Физика металлов и металловедение, 2021, T. 122, № 6, стр. 588-599
Повышение коэрцитивной силы порошков Sm2Fe17N3 механическим измельчением с применением поверхностно-активных веществ
Д. А. Колодкин a, *, А. Г. Попов a, b, В. С. Гавико a, b
a Институт физики металлов УрО РАН
620108 Екатеринбург, ул. С. Ковалевской, 18, Россия
b Институт естественных наук и математики, Уральский Федеральный университет
620002 Екатеринбург, ул. Мира, 19, Россия
* E-mail: kolodkin@imp.uran.ru
Поступила в редакцию 15.12.2020
После доработки 27.01.2021
Принята к публикации 01.02.2021
Аннотация
Проведено систематическое исследование влияния процесса механического измельчения нитрида Sm2Fe17N3 в вибрационной мельнице, включая отношение массы шаров и порошка m, времени измельчения tmill, среды измельчения и концентрации дополнительных вводимых поверхностно-активных веществ (ПАВ), с целью выявления оптимальных параметров, обеспечивающих наиболее высокий уровень гистерезисных свойств магнитно-анизотропного порошка. Показано, что при увеличении m от 15 до 50 прирост коэрцитивной силы Hc порошка на начальных стадиях измельчения (tmill ≤ 4 ч) существенно ускоряется, при этом около 80% частиц имеют размер менее 1 мкм. С увеличением длительности помола (tmill > 4 ч) коэрцитивная сила продолжает увеличиваться, однако удельная остаточная намагниченность σr и максимальное энергетическое произведение (BH)max начинают снижаться из-за развивающегося процесса агломерации частиц, приводящего к ухудшению текстуруемости порошка. Добавка ПАВ к защитным жидкостям заметно интенсифицирует процесс и ускоряет кинетику роста Hc на начальных стадиях измельчения при m = 15. Наилучшей комбинацией магнитных гистерезисных свойств σr ≥ 135 Гс см3/г, Hc ≥ 8 кЭ и (BH)max ≥ 18 МГс Э обладают порошки, измельченные в 5%-ных растворах олеиновой кислоты в ацетоне и капроновой кислоты в толуоле, а также в 1%-ном растворе метилкапроата в толуоле.
1. ВВЕДЕНИЕ
Магнитно-анизотропные порошки соединения Sm2Fe17N3 являются одним из наиболее перспективных материалов для производства магнитопластов [1–3], металлопластов [4–6] и субмикрокристаллических магнитов, спеченных при низкой температуре методом искрового плазменного спекания (ИПС или SPS – spark plasma sintering) [7–14]. Исходные порошки для изготовления анизотропных магнитов Sm–Fe–N должны иметь высокие значения остаточной индукции Br и коэрцитивной силы Нс. Восстановительная диффузия [15–18] и механическое измельчение [19–22] – наиболее распространенные методы для получения таких порошков. Крупнозернистые порошки Sm2Fe17N3 с размером частиц 20–100 мкм после азотирования обладают низкой коэрцитивной силой (0.5–1.5 кЭ). Их Нс повышается с уменьшением размера частиц D менее 1 мкм и приближением к однодоменному состоянию. Экспериментальная оценка размера однодоменности составляет 0.3 мкм [23]. Уменьшить размер частиц порошка Sm–Fe–N менее, чем 2–3 мкм методом традиционного измельчения в вибрационных, шаровых или струйных мельницах представляет собой сложную проблему. Увеличение времени измельчения и применение высокоэнергетических шаровых мельниц для приготовления тонких порошков приводит к образованию агломератов субмикронных частиц, которые не только препятствуют текстурованию порошка в магнитном поле, уменьшая его остаточную намагниченность, но и снижают коэрцитивную силу. Более того, Wang с соавторами показали, что по сравнению с высокоэнергетическим измельчением низкоэнергетический шаровой помол оказывается более приемлемым для повышения Нс и Br порошков [21]. Таким образом, оптимизация процесса получения анизотропных ультрадисперсных порошков Sm–Fe–N становится ключевой задачей.
Одним из активно разрабатываемых подходов к приготовлению субмикронных и наноструктурированных магнитных порошков интерметаллидов является механическое измельчение в среде защитных жидкостей с добавлением поверхностно-активных веществ (ПАВ) [24–29]. Согласно теории Ребиндера [30], молекулы и/или атомы ПАВ, взаимодействуя с поверхностью частиц порошка, уменьшают их поверхностную энергию и снижают механическую прочность материала. Под действием капиллярных сил молекулы ПАВ мигрируют по стенкам микротрещин и, развивая в них высокое внутреннее давление, способствуют дополнительному измельчению частиц порошка. С другой стороны, мелкие частицы, свежие сколы которых покрыты мономолекулярным слоем ПАВ, понижающим поверхностную энергию, в значительно меньшей степени склонны к образованию агломератов и последующей “холодной сварке” частиц под воздействием ударов шаров. Таким образом, действие ПАВ способствует формированию субмикронных порошков с узким распределением частиц по размерам.
Олеиновая кислота (ОК), растворенная в гептане, является наиболее часто используемым поверхностно-активным веществом для приготовления субмикронных частиц Sm2Fe17N3 [31–34]. Однако из-за высокой температуры кипения (360°С) ОК очень трудно удалить с поверхности частиц, а ее остатки значительно ухудшают коррозионную стойкость порошка. Окисление порошка происходит особенно интенсивно, если он используется для консолидации методом SPS. Не было представлено убедительного объяснения широкого использования ОК, и лишь несколько исследований отклонились от этой тенденции. В частности, в предшествующей работе мы проводили измельчение порошка Sm2Fe17N3, применяя в качестве ПАВ порошок стеарата цинка, растворенный в толуоле [35].
В настоящем исследовании мы расширили ряд ПАВ, растворенных в различных защитных жидкостях, для получения субмикронных магнитотвердых порошков Sm2Fe17N3 измельчением в вибрационной мельнице. Представлены результаты по оптимизации соотношения массы шаров и порошка, времени измельчения, концентрации ПАВ и среды измельчения, которые обеспечивают наиболее высокий уровень магнитных гистерезисных свойств магнитно-анизотропного порошка Sm2Fe17N3.
2. МЕТОДИКА ЭКСПЕРИМЕНТА
Исходный сплав Sm2.08Fe17 был изготовлен на Уральском электромеханическом заводе по технологии strip-casting [35]. Скорость вращения колеса при разливке составляла около 1 м/с. Пластинки сплава Sm2.08Fe17 имели толщину 0.2–0.3 мм и ширину около 3 см. Сплав гомогенизировали при температуре 1000°С в течение 1 ч. Для получения порошков пластинки сплава предварительно гидрировали в течение 4 ч при температуре 250°С и давлении водорода 2 атм. Гидрированный сплав измельчали в ступке до размера частиц менее 56 мкм и затем азотировали в течение 4 ч при температуре 500°С в смеси газов H2 и N2 при давлении 2 атм. Для полного удаления водорода после азотирования порошок дополнительно отжигали в вакууме при 350°С, 1 ч. Концентрацию азота х в нитриде Sm2Fe17Nx контролировали взвешиванием порошка до и после азотирования. Азотированные порошки измельчали в вибрационной мельнице при соотношении массы шаров mb и порошка mp от 15 до 50 в среде толуола, гексана, гептана и ацетона с добавками поверхностно-активных веществ. В качестве ПАВ использовали олеиновую, капроновую кислоту и метиловый эфир капроновой кислоты (метилкапроат). Все операции по загрузке, выгрузке и сушке гидрированного, азотированного и измельченного порошка осуществляли в перчаточном боксе, заполненном азотом. Концентрация остаточного кислорода в боксе не превышала 200 ppm. Перед измерением магнитных характеристик азотированные порошки текстуровали в магнитном поле напряженностью 12 кЭ и затем намагничивали в импульсном магнитном поле напряженностью 60 кЭ. Кривые размагничивания измеряли с помощью вибрационного магнетометра Lake Shore с максимальным намагничивающим полем 17 кЭ. Данные рентгеновской дифракции получены на рентгеновском дифрактометре Empyrean (PANanalytical) в Cu Kα-излучении. Изображения микроструктуры порошков получены на настольном сканирующем электронном микроскопе Phenom ProX, оборудованном микроанализатором.
3. РЕЗУЛЬТАТЫ И ОБСУЖДЕНИЕ
3.1. Исследование влияния соотношения масс шаров и порошка на интенсивность измельчения
Интенсивность процесса измельчения контролировали изменением соотношения масс шаров и загружаемого порошка. На рис. 1 (а–г) показаны кривые размагничивания и зависимости магнитных параметров порошков (рис. 1д–1з), измельченных в толуоле, от времени измельчения tmill и соотношения масс шары/порошок m = = mb/mp. С увеличением tmill при m ≤ 40 максимальная удельная намагниченность σ17, измеренная в максимальном намагничивающем поле Н = 17 кЭ, сначала несколько увеличивается, а после достижения максимума при tmill = 2 ч монотонно снижается. При m = 50 максимум на зависимости σ17(tmill) отсутствует. Значения σ17 определяются намагниченностью насыщения материала порошка, но, в большей мере, степенью текстуры порошков. Повышение σ17 при увеличении времени измельчения до 2 ч связано с тем, что часть частиц, которые после азотирования оказались в поликристаллическом состоянии, разбивается на монокристаллические фрагменты, и степень текстуры порошка, ориентированного в магнитном поле, повышается. Монотонное снижение σ17 при tmill > 2 ч обусловлено тремя основными причинами: увеличением доли мелких частиц, повышением плотности дефектов и малоугловых границ в частицах и образованием поликристаллических агломератов субмикронных зерен. Все три эффекта проявляются тем сильнее, чем больше m.
Рис. 1.
Кривые размагничивания (а–г) и зависимости магнитных параметров порошков (д–з) от времени измельчения tmill в толуоле и соотношения масс шаров и порошка m.
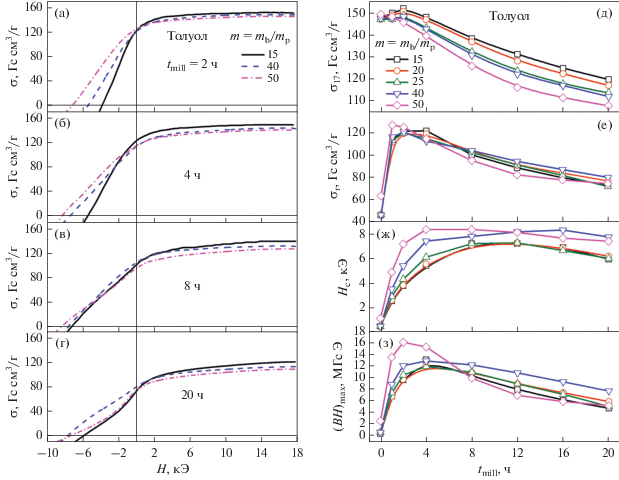
Коэрцитивная сила порошков (рис. 1ж) резко увеличивается при непродолжительном времени измельчения и возрастает тем быстрее, чем больше m. Как правило достигается максимум Нс, положение которого смещается к меньшим значениям tmill с увеличением m. Значения удельной остаточной намагниченности σr (рис. 1е) зависят как от поведения σ17(tmill), так и Нс(tmill). Отчетливый максимум σr достигается при tmill = 4 ч в порошке, измельченном при m = 15, и сдвигается к 1 ч при m = 50. Наиболее высокое максимальное энергетическое произведение (BH)max реализовано интенсивным измельчением порошка при соотношении m = 50 в течение 2 ч. Однако такой режим измельчения приводит к наиболее быстрому снижению как σr, так и (BH)max из-за прогрессирующего процесса агломерации частиц.
Структурное состояние порошков рассмотрим на примере образцов, полученных измельчением с малыми и большими значениями m и tmill. На рис. 2 показаны кривые размагничивания порошков, выбранных для структурного исследования. Исходный азотированный порошок (кривая размагничивания 1) имеет низкую коэрцитивную силу Нс = 1.34 кЭ и самое высокое значение σ17 = = 151.3 Гс см3/г. Измельчение порошков в течение 4 ч существенно увеличивает Нс, но при этом значения σr и σ17 начинают снижаться. После длительного измельчения (20 ч), помимо продолжающегося снижения σr и σ17 порошков, ухудшается прямоугольность кривых размагничивания, что свидетельствует о неоднородности гистерезисных свойств частиц порошков.
Рис. 2.
Кривые размагничивания порошков исходного нитрида (1), измельченного порошка в среде толуола в течение 4 (2) и 20 ч (3) при m = 15, в течение 4 (4) и 20 ч (5) при m = 50.
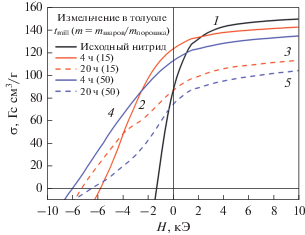
На рис. 3 показано сравнение дифрактограмм исходного азотированного порошка и порошков, измельченных в толуоле с соотношением масс шаров и порошка m = 15 и 50 в течение 4 и 20 ч. Фазовый состав и параметры решетки фаз представлены в табл. 1. Исходный азотированный порошок оказывается практически однофазным. Количество V магнитомягкой фазы α-Fe в нем не превышает 1.8%. Значения параметров а и с ромбоэдрической решетки фазы Sm2Fe17 исходного сплава составляли 8.553 и 12.443 Å соответственно. Параметры а и с фазы Sm2Fe17Nx азотированного порошка существенно увеличились, что указывает на то, что значение х ≈ 3, т.е. атомы азота почти полностью заселяют позиции внедрения 9е [22, 36, 37]. После измельчения при соотношении m = 15 в течение 4 ч дифракционные линии фазы Sm2Fe17Nх несколько уширяются, указывая на уменьшение размера зерен. Сильное уширение линий этой фазы после измельчения в течение 20 ч (рис. 3в) происходит не только из-за уменьшения размера зерен, но также и вследствие повышения плотности дефектов, на что указывает 10-кратное увеличение степени деформации. Количество фазы α-Fe при этом возрастает до 10.6%. Оба этих фактора приводят к появлению множества частиц с пониженной Hc, и на кривой размагничивания (кривая 3 на рис. 2) появляется перегиб, свидетельствующий о неоднородности магнитной твердости порошка. Наиболее высокая коэрцитивная сила реализована интенсивным измельчением при соотношении m = 50 в течение 4 ч. Несмотря на это, объемная доля фазы α-Fe в этом порошке составила 4.3% (рис. 3г), наиболее оптимальное структурное состояние порошка с областями когерентного рассеяния (ОКР) от фазы 2:17 в 24 нм позволило достичь Нс = 8.2 кЭ. Увеличение времени измельчения до 20 ч при m = 50 привело к ярко выраженному эффекту “замола”. Количество фазы α-Fe повысилось до 13%, линии фазы 2:17 существенно уширились, что позволяет судить о начале процесса ее аморфизации. Эти структурные изменения привели к снижению Нс и к появлению прогиба на кривой размагничивания (кривая 5 на рис. 2).
Рис. 3.
Дифрактограммы исходного азотированного порошка и порошков, измельченных в толуоле с соотношением масс шаров и порошка m = 15 и m = 50 в течение 4 и 20 ч.
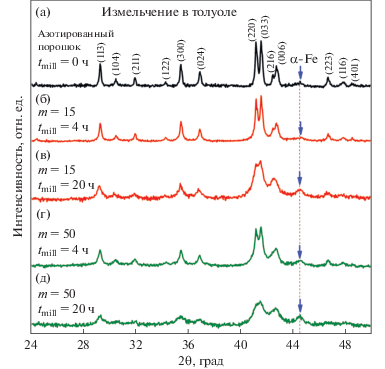
Таблица 1.
Фазовый состав и параметры решетки фаз
m | tmill, ч | Фазовый состав | ||||||
---|---|---|---|---|---|---|---|---|
Sm2Fe17Nх | α-Fe | |||||||
a, Å | с, Å | V, % | ОКР, нм | деформация, % | а, Å | V, % | ||
0 | 8.761 | 12.692 | 98.2 | 100–120 | 0.08 | 2.865 | 1.8 | |
15 | 4 | 8.762 | 12.694 | 98.1 | 35 | 0.01 | 2.885 | 1.9 |
20 | 8.772 | 12.725 | 89.4 | 12 | 0.10 | 2.884 | 10.6 | |
50 | 4 | 8.765 | 12.705 | 95.7 | 24 | 0.10 | 2.883 | 4.3 |
20 | 8.761 | 12.679 | 86.7 | 10 | 1.00 | 2.883 | 13.0 |
На рис. 4 показана микроструктура исходного азотированного порошка и порошков, измельченных при соотношении m = 15 и 50 в течение 4 и 20 ч. Гистограммы распределения частиц по размерам в этих порошках представлены на вставке (рис. 4б, 4в). Для исходного азотированного порошка (рис. 4а) распределение частиц по размерам является бимодальным (рис. 4б). Наряду с частицами размером ~30–50 мкм порошок состоит из большого количества (>30%) мелких частиц размером менее 10 мкм. Средний размер частиц dср исходного порошка, определенный из анализа микроснимков, составил 17.9 мкм.
Рис. 4.
Микроструктура порошка исходного нитрида (а) и порошков после измельчения в толуоле в течение 4 (г) и 20 ч (д) при m = 15; 4 (е) и 20 ч (ж) при m = 50; гистограммы распределения по размерам частиц исходного порошка и порошков после измельчения в толуоле в течение 4 и 20 ч при m = 15 (б) и при m = 50 (в).
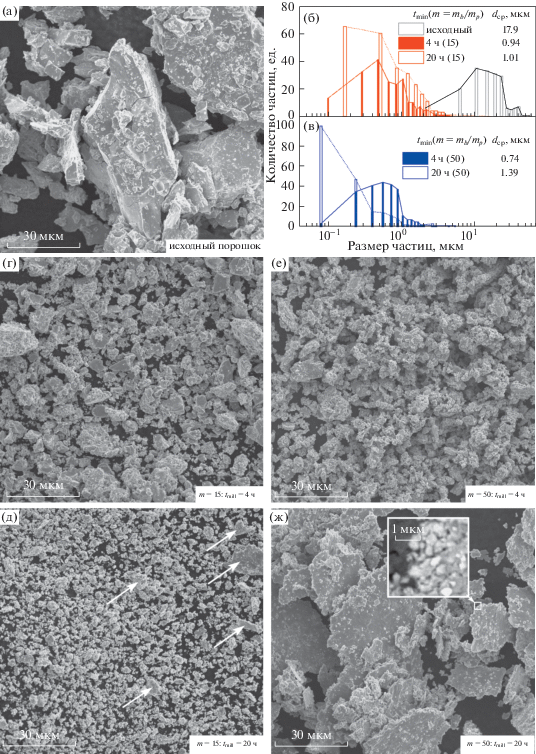
Измельчение порошка при соотношении m = 15 в течение 4 ч (рис. 4г) привело к уменьшению размера частиц до dср = 0.94 мкм. Коэрцитивная сила порошка при этом повысилась до 5.8 кЭ (кривая 2 на рис. 2). Распределение частиц по размерам сохранило бимодальный характер (рис. 4б). Количество мелких частиц размером менее 0.7 мкм выросло до 60%, а количество частиц размером, близким к состоянию однодоменности (<0.3 мкм) [23], составило более 15%. Крупные и мелкие частицы имеют тенденцию к слипанию, образуя блоки. Магнитный момент субмикронных частиц оказывается недостаточным для преодоления сил взаимодействия с крупными частицами и идеального выстраивания своих осей легкого намагничивания вдоль ориентирующего магнитного поля при текстуровании. Этот фактор наряду с повышением плотности дефектов и малоугловых границ в частицах приводит к снижению значений σ17 и σr текстурованного порошка. После измельчения в течение 20 ч (рис. 4д) доля частиц с dср < < 1 мкм составила более 80%, а количество частиц размером, близким к состоянию однодоменности, превысило 25% (рис. 4б). Это привело к увеличению Нс до 7.3 кЭ (кривая 3 на рис. 2). Однако в процессе длительного помола под воздействием удара шаров мелкие частицы подвергаются холодной сварке и формированию поликристаллических агломератов субмикронных зерен с разориентированными осями легкого намагничивания. На рис. 4д такие агломераты показаны стрелками. Появление агломератов становится дополнительным фактором, способствующим снижению σ17 и σr. Кроме того, как было отмечено выше, количество магнитомягкой фазы α-Fe возрастает до 10.6%, и это наряду с неоднородностью распределения частиц по размерам приводит к появлению перегиба на кривой размагничивания.
В сравнении с m = 15 более интенсивное измельчение при m = 50 привело к смещению гистограммы распределения частиц порошка по размерам в сторону меньших значений (рис. 4в). После 4 ч помола распределение частиц по размерам стало более однородным. Количество мелких частиц с dср < 1 мкм в этом порошке увеличилось до 80%, а значение dср снизилось до 0.74 мкм. Это наиболее оптимальное структурное состояние порошка обеспечило повышение значения Hc до 8.06 кЭ. В результате сильной агломерации после измельчения в течение 20 ч при m = 50 порошок представляет совокупность крупных поликристаллических пластинок, которые, как показывает изображение с большим увеличением на вставке рис. 4ж, состоят из субмикронных зерен. Доля частиц размером менее 0.3 мкм в этих агломератах выросла до 60%. Следует отметить, что из-за эффекта агломерации частиц порошки после измельчения в течение 20 ч дают более высокую оценку величины dср как при m = 15 (1.01 мкм), так и при m = 50 (1.39 мкм) по сравнению с порошками, измельченными 4 ч. Измельчение 20 ч при m = 50 привело к самым низким значениям σ17 и σr, понижению Hc до 5.82 кЭ и существенному ухудшению прямоугольности кривой размагничивания (рис. 2, кривая 5). Причинами снижения гистерезисных характеристик являются интенсивный процесс агломерации частиц и появление большого количества фазы α-Fe.
Таким образом, наиболее благоприятным сочетанием магнитных гистерезисных параметров σ17, σr, Hc и (BH)max обладают порошки после измельчения при 2 ≤ tmill ≤ 4 ч. В дальнейших экспериментах по выбору оптимальных условий измельчения в различных защитных жидкостях с применением добавки нескольких ПАВ мы по-прежнему будем проводить помол до tmill = 20 ч, однако более пристальное внимание будет уделено изменению гистерезисных свойств порошков на начальной стадии измельчения.
3.2. Влияние химии рабочих жидкостей (толуол, ацетон, гексан, гептан) на кинетику свойств порошков при измельчении
При измельчении порошков использовали не только толуол, но и другие органические защитные жидкости: гексан, гептан и ацетон. Химические формулы и некоторые свойства этих жидкостей представлены в табл. 2. Основные требования, которые предъявляются к защитным жидкостям, это недопустимость растворения кислорода воздуха и отсутствие химического взаимодействия с материалом порошка. Поскольку эти жидкости в последующих экспериментах планировались для использования в качестве растворителей добавок ПАВ, то предстояло выяснить, в какой степени их собственные свойства оказывают влияние на магнитные характеристики измельчаемого порошка.
Таблица 2.
Свойства жидкостей – защитных сред
Защитная жидкость | Формула | Структурная форма | Молярная масса, M (г/моль) | Плотность, Ρ (г/см3) | Динамическая вязкость, ƞ (мПа с) | Температура кипения, Tb (°С) |
---|---|---|---|---|---|---|
Толуол | С7Н8 | ![]() |
92.14 | 0.8669 | 0.584 | 110.62 |
Гексан | C6H14 | ![]() |
86.18 | 0.6548 | 0.307 | 68 |
Гептан | C7H16 | ![]() |
100.21 | 0.6795 | 0.414 | 98.42 |
Ацетон | C3H6O | ![]() |
58.08 | 0.7899 | 0.325 | 56.1 |
Толуол относится к аренам – циклическим органическим соединениям. В молекуле толуола один атом водорода, связанный с углеродом бензольного кольца, замещен на метильную группу СН3. Гексан и гептан относятся к классу алканов – ациклических углеводородов линейного строения, содержащих только простые связи и образующие гомологический ряд с общей формулой CnH2n + 2. Молекулы гексана и гептана состоят из шести и семи связанных друг с другом метиленовых групп CH2, соответственно. Ацетон относится к насыщенным кетонам – органическим веществам, в молекулах которых карбоксильная группа СО связана с двумя метильными группами СН3. Наличие атома кислорода в этой структуре предопределяет возможность поверхностно активного воздействия молекул ацетона на частицы измельчаемого порошка. Как следует из табл. 2, толуол обладает наибольшими значениями ρ, η и Tb, ацетон – наименьшими M и Tb.
На рис. 5 показана зависимость магнитных свойств от времени измельчения tmill для порошков, измельченных в толуоле, гексане, гептане и ацетоне при соотношениях масс шаров и порошка m = 15 (а–г) и m = 50 (д–з). На начальных стадиях измельчения (tmill ≤ 4 ч) с соотношением m = 15 наиболее низкие значения Нс имеют порошки, измельченные в толуоле и гексане. Кроме того, порошки после измельчения в толуоле имеют самые низкие значения σr и (BH)max при всех временах измельчения. С другой стороны, ацетон, обладающий свойствами ПАВ, обеспечивает наиболее высокие значения σr, Hc и (BH)max порошков в широком интервале времен измельчения. После измельчения порошка в ацетоне в течение 8 ч его (BH)max достигло 18.2 МГсЭ. Однако при интенсивном измельчении при m = 50 активный ацетон по сравнению с пассивным толуолом дает лишь небольшой выигрыш в значениях Нс при 2 ≤ tmill ≤ 8 ч (рис. 5ж). Более низкими значениями (BH)max при всех временах измельчения обладали порошки, измельченные в ацетоне (рис. 5з). Таким образом, интенсивный помол в ацетоне при m = 50 не обеспечил существенного повышения уровня магнитных свойств, но позволил получить максимальные значения Hc и (BH)max за более короткие времена измельчения (tmill ≤ 4 ч). На основании этого результата в последующих экспериментах по измельчению порошка с добавками ПАВ, таких как олеиновая, капроновая кислоты и метилкапроат был использован более мягкий режим помола в вибромельнице при m = 15.
3.3. Влияние поверхностно-активных веществ на интенсивность измельчения и кинетику свойств измельченных порошков
Для интенсификации измельчения на начальных стадиях применяли добавки ПАВ. Химические формулы и некоторые свойства использованных ПАВ представлены в табл. 3. Молекулы использованных ПАВ имеют цепную структуру. Они легко поляризуются со стороны карбоксильных групп COOH, и полярными концами активно взаимодействуют с поверхностью измельчаемых частиц металлического сплава.
Таблица 3.
Свойства ПАВ
ПАВ | Химическая формула Рациональная формула |
Описание | Молярная масса, г/моль | Плотность, г/см3 | Температура кипения, °C |
---|---|---|---|---|---|
Олеиновая кислота | C18H34O2 C17H33COOH |
Мононенасыщенная жирная кислота | 282.46 | 0.895 | 360 |
Капроновая кислота | C6H12O2 СH3(CH2)4СООН |
Одноосновная предельная карбоновая кислота | 116.16 | 0.920 | 203 |
Метилкапроат | C7H14O2 CH3(CH2)4COOCH3 |
Метиловый эфир капроновой кислоты | 130.19 | 0.884 | 152 |
3.3.1. Влияние концентрации олеиновой кислоты, добавляемой в гептан при измельчении, на магнитные свойств порошка. Раствор олеиновой кислоты (ОК) в гептане наиболее часто используется в качестве поверхностно активной среды для получения субмикрокристаллических и нанокристаллических порошков интерметаллических соединений механическим измельчением [31–34]. Концентрация ОК при этом варьируется в очень широких пределах от нескольких единиц до 100% по отношению к массе порошка. В своем эксперименте мы использовали концентрации ОК 0, 5, 10 и 15%; зависимости магнитных свойств от tmill показаны на рис. 6. Добавка ОК при всех концентрациях увеличивает как скорость прироста Нс, так и саму величину Нс. Вследствие этого на начальной стадии процесса измельчения наблюдается прирост значений σr (tmill ≤ 2 ч) и (BH)max (tmill ≤ 4 ч). При дальнейшем увеличении tmill значения σm, σr и (BH)max порошков, измельченных с добавкой ПАВ, быстро понижаются из-за ухудшения текстуруемости порошка подобно тому, как это имело место при увеличении соотношения m.
Рис. 6.
Зависимости магнитных свойств от tmill и концентрации олеиновой кислоты, добавляемой в толуол.
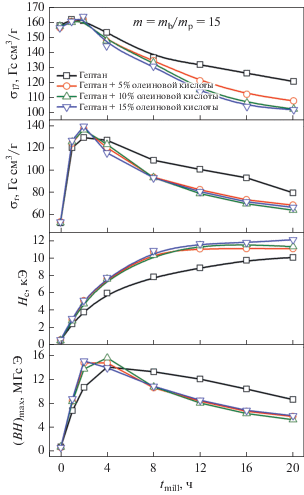
Сушка порошка, измельчаемого с повышенной концентрацией ОК, затруднена. После испарения гептана порошок представляет собой маслянистую пасту. Для того чтобы продолжать дальнейшее экспериментальное исследование такого порошка приходится проводить длительную и тщательную его промывку в органических растворителях (гексан, ацетон, толуол). Поскольку оказалось, что магнитные свойства порошков некритическим образом изменяются при увеличении концентрации ОК от 5 до 15%, в дальнейших экспериментах мы использовали преимущественно 5%-концентрацию как олеиновой кислоты, так и других ПАВ.
3.3.2.Влияние добавки олеиновой кислоты в различные защитные жидкости на магнитные свойства порошка. Олеиновую кислоту добавляли также в толуол, гексан и ацетон. На рис. 7 показана зависимость магнитных свойств порошков от времени измельчения в толуоле, гексане, гептане и ацетоне с добавкой 5% ОК при m = 15. Сравнивая зависимости гистерезисных характеристик от tmill на этом рисунке и на рис. 5, где приведены подобные данные об измельчении порошков в чистых жидкостях, следует отметить их качественное подобие. Отличительной особенностью является более быстрый рост Нс на начальной стадии измельчения (tmill ≤ 4 ч). Прирост Нс от введения 5% ОК в интервале 2 ≤ tmill ≤ 4 ч составляет 2–4 кЭ. Наибольший прирост Нс наблюдается у порошков, измельченных в толуоле и гексане, однако самая высокая коэрцитивная сила сохраняется у порошка, измельченного в ацетоне. В результате ускоренной кинетики роста Нс максимальное значение (BH)max = 18 МГс Э для этого порошка достигается после 2–4 ч измельчения, а не после 8 ч, как это имело место при помоле без добавки ОК.
Рис. 7.
Зависимость магнитных свойств порошков от времени измельчения в толуоле, гексане, гептане и ацетоне при m = 15 и добавке 5% ОК.
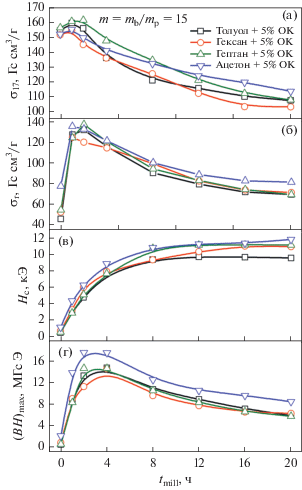
3.3.3. Влияние добавки в толуол капроновой кислоты и метилкапроата на магнитные свойства. Ранее Crouse с соавторами для приготовления наноструктурного порошка SmCo5 использовали в качестве ПАВ широкий ряд карбоновых кислот [27]. Они показали, что применение в качестве ПАВ карбоновых кислот с меньшей, чем ОК, молекулярной массой способствует не только более легкому удалению с поверхности измельченных частиц слоя адсорбированных молекул, но и способствует достижению меньшего размера частиц и, как следствие, повышению Нс порошков. Опираясь на результаты этой работы, при измельчении порошка Sm2Fe17N3 мы использовали капроновую кислоту (КК) с меньшей молярной массой, а также метилкапроат (МК), являющийся эфиром КК. Ранее метилкапроат был нами успешно применен при измельчении порошка сплава Nd–Fe–B, который далее был задействован в PLP-технологии (PLP – pressless process – процесс без прессования) [38]. На рис. 8 (а–г) сравниваются зависимости магнитных свойств от tmill для порошков, измельченных в толуоле, а также с добавкой в толуол 5% олеиновой и капроновой кислот. Значения Нс и (BH)max оказываются самыми высокими при добавке КК при всех временах измельчения. Отличительной особенностью добавки метилкапроата в толуол заключается в том, что при достаточно быстром повышении Нс при увеличении tmill до 8 ч значения σm и σr снижаются достаточно медленно (рис. 8д–8ж). В результате максимальные значения (BH)max достигаются при высоком уровне Нс. Уменьшение концентрации метилкапроата от 5 до 1% способствует повышению значений σm, σr и (BH)max. Отметим, что добавка 1% метилкапроата в толуол превратила его из самой малоэффективной защитной жидкости при измельчении в активную среду, похожую на поверхностно-активный ацетон по своему воздействию на структуру и магнитные свойства порошка. Для сравнения зависимости магнитных свойств порошка от времени измельчения в ацетоне на рис. 8 (д–з) приведены пунктирными линиями.
4. ЗАКЛЮЧЕНИЕ
В настоящей работе проведена детальная оптимизация процесса измельчения в вибрационной мельнице порошка Sm2Fe17N3, синтезированного из сплава типа strip-casting отечественного производства. В результате системного исследования влияния на структуру и магнитные свойства порошка ряда ПАВ, вводимых в защитные органические жидкости при измельчении, получены магнитно-анизотропные порошки Sm2Fe17N3 с максимальным энергетическим произведением (BH)max более 18 МГс Э. Эти порошки обладают наилучшей комбинацией магнитных гистерезисных свойств среди аналогов, реализованных в России [36, 37, 39, 40].
На основании полученных результатов сделаны следующие основные выводы:
1. Показано, что интенсивность процесса измельчения порошка в толуоле возрастает по мере увеличения соотношения масс шаров и порошка m = mb/mp от 15 до 50. При увеличении времени измельчения tmill до 2–4 ч доля субмикронных частиц приближается к 80%, значение Hc повышается до 8 кЭ, а (BH)max достигает максимума. Длительное измельчение (tmill > 4ч) приводит к ухудшению текстуруемости порошка и прямоугольности кривых размагничивания из-за повышения плотности дефектов и малоугловых границ в частицах, усиления процесса агломерации частиц и возрастания объемной доли магнитомягкой фазы α-Fe.
2. Установлено, что органические жидкости (толуол, гексан, гептан и ацетон), используемые для предотвращения контакта порошка с кислородом воздуха, оказывают различное влияние на магнитные свойства измельчаемого порошка. Наиболее низкими гистерезисными свойствами обладал порошок, измельченный в толуоле, имеющем самые высокие значения плотности, динамической вязкости и температуры кипения. С другой стороны, порошок, измельченный в ацетоне, который проявляет свойства поверхностно-активного вещества, имел наилучшее сочетание гистерезисных характеристик, включая (BH)max ≥ 18.2 МГс Э, при tmill = 8 ч и m = 15.
3. Введение поверхностно-активных добавок к защитным жидкостям позволило существенно интенсифицировать процесс измельчения на начальных стадиях (tmill ≤ 4 ч) и, соответственно, ускорить кинетику роста Hc. Наилучшее сочетание магнитных гистерезисных свойств σr ≥ 135 Гс см3/г, Hc ≥ 8 кЭ и (BH)max ≥ 18 МГс Э получено при измельчении порошка в растворе 5% олеиновой кислоты в ацетоне. Подобные характеристики удалось реализовать при добавках 5% капроновой кислоты и 1% метилкапроата в толуол, которые превратили толуол из самой пассивной в наиболее активную защитную жидкость при измельчении.
Работа была выполнена в рамках государственного задания МИНОБРНАУКИ России (тема “Магнит” № АААА-А18-118020290129-5). Рентгеноструктурные исследования и измерения магнитных свойств проведены в Центре коллективного пользования Института физики металлов им. М.Н. Михеева Уральского отделения РАН, Екатеринбург, Россия.
Список литературы
Suzuki S., Miura T., Kawasaki M. Sm2Fe17Nx Bonded Magnets with High Performance // IEEE Trans. Magn. 1993. V. 29. № 6. P. 2815–2817.
Makita K., Hirosawa S. Coercivity of Zn evaporation-coated Sm2Fe17Nx fine powder and its bonded magnets // J. Alloys Compd. 1997. V. 260. № 1–2. P. 236–241.
Yamaguchi W., Soda R., Takagi K. Metal-coated Sm2Fe17N3 magnet powders with an oxide-free direct metal-metal interface // J. Magn. Magn. Mater. 2020. V. 498. 166101.
Otani Y., Moukarika A., Sun H., Coey J.M.D., Devlin E., Harris I.R. Metal bonded Sm2Fe17N3 – δ magnets // J. Appl. Phys. 1991. V. 69. № 9. P. 6735–6737.
Rodewald W., Wall B., Katter M., Velicescu M., Schrey P. Microstructure and magnetic properties of Zn- or Sn-bonded Sm2Fe17Nx magnets // J. Appl. Phys. 1993. V. 73. № 10. P. 5899–5901.
Matsuura M., Shiraiwa T., Tezuka N., Sugimoto S., Shoji T., Sakuma N., Haga K. High coercive Zn-bonded Sm–Fe–N magnets prepared using fine Zn particles with low oxygen content // J. Magn. Magn. Mater. 2018. V. 452. P. 243–248.
Tokita M. Trends in advanced SPS spark plasma sintering systems and technology // J. Soc. Powder Technol. Jpn. 1993. V. 30. № 11. P. 790–804.
Saito T. Production of Sm–Fe–N bulk magnets by spark plasma sintering method // J. Magn. Magn. Mater. 2014. V. 369. P. 184–188.
Zhang D., Yue M., Zhang J. Structure and magnetic properties of Sm2Fel7Nx sintering magnets prepared by spark plasma sintering // J. of Rare Earths. 2006. V. 24. № 1. Sup. 1. P. 325–328.
Saito T. Structures and magnetic properties of Sm–Fe–N bulk magnets produced by the spark plasma sintering method // J. Mater. Res. 2007. V. 22. № 11. P. 3130–3136.
Takagi K., Nakayama H., Ozaki K. Microstructural behavior on particle surfaces and interfaces in Sm2Fe17N3 powder compacts during low-temperature sintering // J. Magn. Magn. Mater. 2012. V. 324. № 15. P. 2336–2341.
Prabhu D., Sepehri-Amin H., Mendis C.L., Ohkubo T., Hono K., Sugimoto S. Enhanced coercivity of spark plasma sintered Zn-bonded Sm–Fe–N magnets // Scripta Materialia. 2012. V. 67. № 2. P. 153–156.
Dudina D.V., Mukherjee A.K. Reactive Spark Plasma Sintering: Successes and Challenges of Nanomaterial Synthesis // J. Nanomaterials. 2013. V. 11. ID 625218.
Saito T., Deguchi T., Yamamoto H. Magnetic properties of Sm–Fe–N bulk magnets produced from Cu-plated Sm–Fe–N powder // AIP Advances. 2017. V. 7. 056204.
Kawamoto A., Ishikawa T., Yasuda S., Takeya K., Ishizaka K., Iseki T., Ohmori K. Sm2Fe17N3 magnet powder made by reduction and diffusion method // IEEE Trans. Magn. 1999. V. 35. P. 3322–3324.
Lee J., Kang S., Si P., Choi C. The influence of mechanical milling on the structure and magnetic properties of Sm–Fe–N powder Produced by the reduction-diffusion process // J. Magnetics. 2011. V. 16. № 2. P. 104–107.
Okada S., Suzuki K., Node E., Takagi K., Ozaki K., Enokido Y. Preparation of submicron-sized Sm2Fe17N3 fine powder with high coercivity by reduction-diffusion process // J. Alloys Compd. 2017. V. 695. P. 1617–1623.
Okada S., Suzuki K., Node E., Takagi K., Ozaki K., Enokido Y. Improvement of magnetization of submicron-sized high coercivity Sm2Fe17N3 powder by using hydrothermally synthesized sintering-tolerant cubic hematite // AIP Advances. 2017. V. 7. 056219.
Wendhausen P.A.P., Gebel B., Eckert D., Műller K.-H. Effect of milling on the magnetic and microstructural properties of Sm2Fe17Nx permanent magnets // J. Appl. Phys. 1994. V. 75. № 10. P. 6018–6020.
Kobayashi K., Skomski R., Coey J.M.D. Dependence of coercivity on particle size in Sm2Fe17N3 powders // J. Alloys Compd. 1995. V. 222. № 1–2. P. 1–7.
Wang J.L., Li W.Z., Zhong X.P., Gao Y.H., Qin W.D., Tang N., Lin W.G., Zhang J.X., Zhao R.W., Yan Q.W., Yang Fu-ming Study on high performance Sm2Fe17Nx magnets // J. Alloys Compd. 1995. V. 222. № 1–2. P. 23–26.
Xing M., Han J., Wan F., Liu S., Wang C., Yang J., Yang Y. Preparation of anisotropic magnetic materials by strip casting technique // IEEE Trans. Magn. 2013. V. 49. № 7. P. 3248–3250.
Mukai T., Fujimoto T. Kerr microscopy observation of nitrogenated Sm2Fe17 intermetallic compounds // J. Magn. Magn. Mater. 1992. V. 103. № 1–2. P. 165–173.
Chakka V.M., Altuncevahir B., Jin Z.Q., Li Y., Liu J.P. Magnetic nanoparticles produced by surfactant-assisted ball milling // J. Appl. Phys. 2006. V. 99. № 8. 08E912.
Yue M., Wang Y.P., Poudyal N., Rong C.B., Liu J.P. Preparation of Nd–Fe–B nanoparticles by surfactant-assisted ball milling technique // J. Appl. Phys. 2009. V. 105. № 7. 07A708.
Poudyal N., Rong C., Liu J.P. Effects of particle size and composition on coercivity of Sm–Co nanoparticles prepared by surfactant-assisted ball milling // J. Appl. Phys. 2010. V. 107. № 9. 09A703.
Crouse C.A., Michel E., Shen Y., Knutson S.J., Hardenstein B.K., Spowart J.E., Leontsev S.O., Semiatin S.L., Horwath J., Turgut Z., Lucas M.S. Effect of surfactant molecular weight on particle morphology of SmCo5 prepared by high energy ball milling // J. Appl. Phys. 2012. V. 111. № 7. 07A724.
Zhao L., Akdogan N.G., Hadjipanayis G.C. Hard magnetic Sm2Fe17N3 flakes nitrogenized at lower temperature // J. Alloys Compd. 2013.V. 554. P. 147–149.
Ullah M., Ali Md.E., Hamid Sh.B.A. Surfactant-assisted ball milling: a novel route to novel materials with controlled nanostructure – a review // Rev. Adv. Mater. Sci. 2014. V. 37. P. 1–14.
Ребиндер П.А., Щукин Е.Д. Поверхностные явления в твердых телах в процессах их деформации и разрушения // УФН. 1972. Т. 108. № 1. С. 3–42.
Ma X.B., Li L.Z., Liu S.Q., Hu B.Y., Han J.Z., Wang C.S., Du H.L., Yang Y.C., Yang J.B. Anisotropic Sm–Fe–N particles prepared by surfactant-assisted grinding method // J. Alloys Compd. 2014. V. 612. P. 110–113.
Yue M., Li Y.Q., Liu R.M., Liu W.Q., Guo Z.H., Li W. Abnormal size-dependent coercivity in ternary Sm–Fe–N nanoparticles // J. Alloys Compd. 2015. V. 637. P. 297–300.
Lu C., Hong X., Bao X., Gao X., Zhu J. Changing phase equilibria: A method for microstructure optimization and properties improvement in preparing anisotropic Sm2Fe17N3 powders // J. Alloys Compd. 2019. V. 784. P. 980–989.
Li Y., Wang F., Liu J.P., Wang F., Wang S., Zhang J. Fabrication of remarkably magnetic-property-enhanced anisotropic Sm2Fe17Nx nanoflakes by surfactant assisted ball milling at low temperature // J. Magn. Magn. Mater. 2020. V. 498. 166191.
Kolodkin D.A., Popov A.G., Protasov A.V., Gaviko V.S., Vasilenko D.Yu., Kavita S., Prabhu D., Gopalan R. Magnetic properties of Sm2 + αFe17Nx powders prepared from bulk and strip-cast alloys // J. Magn. Magn. Mater. 2021. V. 518. 167416.
Менушенков А.П., Савченко А.Г., Иванов В.Г., Иванов А.А., Щетинин И.В., Менушенков В.П., Руднев И.А., Рафальский А.В., Жуков Д.Г., Платунов М., Вилхельм Ф., Рогалев А. Влияние процессов азотирования и гидрирования на магнитные свойства и структуру сплава Sm2Fe17: анализ XMCD данных // Письма в ЖЭТФ. 2018. Т. 107. № 4. С. 232–236.
Shchetinin I.V., Bordyuzhin I.G., Sundeev R.V., Menushenkov V.P., Kamynin A.V., Verbetsky V.N., Savchenko A.G. Structure and magnetic properties of Sm2Fe17Nx alloys after severe plastic deformation by high pressure torsion // Materials Letters. 2020. V. 274. 127993.
Popov A.G., Gaviko V.S., Shchegoleva N.N., Golovnia O.A., Gorbunova T.I., Hadjipanayis G.C. Effect of addition of esters of fatty acids on the microstructure and properties of sintered Nd–Fe–B magnets produced by PLP // J. Magn. Magn. Mater. 2015. V. 386. P. 134–140.
Тарасов В.П., Игнатов А.С., Кутепов Д.А. Разработка способов повышения коррозионной стойкости магнитотвердых материалов Sm2Fe17N3 // Металлург. 2016. № 11. С. 74–76.
Кутепов А.В., Тарасов В.П., Игнатов А.С. Оптимизация режимов азотирования порошков сплавов Sm2Fe17 // Металлург. 2016. № 12. С. 59–62.
Дополнительные материалы отсутствуют.
Инструменты
Физика металлов и металловедение