Физика металлов и металловедение, 2021, T. 122, № 4, стр. 388-395
Электронно-микроскопические исследования выделений избыточных фаз, оказывающих влияние на межкристаллитную коррозию хромоникелевых аустенитных сталей
А. Н. Мазничевский a, b, *, Ю. Н. Гойхенберг b, **, Р. В. Сприкут a, ***
a ООО “Ласмет”
454047 Челябинск, ул. 2-я Павелецкая, 18, ком. 207, Россия
b Южно-Уральский государственный университет (НИУ)
454080 Челябинск, просп. В.И. Ленина, 76, Россия
* E-mail: al.mazn@ya.ru
** E-mail: goikhenbergyn@susu.ru
*** E-mail: mail@lasmet.ru
Поступила в редакцию 24.07.2020
После доработки 03.09.2020
Принята к публикации 29.10.2020
Аннотация
Проведены электронно-микроскопические исследования выделений карбидов, нитридов, карбоборидов, влияющих на межкристаллитную коррозию (МКК) в сильно окислительных средах хромоникелевых аустенитных сталей с различной концентрацией азота, кремния и микролегированных бором и РЗМ. Установлено, что МКК обусловлена, в основном, выделением при провоцирующем нагреве карбидов или карбоборидов хрома типа Cr23(C,B)6, в большей мере обедняющих приграничные области хромом, чем нитриды. Низкой скорости коррозии соответствует более низкая плотность дислокаций. Определены концентрации бора и РЗМ, не оказывающие отрицательного влияния на МКК.
ВВЕДЕНИЕ
Вопрос о механизме влияния таких элементов как кремний, входящий в состав большого числа аустенитных сталей в количестве от 0.2 до 1.0 мас. %, азот, бор и редкоземельные металлы (РЗМ) на межкристаллитную коррозию (МКК) нержавеющих сталей в сильно окислительных средах все еще остается дискуссионным [1–3].
Введение кремния в хромоникелевые нержавеющие стали в качестве легирующего элемента способствует улучшению коррозионной стойкости [3–5]. Вместе с тем повышение содержания кремния ухудшает пластичность сталей при горячей обработке давлением [6]. В то же время малые добавки РЗМ и бора улучшают деформируемость аустенитных сплавов в горячем состоянии [7, 8], но их влияние на коррозионную стойкость изучено недостаточно.
Также следует отметить, что наряду с “безазотистыми” нержавеющими сталями все большее применение находят коррозионностойкие стали легированные азотом и кремнием, обладающие одновременно высокой прочностью, пластичностью, стойкостью против коррозионного растрескивания, износостойкостью и низким коэффициентом трения [9–12].
Целью настоящей работы были электронно-микроскопические исследования выделений избыточных фаз, влияющих на коррозионную стойкость хромоникелевых аустенитных сталей с различной концентрацией азота и кремния, а также микролегированных бором и РЗМ.
МАТЕРИАЛ И МЕТОДИКА ИССЛЕДОВАНИЯ
Выплавлены аустенитные Cr–Ni-стали на основе серийной 03Х18Н11 с концентрациями кремния от 0.14 до 0.78 мас. %, а также содержащие азот в количестве от 0.16 до 0.30 мас. % и микролегированные бором и РЗМ (табл. 1). Влияние бора и РЗМ на коррозионную стойкость стали изучали после фракционной разливки плавок, в ходе которых в один из слитков с концентрацией кремния 0.38 мас. % или азота с концентрацией 0.30 мас. %, вводили бор или РЗМ. Выплавленные слитки были продеформированы методом свободной ковки и прокатки до заготовок требуемого сечения по режимам, использующимся для деформации нержавеющих аустенитных сталей. Заготовки исследуемых нержавеющих сталей подвергали закалке в воду на аустенит от температур 1050 до 1150°С. Провоцирующий нагрев проводили в температурном диапазоне от 500 до 850°С и выдержках от 1 до 100 ч.
Таблица 1.
Химический состав исследованных сталей
Сталь | Химический состав, мас. % | ||||||
---|---|---|---|---|---|---|---|
C | Si | Mn | Cr | Ni | N | * | |
03Х18Н11 | 0.024 | 0.65 | 0.95 | 18.34 | 11.07 | 0.05 | – |
02Х18Н11ГС0,14 | 0.022 | 0.14 | 1.02 | 17.82 | 11.21 | 0.05 | – |
02Х18Н11ГС0,38 | 0.021 | 0.38 | 1.00 | 17.80 | 11.20 | 0.04 | – |
02Х18Н11ГС0,38Р | 0.021 | 0.38 | 1.00 | 17.80 | 11.20 | 0.04 | 0.0015 В |
02Х18Н11ГС0,38Ч | 0.021 | 0.38 | 1.00 | 17.80 | 11.20 | 0.04 | 0.042 Се |
02Х18Н11ГС0,78 | 0.020 | 0.78 | 1.02 | 17.82 | 11.21 | 0.05 | – |
03Х18Н11ГС0,78 | 0.030 | 0.78 | 1.01 | 17.80 | 11.20 | 0.05 | – |
03Х18Н11Г1А0,16 | 0.022 | 0.56 | 1.35 | 18.30 | 11.11 | 0.16 | – |
03Х20Н9Г3А0,30 | 0.025 | 0.30 | 3.02 | 20.26 | 9.60 | 0.30 | – |
03Х20Н9Г3А0,29Р | 0.023 | 0.30 | 3.02 | 20.30 | 9.60 | 0.29 | 0.0015В; 0.0024В; 0.01 B |
03Х20Н9Г3А0,29Ч | 0.025 | 0.29 | 3.05 | 20.23 | 9.61 | 0.29 | 0.016 Y; 0.020Y; 0.037Y |
Микроструктуру сталей изучали с применением оптического микроскопа Carl Zeiss Axio Observer. Электронно-микроскопические исследования тонкой структуры проводили на тонких фольгах с использованием просвечивающего электронного микроскопа JEOL 2000EXI при ускоряющем напряжении до 200 кВ. Заготовки фольг диаметром 3 мм и толщиной 1 мм вырезали из образцов после коррозионных испытаний. Идентификацию фазовых составляющих осуществляли в режимах микродифракции и получения светлопольных или темнопольных изображений.
Подготовку образцов для коррозионных испытаний осуществляли в соответствии с ГОСТ 6032–2017 (метод ДУ). Испытания проводили в кипящем 65% водном растворе азотной кислоты в течение 5 циклов (по 48 ч каждый) или более жесткие – в растворе, содержащем 27% HNO3 и 4 г/л Cr+6, при температуре кипения. Ионы Cr+6 вводили в раствор в виде добавки дихромата калия K2Cr2O7. Все испытания осуществляли при постоянном наблюдении за шлифами под микроскопом.
Скорость коррозии определяли по потере массы двух образцов, испытанных параллельно, независимо друг от друга. При этом один из образцов был приготовлен в виде металлографического шлифа для последующего наблюдения под микроскопом за характером травления стали. После испытаний коррозионной стойкости на одном из двух образцов делали поперечный срез, который затем шлифовали и полировали для измерения глубины проникновения межкристаллитной коррозии.
За предельно допустимый (критический) уровень коррозионных потерь принимали скорость коррозии 0.5 мм/год в соответствии с требованиями ГОСТ 6032–2017.
РЕЗУЛЬТАТЫ ИССЛЕДОВАНИЯ И ИХ ОБСУЖДЕНИЕ
Установлено, что травление (межкристаллитная коррозия) закаленной “безазотистой” стали типа 03Х18Н11 с пониженным содержанием кремния (0.14 мас. %) происходило как по границам зерен, так и, в основном, по границам двойников. Границы зерен при этом были протравлены слабо и неравномерно. С увеличением содержания кремния до 0.38 мас. %, степень травления границ зерен увеличивается и становится соизмеримой со степенью травления границ двойников. При содержании кремния 0.78 мас. %, границы зерен начинают травиться более интенсивно, чем границы двойников. При этом средняя скорость коррозии сталей (0.20–0.25 мм/год) более чем в 2 раза ниже предельно допустимого уровня коррозионных потерь и не зависит от концентрации кремния.
Электронно-микроскопические исследования состояния границ зерен в закаленных сталях (Тзак = = 1080 и 1150°С) не выявили на границах зерен избыточных фаз, что коррелирует с высокой коррозионной стойкостью сталей.
Для установления влияния содержания кремния на стойкость закаленных образцов к межкристаллитной коррозии в окислительных условиях, испытания ужесточили введением в раствор ионов Cr+6 (табл. 2). Видно, что в ужесточенных условиях испытания с ионами Cr+6 все образцы показывают высокую склонность к МКК, но наблюдается явная зависимость коррозионного повреждения сталей от содержания кремния. В высококремнистой стали 02Х18Н11ГС0,78 выпадение зерен с поверхности исследуемых образцов было отмечено уже на первом цикле испытаний, в то время как на образцах с меньшим содержанием кремния (0.14 и 0.38%) только на втором цикле испытаний.
Таблица 2.
Результаты испытаний коррозионной стойкости закаленных нержавеющих сталей в кипящем растворе 27% HNO3 + 4 г/л Cr+6
Концентрация элемента | Средняя скорость коррозии, мм/год | Глубина проникновения МКК, мм | |
C, мас. % | Si, мас. % | ||
0.022 | 0.14 | 1.388 | 0.025 |
0.021 | 0.38 | 3.327 | 0.137 |
0.020 | 0.78 | 5.860 | 0.192 |
Более важным является исследование коррозионной стойкости нержавеющих сталей в состоянии сенсибилизации после провоцирующего нагрева (табл. 3). Видно, что с возрастанием содержания кремния у стали повышаются коррозионные потери. Так после закалки с 1080°C и провоцирующего нагрева при 650°С в течение 1 ч скорость коррозии увеличивается с 0.190 мм/год у стали содержащей 0.14% кремния до 0.489 мм/год при содержании кремния 0.78%, т.е. в 2.5 раза.
Таблица 3.
Результаты испытаний коррозионной стойкости сенсибилизированных (при 650°С, 1 ч) нержавеющих сталей в кипящем 65% растворе азотной кислоты
Концентрация элемента | Средняя скорость коррозии, мм/год | ||
---|---|---|---|
C, мас. % | Si, мас. % | Другое, мас. % | |
0.022 | 0.14 | – | 0.190 |
0.021 | 0.38 | – | 0.248 |
0.021 | 0.38 | 0.0015 В | 2.506 |
0.021 | 0.38 | 0.042 РЗМ | 0.234 |
0.020 | 0.78 | – | 0.489 |
0.030 | 0.78 | – | 16.340 |
Вместе с тем нельзя не отметить тот факт, что даже при повышенном содержании кремния (0.78 мас. %), но низком содержании углерода (0.020 мас. %) величина коррозионных потерь не превышает критической нормы. Увеличение концентрации углерода всего на 0.01 мас. % (сталь 03Х18Н11ГС0.78) приводит к колоссальному росту скорости коррозии с 0.489 мм/год до 16.340 мм/год, т.е. более чем в 30 раз.
Исследование микроструктуры стали и состояния границ зерен в образцах, прошедших испытания по методу ДУ после провоцирующего нагрева, подтвердило явно неблагоприятное влияние сенсибилизациии на склонность нержавеющей стали к межкристаллитной коррозии в кипящей азотной кислоте. Наблюдается повышенная и практически непрерывная травимость границ зерен в стали с высоким содержанием кремния и меньшее растравливание при низком.
Электронно-микроскопические исследования фольг на просвет показали, что в стали с низкой концентрацией кремния (0.14 мас. %) провоцирующий нагрев после закалки не вызывает заметных изменений состояния границ зерен (рис. 1а), в то время как в стали с повышенным содержанием кремния (0.78 мас. %) провоцирующий нагрев приводит к выделению на границах зерен цепочек или колоний дисперсных частиц избыточной фазы (рис. 1б).
Рис. 1.
Электронно-микроскопическое изображение состояния границ зерен сталей 02Х18Н11ГС0,14 (а) и 02Х18Н11ГС0,78 (б), подвергнутых закалке и провоцирующему нагреву в течение 10 ч при 650°С. На рис. 1б сверху приведена электроннограмма с осью зоны 〈120〉, снятая с выделения, обозначенного стрелкой.
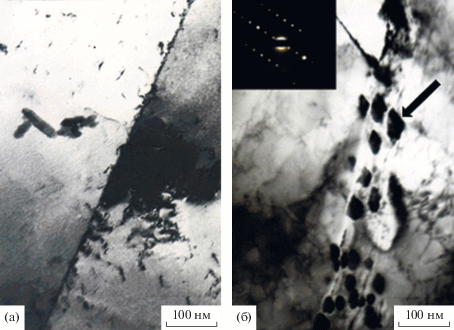
Электроннограмма с одного из выделений, обозначенного стрелкой на рис. 1б, свидетельствует о том, что оно представляет собой монокристалл и когерентно связано с матрицей. Расчет общей дифракционной картины участка фольги стали 02Х18Н11ГС0,78 (рис. 2) показывает, что элементарная ячейка избыточной фазы почти в три раза больше элементарной ячейки матрицы и имеет, как и аустенитная матрица, ГЦК-решетку. Расчет показал, что кремний практически не изменяет размер элементарной ячейки аустенита вдали от границы зерна, где a = 3.565 Å, и существенно уменьшает параметр решетки (a) в приграничных объемах до 3.530 Å. Параметр решетки проидентифицированной исследуемой фазы, являющейся соединением типа Cr23С6, составляет 10.615 Å и несколько отличается от параметра решетки карбида Cr23С6, который равен 10.65 Å.
Рис. 2.
Электроннограмма закаленной стали 02Х18Н11ГС0,78, подвергнутой провоцирующему нагреву при 650°С в течении 10 ч (а), и ее индицирование (б).
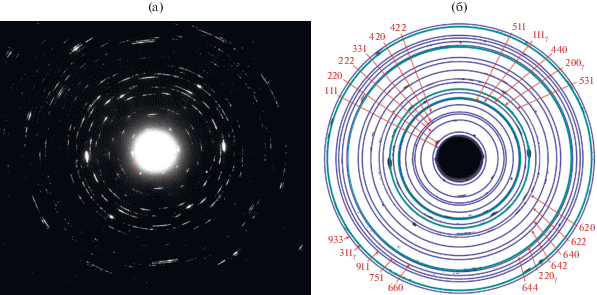
Полученные результаты согласуются с данными работы [13], в которой изучали влияние содержания кремния (0.09–1.03 мас. %) на стойкость к МКК в азотной и серной кислотах стали 12Х18Н10Т и установили пониженную стойкость у образцов, имеющих высокое содержание кремния. Авторы работы считают, что механизм образования таких неравновесных сегрегаций кремния основан на гипотезе накопления примесей вблизи границ из-за движения “вакансионно-примесных атомных комплексов” к границам зерен и фиксации этого состояния при закалке. При этом предполагается, что несовершенство структуры вблизи границ зерен может расти за счет увеличения плотности дислокаций и накопления вакансий. Это было показано в работе [14], где в стали 03Х18Н11 с низким содержанием кремния (менее 0.1 мас. %) дислокации расположены в виде равномерно распределенных ячеек по телу и у границ зерен, а в высококремнистых сталях с 0.8% Si, наблюдаются компланарные скопления дислокаций вдоль границ зерен, и их количество в два раза больше, чем в объеме зерна.
Таким образом, полученные результаты позволяют сделать вывод, что в Cr–Ni-сталях с низким содержанием углерода при концентрации кремния на верхнем пределе (0.78 мас. %) после закалки от 1080°C в процессе последующего нагрева при 650°С по границам зерен выделяются соединения типа Cr23С6 с измененным параметром решетки (несоответствие составляет ~0.33%), что обусловлено вхождением в состав карбида некоторого количества кремния, имеющего меньший атомный радиус чем у хрома (1.18 и 1.28 Å соответственно).
Эти включения имеют определенную ориентационную связь с прилегающим слоем матрицы. Когерентная связь избыточной фазы с аустенитом становится возможной благодаря уменьшению параметра решетки аустенита в непосредственной близости от карбидных включений с 3.565 до 3.530 Å (т.е. примерно на 1%), при этом появляется кратность (равная трем единицам) параметров решетки карбида и аустенита. Уменьшение параметра решетки аустенита в узкой приграничной зоне свидетельствует о расслоении твердого раствора. Кремний, как горофильный элемент, концентрируясь на границах зерен и растворяясь в матрице по типу замещения, уменьшает параметр решетки аустенита, создавая твердый раствор “матрица–кремний” определенного и постоянного состава. От содержания кремния в стали и предварительной термической обработки (температуры нагрева, времени выдержки и т.п.) зависит ширина слоя аустенита с уменьшенным параметром решетки, т.е. степень развития расслоения аустенита – состояния, определяющего готовность к выделению избыточной фазы по границам зерен.
Стали с повышенным содержанием азота (0.16–0.30 мас. %) и низкой концентрацией углерода (менее или равном 0.03 мас. %) обладают высокой коррозионной стойкостью при испытаниях по методу ДУ в кипящем 65% растворе азотной кислоты (табл. 4). При увеличении содержания углерода до 0.037; 0.052 и 0.060 мас. % в той же системе легирования скорость коррозии возрастает до 6–7 мм/год (табл. 4).
Таблица 4.
Результаты испытаний коррозионной стойкости закаленных и сенсибилизированных (при 650°С, 1 ч) нержавеющих сталей с разной концентрацией азота и углерода в кипящем 65% растворе азотной кислоты
Концентрация элемента | Температура аустенитизации, °С | Средняя скорость коррозии, мм/год | |
---|---|---|---|
C, мас. % | N, мас. % | ||
0.025 | 0.30 | 1050 | 0.252 |
1100 | 0.217 | ||
0.030 | 0.27 | 1050 | 0.382 |
1100 | 0.204 | ||
0.060 | 0.23 | 1050 | 6.706 |
1100 | 7.400 | ||
0.052 | 0.21 | 1050 | 7.202 |
1100 | 6.357 | ||
0.037 | 0.16 | 1050 | 1.023 |
1100 | 0.716 |
Электронно-микроскопические исследования свидетельствуют о том, что высокая коррозионная стойкость характеризуется меньшей плотностью дислокаций, и это особенно четко обнаруживается при рассмотрении приграничных зон и когерентных границ двойников (рис. 3). Дислокации при этом распределены неравномерно, образуя ячеистую структуру (рис. 3а, 3б). В то же время в стали 06Х20Н9Г3А0.23 с высоким содержанием углерода и пониженной коррозионной стойкостью наблюдается повышенная плотность дислокаций (рис. 3в). Повышенная плотность дислокаций, дефекты укладки атомов и поля микронапряжений вокруг них являются термодинамически выгодными местами для размещения (сегрегации) большого количества примесных атомов, в частности, углерода (по принципу атмосфер Котрелла). Это приводит к образованию, как локальных электрохимических ячеек с избирательным растворением активных анодных участков, так и к облегчению образования карбидов хрома и обеднению хромом твердого раствора.
Рис. 3.
Тонкая структура сталей 03Х20Н9Г3А0.30, имеющей высокую (а, б), и 06Х20Н9Г3А0.23, имеющей низкую (в) коррозионную стойкость. Режим термической обработки образцов: а, в – закалка 1050°С, 30 мин, вода + нагрев 650°С, 1 ч, воздух; б – закалка 1100°С, 30 мин, вода + нагрев 650°С, 1 ч, воздух.
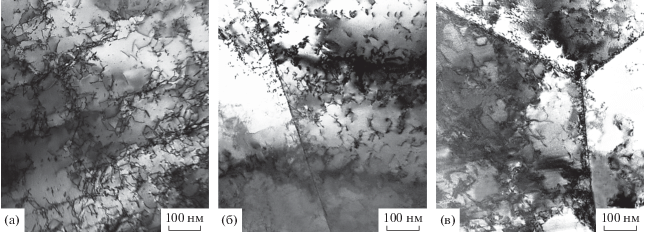
Для установления температурно-временной области склонности азотистой стали 03Х20Н9Г3А0.30 к межкристаллитной коррозии строили диаграмму Ролласона после провоцирующего нагрева при различных температурах и испытаниях в кипящем 65% растворе азотной кислоты (рис. 4). На ней показано, что после провоцирующего нагрева в течение 1 ч при 650°С, скорость коррозии стали 03Х20Н9Г3А0.30 составляет 0.22 мм/год. При этом глубина проникновения межкристаллитной коррозии достигает 20 мкм. Сравнение сталей 03Х20Н9Г3А0.30 и 03Х18Н11 свидетельствует о том, что критическое время выдержки стали, содержащей азот, увеличивается до 16 часов при температуре 650°С, и положение всей области склонности этой стали к межкристаллитной коррозии смещается вправо в область больших выдержек. Нагрев при 600 и 650°С в течение 100 ч вызывает сенсибилизацию и скорость коррозии при этом увеличивается до 1.0–1.5 мм/год, а в структуре стали обнаруживаются избыточные фазы – карбиды и нитриды хрома.
С понижением температуры нагрева до 550°С при сточасовой выдержке происходит выделение значительно большего количества карбидов, чем нитридов, что приводит к увеличению глубины проникновения межкристаллитной коррозии выше 70 мкм и увеличению скорости коррозии до 12 мм/год.
Разделить непосредственное влияние на межкристаллитную коррозию карбидов и нитридов не представляется возможным. Однако, по-видимому, основная роль в возникновении и развитии МКК принадлежит карбидам хрома, о чем свидетельствует тот факт, что, когда выделяются нитриды при температурах выше 750°С скорость коррозии оказывается очень низкой (после сточасовой выдержки при 750°С всего 0.4 мм/год). В то же время при провоцирующем нагреве в течение 100 ч при 550°С, когда преимущественно выделяются карбиды хрома, скорость коррозии оказывается очень высокой (12 мм/год). Это обусловлено тем, что стехиометрически в карбиды Cr23C6 хром входит в значительно большем количестве, чем в нитриды Cr2N. Это приводит к большему обеднению приграничных областей хромом и большему развитию межкристаллитной коррозии.
При коррозионных испытаниях сенсибилизированных азотистых аустенитных сталей, микролегированных бором или редкоземельными металлами, было установлено, что введение этих элементов в малых количествах (бора до 0.0024 мас. %, а РЗМ до 0.037 мас. %) не оказывает отрицательного влияния на МКК. При таких малых добавках бора и РЗМ в сталь 03Х20Н9Г3А0,30 коррозионные потери при испытаниях по методу ДУ составляют не более 0.35 мм/год (табл. 5). Однако при увеличении концентрации бора до 0.01 мас. %, скорость коррозии возрастает до 1.328 мм/год, и границы зерен растравливаются в большей мере. В то же время при микролегировании хромоникелевых аустенитных сталей большими количествами РЗМ у границ зерен сохраняется низкая травимость. Оказалось, что при микролегировании 0.01 мас. % бора на границах зерен нержавеющей стали после провоцирующего нагрева четко выявляется избыточная фаза (рис. 5).
Таблица 5.
Влияние микролегирования бором и РЗМ на коррозионную стойкость стали 03Х20Н9Г3А0.30 в кипящем 65% растворе азотной кислоты
Сталь | Концентрация элемента | Средняя скорость коррозии, мм/год | ||
---|---|---|---|---|
C, мас. % | N, мас. % | Другое, мас. % | ||
03Х20Н9 Г3А0.30 | 0.025 | 0.30 | – | 0.252 |
03Х20Н9 Г3А0.29Р | 0.0015 В | 0.275 | ||
0.023 | 0.29 | 0.0024 В | 0.332 | |
0.01 В | 1.328 | |||
0.02 РЗМ | 0.189 | |||
03Х20Н9 Г3А0.29Ч | 0.025 | 0.29 | 0.016 Y | 0.220 |
0.020 Y | 0.230 | |||
0.037 Y | 0.220 |
Рис. 4.
Область склонности к межкристаллитной коррозии в кипящем 65% растворе азотной кислоты
сенсибилизированных сталей 03Х18Н11 (ограничена штриховой кривой) и 03Х20Н9Г3А0.30
(сплошной); точки обозначают экспериментальные данные для стали 03Х20Н9Г3А0.30, где
⚪ скорость коррозии менее 0.3 мм/год; () скорость коррозии менее 0.5 мм/год; (⚫) скорость коррозии более 0.5 мм/год.
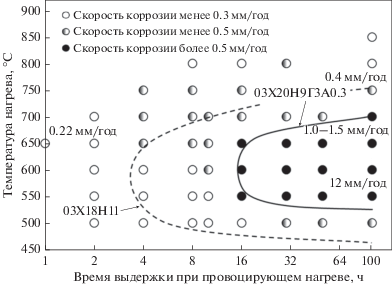
Рис. 5.
Выделения по границам зерен стали, содержащей 0.01 мас. % бора, после закалки от 1080°С и 10 ч выдержки при 650°С.
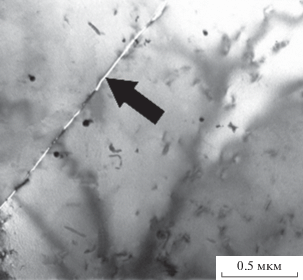
Расчет электроннограмм, снятых с частиц этой избыточной фазы (отмечены стрелкой), позволяет идентифицировать их как карбобориды типа Cr23(C,N,B)6 и бориды Cr3B4. Выделение значительных количеств карбоборидов Cr23(C,N,B)6 и боридов Cr3B4, образующих практически непрерывную прослойку между зернами, существенно обедняет приграничные участки хромом, что приводит к увеличению скорости межкристаллитной коррозии при повышенной концентрации бора.
ВЫВОДЫ
1. Уменьшение концентрации кремния в Cr–Ni аустенитных сталях с 0.78 до 0.14 мас. % повышает коррозионную стойкость сталей в закаленном и, особенно, сенсибилизированном состоянии. Показано, что низкая коррозионная стойкость сенсибилизированной стали обусловлена выделением на границах зерен карбидов Cr23С6, а увеличение концентрации кремния до 0.78 мас. % интенсифицирует этот процесс, сопровождающийся расслоением аустенита на обеденный и обогащенный кремнием твердый раствор.
2. Определены условия стойкости азотистой Cr–Ni-стали 03Х20Н9Г3А0.30 к межкристаллитной коррозии. Установлено, что основную роль в возникновении МКК играют выделяющиеся при сенсибилизации карбиды хрома, в большей мере обедняющие приграничные области хромом, чем нитриды.
3. Установлено, что микролегирование азотистой аустенитной стали даже малыми количествами бора (0.01 мас. %) приводит при провоцирующем нагреве к резкому ухудшению ее стойкости к межкристаллитной коррозии в связи с выделением по границам зерен непрерывной прослойки боридов Cr3B4 и карбоборидов типа Cr23(C,N,B)6, что существенно обедняет приграничные участки хромом и увеличивает скорость коррозии. Напротив, микролегирование аналогичной Cr–Ni-стали более высокими количествами РЗМ (0.037 мас. %) не ухудшает ее коррозионную стойкость.
4. Электронно-микроскопическими исследованиями установлено, что высокая коррозионная стойкость реализуется при низкой плотности образующих ячеистую микроструктуру неравномерно распределенных дислокаций, в то время как при повышенной плотности дислокаций поля микронапряжений вокруг них оказываются термодинамически выгодными местами для сегрегации большого количества примесных атомов, что приводит к возникновению как локальных электрохимических ячеек с избирательным растворением активных анодных участков, так и к облегчению образования карбидов хрома и обеднению хромом твердого раствора.
Список литературы
Науменко В.В. Влияние азота и кремния на механические и коррозионные свойства низкоуглеродистой аустенитной стали для применения в сильноокислительных средах / Дис. … канд. техн. наук: 05.16.01. М.: Центр. науч.-исслед. ин-т чер. металлургии им. И.П. Бардина, 2012. 162 с.
Robin R., Miserque F., Spagnol V. Correlation between composition of passive layer and corrosion behavior of high Si-containing austenitic stainless steels in nitric acid // J. Nuclear Materials. 2008. V. 375. № 1. P. 65–71.
Wilde B.E. Influence of Silicon on the Intergranular Corrosion Behavior of 18Cr–8Ni Stainless Steels // Corrosion Science. 1988. V. 44. № 10. P. 699–704.
Каспарова О.В. Особенности межкристаллитной коррозии кремнийсодержащих аустенитных нержавеющих сталей // Защита металлов. 2004. Т. 40. № 5. С. 475–481.
Ningshen S., Mudali U.K., Amarendra G., Raj B. Corrosion assessment of nitric acid grade austenitic stainless steels // Corrosion Science. 2009. V. 51. № 2. P. 322–329.
Huang K., Logé R.E. Microstructure and flow stress evolution during hot deformation of 304L austenitic stainless steel in variable thermomechanical conditions // Materials Science and Engineering 2018. V. 711. P. 600–610.
Приданцев М.В. Влияние примесей и редкоземельных элементов на свойства сплавов. М.: Металлургиздат, 1962. 208 с.
Ланская К.А. Жаропрочные стали. М.: Металлургия, 1969. 247 с.
Goykhenberg Yu.N., Zhuravlev L.G., Mirzayev D.A., Zhuravleva V.V., Silina Ye.P., Vnukov V.Yu. Corrosion cracking, Structure and Properties of Hardened Cr–Mn austenitic Steels with Nitrogen // The Physics of Metals and Metallography. 1988. V. 65. № 6. P. 83–89.
Коршунов Л.Г., Гойхенберг Ю.Н., Черненко Н.Л. Влияние кремния на структуру, трибологические и механические свойства азотсодержащих Cr–Mn аустенитных сталей // ФММ. 2003. Т. 96. № 3. С. 100–110.
Мушникова С.Ю., Костин С.К., Сагарадзе В.В., Катаева Н.В. Структура, свойства и сопротивление коррозионному растрескиванию азотсодержащей аустенитной стали, упрочненной термомеханической обработкой // ФММ. 2017. Т. 118. № 11. С. 1223–1235.
Сагарадзе В.В., Катаева Н.В., Кабанова И.Г., Афанасьев С.В., Павленко А.В. Влияние температуры ударно-волнового воздействия на структурно-фазовые превращения азотистой аустенитной стали Cr–Mn–Ni // ФММ. 2020. Т. 121. № 7. С. 750–756.
Solntsev Yu.P., Ermakov B. S., Malikov S.O. Role of Si in the formation of the corrosion resistance of austenitic materials for cryogenic engineering // Russian Met. (Metally). 2008. V. 2. P. 133–137.
Ермаков Б.С., Солнцев Ю.П. Межкристаллитная коррозия как главный фактор повышенного разрушения оборудования, изготовленного из аустенитных сталей // Балтийский металлы. 2000. № 2. С. 18–21.
Дополнительные материалы отсутствуют.
Инструменты
Физика металлов и металловедение