Физика металлов и металловедение, 2022, T. 123, № 1, стр. 109-116
Циклическая прочность сплава Zr–1% Nb после равноканального углового прессования
А. Б. Рожнов a, С. О. Рогачев a, b, *, Ханан Алшеих a, Д. В. Просвирнин b
a Национальный исследовательский технологический университет “МИСиС”
119049 Москва, Ленинский просп., 4, Россия
b Институт металлургии и материаловедения имени А.А. Байкова РАН
119334 Москва, Ленинский просп., 49, Россия
* E-mail: csaap@mail.ru
Поступила в редакцию 25.08.2021
После доработки 14.09.2021
Принята к публикации 17.09.2021
- EDN: WIYYUH
- DOI: 10.31857/S0015323022010119
Аннотация
Изучено влияние РКУП на структуру, статическую и циклическую прочность циркониевого сплава Э110 (Zr–1% Nb). РКУП проводили на образцах диаметром и длиной ∅20 × 100 мм по маршруту BC, с углом между каналами 110°, за 6 проходов со ступенчатым понижением температуры с 400 до 300°С. После РКУП в сплаве сформировалась сильно неоднородная ультрамелкозернистая микроструктура, состоящая из областей с ячейками и фрагментами с малой разориентировкой и высокой плотностью дислокаций и областей с преимущественно равноосными структурными элементами. В результате РКУП предел прочности сплава повысился на 40%, предел текучести на 22%, а относительное удлинение уменьшилось в 2 раза. РКУП привело к снижению ограниченного предела усталости на базе 107 циклов с 225 до 150 МПа и к смене механизма разрушения с квазивязкого микробороздчатого на преимущественно хрупкий со вторичным растрескиванием. При высоких напряжениях цикла (выше 280 МПа) долговечность сплава как в исходном состоянии, так и после РКУП сопоставима.
ВВЕДЕНИЕ
Сегодня ввиду возросшей конкуренции производители стоматологических имплантатов заинтересованы в новых конструкционных материалах. Подтвержденная превосходная биосовместимость циркония и некоторых его сплавов позволяет их рассматривать в качестве перспективных материалов для имплантатов [1, 2]. Однако для более успешного применения циркониевых сплавов в медицине необходимо достичь в этих сплавах комплекса высоких механических и функциональных свойств.
Среди существующих промышленных циркониевых сплавов в медицине могут быть применимы двойные сплавы Zr–Nb [3]. Известно, что циркониевые сплавы в ультрамелкозернистом состоянии, в частности, полученные методами больших пластических деформаций, обладают высокой механической прочностью (σВ сплава Zr–2.5% Nb после РКУП выше 800 МПа), повышенным сопротивлением коррозионному разрушению даже в агрессивных средах, например йод + метанол [4–11]. Одним из методов больших пластических деформаций, позволяющих получать ультрамелкозернистую структуру в массивных образцах, является равноканальное угловое прессование (РКУП) [12, 13]. Известно большое число работ, посвященных исследованию структуры и механических свойств циркониевого сплава Э125 (Zr–2.5% Nb), обработанного методом РКУП [4–6, 9]. Результаты исследований подтвердили соответствие достигнутого комплекса свойств сплава после РКУП (высокая статическая и усталостная прочность, улучшенная коррозионная стойкость) требованиям к конструкционному материалу со стороны медицины. Альтернативой сплаву Э125 является менее легированный сплав Э110 (Zr–1% Nb). Количество исследований влияния РКУП на структуру и свойства сплава Э110 в научной литературе ограничено.
Сопротивление статическому и усталостному разрушению – важнейшие характеристики конструкционного материала, в частности применяемого в медицине. Однако повышенная статическая прочность ультрамелкозернистого материала не всегда однозначно коррелирует с улучшенными характеристиками циклической прочности [14]. Поэтому целью настоящей работы является изучение влияния РКУП на статическую и циклическую прочность циркониевого сплава Э110 (Zr–1% Nb).
МАТЕРИАЛ И МЕТОДИКИ ИССЛЕДОВАНИЯ
Прутки длиной 100 мм и диаметром 20 мм из сплава Э110 (Zr–1% Nb) в состоянии поставки обрабатывали методом РКУП. Процесс осуществляли, используя маршрут BC, с углом между каналами 110°, в изотермических условиях, но со ступенчатым понижением температуры, по режиму: 2 прохода при Т = 400°С + 2 прохода при Т = 350°С + 2 прохода при Т = 300°С.
Электронно-микроскопические исследования структуры сплава проводили на тонких фольгах с помощью электронного микроскопа JEM-1400 (JEOL) в светлых и темных полях.
Для испытаний на одноосное растяжение и усталость использовали плоские образцы в форме “лопаток” длиной 65 мм, толщиной 1 мм, шириной рабочей части 3.5 мм, полученные методом электроэрозионной резки с последующей механической шлифовкой и полировкой поверхности.
Испытания на одноосное растяжение проводили на универсальной испытательной машине INSTRON-150LX при комнатной температуре со скоростью растяжения 1 мм/мин. Использовали 3 образца на точку.
Испытания на многоцикловую усталость по схеме повторного растяжения проводили на сервогидравлической машине Instron 8801 при комнатной температуре, с коэффициентом асимметрии R = 0.1 и частотой f = 30 Гц.
Анализ изломов образцов после испытания на усталость проводили на сканирующем микроскопе JSM-IT500 (JEOL) при увеличениях 35–1500 крат.
РЕЗУЛЬТАТЫ ИССЛЕДОВАНИЯ И ИХ ОБСУЖДЕНИЕ
Сплавы Э110 и Э125 в производстве могут быть получены как в частично, так и в полностью рекристаллизованном состоянии. Согласно данным ПЭМ, микроструктура исследованного сплава Э110 в исходном состоянии неоднородная, частично рекристаллизованная. Наблюдаются как области, представленные вытянутыми субзернами шириной 0.9–1.7 мкм и длиной 2–5 мкм, имеющими преимущественную ориентировку (рис. 1а), так и области, представленные рекристаллизованными зернами размером менее 1 мкм (указаны стрелками на рис. 1б).
Рис. 1.
Микроструктура сплава Э110 в исходном состоянии (ПЭМ): а – область вытянутых субзерен, б – область с рекристаллизованными зернами.
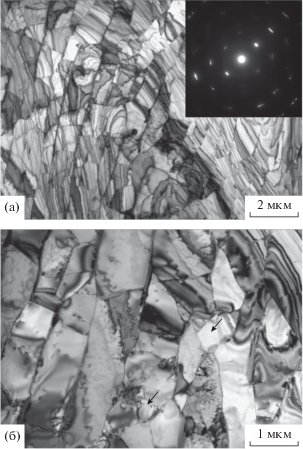
В результате РКУП в сплаве сформировалась сильно неоднородная ультрамелкозернистая микроструктура, состоящая из областей с ячейками и фрагментами с малой разориентировкой и высокой плотностью дислокаций (рис. 2а) и областей с преимущественно равноосными структурными элементами как с большой, так и малой плотностью дислокаций (последние указаны стрелками на рис. 2б). Длина и ширина фрагментов составила 0.7–1.1 и 0.4–0.6 мкм, соответственно, а размер равноосных структурных элементов – 0.2–0.3 мкм. В основном сформированная структура качественно и количественно подобна структурам других циркониевых сплавов, например, Э125, обработанных методом РКУП [4, 5].
Рис. 2.
Микроструктура сплава Э110 после РКУП (ПЭМ): а – область со слаборазориентированными фрагментами, б – область с равноосными структурными элементами.
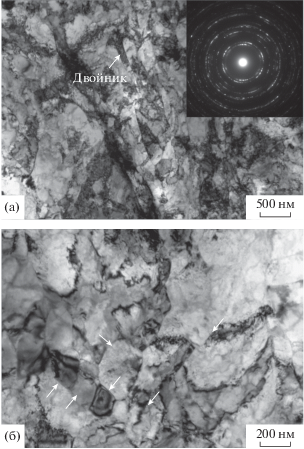
После РКУП наблюдается существенное повышение прочностных характеристик сплава Э110 (рис. 3, табл. 1) при растяжении: пределы текучести и прочности сплава составили 440 и 588 МПа, соответственно, (в исходном состоянии 360 и 420 МПа соответственно), при относительном удлинении 10% (в исходном состоянии 20%). Таким образом, в результате РКУП предел прочности сплава повысился на 40%, предел текучести на 22%, а относительное удлинение уменьшилось в 2 раза. При этом равномерное удлинение сплава после РКУП снизилось с 5 до 2.5%. Кривые деформации сплава в обоих состояниях характеризуются протяженной областью локализованной деформации.
Таблица 1.
Механические свойства сплава Э110
Состояние | σ–1, МПа | σВ, МПа | σТ, МПа | δ, % | σ–1/σВ |
---|---|---|---|---|---|
исходное | 225 | 420 ± 12 | 360 ± 10 | 20 ± 1 | 0.5 |
РКУП | 150 | 588 ± 9 | 440 ± 8 | 10.0 ± 0.5 | 0.3 |
Сравнивая комплекс механических свойств при растяжении РКУП-сплава Э110 с достигнутым ранее на сплаве Э125 [4], можно отметить, что при одинаковой пластичности, сплав Э110 обладает более низкой прочностью (предел текучести составил 440 и 700 МПа соответственно, для сплавов Э110 и Э25), несмотря на более низкую температуру РКУП (температура последнего прохода для сплава Э125 составила 350°С). При повышении температуры последнего прохода РКУП до 400°С прочностные свойства сплава Э125 понижаются (предел текучести составил 470 МПа), однако все равно остаются выше, чем у сплава Э110 после РКУП с температурой последнего прохода 300°С. Такая разница в уровне прочности между сплавами, с учетом схожей микроструктуры, может объясняться наличием в сплаве Э125 пересыщенного твердого раствора ниобия в цирконии, образовавшегося в результате РКУП из-за большего легирования ниобием слава Э125 по сравнению со сплавом Э110.
Кривые усталости в координатах “число циклов (N) – максимальное напряжение цикла (σmax)” образцов сплава Э110 в исходном состоянии и после РКУП на базе 107 циклов приведены на рис. 4, а характеристики усталостной прочности в табл. 1. Видно, что при высоких напряжениях цикла (выше 280 МПа) сплав в обоих состояниях характеризуется примерно одинаковой долговечностью. При исследовании многих материалов (железо, титан, никель и др.) было показано, что при многократном повышении статической прочности в результате РКУП, характеристики малоцикловой усталости не снижались, либо увеличивались по сравнению с состоянием до РКУП [15–17].
Однако при меньших напряжениях цикла долговечность сплава Э110 после РКУП становится меньше, чем сплава в исходном состоянии. Ограниченный предел усталости на базе 107 циклов составил 225 МПа для сплава в исходном состоянии и 150 МПа для сплава после РКУП.
Изломы образцов сплава Э110 после испытаний на усталость изучали при высоком и низком напряжениях цикла. Выбирали сопоставимые уровни напряжений для сплава в исходном состоянии и после РКУП. Таким образом, для фрактографического анализа были выбраны следующие образцы:
– сплав в исходном состоянии, σmax = 325 МПа;
– сплав в исходном состоянии, σmax = 235 МПа;
– сплав после РКУП, σmax = 350 МПа;
– сплав после РКУП, σmax = 200 МПа.
Фотографии изломов приведены на рис. 5 и 6. Все изломы имеют типичное усталостное строение. Трещина зарождалась на одной из боковых поверхностей образца, далее следует зона распространения трещины, которая сменяется зоной статического долома (рис. 5а, 5д, 6а, 6д). С уменьшением максимального напряжения цикла зона распространения трещины (т.е. зона собственно усталостного разрушения) увеличивается, а зона долома уменьшается.
Рис. 5.
Поверхность излома образца сплава Э110 в исходном состоянии для максимального напряжения цикла 325 МПа (а–г) и 235 МПа (д–з): а, д – общий вид излома (А – область зарождения трещины, Б – зона статического долома); б, е – область зарождения трещины; в, ж – область стабильного роста трещины; г, з – область статического долома.
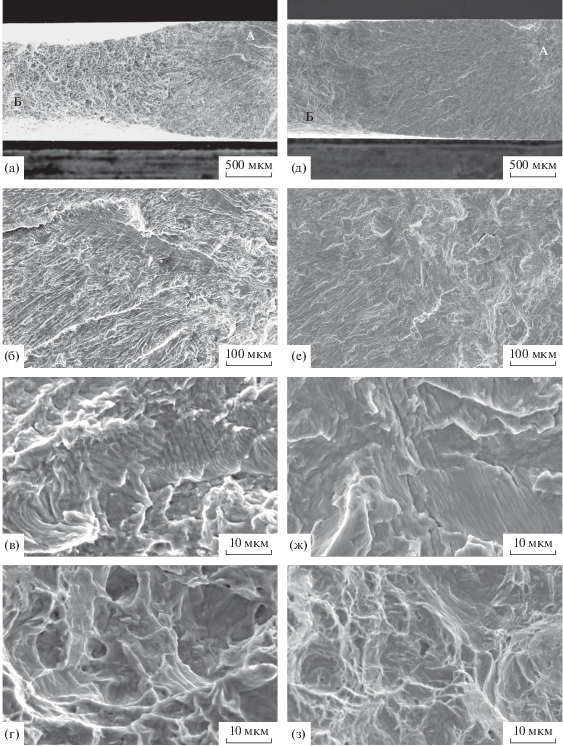
Рис. 6.
Поверхность излома образца сплава Э110 после РКУП для максимального напряжения цикла 350 МПа (а–г) и 200 МПа (д–з): а, д – общий вид излома (А – область зарождения трещины, Б – зона статического долома); б, е – область зарождения трещины; в, ж – область стабильного роста трещины; г, з – область статического долома.
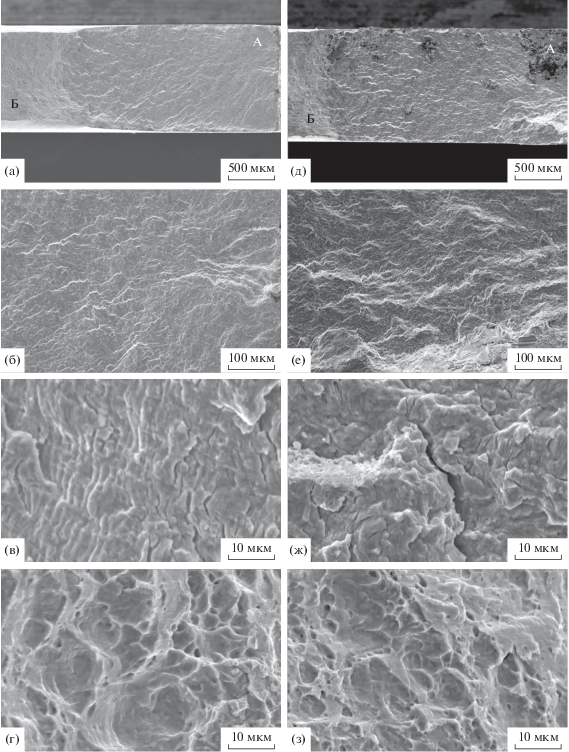
При высоком напряжении цикла зона стабильного роста усталостной трещины сплава в исходном состоянии имеет довольно развитый микрорельеф (рис. 5в). Распространение трещины происходит по квазивязкому механизму, с образованием в некоторых областях типичных вязких усталостных бороздок. Ускоренный рост усталостной трещины носит смешанный характер: области вязкого ямочного разрушения чередуются с областями бороздчатого рельефа. В зоне статического долома наблюдается смешанное квазивязкое и вязкое крупноямочное разрушение (рис. 5г).
При низком напряжении цикла характер усталостного разрушения сплава в исходном состоянии не меняется, однако расстояние между бороздками в зоне стабильного роста усталостной трещины уменьшается (рис. 5ж).
При высоком напряжении цикла зона стабильного роста усталостной трещины сплава после РКУП имеет преимущественно плоский микрорельеф (рис. 6в). Распространение трещины происходит преимущественно с образованием параллельных усталостных хрупких бороздок с интенсивным растрескиванием между ними. В зоне статического долома наблюдается типичное вязкое мелкоямочное разрушение, с существенно меньшим размером ямок, чем для сплава исходного состояния (рис. 6г).
При низком напряжении цикла в зоне стабильного роста усталостной трещины сплава после РКУП наблюдается квазихрупкий плоский микрорельеф с интенсивным растрескиванием по фронту продвижения усталостной трещины (рис. 6ж). В локальных областях наблюдаются усталостные хрупкие микробороздки с растрескиванием между ними. В зоне статического долома наблюдается вязкое мелкоямочное разрушение (рис. 6з).
Пониженное сопротивление усталостному разрушению сплава после РКУП при низком напряжении цикла можно связать с интенсивным растрескиванием материала при усталостном разрушении, т.е. с низким сопротивлением росту усталостной трещины. Подобное поведение материалов иногда встречается на практике. Так, снижение пластичности в результате РКУП и одновременное разупрочнение при циклическом деформировании наблюдалось на ряде материалов, например, на низкоуглеродистой стали (Fe–0.15% C–0.25% Si–1.15% Mn; вес. %) [18].
Полученные результаты отличаются от результатов [5], где повышение статической прочности сплава Э125 привело одновременно к повышению усталостной прочности. Это может быть связано, в частности, с различной исходной структурой сплавов, а также с разным уровнем статической прочности сплавов после РКУП. Так, РКУП сплава Э125 не привело к смене механизма усталостного разрушения, по сравнению с исходным состоянием: в обоих случаях наблюдался квазихрупкий рельеф излома [5]. Это связано с повышенной прочностью сплава Э125 в исходном состоянии. Напротив, в данном исследовании РКУП сплава Э110 привело к смене механизма усталостного разрушения с квазивязкого микробороздчатого на преимущественно хрупкий со вторичным растрескиванием, что способствовало усталостному разупрочнению.
Таким образом, проведенное исследование показало, что после РКУП сплав Э110 уступает сплаву Э125 с точки зрения достигнутого комплекса механических свойств. Тем не менее уровень статической и циклической прочности сплава Э110 после РКУП достаточно высокий, что позволяет рассматривать сплав Э110 в качестве конструкционного материала, потенциально применимого для изготовления медицинских имплантатов. При этом сплав Э110 обладает лучшей технологичностью по сравнению со сплавом Э125, что позволяет проводить его деформационную обработку при более низких температурах.
ВЫВОДЫ
По результатам исследования влияния РКУП (маршрут BC, угол между каналами 110°, 6 проходов со ступенчатым понижением температуры, температура последнего прохода 300°С) на структуру, статическую и циклическую прочность циркониевого сплава Э110 (Zr–1% Nb) сделаны следующие выводы:
1. В результате РКУП в сплаве сформировалась сильно неоднородная ультрамелкозернистая микроструктура, состоящая из областей с ячейками и фрагментами с малой разориентировкой и высокой плотностью дислокаций и областей с преимущественно равноосными структурными элементами;
2. После РКУП предел прочности сплава повысился на 40%, предел текучести на 22%, а относительное удлинение уменьшилось в 2 раза;
3. РКУП вызывает снижение ограниченного предела усталости на базе 107 циклов с 225 до 150 МПа и смену механизма разрушения с квазивязкого микробороздчатого на преимущественно хрупкий со вторичным растрескиванием. Однако при высоких напряжениях цикла (выше 280 МПа) сплав как в исходном состоянии, так и после РКУП характеризуется сопоставимой долговечностью.
Исследование структуры выполнено на оборудовании ЦКП “Материаловедение и металлургия” при финансовой поддержке РФ в лице Минобрнауки (№ 075-15-2021-696).
Список литературы
Steinemann S.G. Corrosion of surgical implants – in vivo and in vitro tests, evaluation of biomaterials. N.Y.: Wiley, 1980. P. 1–34.
Фадеев А.Ю. Цирконий в ортопедической стоматологии // Медтехника и медизделия. 2002. № 4(10). С. 26–30.
Шапошников Ю.Г., Шерепо К.М., Горохов В.Ю., Берченко Г.Н. Цирконий для эксплантатов в травматологии и ортопедии // Ортопедия, травматология и протезирование. 1993. № 1. С. 31–33.
Nikulin S.A., Rozhnov A.B., Rogachev S.O., Khatke-vich V.M., Turchenko V.A., Khotulev E.S. Investigation of structure, phase composition, and mechanical properties of Zr–2.5% Nb alloy after ECAP // Materials Letters. 2016. V. 169. P. 223–226.
Терентьев В.Ф., Добаткин С.В., Никулин С.А., Копылов В.И., Просвирнин Д.В., Рогачев С.О., Банных И.О. Влияние равноканального углового прессования на усталостную прочность титана и циркониевого сплава // Деформация и разрушение материалов. 2010. № 8. С. 26–33.
Никулин С.А., Рогачев С.О., Рожнов А.Б., Копылов В.И., Добаткин С.В. Коррозионная повреждаемость при КРН-испытаниях сплава Zr–2.5% Nb, подвергнутого равноканальному угловому прессованию // Физика и химия обр. материалов. 2012. № 1. С. 74–80.
Companhoni M.V.P., Matheus J.R.G., Marcondes T.L., Pinto A.L. Analysis of microstructure and microhardness of Zr–2.5Nb processed by High-Pressure Torsion (HPT) // J. Mater. Science. 2012. V. 47. P. 7835–7840.
Zhilyaev A.P., Sabirov I., González-Doncel G., Molina-Aldareguía J., Srinivasarao B., Pérez-Prado M.T. Effect of Nb additions on the microstructure, thermal stability and mechanical behavior of high pressure Zr phases under ambient conditions // Mater. Sci. Eng. A. 2011. V. 528. P. 3496–3505.
Sklenicka V., Dvorak J., Kral P., Svoboda M., Kvapilova M., Kopylov V.I., Nikulin S.A. and Dobatkin S.V. Creep Behavior of a Zirconium Alloy Processed by Equal-Channel Angular Pressing // Acta Phys. Polonica A. 2012. V. 122. P. 485–489.
Lee B.S., Kim M.H., Hwang S.K., Kwun S.I., Chae S.W. Grain refinement of commercially pure zirconium by ECAP and subsequent intermediate heat treatment // Mater. Sci. Eng. A. 2007. V. 449–451. P. 1087–1089.
Рогачев С.О., Рожнов А.Б., Никулин С.А., Рыбальченко О.В., Горшенков М.В., Чжен В.Г., Добаткин С.В. Влияние режимов кручения под высоким давлением на структуру и упрочнение сплава Zr–1% Nb // ФММ. 2016. Т. 117. № 4. С. 385–391.
Сегал В.М., Резников В.И., Дробышевский А.Е., Копылов В.И. Пластическая обработка металлов простым сдвигом // Изв. АН СССР. Металлы. 1981. № 1. С. 115–123.
Valiev R.Z., Zhilyaev A.P., Langdon T.G. Bulk Nanostructured Materials: Fundamentals and Applications, by John Wiley & Sons, Inc., 2014. 456 p.
Терентьев В.Ф. Циклическая прочность субмикро- и нанокристаллических металлов и сплавов (обзор) // Новые материалы и технологии в металлургии и машиностроении. 2010. № 1. С. 8–24.
Sawai T., Matsuoka S., Tsuzaki K. Low-and High-cycle Fatigue Properties of Ultrafine – grained Low Carbon Steels // J. Iron and Steel Institute of Japan. 2003. V. 89. P. 726–733.
Vinogradov A., Hashimoto S., Kopylov V.I. Enhanced strength and fatigue life of ultrafine grain Fe–36Ni Invar alloy // Mater. Sci. Eng. A. 2003. V. 355. P. 277–285.
Vinogradov A., Stolyarov V.V., Hashimoto S., Valiev R.Z. Cyclic behavior of ultrafine – grain titanium produced by severe plastic deformation // Mater. Sci. Eng. A. 2001. V. 318. P. 163–173.
Kim H.K., Choi M.I., Chung C.S., Shin D.H. Fatigue properties of ultrafine grained low carbon steel produced by equal channel angular pressing // Mater. Sci. Eng. A. 2003. V. 340. P. 243–250.
Дополнительные материалы отсутствуют.
Инструменты
Физика металлов и металловедение