Физика металлов и металловедение, 2022, T. 123, № 1, стр. 101-108
Влияние температуры закалки на сопротивление ползучести 9% Cr–1% W–1% Mo–V–Nb мартенситной стали
А. Э. Федосеева a, *, И. С. Никитин a, Р. О. Кайбышев a
a Белгородский государственный национальный исследовательский университет
308015 Белгород, ул. Победы, 85, Россия
* E-mail: fedoseeva@bsu.edu.ru
Поступила в редакцию 02.07.2021
После доработки 16.09.2021
Принята к публикации 20.09.2021
- EDN: POYTTE
- DOI: 10.31857/S001532302201003X
Аннотация
Сопротивление ползучести 9% Cr–1% W–1% Mo стали, подвергнутой закалке с температур 1050 и 1150°С, охлаждение на воздухе, с последующим отпуском при температуре 750°С в течение 3 ч, было исследовано при температуре 650°С и приложенных напряжениях 160, 140 и 120 МПа. Увеличение температуры закалки от 1050 до 1150°С привело к увеличению среднего размера исходных аустенитных зерен с 25 до 93 мкм, что было вызвано растворением частиц карбонитридов МХ, обогащенных ниобием, при выдержке в аустенитной области. Увеличение размеров исходных аустенитных зерен сопровождается снижением среднего размера блоков и мартенситных реек на 17 и 43% соответственно. Более того, повышенная температура нагрева под закалку обеспечивает благоприятные условия (доля границ, плотность дислокаций, содержание легирующих элементов в твердом растворе) для выделения при отпуске частиц карбидов М23С6 и карбонитридов МХ более мелкого размера. Увеличение структурного упрочнения из-за пониженного размера блоков и мартенситных реек, а также дисперсионного упрочнения из-за наноразмерных частиц VX оказывает положительное влияние на сопротивление ползучести, уменьшая минимальную скорость ползучести и продолжительность неустановившейся стадии, что увеличивает время до разрушения в несколько раз.
ВВЕДЕНИЕ
В настоящее время развитие теплоэнергетической области направлено на повышение коэффициента полезного действия тепловых энергетических установок за счет перехода на суперсверхкритические параметры пара путем повышения температуры до 600–620°С и давления пара до 25–30 МПа [1–3]. Это достигается переходом к использованию теплотехнических сталей нового поколения. За рубежом в качестве материала для изготовления высокотемпературных контуров котлов и главных паропроводов было разработано несколько высокохромистых сталей, сертифицированных для применения в теплоэнергетике, таких как Р91, Р911 и Р92 стали [1–3]. Наибольшее применение находят стали Р911 (химический состав в вес. % 0.1C–0.05N–9Cr–1W–1Mo–0.24V–0.07Nb–0.003B) и P92 (химический состав в вес .% 0.1C–0.05N–9Cr–1.8W–0.6Mo–0.24V–0.07Nb–0.003B), которые допускают длительную эксплуатацию при температурах до 600°С и короткоресурсную работу до 620°С [1].
Структура этих сталей представляет собой троостит отпуска, получаемый путем термической обработки, состоящей из закалки на воздухе и среднетемпературного отпуска [1, 4, 5]. Сложная иерархическая структура троостита отпуска представляет собой исходные аустенитные зерна (ИАЗ), разделенные на пакеты [1–5]. Границы этих структурных элементов являются большеугловыми [1–5]. Пакеты разделены специальными границами или малоугловыми границами с углом разориентировки 10.54° на блоки, состоящие из мартенситных реек [1–5]. Границы мартенситных реек характеризуются углом разориентировки от 1° до 2° [1–5]. Высокое сопротивление ползучести этих сталей обеспечивается суперпозицией всех четырех упрочняющих механизмов: (а) твердорастворное упрочнение, за которое ответственны Cr, W и Mo; (б) дислокационное упрочнение, (в) субструктурное упрочнение от малоугловых границ мартенситных реек, (г) дисперсионное упрочнение от частиц карбонитридов MХ (где М означает V, Nb, а X – С и/или N), равномерно распределенных по объему матрицы, а также карбидов M23C6, обогащенных хромом, и интерметаллидов фазы Лавеса Fe2(W,Mo), выделяющихся по границам ИАЗ, пакетов, блоков и мартенситных реек [6]. Наиболее важным механизмом упрочнения высокохромистых сталей является дисперсионное упрочнение из-за карбонитридов МХ. Эти наноразмерные карбонитриды служат препятствиями для движения дислокаций, что обеспечивает низкую скорость ползучести и стабильность структуры троостита отпуска при высоких температурах [7–9]. Формирование двух типов карбонитридов с разделением по химическому составу на V(C,N) и Nb(C,N) обеспечивает стабильность этих частиц в процессе ползучести при температурах до 650°С [9].
Влиять на вклады этих механизмов упрочнения в предел текучести и сопротивление ползучести, можно, меняя структуру и распределение частиц вторичных фаз в троостите отпуска за счет изменений в режимах термической обработки. От температуры нагрева под закалку зависит не только размер ИАЗ, но и размеры пакетов, блоков, карбидов M23C6 и преимущественный тип границ, на которых эти карбиды выделяются [10–13]. В работе [10] отмечается, что в сталях с различным легированием, но схожим размером ИАЗ длительная прочность будет одинаковая, несмотря на существенные различия при кратковременных испытаниях. При этом оптимальным размером ИАЗ является 50 мкм [11]. Влияние размера ИАЗ на сопротивление ползучести высокохромистых сталей во многом остается не ясным, принимая во внимание ограниченное количество работ [10–13]. При этом в данных работах сравнивались стали с различным содержанием легирующих элементов, что не дает возможности отделить влияние легирования от влияния термической обработки. Целью настоящей работы является установить влияние температуры закалки на сопротивление ползучести 9% Cr–1% W–1% Mo–V–Nb стали при температуре 650°С.
МЕТОДИКА ПРОВЕДЕНИЯ ИССЛЕДОВАНИЙ
9% Cr сталь с химическим составом (в вес. %): 0.12% C–8.7% Сr–1% Mo–0.9% W–0.2% V–0.07% Nb–0.1% Si–0.4% Mn–0.2% Ni–0.05% N–0.003% B–0.02% Al, обозначенная здесь как P911 сталь, была выплавлена в высокочастотной индукционной печи в ОАО НПО “ЦНИИТМАШ”, г. Москва, Россия. Кованые заготовки были подвергнуты двум режимам термической обработки (стандартному и модифицированному), заключающимся в закалке с последующим среднетемпературным отпуском. Стандартная термическая обработка Р911 стали состояла из закалки с 1050°С с выдержкой в течение 30 мин, охлаждение на воздухе, с последующим отпуском при 750°С в течение 3 ч с охлаждением на воздухе. Модифицированная термическая обработка стали отличалась только температурой нагрева под закалку – 1150°С.
Испытания на ползучесть до разрушения были проведены при температуре 650°С и приложенных напряжениях 160, 140 и 120 МПа с использованием плоских образцов с длиной рабочей части 25 мм и поперечным сечением 7 × 3 мм2 с помощью испытательной машины рычажного типа ATS2330. Размер ИАЗ изучаемой стали был оценен с использованием оптического микроскопа Olympus GX71 (ОМ). Микроструктура была выявлена химическим травлением в растворе состава: HF – 1%, HNO3 – 2%, H2О – 97%.
Просвечивающая электронная микроскопия (ПЭМ) с использование микроскопа JEM JEOL-2100, оснащенного энергодисперсионной приставкой INCA, и сканирующая электронная микроскопия с использованием микроскопа Quanta 600 3D, оснащенного приставкой для EBSD-(electron back-scatter diffraction) анализа, были использованы для оценки размеров пакетов, мартенситных реек, плотности дислокаций, а также типа, морфологии и размера вторичных частиц. EBSD-картины были сняты с участков площадью 200 × 100 мкм2 с шагом 0.1 мкм. Фольги для ПЭМ и EBSD-анализа были подготовлены в 10%-м растворе хлорной кислоты в уксусной под напряжением 21–23 В с использованием специальной установки Struers TENUPOL-5. Углеродные реплики для ПЭМ были получены при помощи универсального вакуумного поста “Quorum Q 150R”. Размер блоков и реек был определен методом случайных секущих с учетом всех видимых границ/(суб)границ. Плотность свободных дислокаций внутри реек/субзерен была оценена по количеству точек выхода дислокаций на поверхность фольги с использованием ПЭМ и с использованием коэффициента Кернела по EBSD-картинам как ρ = 2φ/xb, где φ – среднее значение коэффициента Кернела, как среднее искажение решетки вокруг каждой точки сканирования для первой координационной сферы, x – шаг сканирования и b – вектор Бюргерса [14]. Тип частиц был определен комплексным методом на основе локального химического состава и картин микродифракций электронов, полученных методом ПЭМ углеродных реплик. Объемная доля вторичных фаз была оценена с использованием программного обеспечения Thermo-Calc. Более подробно методики описаны в предыдущих работах [6, 7, 13, 15].
РЕЗУЛЬТАТЫ ИССЛЕДОВАНИЯ И ИХ ОБСУЖДЕНИЕ
Влияние температуры закалки на размер ИАЗ и вторичные фазы
Оптическая металлография Р911 стали приведена на рис. 1. Увеличение температуры закалки с 1050°С до 1150°С приводит к существенному повышению среднего размера ИАЗ от 25 ± 5 до 93 ± ± 5 мкм соответственно (рис. 1). Увеличение размера ИАЗ вызвано растворением карбонитридов МX при выдержке в аустенитной области. Моделирование фазового состава с помощью программы Thermo-Calc показало, что при обеих температурах закалки 1050 и 1150°С присутствуют карбонитриды МX, обогащенные ванадием и ниобием. Отметим, что химический состав фазы МX при температурах закалки 1050 и 1150°С существенно различен. При Т = 1050°С карбонитрид (Nb,V)X содержит 40 вес. % Nb–39% V–15% N–4% Cr–2% C. При Т = 1150°С карбонитрид NbX содержит 80 вес. % Nb–4% V–8% N–3% Cr–5% C. При температуре закалки 1050°С объемная доля карбонитридов NbX составляет 0.11%, в то время как с увеличением температуры закалки до 1150°С объемная доля карбонитридов NbX снижается до 0.024%, что почти в 4 раза меньше, чем при более низкой температуре закалки. В твердом растворе мартенсита после закалки остается 0.16 вес. % V и 0.011 вес. % Nb при 1050°С, и 0.20 вес. % V и 0.024 вес. % Nb при 1150°С, которые при 750°С отпуске также будут участвовать в образовании частиц карбонитридов МХ.
Влияние размера ИАЗ на сопротивление ползучести
На рис. 2 представлена зависимость времени до разрушения от приложенного напряжения для Р911 стали после термической обработки по двум режимам. Видно, что увеличение температуры закалки ведет к существенному приросту времени до разрушения в 10, 5 и 4 раза при приложенных напряжениях 160, 140 и 120 МПа соответственно (рис. 2). Время до разрушения (τr) может быть выражено через приложенное напряжение (σ) следующей зависимостью (1) [10]:
где A – константа, m – константа напряжения. Константы напряжения составили 11 и 6 для закалки при температурах 1050 и 1150°С соответственно (рис. 2). Такие значения соответствуют дислокационной ползучести, контролируемой низкотемпературным переползанием дислокаций, скорость которых определяется трубочной диффузией [2, 10]. Отметим, что со снижением приложенных напряжений прирост во времени до разрушения снижается вплоть до его полного исчезновения (рис. 2).Рис. 2.
Зависимость времени до разрушения от приложенного напряжения при температуре 650°С для Р911 стали, подвергнутой различным режимам термической обработки.
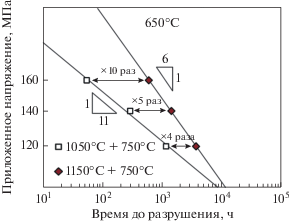
Зависимости скорости ползучести от времени и степени деформации при температуре 650°С и приложенных напряжениях 160, 140 и 120 МПа представлены на рис. 3. Отметим, что характер кривых ползучести схож после обеих температур закалки. Для каждого состояния можно выделить три стадии ползучести: неустановившуюся стадию, при которой скорость ползучести снижается до минимального значения с увеличением времени и степени деформации, достижение минимальной скорости ползучести и ускоренную стадию ползучести, при которой скорость деформации увеличивается с увеличением времени и скорости деформации после достижения минимальной скорости ползучести и до разрушения (рис. 3).
Рис. 3.
Зависимости скорости ползучести от времени (а–в) и степени деформации (г–е) при температуре 650°С и приложенных напряжениях 160 (а, г), 140 (б, д) и 120 МПа (в, е) для Р911 стали после различных режимов термической обработки.
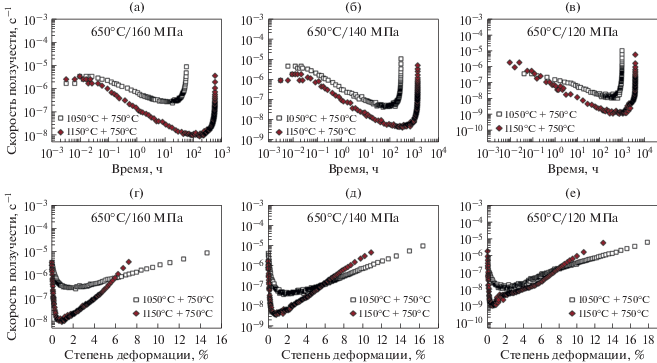
При всех приложенных напряжениях Р911 сталь, подвергнутая закалке с 1150°С с последующим отпуском при 750°С, демонстрирует увеличение продолжительности неустановившейся стадии по времени и снижение минимальной скорости деформации на 1–2 порядка по сравнению со стандартной термической обработкой (рис. 3). Это и обусловливает большее время до разрушения при одинаковых условиях ползучести (рис. 2). Однако, эта разница уменьшается с понижением приложенных напряжений. Так, при приложенном напряжении 160 МПа прирост времени неустановившейся стадии составляет 10 раз, в то время как при 120 МПа всего 4 раза (рис. 3а–3в). Более того, время, необходимое для достижения минимальной скорости ползучести, для стали, закаленной с 1150°С, превышает время до разрушения для стали, закаленной с 1050°С, при всех приложенных напряжениях (рис. 3а–3в).
При всех приложенных напряжениях Р911 сталь, подвергнутая закалке с 1050°С, имеет степень деформации до разрушения 15–18% (рис. 3г–3е). При приложенном напряжении 160 МПа степень деформации до разрушения Р911 стали после закалки с 1150°С в 2 раза ниже, чем после 1050°С (рис. 3г), однако при снижении приложенных напряжениях эта разница уменьшается до 30% (рис. 3д, 3е). Отметим, что температура закалки несущественно влияет на протяженность неустановившейся стадии по степени деформации (рис. 3г–3е). При всех приложенных напряжениях степень деформации, при которой достигается минимальная скорость деформации, близка к 1% для обоих состояний Р911 стали (рис. 3).
Таким образом, увеличение времени до разрушения в Р911 стали, подвергнутой закалке с 1150°С, коррелирует с более продолжительной неустановившейся стадией и снижением минимальной скорости деформации и может быть обусловлено как структурой, формирующейся после отпуска, так и микроструктурными изменениями, протекающими на неустановившейся стадии ползучести [13].
Микроструктурные аспекты высокого сопротивления ползучести стали с большим размером ИАЗ
Чтобы выяснить причины более высокой прочности Р911 стали с большим размером ИАЗ, методами ПЭМ фольг и углеродных реплик и EBSD-анализа были проведены детальные исследования микроструктуры после различных термических обработок. На рис. 4 приведены изображения микроструктуры Р911 стали после закалки с 1050 и 1150°С с последующим отпуском при 750°С. В табл. 1 просуммированы структурные параметры Р911 стали после различных режимов термических обработок.
Рис. 4.
Изображения микроструктуры Р911 стали после закалки с 1050 (а, б) и 1150°С (в, г) с последующим отпуском при 750°С, полученные с помощью ПЭМ тонких фольг (а, в) и EBSD-анализа (б, г).
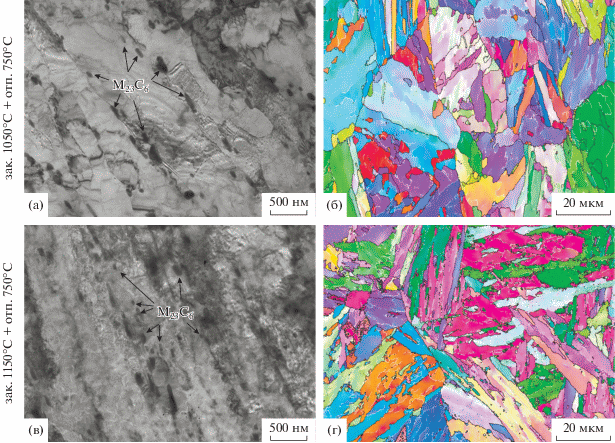
Таблица 1.
Структурные параметры Р911 стали после различных режимов термической обработки
Параметры | Тзакалки | |
---|---|---|
1050°С | 1150°С | |
Размер ИАЗ, мкм | 25 ± 5 | 93 ± 5 |
Размер блока, мкм | 2.6 ± 0.1 | 2.2 ± 0.1 |
Ширина реек, мкм | 0.54 ± 0.05 | 0.31 ± 0.05 |
Плотность дислокаций (по ПЭМ), ×1014 м–2 | 1.8 ± 0.1 | 2.1 ± 0.1 |
Плотность дислокаций (по EBSD анализу), ×1014 м–2 | 8.0 ± 0.1 | 7.6 ± 0.1 |
Размер М23С6, нм | 97 ± 5 | 83 ± 5 |
Плотность частиц по границам, мкм–1 | 1.44 ± 0.2 | 1.03 ± 0.2 |
Размер NbХ, нм | 41 ± 5 | 23 ± 5 |
Размер VХ, нм | 30 ± 5 | 18 ± 5 |
Объемная доля VХ, % | 0.29 | 0.30 |
ПЭМ тонких фольг и EBSD-анализ выявил, что обе термические обработки приводят к формированию структуры троостита отпуска. Увеличение температуры закалки от 1050 до 1150°С приводит к уменьшению размера блока и ширины мартенситных реек на 17 и 43% соответственно (табл. 1) вопреки росту размера ИАЗ. Соотношение между размерами блока и шириной мартенситных реек увеличивается от 4.8 до 7 с увеличением температуры закалки (табл. 1). Отметим, что плотность дислокаций, оцененная методами ПЭМ и EBSD-анализа (через коэффициент Кернела), не зависит от температуры закалки и имеет один порядок (табл. 1), хотя в 9–12% Cr сталях ширина мартенситных реек и плотность дислокаций обычно имеют обратно пропорциональную зависимость [6, 16].
После обеих термических обработок по границам ИАЗ, пакетов, блоков и мартенситных реек были обнаружены частицы карбидов М23С6 округлой формы. Увеличение температуры закалки от 1050 до 1150°С приводит к снижению размера частиц карбидов М23С6 с 97 до 83 нм с одновременным снижением плотности этих частиц по границам пакетов, блоков и реек в 1.5 раза (табл. 1). Такие изменения вызваны, по-видимому, увеличением числа границ при более высокой температуре закалки, а также более равномерным распределением частиц карбидов М23С6 по границам блоков и реек при отпуске.
Особое внимание в 9–12% Cr сталях с содержанием углерода 0.1% и азота 0.05% уделяется карбонитридам МХ, обогащенным ванадием и ниобием, которые являются основными причинами возникновения пороговых напряжений [2, 8, 11, 17]. На рис. 5 приведены изображения различных типов частиц в Р911 стали после закалок с 1050 и 1150°С с последующим отпуском при 750°С совместно с распределением частиц (VX и М23С6) по размерам. Преимущественно в процессе отпуска происходит выделение частиц МХ, обогащенных ванадием, независимо от температуры закалки (рис. 5). В твердом растворе мартенсита после закалки при 1150°С содержится повышенное количество ванадия и ниобия, однако это не ведет к увеличению объемной доли этих частиц (табл. 1) Увеличение температуры закалки от 1050 до 1150°С приводит к двух-кратному снижению среднего размера частиц VX и NbX при отпуске (табл. 1, рис. 5б, 5г) за счет увеличения количества МX частиц, выделившихся в ферритной матрице. Распределение частиц VX по размерам (рис. 5б, 5г) демонстрирует, что около 80% частиц имеют размер меньше 25 нм после закалки с 1150°С с последующим отпуском. Химический состав частиц VX после закалок с 1050 и 1150°С имеет существенные различия (рис. 5а, 5в). Так, увеличение температуры закалки от 1050 до 1150°С меняет соотношение V : Cr в частицах VX с 3 : 1 до 1 : 1 (рис. 5). Такие изменения в дисперсии карбонитридов МХ препятствуют росту мартенситных реек при отпуске, что и обусловливает их меньший размер после модифицированной термической обработки.
Рис. 5.
Изображения частиц вторичных фаз (а,в) в Р911 стали после закалки с 1050 (а, б) и 1150°С (в, г) с последующим отпуском при 750°С совместно с распределением частиц (VX и M23C6) по размерам (б, г), полученные с помощью ПЭМ углеродных реплик.
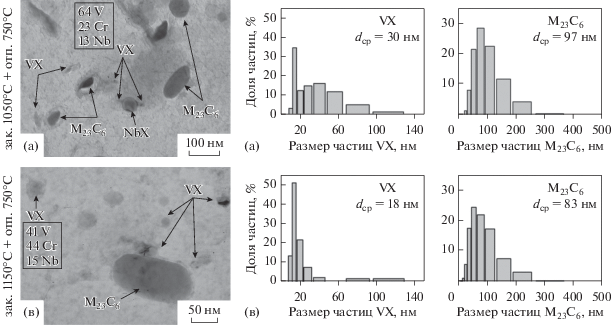
Таким образом, высокое сопротивление ползучести при высоких приложенных напряжениях в стали с большим размером ИАЗ обусловлено структурным упрочнением за счет сниженного размера блока и мартенситных реек, а также дисперсионным упрочнением, преимущественно, из-за наноразмерных частиц VX со средним размером 18 нм. Эти частицы препятствуют переползанию дислокаций при ползучести [2, 8, 11, 17]. Отметим, что измельчение карбида М23С6 также должно положительно сказываться на сопротивлении ползучести, поскольку эти частицы препятствуют миграции границ блоков и мартенситных реек [15].
Нивелирование прироста сопротивления ползучести при снижении приложенного напряжения вызвано исчезновением преимуществ в структурном и дисперсионном упрочнениях стали с большим размером ИАЗ в процессе ползучести. Вместо реечной мартенситной структуры формируется равноосная субзеренная структура, частицы карбидов М23С6 и МХ сильно укрупняются, частицы МХ могут трансформироваться в крупные частицы стабильной Z–фазы [1, 2, 7, 15, 17]. Такие структурные изменения в процессе ползучести не должны зависеть от термической обработки. Дальнейшие работы будут направлены на исследования структурных изменений в процессе ползучести.
ВЫВОДЫ
Механические свойства при ползучести Р911 стали, подвергнутой различным режимам термической обработки, были исследованы. Увеличение температуры закалки от 1050 до 1150°С с последующим отпуском при 750°С приводит к существенным структурным изменениям. Во-первых, размер ИАЗ увеличивается почти в 3 раза, что влияет на размер блоков и мартенситных реек. Размер блоков и мартенситных реек снижается на 17 и 43% соответственно. Во-вторых, снижается размер карбонитридов МХ и карбидов М23С6, а также меняется химический состав частиц карбонитридов VX. Такие изменения в структуре Р911 стали оказали положительное влияние на сопротивление ползучести при температуре 650°С и приложенных напряжениях 160, 140 и 120 МПа, увеличив время до разрушения в 10, 5 и 4 раза соответственно. Увеличение времени до разрушения при всех исследованных условиях ползучести обусловлено увеличением продолжительности неустановившейся стадии ползучести и снижением минимальной скорости ползучести.
Результаты микроструктурных исследований и механических свойств получены за счет средств гранта РФФИ № 20-33-90117. Результаты моделирования фазовых составов получены за счет средств гранта Президента Российской Федерации для государственной поддержки молодых российских ученых – кандидатов наук (соглашение № 075-15-2021-336). Работа выполнена с использованием оборудования Центра коллективного пользования “Технологии и Материалы НИУ “БелГУ”.
Список литературы
Abe F., Kern T.U., Viswanathan R. Creep-resistant steels. Woodhead: Publishing, Cambridge, 2008. 800 p.
Кайбышев Р.О., Скоробогатых В.Н., Щенкова И.А. Новые стали мартенситного класса для тепловой энергетики. Жаропрочные свойства // ФММ. 2010. Т. 109. С. 200–215.
Viswanathan R., Bakker W. Materials for ultrasupercritical coal power plants – boiler materials: Part 1 // J. Mater. Eng. Performance. 2001. V. 10. P. 81–95.
Гундырев В.М., Зельдович В.И., Счастливцев В.М. Кристаллографический анализ и механизм мартенситного превращения в сплавах железа // ФММ. 2020. Т. 121. С. 1142–1161.
Сагарадзе В.С., Кочеткова Т.Н., Катаева Н.В., Козлов К.А., Завалишин В.А., Вильданова Н.Ф., Агеев В.С., Леонтьева-Смирнова М.В., Никитина А.А. Структура и ползучесть российских реакторных сталей с ОЦК-решеткой // ФММ. 2017. Т. 118. С. 522–534.
Nikitin I., Fedoseeva A., Kaibyshev R. Strengthening mechanisms of creep-resistant 12% Cr–3% Co steel with low N and high B contents // J. Mater. Sci. 2020. V. 55. P. 7530–7545.
Федосеева А.Э., Никитин И.С., Дудова Н.Р., Кайбышев Р.О. Влияние условий ползучести и длительного отжига на образование частиц Z-фазы // ФММ. 2020. Т. 121. С. 621–627.
Abe F. Precipitate Design for Creep Strengthening of 9% Cr Tempered Martensitic Steel for Ultra-Supercritical Power Plants // Sci. Tech. Advance.Mater. 2008. V. 9. No. 013002.
Suzuki K., Kumai S., Toda Y., Kushima H., Kimura K. Two-Phase Separation of Primary MX Carbonitride during Tempering in Creep Resistant 9Cr1MoVNb Steel // ISIJ International. 2003. V. 43. P. 104312.
Maruyama K., Sekido N., Yoshimi K. Changes in strengthening mechanisms in creep of 9Cr–1.8W–0.5Mo–VNb steel tested over wide ranges of creep conditions// ISIJ Inter. 2021. V. 190. № 1089–1094
Kostka A., Tak K-G., Hellmig R.J., Estrin Y., Eggeler G. On the contribution of carbides and micrograin boundaries to the creep strength of tempered martensite ferritic steels // Acta Mater. 2007. V. 55. P. 539–550.
Kimura K., Ohi N., Shimazu K., Matsuo T., Tanaka R., Kikuchi M. Effect of prior austenite grain size on high temperature creep properties of Cr–Mo–V rotor steel // Scripta Metal. 1987. V. 21. P. 19–22.
Fedoseeva A., Nikitin I., Tkachev E., Mishnev R., Dudova N., Kaibyshev R. Effect of alloying on the nucleation and growth of Laves phase in the 9–10% Cr–3% Co martensitic steels during creep // Metals. 2021. V. 11. № 60.
Zhilyaev A., Sergeev S., Langdon T. Electron backscatter diffraction (EBSD) microstructure evolution in HPT copper annealed at a low temperature // J. Mater. Research Technology. 2014. V. 3. P. 338–343.
Fedoseeva A., Dudova N., Kaibyshev R. Creep strength breakdown and microstructure evolution in a 3% Co modified P92 steel // Mater. Sci. Eng. A. 2016. V. 654. P. 1–12.
Li Q. Modeling the microstructure-mechanical property relationship for a 12% Cr–2W–V–Mo–Ni power plant steel // Mater. Sci. Eng. A. 2003. V. 361. P. 385–391.
Dudko V., Belyakov A., Kaibyshev R. Origin of Threshold Stresses in a P92-type Steel // Trans Indian Inst Met. 2016. V. 69. P. 223–227.
Дополнительные материалы отсутствуют.
Инструменты
Физика металлов и металловедение