Физика металлов и металловедение, 2021, T. 122, № 6, стр. 608-613
Металлографическое исследование схождения медных цилиндрических оболочек при различной интенсивности взрывного нагружения
В. И. Зельдович a, *, А. Э. Хейфец a, Н. Ю. Фролова a, А. А. Дегтярев b, Е. Б. Смирнов b, Е. В. Шорохов b
a Институт физики металлов УрО РАН
620108 Екатеринбург, ул. С. Ковалевской, 18, Россия
b ФГУП “РФЯЦ–ВНИИТФ им. академ. Е.И. Забабахина
456770 Челябинской обл., Снежинск, а/я 245, Россия
* E-mail: zeldovich@imp.uran.ru
Поступила в редакцию 20.11.2020
После доработки 03.02.2021
Принята к публикации 09.02.2021
Аннотация
Исследован процесс высокоскоростного схождения медных цилиндрических оболочек диаметром 48 мм и толщиной стенки 4 мм при различной интенсивности взрывного нагружения. Описаны два структурных механизма потери устойчивости фронта радиальной деформации. Представлена схема структурных изменений, отражающая последовательные стадии процесса схождения. Выявлена взаимосвязь числа выступов на поверхности оболочек при их гофрировании с интенсивностью взрывного нагружения. Обнаружено, что высокоскоростная деформация в продольном направлении имеет при схождении пульсирующий характер. Установлено, что в центре сошедшейся оболочки температура повышается до ~500°С, а при высокоскоростном захлопывании откольных пор бывает выше 1000°С.
ВВЕДЕНИЕ
Схождение цилиндрических оболочек под действием взрыва является одним из методов экстремального воздействия на материалы. Поэтому исследование взрывного схождения оболочек представляет большой интерес для физического металловедения. Взрывное нагружение оболочек состоит в комбинированном воздействии на материал оболочки ударной волны и последующей высокоскоростной деформации [1–3]. Амплитуда давления ударной волны при скользящей детонации обычно составляет 10–20 ГПа, скорость деформации при инерционном схождении оболочки к оси симметрии – 104–105 1/с [3–5]. При взрывном нагружении цилиндрических оболочек были обнаружены новые структуры. В низкоуглеродистой стали было обнаружено явление баротермической закалки, в результате которой возникла мартенсито-перлитная структура с высокой твердостью [3, 4]. При схождении массивной медной оболочки высокоскоростная деформация происходила с образованием чередующихся мезополос с различной степенью деформации [5, 6].
Исследование структурных изменений при схождении оболочек позволяет зафиксировать особенности процесса, которые трудно обнаружить другими методами, и получить начальные условия для построения упруго-пластических моделей схождения. Сравнение структур в центре цилиндров, полученных при схлопывании массивных медной и стальной оболочек, показало, что температура в центре возрастает до значений выше температуры плавления меди (1083°С), но ниже, чем стали (1550°С). С использованием реперных точек (температур плавления и рекристаллизации) был выполнен расчет изменения температуры вдоль радиуса массивного медного цилиндра в момент его схлопывания [5].
Для того чтобы произошло схлопывание оболочки в сплошной цилиндр, подбирают такие условия нагружения, чтобы к концу схождения вся кинетическая энергия оболочки при инерционном схождении была израсходована на энергию деформации. Однако необходимо знать, как происходит процесс схождения в материале оболочки при недостатке и при избытке подводимой энергии. Цель настоящей работы – исследование влияния интенсивности взрывного нагружения на процесс схождения. При этом режимы нагружения подбираются таким образом, чтобы были реализованы три варианта схождения: оптимальный режим, режим с недостатком подводимой энергии и с ее избытком.
МАТЕРИАЛ И МЕТОДЫ ИССЛЕДОВАНИЯ
Цилиндрические оболочки из меди М1 диаметром 48 мм, толщиной стенки 4 мм и длиной 200 мм окружали цилиндрическим слоем пластического взрывчатого вещества (ВВ). Возбуждение детонационной волны в ВВ осуществляли с торца оболочки с помощью кольцевой системы инициирования. В результате взрыва вдоль боковой поверхности оболочек распространялась скользящая детонационная волна, под действием которой происходило схождение оболочки к оси симметрии. Интенсивность нагружения изменяли за счет изменения толщины слоя ВВ. Толщина слоя и результат нагружения представлены в табл. 1. Оболочки были приготовлены из отожженных прутков, микроструктура меди в исходном недеформированном состоянии состояла из зерен размером 200–300 мкм с многочисленными двойниками отжига. Для исследования макро- и микроструктуры были сделаны поперечные разрезы цилиндров, полученных при схождении оболочек. Металлографические исследования были выполнены на микроскопе EPITYP 2, фольги просматривали на электронном микроскопе Technai G2.
РЕЗУЛЬТАТЫ ИССЛЕДОВАНИЯ И ИХ ОБСУЖДЕНИЕ
Внешний вид и макроструктура поперечных разрезов нагруженных оболочек показали, что режимы нагружения отвечают поставленной задаче. Интенсивность нагружения оболочки № 1 было недостаточной для схлопывания. Оболочки № 4 и № 5 были нагружены при избытке подводимой энергии. Оболочки № 2 и № 3 были нагружены по оптимальному для полного схождения режиму.
Деформация оболочек
В ранее выполненной работе [7] было показано, что медная оболочка таких же размеров как в настоящей работе при слабой интенсивности нагружения (при толщине слоя ВВ 2 мм) разделилась при отколе на два кольца, и внутреннее кольцо не сошлось. Этот результат аналогичен полученному при схождения откольных слоев в стальных оболочках [8].
В оболочке № 1 разделение на кольца не произошло, но образовались большие откольные полости, расположенные под выступами (рис. 1а). В центральной части оболочки высокоскоростная деформация привела к возникновению выбросов, аналогичных описанным в [7]. Выбросы имеют гидродинамическое происхождение [7, 9], но медь в выбросах не испытывала плавления. Микроструктура на участке выброса состоит из субзерен размером 200–400 нм. Субзерна бывают как равноосные (рис. 2а), так и удлиненные (рис. 2б). Полученная структура свидетельствует о том, что произошла большая пластическая деформация, как, например, в пластических струях при сварке взрывом, описанных Рыбиным [10].
Рис. 2.
Электронно-микроскопические снимки структуры в участке выброса. Равноосные (а) и удлиненные (б) субзерна.
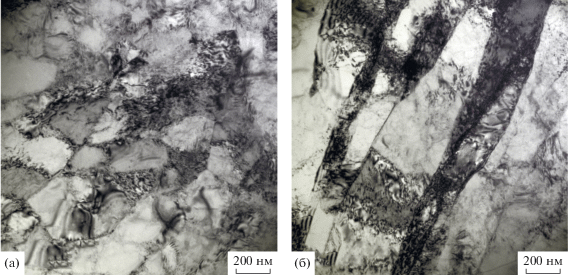
В оболочках № 2 и № 3, нагруженных по оптимальному режиму, разделение на кольца также не произошло, но возникли кольцевые зоны откольных повреждений, которые разделили оболочки на внутреннюю и наружную зоны (рис. 1б, 1в). В оболочке № 3 схождение внутренней зоны закончилось формированием фигуры в виде цветка (рис. 1в), как описано в [7]. Очевидно, что эта правильная фигура получилась в результате смыкания выбросов. В оболочке № 2 из-за нарушения симметрии вместо цветка возникли беспорядочные локализованные течения (рис. 1б). Заметим, что в центре оболочки № 3 осталась небольшая полость. При схождении оболочки № 4 (на участке оболочки, где не было разлета) полость отсутствовала (рис. 1г). В центре образовалась небольшая округлая зона, в которой началась рекристаллизация. Значит, температура в центре этой оболочки повысилась до ~500°С. Очевидно, что такая разница в схождении оболочек № 3 и № 4 связана с увеличением интенсивности нагружения. В остальном структура в приведенных поперечных сечениях хорошо воспроизводится.
Процесс схождения данных оболочек можно разделить на четыре стадии, как показано на схеме (рис. 3). В исходной оболочке (позиция 1) под действием ударной волны образуется зона откольных повреждений (позиция 2). Поры и трещины откольного происхождения располагаются в средней части по толщине оболочки. При дальнейшем инерционном схождении происходит высокоскоростная деформация меди (позиции 3–5). Оболочка становится толще, поэтому зона откольных явлений расширяется. Поры и трещины залечиваются при деформации, при этом формируется средняя зона хаотической деформации. Внутренняя и наружная поверхности оболочки теряют форму круга, возникают выступы и вмятины (позиция 3), происходит гофрирование. Это означает, что теряется устойчивость гладкого фронта деформации. Авторы [11] наблюдали такое явление при нагружении металлических труб с помощью высокого гидростатического давления. В нашем случае деформация является высокоскоростной, вследствие чего при схождении оболочек наблюдаются эффекты, связанные с высокой скоростью деформирования. В местах вмятин образуются полосы локализованной деформации, расположенные под углом 45 градусов к поверхности (позиция 3). При дальнейшем схождении указанные процессы продолжаются. Потеря устойчивости фронта деформации “усиливается”, на внутренней поверхности оболочки возникают выбросы – пластические струи (позиция 4). На последней стадии схождения выбросы сливаются (позиция 5), но сохраняются границы их соприкосновения, похожие на трещины. В центре полученного цилиндра температура повышается до температуры рекристаллизации меди, ~500°С (позиция 5). В центральной части цилиндра деформационная картина имеет вид цветка. Таким образом, потеря устойчивости фронта радиальной деформации осуществляется по двум структурным механизмам; назовем их деформационный и гидродинамический.
На внешней поверхности первых трех оболочек образуются выступы и вмятины (рис. 1а–1в). Число выступов увеличивается с увеличением интенсивности нагружения (см. табл. 1), но их высота уменьшается. Эффект зависимости числа выступов от величины давления при гидростатическом обжатии металлических труб обсуждался в работе [12]. В оболочке № 4 выступы “сглаживаются”. При схождении массивной медной оболочки, при толщине слоя ВВ 40 мм, гофрирование поверхности не наблюдалось [5]. Следовательно, при достаточно большой интенсивности нагружения фронт деформации на внешней поверхности сходящейся оболочки не теряет устойчивость [9]. Из табл. 1 следует, что отношение числа выступов (1 : 1.5 : 2) приблизительно такое же, как отношение квадратов толщин слоев ВВ (1 : 1.4 : 1.8). Значит, число выступов при гофрировании данных оболочек приблизительно прямо пропорционально квадрату энергии, сообщенной оболочке при взрыве, и, следовательно, квадрату ее кинетической энергии. Этот результат важен для анализа устойчивости фронта деформации в процессе высокоскоростного схождения оболочек.
Рассмотрим, как происходит деформация при избытке подводимой энергии. На рис. 4а представлен внешний вид нагруженной оболочки № 4. Видно, что по длине оболочки возникло два участка разрушения (разлета), разделенных участками схождения. Положение центров участков разлета указано стрелками. Расстояние между центрами этих участков равно половине длины оболочки, 100 мм. В оболочке № 5 разлет привел к полному разрушению и распаду оболочки на части. Значит, на начальной стадии разлета процесс носит периодический (пульсирующий) характер, при котором участки полного схождения чередуются с участками разлета. На рис. 4б представлена макроструктура в поперечном сечении оболочки № 4 на участке разлета (сравн. с рис. 1г). Разлет происходит под действием растягивающих напряжений при отражении волн от центра схождения. Разрушение при разлете не имеет центральной симметрии, как могло быть при строгой симметрии нагружения в изотропном материале. Очевидно, что трещины возникают на ослабленных участках микроструктуры, в частности в средней зоне хаотической деформации, и в определенной степени наследуют картину схождения.
Рис. 4.
Внешний вид нагруженной оболочки № 4 (а) и макроструктура в поперечном сечении в месте разлета (б). Зоны разлета указаны стрелками.
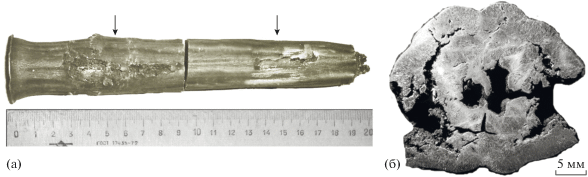
Пульсирующий характер деформации при схождении цилиндрической оболочки под действием скользящей детонации в режиме нагружения с избытком энергии может быть объяснен попеременным возрастанием и сбросом напряжений в продольном (осевом) направлении. Существование таких напряжений приводит к деформации вдоль оси оболочки; эта деформация показана в [3]. Напряжения в продольном направлении складываются с радиальными, и повышают общий уровень напряжений. Таким образом проявляется потеря устойчивости фронта осевой деформации.
Откольные явления
В оболочках, нагруженных с недостатком и избытком подводимой энергии, были обнаружены особенности откольных явлений, не наблюдавшиеся ранее. В оболочке № 1 под выступами образовались большие откольные полости (рис. 1а). Данный эффект объясняется разной степенью деформации вдоль разных радиусов. Вдоль радиуса, соответствующего вмятине, скорость и степень деформации больше, чем вдоль радиуса, соответствующего выступу. Это приводит к тому, что в одних участках откол залечивается, а в других “растягивается”.
В оболочке № 4 были найдены три случая залечивания откольных пор, представленные на рис. 5. На рис. 5а показана вихревая деформация вокруг поры, которая приводит к “затеканию” материала в пору и ее заполнению. Такой способ залечивания описан в [7]. Другой случай показан на рис. 5б. При залечивании поры образовалась округлая область, заполненная столбчатыми кристаллами. Область обведена штриховой линией. Полученная структура указывает на то, что при залечивании происходило плавление и последующая кристаллизация меди. При локализации высокоскоростной деформации вокруг поры энергия деформирования перешла в теплоту, и залечивание (захлопывание) поры привело к повышению температуры до температуры плавления меди, 1083°С. Третий случай показан на рис. 5в. Круглая область, обведенная штриховой линией, заполнена по краям столбчатыми кристаллами. В центральной части области присутствует большое количество мелких пор размером от нескольких микрометров до десятков микрометров. Происхождение мелких пор может быть связано с усадкой при кристаллизации. Однако возможна другая причина. Столбчатые кристаллы по краям большой поры свидетельствуют о том, что медь плавилась. Температура расплава была выше температуры плавления меди. Так как внутри поры был вакуум, то на внутренней поверхности поры могло происходить кипение жидкой меди. Образовавшиеся при кипении пузырьки зафиксировались в материале в виде микропор при быстрой кристаллизации расплава. Таким образом, повышение температуры при захлопывании откольных пор может быть гораздо больше, чем в центре цилиндра при схождении оболочки.
ВЫВОДЫ
1. Исследовано влияние интенсивности взрывного нагружения на схождение медных цилиндрических оболочек. Показано, что потеря устойчивости фронта радиальной деформации может происходить по двум структурным механизмам. Предложена схема структурных изменений, описывающая процессы, происходящие при схождении исследованных оболочек.
2. Обнаружен периодический (пульсирующий) характер осевой деформации при нагружении оболочки скользящей детонационной волной с интенсивностью, немного превышающей необходимую для полного схождения.
3. Найдена взаимосвязь между числом выступов при гофрировании внешней поверхности исследованных оболочек и интенсивностью взрывного нагружения.
4. Обнаружены эффекты залечивания откольных пор при высокоскоростной деформации, сопровождающиеся повышением температуры выше температуры плавления меди.
Электронно-микроскопические исследования проведены на оборудовании ЦКП “Испытательный центр нанотехнологий и перспективных материалов” ИФМ УрО РАН.
Работа выполнена в рамках государственной программы по теме “Структура” № AAAA-A18-118020190116-6).
Список литературы
Забабахин Е.И., Забабахин И.Е. Явления неограниченной кумуляции. М.: Наука, 1988. 172 с.
Огородников В.А. Вязкость и ее роль в динамических процессах. ФГУП “РФЯЦ-ВНИИЭФ”, Саров. 2012. 238 с.
Хейфец А.Э., Зельдович В.И., Фролова Н.Ю., Долгих С.М., Гаан К.В., Шорохов Е.В. Фазовые и структурные превращения в низкоуглеродистой стали, происходящие при схлопывании цилиндрической оболочки // ФММ. 2017. Т. 118. № 7. С. 715–724.
Зельдович В.И., Фролова Н.Ю., Хейфец А.Э., Долгих С.М., Гаан К.В., Шорохов Е.В. Деформационно-температурные процессы, происходящие при схлопывании толстой цилиндрической оболочки из стали 20 // ФММ. 2015. Т. 116. № 3. С. 300–308.
Зельдович В.И., Фролова Н.Ю., Хейфец А.Э., Долгих С.М., Гаан К.В., Шорохов Е.В. Деформационные и термические процессы, происходящие при высокоскоростном схлопывании массивной цилиндрической оболочки из меди // ФММ. 2018. Т. 119. № 6. С. 573–581.
Зельдович В.И., Фролова Н.Ю., Хейфец А.Э., Хомская И.В., Шорохов Е.В. Структурные превращения в меди при высокоскоростной деформации, происходящей при схождении массивной цилиндрической оболочки под действием взрыва // ФММ. 2020. Т. 121. № 5. С. 446–451.
Зельдович В.И., Хейфец А.Э., Фролова Н.Ю., Хомская И.В., Смирнов Е.Б., Дегтярев А.А., Шорохов Е.В. Металлографическое исследование структурных изменений в меди, происходящих при схождении цилиндрических оболочек // ФММ. 2019. Т. 120. № 4. С. 352–359.
Иванов А.Г., Софронов В.Н., Тюнькин Е.С. Особенности осесимметричного схождения откольных слоев в стальных цилиндрических оболочках // ПМТФ. 1984. № 3. С. 125–127.
Зельдович В.И., Фролова Н.Ю., Хейфец А.Э., Хомская И.В., Дегтярев А.А., Шорохов Е.В., Смирнов Е.Б., Долгих С.М., Коваль А.В. Деформационные явления при схождении металлических цилиндрических оболочек. Потеря устойчивости // ФГВ. 2019. № 4. С. 92–102.
Рыбин В.В., Ушанова Э.А., Золоторевский Н.Ю. Особенности строения разориентированных структур в бислойной пластине медь–медь, полученной сваркой взрывом // ЖТФ. 2013. Т. 83. Вып. 9. С. 63–72.
Каменецкий Б.И., Киселев В.В. Исследование процессов пластической деформации цилиндрических оболочек жидкостью высокого давления // Кузнечно-штамповочное производство. Обработка металлов давлением. 2007. № 7. С. 11–18.
Долгих Д.В., Киселев В.В. Управление деформированием круговой цилиндрической оболочки // Известия РАН. Механика твердого тела. 2019. № 6. С. 55–68.
Дополнительные материалы отсутствуют.
Инструменты
Физика металлов и металловедение