Физика металлов и металловедение, 2021, T. 122, № 3, стр. 306-313
Синтез и свойства композиционного материала на основе твердого раствора (V,Cr)AlC
А. Е. Сычёв a, *, В. А. Горшков a, А. В. Карпов a, Н. В. Сачкова a, И. Д. Ковалёв a, А. Ф. Беликова a
a Институт структурной макрокинетики и проблем материаловедения им. А.Г. Мержанова РАН
142432 Черноголовка, ул. Академика Осипьяна, 8, Россия
* E-mail: sytschev@ism.ac.ru
Поступила в редакцию 17.07.2020
После доработки 18.11.2020
Принята к публикации 18.11.2020
Аннотация
Впервые методом самораспространяющегося высокотемпературного синтеза получен материал на основе твердого раствора (VCr)2AlC с использованием реакционной смеси порошков оксидов ванадия(V) и хрома(III) с алюминием и углеродом (графитом). Полученный материал исследован методами рентгенофазового и микроструктурного анализов. Показано, что в продукте присутствуют также карбидные, интерметаллидные соединения ванадия и хрома. Наличие этих фаз связано, по-видимому, с неравновесностью процесса синтеза из-за малого времени “жизни” расплава, быстрым его остыванием и кристаллизацией. Синтезированный материал является электрическим проводником, демонстрирующим металлический характер проводимости во всем измеренном диапазоне изменения температуры 300–1300 К. Удельное электросопротивление композиционного материала на основе твердого раствора (Cr,V)2AlC при комнатной температуре составляет 1.14 мкОм × м, что выше удельного электросопротивления материалов на основе МАХ-фаз Cr2AlC и V2AlC. Микротвердость синтезированного материала равна 6.9 ГПа.
ВВЕДЕНИЕ
Многослойные тройные соединения Mn+ 1AXn (где M – это переходный металл; A – элемент подгруппы A, X – C или N, а n = 1–3), также называемые MAX-фазами, представляют собой слоистые карбиды или нитриды с кристаллической структурой гексагональной симметрии. Эти материалы сочетают достоинства металлов и керамики: имеют тепловую и электрическую проводимость, низкий удельный вес, высокий модуль упругости, низкий коэффициент теплового расширения, высокую теплостойкость и жаростойкость [1–5]. Методом самораспространяющегося высокотемпературного синтеза (СВС) были синтезированы композиционные материалы на основе МАХ-фазы Cr2AlC из смесей порошков оксидов хрома с алюминием и углеродом [6] и на основе МАХ-фазы V2AlC из смесей порошков оксидов ванадия(V) и (IV) с алюминием и углеродом (графитом) [7]. Структура и свойства МАХ-фаз могут быть изменены и соответствующим образом модифицированы введением дополнительных элементов. Принимая во внимание, что Cr имеет на один валентный электрон больше, чем V, и то, что Cr и V имеют практически одинаковый атомный радиус, вызывает интерес получение твердых растворов (CrxV1 – x)2AlC. Упрочнение твердого раствора заменой V на Cr было предсказано в [8, 9]. Создание материалов на основе многокомпонентных соединений со структурой МАХ-фазы путем изоморфного замещения одного элемента другим может привести к изменению физико-механических и теплофизических свойств материала. Стабильность MAX-фаз (Crx,V1 – x)2AlC, представляющих интерес для различных магнитных и высокотемпературных применений, была изучена с использованием первопринципных расчетов на основе теории функционала плотности [10]. Впервые твердые растворы (Cr0.75,V0.25)2AlC, (Cr0.5,V0.5)2AlC и (Cr0.25,V0.75)2AlC были получены методом отжига порошков Cr2AlC и V2AlC, смешанных в советующих пропорциях, при 1273K в течении 170 ч [11].
В работе [12] четырехкомпонентные соединения (V0.5Cr0.5)3AlC2, (V0.5Cr0.5)4AlC3 и (V0.5Cr0.5)5Al2C3 были синтезированы методом реакционного горячего прессования из порошков V, Cr, Al и графита при температуре 1823K в течение 60 мин с приложенным давлением 30 МПа. Авторы считают, что (V0.5Cr0.5)3AlC2 является доминирующей фазой с незначительным количеством (V0.5Cr0.5)4AlC3. MAX-фазы в системе (Crx, V1 – x)n + 1AlCn были синтезированы методом реакционного спекания и горячего изостатического прессования элементарных порошков при температурах от 1673 до 1873 K [13]. Для n = 1 был найден полный диапазон (0 ≤ x ≤ 1) твердых растворов; для n = 2 и 3 диапазоны растворимости составляли 0.25 ≤ x ≤ 0.75 и 0 ≤ x ≤ 0.5 соответственно. Соединения (Cr0.5V0.5)n + 1AlCn (где n = 1, 2, 3) были также синтезированы традиционным методом порошковой металлургии при температурах 1673 и 1773 K в течении 1–3 ч [14]. При n = 1 было обнаружено полное разупорядочение ванадия и хрома в металлических слоях. Преимущественно однофазные и практически плотные твердые растворы (Cr1 –xVx)2AlC (где x = 0, 0.1, 0.25 и 0.5) синтезировали методом импульсно-разрядного спекания (PDS) с использованием порошков Cr, V, Al и C в качестве исходных материалов [15]. Соединения, содержащие ванадий, имеют размер около 9 мкм. Микроструктура состоит преимущественно из равноосных зерен Cr2AlC, которые равномерно распределены по объему, что аналогично предыдущим результатам [6, 12]. С увеличением содержания V форма зерен Cr2AlC меняется от равноосной к удлиненной. МАХ-твердый раствор (Cr,V)2AlC с добавлением Al2O3 был получен в процессе алюминотермического восстановления в режиме самораспространяющегося высокотемпературного синтеза из смеси исходных реагентов Сr2O3/V2O5/Аl/Al4C3 [16, 17]. Экзотермичность процесса горения в этом случае повышалась за счет увеличения количества V2O5 для более полного замещения хрома ванадием, что не только увеличивало температуру горения и скорость реакции, но и облегчало формирование твердых растворов. Образование (Cr1 – yVy)2AlC/Al2O3 было достигнуто при y = = 0.1–0.7. Синтезированный (Cr, V)2AlC имеет слоистую микроструктуру, характерную для тройного MAX-карбида.
В продолжение исследований синтеза МАХ-фаз Cr2AlC [6] и V2AlC [7] в настоящей работе проведено исследование особенностей структуро- и фазообразования и свойств композиционного материала в системе V–Cr–Al–C, синтезированного методом самораспространяющегося высокотемпературного синтеза с восстановительной стадией из порошков V2O5, Cr2O3, Al и графита.
МАТЕРИАЛЫ И МЕТОДЫ ИССЛЕДОВАНИЯ
В проведенных экспериментах использовали смеси порошков оксидов ванадия(V) и хрома(III) марки “ЧДА”, алюминия марки АСД-1 и углерод в виде графита марки ПГ. Расчет соотношений компонентов исходных смесей производили, используя следующие химические реакции:
(1)
${\text{3}}{{{\text{V}}}_{{\text{2}}}}{{{\text{O}}}_{5}} + 13{\text{Al}} + 3{\text{C}} = 3{{{\text{V}}}_{2}}{\text{AlC}} + 5{\text{A}}{{{\text{l}}}_{{\text{2}}}}{{{\text{O}}}_{3}},$(2)
${\text{C}}{{{\text{r}}}_{{\text{2}}}}{{{\text{O}}}_{3}} + 3{\text{Al}} + {\text{C}} = {\text{C}}{{{\text{r}}}_{{\text{2}}}}{\text{AlC}} + {\text{A}}{{{\text{l}}}_{{\text{2}}}}{{{\text{O}}}_{3}},$а также их сочетание в расчете на конечный целевой продукт – твердый раствор (Cr1 – хVх)2AlC.
Расчет содержания каждого компонента (ai) осуществляли по формуле: ai = mi/M, где mi – молекулярный вес компонента, М – молекулярный вес всех компонентов смеси.
Перед проведением экспериментов все реагенты просушивали в сушильном шкафу марки СНОЛ в течение 3 ч при температуре 60°С. Исходные смеси массой 30 г готовили вручную в фарфоровой ступке. При изучении закономерностей синтеза и процессов формирования состава и микроструктуры целевых продуктов реакционные смеси сжигали в кварцевых тиглях диаметром 23–25 мм, высотой 55 мм.
Эксперименты проводили в СВС-реакторе объемом 3 л по методике, описанной в [6, 7]. Для проведения экспериментов СВС-реактор герметизировали, создавали избыточное давление (Рн = 4 МПа) инертного газа (Ar) и воспламеняли исходную смесь с помощью металлической спирали из молибденовой проволоки путем подачи на нее напряжения U = 30 В. Процесс горения изучали визуально, а также с помощью видеокамеры. Среднюю линейную скорость горения рассчитывали как Нсм/tг, где Нсм – высота смеси, tг – время сгорания всего образца. Выход целевого продукта в слиток (η1) относительно массы смеси рассчитывали по формуле: η1 = Мсл/Мсм × 100%, выход целевого продукта в слиток (η2) относительно расчетного значения – η2 = ${{{{М}_{{{\text{сл}}}}}} \mathord{\left/ {\vphantom {{{{М}_{{{\text{сл}}}}}} {М_{{{\text{сл}}}}^{{{\text{расч}}}}}}} \right. \kern-0em} {М_{{{\text{сл}}}}^{{{\text{расч}}}}}}$ × 100%, а потерю массы (диспергирование) при горении: η3 = (Мн – Мк)/Мн × 100%, где Мсл – масса целевого продукта; Мсм – масса исходной смеси, $М_{{{\text{сл}}}}^{{{\text{расч}}}}$ – масса слитка, рассчитанная из состава смеси; Мн – начальная масса; Мк – конечная масса.
Синтезированный материал исследовали методами рентгеновской дифрактометрии (на дифрактометре ДРОН-3М (излучение CuKα) с шагом по углу 0.02° и временем экспозиции 1 с), электронной микроскопии (на автоэмиссионном сканирующем электронном микроскопе сверхвысокого разрешения Zeiss Ultra plus на базе Ultra 55). Измерения удельного электросопротивления проводили на образцах прямоугольного сечения размером 1.5 × 1.5 × 15.0 мм3 стандартным четырехконтактным методом на постоянном токе по методике, описанной в [6, 7].
Для снятия возможных остаточных напряжений исследуемые образцы перед измерениями подвергали термообработке в вакууме в течение 30 мин при температуре 1000 К. Следует отметить, что значения электросопротивления образцов, измеренные при комнатной температуре до и после термообработки, совпадали. Все измерения проводили в вакууме 2 × 10–3 Па, скорость изменения температуры в диапазоне 300–1300 К при цикле нагрев/охлаждение составляла 6 К/мин.
Измерения микротвердости проводили на приборе ПМТ-3 при нагрузке на индентор 50 г.
РЕЗУЛЬТАТЫ ЭКСПЕРИМЕНТОВ И ОБСУЖДЕНИЕ
В процессе горения исходной смеси со стехиометрическим соотношением реагентов, рассчитанным из формулы (1), было обнаружено, что она горит в нестационарном режиме с искривленным фронтом и сильным диспергированием (выбросом) конечных продуктов из реакционной формы. При горении исходной смеси со стехиометрическим соотношением реагентов, рассчитанным из формулы (2), было обнаружено, что после воспламенения смеси через 10–12 мм происходила остановка фронта горения.
Для синтеза целевого продукта в виде твердого раствора в экспериментах использовали смеси, соотношение реагентов в которых рассчитывали согласно уравнений (1) и (2) при различных их сочетаниях в расчете на твердый раствор (CrхV1 – х)2AlC. Такие составы горят с полной сепарацией целевой (Cr–V–Al–C) и оксидной фазы (Al2O3) при х = 0.1–0.6.
Оптимальным составом шихты по выходу целевого продукта в отдельный слиток является смесь с соотношением реагентов, рассчитанным на состав (Cr0.5V0.5)2AlC. Такая смесь горит в стационарном режиме с практически плоским фронтом распространения волны горения. Расчетные составы продуктов и параметры синтеза для смесей различного состава приведены в табл. 1.
Таблица 1.
Расчетные составы продуктов и параметры синтеза
№ | Смесь | Расчетный состав целевой фазы | Uг, см/с | η1, вес. % | η2, вес. % | η3, вес. % |
---|---|---|---|---|---|---|
1 | (I) | V2AlC | 4.5 | 30.2 | 83.2 | 7.8 |
2 | (II) | Cr2AlC | – | 0 | 0 | 0 |
3 | (III)* | (Cr0,5V0,5)2AlC | 0.5 | 45.0 | 98.3 | 1.7 |
Проведенные эксперименты показали, что:
– реакционная смесь, состав которой рассчитывали из химической формулы (1), является высококалорийной. Горение протекает с высокой скоростью, резким приростом давления в реакторе и большим выбросом (диспергированием) конечных продуктов из формы. Из-за больших потерь массы конечных продуктов (η3 = 7.8%) выход целевого продукта относительно массы смеси (η1 = = 30.2%) и относительно расчетного значения (η2 = = 83.7%) сравнительно небольшой (см. табл. 1, № 1);
– реакционная смесь, состав которой рассчитывали из химической формулы (2), является низкокалорийной. После воспламенения через 10–12 мм происходит остановка (затухание) фронта горения (см. табл. 1, № 2);
– реакционная смесь, состав реагентов которой рассчитывали согласно сочетанию уравнений (1) и (2) в расчете на получение (Cr0.5V0.5)2AlC, горит в стационарном режиме с практически плоским фронтом распространения волны горения и небольшим диспергированием.
После прохождения фронта горения происходит разделение (сепарация) конечных продуктов на два слоя: нижний – металлоподобный (Cr–V–Al–C), верхний – оксидный (Al2O3). Типичный внешний вид слитков представлен в работе [7]. При этом потеря массы конечных продуктов (η3 = 1.7%) значительно ниже, чем для смеси № 1, а выход целевого продукта относительно массы смеси (η1 = = 45.0%) и относительно расчетного значения (η2 = 98.3%) значительно выше (см. табл. 1, № 3).
По данным рентгенофазового анализа, в синтезируемом материале присутствуют 3 фазы – основная фаза (Cr,V)2AlC, а также вторичные фазы – интерметаллид Al8Cr5 (PDF 71-140) и двойной карбид Cr0.6V0.4C (PDF 89-7256) (рис. 1).
На рис. 2 представлены микроструктуры поверхности разрушения образца на основе твердого раствора (Cr,V)2AlC. На изломе хорошо видны плоскости спайности с типичными слоистыми наноламинатными структурами с толщиной слоев менее 20 нм (рис. 2б, 2в). Также наблюдаются внутризеренные и межзеренные трещины (рис. 2д, 2е), свидетельствующие о проявлении обоих режимов разрушения в материале на основе (Cr,V)2AlC.
Рис. 2.
Морфологическое разнообразие микроструктуры поверхности излома композиционного материала на основе твердого раствора (Cr,V)2AlC.

На поверхности излома наблюдаются характерные для МАХ-фаз полосы изгиба, ступенчатого расслоения и пластинчатой деформации (рис. 2д).
Процесс структуро- и фазообразования протекает в результате СВС-реакции с восстановлением V2O5 и Cr2O3 (формулы (1) и (2)) и созданием фазового равновесия интерметаллидов Al–Cr и V–Al с последующей реакцией с углеродом и образованием МАХ-фаз Cr2AlC и V2AlC [6, 7], которые в свою очередь взаимодействуют с образованием твердого раствора (Cr,V)2AlC. Микроструктурные исследования показали, что зерна твердого раствора (Cr,V)2AlC имеют равноосную (дискообразную) (рис. 2г) и удлиненную (игольчатую) (рис. 2е) форму.
Интересно отметить, что распределение Cr и Al, приведенное на концентрационных профилях по сечению образца, изменяется противофазно по отношению к распределению V (рис. 3). Увеличение интенсивностей концентрационного профиля V на фоне уменьшения концентрации Cr и Al особенно заметно в зернах двойного карбида Cr0.6V0.4C.
Рис. 3.
Характерный концентрационный профиль элементов на поверхности образца (вдоль линии сканирования).
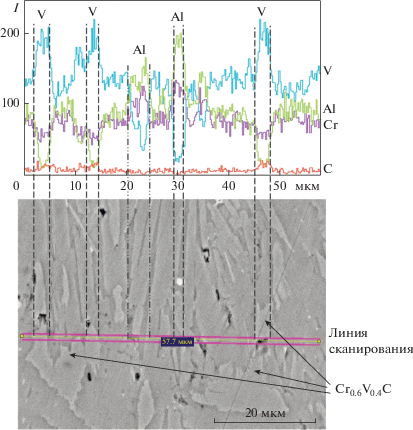
На рис. 4 представлена характерная микроструктура поверхности синтезированного материала. Интерметаллидные зерна Al8Cr5 находятся в виде отдельных включений (фаза белого цвета) размером от 5 до 15 мкм, зерна двойного карбида Cr0.6V0.4C имеют развитую форму и также находятся в виде отдельных включений размером до 20 мкм.
С учетом того, что при энерго-дисперсионном анализе (ЭДА) рабочей поверхности (рис. 5) анализируется тонкий поверхностный слой, а в исходной реакционной смеси использовался графит, результаты ЭДА показывают повышенное содержание углерода, который находится на межфазных границах и в микропорах образца, которые могут достигать 5 мкм.
Рис. 5.
Микроструктура и карта распределения элементов V, Cr, Al и С на поверхности образца (шлифа).
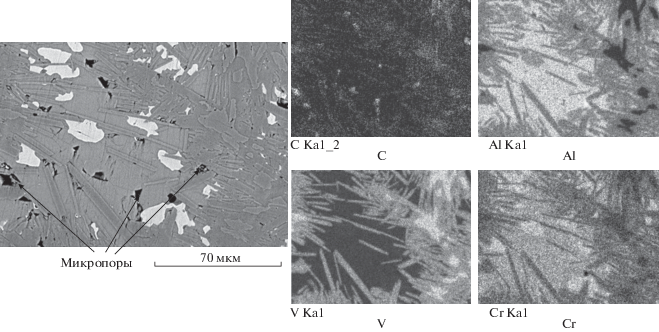
Данные по элементному составу также варьируются в разных точках (C 32.57–42.67; Al 19.02–22.30; Cr 11.49–13.86; V 31.36–31–42.02, ат. %), что скорее всего связано с малым размером наноламинатных составляющих, в первую очередь твердого раствора (Cr,V)2AlC, который сравним или меньше области генерации рентгеновского излучения при энерго-дисперсионном анализе.
Результаты измерения микротвердости HVμ синтезированного материала на основе твердого раствора (Cr,V)2AlC представлены в табл. 2. Несмотря на пластичность твердого раствора (Cr,V)2AlC (рис. 2б, 2д), высокое значение микротвердости HVμ может быть связано с присутствием в синтезированном материале двойного карбида Cr0.6V0.4C.
Таблица 2.
Сравнение результатов измерения твердости HV с литературными данными
Увеличение твердости раствора (Cr1– хVх)2AlС за счет твердорастворного упрочнения материала может быть связано с увеличением содержания V в результате частичного замещения Cr [15].
На рис. 6 представлена температурная зависимость удельного электросопротивления (ρ) продукта синтеза. Синтезированный из исходной реакционной смеси композиционный материал обладает металлической проводимостью во всем измеренном диапазоне температур 300–1300 K.
Удельное электросопротивление композиционного материала на основе твердого раствора (Cr,V)2AlC при комнатной температуре составляет 1.14 мкОм м, что выше чем удельное электросопротивление материалов на основе МАХ-фаз Cr2AlC [6] и V2AlC [7]. Обнаружено, что с ростом температуры кривая электросопротивления твердого раствора (Cr,V)2AlC занимает промежуточное положение между зависимостями для Cr2AlC и V2AlC. На температурной зависимости удельного электросопротивления в диапазоне 1050–1100 К обнаружена интересная особенность. Значение температурного коэффициента сопротивления (ТКС) исследуемого материала в области температур от комнатной до 1050 К постоянно и составляет 7.2 × 10–4 К–1.
В диапазоне температур 1050–1100 К происходит изменение ТКС, при дальнейшем повышении температуры образца от 1100 К ТКС не меняется и составляет 4.2 × 10–4 К–1. Значения ТКС и его поведение при изменениях температуры для материала на основе твердого раствора (Cr,V)2AlC заметно отличаются от характеристик для материалов на основе МАХ-фаз Cr2AlC и V2AlC.
ЗАКЛЮЧЕНИЕ
В работе впервые показано, что методом самораспространяющегося высокотемпературного синтеза из смеси порошков оксидов ванадия(V) и хрома(III) c алюминием и графитом получен материал на основе МАХ-твердого раствора (V,Cr)2AlC, в котором присутствуют также вторичные карбидные, интерметаллидные соединения ванадия и хрома. Наличие вторичных фаз в конечном продукте синтеза связано, по-видимому, с неравновесностью процесса синтеза из-за малого времени “жизни” расплава и быстрой кристаллизацией при остывании. В результате этого вторичные фазы Cr0.6V0.4C и Cr5Al8 не успевают полностью прореагировать с образованием твердого раствора (Cr,V)2AlC. Зерна (V,Cr)2AlC имеют наноламинатную морфологию характерную для МАХ-фаз. Полученный материал является электрическим проводником, демонстрирующим металлический характер проводимости во всем измеренном диапазоне температур 300–1300 К. Удельное электросопротивление материала на основе твердого раствора (Cr,V)2AlC при комнатной температуре составляет 1.14 мкОм м, что выше чем данный параметр материалов на основе МАХ-фаз Cr2AlC и V2AlC. Однако с ростом температуры кривая электросопротивления твердого раствора (Cr,V)2AlC занимает промежуточное положение между зависимостями для Cr2AlC и V2AlC.
Список литературы
Nowotny V.H. Strukturchemie einiger Verbindungen der Übergangsmetalle mitden elementen C, Si, Ge, Sn // Prog Solid State Chem. 1971. V. 5. P. 27–70.
Jeitschko W., Nowotny H., Benesovky F. Kohlenstoffhaltige ternäre Verbindungen (H-phase) // Monatsh Chem. 1963. V. 94. P. 672–678.
Barsoum M.W., Yoo H.I., Polushina I.K., Rud’ V.Yu., Rud’ Yu.V., El-Raghy T. Electrical conductivity, thermopower, and hall effect of Ti3AlC2, Ti4AlN3, and Ti3SiC2 //Phys. Rev. B. 2000. V. 62. P. 10194–10198.
El-Raghy T., Zavaliangos A., Barsoum M.W., Kalidindi S.R. Damage mechanisms around hardness indentations in Ti3SiC2 // J. Am. Ceram. Soc. 1997. V. 80. P. 513–516.
Hu Chunfeng, Zhang Haibin, Li Fangzhi, Huang Qing, Bao Yiwang. New phases’ discovery in MAX family // Int. J. Refractory Metals and Hard Materials. 2013. V. 36. P. 300–312. https://doi.org/10.1016/j.ijrmhm.2012.10.011]
Горшков В.А., Милосердов П.А., Карпов А.В., Щукин А.С., Сычев А.Е. Исследование состава и свойств материала на основе MAX-фазы Cr2AlC, полученного методом СВС-металлургии // ФММ. 2019. Т. 120. № 5. С. 512–517. https://doi.org/10.1134/S0015323019050048
Горшков В.А., Карпов А.В., Ковалев Д.Ю., Сычев А.Е. Синтез, структура и свойства материала на основе MAX-фазы V2AlC // ФММ. 2020. Т. 121. № 8. С. 842–848. https://doi.org/10.31857/S0015323020080033
Wang J.Y., Zhou Y.C. Dependence of elastic stiffness on electronic band structure of nano-laminate M2AlC (M5Ti, V, Nb and Cr) ceramics.// Phys. Rev. B. 2004. V. 69. article no.: 21411.
Sun Z.M., Music D., Ahujia R., Schneider J.M. Electronic origin of shearing in M2AC (M5Ti, V, Cr, A5Al, Ga) // J. Phys.: Conden. Matter. 2005. V. 17. P. 7169–7176.
Grossi J., Shah S.H., Artacho E., Bristowe P.D. Effect of magnetism and temperature on the stability of (Crx,V1 – x)2AlC phases // Phys. Rev. Materials. 2018. V. 2. P. 123603. https://doi.org/10.1103/PhysRevMaterials.2.123603
Schuster J.C., Nowotny H., Vaccaro C. The ternary systems: Cr–Al–C, V–Al–C, and Ti–Al–C and the behavior of H-Phases (M2AlC) // J. Solid State Chem. 1980. V. 32 № 2. P. 213–219.
Zhou Y.C., Meng F.L., Zhang J. New MAX-phase compounds in the V–Cr–Al–C system // J. Am. Ceram. Soc. 2008. V. 91. P. 1357–1360.
Halim J., Chartier P., Basyuk T., Prikhna T., Caspie E.N., Barsoum M.W., Cabioc’h T. Structure and thermal expansion of (Crx,V1 –x)n+ 1AlCn phases measured by X‑ray diffraction // J. European Ceramic Society. 2017. V. 37. P. 15–21. https://doi.org/10.1016/j.jeurceramsoc.2016.07.022
Caspi E.N., Chartier P., Porcher F., Damay F., Cabioc’h T. Ordering of (Cr,V) layers in nanolamellar (Cr0.5V0.5)n + 1AlCn compounds// Materials Research Letters. 2015. V. 32. P. 100–106. https://doi.org/10.1080/21663831.2014.975294
Wu Bian Tian, Zheng Ming Sun, Hitoshi Hashimoto, Yu Lei Du. Synthesis, microstructure and properties of (Cr1 – xVx)2AlC solid solutions // J. Alloys and Compounds. 2009. V. 484. P. 130–133. https://doi.org/10.1016/j.jallcom.2009.04.111
Chun Liang Yeh, Wen Jung Yang. Combustion Synthesis of (Ti,V)2AlC Solid Solutions // Advanced Materials Research. 2014. V. 909. P. 19–23. https://doi.org/10.4028/www.scientific.net/AMR.909.19
Yeh C.L., Yang W.J. Formation of MAX solid solutions (Ti,V)2AlC and (Cr,V)2AlC with Al2O3 addition by SHS involving aluminothermic reduction // Ceramics International. 2013. V. 39. P. 7537–7544. https://doi.org/10.1016/j.ceramint.2013.03.005
Jianfeng Zhu, Hao Jiang, Fen Wang, Qi Ma. Synthesis, microstructure evolution, and mechanical properties of (Cr1 – xVx)2AlC ceramics by in situ hot-pressing method // J. Mater. Res. 2014. V. 29. № 10. P. 1168–1174.
Дополнительные материалы отсутствуют.
Инструменты
Физика металлов и металловедение