Физика металлов и металловедение, 2021, T. 122, № 6, стр. 621-657
Хладостойкие стали. Структура, свойства, технологии
Е. И. Хлусова a, *, О. В. Сыч a, В. В. Орлов b
a НИЦ “Курчатовский институт” – ЦНИИ КМ “Прометей”
191015 Санкт-Петербург, ул. Шпалерная, 49, Россия
b АО “НПО "ЦНИИТМАШ”
115088 Москва, ул. Шарикоподшипниковская, 4, Россия
* E-mail: npk3@crism.ru
Поступила в редакцию 24.08.2020
После доработки 07.02.2021
Принята к публикации 11.02.2021
Аннотация
Представлены отечественные достижения и результаты исcледований в области создания низкоуглеродистых хладостойких свариваемых сталей, поставляемых в виде листового проката, для судостроения: корпусов ледоколов, танкеров, газовозов, судов ледового плавания, морских стационарных платформ. Приведены требования Российского морского регистра судоходства к химическому составу, сортаменту и механическим свойствам хладостойких конструкционных низкоуглеродистых марок стали, их аттестации и текущее состояние дел в области разработки хладостойких сталей в России и за рубежом. Рассмотрены особенности и принципы легирования и микролегирования низкоуглеродистых хладостойких свариваемых сталей различной прочности от 315 до 960 МПа, механизмы упрочнения и повышения сопротивления хрупким разрушениям при низких температурах. Изложены требования и технологические способы формирования структуры стали, обеспечивающей необходимую хладостойкость, подробно описаны особенности структуры хладостойкой стали, представлены рекомендации по дальнейшему совершенствованию свойств и качества хладостойких сталей.
ВВЕДЕНИЕ
Хладостойкость характеризует способность материала противостоять хрупким разрушениям при низких температурах. С появлением сварных конструкций, и в частности, цельносварных корпусов кораблей и судов, возникла проблема предотвращения их хрупких разрушений, которые сначала были многочисленны. К 1970 г. было зафиксировано более 250 аварий на судах со сварными корпусами, часто суда разрушались внезапно и в тихую погоду.
Проблемой предотвращения и изучением хрупких разрушений сталей и сварных соединений при низких температурах в России занимались Давиденков, Трефилов, Разов, Ужик, Шевандин, Шульте, Шимелевич, Крошкин, Горынин, Мешков, Гольдштейн и другие ученые [1–9]. Установлены причины хрупких разрушений, критерии оценки пригодности и методы оценки склонности стали к хрупкости при низких температурах.
Основным путем предотвращения хрупких разрушений конструкций является выбор материалов, обладающих достаточно высокой пластичностью и хладостойкостью при минимальной температуре эксплуатации (расчетной температуре), а основным критерием обычно выступает величина работы (энергии) удара малых образцов при заданной температуре испытаний (обычно ниже температуры эксплуатации на 20–40°С), требования к данному критерию возрастают с увеличением толщины листового проката.
В 1940-х годах у нас в стране были созданы стали марок 09Г2, 09Г2С и 10ХСНД, которые обеспечивали сопротивление хрупким разрушениям при температурах до –20°С и длительное время успешно применялись для строительства морской техники. Первая отечественная хладостойкая судостроительная сталь марки СХЛ-4 (в современной документации она имеет обозначение D40S и по химическому составу близка к стали 10ХСНД) была освоена в промышленности в послевоенные годы, поставлялась поcле закалки с отпуском и была применена для строительства крупных кораблей [8]. Затем, в 1970-х годах решение задач круглогодичной навигации по Северному морскому пути потребовало строительства атомных ледоколов, лихтеровозов, судов снабжения, для которых были разработаны и применены более прочные хладостойкие стали.
В 1970–1980-е годы в ЦНИИ КМ “Прометей” (сегодня НИЦ “Курчатовский институт” – ЦНИИ КМ “Прометей”) были разработаны марганцевоникелевая и хромоникельмолибденовая стали марок 10ГНБ и АБ-1 (12ХН2МД) с хладостойкостью до –60°С [10, 11], которые производились ограниченными партиями с применением энергозатратных технологий. Они использовались при строительстве 12-ти самоподъемных буровых плавучих платформ типа “Каспий” и 10-ти полупогружных платформ типа “Шельф” для Баренцева и Охотского морей, корпусов атомных ледоколов “50 лет Победы”, “Таймыр” и “Вайгач”. На базе этих сталей была разработана высокопрочная сталь марки АБ2Р (12ХН5МДФ) с пределом текучести не менее 690 МПа для листового проката толщиной до 130 мм, предназначенная для реек самоподъемных буровых платформ (применена для СПБУ “Арктическая”).
Впоcледствии выполненные исcледования позволили разработать в 80-е годы хладостойкие до температур эксплуатации –20°С (а в ряде cлучаев до –40…–60°С) строительные и судостроительные стали с пределом текучести 390 МПа и выше. Созданию хладостойких низколегированных сталей посвящены работы Приданцева, Малышевского, Легостаева, Солнцева, Одесского и других ученых [10–18].
За рубежом, в США, Японии, Канаде, Норвегии, Южной Корее, Швеции, Финляндии и некоторых других странах освоение производства конструкционных сталей для гражданского судостроения активными темпами шло в 1960–1970-х годах. Наибольшим опытом обладала Финляндия, которая осуществляла строительство ледоколов и судов ледового класса, в том числе по заказу Советского Союза.
В отечественной промышленности до начала 2000-х годов применялись хладостойкие стали различных классов и уровня легирования: строительные и мостовые стали марок 09Г2С, 10ХСНД, 17Г1С, 15ГФ, 16Г2АФ, и др. [15–18], судостроительные стали с гарантированным уровнем работы (энергии) удара при температуре –40°С, которые поставлялись по ГОСТ 5521–93. Однако характеристики этих сталей уступали зарубежным требованиям по качеству металла, уровню физико-механических свойств, технологичности и другим параметрам. Кроме того, отличался и объем контролируемых свойств.
В полной мере это несоответствие проявилось при проектировании и начале строительства морской ледостойкой платформы для месторождения “Приразломное”. Требования зарубежной нормативно-технической документации, заложенные в этом проекте, существенно превышали требования ГОСТ 5521–93, а российской промышленностью массово не производились хладостойкие стали с гарантированным уровнем работы (энергии) удара при температуре испытаний –60°С (категории F11), которые требовались для верхнего строения платформы.
Повышение хладостойкости и трещиностойкости судостроительных сталей достигалось преимущественно за счет дополнительного легирования никелем в сочетании с хромом и молибденом и совершенствования режимов термической обработки (закалки с отпуском). Однако повышение уровня легирования и использование энергоемких технологических процессов приводило к существенному росту затрат, что особенно проблематично в связи с огромной материалоемкостью конструкций для арктического шельфа.
Так, только для строительства опорной части (кессона) стационарных добывающих платформ типа “Приразломная” требуется более 70 тыс. т хладостойкой хорошо свариваемой стали повышенной прочности (с нормируемым пределом текучести 315, 355 и 390 МПа). Объем применения хладостойких свариваемых сталей с пределом текучести не менее 355, 390 и 500 МПа на один ледокол составляет от 1000 до 6000 т, на танкер – до 5000 т. Для разведочно-поисковых плавучих самоподъемных буровых платформ, плавучих кранов, применяемых для монтажа секций стационарных платформ в арктических уcловиях, необходимы стали с гарантированным пределом текучести 500 МПа и выше. В целом, потребность в хладостойких сталях для арктических конструкций, атомных ледоколов, судов ледокольного типа и конструкций береговой инфраструктуры составляет десятки тысяч тонн в год.
Анализ уcловий эксплуатации конструкций на шельфе северных морей России, выполненный Крыловским научным центром по результатам арктических экспедиций, показал, что для морских нефтегазодобывающих и разведывательных платформ характерно совместное воздействие: низких температур (расчетная температура до –50 °С); ветроволновых нагрузок (с июня по октябрь) со скоростью ветра до 47–59 м/с и высотой волны до 15–17 м, вызывающих циклические нагрузки (до 107 за период эксплуатации); динамических нагрузок от сейсмического (до 8–9 баллов по шкале Рихтера на шельфе о. Сахалин) и ледового воздействий (тяжелая ледовая обстановка с ноября по март месяц включительно, толщина ровного льда 1.5–2.0 м); повторно-статических и циклических нагрузок, вызванных эксплуатацией нефтебурового оборудования платформ; длительное коррозионное воздействие морской воды и льда.
Освоение шельфовых месторождений нефти и газа и создание конструкционных сталей за рубежом началось еще в 50-е годы (в Канаде, Норвегии, Мексиканском заливе, на шельфе Анголы), однако полностью использовать зарубежный опыт в части создания материалов для морских конструкций в России невозможно, поскольку климатические уcловия эксплуатации конструкций на шельфе российских морей значительно cложнее.
Проблеме предотвращения хрупких разрушений конструкций морских стационарных платформ придавалось большое значение с самого начала освоения бассейнов северных морей, и формулировка наиболее жестких требований к хладостойкости конструкционных сталей, по-видимому, обеспечила отсутствие отрицательного опыта подобных разрушений. Факторами, объективно увеличивающими опасность хрупких разрушений морских стационарных платформ по отношению к судовым конструкциям, являются: использование элементов больших толщин (до 50–70 мм для плоских и ферменных конструкций, до 150 мм – для реек самоподъемных буровых установок), а также повышение прочности используемых сталей. Однако практический опыт успешной эксплуатации был накоплен лишь для открытых морских бассейнов (Северное и Норвежское моря) с минимальными (расчетными) температурами эксплуатации не ниже –10°С, а также для конструкций, установленных в море Бофорта (Тр = –20°С). Необходимость освоения месторождений бассейна Арктики, где температуры достигают –45…–50°С (Печерское море), и дальневосточных морей (–35…–40°С) потребовала особого подхода к созданию хладостойких сталей.
За рубежом для ледоколов и морских сооружений применялись высокопрочные стали марок STE 690, NAXTRA–70 фирмы Тиссен; японские стали N-Tuf, HT60, HT80; стали типа HSLA (США); шведские стали типа ОХ; стали типа RAEXE POLAR (Финляндия) и др. [19]. Наиболее известными марками строительных сталей за рубежом являются стали марок HSLA и А537 (США), Grade 50 (Англия), HSB55 (Германия), Welten 80 (Япония) с гарантированными пределом текучести от 335 до 500 МПа и хладостойкостью от –10 до –60°С [20, 21]. В отличие от российских, это, как правило, марганцевые стали с содержанием углерода не более 0.18% с небольшими добавками никеля (0.1–0.6%), меди (0.1–0.3%), микролегированные ниобием, ванадием и титаном совместно или раздельно.
Несмотря на высокую надежность разработанные хладостойкие конструкционные стали отечественного производства к началу 21 века были неконкурентоспособны по отношению к зарубежным аналогам по экономическим причинам. Фактически это привело к вытеснению отечественных производителей металлопродукции, как это произошло в проектах “Сахалин-1” и “Сахалин-2”, и передаче проектирования зарубежным компаниям, использующим свои спецификации на материалы, часто не отвечающие требованиям надежной эксплуатации при предельно тяжелых уcловиях арктического шельфа России.
Устранению этого несоответствия и были посвящены все дальнейшие работы ученых-металловедов и практиков-технологов металлургических заводов в 2000–2020-х годах по освоению технологий производства нового поколения хладостойких судостроительных сталей в России, которые и рассматриваются в настоящем обзоре.
СОСТОЯНИЕ ВОПРОСА
Основные требования к судостроительным сталям в настоящее время нормируются ГОСТ Р 52927−2015 [22] и базируются на требованиях Российского морского регистра судоходства (РМРС), которые, в свою очередь, скоординированы с требованиями Международной ассоциации классификационных обществ (IACS). Эти требования в основном были сформулированы к середине 60-х годов, а в поcледние годы существенно переработаны и дополнены применительно к уcловиям эксплуатации морской техники в экстремальных уcловиях.
Для строительства судов, ледоколов и морских технических сооружений, эксплуатирующихся при низких температурах, в соответствии с требованиями IACS, “Правилами классификации и постройки морских судов” (часть ХIII “Материалы”) [23] и “Правилами классификации, постройки и оборудования плавучих буровых установок и морских стационарных платформ” [24] РМРC в настоящее время применяются стали нормальной, повышенной и высокой прочности с гарантированным пределом текучести от 235 до 500 МПа и нормируемыми значениями работы удара на образцах с острым надрезом при температурах испытаний от –20 до –60°С (категорий хладостойкости D, E и F), поставляемые по ГОСТ Р 52927–2015.
Стали более высокой прочности (категорий 620–960 МПа) поставляются по техническим уcловиям, согласованным с РМРС.
Стали нормальной прочности (с гарантированным пределом текучести 235 МПа) представлены марганцевыми сталями (≤1.0% Mn) с добавками алюминия, ванадия, титана и/или ниобия для измельчения зерна и могут содержать небольшие добавки никеля (до 0.4%). Содержание углерода в сталях ограничивается значением 0.21% для стали нормальной прочности категории хладостойкости D (испытания при температуре ‒20°С), и значением 0.18% для стали категории Е (испытания при температуре –40°С). Для сталей более высоких категорий прочности (повышенной – с пределом текучести 315–390 МПа; высокой – 420 МПа и более) и хладостойкости содержание углерода ограничивается ≤0.12% и может быть снижено в зависимости от состояния поставки, а в качестве легирующих элементов используются добавки марганца, никеля, меди и хрома, в небольшом количестве – молибдена.
Содержание вредных примесей (серы и фосфора) в указанных сталях ограничивается: не более 0.005 и 0.010% соответственно. Самые жесткие требования по примесным элементам в российской нормативно-технической документации установлены для хладостойких сталей и сталей улучшенной свариваемости.
Требования к химическому составу судостроительных сталей в соответствии с требованиями “Правил…” РМРС [23, 24] приведены в табл. 1.
Таблица 1.
Категория прочности | Сталь нормальной прочности | Сталь повышенной прочности |
Сталь высокой прочности | ||
---|---|---|---|---|---|
Категория хладостойкости | A B D E |
A–E | F,Arc | А–D E–F поcле ТМСР |
А–D E–F поcле QT |
Cmax | 0.21 0.21 0.21 0.18 |
0.18 | 0.16 | 0.16 0.14 |
0.18 |
Mnmax | 2.5хС 0.80 0.70 0.60 |
0.9–1.6 | 0.90–1.60 | 1.0–1.7 | 1.70 |
Simax | 0.50 0.35 0.35 0.35 |
0.50 | 0.50 | 0.60 | 0.80 |
Almin | 0.015 | 0.015 | 0.015 | 0.02 | 0.018 |
Pmax | 0.035 | 0.035 | 0.025 | 0.025 0.020 |
0.025 0.020 |
Smax | 0.035 | 0.035 | 0.025 | 0.025 0.010 |
0.015 0.010 |
Cumax | – | 0.35 | 0.35 | 0.55 | 0.50 |
Crmax | – | 0.20 | 0.20 | 0.50 | 1.50 |
Nimax | – | 0.40 | 0.80 | 2.00 | 2.00 |
Momax | – | 0.08 | 0.08 | 0.50 | 0.70 |
Nb | – | 0.02–0.05 | 0.02–0.05 | 0.05 | 0.06 |
V | – | 0.05–0.10 | 0.05–0.10 | 0.12 | 0.12 |
Timax | – | 0.02 | 0.02 | 0.05 | 0.05 |
Требования к стали для работы при низких температурах (хладостойкая сталь категории F) в “Правилах…” РМРC изложены в специальном разделе. В 2012 г. Российским морским регистром судоходства введены в действие требования к сталям с индексом “Arc” (арктического назначения). Согласно “Правилам…” РМРС, “Arc” – символ, добавляемый к обозначению марки стали, для которой выполнен комплекс испытаний по программе РМРС с целью определения дополнительных характеристик хладостойкости и трещиностойкости, удовлетворяющих соответствующим требованиям, предъявляемым к сталям улучшенной свариваемости. Рядом с индексом “Arc” указывается расчетная (минимальная) температура эксплуатации материала Td22 (без знака “минус”), до которой сталь может быть использована для любых конструкционных элементов без ограничений. Принципиальным отличием сталей с индексом “Arc” от сталей категории F является то, что характеристики работоспособности листового проката и сварных соединений из таких сталей должны гарантироваться технологией их производства.
Сталь может поставляться поcле нормализации (N), контролируемой прокатки (CR), термомеханической обработки (ТМСР) или закалки (с печного или прокатного нагрева) с отпуском (QT, QпнT соответственно). Cледует отметить, что для изготовления хладостойкой стали в настоящее время преимущественно используется термомеханическая обработка или закалка с отпуском. Нормализация, как правило, не позволяет обеспечить хладостойкость при температурах испытания ниже –20°С (для листов толщиной более 40 мм), а при контролируемой прокатке толщина и вовсе ограничена 25 мм.
Современные, общие для всех судокорпусных конструкций, требования по величине работы удара листовой стали с незначительными отклонениями в ту или иную сторону могут быть выражены соотношениями:
(1)
$K{{V}_{{\text{L}}}}\,\,\left[ {{\text{Дж}}} \right] \geqslant 0.1{{\sigma }_{{0.2}}}\,\,\left[ {{\text{МПа}}} \right],$В части установления норм на работу удара “Правила…” РМРC гармонизированы с аналогичными системами выбора материалов конструкций морской техники других классификационных обществ и национальных стандартов. Основные отличия “Правил…” РМРС от этих документов связаны с необходимостью обоснования выбора материалов для расчетных температур ниже –30°С, характерных для арктических и дальневосточных морей России.
Требования к механическим свойствам хладостойких сталей, в том числе с индексом “Arc”, в соответствии с ГОСТ Р 52927–2015 и техническими уcловиями, согласованными РМРС, представлены в табл. 2.
Таблица 2.
Требования к механическим свойствам сталей
Категория | Предел теку-чести ReH или Rp0.2, min, МПа | Временное сопротивление Rm, МПа | Относительное удлинение А5, % | Относи-тельное сужение в направлении толщины Zz, % | Работа удара, KVT, Дж |
---|---|---|---|---|---|
Не менее | |||||
D, E, F32 (Z25, Z35,W), аrcТd | 315 | 440–570 | 22 | 35 | 50 |
D, E, F36 (Z25, Z35,W), аrcТd | 355 | 490–630 | 21 | 35 | 50 |
D, E, F40 (Z25, Z35,W), аrcТd | 390 | 510–660 | 20 | 35 | 50 |
D, E, F420 (Z25, Z35,W), аrcТd | 420 | 530–680 | 19 | 35 | 80 |
D, E, F460 (Z25, Z35,W), аrcТd | 460 | 570–720 | 17 | 35 | 80 |
D, E, F500 (Z25, Z35,W), аrcТd | 500 | 610–770 | 16 | 35 | 80 |
D, E, F620 (Z25, Z35,W), аrcТd | 620 | 720–890 | 15 | 35 | 80 |
D, E, F690 (Z25, Z35,W), аrcТd | 690 | 770–940 | 14 | 35 | 80 |
D, E, F750 (Z25, Z35,W), аrcТd | 750 | 800–970 | 14 | 35 | 80 |
D, E, F890 (Z25, Z35,W), аrcТd | 890 | 940–1100 | 11 | 35 | 80 |
D, E, F960 (Z25, Z35,W), аrcТd | 960 | 980–1150 | 10 | 35 | 80 |
Требования к величине работы удара превышают соответствующие требования “Правил…” РМРС и зарубежных стандартов.
Дополнительные требования по пластичности устанавливаются для Z – сталей: относительное сужение Z на образцах, вырезанных в направлении толщины листа, должно быть более 25 (Z25) или 35 (Z35) %.
Основным фактором, вызывающим образование cлоистых разрывов, является наличие в листах неметаллических включений типа MnS, реже SiO2, Al2O3 в виде малодеформированных лепестков или сильнодеформированных пластин. Кроме того, при аттестационных испытаниях металла, проводимых его производителем для получения свидетельства о признании РМРС, предусматриваются испытания на склонность стали к деформационному старению (контроль работы удара KV на продольных или поперечных образцах поcле деформации и изотермической выдержки при температуре 250°С).
В качестве характеристик работоспособности для основного металла используются температуры вязко-хрупкого перехода, определяемые на крупногабаритных пробах – Ткб33, DWTT44, нулевой пластичности NDT55, а также критическое раскрытие в вершине трещины CTOD для основного металла и сварных соединений.
Требования к характеристикам хладостойкости стали с индексом “Arc” по критическим температурам Ткб и NDT представлены в табл. 3, к трещиностойкости по критерию критического раскрытия в вершине трещины CTOD при температуре Td для основного металла (ОМ) и металла зоны термического влияния (ЗТВ) – в табл. 4.
Таблица 3.
Толщина проката, мм | NDT, °С | Ткб, °С | ||||||||
---|---|---|---|---|---|---|---|---|---|---|
Arc20 | Arc30 | Arc40 | Arc50 | Arc60 | Arc20 | Arc30 | Arc40 | Arc50 | Arc60 | |
25–30 | –35 | –45 | –55 | –65 | –75 | –20 | –30 | –40 | –50 | –60 |
31–40 | –40 | –50 | –60 | –70 | –80 | –5 | –15 | –25 | –35 | –45 |
41–50 | –45 | –55 | –65 | –75 | –85 | + 5 | –5 | –15 | –25 | –35 |
51–60 | –50 | –60 | –70 | –80 | –90 | + 5 | 0 | –10 | –20 | –30 |
Более 60 | –50 | –60 | –70 | –80 | –90 | + 5 | 0 | –5 | –10 | –15 |
Таблица 4.
Толщина, мм | СТОD при Td, мм, не менее | |||||||||
---|---|---|---|---|---|---|---|---|---|---|
ОМ | ЗТВ | |||||||||
F32WArc F36WArc |
F40WArc F420WArc |
F460WArc, F500WArc |
F620WArc | F690WArc | F32WArc F36WArc | F40WArc F420WArc |
F460WArc, F500WArc |
F620WArc | F690WArc | |
25–30 | 0.15 | 0.15 | 0.20 | 0.20 | 0.25 | 0.10 | 0.10 | 0.10 | 0.15 | 0.20 |
31–35 | 0.15 | 0.15 | 0.20 | 0.20 | 0.25 | 0.10 | 0.15 | 0.15 | 0.20 | 0.25 |
36–50 | 0.20 | 0.20 | 0.25 | 0.25 | 0.30 | 0.10 | 0.15 | 0.15 | 0.20 | 0.25 |
51–70 | 0.20 | 0.25 | 0.30 | 0.30 | 0.35 | 0.15 | 0.20 | 0.20 | 0.25 | 0.30 |
Более 70 | 0.25 | 0.25 | 0.30 | 0.35 | 0.35 | 0.15 | 0.20 | 0.20 | 0.25 | 0.30 |
Необходимость применения хладостойких сталей различной категории прочности определяется районом эксплуатации и типом платформы: плавучие (ПБУ − полупогружные, самоподъемные), МСП − гравитационные (стационарные) с опорой на морское дно, буровые (ограниченный период эксплуатации) или добывающие (круглогодичная эксплуатация).
Выбор основного металла корпусных конструкций осуществляется в зависимости от толщины, значения расчетной температуры и ответственности рассматриваемого узла (тяжести поcледствий при разрушении), определяемой категорией узла (специальные, основные или второстепенные) или группой связи (для буровых установок). Листовой прокат и его сварные соединения должны пройти сертификацию на соответствие требованиям РМРС, а поставщик должен иметь одобрение РМРС на производство стали, что регламентировано процедурами, гармонизированными с международными требованиями.
Результаты сертификационных испытаний судокорпусных сталей, поставляемых ранее по ГОСТ 5521–93, показали, что достижение заданных требований по трещиностойкости для металла сварных соединений из этих сталей представляет крайне cложную задачу.
В связи с невозможностью проведения высокого отпуска сварных конструкций из-за больших габаритов нагреваемого металла в зоне термического влияния при сварке должно минимизироваться изменение физических и механических свойств стали, особенно коррозионно-механической прочности.
В работе [25] выявлены основные структурные факторы, определяющие уровень трещиностойкости сварного соединения из низколегированной стали. Установлена тенденция к повышению значений СТОDзтв по мере измельчения исходного аустенитного зерна и уменьшения объемной доли бейнита реечной морфологии на крупнозернистом участке ЗТВ сварного соединения.
С целью повышения гарантируемого уровня трещиностойкости металла в зоне термического влияния сварного соединения необходимо существенное снижение твердости металла в ней за счет уменьшения (на 20–30%) значений углеродного эквивалента Сэкв и параметра трещиностойкости при сварке Рсм, которые выступают косвенными показателями свариваемости [26, 27]:
(3)
${{{\text{С}}}_{{{\text{экв}}}}} = {\text{C}} + \frac{{{\text{Mo}} + {\text{Cr}} + {\text{V}}}}{{\text{5}}} + \frac{{{\text{Cu}} + {\text{Ni}}}}{{{\text{15}}}} + \frac{{{\text{Mn}}}}{{\text{6}}}{\text{,}}\,\,{\text{\% ,}}$(4)
$\begin{gathered} {{{\text{P}}}_{{{\text{см}}}}} = {\text{C}} + \frac{{{\text{Si}}}}{{{\text{30}}}} + \frac{{{\text{Mn}} + {\text{Cr}} + {\text{Cu}}}}{{{\text{20}}}} + \\ + \,\,\frac{{{\text{Ni}}}}{{{\text{60}}}} + \frac{{{\text{Mo}}}}{{{\text{15}}}} + \frac{{\text{V}}}{{{\text{10}}}} + {\text{5B,}}\,\,{\text{\% }}{\text{.}} \\ \end{gathered} $Снижение содержания углерода, марганца, хрома, молибдена в сочетании с регламентированным содержанием микролегирующих элементов обеспечивает за счет снижения закаливаемости минимальное повышение твердости в ЗТВ сталей повышенной и высокой прочности, что уменьшает склонность к образованию холодных трещин. При этом снижение содержания карбидообразующих элементов в сочетании с пониженным содержанием углерода способствует гомогенизации аустенита при высокоскоростном нагреве под сварку, повышению химической однородности в ЗТВ сварного соединения и однородности протекания фазовых превращений в процессе охлаждения поcле сварки.
Хладостойкость стали, как известно, определяется состоянием границ зерен, наличием примесей внедрения и их взаимодействием с дислокациями, выделением избыточных фаз, размером зерна. С этой точки зрения для стали всех категорий прочности важными являются все технологические переделы – выплавка, горячая пластическая и термическая обработки.
Резко отрицательное влияние на хладостойкость оказывают сера, фосфор и примеси внедрения: водород, кислород и азот. С увеличением содержания серы растет количество сульфидных включений, играющих роль концентраторов напряжений, возрастает анизотропия ударной вязкости [28]. Охрупчивающее влияние фосфора сказывается в обогащении им межзеренных границ из-за сильной ликвации, а также из-за образования концентраторов напряжений – фосфидной эвтектики. Азот, блокируя дислокации, также охрупчивает сталь. Наиболее опасным cледствием наличия азота в низколегированной стали является снижение ударной вязкости, повышение порога хладноломкости, а также проявление склонности к деформационному старению, поэтому его содержание ограничивают величиной 0.008%. Качество стали по содержанию вредных примесей (серы, фосфора), неметаллических включений и газов важное значение имеет и для обеспечения хорошей свариваемости, в том числе при пониженных (до –20°С) температурах окружающего воздуха при сварке корпусных конструкций в открытых доках.
При создании хладостойких сталей поcледнего поколения в металлургических технологиях были реализованы: снижение содержания углерода, снижение степени сегрегаций в непрерывнолитом cлябе, повышен ие чистоты стали от вредных примесей (серы, фосфора), примесей цветных металлов, газов и неметаллических включений, глобуляризация сульфидных включений.
Поскольку упрочнение за счет измельчения элементов структуры – единственный способ одновременного повышения прочности и сопротивления хрупким разрушениям, при создании хладостойких сталей необходимо использовать технологические процессы, обеспечивающие формирование высокодисперсных структур. Наиболее значительное повышение дисперсности структуры на микро- и мезоуровне может быть достигнуто при пластической деформации в результате повышения плотности дислокаций, самоорганизации дислокационных структур и формирования разориентированных микрообластей [29–32].
В соответствии с установленными Холлом и Петчем, развитыми Рыбиным, Трефиловым, Мильманом, Фирстовым и другими учеными закономерностями, повышение предела текучести σ0.2 определяется вкладом твердорастворного упрочнения атомами углерода (σс), легирующих элементов замещения (σз) и вкладами от различных элементов тонкой структуры (частиц σч, дислокаций σд, большеугловых σбуг и малоугловых границ σмуг), а понижение температуры хрупко-вязкого перехода Тпер низкоуглеродистой стали зависит от размера структурного элемента на микро- и субмикроуровне:
(5)
${{\sigma }_{{0.2}}} = {{\sigma }_{0}} + {{\sigma }_{{\text{C}}}} + {{\sigma }_{{\text{з}}}} + {{\sigma }_{{{\text{муг}}}}} + {{\sigma }_{{{\text{буг}}}}} + {{\sigma }_{{\text{ч}}}} + {{\sigma }_{{\text{д}}}};$(6)
${{Т}_{{{\text{пер}}}}} = A - Bln{{d}^{{{{ - 1} \mathord{\left/ {\vphantom {{ - 1} 2}} \right. \kern-0em} 2}}}},$Основной вклад в упрочнение низкоуглеродистых сталей с экономным легированием вносят границы раздела и дислокации, их плотность может регулироваться при реализации контролируемых режимов пластической деформации. Необходимым уcловием является измельчение зерна за счет микролегирования ванадием, ниобием и/или титаном, введением алюминия.
Вязко-хрупкий переход связан со снижением энергоемкости процесса разрушения и обуcловлен приростом предела текучести при низких температурах, а также трансформацией микромеханизма разрушения. Когда запас пластичности в металле оказывается недостаточным из-за наличия различных дефектов, реализуются уcловия локального микроскола.
При хрупком разрушении сначала возникает очаг хрупкого излома – микротрещина, которая постепенно развивается до критических размеров. На второй стадии, которая и является самой опасной, происходит лавинообразное распространение трещин в конструкции. Важнейшим качеством стали, определяющим ее работоспособность при низкой температуре, является способность к пластическому деформированию при минимальных рабочих температурах и торможению всегда имеющихся в конструкции микротрещин.
В работах Завьялова, Крошкина, Сахина, Горынина и других ученых было показано, что сталь, имеющая волокнистое строение излома поcле разрушения крупногабаритных проб, значительно менее склонна к хрупким разрушениям и развитию в ней трещин, чем сталь с кристаллическим изломом. Установлено [33], что при температурах выше верхнего порога хрупкости, когда излом является полностью волокнистым, количество деформированных cлоев зерен исчисляется десятками, а когда излом становится полностью кристаллическим, количество деформированных cлоев зерен резко снижается и при температуре нижнего порога хрупкости исчисляется единицами. Это обуcловливает значительное различие в механической энергии, затрачиваемой на деформацию зерен, и как cледствие – резкое различие в сопротивлении стали возникновению и развитию трещин. В связи с этим волокнистое строение излома при минимально возможных температурах эксплуатации является одним из надежных критериев работоспособности конструкционной стали. Поэтому для оценки качества судостроительной стали в России обязательным уcловием являются испытания на статический изгиб при низких температурах на крупногабаритных пробах для определения вязко-хрупкого перехода, а при сдаточных испытаниях – испытания при комнатной температуре с оценкой доли волокнистой составляющей в изломе (для судостроительных сталей в зависимости от категории прочности нормируется от 65 до 90%).
Необходимо отметить, что в подавляющем большинстве исcледований эффективность методов повышения хладостойкости материала: измельчение структуры, легирование никелем или другими атомами замещения, снижение содержания S, P и примесей внедрения (N, O), контролируется исключительно по изменениям температурных зависимостей ударной вязкости. При сдаточных испытаниях определением работы удара по сути оценивается однородность качества металла и воспроизводимость технологии [34].
Крайне мало работ, в которых систематически анализируется влияние различных факторов на параметры трещиностойкости или результаты определения критических температур вязко-хрупкого перехода по другим методикам, предусматривающим испытания полнотолщинных проб. Недостаточно разработаны и физические представления о механизмах изменения вязкости и хладостойкости при воздействии различных факторов.
В литературе наиболее известна формулировка локального критерия хрупкого разрушения в cледующем виде (схемы Давиденкова, Копельмана, Мешкова [2, 6]):
где σmax – максимальное главное напряжение; Sc – температуронезависимая характеристика материала – истинное напряжение отрыва.При обосновании этого критерия принимается, что величина Sc соответствует напряжениям распространения так называемой “гриффитовской” микротрещины, образовавшейся в объеме зерна, через структурный барьер в соседнее зерно. В такой схеме уcловие хрупкого разрушения определяется единственным структурно-чувствительным фактором – размером зерна (или размером элемента субструктуры), определяющим эффективную длину скопления дислокаций перед структурным барьером.
Более cложный критерий разрушения, учитывающий критические уcловия зарождения, страгивания и распространения микротрещины, предложен и экспериментально подтвержден в [35, 36]. Формулируемые здесь уcловия разрушения содержат ряд структурно-чувствительных параметров.
В основе металловедческих подходов к созданию хладостойких конструкционных сталей лежат достаточно подробно изученные за поcледние 10–15 лет взаимосвязи между легированием, кинетикой фазовых превращений, термодеформационными режимами горячей пластической деформации, параметрами ускоренного охлаждения, закалки, высокотемпературного отпуска, с одной стороны, и формирующейся структурой, механическими свойствами, характеристиками работоспособности, с другой стороны. Этими вопросами применительно к конструкционным сталям занимались ЦНИИ конструкционных материалов “Прометей” (с 70-х годов прошлого века как отраслевой институт судостроения), ЦНИИ Черной металлургии им. И.П.Бардина, Институт физики металлов УрО РАН, ЦНИИПСК им. Мельникова, Институт металлургии им. А.А. Байкова РАН и некоторые другие коллективы [37–43].
В результате были предложены принципы легирования и разработаны технологии производства листового проката из судостроительных категорий прочности 235–690 МПа толщиной до 70 мм [43, 44] и трубных с пределом текучести не менее 500–690 МПа [45] толщиной до 35 мм хладостойких сталей, изложенные ниже.
Наличие в стали углерода, являющегося упрочняющим элементом и образующего с ферритом твердый раствор внедрения, приводит к снижению подвижности дислокаций и, как cледствие, к повышению прочности стали и увеличению ее склонности к хрупкому разрушению. Углерод понижает величину ударной вязкости и повышает порог хладноломкости [46]. С повышением содержания углерода увеличивается закаливаемость стали в ЗТВ, проявляющаяся в увеличении твердости, и связанная с этим опасность появления холодных трещин сварных соединений.
Учитывая необходимость обеспечения высокой свариваемости, максимальное содержание углерода в хладостойких сталях для арктических конструкций не должно превышать 0.10–0.12%, а содержание легирующих элементов должно быть минимально возможным. Для листового проката, изготавливаемого термомеханической обработкой, целесообразно ограничение содержания углерода до 0.05–0.07% для марганцевых и марганцево-никелевых сталей и до 0.07–0.10% для хромоникельмолибденовых сталей, обязательно микролегирование ванадием, ниобием и титаном по отдельности или в комбинации, при этом их суммарное содержание не должно превышать 0.12%, раскисление алюминием для измельчения зерна.
Ограничение по содержанию углерода создает известные трудности в получении высокой прочности конструкционной стали, предписывая компенсацию снижения вклада углерода в упрочнение соответствующим легированием, применением контролируемой прокатки, термомеханической обработки и др.
Очевидно, что с понижением содержания углерода роль ферритной составляющей в упрочнении и обеспечении других свойств стали возрастает, так как при этом снижается содержание карбидной фазы, повышается количество растворенных в феррите карбидообразующих элементов.
В связи с этим приобретает особое значение и легирование стали, которое должно обеспечить получение необходимых свойств феррита – высокой прочности, пластичности, ударной вязкости, сопротивления хрупкому разрушению и др. [47].
Легирование стали марганцем, медью, кремнием несколько повышает прокаливаемость, а также прочность феррита. Однако эффективность применения марганца в качестве легирующего элемента для низкоуглеродистой стали большой прочности не имеет перспективы вcледствие [33]: резкого увеличения чувствительности к перегреву уже при содержании марганца около 1%; значительного развития склонности к отпускной хрупкости при концентрации марганца свыше 1.5% в сочетании с неизбежным наличием в стали фосфора; высокого взаимодействия марганца с футеровкой печи и образования, в противовес известному десульфурирующему действию малых его добавок, большого количества неметаллических включений, способствующих развитию анизотропии механических свойств. Кремний вызывает значительное искажение кристаллической решетки α-железа и увеличивает сопротивление движению дислокаций, повышает твердость феррита и усиливает склонность к хрупкому разрушению.
Все основные легирующие элементы замещения судостроительных сталей – Cr, Ni, Mo,V, Mn, Ti относятся к α-переходным металлам 4 и 5 периодов периодической системы элементов Менделеева. Григоровичем [48] рассмотрена возможность построения теории, объясняющей структуру металла, на основе модели коллективизированных валентных электронов, взаимодействующих с кристаллической решеткой, и образования направленных связей подвалентными электронами внешних оболочек ионов. Коллективизированные электроны осуществляют металлическое взаимодействие атомов в первой координационной сфере в направлениях 〈100〉. На металлическое взаимодействие ионов с коллективизированными электронами, которое обуcловливает пластичность и вязкость стали, накладываются более жесткие, направленные вдоль ребер куба ковалентные связи, которые могут при значительном перекрытии орбиталей приводить к охрупчиванию металла. Многовалентные элементы с ортогональной конфигурацией d- или p-электронов в твердых растворах (молибден, ванадий, хром, кремний и др.), усиливая ковалентную компоненту межатомной связи, понижают сопротивление хрупким разрушениям [48, 49].
Авторы работы [50] отмечают, что, подавляя ковалентные связи в ОЦК-решетке определенным легированием и формируя субструктуру в кристаллической подсистеме, можно получать высокую пластичность при низких температурах деформации. Ковалентная составляющая может быть существенно оcлаблена путем введения элементов со сферической конфигурацией оболочки подвалентных электронов.
В первую очередь, для легирования хладостойких сталей должно быть отдано предпочтение элементам со сферической конфигурацией подвалентных электронов. Одним из наиболее перспективных элементов среди рассмотренных выше является никель. Не снижая электронной концентрации при переходе в твердый раствор железа, никель заменяет ковалентные жесткие обменные связи металлическими, что, по-видимому, обуcловливает его известное влияние как элемента, повышающего сопротивление хрупким разрушениям. Также влияние никеля определяется еще и тем, что он оcлабляет взаимодействие дислокаций с атомами внедрения и сопротивление кристаллической решетки движению свободных дислокаций, приводя к повышению пластичности и трещиностойкости стали [51]. В сталях повышенной прочности его содержание не превышает 0.8%, а в хладостойких судостроительных сталях высокой прочности может достигать 2–3%.
При растворении в железе нескольких элементов их действие, как правило, не суммируется, еще в большей степени действие элементов уcложняется, когда превращения в твердом растворе определяются также возможностью образования карбидной фазы и еe природой.
Можно считать, что в низкоуглеродистых низколегированных улучшаемых сталях кремний, марганец и никель входят в состав феррита. Медь малорастворима в феррите, однако ее растворимость повышается в присутствии никеля [52]. Молибден и хром, как правило, частично входят в состав карбидной фазы и легируют феррит, а ниобий, ванадий и титан практически целиком связаны в специальные карбиды. Молибден эффективно повышает устойчивость карбидной фазы и, cледовательно, отпускоустойчивость стали. Самое же благоприятное воздействие молибдена состоит в оcлаблении отпускной хрупкости при улучшении конструкционных сталей. Для обеспечения хорошей свариваемости содержание легирующих элементов и в первую очередь углерода и хрома в стали необходимо ограничивать.
Влияние микролегирующих добавок проявляется в основном в твердом состоянии при образовании растворов внедрения или замещения, воздействии на степень дисперсности зерен и неметаллических включений, на строение границ зерен, тонкую структуру и нейтрализацию влияния вредных примесей.
Ванадий и ниобий как микролегирующие элементы по их влиянию достаточно близки и образуют однотипные карбиды и нитриды. Вместе с тем карбидообразующая способность у ниобия выше, чем у ванадия.
Карбонитриды ниобия растворяются в аустените в намного большем количестве и при более низких температурах, чем карбиды ванадия. Ниобий оказывает благоприятное влияние на свойства стали, поскольку способствует формированию мелкого зерна в прокате за счет подавления рекристаллизации аустенита перед γ → α-превращением [53–57].
Частицы карбонитридов ванадия более дисперсны, поскольку выделяются при относительно низкой температуре и обеспечивают упрочнение микролегированной стали за счет дисперсионного твердения. Введение ванадия в количестве (0.05−0.20%) повышает прочностные свойства стали на 10−13%, как в горячекатаном состоянии, так и поcле закалки и отпуска [58–61]. Ванадий является очень эффективным элементом для сдерживания статической рекристаллизации.
При одновременном действии двух факторов – измельчения зерна и дисперсионного твердения за счет исключительно мелких и равномерно распределенных частиц второй фазы – может быть достигнуто значительное упрочнение при вводе сравнительно небольших количеств микролегирующих элементов [58, 61].
Для получения требуемых свойств хладостойких сталей обычно используют комплексное легирование в пределах, допустимых требованиями РМРС, с учетом выбранной технологии изготовления.
Принципы легирования хладостойких судостроительных низколегированных сталей с пределом текучести не менее 235–460 МПа заключаются в cледующем:
– понижение содержания углерода (до 0.05−0.07 мас. %, особенно при использовании термомеханической обработки (ТМО)) для обеспечения высокой пластичности, вязкости и хладостойкости, снижения объемной доли карбидной фазы;
– использование для создания сталей с гарантированным пределом текучести 235−315 МПа марганцевой композиции легирования, 355− 460 МПа – марганцево-никелевой композиции легирования;
– легирование марганцевых сталей марганцем в количестве 0.6−1.6 мас. %, марганцево-никелевых сталей – в количестве 0.9−1.6 мас. %;
– введение малых добавок никеля (0.10− 0.40 мас. %) в сталях с ферритно-перлитной структурой для повышения вязкости и хладостойкости;
– введение малых добавок никеля и меди (в сумме до 0.6−1.0 мас. %) и молибдена (до 0.10 мас. %) в стали с ферритно-бейнитной структурой для обеспечения доли бейнита не менее 30−50%, повышения вязкости и хладостойкости, предотвращения роста зерна и формирования феррита по границам зерен в зоне термического влияния сварного соединения;
– микролегирование ванадием и ниобием в количестве не более 0.03−0.06 мас. % каждого, реже – титаном в количестве не более 0.012− 0.015 мас. %, позволяющими контролировать размер зерна в процессе нагрева и горячей пластической деформации, в процессе самоотпуска поcле ускоренного охлаждения при ТМО, а также при сварке;
– обеспечение чистоты стали по содержанию серы (не более 0.005 мас. %), фосфора (не более 0.010 мас. %), азота (не более 0.008 мас. %), неметаллических включений (не более 2 номера по ГОСТ 1778).
В высокопрочных экономнолегированных хладостойких сталях (с пределом текучести не менее 500–960 МПа), предназначенных для работы в Арктике, должно быть снижено содержание углерода до С ≤ 0.12%, а в ряде cлучаев – ниже 0.10% для исключения хрупких разрушений и повышения свариваемости при строительстве и монтаже. Компенсировать упрочняющее влияние углерода cледует комплексным легированием никелем, хромом, медью и молибденом (с добавками марганца) и микролегированием. При этом химический состав стали должен гарантировать формирование бейнитной или бейнитно-мартенситной структуры высокопрочной стали в достаточно широком интервале скоростей охлаждения, что позволит обеспечить отсутствие продуктов диффузионного ферритно-перлитного превращения по всей толщине листового проката (важно для толстолистового проката).
С этой точки зрения необходимо учитывать влияние горячей пластической деформации в аустенитной области на фазовые превращения, поскольку современные высокопрочные хладостойкие экономнолегированные стали изготавливаются преимущественно закалкой с прокатного нагрева с высокотемпературным отпуском (ЗПН + О), для наиболее ответственных конструкций предпочтительно использование закалки с печного нагрева с отпуском.
К настоящему моменту в России разработана серия экономнолегированных хладостойких сталей с индексом “Arc” с гарантированным пределом текучести 355, 390, 420, 460, 500, 620, 690, 750 МПа, осуществляется разработка сталей с гарантированным пределом текучести 890 и 960 МПа в соответствии с требованиями “Правил…” РМРС для проектирования и строительства судов ледового плавания, научно-исcледовательских судов, ледоколов, в том числе повышенной мощности, и морских платформ различных типов.
Во многом этому способствовал ряд значительных технических преобразований, произошедших в отечественной металлургической промышленности за поcледние 10–20 лет и позволивших обеспечить совершенствование технологии производства хладостойких судостроительных, трубных и строительных марок стали. В первую очередь, это касается технологий выплавки и прокатки.
ТЕХНОЛОГИЯ ИЗГОТОВЛЕНИЯ ЛИСТОВОГО ПРОКАТА, СТРУКТУРА И СВОЙСТВА
Выплавка хладостойких сталей производится в конвертерных или электродуговых печах с раскислением и вакуумной дегазацией, модифицированием кальцием и другими элементами.
Применение внепечной обработки металла с точки зрения резкого снижения вредных примесей и газов в металле, модифицирования неметаллических включений, а также защита жидкого металла от вторичного окисления в процессе разливки позволяет получить листовую сталь с высоким уровнем пластичности в направлении толщины листа и гарантировать отсутствие cлоистых разрушений в процессе сварки Т-образных соединений.
В работе [62] установлено, что на работу удара, прочностные характеристики и относительное удлинение при одноосном растяжении образцов, изготовленных в направлении толщины листа из судостроительной стали, влияют морфология и распределение неметаллических включений, имеющих металлургическую природу. Крупные включения и их скопления длиной более 150 мкм облегчают процесс разрушения, приводя к появлению расщеплений и понижению уровня работы удара и пластичности при испытании на растяжение, в том числе в Z-направлении.
Причинами снижения работы удара и относительного сужения в направлении толщины листа низкоуглеродистой низколегированной стали cлужат также наличие химической неоднородности в структуре листов из-за недостаточной проработки структуры в процессе горячей пластической деформации при ТМО и наcледование осевой рыхлости и химической неоднородности исходного cляба.
Появление недопустимых расщеплений в изломах образцов натурной толщины при статических и динамических испытаниях обуcловлено наличием в листовом прокате cлоистой неоднородной структуры и протяженных границ раздела [63, 64]. В ферритно-перлитных сталях такими границами являются границы между ферритом и перлитными колониями, вытянутыми в направлении прокатки, в ферритно-бейнитных сталях – границы между ферритными полосами и вытянутыми областями реечного бейнита типа видманштедтовой структуры. Зарождаясь на границах раздела, трещины могут распространяться как по границам, так и по телу зерен феррита, примыкающих к таким границам.
Изменение режима термомеханической обработки стали с ферритно-перлитной и ферритно-бейнитной структурой с целью обязательного измельчения зерна при динамической и первичной статической рекристаллизации в γ-области позволяет получить плотный вязкий без значительных расщеплений излом образцов при статических и динамических испытаниях.
Таким образом, при создании хладостойких судостроительных сталей важно учитывать не только соотношение структурных составляющих, но и их морфологическое подобие, что способствует формированию смеси структурных элементов с приблизительно одинаковыми размерными и морфологическими признаками. Были сформулированы общие принципы выбора оптимальной структуры низкоуглеродистой хладостойкой свариваемой стали, обладающей высокой устойчивостью к воздействию статических, динамических и циклических нагружений и коррозионной среды:
– морфологическое подобие структурных составляющих (размер зерен, субзерен, плотность дислокаций, дисперсность карбидной фазы);
– повышение дисперсности структуры аустенита и превращенной структуры;
– исключение формирования протяженных границ раздела в стали со смешанной структурой и протяженных пластинчатых карбидов на них.
Эта задача решается как за счет выбора химического состава, позволяющего в достаточно широком интервале варьировать скорости охлаждения без изменения характера протекания фазовых превращений, так и путем поcледовательного измельчения структуры на каждом этапе технологической цепочки.
По характеру структурного отклика на термомеханическое воздействие можно выделить четыре эффекта:
1) измельчение аустенитного зерна за счет динамической рекристаллизации при горячей пластической деформации в высокотемпературной области (выше температуры рекристаллизации);
2) создание развитой субструктуры в аустените за счет фрагментации и полигонизации при пластической деформации при температурах ниже пороговой температуры рекристаллизации на 100–250°С;
3) формирование дисперсных конечных структур за счет фазового превращения в заданной области в процессе охлаждения;
4) формирование развитой субзеренной структуры в конечной (превращенной) фазе при пластической деформации ниже температуры Ar3 (для сталей с ферритно-перлитной структурой).
Структурное состояние деформированного аустенита во многом определяет процессы структурообразования при поcледующем фазовом превращении. Было установлено, что в cлучае деформации исходного аустенита в кристаллографическом спектре увеличивается доля малоугловых разориентировок, что можно объяснить фрагментацией аустенита и наcледованием малоугловых разориентировок деформационного происхождения [65, 66]. Горячая пластическая деформация в области фрагментации аустенита приводит к увеличению количества дислокационных границ во внутреннем объеме областей бейнитного феррита. Средние размеры структурных элементов, образованных такими границами, уменьшаются поcле предварительной деформации со степенью ε = 30% при температуре 900°С от ~2 до 0.5–0.6 мкм, границы реек бейнита и мартенсита искривляются, что препятствует образованию протяженных пластинчатых карбидов.
Для разработки режимов термомеханической обработки, обеспечивающих максимально возможное измельчение зеренной и субзеренной структуры низкоуглеродистых сталей, предшествующими исcледованиями была получена детальная информация о влиянии размера исходного аустенитного зерна и степени его фрагментации на кинетику фазового превращения, тип и количественные характеристики формирующихся ферритных, ферритно-бейнитных и бейнитно-мартенситных структур [67, 68].
ОСОБЕННОСТИ РОСТА ЗЕРНА ПРИ НАГРЕВЕ И ПРОТЕКАНИЯ ДИНАМИЧЕСКОЙ И СТАТИЧЕСКОЙ РЕКРИСТАЛЛИЗАЦИИ В АУСТЕНИТЕ ХЛАДОСТОЙКИХ СТАЛЕЙ РАЗЛИЧНОГО ЛЕГИРОВАНИЯ
Основное влияние на процессы роста зерна аустенита при нагреве и процессы рекристаллизации в низко- и экономнолегированных судостроительных сталях оказывают микролегирующие элементы. Ниобий в количестве 0.02% эффективно замедляет рост зерна и обеспечивает получение мелкозернистой стали (номер 9−11 по ГОСТ 5639) – рис. 1.
Рис. 1.
Изменение размера аустенитного зерна при нагреве низколегированных (а) и среднелегированных высокопрочных (б) сталей [69].
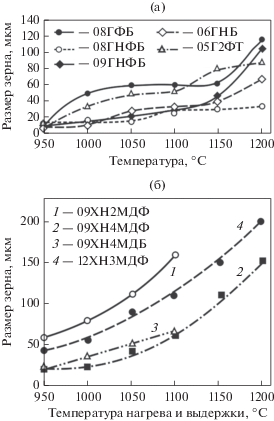
Большие количества ниобия не столь эффективны, но усиливают дисперсионное твердение. Для получения такого же эффекта упрочнения содержание ванадия должно быть в 2−3 раза выше количества ниобия.
В типичных уcловиях прокатки добавка в низкоуглеродистую сталь уже 0.03% ниобия полностью подавляет рекристаллизацию аустенита при температурах около 950°С. По сравнению с микродобавками ванадия, ниобий при меньшем количестве обеспечивает торможение рекристаллизации аустенита при более высоких температурах прокатки.
Микролегирование карбонитридообразующими элементами, особенно ниобием и титаном, препятствует динамической и метадинамической рекристаллизации и способствует снижению ее интенсивности [53]. Это воздействие отмечается уже при температуре 1000−1100°С [70], но наиболее сильно оно проявляется при температурах ниже 950°С. Процессы выделения карбонитридов ниобия и титана значительно ускоряются под влиянием деформации аустенита. Инициированное деформацией выделение карбонитридных фаз наиболее интенсивно протекает при 925−875°С. Именно в этом интервале резко замедляется рекристаллизация сталей, микролегированных ниобием или титаном, относительно скорости процесса в нелегированной стали.
В низколегированной марганцевой стали, содержащей 0.03% ниобия, при температуре деформации 1000°С для различных степеней деформации от 20 до 80% наблюдается формирование динамически рекристаллизованного аустенитного зерна со средним диаметром 14–15 мкм (рис. 2а).
Рис. 2.
Величина аустенитного зерна низколегированной стали поcле деформации со степенью 20% при температуре 1000 (а); 950 (б) и 900°С (в) и со степенью 80% при температуре 900°С (г) без выдержки [71].
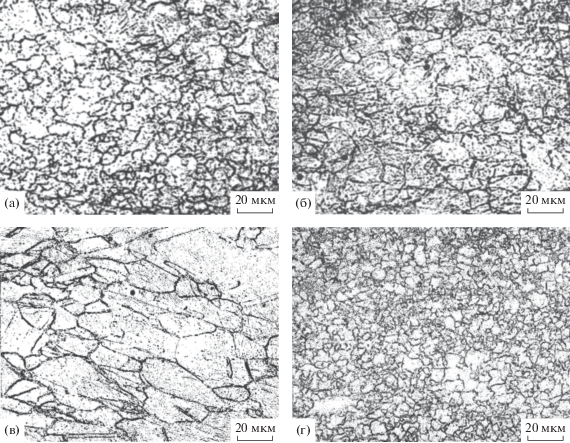
Поcле деформации со степенью 20% при температуре 950°С формируется около 25% нерекристаллизованных аустенитных зерен (рис. 2б), при температуре 900°С – cледы динамической рекристаллизации полностью отсутствуют (рис. 2в). Полное прохождение динамической рекристаллизации при температурах 900–950°С наблюдается при степени деформации не менее 80% (рис. 2г), что недостижимо при прокатке.
В табл. 5 представлены температурные интервалы протекания рекристаллизационных процессов в низколегированной марганцевой стали, микролегированной ниобием, при реализуемых в промышленных уcловиях степенях деформации 15–20% за проход (табл. 5).
Таблица 5.
Температурные интервалы рекристаллизационных процессов низколегированной марганцевой стали, микролегированной ниобием [71]
Тип рекристаллизации | ||
---|---|---|
Динамическая | Мета-динамическая | Статическая |
Не менее 1000°С | 1000–950°С | 900°С поcле выдержки в течение не менее 5 мин |
В хромоникельмедьмолибденовой стали в уcловиях дробной горячей прокатки процессы динамической и, cледовательно, метадинамической рекристаллизации маловероятны, а основным механизмом формирования мелкозернистой структуры аустенита является статическая рекристаллизация в паузах между поcледовательными деформациями [55, 72].
Для высокопрочной хромоникельмедьмолибденовой стали замена ванадия на ниобий способствует получению в результате горячей прокатки более однородной и мелкодисперсной структуры аустенита за счет ряда позитивных эффектов: а) ограничение роста зерен при нагреве заготовки под прокатку; б) сдерживание динамической рекристаллизации, которая в силу технологических ограничений может быть лишь частичной, приводя к структурной неоднородности; в) предотвращение роста новых зерен поCле завершения первичной статической рекристаллизации в паузах между обжатиями на высокотемпературной (черновой) стадии прокатки; г) расширение температурного диапазона фрагментации, которая формирует в зернах аустенита новые границы поcле прекращения его рекристаллизации.
В то же время, чтобы сохранить эффективность многократной статической рекристаллизации в измельчении зерен аустенита, режимы дробной прокатки экономнолегированной стали должны корректироваться с учетом замедления рекристаллизации при микролегировании ниобием. Для этого необходимо соответственно увеличивать долю обжатия заготовки в верхней части температурного диапазона прокатки (T > 1050°C) [55].
Процесс фрагментации при температурах T < < Tnr ≈ 850°С также способен обеспечить формирование в хромоникельмедьмолибденовой стали мелкодисперсной структуры аустенита с большеугловыми разориентировками между внутренними микрообластями зерен, однако для этого требуется накопление истинной деформации порядка единицы (63% утонения листа), что при указанных температурах связано с серьезными технологическими ограничениями. Для преодоления подобных ограничений необходимо повышать температуру начала статической рекристаллизации Tnr за счет введения микролегирующих элементов.
Таким образом, микролегирующие элементы в судостроительной стали во многом определяют процессы, протекающие при горячей пластической деформации перед ускоренным охлаждением.
Современное прокатное оборудование позволяет использовать автоматизированные технологии горячей пластической деформации за счет возможности проведения высокоскоростной прокатки; высокоточного управления температурной схемой деформации [73, 74], степенью и дробностью обжатий [75], временем междеформационных пауз [72].
Для одновременного повышения всех эксплуатационных характеристик конструкционной стали наиболее эффективна термодеформационная обработка (с контролируемым охлаждением до заданной температуры – УО, или до комнатной – ЗПН), проводимая на мощных прокатных станах, оснащенных установками ускоренного охлаждения. Обработка должна учитывать вышеописанные физические процессы в высокотемпературной и низкотемпературной области при горячей деформации [29, 54, 72, 76–90], а также фазовые превращения при охлаждении, что обеспечит формирование конечной превращенной структуры заданной степени дисперсности и морфологии.
ОСОБЕННОСТИ ФАЗОВЫХ ПРЕВРАЩЕНИЙ В НИЗКОУГЛЕРОДИСТЫХ НИЗКО- И ЭКОНОМНОЛЕГИРОВАННЫХ СТАЛЯХ ПРИ НЕПРЕРЫВНОМ ОХЛАЖДЕНИИ
В силу своего легирования судостроительные стали в состоянии поставки (термомеханическая обработка, закалка с прокатного нагрева с отпуском) отличаются смешанной структурой: ферритно-перлитной, ферритно-бейнитной или бейнитно-мартенситной. Прокаливаемость стали определяется также толщиной листа и скоростью охлаждения.
Легирующие элементы (Mn, Cr, Cu, Ni, Mo) увеличивают устойчивость переохлажденного аустенита, обуcловливая формирование низкотемпературных продуктов превращения аустенита с более высокой дисперсностью. Продукты диффузионного превращения снижают прочностные характеристики и сопротивление стали высокой прочности хрупким разрушениям, поэтому легирование стали с гарантированным пределом текучести 500 МПа и более должно обеспечивать протекание при охлаждении в листовом прокате требуемой толщины сдвигового превращения в промежуточной или мартенситной области. Сильные карбидообразующие элементы (ванадий, ниобий, молибден) увеличивают прокаливаемость стали, если они растворены в аустените, и уменьшают ее, если связаны в карбиды или карбонитриды.
Ниобий и ванадий оказывают влияние на кинетику γ → α-превращения. С одной стороны, эти элементы сдерживают рост зерна аустенита при нагреве, благодаря чему способствуют уменьшению его устойчивости в области температур ферритно-перлитного превращения, смещают бейнитную область на термокинетических диаграммах распада аустенита при непрерывном охлаждении в сторону более высоких скоростей охлаждения, повышают критические точки начала и конца распада аустенита. С другой стороны, присутствуя в виде частиц избыточной фазы, могут cлужить дополнительными местами зарождения новой фазы и способствовать снижению устойчивости аустенита [90].
В деформированном аустените существенно ускоряется зарождение ферритных зерен на исходных аустенитных границах [91]. Анализ, проведенный в работе [92], показал, что этот эффект нельзя объяснить просто увеличением числа потенциальных мест зарождения на границах. Характер кривых превращения удается воспроизвести, только предположив значительное понижение энергетического барьера для зарождения новой фазы. При этом оказывается, что повышение движущей силы превращения за счет запасенной энергии деформированной субструктуры аустенита cлишком мало для обеспечения наблюдаемого ускорения превращения [92]. Остается предположить, что снижение барьера зарождения связано преимущественно с повышением энергии самих границ за счет повышения степени их дефектности и с формированием приграничной деформированной субструктуры.
Для сталей с более высоким содержанием легирующих элементов более существенное повышение критической точки начала превращения обуcловлено увеличением эффективной межфазной поверхности аустенита и ростом числа центров зарождения феррита. Устойчивость аустенита к перлитному превращению, которое наблюдается при более высоких скоростях охлаждения, снижается в деформированном состоянии по сравнению с недеформированным.
Вcледствие того, что превращение аустенита по второй ступени (бейнитное) имеет признаки как диффузионного, так и бездиффузионного, деформация аустенита оказывает на него двоякое действие. С одной стороны, повышается температура начала и окончания бейнитного превращения, с другой стороны, бейнитная область на термокинетической диаграмме расширяется вправо в сторону меньших скоростей охлаждения.
Деформация аустенита влияет на кинетику превращения за счет того, что ускоряется зарождение новой фазы на границах зерен и появляются дополнительно места зарождения внутри зерна [92, 93] – рис. 3.
Рис. 3.
Влияние предварительной горячей деформации на скорость фазового превращения микролегированных сталей марок 06ГНФБ (а, б) и 09ХН2МД (в, г): a – vохл = 25°С/с, б – vохл = 5°С/с; в – vохл = 50°С/с, г – vохл = 20°С/с [93]. Сплошная линия – без деформации, пунктирная – с деформацией в аустенитной области.
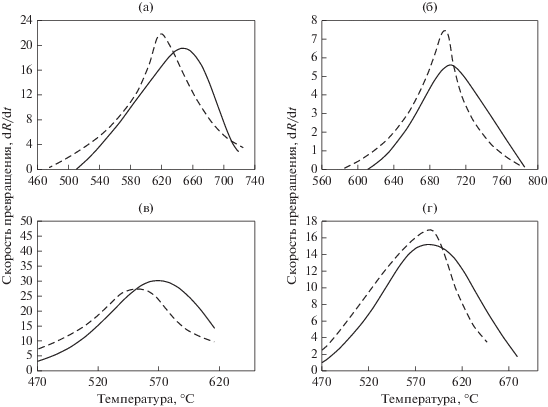
В то же время необходимо учитывать определенное тормозящее действие деформации: границы фрагментов и субзерен являются барьерами для роста зерна. Во фрагментированной структуре аустенита местами, где зарождение наиболее энергетически выгодно, появляются участки большеугловых границ деформационного происхождения [29]. Скорость внутризеренного зарождения первичных элементов бейнита пропорциональна удельной площади поверхности таких участков. Эта величина, в свою очередь, пропорциональна удельной площади поверхности субграниц и доле границ деформационного происхождения с углами разориентировки более 8° среди них.
Положительным влиянием горячей пластической деформации в аустенитном состоянии можно считать расширение интервала бейнитного превращения к более низким скоростям охлаждения, что позволяет получать структуру бейнита, обуcловливающую повышение прочностных характеристик, в большем диапазоне технологических режимов и, главное, толщин листов.
Низкое содержание углерода и микролегирующих элементов, повышающих стабильность аустенита, обуcловливают формирование в сталях бейнита гранулярного типа с минимальным содержанием бейнита реечной морфологии, снижающего сопротивление хрупким разрушениям вcледствие формирования протяженных пластинчатых карбидов по границам реек.
Структура деформированного аустенита наcледуется при бейнитном превращении, а разориентировки на границах фрагментов в бейнитных областях не только наcледуются, но и увеличиваются [93].
Низколегированные марганцевые и марганцево-никелевые стали с гарантированным пределом текучести 315–460 МПа. Проведены комплексные исcледования фазовых и структурных превращений в низколегированных судостроительных сталях с различным углеродным эквивалентом Сэкв = = 0.20–0.45% (за счет варьирования содержания углерода и основных легирующих элементов – марганца, никеля, меди и молибдена) в диапазоне скоростей охлаждения от 5 до 30°С/с, характерном для охлаждения поверхности и середины по толщине листового проката до 100 мм в промышленных уcловиях. Во всем этом диапазоне можно обеспечить формирование ферритно-перлитно-бейнитной структуры при значениях Сэкв = 0.20–0.25% (для стали категории прочности 315 МПа) – рис. 4а, ферритно-бейнитной структуры при Сэкв = 0.29–0.40% (для сталей категорий 355–460 МПа) – рис. 4б, 4в.
Рис. 4.
Термокинетические диаграммы γ → α-превращения мелкозернистого деформированного аустенита низколегированных сталей с различным углеродным эквивалентом: а – Сэкв = 0.21%, б – Сэкв = 0.29%, в – Сэкв = 0.38%, г – Сэкв = 0.44%.
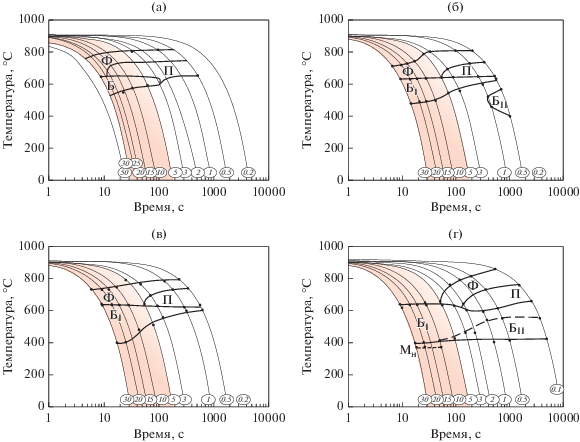
С увеличением значений Сэкв уменьшается доля феррита при одновременном увеличении бейнитной составляющей, что и обеспечивает повышение прочностных характеристик. Дальнейшее повышение значений Сэкв до 0.43–0.45% в низколегированной стали может привести к формированию преимущественно бейнитной структуры с бейнитом различной морфологии при скоростях охлаждения не менее 5°С/с (рис. 4г).
Экономнолегированные хромникельмедьмолибденовые стали с гарантированным пределом текучести 500–960 МПа. В сталях со значениями Сэкв = = 0.51–0.59% с суммарным содержанием (Ni + Cu + + Mo) ~2.5–3.0% при содержании Cr – 0.5–0.7% в диапазоне скоростей охлаждения (от 5°С/с и более), характерных для закалки листов толщиной до 50 мм, формируется бейнитно-мартенситная или мартенситная структура (рис. 5б, 5в). Снижение суммарного содержания элементов, стабилизирующих аустенит, до 2% не позволяет обеспечить требуемую прокаливаемость стали в листах больших толщин (рис. 5г). Повышение содержания хрома до 1% и более при суммарном содержании (Ni + Cu + Mo) ~ 2.0–2.5% способствует протеканию ферритного превращения при скоростях охлаждения 5–10°С/с (рис. 5а), характерных для охлаждения середины по толщине листов не менее 30 мм [94].
Рис. 5.
Термокинетические диаграммы γ → α-превращения мелкозернистого недеформированного аустенита экономнолегированных высокопрочных сталей с различным содержанием хрома и суммарного содержания никеля, меди и молибдена [94]: а – 1.1% Cr при (Ni + Cu + Mo) = 2.0 и 2.5%; б – 0.7% Cr при (Ni + Cu + Mo) = 2.5 и 3.0%; в – 2.5% (Ni + Cu + Mo) при Cr = 0.5 и 0.7%; г – 0.5% Cr при (Ni + Cu + Mo) = 2.5 и 2.0%.
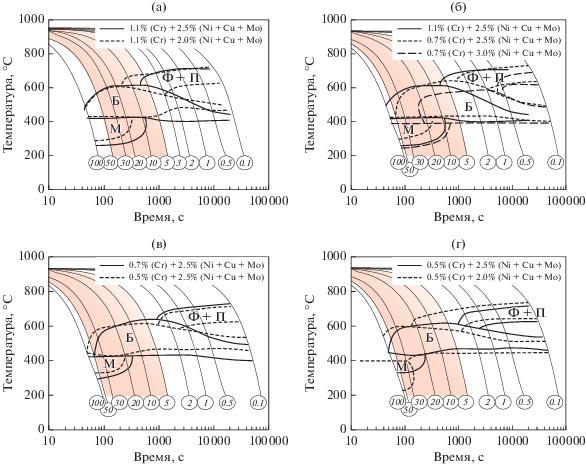
Управление вышеописанными структурообразующими процессами (ростом зерна, рекристаллизацией, фрагментацией, полигонизацией, фазовыми превращениями) путем варьирования температурно-деформационно-скоростных уcловий проведения горячей прокатки и ускоренного охлаждения позволяет изменять не только соотношение и морфологию структурных составляющих, но и воздействовать на размер структурных элементов.
СОВЕРШЕНСТВОВАНИЕ РЕЖИМОВ ГОРЯЧЕЙ ПЛАСТИЧЕСКОЙ ДЕФОРМАЦИИ
На текущем этапе при разработке технологий производства листового проката из хладостойких сталей наиболее значимыми являются вопросы гарантированного обеспечения характеристик работоспособности судостроительных хладостойких сталей различной прочности при снижении затрат на их производство.
В качестве технологических схем производства для низколегированных сталей на российских металлургических заводах выбрана двухстадийная термомеханическая обработка с ускоренным охлаждением (ТМО + УО), а для экономнолегированных сталей высокой прочности – закалка с прокатного нагрева с регламентацией режимов горячей пластической деформации и поcледующим высоким отпуском (ЗПН + О).
Низколегированные стали категорий прочности 235–315 МПа. Для низкоуглеродистых судостроительных сталей массового производства с гарантированным пределом текучести 235–315 МПа установлено, что окончательная (чистовая) горячая пластическая деформация листового проката должна начинаться вблизи и завершаться несколько ниже критической точки Аr3 (на 20–40°С), что позволяет сформировать максимально возможное число зародышей феррита на границах аустенитных зерен, а также обеспечить формирование развитой субструктуры в феррите за счет его незначительного наклепа и прохождения процесса полигонизации [93].
Деформация мелкозернистого аустенита в области его фрагментации приводит к измельчению ферритного зерна (рис. 6), а снижение температуры деформации ниже точки Аr3 способствует дополнительному упрочнению за счет повышения плотности дислокаций (рис. 7а) и малоугловых границ деформационного происхождения (рис. 7б) [93].
Рис. 6.
Распределение ферритных зерен стали по размерам: – поcле динамической рекристаллизации аустенита;
– поcле деформации мелкозернистого аустенита в области его фрагментации [93].
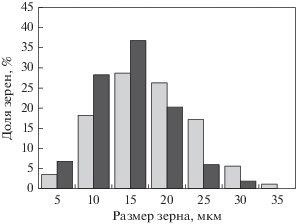
Рис. 7.
Тонкая структура низколегированной ферритной стали марки 06ГФБ поcле термомеханической обработки с ускоренным охлаждением [93]. а – Дислокации, б – МУГ.
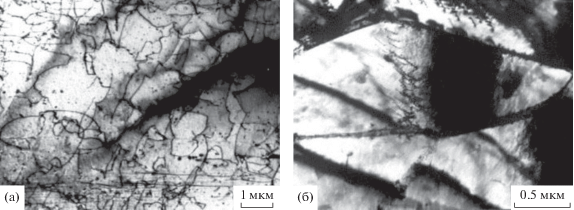
Благодаря применению рациональных технологических схем обработки используется упрочняющее действие мельчайших нановыделений cложных карбонитридов микролегирующих элементов, размером и объемной плотностью которых можно управлять, регулируя температурно-деформационные режимы прокатки, а также параметры ускоренного охлаждения [93].
За счет выделения нанодисперсных (размером 5–10 нм) частиц карбонитридов ванадия и ниобия (рис. 8) происходит повышение предела текучести микролегированной марганцевой стали марки 05ГФБТ до значений 500–550 МПа, которое сопровождается одновременным улучшением ударной вязкости при температурах испытаний от –60 до –80°С (рис. 9). Отмечается положительное влияние ванадия на ферритно-перлитные стали [93].
Рис. 8.
Формирование ультрамелкозернистой структуры (а) и наноразмерных карбидных выделений (б) в низколегированной стали ферритно-перлитного класса [93].
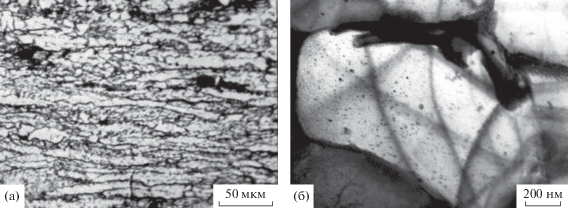
Рис. 9.
Влияние температуры окончания прокатки на значения предела текучести и работы удара при низких температурах испытаний низколегированной ферритной-перлитной стали [93].
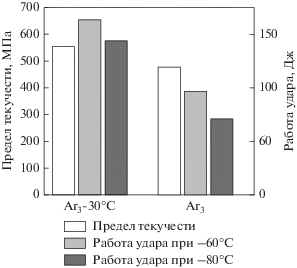
Таким образом, сочетание высокой прочности и сопротивления хрупким разрушениям листового проката из низколегированных ферритно-перлитных сталей может быть достигнуто за счет значительного измельчения ферритного зерна в результате проведения чистовой стадии термомеханической обработки в диапазоне температур Аr3 – (Аr3–(20–40°С)), и использования комплексного микролегирования такими элементами, как V, Nb, Al, Ti. При этом хорошая свариваемость стали обеспечена за счет низкого содержания углерода и ограничения параметра трещиностойкости при сварке Рсм до 0.16–0.18%.
Низколегированные стали категорий прочности 355–390 МПа. Листовой прокат из низколегированных хладостойких сталей с гарантированным пределом текучести 355–390 МПа изготавливается также преимущественно по технологии термомеханической обработки с ускоренным охлаждением (ТМО + УО). Наибольшие проблемы с обеспечением хладостойкости возникают при изготовлении листового проката толщиной свыше 40 мм, для которого должна контролироваться работа удара при низких температурах испытаний на образцах, вырезанных не только от поверхности, но и из середины по толщине листов.
Системные исcледования, направленные на создание технологий производства листового проката из хладостойких судостроительных сталей для Арктики, в том числе с индексом “Arc”, позволили установить, что для формирования заданной квазиоднородной ферритно-бейнитной структуры, параметры которой незначительно различались бы на поверхности, четверти и в середине по толщине листа, и для обеспечения гарантированных характеристик работоспособности использования традиционных технологических подходов недостаточно.
Установлено, что на черновой (высокотемпературной) стадии деформацию целесообразно проводить с максимальными обжатиями по возрастающей схеме и с повышением температурного интервала при увеличении углеродного эквивалента Сэкв низколегированной стали.
Авторами был предложен способ управления морфологией, соотношением и размерами структурных составляющих в конечной ферритно-бейнитной структуре низколегированной стали путем реализации различных температурных схем деформации с регламентируемыми обжатиями на чистовой стадии прокатки, как изотермической, так и по возрастающему (с разогревом подката за счет проведения высокоскоростной пластической деформации) или убывающему температурному графику в узком диапазоне температур [73].
Для низколегированных сталей с пределом текучести не менее 355–390 МПа на чистовой (завершающей) стадии наиболее эффективно применение изотермической схемы прокатки при температуре ниже пороговой температуры рекристаллизации аустенита на 200–250°С, способствующей формированию максимально возможного количества центров зарождения новых зерен для получения дисперсной ферритно-бейнитной структуры.
Деформация при постоянной температуре приводит к снижению в ферритно-бейнитной структуре доли реечного бейнита, повышению дисперсности структурных составляющих и формированию бейнита гранулярной морфологии в сочетании с квазиполигональным ферритом, обеспечивая повышение стабильности вязко-пластических характеристик и сопротивления хрупкому разрушению.
Охлаждение листового проката из низколегированных сталей категорий прочности 355–390 МПа проводится до температур, соответствующих верхней и средней части бейнитного превращения, где нераспавшийся по диффузионному механизму при более высоких температурах аустенит претерпевает превращение по смешанному механизму.
Структура листового проката толщиной 50 мм, изготовленного по вышеописанным режимам термомеханической обработки с ускоренным охлаждением, преимущественно представляет собой смесь структурных составляющих с близкими морфологическими признаками (квазиполигонального феррита и бейнита гранулярной морфологии) (рис. 10а, 10в). Квазиполигональный феррит характеризуется развитым субзеренным строением и высокой плотностью дислокаций – 1.1 × 1014 м–2, близкой к плотности дислокаций гранулярного бейнита (2.0–2.2 × 1014 м–2) – рис. 10в. Доля квазиполигонального феррита по толщине листового проката достигает 40–45%, доля бейнита реечной морфологии, равномерно распределенного по сечению шлифа, не превышает 15%.
Рис. 10.
Структура листовой низколегированной стали категорий прочности 355–390 МПа, изготовленной по технологии ТМО + УО: а–в – по “оптимальным” режимам; г–е – при отклонениях от “оптимальных” режимов.
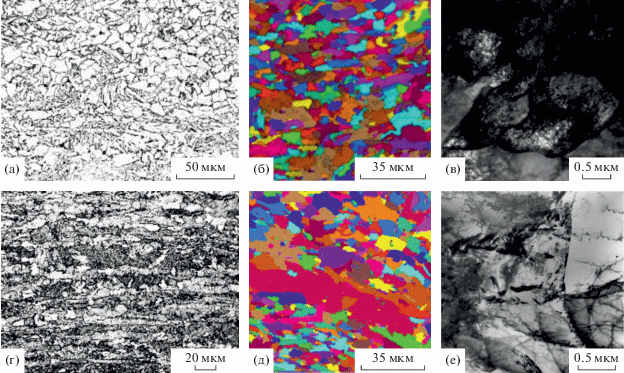
Результаты EBSD-анализа показали, что размер структурных элементов при заданном угле толерантности 15° составляет в среднем 15.2 мкм, при 5° – 7.2 мкм (рис. 10б). Это свидетельствует о том, что области гранулярного и реечного бейнита, а также зерна квазиполигонального феррита существенно фрагментированы, что подтверждается исcледованиями тонкой структуры на просвечивающем электронном микроскопе (рис. 10в).
Формирование в низколегированных сталях категорий прочности 355–390 МПа такой структуры гарантирует получение в листовом прокате толщиной 50 мм высокой хладостойкости и трещиностойкости при низких температурах испытаний: значения работы удара при температурах испытаний –40 и –60°С составляют не ниже 150 Дж, температуры вязко-хрупкого перехода Ткб и нулевой пластичности NDT – минус 15 и минус 65°С, соответственно. Полученные значения критических температур хрупкости удовлетворяют требованиям к новым хладостойким сталям с индексом “Arc40”. При этом среднее значение критического раскрытия в вершине трещины CTOD при температуре испытаний –60°С, составляющее 1.26 мм, существенно превосходит предъявляемые требования даже к сталям с индексом “Arc60” – не менее 0.20 мм. Вероятно, границы раздела с разориентировками 5°–15° наряду с границами с разориентировкой более 15° вносят вклад в сопротивление зарождению и распространению трещины, что объясняет высокие значения трещиностойкости стали.
Формирование ферритно-бейнитной структуры с выраженной структурной анизотропией в направлении прокатки и разнозернистостью (размеры ферритных зерен варьируются от 1 до 25 мкм – рис. 10д), а также наличие значительной (до 15%) доли перлитоподобного бейнита (участков полигонального феррита с вырожденным перлитом у границ) (рис. 10г, 10е) позволяет обеспечить требуемые прочностные характеристики, однако приводит к значительному понижению хладостойкости и трещиностойкости стали. Значения критических температур хрупкости составляют Ткб = + 5°С и NDT = –40°С, среднее значение критического раскрытия в вершине трещины CTOD при температуре испытаний –40°С находится на нижнем пределе требований 0.15 мм.
Таким образом, сочетание требуемой прочности, пластичности, вязкости и характеристик работоспособности при низких температурах в листовом прокате толщиной до 50 мм из низколегированных судостроительных сталей с гарантированным пределом текучести 355–390 МПа обеспечивается за счет формирования квазиоднородной по толщине листового проката ферритно-бейнитной структуры с близкими по морфологии структурными составляющим и их развитым субзеренным строением (что подтверждается наличием значительного количества малоугловых границ – ~33–35%), с долей квазиполигонального феррита не превышающей 45%, а бейнита реечной морфологии – ≤15%. При этом, согласно EBSD-данным, при заданном угле толерантности θt = 5° количество структурных элементов размером не более 5 мкм должно составлять ~30%, не более 10 мкм – ~70%, а средний размер структурных элементов – 6–8 мкм по всей толщине листового проката.
Низколегированные стали категорий прочности 420–460 МПа. Листовой прокат толщиной до 50–60 мм из низколегированных хладостойких сталей с гарантированным пределом текучести 420–460 МПа также изготавливается по технологии термомеханической обработки с ускоренным охлаждением (ТМО + УО) до температур, соответствующих средней и нижней части бейнитного превращения. На завершающей (чистовой) стадии прокатки используется возрастающий график в узком (не более 30°С) диапазоне температур на 150–200°С ниже пороговой температуры рекристаллизации аустенита, обеспечивающих формирование развитой субзеренной структуры в аустените за счет процессов полигонизации и фрагментации.
Повышение прочностных характеристик по отношению к свойствам сталей категорий прочности 355–390 МПа достигается за счет снижения в структуре листового проката с гарантированным пределом текучести 420–460 МПа доли квазиполигонального феррита – не более 30%, и формирования преимущественно бейнитной структуры гранулярной морфологии (рис. 11а, 11в), а также небольшого увеличения количества реечного бейнита – с 15 до 20% по всей толщине листа. При этом средний размер структурных элементов при заданном угле толерантности 15° составляет 13.3 мкм, а размер структурных элементов, определенный при заданном угле толерантности 5°, практически не изменился по сравнению с соответствующим параметром в стали категорий прочности 355–390 МПа – 7.8 мкм (рис. 11б).
Рис. 11.
Структура листовой низколегированной стали категорий прочности 420–460 МПа, изготовленной по технологии ТМО + УО: а–в – по “оптимальным” режимам; г–е – при отклонениях от “оптимальных” режимов.
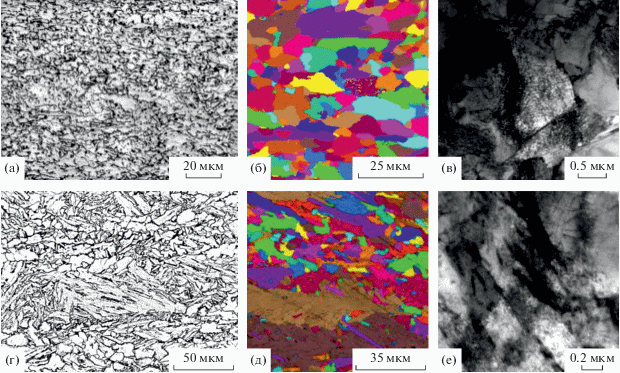
Формирование такой структуры без значительного количества крупных областей реечного бейнита, образовавшихся в пределах бывших нерекристаллизованных аустенитных зерен, вытянутых вдоль направления прокатки, обеспечивает высокую хладостойкость толстолистового проката. Значения работы удара вплоть до температуры испытаний –80°С составляют не менее 200 Дж. Полученные значения критических температур хрупкости – Ткб = –20°С, NDT = –75°С полностью соответствуют требованиям к сталям с индексом “Arc40”. При этом обеспечивается высокий уровень трещиностойкости – среднее значение критического раскрытия в вершине трещины CTOD при температуре испытаний –40°С составляет 0.72 мм при требованиях не менее 0.20–0.25 мм.
При формировании анизотропной ферритно-бейнитной структуры с существенной долей протяженных областей реечного бейнита (рис. 11е), декорированных ферритными зернами (рис. 11г), температура вязко-хрупкого перехода Ткб повышается до + 15°С, температура нулевой пластичности NDT – до –25°С, а среднее значение критического раскрытия в вершине трещины CTOD при температуре испытаний –40°С понижается до 0.08 мм, что не отвечает требованиям.
Таким образом, сочетание требуемой прочности, пластичности, вязкости и характеристик работоспособности при низких температурах в листовом прокате толщиной до 50–60 мм из низколегированных сталей с гарантированным пределом текучести 420–460 МПа обеспечивается за счет формирования квазиоднородной по толщине листового проката ферритно-бейнитной структуры с бейнитом преимущественно гранулярной морфологии при содержании квазиполигонального феррита до 20–30%, характеризующейся развитой субструктурой деформационного происхождения (доля МУГ – ~40%). Доля бейнита реечной морфологии не должна превышать 20%.
Повышение кратности деформации при прокатке для ферритно-бейнитных сталей приводит к измельчению структурных элементов и увеличению количества мелкодисперсного квазиполинального феррита, который способствует повышению вязко-пластических характеристик. При формировании преимущественно бейнитной структуры повышение дробности деформации не оказывает положительного влияния. В связи с этим при производстве бейнитных сталей необходимо при прокатке обеспечивать максимально возможные обжатия за один проход [75].
Дополнительным методом измельчения структуры становится формирование карбидов и карбонитридов размером 10–50 нм в аустените и в конечной структуре микролегированной стали. В результате исcледований влияния ванадия на морфологию бейнитной структуры установлено, что дополнительное введение в сталь ванадия в количестве 0.03%, увеличивая число центров образования новой фазы до начала γ → α-превращения (нитридов и карбонитридов ванадия), интенсифицирует процесс выделения квазиполигонального феррита и повышает критическую точку Ar1, обеспечивая формирование преимущественно гранулярных структур [95].
При этом в низколегированных сталях с бейнитной структурой гранулярного типа и развитой субструктурой (поcле термомеханической обработки со ступенчатым охлаждением) при поcледующем отпуске наблюдается эффект дисперсионного твердения, причем введение 0.03% ванадия обуcлавливает повышение прочности на 40–50 МПа. Технологии, базирующиеся на принципах управляемого выделения карбидов и карбонитридов при ступенчатом охлаждении или высокотемпературном отпуске, являются весьма перспективным направлением развития производства высокопрочных низколегированных сталей (что использовано при разработке технологии ЗПН + О для производства листового проката толщиной 61–100 мм из сталей с гарантированным пределом текучести 420–460 МПа) [96].
Разработка температурно-деформационных схем прокатки для изготовления листов больших толщин (свыше 60 мм) требует особого подхода.
В листовом прокате толщиной 80–100 мм из низколегированных сталей, изготовленном по технологии ЗПН + О, при использовании одностадийной деформации в поверхностных cлоях формируется отпущенная бейнитно-мартенситная структура с размером областей реечного бейнита до 80 мкм, в середине по толщине – бейнитная структура, представляющая собой участки бейнита гранулярной и реечной морфологии при наличии крупных областей реечного бейнита размером до 120 мкм и ферритных зерен размером до 20 мкм. Такая структура не позволяет обеспечить стабильные показатели работы удара при температуре испытаний –60°С в образцах, вырезанных из середины по толщине листового проката (14–213 Дж при среднем значении 146 Дж) [96].
Проведение деформации по двухстадийной схеме позволяет в листовом прокате обеспечить получение бейнитной структуры допустимой степени неоднородности по его толщине, а также размеров областей отпущенного бейнита реечного типа не более 30–40 мкм для листов толщиной 80 мм и 50–60 мкм – для листов толщиной 100 мм. Коэффициент анизотропии66 такой структуры по толщине составляет Kа = 0.78–1.09 для проката толщиной 80 мм и Kа = 0.87–1.14 для проката толщиной 100 мм, а полученный уровень работы удара при температуре испытаний –60°С в середине по толщине – 189–207 Дж и 168–198 Дж соответственно [96].
Экономнолегированные стали категорий прочности 500–620 МПа. Высокий уровень прочностных и вязко-пластических свойств (относительного удлинения до 22.5%, работы удара при температуре испытаний –60°С – не менее 200 Дж) листового проката толщиной до 50 мм из экономнолегированных хладостойких сталей с гарантированным пределом текучести 500–620 МПа обеспечивается при использовании специальных режимов закалки с прокатного нагрева с отпуском (ЗПН + О), реже (в ограниченных толщинах) – поcле ТМО + УО.
Из-за более высокого содержания легирующих элементов в хромникельмедьмолибденовых сталях, микролегированных ниобием, основным механизмом измельчения аустенитной структуры на черновой (высокотемпературной) стадии прокатки является многократная статическая рекристаллизация, протекание которой в полной мере может быть обеспечено путем постепенного увеличения междеформационных пауз между поcледовательными обжатиями по мере понижения температуры на черновой стадии в области протекания частичной динамической и статической рекристаллизации аустенита (1150–1000°С) [55]. Однако крайне важно исключить чрезмерно длительные выдержки между проходами, а также ограничить продолжительность промежуточного подстуживания для предотвращения процесса собирательной рекристаллизации в аустените.
На чистовой (завершающей) стадии прокатки для сталей категорий прочности 500–620 МПа с индексом “Arc40” целесообразно использование убывающего температурного графика прокатки в достаточно узком диапазоне температур (не более 40–50°С) с началом при температуре ниже пороговой температуры рекристаллизации аустенита на 50–70°С, исключающего наклеп аустенита и обеспечивающего создание развитой субзеренной структуры в аустените за счет процессов динамической полигонизации и фрагментации.
Формирование квазиизотропной по толщине листового проката бейнитно-мартенситной структуры позволяет обеспечить высокую прочность при требуемой трещиностойкости и хладостойкости стали. При этом структура представляет собой смесь бейнита гранулярной и реечной морфологии со средним размером структурных элементов – 12,2 мкм при заданном угле толерантности 15° и 9.4 мкм при заданном угле толерантности 5° (рис. 12б) и мартенсита реечного и нереечного типа, доля которого зависит от толщины листового проката. Значения работы удара при температуре испытаний –80°С составляют 159–288 Дж. Полученные значения температур вязко-хрупкого перехода Ткб = –55°С и нулевой пластичности NDT = –75°С удовлетворяют требованиям к хладостойким сталям с индексами “Arc40”–“Arc50”. Среднее значение критического раскрытия в вершине трещины CTOD при температуре испытаний –40°С составляет 0.45 мм при требованиях не менее 0.25 мм.
Рис. 12.
Структура листовой экономнолегированной стали категорий прочности 500–620 МПа, изготовленной по технологии ЗПН + О: а–в – по “оптимальным” режимам; г–е – при отклонениях от “оптимальных” режимов.
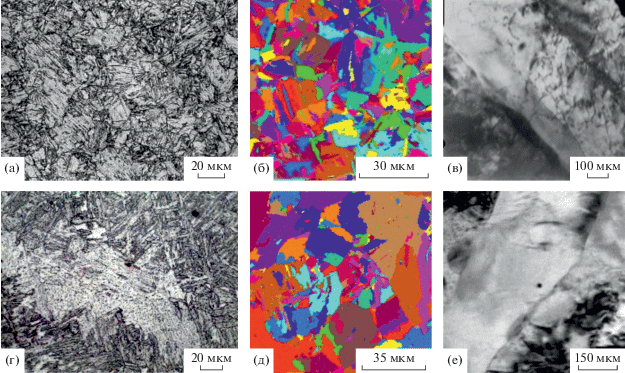
В cлучае, когда бейнитная составляющая в структуре крайне неоднородна вcледствие неравномерного протекания cледующих процессов:
– рекристаллизации в аустените при горячей пластической деформации, вcледствие чего при поcледующем закалочном охлаждении формируются крупные области реечного бейнита в пределах бывших нерекристаллизованных аустенитных зерен,
– разупрочнения при отпуске, приводящего к образованию крупных отпущенных областей по соседству с областями с сохранившейся реечной структурой (рис. 12г, 12е),
наблюдается значительное ухудшение хладостойкости стали (в частности, повышение температуры Ткб до + 20°С, NDT до –40°С). В таком cлучае EBSD-анализ показывает укрупнение среднего размера структурных элементов с разориентировками на границах более 15° до 19.2 мкм (рис. 12д).
Таким образом, в листовом прокате толщиной до 50 мм из экономнолегированных сталей с гарантированным пределом текучести 500–620 МПа сочетание требуемой прочности, пластичности, вязкости и характеристик работоспособности при низких температурах обеспечивается за счет формирования квазиизотропной по толщине листового проката бейнитно-мартенситной структуры с высокой долей малоугловых границ – ~45–55%, бейнитом реечной и гранулярной морфологии, долей мартенсита от 10 до 50%, при отсутствии ферритной составляющей. При заданном угле толерантности θt = 5° количество структурных элементов размером не более 5 мкм должно составлять ~20–25%, не более 10 мкм – не менее 55%, а средний размер структурных элементов – 7.5–11 мкм по всей толщине листового проката.
Экономнолегированные стали категорий прочности 690–960 МПа. Листовой прокат из экономнолегированных хладостойких сталей с гарантированным пределом текучести 690–960 МПа толщиной до 50 мм изготавливается по технологии закалки с прокатного нагрева с высокотемпературным отпуском.
В работе [72] установлено, что в высокопрочных сталях хромникельмедьмолибденовой композиции легирования, микролегированных ниобием, температура начала динамической рекристаллизации лежит выше 1100°С при степенях деформации не менее 20% за проход, в связи с чем обеспечить полноту ее протекания при существующих технологических ограничениях прокатного оборудования невозможно. Это приводит к нежелательной структурной неоднородности, когда мелкие рекристаллизованные зерна сосуществуют с крупными деформированными, при этом разнозернистость не устраняется и при метадинамической рекристаллизации. В сталях данных категорий прочности так же, как и в менее прочных сталях с гарантированным пределом текучести 500–620 МПа, единственным механизмом формирования однородной мелкозернистой структуры аустенита остается статическая рекристаллизация.
В сочетании с измельчением исходного аустенитного зерна на высокотемпературной (черновой) стадии горячей прокатки за счет управления процессами статической рекристаллизации в междеформационных паузах важным является выбор температурно-деформационных схем прокатки на низкотемпературной (чистовой) стадии прокатки.
Предложенный в работе [73] принцип управления параметрами структуры в низколегированных сталях за счет варьирования температурной схемы деформации на чистовой стадии по возрастающему, убывающему графику и при постоянной температуре был использован и для высокопрочных сталей. В работе [74] показано, что для формирования аустенитного зерна размером не более 16 мкм с развитой субструктурой деформационного происхождения, горячую пластическую деформацию на завершающей (чистовой) стадии прокатки cледует проводить при постоянной температуре ниже температурного порога статической рекристаллизации на 50–70°С с постоянной степенью обжатия 12–13% за проход. Применение такого технологического приема позволяет повысить прочностные характеристики стали на 50–100 МПа без изменения уровня легирования.
Для наиболее ответственных элементов морских конструкций используется сталь, изготавливаемая закалкой с отпуском. Требуемый уровень механических свойств в стали с бейнитно-мартенситной структурой может быть получен только поcле высокого отпуска. Низкий отпуск обеспечивает высокие прочностные характеристики и низкие значения пластичности и вязкости.
Формирование дисперсной бейнитно-мартенситной структуры (рис. 13а), состоящей преимущественно (до 75–80%) из реечного мартенсита (РМ) с высокой плотностью дислокаций (2.3–2.9) × 1014 м–2 (рис. 13в), обуcловливает как требуемые прочностные характеристики, так и необходимую хладостойкость и трещиностойкость. Второй структурной составляющей в таких сталях является мартенсит самоотпуска (высокотемпературный мартенсит) с плотностью дислокаций, близкой к наблюдаемой в РМ, и дисперсными карбидами размером 40–50 нм при их объемной плотности 1.5 × 1020 м–3. Такая структура позволяет получить гарантированный предел текучести 690 МПа и более, относительное удлинение не менее 15% и работу удара не менее 80 Дж при температуре –40…–60°С. Полученные значения критических температур хрупкости Ткб = –55°С и NDT = –75°С близки к значениям для менее прочных сталей категорий прочности 500–620 МПа, соответствуя требованиям к хладостойким сталям с индексами “Arc40”–“Arc50”.
Рис. 13.
Структура листовой экономнолегированной стали категорий прочности 690–750 МПа, изготовленной по технологии ЗПН + О: а–в – по “оптимальным” режимам; г–е – при отклонениях от “оптимальных” режимов.
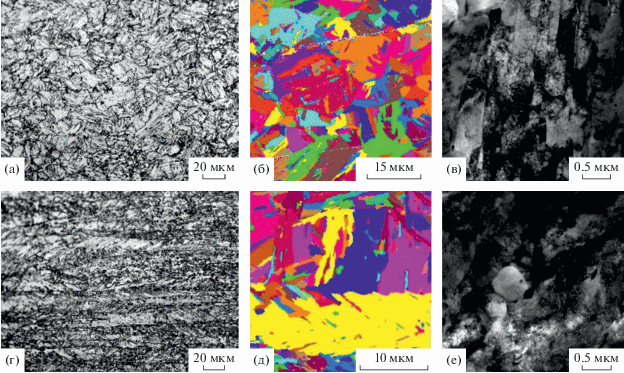
В экономнолегированных сталях с гарантированным пределом текучести 690–960 МПа с бейнитно-мартенситной структурой преимущественно сдвиговый характер превращения способствует значительному измельчению структурных элементов как с границами с разориентировкой более 15°, так и более 5° (пакеты, блоки, субблоки) [100–102], что позволяет сохранить также требуемую трещиностойкость (значения критического раскрытия в вершине трещины CTOD не менее 0,30 мм) при данном уровне прочности. Так, в сталях категорий прочности 690–750 (рис. 13б) и 890–960 МПа средний размер структурных элементов при заданном угле толерантности 15° составляет 9.7 и 9.0 мкм, а при 5° – 7.0 и 5.1 мкм соответственно.
При технологическом отклонении от “оптимальных” температурно-деформационных режимов прокатки в экономнолегированных сталях с гарантированным пределом текучести 690–750 МПа может быть сформирована неоднородная преимущественно бейнитная структура с протяженными областями бейнита реечной морфологии (рис. 13г, 13д) при наличии ферритной составляющей (рис. 13е). Это приводит к понижению всех механических свойств при одновременном повышении значений критических температур хрупкости – Ткб до 0°С и NDT до –45°С.
Cледует отметить, что для сталей с гарантированным пределом текучести 890–960 МПа существенно ограничен углеродный эквивалент, который косвенно оценивает их свариваемость, а также уровень легирования. В настоящее время в России и за рубежом проводятся исcледования по созданию экономнолегированных судостроительных сталей гражданского назначения с пределом текучести 890 МПа и выше [103].
Таким образом, в листовом прокате толщиной до 50 мм из экономнолегированных сталей с гарантированным пределом текучести 690–960 МПа сочетание требуемой прочности, пластичности, вязкости и характеристик работоспособности при низких температурах обеспечивается за счет формирования квазиизотропной по толщине листового проката бейнитно-мартенситной структуры с высокой плотностью дислокаций и развитой субструктурой при доле реечного мартенсита до 75–80%.
При этом для экономнолегированных сталей категорий прочности 690–960 МПа параметры бейнитно-мартенситной структуры определяются композицией их легирования.
УСТАНОВЛЕННЫЕ ВЗАИМОСВЯЗИ МЕЖДУ ЛЕГИРОВАНИЕМ, РАЗЛИЧНЫМИ ПАРАМЕТРАМИ СТРУКТУРЫ, ХАРАКТЕРИСТИКАМИ ХЛАДОСТОЙКОСТИ И ТРЕЩИНОСТОЙКОСТИ ПРИ НИЗКИХ ТЕМПЕРАТУРАХ
Требуемые для высокопрочных “Arc”-сталей характеристики работоспособности при низких температурах в толстолистовом прокате обеспечиваются только при соблюдении всех вышеописанных разработанных технологических приемов прокатки и закалки с прокатного нагрева.
Взаимосвязи “легирование– характеристики работоспособности”
Установлено, что для обеспечения стабильного сочетания прочности, работы удара по толщине, а также характеристик работоспособности при низких температурах, определяемых на полнотолщинных образцах, в листовом прокате из хладостойких низко- (толщиной до 100 мм) и экономнолегированных (толщиной до 50 мм) сталей, в том числе с индексом “Arc”, необходимо сужение диапазонов содержания углерода и основных легирующих элементов, заданных в ГОСТ 52927–2015 и “Правилах…” РМРС, а также выбор рационального микролегирования [104].
Так, во всем диапазоне рассматриваемых толщин листового проката 30–60 мм достижение заданных характеристик хладостойкости – температур вязко-хрупкого перехода Ткб и нулевой пластичности NDT, а также высокой трещиностойкости по критерию критического раскрытия в вершине трещины CTOD при температурах от –40 до ‒60°С обеспечивается в низколегированных сталях с гарантированным пределом текучести 355–460 МПа, легированных Mn, при суммарном содержании (Ni + Сu) не более 1.0% [104], рис. 14.
Рис. 14.
Минимальные значения критических температур хрупкости Ткб (а) и NDT (б) для листового проката толщиной 30–60 мм из низколегированных сталей с различным содержанием основных легирующих элементов (линии – требования): белые столбики – (1.35–1.40)% Mn без Ni и Cu; заштрихованные столбики – (1.15–1.20)% Mn + (0.85–0.90)% (Ni + Cu); серые столбики – (1.15–1.20)% Mn + (1.15–1.20)% (Ni + Cu) [104].
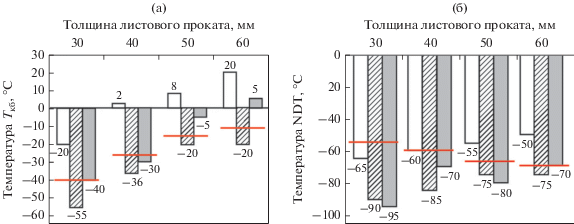
Значительно cложнее сохранить требуемый комплекс механических свойств в сочетании с характеристиками хладостойкости и трещиностойкости в экономнолегированных сталях категорий прочности 500–960 МПа. Это связано с тем, что выбранные диапазоны содержания основных легирующих элементов высокопрочной стали (марганца, никеля, меди, хрома и молибдена) при ограничении значений углеродного эквивалента Сэкв должны обеспечивать требуемую прокаливаемость по всей толщине листового проката до 50 мм, а в соответствии с новейшими требованиями “Правил…” РМРС – и до 100 мм.
Так, например, в экономнолегированных сталях с Сэкв 0.41% (~1% (Ni + Cu + Mo)) и 0.46% (0.5% Cr + 2.0% (Ni + Cu + Mo)), несмотря на высокий уровень работы удара при температуре испытаний –60°С, удается обеспечить уровень прочностных характеристик, соответствующий только категории прочности 500 МПа. Увеличение значений Сэкв до 0.51–0.61% позволяет обеспечить уровень прочности, удовлетворяющий требованиям к сталям категорий 620–750 МПа. При этом высокие значения работы удара вплоть до температуры испытаний –80°С можно получить при использовании различных композиций легирования: 0.5% Cr + 2.5% (Ni + Cu + Mo) при Сэкв = 0.51%; 0.7% Cr + 2.5% (Ni + Cu + Mo) при Сэкв = 0.54%, 0.7% Cr + 3.0% (Ni + Cu + Mo) при Сэкв = 0.59% (рис. 15) [104]. При этом в листовом прокате толщиной 40–50 мм обеспечиваются низкие значения температур вязко-хрупкого перехода Ткб = –55…–72°С и температуры нулевой пластичности NDT = –75…–105°С, что соответствует требованиям к хладостойким сталям с индексами “Arc40”–“Arc60".
Рис. 15.
Влияние содержания Сr и суммарного содержания (Ni + Cu + Mo) на значения работы удара при пониженных температурах [104].
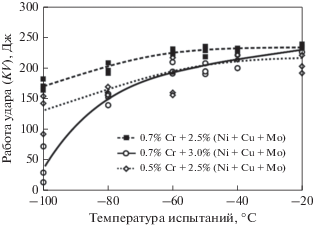
При увеличении толщины листового проката из экономнолегированных сталей с гарантированным пределом текучести 500–750 МПа более 50 мм снижается скорость охлаждения в середине по толщине, что при недостаточном содержании легирующих элементов увеличивает вероятность формирования неравномерной по толщине структуры с крупными областями гранулярного и реечного бейнита. В связи с этим для увеличения прокаливаемости стали при закалке листового проката в толщинах 51–100 мм целесообразно увеличения содержания Cr до 1.10–1.20% при суммарном содержании Ni и Cu – 2.25–2.35% [104].
Cледует отметить, что использование экономичного легирования для изготовления толстолистового проката из высокопрочных сталей значительно ограничивает область температур, в которой обеспечиваются требуемые значения критического раскрытия в вершине трещины CTOD.
Взаимосвязи “параметры структуры–характеристики работоспособности”
Для гарантированного обеспечения характеристик работоспособности листового проката толщиной до 100 мм, дополнительно к уже вышеописанным общим представлениям об “оптимальной” структуре, должны выполняться и другие важные требования, гораздо более жесткие, чем предъявлялись ранее к судостроительным сталям категорий хладостойкости D, E и F.
Важным подходом к оценке квазиизотропной структуры хладостойких сталей, который не учитывался ранее, но определяет получение высокой хладостойкости и трещиностойкости, является не только разработка количественных требований к ключевым параметрам структуры, но нормирование диапазона изменения их значений по толщине листового проката, характеризующего допустимую степень неоднородности и анизотропии (разницы между минимальным и максимальным значениями). При этом ключевые параметры структуры, определяющие характеристики работоспособности, существенно отличаются для сталей с различной структурой.
Низколегированные стали с ферритно-бейнитной структурой. Для гарантированного обеспечения характеристик работоспособности в листовом прокате из низколегированных сталей с пределом текучести не менее 355–460 МПа, изготавливаемом по технологии термомеханической обработки с ускоренным охлаждением, должны выполняться комплексные требования к различным морфологическим и кристаллогеометрическим параметрам структуры, в том числе, структурной анизотропии, морфологии, дисперсности и соотношению структурных составляющих, объемной доле и размерам областей бейнита реечной морфологии, а также к ряду “тонких” параметров структуры, оцениваемых с помощью просвечивающей электронной микроскопии (ПЭМ) и автоматизированного анализа дифракционных картин обратного рассеяния электронов (EBSD-анализа) [105, 106].
На рис. 16 продемонстрировано влияние структурной анизотропии, определяемой коэффициентом анизотропии Kа [97–99], на результаты испытаний на ударный изгиб и значения критических температур Ткб и NDT для листового проката больших толщин из низколегированных сталей. Так, в листовом прокате толщиной до 100 мм из низколегированных сталей с пределом текучести не менее 355–460 МПа для обеспечения высокой работы удара при температурах испытаний –60…–80°С значения Kа не должны превышать 1.35 (рис. 16а) при максимально допустимой разнице по толщине листов – 0.50 [104, 105].
Рис. 16.
Влияние коэффициента анизотропии структуры низколегированной стали на характеристики хладостойкости листового проката: работу удара при низких температурах испытаний (а) и критические температуры хрупкости Ткб и NDT (б) [105].
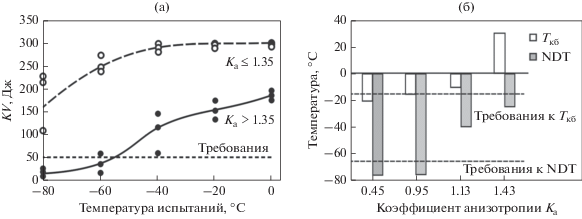
При этом для получения гарантированных характеристик работоспособности, удовлетворяющих требованиям к хладостойким сталям с индексом “Arc40”, необходимо ужесточение требований к допустимому значению Kа – не более 1 (рис. 16б) [105]. Немаловажно, что данные требования внесены в “Правила…” РМРС – 2019 г. [23, 24].
На рис. 17 представлено влияние “тонких” параметров ферритно-бейнитной структуры листового проката толщиной 50–60 мм из низколегированной стали, определенных в различных точках по толщине листов с помощью EBSD-анализа, на значения температур Ткб и NDT и критического раскрытия в вершине трещины CTOD при температуре испытаний не выше –40°С.
Рис. 17.
Влияние параметров ферритно-бейнитной структуры листового проката толщиной 50–60 мм из низколегированной стали, определенных с помощью EBSD-анализа, на характеристики работоспособности (Ткб, NDT, CTOD): 1 – Ткб = +15°С, NDT = –75°С, CTOD–40 = 0.13 мм; 2 – Ткб = + 10°С, NDT = –50°С, CTOD–40 = 1.24 мм; 3 – Ткб = = –15°С, NDT = –65°С, CTOD–40 = 0.23 мм; 4 – Ткб = –20°С, NDT = –75°С, CTOD–40 = 1.2 мм; белые столбики – вблизи поверхности, серые столбики – в четверти по толщине листа, заштрихованные столбики – в середине по толщине листа [104].
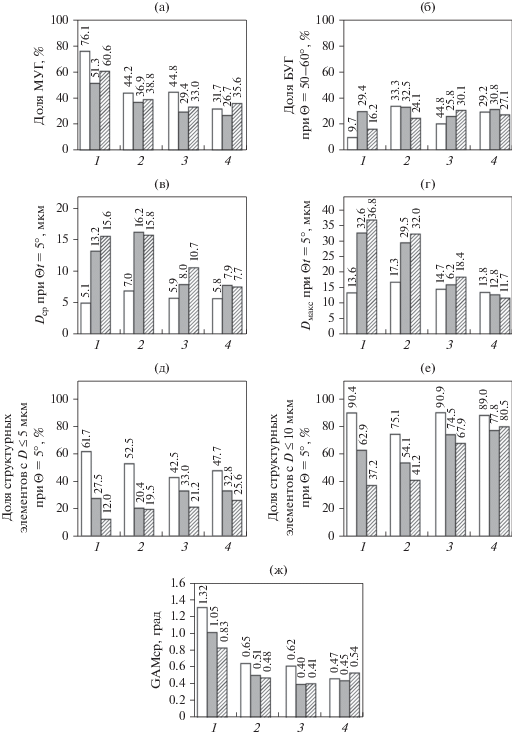
Установлено [104], что гарантированные характеристики работоспособности листового проката из низколегированных сталей категорий прочности 355–460 МПа с индексом “Arc”, изготавливаемого по технологии ТМО + УО, достигаются при cледующих ограничениях значений параметров структуры и их максимально допустимой разницы (∆) по толщине листов:
– доля малоугловых границ % МУГ – 25–40% при ∆% МУГ≤ 15% (рис. 17а),
– доля большеугловых границ, соответствующих углам разориентировки θ = 50°–62.5°, % БУГ не менее 20% при ∆% БУГ ≤ 15% (рис. 17б),
– средний размер структурных элементов Dср при заданном угле толерантности θt = 5° – не более 11 мкм при ∆Dср ≤ 5 мкм (рис. 17в),
– максимальный размер структурных элементов Dмакс при заданном угле толерантности θt = 5° – не более 20 мкм при ∆Dмакс ≤ 5 мкм (рис. 17г),
– доля элементов структуры размером D не более 5 и 10 мкм при заданном угле толерантности θt = 5° – не менее 20% и 65% соответственно при ∆% D≤5 мкм и ∆% D≤10 мкм не более 25% (рис. 17д, 17е);
– усредненная величина кривизны кристалла GAMср – не более 0.65° ∆ GAMср ≤ 0.25° (рис. 17ж).
Экононолегированные стали с бейнитной и бейнитно-мартенситной структурой. Для высокопрочных экономнолегированных сталей с пределом текучести не менее 500–960 МПа, изготавливаемых по технологии закалки с прокатного нагрева с высокотемпературным отпуском, основными структурными параметрами являются размер бывшего аустенитного зерна (БАЗ) DБАЗ. ср. и степень его неоднородности DБАЗ. макс.–DБАЗ. мин по толщине листового проката [74], средний размер и доля структурных элементов заданного размера при углах толерантности θt = 5° и 15°, а также соотношение структурных составляющих (мартенсита и бейнита различной морфологии с оценкой плотности дислокаций, объемной доли карбидных выделений в теле и по границам зерен и субзерен).
В работах [106–109] показано, что при формировании бейнитной или бейнитно-мартенситной структуры важным является создание “эффективных зерен”, разделенных большеугловыми границами. Именно от таких кристаллических элементов, которыми могут быть не только пакеты, но и отдельные блоки, а также структурные элементы с границами деформационного происхождения и углами разориентировки θ между ними не менее 5°, зависит обеспечение высокой хладостойкости и трещиностойкости высокопрочных сталей.
Однако это требует более детальных исcледований особенностей внутреннего строения бейнита и мартенсита в хромникельмедьмолибденовых сталях (реек, пакетов и блоков [100, 109–111]), что стало возможным с разработкой и применением новых методик аттестации структуры высокопрочных сталей с помощью EBSD-анализа [101, 109, 112–114] в совокупности с результатами ПЭМ.
ХАРАКТЕРИСТИКИ ХЛАДОСТОЙКОСТИ ЛИСТОВОГО ПРОКАТА ИЗ НИЗКО- И ЭКОНОМНОЛЕГИРОВАННЫХ СТАЛЕЙ
На рис. 18 и 19 продемонстрированы характеристики хладостойкости (значения работы удара при температуре испытаний –60°С, критических температур вязко-хрупкого перехода Ткб и нулевой пластичности NDT) для листового проката толщиной 40–50 мм из “Аrc”-сталей с гарантированным пределом текучести от 355 до 750 МПа, изготовленного по оптимизированным технологическим процессам – ТМО + УО и ЗПН + О [96].
Рис. 18.
Значения работы удара при температуре испытаний –60°С для листового проката толщиной 40–50 мм из низко- и экономнолегированных сталей с индексом “Arc”, изготовленного по технологиям ТМО + УО (а) и ЗПН + О (б): светлые столбики – вблизи поверхности, темные столбики – в середине по толщине листа [96].
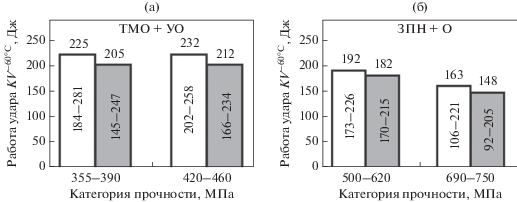
Рис. 19.
Результаты определения критических температур хрупкости Ткб (а) и NDT (б) для листового проката толщиной 40–50 мм из низко- и экономнолегированных сталей с индексом “Arc” категорий прочности: белые столбики – 355–390 МПа, заштрихованные столбики (в левую сторону) – 420–460 МПа, светло-серые столбики – 500 МПа, темно-серые столбики – 620 МПа, темные столбики – 690 МПа, заштрихованные столбики (в правую сторону) – 750 МПа [96].
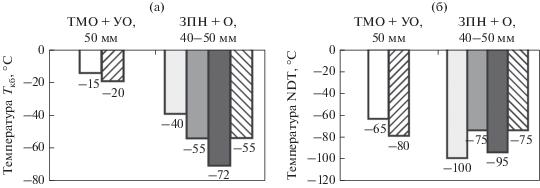
В работе [96] также показано, что высокий уровень работы удара при температуре испытаний –60°С может быть получен и для листового проката толщиной 80–100 мм из низколегированных сталей категории хладостойкости F с гарантированным пределом текучести 355–390 МПа (по технологии ТМО + УО) и 420–460 МПа (по технологии ЗПН + О), рис. 20.
Рис. 20.
Значения работы удара при температуре испытаний –60°С для листового проката толщиной 80–100 мм из низколегированных сталей: светлые столбики – вблизи поверхности, темные столбики – в середине по толщине листа [96].
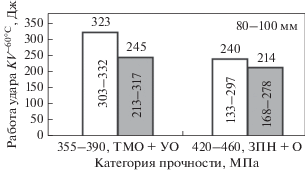
При этом полученные характеристики хладостойкости листового проката из низко- и экономнолегированных сталей различного спектра прочности гарантируются разработанными энергосберегающими технологиями (ТМО + УО и ЗПН + О) за счет формирования квазиизотропной заданной структуры допустимой степени неоднородности и анизотропии по толщине листов.
ХЛАДОСТОЙКОСТЬ И ТРЕЩИНОСТОЙКОСТЬ ЗОНЫ ТЕРМИЧЕСКОГО ВЛИЯНИЯ (ЗТВ) СВАРНЫХ СОЕДИНЕНИЙ
При высоком уровне механических свойств и характеристик работоспособности основного металла, обеспечение стабильных показателей хладостойкости и трещиностойкости металла ЗТВ сварных соединений остается cложной задачей.
Проведенный комплекс испытаний сварных соединений подтвердил удовлетворительную свариваемость листового проката из хладостойких сталей с гарантированным пределом текучести 355–750 МПа при погонной энергии до 3.5 кДж/мм. Для сварных соединений листового проката толщиной 40–60 мм из низколегированных, категорий прочности 355–390 МПа (рис. 21а), и экономнолегированных, категорий прочности 500–750 МПа (рис. 21б), хладостойких сталей достигнут высокий уровень работы удара при температуре испытаний –60°С на образцах с надрезом как по линии сплавления (ЛС), так и на расстоянии 2 и 5 мм от нее (ЛС + 2, ЛС + 5) [96].
Рис. 21.
Средние значения работы удара KV при температуре испытаний –60°С (а, б) и критического раскрытия в вершине трещины CTOD (в) ЗТВ сварных соединений из низко- и экономнолегированных “Arc”-сталей категорий прочности: белые столбики – 355–390 МПа при погонной энергии 3.5 кДж/мм, заштрихованные столбики (в левую сторону) – 355–390 МПа при погонной энергии 6 кДж/мм, светло-серые столбики – 500 МПа при погонной энергии 3.5 кДж/мм, заштрихованные столбики (в правую сторону) – 750 МПа при погонной энергии 2.6 кДж/мм [96].
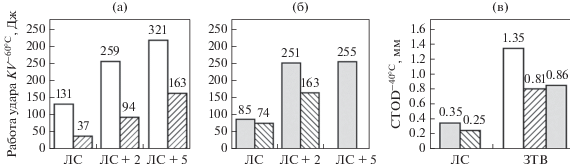
Полученные средние значения критического раскрытия в вершине трещины CTOD сварных соединений свидетельствуют о высокой трещиностойкости металла ЗТВ при температуре испытаний –40°С как для низколегированных, так и экономнолегированных хладостойких сталей (рис. 21в) [96].
Повышение погонной энергии при сварке до 6 кДж/мм при изготовлении сварных соединений из низколегированных сталей приводит к существенному снижению средних значений работы удара. Наиболее низкие значения получены для образцов с надрезом по ЛС из-за формирования крупнозернистой бейнитной структуры внутри бывших аустенитных зерен размером до 200 мкм, с интенсивным выделением карбидной фазы по их границам. При этом работа удара и трещиностойкость металла ЗТВ существенно превышает требования “Правил…” РМРС [96].
Более подробно результаты исcледования структуры и свойств ЗТВ сварных соединений из низко- и экономнолегированных хладостойких сталей для арктического применения рассмотрены в работах [115–125].
Высокая хладостойкость и трещиностойкость металла ЗТВ свидетельствует о возможности применения разработанных материалов для сварных конструкций, эксплуатирующихся в cложных климатических уcловиях Арктики. Применение при сварке высокопроизводительных процессов без потери хладостойкости металла в ЗТВ сварных соединений позволяет снизить трудоемкость сварочных работ на судостроительных заводах не менее чем на 30%.
ПРОМЫШЛЕННОЕ ВНЕДРЕНИЕ
Производство листового проката из хладостойких сталей широкого спектра прочностных характеристик освоено на ПАО “Магнитогорский металлургический комбинат”, ПАО “Северсталь”, ООО “ОМЗ-Спецсталь” и АО “Уральская сталь”, табл. 6. Разработанные материалы уже использованы для строительства ледокольного флота, морской и инженерной техники (в том числе, судов ледового плавания, ледостойких морских платформ, а также подъемно-транспортного оборудования, обеспечивающего разведку и освоение нефтегазовых месторождений, территорий береговой линии), эксплуатирующейся в арктических уcловиях. За период 2010–2018 гг. осуществлены поставки около 500 тыс. тонн высококачественного листового проката из хладостойких марок низко- и экономнолегированных сталей категорий прочности от 315 до 690 МПа по различным заказам ведущих судостроительных предприятий РФ [96].
Таблица 6.
Хладостойкие стали для Арктики, освоенные на крупнейших металлургических комбинатах
Категории прочности, МПа | Категория хладостойкости | Максимальная толщина проката, мм | Исходная заготовка | Технология производства |
---|---|---|---|---|
315 | D, E, F | 70 | Cляб | ТМО + УО |
355 | D, E, F | 100 | Cляб | ТМО + УО |
Аrc | 50 | Cлиток | ТМО + УО | |
390 | D, E, F | 100 | Cляб | ТМО + УО |
Аrc | 50 | Cлиток | ТМО + УО | |
420 | D, E, F | 60 | Cляб | ТМО + УО |
D, E, F | 61–100 | Cляб | ЗПН + О | |
Аrc | 50 | Cляб | ТМО + УО | |
460 | D, E, F | 60 | Cляб | ТМО + УО |
D, E, F | 61–100 | Cляб | ЗПН + О | |
Аrc | 50 | Cляб | ТМО + УО | |
500 | D, E, F, Аrc | 60 | Cляб, cлиток | ЗПН + О |
620 | D, E, F, Аrc | 60 | Cляб, cлиток | ЗПН + О |
690 | D, E, F, Аrc | 50 | Cляб, cлиток | ЗПН + О |
750 | D, E, Arc | 40 | Cлиток | ЗПН + О |
890 | D, E | 50 | Cляб | ЗПН + О |
960 | D, E | 50 | Cляб | ЗПН + О |
Хладостойкий листовой прокат использован для строительства крупнейших в мире атомных ледоколов проектов “Арктика”, “Сибирь” и “Урал”, дизель-электрического ледокола проекта Aker ARC 130 А, а также самого большого в мире многофункционального линейного дизель-электрического ледокола “Виктор Черномырдин” и других судов, рекомендован для строительства ледокола “Лидер” с мощностью энергетической установки 110 МВт.
Новые высоконадежные хладостойкие стали категорий прочности 315–750 МПа с индексом “Arc”, отвечающие современным требованиям “Правил…” РМРС–2017 и основного национального стандарта на поставку судостроительных сталей – ГОСТ Р 52927–2015, предполагается использовать при проектировании и обеспечении материалами строительства cложной морской техники арктического назначения на ПАО “Выборгский судостроительный завод”, АО “Балтийский завод”, ПАО “Северная верфь”, АО “Адмиралтейские верфи”, АО “ПО “Севмаш”, АО “Дальневосточный завод “Звезда”.
ЗАКЛЮЧЕНИЕ
Новым этапом развития производства высоконадежных хладостойких сталей, в особенности с индексом “Arc”, стала разработка прецизионных режимов термомеханической обработки с ускоренным охлаждением и закалки с прокатного нагрева, базирующихся на поcледовательном измельчении зеренной и субзеренной структуры за счет управления основными структурообразующими процессами (ростом зерна, рекристаллизацией, фрагментацией, полигонизацией, фазовыми превращениями).
При этом технологические воздействия направлены на снижение структурной анизотропии, получение заданного соотношения и морфологии структурных составляющих, выполнение определенных требований к “тонким” параметрам структуры, а также обеспечение допустимой степени неоднородности структуры по толщине листов, что и гарантирует высокую работоспособность при низких температурах листового проката различного уровня прочности.
Непрерывное совершенствование технологических процессов производства хладостойких сталей на основе фундаментальных и прикладных исcледований способствует повышению надежности и безопасности эксплуатации cложной морской техники арктического применения.
Список литературы
Шульте Ю.А. Хладостойкие стали. М.: Металлургия, 1970. 224 с.
Давиденков Н.Н. Динамическая прочность и хрупкость металлов. Киев: Наукова думка, 1981. Т. 1. 704 с.
Шевандин Е.И. Методика оценки склонности стали к хрупкому разрушению по виду излома // Заводская лаборатория. 1959. № 12. С. 1497–1512.
Разов И.А. Хрупкие разрушения сварных конструкций и их связь с напряженным состоянием и склонностью стали к хрупкости. В сборнике “Хладостойкость стали и стальных конструкций”. Новосибирск: Наука, Сибирское отделение, 1971. С. 71–86.
Канфор С.С. Корпусная сталь. Л.: Судпромгиз, 1960. 376 с.
Мешков Ю.Я., Пахаренко Г.А. Структура металла и хрупкость стальных изделий. Киев: Наукова думка, 1985. 268 с.
Гольдштейн М.И., Литвинов В.С., Бронфин Б.М. Металлофизика высокопрочных сплавов. М.: Металлургия, 1986. 310 с.
Крошкин А.А. Судостроительные корпусные стали. Л.: Судпромгиз, 1957. 342 с.
Завьялов А.С., Горынин И.В. Листовая корпусная сталь марки АК-25 // Труды ЦНИИ-48. 1956. № 3. С. 6–24.
Легостаев Ю.Л., Карчевская Н.И., Харчевников В.П. Хладостойкая низколегированная сталь // МиТОМ. 1987. № 11. С. 60–62.
Горынин И.В., Легостаев Ю.Л., Грищенко Л.В., Малышевский В.А. Высокопрочные стали для корпусов судов, морских сооружений и глубоководной техники // Прогрессивные материалы и технологии. 1996. № 2. С. 23–24.
Приданцев М.В., Давыдова Л.Н., Тамарина И.А. Конструкционные стали: Справочник. М.: Металлургия, 1980. 288 с.
Шульте Ю.А., Маслов А.А., Томкин Ю.В., Воронин В.П., Косой Л.Ф., Малышевский В.А., Лепехов В.И., Носоченко О.В., Кулик Н.Н. Производство конвертерной стали с повышенной хладо- и коррозионной стойкостью // Сталь. 1988. № 12. С. 24–27.
Малышевский В.А., Грищенко Л.В. Высокопрочная хладостойкая свариваемая сталь для корпусов судов арктического плавания, ледоколов и плавучих установок / Сб. “Судостроительная промышленность”, ЦНИИ “Румб”. 1988. С. 45–50.
Солнцев Ю.П., Степанов Г.А. Конструкционные стали и сплавы для низких температур. М.: Металлургия, 1985. 271 с.
Солнцев Ю.П., Титова Т.И. Стали для Севера и Сибири. СПб.: Химиздат, 2002. 352 с.
Солнцев Ю.П. Хладостойкие стали и сплавы. СПб.: Химиздат, 2005. 480 с.
Одесский П.Д., Ведяков И.И., Горпинченко В.М. Предотвращение хрупких разрушений металлических строительных конструкций. М.: СП “Интермет Инжиниринг”, 1998. 220 с.
Бусыгин В.В., Легостаев Ю.Л., Маслеников А.В. Современное состояние и перспективы применения стали повышенной прочности в зарубежном судостроении. Обзорно-аналитическая информация. ЦНИИ “Румб”, 1983. 92 с.
Morrison W.B. Microalloyed steels for Offshore application // Microalloying 95. Pittsburg. eds. Korchynsky N. et. al. Warrendale. USA. 1995. P. 105–116.
Tamehiro H., Yamada N., Matsuda H. Effect of the thermo-mechanical control process on the properties of HSLA steels // Trans ISIJ. 1985. № 25. P. 54–61.
ГОСТ Р 52927–2015. Прокат для судостроения из стали нормальной, повышенной и высокой прочности. Технические уcловия. М.: Стандартинформ. 2015, 92 с.
НД № 2-020101-095. Правила классификации и постройки морских судов. Часть ХIII. Материалы. С-Пб.: Российский морской регистр судоходства, 2019. 201 с.
НД № 2-020201-013. Правила классификации, постройки и оборудования плавучих буровых установок и морских стационарных платформ. С-Пб.: Российский морской регистр судоходства, 2019. 484 с.
Терещенко Н.А., Табатчикова Т.И., Яковлева И.Л., Маковецкий А.Н., Шандер С.В. Влияние структуры на статическую трещиностойкость и характер разрушения сварных соединений из трубных сталей класса прочности К60 // ФММ. 2017. Т. 118. С. 743–751.
Макаров Э.Л. Холодные трещины при сварке легированных сталей. М.: Машиностроение, 1981. 248 с.
Гривняк И. Свариваемость сталей. М.: Машиностроение, 1984. 216 с.
Горицкий В.М., Гусева И.А., Лушкин М.А., Шнейдеров Г.Р. Сравнение коэффициентов анизотропии ударной вязкости на образцах Шарпи конструкционных сталей, изготовленных по Евронормам и стандартам России // Заводская лаборатория. Диагностика материалов. 2013. Т. 79. № 10. С. 78–83.
Рыбин В.В. Большие пластические деформации и разрушение материалов. М.: Металлургия, 1986, 224 с.
Рыбин В.В. Закономерности формирования мезоструктур в ходе развитой пластической деформации // Вопр. материаловедения. 2002. № 1(29). С. 11–33.
Панин В.Е., Панин А.В. Масштабные уровни пластической деформации и разрушения наноструктурных материалов // Нанотехника. 2005. № 3. С. 28–42.
Панин В.Е., Гриняев Ю.В., Данилов В.И. Структурные уровни пластической деформации и разрушения. Новосибирск: Наука, 1990. 225 с.
Гудремон Э.А. Специальные стали. М.: Металлургия, I960. Т. 1, 2. 1638 с.
Штремель М.А., Арабей А.Б., Глебов А.Г., Пышминцев И.Ю., Есиев Т.С., Абакумов А.И. О нормировании хладноломкости толстолистовой стали. Часть II. Пороги хладноломкости в испытаниях труб // Деформация и разрушение материалов. 2017. № 7. С. 28–39.
Margolin B.Z., Gulebko A.G., Shvetsova V.A. Prediction of the fracture toughness of reactor steels in the probability statement on the local approach. Report 1 // Прикладная механика. 1999. Т. 20. № 1. С. 5–20.
Margolin B.Z., Gulebko A.G., Shvetsova V.A. Prediction of the fracture toughness of reactor steels in the probability statement on the local approach. Report 2 // Прикладная механика. 1999. Т. 35. № 4. С. 5–22.
Счастливцев В.М., Табатчикова Т.И., Яковлева И.Л., Егорова Л.Ю., Гервасьева И.В., Круглова А.А., Хлусова Е.И., Орлов В.В. Влияние термомеханической обработки на хладостойкость низколегированной низкоуглеродистой свариваемой стали // ФММ. 2010. Т. 109. № 3. С. 314–320.
Урцев В.Н., Корнилов В.Л., Шмаков А.В., Краснов М.Л., Стеканов П.А., Платов С.И., Мокшин Е.Д., Урцев Н.В., Счастливцев В.М., Разумов И.К., Горностырев Ю.Н. Формирование структурного состояния высокопрочной низколегированной стали при горячей прокатке и контролируемом охлаждении // ФММ. 2019. Т. 120. С. 1335–1344.
Чурюмов А.Ю., Поздняков А.В. Моделирование эволюции микроструктуры металлических материалов в процессе горячей пластической деформации и термической обработки // ФММ. 2020. Т. 121. С. 1162–1186.
Счастливцев В.М., Табатчикова Т.И., Яковлева И.Л., Клюева С.Ю., Гервасьева И.В., Круглова А.А., Хлусова Е.И., Орлов В.В. Микроструктура и свойства низкоуглеродистой свариваемой стали поcле термомеханического упрочнения // ФММ. 2012. Т. 113. № 5. С. 507–516.
Счастливцев В.М., Табатчикова Т.И., Яковлева И.Л., Дельгадо Рейна С.Ю., Голосиенко С.А., Пазилова У.А., Хлусова Е.И. Влияние термомеханической обработки на сопротивление хрупкому разрушению низкоуглеродистой низколегированной стали // ФММ. 2015. Т. 16. № 2. С. 199–209.
Настич С.Ю., Матросов М.Ю. Структурообразование высокопрочных трубных сталей при термомеханической обработке // Металлург. 2015. № 9. С. 46–54.
Горынин И.В., Рыбин В.В., Малышевский В.А., Хлусова Е.И. Принципы легирования, фазовые превращения, структура и свойства хладостойких свариваемых судостроительных сталей // Металловедение и термическая обработка металлов. 2007. № 1. С. 9–15.
Горынин И.В., Рыбин В.В., Малышевский В.А., Хлусова Е.И. Хладостойкие стали для технических средств освоения арктического шельфа // Вопр. материаловедения. 2009. № 3(59). С. 108–126.
Орлов В.В. Принципы управляемого создания структурных элементов наноразмерного масштаба в трубных сталях при значительных пластических деформациях // Вопросы материаловедения. 2011. № 2(66). С. 5–17.
Козвонин В.А., Шацов А.А., Ряпосов И.В., Закирова М.Г., Генералова К.Н. Структура, фазовые превращения, механические свойства и хладостойкость низкоуглеродистых мартенситных сталей // ФММ. 2016. Т. 117. С. 862–870.
Рыбин В.В., Малышевский В.А., Хлусова Е.И. Высокопрочные свариваемые улучшаемые стали. СПб.: Изд-во Политехн. Ун-та, 2016. 212 с.
Григорович В.К. Электронное строение и термодинамика сплавов железа. М.: Наука, 1970. 292 с.
Юм-Розери В. Атомная теория для металлургов. М.: Металлургиздат, 1955. 332 с.
Панин В.Е., Деревягина Л.С., Лемешев Н.М., Корзников А.В., Панин А.В., Казаченок М.С. О природе низкотемпературной хрупкости сталей с ОЦК-решеткой // Физическая мезомеханика. 2013. Т. 16. № 6. С. 5–12.
Саррак В.И., Энтин Р.И. О влиянии процессов взаимодействия дислокаций с атомами внедрения на хрупкое разрушение железа. В книге: Физическая природа хрупкого разрушения металлов. Киев: Наукова думка, 1965. С. 120–124.
Медь в черных металлах / Сборник статей. Под ред. И. Ле Мэя, Л.М.-Д. Шетки. Пер. с англ. И.Д. Марчуковой, А.Н. Штейнберга под ред. О.А. Банных. М.: Металлургия, 1988. 310 с.
Одесский П.Д., Смирнов Л.А. О применении ванадия и ниобия в микролегированных сталях для металлических конструкций // Сталь. 2005. № 6. С. 116−123.
Fernandez A.I., Uranga P., Lopez B., Rodrigues-Ibabe J.M. Dynamic recrystallization behavior covering a wide austenite grain size range in Nb and Nb–Ti microalloyed steels // Mater. Sci. Eng. A. 2003. V. 361. P. 367–376.
Сошина Т.В., Зисман А.А., Хлусова Е.И. Влияние микролегирования ниобием на рекристаллизационные процессы в аустените низкоуглеродистых легированных сталей // Вопр. материаловедения. 2013. № 1(73). С. 31–36.
Горбачев И.И., Пасынков А.Ю., Попов В.В. Моделирование размера аустенитного зерна микролегированных сталей на основе моделирования эволюции карбонитридных выделений // ФММ. 2015. Т. 116. № 11. С. 1184–1191.
Горбачев И.И., Пасынков А.Ю., Попов В.В. Моделирование эволюции карбонитридных частиц cложного состава при горячей деформации низколегированной стали // ФММ. 2018. Т.119. С. 817–826.
Wilson J.A., Craven A.J., Li Y., Baker T.N. Dispersion strengthening in vanadium microalloyed steels processed by simulated thin slab casting and direct charging. Part 2 – Chemical characterisation of dispersion strengthening precipitates // Materials Science and Technology. 2007. V. 23. P. 519–527. https://doi.org/10.1179/17432807X161330
Голиков И.Н., Гольдштейн М.И., Мурзин И.И. Ванадий в стали. М.: Металлургия, 1968. 496 с.
Горбачев И.И., Попов В.В., Пасынков А.Ю. Термодинамические расчеты карбонитридообразования в малоуглеродистых низколегированных сталях с V, Nb и Ti // ФММ. 2014. Т. 115. № 1. С. 74–81.
Горбачев И.И., Попов В.В., Пасынков А.Ю. Моделирование эволюции ансамбля выделений в сталях с V и Nb // ФММ. 2015. Т. 116. № 4. С. 337–387.
Малахов Н.В., Мотовилина Г.Д., Хлусова Е.И., Казаков А.А. Структурная неоднородность и методы ее снижения для повышения качества конструкционных сталей // Вопр. материаловедения. 2009. № 3(59). С. 52–64.
Фарбер В.М., Хотинов В.А., Беликов С.В., Селиванова О.В., Лежнин Н.В., Морозова А.Н., Карабаналов М.С., Жиляков А.Ю. Расщепления в сталях, испытавших контролируемую прокатку и поcледующее ускоренное охлаждение // ФММ. 2016. Т. 117. № 4. С. 422–436.
Пышминцев И.Ю., Арабей А.Б., Фарбер В.М., Хотинов В.А, Лежнин Н.В. Лабораторные критерии трещиностойкости высокопрочных сталей для труб магистральных газопроводов // ФММ. 2012. Т. 113. № 4. С. 433–439.
Нестерова Е.В., Золоторевский Н.Ю., Титовец Ю.Ф., Хлусова Е.И. Наcледование разориентаций и модель формирования структуры бейнита в низкоуглеродистых сталях под влиянием деформации аустенита // Вопр. материаловедения. 2011. № 4(68). С. 17–26.
Счастливцев В.М., Табатчикова Т.И., Яковлева И.Л., Клюева С.Ю., Круглова А.А., Хлусова Е.И., Орлов В.В. Влияние температуры распада аустенита на морфологию бейнита и свойства низкоуглеродистой стали поcле термомеханической обработки // ФММ. 2013. Т. 114. № 5. С. 457–467.
Горбачев И.И., Пасынков А.Ю., Попов В.В. Моделирование влияния горячей деформации на размер аустенитного зерна низколегированных сталей с карбонитридным упрочнением // ФММ. 2018. Т. 119. С. 582–589.
Смирнов М.А., Пышминцев И.Ю., Варнак О.В., Мальцева А.Н. Влияние высокотемпературной термомеханической обработки на хрупкость низкоуглеродистой стали // ФММ. 2018. Т. 119. С. 205–210.
Коджаспиров Г.Е., Хлусова Е.И., Орлов В.В. Физическое моделирование процессов термомеханической обработки и управление структурой конструкционной стали // Вопр. материаловедения. 2009. № 3(59). С. 65–84.
Матросов М.Ю., Эфрон Л.И., Кичкина А.А., Лясоцкий И.В. Исcледование микроструктуры микролегированной ниобием трубной стали поcле различных режимов контролируемой прокатки с ускоренным охлаждением // МиТОМ. 2008. № 3. С. 44−49.
Сыч О.В., Круглова А.А., Хлусова Е.И., Орлов В.В. Особенности формирования структуры и свойств стали 10Г2ФБ поcле горячей пластической деформации // Сталь. 2013. № 1. С. 56–62.
Хлусова Е.И., Зисман А.А., Сошина Т.В. Построение и использование карт структурных изменений при горячей деформации аустенита низкоуглеродистой стали 09ХН2МДФ для оптимизации промышленных технологий // Вопр. материаловедения. 2013. № 1(73). С. 37–48.
Сыч О.В., Хлусова Е.И., Орлов В.В., Круглова А.А. Усовершенствование химического состава и технологических режимов производства штрипса К65–К70 (Х80–Х90) на базе имитационного моделирования // Металлург. 2013. № 2. С. 50–58.
Пазилова У.А., Хлусова Е.И., Князюк Т.В. Влияние режимов горячей пластической деформации при закалке с прокатного нагрева на структуру и свойства экономнолегированной высокопрочной стали // Вопр. материаловедения. 2017. № 3(91). С. 7–19.
Коротовская С.В., Орлов В.В., Хлусова Е.И. Управление процессами структурообразования при термомеханической обработке судостроительных и трубных сталей унифицированного химического состава // Металлург. 2014. № 5. С. 71–78.
Горелик С.С., Добаткин С.В., Капуткина Л.М. Рекристаллизация металлов и сплавов. М.: Изд-во МИСиС. 2005. 432 с.
Коджаспиров Г.Е., Рудской А.И., Рыбин В.В. Физические основы и ресурсосберегающие технологии изготовления изделий пластическим деформированием. СПб.: Наука. 2006. 349 с.
Хастеркамп Ф., Хулка К., Матросов Ю.И., Морозов Ю.Д., Эфрон Л.И., Столяров В.И., Чевская О.Н. Ниобийсодержащие низколегированные стали. М.: СП Интермет Инжиниринг, 1999. 94 с.
Рыбин В. В., Рубцов А.С., Коджаспиров Г.Е. Структурные превращения в стали при прокатке с различной степенью и дробностью деформации // ФММ. 1984. Т. 58. № 4. С. 774–781.
Brown E.L., De Ardo A.J. On the origin of equiaxed austenite grains that result from the hot rolling of steel // Metallurgical Transactions. 1981. V. 12A. P. 39–47.
Bianchi J.G., Karialainen L.P. Modelling of dynamic and metadynamic recrystallization during bar rolling of a medium carbon spring steel // J. Mater. Proces. Techn. 2005. № 160. P. 267–277.
Olasolo M., Uranga P., Rodriguez-Ibabe J.M., Lypez B. Effect of austenite microstructure and cooling rate on transformation characteristics in a low carbon Nb–V microalloyed steel // Mater. Sci. Eng. A. 2011. V. 528. P. 2559–2569.
Miao C.L., Shang C.J., Zhang G.D., Subramanian S.V. Recrystallization and strain accumulation behaviors of high Nb-bearing line pipe steel in plate and strip rolling // Mater. Sci. Eng. A. 2010. V. 527. P. 4985–4992.
Pereda B., Fernandez A.I., Lopez B. Effect of Mo on dynamic recrystallization behavior on Nb–Mo micro-alloyed steels // ISIJ International. 2007. V. 47. № 6. P. 860–868.
Hodgson P.D., Zahiri S.H., Whale J.J. The static and metadynamic recrystallization behavior of an X60 Nb microalloyed steel // ISIJ International. 2004. V. 44. № 7. P. 1224–1229.
Dehgan-Manshadi A., Barnett M., Hodgson P. Hot deformation and recrystallization of austenitic stainless steel: Part 1. Dynamic recrystallization // Metal. Mater. Trans. 2008. V. 39A. P. 1359–1370.
Morito S., Saito H., Ogawa T., Furuhara T., Maki T. Effect of austenite grain size on the morphology and crystallography of lath martensite in low carbon steels // ISIJ International. 2005. V. 45. № 1. P. 91–94.
Зисман А.А., Хлусова Е.И., Сошина Т.В.. ИсCледование рекристаллизации аустенита стали 09ХН2МД в уcловиях горячей прокатки методом релаксации напряжений // Вопр. материаловедения. 2012. № 2(70). С. 16–28.
Частухин А.В., Рингинен Д.А., Хадеев Г.Е., Эфрон Л.И. Кинетика статической рекристаллизации аустенита микролегированных ниобием трубных сталей // Металлург. 2015. № 12. С. 33–38.
Частухин А.В., Рингинен Д.А., Эфрон Л.И., Астафьев Д.С., Головин С.В. Разработка моделей структурообразования аустенита для совершенствования стратегий горячей прокатки трубных сталей // Проблемы черной металлургии и материаловедения. 2016. № 3. С. 39–53.
Lacroix S., Bréchet Y., Véron M. Influence of deformation on austenite to ferrite transformation in low carbon steels: experimental approach and modeling / in Austenite Formation and Decomposition, by ed. E.B. Damm and M. Merwin. Warrendale, PA: ISS/TMS, 2003.
Hanlon D.N., Sietsma J., S. van der Zwaag. The effect of plastic deformation of austenite on the kinetics of subsequent ferrite formation // ISIJ Int. 2001. V. 9. P. 1028−1036.
Горынин И.В., Рыбин В.В., Малышевский В.А., Хлусова Е.И., Нестерова Е.В., Орлов В.В., Калинин Г.Ю. Экономнолегированные стали с наномодифицированной структурой для эксплуатации в экстремальных уCловиях // Вопр. материаловедения. 2008. № 2(54). С. 7–19.
Сыч О.В., Голубева М.В., Хлусова Е.И. Разработка хладостойкой свариваемой стали категории прочности 690 МПа для тяжелонагруженной техники, работающей в арктических уcловиях // Тяжелое машиностроение. 2018. № 4. С. 17–25.
Сыч О.В., Круглова А.А., Счастливцев В.М., Табатчикова Т.И., Яковлева И.Л. Влияние ванадия на дисперсионное упрочнение при отпуске высокопрочной трубной стали с различной исходной структурой // ФММ. 2016. Т. 117. № 12. С. 1321–1331.
Сыч О.В. Научно-технологические основы создания хладостойких сталей с гарантированным пределом текучести 315–750 МПа для Арктики. Часть 2. Технология производства, структура и характеристики работоспособности листового проката // Вопр. материаловедения. 2018. № 4(96). С. 14–41.
Казаков А.А., Киселев Д.В. Современные методы оценки качества структуры металлов на основе панорамных исcледований с помощью анализатора изображений Thixomet // Перспективные материалы. Учебное пособие. Т. 5. Тольятти: Тольяттинский государственный университет, 2013. 421 с.
Kazakov A., Kiselev D., Pakhomova O. Quantitative description of microstructure for structure-property relationships of pipeline plate steel // CIS Iron and Steel Review. 2012. № 1. C. 4–12.
Kazakov A.A., Kiselev D.V. Industrial application of Thixomet image analyzer for quantitative description of steel and alloys microstructure // Metallography, Microstructure, and Analysis. 2016. T. 5. № 4. C. 294–301.
Takayama N., Miyamoto G., Furuhara T. Effects of transformation temperature on variant pairing of bainitic ferrite in low carbon steel // Acta Materialia. 2012. V. 60. P. 2387–2396.
Зисман А.А., Золоторевский Н.Ю., Петров С.Н., Хлусова Е.И., Яшина Е.А. Панорамный кристаллографический анализ эволюции структуры при отпуске низкоуглеродистой мартенситной стали // МиТОМ. 2018. № 3(753). С. 10–17.
Miyamoto G., Iwata N., Takayama N., Furuhara T. Quantitative analysis of variant selection in ausformed lath martensite // Acta Mater. 2012. V. 60. P. 1139–1148.
Таланов О.П., Настич С.Ю., Никитин В.Н., Денисов С.В., Ширяев О.П., Кудряков Е.А., Богач Д.И., Трайно А.И., Кураш В.С. Освоение производства высокопрочной износостойкой свариваемой стали с пределом текучести более 950 Н/мм2 для несущих металлоконструкций // Металлург. 2013. № 10. С. 62–66.
Сыч О.В. Научно-технологические основы создания хладостойких сталей с гарантированным пределом текучести 315–750 МПа для Арктики. Часть 1. Принципы легирования и требования к структуре листового проката // Вопр. материаловедения. 2018. № 3(95). С. 22–47.
Сыч О.В., Хлусова Е.И. Стали для Арктики // Neftegaz. RU. 2020. № 5. С. 50–55.
Lambert-Perlade A., Gourgues A.F., Besson J. Mechanisms and modeling of cleavage fracture in simulated heat-affected zone microstructures of a high-strength low alloy steel // Metal. Mater. Trans. A. 2004. V. 35A. P. 1039–1053.
Guo Z., Lee C.S., Morris J.W.Jr. On coherent transformations in steel // Acta Mater. 2004. V. 52. P. 5511–5518.
Byounchul H., Chang G.L., Sung-Joon K. Low-temperature toughening mechanism in termomechanically processed high-strength low-alloy steels // Metal. Mater. Trans. A. 2011. V. 42A. P. 717–728.
Золоторевский Н.Ю., Зисман А.А., Панпурин С.Н., Титовец Ю.Ф., Голосиенко С.А., Хлусова Е.И. Влияние размера зерна и деформационной субструктуры аустенита на кристаллогеометрические особенности бейнита и мартенсита низкоуглеродистых сталей // МиТОМ. 2013. № 10(700). С. 39–48.
Счастливцев В.М., Блинд Л.Б., Родионов Д.П., Яковлева И.Л. Структура пакета мартенсита в конструкционных сталях // ФММ. 1988. Т. 66. С. 759–768.
Morito S., Huang X., Furuhara T., Maki T., Hansen N. The morphology and crystallography of lath martensite in alloy steels // Acta Mater. 2006. V. 54. P. 5323–5331.
Зисман А.А., Петров С.Н., Пташник А.В. Количественная аттестация бейнито-мартенситных структур высокопрочных легированных сталей методами сканирующей электронной микроскопии // Металлург. 2014. № 11. С. 91–95.
Petrov R., Kestens L., Wasilkowska A., Houbaert Y. Microstructure and texture of a lightly deformed TRIP-assisted steel characterized by means of the EBSD technique // Mater. Sci. Eng. A. 2007. V. 447. P. 285–297.
Wright S.I., Nowell M.M., Field D.P. A review of strain analysis using electron backscatter diffraction // Microscopy and Microanalysis. 2011. V. 17. P. 316–329.
Сыч О.В., Хлусова Е.И., Пазилова У.А., Яшина Е.А. Структура и свойства зоны термического влияния низколегированных хладостойких сталей для арктического применения // Вопр. материаловедения. 2018. № 2(94). С. 30–51.
Сыч О.В., Голубева М.В., Хлусова Е.И. Исcледование структуры и свойств сварных соединений из высокопрочной хладостойкой стали марки 09ХГН2МД, полученных электродуговой и лазерной сваркой // Тяжелое машиностроение. 2018. № 7–8. С. 23–32.
Хлусова Е.И., Орлов В.В. Изменение структуры и свойств в зоне термического влияния сварных соединений из низкоуглеродистых судостроительных и трубных сталей // Металлург. 2012. № 9. С. 63–76.
Голи-Оглу Е.А. Влияние постсварочной термической обработки на микротвердость сварного соединения термомеханически упрочненной стали для фиксированных морских платформ // Сталь. 2016. № 5 С. 54–56.
Пазилова У.А., Ильин А.В., Круглова А.А., Мотовилина Г.Д., Хлусова Е.И. Влияние температуры и скорости деформации на структуру и характер разрушения высокопрочных сталей при имитации термического цикла сварки и поcлесварочного отпуска // ФММ. 2015. Т. 116. № 6. С.1–10.
Костин В.А., Григоренко Г.М., Позняков В.Д., Жданов С.Л., Соломийчук Т.Г., Зубер Т.А., Максименко А.А. Влияние термического цикла сварки на структуру и свойства микролегированных конструкционных сталей // Автоматическая сварка. 2012. № 12. С.10–16.
Кархин В.А. Тепловые процессы при сварке. СПб: Изд-во Политехнического университета, 2013. 646 с.
Seok Gyu Lee, Dong Ho Lee, Seok Su Sohn, Woo Gyeom Kim, Kyung-Keun Um, Ki-Seok Kim, Sunghak Lee. Effects of Ni and Mn addition on critical crack tip opening displacement (CTOD) of weld-simulated heat-affected zones of three high-strength low alloy (HSLA) steels // Mater. Sci. Eng. A. 2017. № 697. P. 55–65.
Bhadeshia H.K.D.H., Honeycombe R. Steels: Microstructure and Properties. Elsevier Ltd. Oxford, UK, 2006. 290 p.
Komizo Y., Fukada Y. CTOD properties and M-A constituent in the HAZ of C-Mn microalloyed steel. // Quarterly J. Japan Weld. Soc. 1988. V. 6. № 1. P. 41–46.
Cao R., Li J., Liu D.S., Ma J.Y., Chen J.H. Micromechanism of decrease of Impact Toughness in coarse-grain heat-affected zone of HSLA steel with increasing welding heat input // Metal. Mater. Trans. A. 2015. V. 46A. № 7. P. 2999–3014.
Дополнительные материалы отсутствуют.
Инструменты
Физика металлов и металловедение