Физика металлов и металловедение, 2021, T. 122, № 8, стр. 866-872
Влияние микродобавки индия на структуру и упрочнение бинарных Al–Cu-сплавов
П. К. Шуркин a, *, Т. К. Акопян a, Н. В. Летягин a
a НИТУ “МИСиС”
119991 Москва, Ленинский проспект, 4, Россия
* E-mail: pa.shurkin@yandex.ru
Поступила в редакцию 02.02.2021
После доработки 19.03.2021
Принята к публикации 31.03.2021
Аннотация
С использованием термодинамических расчетов в программе Thermo-Calc, а также экспериментальных методов, включая просвечивающую электронную микроскопию (ПЭМ) высокого разрешения, изучено влияние микродобавки индия In на изменение фазового состава и характер упрочнения в результате термической обработки сплавов Al–1.5% Cu и Al–3.5% Cu (мас. %). Показано, что введение 0.1 мас. % In приводит к полному подавлению естественного старения в сплаве Al–3.5% Cu. Однако In значительно интенсифицирует процесс распада алюминиевого твердого раствора (Al) при искусственном старении, что обеспечивает преимущества микролегированных сплавов по сравнению с базовыми сплавами как по времени достижения максимального упрочнения, так и по твердости. В частности, после старения на максимальную прочность твердость сплава Al–3.5% Cu–0.1% In на ~20% выше твердости базового сплава (124 против 105 HV), а твердость сплава Al–1.5% Cu–0.1% In более чем на 60% выше твердости базового сплава Al–1.5% Cu (59 против 37 HV). Анализ с использованием ПЭМ показал, что наблюдаемое повышение твердости при старении сплавов с микродобавкой обусловлено формированием существенно более дисперсной структуры продуктов старения (средний линейный размер упрочняющей θ'-фазы уменьшается с 100 до 50 нм) при более высокой плотности распределения частиц.
ВВЕДЕНИЕ
Бинарные сплавы на основе системы Al–Cu являются классическим примером термоупрочняемых материалов на основе алюминия, исследования которых в начале 20 века обосновали возможность упрочнения сплавов путем старения [1]. На протяжении последующих лет интенсивное изучение данного явления позволило Cu-содержащим сплавам закрепиться в качестве основного конструкционного материала для легких ответственных деталей авиакосмической техники и машиностроения [1–3].
На сегодняшний день исследования Al–Cu-сплавов остаются актуальными, о чем свидетельствуют современные публикации по уточнению двойной диаграммы состояния [4, 5], характера кристаллизации [6], механизмов старения [7, 8] и пластической деформации [9], а также влияния легирования [10–15]. Например, в недавней работе [10] показана возможность повышения термической стабильности бинарных Al–Cu-сплавов, легированных Y и Er в количестве более 2 мас. %. Несмотря на положительные результаты, использование редкоземельных металлов во многих случаях нерационально из-за их высокой стоимости. Более того, они труднорастворимы даже в жидком алюминии и требуют применения лигатур.
К эффективным методам повышения свойств Al–Cu-сплавов также относится микролегирование (до 0.1 маc. %) элементами Sc [11], Ag [12], Cd, Sn, In [12–15], которые способствуют повышению плотности выделений и уменьшению линейного размера упрочняющих дискообразных частиц θ'-и θ"-фаз, являющихся метастабильным модификациями фазы θ-состава Al2Cu [7]. Заведомо можно утверждать, что микролегирование легкоплавкими элементами группы Cd, Sn, In представляется более целесообразным, чем дорогостоящими серебром и редкоземельными металлами. Среди тройки Cd, Sn, In, микролегирование кадмием нашло отражение в марочном сплаве АМ4.5Кд ГОСТ 1583–93, который в состоянии Т6 (искусственное старение на максимальную прочность) способен иметь временное сопротивление 490 МПа. Однако пары кадмия, образующиеся при литейном производстве, крайне токсичны [16], что обусловливает целесообразность его замены, в частности оловом или индием. По сравнению с оловом влияние индия на двойные Al–Cu-сплавы освещено в меньшей степени, что определило тему данного исследования.
В работе конца 20 века [17] показано, что добавка 0.05 мас. % In в сплав Al–4% Cu способствует практически двукратному снижению времени достижения пика твердости и повышению упрочнения примерно на 20% после старения при 130 и 190°C. Аналогичный эффект был достигнут в силумине марки 357 [18], в результате чего удалось повысить его твердость в состоянии Т6 на 20 HV. Схожие результаты были получены в сплавах систем Al–Cu–Mg [19] и Al–Mg–Si [20].
Механизм упрочнения микродобавками легкоплавких элементов до сих пор остается дискуссионным. В работе [17] авторы утверждают, что на начальных стадиях старения формирование предвыделений, содержащих In, происходит на дислокационных петлях, образованных в результате коалесценции вакансионных кластеров. В свою очередь, эти частицы являются местами гетерогенного зарождения θ'-фазы, что способствует ускорению процесса распада алюминиевого твердого раствора (далее (Al)). В более поздней работе [21] способом атомной томографии и просвечивающей электронной микроскопии (ПЭМ) было показано на примере олова, что на начальных стадиях старения происходит формирование сферических выделений β-Sn на которых зарождается θ'-фаза.
Учитывая высокий практический потенциал микролегирования легкоплавкими элементами, данная работа преследует цель исследовать влияние относительно малоизученной добавки In на процессы старения в сплавах на базе системы Al‒Cu. В частности, были поставлены следующие задачи:
1 – изучить особенности структуры сплавов Al–1.5% Cu и Al–3.5% Cu с добавкой 0.1 мас. % In при литье и упрочняющей термообработке;
2 – определить влияние 0.1 мас. % In на упрочнение Al–Cu-сплавов в процессе изотермического старения.
ЭКСПЕРИМЕНТАЛЬНЫЕ МЕТОДЫ
В качестве объектов исследования были получены слитки 10 × 40 × 180 мм четырех модельных сплавов, номинально содержащих 1.5% и 3.5% Cu и легированных 0.1% In (в мас. %). Их фактический состав был определен способом спектрально-эмиссионного анализа (спектрометр ARL3460) и представлен в табл. 1. Плавку проводили при 750°C в электрической печи сопротивления GRAFICARBO в графитовом тигле без использования защитных флюсов и операций рафинирования. Общая масса плавки для каждого сплава составляла 200 г. В качестве шихтовых материалов использовали алюминий марки А99 (99.99% Al, ГОСТ 11069–2001), медь марки М1 (99.9% Cu, ГОСТ 859–2001) и индий (99.999%, ГОСТ 10297–94). После ввода каждой добавки проводили перемешивание графитовой палочкой. Перед разливкой выдерживали 10 мин и снимали шлак. Контроль температуры осуществляли термопарой с градуировкой ХА (хромель-алюмель). Скорость охлаждения при литье в графитовую форму составляла около 40°C/с.
Таблица 1.
Состав модельных сплавов (в мас. %)
Сплав | Cu | In | Al |
---|---|---|---|
Al3.5Cu | 3.71 | 0.00 | 96.29 |
Al3.5Cu0.1In | 3.74 | 0.11 | 96.15 |
Al1.5Cu | 1.65 | 0.00 | 98.35 |
Al1.5Cu0.1In | 1.64 | 0.10 | 98.26 |
Первичный анализ фазового состава проводили с использованием программы Thermo-Calc v.3.1 и базы данных TCAl4.0 [22]. Экспериментальные образцы изучали в литом и термически-обработанном состоянии – после гомогенизации по режиму 505°С, 8 ч, последующей закалки в воду и выдержки при комнатной температуре в течение 7 сут (естественное старение, режим Т4), а также после искусственного изотермического старения при температуре 175°С и дискретных выдержках 2, 6, 8, 15 и 18 ч. Микроструктуру и состав фаз изучали на сканирующем электронном микроскопе (СЭМ) TESCAN VEGA 3, укомплектованном приставкой для спектрального микроанализа (МРСА) Oxford Instruments. Тонкую структуру изучали на просвечивающем электронном микроскопе JEM2100. Контроль упрочнения проводили способом измерения твердости методом Виккерса согласно ГОСТ 2999–75 на установке DUROLINE MH-6 (нагрузка 1 кгс, выдержка 10 с) и удельной электропроводности (УЭП) с помощью вихретокового структуроскопа ВЭ-26НП.
РЕЗУЛЬТАТЫ И ОБСУЖДЕНИЕ
Количество In было выбрано исходя из необходимости достижения его полного растворения в алюминии в результате нагрева под закалку. Согласно монографии [23] в системе Al–Cu–In отсутствуют тройные промежуточные соединения, а растворимости Cu и In в (Al) соответствуют значениям, справедливым для двойных систем Al–Cu и Al–In. В системе Cu–In возможно образование промежуточных соединений на основе меди, чего не наблюдается в области алюминиевого угла при переходе к тройной системе Al–Cu–In. Как видно из разреза, представленного на рис. 1а, расслоение жидкой фазы наблюдается при концентрациях более ~0.25% In при 1.5% Cu. Эта граница снижается на 0.025% с каждым увеличением концентрации Cu на 1%. В то же время при 0.1% In процесс кристаллизации включает образование жидкости богатой In при температуре 495°C, которая одинакова при выбранных содержаниях 1.5% Cu и 3.5% Cu. При этой же температуре одновременно происходит выделение вторичной фазы Al2Cu в сплаве с 3.5% Cu, тогда как при меньшей концентрации Cu она выделяется при 400°C. Соответственно, вышеуказанные явления сопровождаются резким снижением концентрации In и Cu в (Al), что наглядно представлено на зависимости состава твердого раствора от температуры (рис. 1б). Кристаллизация сплавов заканчивается при температуре плавления In (156°C, линия солидус на рис. 1а).
Рис. 1.
(а) Политермический разрез системы Al–Cu–In при 1.5% (сплошная линия) и при 3.5% Cu (пунктирная линия) и (б) расчетная зависимость количества Cu и In в (Al) от температуры в сплавах Al1.5Cu0.1In (сплошная линия) и Al3.5Cu0.1In (пунктирная линия).
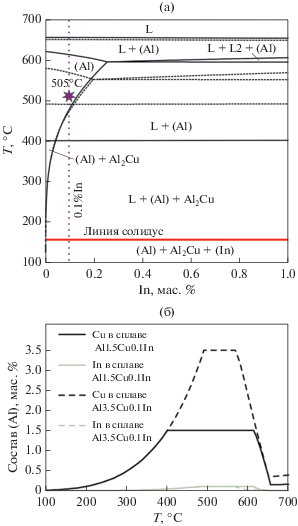
При изучении литой структуры модельных сплавов не выявлено отклонений от аналогичной структуры литейных сплавов типа АМ5. Она мало изменяется с добавкой In за исключением присутствия малых вкраплений легкоплавкой фазы, отличающейся на СЭМ-изображениях более ярким цветом по сравнению с основной фазой Al2Cu. Аналогичные структуры, например, можно наблюдать в работе [24], где рассматривается альтернативная добавка олова. Гораздо больший интерес представляют фактические микроструктуры сплавов после обработки по режиму Т4. Можно ожидать, что в условиях анализа методом СЭМ, эти микроструктуры будут справедливы также для состояния после искусственного старения. Очевидно, что наблюдение полукогерентных выделений θ', образующихся в процессе этой операции, требует более высокого разрешения, реализуемого в методе ПЭМ.
Выбранная температура обработки на твердый раствор (505°C) является характерной для большинства Cu-содержащих марочных литейных алюминиевых сплавов [25] и обеспечивает однофазное состояние модельных сплавов, исследуемых в данной работе. Согласно расчету (рис. 1б) при 505°C состав твердого раствора соответствует составу сплава, т.е. предполагается полное растворение легирующих элементов в (Al). Расчет фазового состава продуктов распада при температуре старения 175°C (табл. 2) показывает, что в модельных сплавах Al3.5Cu и Al3.5Cu0.1In может образовываться ~6 мас. % метастабильной упрочняющей фазы θ', а в сплавах Al1.5Cu и Al1.5Cu0.1In ~ 2 мас. %. Ввиду отсутствия других упрочняющих факторов частично когерентные выделения θ'‑фазы будут являться основной причиной повышенной прочности сплавов после термообработки. Микроструктурный анализ образцов в состоянии Т4 показал, что в сплаве Al1.5Cu наблюдается однофазная структура, а в сплаве Al1.5Cu0.1In на фоне (Al) присутствуют округлые частицы легкоплавкой фазы размером до 1 мкм (рис. 2а). Напротив, в структуре Al3.5Cu обнаружились не полностью растворенные компактные частицы фазы Al2Cu размером до 3 мкм, а в структуре сплава Al3.5Cu0.1In на границах θ-фазы присутствуют включения In (рис. 2б). Тем не менее, согласно представленным результатам МРСА (табл. 2) и картам распределения элементов (рис. 2) в структуре закаленных сплавов с 3.5% Cu, большая часть меди содержится в твердом растворе (Al). С другой стороны, следует отметить, что абсолютная ошибка при определении концентрации In методом МРСА (~0.1 мас. %) не позволяет получить достоверных данных относительно содержания In в (Al). Очевидно, что изучение его растворимости требует более прецизионных методов анализа. Однако присутствие вкраплений частиц In в структуре закаленного сплава указывает на то, что его растворимость в (Al) существенно ниже 0.1 мас. %.
Таблица 2.
Результаты МРСА твердого раствора (Al) после закалки (состояние Т4) и расчетная доля вторичных фаз при 175°C
Сплав | Состав (Al) при 505°C, мас. % | Доля фаз при 175°C, мас. %* | |||
---|---|---|---|---|---|
Сu | In | Al | θ’ | In | |
Al3.5Cu | 3.74 ± 0.22 | 0.00 | Основа | 6.20 | 0.00 |
Al3.5Cu0.1In | 3.64 ± 0.18 | 0.12 ± 0.10 | Основа | 6.02 | 0.12 |
Al1.5Cu | 1.59 ± 0.12 | 0.00 | Основа | 2.20 | 0.00 |
Al1.5Cu0.1In | 1.54 ± 0.12 | 0.08 ± 0.10 | Основа | 2.11 | 0.08 |
Рис. 2.
Микроструктуры и карты распределения элементов в сплавах Al1.5Cu0.1In (а) и Al3.5Cu0.1In (б) в состоянии Т4.
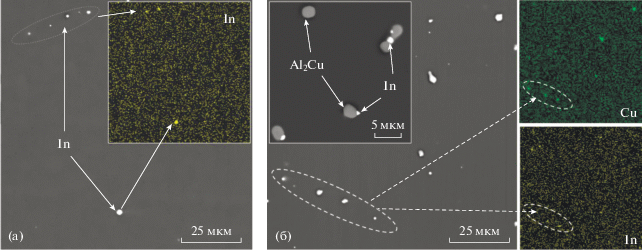
Измерение удельной электропроводности, которая крайне чувствительна к структурно-фазовым трансформациям, в совокупности с результатами по изменению микротвердости позволяет получить первичные данные о процессах, протекающих при старении сплавов. Как можно судить из рис. 3а, по сравнению с литым состоянием, в состоянии Т4 УЭП сплавов закономерно ниже, что связано с насыщением алюминиевого твердого раствора медью и индием при закалке. Для сплавов с 1.5% Cu этот эффект сопровождается малым снижением твердости c ~40 до ~35 HV (рис. 3б). Напротив, для базового сплава Al3.5Cu в аналогичном состоянии наблюдается повышение твердости по сравнению с литым состоянием с 45 до 74 HV. При этом в сплаве Al3.5Cu0.1In твердость остается на прежнем уровне (52 HV). Подобное различие в поведении сплавов с 3.5% Cu объяснено в работе [13] и может быть связано с подавлением формирования зон ГП, так как образование атомно-вакансионных комплексов с In приводит к снижению концентрации свободных вакансий, необходимых для диффузии атомов меди.
Рис. 3.
Кривые зависимости УЭП (а) и твердости (б) от времени изотермического старения при
175°С сплавов Al1.5Cu (), Al1.5Cu0.1In (
), Al3.5Cu (
) и Al3.5Cu0.1In (
).
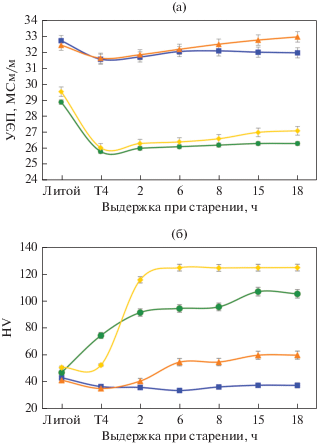
В процессе искусственного старения преимущество In-содержащих сплавов выявляется уже после 2 ч выдержки. При сравнении сплавов Al1.5Cu и Al1.5Cu0.1In это преимущество составляет всего 5 единиц (35 против 40 HV), а при сравнении сплавов Al3.5Cu и Al3.5Cu0.1In уже 24 единицы (91 против 115 HV). Максимум твердости сплава Al3.5Cu0.1In достигается после шести часов изотермической выдержки, тогда как для базового Al3.5Cu сплава требуется свыше 8 ч. После старения на максимальную прочность сплав Al3.5Cu0.1In обладает более чем в два раза большей твердостью по сравнению с состоянием Т4. Аналогичный прирост для сплава Al3.5Сu составил всего 40%. Из-за малой объемной доли упрочняющих частиц θ' для низколегированного базового сплава Al1.5Cu практически не наблюдается роста твердости в процессе старения. Напротив, твердость сплава Al1.5Cu0.1In возросла практически в два раза (до 59 HV). Можно утверждать, что твердость сплавов с 3.5% Cu более, чем в два раза выше вследствие более высокой объемной доли выделений θ'-фазы. Тем не менее примечательно, что всего 0.1% In позволяет упрочнить базовый сплав Al1.5Cu, не склонный к упрочнению при старении, практически вдвое в процессе аналогичного старения. Следует также отметить, что, в сравнении с закаленным состоянием, распад (Al) приводит к повышению электропроводности сплава (рис. 3а). Однако электропроводность сплавов с малой добавкой In в процессе изотермического старения оказывается несколько выше, чем для базовых сплавов. Данное обстоятельство указывает на более полный распад алюминиевого твердого раствора, что, в том числе, является следствием интенсификации процессов старения в сплавах с малой добавкой.
Полученные результаты повышения твердости могут быть связаны с модифицирующим эффектом малой добавки In и вкладом малого размера упрочняющих частиц, который согласно модели Орована [26] является гораздо более существенным фактором, чем их объемная доля. Для установления причин наблюдаемого упрочнения на примере сплавов Al3.5Cu и Al3.5Cu0.1In была исследована тонкая структура сплавов в состоянии Т6. Как видно из рис. 4а, в сплаве без In выделения выглядят как штрихи, представляющие собой характерные поперечные разрезы относительно редких дискообразных частиц фазы θ'. Их линейный размер в некоторых областях достигает ~200 нм при преобладающем размере ~100 нм. При сравнении с In-содержащим сплавом, преимущество по твердости последнего очевидно связано с по крайней мере двукратным снижением преобладающего размера выделений (~ до 50 нм) и заметным увеличением их плотности распределения (рис. 4б). Изображения, полученные при атомном разрешении (рис. 4в, 4г), позволяют более надежно идентифицировать выделения как фазу θ'. Видно, что толщина выделений также уменьшилась с добавкой In c ~4 до ~2.5 нм.
Рис. 4.
Тонкая структура (а, б) и изображения выделений θ' при атомном разрешении (в, г) в сплавах Al3.5Cu (а, в) и Al3.5Cu0.1In (б, г) ПЭМ.
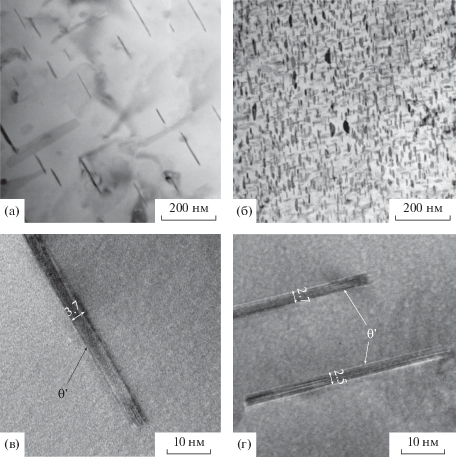
Согласно источникам [13–15], основной кинетический эффект от малой добавки In связан с высокой энергией связи In с вакансиями. Последняя составляет по разным данным 0.24–0.43 эВ [27] и наравне с показателями других легкоплавких элементов (Cd, Sn) является доминирующей над аналогичной энергией связи традиционных легирующих элементов, в частности, Cu (<0.2 эВ). Как показано в работе [13], в процессе выдержки при температуре искусственного старения происходит освобождение “связанных” индием вакансий, что способствует ускорению диффузионного массопереноса в процессе распада алюминиевого твердого раствора и последующего формирования продуктов старения. Модифицирование структуры продуктов старения, предположительно, связано со снижением термодинамического барьера образования критического зародыша. Согласно различным литературным источникам, возможно несколько механизмов объясняющих роль индия в данном процессе. В частности, сообщается о возможной сегрегации малой добавки In на межфазной поверхности θ'/(Al) [13] или же его растворение в выделениях θ' [24], сопровождающееся изменением параметра решетки и снижением упругих напряжений на границе θ'/(Al). Также сообщается об образовании предвыделений легкоплавкой фазы, играющей роль эффективной подложки для зародышей θ'-фазы [21]. Следует отметить, что при использованных условиях съемки при получении ПЭМ-изображений вторичных выделений In-содержащих частиц в настоящей работе не обнаружено. Однако для достоверной интерпретации механизмов влияния индия требуется проведение дополнительных прецизионных исследований сплавов на различных этапах эволюции структуры продуктов старения.
ВЫВОДЫ
1. Расчетными и экспериментальными методами изучено влияние 0.1% In на фазовый состав и физико-механические свойства сплавов Al–1.5% Cu и Al–3.5% Cu (мас. %) в литом состоянии и после упрочняющей термической обработки.
2. Показано, что In подавляет процесс естественного старения, что обусловливает пониженную твердость сплава Al–3.5% Cu–0.1% In в сравнении с базовым бинарным Al–3.5% Cu сплавом после закалки (74 против 54 HV).
3. Показано, что In значительно интенсифицирует процесс распада твердого раствора при искусственном старении, что обусловливает преимущество по степени упрочнения In-содержащих сплавов как на начальных этапах старения, так и в состоянии Т6. Максимальная твердость сплава Al–3.5% Cu–0.1% In достигается после шести часов изотермической выдержки, тогда как для базового Al–3.5% Cu сплава требуется свыше восьми часов выдержки. После старения на максимальную прочность твердость сплава Al–3.5% Cu–0.1% In на ~20% выше твердости базового сплава (124 против 105 HV), а твердость сплава Al–1.5% Cu–0.1% In более чем на 60% выше твердости базового сплава Al–1.5% Cu (59 против 37 HV).
4. Показано, что упрочняющий эффект In связан с модифицированием вторичных метастабильных выделений θ'-фазы, что выражается в более чем двукратном снижении их линейного размера (со 100 до 50 нм) и межчастичного расстояния. По нашему мнению, наибольший кинетический вклад в указанный эффект вносит высокая энергия связи In с вакансиями, в то врем как оценка термодинамического фактора требует дополнительных прецизионных исследований.
Исследование выполнено за счет гранта Российского научного фонда (проект № 20-79-10373).
Список литературы
Sigli C., De Geuser F., Deschamps A., Lépinoux J., Perez M. Recent advances in the metallurgy of aluminum alloys. Part II: Age hardening // Comptes Rendus Physique. 2018. V. 19. № 8. P. 688–709. https://doi.org/10.1016/j.crhy.2018.10.012
Polmear I., StJohn D., Nie J.F., Qian M. Physical metallurgy of aluminium alloys /in Light Alloys (5th ed.). Elseiver, London, 2017. P. 31–107. https://doi.org/10.1016/B978-0-08-099431-4.00002-6
Gloria A., Montanari R., Richetta M., Varone A. Alloys for Aeronautic Applications: State of the Art and Perspectives // Metals. 2019. № 9. P. 662. https://doi.org/10.3390/met9060662
Kroupa A., Zobač O., Richter K.W. The thermodynamic reassessment of the binary Al–Cu system // J. Mater. Sci. 2021. V. 56. P. 3430–3443. https://doi.org/10.1007/s10853-020-05423-7
Liu S., Martínez E., LLorca J. Prediction of the Al-rich part of the Al–Cu phase diagram using cluster expansion and statistical mechanics // Acta Mater. 2020. V. 195. P. 317–326. https://doi.org/10.1016/j.actamat.2020.05.018
Zhu L., Han C., Hou L., Gagnoud A., Fautrelle Y., Rena Z., Li X. Influence of a static magnetic field on the distribution of solute Cu and interdendritic constitutional undercooling in directionally solidified Al–4.5 wt % Cu alloy // Mater. Let. 2019. V. 248. P. 73–77. https://doi.org/10.1016/j.matlet.2019.03.142
Zhou L., Wu C.L., Xie P., Niu F.J., Ming W.Q., Du K., Chen J.H. A hidden precipitation scenario of the θ'-phase in Al–Cu alloys // J. Mater. Sci. Tech. 2021. V. 75. P. 126–138. https://doi.org/10.1016/j.jmst.2020.09.039
Zhu X.-H., Lin Y.C., Wu Q., Jiang Y.-Q. Effects of aging on precipitation behavior and mechanical properties of a tensile deformed Al–Cu alloy // JALCOM. 2020. V. 843. P. 155975. https://doi.org/10.1016/j.jallcom.2020.155975
Кайгородова Л.И., Распосиенко Д.Ю., Пушин В.Г., Пилюгин В.П., Смирнов С.В. Влияние отжига на структуру и свойства стареющего сплава Al–Li–Cu–Mg–Zr–Sc–Zn, подвергнутого мегапластической деформации // ФММ. 2019. Т. 120. № 1. С. 169–175.
Амер С.М., Барков Р.Ю., Яковцева О.А., Поздняков А.В. Сравнительный анализ структуры и свойств квазибинарных сплавов Al–6.5Cu–2.3Y и Al–6Cu–4.05Er // ФММ. 2020. Т. 121. № 5. С. 528–534.
Li Q., Zhang Y., Lan Y., Pei R., Feng X., Xia T., Liu D. Effect of scandium addition on microstructure and mechanical properties of as-cast Al–5% Cu alloys // Vacuum. 2020. V. 177. P. 109385. https://doi.org/10.1016/j.vacuum.2020.109385
Poon I., Marceau R.K.W., Xia J., Liao X.Z., Ringer S.P. Precipitation processes in Al–Cu–Mg–Sn and Al–Cu–Mg–Sn–Ag // Mater. Des. 2016. V. 96. P. 385–391. https://doi.org/10.1016/j.matdes.2016.02.048
Lotter F., Petschke D., Staab T.E.M., Rohrmann U., Schubert T., Sextl G., Kieback B. The Influence of Trace Elements (In, Sn) on the Hardening Process of Al–Cu Alloys // Phys. Status Solidi A. 2018. V. 215. P. 1800038. https://doi.org/10.1002/pssa.201800038
Hu Y., Wang G., Ye M., Wang S., Wang L., Rong Y. A precipitation hardening model for Al–Cu–Cd alloys // Mater. Des. 2018. V. 151. P. 123–132. https://doi.org/10.1016/j.matdes.2018.04.057
Bourgeois L., Dwyer C., Weyland M., Nie J.-F., Muddle B.C. The magic thicknesses of θ' precipitates in Sn-microalloyed Al–Cu // Acta Mater. 2012. V. 60. № 2. P. 633–644. https://doi.org/10.1016/j.actamat.2011.10.015
Genchi G., Sinicropi M.S., Lauria G., Carocci A., Catalano A. The effects of Cadmium toxicity // Int. J. Env. Res. Pub. Health. 2020. V. 17. № 11. P. 3782. https://doi.org/10.3390/ijerph17113782
Polmear I.J. Role of Trace Elements in Aged Aluminium-Alloys // Mater. Sci. Forum. 1987. V. 13–14. P. 195–214. https://doi.org/10.4028/www.scientific.net/MSF.13-14.195
Wang G., Sun Q., Shan L., Zhao Z., Yan L. Influence of Indium trace addition on the precipitation behavior in a 357 cast aluminum alloy // J. Mater. Eng. Perform. 2007. V. 16. P. 752–756. https://doi.org/10.1007/s11665-007-9086-3
Lotter F., Petschke D., De Geuser F., Elsayed M., Sextl G., Staab T.E.M. In situ natural ageing of Al–Cu–(Mg) alloys: The effect of In and Sn on the very early stages of decomposition // Scripta Mater. 2019. V. 168. P. 104–107. https://doi.org/10.1016/j.scriptamat.2019.04.031
Liu M., Zhang X., Körner B., Elsayed M., Liang Z., Leyvraz D., Banhart J. Effect of Sn and In on the natural ageing kinetics of Al–Mg–Si alloys // Materialia. 2019. V. 6. P. 100261. https://doi.org/10.1016/j.mtla.2019.100261
Ringer S.P., Hono K., Sakurai T. Nucleation and growth of θ' precipitation in Sn-modified Al–Cu alloys: APFIM/TEM observations // Appl. Surf. Sci. 1995. V. 87–88. P. 223–227. https://doi.org/10.1016/0169-4332(94)00514-1
Thermo-Calc Software TCAl4 Al-Alloys v4.0, http://www.thermocalc.com (дата обращения 22.01.2021)
Мондольфо Л.Ф. Структура и свойства алюминиевых сплавов. Пер. с англ. М.: Металлургия, 1979. 483 с.
Akopyan T.K., Belov N.A., Letyagin N.V. Effect of trace addition of Sn on the precipitation hardening in Al–Si–Cu eutectic alloy // JOM. 2019. V. 71. P. 1768–1775. https://doi.org/10.1007/s11837-019-03422-x
Энтони У.У., Элиот Ф.Р., Болл М.Д. Алюминий. Свойства и физическое металловедение. Справоч. изд. / Под ред. Дж. Е. Хэтча Пер. с англ. М.: Металлургия, 1989. 324 с.
Nie J.F., Muddle B.C. Strengthening of an Al–Cu–Sn alloy by deformation-resistant precipitate plates // Acta Mater. 2008. V. 56. № 14. P. 3490–3501. https://doi.org/10.1016/j.actamat.2008.03.028
Wolverton C. Solute–vacancy binding in aluminum // Acta Mater. 2007. V. 55. P. 5867–5872. https://doi.org/10.1016/j.actamat.2007.06.039
Дополнительные материалы отсутствуют.
Инструменты
Физика металлов и металловедение