Физика металлов и металловедение, 2021, T. 122, № 9, стр. 977-983
Структура и свойства новых литейных жаропрочных сплавов на основе систем Al–Cu–Y и Al–Cu–Er
С. М. Амер a, b, Р. Ю. Барков a, А. С. Просвиряков a, А. В. Поздняков a, *
a НИТУ “МИСиС”
119049 Москва, Ленинский просп., 4, Россия
b Университет Аль-Азхар, Департамент горного дела, металлургии и нефтяной инженерии,
Инженерный факультет
11884 Каир, Египет
* E-mail: pozdniakov@misis.ru
Поступила в редакцию 08.02.2021
После доработки 27.04.2021
Принята к публикации 30.04.2021
Аннотация
Исследована микроструктура и механические свойства новых жаропрочных литейных алюминиевых сплавов Al–5.6Cu–2.0Y–1Mg–0.8Mn–0.3Zr–0.15Ti–0.15Fe–0.15Si и Al–5.4Cu–3.0Er–1.1Mg–0.9Mn–0.3Zr–0.15Ti–0.15Fe–0.15Si. Модифицирование титаном способствует уменьшению размера зерна со 190 до 40 мкм в сплаве с иттрием, а в сплаве с эрбием размер зерна составляет 25 мкм. По уровню литейных свойств сплавы сопоставимы с силуминами, легированными медью и магнием. Наибольший упрочняющий эффект после закалки достигнут в процессе старения при 210°С, твердость составляет 130–133HV. Предел текучести на растяжение при комнатной температуре составляет 303–306 МПа при относительном удлинении 0.4%. При повышенных температурах 200 и 250°C предел текучести снижается до 246–250 и 209–215 МПа, а удлинение возрастает до 3 и 4–5.5% соответственно. Предел длительной 100-часовой прочности при 250°C составляет 117–118 МПа. Высокую жаропрочность новым сплавам обеспечивают достаточно легированный твердый раствор, наличие упрочняющих дисперсоидов фаз Al3(Zr,Er), Al3(Zr,Y), Al20Cu2Mn3 и фаз кристаллизационного происхождения Al8Cu4Y, (Al,Cu)11Y3, (Al,Cu,Y,Mn) и Al8Cu4Er Al3Er, (Al,Cu,Er,Mn).
ВВЕДЕНИЕ
Большую часть литейных алюминиевых сплавов [1–3] с наилучшими литейными свойствами [2–4] составляют силумины. Однако сплавы на основе системы Al–Si уступают алюминиево-медным по уровню механических свойств, особенно при повышенных температурах [2, 3]. При этом сплавы на основе системы Al–Cu имеют наихудшую среди алюминиевых сплавов технологичность при литье [4–6]. Повышения технологичности при литье алюминиевомедных сплавов можно достичь за счет легирования эвтектикообразующими элементами, такими как Fe, Si, Mn, Ni, Ca [2–8]. С другой стороны, поиск новых систем легирования может позволить создать новые материалы, которые будут сочетать необходимый комплекс свойств. Так, например, сплавы на основе систем Al–Cu–Ce [9, 10], Al–Cu–Y [11, 12], Al–Cu–Er [12, 13], Al–Ca [7, 8, 14], имея узкий интервал кристаллизации и структуру, представленную дисперсной эвтектикой, являются весьма перспективными. При этом стоит отметить, что иттрий и эрбий в алюминиевых сплавах являются эффективными дисперсоидообразующими элементами совместно с цирконием и/или скандием [15–29]. При этом эрбий является хорошим модификатором зерна [16–18], малая добавка иттрия в сплав Al–5Cu снижает горячеломкость [30]. Тройные сплавы систем Al–Cu–Y [11] и Al–Cu–Er [31] на квазибинарных разрезах Al–Al8Cu4Y и Al–Al8Cu4Er имеют узкий интервал кристаллизации, и, соответственно, низкую склонность к образованию трещин кристаллизационного происхождения. При этом механические свойства этих сплавов весьма невелики [11–13]. Дополнительное легирование цирконием [32, 33] и совместно цирконием и марганцем [34, 35] приводит к существенному повышению прочностных характеристик сплавов после деформации. После закалки и старения литых сплавов эффект упрочнения невелик ввиду небольшого количества меди в твердом растворе после закалки [32–35]. Добавка марганца приводит к образованию фаз кристаллизационного происхождения Al25Cu4Mn2Er [34] и Al25Cu4Mn2Y [35], и по форме напоминающей “китайские иероглифы” фазы Al15(Fe,Mn)3Si2 [2, 3, 6]. Примеси железа и кремния не оказывают существенного влияния на механические свойства тройных сплавов [36, 37]. Железо растворяется в фазах кристаллизационного происхождения, не изменяя их морфологии, а кремний приводит к образованию достаточно компактных фаз Al3Er2Si2 и Al11Cu2Y2Si2 [36, 37].
Данная работа представляет исследование структуры и свойств при комнатной и повышенных температурах новых литейных алюминиевых сплавов на основе систем Al–Cu–Y и Al–Cu–Er, дополнительно легированных цирконием, марганцем, титаном, магнием и содержащих примеси железа и кремния.
МЕТОДИКА ЭКСПЕРИМЕНТОВ
Сплавы составов (в мас. %) Al–5.6Cu–2.0Y–1Mg–0.8Mn–0.3Zr–0.15Ti–0.15Fe–0.15Si (AlCuYMg) и Al–5.4Cu–3.0Er–1.1Mg–0.9Mn–0.3Zr–0.15Ti–0.15Fe–0.15Si (AlCuErMg) выплавлены в печи сопротивления при температуре 830°С. Для выплавки использованы алюминий марки А7 и лигатуры Al–51.7Cu, Al–10Y, Al–8Er, Al–10Mn, Al–5Zr, Al–5Ti–1B и магний марки Мг90. Сплавы были разлиты в медную водоохлаждаемую изложницу с размером внутренней полости 20 × 40 × 120 мм и стальной кокиль для получения образцов для испытаний на одноосное растяжение. Для испытаний на растяжение вытачивали образцы с головками и диаметром рабочей части 5 мм. Показатель горячеломкости (ПГ) определяли по карандашной пробе путем трех заливок в стальной разъемный кокиль комнатной температуры и подогретый до 250°С [2, 4–6]. Плотность сплавов определяли методом гидростатического взвешивания. Дифференциальный сканирующий калориметр (ДСК) Labsys Setaram использован для определения температур солидуса и ликвидуса. Гомогенизационный отжиг проводили при 575°С в течение 1, 3 и 6 ч. После отжига 575°С, 3 ч сплав закаливали и проводили старение в интервале температур 150–210°С. Микроструктурные исследования и идентификацию фаз проводили на световом микроскопе (СМ) Zeiss, сканирующем электронном микроскопе (СЭМ) TESCAN VEGA 3LMH и рентгеновском дифрактометре Bruker D8 Advance. Твердость измеряли стандартным методом Виккерса (HV) при нагрузке 5 кг. Испытания на растяжение при комнатной и повышенных температурах проводили на универсальной испытательной машине Zwick/Roll Z250. Испытания на определение предела длительной 100-часовой прочности при 250°С проводили на испытательной машине Instron M3. Испытания на сжатие при комнатной и повышенной температурах проводили на комплексе Gleeble-3800.
РЕЗУЛЬТАТЫ ЭКСПЕРИМЕНТОВ И ОБСУЖДЕНИЕ
ПГ исследуемых сплавов по карандашной пробе составляет 12–14 мм. При заливке в кокиль при комнатной температуре трещины обнаруживали на участках рабочей части диаметром 10 и 12 мм, при заливке в кокиль предварительно подогретый до 250°С – только на участке диаметром 10 мм. Близкий уровень литейных свойств имеют медистые силумины [4, 5]. Интервал кристаллизации исследуемых сплавов составляет примерно 50°С (ДСК-кривые на рис. 1), что примерно на 20°С больше чем в тех же сплавах без магния [11–13, 32–36]. Добавка магния снижает температуру солидуса до 585°С, что примерно на 40°С ниже, чем в сплавах без него. Плотность сплавов AlCuYMg и AlCuErMg составляет 2.83 и 2.89 г/см3 соответственно, что связано с наличием более тяжелого эрбия в сплаве AlCuErMg.
Рисунок 2 иллюстрирует зеренную структуру литых сплавов. Модифицированные титаном сплавы имеют более мелкое зерно в сравнение со сплавами без добавок [32, 33]. К примеру, в сплаве Al–Cu–Y–Zr размер зерна составляет примерно 190 мкм [32], а в исследованном в настоящей работе сплаве AlCuYMg с 0.15% Ti–40 мкм. В сплаве же с эрбием AlCuErMg размер зерна еще меньше и составляет 25 мкм, что подтверждает эффективную модифицирующую способность добавки Ti.
Согласно анализу фазового состава посредством СЭМ (рис. 2) и рентгенограммам (рис. 3), в слитках сплавов присутствуют фазы Al8Cu4Y, (Al,Cu)11Y3, AlCu, Al8Cu4Er и Al3Er, а также четверные фазы (Al,Cu,Y,Mn) и (Al,Cu,Er,Mn), идентифицированные как Al25Cu4Mn2Er [34] и Al25Cu4Mn2Y [35]. Железо растворяется в фазах кристаллизационного происхождения (карты распределения легирующих элементов на рис. 3). Кремний с магнием образуют фазу, которая по морфологии и контрасту соответствует Mg2Si. Ввиду большого количества фаз в сплаве, малой доли Mg2Si в структуре, выявить ее пики на рентгенограмме не удалось (рис. 4). Помимо образования фазы Mg2Si, магний не оказал влияния на фазовый состав сплавов. На рис. 4 приведены для сравнения рентгенограммы сплавов без магния.
Рис. 3.
Микроструктура литых сплавов и распределение легирующих элементов между фазами в выделенной области (белый прямоугольник) в сплавах AlCuYMg (а) и AlCuErMg (б) (СЭМ).
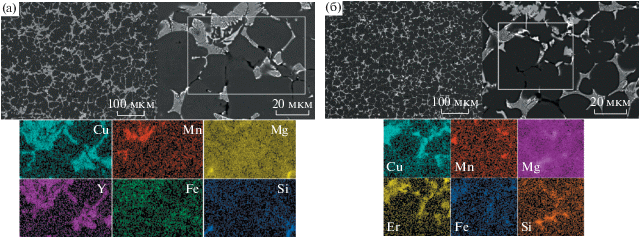
Рис. 4.
Рентгеновские дифрактограммы сплавов AlCuYMg (а) и AlCuErMg (б) (черные линии) в сравнение со сплавами без магния (серые линии).
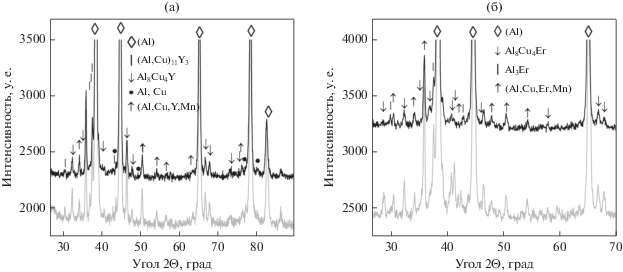
Слитки сплавов отжигали при температуре 575°С (на 10°С ниже солидуса (рис. 1)) перед закалкой в течение 1, 3 и 6 ч. В литом состоянии концентрация меди в твердом растворе составляет 1.1%, магния – 0.6%, циркония, иттрия и эрбия – по 0.2–0.3%, марганца – 0.8%. В процессе гомогенизационного отжига перед закалкой происходит растворение неравновесного избытка фаз кристаллизационного происхождения. Фаза Mg2Si практически полностью растворяется после 1 ч отжига. Полное насыщение твердого раствора медью и магнием происходит после 3 ч отжига, а после 6 ч состав твердого раствора не изменяется. В результате после трех часов гомогенизации в твердом растворе находится примерно 2.1–2.2Cu и 1–1.1Mg, концентрация остальных добавок не изменяется. В процессе отжига также происходит фрагментация и сфероидизация фаз кристаллизационного происхождения. При этом увеличение времени отжига с 1 до 6 ч не приводит к существенному росту частиц. Параллельно с процессами гомогенизации происходят процессы гетерогенизации. Как показано в работах [34, 35], в процессе высокотемпературной гомогенизации образуются дисперсоиды фаз Al3(Zr,Er) и Al3(Zr,Y) в сплавах без магния AlCuEr [33] и AlCuY [34] cсоответственно, а также фаза Al20Cu2Mn3. В теле зерна на изображениях микроструктур на рис. 5 можно увидеть дисперсные светлые включения, которые соответствуют описанным фазам.
Рис. 5.
Микроструктуры сплавов AlCuYMg (а–в) и AlCuErMg (г–е) после отжига при 575°С в течение 1 (а, г), 3 (б, д) и 6 (в, е) ч (СЭМ).
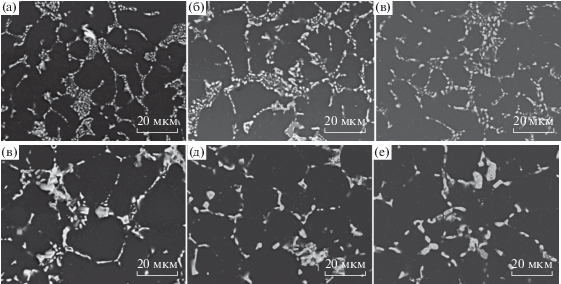
После трех часов гомогенизации при 575°С сплавы были закалены и состарены при 150, 180 и 210°С. Зависимости твердости от времени старения представлены на рис. 6. Вне зависимости от температуры старения сплавы показывают существенный упрочняющий эффект – твердость увеличивается с 80–85 HV до 120–133 HV. Несколько больший упрочняющий эффект происходит в результате старения при 210°С. Упрочнение в процессе старения происходит за счет выделения метастабильной фазы S (Al2CuMg). Твердый раствор в исследуемых сплавах по меди и магнию близок к твердому раствору в жаропрочном деформируемом сплаве АК4-1 [38], в котором упрочнение при старении происходит за счет метастабильных выделений фазы S.
После старения, обеспечивающего максимальную твердость, при 210°C в течение 6 ч, были определены характеристики механических свойств по результатам испытаний на растяжение (табл. 1), сжатие (табл. 2) при комнатной и повышенных температурах. Оба сплава имеют предел текучести на растяжение при комнатной температуре равный 303–306 МПа при удлинении 0.4%. При повышении температуры испытания до 200 и 250°C предел текучести снижается до 246–250 и 209–2115 МПа, а удлинение возрастает до 3 и 4–5.5% соответственно. Для сравнения стандартный литейный алюминиевый сплав АМ5 [1] имеет примерно такой же предел прочности 314–333 МПа, большее относительное удлинение 2–8% и показатель горячеломкости по карандашной пробе более 16 мм [4–6].
Таблица 1.
Характеристики механических свойств по результатам испытаний на растяжение
Сплав | 20°C | 200°C | 250°C | ||||||
---|---|---|---|---|---|---|---|---|---|
σ0.2,МПа | σВ,МПа | δ, % | σ0.2,МПа | σВ,МПа | δ, % | σ0.2,МПа | σВ,МПа | δ, % | |
AlCuYMg | 306 ± 1 | 322 ± 2 | 0.4 ± 0.1 | 250 ± 8 | 280 ± 20 | 3 ± 1 | 215 ± 5 | 244 ± 3 | 5.5 ± 1.5 |
AlCuErMg | 303 ± 2 | 319 ± 4 | 0.4 ± 0.1 | 246 ± 8 | 280 ± 20 | 3 ± 1 | 209 ± 4 | 235 ± 5 | 4 ± 2 |
Таблица 2.
Предел текучести на сжатие (в МПа) при повышенных температурах
Сплав | 200°C | 250°C | 300°C |
---|---|---|---|
AlCuYMg | 237 ± 12 | 223 ± 13 | 151 ± 7 |
AlCuErMg | 243 ± 8 | 197 ± 10 | 160 ± 8 |
Предел текучести на сжатие при повышенных температурах (табл. 2) достаточно хорошо коррелирует с пределом текучести на растяжение (табл. 1). Предел текучести на сжатие при 300°C составляет 151–160МПа, в то время как для большинства алюминиевых сплавов при повышении температуры выше 250°C предел текучести снижается ниже 100 МПа [39]. Для сравнения жаропрочные композиционные материалы на основе сплава Al–5Cu–0.8Mn, армированные карбидом бора, имеют меньший предел текучести на сжатие при 250°C равный 160 МПа [40]. Предел длительной прочности $\sigma _{{100}}^{{250^\circ {\text{C}}}}$ составляет 117–118 МПа. Для сравнения для сплава 201.0 на основе системы Al–Cu–Mg предел 100-часовой прочности при 260°C составляет 95 МПа [39]. Высокую жаропрочность обеспечивают достаточно легированный твердый раствор, наличие упрочняющих дисперсоидов фаз Al3(Zr,Er), Al3(Zr,Y), Al20Cu2Mn3 и фаз кристаллизационного происхождения Al8Cu4Y, (Al,Cu)11Y3, (Al,Cu,Y,Mn) и Al8Cu4Er Al3Er, (Al,Cu,Er,Mn) в сплавах AlCuYMg и AlCuErMg соответственно.
Исследована микроструктура и механические свойства новых жаропрочных литейных алюминиевых сплавов на основе систем Al–Cu–Y и Al–Cu–Er, дополнительно легированных цирконием, марганцем, титаном, магнием и содержащих примеси железа и кремния. Модифицирование титаном способствует уменьшению размера зерна со 190 до 40 мкм в сплаве с иттрием, а в сплаве с эрбием размер зерна составляет 25 мкм. ПГ исследуемых сплавов по карандашной пробе составляет 12–14 мм, что сопоставимо с уровнем литейных свойств силуминов, легированных медью и магнием. Сплавы упрочняются старением. Наибольший упрочняющий эффект достигнут после старения при 210°С, твердость составляет 130–133HV. Предел текучести на растяжение при комнатной температуре составляет 303–306 МПа при удлинении 0,4%. При повышении температуры испытания до 200 и 250°C предел текучести снижается до 246–250 и 209–215 МПа, а удлинение возрастает до 3 и 4–5.5% соответственно. Предел длительной прочности $\sigma _{{100}}^{{250^\circ {\text{C}}}}$ составляет 117–118 МПа. Высокую жаропрочность новым сплавам обеспечивают достаточно легированный твердый раствор, наличие упрочняющих дисперсоидов фаз Al3(Zr,Er), Al3(Zr,Y), Al20Cu2Mn3 и фаз кристаллизационного происхождения Al8Cu4Y, (Al,Cu)11Y3, (Al,Cu,Y,Mn) и Al8Cu4Er Al3Er, (Al,Cu,Er,Mn).
Работа выполнена при финансовой поддержке Российского Научного Фонда (проект № 19-79-10242).
Список литературы
ГОСТ 1583–93. Сплавы алюминиевые литейные ТУ-Минск: ИПК Изд-во стандартов, 2000.
Золоторевский В.С., Белов Н.А. Металловедение литейных алюминиевых сплавов. М.: МИСиС, 2005. 376 с.
Zolotorevsky V.S., Belov N.A., Glazoff M.V. Casting Aluminum Alloys, Alcoa Technical Center, Alcoa Center, PA, United States, 2007. 530 p.
Новиков И.И. Горячеломкость цветных металлов и сплавов. М.: Наука, 1966. 299 с.
Zolotorevskiy V.S., Pozdniakov A.V. Determining the hot cracking index of Al–Si–Cu–Mg casting alloys calculated using the effective solidification range // Int. J. Cast Met. Res. 2014. V. 27. № 4. P. 193–198.
Золоторевский В.С., Поздняков А.В., Чурюмов А.Ю. Поиск перспективных композиций для создания новых многофазных литейных сплавов на основе матрицы Al–Cu–Mg с использованием термодинамических расчетов и математического моделирования // ФММ. 2012. Т. 113. № 11. С. 1111–1120.
Шуркин П.К., Белов Н.А., Мусин А.Ф., Аксенов А.А. Новый высокопрочный литейный алюминиевый сплав на основе системы Al–Zn–Mg–Ca–Fe, не требующий термообработки // Изв. вузов. Цветная металлургия. 2020. № 1. С. 48–58.
Шуркин П.К., Белов Н.А., Мусин А.Ф., Самошина М.Е. Влияние кальция и кремния на характер кристаллизации и упрочнение сплава Al–8% Zn–3% Mg // ФММ. 2020. Т. 121. № 2. С. 149–156.
Belov N.A., Khvan A.V., Alabin A.N. Microstructure and phase composition of Al–Ce–Cu alloys in the Al-rich corner // Mater. Sci. Forum 2006. V. 519–521(PART 1). P. 395–400.
Belov N.A., Khvan A.V. The ternary Al–Ce–Cu phase diagram in the aluminum-rich corner // Acta Mater. 2007. V. 55. P. 5473–5482.
Pozdniakov A.V., Barkov R.Y. Microstructure and materials characterisation of the novel Al–Cu–Y alloy // Mater. Sci. and Tech. 2018. V. 34. № 12. P. 1489–1496.
Амер С.М., Барков Р.Ю., Яковцева О.А., Поздняков А.В. Сравнительный анализ структуры и свойств квазибинарных сплавов Al–6.5Cu–2.3Y и Al–6Cu–4.05Er // ФММ. 2020. Т. 121. № 5. С. 528–534.
Поздняков А.В., Барков Р.Ю., Сарсенбаев Ж., Кхамеес Е., Просвиряков А.С. Эволюция микроструктуры и механических свойств нового деформируемого сплава системы Al–Cu–Er // ФММ. 2019. Т. 120. № 6. С. 668–672.
Белов Н.А., Наумова Е.А., Базлова Т.А., Алексеева Е.В. Структура, фазовый состав и упрочнение литейных алюминиевых сплавов системы Al–Ca–Mg–Sc // ФММ. 2016. Т. 117. № 2. С. 208–215.
Поздняков А.В., Осипенкова А.А., Попов Д.А., Махов С.В., Напалков В.И. Влияние малых добавок Y, Sm, Gd, Hf и Er на структуру и твердость сплава Al–0.2% Zr–0.1% Sc. Металловедение и термическая обработка металлов // МИТОМ. 2016. Т. 58. № 9. С. 25–30.
Pozdniakov A.V., Yarasu V., Barkov R.Yu., Yakovtseva O.A., Makhov S.V., Napalkov V.I. Microstructure and mechanical properties of novel Al–Mg–Mn–Zr–Sc–Er alloy // Mat. Let. 2017. V. 202. P. 116–119.
Hao H.L., Ni D.R., Zhang Z., Wang D., Xiao B.L., Ma Z.Y. Microstructure and mechanical properties of Al–Mg–Er sheets jointed by friction stir welding // Mater. and Des. 2013. V. 52. P. 706–712.
Барков Р.Ю., Просвиряков А.С., Хомутов М.Г., Поздняков А.В. Влияние содержания Zr и Er на структуру и свойства сплава Al–5Si–1.3Cu–0.5Mg // ФММ. 2021. Т. 122. № 6. С. 658–664.
Pozdniakov A.V., Barkov R.Yu., Prosviryakov A.S., Churyumov A.Yu., Golovin I.S., Zolotorevskiy V.S. Effect of Zr on the microstructure, recrystallization behavior, mechanical properties and electrical conductivity of the novel Al–Er–Y alloy // J. All. Comp. 2018. V. 765. P. 1–6.
Pozdniakov A.V., Barkov R.Yu. Microstructure and mechanical properties of novel Al–Y–Sc alloys with high thermal stability and electrical conductivity // J. Mater. Sci. & Techn. 2020. V. 36. P. 1–6.
Zhang Y., Gao K., Wen S., Huang H., Nie Z, Zhou D. The study on the coarsening process and precipitation strengthening of Al3Er precipitate in Al–Er binary alloy // J. Alloys Compd. 2014. V. 610. P. 27–34.
Wen S.P., Gao K.Y., Li Y., Huang H., Nie Z.R. Synergetic effect of Er and Zr on the precipitation hardening of Al–Er–Zr alloy // Scr. Mater. 2011. V. 65. P. 592–595.
Wen S.P., Gao K.Y., Huang H., Wang W., Nie Z.R. Precipitation evolution in Al–Er–Zr alloys during aging at elevated temperature // J. Alloys Compd. 2013. V. 574. P. 92–97.
Zhang Y., Gao H., Kuai Y., Han Y., Wang J., Sun B., Gu S., You W. Effects of Y additions on the precipitation and recrystallization of Al–Zr alloys // Mater. Charact. 2013. V. 86. P. 1–8.
Zhang Y., Gu J., Tian Y., Gao H., Wang J., Sun B. Microstructural evolution and mechanical property of Al–Zr and Al–Zr–Y alloys // Mater. Sci. Eng. A. 2014. V. 616. P. 132–140.
Song M., Du K., Huang Z.Y., Huang H., Nie Z.R., Ye H.Q. Deformation-induced dissolution and growth of precipitates in an Al–Mg–Er alloy during high-cycle fatigue // Acta Mater. 2014. V. 81. P. 409–419.
Wen S.P., Wang W., Zhao W.H., Wu X.L., Gao K.Y., Huang H., Nie Z.R. Precipitation hardening and recrystallization behavior of Al–Mg–Er–Zr alloys // J. All. and Comp. 2016. V. 687. P. 143–151.
Barkov R.Yu., Pozdniakov A.V., Tkachuk E., Zolotorevskiy V.S. Effect of Y on microstructure and mechanical properties of Al–Mg–Mn–Zr–Sc alloy with low Sc content // Mat. Letters. 2018. V. 217. P. 135–138.
Барков Р.Ю., Мочуговский А.Г., Хомутов М.Г., Поздняков А.В. Влияние малых добавок Zr и Er на фазовый состав и механические свойства сплава Al–5Si–1.3Cu–0.5Mg // ФММ. 2021. Т. 122. № 2. С. 173–180.
Li M., Wang H., Wei Z., Zhu Z. The effect of Y on the hot-tearing resistance of Al–5 wt % Cu based alloy // Mat. and Des. 2010. V. 31. P. 2483–2487.
Zhang L., Masset P.J., Cao F., Meng F., Liu L., Jin Z. Phase relationships in the Al-rich region of the Al–Cu–Er system // J. of All. and Comp. 2011. V. 509. P. 3822–3831.
Pozdniakov A.V., Barkov R.Yu., Amer S.M., Levchenko V.S., Kotov A.D., Mikhaylovskaya A.V. Microstructure, mechanical properties and superplasticity of the Al–Cu–Y–Zr alloy // Mater. Sci. Eng. A. 2019. V. 758. P. 28–35.
Amer S.M., Barkov R. Yu., Yakovtseva O.A., Loginova I.S., Pozdniakov A.V. Effect of Zr on microstructure and mechanical properties of the Al–Cu–Er alloy // Mater. Sci. Tech. 2020. V. 36. № 4. P. 453–459.
Amer S.M., Yakovtseva O.A., Loginova I.S., Medvedeva S.V., Prosviryakov A.S., Bazlov A.I., Barkov R.Yu., Pozdniakov A.V. The Phase Composition and Mechanical Properties of the Novel Precipitation-Strengthening Al–Cu–Er–Mn–Zr Alloy // Appl. Sci. 2020. V. 10. № 15. P. 5345–5353.
Амер С.М., Барков Р.Ю., Поздняков А.В. Влияние Mn на фазовый состав и свойства сплава Al–Cu–Y–Zr // ФММ. 2020. Т. 121. № 12. С. 1331–1337.
Амер С.М., Барков Р.Ю., Поздняков А.В. Влияние примесей на фазовый состав и свойства деформируемого сплава Al–6% Cu–4.05% Er // ФММ. 2020. Т. 121. № 5. С. 550–554.
Амер С.М., Барков Р.Ю., Поздняков А.В. Влияние примесей железа и кремния на фазовый состав и механические свойства сплава Al–6.3Cu–3.2Y // ФММ. 2020. Т. 121. № 10. С. 1095–1100.
ГОСТ 4784–2019. Алюминий и сплавы алюминиевые деформируемые. Марки: ИПК Изд-во стандартов, 2019.
ASM HANDBOOK. Properties and Selection: Nonferrous Alloys and Special-Purpose Materials. V. 2. The Materials Information Company, 2010.
Lotfy A., Pozdniakov A.V., Zolotorevskiy V.S., Mohamed E., Abou El-Khair M.T., Daoud A., Fairouz F. Microstructure, compression and creep properties of Al–5% Cu–0.8Mn/5% B4C composites // Mater. Res. Exp. 2019. V. 6. P. 095530.
Дополнительные материалы отсутствуют.
Инструменты
Физика металлов и металловедение