Физика металлов и металловедение, 2021, T. 122, № 9, стр. 984-992
Структура и свойства новых деформируемых сплавов на основе систем Al–Cu–Y и Al–Cu–Er
С. М. Амер a, Р. Ю. Барков a, А. С. Просвиряков a, А. В. Поздняков a, *
a НИТУ “МИСиС”
119049 Москва, Ленинский пр., 4, Россия
* E-mail: pozdniakov@misis.ru
Поступила в редакцию 08.02.2021
После доработки 02.04.2021
Принята к публикации 13.04.2021
Аннотация
Исследованы структура и свойства новых деформируемых алюминиевых сплавов Al–4.5Cu–1.6Y–0.9Mg–0.6Mn–0.2Zr–0.1Ti–0.15Fe–0.15Si и Al–4.0Cu–2.7Er–0.8Mg–0.8Mn–0.2Zr–0.1Ti–0.15Fe–0.15Si. После гомогенизации и прокатки в сплавах формируется структура, состоящая из алюминиевого твердого раствора, упрочненного дисперсными частицами фаз Al3(Zr,Er), Al3(Zr,Y) и Al20Cu2Mn3, и компактных термически стабильных фаз кристаллизационного происхождения размером 1–5 мкм. Рекристаллизация после прокатки проходит при температурах выше 350°С. При увеличении температуры отжига с 400 до 550°С размер рекристаллизованного зерна возрастает с 6–8 до 10–12 мкм. При температурах 150–180°С твердость увеличивается после первых часов отжига, что связано с прохождением старения, аналогичный эффект отмечен в литейных сплавах тех же систем. В прокатанном сплаве с иттрием после 6 часов отжига при 150°С предел текучести составляет 405 МПа при относительном удлинении 4.5%. Увеличение температуры отжига до 210°С приводит к снижению предела текучести обоих сплавов до 300 МПа, а удлинение при этом остается на том же уровне. В закаленных после прокатки сплавах при последующем старении при 210°С достигнут предел текучести в 264–266 МПа, предел прочности в 356–365 МПа при относительном удлинении 11.3–14.5%. В результате новые деформируемые сплавы на основе систем Al–Cu–Y и Al–Cu–Er могут составлять конкуренцию существующим промышленным сплавам.
ВВЕДЕНИЕ
Алюминиевые сплавы на основе системы Al‒Cu отличаются достаточно высокой прочностью, как при комнатной, так и при повышенной температурах, но очень низкой технологичностью при литье [1–6]. Высокая технологичность при литье, в частности низкая склонность к образованию трещин кристаллизационного происхождения, важна как для фасонных отливок, так и для слитков полунепрерывного литья [2–7]. Легирование эвтектикообразующими элементами, такими как Fe, Si, Mn, Ni, Ca, способствует повышению технологичности при литье [3–9]. Однако часто при достижении низкой склонности к образованию трещин кристаллизационного происхождения сплавы имеют сильно гетерогенную структуру и невысокую пластичность [6], что, в свою очередь затрудняет получение деформируемых полуфабрикатов. Альтернативный вариант – поиск новых систем легирования, при которых в сплаве могли бы сочетаться структура с дисперсными фазами кристаллизационного происхождения и узкий интервал кристаллизации. К таким можно отнести, сплавы на основе систем Al–Cu–Ce [10, 11], Al–Cu–Y [12, 13], Al–Cu–Er [13, 14], Al–Ca [8, 9, 15]. Отличительной особенностью сплавов, содержащих иттрий и эрбий совместно с цирконием и/или скандием, является возможность дисперсионного упрочнения в процессе отжига слитков [16–36]. Малые добавки иттрия и эрбия в сплаве на основе алюминия [16–23] и в магналии [24–28] повышают упрочняющий эффект при отжиге слитков, сдерживают разупрочнение в процессе отжига после прокатки за счет повышения плотности выделения дисперсоидов, образованных при первой термообработке. Эрбий эффективно модифицирует зеренную структуру [24–26, 30], снижает горячеломкость сплава Al–5Cu [31]. Тройные сплавы систем Al–Cu–Y и Al–Cu–Er [12–14] имеют узкий интервал кристаллизации, а фазы кристаллизационного происхождения малый размер и высокую термическую стабильность. Легирование цирконием [32, 33] и совместно цирконием и марганцем [34, 35] приводит к существенному повышению прочностных характеристик сплавов после деформации. Добавка марганца приводит к образованию фаз кристаллизационного происхождения Al25Cu4Mn2Er [34] и Al25Cu4Mn2Y [35]. Примесь железа растворяется в фазах кристаллизационного происхождения, не изменяя их морфологии, а кремний приводит к образованию достаточно компактных фаз Al3Er2Si2 и Al11Cu2Y2Si2 [36, 37]. Сложнолегированные сплавы на основе систем Al–Cu–Y и Al–Cu–Er с добавками магния, марганца, циркония, титана имеют хорошую технологичность при литье, высокую твердость и характеристики механических свойств при повышенных температурах [38]. Основной недостаток этих сплавов невысокая пластичность [38].
Данная работа представляет исследование структуры и свойств новых деформируемых алюминиевых сплавов на основе систем Al–Cu–Y и Al–Cu–Er, с пониженной концентрацией основных легирующих элементов меди, иттрия, эрбия, циркония, марганца, титана, и содержащих магний и примеси железа и кремния.
МЕТОДИКА ЭКСПЕРИМЕНТОВ
Сплавы составов (в мас. %) Al–4.5Cu–1.6Y–0.9Mg–0.6Mn–0.2Zr–0.1Ti–0.15Fe–0.15Si (AlCuYMg) и Al–4.0Cu–2.7Er–0.8Mg–0.8Mn–0.2Zr–0.1Ti–0.15Fe–0.15Si (AlCuErMg) выплавлены в печи сопротивления из алюминия марки А7 и лигатур Al–51.7Cu, Al–10Y, Al–8Er, Al–10Mn, Al–5Zr, Al–5Ti–1B и магния марки Мг90 при температуре 780°С и разлиты в медную водоохлаждаемую изложницу с размером внутренней полости 20 × × 40 × 120 мм. Исследуемые в данной работе композиции отличаются от литейных аналогов [38] пониженным содержанием меди, иттрия, эрбия, циркония, марганца и титана. Плотность сплавов определяли методом гидростатического взвешивания. Дифференциальный сканирующий калориметр (ДСК) Labsys Setaram использован для определения температур солидуса и ликвидуса. Гомогенизационный отжиг проводили при 575°С в течение 3 ч. После гомогенизационного отжига сплавы были прокатаны до толщины 10 мм при температуре 500°С и до 1 мм при комнатной температуре. После деформации сплавы отжигали при 100–550°С с выдержкой разной продолжительности. Старение при 150–210°С в течение 0.5–6 ч проводили после деформации и последующей закалки с 575°С с выдержкой при этой температуре 15 мин. Микроструктурные исследования и идентификацию фаз проводили на световом микроскопе (СМ) Zeiss, сканирующем электронном микроскопе (СЭМ) TESCAN VEGA 3LMH. Твердость измеряли стандартным методом Виккерса (HV) при нагрузке 5 кг. Испытания на растяжение проводили на универсальной испытательной машине Zwick/Roll Z250. Испытания на общую коррозию проводили в искусственной морской воде.
РЕЗУЛЬТАТЫ ЭКСПЕРИМЕНТОВ И ОБСУЖДЕНИЕ
Температура ликвидуса в исследуемых сплавах составила 635–637°С (рис. 1), что на 3–5°С выше чем в литейных аналогах [38]. Температура ликвидуса определяется содержанием основных добавок меди, иттрия и эрбия согласно тройным диаграммам [39, 40]. Температура солидуса практически не изменилась и составила 588°С (см. рис. 1). Сплавы имеют узкий интервал кристаллизации 47–49°С, что обеспечивает высокую технологичность при литье. Плотность исследуемых сплавов AlCuYMg и AlCuErMg составляет 2.81 и 2.86 г/см3 соответственно, что ниже на 0.2–0.3 г/см3, чем плотность литейных сплавов, содержащих большее количество легирующих добавок [38].
Рисунок 2 иллюстрирует микроструктуру сплавов в литом состоянии. Снижение концентрации основного модификатора титана до 0.1% привело к формированию зерна размером 80–100 мкм в обоих сплавах (рис. 2а, 2в). Для сравнения в сплаве без титана Al–Cu–Y–Zr размер зерна составляет примерно 190 мкм, а в литейном сплаве AlCuErMg с 0.15Ti – 25 мкм. Снижение концентрации основных легирующих элементов не сказалось на фазовом составе сплавов (рис. 2б, 2г и данные работы [38]). Микроструктура представлена алюминиевым твердым раствором, дисперсной эвтектикой, а так же интерметаллидами, образованными добавками марганца, магния, кремния и меди (рис. 2б, 2г). Железо не образует типичных для алюминиевых сплавов фаз.
Рис. 2.
Зеренная структура (а, в (СМ)) и микроструктура (б, г (СЭМ)) сплавов в литом состоянии AlCuYMg (а, б) и AlCuErMg (в, г).
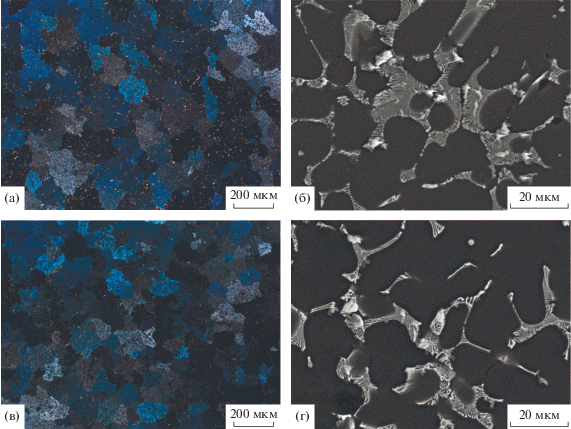
Слитки сплавов отжигали при температуре 575°С перед закалкой в течение 3 ч, в соответствии с режимом, выбранным в работе [38] для литейных аналогов. Растворение неравновесного избытка фаз кристаллизационного происхождения приводит к тому, что концентрация меди в твердом растворе увеличивается до 2.1–2.2%, магния – до 0.9–1.0%. В процессе отжига происходит фрагментация и сфероидизация фаз кристаллизационного происхождения (рис. 3а, 3б), которые частично дробятся и вытягиваются в направлении деформации в ходе прокатки (рис. 3в, 3г). В результате их размер составляет 1–5 мкм. Совместно с процессами гомогенизации происходит выделение из пересыщенного цирконием, иттрием, эрбием и марганцем твердого раствора дисперсоидов фаз Al3(Zr,Er), Al3(Zr,Y) и Al20Cu2Mn3 [34, 35]. В алюминиевом твердом растворе на изображениях микроструктур, полученных с помощью СЭМ, на рис. 3 видны дисперсные светлые включения, которые соответствуют описанным фазам.
Рис. 3.
Микроструктуры сплавов AlCuYMg (а, в) и AlCuErMg (б, г) после отжига при 575°С в течение 3 ч (а, б) и последующей прокатки (в, г).
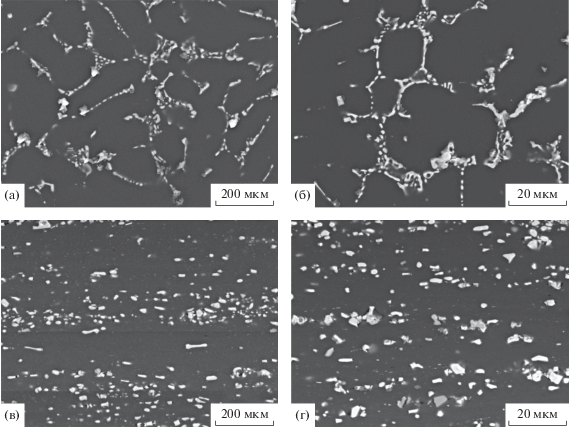
Деформированные листы отжигали при температурах 100–550°С для определения температурного интервала рекристаллизации и анализа изменения твердости (рис. 4). В обоих сплавах отжиг при температурах ниже 350°С сохраняет нерекристаллизованную структуру. При этом твердость сначала (при температуре ниже 150°С) незначительно возрастает, а затем снижается. Рост твердости скорее всего связан с прохождением старения, аналогичный эффект отмечен в сплавах тех же систем без магния [34, 35]. Разупрочнение происходит за счет прохождения процессов полигонизации, а рекристаллизованные зерна отмечены после отжига при 400°С (вставки на рис. 4). При этом размер рекристаллизованного зерна в обоих сплавах составляет 6–8 мкм. Увеличение температуры отжига до 550°С приводит к росту зерна до 10–12 мкм. При этом твердость не изменяется и составляет 65–68 HV.
Рис. 4.
Зависимости твердости HV от температуры отжига в течение одного часа для прокатанных сплавов AlCuYMg (а) и AlCuErMg (б).
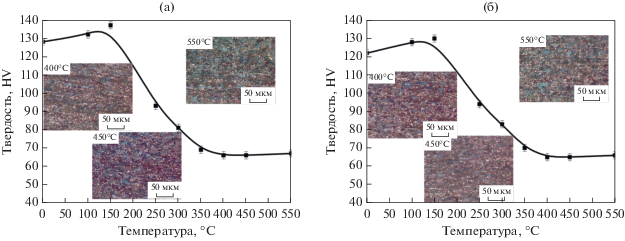
Зависимости твердости деформированных сплавов от времени отжига при низких температурах представлены на рис. 5. Как и было отмечено ранее, при температурах около 150°С в течение первых часов отжига происходит небольшое упрочнение. При увеличении температуры до 180°С после одного часа наблюдается разупрочнение, связанное с прохождением полигонизации. В процессе отжига при 210°С твердость снижается через три часа и не изменяется при увеличении времени выдержки до 6 ч. В данном случае проходит два противоположных процесса: упрочнение, связанное со старением, и разупрочнение, определяемое возвратом и полигонизацией. Таблица 1 иллюстрирует результаты испытаний на растяжение сплавов в деформированном и отожженном состояниях. Предел текучести обоих сплавов в деформированном состоянии составил 380–390 МПа, а относительное удлинение 1.8–2.4%. При этом рост предела текучести в процессе отжига при 150°С отмечен только в сплаве AlCuYMg. После 6 ч отжига предел текучести увеличился с 380 до 405 МПа, при этом пластичность также выросла с 1.8 до 4.5%. Твердость и предел текучести при испытаниях на растяжение показывают разную чувствительность к структурным изменениям. Аналогичный эффект отмечен в сплавах близкого состава без магния [34, 35]. Увеличение температуры отжига до 210°С приводит к снижению предела текучести до примерно 300 МПа, а удлинение при этом остается на невысоком уровне.
Рис. 5.
Зависимости твердости HV от времени отжига деформированных сплавов AlCuYMg (а) и AlCuErMg (б).
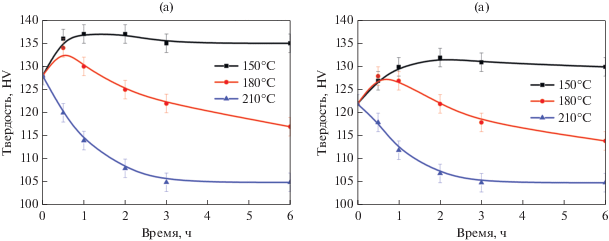
Таблица 1.
Характеристики механических свойств при растяжении сплавов в деформированном и отожженном состояниях
Состояние | σ0.2, МПа | σВ, МПа | δ, % |
---|---|---|---|
AlCuYMg | |||
Деформированное | 380 ± 4 | 381 ± 5 | 1.8 ± 0.5 |
Отжиг 150°С, 1 ч | 390 ± 5 | 422 ± 3 | 4.8 ± 0.4 |
Отжиг 150°С, 6 ч | 405 ± 3 | 432 ± 1 | 4.5 ± 1.2 |
Отжиг 180°С, 0.5 ч | 382 ± 4 | 416 ± 2 | 4.5 ± 0.2 |
Отжиг 180°С, 6 ч | 327 ± 3 | 360 ± 4 | 4.0 ± 0.9 |
Отжиг 210°С, 0.5 ч | 325 ± 4 | 358 ± 4 | 1.5 ± 0.5 |
Отжиг 210°С, 2 ч | 303 ± 2 | 330 ± 4 | 4.4 ± 0.8 |
AlCuErMg | |||
Деформированное | 391 ± 8 | 401 ± 10 | 2.4 ± 0.8 |
Отжиг 150°С, 1 ч | 370 ± 3 | 405 ± 2 | 4.2 ± 0.2 |
Отжиг 150°С, 6 ч | 376 ± 4 | 409 ± 7 | 4.5 ± 1.2 |
Отжиг 180°С, 0.5 ч | 358 ± 4 | 398 ± 2 | 6.2 ± 0.5 |
Отжиг 180°С, 6 ч | 316 ± 2 | 348 ± 2 | 4.0 ± 1.4 |
Отжиг 210°С, 0.5 ч | 320 ± 1 | 345 ± 4 | 2.7 ± 0.5 |
Отжиг 210°С, 2 ч | 295 ± 5 | 327 ± 2 | 5 ± 1 |
Д16 | |||
Нагартованный и отожженный лист [41] | 230–360 | 365–475 | 8–13 |
Пруток [42] | 325–345 | 450–470 | 8–10 |
АК4-1 | |||
Пруток [42] | 335 | 390 | 6 |
После прокатки сплавы закаливали с 575°С с выдержкой 15 мин и старили при 150, 180 и 210°С. На рис. 6 представлены зависимости твердости HV от времени старения листов после закалки. Наблюдаются зависимости качественно аналогичные тем, что получены при старении литейных аналогов [38]. Твердость увеличивается в процессе старения с 64–66 до 105–115 HV. Созданная в сплавах рекристаллизованная структура (вставки на рис. 6) позволяет существенно повысить пластичность сплавов. По результатам испытаний на растяжение относительное удлинение после старения при 210°С в течение 3 ч составляет 11.3–14.5% (табл. 2). При этом предел текучести составил 264–266 МПа, а предел прочности 356–365 МПа. Для сравнения деформируемый сплав Д16 в нагартованном и отожженном состоянии в виде листов [41] имеет предел текучести 230–360 МПа, предел прочности 365–475 МПа, относительное удлинение 8–13%, а в виде прутков [42] – предел текучести 325–345 МПа, предел прочности 450–470 МПа, относительное удлинение 8–10%. Рекристаллизованные прутки [42] имеют предел текучести 265 МПа, предел прочности 410 МПа при относительном удлинении 12%. При этом технологичность при литье у сплава Д16 существенно ниже, чем у исследуемых композиций. Деформируемый сплав АК4-1 с повышенной жаропрочностью [42] в виде прутков имеет предел текучести 335 МПа, предел прочности 390 МПа при относительном удлинении 6%. Таким образом, новые деформируемые сплавы на основе систем Al–Cu–Y и Al–Cu–Er могут составлять конкуренцию существующим промышленным сплавам.
Рис. 6.
Зависимости твердости HV от времени старения листов после закалки с 575°С с выдержкой 15 мин для сплавов AlCuYMg (а) и AlCuErMg (б).
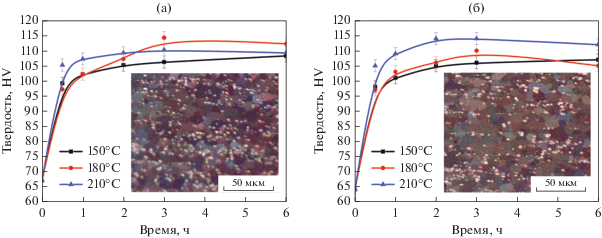
Таблица 2.
Характеристики механических свойств при растяжении сплавов после прокатки и последующих закалки с 575°С с выдержкой 15 мин и старении при 210°С в течение 3 ч
Сплав | σ0,2, МПа | σВ, МПа | δ, % |
---|---|---|---|
AlCuYMg | 266 ± 2 | 365 ± 1 | 14.5 ± 0.5 |
AlCuErMg | 264 ± 2 | 356 ± 1 | 11.3 ± 1.5 |
Д16 (рекристаллизованный) | 265 | 410 | 12 |
Известно, что алюминиевомедные сплавы склонны к коррозии. В данной работе проведена упрощенная оценка коррозионной стойкости по определению общей коррозионной стойкости в искусственной морской воде. После испытания предел текучести сплава AlCuYMg снизился с 405 до 374 МПа, а относительное удлинение с 4.5 до 3% (табл. 3). В сплаве AlCuErMg снижение предела текучести менее существенно.
Таблица 3.
Характеристики механических свойств при растяжении сплавов, прокатанных и отожженных при 150°С в течение 6 ч, до и после испытаний на общую коррозию
Сплав | До коррозионных испытаний | После коррозионных испытаний | ||||
---|---|---|---|---|---|---|
σ0.2, МПа | σВ, МПа | δ, % | σ0.2, МПа | σВ, МПа | δ, % | |
AlCuYMg | 405 ± 3 | 432 ± 1 | 4.5 ± 1.2 | 374 ± 3 | 395 ± 5 | 3 ± 1 |
AlCuErMg | 376 ± 4 | 409 ± 7 | 4.5 ± 1.2 | 365 ± 5 | 388 ± 6 | 2.7 ± 1.2 |
ВЫВОДЫ
Исследованы структура и свойства новых деформируемых алюминиевых сплавов на основе систем Al–Cu–Y и Al–Cu–Er, легированных цирконием, марганцем, магнием, титаном, содержащих примеси железа и кремния. Сплавы имеют узкий интервал кристаллизации 47–49°С, что обеспечивает высокую технологичность при литье. Плотность исследуемых сплавов AlCuYMg и AlCuErMg составляет 2.81 и 2.86 г/см3 соответственно. После гомогенизации и прокатки в сплавах формируется структура, состоящая из алюминиевого твердого раствора, упрочненного дисперсными частицами фаз Al3(Zr,Er), Al3(Zr,Y) и Al20Cu2Mn3, и компактных термически стабильных фаз кристаллизационного происхождения размером 1–5 мкм. Разупрочнение в ходе отжига после прокатки происходит за счет процессов полигонизации при температурах ниже 350°С, а рекристаллизация проходит при более высоких температурах. Размер зерна после отжига при 400°С составляет 6–8 мкм и увеличивается до 10–12 мкм после часового отжига при 550°С. При температурах 150–180°С твердость несколько увеличивается, что связано с прохождением старения, аналогичный эффект отмечен в литейных сплавах тех же систем. В сплаве AlCuYMg. после 6 ч отжига при 150°С после прокатки предел текучести составляет 405 МПа при относительном удлинении 4.5%. Увеличение температуры отжига до 210°С приводит к снижению предела текучести обоих сплавов до 300 МПа, а удлинение при этом остается на том же уровне. В закаленном после прокатки и состаренном при 210°С состоянии пластичность существенно возрастает до 11.3–14.5%, предел текучести составляет 264–266 МПа, а предел прочности 356–365 МПа. В результате новые деформируемые сплавы на основе систем Al–Cu–Y и Al–Cu–Er могут составлять конкуренцию существующим промышленным сплавам.
Работа выполнена при финансовой поддержке Российского Научного Фонда (проект № 19-79-10242).
Список литературы
ГОСТ 1583–93. Сплавы алюминиевые литейные ТУ-Минск: ИПК Изд-во стандартов, 2000.
Zolotorevsky V.S., Belov N.A., Glazoff M.V. Casting Aluminum Alloys, Alcoa Technical Center, Alcoa Center, PA, United States. 2007. 530 p.
ГОСТ 4784–97. Алюминий и сплавы алюминиевые деформируемые. Марки. ИПК Изд-во стандартов, 2001.
Новиков И.И. Горячеломкость цветных металлов и сплавов. М.: Наука, 1966.
Zolotorevskiy V.S., Pozdniakov A.V. Determining the hot cracking index of Al–Si–Cu–Mg casting alloys calculated using the effective solidification range // Int. J. Cast Met. Res. 2014. V. 27. № 4. P. 193–198.
Золоторевский В.С., Поздняков А.В., Чурюмов А.Ю. Поиск перспективных композиций для создания новых многофазных литейных сплавов на основе матрицы Al–Cu–Mg с использованием термодинамических расчетов и математического моделирования // ФММ. 2012. Т. 113. № 11. С. 1111–1120.
Eskin D.G, Suyitno, Katgerman L. Mechanical properties in the semi-solid state and hot tearing of aluminium alloys // Prog. in Mat. Sci. 2004. V. 49. P. 629–711.
Белов Н.А., Наумова Е.А., Базлова Т.А., Алексеева Е.В. Структура, фазовый состав и упрочнение литейных алюминиевых сплавов системы Al–Ca–Mg–Sc // ФММ. 2016. Т. 117. № 2. С. 208–215.
Шуркин П.К., Белов Н.А., Мусин А.Ф., Самошина М.Е. Влияние кальция и кремния на характер кристаллизации и упрочнение сплава Al–8% Zn–3% Mg // ФММ. 2020. Т. 121. № 2. С. 149–156.
Belov N.A., Khvan A.V., Alabin A.N. Microstructure and phase composition of Al–Ce–Cu alloys in the Al-rich corner // Mater. Sci. Forum 2006. V. 519–521 (PART 1). P. 395–400.
Belov N.A., Khvan A.V. The ternary Al–Ce–Cu phase diagram in the aluminum-rich corner // Acta Mater. 2007. V. 55. P. 5473–5482.
Pozdniakov A.V., Barkov R.Y. Microstructure and materials characterisation of the novel Al–Cu–Y alloy // Mater. Sci. and Tech. 2018. V. 34. № 12. P. 1489–1496.
Амер С.М., Барков Р.Ю., Яковцева О.А., Поздняков А.В. Сравнительный анализ структуры и свойств квазибинарных сплавов Al–6.5Cu–2.3Y и Al–6Cu–4.05Er // ФММ. 2020. Т. 121. № 5. С. 528–534.
Поздняков А.В., Барков Р.Ю., Сарсенбаев Ж., Кхамеес Е., Просвиряков А.С. Эволюция микроструктуры и механических свойств нового деформируемого сплава системы Al–Cu–Er // ФММ. 2019. Т. 120. № 6. С. 668–672.
Акопян Т.К., Летягин Н.В., Белов Н.А., Кошмин А.Н., Гизатулин Д.Ш. Анализ микроструктуры и механических свойств нового деформируемого сплава на основе ((Al) + Al4(Ca,La))-эвтектики // ФММ. 2020. V. 121. № 9. P. 1003–1008.
Поздняков А.В., Осипенкова А.А., Попов Д.А., Махов С.В., Напалков В.И. Влияние малых добавок Y, Sm, Gd, Hf и Er на структуру и твердость сплава Al–0.2% Zr–0.1% Sc. Металловедение и термическая обработка металлов // МИТОМ. 2016. Т. 58. № 9. С. 25–30.
Pozdniakov A.V., Barkov R.Yu., Prosviryakov A.S., Churyumov A.Yu., Golovin I.S., Zolotorevskiy V.S. Effect of Zr on the microstructure, recrystallization behavior, mechanical properties and electrical conductivity of the novel Al–Er–Y alloy // J. All. Comp. 2018. V. 765. P. 1–6.
Pozdniakov A.V., Barkov R.Yu. Microstructure and mechanical properties of novel Al–Y–Sc alloys with high thermal stability and electrical conductivity // J. Mater. Sci. & Techn. 2020. V. 36. P. 1–6.
Zhang Y., Gao K., Wen S., Huang H., Nie Z., Zhou D. The study on the coarsening process and precipitation strengthening of Al3Er precipitate in Al–Er binary alloy // J. Alloys Compd. 2014. V. 610. P. 27–34
Wen S.P., Gao K.Y., Li Y., Huang H. and Nie Z.R. Synergetic effect of Er and Zr on the precipitation hardening of Al–Er–Zr alloy // Scr. Mater. 2011. V. 65. P. 592–595.
Wen S.P., Gao K.Y., Huang H., Wang W., Nie Z.R. Precipitation evolution in Al–Er–Zr alloys during aging at elevated temperature // J. Alloys Compd. 2013. V. 574 P. 92–97.
Zhang Y., Gao H., Kuai Y., Han Y., Wang J., Sun B., Gu S., You W. Effects of Y additions on the precipitation and recrystallization of Al–Zr alloys // Mater. Charact. 2013. V. 86. P. 1–8.
Zhang Y., Gu J., Tian Y., Gao H., Wang J., Sun B. Microstructural evolution and mechanical property of Al–Zr and Al–Zr–Y alloys // Mater. Sci. Eng. A. 2014. V. 616. P. 132–140.
Pozdniakov A.V., Yarasu V., Barkov R.Yu., Yakovtseva O.A., Makhov S.V., Napalkov V.I. Microstructure and mechanical properties of novel Al–Mg–Mn–Zr–Sc–Er alloy // Mat. Let. 2017. V. 202. P. 116–119.
Song M., Du K., Huang Z.Y., Huang H., Nie Z.R. and Ye H.Q. Deformation-induced dissolution and growth of precipitates in an Al–Mg–Er alloy during high-cycle fatigue // Acta Mater. 2014 V. 81. P. 409–419.
Hao H.L., Ni D.R., Zhang Z., Wang D., Xiao B.L., Ma Z.Y. Microstructure and mechanical properties of Al–Mg–Er sheets jointed by friction stir welding // Mater. and Des. 2013. V. 52. P. 706–712.
Wen S.P., Wang W., Zhao W.H., Wu X.L., Gao K.Y., Huang H., Nie Z.R. Precipitation hardening and recrystallization behavior of Al–Mg–Er–Zr alloys // J. All. and Comp. 2016. V. 687. P. 143–151.
Barkov R.Yu., Pozdniakov A.V., Tkachuk E., Zolotorevskiy V.S. Effect of Y on microstructure and mechanical properties of Al–Mg–Mn–Zr–Sc alloy with low Sc content // Mat. Let. 2018. V. 217. P. 135–138.
Барков Р.Ю., Мочуговский А.Г., Хомутов М.Г., Поздняков А.В. Влияние малых добавок Zr и Er на фазовый состав и механические свойства сплава Al–5Si–1.3Cu–0.5Mg // ФММ. 2021. Т. 121. № 2. С. 173–180.
Барков Р.Ю., Просвиряков А.С., Хомутов М.Г., Поздняков А.В Влияние содержания Zr и Er на структуру и свойства сплава Al–5Si–1.3Cu–0.5Mg // ФММ. 2021. В печати.
Li M., Wang H., Wei Z., Zhu Z. The effect of Y on the hot-tearing resistance of Al–5 wt % Cu based alloy // Mat. and Des. 2010. V. 31. P. 2483–2487.
Pozdniakov A.V., Barkov R.Yu, Amer S.M., Levchenko V.S., Kotov A.D., Mikhaylovskaya A.V. Microstructure, mechanical properties and superplasticity of the Al–Cu–Y–Zr alloy // Mater. Sci. Eng. A. 2019. V. 758. P. 28–35.
Amer S.M., Barkov R. Yu., Yakovtseva O.A., Loginova I.S., Pozdniakov A.V. Effect of Zr on microstructure and mechanical properties of the Al–Cu–Er alloy // Mater. Sci. Tech. 2020. V. 36. № 4. P. 453–459.
Amer S.M., Yakovtseva O.A., Loginova I.S., Medvedeva S.V.,Prosviryakov A.S., Bazlov A.I., Barkov R.Yu. and Pozdniakov A.V. The Phase Composition and Mechanical Properties of the Novel Precipitation-Strengthening Al–Cu–Er–Mn–Zr Alloy // Appl. Sci. 2020. V. 10. № 15. P. 5345–5353.
Амер С.М., Барков Р.Ю., Поздняков А.В. Влияние Mn на фазовый состав и свойства сплава Al–Cu–Y–Zr // ФММ. 2020. Т. 121. №12. С. 1331–1337.
Амер С.М., Барков Р.Ю., Поздняков А.В. Влияние примесей на фазовый состав и свойства деформируемого сплава Al–6% Cu–4.05% Er // ФММ. 2020. Т. 121. № 5. С. 550–554.
Амер С.М., Барков Р.Ю., Поздняков А.В. Влияние примесей железа и кремния на фазовый состав и механические свойства сплава Al–6.3Cu–3.2Y // ФММ. 2020. Т. 121. № 10 С. 1095–1100.
Амер С.М., Барков Р.Ю., Просвиряков А.С., Поздняков А.В. Структура и свойства новых литейных жаропрочных сплавов на основе системl Al–Cu–Y и Al–Cu–Er // ФММ. 2021. Т. 122. № 9. C. 977–983.
Zhang L., Masset P.J., Tao X., Huanga G., Luo H., Liu L., Jin Z. Thermodynamic description of the Al–Cu–Y ternary system // CALPHAD: Comp. Coup. of Ph. Diag. and Thermochem. 2011. V. 35. P. 574–579.
Zhang L.G., Liu L.B., Huang G.X., Qi H.Y., Jia B.R., Jin Z.P. Thermodynamic assessment of the Al–Cu–Er system // Comp. Coup. of Ph. Diag. and Thermochem. 2008. V. 32. P. 527–534.
ГОСТ 21631–76. Листы из алюминия и алюминиевых сплавов. Технические условия. Стандартинформ, 2008.
ГОСТ Р-51834–2001. Прутки, прессованные из алюминиевых сплавов высокой прочности и повышенной пластичности. Технические условия. ИПК Изд‑во стандартов, 2002.
Дополнительные материалы отсутствуют.
Инструменты
Физика металлов и металловедение