Физика металлов и металловедение, 2021, T. 122, № 8, стр. 816-823
Коррозионная стойкость сварных соединений ультрамелкозернистого псевдо-α-титанового сплава Ti–5Al–2V
В. Н. Чувильдеев a, *, А. В. Нохрин a, П. В. Андреев a, Н. Г. Сандлер b, А. М. Бахметьев b, М. М. Востоков a, К. В. Лихницкий a, В. И. Копылов a, c, М. С. Болдин a, Д. А. Гудзь a, Н. Ю. Табачкова d, e
a Нижегородский государственный университет им. Н.И. Лобачевского
603022 Нижний Новгород, пр. Гагарина, 23, Россия
b ОКБМ Африкантов
603074 Нижний Новгород, Бурнаковский проезд, 15, Россия
c Физико-технический институт Национальной академии наук Беларуси
220141 Минск, ул. Купревича, 10, Беларусь
d Национальный исследовательский технологический университет “МИСиС”
119049 Москва, Ленинский пр-т, 4, Россия
e Институт общей физики им. А.М. Прохорова Российской академии наук
119991 Москва, ул. Вавилова, 38, Россия
* E-mail: chuvildeev@nifti.unn.ru
Поступила в редакцию 09.12.2020
После доработки 23.03.2021
Принята к публикации 09.04.2021
Аннотация
Методом электроимпульсного плазменного спекания проведена диффузионная сварка ультрамелкозернистых (УМЗ) образцов титанового псевдо-α-сплава Ti–4.73% Al–1.88% V. Показано, что разрушение сваренных УМЗ образцов в условиях горячей солевой коррозии (ГСК) имеет двухстадийный характер – на первом этапе развивается межкристаллитная коррозия (МКК), которая затем переходит в язвенную коррозию. Установлено, что стойкость против МКК сварных швов определяется концентрацией ванадия на границах зерен, размером и объемной долей частиц β-фазы, а также наличием пор в сварном соединении. Показано, что сварные соединения УМЗ-образцов имеют более высокую твердость и стойкость против ГСК, чем крупнозернистых образцов.
ВВЕДЕНИЕ
В настоящее время титановые α- и псевдо-α-сплавы состава Ti–Al–V, Ti–Al–Zr, Ti–Al–Mo–V и др. широко используются в судостроении, паровых турбинах, ядерной энергетике и др. [1]. Формирование ультрамелкозернистой (УМЗ) структуры в титановых сплавах методом интенсивной пластической деформации является одним из перспективных способов повышения их характеристик. УМЗ-титановые сплавы имеют повышенную прочность, сопротивление ползучести, усталостную прочность [2, 3].
Важной проблемой стоящей на пути применения УМЗ-сплавов является задача их сварки. Широко используемые аргонно-дуговая или электронно-лучевая сварка не позволяют сохранить УМЗ-структуру. Электроимпульсное плазменное спекание (ЭИПС) [4] является одним из новых методов твердофазной сварки конструкционных материалов, в том числе титановых сплавов [5, 6]. Важным преимуществом ЭИПС является возможность реализации высоких скоростей нагрева (до 2500°С/мин), что позволяет сохранить в титановых сплавах УМЗ-структуру с высокими механическими свойствами.
Одним из наиболее опасных процессов для титановых сплавов, используемых в ядерной энергетике, является горячая солевая коррозия (ГСК) [7]. Она возникает при наличии солевых отложений на поверхности теплообменного оборудования, работающего при повышенных температурах (250–270°С). ГСК титановых сплавов представляет собой многостадийный процесс разрушения, протекающий в условиях воздействия повышенных температур, коррозионно-активных солевых растворов и кислорода [7].
Цель работы – изучение особенностей разрушения сварных соединений УМЗ-образцов сплава ПТ-3В в условиях ГСК и, в частности, изучение влияния параметров микроструктуры сварных образцов на сопротивление ГСК.
МАТЕРИАЛЫ И МЕТОДЫ
Объектом исследования является псевдо-α сплав ПТ-3В (Ti–4.73% Al–1.88% V), полученный на АО “Чепецкий механический завод” путем горячей деформации с постепенным понижением температуры из β- в (α + β)-область. УМЗ-структура формировалась методом равноканального углового прессования (РКУП) (режим Bc, число циклов N = 4, температура 450°С). Микроструктура крупнозернистых (КЗ) и УМЗ-образцов представлена на рис. 1. Подробное описание микроструктуры сплава в КЗ- и УМЗ-состоянии приведено в работах [5, 8].
Сварку образцов размером 7 × 7 × 3.5 мм проводили на установке Dr. Sinter SPS-625. Скорость нагрева Vh варьировали от 10 до 350°С/мин, приложенное давление Р – от 50 до 100 МПа, время t – от 0 до 90 мин. Сварку проводили при температурах, соответствующих двухфазной (α + β)-области (600, 700, 800°С) и однофазной β-области (1030, 1140°С). ЭИПС осуществляли в вакууме, без использования пресс-форм, что приводило к появлению касательных напряжений, действующих перпендикулярно оси приложения давления (рис. 2).
Рис. 2.
Схема диффузионной сварки образцов с помощью ЭИПС и расположение различных зон в исследуемых образцах.
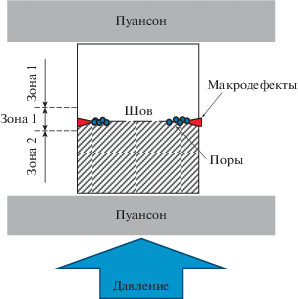
Микроструктуру исследовали с помощью растрового электронного микроскопа Jeol JSM-6490 и просвечивающего электронного микроскопа Jeol JEM-2100. Рентгенофазовый анализ (РФА) проводили с помощью дифрактометра Shimadzu XRD-7000. Измерения микротвердости Hv проводили на твердомере Duramin Struers 5 с нагрузкой 2 кг. Испытания на ГСК проводили в смеси кристаллических солей NaCl и KBr, смешанных в пропорции 300 : 1, при температуре 250°С в течение 500 ч, в условиях доступа кислорода. Характер коррозионного повреждения поверхности образцов оценивали с помощью металлографического микроскопа Leica DM IRM.
ЭКСПЕРИМЕНТАЛЬНЫЕ РЕЗУЛЬТАТЫ
Исследования показывают, что на краях КЗ-образцов, сваренных при низких давлениях, низких температурах или повышенных скоростях нагрева, присутствуют стыковые непровары размером ~50–70 мкм (рис. 3а, 3б). В вершинах макродефектов располагаются крупные поры, объемная доля которых уменьшается при удалении от края образца (от области максимальных растягивающих напряжений). На остальной бóльшей площади шва присутствуют микропоры, объемная доля которых зависит от режима ЭИПС (рис. 3в, 3г). Малая объемная доля пор наблюдается при диффузионной сварке КЗ образцов в интервале температур 700–800°C и при низких давлениях (50 МПа).
Рис. 3.
Типичные дефекты сварных соединений крупнозернистых (а, в) и УМЗ (б, г) сплавов ПТ-3В после диффузионной сварки (Vh = 50°C/мин, T = 800°C, t = 10 мин): (а, б) дефект шва, (в, г) микропора.
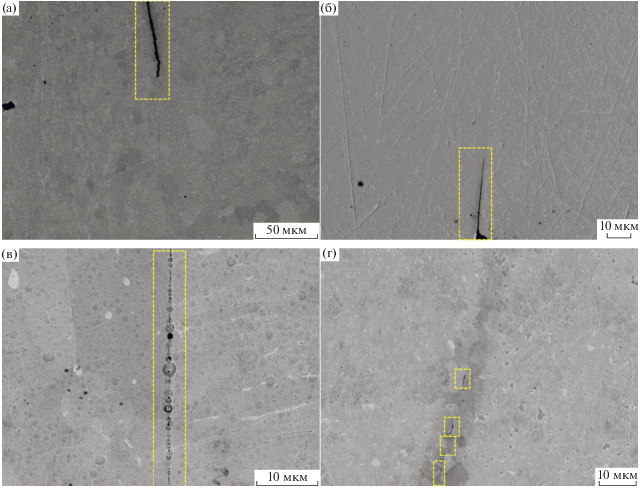
В сварных швах образцов УМЗ-сплавов стыковые макродефекты практически отсутствуют, объемная доля макро- и микропор мала, и они наблюдаются, преимущественно, в случае сварки при низких температурах (600°С) или при больших давлениях (70–100 МПа). Варьирование основных параметров ЭИПС не оказывает заметного влияния на средний размер зерна КЗ сплавов (табл. 1), в которых по границам зерен α-фазы пластинчатой формы наблюдается выделение частиц β-фазы (на рис. 1 более светлые частицы β‑фазы указаны стрелочками).
Таблица 1.
Параметры микроструктуры сплава ПТ-3В после диффузионной сварки
Режим сварки | Крупнозернистый сплав | УМЗ сплав | |||||||||||
---|---|---|---|---|---|---|---|---|---|---|---|---|---|
Т, °С | Vh, °С/мин |
t, мин | Р, МПа | dα, мкм |
dβ, мкм |
П | HV, ГПа | dα, мкм |
dβ, мкм |
П | HV, ГПа | ||
Шов | ОМ | Шов | ОМ | ||||||||||
Исходное состояние | 10–100 | 3–15 | – | – | 2.0–2.1 | 0.5 | – | – | – | 3.1–3.2 | |||
600 | 100 | 10 | 50 | 16 | 3.2 | В | 2.5 | 2.4–2.5 | 4.8 | 2.4 | В | 3.0 | 3.0–3.1 |
700 | 17 | 3.0 | С | 2.5 | 2.5–2.6 | 5.9 | 3.0 | Н | 2.8 | 2.8–2.9 | |||
800 | 18–19 | 5.1 | С | 2.3 | 2.3–2.4 | 6.9 | 3.3 | С | 3.2 | 3.2 | |||
1030 | 12 | – | Н | 2.5 | 2.4 | – | – | – | – | – | |||
1142 | – | – | – | – | – | 5.2 | Н | 2.6 | 2.6–2.7 | ||||
700 | 10 | 10 | 50 | 16–18 | 5.0 | Н | 2.6 | 2.5 | 6.8 | 3.1 | В | 2.5 | 2.5–2.6 |
50 | 17–18 | 3.5 | С | 2.6 | 2.4–2.3 | 5.5 | 3.3 | С | 2.7 | 2.8–2.9 | |||
100 | 18–19 | 3.0 | С | 2.4 | 2.5 | 5.9 | 3.0 | Н | 2.7 | 2.7–2.9 | |||
350 | 18 | 3.0 | В | 2.4 | 2.5 | 3.8 | 3.3 | Н | 2.9 | 3.0–3.1 | |||
700 | 100 | 10 | 50 | 18–19 | 3.5 | С | 2.5 | 2.4–2.6 | 5.9 | 3.3 | Н | 2.7 | 2.8–2.9 |
70 | 15 | 3.2 | В | 2.7 | 2.6–2.7 | 5.3 | 2.6 | В | 2.7 | 2.9–3.0 | |||
100 | 10 | 2.9 | В | 2.7 | 2.5–2.6 | 4.9 | 2.5 | В | 2.7 | 3.0–3.1 | |||
700 | 100 | 0 | 50 | 18–19 | 3.5 | В | 2.5 | 2.5–2.6 | 4.7 | 2.0 | В | 2.9 | 2.9–3.1 |
10 | 18–19 | 3.0 | С | 2.4 | 2.4–2.5 | 5.9 | 3.3 | С | 2.7 | 2.8–2.9 | |||
50 | 16–17 | 2.0 | С | 2.3 | 2.3–2.6 | 9.1 | 3.5 | Н | 2.6 | 2.8 | |||
90 | 12–13 | 2.0 | С | 2.4 | 2.4–2.6 | 9.3 | 3.5 | Н | 2.5 | 2.5–2.6 |
Объемная доля β-фазы в металле сварного соединения оказывается больше, чем в исходном КЗ-сплаве. Увеличение скорости нагрева, давления и времени выдержки приводит к снижению размера частиц β-фазы (табл. 1). Исследования УМЗ-образцов показывают, что увеличение температуры сварки от 600 до 800°С приводит к увеличению размера зерна от 4.8 до 6.9 мкм. Отметим, что размер зерна в УМЗ-образцах в 3–4 раза меньше, чем в КЗ-образцах, а на границах зерен присутствуют единичные частицы β-фазы размером 2–3 мкм. Повышение температуры и времени ЭИПС приводит к увеличению размера частиц β-фазы и размера зерен (табл. 1). Скорость нагрева не оказывает заметного влияния на размер частиц β-фазы, но приводит к уменьшению среднего размера зерна УМЗ-сплава.
Согласно РФА, солевые отложения на поверхности образцов после испытаний на ГСК представляют собой смеси NaCl, оксидов титана (TiO2,TiO) и глинозема, а также фаз на основе ванадия (VO1.15, V2Ti3O9) и Al3V. В продуктах коррозии образцов, сваренных при температурах выше 1000°С, вместо фаз на основе ванадия были обнаружены алюминийсодержащие фазы (TiAl2Cl8, AlTi3), а также следы VO2.
Результаты исследований сварных соединений показывают, что механизмы коррозионного разрушения металла в зоне сварного соединения и вне ее различны (табл. 2). В области сварного соединения КЗ-сплавов имеет место комбинация язвенной и щелевой коррозии (рис. 4a, 4б), причем глубина щелевой коррозии в случае высокопористых швов превышает 300 мкм. Вдали от сварных соединений наблюдается сочетание межкристаллитной коррозии (МКК) и язвенной коррозии. Наиболее интенсивная коррозия наблюдается в области скопления пластин α-фазы с повышенной объемной долей частиц β-фазы, что приводит к неоднородному распределению язв по поверхности образцов. Под крупными коррозионными язвами наблюдается МКК (рис. 4в).
Таблица 2.
Результаты коррозионных испытаний сварных соединений сплава ПТ-3В
Режим сварки | Крупнозернистый сплав | УМЗ сплав | |||||||||
---|---|---|---|---|---|---|---|---|---|---|---|
Т, °С | Vh, °С/мин |
t, мин | Р, МПа | Тип коррозии | hmax, мкм | hср, мкм |
Тип коррозии | hmax, мкм |
hср, мкм |
||
Зона I | Зона II | Зона I | Зона II | ||||||||
Исходное состояние | МКК | ~600 | ~400 | МКК | ~150 | ~100 | |||||
600 | 100 | 10 | 50 | Щ | Я, МКК | 223 | 162 ± 43 | Щ | Я, МКК | 188 | 124 ± 34 |
700 | Щ | Я, МКК | 235 | 231 ± 39 | – | Я, МКК | 420 | 273 ± 62 | |||
800 | Щ | Я | 280 | 265 ± 48 | Щ | Я, МКК | 400 | 285 ± 59 | |||
1030 | – | Я | 358 | 184 ± 35 | – | – | – | – | |||
1142 | – | – | – | Щ | Я, МКК | 557 | 211 ± 45 | ||||
700 | 10 | 10 | 50 | Щ | Я, МКК | 238 | 182 ± 45 | – | Я | 171 | 132 ± 24 |
50 | Щ | Я, МКК | 235 | 231 ± 39 | – | Я, МКК | 442 | 304 ± 51 | |||
100 | Щ | Я, МКК | 358 | 185 ± 75 | – | Я, МКК | 420 | 273 ± 42 | |||
350 | Щ | Я, МКК | 444 | 220 ± 92 | – | Я, МКК | 451 | 189 ± 36 | |||
700 | 100 | 10 | 50 | Щ | Я, МКК | 290 | 215 ± 49 | – | Я, МКК | 430 | 280 ± 30 |
70 | Щ | Я, МКК | 132 | 108 ± 21 | – | Я | 138 | 113 ± 28 | |||
100 | Щ | Я, МКК | 246 | 178 ± 77 | – | Я | 163 | 93 ± 40 | |||
700 | 100 | 0 | 50 | Щ | Я, МКК | 390 | 211 ± 82 | Щ | Я, МКК | 385 | 249 ± 58 |
10 | Щ | Я, МКК | 358 | 184 ± 75 | – | Я, МКК | 358 | 284 ± 45 | |||
50 | Щ | Я, МКК | 354 | 191 ± 67 | – | Я, МКК | 495 | 237 ± 40 | |||
90 | Щ | Я, МКК | 163 | 125 ± 62 | – | Я, МКК | 512 | 297 ± 47 |
Рис. 4.
Коррозионные дефекты на поверхностях КЗ образцов после испытания на ГСК: (а, б) щелевая коррозия в зоне I; (в) МКК в зоне II.
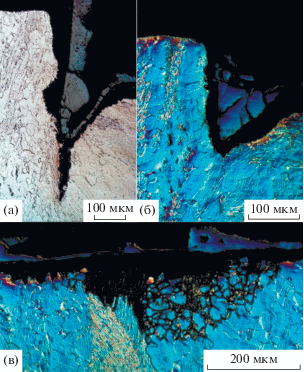
Следовательно, можно предположить, что на первом этапе ГСК происходит МКК в мелкозернистых областях скопления пластин α-фазы, а затем развивается язвенная коррозия. Наиболее существенно на глубину коррозии сварных соединений КЗ-образцов влияет давление и время ЭИПС (табл. 2). Отметим, что размер коррозионных дефектов в сварных КЗ-образцах оказывается меньше, чем в сплаве ПТ-3В в исходном состоянии (см. [7]).
В УМЗ-образцах щелевая коррозия наблюдалась только в случае сварных соединений с повышенной пористостью. Вдали от линии сварного соединения наблюдается комбинация МКК и язвенной коррозии (рис. 5), как и в случае КЗ-образцов. Увеличение времени и температуры ЭИПС приводит к увеличению глубины коррозии в сварных соединениях УМЗ-сплавов (табл. 2). В случае малых температур сварки, скоростей нагрева и давления глубина коррозии оказалась достаточно мала и не превышала глубины МКК в УМЗ-сплаве после РКУП (см. [8]). Сварка при температуре 700°С, вблизи границы (α + β)-области, при среднем давлении (70 МПа) и при скорости нагрева 10°С/мин является наиболее оптимальной – средняя глубина коррозионных дефектов составляла ~110–130 мкм, а щелевая коррозия швов отсутствовала. Подчеркнем, что при этих режимах ЭИПС средняя глубина язв в УМЗ-образцах оказалась в 1.5–2 раза меньше, чем глубина коррозионных язв в КЗ-образцах. Таким образом, можно сделать вывод, что УМЗ-образцы имеют более высокую коррозионную стойкость по сравнению с КЗ-образцами.
Результаты испытаний на ГСК УМЗ-образцов показывают, что повышение температуры ЭИПС от 600 до 800°С приводит к увеличению средней глубины коррозионных язв от 124 ± 34 до 285 ± ± 59 мкм, максимальная глубина коррозии при этом увеличивается от 188 до 400–420 мкм. Увеличение скорости нагрева от 50 до 350°С/мин приводит к уменьшению средней глубины коррозии от 304 ± 51 до 189 ± 36 мкм. Приложенное давление приводит к слабому уменьшению глубины коррозии, а варьирование время выдержки практически не влияло на коррозионную стойкость сварных УМЗ-образцов (см. табл. 2).
Исследования твердости показали, что режимы ЭИПС не оказывают существенного влияния на Hv металла швов и основного металла КЗ образцов. Твердость КЗ-образцов составляет 2.4–2.6 ГПа. Повышенная твердость сварных образцов по сравнению с твердостью сплава ПТ-3В в исходном состоянии (~2.1–2.2 ГПа) связана, вероятно, с деформационным упрочнением сплава. Этот вывод косвенно подтверждается увеличением твердости металла шва до 2.7 ГПа в случае сварки под давлением 100 МПа (табл. 1).
Твердость металла шва и основного металла УМЗ-образцов превышает твердость КЗ-образцов на ~0.4–0.8 ГПа. Самая высокая твердость металла шва (~3.0–3.2 ГПа) наблюдается в УМЗ-образцах, полученных при низких температурах, высоких скоростях нагрева и малых временах выдержки. Увеличение скорости нагрева до 350°С/мин позволяет сформировать высокоплотный шов с УМЗ-структурой и высокой твердостью (2.9–3.1 ГПа).
ОБСУЖДЕНИЕ РЕЗУЛЬТАТОВ
Как отмечалось во введении, ГСК является одним из наиболее опасных процессов разрушения титановых сплавов. Анализ данных [7–9] показывает, что ГСК в α- и псевдо-α-титановых сплавах имеет преимущественно межзеренный характер. При заданных условиях испытаний склонность α- и псевдо-α-титановых сплавов к ГСК зависит, прежде всего, от химического и фазового состава границ зерен [7, 8].
В нашем случае наиболее заметное влияние на склонность сплава к ГСК оказывает: (i) концентрация коррозионно-активных легирующих элементов (ЛЭ) на границах зерен, (ii) наличие частиц β-фазы на границах зерен, (iii) наличие пор в сварных соединениях. Согласно [8], образование зернограничных сегрегаций коррозионно-активных ЛЭ, а также наличие частиц β-фазы, содержащих высокую концентрацию β-стабилизаторов (ванадия), может привести к образованию микрогальванических пар, ускоряющих электрохимическую коррозию, а также к ускоренной химической коррозии границ зерен. Отрицательное влияние пор проявляется, прежде всего, за счет увеличения площади свободной поверхности, участвующей в химических или электрохимических реакциях.
Проанализируем влияние режимов диффузионной сварки методом ЭИПС на стойкость сварных образцов КЗ и УМЗ-сплава ПТ-3В к ГСК.
Для простоты анализа предположим, что пластическая деформация металла в ходе ЭИПС влияет на интенсивность МКК, прежде всего за счет влияния на пористость шва и структурно-фазовое состояние границ зерен титанового сплава.
Как уже упоминалось, щелевая коррозия имела место в пористых сварных соединениях – чем больше макродефектов и макропор в сварных соединениях – тем интенсивнее происходит щелевая коррозия сварных образцов при ГСК.
Проанализируем коррозионную стойкость металла вдали от зоны сварки. Для этого, прежде всего, следует учитывать особенности эволюции структуры сплавов в условиях высокоскоростной диффузионной сварки под давлением.
В исходном состоянии микроструктура сплава ПТ-3В представляет смесь равноосных зерен и пластин α-фазы (рис. 1). Толщина пластин α-фазы составляет 10–20 мкм, размер равноосных зерен α-фазы составляет 50–100 мкм. На границах пластин α-фазы присутствуют вытянутые частицы β-фазы длиной до ~10 мкм и шириной менее 0.5 мкм (рис.1). Как показано в [8], в структуре КЗ-сплава ПТ-3В наблюдается два типа границ зерен. Границы зерен первого типа (~90–95 об. %) свободны от сегрегаций ЛЭ. Локальная концентрация алюминия в таких границах составляет 3.8 ± 0.9%, а концентрация ванадия – 1.9 ± 0.2%, что мало отличается от концентрации алюминия и ванадия в зернах титана. Границы зерен второго типа “обогащены” ванадием, локальная концентрация которого может достигать 10%. Отметим также, что в частицах β-фазы концентрация ванадия достигала 16–18%, а концентрация алюминия составляет менее 1% [8].
Как показано в [8], уменьшение концентрации ванадия на границах зерен, а также отсутствие частиц β-фазы на границах зерен после РКУП при температуре 450–475°C, является причиной высокой стойкости УМЗ сплава ПТ-3В к ГСК.
После нагрева со скоростью 100°С/мин до 600°C и выдержки в течение 10 мин под давлением 50 МПа глубина коррозионных дефектов в КЗ-сплаве уменьшилась от 400–600 до 162 ± 43 мкм. Поскольку при таком режиме не происходит заметного изменения параметров частиц β-фазы (табл. 1), то можно предположить, что причиной повышенной коррозионной стойкости образцов является уменьшение локальной концентрации ванадия в границах зерен второго типа (см. выше) при ЭИПС.
Обобщение результатов исследований структуры КЗ-образцов показало, что при ЭИПС наблюдается увеличение размера и объемной доли частиц β-фазы (табл. 1). Наиболее отчетливо это выражалось после сварки при 800°C, соответствующей двухфазной (α + β)-области. Этот результат хорошо согласуется с данными работы [9], где было показано, что отжиг в (α + β)-области приводит к увеличению размеров частиц β-фазы и одновременному уменьшению в них концентрации ванадия. Видимо, увеличение размеров и объемной доли частиц β-фазы привело к увеличению глубины коррозионных дефектов.
Этот результат также хорошо объясняет наблюдаемое повышение коррозионной стойкости КЗ-образцов с увеличением времени сварки от 0 до 90 мин при температуре 700°С вблизи границы (α + β)-области (табл. 2). Выдержка при этой температуре привела к частичному растворению частиц β-фазы (табл. 1), и, вероятно, к снижению концентрации ванадия на границах зерен титана, что в соответствии с [8] приводит к уменьшению глубины МКК.
Рассмотрим характер изменений структуры УМЗ-сплава в процессе диффузионной сварки. Как было показано выше, структура УМЗ-сплава близка к структуре чистого титана (зернограничные сегрегации ванадия и частицы β-фазы отсутствуют). Отметим, что процесс рекристаллизации начинается при нагреве УМЗ-сплава до 500–550°C [8], в результате чего быстро мигрирующие границы зерен при ЭИПС захватывают атомы ванадия, изначально равномерно распределенные в кристаллической структуре титана. Этот фактор, по нашему мнению, является одной из причин снижения коррозионной стойкости УМЗ-сплавов с повышением температуры ЭИПС (табл. 2). В случае повышения температуры сварки до границы (α + β)-области, образование и рост частиц β-фазы может быть дополнительным фактором, способствующим снижению коррозионной стойкости УМЗ-сплавов.
Отметим, что увеличение времени выдержки при 700°C также приводит к интенсивному росту зерен (табл. 1) и, следовательно, к увеличению концентрации ванадия на мигрирующих границах зерен. Это способствует увеличению глубины дефектов МКК (см. табл. 2). Уменьшение размеров коррозионных дефектов с увеличением скорости нагрева можно объяснить аналогичным образом – уменьшение продолжительности нагрева приведет к снижению скорости роста зерна и, как следствие, к снижению концентрации “вредных” ЛЭ на мигрирующих границах зерен.
Отметим, что приведенные выше доказательства важной роли сегрегаций ванадия на границах зерен и частиц β-фазы в развитии МКК, косвенно хорошо соответствуют результатам испытаний образцов, сваренных при Т > 1000°C. Объемная доля частиц β-фазы в этом случае достаточно велика, однако это не приводит к существенному снижению коррозионной стойкости сплава – средняя глубина дефектов МКК в КЗ и УМЗ-образце составляет 184 мкм и 211 мкм соответственно (табл. 2). По нашему мнению, это связано с исчезновением зернограничных сегрегаций ванадия и снижением его концентрации в частицах β-фазы после нагрева до Т > 1000°C, что хорошо соответствует результатам работ [9, 10].
ЗАКЛЮЧЕНИЕ
1. Показано, что образцы сплава с УМЗ-структурой обладают более высокой свариваемостью по сравнению с крупнозернистыми сплавами, в сварных соединениях которых наблюдались непровары, вызывающие щелевую коррозию. В УМЗ-образцах макродефекты швов практически отсутствовали, а пористость шва очень мала, что обеспечивает высокую стойкость сварных соединений УМЗ-образцов к щелевой коррозии.
2. Коррозионная стойкость КЗ сварных образцов выше коррозионной стойкости сплава ПТ-3В в исходном состоянии. Коррозионные дефекты на поверхности КЗ образцов сосредоточены в области мелкозернистых пластин α-фазы, на границах зерен которых наблюдается повышенная объемная доля β-фазы. Разрушение КЗ образцов в процессе ГСК имеет двухстадийный характер – на первом этапе развивается МКК, которая затем переходит в язвенную коррозию.
3. Коррозионная стойкость УМЗ-образцов зависит, главным образом, от концентрации ванадия на границах зерен. Увеличение концентрации ванадия на мигрирующих границах зерен с ростом температуры и времени ЭИПС отрицательно влияет на устойчивость к ГСК. Показано, что диффузионная сварка, выполняемая в режиме высокоскоростного нагрева (350°С/мин) до температуры, близкой к границе фазового перехода (700°C), при давлении 50 МПа и выдержке 10 мин, позволяет обеспечить формирование мелкозернистой структуры с повышенной твердостью и коррозионной стойкостью.
Работа выполнена при поддержке Российского научного фонда (грант № 19-73-00295).
Список литературы
Горынин И.В., Ушков С.С., Хатунцев А.Н., Лошакова Н.И. Титановые сплавы для морской техники. Санкт-Петербург: Политехника, 2007. 384 с.
Segal V.M. Equal-channel angular extrusion (ECAE): From a laboratory curiosity to an industrial technology // Metals. 2020. V. 10. № 2. Art. 244.
Жеребцов С.В. Эффективность упрочнения титана и титановых сплавов разных классов при формировании ультрамелкозернистой структуры большой пластической деформацией // Металлы. 2012. № 6. С. 63–70.
Дудина Д.В. Использование установки электроискрового спекания для термической обработки порошковых и компактных материалов // Неорганич. материалы. 2017. Т. 53. № 6. С. 673–678.
Chuvil’deev V.N., Nokhrin A.V., Kopylov V.I., Boldin M.S., Vostokov M.M., Gryaznov M.Yu., Tabachkova N.Y., Tryaev P. Spark plasma sintering for high-speed diffusion bonding of the ultrafine-grained near-α Ti–5Al–2V alloy with high strength and corrosion resistance for nuclear engineering // J. Mater. Sci. 2019.V. 54. № 24. P. 14926–14949.
Yang J., Wang G.F., Jiao X., Gu Y., Liu Q., Li Y. Current-assisted diffusion bonding of extruded Ti–22Al–25Nb alloy by Spark Plasma Sintering: Interfacial microstructure and mechanical properties // J. Mater. Eng. Perform. 2018. V. 27. № 6. P. 3035–3043.
Chevrot Th. Pressure effects on the holt-salt stress-corrosion cracking of titanium alloys. PhD Thesis. Cranfield University. School of Industrial and Manufacturing Science. 1994. 215 p.
Chuvil’deev V.N., Kopylov V.I., Nokhrin A.V., Tryaev P.V., Kozlova N.A., Tabachkova N.Yu., Lopatin Yu.G., Ershova A.V., Mikhaylov A.S., Gryaznov M.Yu., Chegurov M.K. Study of mechanical properties and corrosive resistance of ultrafine-grained α-titanium alloy Ti–5Al–2V // J. All. Comp. 2017. V. 723. P. 354–367.
Gornakova A.S., Straumal B.B., Prokofiev S.I. Coarsening of (αTi) + (βTi) microstructure in the Ti–Al–V alloy at constant temperature // Adv. Eng. Mater. 2018. V. 20. № 11. Art. № 1800510.
Gornakova A.S., Prokofjev S.I. Energetics of intergranular and interphase boundaries in Ti–6Al–4V alloys // J. Mater. Sci. 2020. V. 55. P. 9225–9236.
Дополнительные материалы отсутствуют.
Инструменты
Физика металлов и металловедение