Физика металлов и металловедение, 2021, T. 122, № 9, стр. 963-976
Эволюция микроструктуры и механическое поведение суперсплава Инконель 625, полученного прямым лазерным осаждением металла
Синчен Ван a, b, Чанюнь Чен a, b, *, Ланьлань Цинь b, Минь Чжан a, b
a Главная лаборатория передовых промышленных технологий в Цзиансу, Хуайиньский Технологический Институт
223001 Хуайань, Китай
b Исследовательский центр лазерной обработки, Факультет электромеханического машиностроения, Государственный университет Сучжоу
215131 Сучжоу, Тайвань
* E-mail: 503047820@qq.com
Поступила в редакцию 13.12.2020
После доработки 08.03.2021
Принята к публикации 18.05.2021
Аннотация
Изучены микроструктура и механическое поведение суперсплава Инконель 625, изготовленного по аддитивной технологии послойного синтеза методом прямого лазерного осаждения металла (DLMD), а затем подвергнутого термической обработке отжигом при трех различных температурах (1000, 1100, 1200°C). В исследовании объекты цилиндрической формы были изготовлены с помощью мощного импульсно-волнового оптоволоконного лазера, что позволило добиться их высокого качества – без трещин, ошибок упаковки на границах сопряжения или пористости. Для анализа микроструктуры полученных образцов были использованы сканирующая и просвечивающая электронная микроскопия. Было установлено, что выделение некоторых фаз Лавеса в междендритных областях явилось результатом сегрегации ниобия и молибдена. Для исследования термической стабильности дендритной морфологии были проведены отжиги при температурах от 1000 до 1200°C. Выделились карбиды двух типов: эллипсоидальной формы – карбиды NbC и блочного вида – Nb(Ti)C. Более того, морфология фазы Лавеса изменялась от неправильной формы крупных частиц до мелкодисперсной блочной или стержневидной формы. С повышением температуры отжига от 1000 до 1200°C, указанная фаза Лавеса частичное растворяется в γ-Ni матрице, что приводит к формированию крупных рекристаллизованных зерен. Результаты испытаний на растяжение показали, что после отжига сплав имеет более высокие предел прочности при растяжении и относительное удлинение в сравнении со значениями для образцов после DLMD-синтеза.
ВВЕДЕНИЕ
Суперсплав на основе никеля Инконель 625 широко используется в различных областях, таких как аэронавтика, аэрокосмическая, морская, химическая и нефтехимическая промышленность. Этот сплав показал высокую прочность, отличную коррозионную стойкость и высокую термостойкость – характеристики, которые могут быть использованы в приложениях, требующих экстремальной устойчивости к ползучести [1, 2].
Сплав Инконель 625 получают с помощью обычной технологии ковки, прокатки, литья или экструзии. Он также может быть изготовлен по новой распространенной аддитивной технологии (3D-печати), предполагающей многочисленные преимущества по сравнению с обычным производственным процессом с точки зрения изготовления изделий сложной или почти точной формы и т.д. Для металлов существуют две распространенные технологии аддитивного производства на основе использования лазера, включая селективное лазерное плавление в слое порошка (SLM) и прямое лазерное нанесение металла (DLMD). Как SLM, так и DLMD способы позволяют производить полностью функциональные детали непосредственно из металлического порошка на основе системы автоматизированного проектирования (CAD) без специальной оснастки. В исследованиях многие ученые сосредоточены на анализе феноменологии процесса, а также на влиянии параметров обработки на получение плотных компонентов [3–8]. Например, Sateesh и др. [6] изготовили SLM суперсплав Инконель 625 и изучили взаимодействие различных параметров в плане их влияния на точность размеров изделия, микротвердость и плотность сплава. Carter и др. [7] в основном сосредоточили свое внимание на плотности энергии, чтобы получить образцы из сплава Инконель 625 с относительной плотностью 100%.
Чрезвычайно высокие скорости затвердевания, присущие SLM, приводят к образованию тонкой дендритной структуры и подавлению макросегрегаций с образованием крупных фаз Лавеса или карбидов, что может отрицательно сказаться на механических свойствах [9–12]. Микроструктура, полученная методом лазерного поверхностного плавления, находится вне равновесия, и необходимо проведение термической обработки для гомогенизации микроструктуры, снижения уровня остаточных напряжений и устранения микропористости, связанной с технологией, с целью улучшения механических свойств [9–11]. Термическая обработка сплава Инконель 625 может способствовать образованию различных выделений, таких как фазы Лавеса и карбиды, которые могут повлиять на его механические свойства [13, 14]. Например, Kreitcberg и др. [13] изучили влияние различных термических обработок и горячего изостатического прессования на микроструктуру и механические свойства сплава Инконель 625, полученного лазерным плавлением порошка. В их работе были проведены отжиг для снятия напряжений, рекристаллизационный отжиг и низкотемпературная обработка на твердый раствор. Кроме того, образцы на растяжение из сплава Инконель 625, изготовленные методом SLM и подвергнутые различным обработкам, таким как отжиг для снятия напряжений, низкотемпературная обработка на твердый раствор и горячее изостатическое прессование, были испытаны при комнатной температуре и при 760°C [14].
Для изучения влияния различных упорядоченных фаз и их роста на свойства при растяжении при комнатной температуре и поведение при разрушении суперсплава Инконель 625 образцы этого сплава выдерживали изотермически при 540, 700 и 850°С в каждом случае в течение 10, 100 и 1200 ч [15]. Характеристики упорядоченных фаз Ni2(Cr, Mo), γ" и δ изучали с помощью просвечивающей электронной микроскопии. Было обнаружено, что первичные карбиды ответственны за зарождение пустот, приводящих к появлению больших ямочек на поверхности разрушения суперсплава Инконель 625, в котором матрица представляет собой твёрдый раствор. Фазы Ni2(Cr, Mo) и γ" как на стадии их формирования, так и в ходе последующего роста при 540°С, были ответственны за увеличение прочности без значительного снижения пластичности. Выделение δ-фазы, после 1200 ч изотермической выдержки при 850°С, способствует формированию поверхности излома аналогичной поверхности излома сплава, в котором после 1200 ч изотермической выдержки при 700°С выделилась γ"-фаза.
Недавние сообщения показали, что быстрый нагрев и высокая скорость охлаждения приводят к направленному росту зерен, а затем к образованию столбчатых зерен вытянутой формы [16–18]. Направление роста зерен в основном перпендикулярно подложке, и, тем самым, наблюдается анизотропия направления роста. Как для процесса SLM, так и для процесса DLMD изготовленные по аддитивной технологии детали демонстрируют сильную анизотропию текстуры, которая оказывает значительное влияние на механические свойства. В зависимости от промышленного применения и амплитуды и направлений механических нагрузок острая текстура в этих деталях может снизить механическое сопротивление при эксплуатации с появлением внезапного хрупкого разрушения материала. Поэтому необходимо изучить влияние термической обработки на микроструктуру и свойства деталей, произведeнных по технологиям SLM и DLMD. Dinda и др. [18] изучали влияние термообработки на дендритную микроструктуру сплава Инконель 625, изготовленного по DLMD технологии. Было обнаружено, что микроструктура имеет столбчатую дендритную природу, структура росла эпитаксиально от подложки. Авторами [18] была исследована термическая стабильность дендритной структуры в диапазоне температур 800–1200°С. Они обнаружили, что дендритная микроструктура может быть изменена только в результате обработки при температуре выше 1000°С, после которой для структуры характерны рекристаллизованные равноосные зерна.
На сегодняшний день опубликовано лишь несколько работ по механическим свойствам и микроструктуре термически обработанных образцов из суперсплава Инконель 625, изготовленных по технологии DLMD. Например, плотная ячеисто-дендритная структура, содержащая карбиды типа MC, M23C6 и M6C, была обнаружена методом рентгеновской дифракции после лазерного осаждения металла. Испытания на сжатие вдоль и перпендикулярно направлению аддитивной сборки показывают незначительную анизотропию сопротивления на излом [19]. Когда температура обработки на твёрдый раствор достигала 1200°С, статическая рекристаллизация протекала более полно. Результаты испытаний на растяжение показали, что показатели относительного удлинения и деформационного упрочнения суперсплава Инконель 625 улучшались по мере роста температуры обработки на твeрдый раствор, в то же время предел текучести снижался. Это указывает на то, что способность к равномерной пластической деформации усиливается с повышением температуры обработки на твeрдый раствор. Снижение предела текучести было обусловлено уменьшением плотности дислокаций. Увеличение показателя деформационного упрочнения задерживало появление шейки, а растворение фазы Лавеса приводило к увеличению пластичности.
Мы рассматриваем данную работу как логическое продолжение наших предыдущих исследований по влиянию различных обработок на микроструктуру, текстуру и механические свойства (на растяжение) образцов из суперсплава Инконель 625, полученных аддитивным методом [20]. Работа проведена с целью достижения более глубокого понимания взаимосвязей между микроструктурой и механическими свойствами исследуемого сплава, в первую очередь, при различных температурах отжига.
МАТЕРИАЛЫ И МЕТОДЫ ИССЛЕДОВАНИЯ
Использовали находящийся в свободном доступе порошок марки Inconel 625 (Höganäs, Halmstad, Швеция). Химический состав приведeн в табл. 1. Никель и хром в составе сплава Inconel 625 обеспечивают его устойчивость по отношению к окислительной среде, а никель и молибден – то же в условиях других агрессивных сред. Между тем молибден способен предотвратить точечную и щелевую коррозию, а ниобий повышает стабильность сплава к межкристаллитной коррозии при сварке [4].
Таблица 1.
Химический состав порошка Inconel 625 (вес. %)
Хим.элемент | Ni | Cr | Mo | Nb | Ti | Al | C |
---|---|---|---|---|---|---|---|
Состав | 64.57 | 22.69 | 8.72 | 3.54 | 0.2 | 0.16 | 0.1 |
На рис. 1a представлены морфология и размер частиц порошка, изображение получено с помощью растровой электронной микроскопии (РЭМ). Форма частиц порошка почти сферическая с небольшими отклонениями, а размер частиц составляет 38–186 мкм. На рис. 1б можно видеть изображение внутренней, микродендритной структуры частиц порошка сплава Инконель 625, с присутствием характерной для них аустенитной γ фазы. Система прямого лазерного осаждения металлов модели Huffman HP150 (Huffman Corporation, Кловер, Южная Каролина, США) оснащена иттербиевым оптоволоконным лазером мощностью 2000 Вт непрерывного действия. Образцы в виде полых цилиндров (с внешним диаметром 13 мм, внутренним диаметром 9 мм, высотой 6–9 мм) были изготовлены для изучения микроструктуры. Для проведения испытаний на прочность при растяжении были также изготовлены образцы размерами 60 × 50 × 13 мм. Значения производственных DLMD технологических параметров представлены в табл. 2. Для эффективности контроля за процессом изготовления, были предусмотрены: (i) система автоматической подачи порошка марки Twin Sulzer; (ii) сборочная платформа, (iii) компьютеризированная система отслеживания сборки. В качестве защитного газа, в струе которого осуществлялась подача порошка, был выбран аргон. Использована двунаправленная стратегия сканирования с поворотом лазерного луча на 90° после каждого слоя осаждения.
Рис. 1.
РЭМ-изображение порошка Inconel 625, использованного в DLMD процессе: (a) морфология частиц и (б) микродендритная микроструктура.
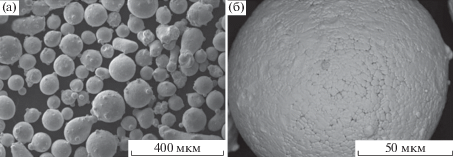
Таблица 2.
DLMD технологические параметры
Параметр | Величина |
---|---|
Мощность, Вт | 650 |
Скорость сканирования, мм мин–1 | 350 |
Скорость подачи порошка, г мин–1 | 6 |
Люфт по оси z, мм | 0.2 |
“Глубина” дефокусировки, мм | –0.8 |
Диаметр лазерного пятна, мм | 1.33 |
Для изучения влияния последующей термической обработки на микроструктуру, DLMD-образцы отжигали при 1000, 1100 и 1200°С в каждом случае в течение 1 ч, а затем охлаждали с печью. Скорость нагрева в печи составляла 8 К мин–1, а скорость охлаждения – 68 К мин–1. РЭМ-анализ структуры (микроскоп Hitachi SU-5000) проводили на горизонтальной (x–y сечение) и вертикальной (z–x сечение) гранях цилиндрических образцов (рис. 2б) после различных термообработок и в исходном состоянии. Оценку микроструктуры после испытаний на растяжение проводили вблизи поверхности разрушения.
Рис. 2.
(а) Схематическая иллюстрация использованной в работе установки для DLMD процесса; (б) плоскости A и B отмечены на DLMD образце из суперсплава Inconel 625; (в) геометрия образцов для испытаний на растяжение.
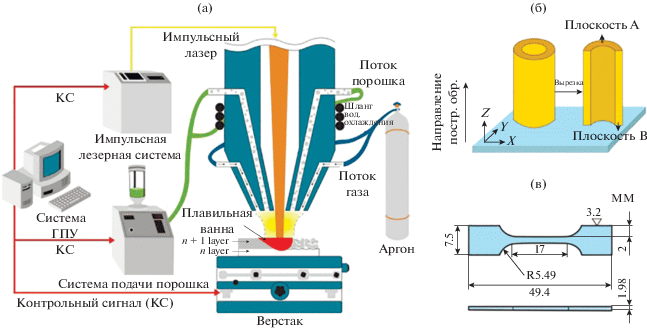
РЭМ-наблюдение выделившихся фаз проводили в двух режимах визуализации изображений: во вторичных (SE) и обратно рассеянных (BSE) электронах, а также с привлечением энерго-дисперсионного рентгеновского анализа. Образцы полировали и травили в реагенте состава 10 мл HNO3 и 30 мл HCl. Горизонтальная плоскость, перпендикулярная направлению построения образца – плоскость A (x–y сечение), и вертикальная плоскость, параллельная направлению построения – плоскость B (x–z сечение), были изучены с целью их микроструктурной аттестации.
Выделившиеся фазы были идентифицированы с привлечением ПЭМ-микроскопа F20, при ускоряющем напряжении 200 кВ. Тонкие фольги были приготовлены посредством их вырезки, механической полировки и утонения до толщины около 100–400 нм с помощью бомбардировки сфокусированным ионным (Ba+) пучком. Образцы для испытаний на растяжение были выточены из прямоугольной формы брусков так, как это показано на рис. 2в. Образцы были ориентированы параллельно плоскости B. Для обеспечения статистической достоверности, испытывали, по меньшей мере, по три образца в одинаковом состоянии. Микротвeрдость образцов по Виккерсу измеряли на твердомере модели HXD-1000TMC/LCD. Измерения производили с нагрузкой на индентор в 300 грамм (силы), а время экспозиции при замере микротвердости составляло 10 с. Прибор, использованный в этом эксперименте, представлял собой нанотвердомер производства фирмы Swiss CSM Instruments, оснащенный испытательным модулем NHT2. Максимальная использованная нагрузка на индентор составила 500 мН, время нагружения – 30 с, нагрузка не снималась 10 с, а время разгрузки составило 30 с. Испытания на растяжение проводили с помощью универсального растягивающего компрессора (RGM-4100), скорость растяжения при нагрузке составляла 0.5 мм мин–1.
РЕЗУЛЬТАТЫ И ИХ ОБСУЖДЕНИЕ
Характеристика микроструктуры
На рис. 3 и 4 представлены РЭМ-изображения структуры для всех образцов в их продольном (плоскость B), а также горизонтальном (плоскость A) сечениях. О типичных дендритах в микроструктуре осажденных образцов в исходном состоянии, без термической обработки, сообщалось в предыдущей работе авторов [20]. На рис. 3а и 4а показаны РЭМ-изображения основных фаз в образцах сразу после их синтеза. Можно видеть, что некоторые мелкие частицы блочной формы (карбиды MC) и большое количество частиц фаз Лавеса неправильной формы осаждались в междендритных областях. По сравнению с микроструктурой осажденных образцов без отжига, можно наблюдать большее изменение микроструктуры образцов, отожженных именно в условиях 1000°C в течение 1 ч, как показано на рис. 3б и 4в. В то же время немногие частицы фазы Лавеса, существовавшие в междендритных областях, растворяются, что приводит к выделению карбидов MC в междендритных областях. Хорошо видно, что морфология, свойственная дендритной структуре, исчезает при термообработке образцов при 1100°С в течение 1 ч, что показано на рис. 3в и 4в. Между тем, небольшое количество частиц фазы Лавеса в междендритных областях растворяется, а остальные частицы фаза Лавеса имеют стержневидную форму. Указанные характеристики дендритной структуры полностью исчезают после отжига при 1200°C в течение 1 ч, как показано на рис. 3г и 4г. При этом, частицы фазы Лавеса в междендритных областях частично растворились, а оставшиеся частицы фазы Лавеса имеют блочную форму и равномерно распределяются в матрице. В настоящем исследовании время отжига недостаточно велико, поэтому фаза Лавеса полностью не растворилась.
Выделившиеся фазы
ПЭМ использовали для дальнейшего анализа фаз, выделившихся в синтезированном материале. На рис. 5а–5г показаны светло-польное ПЭМ изображение микроструктуры нерегулярной фазы, результаты элементного анализа, полученные с помощью энерго-дисперсионного спектрометра (EDS), электронограмма дифракции электронов в выбранной области (SAED) и увеличенное изображение нерегулярной зоны, полученное с помощью просвечивающего электронного микроскопа высокого разрешения (ПЭМВР). Согласно рис. 5б, нерегулярная фаза в основном содержит элементы Ni, Cr, Nb, Mo. На дифракционной картине, полученной методом SAED, должно быть дифракционное пятно, расположенное вдоль оси кристаллографической зоны [20]. Это может дополнительно подтвердить, что частицы неправильной формы являются частицами фазы Лавеса. Поскольку кристаллографически плотноупакованная фаза образуется в жаропрочном суперсплаве, ее кристаллическая структура представляет собой сложную плотноупакованную гексагональную структуру. На основании изображения рис. 5г можно сделать вывод, что межплоскостное расстояние составляет 0.25 нм.
Рис. 5.
ПЭМ-светлопольное изображение нерегулярной фазы (а); результаты EDS-элементного анализа (б); SAED-электронограмма (в); ПЭМВР-изображение нерегулярной фазы (в синтезированном образце) (г).
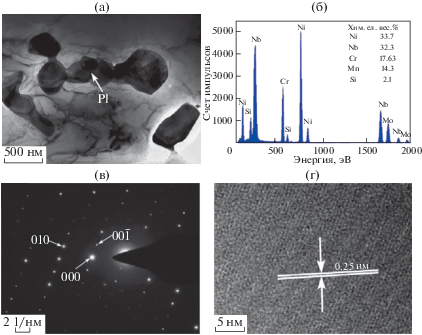
Невозможно четко проследить тип и характеристики выделения сферических частиц из-за их нанометрового размера. Следовательно, сферические частицы непременно надо наблюдать с помощью ПЭМ. На рис. 6 представлены светло-польные изображения наноразмерных частиц с соответствующими SAED-электронограммами. Сферические частицы, согласно SAED-электронограммам имеют кубическую кристаллическую структуру, характерную для карбидов, тогда как фазы Лавеса имеют гексагональную плотно упакованную решетку. Это связано с сильной склонностью элементов Nb, Mo и Si к сегрегации. Основной реакцией на заключительной стадии затвердевания должно быть образование фазы Лавеса и карбидов MC. Согласно равновесной фазовой Ni–Nb–C-диаграмме, когда концентрации Nb и C в ванне расплава достаточно высоки, карбиды MC выделяются в результате эвтектической реакции (L → γ + MC). Из-за высокой скорости охлаждения в DLMD-процессе атомы растворенного вещества легко захватываются в дендритной межкристаллической области. Таким образом, можно сделать вывод, что более высокое содержание Nb может способствовать образованию карбидов MC в продукте эвтектической реакции [21]. После идентификации дифракционных рефлексов и по результатам EDS-анализа (рис. 7) можно утверждать, что в структуре присутствовали два типа карбидов MC: эллипсоидной формы – частицы NbC (рис. 6а, 6б), и блочной формы – частицы Nb(Ti)C (рис. 6в). Мелкодисперсные частицы карбида MC выделяются в дендритах или на границах зерен. При этом размер зёрен был около 200–700 нм. Размер и концентрация этих фаз в значительной степени зависят от параметров термической обработки, таких как температура, время, скорость охлаждения и химический состав сплава [22, 23]. В настоящей работе небольшой размер карбида в основном связан с чрезвычайно низким содержанием углерода и высокой скоростью охлаждения, эти скорости охлаждения препятствуют росту карбида.
Рис. 6.
Светлопольные изображения и соответствующие SAED-электронограммы для (а, б) частиц карбида MC эллипсоидальной формы и (в) блочных частиц MC.
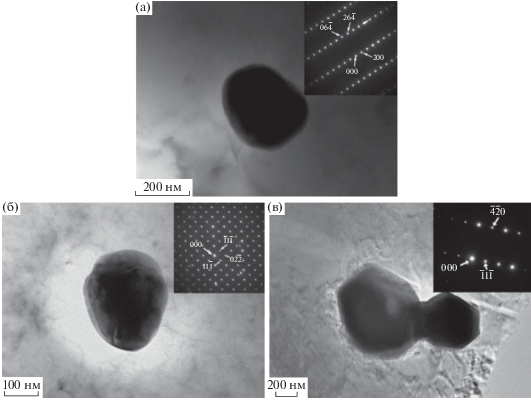
Присутствие дисперсных МС-частиц является причиной увеличения прочности матрицы сплава. Это происходит потому, что частицы MC, как частицы второй фазы, сохраняют хорошую когерентную связь с матрицей, что обеспечивает подавление проскальзывания границ зерен. Результаты EDS-анализа (рис. 7) свидетельствуют, что содержание Ti в карбидах MC больше в сравнении с содержанием атомов Nb. Это можно объяснить тем, что способность к фазообразованию выше между атомами Ti и C по сравнению с элементами Nb и C.
На рис. 8 и в табл. 3 представлены светлопольные ПЭМ-изображения и результаты EDS-анализа для основных выделившихся фаз, зафиксированных в образцах после их термообработки. Анализ показал, что выделившиеся фазы богаты элементами Nb и Mo. После расшифровки соответствующих SAED-электронограмм эти фазы могут быть идентифицированы как фазы Лавеса. По мере увеличения температуры для фаз Лавеса характерна тенденция к растворению в матрице. При этом ранее наблюдали, что форма частиц изменяется с неправильной (нерегулярной) на форму, характерную для равноосных и стержневидных дисперсных частиц.
Рис. 8.
Светлопольные ПЭМ-изображения структуры, с соответствующими SAED-электронограммами, для образцов, отожженных при разных температурах: (a) 1000; (б) 1100; (в) 1200°С.
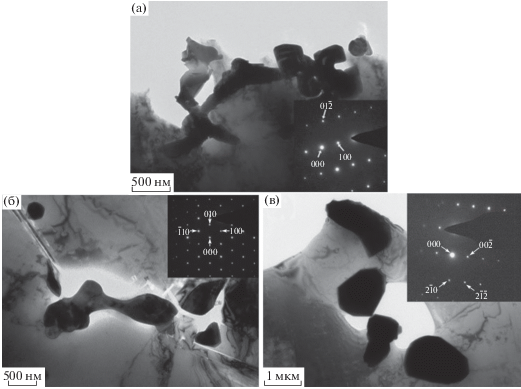
Таблица 3.
EDS-анализ выделившихся фаз (ат. %) в образцах, отожженных при разных температурах
Параметры отжига | Ni | Cr | Nb | Mo |
---|---|---|---|---|
1000°C/1 ч | 0.397 | 0.228 | 0.164 | 0.131 |
1100°C/1 ч | 0.435 | 0.236 | 0.189 | 0.140 |
1200°C/1 ч | 0.420 | 0.220 | 0.209 | 0.151 |
На рис. 9 показаны кривые наноиндентирования DLMD-образцов суперсплава Инконель 625 после различных термических обработок. Все кривые наноиндентирования показывают сходную тенденцию. На стадии нагружения, при одной и той же нагрузке, смещение индентора относительно невелико для образцов, не прошедших термообработку, а величина смещения составляет около 2500 нм. Нет большой разницы в виде кривых наноиндентирования для образцов после различных термообработок. А самая большая глубина перемещения индентора составляет около 2640 нм. Большее сопротивление материала непрерывному деформированию соответствует меньшему значению глубины перемещения индентора, и наоборот. Микроструктура синтезированного образца представляет собой мелкодисперсную дендритную структуру. При отжиге происходит определенная рекристаллизация, и, таким образом, сопротивление материалов непрерывному деформированию снижается.
Рис. 9.
Кривые наноиндентирования DLMD образцов суперсплава Инконель 625 после различной термической обработки.
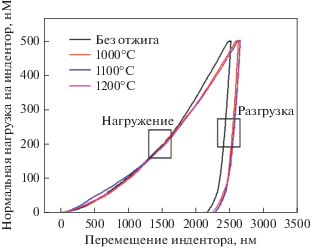
На этапе разгрузки упругая деформация способна к восстановлению, при этом пластическая сохраняется. Глубина остаточного отпечатка в материале отражает степень пластической деформации материала после разгрузки. Из рис. 9 видно, что пластическая деформация для отожженных образцов больше, в то время как у неотожжeнного образца она сравнительно меньше. Твердость неотожжeнного образца выше по сравнению с образцами, подвергнутыми отжигу. Из приведенных выше результатов можно сделать вывод, что пластичность может быть в некоторой степени повышена после высокотемпературной термообработки. Во время высокотемпературной термической обработки мелкая дендритная структура исчезает и превращается в рекристаллизованные зерна. В то же время хрупкая фаза Лавеса в матрице будет в определенной степени растворена, что может повысить пластичность материала.
Тенденция средней нанотвердости почти такая же, как и микротвердости, показанной в предыдущей работе [20]. Нанотвердость синтезированных образцов выше, чем нанотвердость образцов, подвергнутых отжигу. Влияние термической обработки на нанотвердость незначительно (как показано в табл. 4). При различных температурах отжига модуль упругости образцов практически не изменяется и составляет около 270 ГПа. Модуль упругости – это характеристика межатомной связующей способности, которая относительно нечувствительна к микроструктуре материалов [24]. Таким образом, величина модуля упругости показывает небольшие численные колебания до и после отжигов даже при различных температурах.
Механические свойства
В результате анализа микроструктуры сплава после отжига было установлено, что микроструктура и характер выделений в определенной степени изменились. И изменения в микроструктуре оказали влияние на механические свойства сплава. Испытание на растяжение является очень распространенным методом оценки прочности материала. Предел упругости, относительное удлинение, модуль упругости, предел прочности при растяжении, предел текучести и т.д. могут быть определены из результатов испытаний на растяжение. Естественная поверхность двух частей образца после разрыва при растяжении называется поверхностью разрушения, причем разрыв обычно происходит в месте расположения самой слабой стороны металлических образцов. Морфология и микроструктура места разрыва фиксируют весь процесс разрушения.
На рис. 10 показаны изображения поверхности разрушения жаропрочного сплава Инконель 625 при малом увеличении после различных температур отжига. Видно, что поверхности излома образцов во всех четырех состояниях серо-черные, без металлического блеска, изломы не плоские, и зоны хрупкого разрушения не обнаружено. Таким образом, разрушение является вязким. Кроме того, некоторые дефекты можно легко увидеть на изломах образцов, представленных на рис. 10а, 10б.
Рис. 10.
Морфология поверхности разрушения при растяжении образцов в исходном синтезированном состоянии (а); после отжига при 1000 (б); 1100 (в); 1200°С (г).
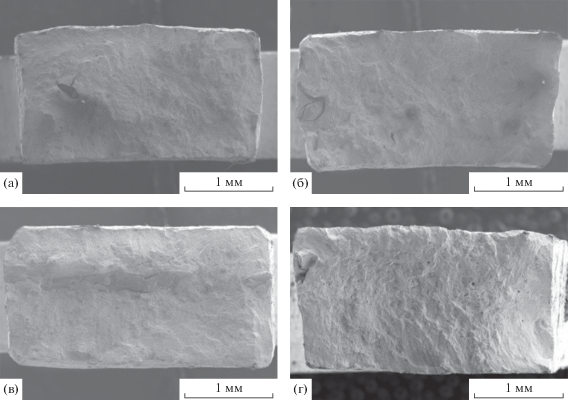
Кривые напряжение–деформация показаны на рис. 11, а свойства сплава при растяжении приведены в табл. 5. На начальном этапе напряжение линейно зависит от деформации. По мере продолжения процесса растяжения напряжение медленно увеличивается с увеличением деформации, что приводит к пластической деформации. Результаты показывают, что образцы, подвергнутые отжигу, демонстрируют более высокие прочность при растяжении и относительное удлинение по сравнению с исходным синтезированным образцом, в то время как предел текучести несколько снижается. После отжига при 1000°C в течение 1 ч прочность образца при растяжении увеличилась на 12.7%, относительное удлинение увеличилось на 116%, а предел текучести снизился на 11.1%, что свидетельствует о большем упрочняющем эффекте. В образце, отожженном при 1100°С в течение 1 ч, величина относительного удлинения была максимальной, а именно, 31.2%, но величина предела текучести была наименьшей.
Рис. 11.
Кривые напряжение–деформация DLMD образцов суперсплава Инконель 625 после различной термической обработки.
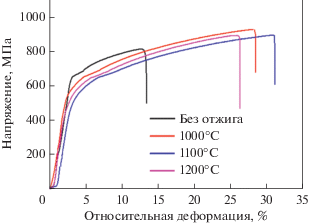
Поверхности разрушения образцов, отожженных при различных температурах, показаны на рис. 12. Можно заметить, что поверхность излома исходного синтезированного образца имеет в основном ямочную морфологию в направлении перпендикулярном к расположению дендритов, демонстрируя типичный характер транскристаллитного разрушения. При большом увеличении видно, что в ямках локализовано много частиц, как показано на рис. 12б. По результатам EDS-анализа эти частицы были идентифицированы в основном как частицы фазы Лавеса; небольшое количество частиц – карбиды MC. Морфология поверхностей изломов образцов после отжига показана на рис. 12в–12з. Во всех случаях мы имели дело с ямочной морфологией поверхностей разрушения. Поэтому разрушение синтезированных образцов до и после высокотемпературного отжига носило вязкий характер. Однако, по сравнению с исходным синтезированным образцом, ямки на поверхностях изломов образцов после отжига распределены более однородно; они мельче и равноосные, что является результатом превосходной пластичности материала.
Рис. 12.
Морфология поверхностей излома разрывных образцов: в исходном синтезированном состоянии (a–б); и после отжига при температуре (в–г) 1000; (д–е) 1100; (ж–з) 1200°С.
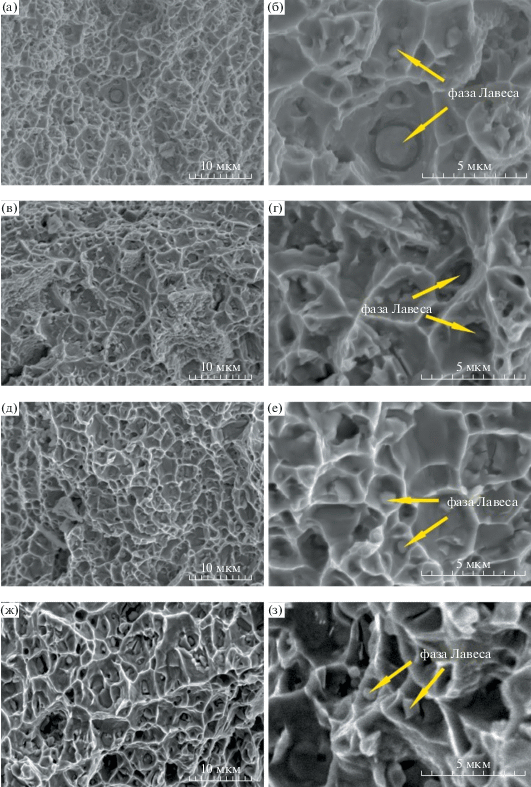
На фоне упомянутых ямок или “пустот” на поверхностях изломов присутствуют мелкодисперсных частиц фазы Лавеса и МС карбидов, что можно видеть на рис. 12б, 12г, 12е, 12з. В области границы раздела фаз, являющейся “слабым местом”, во время испытания на растяжение происходит распространение трещин из-за декогезии и разрушения частиц. Эти трещины могут эволюционировать в пустоты сферической или эллипсоидальной формы и соединяться друг с другом. Во время распространения трещины на ее кончике возникает поле гидростатических напряжений. Это напряжение может привести к образованию и росту микропор в металле [25]. Когда размер микропор достигает определeнной величины, две соседние микропоры становятся очень нестабильными и быстро растут, затем сливаются друг с другом в одну большего размера. В это время нагрузка очень велика, и материал может растрескиваться. Исходя из приведенных выше результатов, процесс растяжения можно разделить на три этапа: образование микропор → их рост → их слияние друг с другом. И можно сделать вывод, что существование мелкодисперсных MC карбидов и фазы Лавеса обеспечивают благоприятные условия для образования микропор. Таким образом, основная выделившаяся фаза – фаза Лавеса, является одной из важных причин, вызывающих разрушение образца.
Общепризнано, что фаза Лавеса вредна для механических свойств материалов. Фаза Лавеса в Инконеле 625 может снизить его пластичность, вязкость разрушения, усталостную прочность и сопротивление разрыву при ползучести. Как вредная фаза, фаза Лавеса не только “захватывает” некоторые элементы из матрицы, особенно Nb, в результате чего выделяется меньше упрочняющей фазы, но она выступает и как хрупкая фаза, которая обеспечивает благоприятные условия для образования и распространения трещин. Однако фаза Лавеса частично растворилась при высокотемпературном отжиге DLMD-образцов суперсплава Инконель 625. Форма ее частиц изменилась от начальной относительно большой неправильной до блочной формы мелкодисперсных частиц. Измельчение частиц фазы Лавеса и изменение их формы являются основными причинами, которые приводят к повышению пластичности материала после отжига. Хотя разрушение произошло в месте локализации дендрита, после термической обработки на поверхности излома можно обнаружить большую однородность и более глубокие ямки.
ВЫВОДЫ
1) Микроструктура синтезированого суперсплава Инконель 625 содержит грубые неправильной формы частицы фазы Лавеса и наноразмерные выделения карбидов MC в междендритной области. Фаза Лавеса богата элементами с высокой температурой плавления – Nb и Mo. Выделения карбидов имеют два типа: эллипсоидальной формы – NbC и блочной формы – карбид Nb(Ti)C, размеры которых варьируются от 200 до 700 нм. При повышении температуры отжига с 1000 до 1200°C выделения фазы Лавеса частично растворяются, и их морфология соответственно изменится. Выделения изменяются от относительно грубых неправильной формы частиц до мелких частиц в виде стержней или блоков. Вторая фаза становится более мелкой и более равномерно распределена в матрице, что обусловливает повышение пластичности сплава.
2) После высокотемпературного отжига рекристаллизация твердого γ-Ni твердого раствора значительно суживает разориентацию зерен. Нанотвердость исходного синтезированного и отожженных при 1000, 1100 и 1200°C образцов составляла 3769, 3375, 3380 и 3329 МПа соответственно. Модуль упругости всех образцов составлял около 270 ГПа.
3) По сравнению с не отожжeнным образцом, более высокая прочность на растяжение и скорость удлинения могут быть получены при относительно более низком пределе текучести в отожженных образцах. В результате отжига при 1000°C в течение 1 ч удалось достигнуть максимальной величины прочности на растяжение, составившей 915 МПа, тогда как в исходном синтезированном образце эта величина была лишь 812 МПа. Относительное удлинение в последнем и в первом случае составило 13.1 и 28.3% соответственно. Величина предела текучести для отожжeнного при 1000°С, 1 ч образца составила 564 против 635 МПа в не отожженном образце. Все образцы после отжига продемонстрировали типичный механизм образования ямок при испытаниях на растяжение. Причем с повышением температуры отжига распределение ямок по поверхности излома становилось более равномерным.
Таблица 5.
Свойства сплава при растяжении после различных условий термообработки
Обработка | Прочность, МПа | Предел текучести, МПа | Удлинение, % |
---|---|---|---|
Синтезированный | 812 | 635 | 13.1 |
1000°С/1 ч | 915 | 564 | 28.3 |
1100°С/1 ч | 853 | 512 | 31.2 |
1200°С/1 ч | 854 | 552 | 26.1 |
Исследование финансировалось Главной лабораторией передовых промышленных технологий провинции Цзянсу Хуайиньского Технологического института [грант № HGAMTL-1701]; и проектом № 333 для молодых талантливых учeных провинции Цзянсу [грант № BRA2017098].
Авторы заявляют об отсутствии конфликта интересов.
Список литературы
Huebner J., Kata D., Kusiński J., Rutkowski P., Lis J. Microstructure of laser cladded carbide reinforced Inconel 625 alloy for turbine blade application // Ceram. Int. 2017. V. 43. P. 8677–8684.
Zhang Y.C., Jiang W.C., Tu S.T., Zhang X.C., Ye Y.J. and Wang R.Z. Experimental investigation and numerical prediction on creep crack growth behavior of the solution treated Inconel 625 superalloy // Eng. Fract. Mech. 2018. V. 199. P. 327–342.
Ren B., Chen C.J., Zhang M. Effect of heat treatment on the microstructure of Co–Cr–W alloy fabricated by laser additive manufacturing // Opt. Eng. 2018. V. 57. P. 041409.
Ren B., Zhang M., Chen C.J., Wang X.N., Zou T., Hu Z.R. Effect of Heat Treatment on Microstructure and Mechanical Properties of Satellite 12 Fabricated by Laser Additive Manufacturing // J. Mater. Eng. Perform. 2017. V. 26. P. 5405–5413.
Xiao H.N., Chen C.J., Zhang M. Microstructure and Mechanical Properties of H13 Steel/High-Speed Steel Composites Prepared by Laser Metal Deposition // J. Mater. Eng. Perform. 2020. V. 29. P. 66–77.
Sateesh N.H., Kumar G.C.M., Prasad K., Srinivasa C.K., Vinod A.R. Microstructure and mechanical characterization of laser sintered Inconel 625 superalloy // Procedia Mater. Sci. 2014. V. 5. P. 772–779.
Carter L.N., Wang X., Read N., Khan R., Aristizabal M., Essa K., Attallah M.M. Process optimisation of selective laser melting using energy density model for nickel based superalloys // Mater. Sci. Technol. 2016. V. 32. P. 657–661.
Aleksandrova A.A., Bazaleeva K.O., Balakirev E.V., Brykov A.A., Grigor’yants A.G. Direct Laser Growth of Inconel 625/TiC Composite: Effect of Structural State of Initial Powder // Phys. Met. Metallogr. 2019. V. 120. P. 459–464.
Zhan D., Niu W., Cao X., Liu Z. Effect of standard heat treatment on the microstructure and mechanical properties of selective laser melting manufactured Inconel 718 superalloy // Mater. Sci. Eng. A. 2015. V. 644. P. 32–40.
Wang X., Carter L.N., Pang B., Attallah M.M., Loretto M.H. Microstructure and yield strength of SLM-fabricated CM247LC Ni-Superalloy // Acta Mater. 2017. V. 128. P. 87–95.
Attallah M.M., Jennings R., Wang X., Carter L.N. Additive manufacturing of Ni-based superalloys: the outstanding issues // MRS Bull. 2016. V. 41. P. 758–764.
Staritsyn M.V., Kuznetsov P.A., Petrov S.N., Mikhailov M.S. Composite Structure as a Strengthening Factor of Stainless Austenitic Chromium–Nickel Additive Steel // Phys. Met. Metallogr. 2020. V. 121. P. 337–343.
Kreitcberg A., Brailovski V., Turenne S. Effect of heat treatment and hot isostatic pressing on the microstructure and mechanical properties of Inconel 625 alloy processed by laser powder bed fusion// Mater. Sci. Eng. A. 2017. V. 689. P. 1–10.
Kreitcberg A., Brailovski V., Turenne S. Elevated temperature mechanical behavior of IN625 alloy processed by laser powder-bed fusion // Mater. Sci. Eng. A. 2017. V. 700. P. 540–553.
Mittra J., Banerjee S., Tewari R. and Dey G.K. Fracture behavior of Alloy 625 with different precipitate microstructures,” Mater. Sci. Eng. A. 2013. V. 574. P. 86–93.
Marchese G., Colera X.G., Calignano F., Lorusso M., Biamino S., Minetola P., Manfredi D. Characterization and Comparison of Inconel 625 Processed by Selective Laser Melting and Laser Metal Deposition// Adv. Eng. Mater. 2017. V. 19. P. 1–9.
Marchese G., Bassini E., Calandri M., Ambrosio E.P., Calignano F., Lorusso M., Manfredi D., Pavese M., Biamino S., Fino P. Microstructural investigation of as-fabricated and heat-treated Inconel 625 and Inconel 718 fabricated by direct metal laser sintering: contribution of Politecnico di Torino and Istituto Italiano di Tecnologia (IIT) di Torino // Met. Powder Rep. 2016. V. 71. P. 273–278.
Dinda G.P., Dasgupta A.K., Mazumder J. Laser aided direct metal deposition of Inconel 625 superalloy: Microstructural evolution and thermal stability // Mater. Sci. Eng. A. 2009. V. 509. P. 98–104.
Rombouts M., Maes G., Mertens M., Hendrix W. Laser metal deposition of Inconel 625: Microstructure and mechanical properties // J. Laser Appl. 2012. V. 24. P. 052007.
Qin L.L., Chen C.J., Zhang M., Yan K., Cheng G.P., Jing H.M., Wang X.N. The microstructure and mechanical properties of deposited-IN625 by laser additive manufacturing// Rapid Prototyping J. 2017. V. 23. P. 1119–1129.
Chen L., Sun Y.Z., Li L., Ren X.D. Effect of heat treatment on the microstructure and high temperature oxidation behavior of TiC/Inconel 625 nanocomposites fabricated by selective laser melting// Corrosion Sci. 2020. V. 169. P. 108606.
Marchese G., Parizia S., Rashidi M., Saboori A., Manfredi D., Ugues D., Lombardi M., Hryha E., Biamino S. The role of texturing and microstructure evolution on the tensile behavior of heat-treated Inconel 625 produced via laser powder bed fusion // Mater. Sci. Eng. A. 2020. V. 769. P. 138500.
Rogachev A.S. Structure, Stability, and Properties of High-Entropy Alloys // Phys. Met. Metallogr. 2020. V. 121. P. 733–764.
Oliver W.C., Pharr G.M. An improved technique for determining hardness and elastic modulus using load and displacement sensing indentation experiments // J. Mater. Res. 1992. V. 7. P. 1564–1583.
Anderson T.L. Fracture Mechanics: Fundamentals and Applications. Fourth Edition. CRC Press, USA, 2017.
Дополнительные материалы отсутствуют.
Инструменты
Физика металлов и металловедение