Физика металлов и металловедение, 2021, T. 122, № 7, стр. 737-744
Влияние поверхностной ультразвуковой электроимпульсной ударной обработки на микроструктуру, фазовый состав и микротвердость 3D-напечатанного сплава Ti–6Al–4V
О. Б. Перевалова a, А. В. Панин a, b, Е. Н. Боянгин a, *
a Институт физики прочности и материаловедения СО РАН
634055 Томск, Академический просп., 2/4, Россия
b Национальный исследовательский политехнический университет
634050 Томск, Ленина просп., 30, Россия
* E-mail: jeck2000@list.ru
Поступила в редакцию 28.01.2021
После доработки 20.02.2021
Принята к публикации 26.02.2021
Аннотация
Методами рентгеноструктурного анализа и просвечивающей электронной микроскопии, а также энергодисперсионного анализа химического состава исследованы фазовый и элементный состав, микроструктура поверхностных слоев сплава Ti–6Al–4V, полученного аддитивным методом 3D-печати и подвергнутого ультразвуковой электроимпульсной ударной обработке (ультразвуковой обработке с током – УЗОТ). Материалом ударного бойка была сталь. Обнаружено, что в процессе УЗОТ происходит микролегирование железом поверхностного слоя глубиной до 5 мкм, концентрация железа достигает 22 ат. %. В процессе УЗОТ в поверхностном слое глубиной до 2 мкм образуется нанокристаллическая многофазная структура, состоящая из оксидов титана и железа, метастабильной фазы Ti4Fe и α"-Ti, под нанокристаллическим слоем – слой с крупнокристаллической метастабильной фазой Ti4Fe и аморфной фазой. На глубине более 4 мкм образуется фаза Ti4Fe с субмикрокристаллической структурой, на глубине от 5 до 10 мкм – субмикрокристаллическая структура образована фазами (α-Ti + β-Ti). Внутри зерен α- и β-Ti расположена нанокристаллическая фаза α"-Ti. Микротвердость поверхностного слоя по сравнению с микротвердостью необработанного металла вдали от поверхности возрастает на 0.9–1.1 ГПа.
ВВЕДЕНИЕ
Ультразвуковая обработка (УЗО) поверхности сплава Ti–6Al–4V является одним из методов повышения коррозионной стойкости [1], износостойкости [2] и усталостной долговечности материала [3, 4]. В результате УЗО в поверхностном слое возникает нанокристаллическая структура как в сплаве Ti–6Al–4V [5], так и в сталях [6]. Модификация микроструктуры в поверхностных слоях сопровождается появлением упругих остаточных макронапряжений сжатия [7]. УЗО проводят с использованием ударника, колеблющегося с ультразвуковой частотой. В качестве развития метода УЗО было предложено проведение ультразвукового ударного воздействия в условиях подключения ударника и образца к источнику постоянного электрического тока (УЗОТ) [8]. Такая обработка повышает глубину и интенсивность модификации. В процессе УЗОТ в обрабатываемый сплав попадает железо из стального ударника, кислород и азот – из окружающего воздуха. В результате при комбинированной УЗО с током происходит искровое микролегирование поверхностного слоя обрабатываемого образца. К сожалению, авторы работы [8] не исследовали микроструктуру и фазовый состав модифицированных поверхностных слоев.
В настоящей работе предложено использование при УЗОТ источника не постоянного тока, а высокочастотного импульсного тока, изменение параметров которого позволит управлять процессами искрового микролегирования и модификации микроструктуры поверхностных слоев.
В последнее время большое внимание уделяется материалам, полученным аддитивными технологиями. Среди многообразия методов 3D-печати особый интерес представляет технология электронно-лучевого изготовления произвольных форм (ЭЛИПФ), достоинством которой является высокая производительность прямого получения достаточно сложных деталей путем плавления проволоки электронным пучком в вакууме. Однако для 3D-напечатанных образцов из сплава Ti–6Al–4V есть проблема наличия анизотропии свойств ввиду эпитаксиального роста больших первичных β-зерен и возникающих макронапряжений растяжения [9], приводящих к ухудшению механических свойств. Использование нового метода УЗОТ для 3D-напечатанных изделий из сплава Ti–6Al–4V может приводить к одновременной релаксации макронапряжений, модификации микроструктуры в поверхностных слоях за счет пластического деформирования и микролегирования от ударника. В связи с этим в настоящей работе поставлена задача исследовать влияние УЗОТ на микроструктуру, фазовый состав и микротвердость сплава Ti–6Al–4V, полученного методом 3D-печати по технологии ЭЛИПФ.
МАТЕРИАЛЫ И МЕТОДЫ ИССЛЕДОВАНИЯ
Заготовки из сплава Ti–6Al–4V были получены на установке 6Е400 (ООО “НПК ТЭТА”) аддитивным методом по технологии ЭЛИПФ [9]. Размеры 3D-напечатанных заготовок составляли 22 × 30 × 80 мм. В ходе процесса ЭЛИПФ использовали проволоку диаметром 1.6 мм, ее плавление осуществляли в вакууме 1.3 × 10–3 Па пушкой с плазменным катодом при ускоряющем напряжении 30 кВ и токе пучка 20 мА. Подачу проволоки осуществляли со скоростью 2 м/мин под углом 35° к поверхности подложки. Стратегия печати выполнялась по траектории меандра с зеркальным наплавлением слоев. Химический состав исходной проволоки соответствовал стандарту ASTM B348.
Ультразвуковую ударную обработку с высокочастотным током проводили с помощью комплекса оборудования: генератор ИЛ4 (ООО “ИНЛАБ-УЛЬТРАЗВУК” г. С.-Петербург), преобразующий электрическую энергию ультразвукового генератора в ультразвуковые колебания с частотой 25 кГц и мощностью 630 Вт; импульсный инвертор тока (ИИТ) с длительностью импульса тока – 50 мкс, частотой – 600 Гц, амплитудой напряжения, прикладываемого к обрабатываемому изделию – 50 В, максимальной амплитудой генерируемого тока – 1500 А. Для того, чтобы объединить электроискровой процесс с УЗО, образец и ударный шар были подключены к ИИТ во время обработки. Ударник был изготовлен из стали ШХ15.
Микроструктуру образцов изучали с помощью электронного микроскопа JEM 2100 в режиме как ПРЭМ (просвечивающей растровой электронной микроскопии), так и ПЭМ (просвечивающей электронной микроскопии). Для идентификации фаз использовали темнопольную методику. Элементный состав сплава определяли энергодисперсионным методом.
Рентгеноструктурный анализ (РСА) фазового состава проводили с использованием съемки в Cо Kα-излучении по симметричной геометрии Брэгга–Брентано [10] на рентгеновском дифрактометре ДРОН-7. Объемную долю фаз β-Ti и α"-Ti оценивали методом РСА с погрешностью 3 об. %.
Микротвердость по Виккерсу измеряли с использованием твердомера ПМТ-3 при нагрузке 0.4905 Н.
РЕЗУЛЬТАТЫ И ИХ ОБСУЖДЕНИЕ
В исходном состоянии 3D-напечатанных образцов из сплава Ti–6Al–4V основной фазой является фаза α-Ti, вторыми фазами – β-Ti и α"-Ti. Это видно на дифрактограмме образца до обработки УЗОТ (рис. 1а). В данном образце объемная доля фазы β-Ti составляет 4 об. %, фазы α"‑Ti – 10 об. %. Параметры решетки α-Ti а и с и их отношение c/a имеют значения: a = 0.29248 нм, с = 0.46944 нм, c/a = 1.6. Микроструктура представлена наследственными β-зернами [11], внутри которых имеется пластинчатая структура α‑фазы с двухфазными прослойками (β + α") по границам пластин (рис. 2). Локальная концентрация элементов алюминия и ванадия при средних значениях в сплаве Ti–6A–4V, соответственно, 9.8 и 3.5 ат. %, в теле α-пластин составляет 9.8 и 1.7 ат. % и в зернограничных прослойках – 4.9 и 13 ат. % [11].
Рис. 1.
Участки дифрактограмм образца сплава Ti–6Al–4V, полученного аддитивным методом ЭЛИПФ, в исходном состоянии (а) и после УЗОТ (б) в интервале углов дифракции 20–100 град. Участок дифрактограммы образца после УЗОТ в интервале углов дифракции 35–65 град (в).
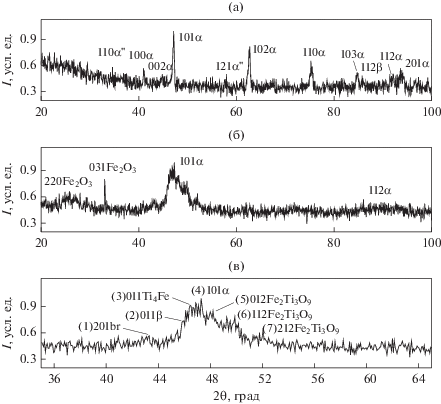
Рис. 2.
Электронно-микроскопические изображения микроструктуры сплава в исходном состоянии. Светлое поле (а), микродифракционная картина (б), темные поля, полученные в рефлексах следующих фаз: 100 (012) α (в), 110 $\left( {\bar {1}1\bar {2}} \right)$ α" (г), $\bar {1}10$ (331) β (д).
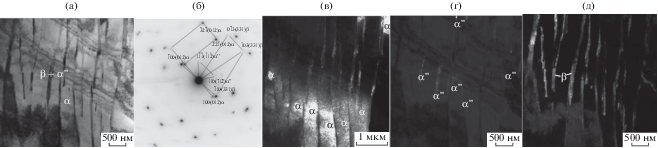
После УЗОТ микроструктура поверхностных слоев изменяется. На рис. 3, полученном в режиме ПРЭМ, видно, что микроструктура является градиентной, изменяющейся с удалением от поверхности.
Рис. 3.
Электронно-микроскопическое изображение микроструктуры вблизи поверхности в режиме ПРЭМ в сплаве после УЗОТ.
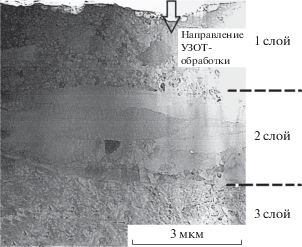
Можно выделить несколько слоев, различающихся размером фаз. На глубине до 2 мкм (1 слой) наблюдаются дисперсные фазы, на глубине от 2 до 4 мкм (2 слой) – основная фаза с размером зерна более 6 мкм и дисперсными вторыми фазами, и наконец, на глубине более 4 мкм (3 слой) –дисперсные фазы. Границы между 1 и 2 слоями и между 2 и 3 слоями четкие и приблизительно параллельны поверхности обработки.
Распределение элементов (Ti, O, Fe, Al, V) с удалением от поверхности УЗОТ представлено на рис. 4. Концентрация Fe имеет максимальное значение на глубине до 2 мкм от поверхности и составляет ≈22 ат. %. На глубине от 2 до 5 мкм концентрация железа уменьшается и становится равной ≈15 ат. %, а на глубине более 5 мкм – менее 1 ат. %. Помимо железа, в поверхностном слое глубиной до 5–6 мкм обнаружен также кислород. Максимальная его концентрация до 27 ат. % отмечается на самой поверхности, и значение ≈3 ат. % – на глубине до 6 мкм.
Рис. 4.
Распределение химических элементов (Ti, Fe, Al, V, O) в зависимости от расстояния от поверхности обработки.
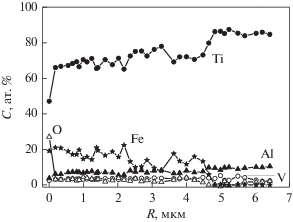
Методом ПЭМ показано, что самый поверхностный слой (слой 1 на рис. 3) имеет нанокристаллическую структуру (рис. 5). Микродифракционная картина на рис. 5б получена с использованием селекторной диафрагмы, диаметр которой на светлопольном изображении составляет 1.4 мкм. О том, что структура является нанокристаллической свидетельствуют кольцевой характер микродифракционной картины (рис. 5б) и темнопольные изображения в рефлексах фаз TiO2 (брукит) с межплоскостным расстоянием d, равным 0.269 нм (рис. 5в), оксидов титана TiO2 (брукит и шриланкит) c d = 0.211 нм (рис. 5г), α"-Ti и фазы Ti4Fe с d = 0.226 нм (рис. 5д).
Рис. 5.
Электронно-микроскопические изображения микроструктуры 1 слоя в образце после обработки УЗОТ. Светлое поле (а), микродифракционная картина (б), темные поля, полученные в рефлексах следующих фаз: 130 TiO2 брукит (br) (в), 121 TiO2 шриланкит (sr) и 221 TiO2 брукит (br) с одинаковым межплоскостным расстоянием, равным 0.212 нм (г), 101 Ti4Fe и 002α" (д).
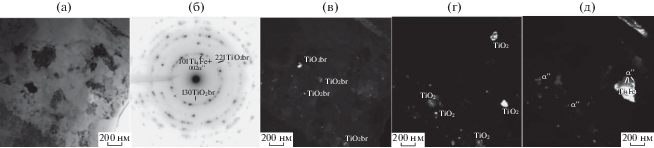
2-й слой образован фазой Ti4Fe с равномерно распределенными частицами размером около 5 нм (рис. 6). На микродифракционной картине, полученной при использовании селекторной диафрагмы диаметром 1.4 мкм на светлопольном изображении, присутствуют сильные рефлексы, принадлежащие плоскости обратной решетки (130) фазы Ti4Fe с ОЦК-структурой (рис. 6б), и два диффузных кольца, характерные для аморфного состояния. Предположительно, наноразмерные частицы имеют аморфную структуру.
Рис. 6.
Электронно-микроскопическое изображение микроструктуры в слое на глубине более 2 мкм от поверхности: светлое поле (а), микродифракционная картина (б). Диффузные кольца указаны черточками, первое кольцо имеет радиус, меньший, чем r002 фазы Ti4Fe, второе – меньший, чем ${{r}_{{3\bar {1}0}}}$ этой фазы.

В 3-м слое, расположенном на расстоянии более 4 мкм от поверхности, основная фаза имеет размеры зерен менее 1 мкм и относится к субмикрокристаллической (рис. 7а). Фазовый состав в данном слое изменяется с увеличением расстояния от поверхности.
Рис. 7.
Электронно-микроскопические изображения микроструктуры в слое 3 на глубине от 4 до 5 мкм. Светлое поле (а), микродифракционная картина (б), темные поля, полученные в рефлексах следующих фаз: 010 α" (в), 111 α" + 012 $\left( {0\bar {2}1} \right)$ TiO2 брукит (br) (г), $\bar {1}10$ Ti4Fe+002 α" + 112 $\left( {0\bar {2}1} \right)$ TiO2 брукит(br) (д).
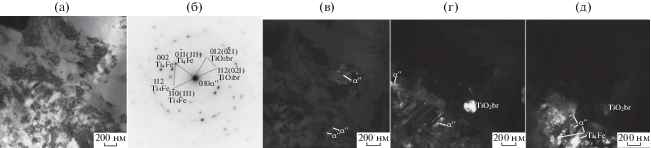
На глубине от 4 до 5 мкм от поверхности основной фазой является фаза Ti4Fe, так как все сильные рефлексы на микродифракционной картине принадлежат этой фазе (рис. 7б). Вторыми фазами являются α"-Ti и TiO2 (брукит). Наличие фаз α"-Ti и TiO2 (брукит) подтверждается темнопольными изображениями, полученными в рефлексах этих фаз (рис. 7б–7г).
Фаза α"-Ti является нанокристаллической. Это хорошо видно на темнопольном изображении (рис. 7в), полученном в одиночном рефлексе 010 этой фазы. Как уже отмечалось выше, концентрация железа в этом слое составляет 15 ат. %.
В 3 слое на глубине более 5 мкм от поверхности, где содержание железа не превышает 1 ат. %, формируется субмикрокристаллическая структура, образованная фазами (α-Ti + β-Ti) (рис. 8). На темнопольных изображениях на рис. 8в–8г, полученных в сильных рефлексах α- и β-фаз, внутри зерен указанных фаз наблюдается также нанокристаллическая фаза. Поскольку рефлексы 002 α"-фазы и 101α- и 011 β-фазы имеют близкие значения межплоскостных расстояний, можно предположить, что нанокристаллические частицы принадлежат α"-фазе. Темнопольное изображение на рис. 8д, полученное в рефлексе 110 α"-фазы, однозначно доказывает, что нанокристаллические частицы являются α"-фазой.
Рис. 8.
Электронно-микроскопические изображения микроструктуры в 3 слое на глубине более 5 мкм от поверхности. Светлое поле (а), микродифракционная картина (б), темные поля, полученные в рефлексах следующих фаз: 101α + 002 α" (в), 011β + 002 α" (г), 110 α" (д).
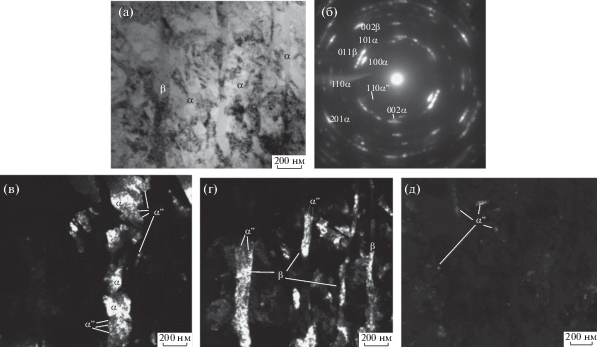
Таблица 1.
Углы дифракции (2θ) и межплоскостные расстояния (d) фаз
№ пика (рис. 1в) | 2θ, град | d, нм | Фазы |
---|---|---|---|
1 | 43.26 | 0.243 | 201TiO2 (брукит) + 311Fe3O4 |
2 | 45.80 | 0.229 | 011β |
3 | 46.53 | 0.226 | 011 Ti4Fe |
4 | 47.24 | 0.223 | 101α |
5 | 48.13 | 0.219 | 012 Fe2Ti3O9 |
6 | 49.66 | 0.213 | 112Fe2Ti3O9 |
7 | 51.94 | 0.204 | 212Ti3O9 + 400 Fe3O4 |
Изменение фазового состава в поверхностном слое в результате УЗОТ было обнаружено также и методом РСА (рис. 1б). Появляются пики, наблюдаемые при углах дифракции 2θ = 25.8 град и 33.1 град и принадлежащие пикам 220 (d = 0.4 нм) и 031 (d = 0.314 нм) оксида железа Fe2O3 с моноклинной структурой. Пик, наблюдаемый вблизи угла дифракции 2θ = 47.5 град, до обработки принадлежащий пику 101 фазы α-Ti, становится асимметричным, и его полуширина увеличивается от 0.3 град в состоянии до УЗОТ до 3.5 град в состоянии после УЗОТ. После развертки участка дифрактограммы вблизи данного угла дифракции (рис. 1в) становится очевидным, что данный пик представляет собой суперпозицию пиков разных фаз (табл. 1), а именно, оксидов титана и железа, фаз α-Ti, β-Ti и Ti4Fe с ОЦК-структурой.
Фаза Ti4Fe представляет собой твердый раствор железа в β-Ti. По пику 011 этой фазы можно оценить параметр решетки. Он равен 0.32 нм. Если считать, что в твердом растворе на основе β-Ti находятся только атомы железа, то значение концентрации железа, оцененное с использованием правила Вегарда при параметре решетки, равном 0.32 нм, составляет 25 ат. %.
Это оценочное значение концентрации железа близко к значению, определенному энергодисперсионным методом в режиме ПРЭМ. В равновесных условиях при температуре 590°С, согласно диаграмме состояния Ti–Fe, происходит эвтектоидный распад этой фазы на α-Ti и интерметаллид FeTi. В условиях УЗОТ распад фазы Ti4Fe не произошел. В [12] установлено, что в высокопрочном титановом сплаве Ti–5Al–5Mo–5V–3Cr расслоение β-твердого раствора по концентрации легирующих элементов и фазообразование зависят от скорости закалки и от температуры нагрева под закалку. Вероятно, распад фазы Ti4Fe не произошел при УЗОТ из-за высокой скорости охлаждения. Фазу Ti4Fe в метастабильном состоянии с параметром решетки, равным 0.318 нм, также наблюдали в [13].
Наблюдаемое изменение микроструктуры поверхностного слоя образца сплава Ti–6Al–4V в процессе УЗОТ обусловлено циклическим ударным воздействием и локальным плавлением, вызванным электроискровым воздействием [8]. До того момента, как возникает электрическая искра между образцом и ударником, ударное воздействие приводит к образованию субмикрокристаллической структуры в (α + β) фазах и образованию α"-фазы внутри α- и β-фаз (3-й слой на рис. 3). После возникновения электрической искры происходит оплавление поверхности образца и ударника. В результате этого железо попадает в расплавленный слой титанового сплава.
При охлаждении из расплава образуется фаза Ti4Fe с размером зерна более 6 мкм и с содержанием железа до 22 ат. % (2-слой). Диффузионным путем железо попадает также и в нижележащий слой с субмикрокристаллической структурой (3 слой), что также приводит к образованию фазы Ti4Fe. Образование частиц с аморфной структурой во 2-м слое обусловлено тем, что произошло легирование железом. В рамках модели ассоциированного раствора в [14] прогнозируется, что в сплавах системы Fe–Ti аморфизация возможна в концентрационном интервале XFe = 0.23–0.81. Экспериментально аморфизацию в системе Fe–Ti в пределах указанного концентрационного интервала наблюдали в [15]. Аморфная фаза в поверхностном слое сплава Ti–6Al–4V, обработанного стальным бойком, была обнаружена в [16] даже после ультразвуковой ударной обработки без тока. И, наконец, нанокристаллический оксидный слой (1-й слой на рис. 3) образовался в процессе охлаждения обработанной поверхности из-за высокой активности титана и железа к кислороду. Образование оксида титана TiO2 на поверхности сплава Ti–6Al–4V также наблюдали авторы настоящей работы при УЗО без тока. Оксиды титана TiO2 и алюминия также образуются на поверхности электроспеченного титан-алюминиевого сплава [17].
Модификация микроструктуры поверхностных слоев образца сплава в результате УЗОТ сопровождается увеличением микротвердости. На рис. 9 представлено распределение микротвердости в поперечном сечении образца, обе поверхности которого подвергли УЗОТ. Видно, что вблизи обработанных поверхностей микротвердость увеличивается на 0.9–1.1 ГПа.
Рис. 9.
Распределение микротвердости в поперечном сечении 3D-напечатанного образца сплава Ti–6Al–4V, подвергнутого УЗОТ с двух сторон.
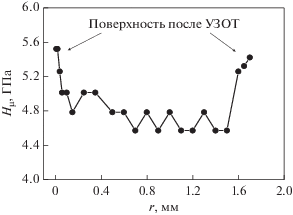
Увеличение микротвердости поверхностного слоя обусловлено дисперсионным упрочнением за счет образования нанокристаллических оксидных фаз и фазы α"-Ti и твердорастворным упрочнением в фазе Ti4Fe, представляющей собой твердый раствор железа в β-Ti. Микротвердость становится близкой к значениям, характерным для псевдо-β сплава (6.6 ГПа [18]).
ВЫВОДЫ
1. В процессе УЗОТ 3D-напечатанного образца сплава Ti–6Al–4V происходит интенсивная деформация поверхностного слоя, его расплавление, образование оксидного слоя на поверхности, а также микролегирование поверхностного слоя глубиной до 5 мкм железом с концентрацией до 22 ат. %.
2. В результате УЗОТ в поверхностном слое возникает градиентная микроструктура. На глубине до 2 мкм от поверхности образуется нанокристаллическая структура следующего фазового состава: оксиды титана и железа, метастабильная фаза Ti4Fe и α"-Ti. Под слоем с нанокристаллической структурой на глубине до 4 мкм образуется слой с метастабильной фазой Ti4Fe с размером зерна более 6 мкм и наночастицами аморфной фазы. На глубине более 5 мкм образуется субмикрокристаллическая структура, образованная фазами Ti4Fe и (α-Ti + β-Ti) с нанокристаллическими частицами фазы α"-Ti внутри зерен фаз α-Ti и β-Ti.
3. В результате УЗОТ микротвердость поверхностного слоя по Виккерсу по сравнению с микротвердостью основного металла вдали от поверхности возрастает на 0.9–1.1 ГПа.
Работа выполнена в рамках государственного задания ИФПМ СО РАН, тема номер FWRW-2021-0010.
Список литературы
Conghui Zhang, Wei Song, Fengbo Li, Xu Zhao, Yaomian Wang, Guizhi Xiao. Microstructure and corrosion properties of Ti–6Al–4V alloy by ultrasonic shot peening // Inst. J. Electrochem. Sci. 2015. V. 10. P. 9167–9178.
Li G., S.G. Qu, Pan Y.X., Li X.Q. Effects of the different frequencies and loads of ultrasonic surface rolling on surface mechanical properties and fretting wear resistance of HIP Ti–6Al–4V alloy // Applied Surface Science. 2016. V. 389. P. 324–334.
Панин В.Е., Сурикова Н.С., Лидер А.М., Бордулев Ю.С., Овечкин Б.Б., Хайруллин Р.Р., Власов И.В. Многоуровневый механизм усталостного разрушения титанового сплава Ti-6Al-4V в рамках подхода мезомеханики “пространство–время–энергия” // Физич. мезомеханика. 2018. Т. 21. № 4. С. 57–69.
Панин В.Е., Овечкин Б.Б., Хайруллин Р.Р., Лидер А.М., Бордулев Ю.С., Панин А.В., Перевалова О.Б., Власов И.В. Влияние кривизны решетки титана и титанового сплава Ti–6Al–4V на усталостную долговечность и ударную вязкость // Физич. мезомеханика. 2019. Т. 22. № 5. С. 5–12.
Jun Liu, Sergey Suslov, Azhar Vellor, Zhencheng Ren, Auezhan Amanov, Young-Sik Pyun, Ashlie Martini, Yalin Dong, Chang Ye. Surface nanocrystallization by ultrasonic nanocrystal surface modification and its effect on gas nitriding of Ti6Al4V alloy // Mater. Sci. Eng. A. 2018. V. 736. P. 335–343.
Хлыбов А.А., Кувшинов М.О. Исследование поверхностного слоя стали 03Н18К9М51 после ультразвуковой обработки // Физич. мезомеханика. 2019. Т. 22. № 6. С. 100–106.
Ультразвуковая обработка конструкционных материалов / Под ред. А.В. Панина. Томск: Издательский дом ТГУ. 2016. 172 с.
Yang Liu, Dongpo Wang, Caiyan Dang, Lixing Huo, Lijun Wang, Shu Cao. Feasibility study on preparation of coatings on Ti–6Al–4V by combined ultrasonic impact treatment and electrospark deposition // Mater. Design. 2014. V. 63. P. 488–492.
Panin A., Kazachenok M., Perevalova O., Martynov S., Panina A., Sklyarova E. Continuous Electron Beam Post-Treatment of EBF3-Fabricated Ti–6Al–4V Parts // Metals. 2019. V. 9(6). P. 699(16).
Горелик C.С., Расторгуев Л.Н., Скаков Ю.А. Рентгенографический и электронно-оптический анализ. М.: Металлургия, 1970. 328 с.
Перевалова О.Б., Панин А.В., Казаченок М.С. Влияние охлаждения подложки на микроструктуру и фазовый состав изделий из титанового сплава Ti–6Al–4V, полученных методами аддитивных технологий // Журн. технич. физики. 2020. Т. 90. Вып. 3. С. 410–418.
Илларионов А.Г., Нарыгига И.В., Илларионова С.М., Карабаналов М.С. Влияние параметров закалки на стабильность β-твердого раствора в высокопрочном титановом сплаве // ФММ. 2019. Т. 120. № 5. С. 518–523.
Sumiyama K., Ezawa H., Nakamura Y. Metastable Fe1 – xTix alloys produced by vapor quenching // Phys. Status Solidi, 1986. V. 93. № 1. P. 81–86.
Агравал П.Г., Древаль Л.А., Турчанин М.А. Термодинамические свойства расплавов железа с титаном, цирконием, гафнием // Порошковая металлургия. 2016. № 11/12. С. 93–104.
Donald I.W., Davies H.A. Prediction of glass-forming ability for metallic systems // J. Non-Cryst. Sol. 1978. V. 30. № 1. P. 77–85.
Vasylyev M.A., Chenakin S.P., Yatsenko L.F. Ultrasonic impact treatment induced oxidation of Ti6Al4V alloy // Acta Mater. 2016. V. 103. P. 761–774.
Гарип Й., Оздемир О. Изучение термоциклического окисления двухфазных электроспеченных титаналюминиевых сплавов с добавками хрома, молибдена и кремния // ФММ. 2020. Т. 121. № 4. С. 365–373.
Моисеев В.Н. Бета-титановые сплавы и перспективы их применения // Металловедение и термич. обр. металлов. 1998. № 12. С. 11–14.
Дополнительные материалы отсутствуют.
Инструменты
Физика металлов и металловедение