Физика металлов и металловедение, 2021, T. 122, № 7, стр. 769-775
Оценка роли ванадия и молибдена в изменении кинетики распада аустенита и механических свойств смоделированной зоны перегрева малоуглеродистых ниобийсодержащих сталей
И. Ю. Уткин a, *, Л. А. Ефименко a, В. Ю Бобринская b, О. Е. Капустин a
a РГУ нефти и газа (НИУ) им. И.М. Губкина
119991 Москва, Ленинский просп., 65, корп. 1, Россия
b ФГУП “ЦНИИчермет им. И.П. Бардина”
105005 Москва, ул. Радио 23/9, стр. 2, Россия
* E-mail: svarka@gubkin.ru
Поступила в редакцию 21.10.2020
После доработки 04.03.2021
Принята к публикации 10.03.2021
Аннотация
Исследовано влияние ванадия и молибдена на кинетику фазовых превращений аустенита и механические свойства зоны перегрева малоуглеродистых высокопрочных сталей. Показано изменение структуры и механических свойств металла при скоростях охлаждения, характерных для различных способов сварки.
ВВЕДЕНИЕ
Малоуглеродистые стали широко используются при производстве труб для магистральных и линейных трубопроводов [1, 2]. Эти стали легированы стойкими карбидообразующими элементами, такими как ванадий, молибден и ниобий, которые влияют на механические свойства как основного металла, так и сварных соединений. Наиболее распространенными разновидностями трубных сталей по сочетанию легирующих элементов являются: Nb–V, Nb–Mo, Nb–V–Mo и Nb–Cr/Ni. Все они имеют низкий уровень углерода и содержат до 0.11% ниобия [3]. Для таких сталей актуальным является изучение влияния легирующих (Mo, Cr, Ni) и микролегирующих (V, Nb, Ti) элементов на микроструктуру и механические свойства сварных соединений и в том числе зону термического влияния (ЗТВ) [4–6]. Однако не всегда удается понять влияние сочетания элементов между собой в процессе сварочного нагрева и охлаждения металла, так как при добавлении определенного элемента, при прочих равных условиях, механические свойства ЗТВ могут изменяться кардинальным образом. Поэтому в работе изучено влияние ванадия и молибдена в малоуглеродистых ниобийсодержащих сталях на микроструктуру и механические свойства зоны перегрева – участка, в котором могут наблюдаться негативные изменения свойств.
МЕТОДИКА ИССЛЕДОВАНИЯ
Исследования выполнены на двух трубных сталях, одна из которых содержала 0.027% V; 0.06% Nb; 0.24% Mo (далее – комплексно легированная сталь), другая была микролегирована только 0.07% Nb при прочих равных условиях. Базовый химический состав сталей представлен в табл. 1. Содержание серы и фосфора составляло около 0.001 и 0.01% соответственно.
Таблица 1.
Базовый химический состав исследованных сталей, мас. %
Сталь | С | Si | Mn | Ti | Ni | Cr | N |
---|---|---|---|---|---|---|---|
V–Nb–Mo | 0.06 | 0.19 | 1.75 | 0.019 | 0.28 | 0.07 | 0.003 |
Nb | 0.06 | 0.21 | 1.76 | 0.022 | 0.32 | 0.04 | 0.004 |
Кинетику фазовых превращений аустенита в зоне перегрева изучали с использованием дилатометрического метода [7]. Применяли закалочный дилатометр марки L78 RITA (Rapid Induction Thermal Analysis). К каждому цилиндрическому образцу размером 3 × 10 мм приваривали хромель-алюмелевые термопары. Образец помещали в камеру дилатометра, где находился кольцевой индуктор токов высокой частоты (ТВЧ), и фиксировали двумя кварцевыми стержнями, один из которых подвижный. Далее происходил нагрев образца до температуры 1300°С. Скорость нагрева была 150°С/с, а скорость охлаждения в интервале температур диффузионного распада аустенита 800–500°С (w8-5) изменялась в диапазоне от 1 до 160°С/с. Охлаждение металла осуществляли равномерно и регулировали расходом пропускаемого внутри камеры инертного газа (аргона). Дилатометрические кривые для скорости охлаждения 90°С/с представлены на рис. 1. Скорости охлаждения металла соответствуют наиболее распространенным способам сварки: многодуговой автоматической сварке под флюсом, w8-5 – 2–7°C/c (МДСФ); ручной дуговой сварке и автоматической сварке в защитных газах, w8-5 – 20–60°C/c (РДС, АДСЗГ); лазерной сварке, w8-5 – 70–100°C/c (ЛС) [8–10].
Рис. 1.
Термокинетические кривые для стали, комплексно легированной V–Nb–Mo (а) и микролегированной Nb (б), полученные при скорости охлаждения 90°С/с.
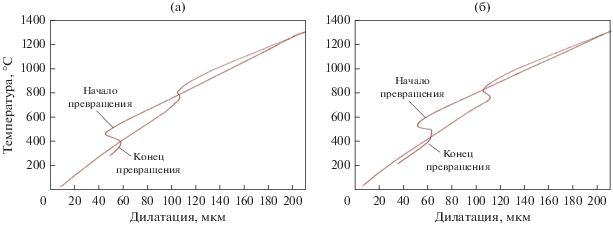
Оценку микроструктуры зоны перегрева при скорости охлаждения 20°С/с проводили с помощью просвечивающего электронного микроскопа, определение состава фаз (w8-5 – 5°С/с) – сканирующего электронного микроскопа после травления в растворе Ле Пера. Определение твердости по Виккерсу (HV0.5) и ударной вязкости (KCV, от минус 20 до минус 60°С) зоны перегрева проводили по ГОСТ 6996 [11]. Предварительно к центру каждого образца (в месте будущего V- образного надреза) размером 10 × 10 × 55 мм приваривали хромель-алюмелевые термопары. Образец помещали в индуктор ТВЧ и нагревали по такому же термическому циклу сварки (ТЦС), как и при дилатометрическом методе исследования, с тем лишь отличием, что скорости охлаждения изменялись в диапазоне от 1 до 100°С/с. Скорость охлаждения регулировали путем опускания торца образца в воду на различную глубину. Размер аустенитного зерна определяли по ГОСТ 5639 путем нагрева образца на установке ТВЧ до температуры 1300°С и его охлаждения в воде, что обеспечивало полностью мартенситную структуру [12].
РЕЗУЛЬТАТЫ ИССЛЕДОВАНИЯ
Металл проката обеих сталей в исходном состоянии имеет близкую микроструктуру, состоящую из феррита и ферритно-карбидной смеси различной дисперсности. Содержание ферритной фазы составляет около 70%.
После имитации ТЦС произошло изменение структуры обеих сталей (рис. 2). Ферритная фаза в структуре стали, микролегированной только ниобием, образуется в результате распада аустенита при скоростях охлаждения менее 7°С/с, а в стали с комплексным легированием – менее 4°С/с. Перлитное превращение ограничивается скоростями охлаждения 1–4°С/с, содержание перлита не превышает 15–20% (при w8-5 – 1°С/с). Наличие в стали молибдена и ванадия приводит к снижению температуры начала ферритного превращения с 720 до 700°С относительно стали содержащей только ниобий.
Рис. 2.
Термокинетические диаграммы распада аустенита в зоне перегрева низкоуглеродистых сталей: комплексно легированная ванадием, ниобием и молибденом (- - -), микролегированная только ниобием (—).
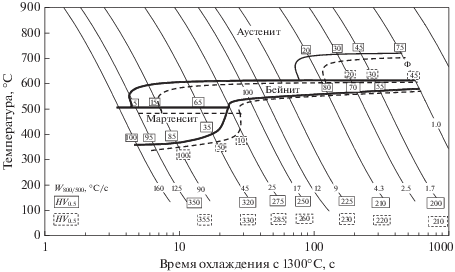
Бейнитное превращение аустенита обеих сталей протекает в широком диапазоне скоростей охлаждения и прекращается в стали с комплексным легированием при 90°С/с, а в стали, микролегированной ниобием, при 130°С/с.
Мартенситная фаза образуется в комплексно легированной стали при скорости охлаждения около 20°С/с и температуре 480°С. В стали, микролегированной ниобием, температура начала мартенситного превращения составляет 500°С при скорости охлаждения 25°С/с. Как видно, добавки ванадия и молибдена способствуют повышению устойчивости аустенита к распаду как в бейнитной, так и мартенситной областях превращения и сдвигу их к меньшим скоростям охлаждения.
Наличие в стали ванадия и молибдена, вследствие повышения устойчивости аустенита к распаду во всех областях, привело к увеличению средних значений твердости [13] металла во всем диапазоне скоростей охлаждения примерно на 10 HV (рис. 2).
Изменение структурного состава, твердости и ударной вязкости (KCV–20) зоны перегрева в зависимости от скорости охлаждения металла представлено на рис. 3а, 3б.
Рис. 3.
Изменение структурного состава, твердости и ударной вязкости (KCV–20) металла зоны перегрева стали, комплексно легированной V–Nb–Mo, (а) и стали, микролегированной Nb, (б) в зависимости от скорости охлаждения.
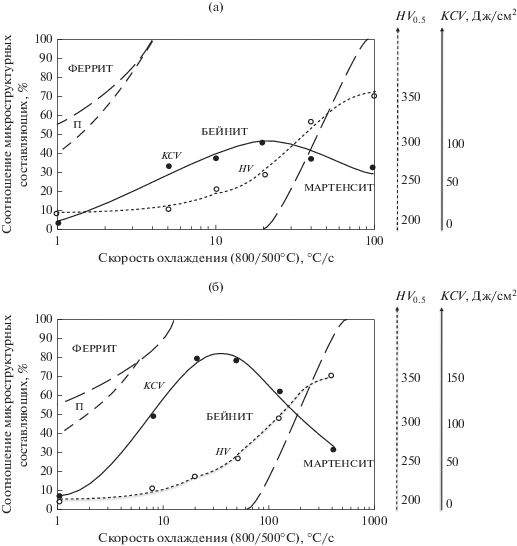
С увеличением скорости охлаждения и уменьшением количества ферритной фазы в структуре ударная вязкость и твердость в зоне перегрева начинают расти.
Анализ кривых изменения твердости в зависимости от скорости охлаждения показывает, что в диапазоне от 1 до 5°С/с твердость металла зоны перегрева практически не увеличивается. Дальнейшее увеличение скорости охлаждения, которая способствует прекращению выделения ферритной фазы и перлитной составляющей структуры, приводит к повышению интенсивности возрастания твердости особенно в области образования полностью бейнитной структуры. Это тенденция сохраняется вплоть до появления в структуре 50–60% мартенситной фазы. При формировании полностью мартенситной структуры твердость металла составляет ≈350 HV.
Анализ кривых изменения ударной вязкости металла зоны перегрева при формировании различного структурно-фазового состава показывает, что с уменьшением ферритной и перлитной составляющих структуры ударная вязкость увеличивается и достигает наибольшего значения в комплексно легированной стали и стали, микролегированной ниобием, при скоростях охлаждения 20 и 15°С/с соответственно. Именно при данных скоростях охлаждения в металле зоны перегрева сталей, содержащих V–Nb–Mo или только Nb, формируется бейнит реечной морфологии (длина реек 10–15 мкм, ширина 0.5–3 мкм), рис. 4, что приводит к повышению значений ударной вязкости металла. Появление мартенситной фазы в структуре способствует уменьшению ударной вязкости в зоне перегрева обеих сталей. Эта тенденция прослеживается и при оценке влияния температуры испытания на изменение значений ударной вязкости (рис. 5).
Рис. 4.
Бейнит реечной морфологии в металле зоны перегрева стали, легированной V–Nb–Mo, образовавшийся при скорости охлаждения 20°С/с.
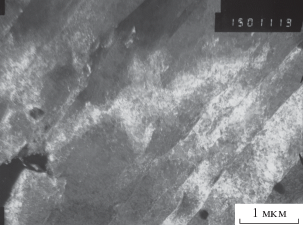
Рис. 5.
Изменение ударной вязкости в зависимости от температуры испытания (указана на кривых) и скорости охлаждения металла зоны перегрева стали, комплексно легированной V–Nb–Mo, (а) и стали, микролегированной Nb, (б).
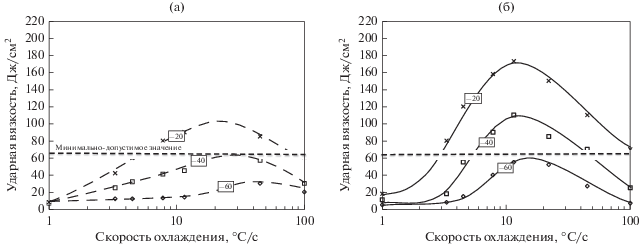
На рис. 5 показано изменение ударной вязкости в зависимости от температуры испытания и скорости охлаждения металла зоны перегрева. Максимальные значения ударной вязкости металла зоны перегрева стали, микролегированной ниобием, в 1.7–2.0 раза превышают соответствующие показатели зоны перегрева комплексно легированной стали. В связи с отсутствием нормативных значений ударной вязкости зоны перегрева при использовании имитационных методов исследования в статье в качестве нормативного критерия принята величина рекомендованная стандартом [14] (не менее 63 Дж/см2).
Как видно из рис. 5а, в комплексно легированной стали значения ударной вязкости при температурах испытания минус 40 и минус 60°С находятся ниже допустимого уровня во всем диапазоне скоростей охлаждения металла. При температуре минус 20°С нормативные значения ударной вязкости достигаются при скоростях охлаждения от 5 до 90°С/с, что в определенной степени охватывает весь диапазон характерный для рассматриваемых способов сварки (МДСФ, РДС, АДСЗГ, ЛС). В стали, микролегированной только ниобием (рис. 6б) значения ударной вязкости при температуре минус 60°С также находятся ниже нормативного уровня. При минус 40 и минус 20°С значения KCV ≥ 63 Дж/см2 обеспечиваются при скоростях охлаждения металла зоны перегрева в диапазоне от 5.5 до 45°С/с и от 3 до ≥ 100°С/с соответственно.
Рис. 6.
Фазы на границах и в аустенитных зернах зоны перегрева стали, легированной V–Nb–Mo, (а) и стали, микролегированной Nb, (б) (wохл – 5°С/с).
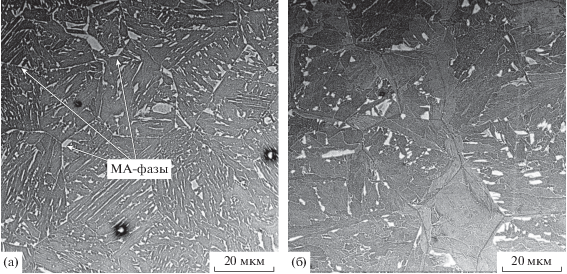
Оценка размера зерна аустенита в зоне перегрева обеих сталей показала, что существенных отличий не наблюдается. В среднем размер зерна аустенита составлял 50–60 мкм. Схожий размер зерна аустенита в исследованных сталях объясняется примерно одинаковым содержанием титана и азота, образующих частицы TiN, которые начинают растворяться при температуре более 1250°С [15–17]. Карбонитриды Nb растворяются при более низких температурах (1150°С) [16, 18], что даже при кратковременном сварочном нагреве не приводит к торможению роста зерна. Mo2C переходит в твердый раствор при температуре менее 700°С [16], а VC и VN при температуре около 1100°С [4, 19]. Экспериментальные данные, приведенные в статье [20], показывают влияние содержания молибдена при прочих равных условиях на размер зерна аустенита. Так, при его содержании в сталях примерно 0.009 и 0.03% размер зерна аустенита в зоне перегрева составляет 76–83 и 120–150 мкм соответственно. В работах [16, 21, 22] при исследовании сталей с близким к композиции легирования V–Mo–Nb химическим составом был получен схожий размер зерна аустенита (до 60 мкм).
Также стоит отметить различные мнения о влиянии содержания молибдена и ванадия при прочих равных условиях на ударную вязкость сварных соединений (зоны перегрева). Так, повышение содержания ванадия [4] в стали приводит к понижению значений ударной вязкости зоны перегрева из-за увеличения размера мартенситно-аустенитных фаз (МА-фаз). В работах [20, 17 ] установлено положительное влияние содержания молибдена на повышение величины параметра CTOD и ударную вязкость сварных соединений за счет формирования бейнита благоприятной морфологии. Однако в работе [23] экспериментально показано, что повышение содержания молибдена в стали приводит к понижению значений ударной вязкости сварных соединений.
Также было обнаружено, что в стали с комплексным легированием в металле зоны перегрева (wохл – 5°С/с) количество МА-фаз, в том числе на границах аустенитных зерен, существенно выше, чем в стали, содержащей только ниобий (рис. 6). Согласно литературным данным [4, 16, 24], в сталях с близким химическим составом при сварке также формируются МА-фазы. В исследованных сталях размер МА-фаз составляет до 7 мкм, при этом в стали, содержащей только ниобий, встречаются единичные области размером около 10 мкм. Таким образом, МА-фазы (большее их содержание в комплексно легированной стали), расположенные на границах и в аустенитных зернах, приводят к более низким значениям ударной вязкости металла зоны перегрева стали с комплексным легированием по сравнению со сталью, микролегированной только Nb.
На основании оценки влияния композиции легирования стали на формирование структурно-фазового состава и механических свойств металла зоны перегрева показано, что наиболее предпочтительным является использование стали, микролегированной только ниобием.
ВЫВОДЫ
Наличие в ниобийсодержащей стали ванадия и молибдена приводит к повышению устойчивости аустенита к распаду в металле зоны перегрева, по сравнению со сталью, микролегированной только ниобием, и формированию структурно-фазового состава, характеризующегося большим количеством высокодисперсного бейнита, мартенсита и МА-фаз.
Более высокая загрязненность границ аустенитных зерен зоны перегрева выделениями МА-фаз в комплексно легированной стали, а также большее количество мартенсита в структурно-фазовом составе оказывает негативное влияние на сопротивление стали хрупкому разрушению во всем диапазоне исследованных скоростей охлаждения.
Список литературы
Zhang Ying-qiao, Zhang Han-qian, Li Iin-fu, Liu Wei-ruing. Effect of Heat Input on Microstructure and Toughness of Coarse Grain Heat Affected Zone in Nb Microalloyed HSLA Steels // J. Iron and Steel Research International. 2009. V. 16. № 5. P. 73–80.
Уткин И.Ю., Усков Д.П., Франтов И.И., Лонгинов А.М., Мозговой А.В., Домов Д.В. Освоение новой композиции легирования стали для производства линейных труб классов прочности К52–К55 // Металлург. 2015. № 11. С. 105–109.
Procario J.R., Melfi T. Weld metal alloy systems for seam welding of niobium micro-alloyed pipe steels. / Proceeding of the International Seminar on Welding of High Strength Pipeline Steels. Held in Araxa, MG, Brasil, 27–30 November 2011. P. 110–121.
Chen Y.T., Guo A.M., Wu L.X., Zeng J., Li P.H. Microstructure and mechanical property development in the simulated heat affected zone of V treated HSLA steels // Acta Met. Sin. (Engl. Lett.). 2006. V. 19. № 1. P. 57–67.
Степанов П.П., Зикеев В.Н., Эфрон Л.И., Франтов И.И., Морозов Ю.Д. Улучшение свариваемости для толстостенных газопроводных труб большого диаметра путем оптимизации химического состава // Металлург. 2010. № 11. С. 62–67.
Aimin Guo, Misra R.D.K., Jibin Liu, Ling Chen, Xinlai He, Jansto S.J. An analysis of the microstructure of the heat–affected zone of an ultra–low carbon and niobium–bearing acicular ferrite steel using EBSD and its relationship to mechanical properties // Mater. Sci. Eng. A. 2010. V. 527. P. 6440–6448.
Шоршоров М.Х., Чернышова Т.А., Красовский А.И. Испытания металлов на свариваемость. М.: Металлургия, 1972. 240 с.
Борцов А.Н., Шабалов И.П., Величко А.А., Ментюков К.Ю., Уткин И.Ю. Особенности много электродной сварки под слоем флюса при производстве высокопрочных толстостенных труб // Металлург. 2013. № 4. С. 69–76.
Ефименко Л.А., Елагина О.Ю., Вышемирский Е.М., Капустин О.Е., Мурадов А.В., Прыгаев А.К. Традиционные и перспективные стали для строительства магистральных газопроводов. М.: Логос, 2011. 316 с.
Ефименко Л.А., Капустин О.Е., Уткин И.Ю., Деркач А.П., Шамов Е.М., Бегунов И.А., Горский А.И. Особенности формирования структуры и механических свойств металла сварного соединения при лазерной сварке неповоротных стыков труб // Сварочное производство. 2018. № 10. С. 18–24.
ГОСТ 6996-66. Сварные соединения. Методы определения механических свойств. М: Издательство стандартов. 64 с.
ГОСТ 5639-82. Методы выявления и определения величины зерна. М.: Издательство стандартов. 38 с.
Сыч О.В., Круглова А.А., Счастливцев В.М., Табатчикова Т.И., Яковлева И.Л. Влияние ванадия на дисперсионное упрочнение при отпуске высокопрочной трубной стали с различной исходной структурой // ФММ. 2016. Т. 117. № 12. С. 1321–1331.
СТО Газпром 2-4.1-713-2013. Технические требования к трубам и соединительным деталям: стандарт организации: введен 2013-02-11 – Москва: ОАО “Газпром”, 2014. 146 с.
Урцев В.Н., Корнилов В.Л., Шмаков А.В., Краснов М.Л., Стеканов П.А., Платов С.И., Мокшин Е.Д., Урцев Н.В., Счастливцев В.М., Разумов И.К., Горностырев Ю.Н. Формирование структурного состояния высокопрочной низколегированной стали при горячей прокатке и контролируемом охлаждении // ФММ. 2019. Т. 120. № 12. С. 1335–1344.
Maalekian M., Radis R., Militzer M., Moreau A., Poole W.J. In situ measurement and modelling of austenite grain growth in a Ti/Nb microalloyed steel // Acta Mater. 2012. V. 60. P. 1015–1026.
Эфрон Л.И. Металловедение в “большой” металлургии Трубные стали. М.: Металлургиздат, 2012. 694 с.
Горбачёв И.И., Пасынков А.Ю., Попов В.В. Прогнозирование размера аустенитного зерна микролегированных сталей на основе моделирования эволюции карбонитридных выделений // ФММ. 2015. Т. 116. № 11. С. 1184–1191.
Медина С.Ф., Валлес П., Джессика Кальво, Хосе М. Кабрера. Зарождение и рост выделений в микролегированной ванадием стали: физическая теория и экспериментальные результаты // ФММ. 2020. Т. 121. № 1. С. 37–47.
Терещенко Н.А., Табатчикова Т.И., Яковлева И.Л., Маковецкий А.Н., Шандер С.В. Влияние структуры на статическую трещиностойкость и характер разрушения сварных соединений из трубных сталей класса прочности К60 // ФММ. 2017. Т. 118. № 7. С. 743–751.
Barbaro F.J., Zhu Z., Kuzmikova L., Li H.and Gray J.M. Steel alloy designs for control of weld heat affected zone properties. /Fundamentals and Applications of Mo and Nb Alloying in High Performance Steels – Volume 2. Edited by Hardy Mohrbacher. CBMM, IMOA and TMS, 2015. P. 161–177.
Yu Gu, Peng Tian, XuWang, Xiu-lin Han, Bo Liao, Fu-ren Xiao. Non-isothermal prior austenite grain growth of a high-Nb X100 pipeline steel during a simulated welding heat cycle process // Mater. Design 2016. V. 89. P. 589–596.
Stallybrass C., Konrad J. and Meuser H. The effect of low levels of molybdenum in high strength linepipe steels. / Fundamentals and Applications of Mo and Nb Alloying in High Performance Steels – Volume 2. Edited by Hardy Mohrbacher. CBMM, IMOA and TMS, 2015. P. 125–140.
Fang Bai, Hongsheng Ding, Lige Tongb, Liqing Pan. Microstructure and properties of the interlayer heat-affected zone in X80 pipeline girth welds // Progress in Natural Science: Materials International. 2020. V. 30. P. 110–117.
Дополнительные материалы отсутствуют.
Инструменты
Физика металлов и металловедение