Физика металлов и металловедение, 2021, T. 122, № 9, стр. 948-956
Влияние термообработки на структуру и механические свойства нанокристаллического сплава Cu–14Al–3Ni, полученного кручением под высоким давлением
А. Э. Свирид a, *, В. Г. Пушин a, b, Н. Н. Куранова a, b, В. В. Макаров a, А. Н. Уксусников a
a Институт физики металлов УрО РАН
620990 Екатеринбург, ул. С. Ковалевской, 18, Россия
b Уральский федеральный университет им. первого Президента РФ Б.Н. Ельцина
620002 Екатеринбург, ул. Мира, 19, Россия
* E-mail: svirid2491@rambler.ru
Поступила в редакцию 24.03.2021
После доработки 14.05.2021
Принята к публикации 18.05.2021
Аннотация
Изучено влияние термообработки на микроструктуру, фазовый состав, механические свойства и микротвердость сплава с эффектом памяти формы Сu–14 мас. % Al–3 мас. % Ni, полученного в нанокристаллическом состоянии в результате мегапластической деформации кручением под высоким давлением (КВД). Используя методы электронной микроскопии и рентгеновского анализа в комплексе с измерениями электросопротивления, получены данные об особенностях термоупругих мартенситных превращений и распада в КВД-сплаве при термических воздействиях.
ВВЕДЕНИЕ
Использование температурных воздействий, механических нагрузок и магнитных полей для обеспечения термоупругих мартенситных превращений (ТМП) в различных сплавах позволяет реализовать целый ряд исключительно важных физических явлений. К ним относятся одно- или многократно обратимые эффект памяти формы (ЭПФ), гигантские сверхупругость, эласто- и магнитокалорические и демпфирующий эффекты, которые выделяют так называемые интеллектуальные или smart-материалы в особый отдельный класс практически важных конструкционных полифункциональных материалов [1–5]. При современном развитии техники и технологий необходимы такие smart-материалы, которые могут быть использованы в разных температурных, силовых и иных практически важных условиях, и в том числе в крупногабаритном состоянии. Вместе с тем пока существенным их недостатком, за исключением бинарных сплавов никелида титана, являются низкая пластичность и хрупкость, исключающие реализацию в поликристаллическом состоянии данных уникальных эффектов. Поэтому все более важными, но практически не решенными остаются задачи оптимального легирования и разработки способов и технологий пластификации различных поликристаллических материалов с ЭПФ с целью их разнообразного индустриального применения.
Медные β-сплавы, такие как Cu–Al–Ni, Cu–Zn–Al, Cu–Zn–Sn, отличаются гораздо меньшей стоимостью, лучшими тепло- и электро-проводностью, технологичностью при обработке по сравнению, например, со сплавами никелида титана [3–6]. Тем более, что они в монокристаллическом состоянии демонстрируют превосходные характеристики ЭПФ. В обычном же крупнозернистом (КЗ) поликристаллическом состоянии данные сплавы имеют чрезвычайно низкие пластичность, трещиностойкость, усталостную долговечность [1, 3, 6]. Это не позволяет реализовать ЭПФ, присущие их монокристаллам.
Специфической причиной интеркристаллитного разрушения является высокая анизотропия упругих модулей A = C44/C ' (12–13 единиц) медных сплавов, метастабильных по отношению к ТМП [7], которая для упругоизотропных низкомодульных и пластичных сплавов никелида титана составляет 1–2 [4, 5]. Большая упругая анизотропия при ТМП приводит на стыках мартенситных пакетов и особенно на границах зерен к значительным упругим напряжениям, а их величина и локализация на границах тем больше, чем крупнее зерна сплавов. Усугубляют снижение пластичности химическая ликвация и гетерогенный распад в данных КЗ-сплавах, прежде всего при температурах ниже границы эвтектоидного распада (Tэр), близкой 840 К [3]. Очевидно, что интеркристаллитная хрупкость является одной из ключевых причин, препятствующих практическому применению сплавов с ЭПФ. Ослабление роли указанных факторов в охрупчивании медных сплавов с ЭПФ возможно за счет радикального уменьшения размера зерен при мегапластической деформации (МПД) и, соответственно, увеличения протяженности их границ [8–14]. Вместе с тем, различные иные методы измельчения зеренной структуры данных сплавов [15–21] с использованием легирующих добавок [17, 21], термообработки [15–18], быстрой закалки [6], порошковой металлургии и ряда других [19, 20], как правило, оказывались безуспешными.
Целью данной работы было исследование влияния термообработки на размеры зерен, структурно-фазовые превращения, механические свойства и твердость сплава с ЭПФ Cu–14Al–3Ni, подвергнутого МПД.
МАТЕРИАЛ И МЕТОДЫ ИССЛЕДОВАНИЯ
Сплав номинального состава Сu–14 мас. % Al–3 мас. % Ni (далее Cu–14Al–3Ni) был выплавлен из высокочистых компонентов Cu, Al, Ni (чистотой 99.99%), подвергнут горячей ковке при 1173–1273 К в пруток сечением 20 × 20 мм и закалке в воде от 1223 К, 10 мин. Ряд образцов подвергался также повторной закалке в воде от 1273 К после нагрева в течение 30 мин. Для измельчения зеренной структуры сплава был применен метод МПД кручением под высоким давлением 6 ГПа при комнатной температуре (КТ) на 1, 5 и 10 оборотов в плоских бойках c “канавкой” (цилиндрическим углублением в нижнем бойке), а также при температуре 423 К на 10 оборотов. Образцы для КВД были изготовлены в форме дисков диаметром 20 мм, толщиной 1.2 мм. Величина их истинной деформации (е) после 10 оборотов на половине радиуса образца составила 6.0. Изохронные изотермические отжиги КВД-образцов проводили в диапазоне температур 373–873 К (с шагом 100 К) в течение 30 мин. Кроме того, проводили кратковременный отжиг КВД-образца в течение 10 с при температуре 1073 К. Температуры ТМП определяли при циклических температурных измерениях электросопротивления ρ(T) со скоростью нагрева–охлаждения, близкой 5 К/мин. Структуру и фазовый состав сплава после деформации при КТ и последующих отжигов изучали методами рентгеновской дифрактометрии (РД), просвечивающей и растровой электронной микроскопии (ПЭМ и РЭМ, включая дифракцию обратнорассеянных электронов, ДОЭ). РД проводили в монохроматизированном медном излучении Kα. Использовали оборудование ЦКП ИФМ УрО РАН: ПЭМ Tecnai G2 30 (при ускоряющем напряжении 300 кВ) и РЭМ Quanta 200, оснащенный системой Pegasus (при ускоряющем напряжении 30 кВ). Тонкие фольги ∅3 мм изготовили на установке Fischione 1010 IonMill из дисков, вырезанных на половине радиуса образца и подвергнутых шлифованию на приборе Metaserv 250. Измерения микротвердости по Виккерсу (HV) проводили на приборе Micromet 5101 с пирамидальным алмазным индентором при нагрузке 1Н. Испытания на растяжение плоских образцов длиной 10.0, толщиной 0.25, шириной 1.0 и длиной 4.5 мм рабочей части, расположенной поперек на половине радиуса исходного диска, выполняли в УГАТУ (г. Уфа). Поверхность образцов перед испытанием полировали алмазной пастой.
РЕЗУЛЬТАТЫ ИССЛЕДОВАНИЙ
В проведенных ранее исследованиях было установлено, что горячая деформация ковкой позволяет измельчить зерна до 0.5–1 мм. Однако последующее охлаждение прутков данного сплава на воздухе приводит к распаду по схеме β1 → β1 + γ2 (при температурах выше Tэр, близкой 840 К) и эвтектоидному распаду β1 → α + γ2 (при температурах ниже Tэр), где α-фаза с ГЦК-решеткой, а γ2-фаза c кубической решеткой D83 на основе интерметаллида Cu9Al4 [9–11]. Закалка сплавов после горячей ковки предотвращает эвтектоидный распад. Вместе с тем, β-аустенит выше эвтектоидной температуры и точки Ms начала ТМП последовательно испытывает два перехода “беспорядок–порядок” (β → β2(B2) → β1(D03)), что обеспечивает наследование дальнего атомного порядка от исходной атомно-упорядоченной аустенитной фазы мартенситом и, как следствие, его термоупругость [1–6].
По данным РД в закаленном β1-сплаве при температурах ниже Ms, близкой 250 К (рис. 1а, табл. 1) появляются две мартенситные фазы: β1 (18R) (с параметрами длиннопериодной моноклинной решетки, близкими a = 0.4450 нм, b = = 0.5227 нм, c = 3.8050 нм, β = 91.0°) и $\gamma _{1}^{'}$ (2H) (c параметрами орторомбической решетки, близкими a = 0.4390 нм, b = 0.5190 нм, c = 0.4330 нм) Установлено, что КВД на 10 оборотов при КТ вызывает деформационное ТМП с образованием смеси трех мартенситных фаз α-, $\beta _{1}^{'}$- и $\gamma _{1}^{'}$- (рис. 1б). Обнаруживаемые при этом брэгговские отражения существенно уширены (с полушириной до 2 град), и совпадают с наиболее сильными линиями данных мартенситных фаз. Приведенные на рис. 2 температурные зависимости ρ(Т) демонстрируют при измерениях в различных термоциклах “охлаждение–нагрев” (кривые 1, 2) или “нагрев–охлаждение” (3) изменение формы петель гистерезиса ТМП и их температур, определенных методом двух касательных (табл. 1), в согласии с РД-данными фазового анализа (рис. 1).
Рис. 1.
Рентгеновские дифрактограммы сплава Cu–14Al–3Ni после закалки (а), КВД на 10 оборотов (б), КВД и отжига при 373 (в) или при 573 К (г). Температуры измерений: 200 К (а), КТ (б–г).
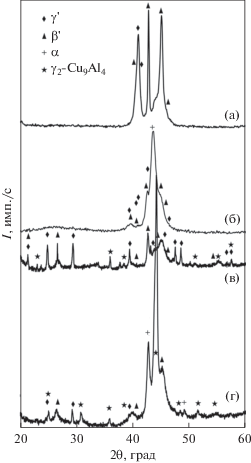
Таблица 1.
Критические температуры начала (Ms, As) и конца (Мf, Af) ТМП сплава Cu–14Al–3Ni после различных обработок (кривые 1, 2, 3 рис. 2)
Обработка | Ms, К | Мf, K | As, K | Af, K | ΔT*, K |
---|---|---|---|---|---|
Зак. 1223 К (1) | 250 | 230 | 265 | 285 | 35 |
КВД 10 (2) | 320 | 300 | 400 | 440 | 110 |
КВД 10 (3) | – | – | 380 | 470 | – |
Рис. 2.
Температурные зависимости ρ(T) сплава Cu–14Al–3Ni после закалки от 1223 К в воде в цикле измерений 300 К → 90 К → 300 К (кривая 1); после КВД в циклах измерений 300 К → ТЖ/а → 470 К → 300 К (2) и 300 К → 573 К → 300 К (3).
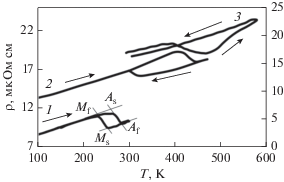
Важно отметить, что гистерезис ТМП (ΔT) в КВД-сплаве возрастает более чем втрое при заметном повышении всех критических температур.
Из анализа рентгенограмм КВД-сплава, подвергнутого отжигу при 373 и 473 К, следует, что в сплаве сохраняются мартенситные фазы $\beta _{1}^{'}$- и $\gamma _{1}^{'}$- и появляются отражения от γ2-фазы старения (см. рис. 1в). Отжиг при более высоких, чем Af, температурах 573–773 К приводит к эвтектоидному распаду уже β1-аустенита на фазы (α + γ2) (см. рис. 1г). И наконец, отжиг при 873 К вызывает распад аустенита с выделением γ2-фазы. Последующее после отжига охлаждение КВД-сплава до КТ сопровождается ТМП в остаточной β1-матрице (рис. 1б, 1г).
ПЭМ-исследования показали, что в результате КВД с увеличением числа оборотов от 1 до 10 (и, соответственно, величины деформации) в мартенситном сплаве Cu–14Al–3Ni формировалась все более однородная нанозеренная структура (рис. 3), характеризуемая кольцевым распределением рефлексов на электронограммах (см. рис. 3).
Рис. 3.
Светло- (а) и темнопольное (б) ПЭМ-изображения микроструктуры сплава Cu–14Al–3Ni после повторной закалки от 1273 К и КВД на 10 оборотов и соответствующая микродифракция электронов со схемой расшифровки (в, г).
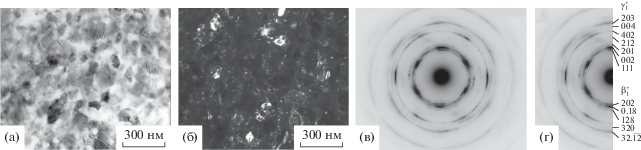
Из количественного анализа светло- и темнопольных ПЭМ-изображений микроструктуры сплава после КВД на 10 оборотов следует, что размеры наблюдаемых наиболее часто встречающихся произвольно ориентированных структурных фрагментов варьируются в пределах от 10 до 80 нм и составляют в среднем 30 нм. Видно, что в более крупных из них присутствуют пластинчатые нанодвойники. Расшифровка электронограмм показала, что полученная в сплаве нанокристаллическая структура преимущественно содержит $\beta _{1}^{'}$- и $\gamma _{1}^{'}$-мартенситные фазы. Кольцевое распределение рефлексов указывает на наличие нанофаз, образующих разориентированную ультрамелкозернистую (УМЗ)-структуру.
Изучение влияния температуры отжига на микроструктуру КВД-сплава методом РЭМ выявило следующее. Отжиги при 373 и 473 К не привели к заметным размерно-морфологическим изменениям в мартенситной УМЗ структуре, образовавшейся в результате КВД (рис. 4а). Рост глобулярных зерен в сплаве обеспечили отжиги в диапазоне температур от 573 до 873 К (рис. 4б, 4в).
Рис. 4.
РЭМ-изображения структуры сплава Cu–14Al–3Ni после КВД на 10 оборотов и отжигов в течение 30 минут, при температурах 373 (а), 673 (б), 873 К (в); а, б – во вторичных электронах; в – ДОЭ для фаз γ2-Cu9Al4 и медной матрицы.
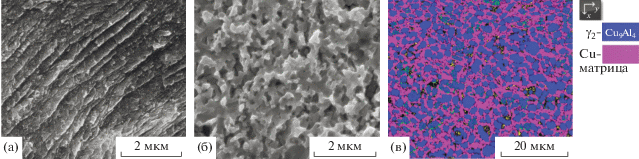
Были также выполнены исследования сплава Cu–14Al–3Ni после КВД на 10 оборотов и отжигов в состоянии β1-аустенита методами ПЭМ (рис. 5). Из светлопольных ПЭМ-изображений микроструктуры сплава после отжигов следует, что в β1-матрице формируются и начинают расти глобулярные нанокристаллиты в основном двух фаз α и γ2 в соответствии с данными расшифровки электронограмм (средний размер 〈dз〉 зерен-кристаллитов приведен в табл. 2).
Рис. 5.
Светлопольные ПЭМ-изображения УМЗ-структуры и соответствующие электронограммы сплава Cu–14Al–3Ni после КВД на 10 оборотов и изохронных отжигов (в течение 30 мин) при: 573 (а, д); 673 (б, е); 773 (в, ж); 873 К (г, з).
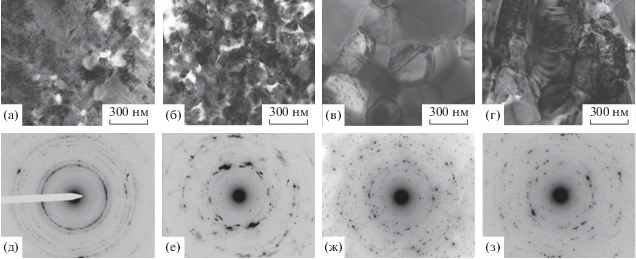
Таблица 2.
Средний размер зерен сплава Cu–14Al–3Ni, подвергнутого КВД на 10 оборотов и различным отжигам по данным ПЭМ
Обработка сплава | Средний размер зерна 〈dз〉, нм |
---|---|
КВД, n = 10 оборотов | 30 |
КВД + 373 К, 30 мин | 30 |
КВД + 473 К, 30 мин | 30 |
КВД + 573 К, 30 мин | 100 |
КВД + 673 К, 30 мин | 150 |
КВД + 773 К, 30 мин | 350 |
КВД + 873 К, 30 мин | 400 |
Очевидно, что нагрев при 573 К в ревертированном β1-аустените обеспечивает комплексную реакцию процесса рекристаллизации и эвтектоидного (α + γ2)-распада. При этом в основном меньшие зерна-кристаллиты на фоне более крупных рекристаллизованных отличает сильный деформационный контраст, и они остаются по размерам практически неизменными. В среднем 〈dз〉 близок 100 нм (см. рис. 5а). Следует отметить, что в этом случае на картинах микродифракции электронов рефлексы имели сплошное кольцевое распределение (рис. 5д). Наблюдаемые структурно-ориентационные и морфологические особенности свидетельствуют о присутствии мало- и большеугловых границ, наследуемых после КВД как ревертированным аустенитом, так и затем мартенситными фазами, присутствующими уже при КТ после ТМП в остаточной β1-фазе.
Увеличение температуры отжига до 673 К, судя по данным ПЭМ, привело к практически полной первичной рекристаллизации β1-аустенита и формированию (β1 + α + γ2)-триплекс-структуры в составе однородного УМЗ-аустенита при выросшем 〈dз〉, близком 150 нм. Зерна-кристаллиты оставались округлыми, а их границы искривленными, в структуре еще сохранялась повышенная плотность дефектов (рис. 5б). Кольцевой характер уже менее однородного распределения точечных рефлексов на картинах микродифракции КВД-сплава после отжига при 673–873 К свидетельствует о присутствии в сплаве большого количества случайных разориентировок возникших глобулярных зерен-кристаллитов (см. рис. 5е–5з). При более высокой температуре изохронного отжига 773 К имело место более интенсивное укрупнение сформированных в β1-аустените глобулей α и γ2-фаз при 〈dз〉, близком 350 нм (рис. 5в). После отжига при 873 К 〈dз〉 для фаз β1 и γ2 близок 400 нм (табл. 2, рис. 4в). В последнем случае изображения границ зерен-кристаллитов дуплекс-структуры (β1 + γ2) становятся еще более четкими, и виден контраст от двойников в мартенсите (см. рис. 5г). “Острые” точечные рефлексы на картинах микродифракции электронов свидетельствуют о значительной релаксации внутренних напряжений и межфазных искажений в УМЗ-структуре, образованной выделившимися фазами и мартенситом.
Таким образом, в результате проведенных исследований установлено, что изохронные отжиги, начиная от температур выше Af в диапазоне от 473 до 873 К, приводят к рекристаллизации β1-D03 аустенита в КВД-сплаве Cu–14Al–3Ni и формированию достаточно однородных УМЗ-структур, при этом размеры зерен возрастают в интервале от 30 до 400 нм, соответственно (табл. 2).
Во всех случаях, начиная от низкотемпературного (ниже Ms) отжига при 373–473 К, при котором КВД-сплав испытал частичный распад мартенсита с выделением дисперсных частиц γ2-фазы, ее рефлексы присутствуют на полученных рентгено- и электронограммах: после отжигов при 573–773 К в результате эвтектоидного (α + γ2)-распада аустенита, при 873 К – проэвтектоидного (β1 + γ2) распада. Если при отжиге сохранялась матричная аустенитная β1-фаза, что имеет место для выбранных режимов, при последующем охлаждении происходило ТМП.
Данные измерений HV на половине радиуса дисков КВД сплава Cu–14Al–3Ni в зависимости от температуры отжига приведены на рис. 6. После отжига при 573 К КВД-сплав Cu–14Al–3Ni имеет максимальные значения HV (вплоть до 5850 МПа) после одинарной закалки от 1223 К и 5550 МПа после повторной закалки от 1273 К. Повторная закалка обеспечила лучшую гомогенизацию твердого раствора сплава, чем одинарная, приводя к несколько меньшим значениям HV. Стоит отметить, что после КВД HV возросла на 1000 МПа по сравнению с твердостью в исходном закаленном состоянии. Тенденция роста HV КВД-сплава сохранилась и после применения отжигов.
Рис. 6.
Зависимость микротвердости HV сплава Cu–14Al–3Ni (кривая 1 – зак. от 1223 К, кривая 2 – зак. от 1273 К) от температуры отжига в течение 30 мин.
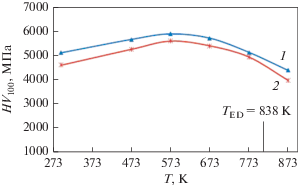
Результаты измерений механических свойств на растяжение при КТ сплава Cu–14Al–3Ni представлены в табл. 3. Испытания показали, что закаленный КЗ-сплав имел временное сопротивление (σв) 620 МПа, критическое напряжение мартенситного сдвига (σм) 160 МПа с псевдоупругой фазовой текучестью (εм) до 2% и величину относительного удлинения до разрушения (δ) 7%. При некотором разупрочнении за счет создания мелкозернистого (МЗ) состояния повторная закалка сплава привела к росту δ до 11%. В упрочненном УМЗ-сплаве, подвергнутом КВД при КТ, величина δ снизилась до 4%, а разрушение происходило хрупко без образования шейки. Площадка фазовой текучести при этом не фиксировалась в отличие от закаленного КЗ- или МЗ-сплава (где εм = = 2%). Повышение температуры КВД до 423 К (на 130 К выше КТ) привело к необычайно высокому деформационному упрочнению сплава Cu–14Al–3Ni и, вместе с тем, значительному увеличению δ, которое составило 12%. В КВД-сплаве были достигнуты наиболее высокие механические характеристики. Так, предел текучести составил 1400 МПа, а предел прочности – 1450 МПа при высоком δ до разрушения (12%). Значительные изменения в механическом поведении сплава наблюдались после КВД на 10 оборотов при варьировании режимов отжигов в диапазоне температур от 573 до 1073 К с различным временем выдержки (от 10 с до 30 мин), приводящих к созданию УМЗ-структуры (см. табл. 3).
Таблица 3.
Результаты механических испытаний на растяжение сплава Cu–14Al–3Ni после различных деформационно-термических обработок
№ | Обработка | σм, МПа | σв, МПа | εм, % | δ, % |
---|---|---|---|---|---|
1 | Зак. от 1223 К | 160 | 620 | 2 | 7 |
2 | Зак. от 1273 К | 60 | 400 | 2 | 11 |
3 | КВД 10 об., (293 К) | – | 820 | – | 4 |
4 | КВД 10 об., (423 К) | – | 1450 | 2 | 12 |
5 | КВД + 573 К, 30 мин | 120 | 450 | 2 | 6 |
6 | КВД + 773 К, 30 мин | 50 | 320 | 3 | 8 |
7 | КВД + 1073 К, 10 с | 250 | 900 | 5 | 13 |
Фрактографические исследования картины разрушения образцов после растяжения показали, что в исходном горячекованом закаленном КЗ-сплаве разрушение происходило хрупко, преимущественным сколом по границам зерен и крупных пакетов мартенситных кристаллов (рис. 7а). Наноразмерная зеренно-субзеренная структура после КВД на 10 оборотов изменила вид излома и характер разрушения образцов (рис. 7б).
Рис. 7.
РЭМ-изображения изломов горячекованного закаленного (а) и после КВД на 10 оборотов (б) сплава Cu–14Al–3Ni.
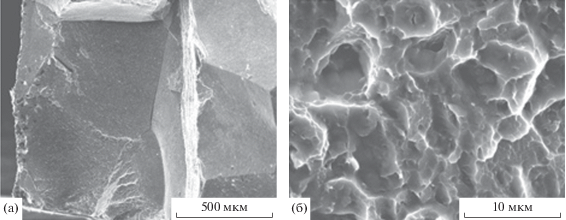
На поверхности разрушения наблюдалось множество центров локализации деформации с образованием мелких плоских ямок и, соответственно, невысоких гребней отрыва. Это характерно для вязкого внутризеренного механизма разрушения с низкой энергией. Но средний размер ямок составил 2–5 мкм, что на два порядка превышало размер элементов УМЗ-структуры КВД-сплава. Данное обстоятельство свидетельствует об особом межкристаллитном механизме его разрушения, происходящего в основном по большеугловым границам УМЗ-структуры. Однако на два порядка меньше стал размер ячеистых фрагментов (ямок) отрыва при вязко-хрупком разрушении по сравнению с размером зерен и областей хрупкого скола в исходном КЗ-сплаве и это, очевидно, в конечном счете определило повышенную пластичность УМЗ-сплава.
ОБСУЖДЕНИЕ РЕЗУЛЬТАТОВ
Как уже ранее было обнаружено [8–14], МПД эвтектоидных сплавов Cu–Al–Ni с ЭПФ является при определенных условиях эффективным методом радикального измельчения их зеренной структуры и, как следствие, пластификации. В настоящей работе показано, что КВД на большие пластические деформации обеспечивает механоиндуцированное ТМП в метастабильном аустенитном сплаве Cu–14Al–3Ni при одновременно происходящем формировании однородной наноразмерной УМЗ-структуры. Она характеризуется высокой твердостью, прочностью и большей стабильностью мартенситных фаз по отношению к обратному ТМП при нагреве. Критические температуры ТМП сплава, подвергнутого КДВ на 10 оборотов, повысились: Ms и Mf на 70 К, а As и Af на 150 К. Можно сделать вывод, что рост температур обратного ТМП в цикле нагрева и последующего охлаждения при измерении ρ(T) обусловлен, по данным фазового анализа, в основном эффектом гетерогенного (на границах и субграницах мартенсита) выделения γ2-фазы, ответственного, как за размерную стабилизацию мартенситных зерен-кристаллитов, так и химическую, обусловленную их обеднением по алюминию и обогащением по меди (на 1–2 ат. %, судя по данным Ms–Af). В этом случае определить химический состав β1-матрицы закаленных сплавов системы Cu–Al–Ni позволяет известная концентрационная зависимость температур ТМП от состава по меди и алюминию.
С другой стороны, при комплексном анализе методами РД, ПЭМ и РЭМ был выявлен ряд особенностей тонкой структуры и фазового состава КВД-сплава после указанных изотермических отжигов. Установлено, что при относительно низких температурах отжига (373–473 К) в КВД-сплаве сохраняются мартенситные фазы. При этом фиксируется появление рефлексов γ2-фазы старения и исчезновение рефлексов α'-фазы, по-видимому трансформирующейся в β'-мартенсит. Напротив, отжиг при более высоких температурах (выше Af) приводит к исчезновению мартенситных фаз вследствие обратного ТМП в УМЗ-аустенит. В этом случае при отжиге ниже Tэр происходит эвтектоидный (α + γ2)-распад аустенитной фазы в глобулярную УМЗ триплекс-структуру, а при отжиге выше Tэр будет происходить выделение γ2-фазы с образованием дуплекс-структуры (β1 + γ2). При охлаждении до КТ и деформации возможно ТМП.
При этом важно, что последеформационные отжиги КВД-сплава сформировали структуры, способные испытывать ЭПФ и фазовую текучесть в широком диапазоне напряжений мартенситного течения σм от 50 до 450 МПа (табл. 3). В целом, мартенситная деформация, включая образование мартенситных кристаллов, раздвойникование и их переориентацию в направлении действующих сил, вносит ощутимый вклад в способность сплава испытывать пластическую деформацию. Так, например, сплав Cu–14Al–3Ni после КВД на 10 оборотов и кратковременного отжига при температуре 1073 К в течение 10 с имел относительно высокое δ (13%), что обусловлено комбинацией фазовой текучести (εм) и протяженной стадии последующей пластической деформации мартенсита (табл. 3). После достижения величины σв = 900 МПа наступала локализация деформации с развитием небольшого сужения [11].
ВЫВОДЫ
1. Обнаружено, что мегапластическая деформация метастабильного аустенитного сплава Cu–14Al–3Ni кручением под высоким давлением 6 ГПа (с числом оборотов от 1 до 10) приводит к созданию деформационно-индуцированной ультрамелкозернистой структуры мартенсита, ответственной за его высокие твердость и прочностные свойства.
2. Показано, что непродолжительный последующий отжиг обеспечивает сохранение ультрамелкозернистой структуры и упрочнение сплава. Наибольшие прочностные (σв до 1400 МПа) и улучшенные пластические (δ = 12–13%) свойства получены в ультрамелкозернистых мартенситных сплавах при использовании после КВД на 10 оборотов кратковременного отжига при 1073 К, 10 с, или за счет повышения температуры КВД до 423 К (150°С).
3. Установлено, что при отжиге ниже температуры Ms, инициирующем гетерогенный (проэвтектоидный) распад мартенсита в КВД-сплаве с выделением обогащенной алюминием γ2-фазы, сохраняются размер зерна, фазовый состав и субструктура мартенсита, но его обеднение по алюминию на 1–2 ат. % вызывает стабилизацию мартенсита и заметное повышение критических температур ТМП (на 70–150 К).
4. Отжиг в аустенитном состоянии выше температуры Af в интервале 570–840 К приводит к первичной рекристаллизации, сопровождаемой гетерогенным эвтектоидным (α + γ2)-распадом β1-аустенита с сохранением однородной ультрамелкозернистой (β1 + α + γ2)-триплекс-структуры. А выше Tэр, близкой 840 К, (β1 + γ2) формируется дуплекс-структура при выделении γ2-нанофазы с повышенной микротвердостью сплава после ТМП при охлаждении до комнатной температуры.
5. По данным фрактографических исследований, сплав в ультрамелкозернистом состоянии отличает вязко-хрупкий характер разрушения с высокой дисперсностью ямок отрыва по большеугловым границам ансамблей нанозерен, объединенных малоугловыми разориентациями.
Работа выполнена по тематике госзадания № АААА-А18-118020190116-6 (“Структура”) ИФМ УрО РАН, совместной лаборатории ИФМ УрО РАН и УрФУ. Авторы благодарят УГАТУ за проведение механических испытаний.
Список литературы
Варлимонт Х., Дилей Л. Мартенситные превращения в сплавах на основе меди, серебра и золота. М.: Наука, 1980. 205 с.
Лихачев В.А., Кузьмин С.Л., Каменцева З.П. Сплавы с эффектом памяти формы. Ленинград: ЛГУ, 1987. 218 с.
Ооцука К., Симидзу К., Судзуки Ю., Сэкигути Ю., Тадаки Ц., Хомма Т., Миядзаки С. Сплавы с эффектом памяти формы. М.: Металлургия, 1990. 224 с.
Хачин В.Н., Пушин В.Г. Кондратьев В.В. Никелид титана: Структура и свойства. М.: Наука, 1992. 160 с.
Пушин В.Г., Кондратьев В.В., Хачин В.Н. Предпереходные явления и мартенситные превращения. Екатеринбург: УрО РАН, 1998. 368 с.
Dasgupta R. A look into Cu–based shape memory alloys: Present Scenario and future prospects // J. Mater. Res. 2014. V. 29. № 16. P. 1681–1698.
Sedlak P., Seiner H., Landa M., Novák V., Šittner P., Manosa L.I. Elastic Constants of bcc Austenite and 2H Orthorhombic Martensite in CuAlNi Shape Memory Alloy // Acta Mater. 2005. V. 53. P. 3643–3661.
Lopez G.A., Lopez-Ferreno I., Kilmametov A.R., Breczewski T., Straumal B.B., Baretzky B., No M.L., San Juan J. Severe plastic deformation on powder metallurgy Cu–Al–Ni shape memory alloys // Mater. Today: Proceedings 2S. 2015. V. 2. P. S747–S750.
Svirid A.E., Pushin V.G., Kuranova N.N., Luk’yanov A.V., Pushin A.V., Uksusnikov A.N., Ustyugov Y.M. The structure–phase transformations and mechanical properties of the shape memory effect alloys based on the system Cu–Al–Ni // Materials Today: Proceedings. 2017. V. 4. P. 4758–4762.
Свирид А.Э., Куранова Н.Н., Лукьянов А.В., Макаров В.В., Николаева Н.В., Пушин В.Г., Уксусников А.Н. Влияние термомеханической обработки на структурно-фазовые превращения и механические свойства сплавов Cu–Al–Ni с памятью формы // Изв. вузов. Физика. 2018. Т. 61. № 9. С. 114–119.
Лукьянов А.В., Пушин В.Г., Куранова Н.Н., Свирид А.Э., Уксусников А.Н., Устюгов Ю.М., Гундеров Д.В. Влияние термомеханической обработки на структурно-фазовые превращения в сплаве Cu–14Al–3Ni с эффектом памяти формы, подвергнутом кручению под высоким давлением // ФММ. 2018. Т. 119. № 4. С. 393–401.
Свирид А.Э., Лукьянов А.В., Пушин В.Г., Белослудцева Е.С., Куранова Н.Н., Пушин А.В. Влияние температуры изотермической осадки на структуру и свойства сплава Cu–14 мас. % Al–4 мас. % Ni с эффектом памяти формы // ФММ. 2019. Т. 120. С. 1257–1263.
Свирид А.Э., Лукьянов А.В., Пушин В.Г., Куранова Н.Н., Макаров В.В., Пушин А.В., Уксусников А.Н. Применение изотермической осадки для мегапластической деформации beta-сплавов Cu–Al–Ni // ЖТФ. 2020. Т. 90. С. 1088–1094.
Свирид А.Э., Лукьянов А.В., Макаров В.В., Пушин В.Г., Уксусников А.Н. Влияние легирования алюминием на структуру, фазовые превращения и свойства сплавов Cu–Al–Ni с эффектом памяти формы // Челябинский физико-математический журнал. 2019. Т. 4. С. 108–117.
Pelosin A., Riviere A. Structural and mechanical spectroscopy study of the $\beta _{1}^{'}$ martensite decomposition in Cu–12% Al–3% Ni (wt %) alloy // J. Alloys and Compounds. 1998. V. 268. P. 166–172.
Dagdelen F., Gokhan T., Aydogdu A., Aydogdu Y., Adiguzel O. Effect of thermal treatments on transformation behavior in shape memory Cu–Al–Ni alloys // Mater. Letters. 2003. V. 57. P. 1079–1085.
Li Z., Pan Z.Y., Tang N., Jiang Y.B., Liu N., Fang M., Zheng F. Cu–Al–Ni–Mn shape memory alloy processed by mechanical alloying and powder metallurgy // Mater. Science and Engineering A. 2006. V. 417. P. 225–229.
Suresh N., Ramamurty U. Aging response and its effect on the functional properties of Cu–Al–Ni shape memory alloys // J. Alloys and Compounds. 2008. V. 449. P. 113–118.
Dar R.D., Yan H., Chen Y. Grain boundary engineering of Co–Ni–Al, Cu–Zn–Al, and Cu–Al–Ni shape memory alloys by intergranular precipitation of a ductile solid solution phase // Scripta materialia. 2016. V. 115. P. 113–117.
La Roca P., Isola L., Vermaut Ph., Malarria J. Relationship between grain size and thermal hysteresis of martensitic transformations in Cu-based shape memory alloys // Scripta Mater. 2017. V. 135. P. 5–9.
Zhang X., Zhao X, Wang F, Qingsuo L., Wang Q. Microstructure, mechanical properties and shape memory effect of Cu–Hf–Al–Ni alloys // Mater. Sci. Tech. 2018. V. 34. № 12. P. 1497–1501.
Дополнительные материалы отсутствуют.
Инструменты
Физика металлов и металловедение