Физика металлов и металловедение, 2021, T. 122, № 2, стр. 159-165
Влияние лазерного УФ излучения наносекундной длительности на структуру и адгезионные свойства металлов и сплавов
С. И. Миколуцкий a, *, Ю. В. Хомич a
a Институт электрофизики и электроэнергетики РАН
191186 Санкт-Петербург, Дворцовая наб., 18, Россия
* E-mail: mikolserg@mail.ru
Поступила в редакцию 26.06.2020
После доработки 17.09.2020
Принята к публикации 23.09.2020
Аннотация
Экспериментально исследовано влияние лазерного УФ излучения на структуру и адгезионные свойства таких материалов, как хромированная бронза, нержавеющие жаропрочные аустенитные хромоникелевые стали, медь. Показано, что микроструктурирование поверхности элементов диффузионно-сварного соединения позволяет улучшить его механические свойства в виде предела прочности и относительного удлинения. Приведены результаты по лазерной перфорации медной прослойки и лазерному микроструктурированию поверхности керамических заготовок, способствовавшим повышению механических свойств сварного соединения Si3N4/Cu/Si3N4.
ВВЕДЕНИЕ
Структурирование поверхности металлов в микронном и субмикронном масштабе приводит к изменению их электрических, адгезионных, тепловых, электронно-эмиссионных и излучательных свойств. Например, можно добиться увеличения прочности совместно с пластичностью в металлах и сплавах [1] или контролируемого изменения электрических свойств поверхности проводников и диэлектриков [2]. За счет микро- и наноструктурирования поверхности заготовок для диффузионной сварки разнородных материалов, широко применяемой в атомной, авиационной, космической и других областях промышленности, науки и техники, возможно улучшение механических свойств сварного шва [3] и качества соединения в целом.
Учитывая вышесказанное, большой практический интерес представляет разработка физических основ новых производительных методов создания рельефов с характерными микронными и особенно субмикронными периодами на поверхности таких материалов, как широко используемые металлические сплавы и сверхтвердые тугоплавкие керамики. Хорошо зарекомендовавшим себя инструментом для обработки таких материалов в последние десятилетия стало лазерное микро- и наноструктурирование. К его методам относятся: лазерная литография с использованием всевозможных масок и шаблонов [4, 5], интерференция двух или более лазерных пучков на поверхности или в объеме материала [6], создание эффекта ближнего поля при комбинации лазерного луча с иглой атомно-силового микроскопа [7]. Недостатками таких методов являются их многостадийность (оптическая и наносферная литография), низкая производительность (комбинация лазерного луча с зондом микроскопа), использование сложного и дорогостоящего оборудования (структурирование с помощью фемто- и пикосекундных лазеров).
Одним из перспективных методов получения микро- и нанорельефов является метод прямого лазерного наноструктурирования [8–10]. Благодаря своей простоте, производительности, возможности обрабатывать с высокой точностью достаточно большие площади поверхностей сложной формы этот метод находит широкое применение в науке и технике. При этом чем короче длина волны и длительность импульсов излучения, тем большая дисперсность структур достигается при лазерной обработке поверхностей [8]. В связи с этим целесообразно использовать лазеры, генерирующие наносекундные импульсы в УФ- и ВУФ-диапазоне [11, 12]. Обладая достаточно высокой мощностью и эффективностью они способны служить перспективным инструментом для совершенствования методов улучшения поверхностных свойств металлов и сплавов.
В настоящей работе исследовано влияние лазерного излучения УФ диапазона на структуру поверхности и адгезионные свойства таких материалов, как медь, хромированная бронза и нержавеюшая сталь, а также на механические свойства соединений, полученных при их диффузионной сварке.
МЕТОДИКА ЭКСПЕРИМЕНТОВ
В качестве источника излучения использовали импульсно-периодический Nd:YaG-лазер, генерирующий третью гармонику (λ = 0.355 мкм). Энергия в импульсе достигала 8 мДж при длительности τ = 10 нс и частоте повторения f = 100 Гц. Схема установки для микро- и наноструктурирования поверхности исследуемых материалов показана на рис. 1. Излучение от лазера 1 направляется к затвору 2. Калибровка энергии лазерного импульса осуществляется при помощи измерителя энергии 3 NOVA II c пироэлектрическим датчиком. Далее лазерное излучение попадает на полупрозрачное зеркало 4. Около 90% энергии излучения направляется на конденсор 6, а небольшая часть (~10%) поступает на приемник излучения 5. Приемник излучения входит в узел подсчета лазерных импульсов. Далее излучение направляется в формирующую оптическую систему, состоящую из конденсора 6, диафрагмы 7 и проекционной линзы 8. Система 6–8 обеспечивает изменения диаметра поперечного сечения лазерного пучка в плоскости обрабатываемой поверхности в диапазоне от 20 мкм до 500 мкм. После формирующей оптической системы излучение попадает в камеру 12 с флюоритовыми окнами 9 и 10, где закрепляется образец 11. Камера вместе с образцом устанавливается на трехкоординатном столике 19, состоящем из трех моторизованных подвижек. Данная экспериментальная установка позволяла обрабатывать образцы в различных режимах: при неподвижном пятне, при сканировании лазерного пучка по поверхности образца с определенной скоростью, а также в режиме сверления микроотверстий при перемещении пучка от одного пятна к другому.
Рис. 1.
Схема установки для лазерного микроструктурирования: 1 – Nd:YAG-лазер; 2 – затвор; 3 – калиброванный измеритель энергии; 4 – полупрозрачное зеркало; 5 – приемник излучения, 6 – конденсор; 7 – диафрагма; 8 – проекционная линза; 9, 10 – флюоритовые окна; 11 – облучаемый образец; 12 – газовая камера, 13, 14 – вентили; 15 – вакуумный насос; 16 – манометр, 17 – вентиль, 18 – газовый баллон, 19 – трехкоординатный подвижный столик.
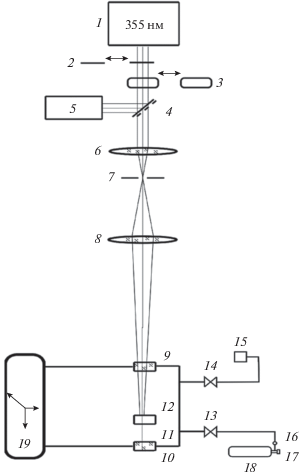
В основном, для экспериментов использовали образцы цилиндрической формы высотой 10 мм и диаметром 15 мм. Образцы из CuCr-бронзы и нержавеющей стали подвергали только механической обработке, вследствие чего на необлученной поверхности наблюдали борозды шириной до нескольких десятков микрометров и высотой около 10 мкм, на склонах которых можно было различить микроострия и структуры в виде выступов с размерами от 1 до 5 мкм. Дополнительную полировку поверхности не проводили, так как метод прямого лазерного микро- и наноструктурирования при достаточной энергии позволял удалять незначительные дефекты рельефа и обрабатывать поверхность при грубой подготовке “из-под станка”, т.е. перепадах высот рельефа около 10 мкм. Медные прокладки для сверления микроотверстий были изготовлены из медной фольги марки М1 толщиной 100 мкм.
Обработанные поверхности образцов исследовали с помощью профилометра NewView 7300 (ZYGO Corp.), сканирующего электронного микроскопа (СЭМ) Phenom Pro и атомно-силового микроскопа (АСМ) Alpha 300 (WITec).
Для определения адгезионных свойств исследуемых образцов проводили их диффузионную сварку, осуществляемую либо в условиях горячего изостатического прессования, либо посредством сварочной камеры с пневмоцилиндром, который может развивать усилия до 5500 кН, и нагревом свариваемых деталей токами высокой частоты. После чего проводили механические испытания полученных соединений.
РЕЗУЛЬТАТЫ ИСПЫТАНИЙ
Обработку образцов из CuCr-бронзы проводили лазерным пучком диаметром около 200 мкм при сканировании пучка по поверхности со скоростью перемещения по горизонтали от 0.5 до 1 мм/с. Так как частота следования импульсов излучения составляла 100 Гц, то смещение лазерного пятна за время между импульсами составляло величину от 10 до 20 мкм. Смещение пучка по вертикали при движении в обратном направлении также составляло около 15 мкм. При сравнительно малой скорости сканирования на каждый участок облучаемой поверхности приходилось более 100 импульсов. Плотность энергии в импульсе варьировалась от 0.2 до 1.7 Дж/см2.
Исследование обработанной наносекундными лазерными импульсами поверхности бронзы выявило образование шарообразных субмикронных структур. На рис. 2 приведено СЭМ-изображение поверхности CuCr-бронзы после сканирования лазерным пучком с плотностью энергии в импульсе 0.85 Дж/см2. На рис. 2а видны светлые участки продольных холмообразных структур, расположенных на расстоянии нескольких микрометров друг от друга. На их вершинах наблюдаются шарообразные структуры. При ближайшем рассмотрении (рис. 2б) они напоминают застывшие капли на ножках-подставках. Верхняя часть элемента субмикронной структуры сферическая, ее диаметр составлял около 600 нм. У ножки, на которой расположена капля, длина примерно 1 мкм. Диаметры конической ножки у разных структур отличаются и лежат в диапазоне от 350 нм (почти в 2 раза меньше диаметра вершины) до 600 нм, что примерно равно диаметру верхней части элемента структуры.
Рис. 2.
СЭМ-изображение поверхности CuCr-бронзы после обработки сканирующим пучком наносекундных импульсов с плотностью энергии 0.85 Дж/см2: (а) общий вид; (б) увеличенное изображение.
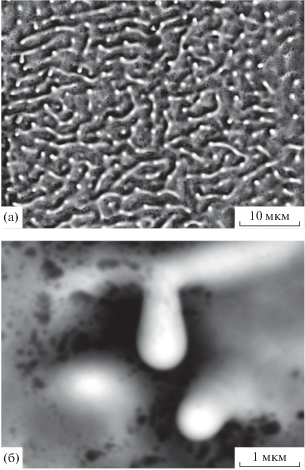
При достаточно низких плотностях энергии около 0.3 Дж/см2 количество шарообразных структур на единицу площади невелико – несколько структур на 100 мкм2. С ростом плотности энергии в импульсе пространственная плотность таких структур увеличивается. Причем наибольшая пространственная плотность новых структур около 20 на 100 мкм2 наблюдается при плотностях энергии 0.85 Дж/см2 (рис. 2а). При более высоких плотностях энергии количество таких структур уменьшается, и уже выше 2 Дж/см2 они практически не заметны. Причем наблюдается некоторая корреляция между количеством шарообразных структур и изменением концентрации хрома в приповерхностном слое бронзы, что является темой для дальнейших исследований.
При обработке стали марки 12Х18Н10Т (в % маc. C < 0.12; Si < 0.8; Mn < 2; Ni 9–11; S < 0.02; P < < 0.035; Cr 17–19; Cu < 0.3; Ti 0.4–1) при том же диаметре лазерного пучка, частоте следования импульсов и схожей механической обработке наиболее развитая поверхность наблюдалась при плотностях энергии 1.1 Дж/см2 (рис. 3а). При скорости сканирования лазерным пучком 1 мм/с наблюдается сильное оплавление поверхности. Борозды от механической обработки в процессе оплавления начинают разбиваться, образуются круглые холмообразные островки с поперечными размерами от 5 до 10 мкм и высотой приблизительно 500 нм (рис. 3а).
Рис. 3.
Изображение поверхности стали 12Х18Н10Т после обработки сканирующим пучком Nd:YAG лазера при плотности энергии 1.1 Дж/см2: (а) скорость сканирования 1 мм/с; (б) скорость сканирования 0.25 мм/с.
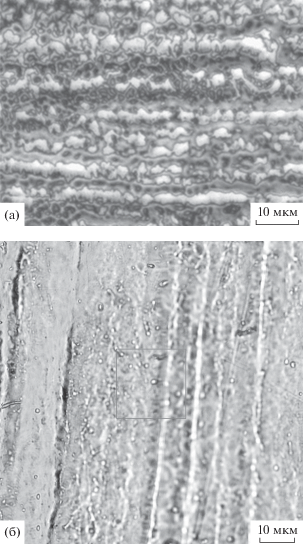
При понижении скорости сканирования до 0.25 мм/с при той же плотности энергии 1.1 Дж/см2 наблюдается прежний рельеф в виде борозд шириной около 10 мкм (рис. 3б), однако многочисленных следов оплавления, как на рис. 3а, не заметно. Это, скорей всего, является следствием дальнейшего оплавления и удаления части материала с поверхности образца.
На рис. 3б также видно несколько одиночных структур округлой формы диаметром 1 мкм, которые похожи на шарообразные структуры, возникающие при обработке бронзы. Видно, что образование таких округлых структур происходит вдоль кривых червеобразных борозд, но их пространственная плотность по сравнению со структурами на бронзе не высока.
Далее для сравнения адгезионных свойств обработанных лазерным излучением поверхностей бронзы и нержавеющей стали были получены их диффузионно-сварные соединения в условиях горячего изостатического прессования. Рассматривали три группы заготовок: без обработки (1), с обработанной поверхностью стали (2), обработанными поверхностями стали и бронзы (3). Сварку проводили при одинаковых параметрах в камере высокого давления в течение 3 ч. Из сваренной заготовки вырезали не менее трех аналогичных образцов и испытывали их на статическое растяжение при комнатной температуре. Результаты испытаний представлены в табл. 1.
Таблица 1.
Результаты механических испытаний диффузионно-сварных соединений сталей и бронзы
Обработка | Предел прочности, МПа |
---|---|
1 | 242 |
2 | 240 |
3 | 263 |
4 | 416 |
5 | 474 |
Как видно, предел прочности сварного соединения необработанных стали и хромированной бронзы в среднем составляет 242 МПа, причем обработка только стальной заготовки (2) не дала приращения предела прочности сварного шва – наблюдалось некоторое уменьшение с 242 до 240 МПа, которое, впрочем, можно отнести к погрешностям измерений. При обработке же одновременно двух поверхностей (3) качество сварного соединения улучшается – предел прочности увеличивается на 9% – с 242 до 263 МПа, оставляя место для дальнейших исследований, подборки оптимальных режимов лазерной обработки и диффузионной сварки. Также положительный эффект наблюдается при диффузионной сварке сталей марок 12Х18Н10Т и 09Х17Н (в % мас. C < 0.09; Si 0.4–0.8; Mn < 0.5; Ni 0.8–1.2; S < 0.025; P < 0.03; Cr 15.6–17.6; Cu < 0.25). В табл. 1 представлены значения предела прочности сварных соединений при необработанных поверхностях сталей (4) и обработанных лазерным излучением с плотностью энергии около 2 Дж/см2 (5). Во втором случае предел прочности на 14% выше.
Помимо обработки материалов в режиме сканирования экспериментальная установка позволяет проводить сверление микроотверстий в металлической фольге с определенными диаметром и расстоянием между отверстиями. Такое микроструктурирование приводит к интенсивной деформации металла прокладки, снижает сварочные давления и повышает скорость формирования физического контакта при диффузионной сварке керамик или разнородных материалов с применением металлической прослойки.
Для экспериментов по соединению керамики из нитрида кремния были использованы прокладки, изготовленные из медной фольги марки М1 толщиной 100 мкм. В них просверлили отверстия диаметром около 30 мкм с расстоянием между отверстиями в 125 мкм (рис. 4). Также для улучшения конструкционной прочности соединения установка позволила дополнительно обработать керамические поверхности: по прямоугольной сетке 8 × 8 мм с шагом 1 мм были сформированы углубления диаметром 0.1 мм и глубиной 2 мм.
Для сравнения механических свойств диффузионно-сварных соединений, полученных посредством сварочной камеры с пневмоцилиндром, проводили экспериментальные исследования материалов после различных вариантов обработки: со сплошными медными прокладками (1); с микроструктурированными медными прокладками (2); с микроструктурированными медными прокладками и облученной поверхностью керамики (3). Результаты представлены в табл. 2.
Таблица 2.
Результаты механических испытаний диффузионно-сварных соединений керамики посредством медной прокладки
Обработка | Предел прочности, МПа | Относительное удлинение, % |
---|---|---|
1 | 61 | 22 |
2 | 80 | 32 |
3 | 88 | 33 |
При температуре сварки 1000–1050°С использование сплошной медной прослойки дает предел прочности полученного соединения около 61 МПа, при этом относительное удлинение составляет 22% (табл. 2).
При применении перфорированных прокладок прочностные характеристики составили 77–82 МПа. Дополнительное нанесение отверстий на керамические поверхности дало увеличение прочности до 85–91 МПа. Относительное удлинение для второй и третьей групп образцов также увеличивается до 32 и 33%, соответственно. Из этого можно сделать вывод, что предварительная лазерная обработка поверхностей элементов соединения существенно улучшает механические свойства шва при диффузионной сварке.
ОБСУЖДЕНИЕ РЕЗУЛЬТАТОВ
Выявленные на поверхности хромированной бронзы при воздействии наносекундного излучения Nd:YaG-лазера структуры в виде субмикронных сферических капель на ножках располагаются на характерном расстоянии между ними 2–3 мкм (рис. 2). Их развитие может быть обусловлено совместным действием плавления и испарения в определенном диапазоне плотностей энергии выше порога плавления. Модуляция рельефа поверхности, к примеру, в виде капиллярных волн с характерными для металлов и сплавов микронными периодами [13] приводит к соответствующей модуляции температуры и испарительного давления вдоль поверхности в виде некоторой двумерной квазипериодической решетки. Расплав при таком неоднородном испарении выдавливается вдоль поверхности в места минимумов испарительного давления, где и происходит выброс жидких струй расплава преимущественно в направлении перпендикулярном поверхности. При этом силы поверхностного натяжения приводят к формированию сферических капель на концах этих струй на заключительной стадии их развития, когда заканчивается действие импульсного испарительного давления и начинается затвердевание расплава [14].
Стоит отметить, что такой микрорельеф похож на микроструктуры, получаемые при облучении поверхности металлов и сплавов фемтосекундными лазерными импульсами [15]. При такой длительности импульсов и мощности энергии образование подобных структур объясняется вспениванием приповерхностного слоя, расширением и его отколом с дальнейшим формированием наноструктур при затвердевании расплава [15]. Для наносекундных длительностей импульсов вопрос о механизмах формирования шарообразных микроструктур остается открытым.
Улучшение механических свойств (увеличение предела прочности, табл. 1) сварного соединения из стали и бронзы, вероятно, вызвано уменьшением среднего размера зерен, сформировавшихся в процессе предварительной лазерной обработки. Это существенным образом влияет на кинетику формирования твердофазного соединения, ускоряя схлопывание микропор [16], и позволяет уменьшить температуру процесса сварки. Известно, что коэффициент диффузии по границам зерен может на порядки превышать его значения в объеме зерен [16]. Создание поверхностных наноструктур может улучшить качество соединения как за счет большей плотности сетки границ зерен, обеспечивающих более активную диффузию в материале, так и в результате облегченной пластической деформации ультрамелкозернистого материала. Второй причиной улучшения механических свойств сварного соединения может являться более равномерное распределение деформации в соединениях с предварительной лазерной обработкой поверхности, приводящее к более эффективному диффузионному схлопыванию пор в зоне соединения.
Изменение напряженно-деформированного состояния прокладки и прилегающей к ней области также приводит к улучшению механических свойств сварного соединения керамика–металл–керамика при использовании микроструктурированных прокладок по сравнению со сплошными.
Исследования влияния перфорированных прокладок на кинетику формирования физического контакта металл–керамика и прочностные характеристики полученных сварных соединений показали: металл прокладки подвержен деформации по схеме “давление + сдвиг” и деформируется с высокой скоростью (3.5 × 10–2 мин–1). Такое поведение обусловлено изменением напряженно-деформированного состояния перфорированной прокладки (по сравнению со сплошной) в процессе её деформации [17, 18]. В этом случае более значительные сдвиговые деформации возникают во всём объёме металла прокладки, и распределены они более равномерно по контактной поверхности, чем в случае сплошной прокладки, где эти деформации развиты лишь в краевой области. Выбранные размеры и шаг отверстий обеспечили трансформацию перфорированной прокладки в процессе сварки в сплошную, что увеличивает прочность сварного соединения вследствие снижения послесварочных остаточных напряжений и контактного упрочнения пластичной прокладки [17]. Кроме того, повышение химической активности материала прокладки и его взаимодействие со свариваемым материалом и вышеописанные факторы позволили повысить предел прочности шва на 30% (табл. 2) при использовании перфорированной прокладки.
Еще одна причина повышения прочности сварного соединения по мнению авторов связана с появлением армированных каналов в керамике. Если в контактной поверхности керамики создать систему отверстий, то при сварке металл прокладки начнет затекать в эти отверстия вследствие развития деформаций. Постепенно отверстия заполнятся металлом, и приконтактная зона керамического материала будет представлять собой “композит” – “хрупкая матрица–пластичные волокна”.
ЗАКЛЮЧЕНИЕ
Проведены экспериментальные исследования влияния УФ-лазерного излучения на структуру и адгезионные свойства стали, меди и хромированной бронзы. В процессе обработки поверхности бронзы наносекундными импульсами Nd:YaG-лазера выявлены шарообразные структуры диаметром около 500 нм на конических ножках высотой 1 мкм. При этом определен диапазон плотностей энергий (0.3–2 Дж/см2), в котором формируются данные структуры, и установлена зависимость их пространственной плотности от энергии излучения. Применение таких структур возможно в области формирования электрогидродинамических потоков, а также изменения гидрофильных свойств поверхностей.
Показано, что микроструктурирование элементов диффузионно-сварного соединения из нержавеющих сталей и хромированной бронзы позволяет улучшить его механические свойства в виде увеличения предела прочности на 15%. Помимо этого лазерная перфорация медных прослоек в соединении керамика-металл-керамика позволяет интенсифицировать пластическую деформацию прокладки, тем самым увеличивая предел прочности соединения до 77–82 МПа, а величину относительного удлинения до 28–38% по сравнению с 53–75 МПа и 18–30% для сплошных прокладок; причем в случае сочетания микроструктурированных и прокладок и поверхности керамики достигается прочность в среднем в 1.45 раза больше, чем прочность соединения со сплошной прокладкой и необработанной поверхностью керамики при одновременном увеличении средних значений относительного удлинения почти на 50%.
Таким образом, лазерное микроструктурирование позволяет снизить основные параметры процесса сварки, при которых формируются высокопрочные соединения, а именно время, давление и температуру, что в целом открывает возможность улучшения качества соединения металлических сплавов при диффузионной сварке за счет лазерной обработки поверхностей заготовок.
Работа выполнена при поддержке Министерства науки и высшего образования РФ в рамках темы № 0057-2019-0005.
Список литературы
Matsui I., Kawakatsu T., Takigawa Y., Uesugi T., Higashi K. Fabrication of bulk nanocrystalline Fe–Ni alloys with high strength and high ductility by an electrodeposition // Mater. Let. 2014. V. 116. P. 71–74.
Lu L., Shen Y., Chen X., Qian L., Lu K. Ultrahigh strength and high electrical conductivity in copper // Science. 2004. V. 304. P. 422–426.
Хазгалиев Р.Г., Имаев М.Ф., Мулюков Р.Р., Сафин Ф.Ф. Модифицирование поверхности прослойки никеля для делокализации деформации при сварке давлением образцов титанового сплава и нержавеющей стали // Письма о материалах. 2015. Т. 5(2). С. 133–137.
Сейсян Р.П. Нанолитография в микроэлектронике // ЖТФ. 2011. Т. 81(8). С. 1–14.
Hong M.H., Wang Z.B., Lukyanchuk B.S., Tan L.S., Chong T.C. From transparent particle light enhancement to laser nanoimprinting // J. Laser Micro/Nanoengin. 2006. V. 1. P. 61–66.
Marconi M.C., Wachulak P.C. Extreme ultraviolet lithography with table top lasers // Prog. Quantum. Electron. 2010. V. 34. P. 173–190.
Lu Y.F., Hu B., Mai Z.H., Wang W.J., Chim W.K., Chong T.C. Laser-SPM based nanoprocessing of electronics materials // Jap. J. Appl. Phys. 2001. V. 40. P. 4395–4398.
Хомич В.Ю., Шмаков В.А. Механизмы и модели прямого лазерного наноструктурирования материалов // УФН. 2015. Т. 185. С. 489–499.
Ёлкин В.Н., Малинский Т.В., Миколуцкий С.И., Хасая Р.Р., Хомич Ю.В., Ямщиков В.А. Влияние облучения наносекундными лазерными импульсами на структуру поверхности сплавов металлов // ФХОМ. 2016. № 6. С. 5–12.
Mikolutskiy S.I., Khasaya R.R., Khomich Yu.V., Yamshchikov V.A. Formation of various types of nanostructures on germanium surface by nanosecond laser pulses // J. Phys. Conf. Ser. 2018. V. 987. P. 012007.
Вартапетов С.К., Жигалкин А.А., Лапшин К.Э., Обидин А.З., Хомич В.Ю., Ямщиков В.А. Исследование электроразрядного ВУФ лазера на молекулярном фторе // Квантовая электроника. 2006. Т. 36. № 5. С. 393–398.
Хомич В.Ю., Ямщиков В.А. Основы создания систем электроразрядного возбуждения мощных CO2-, N2- и F2-лазеров. М.: Физматлит, 2014. 164 с.
Ахманов С.А., Емельянов В.И., Коротеев Н.И., Семиногов В.Н. Воздействие мощного лазерного излучения на поверхность полупроводников и металлов: нелинейно-оптические эффекты и нелинейно-оптическая диагностика // УФН. 1985. Т. 147. С. 675–745.
Вашуков Ю.А., Демичев С.Ф., Еленев В.Д., Малинский Т.В., Миколуцкий С.И., Хомич Ю.В., Ямщиков В.А. Лазерная обработка поверхности металлических сплавов для диффузионной сварки // Прикладная физика. 2019. № 1. С. 82–87.
Ashitkov S.I., Komarov P.S., Ovchinnikov A.V., Struleva E.V., Zhakhovskii V.V., Inogamov N.A., Agranat M.B. Ablation and nanostructuring of metals by femtosecond laser pulses // Quantum Electron. 2014. V. 44. № 6. P. 535–539.
Мухаметрахимов М.Х. Твердофазная свариваемость листов титанового сплава ВТ6 при пониженной температуре // Письма о материалах. 2015. Т. 2. № 5. С. 194–197.
Лямин Я.В. Модель трансформации перфорированной прокладки в сплошную при диффузионной сварке материалов // Вестник ПГТУ. Машиностроение, материаловедение. 2010. Т. 12. С. 25–31.
Перевезенцев В.Н., Пупынин А.С., Свирина Ю.В. Анализ влияния пластической деформации на диффузионные свойства границ зерен // ФММ. 2005. Т. 100. № 1. С. 17–23.
Дополнительные материалы отсутствуют.
Инструменты
Физика металлов и металловедение