Физика металлов и металловедение, 2021, T. 122, № 8, стр. 831-837
Стабильность ультрамелкозернистой структуры аустенитных коррозионно-стойких сталей в процессе отжига
М. В. Однобокова a, *, А. Н. Беляков b, Н. А. Еникеев a, Р. О. Кайбышев b
a Институт физики перспективных материалов, Уфимский государственный авиационный
технический университет
450008 Уфа, ул. Карла Маркса, 12, Россия
b Белгородский государственный национальный исследовательский университет
308015 Белгород, ул. Победы, 85, Россия
* E-mail: odnobokova_marina@mail.ru
Поступила в редакцию 19.12.2020
После доработки 02.03.2021
Принята к публикации 06.03.2021
Аннотация
Работа посвящена изучению стабильности ультрамелкозернистой структуры в аустенитных коррозионно-стойких сталях AISI 304L (основа Fe–0.05C–18.2Cr–8.8Ni–1.7Mn–0.4Si в мас. %) и AISI 316L (основа Fe–0.04C–17.3Cr–10.7Ni–1.7Mn–0.4Si–2Mo в мас. %) в процессе отжига при температуре 700°С. Формированию ультрамелкозернистой структуры в исследуемых сталях в процессе прокатки при температуре 200°С способствовало развитие деформационного двойникования и микрополос сдвига. Отжиг после прокатки приводит к развитию непрерывной рекристаллизации и росту зерен. Сталь 316L характеризуется более высокой стабильностью к укрупнению зерен, чем сталь 304L, особенно при отжиге в интервале 30–480 мин. Рост зерен в стали 316L в процессе длительного отжига сопровождается выделением фазы Лавеса. Ультрамелкозернистая структура с размером зерен менее 1 мкм сохраняется в стали 316L после отжига в течение 480 мин. Рост зерен в процессе отжига сопровождается разупрочнением обеих сталей.
ВВЕДЕНИЕ
Развитие науки и техники требует создания конструкционных материалов, отличающихся высокой прочностью и пластичностью. В настоящее время аустенитные коррозионно-стойкие стали являются востребованными в широком спектре применений, благодаря высокой коррозионной стойкости в различных средах. Одним из эффективных способов повышения механической прочности аустенитных сталей является структурное упрочнение по закону Холла–Петча за счет уменьшения размера зерен [1, 2]. Наиболее перспективным методом измельчения структуры металлических материалов является интенсивная пластическая деформация или большая пластическая деформация при пониженных температурах [3]. В результате такой деформационной обработки дополнительный вклад в прочность может вносить дислокационное упрочнение по соотношению Тейлора [4, 5]. Общим недостатком сильнодеформированных металлических материалов является низкое относительное удлинение [6, 7]. Частично пластичность в сильнодеформированных материалах может быть восстановлена в результате последующего отжига при температуре, исключающей развитие прерывистой рекристаллизации. Прерывистая рекристаллизация характеризуется значительным ростом зерен [8], что не позволит сохранить ультрамелкозернистую структуру с размером зерен менее 1 мкм. Выгодное сочетание прочностных и пластических характеристик было достигнуто в процессе отжига сильнодеформированных аустенитных сталей в интервале температур 700–750°С [9–11]. Однако на стабильность ультрамелкозернистой структуры будет влиять не только температура, но и длительность отжига. В работе Burke и Turnbull была предложена зависимость, описывающая изменение размера зерен (D) от времени отжига (t) в случае развития собирательной (непрерывной) рекристаллизации или нормального роста зерен, а именно D2 ~ KγVAt, где K – константа, γ – поверхностная энергия границы, VA – атомный объем [12]. Изменение плотности дислокаций (ρ) в процессе их аннигиляции при отжиге было описано зависимостью dρ/dt = –CRρ2, где CR – константа [8]. Кроме того, в процессе отжига при температуре выше 600°С в аустенитных коррозионно-стойких сталях могут выделяться вторые фазы [13], влияние которых на стабильность зерен к укрупнению требует детального изучения. Таким образом, цель настоящего исследования заключается в изучении влияния длительности отжига при температуре 700°С на стабильность ультрамелкозернистой структуры в аустенитных коррозионно-стойких сталях 304L и 316L.
МАТЕРИАЛ И МЕТОДЫ ИССЛЕДОВАНИЙ
Для проведения исследований использовали аустенитные коррозионно-стойкие стали типа AISI 304L (химический состав: основа Fe–0.05%C–18.2%Cr–8.8%Ni–1.7%Mn–0.4%Si–0.05%P–0.04%S, аналог 03Х19Н10) и AISI 316L (химический состав: основа Fe–0.04%C–17.3%Cr–10.7%Ni–1.7%Mn–0.4%Si–0.04%P–0.05%S–2%Mo, аналог 03Х17Н12М2). Слитки сталей были перекованы при температуре 1100°С на заготовки в виде прутков квадратного сечения 30 × 30 мм2. После горячей ковки был проведен высокотемпературный отжиг при температуре 1100°С в течение 30 мин с последующим охлаждением в воду. Полученные в результате горячей ковки и высокотемпературного отжига исходные заготовки были прокатаны в лист при температуре 200°С до истинной деформаций е = 3 (е = ln(h0/hk), где h0, hk – начальная и конечная толщина стального листа).
После прокатки был проведен отжиг при температуре 700°С в течение 30, 60, 120 и 480 мин с последующим охлаждением в воду. Структурные исследования были выполнены с помощью растрового электронного микроскопа Nova Nanosem 450, оснащенного детектором регистрации обратно-рассеянных электронов (метод EBSD), и просвечивающего электронного микроскопа (ПЭМ) JEOL JEM-2100. Размер зерен определяли методом случайных секущих в направлении, перпендикулярном направлению прокатки по EBSD-картам (в расчет принимали только высокоугловые границы (ВУГ) с углом разориентировки не менее 15°). Плотность дислокаций определяли по точкам выхода дислокаций на поверхность фольги с помощью ПЭМ. Идентификацию частиц вторичных фаз проводили по анализу микродифракций, полученных в ПЭМ. Механические испытания на растяжение проводили при скорости движения траверсы 2 мм/мин на плоских образцах с длиной рабочей части 16 мм и начальной площадью поперечного сечения 1.5 × 3 мм2 с помощью испытательной машины фирмы Instron.
РЕЗУЛЬТАТЫ ИССЛЕДОВАНИЙ И ИХ ОБСУЖДЕНИЕ
Тонкая структура исследуемых сталей после прокатки при температуре 200°С до истинной деформации е = 3 показана на рис. 1. Структура катаных сталей представлена ультрамелкими кристаллитами, о чем свидетельствуют кольцевые электроннограмы. Кристаллиты вытянуты вдоль направления прокатки, поэтому имеют пластинчатую морфологию, а их поперечный размер составил около 100–150 нм. Стоит отметить, что на электронограмме стали 304L видны яркие дифракционные максимумы {022} и {112} от α'-Fe. На электроннограмме стали 316L наблюдается только слабый рефлекс {112} от α'-Fe. Таким образом, прокатка при 200°С до больших пластических деформаций сопровождается развитием мартенситного превращения [14]. Часто кристаллиты мартенсита деформации наблюдаются в микрополосах сдвига, где они чередуются с кристаллитами аустенита (рис. 1а, ТП). Доля мартенсита деформации после прокатки при 200°С составила около 25 и 3% в стали 304L и 316L соответственно. После прокатки при комнатной температуре до е = 3 доля мартенсита деформации составила около 80% в стали 304L и 25% в стали 316L [7, 15]. Кроме того, в структуре возможно формирование гетерогенных областей в форме “глаза” (“eye” domain [16]), которые показаны пунктирными линиями на рис. 1. Данные гетерогенные области состоят из тонких пластин двойников, что подтверждается картинами микродифракций, и окружены микрополосами сдвига – участками структуры, которые характеризуются искривлением кристаллитов в результате сдвига. Расстояние между двойниками в области “глаза” составило около 50 нм. Ориентация кристаллитов внутри самих микрополос сдвига отличается от ориентации кристаллитов в остальной структуре. Формирование этих гетерогенных областей связано с развитием микрополос сдвига в разных направлениях, что приводит к их пересечению между собой и перерезанию двойниковых прослоек. В результате двойниковые прослойки оказываются охваченными микрополосами сдвига с четырех сторон. Тонкая структура после прокатки при 200°С подобна тонкой структуре после прокатки при комнатной температуре, хотя отличается размером кристаллитов и долей мартенсита деформации [7, 14, 15].
Рис. 1.
Тонкая структура сталей 304L (а) и 316L (б) после прокатки при температуре 200°С до истинной деформации е = 3. Темное поле (ТП) получено в рефлексе (022) для α'-Fe. МС – микрополосы сдвига, НП – направление прокатки, НН – направление нормали к плоскости прокатки, м – матрица, д – двойник.
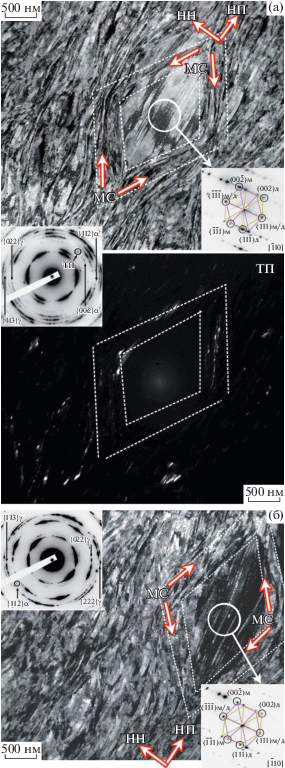
Микроструктура (в виде ориентационных EBSD-карт с наложенной схемой границ) исследуемых сталей 304L и 316L после прокатки при 200°С до истинной деформации е = 3 и последующего отжига при температуре 700°С показана на рис. 2. Тонкая структура после отжига исследуемых сталей 304L и 316L показана на рис. 3 и 4 соответственно. Отжиг при 700°С катаных сталей 304L и 316L приводит к развитию непрерывной рекристаллизации, которая более активно протекает в стали 304L, а также полному обратному α' → γ-превращению. Микроструктура стали 304L уже после 30-минутного отжига представлена относительно равноосными зернами, в то время как пластинчатая морфология зерен сохраняется в стали 316L. В микроструктуре стали 316L наблюдается большое число малоугловых границ деформационного происхождения. Так как непрерывная рекристаллизация связана с перераспределением дислокаций во время отжига, в тонкой структуре стали 304L после отжига в интервале 30–120 мин наблюдаются зерна размером 500–700 нм с низкой плотностью дислокаций, которые чередуются с ультрамелкими кристаллитами (рис. 3а–3в). Тонкая структура стали 316L существенно не меняется в процессе увеличения длительности отжига от 30 до 120 мин и очень похожа на тонкую структуру после прокатки (рис. 4а–4в).
Рис. 2.
Микроструктура (ориентационные EBSD-карты с наложенной схемой границ) сталей 304L (а, б, в) и 316L (г, д, е) после прокатки при 200°С до истинной деформации е = 3 и последующего отжига при температуре 700°С в течение 30 (а, г), 120 (б, д) и 480 мин (в, е). Цвет на изображениях микроструктуры показывает кристаллографическое направление вдоль нормали к плоскости прокатки (НН). Черные и красные линии (цветное изображение on-line) соответствуют высокоугловым и малоугловым границам соответственно.
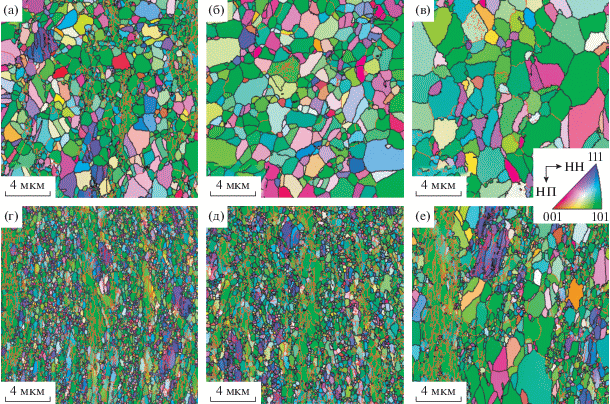
Рис. 3.
Тонкая структура стали 304L после прокатки при 200°С до истинной деформации е = 3 и последующего отжига при температуре 700°С в течение 30 (а), 60 (б), 120 (в) и 480 мин (г).
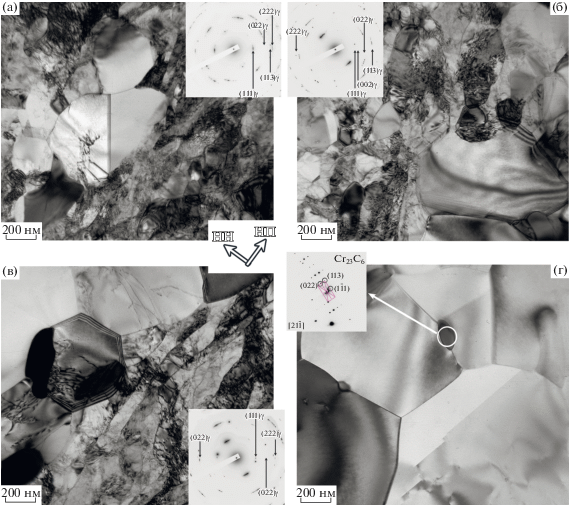
Рис. 4.
Тонкая структура стали 316L после прокатки при 200°С до истинной деформации е = 3 и последующего отжига при температуре 700°С в течение 30 (а), 60 (б), 120 (в) и 480 мин (г). Для фазы Fe2Mo темное поле (ТП) получено в рефлексе (201).
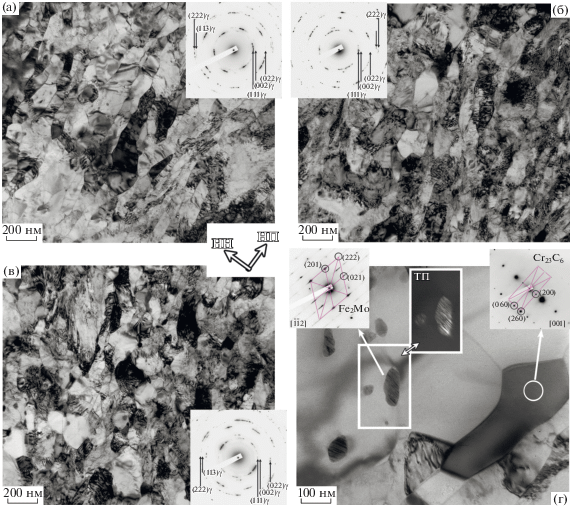
Первые крупные рекристаллизованные зерна появляются в структуре стали 316L только после увеличения длительности отжига до 480 мин. Более высокая стабильность стали 316L к непрерывной рекристаллизации и росту зерен связана с ее легированием молибденом в отличие от стали 304L. Молибден, находясь в твердом растворе, подавляет диффузионные процессы и препятствует миграции границ зерен. Увеличение длительности отжига до 480 мин приводит к выделению фазы Лавеса (Fe2Mo), обогащенной молибденом (рис. 4г).
Стоит отметить, что в процессе отжига при 700°С в обеих сталях происходит выделение карбидов Cr23C6 (рис. 3г, 4г, 5). После коротких отжигов (60 мин) карбиды Cr23C6 имеют небольшие размеры (длина не более 300 нм, как видно из рис. 5), а с увеличением длительности отжига до 480 мин они увеличиваются в размерах и могут принимать сложную морфологию схожую с морфологией (суб)зерен (рис. 4г). Карбиды Cr23C6 выделяются одновременно в обеих сталях, которые характеризуются разной стабильностью к укрупнению зерен, что свидетельствует об отсутствии влияния этих карбидов на миграцию границ зерен при их росте.
Рис. 5.
Тонкая структура стали 304L после прокатки при 200°С до истинной деформации е = 3 и последующего отжига при температуре 700°С в течение 60 минут. Для фазы Cr23C6 темное поле (ТП) получено в рефлексе (200).
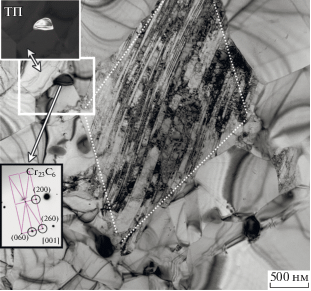
Дополнительное влияние на стабильность к укрупнению зерен оказывает наличие в структуре гетерогенных областей в форме “глаза”, полученных предварительной прокаткой. Данные области препятствуют быстрому росту рекристаллизованных зерен внутрь этих гетерогенных областей, состоящих из нанодвойниковой структуры (рис. 5).
Влияние длительности отжига на размер зерен и плотность дислокаций в исследуемых сталях 304L и 316L показано на рис. 6. Увеличение длительности отжига от 30 до 120 мин приводит к постепенному увеличению размера зерен от 550 до 720 нм в стали 304L, и от 300 до 400 нм в стали 316L. С последующим увеличением длительности отжига до 480 минут размер зерен увеличивается более чем в 2 раза и достигает значений около 1550 и 850 нм в стали 304L и 316L соответственно. Стоит отметить, что средний размер зерен в стали 316L не превысил 1 мкм после отжига при 700°С длительностью 480 мин, т.е. структура остается ультрамелкозернистой. Изменение размера зерен от времени отжига в обеих сталях было описано с помощь зависимости D ~ m × t 0.5 (m –константа) [11], которая была выведена из теоритической модели для нормального роста зерен в процессе отжига, предложенной в работе Burke и Turnbull [12]. В результате аппроксимации экспериментальных значений размера зерен (на рис. 6) с помощью предложенной выше зависимости были получены коэффициенты m = 70 [нм/мин0.5] для стали 304L и m = 40 [нм/мин0.5] для стали 316L. Значение коэффициента m больше в стали 304L, которая характеризуется более быстрой кинетикой роста зерен.
Рис. 6.
Влияние длительности отжига при 700°С на размер зерен и плотность дислокаций в сталях 304L и 316L.
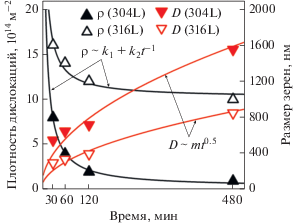
Плотность дислокаций резко уменьшается в обеих сталях с увеличением длительности отжига от 30 до 120 мин (от 8 до 2 × 1014 м–2 в стали 304L; от 16 до 12 × 1014 м–2 в стали 316L), а с последующим увеличением длительности отжига до 480 мин существенно не изменяется. Влияние времени отжига на изменение плотности дислокаций было описано с помощь зависимости ρ ~ k1 + k2 × t –1 (где k1 и k2 – константы). Данная зависимость была получена на основании модели аннигиляции дислокаций в процессе отжига, предложенной в работе Humphreys и Hatherly [8], и с помощью нее была аппроксимирована плотность дислокаций на рис. 6. В результате данной аппроксимации были получены следующие значения коэффициентов: k1 = 0.3 [1014 м–2] и k2 = 230 [1014 м–2 мин] для стали 304L; а также k1 = 10 [1014 м–2] и k2 = = 190 [1014 м–2 мин] для стали 316L. Стоит отметить, что коэффициент k2 для двух сталей имеет близкое значение, что сказывается на подобии кривых. Исследуемые стали существенно отличаются значением коэффициента k1, который меньше на два порядка в стали 304L. Кривая, описывающая изменение плотности дислокаций от длительности отжига, для стали 304L лежит гораздо ниже кривой для стали 316L, что свидетельствует о влиянии коэффициента k1 на положение кривых.
Длительность отжига оказывает влияние на прочность исследуемых сталей (рис. 7). Предел текучести (σ0,2) постепенно уменьшается в стали 304L от 770 до 580 МПа с увеличением длительности отжига от 30 до 480 мин. В стали 316L предел текучести существенно не изменяется при отжиге в интервале 30–120 минут (1030 МПа < σ0.2 < 980 МПа), и только с увеличением длительности отжига до 480 мин снижается до 740 МПа.
Рис. 7.
Влияние длительности отжига при 700°С на предел текучести в сталях 304L и 316L. Столбцы соответствуют экспериментальным значениям; красные точки соответствуют значениям, посчитанным с помощью уравнения (1).
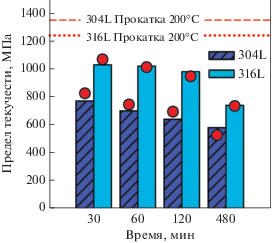
Для изменения предела текучести в процессе отжига катаной стали 316L была предложена зависимость, включающая зернограничное и дислокационное упрочнение [11]:
(1)
${{\sigma }_{{0.2}}} = {{\sigma }_{0}} + {{K}_{{\text{y}}}}{{D}^{{--0.5}}} + \alpha Gb{{\rho }^{{0.5}}},$ЗАКЛЮЧЕНИЕ
Прокатка сталей 304L и 316L при температуре 200°С до е = 3 приводит к формированию ультрамелкокристаллической структуры с гетерогенными областями в форме “глаза”. Такие гетерогенные области ограничены микрополосами сдвига и внутри состоят из нанодвойников. Данные области могут сохраняться в процессе последующего отжига. Отжиг при 700°С катаных сталей 304L и 316L приводит к развитию непрерывной рекристаллизации и росту зерен. Сталь 316L характеризуется более медленной кинетикой роста зерен, чем сталь 304L. Размер зерен составил 400 и 700 нм в стали 316L и 304L соответственно, после отжига в течение 120 мин. Более высокая стабильность ультрамелкозернистой структуры в стали 316L в процессе отжига связана с ее легированием молибденом. Пока молибден находится в твердом растворе, он подавляет диффузию и миграцию границ зерен в процессе отжига, поэтому непрерывная рекристаллизация развивается слабо и размер зерен заметно не изменяется. Увеличение длительности отжига до 480 мин приводит к выделению фазы Лавеса. Выделение карбидов Cr23C6 в обеих сталях не оказывает заметного влияния на стабильность размера зерен к укрупнению. Изменение размера зерен и плотности дислокаций от времени отжига было описано с помощь зависимости D ~ m × t0.5 и ρ ~ k1 + k2 × t–1, где m, k1 и k2 – константы. Предел текучести обеих сталей можно выразить уравнением σ0.2 = σ0 + KyD–0.5 + αGbρ0.5, где σ0 = 160 МПа, Ky = 0.4 MПa м0.5, α = 0.22.
Исследование выполнено при финансовой поддержке РФФИ в рамках научного проекта № 19-38-60047.
Список литературы
Hall E.O. The deformation and ageing of mild steel: II characteristics of the Lüders deformation // Proc. Phys. Soc. B. 1951. V. 64. P. 742–747.
Petch N. The cleavage strength of polycrystals // J. Iron Steel Inst. 1953. V. 174. P. 25–28.
Valiev R.Z., Islamgaliev R.K., Alexandrov I.V. Bulk nanostructured materials from severe plastic deformation // Prog. Mater. Sci. 2000. V. 45. P. 103–189.
Taylor G.I. The mechanism of plastic deformation of crystals. Part I. Theoretical // Proceedings Royal Soc. A. 1934. V. 145. P. 362–388.
Сагарадзе В.В., Уваров А.И. Упрочнение аустенитных сталей. М.: Наука, 1989. 270 с.
Belyakov A., Odnobokova M., Kipelova A., Tsuzaki K., Kaibyshev R. Nanocrystalline structures and tensile properties of stainless steels processed by severe plastic deformation // IOP Conf. Series: Mater. Sci. Eng. 2014. V. 63. № 012156.
Odnobokova M., Belyakov A., Kaibyshev R. Grain refinement and strengthening of austenitic stainless steels during large strain cold rolling // Phil. Mag. 2019. V. 99. № 5. P. 531–556.
Humphreys F.J., Hatherly M. Recrystallization and related annealing phenomena 2nd edn. Elsevier, Amsterdam, 2004. 658 p.
Odnobokova M., Belyakov A., Enikeev N., Molodov D.A., Kaibyshev R. Annealing behavior of a 304L stainless steel processed by large strain cold and warm rolling // Mater. Sci. Eng. A. 2017. V. 689. P. 370–383.
Guosheng S., Linxiu D., Jun H., Bin Z., Misra R.D.K. On the influence of deformation mechanism during cold and warm rolling on annealing behavior of a 304 stainless steel // Mater. Sci. Eng. A. 2019. V. 746. P. 341–355.
Odnobokova M., Yanushkevich Z., Kaibyshev R., Belyakov A. On the strength of a 316L-type stainless steel subjected to cold or warm rolling followed by annealing // Materials. 2020. V. 13. № 2116.
Burke J., Turnbull D. Recrystallization and grain growth // Prog. Met. Phys. 1952. V. 3. P. 220–292.
Weiss B., Stickler R. Phase instabilities during high temperature exposure of 316 austenitic stainless steel // Met. Trans. 1972. V. 3. P. 851–866.
Odnobokova M., Belyakov A., Enikeev N., Kaibyshev R., Valiev R.Z. Microstructural changes and strengthening of austenitic stainless steels during rolling at 473 K // Metals. 2020. V. 10. № 1614.
Однобокова М.В., Беляков А.Н., Нугманов И.Н., Кайбышев Р.О. Эволюция структуры и текстуры в процессе холодной деформации метастабильной аустенитной стали // ФММ. 2020. Т. 121. № 7. С. 742–749.
Miura H., Kobayashi M., Todaka Y., Watanabe C., Aoyagi Y., Sugiura N., Yoshinaga N. Heterogeneous nanostructure developed in heavily cold-rolled stainless steels and the specific mechanical properties // Scr. Mater. 2017. V. 133. P. 33–36.
Дополнительные материалы отсутствуют.
Инструменты
Физика металлов и металловедение