Физика металлов и металловедение, 2021, T. 122, № 8, стр. 858-865
Микромеханические характеристики поверхностного слоя метастабильной аустенитной стали, подвергнутой фрикционной обработке
Р. А. Саврай a, *, Ю. М. Колобылин a, Е. Г. Волкова b
a Институт машиноведения УрО РАН
620049 Екатеринбург, ул. Комсомольская, 34, Россия
b Институт физики металлов УрО РАН
620108 Екатеринбург, ул. С. Ковалевской, 18, Россия
* E-mail: ras@imach.uran.ru
Поступила в редакцию 13.01.2021
После доработки 07.04.2021
Принята к публикации 13.04.2021
Аннотация
Исследовано влияние фрикционной обработки скользящим индентором на микромеханические характеристики коррозионно-стойкой хромоникелевой (в мас. %: 16.80Cr; 8.44Ni) аустенитной стали. По данным инструментированного микроиндентирования, которое проводили на поверхности стали и на различной глубине от поверхности, установлено, что характер распределения максимальной и остаточной глубины вдавливания индентора hmax и hp, твердости по Мартенсу HM, твердости вдавливания при максимальной нагрузке HIT, работы обратной упругой деформации вдавливания We, общей механической работы вдавливания Wt, упругого восстановления Rе, отношения твердости вдавливания к контактному модулю упругости НIT/Е*, степенного отношения ${{H_{{{\text{IT}}}}^{3}} \mathord{\left/ {\vphantom {{H_{{{\text{IT}}}}^{3}} {{{E}^{{*2}}}}}} \right. \kern-0em} {{{E}^{{*2}}}}}$ и показателя пластичности δA по глубине градиентного упрочненного слоя приблизительно следует экспоненциальному закону. При этом поверхность стали характеризуется наибольшими значениями HM, HIT, We, Rе, НIT/Е*, ${{H_{{{\text{IT}}}}^{3}} \mathord{\left/ {\vphantom {{H_{{{\text{IT}}}}^{3}} {{{E}^{{*2}}}}}} \right. \kern-0em} {{{E}^{{*2}}}}}$ и наименьшими значениями hmax, hp, Wt, δA. Контактный модуль упругости E* стали после фрикционной обработки вырос, однако наблюдается немонотонное распределение величины E* по глубине упрочненного слоя. Это обусловлено формированием различных дислокационных структур на поверхности стали и в нижележащих слоях. По результатам индентирования также установлено, что после фрикционной обработки повышенным сопротивлением механическому контактному воздействию обладает как поверхность стали, так и упрочненный слой глубиной до 500 мкм.
ВВЕДЕНИЕ
Фрикционная обработка скользящим индентором является эффективным способом формирования градиентного упрочненного слоя на поверхности металлических материалов [1–8], в том числе коррозионно-стойких аустенитных сталей [8–12]. К основным научно-технологическим аспектам фрикционной обработки относятся: 1) негомогенная деформация сдвигом с наличием резкого градиента [2, 13]. Именно сдвиговая компонента деформации вносит определяющий вклад в накопление пластической деформации (и соответственно в деформационное упрочнение металла) при контактном фрикционном воздействии [1, 14]; 2) обоснованный выбор материала индентора, который должен исключать адгезионное схватывание и разрушение поверхности, обеспечивая при этом достаточно высокий коэффициент трения для накопления деформации [2]. В качестве материала индентора могут быть использованы такие сверхтвердые материалы, как твердый сплав, природный и синтетический алмаз, плотный нитрид бора [15]. При фрикционной обработке аустенитных нержавеющих сталей наиболее эффективно использование индентора из синтетического алмаза [16]; 3) использование безокислительной среды обработки (например, инертных газов), которая обеспечивает накопление максимальных степеней пластической деформации в возможно более толстом поверхностном слое [2]. Деформационная поверхностная обработка в окислительной среде воздуха может приводить к шелушению и отслаиванию упрочненного слоя, а также к его ускоренному разрушению при последующем контактном нагружении [17]. Это обусловлено охрупчиванием поверхностных слоев из-за механохимического взаимодействия металла с кислородом воздуха. Кроме того, важными параметрами фрикционной обработки также являются нормальная нагрузка на индентор и кратность деформирующего воздействия индентора на обрабатываемую поверхность [2, 18].
Упрочненный поверхностный слой должен выдерживать максимальные контактные нагрузки в заданных условиях нагружения. Для оценки способности упрочненных поверхностных слоев выдерживать контактные нагрузки и сопротивляться механическому контактному воздействию в процессе эксплуатации целесообразно использование метода микроиндентирования [3, 15, 19–21]. Поскольку слои, формируемые фрикционной обработкой, градиентны, то по мере удаления от поверхности, свойства материала будут изменяться. Поэтому актуальной задачей является определение характеристик индентирования не только на поверхности упрочненной стали, но и на различной глубине от поверхности.
Цель настоящей работы – исследование микромеханических характеристик поверхностного слоя аустенитной стали AISI 321, подвергнутой фрикционной обработке скользящим индентором.
МАТЕРИАЛ И МЕТОДИКА ЭКСПЕРИМЕНТА
Исследовали коррозионностойкую аустенитную сталь AISI 321 промышленной плавки состава (мас. %): 0.05С; 16.80Cr; 8.44Ni; 0.33Ti; 1.15Mn; 0.67Si; 0.26Mo; 0.13Co; 0.03Nb; 0.31Cu; 0.036P; 0.005S; остальное Fe. В состоянии поставки сталь представляла собой прокатанный лист толщиной 10 мм. Образцы для фрикционной обработки изготавливали в виде пластин размерами 70 × 40 мм. Термическую обработку (закалку) подготовленных образцов из стали AISI 321 проводили по следующему режиму: нагрев до температуры 1100°С, выдержка при этой температуре в течение 40 мин, охлаждение в воде. Поверхность образцов подвергали механическому шлифованию и электролитическому полированию.
Фрикционную обработку поверхности образцов осуществляли в безокислительной среде аргона с обдувом путем прямолинейного скольжения сферического индентора из синтетического алмаза с радиусом сферы 3 мм, при нагрузке P = = 294 Н и средней скорости скольжения V = = 0.01 м/с. После каждого хода индентора происходила смена направления движения на противоположное с поперечным смещением d = 0.02 мм [9].
Структуру стали после фрикционной обработки изучали с применением сканирующего электронного микроскопа Tescan VEGA II XMU. Исследование тонкой структуры осуществляли методом просвечивающей электронной микроскопии на микроскопе JEOL JEM-200CX. Изображения тонкой структуры получали с использованием метода тонких фольг. Рентгеноструктурный фазовый анализ выполняли на дифрактометре Shimadzu XRD-7000 в CrKα-излучении.
Инструментированное микроиндентирование с записью диаграммы нагружения проводили на измерительной системе Fischerscope HM2000 XYm с использованием индентора Виккерса и программного обеспечения WIN-HCU при максимальной нагрузке P = 0.245 Н, времени нагружения 5 с, выдержке при нагрузке 20 с и времени разгрузки 5 с согласно стандарту ISO 14577 [22]. На основе измеряемых при индентировании характеристик рассчитывали следующие параметры: отношение твердости вдавливания к контактному модулю упругости НIT/Е* [23], упругое восстановление Rе = ((hmax – hp)/hmax) × 100% [24, 25], степенное отношение ${{H_{{{\text{IT}}}}^{3}} \mathord{\left/ {\vphantom {{H_{{{\text{IT}}}}^{3}} {{{E}^{{*2}}}}}} \right. \kern-0em} {{{E}^{{*2}}}}}$ [26] и показатель пластичности δA = 1 – (We/Wt) [27], характеризующие способность материала сопротивляться упругопластическому деформированию.
ЭКСПЕРИМЕНТАЛЬНЫЕ РЕЗУЛЬТАТЫ И ИХ ОБСУЖДЕНИЕ
Микроструктура закаленной стали AISI 321 перед фрикционной обработкой является полностью аустенитной с отдельными включениями карбида титана TiC [9, 10, 28]. Фрикционная обработка приводит к формированию 100%-ного мартенсита деформации на поверхности стали, что подтверждается результатами рентгеноструктурного анализа (табл. 1). Структура поверхностного слоя стали AISI 321 после фрикционной обработки представлена на рис. 1, из которого видно, что на глубине до 25–35 мкм возникает относительно однородная дисперсная структура (см. рис. 1, слой 1), а на глубине от 25–35 до 40–50 мкм наблюдается деформированная структура с вытянутыми кристаллами (см. рис. 1, слой 2). На глубине более 50 мкм наблюдается структура деформированного аустенита с образованием мартенсита деформации в пределах исходных аустенитных зерен (см. рис. 1, слой 3). При этом мартенсит деформации в поверхностном слое стали, подвергнутой фрикционной обработке, наблюдается на глубине до 240 мкм (см. табл. 1). Микротвердость поверхности стали после фрикционной обработки составила 780 ± 30 НV0.025 при общей глубине упрочненного слоя около 500 мкм [9].
Рис. 1.
Структура поверхностного слоя стали AISI 321 (электронная сканирующая микроскопия ) после фрикционной обработки: 1 – слой с сильно диспергированной мартенситной структурой; 2 – деформированный слой с преимущественно мартенситной структурой; 3 – деформированный слой с аустенитно-мартенситной структурой.
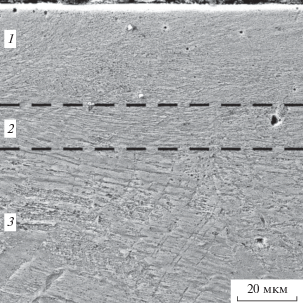
Данные просвечивающей электронной микроскопии показывают, что на глубине до 25–35 мкм структура преимущественно субмикрокристаллическая с размером кристаллитов α-фазы менее 500 нм (рис. 2а, 2б). Кроме вытянутых субзерен, присутствуют сформировавшиеся отдельные зерна с формой, приближенной к округлой. Расчет среднего размера зерна α-фазы дает величину dα = 180 ± 10 нм (см. рис. 2б). На представленной микроэлектроннограмме видно, что рефлексы растягиваются по окружности (см. рис. 2а), а на темнопольном изображении светятся достаточно протяженные участки (см. рис. 2б). Это свидетельствует о начале формирования смешанной структуры, образованной ячейками и микрокристаллитами с высокоугловыми границами [29], однако доля высокоугловых границ еще невелика. Отметим, что деформированная структура с вытянутыми мартенситными кристаллами, которая наблюдается на глубине от 25–35 до 40–50 мкм, характеризуется высокой плотностью дислокаций, равномерно распределенных в объеме материала (см. рис. 2в, 2г). Следует также подчеркнуть, что с помощью фрикционной обработки в поверхностном слое метастабильных аустенитных сталей может быть сформирована как субмикрокристаллическая, так и нанокристаллическая структура, причем формирование последней может быть достигнуто, например, путем увеличения кратности деформирующего воздействия индентора на обрабатываемую поверхность [18]. Однако в этом случае может происходить снижение качества поверхности, что необходимо учитывать при выборе параметров фрикционной обработки.
Рис. 2.
Микроструктура стали AISI 321 (просвечивающая электронная микроскопия) после фрикционной обработки на глубине 1–5 мкм (а, б) и на глубине 40 мкм (в, г): а, в – светлопольные изображения с соответствующими микроэлектроннограммами; б, г – темнопольные изображения в рефлексах (110)α (обозначены окружностями на микроэлекторонограммах на рис. а, в).
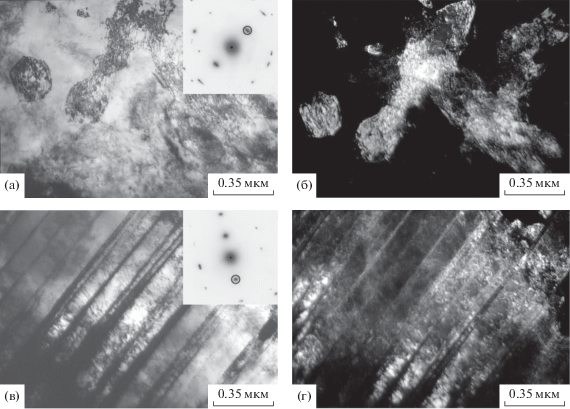
На рис. 3 представлены данные инструментированного микроиндентирования, которые показывают характеристики индентирования на различной глубине от поверхности стали AISI 321 после фрикционной обработки. Из рис. 3 видно, что поверхность стали AISI 321 после фрикционной обработки характеризуется наименьшими значениями максимальной и остаточной глубины вдавливания индентора hmax и hp, общей механической работы вдавливания Wt, и наибольшими значениями твердости по Мартенсу HM и твердости вдавливания при максимальной нагрузке HIT, работы обратной упругой деформации вдавливания We. Подобное изменение измеряемых при индентировании характеристик hmax, hp, HM, HIT, We и Wt обусловлено упрочнением материала [4, 9, 10, 21]. Результаты анализа распределения этих характеристик по глубине упрочненного слоя свидетельствуют о том, что характер их распределения hmax, hp, HM, HIT, We и Wt (см. рис. 3а–3е) приблизительно следует экспоненциальному закону и соответствует расчетному распределению накопленной деформации в поверхностном слое отожженной стали Ст3 после фрикционной обработки скользящим цилиндрическим индентором [1, 14].
Рис. 3.
Распределение максимальной и остаточной глубины вдавливания индентора hmax (а) и hp (б), твердости по Мартенсу HM (в), твердости вдавливания при максимальной нагрузке HIT (г), работы обратной упругой деформации вдавливания We (д), общей механической работы вдавливания Wt (е), контактного модуля упругости E* (ж), упругого восстановления Rе (з), отношения твердости вдавливания к контактному модулю упругости НIT/Е* (и), степенного отношения ${{H_{{{\text{IT}}}}^{3}} \mathord{\left/ {\vphantom {{H_{{{\text{IT}}}}^{3}} {{{E}^{{*2}}}}}} \right. \kern-0em} {{{E}^{{*2}}}}}$ (к) и показателя пластичности δA (л) по глубине h упрочненного слоя стали AISI 321 после фрикционной обработки. Штриховой линией обозначены характеристики стали в закаленном состоянии.
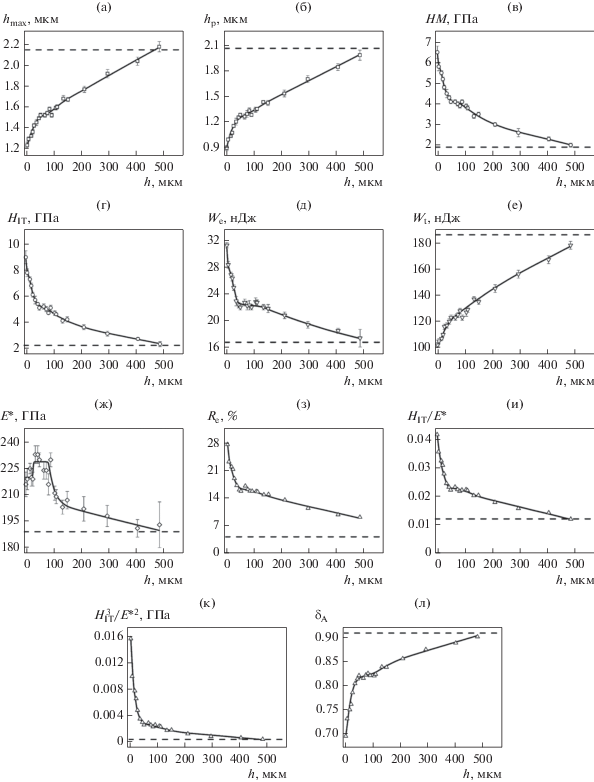
Фрикционная обработка привела также к росту контактного модуля упругости E* стали AISI 321, однако наблюдается немонотонное распределение величины E* по глубине упрочненного слоя (см. рис. 3ж). В частности, на глубине до 35 мкм средние значения контактного модуля упругости составили E* = 220 ГПа, на глубине от 35 до 90–100 мкм, E* = 229 ГПа, на глубине более 100 мкм наблюдается непрерывное снижение величины E* до значения, характерного для стали в закаленном состоянии (см. рис. 3ж). Это обусловлено формированием различной структуры по глубине упрочненного слоя (см. рис. 1, 2). В частности, рост модуля упругости поверхности упрочненной стали обусловлен формированием ячеистой дислокационной структуры (см. рис. 2а, 2б) [30]. Согласно модели Мотта, дислокации могут изгибаться в своих плоскостях скольжения, создавая дополнительную упругую деформацию и, следовательно, уменьшать модуль упругости. Это справедливо в тех случаях, когда плотность дислокаций невелика, и они могут свободно двигаться. Если дислокации закреплены (например, дислокации, находящиеся в стенках ячеек при формировании ячеистой структуры), то они уже не могут создавать дополнительную упругую деформацию. В этом случае дислокации будут повышать модуль упругости материала [30–33].
Контактный модуль упругости E* на глубине от 35 до 90–100 мкм, где сформировалась мартенситная структура (см. рис. 1, слой 2; рис. 2в, 2г), переходящая в аустенитно-мартенситную структуру (см. рис. 1, слой 3), выше, чем на поверхности стали. Причиной этого является пониженная плотность дислокаций внутри ячеек (см. рис. 2а), что частично компенсирует рост величины E*, обусловленный влиянием дислокаций, находящихся в стенках ячеек [30]. Между тем, как было отмечено выше, деформированная структура с вытянутыми мартенситными кристаллами характеризуется высокой плотностью дислокаций, которые равномерно распределены в объеме материала, что приводит к ограничению их подвижности. Кроме того, границы дисперсных мартенситных кристаллов (см. рис. 2в, 2г) также эффективно тормозят движение дислокаций. Это и обуславливает более высокие значения E* по сравнению с модулем упругости поверхности стали (см. рис. 3ж). По-видимому, высокая плотность дислокаций сохраняется на глубине до 90–100 мкм, когда в структуре стали присутствует достаточно большое количество мартенсита деформации (см. табл. 1).
Фрикционная обработка повышает сопротивление поверхности стали AISI 321 упруго-пластическому деформированию, о чем свидетельствует рост параметров Re, HIT/E* и ${{H_{{{\text{IT}}}}^{3}} \mathord{\left/ {\vphantom {{H_{{{\text{IT}}}}^{3}} {{{E}^{{*2}}}}}} \right. \kern-0em} {{{E}^{{*2}}}}}.$ При этом характер распределения указанных параметров также приблизительно следует экспоненциальному закону, и их повышенные значения сохраняются по всей глубине упрочненного слоя (см. рис. 3з–3к). Показатель пластичности δA после фрикционной обработки, напротив, снизился, и его пониженные значения сохраняются по всей глубине упрочненного слоя (см. рис. 3л). Таким образом, в результате фрикционной обработки можно ожидать повышения сопротивления механическому контактному воздействию как поверхности стали AISI 321, так и упрочненного слоя глубиной до 500 мкм.
Следует также отметить, что параметры Re, HIT/E* и ${{H_{{{\text{IT}}}}^{3}} \mathord{\left/ {\vphantom {{H_{{{\text{IT}}}}^{3}} {{{E}^{{*2}}}}}} \right. \kern-0em} {{{E}^{{*2}}}}}$ являются наиболее информативными с точки зрения оценки износостойкости материала. Сопоставление полученных результатов с имеющимися данными о трибологических свойствах поверхностно-упрочненных хромоникелевых аустенитных сталей показало, что достижение таких значений характеристик микроиндентирования приводит к росту износостойкости. В частности, сталь 12Х18Н10Т после фрикционной обработки, имеющая близкие значения Re, HIT/E* и ${{H_{{{\text{IT}}}}^{3}} \mathord{\left/ {\vphantom {{H_{{{\text{IT}}}}^{3}} {{{E}^{{*2}}}}}} \right. \kern-0em} {{{E}^{{*2}}}}},$ характеризуется существенным снижением интенсивности изнашивания и коэффициента трения в условиях сухого трения скольжения. Это обусловлено ограничением развития на упрочненной поверхности процессов схватывания и переходом к изнашиванию по механизму пластического оттеснения [11].
ЗАКЛЮЧЕНИЕ
Исследовано влияние фрикционной обработки скользящим индентором на микромеханические характеристики коррозионностойкой аустенитной стали AISI 321. По данным инструментированного микроиндентирования установлено, что характер распределения максимальной и остаточной глубины вдавливания индентора hmax и hp, твердости по Мартенсу HM, твердости вдавливания при максимальной нагрузке HIT, работы обратной упругой деформации вдавливания We, общей механической работы вдавливания Wt, упругого восстановления Rе, отношения твердости вдавливания к контактному модулю упругости НIT/Е*, степенного отношения ${{H_{{{\text{IT}}}}^{3}} \mathord{\left/ {\vphantom {{H_{{{\text{IT}}}}^{3}} {{{E}^{{*2}}}}}} \right. \kern-0em} {{{E}^{{*2}}}}}$ и показателя пластичности δA по глубине градиентного упрочненного слоя приблизительно следует экспоненциальному закону. При этом поверхность стали характеризуется наибольшими значениями HM, HIT, We, Rе, НIT/Е*, ${{H_{{{\text{IT}}}}^{3}} \mathord{\left/ {\vphantom {{H_{{{\text{IT}}}}^{3}} {{{E}^{{*2}}}}}} \right. \kern-0em} {{{E}^{{*2}}}}},$ и наименьшими значениями hmax, hp, Wt, δA. Фрикционная обработка также привела к росту контактного модуля упругости E* стали AISI 321, однако наблюдается немонотонное распределение величины E* по глубине упрочненного слоя. Это обусловлено формированием различных дислокационных структур на поверхности стали и в нижележащих слоях.
Результаты инструментированного микроиндентирования также свидетельствуют, что после фрикционной обработки повышенным сопротивлением механическому контактному воздействию обладает как поверхность стали AISI 321, так и упрочненный слой глубиной до 500 мкм.
Работа выполнена в рамках государственных заданий ИМАШ УрО РАН по теме № АААА-А18-118020790148-1 и ИФМ УрО РАН по теме № АААА-А18-118020190116-6 в части исследованных материалов и способов их обработки, и при поддержке гранта РФФИ № 20-58-00057 Бел_а в части методики исследования микромеханических характеристик модифицированных поверхностных слоев. Электронная сканирующая микроскопия и инструментированное микроиндентирование выполнены в ЦКП “Пластометрия” ИМАШ УрО РАН. Просвечивающая электронная микроскопия выполнена в отделе электронной микроскопии ЦКП “Испытательный центр нанотехнологий и перспективных материалов” ИФМ УрО РАН.
Авторы выражают благодарность А.Л. Осинцевой за участие в экспериментальных исследованиях.
Список литературы
Makarov A.V., Savrai R.A., Pozdejeva N.A., Smirnov S.V., Vichuzhanin D.I., Korshunov L.G., Malygina I.Yu. Effect of hardening friction treatment with hard-alloy indenter on microstructure, mechanical properties, and deformation and fracture features of constructional steel under static and cyclic tension // Surf. Coat. Technol. 2010. V. 205. № 3. P. 841–852. https://doi.org/10.1016/j.surfcoat.2010.08.025
Макаров А.В., Коршунов Л.Г. Металлофизические основы наноструктурирующей фрикционной обработки сталей // ФММ. 2019. Т. 120. № 3. С. 327–336.
Макаров А.В., Поздеева Н.А., Саврай Р.А., Юровских А.С., Малыгина И.Ю. Повышение износостойкости закаленной конструкционной стали наноструктурирующей фрикционной обработкой // Трение и износ. 2012. Т. 33. № 6. С. 444–455.
Savrai R.A., Makarov A.V., Malygina I.Yu., Volkova E.G. Effect of nanostructuring frictional treatment on the properties of high-carbon pearlitic steel. Part I: microstructure and surface properties // Mater. Sci. Eng. A. 2018. V. 734. P. 506–512. https://doi.org/10.1016/j.msea.2018.07.099
Deng S.Q., Godfrey A., Liu W., Zhang C.L. Microstructural evolution of pure copper subjected to friction sliding deformation at room temperature // Mater. Sci. Eng. A. 2015. V. 639. P. 448–455. https://doi.org/10.1016/j.msea.2015.05.017
Макаров А.В., Коршунов Л.Г., Саврай Р.А., Давыдова Н.А., Малыгина И.Ю., Черненко Н.Л. Влияние длительного нагрева на термическое разупрочнение, химический состав и эволюцию нанокристаллической структуры, сформированной в закаленной высокоуглеродистой стали при фрикционной обработке // ФММ. 2014. Т. 115. № 3. С. 324–336.
Макаров А.В., Коршунов Л.Г., Выходец В.Б., Куренных Т.Е., Саврай Р.А. Влияние упрочняющей фрикционной обработки на химический состав, структуру и трибологические свойства высокоуглеродистой стали // ФММ. 2010. Т. 110. № 5. С. 530–544.
Макаров А.В., Саврай Р.А., Скорынина П.А., Волкова Е.Г. Развитие методов поверхностного деформационного наноструктурирования сталей // МиТОМ. 2020. № 1(775). С. 62–69.
Savrai R.A., Osintseva A.L. Effect of hardened surface layer obtained by frictional treatment on the contact endurance of the AISI 321 stainless steel under contact gigacycle fatigue tests // Mater. Sci. Eng. A. 2021. V. 802. Art. 140679. P. 1–10.
Savrai R.A., Makarov A.V., Malygina I.Yu., Rogovaya S.A., Osintseva A.L. Improving the strength of the AISI 321 austenitic stainless steel by frictional treatment [Digital resource] // Diagnostics, Resource and Mechanics of materials and structures. 2017. № 5. P. 43–62. http:// dream-journal.org/issues/2017-5/2017-5_149.html.
Макаров А.В., Скорынина П.А., Осинцева А.Л., Юровских А.С., Саврай Р.А. Повышение трибологических свойств аустенитной стали 12Х18Н10Т наноструктурирующей фрикционной обработкой // Обработка металлов (Технология, оборудование, инструменты). 2015. № 4 (69). С. 80–92.
Наркевич Н.А., Шулепов И.А., Миронов Ю.П. Структура, механические и триботехнические свойства аустенитной азотистой стали после фрикционной обработки // ФММ. 2017. Т. 118. № 4. С. 421–428.
Li J.G., Umemoto M., Todaka Y., Tsuchiya K. Role of strain gradient on the formation of nanocrystalline structure produced by severe plastic deformation // J. Alloys Compd. 2007. V. 434–435. P. 290–293. https://doi.org/10.1016/j.jallcom.2006.08.167
Вичужанин Д.И., Макаров А.В., Смирнов С.В., Поздеева Н.А., Малыгина И.Ю. Напряженно-деформированное состояние и поврежденность при фрикционной упрочняющей обработке плоской стальной поверхности скользящим цилиндрическим индентором // Проблемы машиностроения и надежности машин. 2011. № 6. С. 61–69.
Кузнецов В.П., Макаров А.В., Псахье С.Г., Саврай Р.А., Малыгина И.Ю., Давыдова Н.А. Трибологические аспекты наноструктурирующего выглаживания конструкционных сталей // Физическая мезомеханика. 2014. Т. 17. № 3. С. 14–30.
Makarov A.V., Skorynina P.A., Yurovskikh A.S., Osintseva A.L. Effect of the technological conditions of frictional treatment on the structure, phase composition and hardening of metastable austenitic steel // AIP Conf. Proc. 2016. V. 1785. Art. 040035. 4 p. https://doi.org/10.1063/1.4967092
Savrai R.A., Makarov A.V. Effect of nanostructuring frictional treatment on the properties of high-carbon pearlitic steel. Part II: mechanical properties // Mater. Sci. Eng. A. 2018. V. 734. P. 513–518.
Макаров А.В., Скорынина П.А., Юровских А.С. Осинцева А.Л. Влияние технологических условий наноструктурирующей фрикционной обработки на структурно-фазовое состояние и упрочнение метастабильной аустенитной стали // ФММ. 2017. Т. 118. № 12. С. 1300–1311.
Пугачева Н.Б., Быкова Т.М., Трушина Е.Б. Влияние состава стали-основы на структуру и свойства диффузионных боридных покрытий // Упрочняющие технологии и покрытия. 2013. № 4. С. 3–7.
Пугачева Н.Б., Трушина Е.Б., Быкова Т.М. Исследование трибологических свойств боридов железа в составе диффузионных покрытий // Трение и износ. 2014. Т. 35. № 6. С. 643–654.
Саврай Р.А., Скорынина П.А., Макаров А.В., Осинцева А.Л. Влияние жидкостной цементации при пониженной температуре на микромеханические характеристики метастабильной аустенитной стали // ФММ. 2020. Т. 121. № 10. С. 1109–1115.
ГОСТ Р 8.748-2011 (ИСО 14577-1:2002) Государственная система обеспечения единства измерений (ГСИ). Металлы и сплавы. Измерение твердости и других характеристик материалов при инструментальном индентировании. Часть 1. Метод испытаний.
Cheng Y.T., Cheng C.M. Relationships between hardness, elastic modulus and the work of indentation // Appl. Phys. Lett. 1998. V. 73. № 5. P. 614–618.
Page T.F., Hainsworth S.V. Using nanoindentation techniques for the characterization of coated systems: a critique // Surf. Coat. Technol. 1993. V. 61. № 1–3. P. 201–208.
Petrzhik M.I., Levashov E.A. Modern methods for investigating functional surfaces of advanced materials by mechanical contact testing // Crystallography Reports. 2007. V. 52. № 6. P. 966–974.
Mayrhofer P. H., Mitterer C., Musil J. Structure-property relationships in single- and dual-phase nanocrystalline hard coatings // Surf. Coat. Technol. 2003. V. 174–175. P. 725–731.
Мильман Ю.В., Чугунова С.И., Гончарова И.В. Характеристика пластичности, определяемая методом индентирования // Вопросы атомной науки и техники. 2011. № 4. С. 182–187.
Саврай Р.А., Скорынина П.А., Макаров А.В., Осинцева А.Л. Особенности структуры и свойства поверхности метастабильной аустенитной стали, подвергнутой жидкостной цементации при пониженной температуре // ФММ. 2020. Т. 121. № 1. С. 72–78.
Дегтярев М.В., Воронова Л.М., Чащухина Т.И. Рост зерна при отжиге армко-железа с ультрадисперсной структурой различного типа, созданной деформацией сдвигом под давлением // ФММ. 2005. Т. 99. № 3. С. 58–68.
Benito J.A., Jorba J., Manero J.M., Roca A. Change of Young’s modulus of cold-deformed pure iron in a tensile test // Metall. Mater. Trans. A. 2005. V. 36. № 12. P. 3317–3324.
Ledbetter H.M., Kim S.A. Low temperature elastic constants of deformed polycrystalline copper // Mater. Sci. Eng. A. 1988. V. 101. P. 87–92.
Shima S., Yang M. A study of accuracy in an intelligent V-bending process for sheet metals – change in Young’s modulus due to plastic deformation and its effect on springback // J. Soc. Mater. Sci. Jpn. 1995. V. 44. № 500. P. 578–583.
Morestin F., Boivin M. On the necessity of taking into account the variation in the Young modulus with plastic strain in elastic-plastic software // Nucl. Eng. Design. 1996. V. 162. № 1. P. 107–116.
Дополнительные материалы отсутствуют.
Инструменты
Физика металлов и металловедение