Физика металлов и металловедение, 2021, T. 122, № 8, стр. 838-844
Исследование кратковременной высокотемпературной ползучести алюмоматричного композита Al–6Zn–2.5Mg–2Cu/10SiCp
Н. Б. Пугачева a, Д. И. Крючков a, *, А. В. Нестеренко a, С. В. Смирнов a, В. П. Швейкин a
a Институт машиноведения УрО РАН
620049 Екатеринбург, ул. Комсомольская, 34, Россия
* E-mail: kru4koff@bk.ru
Поступила в редакцию 21.12.2020
После доработки 01.04.2021
Принята к публикации 08.04.2021
Аннотация
Исследовано изменение микроструктуры алюмоматричного композита (АМК) в условиях кратковременной высокотемпературной ползучести при температурах в диапазоне 470–570°C. Установлена возможность деформирования композита без разрушения, преимущественно в условиях сжимающих напряжений, при давлениях ниже предела текучести. Показано, что существенной деформируемости материала способствуют структурные изменения в алюминиевой матрице (сплав Al–6Zn–2.5Mg–2Cu). При температурах выше 530°С увеличение скорости деформации и значений истинной деформации обусловлено локальным образованием жидкой фазы по эвтектической реакции α + S(Al2CuMg) → L. В условиях действия сжимающих напряжений при температуре деформации 540–570°С образовавшийся расплав затекает в микропоры между частицами наполнителя SiC. При этом происходит частичное растворение карбида кремния в алюминиевой матрице, и упрочняются связи между матрицей и наполнителем.
ВВЕДЕНИЕ
Изучение деформационного поведения новых композитных материалов необходимо для оценки их применимости в машиностроении. Вызывает интерес алюмоматричные композиты (АМК) с металлической матрицей из алюминия и его сплавов [1, 2]. Эти материалы обладают малым удельным весом, высокими показателями тепло- и электропроводности, что предполагает их использование в качестве конструкционных материалов в автомобилестроении, электронике и авиационной технике [3–6].
Все большее внимание уделяется исследованиям специальных технологических обработок (термической и термо-деформационной), направленных на изменение структуры, фазового состава и свойств АМК. Например, за счет предварительной обработки и создания мелкозеренной структуры появляется возможность сверхпластического деформирования сплава системы Al–Mg–Zn–Fe–Ni–Zr–Sc [7–9] или композита Al6013/20SiCp (p – означает, что использован армирующий компонент в виде частиц) [10]. При использовании в качестве матрицы термически упрочняемых сплавов появляется дополнительная возможность повышения прочностных характеристик или улучшения технологической обрабатываемости за счет реализации фазовых превращений [11–13]. К числу наиболее перспективных технологических процессов, предполагающих развитие и совершенствование способов обработки высокопрочных алюминиевых сплавов и композитов на их основе, относятся медленное горячее формоизменение заготовок в режиме кратковременной ползучести [14–19] и деформация в полужидком состоянии [20].
Цель нашего исследования – оценка деформационного поведения и изменения структуры АМК на основе высокопрочного алюминиевого сплава системы Al–6Zn–2.5Mg–2Cu с дискретным армированием 10% по массе частицами карбида кремния при осевом сжатии в условиях кратковременной высокотемпературной ползучести.
МАТЕРИАЛ И МЕТОДИКА ИССЛЕДОВАНИЯ
Исследована структура, фазовый состав, фазовые превращения и высокотемпературная кратковременная ползучесть композита, полученного спеканием гранулированного алюминиевого сплава Al–6Zn–2.5Mg–2Cu (российское обозначение В95) с частицами карбида кремния SiC в количестве 10 мас. %. Микроструктуру композита в исходном состоянии и после испытаний на ползучесть исследовали на поперечных шлифах с помощью оптического микроскопа NEOPHOT-21. Фазовый состав определяли на рентгеновском дифрактометре Shimadzu XRD 7000 в монохроматизированном Kα излучении хромового анода в узком интервале дифракционных максимумов с максимальной интенсивностью для фаз T-(Mg3Zn3Al2), η-(MgZn2), S-(Al2CuMg), Al4SiC4 и Al4C3 при скорости вращения гониометра 0,25 град/мин. Локальный химический состав определяли на сканирующем электронном микроскопе TESCAN VEGAII XMU с энергодисперсионной приставкой фирмы OXFORD и программным обеспечением INCA. Измерение тепловых эффектов и определение характеристических температур композита выполнено методом дифференциальной сканирующей калориметрии (ДСК) на термоанализаторе STA 409 Netzsch-Geratebau-Gmbh.
Таблица 1.
Параметры испытаний и характеристики образцов после деформации
T, °С | p0, МПа | p, МПа | t, мин | ξ*, с–1 | е |
---|---|---|---|---|---|
470 | 4.83 | 4.79 | 66 | 5.05 × 10–6 | 0.02 |
500 | 4.82 | 4.73 | 70 | 9.52 × 10–6 | 0.04 |
510 | 4.90 | 4.89 | 81 | 1.44 × 10–5 | 0.07 |
520 | 4.82 | 4.56 | 72 | 5.79 × 10–5 | 0.25 |
530 | 4.73 | 3.90 | 78 | 8.33 × 10–5 | 0.39 |
540 | 4.80 | 3.73 | 75 | 1.22 × 10–4 | 0.55 |
550 | 4.50 | 2.90 | 78 | 1.52 × 10–4 | 0.71 |
560 | 4.79 | 2.37 | 86 | 1.71 × 10–4 | 0.88 |
570 | 4.81 | 1.94 | 104 | 1.65 × 10–4 | 1.03 |
Деформационные испытания проводили в условиях одноосного сжатия (осадки) цилиндрических образцов с использованием специального разработанного устройства. Устройство и методика проведения испытаний подробно описаны в работе [21]. По геометрическим размерам определяли истинную деформацию е = ln(h0/h), где h0 – начальная высота образца, h – конечная высота образца. Начальное давление p0 на образец рассчитывали как отношение веса груза к исходной площади образца. После испытания рассчитывали среднюю, за общее время испытания t, скорость деформации ξ*. Нагрев образцов проводили до температур в диапазоне от 470 до 570°С.
РЕЗУЛЬТАТЫ И ОБСУЖДЕНИЕ
В исходном состоянии исследованный композит имеет ячеистое строение: частицы наполнителя SiC расположены на поверхности матричных гранул (рис. 1). Известно [12, 13, 22], что термически упрочняемые алюминиевые сплавы системы Al–Zn–Mg–Cu имеют следующий фазовый состав: α-твердый раствор на основе алюминия, частицы упрочняющих интерметаллидных S-, Т- и η-фаз. Частицы S-фазы Al2CuMg имеют форму игл длиной 2 мкм и шириной 0,5 мкм. В исследованном композите частицы S-фазы обнаружены по границам зерен внутри гранул матрицы (рис. 1). Размер гранул матрицы составляет от 10 до 150 мкм, а размеры зерна меняются от 0.5 до 5 мкм. Фазовый рентгеноструктурный анализ показал наличие двух интерметаллидов в исследованном композите: S-фазы Al2CuMg и η-фазы MgZn2 (рис. 2). Выделение частиц Т- и η-фаз в полном объеме, имеющих размеры 20–50 нм, происходит в ходе старения сплава В95 при 120–170°С [13]. В исследованном композите их количество крайне мало, а рефлексы на дифрактограммах весьма слабые или находятся на уровне фона.
Рис. 1.
Микроструктура исследованного композита (изображение во вторичных электронах): М – матрица Al–6Zn–2.5Mg–2Cu; SiC – частицы наполнителя; S – игольчатые частицы интерметаллида Al2CuMg по границам зерен матрицы.
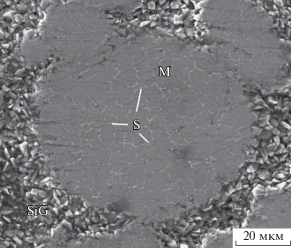
Калориметрические исследования композита показали, что при температуре 534°C в нем начинает реализовываться эндотермическое превращение (рис. 3), которое, очевидно, соответствует эвтектическому превращению α + S(Al2CuMg) → L.
В работе [23] было установлено, что данный АМК с представленной исходной структурой в условиях жесткого нагружения проявляет низкие пластические свойства. Поэтому предварительно, для улучшения структуры и пластических свойств, подобные материалы подвергаются горячей обработке давлением с преобладанием в очаге деформации сжимающих напряжений [24]. Учитывая это, для изучения деформационного поведения композита в условиях ползучести использовали одноосную осадку цилиндрических образцов в интервале температур 470–570°С. При более низких температурах в матрице присутствуют частицы упрочняющих Т-, η- и S-фаз, которые будут препятствовать развитию процесса ползучести в композите. При температуре 470°С частицы Т-, η-фаз растворятся полностью, а частицы S-фазы частично. При температуре выше 570°C существует вероятность появления жидкой фазы во всем объеме композита, что приведет к потере устойчивости образцов и их разрушению.
Изменение температуры образца при нагреве до заданных значений отражено на рис. 4. Как видно из графика, режим нагрева для всех образцов практически совпадает. Можно выделить начальный участок приблизительно до 100°C, с низкой скоростью нагрева, далее до 400°C скорость нагрева постоянна, после чего начинает уменьшаться к моменту выхода на заданную для каждого образца температуру. Замедление скорости нагрева на этапе завершения испытания, наиболее характерно выражено для температур 510 и 570°C.
Зависимость средней скорости деформации от температуры нагрева представлена на рис. 5. При деформации, сопровождающейся нагревом до 500°С, средняя за процесс скорость деформации (ξ*) составила не более 1 × 10–5 с–1. В интервале температур от 500 до 540°С ξ* варьируется от 1 × 10–5 до 1 × 10–4 с–1. При температурах выше 540°С ξ* чуть выше 1 × 10–4 с–1. Начиная с температуры нагрева 510°С наблюдается рост значений скорости деформации, а после 550°С ее значения находятся приблизительно на одном уровне.
При увеличении деформации наблюдается снижение давления за счет увеличения площади контактной поверхности образца. Давление на заготовку в начальный и конечный момент времени отображено в табл. 1 (p0 – начальное давление на недеформированный образец, обеспечивающееся грузом, и p – давление в конечный момент испытания). Начиная с температуры 520°C прослеживается существенное падение давления p, которое при росте температуры нагрева продолжает снижаться и при 570°C составляет 0.4 от начального значения.
При нагреве образцов до 510°C включительно, деформация не превышает 0.07. При более высоких температурах происходит интенсивный рост значений истинной деформации. Начиная с температуры нагрева 520°C деформация достигает уже 0.25, увеличиваясь в дальнейшем приблизительно на 0.15 при повышении температуры нагрева на каждые 10 градусов.
После деформации за время нагрева до 470°C размеры образца изменились несущественно. При этом состояние поверхности сохранилось в неизменном виде, каких-либо следов деформационного происхождения на боковой поверхности не зафиксировано (рис. 6а). В центральной части отмечено скопление частиц наполнителя SiC.
Рис. 6.
Состояние боковой поверхности образцов после испытаний при нагреве до 470 (а), 530 (б), 570°С (в).
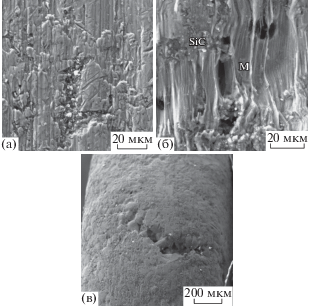
Заметная деформация образцов происходит при нагреве до температуры выше 520°C. При нагреве до 530°C истинная деформация составила 0.39. После испытания на боковой поверхности образца (рис. 6б) появляются полосы локализации деформации матрицы, расположенные на расстоянии 5–10 мкм друг от друга. Полосы деформации прерываются на частицах наполнителя SiC или огибают их. Частицы наполнителя SiC, расположенные на боковой поверхности образца, не меняют свои размеры, форму, характер распределения и не разрушаются. Такая же картина наблюдается и при температуре испытаний 540°C. При температурах нагрева выше 550°C истинная деформация образцов составляет более 0.7, а изменение высоты образцов более 50%. Максимальную деформацию образец претерпевает за время нагрева до 570°C. На рис. 6в показана боковая поверхность такого образца, на которой наблюдается макроразрушение. На наш взгляд, это происходит в результате ослабления связей на границах зерен внутри гранул матрицы, а также на границе “матрица–наполнитель” после образования жидкой фазы в результате протекания эвтектического превращения α + S(Al2CuMg) → L. При этом стоит учитывать, что на боковой поверхности образцов при образовании бочки действуют растягивающие напряжения.
В процессе испытаний на высокотемпературную кратковременную ползучесть в исследованном композите происходят изменения структуры, которые и определяют полученные результаты. При исследованиях алюмоматричного композита методом ДСК в нашей работе установлены три критические температуры: Т1 = 534°C, Тс = 594°C и Тл = 636°C. Малый эндотермический пик при температуре 534°C соответствует локальному оплавлению по межфазным границам между α-твердым раствором и частицами S-фазы в алюминиевой матрице, что совпадает с результатами исследований [25–27]. По мнению авторов этих работ, появление маленького эндотермического пика объясняется только повышенной концентрацией атомов растворенных веществ в твердом растворе. На наш взгляд, главным является локальное появление жидкой фазы в результате эвтектического превращения α + S(Al2CuMg) → L в соответствие с диаграммой состояния системы Al–Zn–Mg–Cu [13]. В результате этого превращения возможна сегрегация атомов растворенных элементов (Mg, Zn и Cu) в твердом растворе на основе алюминия, но первенство остается за эвтектическим превращением. Согласно выводам работ [28, 29], в композитах, имеющих одинаковый матричный и армирующий состав, образование жидкой фазы может начинаться при различной температуре, из-за различий в морфологии и размерах упрочняющих частиц. В использованном нами материале для деформирования оптимальны температуры 530–550°C, выше которых увеличившееся количество жидкой фазы приводит к ослаблению связей на границах раздела зерен матрицы между собой и с упрочняющими частицами, из-за чего возникает макротрещина (рис. 6в).
При температуре 520°C в матрице композита полностью растворились интерметаллиды Т(Mg3Zn3Al2) и η(MgZn2), а частицы S(Al2CuMg) частично растворились и коагулировали, приобретя сферическую форму, а их размер составил менее 1 мкм. В этих условиях деформация образца происходит более легко за счет скольжения дислокаций в алюминиевой матрице.
На боковой поверхности образца деформация матрицы проявляется в образовании полос сброса (полос локализованной деформации), длина которых ограничена размерами гранул матрицы, что соответствует данным работ [18, 19]. Полоса деформации прерывается на границах гранул матрицы, где сосредоточены частицы наполнителя SiC (рис. 6б). Если размер матричных гранул более 70 мкм, то расстояние между полосами деформации составляет 15–20 мкм. При размере гранул менее 30 мкм, полосы деформации расположены гораздо ближе друг к другу – примерно на расстоянии 5–10 мкм. Таким образом, после испытаний при 530°C матрица находится в неоднородном деформированном состоянии: матричные гранулы меньших размеров (менее 30 мкм) деформируются в большей степени.
Увеличение температуры выше 530°C приводит к образованию жидкой фазы по эвтектической реакции α + S(Al2CuMg) → L. Об этом свидетельствуют характерные для эвтектик скелетообразные структуры, наблюдаемые на поперечных сечениях образцов в зонах действия растягивающих напряжений (рис. 7а, 7в, 7г). Появление жидкой фазы вблизи частиц наполнителя облегчает растворение поверхностного слоя частиц карбида кремния SiC, что экспериментально подтверждает зафиксированное при микрорентгеноспектральном анализе повышенное содержание кремния (до 12 мас. %) в продуктах эвтектического превращения. Образовавшийся расплав проникает между частицами наполнителя SiC в местах их скопления, происходит “залечивание” микропор на участках стыка трех и более частиц карбида кремния SiC.
Рис. 7.
Структура образца после испытаний при 570°С: а – общий вид поперечного разреза образца; б – микроструктура в центральной части (участок А); в – микроструктура на участке В; г – микроструктура на участке С.
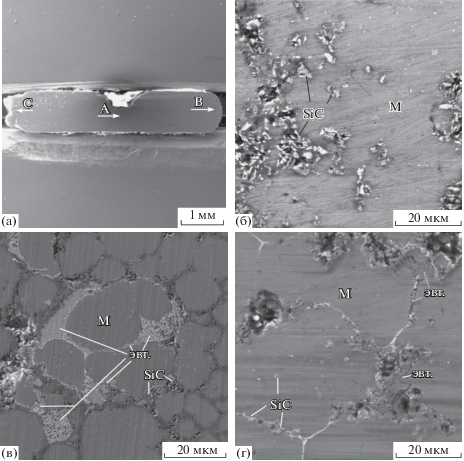
В центральной части (участок А на рис. 7а) образцов, где деформация в условиях сжимающих напряжений максимальна, наблюдали заполнение промежутков между частицами SiC алюминиевой матрицей, разбиение сетчатых скоплений частиц SiC и формирование более однородного их распределения по объему (рис. 7б). Эвтектические структуры в центральной части отсутствовали.
Авторы работы [30] на основе исследований ползучести сделали вывод, что максимальная деформируемость проявляется при некотором оптимальном количестве жидкой фазы. Дальнейшее увеличение количества жидкой фазы приводит к межкристаллитному разрушению, что снижает способность деформироваться без образования дефектов.
Проведенное исследование показало, что условия кратковременной ползучести способствуют деформации без разрушения. Даже несмотря на то, что такие условия не соответствуют развитию динамической рекристаллизации, как указано в работе [31]. Кроме того, в условиях кратковременной ползучести не происходит растрескивание или какого-либо повреждения частиц наполнителя SiC, в отличие от работ [32, 33], где зарождение трещин возникало при растрескивании частиц упрочняющей фазы.
ЗАКЛЮЧЕНИЕ
Установлено, что, начиная с температуры 520°C, нагрев на каждые 10 градусов дает прирост истинной деформации приблизительно на 0.15 в условиях снижающегося давления и роста скорости деформации.
Установлено, что при температурах испытаний выше 530°C на границах между твердым раствором и частицами S-фазы локально образуется жидкая фаза по реакции α + S(Al2CuMg) → L. В результате после охлаждения композита в зонах действия растягивающих напряжений образуется эвтектическая структура.
Образование легкоплавкой эвтектики в исследованном композите приводит к затеканию расплава в микропоры между частицами наполнителя SiC в областях действия сжимающих напряжений. При этом происходит частичное растворение карбида кремния в алюминиевой матрице, и упрочняются связи между матрицей и наполнителем.
Результаты выполненных исследований показали, что формоизменение алюмоматричного композита Al–6Zn–2.5Mg–2Cu/10SiCp изготовленного методом порошковой металлургии целесообразно проводить в режиме высокотемпературной ползучести в температурном диапазоне 530–550°С, при котором эффективно проявляются фазовые превращения в алюминиевой матрице.
Работа выполнена в рамках программы ФНИ государственных академий наук по теме АААА-А18-118020790142-9. При проведении испытаний использовалось оборудование ЦКП “Пластометрия” ИМАШ УрО РАН.
Список литературы
Hunt W.H. Particulate Reinforced MMCs, Chapter 3.26 in Comprehensive Composite Materials, Vol. 3: Metal Matrix Composites, by ed. T.W. Clyne. Pergamon, Oxford, UK, 2000. P. 701–715.
Miracle D.B. Metal matrix composites–from science to technological significance // Compos. Sci. Technol. 2005. V. 65. № 15. P. 2526–2540.
Kaczmar J.W., Pietrzak K., Włosin´ski W. The production and application of metal matrix composite materials // J. Mater. Process Technol. 2000. V. 106. № 1. P. 58–67.
Sumankant Yashpal, Jawalkar C.S., Verma Ajay Singh, Suri N.M. Fabrication of Aluminium Metal Matrix Composites with Particulate Reinforcement: A Review // Mater. Today: Proceedings. 2017. V. 4. № 2. Part A. P. 2927–2936.
Mavhungu S.T., Akinlabi E.T., Onitiri M.A., Varachia F.M. Aluminum Matrix Composites for Industrial Use: Advances and Trends // Procedia Manufacturing. 2017. V. 7. P. 178–182.
Koli Dinesh Kumar, Agnihotri Geeta, Purohit Rajesh. Advanced Aluminium Matrix Composites: The Critical Need of Automotive and Aerospace Engineering Fields // Mater. Today Proceedings. 2015. V. 2. P. 3032–3041.
Яковцева О.А., Котов А.Д., Ситкина М.Н., Иржак А.В., Михайловская А.В. Механизмы сверхпластической деформации при повышенной скорости в сплаве системы Al–Mg–Zn–Fe–Ni–Zr–Sc // ФММ. 2019. № 10. С. 1109–1115.
Яковцева О.А., Михайловская А.В., Котов А.Д., Мамзурина О.И., Портной В.К. Влияние степени и скорости сверхпластической деформации на структуру и действующие механизмы // ФММ. 2019. № 1. С. 93–100.
Кищик А.А., Котов А.Д., Михайловская А.В. Особенности микроструктуры и сверхпластичности при повышенных скоростях деформации сплава системы Al–Mg–Ni–Fe–Mn–Cr–Zr // ФММ. 2019. № 10. С. 1101–1108.
Ceschini L., Morri A., Orazi L. High strain rate superplasticity in aluminium matrix composites // Proceedings of the Institution of Mechanical Eng. Part L J. Mater. Design Appl. 2002. T. 216. № 1. P. 43–48.
Lee Doh-Jae, Vaudin M.D., Handewerker C.A., Katter U.R. Phase Stability and Interface Reactions in the Al–SiC System // Mater. Res. Symp. Proc. 1988. V. 120. № 357. P. 293–299
Пугачева Н.Б., Мичуров Н.С. Сенаева Е.И., Быкова Т.М. Структура и термодинамические свойства алюмоматричных композитов // ФММ. 2016. Т. 117. P. 1188 0 1195.
Колачев Б.А., Елагин В.И., Ливанов В.А. Металловедение и термическая обработка цветных металлов и сплавов. М.: МИСИС, 2001. 416 с.
Li Y., Langdon T.G. Creep behavior of a reinforced Al-7005 alloy: implications for the creep processes in metal matrix composit // Acta Mater. 1998. V. 46. P. 1143–l155.
Evangelista E., Spigarelli S. Constitutive Equations for Creep and Plasticity of Aluminum Alloys Produced by Powder Metallurgy and Aluminum-Based Metal Matrix Composites // Metal. and Mater. Trans. A. 2002. V. 33. P. 341–381.
Zhu Z.G., Weng G.J. Creep Deformation of Particle-Strengthened Metal-Matrix Composites // J. Eng. Mater. Technol. 1989. V. 111. № 1. P. 99–105.
Li Y., Langdon T.G. Characteristics of creep deformation in discontinuously reinforced metal matrix Composites // Mater. Sci. Techn. 1999. V. 15. P. 357–365.
Li Y., Langdon T.G. Fundamental Aspects of Creep in Metal Matrix Composites // Metallurgical and Materials Transactions A. 1999. V. 30. P. 315–324.
Fernandez R., Gonzalez-Doncel G. Understanding the creep fracture behavior of aluminum alloys and aluminum alloy metal matrix composites // Mater. Sci. Eng. A. 2011. V. 528. P. 8218–8225.
Jufu Jiang, Gang Chen, Ying Wang. Compression Mechanical Behaviour of 7075 Aluminium Matrix Composite Reinforced with Nano-sized SiC Particles in Semisolid State // J. Mater. Sci. Techn. 2016. V. 32. P. 1197–1203.
Смирнов С.В., Крючков Д.И., Нестеренко А.В., Березин И.М., Вичужанин Д.И. Экспериментальное исследование кратковременной неустановившейся ползучести алюмоматричного композита в условиях одноосного сжатия // Вестник ПНИПУ. Механика. 2018. № 4. С. 98–105.
Fridlyander I.N. Modern Aluminum and Magnesium Alloys and Composite Materials Based on Them // Metal Sci. Heat Treatment. 2002. V. 44. № 7. P. 292–296.
Vichuzhanin D.I., Smirnov S.V., Nesterenko A.V., Igumnov A.S. A fracture locus for a 10 volume-percent B95/SiC metal matrix composite at the near-solidus temperature // Letters on Mater. 2018. V. 8. № 1. P. 88–93.
Bin Z.L., Jintao H., Yanwen W. Plastic working and superplasticity in aluminium-matrix composites reinforced with SiC particulates // J. Mater Process Technol. 1998. V. 84. № 1–3. P. 271–273.
Mabuchi M., Higashi K. Thermal stability and superplastic characteristics in Si3N4/Al–Mg–Si composites // Mater. Trans., JIM. 1994. V. 35. № 6. P. 399–405.
Mabuchi M., Higashi K. On accommodation helper mechanism for superplasticity in metal matrix composites // Acta Mater. 1999. V. 47. № 6. P. 1915–1922.
Koike J., Mabuchi M., Higashi K. In situ observation of partial melting in superplastic aluminum alloy composites at high temperatures // Acta Metall. Mater. 1995. V. 43. P. 199–206.
Kim W.J., Hong S.H., Lee J.H. Superplasticity in PM 6061 Al alloy and elimination of strengthening effect by reinforcement in superplastic PM aluminum composites // Mater. Sci. Eng. A. 2001. V. 298. P. 166–173.
Higashi K., Mabuchi M. Critical aspects of high strain rate superplasticity // Mater. Sci. Forum. 1997. V. 243–245. P. 267–276.
Jeong H.G., Higara K., Mabuchi M., Higashi K. The role of partial melting on superplasticity of Si3N4p/Al–Cu–Mg composite // Scr. Mater. 2000. V. 42. P. 479–485.
Rajamuthamilselvan M., Ramanathan S., Karthikeyan R. Processing map for hot working of SiCp/7075 Al composites // Trans. Nonferrous Met. Soc. China. 2010. V. 20. P. 668−674.
Kim W.-J., Sherby O.D. Particle weakening in superplastic SiC/2124 Al composites at high temperature // Acta Mater. 2000. V. 48. № 8. P. 1763–1774.
Cheng N.P., Zeng B.S.M., Liu J.B.Z.Y. Preparation, microstructures and deformation behavior of SiCp/6066Al composites produced by P/M rout [J] // J. Mater. Proces. Techn. 2008. V. 202. P. 27–40.
Дополнительные материалы отсутствуют.
Инструменты
Физика металлов и металловедение