Физика металлов и металловедение, 2021, T. 122, № 5, стр. 541-552
Влияние многократного гофрирования–распрямления на микроструктуру и механические свойства алюминиево-марганцевого сплава AА3003
К. Рейес-Руис a, *, К. Г. Фигероа b, Г. Гонзалес c, А. Ортис a
a Кафедра проектирования и производства, Инженерно-технологический факультет,
Национальный автономный университет Мексики (UNAM)
04510 Мехико, Университетский городок, Мексика
b Кафедра проектирования и производства, Инженерно-технологический факультет,
Национальный автономный университет Мексики (UNAM), Научно-исследовательский
и технологический инновационный парк (PIIT)
66629 Аподака, Мексика
c Научно-исследовательский институт материалов, Национальный автономный университет Мексики
04510 Мехико, Университетский городок, Мексика
* E-mail: c.reyesruiz@unam.com
Поступила в редакцию 27.10.2020
После доработки 11.01.2021
Принята к публикации 19.01.2021
Аннотация
Новая разработка профиля матрицы для процедуры многократного гофрирования–распрямления (МГР) прошла аттестационную оценку на предмет механических характеристик и микроструктурных модификаций обрабатываемого материала. Лист отожженного алюминиево-марганцевого сплава АA3003 был подвергнут шестипроходной МГР обработке при комнатной температуре, продемонстрировав значительное увеличение предела текучести и твердости. Изменения значений профилометрических характеристик поверхности листа сплава были изучены на различных этапах МГР процесса, это показало явную корреляцию между областью большей деформации и максимумом твердости. Более того, различия в неровности поверхности листа зависели от реальной площади поверхности контакта между материалом обработки и обеспечивающими его гофрировку участками матрицы. Локальное распределение деформации, возникающее в результате МГР воздействия, было определено с помощью анализа средней локальной разориентации (КАМ), что находилось в соответствии с результатами картирования микротвердости. Картирование распределения ориентации показало, что в зернах с нормалью, параллельной 〈111〉, более активны процессы выстраивания дислокаций и фрагментации зерен в сравнении со случаями других основных ориентаций. Несмотря на улучшение механических свойств, сохраняются исходные текстурные компоненты.
ВВЕДЕНИЕ
Методики интенсивной пластической деформации (ИПД) находят последнее время все более широкое применение, благодаря способности ИПД повышать предел текучести, твердость и сопротивление усталости посредством измельчения зерна, вплоть до ультрамикроскопических размеров. Подобные явления происходят без изменения геометрии образца, исключительно за счет введения большого числа дислокаций в каждом акте повторяющегося деформационного процесса [1–3]. Ряд отраслей производства заинтересованы в вышеперечисленных свойствах, в частности, это автомобильная и аэрокосмическая отрасли, где требуются особенно высокие значения предела текучести материалов малого удельного веса, например, алюминиевых сплавов. Среди чаще всего применяемых ИПД-методик упоминаются в первую очередь равноканальное угловое прессование (РКУП) [4–6], кручение под высоким давлением (КВД) [7], всесторонняя ковка [8], экструзия через фильеру [9], аккумулирующая прокатка [10], процедура многократного гофрирования–распрямления (МГР) [11, 12]. Последняя из упомянутых методик, это – одна из наиболее простых в применении и хорошо приспособленная для повышения прочности листового металла. В результате использования ИПД методики можно достичь значений деформации ~10 при значительном уменьшении размера зерна [13–15]. Тем самым чрезвычайно важно отслеживать изменение размеров зерен и их разориентировку на стадиях деформации на высокие степени, когда может реализоваться динамический возврат, причем даже при низких температурах [16–18]. Что касается других ИПД методик, МГР-процесс оказался способным приводить к формированию объемных наноструктурированных материалов [12]. Предложено несколько типов МГР-матриц [19‒24], их цель состоит в создании в образце наиболее однородной деформации в сочетании с ультрамелкозернистой (УМЗ) структурой.
Недавно было опубликовано, что материалы, сочетающие в себе крупные и мелкие зерна микронного размера, могут обладать неожиданными механическими свойствами [25]. Такие неоднородные материалы могут быть получены при применении новой МГР-матрицы, позволяющей получать неоднородное распределение деформации в материале. Гипотетически, последнее может привести к улучшению механических свойств не только в материалах с УМЗ-структурой, но и с “выгодной” текстурой, допускающей широкие приложения. В последние годы МГР-обработка была применена к алюминиевым сплавам предпочтительно Al–Mg и Al–Li-систем. Сплаву AA3003 не было уделено должное внимание, несмотря на его хорошую коррозионную стойкость, хорошую формуемость и свариваемость. Более того, явления, наблюдаемые при фрикционном износе на поверхности материала, а также изменения в его геометрической форме, слабо изучены и недостаточно полно отражены в литературе.
Цель настоящей статьи состоит в том, чтобы оценить и соотнести механические свойства и микроструктурные изменения, возникающие при МГР-обработке, при использовании матрицы с геометрией нового типа, обеспечивающей неоднородное распределение деформации в образце сплава AA3003. Сплав был подвергнут деформации при комнатной температуре с использованием шестипроходной МГР-обработки. Механические свойства были изучены в испытаниях на растяжение при анализе картирования микротвердости. Модифицирование поверхности образцов оценивали методами оптической профилометрии. Кристаллографическая текстура и микроструктурные изменения были исследованы с помощью анализа уширения рентгеновских дифракционных пиков, а также полюсных фигур и ориентационных карт, полученных при дифракции обратно-рассеянных электронов (ДОРЭ/EBSD).
МЕТОДИКА ЭКСПЕРИМЕНТА
Алюминиевый лист из сплава АА3003 толщиной 1.2 мм был приобретен у коммерческого дистрибьютора. Перед МГР-обработкой, образцы прошли смягчающий отжиг при 450°C в течение 3 ч. Химический состав был установлен с помощью флуоресцентного спектрометра и представлен в табл. 1.
Таблица 1.
Химический состав алюминиевого сплава А3003
Si | Fe | Cu | Mn | Zn | Проч. | Al |
---|---|---|---|---|---|---|
0.6 | 0.58 | 0.1 | 0.85 | 0.05 | 0.1 | Ост. |
МГР-процедура осуществлялась с использованием матриц, вид которых представлен на рис.1a; образец представлял собой лист материала размерами 112 × 112 мм. Геометрия матрицы соответствовала виду синусоидальной функции, имевшей амплитуду 4 мм и период 16 мм. Первый этап – гофрирование образца – протекал со скоростью 5 мм/мин. Затем следовало первое выпрямление. Отметки, показанные на рис. 1б, представляют низшее положение нижней части матрицы. После разворота образца на 90°, было произведено второе гофрирование–распрямление, оставившее новые отметки, положение которых показано на рис. 1в. Процедура двойного “гофрирования–распрямления”, проиллюстрированная на рис. 1б–1г, рассматривается как единичный МГР проход, который, согласно Rosochowski [26], производит эквивалентную пластическую деформацию ~1.1. Принимая в расчет симметрию матрицы, можно считать, что заштрихованная на рис. 1д область образца указывает репрезентативный участок анализа распределения твердости и картирования ориентации зерен. При проведении всей технологической процедуры вещество MoS2 использовалось в качестве смазки между образцом и штампами для гофрирования и распрямления. Исходный (эталонный) образец был маркирован символом 0P; образцы, испытавшие один и шесть проходов МГР, были маркированы символами 1P и 6P, соответственно.
Рис. 1.
Геометрия МГР-матрицы – а; схема МГР процесса – б, в, г; зоны материала для аттестации микроструктуры и механических свойств – д.
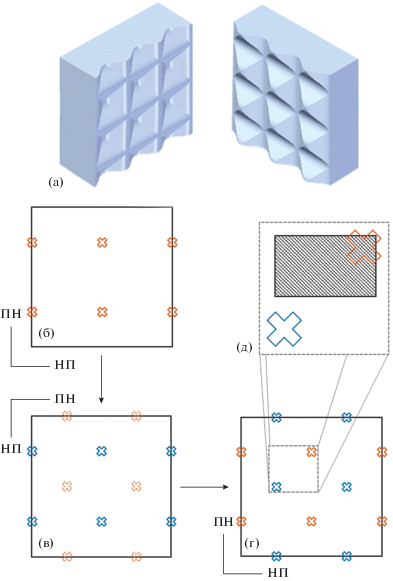
Образцы для растяжения отбирали из серии 0P и из деформированных образцов, причем, все вырезались параллельно направлению прокатки. Скорость деформирования при растяжении на универсальной испытательной установке Instron была равна 10–3 с–1.
Замер профилей поверхности образцов и измерение твердости осуществляли на оборудовании фирмы NANOVEA, сочетающем в себе хроматический софокусный оптический профилометр и твердомер с пирамидальным индентором Виккерса. Картирование микротвердости осуществлялось при использовании нагрузки 1 Н, с продолжительностью выдержки 10 с на максимуме нагрузки. Созданию на испытуемых поверхностях сетки с шагом 500 мкм предшествовала их механическая полировка. С учетом симметричности деформации, выбор участков для характеристики поверхности осуществлялся, как это показано на рис. 1д. Для аттестации изменения поверхности, вызванного процессом ИПД, с помощью оптического профилометра были произведены замеры неровностей (по высоте). Обработка данных состояла в разделении формы и шероховатости путем подбора многочлена пятой степени. Среднеквадратичная шероховатость поверхности (Rq) была рассчитана по 1-мм линиям, размещенным случайным образом на обработанных поверхностях образцов, на которых выделялось три различные зоны, каждая из которых соответствовала своей зоне контакта с поверхностью матрицы. Упомянутыми зонами являлись: зона базовой линии, самые “глубокие”, а также самые “высокие” зоны обработанной поверхности.
Дифрактометр Rigaku Ultima IV, оснащенный рентгеновской трубкой с Cu Kα-излучением и модулем формирования параллельного пучка, был использован для снятия рентгенограмм и установления кристаллографической текстуры образцов. Данные для построения полюсных фигур были получены в режиме “в плоскости”, с размерами области сканирования по α и β: 0°–90° и 0°–360° соответственно. Анализ текстуры проводился на основе расчета функции распределения ориентаций (ФРО) с помощью софта MATLAB toolbox и MTEX [27].
В предположении выполнения условия Брэгга–Брентано были построены рентгеновские дифрактограммы со значениями 2θ углов в пределах 20°–140°, с шагом 0.01° и скоростью съeмки 0.2°/мин. Уширение максимумов рентгеновских пиков было оценено по усовершенствованной методике Ле Бэйла с использованием программного обеспечения FULLPROF [28]. Параметры эталонного порошка LaB6 были взяты при расчете инструментального уширения рентгеновских пиков, а также для деконволюции интегрального уширения из гауссовского и лоренцевского вкладов.
Предположив, что дифракционный профиль от образца носит в основном лоренцевский характер, мы смогли установить значения размера кристаллических доменов и величины относительной деформации материала с помощью графического построения уравнения Вильямсона–Холла, позволившего выделить вклады от размера (D) кристаллических доменов и от деформации (ε) в интегральное уширение (β) на основании соотношения β cos θ = kλ/D + 2ε sin θ, что в свою очередь обеспечило получение очень ценной качественной информации о вариации значений деформации как функции числа МГР проходов.
Сканирование в режиме ДОРЭ было выполнено на полевом растровом электронном микроскопе марки JEOL JEM7600FEG. Образцы были приготовлены с помощью стандартной методики механической полировки. Построение ориентационных карт было осуществлено выборочно – для зон, указанных на рис. 1д. Компьютерный анализ с привлечением программного обеспечения MTEX был использован при обработке данных по распределению ориентации зерен.
РЕЗУЛЬТАТЫ И ОБСУЖДЕНИЕ
МГР-обработка была успешно применена к отожженному листу из алюминиевого сплава АА3003, причем без видимого повреждения материала. Кривые “напряжение–деформация”, представленные на рис. 2, показывают значительный рост предела текучести сплава при переходе от 0P к 1P образцу. Предел текучести исходных образцов (0P) составлял ~57 МПа, тогда как после полного цикла МГР (1Р) было достигнуто значение предела текучести ~87 МПа. После шести циклов МГР (6Р) наблюдалось незначительное (~92 MПa) увеличение предела текучести. Как следствие увеличения предела текучести, было зарегистрировано снижение пластичности материала, что вполне согласуется с результатами, полученными при ИПД, проведенной при комнатной температуре [29]. Несмотря на такое упрочнение, сегодня уделяют внимание и другим механическим и микроструктурным свойствам и возможностям, которые требуют тщательного изучения в области ИПД-материалов [30].
Данные по микротвердости в репрезентативной зоне поверхности 0P образцов показывают однородные по величине значения ~31 ± 0.5 HV. Распределение микротвердости по поверхности деформированных 1P и 6P образцов, отвечающее зоне поверхности, заштрихованной на рис. 1д, представлено на рис. 3. Для обоих образцов, наибольшие значения твердости соответствуют наиболее деформированным зонам поверхности; последние соответствуют выступам в нижней пластине матрицы, обеспечивающей эффект гофрирования. В 1P-образце наибольшее увеличение твердости составило 50% от исходного значения. В случае 6P образца было зарегистрировано дополнительное увеличение твердости на 10%. Кроме того, наблюдалось расширение зоны упрочнения по мере увеличения числа МГР-проходов. Эти результаты могли бы быть полезны в зависимости от сферы окончательного использования материала, поскольку градиент в распределении твердости является весьма желательным для некоторых материалов, например, используемых при производстве скользящих контактов [31].
Некоторые 3D-профили высоты для 1P и 6P образцов представлены на рис. 4a и 4г, соответственно. Видно, что по мере увеличения числа МГР-проходов морфология обработанной поверхности становится более четко “прорисованной” вследствие того, что самые глубокие и самые высокие зоны оказываются ближе к базовой линии. Это обстоятельство позволяет идентифицировать каждую зону поверхности, как указано на рис. 4б и 4д, на которых представлены данные о форме поверхности после одного и шести проходов. Выявляется две зоны, которые не соответствуют базовой линии, отмеченные символами А и В. В случае зоны А, материал находится ниже базовой линии. Это является следствием образования дислокационных скоплений в областях, прилегающих к области материала с наибольшим значением твердости. Такое заключение сделано на основе результатов картирования шероховатости поверхности (см. рис. 4в и 4е), где нетрудно заметить более высокие значения шероховатости, отвечающие большей площади контакта. В зоне В более низкие уровни высоты означают, что геометрия матрицы изменила форму материала, но не обеспечила достаточной пластической деформации для увеличения его твердости. Более того, шероховатость говорит в пользу меньшей реальной площади контакта. Так что, на шаге распрямления не удалось достичь базовой линии.
Рис. 4.
3D-профиль высоты (а); контуры формы (б) и шероховатость для образца 1P (в); 3D-профиль высоты (г); контуры формы (д) и шероховатость для образца 6P (е).
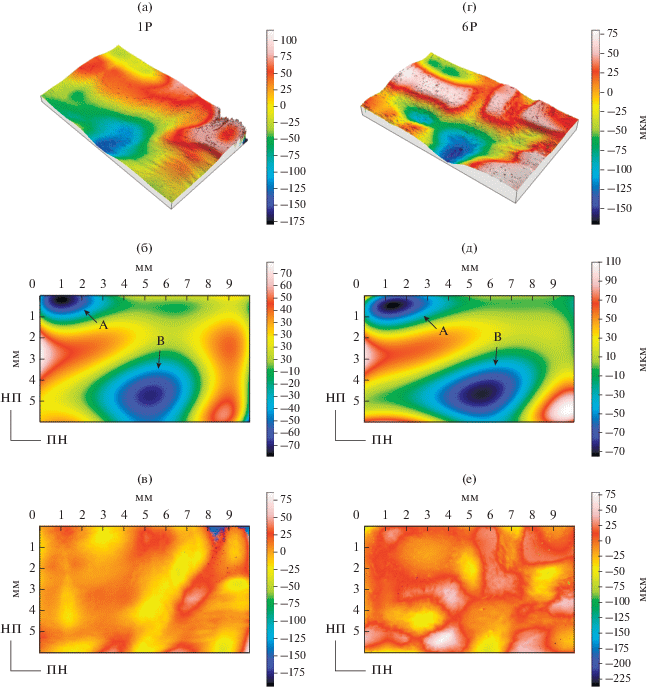
В табл. 2 собраны значения среднеквадратичной шероховатости (Rq) для зон, отвечающих базовой линии, и самых “глубоких” и самых “высоких” зон. Значения Rq для последних двух зон указывают на неуклонный рост шероховатости, что выражается в больших значениях для 6P образцов. Значения Rq, отвечающих базовой линии, практически одинаковые. Кроме того, видно, что в самых “высоких” зонах поверхности материала в обоих случаях умеренный “износ” приводит к снижению величин Rq [32]. Детальный обзор рис. 4 и табл. 2 позволяет отметить, что основными поверхностными эффектами от увеличения числа проходов МГР было увеличение “зазоров по высоте”. Вместе с тем в настоящих условиях существенные изменения шероховатости поверхностей произошли только при переходе от образца 0P к образцу 1P, тогда как последующие МГР-проходы не вносят существенных изменений.
Таблица 2.
Среднеквадратичная шероховатость поверхности, Rq, для образцов 0P, 1P и 6P
Число МГР проходов | Rq, мкм | ||
---|---|---|---|
базовая линия | самые глубокие зоны | самые высокие зоны | |
0P | 0.56 ± 0.03 | ||
1P | 0.76 ± 0.12 | 0.87 ± 0.2 | 0.62 ± 0.7 |
6P | 0.77 ± 0.18 | 0.92 ± 0.26 | 0.73 ± 0.13 |
Рентгеновские дифрактограммы, представленные на рис. 5, свидетельствуют о том, что для образцов 0P, 1P и 6P характерно присутствие отражений относительно высокой интенсивности от плоскостей (220); особенно это заметно для 0P образца. Это свидетельствует о предпочтительной кристаллографической ориентации. Хотя для 1P и 6P образцов наблюдается относительное увеличение интенсивности (111) и (200) рефлексов, для них предпочтительной ориентацией остается (220). Такое поведение говорит о том, что изменение остроты текстуры на протяжении всего процесса МГР может быть обнаружено после различного числа проходов. Нормализованное уширение отражения от плоскостей (220) представлено на рис. 6. При сравнении образцов 0P и 1P для последнего было зарегистрировано увеличение ширины пика на его полувысоте (FWHM, полуширина), что свидетельствовало о нарастании степени относительной деформации материала и измельчении его зеренной структуры. При этом, при переходе от состояния 1P к 6P было отмечено незначительное уменьшение уширения рентгеновского пикав, что предполагало перегруппировку дислокаций, обусловливающую частичную релаксацию напряжений.
Руководствуясь критерием Ле Бэйла относительно профиля рентгеновских пиков, нетрудно понять, каким образом эволюционирует уширение этих пиков в процессе МГР. На рис. 7 представлены зависимости Уильямсона–Холла (У–Х) для разного числа МГР-проходов. Для 0P образца, наклон графика пренебрежимо мал. Это говорит о том, что в результате отжига в материале произошла релаксация напряжений, ассоциируемая с самой низкой плотностью дислокаций. Для 1P образца отмечен уже рост наклона графика, что свидетельствует о росте плотности дислокаций и, возможно, о формировании отдельных дислокационных скоплений. Снижение тангенса угла наклона соответствующих графиков отмечено при переходе от 1P к 4P образцу. Для образцов 4P и 6P изменения наклона графиков не зарегистрировано. Описанное поведение было уже отмечено в ряде работ, исследовавших ИПД [33], что привело к формулировке двух гипотез. Согласно первой, релаксация напряжений связана с присутствием микротрещин. Согласно второй гипотезе, на описываемой стадии материал обнаруживает способность к эффективной аннигиляции дислокаций, даже при холодном деформировании [10, 14, 15, 34, 35]. Так как трещин в микроструктуре образцов не наблюдалось, вторая гипотеза кажется более предпочтительной. Более того, значения β (точка пересечения графиков с ось y) указывают на значительное уменьшение размера кристаллических доменов уже после первого МГР-прохода. Для 4P состояния указанное значение остается неизменным и вновь снижается для 6P образца.
На рис. 8 показана эволюция текстуры 0P, 1P и 6P образцов. Основные текстурные компоненты и их относительная объемная доля были рассчитаны с использованием программного обеспечения MTEX. После отжига были установлены две главные текстурные компоненты (P1 и P2), соответствующие P-ориентации {100}❬554❭ отожженного образца [36–38]. Изменений текстурных компонент в 1P образце установлено не было, но острота текстуры уменьшилась. Это, возможно, было обусловлено возникновением субструктуры на ранних стадия процесса ИПД, что согласуется с результатами замеров уширения рентгеновских пиков. В случае 6P образца было отмечено усиление рассеяния текстуры на несколько градусов вокруг исходных компонентов (P1 и P2). Это было вызвано возникновением особого напряженного состояния при МГР, которое, предположительно, активизирует различные системы скольжения, вызывая разориентацию на границах субзерен, и способствует образованию малоугловых (МУГ) и большеугловых границ зерен (БУГ) [12]. В отличие от других методов ИПД [33, 39–41], указанная МГР-обработка листа из сплава АА3003 не привела к изменению исходных текстурных компонент. Поэтому улучшение механических свойств произошло исключительно за счет увеличения плотности дислокаций. Такое поведение материала могло бы стать весьма полезным в случае тех его промышленных применений, когда требуется сохранение исходной ориентации зерен.
Ориентационные карты зеренной структуры, полученные с помощью ДОРЭ (рис. 9), показали, что большинство структурных изменений, произошедших в результате пластической деформации, свелось к формированию субструктуры благодаря величине среднего размера зерна. В более ранних работах было показано, что на оцениваемой стадии процесса условие реализации ультрамелкого зерна не было достигнуто [42]. Вместе с тем, проводя сравнение гистограмм распределения границ по углам разориентировки для образцов 0P, 1P и 6P, было установлено, что доля МУГ (5°–15°) росла с увеличением числа МГР проходов и составила 7, 12 и 30% соответственно. Даже когда измельчение зерна ещё не наблюдалось, доля МУГ увеличивалась, а графики У–Х свидетельствовали о возникновении субструктуры в процессе МГР-обработки, так как согласно им, плотность дислокаций возрастала после первого МГР-прохода, уменьшалась по завершении четвертого прохода и сохранялась неизменной в 4P- и 6P-состояниях материала. Пластическая деформация, генерируемая в последних циклах МГР-обработки, сопровождалась увеличением плотности дислокаций, однако пространственное перераспределение дислокаций приводило к уменьшению размера кристаллитов, как, впрочем, и к снижению величины внутренней деформации.
Рис. 9.
Ориентационные карты и соответствующие им гистограммы распределения границ по углам разориентировки для образцов 0P, 1P и 6P.
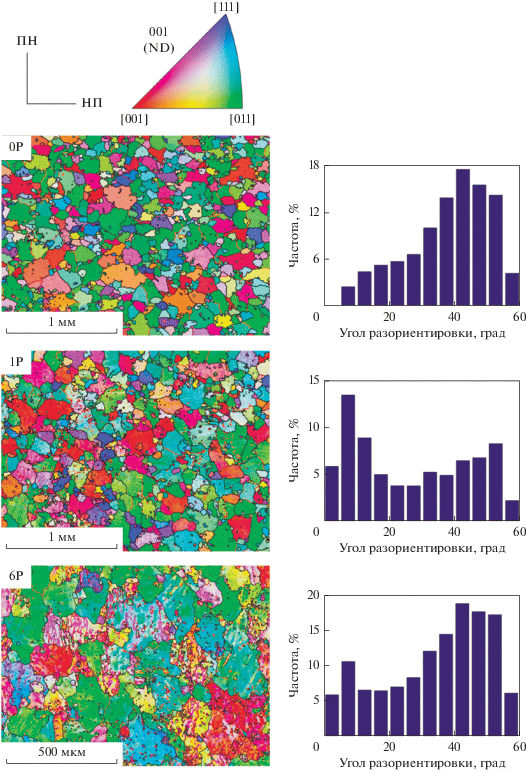
Локальное распределение МУГ было подтверждено в расчетах средней локальной разориентации (KAM – средний угол разориентации данной точки со всеми соседними на заданном расстоянии) с учетом соседей второго порядка. КАМ-карта, представленная на рис. 10, позволяет сопоставить локальные разориентировки с результатами картирования микротвердости, доказывая тем самым, что более высоким значениям микротвердости соответствует увеличение угла локальной разориентировки. Таким образом, обе методики (КАМ и картирование твердости) позволяют установить распределение деформации, созданное в рассмотренном МГР-процессе.
Рис. 10.
КАМ-карта для образца 1P и положение места замера локальной разориентации на карте распределения твердости того же образца (верхнее изображение).
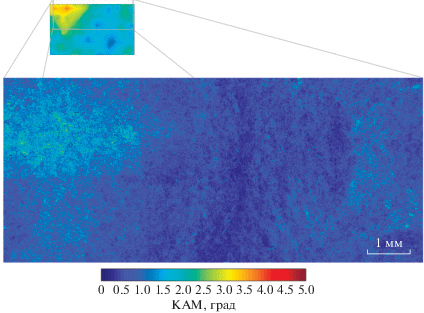
Репрезентативные зерна, нормаль которых параллельна направлениям 〈001〉, 〈011〉 и 〈111〉, были подвергнуты анализу с точки зрения эволюции их локальной разориентации. KAM гистограммы и соответствующие им карты, представленные на рис. 11, показывают, что до начала МГР-процесса (0P) во всех зернах наблюдалась сходная локальная разориентация, независимо от направлений нормалей. После первого МГР-прохода (1P) гистограммы сдвигаются вправо, что говорит об общем увеличении локальных разориентировок, указывая тем самым на начало процесса зеренной фрагментации, особенно сильно проявившейся в 〈111〉 зернах. При дальнейшем увеличении числа МГР-проходов (6P) тенденция к смещению гистограмм в сторону больших углов продолжилась для 〈001〉 и 〈011〉 кристаллитов, в отличие от 〈111〉 зерен, которые продемонстрировали смещение к меньшим значениям KAM-угла. Это свидетельствует о том, что процесс пространственного перераспределения дислокаций в последнем случае был активирован раньше, чем в зернах других ориентаций. Последнее заключение согласуется с результатами, представленными выше, когда уменьшение наклона У–Х-зависимостей было отмечено для 6P образца.
ЗАКЛЮЧЕНИЕ
Применение матрицы с инновационной геометрией, предложенной к внедрению в данной работе, позволило получить механические, поверхностные и микроструктурные модификации материала, которые привели к общему улучшению его свойств, позволив расширить сферу применения листов из алюминиевого сплава АА3003 в промышленности.
Предел текучести увеличился на самых ранних стадиях МГР-обработки. Неоднородное распределение деформации, возникшее в материале, было установлено по результатам картирования микротвердости. Области материала, которые показали более высокую твердостью и большую площадью контакта с матрицей после первого МГР-прохода, расширялись с увеличением числа проходов.
Анализируемый процесс МГР не привёл к изменению исходных текстурных компонент, что может оказаться полезным в случае, когда требуется увеличение прочности материала без изменения ориентации зерен. Также МГР процесс привел к появлению большого количества малоугловых границ, показав тем самым, что дальнейшее увеличение числа проходов должно привести к измельчению зеренной структуры материала.
Было установлено, что в зернах с нормалью, параллельной направлению 〈111〉, перераспределение дислокаций и формирование ячеистой структуры происходило на ранних стадиях МГР-процесса, опережая их развитие в зернах с нормалью, параллельной направлениям 〈001〉 и 〈011〉. Более того, ход У–Х-графиков вполне согласуется с перераспределением дислокаций в зернах 〈111〉, что приводило к снижению в них величин локальной разориентации.
Рейес-Руис признателен Главному Управлению по Делам Академического Персонала [DGAPA] за предоставленную ему возможность обучения в аспирантуре. Г. Гонзалес благодарен за финансирование, предоставленное в рамках академического проекта PAPIIT IN107917 [Научно-исследовательского и технологического инновационного парка]. Авторы хотели бы поблагодарить за техническую поддержку, оказанную E. Hernàndez-Mecinas, Adriana Tejeda и Omar Novelo.
Список литературы
Sabirov I., Murashkin M.Y., Valiev R.Z. Nanostructured aluminium alloys produced by severe plastic deformation: New horizons in development // Mater. Sci. Eng. A. 2013. V. 560. P. 1–24.
Langdon T.G. The processing of ultrafine-grained materials through the application of severe plastic deformation // J. Mater. Sci. 2007. V. 42. P. 3388–3397.
Valiev R.Z., Murashkin M.Y., Ganeev A.V, Enikeev N.A. Superstrength of nanostructured metals and alloys produced by severe plastic deformation// Phys. Met. Metallogr. 2012. V. 113. P. 1193–1201.
Segal V.M. Severe plastic deformation: simple shear versus pure shear/ / Mater. Sci. Eng. A. 2002. V. 338. P. 331–344.
Iwahashi Y., Wang J., Horita Z., Nemoto M., Langdon T.G. Principle of equal-channel angular pressing for the processing of ultra-fine grained materials // Scr. Mater. 1996. V. 35. P. 143–146.
Valiev R.Z., Langdon T.G. Principles of equal-channel angular pressing as a processing tool for grain refinement // Prog. Mater. Sci. 2006. V. 51. P. 881–981.
Zhang J., Gao N., Starink M.J. Microstructure development and hardening during high pressure torsion of commercially pure aluminium: Strain reversal experiments and a dislocation based model // Mater. Sci. Eng. A. 2011. V. 528. P. 2581–2591.
Liu G., Gu J., Ni S., Liu Y., Song M. Microstructural evolution of Cu–Al alloys subjected to multi-axial compression // Mater. Charact. 2015. V. 103. P. 107–119.
Hajizadeh K., Ejtemaei S., Eghbali B., Kurzydlowski K.J. Microstructure and Mechanical Properties of 1050 Aluminum after the Combined Processes of Constrained Groove Pressing and Cold Rolling // Phys. Met. Metallogr. 2020. V. 121. P. 72–77.
Tohidi A.A., Ketabchi M., Hasannia A. Nanograined Ti–Nb microalloy steel achieved by Accumulative Roll Bonding (ARB) process // Mater. Sci. Eng. A. 2013. V. 577. P. 43–47.
Huang J., Zhu Y.T., Alexander D.J., Liao X., Lowe T.C., Asaro R.J. Development of repetitive corrugation and straightening // Mater. Sci. Eng. A. 2004. V. 371. P. 35–39.
Huang J.Y., Zhu Y.T., Jiang H., Lowe T.C. Microstructures and dislocation configurations in nanostructured Cu processed by repetitive corrugation and straightening // Acta Mater. 2001. V. 49. P. 1497–1505.
Brodova I.G., Shorokhov E.V, Shirinkina I.G., Zhgilev I.N., Yablonskikh T.I., Astaf’ev V.V., Antonova O.V. Evolution of the structure formation during dynamic pressing of the AMts alloy // Phys. Met. Metal. 2008. V. 105. P. 594–601.
Pippan R., Wetscher F., Hafok M., Vorhauer A., Sabirov I. The limits of refinement by severe plastic deformation // Adv. Eng. Mater. 2006. V. 8. P. 1046–1056.
Volokitina I.E., Volokitin A.V. Evolution of the Microstructure and Mechanical Properties of Copper during the Pressing–Drawing Process // Phys. Met. Metal. 2018. V. 119. P. 917–921.
Zahid G.H., Huang Y., Prangnell P.B. Microstructure and texture evolution during annealing a cryogenic-SPD processed Al-alloy with a nanoscale lamellar HAGB grain structure // Acta Mater. 2009. V. 57. P. 3509–3521.
Moreno-Valle E.C., Sabirov I., Perez-Prado M.T., Murashkin M.Y., Bobruk E.V., Valiev R.Z. Effect of the grain refinement via severe plastic deformation on strength properties and deformation behavior of an Al6061 alloy at room and cryogenic temperatures // Mater. Lett. 2011. V. 65. P. 2917–2919.
Witkin D.B., Lavernia E.J. Synthesis and mechanical behavior of nanostructured materials via cryomilling // Prog. Mater. Sci. 2006. V. 51. P. 1–60.
Khodabakhshi F., Abbaszadeh M., Eskandari H., Mohebpour S.R. Application of CGP-cross route process for microstructure refinement and mechanical properties improvement in steel sheets // J. Manuf. Process. 2013. V. 15. P. 533–541.
Lianxi H., Yuping L., Erde W., Yang Y. Ultrafine grained structure and mechanical properties of a LY12 Al alloy prepared by repetitive upsetting-extrusion // Mater. Sci. Eng. A. 2006. V. 422. P. 327–332.
Khodabakhshi F., Gerlich A.P. Accumulative fold-forging (AFF) as a novel severe plastic deformation process to fabricate a high strength ultra-fine grained layered aluminum alloy structure // Mater. Charact. 2018. V. 136. P. 229–239.
Shokuhfar A., Nejadseyfi O. A comparison of the effects of severe plastic deformation and heat treatment on the tensile properties and impact toughness of aluminum alloy 6061 // Mater. Sci. Eng. A. 2014. V. 594. P. 140–148.
Thangapandian N., Prabu S.B., Padmanabhan K.A. Effects of die profile on grain refinement in Al–Mg alloy processed by repetitive corrugation and straightening // Mater. Sci. Eng. A. 2016. V. 649. P. 229–238.
Thangapandian N., Prabu S.B., Padmanabhan K.A. On the Role of Experimental Variables in the Repetitive Corrugation and Straightening of an Al–Mg Alloy // Procedia Eng. 2017. V. 207. P. 1457–1462.
Wu X., Zhu Y. Heterogeneous materials: a new class of materials with unprecedented mechanical properties // Mater. Res. Lett. 2017. V. 5. P. 527–532.
Rosochowski A. Processing Metals by Severe Plastic Deformation // Solid State Phenom. 2005. V. 101–102. P. 13–22.
Bachmann F., Hielscher R., Schaeben H. Texture Analysis with MTEX – Free and Open Source Software Toolbox // Solid State Phenom. 2010. V. 160. P. 63–68.
Roisnel T., Rodríquez-Carvajal J. WinPLOTR: A Windows Tool for Powder Diffraction Pattern Analysis // Mater. Sci. Forum. 2001. V. 378–381. P. 118–123.
Satheesh Kumar S.S., Raghu T. Structural and mechanical behaviour of severe plastically deformed high purity aluminium sheets processed by constrained groove pressing technique // Mater. Des. 2014. V. 57. P. 114–120.
Estrin Y., Vinogradov A. Extreme grain refinement by severe plastic deformation: A wealth of challenging science // Acta Mater. 2013. V. 61. P. 782–817.
Figueroa C., Schouwenaars R., Jacobo V., Ortiz A., Petrov R., Kestens L. Tribological and Microstructural Characterization of Ultrafine Layers Induced by Wear in Ductile Alloys // Tribol. Online. 2016. V. 11. P. 389–395.
Williams J. Engineering Tribology, Cambridge University Press, Cambridge, 2005.
Reyes-Ruiz C., Figueroa I.A., Braham C., Cabrera J.M., Alfonso I., Gonzalez G. Texture and Lattice Distortion Study of an Al-6061-T6 Alloy Produced by ECAP// Mater. Trans. 2015. V. 56. P. 1781–1786.
Skrotzki W., Eschke A., Jóni B., Ungár T., Tóth L.S., Ivanisenko Y., Kurmanaeva L. New experimental insight into the mechanisms of nanoplasticity // Acta Mater. 2013. V. 61. P. 7271–7284.
Renk O., Hohenwarter A., Wurster S., Pippan R. Direct evidence for grain boundary motion as the dominant restoration mechanism in the steady-state regime of extremely cold-rolled copper // Acta Mater. 2014. V. 77. P. 401–410.
Liu J., Morris J.G. Recrystallization Textures of Continuous Cast AA 3015 Alloy: Development of the P Orientation {011} 〈566〉 // Metall. Mater. Trans. A. 2003. V. 34. P. 2029–2032.
Wang W.X., Ma M., Li H.L., Zhang J.X., Liu W.C. Effect of Preheat Treatment on the Texture Evolution During Cold Rolling of AA 3003 Aluminum Alloy // J. Mater. Eng. Perform. 2015. V. 24. P. 4283–4289.
Wang W.X., Zhang J.X., Wang Z.J., Liu W.C. A comparative study of the transformation kinetics of recrystallization texture of CC and DC 3003 aluminum alloys // Mater. Charact. 2018. V. 141. P. 412–422.
Beyerlein I.J., Tóth L.S. Texture evolution in equal-channel angular extrusion // Prog. Mater. Sci. 2009. V. 54. P. 427–510.
Tóth L.S. Texture Evolution in Severe Plastic Deformation by Equal Channel Angular Extrusion // Adv. Eng. Mater. 2003. V. 5. P. 308–316.
Figueroa C.G., Schouwenaars R., Cortés-Pérez J., Petrov R., Kestens L. Ultrafine gradient microstructure induced by severe plastic deformation under sliding contact conditions in copper // Mater. Charact. 2018. V. 138. P. 263–273.
Jenix Rino J., Balasivanandha Prabu S., Padmanabhan K.A. On the influence of repetitive corrugation and straightening on the microstructure and mechanical properties of AA 8090 Al–Li alloy // Arch. Civ. Mech. Eng. 2018. V. 18. P. 280–290.
Дополнительные материалы отсутствуют.
Инструменты
Физика металлов и металловедение