Физика металлов и металловедение, 2021, T. 122, № 6, стр. 658-664
Влияние содержания Zr и Er на структуру и свойства сплава Al–5Si–1.3Cu–0.5Mg
Р. Ю. Барков a, *, А. С. Просвиряков a, М. Г. Хомутов a, А. В. Поздняков a
a НИТУ “МИСиС”
119049 Москва, Ленинский пр., 4, Россия
* E-mail: barkov@misis.ru
Поступила в редакцию 29.10.2020
После доработки 23.01.2021
Принята к публикации 01.02.2021
Аннотация
Проведено исследование влияния добавок циркония и эрбия на структуру и механические свойства сплава Al–5Si–1.3Cu–0.5Mg в литом состоянии, после закалки и старения слитка и деформированного листа. Увеличение содержания циркония и эрбия с 0.15 до 0.2 мас. % каждого приводит к существенному эффекту модифицирования, сравнимому с модифицированием лигатурой AlTi5B1. Размер зерна при этом уменьшается с 200 до 80 мкм, в то время как в сплаве без добавок размер зерна достигает 750 мкм. Исследуемые сплавы имеют существенно больший предел текучести при сжатии как при комнатной температуре (290–295 МПа), так и при 200°С (230–235 МПа), за счет меньшего размера зерна и большего количества фаз кристаллизационного происхождения. При этом образование эрбий-содержащей фазы нерастворимой в процессе гомогенизации перед закалкой несколько снижает содержание меди в твердом растворе. Увеличение содержания циркония и эрбия повышает температуру начала рекристаллизации, и при этом не оказывает существенного влияния на свойства деформированных сплавов после их закалки и старения: предел текучести составляет 271–285 МПа, предел прочности – 337–378 МПа и относительное удлинение – 6.7–17.5%.
ВВЕДЕНИЕ
Цирконий в алюминии [1–5] и деформируемых алюминиевых сплавах системы Al–Mg [6–8] способствует достаточно эффективному упрочнению за счет выделения дисперсоидов в процессе отжига слитков при температурах выше 375°C. Скандий существенно повышает упрочняющий эффект [9–11], но является весьма дорогостоящей добавкой. Редкоземельный элемент эрбий представляется альтернативной заменой скандию согласно исследованиям последних лет [12–31]. Эрбий совместно с цирконием и без него способствует образованию L12-дисперсоидов в процессе отжига слитков, повышая прочность и температуру начала рекристаллизации алюминия [12–17], магналиев [18–23], сплавов на основе системы Al–Cu [24–27] и силуминов [28–32]. Добавки эрбия и циркония приводят к образованию сложных фаз кристаллизационного происхождения, повышают механические свойства как при комнатной, так и при повышенной температурах сплавов Al–7Si–0.4Mg (A356) [28–31] и Al–5Si–1.3Cu–0.5Mg (типа АК5М) [32].
Настоящее исследование направлено на определение влияния содержания эрбия и циркония на структуру и механические свойства сплава Al–5Si–1.3Cu–0.5Mg. Как известно, силумины с содержанием кремния более 4 мас. % отличаются хорошей технологичностью при литье [33–36], при этом невысокое содержание кремния должно обеспечить хорошую технологичность при обработке давлением, а добавки циркония и эрбия снизить склонность к разупрочнению в процессе отжига после деформации.
МЕТОДИКА ЭКСПЕРИМЕНТОВ
Сплавы составов Al–5Si–1.3Cu–0.5Mg–0.15Zr–0.15Er (AlSiErZr0.15) и Al–5Si–1.3Cu–0.5Mg–0.2Zr–0.2Er (AlSiErZr0.2) выплавлены в печи сопротивления из Al (99.99 мас. %), магния (99.9 мас. %), лигатур Al–53.5Cu, Al–12Si, Al–5Zr и Al–8Er. Для сравнения использовали базовый сплав Al–5Si–1.3Cu–0.5Mg (AlSi) и тот же сплав, модифицированный лигатурой AlTi5B1 из расчета введения 0.15 мас. % Ti (AlSiTi0.15). Разливку проводили в графитовую изложницу с внутренней полостью шириной 30 мм, толщиной 15 мм и высотой 150 мм. Скорость охлаждения составила примерно 15 K/с.
Термическую обработку проводили в печах “Nabertherm” и “SNOL” с вентилятором и точностью поддержания температуры 1°С. Слитки после термической обработки (гомогенизация 495°С, 3 ч + закалка) были прокатаны до толщины 8 мм при температуре 460–480°С и до 1 мм при комнатной температуре.
Подготовку шлифов для микроструктурных исследований производили на шлифовально – полировальной установке Struers Labopol-5. Микроструктурные исследования и идентификацию фаз проводили на световом микроскопе (СМ) Neophot 30 и на сканирующем электронном микроскопе (СЭМ) TESCAN VEGA 3LMH с использованием энергодисперсионного детектора X-Max 80.
Твердость измеряли стандартным методом Виккерса (HV) при нагрузке 5 кг и времени выдержки под нагрузкой 15 с, ошибка в определении не превышала 3 HV. Испытания на растяжение образцов, изготовленных из 1 мм листов, проводили на универсальной испытательной машине Zwick/Roll Z250 серии Allround в комплексе с автоматическим датчиком продольной деформации. Испытания на сжатие при комнатной и повышенной температурах проводили на комплексе Gleeble-3800.
РЕЗУЛЬТАТЫ ЭКСПЕРИМЕНТОВ И ОБСУЖДЕНИЕ
На рис. 1 представлена зеренная структура исследованных сплавов. В базовом сплаве AlSi (рис. 1а) размер зерна варьируется в интервале 150–750 мкм. Добавки циркония и эрбия по 0.15 мас. % приводит к видимому измельчению зеренной структуры – размер зерна в среднем составляет 200 мкм (рис. 1б). Увеличение содержания циркония и эрбия до 0.2 мас. % (в сумме 0.4 мас. %) позволяет существенно снизить размер зерна до 80 мкм (рис. 1в). Такая же зеренная структура формируется в сплаве, модифицированном 0.15 мас. % Ti (рис. 1г).
Рис. 1.
Зеренная структура слитков исследованных сплавов: а – базовый сплав Al–Si, б – сплав AlSiErZr0.15, в – сплав AlSiErZr0.2, г – сплав AlSiTi0.15.
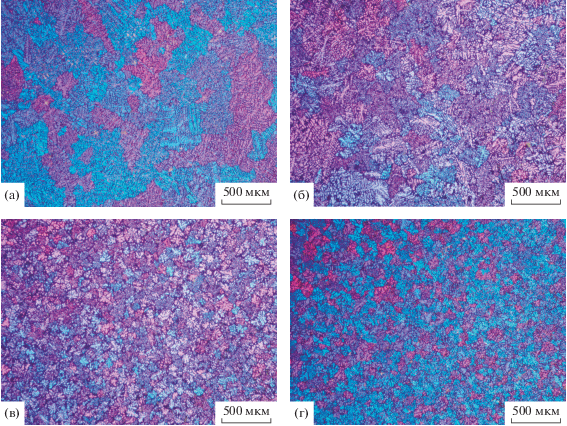
Литая микроструктура сплавов и распределение легирующих элементов между фазами в выделенной области представлены на рис. 2. Структура исследуемых сплавов представлена алюминиевым твердым раствором (Al), эвтектикой ((Al) + Si) и светлыми включениями избыточных фаз θ(Al2Cu), Q(Al5Cu2Mg8Si6) и (Al, Si, Mg, Cu, Er). Аналогичная структура сформирована в сплаве с меньшим содержанием эрбия и циркония [32]. В сплаве AlSiErZr0.2 отмечено наличие иглообразных первичных кристаллов фазы, обогащенной цирконием и эрбием (распределение элементов между фазами в левом прямоугольнике на рис. 2б). Выделения первичных кристаллов фазы Al3(Zr, Er) являются эффективными центрами зарождения первичного алюминия ввиду близости параметра решетки, что подтверждает высокую модифицирующую способность исследуемых добавок. В результате можно отметить, что для достижения эффективного модифицирования зерна и избежания образования избыточных грубых первичных кристаллов сплав необходимо легировать эрбием и цирконием от 0.15 до 0.2 мас. % каждого.
Рис. 2.
Литая микроструктура (СЭМ) сплавов AlSi ErZr015 (а) и AlSiErZr02 (б) и распределение легирующих элементов между фазами в выделенной области (белые прямоугольники).
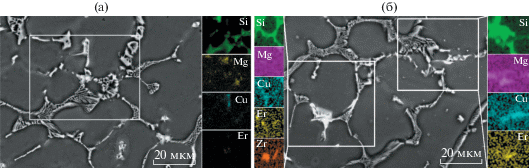
В процессе гомогенизации перед закалкой при 495°С происходит фрагментация и сфероидизация кремния и растворение неравновесного избытка фаз θ и Q (рис. 3), в результате которого концентрация легирующих элементов в твердом растворе увеличивается (табл. 1). Полное растворение неравновесного избытка фаз происходит после 3 ч отжига, когда концентрация меди и магния в твердом растворе достигает максимума (табл. 1). Светлые включения фаз, обогащенных эрбием, не изменяют морфологии и не растворяются в процессе гомогенизации (рис. 3). Концентрация Er и Zr в твердом растворе составляет 0.1–0.2 мас. %. При этом в сплаве AlSiErZr0.2 фиксируется несколько меньшее содержание меди в твердом растворе, чем в сплаве AlSiErZr0.15 (табл. 1). Это, вероятно, связано с образованием большего количества эрбий-содержащих фаз (ввиду большей концентрации эрбия в сплаве), которые не растворяются при гомогенизации.
Рис. 3.
Эволюция микроструктуры (СЭМ) литых сплавов AlSi ErZr015 (а), AlSiErZr02 (б) в процессе гомогенизации в течение 3 ч перед закалкой с 495°С.
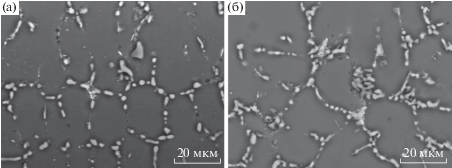
Таблица 1.
Изменение концентрации легирующих элементов в алюминиевом твердом растворе в зависимости от времени гомогенизации перед закалкой
Элемент | AlSi [32] | AlSiErZr015 | AlSiErZr02 | |||||||||
---|---|---|---|---|---|---|---|---|---|---|---|---|
литой | 1 ч | 3 ч | 5 ч | литой | 1 ч | 3 ч | 5 ч | литой | 1 ч | 3 ч | 5 ч | |
Cu | 0.5 | 1.3 | 1.5 | 1.5 | 0.5 | 1.3 | 1.4 | 1.5 | 0.5 | 1.2 | 1.3 | 1.3 |
Si | 0.6 | 0.6 | 0.6 | 0.6 | 0.6 | 0.9 | 0.9 | 0.9 | 0.6 | 0.9 | 0.9 | 0.9 |
Mg | 0.2 | 0.3 | 0.4 | 0.4 | 0.2 | 0. 3 | 0.4 | 0.4 | 0.2 | 0.4 | 0.4 | 0.4 |
Er | – | – | – | – | 0.1–0.2 | |||||||
Zr | – | – | – | – | 0.1–0.2 |
После трех часов гомогенизации при 495°С литые сплавы были закалены и состарены в течение разного времени при температурах 150, 180 и 210°С. Старение имеет характерные особенности: с увеличением температуры уменьшается время достижения пиковой твердости, максимальная твердость достигнута после старения при 150 и 180°С (рис. 4).
Рис. 4.
Зависимости твердости от времени и температуры старения закаленных сплавов AlSiErZr0.15 (а) и AlSiErZr0.2 (б).
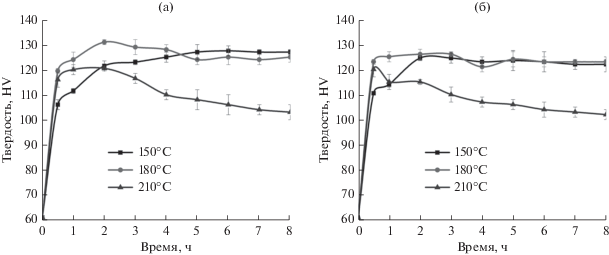
При этом твердость исследуемых сплавов в среднем на 5–10 HV выше, чем твердость базового сплава [32], что связано с влиянием дисперсоидов фазы Al3(Er, Zr), образованной в процессе гомогенизации. Похожие результаты получены в работах [26, 27]. При этом можно отметить, что больший прирост твердости при старении выявлен в сплаве с меньшим содержанием эрбия и циркония, вероятно, за счет несколько большей степени легирования алюминиевого твердого раствора после гомогенизации. Максимальный прирост твердости отмечен после двух часов старения при 180°C.
В табл. 2 представлены результаты испытаний на сжатие при комнатной и повышенной температурах закаленных сплавов, состаренных на максимальную твердость. Предел текучести исследуемых сплавов при комнатной температуре существенно выше, чем в базовом сплаве и сплаве с добавками эрбия и циркония по 0.1 мас. % (AlSiErZr). Больший предел текучести в первую очередь объясняется меньшим размером зерна. Что так же совместно с большим количеством эрбий-содержащих фаз, позволяет получить существенно больший предел текучести при 200°С – примерно на 50 МПа выше (табл. 2).
Закаленные сплавы после прокатки отжигали при 495°С с выдержкой 10 мин, закаливали и старили при температурах 150, 180 и 210°С. После закалки с 495°С исходно деформированные сплавы имеют рекристаллизованную структуру. При этом в обоих сплавах размер зерна составляет 8–12 мкм, что примерно соответствует зеренной структуре сплава с меньшим количеством циркония и эрбия [32]. Старение после закалки деформированных листов (рис. 5) проходит примерно так же, как и старение после закалки слитков (рис. 4). При этом несколько больший прирост твердости достигнут после старения при 150°С за счет того, что деформация, накопленная при прокатке, активирует низкотемпературное старение.
Рис. 5.
Зависимости твердости от времени и температуры старения сплавов AlSiErZr0.15 (а) и AlSiErZr0.2 (б) после прокатки и закалки с 495°С с выдержкой 10 мин. На вставках приведена структура сплавов после прокатки и закалки.
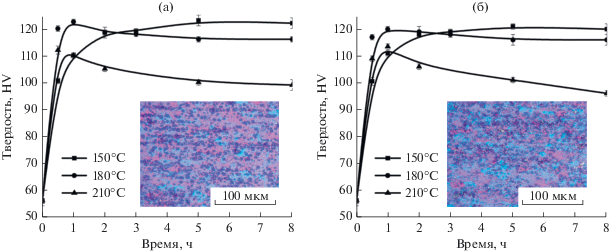
Рекристаллизация в исследуемых сплавах начинается в интервале 300–350°С (рис. 6) так же, как и в сплаве без добавок и с меньшим их количеством [32]. Однако исходно деформированные сплавы AlSiErZr0.15 и AlSiErZr0.2 после часового отжига при 350°С имеют частично рекристаллизованную структуру (вставки микроструктур на рис. 6).
Рис. 6.
Зависимости твердости от температуры отжига в течение 1 ч деформированных сплавов AlSiErZr0.15 и AlSiErZr0.2 и зеренная структура после отжига при 300 и 350°С.
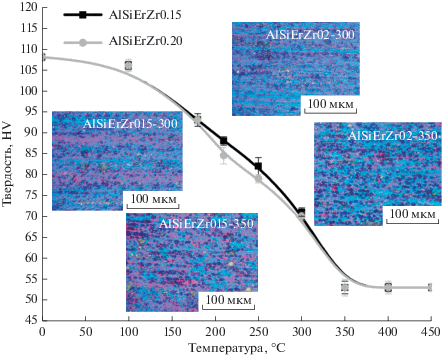
В деформированном состоянии исследованные сплавы имеют предел текучести в интервале 338–343 МПа при небольшом удлинение в 3%. Закалка деформированных листов с 495°С с последующим старением приводит к достижению предела текучести 271–285 МПа, пределу прочности 337–378 МПа и относительному удлинению 7–18%. При этом сплав с малыми добавками циркония и эрбия имеет более высокие характеристики как прочности, так и пластичности (табл. 3).
Таблица 3.
Характеристики механических свойств после испытаний на растяжение в деформированном и отожженном состояниях
Состояние | σ0.2, МПа | σв, МПа | δ, % | σ0.2, МПа | σв, МПа | δ, % |
---|---|---|---|---|---|---|
AlSiErZr015 | AlSiErZr02 | |||||
Деформированное | 338 ± 3 | 365 ± 4 | 3 ± 1 | 343 ± 5 | 368 ± 3 | 3 ± 1 |
Отжиг 150°С, 4 ч | 260 ± 2 | 372 ± 2 | 18 ± 3 | 259 ± 2 | 368 ± 3 | 14 ± 2 |
Отжиг 150°С, 8 ч | 276 ± 1 | 378 ± 1 | 15 ± 3 | 273 ± 3 | 377 ± 3 | 17 ± 1 |
Отжиг 180°С, 4 ч | 283 ± 1 | 362 ± 1 | 13 ± 1 | 285 ± 2 | 362 ± 2 | 13 ± 2 |
Отжиг 180°С, 8 ч | 280 ± 2 | 353 ± 2 | 12 ± 1 | 285 ± 3 | 350 ± 8 | 11 ± 1 |
Отжиг 210°С, 1 ч | 271 ± 2 | 338 ± 2 | 11 ± 2 | 271 ± 1 | 337 ± 4 | 7 ± 1 |
Тот же уровень свойств достигнут в сплаве с добавками циркония и эрбия по 0.1 мас. % [32]. Единственное отличие свойств после прокатки, заключается в большем пределе текучести после низкотемпературного старения при 150°С, при этом отмечена наибольшая пластичность 14–18%.
ВЫВОДЫ
Определено влияние добавок циркония и эрбия по 0.15 и 0.2% на структуру и механические свойства сплава Al–5Si–1.3Cu–0.5Mg в литом состоянии, после закалки и старения слитка и деформированного листа. При этом выявлены следующие особенности:
– введение добавок циркония и эрбия приводит к существенному эффекту модифицирования, сравнимому с модифицированием лигатурой AlTi5B1: при увеличении содержания добавок размер зерна уменьшается с 200 до 80 мкм, при 750 мкм в базовом сплаве;
– увеличение содержания добавок приводит к уменьшению содержания меди в твердом растворе, связанному с увеличением доли эрбий-содержащей фазы нерастворимой в процессе гомогенизации перед закалкой;
– исследуемые сплавы имеют существенно больший предел текучести на сжатие как при комнатной температуре (290–295 МПа), так и при 200°С (230–235 МПа), за счет меньшего размера зерна и большего количества фаз кристаллизационного происхождения;
– увеличение содержания циркония и эрбия несколько повышает температуру начала рекристаллизации, и при этом не оказывает существенного влияния на свойства деформированных сплавов после закалки и старения.
– для повышения эксплуатационных характеристик исследуемого сплава можно рекомендовать введение циркония и эрбия по 0.15–0.2 мас. % каждого.
Работа выполнена при поддержке Минобрнауки России в рамках государственного задания (код проекта 0718-2020-0030).
Список литературы
Zariff A., Chaudhury C., Suryanarayana A. TEM study of decomposition behavior of a melt-quenched A1–Zr alloy // Metallography. 1984. V. 17. P. 231–250.
Nes E. Precipitation of the metastable cubic Al3Zr-phase in subperitectic Al–Zr alloys //Acta Metall. 1972. V. 20. P. 499–506.
Xin-yu Ü., Er-jun G., Rometsch P., Li-juan W. Effect of one-step and two-step homogenization treatments on distribution of Al3Zr dispersoids in commercial AA7150 aluminium alloy // Trans. Nonferrous Metals Soc. China. 2012. V. 22. P. 2645–2651.
Knipling K.E., Dunand D.C., Seidman D.N. Precipitation evolution in Al–Zr and Al–Zr–Ti alloys during aging at 450–600°C // Acta Mater. 2008. V. 56. P. 1182–1195.
Knipling K.E., Dunand D.C., Seidman D.N. Precipitation evolution in Al–Zr and Al–Zr–Ti alloys during isothermal aging at 375–425°C // Acta Mater. 2008. V. 56. P. 114–127.
Mikhaylovskaya A.V., Portnoy V.K., Mochugovskiy A.G., Zadorozhnyy M.Yu., Tabachkova N.Yu., Golovin I.S Effect of homogenisation treatment on precipitation, recrystallisation and properties of Al–3% Mg–TM alloys (TM = Mn, Cr, Zr) // Mater. Des. 2016. V. 109. P. 197–208.
Mikhaylovskaya A.V., Mochugovskiy A.G., Levchenko V.S., Tabachkova N.Yu., Mufalo W., Portnoy V.K. Precipitation behavior of L12 Al3Zr phase in Al–Mg–Zr alloy // Mat. Char. 2018. V. 139. P. 30–37.
Ma Y., Mishra R.S. Development of ultrafine-grained microstructure and low temperature (0.48 Tm) superplasticity in friction stir processed Al–Mg–Zr // Scr. Mater. 2005. V. 53. P. 75–80.
Fuller C.B., Seidman D.N. Temporal evolution of the nanostructure of Al3(Sc, Zr) alloys: Part II-coarsening of Al3(Sc1 – xZrx) precipitates // Acta Mater. 2005. V. 53(20). P. 5415–5428.
Золоторевский В.С., Доброжинская Р.И., Чеверикин В.В., Хамнагдаева Е.А., Поздняков А.В., Левченко В.С., Бесогонова Е.С. Эволюция структуры и механических свойств листов из сплава Al–4.7Mg–0.32Mn–0.21Sc–0.09Zr за счет накопленной деформации при прокатке // ФММ. 2016. Т. 117. № 11. С. 1207–1214.
Золоторевский В.С., Доброжинская Р.И., Чеверикин В.В., Хамнагдаева Е.А., Поздняков А.В., Левченко В.С., Бесогонова Е.С. Прочность и субструктура листов из сплава Al–4.7Mg–0.32Mn–0.21Sc–0.09Zr // ФММ. 2017. Т. 118. № 4. С. 429–436.
Zhang Y., Gao K., Wen S., Huang H., Nie Z., Zhou D. The study on the coarsening process and precipitation strengthening of Al3Er precipitate in Al–Er binary alloy // J. Alloys Compd. 2014. V. 610. P. 27–34.
Wen S.P., Gao K.Y., Li Y., Huang H., Nie Z.R. Synergetic effect of Er and Zr on the precipitation hardening of Al–Er–Zr alloy // Scr. Mater. 2011. V. 65. P. 592–595.
Wen S.P., Gao K.Y., Huang H., Wang W., Nie Z.R. Precipitation evolution in Al–Er–Zr alloys during aging at elevated temperature // J. Alloys Compd. 2013. V. 574. P. 92–97.
Pozdniakov A.V., Barkov R.Yu., Prosviryakov A.S., Churyumov A.Yu., Golovin I.S., Zolotorevskiy V.S. Effect of Zr on the microstructure, recrystallization behavior, mechanical properties and electrical conductivity of the novel Al–Er–Y alloy // J. Alloys Compd. 2018. V. 765. P. 1–6.
Pozdnyakov A.V., Osipenkova A.A., Popov D.A., Makhov S.V., Napalkov V.I. Effect of Low Additions of Y, Sm, Gd, Hf and Er on the Structure and Hardness of Alloy Al–0.2% Zr–0.1% Sc // Met. Sci. Heat Treat. 2017. V. 58. № 9–10. P. 537–542.
Поздняков А.В., Барков Р.Ю. Влияние примесей на фазовый состав и свойства нового сплава системы Al–Y–Er–Zr–Sc // Металлург. 2019. № 1. С. 65–70.
Song M., Du K., Huang Z.Y., Huang H., Z.R. Nie, Ye H.Q. Deformation-induced dissolution and growth of precipitates in an Al–Mg–Er alloy during high-cycle fatigue // Acta Mater. 2014. V. 81. P. 409–419.
Hao H.L., Ni D.R., Zhang Z., Wang D., Xiao B.L., Ma Z.Y. Microstructure and mechanical properties of Al–Mg–Er sheets jointed by friction stir welding // Mater. and Des. 2013. V. 52. P. 706–712.
Wen S.P., Wang W., Zhao W.H., Wu X.L., Gao K.Y., Huang H., Nie Z.R. Precipitation hardening and recrystallization behavior of Al–Mg–Er–Zr alloys // J. Alloys Compd. 2016. V. 687. P. 143–151.
Yang Dongxi, Lixiaoyan, Hedingyong, Huanghui. Effect of minor Er and Zr on microstructure and mechanical properties of Al–Mg–Mn alloy (5083) welded joints // Mater. Sci. & Eng. A. 2013. V. 561. P. 226–231.
Pozdniakov A.V., Yarasu V., Barkov R.Yu., Yakovtseva O.A., Makhov S.V., Napalkov V.I. Microstructure and mechanical properties of novel Al–Mg–Mn–Zr–Sc–Er alloy // Mat. Let. 2017. V. 202. P. 116–119.
Mochugovskiy A.G., Mikhaylovskaya A.V., Tabachkova N.Yu., Portnoy V.K. The mechanism of L12 phase precipitation, microstructure and tensile properties of Al–Mg–Er–Zr alloy // Mater. Sci. & Eng. A. 2019. V. 744. P. 195–205.
Поздняков А.В., Барков Р.Ю., Сарсенбаев Ж., Кхамеес Е., Просвиряков А.С. Эволюция микроструктуры и механических свойств нового деформируемого сплава системы Al–Cu–Er // ФММ. 2019. Т. 120. № 6. С. 668–672.
Амер С.М., Барков Р.Ю., Яковцева О.А., Поздняков А.В. Сравнительный анализ структуры и свойств квазибинарных сплавов Al–6.5Cu–2.3Y и Al–6Cu–4.05Er // ФММ. 2020. Т. 121. № 5. С. 528–534.
Amer S.M., Barkov R.Yu., Yakovtseva O.A., Loginova I.S., Pozdniakov A.V. Effect of Zr on microstructure and mechanical properties of the Al–Cu–Er alloy // Mater. Sci. and Techn. 2020. V. 36. № 4. P. 453–459.
Amer S.M., Yakovtseva O.A., Loginova I.S., Medvedeva S.V., Prosviryakov A.S., Bazlov A.I., Barkov R.Yu., Pozdniakov A.V. Phase composition and mechanical properties of a novel precipitation strengthening Al–Cu–Er–Mn–Zr alloy // Applied Sciences (Switzerland). 2020. V. 10(15). P. 5345.
Hu X., Jiang F., Ai F., Yan H. Effects of rare earth Er additions on microstructure development and mechanical properties of die-cast ADC12 aluminum alloy // J. Alloys Compd. 2012. V. 538. P. 21–27.
Shi Z.M., Wang Q., Zhao G., Zhang R.Y. Effects of erbium modification on the microstructure and mechanical properties of A356 aluminum alloys // Mater. Sci. Eng. A. 2015. V. 626. P. 102–107.
Colombo M., Gariboldi E., Morri A. Er addition to Al–Si–Mg-based casting alloy: effects on microstructure, room and high temperature mechanical properties // J. Alloys Compd. 2017. V. 708. P. 1234–1244.
Colombo M., Gariboldi E., Morri A. Influences of different Zr additions on the microstructure, room and high temperature mechanical properties of an Al–7Si–0.4Mg alloy modified with 0.25% Er // Mater. Sci. Eng. A. 2018. V. 713. P. 151–160.
Барков Р.Ю., Мочуговский А.Г., Хомутов М.Г., Поздняков А.В. Влияние малых добавок Zr и Er на фазовый состав и механические свойства сплава Al–5Si–1.3Cu–0.5Mg // ФММ. 2021. Т. 122. № 2. P. 173–180.
Новиков И.И. Горячеломкость цветных металлов и сплавов. М.: Наука, 1966.
Eskin D.G., Suyitno, Katgerman L. Mechanical properties in the semi-solid state and hot tearing of aluminium alloys // Prog. in Mat. Sci. 2004. V. 49. P. 629–711.
Zolotorevskiy V.S., Pozdniakov A.V. Determining the hot cracking index of Al–Si–Cu–Mg casting alloys calculated using the effective solidification range // Int. J. Cast Met. Res. 2014. V. 27. № 4. P. 193–198.
Золоторевский В.С., Поздняков А.В., Чурюмов А.Ю. Поиск перспективных композиций для создания новых многофазных литейных сплавов на основе матрицы Al–Cu–Mg с использованием термодинамических расчетов и математического моделирования// ФММ. 2012. Т. 113. № 11. С. 1111–1120.
Дополнительные материалы отсутствуют.
Инструменты
Физика металлов и металловедение