Физика металлов и металловедение, 2021, T. 122, № 3, стр. 294-305
Механизм окисления фаз в жаропрочных сплавах системы Fe–25Cr–35Ni
А. И. Рудской a, С. Ю. Кондратьев a, *, Г. П. Анастасиади a, А. В. Цеменко b
a Санкт-Петербургский политехнический университет Петра Великого
195251 Санкт-Петербург, ул. Политехническая, 29, Россия
b Центральный научно-исследовательский институт конструкционных материалов “Прометей”
им. И.В. Горынина – НИЦ “Курчатовский институт”
191015 Санкт-Петербург, ул. Шпалерная, 49, Россия
* E-mail: petroprom2013@yandex.ru
Поступила в редакцию 01.07.2020
После доработки 11.10.2020
Принята к публикации 20.10.2020
Аннотация
Методами электронной микроскопии исследованы механизм и кинетика эволюции микроструктуры и фазового состава поверхностной диффузионной зоны литого жаропрочного сплава системы Fe–25Cr–35Ni при длительной высокотемпературной выдержке в окислительной атмосфере. При окислении сплава химический состав фаз непрерывно изменяется по сложным законам, зависящим от окружающей среды, температуры и продолжительности воздействия, причем процесс окисления каждой фазы сплава уникален. Между различными фазами происходит интенсивный обмен химическими элементами. После длительной высокотемпературной выдержки сплава процесс окисления фаз, вероятно, достигает устойчивого предельного состояния. Полученные результаты сопоставлены с известными на основе обзора публикаций по исследованной теме.
ВВЕДЕНИЕ
Литейные сплавы HP40NbTi на основе системы Fe–25Cr–35Ni являются одними из наиболее жаростойких жаропрочных материалов, применяемых в нефтехимической промышленности в жестких условиях эксплуатации: температура 800–1150°С, рабочие напряжения 5–10 МПа, агрессивная среда, установок пиролиза углеводородного сырья. Одной из причин потери работоспособности сплавов при эксплуатации является высокотемпературное окисление. Особенности эксплуатации, деградации структуры и разрушения деталей установок пиролиза из сплавов HP40NbTi рассмотрены в [1–19].
Сплавы HP40NbTi имеют сложный химический и фазовый состав. Кинетика высокотемпературного окисления определяется их многофазной структурой, состоящей из исходных и образующихся в процессе эксплуатации фаз. Исходные фазы: γ-твердый раствор (~95 об. %); эвтектика, состоящая из матричной γ-фазы и карбидов на основе хрома и ниобия (4–6 об. %); равномерно распределенные в матрице включения карбидов ниобия и хрома (1–2 об. %) [20, 21]. В процессе высокотемпературной эксплуатации образуются интерметаллиды различного химического состава [22–26]. Фазы в структуре литых HP-сплавов, а также первичные оксиды, образующиеся при высокотемпературной выдержке, значительно различаются по способности к окислению [27–31]. Протекторные свойства комплексных оксидов, образующихся в сплавах при эксплуатации, можно оценить только экспериментально.
Процесс окисления сплавов сложного химического состава имеет неустойчивый вероятностный характер, зависящий от структуры и фазового состава, условий кристаллизации, локальной химической неоднородности, температуры и др. В связи с этим, изучение процесса высокотемпературного окисления жаростойких жаропрочных HP-сплавов является актуальной задачей и требует подробного анализа на макро- и микроуровне.
Целью работы является изучение механизма и кинетики высокотемпературного окисления фаз в структуре сплава HP40NbTi, существенно различающихся по строению, химическому составу и характеру взаимодействия с кислородом.
МАТЕРИАЛ И МЕТОДИКИ ИССЛЕДОВАНИЯ
Сплав выплавляли в индукционной печи, литые заготовки получали статическим литьем в песчаные формы. Химический состав сплава (мас. %): Fe–0.45C–26.3Cr–33.1Ni–1.70Nb–1.68Si–0.95Mn–0.36W–0.25Mo–0.11V–0.21Ti-≤ 0.5РЗЭ.
Металлографические исследования и рентгеноспектральный микроанализ (РСМА) выполняли с использованием оптического микроскопа Carl Zeiss Axiovert 40 и растрового электронного микроскопа (СЭМ) TESCAN VEGA 2 LM, оснащенного автоэмиссионной пушкой и энергодисперсионным рентгеновским спектрометром INCA X-Max-50. Точность определения концентрации элементов в фазах составляла (отн. %): для Fe, Ni, Cr, Si, Nb, Mo, W, Ti – 3%; для С, N – 20%, для О – 10%.
Для окисления в контролируемой атмосфере использовали образцы сплава размером 10 × 10 × × 15 мм. Испытания проводили с использованием вакуумной камеры с водяным охлаждением и вольфрамовым нагревателем. Установка поддерживает вакуум на уровне 10–2–10–3 мм. рт. ст. Контроль температуры осуществляли термопарой типа ВР (W–Re), закрепленной к середине образца и выведенной через специальное вакуумное уплотнение. Точность измерения температуры образца составляла ±2°С.
РЕЗУЛЬТАТЫ ИССЛЕДОВАНИЙ И ИХ ОБСУЖДЕНИЕ
Окисление сплава HP40NbTi при 800°С
На рис. 1 показана структура поверхностного слоя сплава после кратковременного окисления 10 мин при 800°С в среднем вакууме и на воздухе. Содержание O2 в оксидных пленках, на разных фазах сплава, существенно различается и после окисления в вакууме и на воздухе составляет соответственно (мас. %): γ-фаза – ~3 и 11%, карбид хрома ~6 и 5%, карбид ниобия ~4 и 42%, интерметаллид ~7 и 13%.
Рис. 1.
Структура поверхностного слоя сплава HP40NbTi после окисления при 800°С, 10 мин в вакууме 10–2–10–3 мм рт. ст. (а) и на воздухе (б).
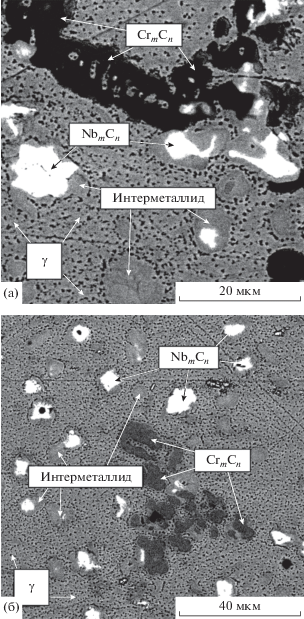
В вакууме характер окисления разных фаз в начальный период одинаковый, вероятно, вследствие недостатка кислорода в окружающей среде и малого времени окисления. При окислении на воздухе различие в поведении фаз выявляется уже при кратковременной выдержке (10 мин). В этих условиях стойкость к окислению карбида хрома выше, чем γ-фазы. Вероятно, при высокой концентрации (~80 мас. %) хрома в карбиде на нем образуется плотная оксидная пленка комплексных оксидов на основе хрома МO2. Пленка замедляет процесс окисления фазы до момента своего разрушения, которое возникает вследствие напряжений, возникающих в окалине из-за разной скорости ее роста на соседних зернах γ-фазы и на частицах карбидных фаз, образующих наноразмерный рельеф поверхности сплава (рис. 2).
Рис. 2.
Поверхностный рельеф на межфазной границе карбид хрома/аустенит в литом сплаве HP40NbTi (3D-изображение поверхности образца без химического травления). Наноиндентер Hysitron TI 750 UBI.
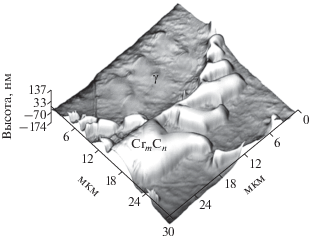
Наименее устойчивым к окислению является карбид ниобия: после выдержки 10 мин при 800°С содержание O2 в нем достигает 42% (мас.), а содержание Nb снижается с 88 до 29–46% (мас.). Этому может способствовать фрагментированная структура карбида ниобия [32], вследствие чего оксид, растущий на карбиде ниобия, также является фрагментированным и не образует сплошную окалину (рис. 3).
Рис. 3.
Фрагментированные частицы карбида ниобия в структуре литого сплава HP40NbTi после окисления при 800°С, 10 мин (а) и 6 ч (б) на воздухе.
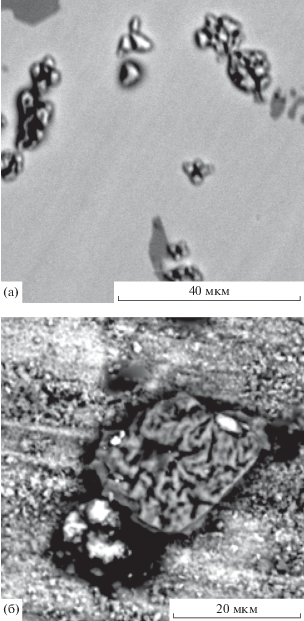
Увеличение длительности выдержки до 6 ч при 800°С на воздухе увеличивает различие в характере окисления фаз в структуре литого сплава. После окисления наименьшее количество кислорода (20–28 мас. %) содержит γ-фаза, причем кислород замещает в ней Fe и Ni и незначительно изменяет содержание Cr. Содержание кислорода в интерметаллидах, образующихся в структуре сплава при 800°С, несколько больше (24–32 мас. %), чем в γ-фазе. Карбид хрома имеет высокое содержание O2 (33–39 мас. %), который замещает в нем Cr и Fe. Наибольшее количество O2 содержит окисленный карбид ниобия (42–45 мас. %). В нем появляется значительное количество Cr (11–29 мас. %) и содержание Nb уменьшается до 20–40 (мас. %).
Формулы оксидов, образующихся при окислении сплава HP40NbTi, определены при сопоставлении экспериментальных результатов РСМА состава фаз после окисления со стандартными составами оксидов хрома [33]. Матричная γ-фаза окисляется с образованием оксидов M2O3 и МО2 на основе Cr или МО на основе Cr–Fe–Ni, интерметаллиды образуют оксиды М2О3 на основе Cr, карбид хрома – оксиды CrO2. В результате одновременного окисления карбида ниобия и карбида хрома, вероятно, вначале образуются промежуточные оксиды Cr2O3, CrO2, CrO3 и NbO, Nb2O5, а затем – комплексные оксиды (CrNb)O4 или MO2 на основе CrNb. Аналогичные результаты получены в [34] после 24 ч окисления сплава HP40NbTiZr на воздухе при 820 и 1000°C. В [34] наблюдали на начальной стадии окисления образование оксидов Cr2O3 и Nb2O5 с последующим переходом в комплексные оксиды (CrNb)O4.
Окисление сплава HP40NbTi при 1150°С
На рис. 4 показана поверхность сплава HP40NbTi без окалины и поверхностный слой с окалиной после окисления в течение 2 ч при 1150°С на воздухе. Толщина окалины составляет ~60 мкм (рис. 4б). РСМА показал, что матричная γ-фаза в структуре сплава на границе с окалиной значительно обеднена хромом. Содержание Cr в матричном твердом растворе составляет (мас. %): в глубине от поверхности – 23–25%, на поверхности под окалиной – 12.6–12.9%. Это согласуется с результатами работы [35]. Основным элементом, образующим окалину, является хром. Кроме хрома в состав оксидов входят в небольшом количестве Mn, Si, Nb и другие элементы, активно взаимодействующие с кислородом. Химический состав оксидов на фазах соответствует MO2 на основе хрома, кроме карбида ниобия, на котором образуется комплексный оксид (CrNb)2O5.
Рис. 4.
Поверхность сплава HP40NbTi без окалины (а) и структура поверхностного слоя с окалиной (б) после окисления при 1150°С, 2 ч на воздухе.
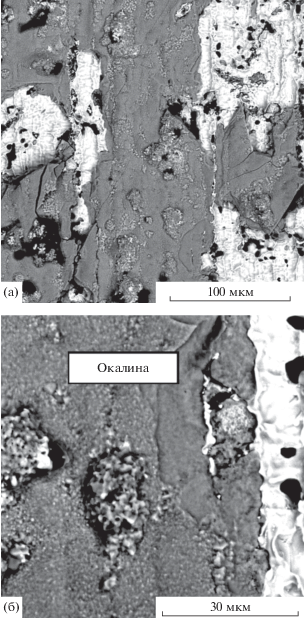
Увеличение длительности выдержки при 1150°С изменяет кинетику окисления сплава и состав γ-фазы в структуре поверхностного слоя: обеднение γ-фазы хромом до ~13 (мас. %) компенсируется обогащением ее железом до ~37 (мас. %) и никелем до 43–47 (мас. %).
Состав окалины на поверхности сплава также изменяется при увеличении длительности окисления. Образуется окалина из стабильных комплексных оксидов МО, МО2 или М3О4 на основе Cr и Si. После 500 ч окисления при 1150°С на воздухе окалина состоит из двух слоев: внешний – сформирован оксидом хрома, внутренний – оксидом кремния (рис. 5, табл. 1). Подобное строение окалины при окислении HP сплавов наблюдали в [12]. В поверхностном слое глубиной до 300 мкм карбид хрома, выделившийся по границам дендритов γ-фазы, растворяется вследствие внутреннего окисления за счет диффузии кислорода (рис. 5).
Рис. 5.
Микроструктура окалины и поверхностного диффузионного слоя литого сплава HP40NbTi после окисления при температуре 1150°С, 500 ч на воздухе.
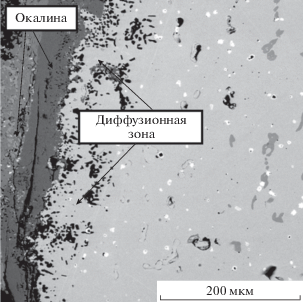
Таблица 1.
Химический состав окалины, образовавшейся на поверхности литого сплава HP40NbTi после окисления при 1150°С, 500 ч на воздухе
Формула оксида по химическому составу | Содержание химических элементов, % (мас.) | |||||
---|---|---|---|---|---|---|
O | Si | Cr | Fe | Ni | Nb | |
CrO2 | 36.9 | 0.4 | 62.1 | 0.6 | – | – |
(CrSi)3O4 | 32.1 | 12.5 | 55.4 | – | – | – |
MO2 (на основе Si) | 44.5 | 22.6 | 3.0 | 8.4 | 8.2 | 13.3 |
MO (на основе Ni, Fe, Si) | 24.2 | 10.3 | 8.9 | 24.5 | 27.2 | 4.9 |
Анализ характера и кинетики окисления фаз в сплаве HP40NbTi
В состав современных жаростойких жаропрочных сплавов HP-серии входит большое количество химических элементов. Диаграммы состояния таких многокомпонентных систем (даже для равновесных условий) отсутствуют. Одним из немногих эффективных методов изучения кинетики трансформации структуры многокомпонентных сплавов при высокотемпературном окислении является статистический анализ результатов РСМА изменяющегося химического состава фаз.
Статистический анализ базируется на соблюдении условия баланса содержания отдельных элементов в фазах, которое контролируется по результатам определения среднего химического состава сплава и определения состава и средней доли каждой фазы в структуре сплава методами количественной металлографии [36].
Достоверно оценить изменение состава фаз в сплаве при окислении позволяют вероятностные показатели содержания химических компонентов в исходном литом состоянии и после различных режимов окисления. Вероятностными показателями являются: среднее значение содержания компонента μ (мас. %), стандартное отклонение s (мас. %) и коэффициент вариации s/μ × 100 (%) [37]. Их значения позволяют оценить устойчивость или изменчивость процессов взаимодействия элементов, входящих в состав разных фаз, и с элементами окружающей среды при разных условиях окисления.
Анализ вероятностного процесса обычно проводят для значения коэффициента вариации s/μ ≤ 33%. В этом случае разброс значений параметра в интеграле вероятности равен Δu = ±0.33, а вероятность выборки данных в интервале значений ±∆u составляет:
Установленные нормативной документацией технические требования к интервалу содержания основных легирующих элементов сплава – Cr, Ni, Si и Nb обычно не превышают Δμ/μ ≤ 0.10 = 10%. Таким образом, для корректного статистического анализа необходимо уменьшить допустимый разброс параметра s/μ.
Авторы [38], исследовав результаты 906 экспериментов, заключили, что наиболее обоснованные результаты статистического анализа получаются при s/μ ≤ 20%. Увеличение значения коэффициента вариации относительно этого значения является результатом преимущественного влияния на процесс какого-то одного слабо контролируемого фактора.
Кинетику окисления фаз в сплаве исследовали методом статистического РСМА. Результаты определения химического состава фаз в структуре сплава в литом состоянии и после окисления по разным режимам приведены в табл. 2–5.
Таблица 2.
Вероятностные показатели химического состава γ-фазы в поверхностном диффузионном слое сплава HP40NbTi в литом состоянии и после окисления по разным режимам
Фаза | Состояние сплава | Вероятностные показатели | Химические элементы состава | |||||
---|---|---|---|---|---|---|---|---|
О | Si | Cr | Fe | Ni | W | |||
γ-фаза | Литое | μ, (мас. %) | – | 1.9 | 23.6 | 38.7 | 34.3 | 0.60 |
s, (мас. %) | – | 0.2 | 0.4 | 0.8 | 0.3 | 0.13 | ||
s/μ, % | – | 10.5 | 1.7 | 2.1 | 0.9 | 22.2 | ||
800°С, 10 мин, вакуум (режим 1) | μ, (мас. %) | 5.2 | 1.4 | 21.7 | 34.3 | 31.5 | 5.5 | |
s, (мас. %) | 0.8 | 0.3 | 0.7 | 0.7 | 1.4 | 0.7 | ||
s/μ, % | 15.4 | 21.4 | 3.2 | 2.0 | 4.4 | 12.7 | ||
800°С, 10 мин, воздух (режим 2) | μ, (мас. %) | 8.4 | 1.8 | 22.3 | 33.2 | 32.1 | 1.5 | |
s, (мас. %) | 1.4 | 0.2 | 1.3 | 3.0 | 2.0 | 0.3 | ||
s/μ, % | 16.7 | 11.1 | 5.8 | 9.0 | 6.2 | 20.0 | ||
800°С, 6 ч, воздух (режим 3) | μ, (мас. %) | 25.7 | 2.3 | 32.3 | 16.7 | 19.1 | 3.2 | |
s, (мас. %) | 2.5 | 0.5 | 4.6 | 2.7 | 2.9 | 0.5 | ||
s/μ, % | 9.7 | 21.7 | 14.2 | 16.2 | 15.2 | 15.6 | ||
1150°С, 2 ч, воздух (режим 4) | μ, (мас. %) | 12.9 | 3.0 | 20.9 | 29.5 | 33.1 | 0.2 | |
s, (мас. %) | 2.8 | 0.2 | 3.3 | 2.9 | 4.4 | 0.04 | ||
s/μ, % | 21.7 | 6.7 | 15.8 | 9.8 | 13.3 | 20.0 | ||
1150°С, 500 ч, воздух (режим 5) | μ, (мас. %) | – | 0.4 | 12.8 | 39.4 | 45.5 | 1.1 | |
s, (мас. %) | – | 0.07 | 0.4 | 0.2 | 0.4 | 0.2 | ||
s/μ, % | – | 17.5 | 3.1 | 0.5 | 0.9 | 18.2 |
Таблица 3.
Вероятностные показатели химического состава карбида хрома (CrmCn) в поверхностном слое сплава HP40NbTi в литом состоянии и после окисления по разным режимам
Фаза | Состояние сплава | Вероятностные показатели | Химические элементы состава | |||||
---|---|---|---|---|---|---|---|---|
О | C | Cr | Fe | Ni | W | |||
CrmCn | Литое | μ, (мас. %) | – | 9.2 | 78.8 | 8.5 | 1.6 | 1.5 |
s, (мас. %) | – | 0.2 | 0.4 | 0.8 | 0.3 | 0.2 | ||
s/μ, % | – | 2.2 | 0.5 | 9.4 | 18.8 | 13.3 | ||
800°С, 10 мин, вакуум (режим 1) | μ, (мас. %) | 4.0 | – | 76.7 | 10.9 | 3.3 | 4.7 | |
s, (мас. %) | 0.9 | – | 4.7 | 3.2 | 1.6 | 1.2 | ||
s/μ, % | 22.5 | – | 6.1 | 29.4 | 48.5 | 25.5 | ||
800°С, 10 мин, воздух (режим 2) | μ, (мас. %) | 5.0 | – | 79.2 | 9.8 | 4.0 | 1.7 | |
s, (мас. %) | 1.1 | – | 3.0 | 0.6 | 0.9 | 0.5 | ||
s/μ, % | 22.0 | – | 3.8 | 6.1 | 22.5 | 29.4 | ||
800°С, 6 ч, воздух (режим 3) | μ, (мас. %) | 30.3 | – | 50.9 | 5.9 | 4.2 | 8.2 | |
s, (мас. %) | 10.1 | – | 10.8 | 2.9 | 1.8 | 1.4 | ||
s/μ, % | 33.3 | – | 21.2 | 49.2 | 42.9 | 17.1 | ||
1150°С, 2 ч, воздух (режим 4) | μ, (мас. %) | 35.3 | – | 63.1 | 0.5 | 0.4 | – | |
s, (мас. %) | 2.1 | – | 2.7 | 0.2 | 0.2 | – | ||
s/μ, % | 6.0 | – | 4.3 | 40.0 | 50.0 | – | ||
1150°С, 500 ч, воздух (режим 5) | μ, (мас. %) | 38.3 | – | 53.7 | 0.6 | 0.4 | – | |
s, (мас. %) | 1.9 | – | 2.3 | 0.1 | 0.1 | – | ||
s/μ, % | 5.0 | – | 4.3 | 16.7 | 25.0 | – |
Таблица 4.
Вероятностные показатели химического состава интерметаллида (Cr7Ni5Si3N3FeNb) в поверхностном слое сплава HP40NbTi после окисления по разным режимам
Фаза | Состояние сплава | Вероятностные показатели | Химические элементы состава | ||||||
---|---|---|---|---|---|---|---|---|---|
О | Si | Cr | Fe | Ni | Nb | W | |||
Интерметаллид Cr7Ni5Si3N3FeNb |
800°С, 10 мин, вакуум (режим 1) |
μ, (мас. %) | 5.2 | 7.5 | 35.3 | 6.4 | 29.5 | 8.7 | 7.1 |
s, (мас. %) | 0.9 | 0.9 | 2.6 | 1.3 | 0.6 | 1.9 | 1.2 | ||
s/μ, % | 17.3 | 12.0 | 7.4 | 20.3 | 2.0 | 21.8 | 16.9 | ||
800°С, 10 мин, воздух (режим 2) |
μ, (мас. %) | 28.3 | 5.3 | 24.6 | 5.6 | 13.9 | 7.0 | 14.9 | |
s, (мас. %) | 4.3 | 1.0 | 2.4 | 0.7 | 2.4 | 0.9 | 1.5 | ||
s/μ, % | 15.2 | 18.9 | 9.8 | 12.5 | 17.2 | 12.9 | 10.1 | ||
800°С, 6 ч, воздух (режим 3) |
μ, (мас. %) | – | 5.0 | 21.0 | 18.6 | 25.0 | 10.6 | 19.5 | |
s, (мас. %) | – | 1.0 | 2.1 | 1.9 | 3.2 | 0.5 | 1.6 | ||
s/μ, % | – | 20.0 | 10.0 | 10.2 | 12.8 | 4.7 | 8.2 | ||
1150°С, 2 ч, воздух (режим 4) |
μ, (мас. %) | 19.2 | 10.3 | 8.9 | 29.3 | 27.2 | 4.9 | – | |
s, (мас. %) | 3.1 | 2.3 | 0.7 | 4.2 | 4.6 | 0.2 | – | ||
s/μ, % | 16.2 | 22.3 | 7.9 | 14.3 | 16.9 | 4.1 | – |
Таблица 5.
Вероятностные показатели химического состава карбида ниобия (NbC) в поверхностном слое сплава HP40NbTi в литом состоянии и после окисления по разным режимам
Фаза | Состояние сплава | Вероятностные показатели | Химические элементы состава | |||||||
---|---|---|---|---|---|---|---|---|---|---|
О | C | Cr | Fe | Ni | Nb | Si | W | |||
NbC | Литое | μ, (мас. %) | – | 11.5 | 1.2 | 0.7 | 0.7 | 85.3 | – | – |
s, (мас. %) | – | 2.2 | 0.3 | 0.2 | 0.2 | 8.7 | – | – | ||
s/μ, % | – | 19.1 | 25.0 | 28.6 | 28.6 | 10.2 | – | – | ||
800°С, 10 мин, вакуум (режим 1) |
μ, (мас. %) | 5.4 | – | 2.3 | 11.3 | 2.8 | 76.1 | – | 1.9 | |
s, (мас. %) | 1.6 | – | 0.6 | 2.5 | 1.1 | 9.3 | – | 0.6 | ||
s/μ, % | 29.6 | – | 26.1 | 22.1 | 39.3 | 12.2 | – | 31.6 | ||
800°С, 10 мин, воздух (режим 2) |
μ, (мас. %) | 33.9 | – | 9.7 | 8.7 | 7.2 | 31.5 | – | 8.2 | |
s, (мас. %) | 5.8 | – | 2.7 | 4.2 | 4.2 | 8.8 | – | 0.8 | ||
s/μ, % | 17.1 | – | 27.8 | 48.3 | 58.3 | 27.9 | – | 9.8 | ||
800°С, 6 ч, воздух (режим 3) |
μ, (мас. %) | 42.4 | – | 17.4 | 6.9 | 3.6 | 26.8 | – | 2.4 | |
s, (мас. %) | 2.1 | – | 6.3 | 3.9 | 2.3 | 9.7 | – | 0.3 | ||
s/μ, % | 5.0 | – | 36.2 | 56.5 | 63.9 | 36.2 | – | 12.5 | ||
1150 °С, 2 ч, воздух (режим 4) |
μ, (мас. %) | 34.7 | – | 34.4 | 0.5 | 0.4 | 29.4 | – | – | |
s, (мас. %) | 2.4 | – | 8.3 | 0.1 | 0.1 | 8.2 | – | – | ||
s/μ, % | 6.9 | – | 24.1 | 20.0 | 25.0 | 27.9 | – | – | ||
1150°С, 500 ч, воздух (режим 5) |
μ, (мас. %) | 44.5 | – | 3.0 | 8.4 | 7.9 | 13.3 | 22.5 | – | |
s, (мас. %) | 2.7 | – | 0.7 | 4.7 | 4.3 | 5.5 | 3.6 | – | ||
s/μ, % | 6.1 | – | 23.3 | 56.0 | 54.4 | 41.4 | 16.0 | – |
Матричная γ-фаза
В литом сплаве γ-фаза характеризуется малыми значениями коэффициентов вариации содержания легирующих элементов – s/μ < 20% за исключением вольфрама с низкой исходной концентрацией 0.4 (мас. %) (табл. 2). Это свидетельствует, что структура сплава в литом состоянии является квазиравновесной, поскольку γ-фаза составляет в ней >90% (об.).
Процесс окисления γ-фазы также характеризуется умеренным коэффициентом вариации содержания кислорода и основных легирующих элементов в образующихся на ней оксидах: при 800–1150°С в среднем вакууме и на воздухе s/μ < < 22% (табл. 2).
Из табл. 2 видно, что распределение легирующих элементов в γ-фазе при увеличении температуры и длительности окисления однородное, некоторым исключением являются Si и W. Это определяет высокую работоспособность сплавов HP40NbTi при длительном высокотемпературном окислении. Химический состав γ-фазы на поверхности сплава после окисления при 1150°С, 500 ч стремится к некоторому предельному (в соответствии с активностью окружающей среды) химическому составу (мас. %): 0.4 Si; 12.8 Cr; 39.4 Fe; 45.5 Ni; 1.1 W. Вдали от границы с окалиной состав γ-фазы соответствует исходному литому состоянию (мас. %): 2.1 Si; 21.3 Cr; 37.3 Fe; 37.3 Ni; 0.7 W. Характерно, что при образовании на поверхности сплава сплошной окалины γ-фаза практически не содержит O2. Кислород накапливается в окалине в результате диффузионного стока Cr из γ-фазы (23.6 → 12.8 Cr), за счет чего происходит рост окалины по реакции 2O + Cr → CrO2.
Активность Cr, образующего протекторный слой окалины сплава, повышается при переходе от вакуума к воздушной атмосфере и при увеличении температуры и длительности окисления. Однако при всех режимах окисления в окалине, образующейся на поверхности сплава вблизи γ‑фазы, накапливается небольшое количество O2 – <26 (мас. %) и незначительно изменяется содержание Ni, Cr и Fe. В объеме сплава, у границы с окалиной, O2 в γ-фазе отсутствует. Кислород, диффундируя в сплав по границам дендритов, образует вблизи границы с окалиной оксиды типа MO2 на основе Si и Cr и консолидированные включения оксидов кремния в виде барьеров на поверхности сплава по границам дендритных ячеек (рис. 5).
Карбид хрома
После кратковременной выдержки окисление карбида хрома меньше, чем γ-фазы (табл. 3). При увеличении длительности и повышении температуры окисления элементы, вошедшие в состав карбида хрома при первичной кристаллизации (Fe, Ni, W), практически полностью окисляются и удаляются из частиц карбидов, находящихся в зоне окисления – в поверхностном слое сплава. Коэффициент вариации содержания хрома в оксидах карбида умеренный – s/μ ≤ 21%. Значительный коэффициент вариации для Fe, Ni и W – s/μ = 30–50%, вероятно, объясняется их малым (по сравнению с хромом) содержанием.
Окисление карбида хрома на поверхности сплава при 1150°С на воздухе достаточно быстро (~2 ч) приводит к достижению предельного состава окалины – CrO2 с удалением других элементов (Fe, Ni, Cr). На начальной стадии окисление может происходить по двум реакциям (в зависимости от типа карбида хрома) с образованием основного первичного оксида хрома Cr2O3 [39]:
После окисления при 800 и 1150°С соответственно 6 и 2 ч содержание O2 в образующихся на карбиде хрома оксидах превышает 30 (мас. %), а Cr – составляет ~60 (мас. %). Такой оксид хрома по химическому составу соответствует формуле CrO2 и, вероятно, является продуктом окисления первичного оксида по реакции 2Cr2O3 + O2 = = 4CrO2↑. При 1150°С в окалине и в поверхностном слое сплава образуется практически однородный оксид хрома CrO2 с небольшим содержанием основных легирующих элементов сплава – Fe и Ni (~1 мас. %). Этот оксид образуется за счет растворения эвтектического карбида (с выделением свободного хрома) по границам дендритов на глубине до 300 мкм, а также образования в отдельных зернах γ-фазы градиента концентрации Cr (~13 → 24 мас. %) в поверхностной диффузионной зоне глубиной до 500 мкм (см. табл. 2). Толщина окалины на поверхности сплава при температуре 800°С (6 ч) составляет <1 мкм, а при 1150°С (2 ч) увеличивается до ~30 мкм. На поздней стадии окисления (1150°C, 500 ч) в местах существования бывшего карбида хрома на расстоянии 15–20 мкм от поверхности сплава образуется азотированный оксид хрома, а на расстоянии 150–250 мкм – азотированный хром. В поверхностной зоне сплава толщиной до 100 мкм карбид хрома одновременно насыщается O2 и N (38.3 мас. % O2 и 5.7 мас. % N) за счет их диффузии по границам дендритов γ-фазы, а на глубине 150–250 мкм – теряет углерод и насыщается азотом (82 мас. % Cr и 8.5 мас. % N). Диффузионная зона проникновения в сплав азота l ≈ (Dτ)0.5 ≈ 200 мкм для коэффициента диффузии D ≈ 10–8 см2/с и времени τ = 500 ч. Учитывая, что концентрация азота в воздухе в 4 раза больше, чем кислорода, насыщение сплава азотом существенно выше.
Коэффициент вариации содержания кислорода в продуктах окисления карбида хрома имеет значения s/μ = 22–33%. Это свидетельствует об избирательности и неоднородности процесса окисления карбидных частиц. Режимы окисления 3, 4 и 5 приводят к образованию пористого слоя окалины на основе хрома (CrO2).
Интерметаллид
В сплавах HP40NbTi при высокотемпературной выдержке образуются интерметаллиды. Состав их определяется особенностями состава сплавов, применяемых в разных странах. По этой причине исследователи обнаруживают и публикуют наличие в сплавах различных интерметаллидов. В сплавах HP40NbTi интерметаллид часто определяют как G‑фазу (Ni16Nb6Si7Ti6) [23, 25, 40].
В наших исследованиях G-фаза не обнаружена, поскольку содержание титана в сплаве низкое (0.21 мас. %). В исследованном сплаве определена фаза с условной формулой Cr7Ni5Si3N3FeNb в соответствии с химическим составом, установленным РСМА с учетом статистической обработки результатов [41]. Она образуется в структуре литого сплава после кратковременного высокотемпературного нагрева и растворяется после ~100 ч выдержки.
Этот интерметаллид окисляется при 800–1150°C подобно γ-фазе со значительным перераспределением основных легирующих элементов – Ni, Cr и Fe (табл. 4). При увеличении длительности и повышении температуры окисления сплава содержание Cr и Nb в окисленном интерметаллиде снижается в 2–3 раза, а содержание Fe и W повышается в 3–5 раз. При 1150°С W практически полностью удаляется из интерметаллида в окружающую среду, вероятно, из-за высокой летучести оксидов. Содержание Ni и Si изменяется значительно меньше и зависит от температуры окисления. В окислении интерметаллида участвуют все исходные элементы, при этом коэффициент вариации s/μ элементов химического состава относительно стабилен (<25%).
После выдержки сплава при 800°С, 6 ч (табл. 4, режим окисления 3) происходит также внутреннее окисление отдельных частиц интерметаллида, образовавшихся на глубине до 30 мкм от поверхности сплава на границах дендритов γ-фазы и карбидов ниобия. Этот процесс реализуется, в основном, за счет окисления хрома и никеля (их концентрация уменьшается с 35 до 21 мас. % и с 30 до 25 мас. % соответственно), образования оксидов этих элементов и их испарения с поверхности сплава.
Интерметаллидная фаза, образующаяся в структуре сплавов HP40NbTi при эксплуатации, имеет устойчивое сопротивление окислению при температурах 800–1150°С.
Карбид ниобия
Карбид ниобия является наименее стойкой к окислению фазой в структуре сплава. Согласно [39] скорость окисления карбида ниобия имеет сложную зависимость от температуры. Полученные в нашей работе экспериментальные данные подтверждают неустойчивый характер окисления NbC в сплаве HP40NbTi (табл. 5). Содержание кислорода в оксиде, образующемся на карбиде ниобия после кратковременного окисления в вакууме и на воздухе при 800°С, различается в ~6 раз. При окислении на воздухе в карбиде происходит значительное “выгорание” ниобия, его концентрация в оксиде резко снижается по сравнению с исходным состоянием – 85.3 → 31.5 (мас. %). После длительного окисления сплава при 800°С коэффициент вариации s/μ содержания Nb в оксиде равен ~40%. После длительного (500 ч) окисления сплава при 1150°С содержание Nb в карбиде снижается по сравнению с литым состоянием с 85 до 13% (мас.). “Выгорание” Nb в карбиде компенсируется увеличением содержания основных легирующих элементов сплава – Cr (1.2→34.4 (мас. %), Ni и Fe (0.7 → 4–8 мас. % каждого), а также насыщением его Si (>20 мас. %). Состав окалины, образующейся на поверхности сплава на карбиде ниобия, составляет (ат. %): 68.4 O; 19.2 Si; 3.5 Nb; 1.5 Cr; 3.7 Fe; 3.7 Ni, что условно соответствует формуле оксида МО2 на основе кремния.
Коэффициент вариации содержания элементов при окислении карбида ниобия очень большой (s/μ ≈ 20–60%), в том числе кислорода. Содержание ниобия в продуктах окисления исходного карбида резко снижается в интервале температур окисления 800–1150°С. Это свидетельствует об очень высокой неустойчивости процесса окисления.
Особенностью процесса окисления карбида ниобия является интенсивное взаимодействие ниобия с кислородом, в результате чего образуется летучий оксид Nb2O5, который удаляется в окружающую среду. На начальной стадии окисления Nb в оксиде замещается основными легирующими элементами сплава (Cr, Fe, Ni и W) с образованием оксида (CrNb)O4, а на поздней стадии (500 ч) – в основном кремнием с образованием комплексного оксида МО2 на основе Si (см. табл. 5). На поздней стадии окисления в местах существования бывшего карбида ниобия по границам дендритов γ-фазы в приповерхностном объеме сплава (глубиной до 300 мкм при окислении 1150°С, 500 ч) “in situ” образуется твердый раствор на основе Nb, содержащий до 93 (мас. %) Nb и по 1–2 (мас. %) Fe, Ni, Ti, Cr.
Результаты исследования показывают, что процессы, протекающие в сплавах HP40NbTi при высокотемпературном окислении, являются уникальными для каждой из фаз и определяются химическим составом фаз. При окислении сплава химический состав фаз непрерывно изменяется по сложным законам в зависимости от окружающей среды, температуры и длительности выдержки. Происходит интенсивный обмен химическими элементами между различными фазами. После длительной высокотемпературной эксплуатации сплава процесс окисления фаз, вероятно, приходит к предельному состоянию. Образуются стабильные оксиды и высоко окисленные твердые растворы замещения: для карбида хрома СrmCn – оксид МО2 на основе Cr; для карбида ниобия NbC – оксид МО2 на основе Si; для γ-фазы и интерметаллидов – высоко окисленные твердые растворы переменного состава.
ЗАКЛЮЧЕНИЕ
Высокотемпературное окисление фаз в сплаве HP40NbTi является неустойчивым процессом – содержание кислорода и металлических элементов в локальных объемах продуктов окисления, образующихся как на разных фазах, так и на разных частицах одинаковых фаз, может изменяться в широких пределах. Степень высокотемпературного окисления фаз, составляющих структуру сплава НР40NbTi, определяется активностью входящих в них металлических элементов по отношению к кислороду и уменьшается в ряду: карбид ниобия, карбид хрома, интерметаллические фазы, матричная γ-фаза.
Окисление фаз в сплаве HP40NbTi при температурах 800–1150°С характеризуется одновременным “участием” в процессе всех химических элементов, входящих в их состав. Конечными продуктами окисления фаз в сплаве HP40NbTi при 1150°C длительностью ~500 ч являются оксиды кремния (SiO2) и оксиды на основе хрома (CrO2), содержащие другие легирующие элементы сплава, а также комплексные оксиды (CrSi)3O4.
На поздней стадии окисления сплава (1150°С, 500 ч) в местах существования бывшего карбида хрома по границам дендритов γ-фазы в приповерхностном объеме сплава образуются новые фазы: азотированный оксид хрома (мас. %: до 6 N, 38 O, 54 Cr) – на расстоянии до 100 мкм от поверхности, и азотированный хром (мас. %: 82 Cr; 8.5 N; 1 Fe и 1 Ni) – на расстоянии 150–250 мкм; а в местах существования бывшего карбида ниобия образуется твердый раствор на основе ниобия (мас. %: 93 Nb и по 1–2 Fe, Ni, Ti и Cr) – на расстоянии 150–300 мкм.
Кислород, диффундирующий в сплав, по-видимому, полностью расходуется на внутреннее окисление карбидов ниобия и хрома, а также на создание буферной зоны из оксида кремния (на глубине до 100 мкм), препятствующей стоку хрома из объема сплава к поверхности.
Список литературы
Tillack D.J., Guthrie J.E. Wrought and Cast Heat-Resistant Stainless Steels and Nickel Alloys for the Refining and Petrochemical Industries/ In: Nickel Development Institute, Toronto, Technical Series. 1998. № 10. P. 71–85.
Kaya A.A., Krauklis P., Young D.J. Microstructure of HK40 alloy after high-temperature service in oxidizing/carburizing environment: I. Oxidation phenomena // Mater. Charact. 2002. V. 49. № 1. P. 11–21.
Kaya A.A. Microstructure of HK40 alloy after high-temperature service in oxidizing/carburizing environment: II. Carburization // Mater. Charact. 2002. V. 49. № 1. P. 23–34.
Kenik E.A., Maziasz P.J., Swindeman R.W., Cervenka J., May D. Structure and phase stability in cast modified-HP austenite after long-term ageing // Scr. Mater. 2003. V. 49. P. 117–122.
De Almeida L.H., Ribeiro A.F., Le May I. Microstructural characterization of modified 25Cr–35Ni centrifugally cast steel furnace tubes // Mater. Charact. 2003. V. 49. P. 219–229.
Ul-Hamid A., Tawancy H.M., Mohammed A.-R.I., Abbas N.M. Failure analysis of furnace radiant tubes exposed to excessive temperature // Eng. Fail. Anal. 2006. V. 13. P. 1005–1021.
Tawancy H.M., Ul-Hamid A., Mohammed A.I., Abbas N.M. Effect of materials selection and design on the performance of an engineering product – An example from petrochemical industry // Mater. Des. 2007. V. 28. P. 686–703.
Nunes F.C., De Almeida L.H., Dille J., Delplancke J.-L., Le May I. Microstructural changes caused by yttrium addition to NbTi-modified centrifugally cast HP-type stainless steels // Mater. Charact. 2007. V. 58. P. 132–142.
Alvino A., Lega D., Giacobbe F., Mazzocchi V., Rinaldi A. Damage characterization in two reformer heater tubes after 10 years of service at different operative and maintenance conditions // Eng. Fail. Anal. 2010. V. 17. P. 1526–1541.
Garbiak M., Jasiňski W., Piekarski B. Materials for reformer furnace tubes. History of evolution // Arch. Foundry Eng. 2011. V. 11. P. 47–52.
Jingbo Y., Yimin G., Fang Y., Caiying Y., Zhaozhong Y., Dawei Y., Shengqiang M. Effect of tungsten on the microstructure evolution and mechanical properties of yttrium modified HP40Nb alloy // Mater. Sci. Eng. A. 2011. V. 529A. P. 361–369.
Zhu Z., Cheng C., Zhao J., Wang L. High temperature corrosion and microstructure deterioration of KHR35H radiant tubes in continuous annealing furnace // Eng. Fail. Anal. 2012. V. 21. P. 59–66.
Borjali S., Allahkaram S.R., Khosravi H. Effects of working temperature on the microstructure of high pressure heat-resistant stainless steel tubes used in pyrolysis furnaces during service condition // Mater. Des. 2012. V. 34. P. 65–73.
Рудской А.И., Орыщенко А.С., Кондратьев С.Ю., Анастасиади Г.П., Фукс М.Д., Петров С.Н. Особенности структуры и длительная прочность литого сплава 45Х26Н33С2Б2 // МиТОМ. 2013. № 4. С. 42–47. (Rudskoy A.I., Oryshchenko A.S., Kondrat’ev S.Yu., Anastasiadi G.P., Fuks M.D., Petrov S.N. Special features of structure and long-term strength of cast refractory alloy 45Kh26N33S2B2 // Met. Sci. Heat Treat. 2013. V. 55. № 3–4. P. 209–215.)
Monobe L.S., Schőn C.G. Microstructural and fractographic investigation of cast 20Cr32Ni + Nb alloy tube in the ̀as cast́ and aged states // J. Mater. Res. Technol. 2013. V. 2. № 2. P. 195–201.
Рудской А.И., Кондратьев С.Ю., Анастасиади Г.П., Орыщенко А.С., Фукс М.Д., Петров С.Н. Трансформация структуры жаропрочного сплава 0.45C–26Cr–33Ni–2Si–2Nb при высокотемпературной выдержке // МиТОМ. 2013. № 10. С. 7–14. (Rudskoy A.I., Kondrat’ev S.Yu., Anastasiadi G.P., Oryshchenko A.S., Fuks M.D., Petrov S.N. Transformation of the structure of refractory alloy 0.45C–26Cr–33Ni–2Si–2Nb during a long-term high-temperature hold // Met. Sci. Heat Treat. 2014. V. 55. № 9–10. P. 517–525.)
Bonaccorsi L., Guglielmino E., Pino E., Servetto C., Sili A. Damage analysis in Fe–Cr–Ni centrifugally cast alloy tubes for reforming furnaces // Eng. Fail. Anal. 2014. V. 36. P. 65–74.
Рудской А.И., Орыщенко А.С., Кондратьев С.Ю., Анастасиади Г.П., Фукс М.Д. Механизм и кинетика фазовых превращений в жаропрочном сплаве 45Х26Н33С2Б2 при длительных высокотемпературных выдержках. Часть 1 // МиТОМ. 2014. № 1. С. 3–8. (Rudskoy A.I., Oryshchenko A.S., Kondrat’ev S.Yu., Anastasiadi G.P., Fuks M.D. Mechanisms and kinetics of phase transformations in refractory alloy 45Kh26N33S2B2 in long-term high-temperature holds. Part 1 // Met. Sci. Heat Treat. 2014. V. 56. № 1–2. P. 3–8.)
Рудской А.И., Кондратьев С.Ю., Анастасиади Г.П., Орыщенко А.С., Фукс М.Д. Механизм и кинетика фазовых превращений в жаропрочном сплаве 45Х26Н33С2Б2 при длительных высокотемпературных выдержках. Часть 2 // МиТОМ. 2014. № 3. С. 12–19. (Rudskoy A.I., Kondrat’ev S.Yu., Anastasiadi G.P., Oryshchenko A.S., Fuks M.D. Mechanism and kinetics of phase transformations in refractory alloy 45Kh26N33S2B2 under long-term high-temperature holds. Part 2 // Met. Sci. Heat Treat. 2014. V. 56. № 3–4. P. 124–130.)
Buchanan K.G., Kral M.V. Crystallography and Morphology of Niobium Carbide in As-Cast HP-Niobium Reformer Tubes // Metall. Mater. Trans. 2012. V. 43A. № 6. P. 1760–1769.
Buchanan K.G., Kral M.V., Bishop C.M. Crystallography and morphology of MC carbides in niobium-titanium modified as-cast HP alloys // Metall. Mater. Trans. 2014. V. 45A. № 8. P. 3373–3385.
Рудской А.И., Анастасиади Г.П., Кондратьев С.Ю., Орыщенко А.С., Фукс М.Д. Влияние фактора числа электронных вакансий на кинетику образования, роста и растворения фаз при длительных высокотемпературных выдержках жаропрочного сплава 0.45C–26Cr–33Ni–2Si–2Nb // ФММ. 2014. Т. 115. № 1. С. 3–13. (Rudskoi A.I., AnastasiadiG.P., Kondrat’ev S.Yu., Oryshchenko A.S., Fuks M.D. Effect of electron factor (number of electron holes) on kinetics of nucleation, growth, and dissolution of phases during long-term high-temperature holdings of 0.45C–26Cr–33Ni–2Si–2Nb superalloy // Phys. Met. Metall. 2014. V. 115. № 1. 1–11.)
Sourmail T. Precipitates in creep resistant austenitic stainless steels // Mater. Sci. Technol. 2001. V. 17. № 1. P. 1–14.
Garbiak M., Chyliňska R. Precipitation kinetics in austenitic 18Cr–30Ni–Nb cast steel // Arch. Foundry Eng. 2008. V. 8. № 3. P. 27–30.
Vander Voort G.F., Lucas G.M., Manilova E.P. Metallography and microstructures of heat-resistant alloys/ In: Davis J.R., Davis & Associates, editors. ASM International ASM Handbook, 2004. V. 9: Metallography and Microstructures, P. 820–859.
Ibanez R.A.P., De Almeida Soares G.D., De Almeida L.H., Le May I. Effects of Si content on the microstructure of modified-HP austenitic steels // Mater. Charact. 1993. V. 30. P. 243–249.
Анастасиади Г.П., Кондратьев С.Ю., Рудской А.И. Избирательное высокотемпературное окисление фаз в литом жаропрочном сплаве системы 25Cr–35Ni–Si–Nb–C // МиТОМ. 2014. № 8. С. 3–8. (Anastasiadi G.P., Kondrat’ev S.Yu., Rudskoy A.I. Selective high-temperature oxidation of phases in a cast refractory alloy of the 25Cr–35Ni–Si–Nb–C system // Met. Sci. Heat Treat. 2014. V. 56. P. 403–408.)
Кондратьев С.Ю., Анастасиади Г.П., Рудской А.И. Наноструктурный механизм образования оксидной пленки в жаростойких сплавах на основе Fe–25Cr–35Ni // МиТОМ. 2014. № 10. С. 15–20. (Kondrat’ev S.Yu., Anastasiadi G.P., Rudskoy A.I. Nanostructure mechanism of formation of oxide film in heat-resistant Fe–25Cr–35Ni superalloys // Met. Sci. Heat Treat. 2015. V. 56. № 9–10. P. 531–536.)
McIntyre N., Chan N., Chen C. Characterization of oxide structures formed on nickel-chromium alloy during low pressure oxidation at 500–600°C // Oxid. Met. 1990. V. 33. № 5–6. P. 458–479.
Ишлинский А.Ю. Новый политехнический словарь. М.: Большая Российская энциклопедия, 2000. 672 с.
Бугров А.Н., Альмяшева О.В. Формирование наночастиц Cr2O3 в гидротермальных условиях // Наносистемы: физика, химия, математика. 2011. Т. 2. № 4. С. 126–132.
Kondrat'ev S.Yu., Sviatysheva E.V., Anastasiadi G.P., Petrov S.N. Fragmented structure of niobium carbide particles in as-cast modified HP alloys // Acta Mater. 2017. V. 127. P. 267–276.
Федоров И.П. Химическая энциклопедия. Т. 5. Хрома оксиды. Изд-во “Большая Российская энциклопедия”, 1999. С. 311–313.
Zapała R., Kalandyk B. Identification of scale formed on Cr–Ni cast steel // Arch. Foundry Eng. 2010. V. 10. № 4. P. 217–220.
Voicu R., Andrieu E., Poquillon D., Furtado J., Lacaze J. Microstructure evolution of HP40–Nb alloys during aging under air at 1000°C // Mater. Charact. 2009. V. 60. № 9. P. 1020–1027.
Kondrat’ev S.Yu., Ptashnik A.V., Anastasiadi G.P., Petrov S.N. Analysis of transformations of carbide phases in alloy 25Cr35Ni by the method of quantitative electron microscopy // Met. Sci. Heat Treat. 2015. V. 57. № 7–8. P. 402–409.
Koopmans L.H., Owen D.B., Rosenblatt J.I. Confidence intervals for the coefficient of variation for normal and log normal distributions // Biometrika. 1964. V. 51. P. 25–32.
Patel J.K., Patel N.M., Shiyani R.L. Coefficient of variation in field experiments and yardstick thereof – An empirical study // Curr. Sci. 2001. V. 81. № 9–10. P. 1163–1164.
Voitovich R.F., Pugach É.A. High-temperature oxidation characteristics of the carbides of the Group VI transition metals // Powder Metall. Met. Ceram. 1973. V. 12. P. 314–318.
Babakr A.M., Al-Ahmari A., Al-Jumayiah K., Habiby F. Sigma Phase Formation and Embrittlement of Cast Iron–Chromium–Nickel (Fe–Cr–Ni) Alloys // J. Miner. Mater. Char. Eng. 2008. V. 7. P. 127–145.
Kondrat’ev S.Y., Anastasiadi G.P., Petrov S.N., Ptashnik A.V. Kinetics of the Formation of Intermetallic Phases in HP-Type Heat-Resistant Alloys at Long-Term High-Temperature Exposure // Metall. Mater. Trans. 2017. V. 48A. P. 482–492.
Дополнительные материалы отсутствуют.
Инструменты
Физика металлов и металловедение