Физика металлов и металловедение, 2021, T. 122, № 7, стр. 776-782
Структура и свойства сплава Al–1% Ca–0.5% Fe–0.25% Si–0.5% Zr, полученного литьем в электромагнитный кристаллизатор
Н. О. Короткова a, *, С. О. Черкасов a, В. Н. Тимофеев b, А. А. Аксенов a
a НИТУ “МИСиС”
119049 Москва, Ленинский просп., д. 4, Россия
b Сибирский федеральный университет
660041 Красноярск, просп. Свободный, 79/10, Россия
* E-mail: kruglova.natalie@gmail.com
Поступила в редакцию 02.12.2020
После доработки 29.01.2021
Принята к публикации 09.02.2021
Аннотация
Проведен анализ структуры, механических свойств и электросопротивления холоднокатаной проволоки из сплава Al–1% Ca–0.5% Fe–0.25% Si–0.5% Zr, получаемого методом литья в электромагнитный кристаллизатор. Объектом сравнения являлась термостойкая проволока из сплава Al–7% РЗМ (01417), разработанного для гранульной технологии порошковой металлургии (RS/PM). Показано, что добавка кальция в присутствии железа и кремния позволяет получить фазовый состав, обеспечивающий термическую стабильность при нагреве до 300°С включительно.
ВВЕДЕНИЕ
Одним из ведущих направлений развития авиастроения является снижение веса авиатехники. По данным [1, 2], вес бортовой кабельной сети (БКС) авиаконструкций составляет ~20–25% от общего веса. При этом использование алюминиевых проводов вместо медных позволяет снизить вес БКС до 30% [3–5]. Все это делает алюминий весьма привлекательным материалом для обеспечения электротехнических нужд авиации.
Условия эксплуатации бортовых проводов предусматривают их нагревы до 250°С. Поскольку температура рекристаллизации нелегированного алюминия (типа А7Е) ниже 250°С [6], то задача повышения термической стабильности провода при сохранении уровня электрической проводимости является актуальной. В работах [7, 8] под руководством Добаткина был предложен способ повышения термостойкости алюминия за счет введения добавок редкоземельных металлов (РЗМ, в основном, Ce и La). Данный подход нашел реализацию в составе сплава Al–7% РЗМ (01417 по ТУ 1-809-1038-96), получаемого по гранульной технологии с последующими операциями порошковой металлургии (технология RS/PM).
Ввиду сложности исполнения технологии RS/PM предприятием “НПЦ Магнитной гидродинамики” для производства слитков с мелкодисперсной структурой был предложен способ литья в электромагнитный кристаллизатор (технология ЭМК) [9]. Технология ЭМК обеспечивает скорости охлаждения литой заготовки, сопоставимые со скоростями при технологии RS/PM. В частности, сравнительный анализ электропроводности и прочности волоченой проволоки из сплава 01417 [10], полученного по технологии RS/PM и технологии ЭМК, показал сопоставимые значения.
В то же время оценка свойств электропроводности, прочности и термостойкости, проведенная в [11] в условиях моделирования процесса непрерывного литья и прокатки для сплава состава Al–0.5% Ca–0.5% Fe–0.25% Si–0.2% Zr–0.1% Sc, показала сбалансированное сочетание этих характеристик. Результаты исследования, приведенные в работе [12], показали, что наличие в сплаве 4 мас. % Ca, 1 мас. % Fe и 0,6 мас. % Si позволяет реализовать тип структуры аналогичный структуре сплава 01417 за счет образования дисперсной эвтектики (Al) + Al4Ca + Al10CaFe2 + Al2CaSi2. Стоит отметить, что использование кальция в качестве легирующей добавки положительно сказывается на снижении общей плотности сплава. А наноразмерные дисперсоиды Al3Zr (L12), формирующиеся в процессе отжига, являются эффективными антирекристаллизаторами за счет торможения движения дислокаций [13–16].
По совокупности приведенных аспектов была сформулирована цель настоящей работы: проведение сравнительного анализа электропроводности, прочности и термостойкости проволоки из сплава на базе системы Al–Ca–Fe–Si–Zr, производимого по технологии ЭМК, и сплава 01417, получаемого по технологии RS/PM.
ЭКСПЕРИМЕНТАЛЬНЫЕ МЕТОДИКИ
Объектом исследования являлся сплав A1KЖЦр расчетного состава Al–1% Ca–0.5% Fe–0.25% Si–0.5% Zr в виде литого прутка диаметром 8 мм, полученного по технологии ЭМК. Поскольку в сплаве 01417 содержится около 9 об. % эвтектической фазы при реализации технологии RS/PM [17], то выбор состава сплава A1KЖЦр определялся ранее полученными результатами по диаграмме состояния Al–Ca–Fe–Si [18, 19] и из расчета суммарной доли вторых фаз около 5 об. % с увеличением доли Al4Ca в эвтектике [11]. Добавка Zr задана на уровне предельной растворимости элемента при применяемой скорости охлаждения слитка [20–22]. Фактический состав сплава приведен в табл. 1. Сплав приготавливали на базе алюминия марки А85 ГОСТ 11609–2001. Анализ фазового состава производили с помощью программного обеспечения Thermo-Calc (база TTAL5).
Таблица 1.
Фактический химический состав экспериментального сплава A1KЖЦр
Элемент | Содержание, мас. % |
---|---|
Ca | 0.81 ± 0.02 |
Fe | 0.48 ± 0.03 |
Si | 0.24 ± 0.02 |
Zr | 0.46 ± 0.05 |
Al | Основа |
Далее из литого прутка холодной прокаткой на вальцах ВЭМ 3М была получена проволока с квадратным сечением 1 × 1 мм. Проволоку подвергали одноступенчатой термической обработке с целью оценки термической стабильности, а также отжигали по двухступенчатым режимам с целью образования в микроструктуре наноразмерных дисперсоидов Al3Zr (L12). Режимы обработки проволоки приведены в табл. 2.
Таблица 2.
Режимы термообработки холоднокатаной проволоки из сплава А1КЖЦр
Обозначение | Режим отжига | |
---|---|---|
Температура, °С | Время, ч | |
S0 | холоднокатаное, исходное | |
одноступенчатый отжиг | ||
ST300 | 300 | 1 |
двухступенчатый отжиг: | ||
S400 | 350 | 3 |
400 | 3 | |
двухступенчатый отжиг: | ||
S450 | 350 | 3 |
450 | 3 |
Влияние температуры отжига на удельную электропроводность (далее УЭП) и твердость оценивали на литом образце и холоднокатаном листе толщиной 2 мм, полученном из литого прутка. Температурный диапазон отжигов находился в интервале 300–600°С с шагом 50°С и выдержкой 3 часа на каждой ступени. Величину УЭП оценивали методом вихревых токов на структуроскопе ВЭ-26НП по методике ГОСТ Р ИСО 15549–2009. Значения удельного электросопротивления (УЭС) рассчитывали, как обратную величину от удельной электропроводности. Измерение твердости производили на микротвердомере Metkon DURALINE MH-6 при нагрузке – 1 Н, времени теста – 10 с по методике ГОСТ 2999–75.
Микроструктуру слитков и листов изучали на сканирующем электронном микроскопе TESCAN VEGA 3 SBH (СЭМ) с использованием энергодисперсионной приставки для микроанализа (МРСА) X-Act Oxford Instruments. Механические испытания холоднокатаной проволоки сечением 1 мм2, полученной из литого прутка, проводили на испытательной машине Zwick Roell Z250 по методике ГОСТ 10446–80. Значения удельного электросопротивления проволоки получены с помощью милиомметра GOM-804 по методике ГОСТ 7229–76.
ЭКСПЕРИМЕНТАЛЬНЫЕ РЕЗУЛЬТАТЫ
Микроструктура литого прутка характеризуется тонкими прожилками эвтектики по границам дендритных ячеек алюминиевого твердого раствора (Al) (рис. 1а).
Рис. 1.
Микроструктура сплава A1KЖЦр (СЭМ): а – исходное состояние (литой пруток), б – медленное охлаждение.
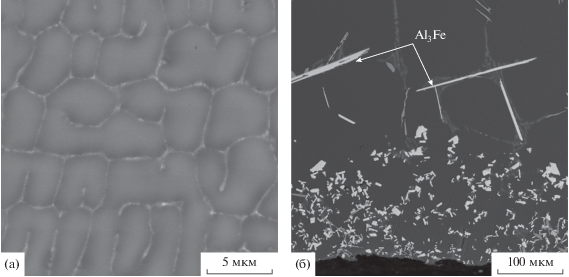
Наличие первичных кристаллов Al3Zr (D023) в структуре прутка не выявлено. Параметр дендритной ячейки (d) составил 2.30 ± 0.07 мкм, что соответствует скорости охлаждения Vc ~ 103–104 К/с согласно [23]. Расчет фазового состава в условиях метастабильного равновесия по цирконию сплава A1KЖЦр в сравнении со сплавом АК0.5Ж [11] выявил рост долей двух фаз – Al4Ca и Al3Zr (L12) (табл. 3). Поскольку в сплаве Al–0.5% Fe–0.2% Si–0.2% Zr–0.1% Sс [11] установлено наличие фаз Al4Ca, Al10CaFe2 и Al2CaSi2 ожидаема реализация в структуре сплава A1KЖЦр данных соединений в составе эвтектики. Анализ структуры медленно закристаллизованного сплава A1KЖЦр (рис. 1б) показал огрубление структурных составляющих, а также выявил наличие соединения Al3Fe игольчатой морфологии. Согласно [18, 24] изменение фазового состава обусловлено подавлением перитектической реакции L + Al3Fe → (Al) + Al10CaFe2 + Al2CaSi2.
Таблица 3.
Фазовый состав экспериментального сплава A1KЖЦр и сплава АК0.5Ж [11] при температуре 300°С
Сплав | Массовая доля (Qm) вторых фаз | Суммарная объемная доля вторых фаз (∑Qv) | |||
---|---|---|---|---|---|
Al4Ca | Al2CaSi2 | L12 | Al10CaFe2 | ||
A1KЖЦр | 1.66 | 0.64 | 0.91 | 1.98 | 4.74 |
АК0.5Ж | 0.46 | 0.70 | 0.52 | 2.07 | 3.24 |
Анализ изменений в микроструктуре в процессе отжига листа показал, что при 400°С имеет место частичная фрагментация частиц (рис. 2б), выявляемая при сравнении с исходной структурой холоднокатаного сплава (рис. 2а) При температуре отжига 500°С (рис. 2в) наблюдается сфероидизация интерметаллидов кальций-содержащих фаз (Al4Ca, Al10CaFe2, Al2CaSi2). При 600°С (рис. 2г) имеет место общее огрубление структуры за счет роста частиц, прежде всего Al10CaFe2, идентифицируемых методом МРСА.
Рис. 2.
Микроструктура (СЭМ) холоднокатаного сплава (листа толщиной 2 мм) в исходном состоянии (а) и после отжига при температурах: 400 (б), 500 (в), 600°С (г).
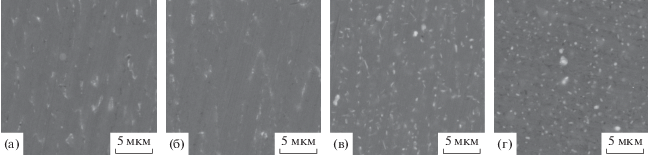
На образцах из литого прутка и холоднокатаного листа экспериментального сплава также были получены значения УЭС и твердости после отжигов в температурном интервале 300–600°С. Поскольку определение УЭС для литого образца ограничено возможностями измерительного прибора, удельное электросопротивление анализировали только в холоднокатаном сплаве. Анализ значений УЭС в зависимости от режима отжига (рис. 3) выявил снижение значений после 350°С, что вызвано процессом распада (Al) по Zr. При температуре отжига 450°С УЭС составляет 30.9 нОм м, минимальное значение – 30.0 нОм м достигается в результате отжига при 500°С. После отжига при 550°С эта величина составляет 30.3 нОм м. Полученные значения после отжига при 450°С говорят о стабильности фазового состава при высоких температурах. Общий разброс значений невелик и составляет 9.4 нОм м.
Рис. 3.
Влияние температуры отжига на удельное электросопротивление (а) и твердость (б) экспериментальных образцов из сплава A1KЖЦр.
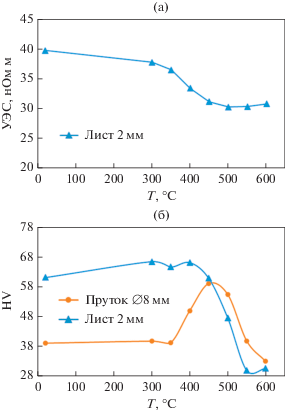
Анализ зависимостей твердости литого и деформированного сплава от температуры отжига выявил интересное соотношение: деформационное упрочнение холоднокатаного листа (с разницей в ~30 HV относительно литого сплава) сохраняется до 300°С включительно. Поскольку данная температура недостаточна для прохождения распада (Al) по Zr, такой эффект можно объяснить отсутствием структурных изменений эвтектических фаз при нагреве, и можно говорить об их термической стабильности. Незначительное колебание значений при 350°С, вероятно, обусловлено процессом образования зон Гинье–Престона и предвыделений [25, 26], характерных для начала распада (Al) по Zr. При температуре свыше 450°С для холоднокатаного листа характерно разупрочнение, что объясняется процессами изменения микроструктуры, описанными выше, изменением модификации частиц фазы Al3Zr c L12 на D023 [25, 26] и далее закономерно протекающим процессом рекристаллизации [16, 19]. Литой сплав также демонстрирует стабильность значений твердости до температуры 350°С. Затем при температуре отжига 450°С, соответствующей максимальной скорости распада (Al) по Zr, твердость достигает максимума (~60 HV). Отжиг при температуре выше 450°С приводит к разупрочнению, что вызвано огрублением структуры за счет формоизменения и роста частиц. Примечательно, что при температуре отжига 450°С значения HV для прутка и для листа практически одинаковы. Поскольку при этой температуре происходит фрагментация Ca-содержащих частиц (рис. 2а–2в), и следовало бы ожидать процесса движения дислокаций, то вероятно при этой температуре основную роль выполняют дисперсоиды Al3Zr (L12), сохраняющие размер около 10 нм [6, 16].
Основываясь на полученном в процессе отжигов эффекте упрочнения, термостойкости, а также показателях УЭС холоднокатаного листа и литого прутка (рис. 3) была определена дальнейшая схема получения проволоки. Схема термомеханической обработки состояла в получении холоднокатаной проволоки сечением 1 мм2 (степень обжатия 98%) и проведении ступенчатых отжигов проволоки с целью выделения дисперсоидов Al3Zr (L12) из (Al) (табл. 2) [6, 13]. Результаты механических испытаний на одноосное растяжение, а также полученные значения электросопротивления проволоки в исходном состоянии, после ступенчатых отжигов приведены в табл. 4. Объектом сравнения являлась холоднокатаная проволока из сплава 01417, полученная по технологии RS/PM [7].
Таблица 4.
Сравнение физико-механических свойств холоднокатаной проволоки из сплава A1KЖЦр и из сплава 01417 [7]
Сплав | Состояние | Механические свойства | Физические свойства | ||
---|---|---|---|---|---|
σв, МПа | δ, % | УЭС, мкОм м | %, IACS | ||
A1KЖЦр | S0 (холоднокатаное) | 268 ± 2 | 2.9 ± 0.7 | 0.044 ± 0.001 | 39 |
ST300 | 276 ± 5 | 1.1 ± 0.4 | – | – | |
S400 | 198 ± 7 | 3.1 ± 0.5 | 0.035 ± 0.002 | 49 | |
S450 | 180 ± 2 | 3.5 ± 0.5 | 0.032 ± 0.001 | 54 | |
01417 RS/PM | холоднокатаное | 180–230 | 2.5–4.6 | 0.031–0.032 | 56–54 |
Как видно из табл. 4, холоднокатаная проволока (S0) из экспериментального сплава A1KЖЦр обладает более высоким пределом прочности и сопоставимой пластичностью по сравнению с проволокой из сплава 01417 в аналогичном состоянии. Низкие значения удельного электросопротивления для проволоки из сплава A1KЖЦр в состоянии S0 обусловлены, прежде всего, цирконием, растворенным в твердом растворе алюминия. Последующая термическая обработка позволяет существенно снизить удельное электросопротивление до уровня УЭС сплава 01417. Двухступенчатый отжиг по режиму S400 снижает предел прочности на 60 МПа, при неизменной пластичности. А отжиг по режиму S450 снижает прочность до 180 МПа, при росте абсолютного значения пластичности и электропроводности (как обратной величине электросопротивления). Полученные результаты показывают, что обработка проволоки из сплава A1KЖЦр по режиму S450 позволяет достичь уровня свойств сопоставимого со свойствами проволоки из сплава 01417. Фрактограммы проволоки в исходном состоянии (S0) и состоянии S450 демонстрируют вязкие мелкоямочные изломы (рис. 4). Изломы проволоки образованы при осевом растяжении и имеют локальное утонение (шейку) в месте наибольшей локализации деформации.
Рис. 4.
Фрактограммы холоднокатаной проволоки сечением 1 мм2 из сплава A1KЖЦр после испытания на разрыв (СЭМ): а) исходное состояние (S0), б) S450 (см. табл. 2). BSE – детектор обратно отраженных электронов, SE – детектор вторичных электронов.
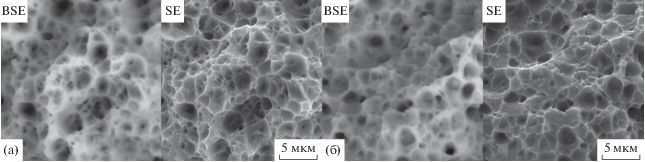
Особого внимания заслуживают значения механических свойств экспериментальной проволоки после одноступенчатого отжига при 300°С (ST300). Поскольку при данной температуре цирконий не оказывает своего влияния [6, 17], то полученный эффект может быть обусловлен только устойчивостью к нагревам структурных составляющих эвтектического происхождения. Данные значения демонстрируют возможность получения термически стабильного проводникового материала на базе системы Al–Ca–Fe–Si, что влечет за собой дополнительное преимущество в экономических показателях.
ВЫВОДЫ
1. Изучено влияние температуры отжига на структуру, удельное электросопротивление и твердость холоднокатаного листа из сплава Al–1% Ca–0.5% Fe–0.25% Si–0.5% Zr, полученного из прутка, отлитого по технологии литья в электромагнитный кристаллизатор. Установлено, что отжиг снижает электросопротивление и при 450°С оно составляет 0.031 мкОм м. Значения твердости для листа остаются высокими и практически не меняются до 450°С.
2. Экспериментальным путем установлено, что холоднокатаная проволока из сплава Al–1% Ca–0.5% Fe–0.25% Si–0.5% Zr, полученного с применением технологии литья в электромагнитный кристаллизатор, обладает более высоким пределом прочности, сопоставимой пластичностью по сравнению с проволокой из сплава Al–7% РЗМ, полученного по технологии RS/PM. Однако высокое электросопротивление материала за счет растворенного циркония требует проведения термической обработки.
3. Показано, что достичь сопоставимого со сплавом Al–7% РЗМ уровня свойств прочности, электропроводности и пластичности на проволоке из сплава Al–1% Ca–0.5% Fe–0.25% Si–0.5% Zr позволяет двухступенчатый отжиг при температурах 350 и 450°С с выдержкой 3 ч на каждой ступени.
4. Установлено, что за счет образования Ca-содержащих фаз эвтектического происхождения возможно обеспечение термической стабильности сплава до 300°С включительно. Это позволяет рассматривать систему Al–Ca–Fe–Si в качестве перспективной для разработки проводниковых экономнолегированных термостойких сплавов.
Исследование выполнено за счет гранта Российского научного фонда (проект № 20-79-00239).
Список литературы
Егер С.М., Матвеенко А.М., Шаталов И.А. Основы авиационной техники. 2-е изд. Под ред. И.А. Шаталова. М.: Изд-во МАИ, 1999. 576 с.
Avdulov A.A., Sergeev N.V., Gudkov I.S., Timofeev V.N., Gorokhov Yu.V. Avdulova Yu.S. Wire production development of special aluminum alloys based on electromagnetic mold casting method and continuous extrusion process known as conform // J. Sib. Fed. Univ. Eng. technol. 2017. V. 10(1). P. 85–94. https://doi.org/10.17516/1999-494X-2017-10-1-85-94
Технический справочник: Кабели, провода, материалы для кабельной индустрии. 3-е изд. М.: НКП “Эллипс”, 2006. 360 с.
Вульф Б.К., Ромадин К.П. Авиационное материаловедение. 3-е изд. М.: Машиностроение, 1967. 422 с.
Матвеев Ю.В., Гаврилова В.П., Баранов В.В. Легкие проводниковые материалы для авиапродов // Кабели и провода. 2006. № 5. С. 22–23.
Belov N.A., Alabin A.N., Prokhorov A.Y. The influence that a zirconium additive has on the strength and electrical resistance of cold-rolled aluminum sheets. // Russ. J. Non-ferrous Met. 2009. V. 50. P. 357–362. https://doi.org/10.3103/S1067821209040099
Добаткин В.И., Елагин В.И., Федоров В.М. Быстрозакристаллизованные алюминиевые сплавы. М.: ВИЛС, 1995. 341 с.
Добаткин В.И., Елагин В.И., Федоров В.М. Гранулируемые алюминиевые сплавы с особыми физическими свойствами // Авиационная промышленность. 1990. № 7. С. 55–57.
Первухин М.В., Тимофеев В.Н. Современные электротехнологии для производства высококачественных алюминиевых сплавов. Красноярск: СФУ, 2015. 155 с.
Korotkova N.O., Belov N.A., Timofeev V.N., Motkov M.M., Cherkasov S.O. Influence of heat treatment on the structure and properties of an Al–7% REM conductive aluminum alloy casted in an electromagnetic crystallizer // Phys. Met. Metal. 2020. V. 121. № 2. P. 182–188. https://doi.org/10.1134/S0031918X2002009X
Korotkova N.O., Belov N.A., Avksentieva N.N., Aksenov A.A. Effect of calcium additives on the phase composition and physicomechanical properties of a conductive alloy Al–0.5% Fe–0.2% Si–0.2% Zr–0.1% Sc // Phys. Met. Metal. 2020. V. 121. № 1. P. 95–101. https://doi.org/10.1134/S0031918X20010093
Belov, N.A., Akopyan, T.K., Korotkova, N.O., Naumova E.A., Pesin A.M., Letyagin N.V. Structure and properties of Al–Ca(Fe, Si, Zr, Sc) wire alloy manufactured from as-cast billet // JOM. 2020. V. 72. P. 3760–3768. https://doi.org/10.1007/s11837-020-04342-x
Çadırl E., Tecer H., Sahin M., Yılmaz E., Kırındı T., Gündüz M. Effect of heat treatments on the microhardness and tensile strength of Al–0.25 wt % Zr alloy // J. Alloys Compd. 2015. V. 632. P. 229–237. https://doi.org/10.1016/j.jallcom.2015.01.193
Orlova T.S., Mavlyutov A.M., Latynina T.A., Ubyivovk E.V., Murashkin M.Y., Schneider R., Gerthsen D., Valiev R.Z. Influence of severe plastic deformation on microstructure strength and electrical conductivity of aged Al–0.4Zr (wt %) alloy // Rev. Adv. Mater. Sci. 2018. V. 55. P. 92–101. https://doi.org/10.1515/rams-2018-0032
Yuan W., Liang Zh. Effect of Zr addition on properties of Al–Mg–Si aluminum alloy used for all aluminum alloy conductor // Mater. Des. 2011. V. 32 № 8–9. P. 4195–4200. https://doi.org/10.1016/j.matdes.2011.04.034
Knipling K.E., Dunand D.C., Seidman D.N. Precipitation evolution in Al–Zr and Al–Zr–Ti alloys during isothermal aging at 375–425°C // Acta Mater. 2008. V. 56. P. 114–127. https://doi.org/10.1016/j.actamat.2007.09.004
Belov N.A., Alabin A.N., Teleuova A.R. Comparative analysis of alloying additives as applied to the production of heat-resistant aluminum-base wires // Met. Sci. Heat. Treat. 2012. V.53. P. 455–459. https://doi.org/10.1007/s11041-012-9415-5
Belov N.A., Naumova E.A., Akopyan T.K. Doroshenko V.V. Phase Diagram of the Al–Ca–Fe–Si system and its application for the design of aluminum matrix composites // JOM. 2018. V. 70. P. 2710–2715. https://doi.org/10.1007/s11837-018-2948-3
Белов Н.А., Наумова Е.А., Акопян Т.К. Эвтектические сплавы на основе алюминия: новые системы легирования. М.: Руда и Металлы, 2016. 256 с.
Brubak J.P., Eftestol B., Ladiszlaldesz F. Aluminium alloy, a method of making it and an application of the alloy. Patent US 5067994. Publication: 1991–11–26.
Kenichi S., Kazuhisa Y., Yasumasa H.,Takasi K., Minoru Y. High conductive heat-resistant aluminum alloy. Patent US 4402763. Publication: 1983–09–06.
Jabłoński M., Knych T.A., Smyrak B. New aluminium alloys for electrical wires of fine diameter for automotive industry // Arch. Metall. Mater. 2009. V. 54. № 3. P. 671–676. https://www.researchgate.net/publication/263734063_New_aluminium_alloys_for_electrical_wires_of_fine_diameter_for_automotive_industry.
Телешов В.В. Фундаментальная закономерность изменения структуры при кристаллизации алюминиевых сплавов с разной скоростью охлаждения // Технология легких сплавов. 2015. № 2. С. 13–18.
Belov N.A., Naumova E.A., Ilyukhin V.D., Doroshenko V.V. Structure and mechanical properties of Al–6% Ca–1% Fe alloy foundry goods, obtained by die casting // Tsvet. Met. 2017. V. 3. P. 55–61. https://doi.org/10.17580/tsm.2017.03.11
Lefebvre W., Danoix F., Hallem H., Forbord B., Bostel A., Marthinsen K. Precipitation kinetic of Al3(Sc, Zr) dispersoids in aluminium // J. Alloys Compd. 2009. V. 470. P. 107–110. https://doi.org/10.1016/j.jallcom.2008.02.043
Clouet E., Barbu A., Lae L., Martin G. Precipitation kinetics of Al3Zr and Al3Sc in aluminum alloys modeled with cluster dynamics // Acta Mater. 2005. V. 53. P. 2313–2325. https://doi.org/10.1016/j.actamat.2005.01.038
Дополнительные материалы отсутствуют.
Инструменты
Физика металлов и металловедение