Физика металлов и металловедение, 2022, T. 123, № 1, стр. 47-54
Структура и свойства СВС-композита системы Cu–Ti–C–B
Н. Б. Пугачева a, *, Ю. В. Николин b, Т. М. Быкова a, Е. И. Сенаева a
a Институт машиноведения УрО РАН
620049 Екатеринбург, ул. Комсомольская, 34, Россия
b ООО “Солид Флэйм”
620075 Екатеринбург, пр. Ленина, 54, кор. 5, Россия
* E-mail: nat@imach.uran.ru
Поступила в редакцию 11.06.2021
После доработки 04.09.2021
Принята к публикации 10.09.2021
- EDN: TCBQDU
- DOI: 10.31857/S0015323022010107
Аннотация
Исследованы структура, химический и фазовый составы, твердость композита системы Cu–Ti–C–B, полученного методом самораспространяющегося высокотемпературного синтеза (СВС). Показано, что матрицей композита является твердый раствор на основе меди (γ), упрочняющие фазы – TiC и TiB2, которые неравномерно распределены в объеме композита. Области твердого раствора имеют микротвердость 450 HV 0.05, области (γ + TiC) – 760 HV 0.1, а области с преобладанием частиц TB2 (γ + TiB2) – 1042 HV 0.1. Интегральная твердость композита составляет 62 HRC. Неравномерное распределение частиц наполнителя в объеме композита обусловило неоднородность микромеханических свойств. Наиболее прочной структурной составляющей композита являются области (γ + TiB2), характеризующиеся высокими значениями модуля упругости, работы сил на упругое восстановление и условного показателя износостойкости HIT/E. По показателям абразивной износостойкости композит системы Cu–Ti–C–B не уступает композиту системы Fe–Ti–C–B. При этом шероховатость поверхности после испытаний минимальна у композита Cu–Ti–C–B, что связано с большей пластичностью твердого раствора на основе Cu. Изнашивание композита происходит по механизму пластического оттеснения.
ВВЕДЕНИЕ
Широкое применение нашли композиционные материалы и покрытия, получаемые методом самораспространяющегося высокотемпературного синтеза (СВС) [1–5]. Отличительной особенностью СВС-композитов являются высокая твердость и износостойкость. В условиях постоянного роста эксплуатационных нагрузок современной техники необходимо получение материалов с высокой конструкционной прочностью. Важным является выбор химического состава матрицы композита, которая главным образом определяет склонность к развитию трещин при нагрузках. Определенные успехи достигнуты в разработке способов получения новых СВС-композитов с регулируемым содержанием упрочняющих фаз [2, 5–7].
Известно [1], в СВС выделяют три основные стадии: горение, образование новых фаз и охлаждение продуктов горения. На стадии горения происходят экзотермические реакции, повышающие температуру порошковой смеси вплоть до температур плавления еe составляющих. Основными экзотермическими реакциями являются:
(2)
$3{\text{Ti}} + {{{\text{B}}}_{{\text{4}}}}{\text{C}} \to {\text{TiC}} + 2{\text{Ti}}{{{\text{B}}}_{2}} + Q;$Интерес представляет использование в качестве матрицы СВС-композитов меди, особенно для деталей и элементов конструкций электротехнического и теплообменного назначения. Медь обладает высокой пластичностью, а также тепло- и электропроводна [8]. Относительно невысокая температура плавления меди (1083°С) [9] позволяет обеспечить высокую сплошность формируемой структуры композитов, сближение значений их реальной и теоретической плотности после дополнительного горячего компактирования. СВС-композиты системы Cu–Ti–C–B практически не изучены. Научный и практический интерес представляет определение их химического и фазового составов, а также прочности и износостойкости. Для оценки физико-механических свойств композитов и сплавов все большее распространение получает метод инструментального индентирования, который позволяет непрерывно регистрировать кривую “нагрузка на индентор–глубина внедрения индентора” и получать количественные характеристики материала (например, твердость, модуль Юнга и др.) на различных масштабных (нано, микро и макро) уровнях [10, 11].
Цель работы – установить химический и фазовый составы монолитных СВС-композитов системы Cu–Ti–C–B, определить их пористость, плотность, твердость, микромеханические свойства и износостойкость.
МАТЕРИАЛЫ И МЕТОДЫ ИССЛЕДОВАНИЯ
Исследовали структуру, пористость, плотность и твердость композиционного материала системы Сu–Ti–C–B, полученного методом СВС в режиме безгазового твердофазного горения при постоянной скорости перемещения фронта горения. Исходными материалами для синтеза были выбраны порошки Ti, Сu, C и В4С (рис. 1). Порошки перемешивали в шаровой мельнице в течение 12 ч и засыпали в стальную трубу (марка Ст3), выполняющую одновременно роль реактора открытого типа и внешней оболочки заготовки [6, 12–14]. Затем заготовку помещали в электрическую печь и нагревали до температуры начала экзотермических реакций (1020°С).
Порошок меди формирует металлическую матрицу будущего композита. Порошки Ti, C, B4С являются термореагирующими компонентами (ТРК), обеспечивающими протекание экзотермических реакций (1), (2) и (3). Расчет процентного содержания ТРК в составе исходной смеси производится из условия осуществления реакций (1) и (2) в стехиометрических пропорциях. Доля ТРК в исходной смеси составляла 30%, в соответствии с результатами, обсужденными ранее в работе [12]. Сразу после завершения процесса синтеза заготовки подвергали горячему компактированию – прессованию на гидравлическом прессе при температуре 900°С под нагрузкой 250 МПа.
Микроструктуру, химический и фазовый составы полученного композита исследовали на поперечных резах полученных заготовок (рис. 2а) с помощью сканирующего электронного микроскопа TESCAN VEGAII XMU с энергодисперсионной и волнодисперсионной (для определения содержания бора) приставками фирмы OXFORD. Фазовый рентгеноструктурный анализ выполнен на рентгеновском дифрактометре SHIMADZU в Kα излучении хрома.
Рис.2.
Внешний вид продольного (а) и поперечного (б) резов полученной заготовки композита (стрелками отмечены поры на границе с внешней оболочкой, показана схема вырезки образцов для испытаний на абразивную износостойкость).
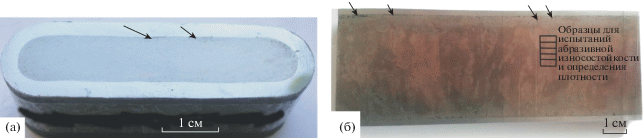
Измеряли твердость композита по Роквеллу по шкале HRC. Плотность и пористость определяли методом гидростатического взвешивания образцов (схема вырезки образцов показана на рис. 2б) на воздухе и в дистиллированной воде плотностью 998 кг/м3. Взвешивание проводили на аналитических весах Ohas Pioner PA 214. Плотность композита определяли по формуле:
где m1 – масса образца на воздухе, m2 – масса образца в воде, ρв – плотность дистиллированной воды. Погрешность составляла не более 0.2% от измеряемой величины.Микромеханические свойства композита определяли в соответствии с требованиями ГОСТ Р 8.748–2011 (ИСО 14577-1: 2002) [15]. Инструментальное микроиндентирование с записью диаграммы нагружения проводили на измерительной системе Fischerscope HM2000 XYm с использованием индентора Виккерса и программного обеспечения WIN-HCU при максимальной нагрузке 0.980 Н, времени нагружения 20 с, выдержке при нагрузке 15 с и времени разгрузки 20 с. Погрешность характеристик микротвердости и микроиндентирования по 10 измерениям рассчитывали с доверительной вероятностью p = = 0.95. По результатам интентирования определяли следующие показатели микромеханических свойств: микротвердость по Виккерсу (НV), контактный модуль упругости (Е*), составляющую работы пластической деформации при индентировании (φ), ползучесть при индентировании (СIT), показатель доли упругой деформации в общей деформации при индентировании HIT/E, где HIT – значений твердости вдавливания при максимальной нагрузке. Расчеты показателей φ и СIT проводили по следующим формулам:
(5)
$\varphi = (1 - ({{{{W}_{{\text{e}}}}} \mathord{\left/ {\vphantom {{{{W}_{{\text{e}}}}} {{{W}_{{\text{t}}}}}}} \right. \kern-0em} {{{W}_{{\text{t}}}}}})) \times 100\% ;$Испытания на износостойкость проводили на лабораторной установке по методике, описанной в работах [16, 17]. В качестве абразива использовали электрокорунд Al2O3 и карбид кремния SiC. Образцы для испытаний имели размеры 7 × 7 × × 20 мм и вырезались таким образом, что грань наибольшего размера была направлена вдоль длины заготовок (рис. 2б). Износостойкость образцов оценивали по относительному изменению массы (Δmотн), которую рассчитывали по формуле:
(7)
$\Delta {{m}_{{{\text{отн}}}}} = {{({{m}_{0}}--{{m}_{1}})} \mathord{\left/ {\vphantom {{({{m}_{0}}--{{m}_{1}})} {{{m}_{0}}}}} \right. \kern-0em} {{{m}_{0}}}},$(8)
$f = {{{{F}_{{{\text{тр}}}}}} \mathord{\left/ {\vphantom {{{{F}_{{{\text{тр}}}}}} N}} \right. \kern-0em} N};$(9)
$\varepsilon = {{\Delta m} \mathord{\left/ {\vphantom {{\Delta m} {\Delta {{m}_{{{\text{эт}}}}}}}} \right. \kern-0em} {\Delta {{m}_{{{\text{эт}}}}}}},$(11)
$W = {{fNL\rho } \mathord{\left/ {\vphantom {{fNL\rho } {\Delta m}}} \right. \kern-0em} {\Delta m}}.$Поверхность износа после испытаний исследовали с помощью оптического интерферометра-профилометра Wyko NT-1100 для определения шероховатости Ra.
РЕЗУЛЬТАТЫ ИССЛЕДОВАНИЙ И ИХ ОБСУЖДЕНИЕ
Обычно температура инициализации СВС значительно ниже температуры плавления каждого компонента исходной порошковой смеси [1, 2]. При использовании порошка меди для получения композита плавление меди начинается практически оновременно с синтезом. Очевидно, именно это объясняет отсутствие пор в центральной части сендвич-пластины после горячего компактирования. Незначительное количество пор образовалось лишь на границе с внешней стальной оболочкой (отмечены стрелками на рис. 2). После синтеза новые структурные составляющие неравномерно распределены в объеме копозита, а его макроструктура имеет слоистое строение (рис. 2б). Плотность композита составила 6.8 г/см3.
Металлическая матрица представляет собой твердый раствор на основе меди (рис. 3). По данным микрорентгеноспектрального анализа, в кристаллической решетке Cu растворено небольшое количество титана (область 1 в табл. 1). Упрочняющими фазами являются образовавшиеся в результате синтеза частицы карбида титана TiC и диборида титана TiB2. По результатам фазового рентгеноструктурного анализа в композите зафиксированы три фазы (рис. 3). Частицы серого цвета глобулярной формы или формы куба со скругленными вершинами соответствуют соединению TiC (рис. 4а), а частицы черного цвета правильной огранки соответствуют по химическому составу соединению TiB2 (рис. 4б). Частицы карбида титана TiC имеют размеры от 0.1 до 1.0 мкм, а частицы диборида титана TiB2 – от 0.5 до 3.0 мкм.
Таблица 1.
Химический состав участков, отмеченных на рис. 4, ат. %
№ | Cu | Ti | C | B |
---|---|---|---|---|
1 | 71.4 | 13.6 | 11.2 | 0 |
2 | 47.8 | 23.7 | 20.9 | 7.3 |
3 | 39.4 | 24.5 | 12.9 | 23.2 |
Рис. 4.
Микроструктура композита Cu–Ti–C–B, изображение во вторичных электронах: а – участок с преобладанием частиц карбида титана TiC; б – участок с преобладанием частиц диборида титана TiB2.
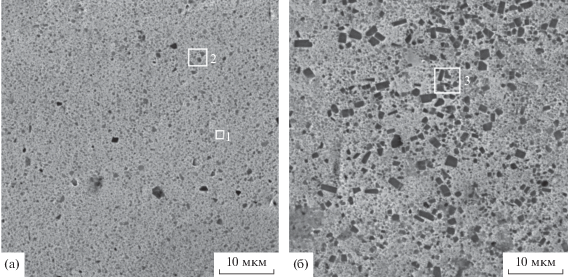
Микротвердость медной матрицы ситнезированного композита составила 450 HV0.05, что свидетельствует об еe упрочнении. Выполненные ранее исследования показали, что при охлаждении легированного титаном твердого раствора на основе меди возможно гомогенное выделение наноразмерных частиц интерметаллидов, например TiCu4 [18]. При анализе химического состава участков с минимальным количеством частиц (например, участок 1 на рис. 4а) было обнаружено, что содержание титана несколько выше, чем необходимо для образования частиц TiC (табл. 1). Поэтому нельзя исключать возможность гомогенного выделения наноразмерных частиц TiCu4 в твердом растворе.
Микротвердость участков с наибольшим количеством частиц TiC (таких, как участок 2 на рис. 4а) в среднем составляет 760 HV0.1, а участков, обогащенных частицами TiB2 (участок 3 на рис. 4б), достигает значений 1042 HV 0.1. Общая твердость композита – 60–62 HRC.
На границе композита со стальной оболочкой наблюдается диффузионное взаимодействие. Медь диффундирует в сталь на глубину 80 мкм, а титан – на глубину 20 мкм (рис. 5а). Железо из стали проникает в композит на глубину 50 мкм. Значения микротвердости в этой зоне плавно меняются (рис. 5б).
Рис. 5.
Распределение химических элементов (а) и микротвердости (б) в диффузионной зоне на границе композита и внешней стальной оболочки.
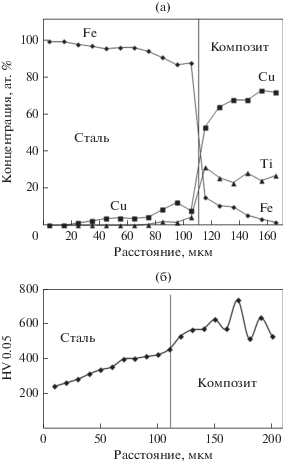
По результатам инструментального микроиндентирования (рис. 6, табл. 2) установлено, что неравномерное распределение упрочняющих фаз по объему композита обусловливает неравномерность распределения микромеханических свойств. Максимальное упрочнение наблюдается в зонах с повышенным содержанием диборида титана TiB2, таких как участок 3 на рис. 4б. Контактный модуль упругости композитов E* в областях, обогащенных частицами упрочняющих фаз, значительно увеличивается, что обусловлено наличием частиц упрчняющих фаз TiC и TiB2.
Рис. 6.
Кривые нагружения структурных составляющих композита (цифры соответствуют участкам, отмеченным на рис. 4).
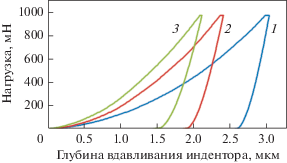
Таблица 2.
Микромеханические свойства композита Cu–Ti–C–B
№ участка на рис. 4 | HIT, ГПа (±1.5) | HV 0.1 (±1.4) | E*, ГПа (±18) | Wt, нДж (±7.3) | Wе, нДж (±1.2) | hmax, мкм (±0.2) | HIT/E* | φ, % | CIT, % |
---|---|---|---|---|---|---|---|---|---|
1 | 4.8 | 450 | 243 | 100 | 16.5 | 3.1 | 0.019 | 83.6 | 14.8 |
2 | 8.1 | 760 | 278 | 80.8 | 19.1 | 2.5 | 0.028 | 77 | 13.6 |
3 | 11.0 | 1042 | 293 | 74.5 | 21.9 | 2.2 | 0.037 | 71 | 4.7 |
В работе [19] показано, что отношение HIT/E* характеризует долю упругой деформации в общей деформации при индентировании. Кроме того, этот показатель косвенно характеризует износостойкость структурных составляющих композита [11]. Как и следовало ожидать, повышенное содержание частиц TiB2 в композите наиболее заметно повлияло на повышение этого отношения (табл. 2).
Областям (γ + TiB2) соответствует минимальное значение работы пластической деформации при индентировании (φ). Ползучесть при индентировании СIT (indentation creep) [15], характеризует склонность материала к формоизменению при постоянно действующей нагрузке. Максимальные значения СIT зафиксированы в зонах композита с минимальным содержанием упрочняющих фаз, таких как участок 1 на рис. 4а. Интересно, что области, упрочненные преимущественно частицами карбида титана TiC (участок 2 на рис. 4а), характеризуются практически такими же значениями показателя СIT, что и области без упрочняющих фаз (табл. 2).
Испытания на абразивный износ показали, что трибологические свойства композита Cu–Ti–C–B существенно превышают свойства эталона и находятся на уровне свойств композита системы Fe–Ti–C–B (табл. 3), структура которого подробно была рассмотрена ранее в работе [12]. Интенсивность изнашивания Ih одинакова для этих композитов при испытаниях по корунду и карбиду кремния (табл. 3).
Таблица 3.
Результаты испытаний на абразивную износостойкость
Тип абразива | m0, г | m1, г | Δmотн, % | Ih, 10–8 | W, кДж/см3 | ε | f | Ra, мкм |
---|---|---|---|---|---|---|---|---|
40Х (эталон) | ||||||||
Al2O3 | 7.266 | 7.067 | 2.7 | 3.6 | 18.5 | 1 | 0.65 | 2.0 |
SiC | 6.782 | 6.7 | 3.5 | 19.1 | 1 | 0.66 | 2.2 | |
CВC-композит системы Cu–Ti–C–B | ||||||||
Al2O3 | 7.925 | 7.833 | 1.1 | 1.2 | 9.7 | 0.4 | 0.45 | 1.1 |
SiC | 7.636 | 3.7 | 1.5 | 11.3 | 0.5 | 0.55 | 1.1 | |
CВC-композит системы Fe–Ti–C–B (структура описана в работе [12]) | ||||||||
Al2O3 | 7.332 | 7.242 | 1.2 | 1.2 | 9.5 | 0.3 | 0.4 | 1.3 |
SiC | 7.087 | 3.3 | 1.5 | 10.3 | 0.7 | 0.5 | 1.5 |
Удельная работа изнашивания W, относительный износ ε и коэффициент трения f немного меньше при испытаниях по корунду, чем по карбиду кремния. Шероховатость поверхности СВС-композитов в 2 раза меньше по сравнению с эталоном (табл. 3). Минимальные значения Ra зафиксированы для композита с медной матрицей. Вероятно, это обусловлено более высокой по сравнению с железом пластичностью медной матрицы, которая хорошо релаксирует возникающие в ходе испытаний на абразивную износостойкость напряжения, препятствуя появлению микросколов на границах между матрицей и частицами упрочняющих фаз (рис. 7). Рельеф поверхности износа композита системы Cu–Ti–C–B соответствует абразивному изнашиванию по механизму пластического оттеснения (царапания) в результате многократно повторяющегося деформирования медной матрицы, предложенному и подробно рассмотренном Хрущовым [20].
ЗАКЛЮЧЕНИЕ
При СВС исходных порошков Cu, Ti, C, B4C, размещенных во внутреннем объеме стальной трубной оболочки и нагретых в печи до температуры начала синтеза 1020°С, формируется единая монолитная “сэндвич-пластина”, состоящая из наружной стальной оболочки, диффузионно связанной с синтезированным внутри нее композитом. Матрицей образовавшегося после СВС-композита является твердый раствор на основе меди. Упрочняющие фазы – частицы карбида титана TiC размерами от 0.1 до 1.0 мкм и диборида титана TiB2 размерами от 0.5 до 3.0 мкм, которые неравномерно распределены по объему композита.
При выбранном соотношении исходных порошков после прессования в гидравлическом прессе при нагрузке 250 МПа при температуре 900°С в центральной части сэндвич-пластины поры отсутствовали. Плотность композита составила 6.8 г/см3. Единичные поры наблюдали только на границе композита с внешней стальной оболочкой.
Неравномерное распределение частиц упрочняющих фаз по объему композита обусловило неоднородность механических свойств отдельных структурных составляющих. Области твердого раствора с минимальным содержанием упрочняющих фаз характеризуются минимальными значениями твердости, модуля упругости, работы упругой деформации при индентировании и соотношения HIT/E* и максимальными значениями показателей пластичности: составляющей работы пластической деформации при индентировании и ползучести (indentation creep).
Трибологические свойства композита Cu–Ti–C–B находятся на уровне композита системы Fe–Ti–C–B. Изнашивание композита системы Cu–Ti–C–B происходит по механизму пластического оттеснения (царапания) в результате многократно повторяющегося деформирования медной матрицы без образования сколов и микротрещин.
Работа выполнена при поддержке гранта РНФ № 22-29-00188.
Список литературы
Амосов А.П., Боровинская И.П., Мержанов А.Г. Порошковая технология самораспространяющегося высокотемпературного синтеза материалов. М.: Машиностроение-1, 2007. 472 с.
Мержанов А.Г. Твердопламенное горение. Черноголовка: ИСМАН, 2000. 224 с.
Криволуцкий К.С., Амосов А.П., Самборук А.Р. Самораспространяющийся высокотемпературный синтез ультрадисперсных и наноразмерных порошков композиций TiC–SiC и TiC–Nb // Вестн. Самарского гос. техн. ун-та. Сер. Технические науки. 2016. Т. 51. № 3. С. 137–143.
Левашов Е.А., Рогачев А.С., Курбаткина В.В., Миксимов Ю.М., Юхвид В.И. Перспективные материалы и технологии самораспространяющегося высокотемспературного синтеза. М.: МИСиС, 2011. 377 с.
Баят О., Хаванди А.Р., Гесемзаде Р. Синтез интерметаллического соединения TiCr2 из исходно механоактивированных порошков путем их совместного кальцитермического восстановления // ФММ. 2018. Т. 119. № 5. С. 469–477.
Николин Б.В., Матевосян М.Б., Кочугов С.П., Пугачева Н.Б. Патент на изобретение № 2680489. Способ изготовления многослойной износостойкой пластины. Приоритет от 10.11.2017 до 10.11.2037.
Щукин А.С., Сычёв А.Е. Особенности строения переходной зоны NiAl/Mo, сформированной в процессе самораспространяющегося высокотемпературного синтеза // ФММ. 2019. Т. 120. № 9. С. 925–930.
Колачев Б.А., Елагин В.И., Ливанов В.А. Металловедение и термическая обработка цветных металлов и сплавов. М.: МИСиС. 2005. 432 с.
Захаров А.М. Диаграмма состояния двойных и тройных систем. М.: Металлургия, 1990. 350 с.
Головин Ю.И. Наноиндентирование и его возможности. М.: Машиностроение, 2009. 312 с.
Leyland A., Matthews A. On the Significance of the H/E Ratio in Wear Control: a Nanocomposite Coating Approach to Optimized Tribological Behavior // Wear. 2000. V. 246. P. 1–11.
Пугачева Н.Б., Николин Ю.В., Сенаева Е.И., Малыгина И.Ю. Структура СВС-композитов системы Fe–Ti–C–B// ФММ. 2019. Т. 120. № 11. С. 1174–1180.
Pugacheva N.B., Nikolin Tu.V., Malygina I. Yu., Trushina E.B. Formation of the structure of Fe–Ni–Ti–C–B composites under self-propagating hightemperature synthesis // AIP Conference Proceedings. 2018. V. 2053. P. 020013. https://doi.org/10.1063/1.5084359
Pugacheva N.B., Nikolin Yu.V., Senaeva E.I. The structure and wear resistance of a Ti–Ni–Fe–C–B composite // AIP Conference Proceedings. 2019. V. 2176. P. 020007. https://doi.org/10.1063/1.5135119
ГОСТ Р 8.748–2011 (ИСО 14577-1: 2002). Металлы и сплавы. Измерение твердости и других характеристик материалов при инструментальном индентировании. М.: Стандартинформ, 2012. 32 с.
Макаров А.В., Коршунов Л.Г., Малыгина И.Ю. Осинцева А.Л. Влияние лазерной закалки и последующей термической обработки на структуру и износостойкость цементированной стали 20ХН3А // ФММ. 2007. Т. 103. № 5. С. 536–548.
Саврай Р.А., Скорынина П.А., Макаров А.В., Осинцева А.Л. Влияние жидкостной цементации при пониженной температуре на микромеханические свойства метастабильной аустенитной стали // ФММ. 2020. Т. 121. № 10. С. 1109–1115.
Пугачева Н.Б. Сенаева Е.И. Волкова Е.Г. Макаров А.В. Горулева Л.С. Микроструктура выполненного лазерной сваркой соединения хромоникелевой стали и титанового сплава с медной вставкой // ФММ. 2019. Т. 120. № 8. С. 845–853. https://doi.org/10.1134/S0015323019080126
Petrzhik M.I., Levashov E.A. Modern methods for investigating functional surfaces of advanced materials by mechanical contact testing. //Crystallogr. Reports. 2007. V. 52. P. 966–974. https://doi.org/10.1134/S1063774507060065
Хрущов М.М., Бабичев М.А. Абразивное изнашивание. М.: Наука, 1970. 252 с.
Дополнительные материалы отсутствуют.
Инструменты
Физика металлов и металловедение