. Меньшее упрочняющее действие углерода, по сравнению с азотом и кислородом, объясняют меньшими силами связи атомов углерода с дислокациями, по сравнению с системами Ti–O и Ti–N. Прочностные характеристики титана повышаются при увеличении содержания углерода до 0.3 мас. %, после чего практически не зависят от содержания углерода. В области малых концентраций (до 0.3 мас. %) добавка одной сотой доли процента (по массе) углерода повышает временное сопротивление разрыву и предел текучести α-титана примерно на 7 МПа [9]. Аналогичное влияние углерода также наблюдается у легированных титановых сплавов [10]. Однако повышенное содержание углерода более 0.5 мас. % существенно снижает пластичность, вязкость разрушения и сопротивление усталости. Тем не менее исследования влияния углерода на механические свойства и деформационное поведение титановых сплавов продолжаются [11–17]. В частности, в работе [11] были получены новые данные по технологической пластичности сплава Ti6Al4V с 0.77 мас. % С в диапазоне температур 900–1100°С. В работе [12] установлено, что добавка углерода и бора в метастабильных β-сплавах (Ti-15333, Ti-1023, Ti-5553) уменьшает размер β‑зерен и дисперсной α-фазы, определили их влияние на прочность и пластичность. В работе [13] было продемонстрировано благоприятное влияние добавления углерода (0.23 мас. %) на прочность и сопротивление ползучести сплава Ti–8Al–1Mo–1V. В работах [16–20] были представлены данные о влиянии углерода на деформационное поведение сплавов, исследовано изменение микроструктуры в области пластической деформации образцов после испытания на растяжение. Однако работ, в которых было бы исследовано влияние углерода вблизи области максимальной его растворимости на деформационное поведение (α + β)-титановых сплавов переходного класса, крайне мало. В нашей предыдущей работе [16] было установлено, что с увеличением содержания углерода до предела его растворимости прочность сплава Ti–10V–2Fe–3Al возрастает.
Целью представленной статьи было исследовать деформационное поведение сплава Ti–10V–2Fe–3Al с содержанием углерода до и выше предела его растворимости в сплаве и установить природу изменения механических свойств.
МАТЕРИАЛ И МЕТОДИКИ
Материалом для исследования были прутки диаметром 22 мм из сплава химического состава Ti–10V–2Fe–3Al (мас. %) производства ПАО “Корпорация ВСМПО-АВИСМА”. Исследовали три состава с различным содержанием углерода 0.008, 0.034 и 0.063 мас. %, (содержание углерода в сплаве определено атомно-эмиссионным методом) (табл. 1). Механические свойства образцов изучали в термически обработанном состоянии. Первая ступень термообработки включала закалку в воду из (α + β)-области с температуры ниже температуры полиморфного превращения на 45°С, вторая ступень – старение при температуре 500°С с выдержкой 8 ч.
Таблица 1.
Химический состав исследованных сплавов Ti–10V–2Fe–3Al
Содержание углерода, мас. % | Содержание кислорода, мас. % | Alстр.экв | Moстр.экв |
---|---|---|---|
0.008 | 0.11 | 4.3 | 11.10 |
0.034 | 0.10 | 4.49 | 11.30 |
0.063 | 0.10 | 4.73 | 11.27 |
Испытание образцов на растяжение проводили на разрывной машине Zwick Z600 при комнатной температуре в соответствии со стандартом ASTM E8 [20]. На каждое состояние испытывали по два образца.
Исследование микроструктуры образцов проводили в продольном сечении прутка на микрошлифах с зеркальной поверхностью полученной полировкой коллоидным оксидом кремния. Использовали растровый электронный микроскоп Quanta 3D FEG, оснащенный детектором обратно-отраженных электронов (BSED, Z-контраст), детектором дифракции обратно-отраженных электронов (EBSD) и приставкой для микрорентгеноспектрального анализа EDAX Genesis 2000.
РФА образцов проводили на дифрактометре Bruker D8 Advance с детектором LynxEye, напряжение 40 кВ, ток 40 мА, шаг 0.01°, выдержка 0.5 секунды на точку.
Программное обеспечение JMatPro было использовано для моделирования структурно-фазовых превращений в исследуемом сплаве.
РЕЗУЛЬТАТЫ И ОБСУЖДЕНИЕ
Микроструктура образцов сплава Ti–10V–2Fe–3Al после закалки и старения характеризуется первичной α-фазой (αI) глобулярной морфологии среднего размера 2–3 мкм и мелкодисперсной вторичной α-фазой (αII) пластинчатой морфологии (рис. 1). Наблюдаются субзерна β-фазы размерами от 2 до 5 мкм, которые сформировались на этапе деформации прутков в (α + β) области и декорировались вторичной α-фазой при старении.
Рис. 1.
РЭМ-изображение микроструктуры образцов сплава Ti–10V–2Fe–3Al с содержанием углерода (мас. %): а, б – 0.008; в – 0.034; г – 0.063.
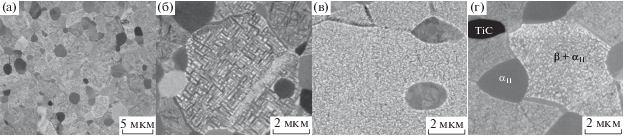
В результате исследования микроструктуры образцов с различным содержанием углерода в состоянии после старения было обнаружено отличие дисперсности вторичной α-фазы в структуре образцов, что связано с влиянием углерода на интенсификацию распада метастабильной β‑фазы. Увеличение дисперсности продуктов распада пересыщенного β-твердого раствора при добавлении углерода наблюдали в ряде других работ [12, 23]. Методом полнопрофильного анализа дифрактограмм [24] была проведена оценка размеров (толщины пластин) вторичной α-фазы.
Дифрактограммы с профилями подгонки отдельных фаз представлены на рис.2. По полученным данным толщина пластин вторичной α-фазы составила 47, 27 и 33 нм для образцов сплава с содержанием 0.008, 0.034 и 0.063 мас. % углерода. В свою очередь, увеличение дисперсности вторичной α-фазы оказывает влияние на свойства сплава, а именно, приводит к увеличению прочностных характеристик за счет увеличения количества межфазных границ и уменьшения пути движения дислокаций [25, 26]. В табл. 2 представлены результаты РФА-анализа образцов. Повышение содержания элемента внедрения – углерода в сплаве приводит к увеличению параметров кристаллической решетки, прежде всего возрастает параметр с кристаллической решетки α-фазы. Полученные результаты согласуются с литературными данными [9].
Рис. 2.
Дифрактограммы образцов с профилями линий отдельных фаз (мас. % С): (а) 0.008, (б) 0.034, (в) 0.063.
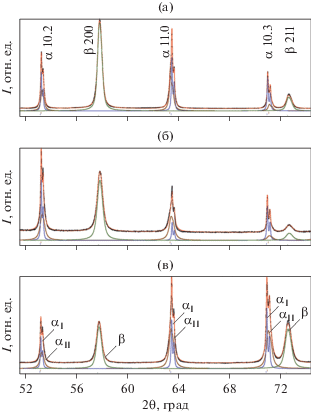
Таблица 2.
Параметры кристаллической решетки исследованных сплавов Ti–10V–2Fe–3Al
Содержание С | β-фаза | Первичная α-фаза | Вторичная α-фаза | |||||
---|---|---|---|---|---|---|---|---|
aβ, Å | a, Å | c, Å | c/a | a, Å | c, Å | c/a | d, нм | |
0.008 мас. % | 3.190 | 2.930 | 4.675 | 1.595 | 2.935 | 4.662 | 1.588 | 46.7 |
0.034 мас. % | 3.190 | 2.930 | 4.677 | 1.596 | 2.934 | 4.664 | 1.590 | 27.4 |
0.063 мас. % | 3.193 | 2.932 | 4.680 | 1.596 | 2.934 | 4.670 | 1.591 | 33.3 |
После термообработки образцов в теле и по границам β-зерен сплава с содержанием углерода 0.063 мас. % обнаружены глобулярные частицы третьей фазы (с объемной долей менее 5%), по морфологии идентичные первичной α-фазе, но имеющие темный контраст при исследовании в режиме обратно-отраженных электронов и объемное очертание при исследовании в режиме вторичных электронов (рис. 3а, 3в). Как известно, при исследовании структуры в режиме обратно-отраженных электронов, чем больше различие в плотности элементов структуры (атомном номере химических элементов), тем больше различие в контрасте структурных элементов. Связано это с большим количеством электронов, отразившихся от участка с большей плотностью (большим атомным номером химических элементов), что приводит к формированию более светлого изображения от данного участка. Плотность β-фазы больше плотности α-фазы, так как β-фаза содержит больше β-стабилизаторов (элементов с большим атомным номером) и меньше алюминия, поэтому на снимках в отраженных электронах β-фаза имеет более светлый контраст, чем α-фаза. Так как карбид титана содержит больше углерода и его плотность меньше, чем α-фазы, то данные частицы имеют более темный контраст в сравнении с α-фазой.
Рис. 3.
Области исследования химического состава (а), рентгеновские спектры (б) и картина полос Кикучи, полученная при EBSD анализе частицы карбида титана сплава Ti–10V–2Fe–3Al с содержанием 0.063 мас. % углерода (в).
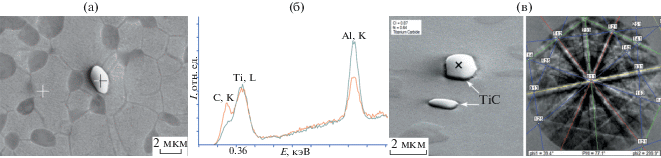
Проведено исследование частиц третьей фазы (рис.3а) методом микрорентгеноспектрального анализа химического состава. Интенсивность линии спектра частиц в области энергии, соответствующей углероду, выше, чем в близлежащей области металла (рис. 3б). Однако на дифрактограмме образца дополнительных дифракционных линий, помимо линий α- и β-фаз титана, обнаружено не было (рис. 2в). Отсутствие на полученной дифрактограмме линий, характерных для карбида титана, объясняется малой объемной долей частиц третьей фазы в структуре (менее 5%). При исследовании микроструктуры образцов методом EBSD-анализа была получена дифракционная картина с полосами Кикучи, снятая с частиц третьей фазы (рис. 3в), обнаруженные частицы третьей фазы идентифицируются как карбид титана TiC, однако химический состав требует уточнения.
Методом компьютерного моделирования структурно-фазовых превращений с помощью программы JMatPro был произведен расчет предела максимальной растворимости углерода в сплаве Ti–10V–2Fe–3Al, который составил 0.053 мас. %. Таким образом, наличие наблюдаемых частиц карбида титана в структуре сплава с содержанием 0.063 мас. % углерода подтверждается данными компьютерного моделирования.
На рис.4 представлены кривые напряжение – деформация, полученные при испытании на растяжение образцов сплава Ti–10V–2Fe–3Al. На всех кривых можно выделить три характерных участка: участок упругой деформации, участок быстрого роста напряжения при увеличении деформации, участок равномерного удлинения, на котором напряжение изменяется несущественно, и участок, соответствующий образованию шейки на образце, где напряжение начинает стремительно падать.
Характеристики прочности и пластичности сплавов Ti–10V–2Fe–3Al с содержанием углерода в диапазоне от 0.008 до 0.063 мас. % представлены в табл. 3. Полученный диапазон механических свойств является характерным для сплава Ti–10V–2Fe–3Al после указанного выше режима термообработки. Однако следует отметить, что на окончательный комплекс механических свойств сплава, помимо всего прочего, оказывает влияние маршрут деформации полуфабриката [27]. При увеличении содержания углерода от 0.008 до 0.034 мас. % (на 0.026 мас. %) предел текучести сплава увеличивается на 73 МПа (см. табл. 3). Однако при содержании углерода 0.063 мас. % предел текучести становится меньше на 30 МПа, а относительное удлинение больше на 2%, чем при 0.034 мас. % углерода, что, вероятнее всего, связано с выделением частиц карбида титана, образование которых приводит к снижению дисперсности вторичной α-фазы. Анализ данных табл. 2 позволяет говорить, что содержание углерода в первичной и вторичной α-фазе сплава с 0.063 мас. % углерода больше, чем в сплаве, содержащем 0.034 мас. % углерода.
Таблица 3.
Механические свойства сплава Ti–10V–2Fe–3Al
Содержание углерода | σ0.2, МПа | σв, МПа | δ, % |
---|---|---|---|
0.008 мас. % | 1121 | 1213 | 12.6 |
0.034 мас. % | 1194 | 1280 | 11.3 |
0.063 мас. % | 1164 | 1238 | 13.5 |
Используя уравнение Холла–Петча [28], был рассчитан предел текучести сплава в зависимости от d:
Расчетное отличие предела текучести получилось 77 и 31 МПа между исследуемыми сплавами с 0.008 и 0.034, 0.034 и 0.063 мас. % углерода, соответственно. Таким образом, изменение прочности сплава, наблюдаемое при повышении содержания углерода от 0.008 до 0.063 мас. %, связано, прежде всего, с изменением дисперсности вторичной α-фазы.
При фрактографическом исследовании поперечных изломов образцов влияние содержания углерода на изменение поверхности разрушения сплава Ti–10V–2Fe–3Al не обнаружено (рис. 5). Существенных отличий между образцами не наблюдали, изломы всех образцов классические для вязкого разрушения типа конус-чашечка с характерными равноосными ямками разрушения (рис. 5а, 5в, 5г). Частиц карбида в изломе образца с 0.063 мас. % углерода обнаружено не было. На рис. 5б представлена образующая поверхность данного образца в области шейки, на которой видны множественные ступеньки, параллельные линии скольжения на поверхности и очертания вытянутых деформированных элементов структуры, что свидетельствует о высокой пластичности металла, основным механизмом деформации которого является внутризеренное дислокационное скольжение.
Рис. 5.
Излом и образующая поверхность образца (0.063 мас. % углерода) после испытания на растяжение (а, б) и морфология изломов образцов с содержанием углерода 0.008 (в) и 0.063 мас. % (г).
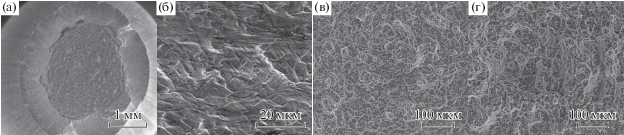
На рис. 6 представлена микроструктура в продольном сечении образца с 0.063 мас. % углерода после испытания на растяжение в области равномерной деформации (рис. 6а) и вблизи излома (рис. 6б–6г). В области локализации деформации около частиц карбида титана наблюдается образование микропор (рис. 6б–6г). Твердые частицы карбида титана имеют существенно большую жесткость в сравнении с матрицей и служат барьером для движения дислокаций, аккумулируют их и, в результате, на границе раздела с матрицей при деформации образуются микропоры. При исследовании частиц карбида титана в области равномерного удлинения образцов (рис. 6а), образования микропор не было обнаружено, что свидетельствует о достаточно большой силе адгезии частиц с матрицей. Образование микропор и их дальнейший рост при деформации зависит от большого числа параметров материала и деформации. Преимущественными местами зарождения микропор являются границы зерен и субзерен, включения, границы раздела фаз, то есть области с высокой плотностью дислокаций, [29, 30]. После значительного роста пор, при достижении определенной объемной доли, поры начинают соединяться, образуется трещина, приводящая к разрушению образца. Влияние включений и пор на особенности деформационного поведения сплава 10V–2Fe–3Al исследовано в работе [31]. Было установлено, что включения микронного размера не участвуют в процессе разрушения до определенного расстояния между частицами. Т.е. включения и поры только при определенном их распределении в материале могут формировать зародыши, которые становятся местами зарождения магистральной трещины и оказывают влияние на разрушение при деформации. В случае рассмотренного образца сплава 10V–2Fe–3Al с 0.063 мас. % углерода с частицами карбида титана в структуре, сочетание их размера и объемной доли не оказывает существенного влияния на деформационное поведение сплава Ti–10V–2Fe–3Al. Таким образом, полученные данные раскрывают механизмы влияния углерода на микроструктуру и деформационное поведение сплава Ti–10V–2Fe–3Al.
ЗАКЛЮЧЕНИЕ
Проведено исследование влияния углерода на механические свойства и структуру высокопрочного титанового сплава Ti–10V–2Fe–3Al. При повышении содержания углерода в сплаве до предела его максимальной растворимости, составившего по результатам компьютерного моделирования 0.053 мас. %, наблюдается рост прочности сплава за счет повышения дисперсности вторичной α-фазы. После исследуемого режима термообработки в структуре сплава с содержанием 0.063 мас. % углерода обнаружены частицы карбида титана по морфологии схожие с частицами первичной α-фазы, при этом дисперсность вторичной α-фазы уменьшается, что приводит к снижению прочности сплава в сравнении со сплавом, содержащим 0.034 мас. % углерода. Установленная взаимосвязь прочности с дисперсностью вторичной α-фазы хорошо описывается уравнением Холла–Петча. При деформации образцов сплава с 0.063 мас. % углерода частицы карбида титана на этапе локализации деформации служат местами зарождения микропор. Объемная доля частиц карбидов титана в структуре сплава сравнительно небольшая, поэтому частицы карбида титана не оказывают влияния на характеристики пластичности и прочности сплава Ti–10V–2Fe–3Al при испытании на растяжение.
Список литературы
Boyer R.R., Briggs R.D. The use of β titanium alloys in the aerospace industry // J. Mater. Eng. Perform. 2005. V. 14. № 6. P. 681–685.
Cotton J.D., Briggs R.D., Boyer R.R., Tamirisakandala S., Russo P., Shchetnikov N., Fanning J.C. State of the art in beta titanium alloys for airframe applications // JOM. 2015. V. 67. № 6. 1281–1303.
Titanium alloy forgings 10V–2Fe–3Al, Aerospace Material Specification, ASM4984. 1987.
Ogden H.R., Jaffee R.I. Titanium Metallurgical Laboratory Report No. 20, Ohio 1955.
Conrad H. Effect of interstitial solutes on the strength and ductility of titanium // Prog. Mater. Sci. 1981. V. 26(2). P.123–403.
Cam G., Flower H.M., West D.R.F. Constitution of Ti–Al–C alloys in temperature range 1250–750°C // Mater. Sci. Technol. 1991. V. 7. № 6. P. 505–511.
Yan M., Qian M., Kong C., Dargusch M.S. Impacts of trace carbon on the microstructure of as-sintered biomedical Ti–15Mo alloy and reassessment of the maximum carbon limit // Acta Biomater. 2014. V. 10. № 2. P. 1014–1023.
Storms E.K. Refractory Materials, V. 2. The Refractory Carbides. Academic Press, N.Y., 1967, 299 p.
Колачев Б.А., Ливанов В.А., Буханова А.А. Механические свойства титана и его сплавов. М.: Металлургия, 1974. 544 с.
Solonina O.P., Ulyakova N.M. Effect of carbon on the mechanical properties and structure of titanium alloys // Met. Sci. Heat Treat. 1974. V. 16. № 4. P. 310–312.
Szkliniarz A. Deformation of Ti–6Al–4V alloy with carbon // Solid State Phenom. – Trans Tech Publications. 2011. V. 176. P. 149–156.
Banoth R., Sarkar R., Bhattacharjee A., Nandy T.K., Nageswara Rao G.V.S. Effect of boron and carbon addition on microstructure and mechanical properties of metastable beta titanium alloys // Mater. Des. 2015. V. 67. P. 50–63.
Szkliniarz A. Effect of heat treatment on the microstructure and properties of Ti–8Al–1Mo–1V alloy with carbon addition // Solid State Phenom. 2015. V. 229. P. 131–136.
Szkliniarz A. Microstructure and Properties of Beta 21S Alloy with 0.2 wt % of Carbon // Solid State Phenom. 2016. V. 246. P. 19–24.
Zhelnina, A.V., Illarionov A.G., Trubochkin A.V. Study of interstitial impurities influence on properties of titanium alloy Ti–5Al–5V–5Mo–3Cr–1Zr // Solid State Phenomena. 2018. V. 284. P. 460–464.
Zhelnina A.V., Illarionov A.G., Kalienko M.S., Popov A.A., Schetnikov N.V. Effect of Carbon Content on the Structure and Mechanical Properties of TI–10V–2Fe–3Al Alloy // XIX International scientific-technical conference “The Ural school-seminar of metal scientists-young researchers” KnE Engineering. 2019. P. 170–175.
Zhang S., Zeng W., Gao X., Zhou D., Lai Y. Role of titanium carbides on microstructural evolution of Ti–35V–15Cr–0.3 Si–0.1 C alloy during hot working // J. Alloys Compd. 2016. V. 684. P. 201–210.
Chen Z.Q., Hu D., Loretto M.H., Wu X. Influence of 0.2 wt % C on the aging response of Ti–15–3 // Mater. Sci. Technol. 2004. V. 20. № 6. P. 756–764.
Chen L.-H., Blenkinsop P.A., Jones I.P. Effects of boron, carbon, and silicon additions on microstructure and properties of a Ti–15Mo based beta titanium alloy // Mater. Sci. Technol. 2001. V. 17. № 5. P. 573–580.
Sarkar R., Ghosal P., Muraleedharan K., Nandy T.K., Ray K.K. Effect of boron and carbon addition on microstructure and mechanical properties of Ti–15–3 alloy // Mater. Sci. Eng. A. 2011. V. 528. № 13–14. P. 4819–4829.
ASTM E8/8M–16a. Standard test methods for tension testing of metallic materials. American Society for Testing and Materials, Annual book of ASTM Standards. 2016.
TOPAS. V3, General Profile and Structure Analysis Software for Powder Diffraction Data. User’s manual. Karlsruhe, Germany: Bruker AXS, 2005.
Wain N., Hao X., Ravi G.A., Wu X. The influence of carbon on precipitation of α in Ti–5Al–5Mo–5V–3Cr // Mater. Sci. Eng. A. 2010. V. 527. № 29–30. P. 7673–7683.
Калиенко М.С., Волков А.В., Желнина А.В. Использование полнопрофильного анализа дифрактограмм для оценки дисперсности вторичной альфа фазы титана в высокопрочных титановых сплавах // Кристаллография. 2020. № 3. С. 428–433.
Hamajima T., Lütjering G., Weissmann S. Importance of slip mode for dispersion-hardened β-titanium alloys // Metall. Trans. 1973. V. 4. № 3. P. 847–856.
Kalienko M.S., Volkov A.V., Kropotov V.A., Konovalov M.A., Dukhtanov V.A. Primary α-Phase VST5553 Alloy with Lamellar Structure Properties Effect // Titanium'2011: Science and technology. Proc. 12-th Int. Conf. of Titanium. Beijing, China, 2011. P. 1303–1311.
Srinivasu G., Natraj Y., Bhattacharjee A., Nandy T.K., Nageswara Rao G.V.S. Tensile and fracture toughness of high strength b Titanium alloy, Ti–10V–2Fe–3Al, as a function of rolling and solution treatment temperatures // J. Mat. Des. 2013. V. 47. P. 323–330.
Petch N.J. The cleavage strength of polycrystals // J. Iron Steel Inst. 1953. V. 174. P. 25–28.
Terlinde G.T., Duerig T.W., Williams J.C. Microstructure, tensile deformation, and fracture in aged ti 10V–2Fe–3Al // Metall. Trans. A. 1983. V. 14. № 10. P. 2101–2115.
Hutchinson J.W., Tvergaard V. Softening due to void nucleation in metals. In: Fracture Mechanics: Perspectives and Directions (Twentieth Symposium). ASTM International. 1989. P. 61–83.
Moody N.R., Garrison W.M., Costa J.E., Smugeresky J.E. The role of defect size on the fracture toughness of powder processed Ti–10V–2Fe–3Al // Scr. Metall. 1989. V. 23. № 7. P. 1147–1150.
Дополнительные материалы отсутствуют.
Инструменты
Физика металлов и металловедение