Физика металлов и металловедение, 2021, T. 122, № 7, стр. 729-736
Механохимический синтез порошков сплавов системы Cu–Al и их консолидация методом электроискрового спекания
Т. Ф. Григорьева a, *, С. А. Петрова b, С. А. Ковалева c, Д. В. Дудина a, d, e, И. С. Батраев d, Т. Ю. Киселева f, С. И. Жолудев g, С. В. Восмериков a, Е. Т. Девяткина a, Т. А. Удалова a, e, С. Н. Поляков g, Н. З. Ляхов a, h
a Институт химии твердого тела и механохимии СО РАН
630128 Новосибирск, ул. Кутателадзе, 18, Россия
b Институт металлургии УрО РАН
620016 Екатеринбург, ул. Амундсена, 101, Россия
c Объединенный институт машиностроения НАНБ
220072 Минск, ул. Академическая, 12, Республика Беларусь
d Институт гидродинамики им. М.А. Лаврентьева
630090 Новосибирск, пр. Лаврентьева, 15, Россия
e Новосибирский государственный технический университет
630073 Новосибирск, пр. К. Маркса, 20, Россия
f Московский государственный университет им. М.В. Ломоносова, Физический факультет
119991 Москва, Ленинские горы, 1, Россия
g Технологический институт сверхтвердых и новых углеродных материалов
108840 Троицк, ул. Центральная, 7а, Россия
h Новосибирский государственный университет
630090 Новосибирск, ул. Пирогова, 1, Россия
* E-mail: grig@solid.nsc.ru
Поступила в редакцию 10.01.2021
После доработки 05.03.2021
Принята к публикации 11.03.2021
Аннотация
Методами рентгеноструктурного анализа и растровой электронной микроскопии изучены продукты механохимического синтеза в системе Cu–20 мас. % Al. Показано, что после 20 мин механической активации формируется монофазный интерметаллид Cu9Al4 с размером кристаллитов ~3 нм, низким уровнем микронапряжений (~0.03%) и размером частиц от 0.2–0.4 до 2–4 мкм. Изучены морфологические характеристики твердого раствора алюминия в меди, механохимически синтезированного в системе Cu–10 мас. % Al. Показано, что он формируется в виде пластинчатых частиц с размерами 10–50 мкм в плоскости и толщиной 2–10 мкм. По данным растровой электронной и оптической микроскопии материалы, полученные электроискровым спеканием частиц твердого раствора Cu(Al) при 700°С, характеризуются низкой остаточной пористостью (<0.5%). Твердость по Виккерсу составляет 290 ± 30 HV.
ВВЕДЕНИЕ
В последние годы все чаще интерметаллиды используют в качестве модификаторов, упрочняющих пластичные металлы, такие как медь, алюминий, платина и другие, формируя композитную структуру на их основе [1–4]. Другая область использования алюминидов переходных металлов, например, Fe, Ni, Cu, Ti [5–12] – создание конструкционных материалов, работающих при высоких температурах и в коррозионных средах, поскольку на поверхности алюминидов за счет окисления алюминия образуется защитный оксидный слой.
Одним из технически достаточно простых и эффективных методов получения интерметаллидов является механохимический синтез (МХС) [9–15]. Основной недостаток этого метода – неоднородность фазового состава получаемых продуктов, поскольку теплоты образования разных интерметаллических соединений в одной и той же системе обычно близки [16, 17]. Большинство интерметаллидов характеризуется повышенной хрупкостью, что ограничивает технологические возможности и области их применения. Повышение пластичности спеченных из интерметаллида материалов может быть достигнуто за счет измельчения до микрометрических размеров зерна интерметаллида в консолидированном состоянии, что практически недостижимо традиционными методами порошковой металлургии [18, 19].
В последние годы интенсивно развиваются методы спекания порошков, использующие действие импульсного электрического тока на заготовку [20, 21]. Электроискровое спекание (низковольтная консолидация) происходит за счет энергии электрического тока, протекающего через оснастку из проводящего материала (пресс-форму и пуансоны) и непосредственно через образец (в случае спекания материалов, проводящих электрический ток). Особенностью электроискрового спекания является пропускание через образец постоянного тока в импульсном режиме. Протекание импульса электрического тока по пористому образцу может приводить к разогреву контактов между частицами порошка. Показано, что перегрев и плавление материала в области межчастичных контактов связаны с морфологией частиц [22]. Возможность реализации больших скоростей нагрева позволяет уменьшить общее время нахождения материала при повышенных температурах. Интерес к методу электроискрового спекания обусловлен возможностями сохранения ценных структурных характеристик материала, полученных в порошках, в спеченном состоянии за счет сокращения времени воздействия по сравнению с традиционными методами спекания. Активно проводятся исследования структуры и свойств сплавов, получаемых методом электроискрового спекания [23, 24].
Цель настоящей работы – изучение структурно-фазовой эволюции продуктов механохимического взаимодействия в системе Cu–20 мас. % Al, а также возможностей получения объемных сплавов посредством электроискрового спекания порошков механохимически синтезированного твердого раствора Cu(Al) состава Cu–10 мас. % Al.
ЭКСПЕРИМЕНТАЛЬНАЯ ЧАСТЬ
Использовали порошки меди марки ПМС-1 (ГОСТ 4960-75) и алюминия марки ПА-4 (ГОСТ 6058-73) c размером частиц ~45 мкм. Механохимический синтез проводили в высокоэнергетической планетарной шаровой мельнице АГО-2 с водяным охлаждением в атмосфере аргона [25]. Объем барабана 250 см3, диаметр шаров 5 мм, загрузка шаров 200 г, навеска обрабатываемого образца 10 г, скорость вращения барабанов вокруг общей оси ~1000 об/мин.
Рентгеноструктурные исследования проводили на дифрактометре Empyrean Panalytical (CuKα-излучение, позиционно-чувствительный детектор PIXcel3D, шаг Δ2θ = 0.026°, время в точке 100 с). Фазовый состав и кристаллическую структуру образцов определяли по данным рентгеновской дифракции с использованием программного пакета DIFFRACplus: EVA [26] и базы данных Международного центра дифракционных данных (ICDD) PDF4 [27]. Параметры элементарных ячеек сосуществующих фаз рассчитывали методом наименьших квадратов с использованием программы Celref [28]. Количество образовавшихся фаз определяли по результатам полнопрофильного анализа по методу Ритвельда [29] с использованием программного пакета DIFFRACplus: TOPAS [30]. Микроструктурные характеристики (размер областей когерентного рассеяния, или кристаллитов, L и микронапряжения ε) оценивали с использованием “дубль-Фойгт” (double Voigt) методологии. Для разделения вкладов в уширение пиков от L использовали функцию Лоренца, от микронапряжений ε – функцию Гаусса.
Электроискровое спекание механохимически синтезированного сплава Cu(Al), полученного из смеси Cu-10 мас. % Al в результате механической активации в течение 8 мин [31], осуществляли на установке SPS Labox 1575 (SINTER LAND Inc.), с использованием графитовой пресс-формы (внутренний диаметр 10 мм) и вольфрамовых пуансонов. Температура спекания составляла 700°С, время выдержки при данной температуре 1 мин. Скорость нагрева до максимальной температуры составляла 70° мин–1. Спекание проводили в условиях динамического вакуума. Одноосное давление, приложенное к образцу, составляло 40 МПа.
Морфологию синтезированных порошковых сплавов и микроструктуру спеченного сплава исследовали с помощью растровой электронной микроскопии (РЭМ) на приборе Hitachi-Tabletop TM-1000. Пористость спеченного сплава определяли посредством анализа оптических изображений в программе OLYMPUS Stream Image Analysis Software Stream Essentials 1.9.1. Оптические изображения были получены при помощи микроскопа OLYMPUS GX-51.
Твердость по Виккерсу измеряли при помощи прибора DuraScan 50 с приложенной нагрузкой 1 кг. Значение твердости определяли как среднее из измерений в 16 точках на металлографическом шлифе спеченного материала. Направление приложения нагрузки при индентировании совпадало с направлением приложения давления при электроискровом спекании образца.
РЕЗУЛЬТАТЫ И ОБУЖДЕНИЕ
Выбранная в работе система Cu–Al – одна из тех, которые интенсивно исследуются, не только вследствие ее востребованности для применений, но также ввиду ряда особенностей фазовых превращений (мартенситные превращения, реакции упорядочения в β-фазе, появление метастабильных состояний, называемых зонами Гинье–Престона и пр.) [32]. Согласно результатам исследований фазовых превращений, представленным в [33], в этой системе существуют несколько неоднозначных диапазонов, которые до сих пор остаются предметом дискуссий, в частности, область концентраций 12.4–22.1 мас. % Al.
Фазовая диаграмма системы медь – алюминий характеризуется набором интерметаллических фаз со сложными соотношениями между ними, проявляющимися во всех областях диаграммы [34]. Основными ключевыми точками взаимодействия элементов Cu и Al являются пределы их взаимной растворимости, определяемые энергией взаимодействия и термодинамикой образования интерметаллических фаз [35].
Согласно равновесной диаграмме состояния, в области от 16 до 19.9 мас. % Al существует гомогенная фаза твердого раствора на основе Cu9Al4 (γ2). Эта фаза имеет кристаллическую структуру γ‑латуни с параметром a кубической решетки от 0.870 до 0.873 нм.
При механохимическом синтезе в системе Cu–Al наблюдается изменение фазового состава с увеличением времени активации (рис. 1).
Рис. 1.
Дифрактограммы смесей Cu–20% Al после механической активации в течение: 1 – 40 с, 2 – 2 мин, 3 – 4 мин, 4 – 8 мин, 5 –20 мин. Стрелкой обозначен твердый раствор типа Cu(Al).
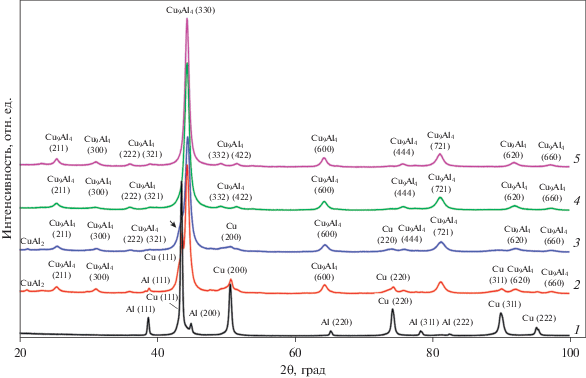
Формирование интерметаллического соединения Cu9Al4 идет через образование CuAl2. Уже после 40 с механической активации в смеси остается только около 55 мас. % меди (табл. 1), и образуется твердый раствор Cu(Al) в количестве ~20 мас. % с высоким уровнем микронапряжений. Кроме того, наблюдается начало формирования конечного продукта – интерметаллида Cu9Al4. Увеличение времени механической активации до 2 мин приводит к значительному уменьшению количества меди и росту микронапряжений в ней, появлению фазы CuAl2, снижению содержания в смеси твердого раствора и резкому росту количества Cu9Al4 (рис. 1, табл. 2). Разложение дифракционного рефлекса 2θ = 43°–44° с учетом фаз Cu, интерметаллида Cu9Al4 и твердого раствора Cu(Al) подтверждает высокую концентрацию Cu9Al4 в продукте МХС (рис. 2а).
Таблица 1.
Фазовый состав и параметры микроструктуры продуктов МХС в системе Cu–20 мас. % Al, длительность механической активации 40 с
№ п/п | Фаза | Пространственная группа | a, нм | V, нм3 | Концентрация, мас. % | L, нм | ε, % |
---|---|---|---|---|---|---|---|
1 | Cu | Fm-3m | 0.3615 | 0.0473 | 55.2 | ~30 | 0.24 |
2 | Al | Fm-3m | 0.4049 | 0.0664 | 15.6 | ~45 | 0.2 |
3 | Cu9Al4 | P-43m | 0.8690 | 0.6578 | 9.1 | – | – |
4 | Cu(Al) | Fm-3m | 0.3628 | 0.0478 | 20.1 | >500 | 2.0 |
Таблица 2.
Фазовый состав и параметры микроструктуры продуктов МХС в системе Cu–20 мас. % Al, длительность механической активации 2 мин
№ п/п | Фаза | Пространственная группа | a, нм | c, нм | V, нм3 | Концентрация, мас. % | L, нм | ε, % |
---|---|---|---|---|---|---|---|---|
1 | Cu | Fm-3m | 0.3617 | 0.0473 | 6.6 | ~30 | 0.55 | |
2 | Al | Fm-3m | 0.4050 | 0.0665 | 2.5 | – | – | |
3 | Cu9Al4 | P-43m | 0.8713 | 0.6615 | 70.7 | ~10 | 0.46 | |
4 | Cu(Al) | Fm-3m | 0.3644 | 0.0484 | 18.5 | ~70 | 1.68 | |
5 | CuAl2 | I4/mcm | 0.6069 | 0.4874 | 0.1795 | 1.7 | – | – |
Рис. 2.
Разложение главного максимума с учетом фаз меди, интерметаллида Cu9Al4 и твердого раствора Cu(Al) после механической активации в течение: а – 2 мин, б – 4 мин, в – 20 мин. 1 – Медь, 2 – интерметаллид, 3 – твердый раствор типа Cu(Al), 4 – аппроксимирующая кривая.
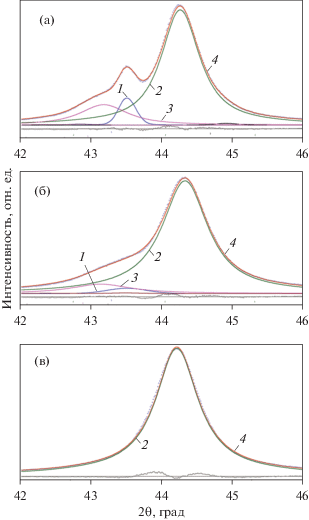
Для твердого раствора наблюдается снижение уровня микронапряжений до 1.68% (табл. 2).
При увеличении времени механической активации до 4 мин продолжает увеличиваться содержание интерметаллида Cu9Al4, при этом размер его зерен и уровень микронапряжений практически не меняются (рис. 2б, табл. 3). Существенно снижается количество твердого раствора, а также размер его кристаллитов и уровень микронапряжений.
Таблица 3.
Фазовый состав и параметры микроструктуры продуктов МХС в системе Cu–20 мас. % Al, длительность механической активации 4 мин
№ п/п | Фаза | Пространственная группа | a, нм | c, нм | V, нм3 | Концентрация, мас. % | L, нм | ε, % |
---|---|---|---|---|---|---|---|---|
1 | Cu | Fm-3m | 0.3610 | 0.0473 | 2.3 | ~15 | 0.43 | |
2 | Cu9Al4 | P-43m | 0.8714 | 0.6617 | 84.7 | 10 | 0.52 | |
3 | Cu(Al) | Fm-3m | 0.3650 | 0.0486 | 11.4 | ~10 | 0.43 | |
4 | CuAl2 | I4/mcm | 0.6060 | 0.479 | 0.1762 | 1.6 | – | – |
После 8 мин МХС формируется однофазный твердый раствор на основе Cu9Al4 (γ-латунь) (рис. 1, кривая 4) с параметром кубической решетки 0.872 нм и размером кристаллитов около 8 нм. Увеличение времени активации до 20 мин уменьшает размеры образующихся кристаллитов до 3 нм и снижает уровень микронапряжений до 0.03%. Величина параметра решетки γ-латуни увеличивается и достигает максимального размера 0.8735 нм, что свидетельствует об увеличении концентрации алюминия в твердом растворе.
Исследования методом РЭМ механохимически синтезированного в течение 20 мин интерметаллида Cu9Al4 показали наличие мелкозернистой структуры с бимодальным распределением частиц с размерами 0.2–0.4 и 2–4 мкм (рис. 3).
Рис. 3.
РЭМ изображение продукта МХС в системе Cu–20 мас. % Al, длительность механической активации 20 мин.
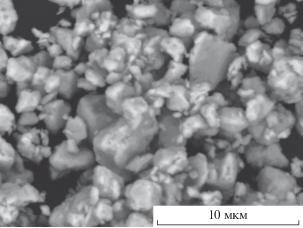
Частицы ранее полученного твердого раствора Cu(Al), образовавшегося при механохимическом взаимодействии в системе Cu–10 мас. % Al [31], имеют совершенно иную морфологию. Этим частицам свойственна ярко выраженная пластинчатая форма, их размеры составляют 10–50 мкм в плоскости и 2–10 мкм по толщине (рис. 4).
Рис. 4.
РЭМ-изображение продукта МХС в системе Cu–10 мас. % Al, длительность механической активации 20 мин.
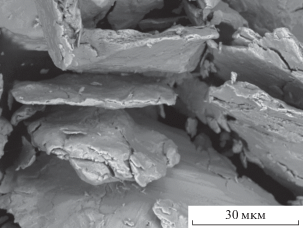
Различие в микроструктурных характеристиках и свойствах механохимически полученных твердого раствора алюминия в меди (исходная смесь Cu–10 мас. % Al) и интерметаллида Cu9Al4 (исходная смесь Cu–20 мас. % Al) предопределяет различные возможности их использования. Так, высокая дисперсность наноструктурированного интерметаллида (рис. 3, табл. 4) делает его перспективным в качестве дисперсно-упрочняющей добавки для пластичных металлов и сплавов, в то время как слоистый порошок твердого раствора алюминия в меди (рис. 4) может быть использован для получения изделий и покрытий различными методами спекания.
Таблица 4.
Фазовый состав и параметры микроструктуры продукта МХС в системе Cu–20 мас. % Al, длительность механической активации 20 мин
№ п/п | Фаза | Пространственная группа | a, нм | V, нм3 | Концентрация, мас. % | L, нм | ε, % |
---|---|---|---|---|---|---|---|
1 | Cu9Al4 | P-43m | 0.8735 | 0.6665 | 100 | ~3 | 0.03 |
Из данных РЭМ (рис. 5) и оптической микроскопии (рис. 6) следует, что сплав, полученный электроискровым спеканием твердого раствора Cu(Al), имеет малую остаточную пористость.
Рис. 5.
РЭМ-изображения материала, полученного электроискровым спеканием механохимически синтезированного твердого раствора Cu(Al): а – общий вид микроструктуры, б – микроструктура отдельных частиц-агломератов.
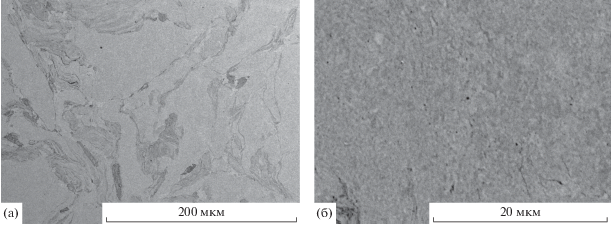
Рис. 6.
Оптическая микрофотография материала, полученного электроискровым спеканием механохимически синтезированного твердого раствора Cu(Al).
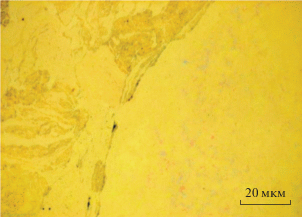
Оценка пористости из оптических микрофотографий дает величину менее 0.5%. Узкие черные полоски на рис. 6 (ширина менее 1 мкм, длина 4–5 мкм) представляют собой поры между отдельными частицами-агломератами. Поры в объеме частиц-агломератов отсутствуют.
Твердость спеченного сплава составила 290 ± ± 30 HV. При выбранной нагрузке размеры отпечатков, полученных при индентировании светлых и темных областей в микроструктуре, различимых на РЭМ-изображениях, близки, что свидетельствует о влиянии на результат измерения слоев материала, находящихся непосредственно под слоем, наблюдаемым на металлографическом шлифе. Соответственно, полученное значение твердости характеризует композиционную структуру сплава.
Оценка предела текучести материала из данных твердости может быть проведена по формуле Табора [36]: σy = H/3 = 1000 ± 100 МПа (с учетом погрешности измерения твердости).
Данное значение предела текучести близко к значению предела текучести сплавов на основе меди, содержащих бериллий, после холодной деформации и старения [37], а также к значению предела текучести металлокерамических композитов TiC–Cu [38].
ВЫВОДЫ
1. Механохимически синтезирован монофазный интерметаллид Cu9Al4 с размерами кристаллитов ~3 нм и низким уровнем микронапряжений (~0.03%).
2. Частицы механохимически синтезированного интерметаллида Cu9Al4 имеют бимодальное распределение по размерам в диапазонах 0.2–0.4 и 2–4 мкм.
3. Электроискровое спекание порошкового сплава, представляющего собой твердый раствор Cu(Al), при 700°С в течение 1 мин позволяет получить консолидированный материал с малой остаточной пористостью (менее 0.5%) и высокой твердостью (290 HV).
Работа выполнена при финансовой поддержке проектов РФФИ № 20-53-00037 и БРФФИ № Т20Р-037.
Список литературы
Grigoreva T.F., Kovaleva S.A., Zhornik V.I., Vosme-rikov S.V., Vityaz P.A., Lyakhov N.Z. Copper–Tin Materials for Tribotechnical Purposes // Inorganic Materials: Applied Research. 2020. V. 11. № 3. P. 744–749.
Батаев И.А., Батаев А.А., Мали В.И., Павлюкова Д.В., Ярцев П.С., Головин Е.Д. Зарождение и рост алюминида титана в слоистом композите, сваренном взрывом // ФММ. 2012. Т. 113. № 10. С. 998–1007.
Feldshtein E., Kielek P., Kielek T., Dyachkova L., Letsko A. One some mechanical properties and wear behavior of sintered bronze composities reinforced with some aluminides microadditives // J. App. Mech. Eng. 2017. V. 22. № 2. P. 293–302.
Celikyurek I., Korpe N.O., Olcer T., Galer R. Microstructure, properties and wear behaviors of (Ni3Al) reinforced Cu matrix composites // J. Mater. Sci. Technol. 2011. V. 27. № 10. P. 937–943.
Deevi S.C., Sikka V.K. Nickel and iron aluminides: an overview on properties, processing, and applications // Intermetallics. 1996. V. 4. P. 357–375.
Stoloff N.S., Liu C.T., Deevi S.C. Emerging applications of intermetallics // Intermetallics. 2000. V. 8. P. 1313–1320.
Morsi K. Review: reaction synthesis processing of Ni–Al intermetallic materials // Mater. Sci. Eng. 2001. V. A299. P. 1–15.
Schwarz R.B., Srinivasan S., Desch P.B. Synthesis of metastable aluminum-based intermetallics by mechanical alloying // Mater. Sci. Forum. 1992. V. 88–90. P. 595–602.
D’Angelo L., Ochoa J., González G. Comparative study for the formation of the NiAl, TiAl, FeAl intermetallic compounds by mechanical alloying // J. Metastable and Nanocryst. Mater. 2004. V. 20–21. P. 231–236.
Cardellini F., Contini V., Mazzone G. Solid-state reactions in the Al–Fe system induced by ball milling of elemental powders // J. Mater. Sci. 1996. V. 31. № 16. P. 4175–4180.
Zhu S.-M., Iwasaki K. Characterization of mechanically alloyed ternary Fe–Ti–Al powders // Mater. Sci. Eng. A. 1999. V. 270. № 2. P. 170–177.
Tcherdyntsev V.V., Sviridova T.A., Shevchukov A.P., Kaloshkin S.D. Formation of decagonal quasicrystals in mechanically alloyed Al–Cu–Cr powders // Z. Kristallogr. 2008. V. 223. P. 751–755.
Bakker H., Zhou G.F., Yang H. Prediction of phase transformations in intermetallic compounds induced by milling // Mater. Sci. Forum. 1995. V. 179–181. P. 47–52.
Diakonova N.P., Sviridova T.A., Semina V.K., Skakov Yu.A. Intermetallic phase stability on high energy treatments (rapid quenching, ion irradiation and mechanical milling) // J. Alloys and Compounds. 2004. V. 367. № 1–2. P. 199–204.
Feng L., Ishihara K.N., Shingu P.H. The formation of metastable phases by mechanical alloying in the aluminum and copper system // Metal. Trans. A. 1991. V. 22. P. 2849–2854.
Miedema A.R. On the heat of formation of solid alloys (II) // J. Less-Common Met. 1976. V. 46. P. 67–83.
Bakker H. Miedema’s semi–empirical model for estimating enthalpies in alloys // Mater. Sci. Briefings. 1988. V. 1. P. 1–80.
Рогуля А.В., Скороход В.В. Консолидированные наноструктурные материалы. Киев: Наукова думка, 2007. 374 с.
Дьячкова Л.Н., Керженцева Л.Ф., Маркова Л.В. Порошковые материалы на основе железа. Минск: ОДО “ТОНПИК”, 2004. 228 с.
Анисимов А.Г., Мали В.И. Исследования возможности электроимпульсного спекания порошковых наноструктурных композитов // Физика горения и взрыва. 2010. Т. 46. № 2. С. 135–139.
Olevsky E.A., Dudina D.V. Field-Assisted Sintering: Science and Applications. Cham, Switzerland: Springer International Publishing, 2018. 425 p.
Vidyuk T.M., Dudina D.V., Korchagin M.A., Gavrilov A.I., Skripkina T.S., Ukhina A.V., Anisimov A.G., Bokhonov B.B. Melting at the inter-particle contacts during Spark Plasma Sintering: Direct microstructural evidence and relation to particle morphology // Vacuum. 2020. V. 181. P. 109566.
Sasaki T.T., Mukai T., Hono K. A high-strength bulk nanocrystalline Al–Fe alloy processed by mechanical alloying and spark plasma sintering // Scr. Mater. 2007. V. 57. P. 189–192.
Shevtsova L., Mali V., Bataev A., Anisimov A., Dudina D. Microstructure and mechanical properties of materials obtained by spark plasma sintering of Ni3Al–Ni powder mixtures // Mater. Sci. Eng. A. 2020. V. 773. Article № 138882.
Аввакумов Е.Г. Механические методы активации химических процессов. Новосибирск: Наука, Сиб. отд., 1986. 302 с.
DIFFRACplus: EVA. Bruker AXS GmbH, Ostliche. Rheinbruckenstraße 50, D-76187, Karlsruhe, Germany. 2008.
Gates-Rector S., Blanton T. The Powder Diffraction File: A Quality Materials Characterization Database // Powder Diffr. 2019. V. 34. № 4. P. 352–360.
Laugier J., Bochu B. LMGP-Suite of Programs for the interpretation of X-ray Experiments. ENSP. Grenoble: Lab. Materiaux genie Phys., 2003.
Rietveld H.M. A Profile Refinement Method for Nuclear and Magnetic Structures // J. Appl. Crystallogr. 1969. V. 2. P. 65–71.
DIFFRACplus: TOPAS. Bruker AXS GmbH, Ostliche. Rheinbruckenstraße 50, D-76187, Karlsruhe, Germany. 2006.
Григорьева Т.Ф., Петрова С.А., Ковалева С.А., Киселева Т.Ю., Жолудев С.И., Восмериков С.В., Удалова Т.А., Девяткина Е.Т., Поляков С.Н., Ляхов Н.З. Механохимическое формирование твердого раствора алюминия в меди // ФММ. 2021. Т. 122. № 4. С. 396–401.
Liu X.J., Ohnuma I., Kainuma R., Ishida K. Phase equilibria in the Cu-rich portion of the Cu–Al binary system // J. Alloys and Compounds. 1998. V. 264. P. 201–208.
Zobac Ondrej, Kroupa Ales, Zemanova Adela, Richter Klaus W. Experimental Description of the Al–Cu Binary Phase Diagram // Metall. Mater. Trans. A. 2019. V. 50A. P. 3805–3815.
Диаграммы состояния двойных металлических систем: Справочник: В 3 т.: Т. 1 / Под общ. ред. Н.П. Лякишева. М.: Машиностроение, 1996. 992 с.
Deng Zhenghua, Yin Haiqing, Zhang Cong, Zhang Guofei, Zhang Tong, Liu ZiKui, Wang Haibao, Qu Xuanhui. Sintering mechanism of Cu–9Al alloy prepared from elemental powders // Progress in Natural Science: Materials International. 2019. V. 29. № 4. P. 425–431. https://doi.org/10.1016/j.pnsc.2019.04.007
Tabor D. The Hardness of Metals. Oxford University Press, 1951. 176 p.
Li M., Zinkle S.J. Physical and mechanical properties of copper and copper alloys / In Comprehensive Nuclear Materials by ed. Konings R.J.M. Amsterdam: Elsevier, 2012. V. 4. P. 667–690.
Дудина Д.В., Видюк Т.М., Квашнин В.И., Штерцер А.А., Анисимов А.Г., Мали, В.И. Есиков М.А., Ухина А.В., Корчагин М.А., Бохонов Б.Б., Леган М.А. Особенности формирования композиционных структур и локальные эффекты при электроискровом спекании // Композиты и наноструктуры. 2020. Т. 12. Вып. 3(47). С. 75–87.
Дополнительные материалы отсутствуют.
Инструменты
Физика металлов и металловедение