Физика металлов и металловедение, 2021, T. 122, № 5, стр. 553-564
Сравнительное исследование стальных образцов H20: аддитивное производство и порошковая металлургия
С. Насар a, Л. Дж. Барух b, С. Дж. Вижай c, С. К. Сринавас a, Дж. Жозе c, В. В. Попов d, *
a Madanapalle Institute of Technology & Science
Andhra Pradesh, India
b MVJ College of Engineering
Bangaluru, Karnataka, India
c Karunya Institute of Technology and Sciences
Coimbatore, Tamil Nadu, India
d Israel Institute of Metals, Technion’s R&D Foundation
3200003 Haifa, Israel
* E-mail: vvp@technion.ac.il
Поступила в редакцию 05.06.2020
После доработки 24.08.2020
Принята к публикации 07.10.2020
Аннотация
Аддитивное производство – одна из революционных технологий современной промышленности. Эта технология раз за разом подтверждает, что с ее помощью можно изготавливать практически любой материал, если используется правильный процесс и подобраны его параметры. Традиционные технологии, такие как порошковая металлургия, также занимают ключевые позиции в обрабатывающей промышленности несмотря на их ограниченность в производстве изделий сложных форм. В этой работе были изготовлены цилиндрические детали с помощью обеих технологий, и проведено сравнение их свойств. Исследование показало, что оба материала имеют схожую микроструктуру, но при использовании порошковой металлургии были получены более высокие механические свойства. Однако было замечено, что трибологические свойства лучше у аддитивно изготовленных деталей.
ВВЕДЕНИЕ
Аддитивное производство (АП) – это технология производства, в которой детали или компоненты создаются путем последовательного добавления материала в виде слоев согласно цифровой модели. По стандарту ASTM АП – это процесс, в котором материалы соединяются для изготовления желаемых продуктов согласно данным 3D-модели CAD, обычно один слой последовательно наносится за другим, в отличие от технологий удаления материала, которые используются для изготовления тех же самых изделий [1].
После многих лет обширных исследований АП теперь успешно применяется в различных областях, таких как биомедицина [2], автомобильная отрасль [3], аэрокосмическая отрасль [4], медицинские устройства [5], ювелирные изделия, музыкальные инструменты и искусство [6, 7]. Короткий цикл разработки продукта и высокое качество продукта [8], характеризующие АП технологию, а также ее способность производить функциональные материалы [9, 10] сделали ее одной из самых перспективных, растущих и хорошо зарекомендовавших себя технологий в современной промышленности.
Порошковая металлургия (ПМ) появилась задолго до технологии АП. ПМ дает широкие возможности для производства изделий сложной геометрии и микропроизводства. Спекание, в свою очередь, это один из самых распространенных методов, используемых для изготовления изделий из металлических и керамических порошков.
На рис. 1 показаны основные этапы производства в металлическом АП и ПМ. В обоих процессах в качестве сырья используется порошок. Однако для металлического AП применимы только сферические порошки, поскольку сыпучесть порошка является ключевым параметром для успешного производства. Для процессов ПМ сыпучесть порошка не имеет решающего значения. Следовательно, можно использовать порошки неправильной формы.
Из рис. 1 видно, что основным отличием технологической цепочки являются этапы производства [11].
И АП, и ПМ требуют термической обработки, постобработки и чистовой обработки. Таким образом, можно сказать, что основное различие в производственной цепочке состоит в том, что АП позволяет изготавливать компоненты со свободой дизайна, а также со сложной геометрией и высокими механическими свойствами. Это делает АП многообещающей производственной технологией.
Настоящее исследование сосредоточено на определении подходящего производственного процесса, особенно с точки зрения улучшенния механических свойств, таких как износ, твердость, а также гибкости процесса для производства сложных деталей за минимальное время.
ПМ – это широкий спектр технологий, в которых компоненты изготавливаются с использованием микро- и нанопорошков. В значительной степени это исключает потери материала с коэффициентом преобразования материала более 90%, тем самым снижая общую стоимость продукта. Порошок, используемый в процессе ПМ, прессуется в специально разработанной пресс-форме, которая называется “зеленой” заготовкой. Затем ее спекают в высокотемпературной печи с приложением давления к детали во время нагрева или без него. Основные этапы ПМ показаны на рис. 1.
Метод лазерного спекания является одним из самых промышленно распространенных АП процессов из-за его способности изготавливать металлические детали с высокой точностью размеров и производить сложные геометрические компоненты. Однако, чтобы установить его пригодность для замены других производственных технологий, необходимо изучить такие свойства материала, как трибологические свойства и твердость. Стандартные параметры процессов лазерного сплавления (SLM) и спекания (DMLS): расстояние между линиями прохождения лазера (HD); мощность лазера (LP); скорость лазерного сканирования (LSS) и т.д.
Многие стальные инструменты подвергаются сильному износу [12]. Однако число работ посвященных влиянию параметров лазерного процесса на трибологические свойства деталей из стали, спеченных лазером, ограничено.
Ramesh и др. изготовили железные детали с использованием метода DMLS [13]. Эти детали продемонстрировали повышенную плотность, микротвердость и радикальное увеличение прочности на разрыв, пластичность и износ при более низкой скорости сканирования.
Keshavamurthy и др. оптимизировали технологические параметры АП для стали H13 на основе техники Тагучи с ортогональной решеткой L9 [14]. Они оптимизировали параметры процесса: LP 400Вт, LSS 200мм/мин и скорость потока порошка: 1г/мин.
Казанцева и др. исследовали лазерное сплавление нержавеющей стали с магнитными свойствами [15]. Было обнаружено, что микроструктура мартенситностареющей нержавеющей стали, изготовленной АП методом, отличается от производимой традиционным способом. Это было дополнительно подтверждено в [16].
Khorsand и др. оценили влияние технологических параметров ПМ на усталостную прочность и трибологические характеристики спеченной низколегированной стали Fe–1.75, Ni–1.5, Cu–0.5, Mo–0.6 C [17]. Результаты показывают, что эти свойства были значительно улучшены за счет термической обработки для уменьшения пористости.
Ceschini и др. изучали влияние параметров процесса ПМ на трибологическое поведение спеченной стали Fe–C–Mo и Fe–C–Cr в условиях сухих и абразивных испытаний [18]. Было установлено, что сталь Fe–C–Mo работает лучше, чем сталь Fe–C–Cr при тех же переменных процесса.
Senthur и др. провели исследования износа в сухих условиях на спеченном и горячеэкструдированном материале с такими комбинациями, как Fe–1% C в качестве основного элемента, легированного вольфрамом и титаном и некоторыми другими элементами [19]. Увеличение нагрузки при спекании улучшило износостойкость рассматриваемого материала.
Из обзора литературы установлено, что исследователи проводят значительный объем работы по оценке физических и трибологических свойств деталей, произведенных обоими способами. Однако информации об исследованиях, сравнивающих их на основе физических и трибологических свойств полученных материалов, нет.
Настоящая работа направлена на сравнение физических и трибологических свойств стальных образцов, полученных методами ПМ и АП.
МЕТОДЫ И МАТЕРИАЛЫ
Стальной порошок H20 размером 20 мкм сферической формы был использован для изготовления АП и ПМ образцов. АП образцы были напечатаны с использованием машины EOSINT M250 в Центральном производственном технологическом институте в Бангалоре. Порошок H20 был тщательно утрамбован в резервуар поставщика, так что весь захваченный воздух был удален. Толщина слоя порошка поддерживалась на уровне 20 мкм. LSS варьировалось от 50 до 125 мм/с.
Для лазерного сканирования в АП использовался линейный шаблон полос вверх–вниз. Параметры АП (DMLS) представлены в табл. 1. LP – 240 Вт, и LSS будет оптимизирован для получения образцов с высокими механическими свойствами.
Таблица 1.
Параметры процесса АП (лазер)
Sl. no. | Параметры печати | Значение |
---|---|---|
1 | Расстояние между проходом лазера (HD) |
0.3 мм |
2 | Ширина штриховки (HW) | 5 мм |
3 | Толщина слоя | 20 мкм |
4 | Размер образцов | ∅12 × 8 мм |
5 | Время изготовления | 3 ч |
6 | Мощность луча (LP) | 240 Вт |
7 | Диаметр луча лазера | 0.4 мм |
8 | Скорость сканирования лазера (LSS) |
50~125 мм/с |
ПМ образцы были изготовлены в компании METMECH ENGINEERS, Ченнаи. “Спекание” было выбрано как широко используемый метод изготовления изделий, связанных с ПМ. Спекание следует за процедурой прессования и формования, чтобы получить твердую массу материала путем приложения тепла и/или давления без плавления до момента ликвации. Табл. 2 приводит подробные сведения о параметрах ПМ процесса.
Таблица 2.
Параметры процесса ПМ
Sl. no. | Параметры процесса | Range |
---|---|---|
1 | Температура | 900~950°C |
2 | Время спекания | 1~4 ч |
3 | Атмосфера процесса | Азот |
4 | Размер образцов | ∅20 × 10 |
5 | Скорость нагрева | 5°C/мин |
7 | Время релаксации в уплотнении | 2 мин |
8 | Время изготовления | 4 ч |
9 | Время уплотнения (4 образца) | 1 ч |
Необработанный прессованный материал помещали в электропечь при 950°C в атмосфере азота для спекания компонента. Стальной порошок уплотняют с приложенной нагрузкой 220 МПа с помощью ручного пресса. Это делается, чтобы повысить прочность и целостность. Температуру обычно поддерживают ниже точки плавления основной составляющей материала.
Материал Н20 обладает высокой прочностью, твердостью, высокой износостойкостью и поверхностной плотностью (табл. 3). Это делает его подходящим для инструментальной промышленности, особенно для непосредственного применения в инструментах, таких как вставки для литья под давлением и матрицы для литья.
Таблица 3.
Свойства стального порошка H20
No. | Свойства стали H20 | |
---|---|---|
1 | Прочность на растяжение (MPIF 10) | 1100 МПа |
2 | Модуль Юнга | 180 ГПа |
3 | Твердость | 350–420 HRC |
4 | Растяжение на разрыв | 4.0% |
5 | Хим. состав после АП (DMLS) | Fe + Cr, Ni, Mo, Si, V, C |
6 | Плотность (на поверхности) | 7.8 г/см3 |
7 | Плотность (внутри) | 7.0 г/см3 |
8 | Пористость | <0.5% |
9 | КТР | 13–15 × 10–6 м/м°C |
10 | Теплопроводимость | 15–18 Вт/мK |
11 | Макс.раб. температура | 1100 –1470°C |
Для изучения поверхности и микроструктуры использовались оптический и сканирующий электронный микроскоп (СЭМ) ZEISS JSM-6480 LV. Инвертированный тринокулярный металлургический микроскоп DE-WINTOR был использован для исследования фазового контраста и оценки размера зерна.
Микротвердость по Виккерсу измеряли с помощью прибора Clemex dual CMT 07-895 (Канада). Измерения проведены при постоянной нагрузке 0.3 г и времени выдержки 10 с в различных местах в направлениях построения. Испытания проводились в соответствии с требованиями ASTM E384, по крайней мере, по 8 измерений для каждого образца.
Чтобы определить плотность спеченных деталей, сначала образцы взвешивали в воздухе, а затем в воде и, применяя принцип Архимеда, были рассчитаны значения. Для измерения плотности использовали электронные весы Sartorius (MC 210S).
Тестер Pin-on-Disc (Ducom: TR-20LE-PHM400-CHE600) использовали для измерения характеристик износа АП и ПМ образцов. Эти эксперименты проводили с постоянной нагрузкой 20 Н, прикладываемой в течение примерно 10 мин при скорости вращения 803 об./мин к контрдиску, сделанному из стали EN31. Размер контрдиска составляет 160 мм в диаметре при толщине около 8 мм, твердость материала контрдиска 60 HRC. В качестве штифта служил цилиндрический сплющенный спеченный образец диаметром 10 мм и высотой 35 мм. Перед каждым испытанием на трение и износ шероховатость поверхности (Rа) спеченного образца и контрдиска на приборе для испытания на износ поддерживалась на уровне средних значений (CLA) 0.9 и 0.8 мкм соответственно. Перед каждым испытанием образцы и диск очищали ацетоном. Штифт на дисковом трибометре использовался для исследования износа. Скорость скольжения поддерживалась на уровне 1.26 м/с, а нагрузка поддерживалась на уровне 20 Н для образцов АП и ПМ. Объемную скорость износа оценивали путем измерения потери веса во время процесса скольжения.
ОБСУЖДЕНИЕ РЕЗУЛЬТАТОВ
Далее представлены результаты, характеризующие образцы. На рис. 2а показана микроструктура АП образца. LSS поддерживали на уровне 50 мм/с. Более низкая скорость лазера обеспечивает хорошее сплавление частиц порошка. Более низкая скорость и более высокая удельная теплоемкость привели к превращению материала стальных порошков в частично отпущенный мартенсит в не превращенной ферритной матрице. В матрице также присутствуют мелкие дисперсные карбиды. Чем ниже скорость лазера, тем выше тепло конверсии мартенсита, и выше твердость всех образцов, что подтверждается испытаниями на микротвердость.
Рис. 2.
Оптические снимки микроструктуры образцов, напечатанных со скоростью LSS: (a) 50; (б) 75; (в) 100; (г) 125 мм/с.
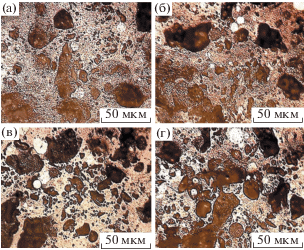
Рисунки 2 (б–г) иллюстрируют микроструктуру образцов, для которых скорость лазера поддерживалась на уровне 75, 100, 125 мм/с соответственно. Более высокая скорость LSS сопровождается выделением меньшего количества тепла, и приводит к трансформированию материала стальных порошков в частично менее отпущенный мартенсит в ферритовой матрице. В матрице также присутствуют мелкие дисперсные карбиды. Соответствующая твердость также имеет меньшее значение. Незначительное уменьшение размера зерна наблюдается между разными скоростями лазерного нагрева.
Рисунок 3а показывает тонкий перлит в зернах феррита с некоторым количеством преобразованного мартенсита. Микроструктура ПМ образцов более однородная, и больших полостей не наблюдается. Рисунок 3б показывает наличие в микроструктуре мелких карбидов и наименее отпущенного мартенсита. Несмотря на проплавление материала в образцах наблюдается пористость.
Рис. 3.
Оптические снимки микроструктуры ПМ образцов, спеченных в течение (a) 1; (б) 2; (в) 3; (г) 4 ч.
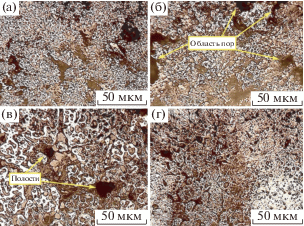
На рис. 3в видно хорошее проплавление порошка основного металла за счет уплотнения и спекания, но наблюдается более низкая степень превращения мартенсита. Зерна крупнее. Кроме того, видно, что между зернами меньше пустот, и это указывает на эффект уплотнения.
Из рис. 3г видно, что прессование и спекание приводят к хорошему сплавлению порошка, но наблюдается больший распад мартенсита. Микроструктура более однородная, больших полостей не наблюдается.
Образцы после 3 и 4 ч спекания (рис. 3в, 3г) имеют более грубую микроструктуру и большее количество зерен перлита в ферритной матрице, что приводит к незначительному увеличению твердости.
Микроструктура, полученная методом СЭМ, образцов АП показана на рис. 4. Микроструктура образца, полученного при LSS 50 мм/с, приведена на рис. 4а. При увеличении 750 крат, можно увидеть микроструктуру, представляющую собой отпущенный мартенсит, с наличием вторичных карбидов, которые образовались во время охлаждения [13, 20]. Зерна однородны, после проплавления происходит мартенситное превращение. В этом поле не наблюдается пор между зернами, и мартенсит представляет собой матрицу со вторичными фазами. Наблюдается полное и эффективное проплавление матрицы, что приводит к более высокой однородности, что дает более высокую твердость.
Рис. 4.
СЭМ-снимки микроструктуры АП образцов, полученных при различной скорости LSS: (a) 50; (б) 75; (в) 100; (г) 125 мм/с.
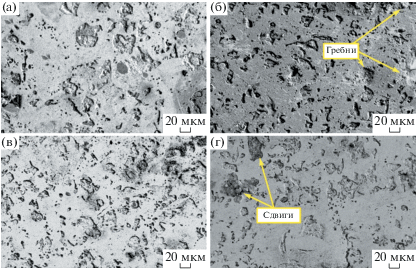
Рисунок 4б показывает микроструктуру образца, изготовленного с более высоким LSS – 75 мм/с. В этом образце поверхность более неровная, присутствуют несколько крупных гребней и впадин. Микроструктура показывает крупно- и мелкозернистую матрицу. В матрице отсутствуют поры между крупинками порошка. Увеличение 750 крат позволяет различить карбидную вторичную фазу. В микроструктуре видны вырванные частицы, которые привели к образованию впадин. Высокая скорость лазера привела к меньшему времени спекания и трансформации частиц.
В микроструктуре образца, изготовленного при LSS 100 мм/с (рис. 4в), вторичные фазы равномерно распределены в матрице первичного отпущенного мартенсита, сформированной в процессе лазерного отверждения/плавления [20]. Вторичные фазы в определенных местах образуют комки. На фоне матрицы выделяются не спеченные частицы. Скорость LSS 125 мм/с (рис. 4г) привела к тому, что вторичные фазы стали равномерно распределенными в матрице первичного отпущенного мартенсита, которая образовалась в процессе лазерного АП. Однако в этом образце наблюдаются более глубокие полости по границам карбидных фаз/зерен. На фоне матрицы также выделяются не спеченные частицы.
Для ПМ образцов, спеченных в течение 1 ч (рис. 5а), микроструктура имеет мелкозернистую морфологию отпущенного мартенсита с мелкими порами между зернами. Спекание в печи дало однородную микроструктуру. Видны границы зерен, и поры, однородно распределенные в матрице. Это может быть связано с недостаточным давлением уплотнения.
Микроструктура образцов, спеченных в течение 2 ч (рис. 5б), показывает распределение частиц карбида в мелкозернистой мартенситной матрице. Наблюдаемое здесь большее количество пор между зернами, вероятно, также связано с недостаточным давлением уплотнения. Это поле показывает большую площадь шероховатой поверхности, обусловленной более низким давлением прессования, и последующее спекание не смогло связать частицы. Распределение первичной и вторичной фаз однородно. СЭМ при увеличении 750 крат также показывает тонкую однородную микроструктуру отпущенного мартенсита с распределением частиц карбида.
На рис. 5в показана микроструктура образца, спеченного в течение 3 ч. Видно, что имеется мелкодисперсная однородная мартенситная матрица с распределением карбидных частиц. В матрице после спекания присутствует меньшее количество пор, и их размер меньше.
В микроструктуре образцов, спеченных в течение 4 ч (рис. 5г), видны мелкие однородные зерна первичной и вторичной фаз: отпущенный мартенсит и выделившиеся карбиды соответственно. Здесь видно лучшее сплавление с меньшим количеством пор между зернами, чем на трех предыдущих снимках.
Микротвердость каждого образца измеряли в 8 различных местах на разном расстоянии от центра. Явные изменения микротвердости от одного места к другому в каждом из образцов можно объяснить наличием нерегулярной пористости, которая влияет на твердость. Микротвердость для каждого образца была усреднена по 8 измерениям. Изменение микротвердости в зависимости от скорости LSS показано на рис. 6а. Видно, что уменьшение LSS приводит к увеличению микротвердости напечатанных деталей.
Микротвердость 370 HV отмечена на образцах, при скорости лазера 50 мм/с. Снижение скорости лазера приводит к увеличению плотности АП деталей, и к удельному увеличению микротвердости. При низкой скорости лазера наличие твердых нитридов и оксидов железа, действующих как барьеры для движения дислокаций, способствовало увеличению твердости образцов [13, 21, 22]. Увеличение LSS в свою очередь привело к снижению микротвердости и плотности.
Рисунок 6б показывает изменение локальной микротвердости ПМ образцов, измеренной на разных расстояниях от центра образца, при различном времени спекания. Как и в случае АП образцов, микротвердость значительно варьируется от одного места к другому. При этом увеличение времени спекания приводит к увеличению микротвердости. Максимальная микротвердость 331.2 HV наблюдается для ПМ деталей, спеченных в течение 3 ч. Повышение микротвердости этих деталей при увеличении времени спекания можно отнести к более высокой плотности готового продукта.
Рисунки 6а–6б показывают более высокую микротвердость АП образцов, по сравнению с ПМ образцами. Это происходит из-за более высокой температуры спекания до 1200°C, а также из-за диаметра луча (0.40 мм), используемого в АП. Образцы поглощают большое количество тепловой энергии по сравнению с обычным процессом спекания (950°C). Таким образом, более высокая твердость получается у АП образцов, по сравнению с ПМ образцами. Улучшение микротвердости печатных деталей при более низкой скорости LSS может быть результатом их более высокой плотности.
Рисунок 7а показывает изменение плотности АП образцов при изменении скорости LSS. Более низкой скорости LSS соответствует увеличение плотности, а также уменьшение пористости спеченных деталей. Более низкая скорость LSS обеспечивает повышенное поглощение энергии порошком во время печати, что приводит к эффективному проплавлению и уплотнению материала. Это объяснение согласуется с [23]. Повышенная скорость LSS в свою очередь наоборот снижает эффективное поглощение энергии порошком, снижает плотность образцов и повышает пористость, что приводит к более низкой микротвердости.
На рис. 7б показана зависимость плотности ПМ образцов от времени спекания. Наблюдалось увеличение плотности и уменьшение их пористости при каждом увеличении времени спекания до 3 ч. Микротвердость также улучается при увеличении времени спекания благодаря повышению плотностью.
Плотности образцов АП и ПМ отличаются. Наблюдается увеличение плотности и уменьшение пористости АП образцов при низкой скорости лазера. В то время как при ПМ чем дольше происходит спекание, тем выше энергия, поглощаемая порошком, что приводит к улучшенному проплавлению и большей плотности детали. Эти результаты соответствуют [22].
На рис. 8 показано изменение скорости износа AП деталей в зависимости от времени и от параметров процесса, учитываемых в испытаниях на износ, таких как нагрузка 20 Н, скорость скольжения 1.2 м/с, путь трения 756 м и продолжительность 10 мин.
Рисунок 8 показывает результаты испытаний на износ 4-х AП образцов. Средняя скорость износа рассчитывается с использованием средних значений скорости износа, полученных в разное время в процессе испытания для каждого образца. Износостойкость ухудшается с уменьшением LSS. Это связано с тем, что уменьшение LSS привело к повышению твердости и прочности изготавливаемых деталей. Снижение потерь от износа спеченных деталей также может быть связано с включениями, такими как твердые оксиды и нитриды, в конечных продуктах [13].
Рисунок 9 иллюстрирует зависимость скорости износа ПМ-образцов от времени спекания. Снижение скорости износа с увеличением времени спекания может быть связано с ростом твердости. Увеличение плотности и твердости приводит к повышению износостойкости ПМ-образцов.
Рисунок 10 показывает пониженную скорость износа АП-образцов, по сравнению с ПМ-образцами. Снижение скорости LSS привело к повышению твердости и сделало АП-образцы более прочными.
На рис. 11, 12 представлены изображения образцов АП и ПМ после испытания на износ. На них четко видны области, где начинается окисление (ржавчина) из-за повышения температуры.
Рисунок 13а показывает зависимость коэффициента трения от скорости LSS для АП образцов. Увеличение LSS привело к снижению коэффициента трения. Причина этого связана с большой пористостью образцов. Снижение плотности приводит к уменьшению шероховатости, тем самым уменьшая трение, возникающее из-за скольжения сопрягаемых деталей. Кроме того, снижение скорости лазера приведет к увеличению содержания оксидов и нитридов, как упоминалось выше.
Рисунок 13б показывает зависимость коэффициента трения от времени спекания ПМ образцов. Увеличение времени спекания может привести к снижению коэффициента трения. Рисунки 13a–13б показывают низкий коэффициент трения АП образцов, по сравнению с ПМ образцами. Уменьшение LSS привело к повышению твердости и прочности АП образцов, и соответственно к увеличению коэффициента трения.
ЗАКЛЮЧЕНИЕ
1. Напечатаны (АП) образцы из стального порошка H20 с применением разной скорости лазерного сканирования от 50 до 125 мм/с. Образцы ПМ изготовлены с изменением времени спекания от 1 до 4 ч.
2. АП образцы, построенные при пониженной скорости LSS, имеют повышенную плотность, микротвердость и коэффициент трения, по сравнению с образцами, напечатанными с более высокими скоростями сканирования.
3. Микроструктурный анализ показал эффективное проплавление материала при понижении LSS за счет более высокого энерговложения, что приводит к более высокой плотности. Повышение прочности можно было ожидать из-за повышенной плотности АП образцов в соответствии с [24].
4. Для метода ПМ, оптимальное давление составило 240 МПа, температура 950°C, время спекания – 3 ч. Это обеспечило повышенную плотность и микротвердость образцов. Увеличение скорости износа пропорционально увеличению времени спекания. Увеличение коэффициента трения наблюдается для деталей, спеченных в течение 1 ч.
5. Таким образом, образцы АП демонстрируют более высокие механические свойства, по сравнению с ПМ образцами.
Список литературы
ASTM International, “F2792-12a – Standard Terminology for Additive Manufacturing Technologies,” 2013.
Popov V.V. Jr., Muller-Kamskii G., Kovalevsky A., Dzhenzhera G., Strokin E., Kolomiets A., Ramon J. Design and 3D-printing of titanium bone implants: brief review of approach and clinical cases// Biomed. Eng. Lett. 2018. V. 8, № 4. P. 337–344.
Muthuchamy A., Raja Annamalai A., Karthikeyan M., Abhijeet Thakur, Nidhi Nagaraju, Dinesh K. Agrawal. Microstructural Evolution of Iron Based Alloys Produced by Spark Plasma Sintering Method // Phys. Met. Metallogr. 2018. V. 119. № 7. P. 678–684.
Katz-Demyanetz A., Popov V.V. Jr., Kovalevsky A., Safranchik D., Koptyug A. Powder-bed additive manufacturing for aerospace application: Techniques, metallic and metal/ceramic composite materials and trends // Manuf. Rev. 2019. V. 6. P. 5.
Koptyug A., Bäckström M., Rännar L.-E. 3D-printing: A future ‘magic wand’ for global manufacturing how can we benefit from it today for sports and health care?/ in icSPORTS 2017 – Proc. of the 5th Int. Congress, 2017. P. 5–16.
Guo N., Leu M.C. Additive manufacturing: Technology, applications and research needs // Front. Mech. Eng. 2013. V. 8. № 3. P. 215–243.
Kolomiets A., Grobman Y.J., Popov V.V. Jr, Strokin E., Senchikhin G., Tarazi E. The Titanium 3D Printed Flute: new prospects of Additive Manufacturing for Musical Wind Instruments Design // J. New Music Res. 2020. https://doi.org/10.1080/09298215.2020.1824240
Sarkar P., Chakrabarti A. Assessing design creativity// Des. Stud. 2011. V. 32. № 4. P. 348–383.
Koptyug A., Popov V.V. Jr., Vega C.A.B., Jiménez-Piqué E., Katz-Demyanetz A., Rännar L.-E., Bäckström M. Compositionally-tailored steel-based materials manufactured by electron beam melting using blended pre-alloyed powders // Mater. Sci. Eng. A. 2020. V. 771. P. 138587.
Radulov I., Popov V.V. Jr, Koptyug A., Maccari F., Kovalevsky A., Essel S., Gassmann J., Skokov K.P., Bamberger M. Production of net-shape Mn–Al permanent magnets by electron beam melting// Addit. Manuf. 2019. V. 30. P. 100787.
Popov V.V. Jr., Fleisher A. Hybrid additive manufacturing of steels and alloys // Manuf. Rev. 2020. V. 7. The emerging materials and processing technologies. P. 6.
Bhattacharya A., Bagdi A., Das D. Influence of microstructure on high-stress abrasive wear behaviour of a microalloyed steel // Perspect. Sci. 2016. V. 8. P. 614–617.
Ramesh C.S., Srinivas C.K., Srinivas K. Friction and wear behaviour of rapid prototype parts by direct metal laser sintering // Tribology – Materials, Surfaces & Interfaces. 2007. V. 1. № 2. P. 73–79.
Keshavamurthy R., Padmanav Rashmirathi, Vinod A.R., Srinivasa C.K., Shashikumar P.V. Optimization of Process Parameters for Direct Metal Deposition of H13 tool Steel // Adv. Mater. Manuf. Charact. 2013. V. 3. № 2. P. 515–519.
Kazantseva N.V., Merkushev A.G., Shishkin D.A., Ezhov I.V., Davidov D.I., Rigmant M.B., Terent’ev P.B., Egorova L.Yu. Magnetic Properties and Structure of Products from 1.4540 Stainless Steel Manufactured by 3D Printing // Phys. Met. Metallogr. 2019. V. 120. № 13. P. 1270–1275.
Krakhmalev P., Fredriksson G., Thuvander M., Åsberg M., Vilardell A.M., Oikonomou C., Maistro G., Medvedeva A., Kazantseva N. Influence of heat treatment under hot isostatic pressing (HIP) on microstructure of intermetallic-reinforced tool steel manufactured by laser powder bed fusion// Mater. Sci. Eng. A. 2020. V. 772. P. 138699.
Khorsand H., Habibi S.M., Yoozbashizadea H, Janghorban K., Reihani S.M.S., Rahmani Seraji H., Ashtari M. The role of heat treatment on wear behavior of powder metallurgy low alloy steels // Mater. Des. 2002. V. 23. № 7. P. 667–670.
Ceschini L., Palombarini G., Sambogna G., Firrao D., Scavino G., Ubertalli G. Friction and wear behaviour of sintered steels submitted to sliding and abrasion tests // Tribol. Int. 2006. V. 39. № 8. P. 748–755.
Prabu S.S., Prathiba S., Asokan M.A., Anshul Jain, Neeraj Kumar Jain, Pratyush Kumar Chourasiya. Investigations on dry sliding wear behaviour of Sintered/Extruded P/M Alloy Steels (Fe–C–W–Ti)// Procedia Engineering. 2014. V. 97. P. 2119–2126.
Li X., Tan Y.H., Willy H.J., Wang P., Lu W., Cagirici M., Ong C.Y.A., Herng T.S., Wei J., Ding J. Heterogeneously tempered martensitic high strength steel by selective laser melting and its micro-lattice: Processing, microstructure, superior performance and mechanisms // Mater. Des. 2019. V. 178. P. 107881.
Khaleghi M. Sintering and heat-treatment of P/M low alloy steels prepared from a particially prealloyed powder. Loughborough University of Technology, 1982.
Sintering of steels. Linde AG. Gases Division, Germany, 2020.
Adeyemi A., Akinlabi E.T., Mahamood R.M. Powder bed based laser additive manufacturing process of stainless steel: A review // Materials Today: Proceedings. 2018. V. 5. № 9. P. 18510–18517.
Milovanovic J., Stojkovic M., Trajanovic M. Metal Laser Sintering for Rapid Tooling in Application to Tyre Tread Pattern Mould/in Sinter. – Methods Prod. 2012. P. 73–90.
Дополнительные материалы отсутствуют.
Инструменты
Физика металлов и металловедение