Физика металлов и металловедение, 2022, T. 123, № 1, стр. 55-62
Влияние температуры механических испытаний на свойства нанокристаллического сплава Cu–14Al–3Ni, полученного кручением под высоким давлением
А. Э. Свирид a, *, В. Г. Пушин a, b, Н. Н. Куранова a, b, Н. В. Николаева a, А. Н. Уксусников a
a Институт физики металлов УрО РАН
620108 Екатеринбург, ул. С. Ковалевской, 18, Россия
b Уральский федеральный университет им. первого Президента РФ Б.Н. Ельцина
Екатеринбург, ул. Мира, 19, Россия
* E-mail: svirid2491@rambler.ru
Поступила в редакцию 13.07.2021
После доработки 26.08.2021
Принята к публикации 03.09.2021
- EDN: XKYIUT
- DOI: 10.31857/S0015323022010132
Аннотация
Используя испытания на растяжение в комплексе с методами электронной микроскопии и рентгеновского анализа, получены данные о механических свойствах при различных температурах и характере разрушения ультрамелкозернистого (УМЗ) сплава с эффектом памяти формы Сu–14 мас. % Al–3 мас. % Ni. УМЗ-структура сплава была создана методом большой пластической деформации кручением под высоким давлением. По результатам выполненных исследований, в зависимости от температуры и скорости деформации при механических испытаниях выявлены два варианта механического поведения УМЗ-сплава. В первом случае, при умеренных температурах испытаний (300, 423, 473 К) наблюдается стадия деформации сплава в мартенситном состоянии с высоким коэффициентом упрочнения и умеренным равномерным относительным удлинением и сужением. Второй, при повышенных температурах испытаний (573 и 673 К) отличается, прежде всего, за счет динамической рекристаллизации, повышенной равномерной и, особенно, сосредоточенной пластической деформацией наряду с умеренным упрочнением.
ВВЕДЕНИЕ
Температурные, механические и другие внешние воздействия, обеспечивающие термоупругие мартенситные превращения (ТМП), позволяют реализовать целый ряд необычных и практически важных физических явлений в различных сплавах. Обусловленные ТМП циклически обратимые эффекты памяти формы (ЭПФ), гигантские сверхупругость, демпфирование, калорические эффекты (включающие магнитокалорические, электрокалорические, барокалорические, эласто-калорические), выделяют интеллектуальные (или smart) сплавы в особый отдельный класс инновационно привлекательных конструкционных полифункциональных металлических материалов, востребованных в эффективных наукоемких и экологических технологиях [1–10].
Развитие современной техники диктует создание таких smart-сплавов, которые могут быть использованы в изделиях, устройствах и механизмах в широком спектре соответствующих термосиловых и иных условий эксплуатации. Однако, критическим недостатком большинства поликристаллических smart-материалов (за исключением бинарных сплавов никелида титана) являются их низкая пластичность и хрупкость, которые не позволяют реализовать присущие им уникальные эффекты не только в циклическом многократном, но даже в однократном применении. Поэтому все более важными становятся задачи разработки методов получения, выбора оптимального легирования и термомеханической обработки различных поликристаллических smart-материалов с целью их пластификации для последующего разнообразного индустриального применения.
К таким экономически перспективным материалам относятся медные β-сплавы с ТМП и ЭПФ систем Cu–Al–Ni, Cu–Zn–Al и других, которые имеют гораздо меньшую стоимость, лучшие тепло- и электропроводность, технологическую обрабатываемость по сравнению с сплавами никелида титана [2, 3, 11]. В монокристаллическом состоянии медные β-сплавы обладают превосходными характеристиками ЭПФ. Вместе с тем в обычном крупнозернистом состоянии данные поликристаллические сплавы отличают низкие пластичность, трещиностойкость, усталостная долговечность [3, 11]. Одной из ключевых причин, препятствующих практическому использованию сплавов с ЭПФ, является их интеркристаллитная хрупкость [3].
Известно, что заметное улучшение прочностных и пластических характеристик сплавов с ЭПФ на основе никелида титана достигается при формировании ультрамелкозернистой (УМЗ) структуры [12]. УМЗ-структура в данных сплавах в научных исследованиях обеспечивается применением прогрессивных термо-деформационных технологий на основе ряда методов большой пластической деформации, в том числе прессованием или кручением под высоким давлением (КВД), а в практике – многопроходной прокаткой или волочением в полосу, стержни и проволоку.
В наших недавних работах [12–17] было также обнаружено существенное ослабление охрупчивания медных сплавов с ЭПФ, достигаемое за счет радикального уменьшения при большой пластической деформации размера зерен и увеличения протяженности их границ. Различные иные способы с использованием легирующих добавок, термообработки, быстрой закалки, порошковой металлургии и ряда других оказались безуспешными и не обеспечивали заметного измельчения зеренной структуры данных сплавов и улучшения их пластичности [18–27]. Поскольку механическое поведение медных УМЗ-сплавов с ЭПФ в широком интервале температур не было изучено, в данной работе предпринято исследование влияния температуры механических испытаний на фазовый состав, структуру и механические свойства УМЗ-сплава с ЭПФ системы Cu–Al–Ni.
МАТЕРИАЛ И МЕТОДЫ ИССЛЕДОВАНИЯ
Сплав номинального химического состава Сu–14 мас. % Al–3 мас. % Ni, находящийся в аустенитном состоянии при комнатной температуре (КТ), был выплавлен из высокочистых компонентов Cu, Al, Ni (чистотой 99.99%). По данным спектрального анализа он содержит 13.95% Al, 3.02% Ni, ост. Cu в мас. %. Слиток сплава был подвергнут при 1173–1273 К горячей ковке в пруток сечением 20 × 20 мм и закалке в воде от 1223 К, 10 мин. Для измельчения зеренной структуры сплава был применен метод КВД при 6 ГПа на 10 оборотов при КТ в плоских бойках c “лункой” (цилиндрическим углублением в нижнем бойке), выполненных из металлокерамики типа ВК-6 (92 HRC). Образцы для КВД были изготовлены в форме дисков диаметром 20 мм исходной толщиной 1.2 мм. После КВД на 10 оборотов их толщина уменьшилась до 0.5 мм. При этом истинная деформация на половине радиуса составила 6 единиц. Плоские образцы для механических испытаний на растяжение вырезали на электроискровом станке. Образцы длиной 10.0, толщиной 0.25, шириной 1.0 и длиной 4.5 мм рабочей части вырезали поперек на половине радиуса исходного диска. Поверхность образцов перед испытанием полировали алмазной пастой. Скорость испытаний Vисп составляла 10–3 и 10–4 1/с. Критические температуры начала (Ms, As) и конца (Mf, Af) прямого (Ms, Mf) и обратного (As, Af) ТМП определяли при циклических температурных измерениях магнитной восприимчивости (в циклах “охлаждение–нагрев–охлаждение”) χ(T) и электросопротивления ρ(T) со скоростью, близкой 5 К/мин (табл. 1). Структуру и фазовый состав изучали методами рентгеновской дифрактометрии (РД), оптической металлографии (ОМ), просвечивающей (ПЭМ) и растровой электронной микроскопии (РЭМ). РД выполняли в монохроматизированном медном излучении Kα. Использовали ПЭМ Tecnai G2 30 при ускоряющем напряжении 300 кВ, РЭМ Quanta 200, оснащенный системой Pegasus, при ускоряющем напряжении 30 кВ. Измерения микротвердости по Виккерсу (HV) проводили на приборе Micromet 5101 с пирамидальным алмазным индентором при нагрузке 1 Н.
РЕЗУЛЬТАТЫ ИССЛЕДОВАНИЙ
Изученный литой и кованый медный β-сплав при последующем охлаждении на воздухе слитка или поковки испытывает распад по схеме β → β1 + + γ2 (при температурах выше TЭР, близкой 840 К) и эвтектоидный распад β1 → α + γ2 (при температурах ниже TЭР) (рис. 1а), что согласуется с известными данными [2].
Рис. 1.
РЭМ-изображение в обратно рассеянных электронах (a), ОМ-изображение (б) и ПЭМ-изображение (в) структуры сплава Cu–14Al–3Ni в литом (a) и закаленном аустенитном (б, в) состояниях.
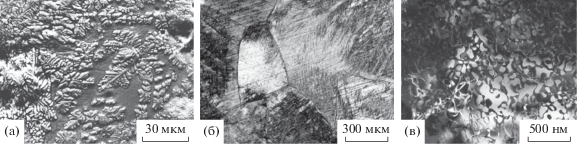
Однако закалка сплава после горячей ковки может предотвратить эвтектоидный распад (рис. 1б). Известно, что β-аустенит даже при закалке в процессе быстрого охлаждения при температурах выше TЭР и Ms успевает испытать два последовательных фазовых структурных перехода “беспорядок–порядок” (β → β2(B2) → β1(D03)) [3]. При этом вследствие многозародышевого механизма перехода образуется особая субструктура антифазных доменов, визуализируемых по появлению их границ (АФГ) на темнопольных ПЭМ-изображениях в сверхструктурных отражениях (рис. 1в). Поскольку дальний атомный порядок упорядоченной аустенитной фазы наследуется мартенситом при ТМП, это обеспечивает реализацию эффектов ориентационной кристаллоструктурной обратимости и фазовой термоупругости в сплавах [1–6].
По данным РД в закаленном β1-сплаве при температурах ниже Ms, близкой 250 К (табл. 1) появляются две мартенситные фазы: $\beta _{{\text{1}}}^{'}$ (18R) (с параметрами длиннопериодной моноклинной решетки, близкими a = 0.4450 нм, b = 0.5227 нм, c = 3.8050 нм, β = 91.0°) и γ' (2H) (c параметрами орторомбической решетки, близкими a = = 0.4390 нм, b = 0.5190 нм, c = 0.4330 нм). Установлено, что КВД на 10 оборотов при КТ вызывает деформационное ТМП с образованием смеси трех мартенситных фаз α', $\beta _{{\text{1}}}^{'}$ и $\gamma _{{\text{1}}}^{'}.$ Обнаруживаемые при этом брэгговские отражения существенно уширены (с полушириной линий до 2 град), и совпадают с наиболее сильными линиями данных мартенситных фаз.
ПЭМ-исследования показали, что в результате КВД на 10 оборотов в сплаве Cu–14Al–3Ni сформировалась однородная нанозеренная мартенситная структура, характеризуемая кольцевым распределением рефлексов на микроэлектронограммах (см. рис. 2). Из количественного анализа светло- и темнопольных ПЭМ-изображений микроструктуры сплава после КВД на 10 оборотов следует, что размеры наблюдаемых произвольно ориентированных наноразмерных зерен варьируются в пределах от 10 до 80 нм и составляют в среднем 30 нм. Видно, что в более крупных из них присутствуют пластинчатые нанодвойники. Расшифровка электронограмм также показала, что полученная в сплаве нанокристаллическая структура преимущественно содержит $\beta _{{\text{1}}}^{'}$- и $\gamma _{{\text{1}}}^{'}$-мартенситные фазы. Кольцевое распределение рефлексов указывает на наличие нанофаз, образующих разориентированную ультрамелкозернистую структуру.
Рис. 2.
Светло- (а) и темнопольное (б) ПЭМ-изображения микроструктуры и соответствующая микроэлектронограмма (в) сплава Cu–14Al–3Ni после закалки от 1223 К и КВД на 10 оборотов.
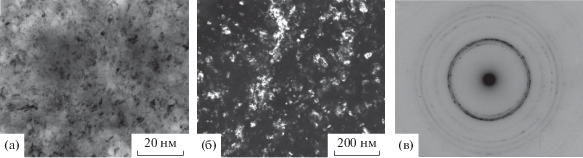
Испытания механических свойств КВД-сплава на растяжение при двух скоростях Vисп 10–3 1/с (рис. 3а) и 10–4 1/с (рис. 3б) были выполнены в широком диапазоне температур 300–673 К ниже ТЭР (рис. 3, табл. 2). Оказалось, что механическое поведение УМЗ-сплава в мартенситном состоянии (кривые 1 – при 300 К; 2, 5 – при 423К; 6 – при 473К) и в аустенитном (кривые 3, 7 – при 573 К и 4, 8 – при 673 К) отличается радикально. Кривые “напряжение σ – деформация δ” аустенитного УМЗ-сплава при повышенных температурах 573 и 673 К характеризуются наличием нескольких типичных стадий деформации: упругой (I), псевдоупругой с участком или площадкой фазовой текучести (II, на кривых 3, 4), равномерной (III, вплоть до предела прочности σв) и двух локализованных (IV и V) вначале с постепенным и затем с ускоренным разупрочнением в формирующейся клиновидной области “шейки” разрывных образцов. Кривые “σ–δ” УМЗ-сплава в мартенситном состоянии при более низких температурах испытаний (300–473 К) отличаются, во-первых, прогрессирующим по мере увеличения степени деформации упрочнением dσ/dεм, что определяет необычный вид их упругой и псевдоупругой стадий (I и II). Затем от предела текучести σ0.2 следует стадия III равномерной деформации. Другим ярким отличием является отсутствие стадий локализованной деформации (IV, V), очевидно вследствие иного механизма пластической деформации и отсутствия эффекта разупрочнения в мартенситном сплаве.
Рис. 3.
Условные кривые “напряжение–деформация” сплава Cu–14Al–3Ni, полученные после КВД на 10 оборотов при Vисп 1 × 10–3 1/с при температурах: 300 (кривая 1), 423 (2); 573 (3); 673 К (4) (а) и при Vисп 10–4 1/с при 423 (5); 473 (6); 573 (7); 673 К (8) (б). Обозначены стадии деформации I–V.
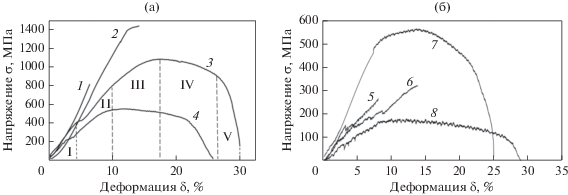
Таблица 2.
Результаты механических испытаний на растяжение при повышенных температурах УМЗ-сплава Cu–14Al–3Ni, полученного КВД на 10 оборотов
№ | Т испытания, К | Скорость, 1/с | σв, МПа | σ0.2, МПа | dσ/dεм, ГПа | σм, МПа | δр, % | δс1, % | δс2, % | δ, % | εм, % |
---|---|---|---|---|---|---|---|---|---|---|---|
1 | 300 | 10-3 | 800 | – | 20.0 | – | 5 | – | – | 5 | – |
2 | 423 | 10–3 | 1450 | 1000 | 12.8 | – | 6 | – | – | 6 | – |
3 | 573 | 10–3 | 1100 | 800 | 5.3 | 400 | 8 | 9 | 3 | 20 | 1.5 |
4 | 673 | 10–3 | 580 | 400 | 3.2 | 200 | 6 | 10 | 4 | 20 | 1.5 |
5 | 423 | 10–4 | 280 | 200 | 4.0 | 100 | 6 | – | – | 6 | 1.5 |
6 | 473 | 10–4 | 320 | 280 | 2.7 | 150 | 11 | – | – | 11 | 2.0 |
7 | 573 | 10–4 | 570 | 470 | 1.7 | – | 6 | 9 | 3 | 18 | – |
8 | 673 | 10–4 | 170 | 60 | 1.6 | – | 10 | 15 | 2 | 27 | – |
Как известно, наблюдаемая на диаграммах “σ–ε” при пониженной Vисп площадка фазовой текучести, начало которой идентифицируется напряжением σм, обусловлена сдвиговой переориентацией мартенситных кристаллов в направлении действующей силы при температурах ниже Аf. При несколько более высоких температурах (выше Аs вплоть до Md – температуры деформационного мартенситного превращения) площадка фазовой текучести определяется в основном активацией собственно деформационно-индуцированного механизма ТМП.
Итак, УМЗ-сплав Cu–14Al–3Ni при КТ и 423 К деформируется с высоким коэффициентом деформационного упрочнения при умеренной равномерной деформации и разрушается до начала процесса локализации пластической деформации. С повышением температуры деформации до 573 и 673 К, напротив, инженерные кривые растяжения приобретают обычный вид кривых растяжения для сталей и сплавов (рис. 3). При повышенных температурах растет величина сосредоточенной деформации δс и снижается величина равномерной пластической деформации δр УМЗ-сплава Cu–14Al–3Ni (табл. 2).
Площадка фазовой текучести, наблюдаемая в процессе растяжения при 423 и 473 К образцов сплава Cu–14Al–3Ni, отсутствует при повышенных температурах деформации 573 и 673 К в случае испытаний со скоростью деформации 10–4 1/с, поскольку деформация проходит в стабильном аустените (выше температуры Аf и Md; рис. 3б, кривые 7, 8) и не способна индуцировать ТМП (в отличие кривых 5 и 6 на рис. 3). Однако, площадка появляется в случае увеличения Vисп на порядок, т.е. до 10–3 1/с (кривые 3, 4 на рис. 3а). При этом εм составляет 1–2%.
Интересно также отметить, что в процессе растяжения УМЗ-сплава при температуре 573 К достигается высокая пластичность при достаточно высоком напряжении течения σ0.2 и интенсивном падении напряжения на стадии локализации деформации δс. Возможно, это связано с осуществлением механизма зернограничного проскальзывания в УМЗ-сплаве Cu–14Al–3Ni. Однако сплав не проявил сверхпластического поведения при выбранных температурах и скоростях деформации. Это можно объяснить заметным динамическим ростом зерен при повышенных температурах испытаний.
Как известно, с ростом размера зерен затрудняется зернограничное проскальзывание, являющееся необходимым условием сверхпластичности. Снижение Vисп с 10–3 до 10–4 1/с приводит к снижению временного сопротивления σв и предела текучести σ0.2 более, чем вдвое при сохранении пластичности (табл. 2). Это можно объяснить, как влиянием снижения скорости деформации, так и большей длительностью испытаний при повышенных температурах, что соответственно, приводит к большему росту зерен.
Для более глубокого понимания структурных изменений при испытаниях была изучена микроструктура после статического отжига КВД-образцов при 673 К и после растяжения КВД-образцов при 673 К. Изучение микроструктуры образца после растяжения проводили в области его равномерной деформации и в шейке. УМЗ-сплав после КВД на 10 оборотов и отжига при 673 К (30 мин) имел средний размер зерен близкий 150 нм (рис. 4а). В результате пластической деформации при повышенной температуре в микроструктуре сплава произошли существенные изменения зеренной структуры. В области однородной деформации можно было наблюдать разнозернистость: как отдельные более крупные зерна размером ~450 нм, так и более мелкие – размером около 100 нм, вновь образовавшиеся в результате динамической рекристаллизации (рис. 4б). Границы крупных зерен искривлены, а сами зерна имеют форму, вытянутую, как правило, в одном из двух направлений. Очевидно, что границы вновь формирующихся зерен при динамической рекристаллизации начинают мигрировать, поглощая исходные зерна с повышенной плотностью дислокаций. В условиях механических испытаний при повышенной температуре эти зерна будут продолжать расти, а их границы – продолжать мигрировать. Поэтому, вероятнее всего, в области равномерной деформации процесс замещения деформированных зерен рекристаллизованными воспроизводится и не заканчивается вплоть до разрушения образцов. В области шейки вследствие более значительной пластической деформации произошли также и качественные изменения в микроструктуре, сформированной в результате КВД: исчезла разнозернистость, свойственная начальной стадии динамической рекристаллизации, а зерена приобрели более четкую равноосную полиэдрическую огранку (рис. 4в). В среднем, размер зерен, сформированных в результате динамической рекристаллизации при растяжении образца при 673 К, составил 250 нм, что более, чем в 1.5 раза выше, чем после статической при 673 К, 30 мин.
Рис. 4.
РЭМ-изображения микроструктуры сплава Cu–14Al–3Ni после отжига при 673 К, 30 мин (а), после деформации растяжением при температуре 673 К со скоростью Vисп = 10–4 1/с в области равномерной деформации (б) и в области локализации деформации (в).
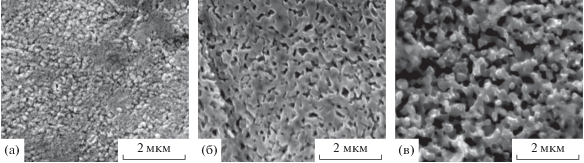
На образцах после механических испытаний растяжением была определена микротвердость HV. Измерения проводили на плоских захватах и в шейке образца после растяжения до разрушения (табл. 3). Видно, что после растяжения при КТ сплава Cu–14Al–3Ni HV в шейке образца больше, чем в области захватов, т.е. в сплаве при испытании происходят процессы упрочнения. Напротив, в УМЗ-образцах, деформированных при температуре 673 К, значения HV в шейке ниже, чем HV в области захватов. Это обусловлено тем, что в первом случае при активизации динамической рекристаллизации происходит рост зерен более интенсивно, чем при статическом отжиге без нагрузки. На протекание динамической рекристаллизации косвенно указывает и осциллирующий вид кривых на стадии пластического течения при повышенных температурах, особенно при Vисп = 10–4 1/с (рис. 3б).
Таблица 3.
Значения микротвердости HV сплава, подвергнутого КВД на 10 оборотов, в различных структурных состояниях: после статического отжига (в захватах) и после деформации растяжением при температуре испытаний (в шейке)
Обработка | Тисп, К | έ, с–1 | HV, МПа | |
---|---|---|---|---|
захваты | шейка | |||
Закалка от 1223 К | 300 | 10–3 | 3300 | 3450 |
КВД, 10 оборотов | 300 | 5650 | 6550 | |
КВД, 10 оборотов | 673 | 4600 | 3800 |
Фрактографический анализ показал, что при повышенных температурах деформации характер разрушения по деформационному и микроструктурному признакам является вязким с высокой дисперсностью ямок (или чашечек) отрыва (рис. 5б, 5г, 5е, 5з). Разрушение при повышенных температурах происходит с формированием лезвийного мелкоямочного излома во всех структурных состояниях. На изломах в области отрыва видны глубокие равноосные и продолговатые ямки. Боковая поверхность образцов после растяжения в области локализации деформации содержит равномерно распределенные линии скольжения (рис. 5а, 5в, 5д, 5ж). Таким образом, можно заключить, что характер разрушения в изучаемых сплавах зависит от структурного состояния: оно является хрупким интеркристаллитным в мартенситном исходно крупнозернистом состоянии, вязкохрупким в мартенситном УМЗ-состоянии [17] и становится квазивязким (мелкочашечным) в аустенитном УМЗ-состоянии при повышенных температурах деформации. Однако размеры ямок (или чашечек), составляя несколько микрометров, на порядок превышают средние размеры ультрамелких зерен сплава. Это обстоятельство указывает на особый интеркристаллитный, а не транскристаллитный тип вязкого разрушения, происходящего, очевидно, по большеугловым границам в УМЗ-структуре.
ВЫВОДЫ
1. Обнаружено, что сплав Cu–14Al–3Ni, подвергнутый кручению на 10 оборотов под высоким давлением 6 ГПа, сохраняя УМЗ-структуру в мартенситном состоянии в процессе механических испытаний на растяжение при 300, 423 и 473 К, обладает высокими прочностью (σв = 800–1400 МПа) и коэффициентом упрочнения, а также умеренным равномерным относительным удлинением (до 10%).
2. Установлено, что УМЗ-сплав в аустенитном состоянии при повышенных температурах испытаний 573 и 673 К характеризуется способностью за счет динамической рекристаллизации к повышенной равномерной и, особенно, сосредоточенной локализованной пластической деформации (18–27%) наряду с умеренным упрочнением (σв = = 570–580 МПа).
3. По данным фрактографических исследований УМЗ-сплав в мартенситном состоянии отличается вязко-хрупким (без шейкообразования), а в аустенитном состоянии (при повышенных температурах деформации) более вязким мелкоямочным (с развитой шейкой) разрушением интеркристаллитного типа по большеугловым границам ультрамелких зерен.
Работа выполнена по тематике госзадания № АААА-А18-118020190116-6 (“Структура”) ИФМ УрО РАН с использованием научного оборудования ЦКП ИФМ УрО РАН.
Список литературы
Perkins J. (Ed.) Shape Memory Effects in Alloys. Plenum. London: UK, 1975. 583 p.
Варлимонт Х., Дилей Л. Мартенситные превращения в сплавах на основе меди, серебра и золота. М.: Наука, 1980. 205 с.
Ооцука К., Симидзу К., Судзуки Ю., Сэкигути Ю., Тадаки Ц., Хомма Т., Миядзаки С. Сплавы с эффектом памяти формы. М.: Металлургия, 1990. 224 с.
Duering T.W., Melton K.L., Stockel D., Wayman C.M. (Eds.) Engineering Aspects of Shape Memory Alloys; Butterworth-Heineman: London, UK, 1990.
Хачин В.Н., Пушин В.Г. Кондратьев В.В. Никелид титана: Структура и свойства. М.: Наука, 1992. 160 с.
Пушин В.Г., Кондратьев В.В., Хачин В.Н. Предпереходные явления и мартенситные превращения. Екатеринбург: УрО РАН, 1998. 368 с.
Bonnot E., Romero R., Mañosa L., Vives E., Planes A. Elastocaloric effect associated with the martensitic transition in shape-memory alloys // Phys. Rev. Lett. 2008. V. 100. P. 125901.
Cui J., Wu Y., Muehlbauer J., Hwang Y., Radermacher R., Fackler S., Wuttig M., Takeuchi I. Demonstration of high efficiency elastocaloric cooling with large δT using NiTi wires // Appl. Phys. Lett. 2012. V. 101. P. 073904.
Mañosa L., Jarque-Farnos S., Vives E., Planes A. Large temperature span and giant refrigerant capacity in elastocaloric Cu–Zn–Al shape memory alloys // Appl. Phys. Lett. 2013. V. 103. P. 211904.
Sedlak P., Seiner H., Landa M., Novák V., Šittner P., Manosa L.I. Elastic Constants of bcc Austenite and 2H Orthorhombic Martensite in CuAlNi Shape Memory Alloy // Acta Mater. 2005. V. 53. P. 3643–3661.
Dasgupta R. A look into Cu-based shape memory alloys: Present Scenario and future prospects // J. Mater. Res. 2014. V. 29. № 16. P. 1681–1698.
Pushin V., Kuranova N., Marchenkova E., Pushin A. Design and Development of Ti–Ni, Ni–Mn–Ga and Cu–Al–Ni-based Alloys with High and Low Temperature Shape Memory Effects // Materials. 2019. V. 12. P. 2616–2640.
Лукьянов А.В., Пушин В.Г., Куранова Н.Н., Свирид А.Э., Уксусников А.Н., Устюгов Ю.М., Гундеров Д.В. Влияние термомеханической обработки на структурно-фазовые превращения в сплаве Cu–14Al–3Ni с эффектом памяти формы, подвергнутом кручению под высоким давлением // ФММ. 2018. Т. 119. № 4. С. 393–401.
Свирид А.Э., Лукьянов А.В., Пушин В.Г., Белослудцева Е.С., Куранова Н.Н., Пушин А.В. Влияние температуры изотермической осадки на структуру и свойства сплава Cu–14 мас. % Al–4 мас. % Ni с эффектом памяти формы // ФММ. 2019. Т. 120. С. 1257–1263.
Свирид А.Э., Пушин В.Г., Куранова Н.Н., Белослудцева Е.С., Пушин А.В., Лукьянов А.В. Эффект пластификации сплава Cu–14Al–4Ni с эффектом памяти формы при высокотемпературной изотермической осадки // Письма в ЖТФ. 2020. Т. 46. С. 19–22.
Свирид А.Э., Лукьянов А.В., Пушин В.Г., Куранова Н.Н., Макаров В.В., Пушин А.В., Уксусников А.Н. Применение изотермической осадки для мегапластической деформации beta-сплавов Cu–Al–Ni // ЖТФ. 2020. Т. 90. С. 1088–1094.
Свирид А.Э., Пушин В.Г., Куранова Н.Н., Макаров В.В., Уксусников А.Н. Влияние термообработки на структуру и механические свойства нанокристаллического сплава Cu–14Al–3Ni, полученного кручением под высоким давлением // ФММ. 2021. Т.122. № 9. С. 948–956.
Pelosin A., Riviere A. Structural and mechanical spectroscopy study of the $\beta _{{\text{1}}}^{'}$ martensite decomposition in Cu–12% Al–3% Ni (wt %) alloy // J. Alloys Compounds. 1998. V. 268. P. 166–172.
Dagdelen F., Gokhan T., Aydogdu A., Aydogdu Y., Adiguzel O. Effect of thermal treatments on transformation behavior in shape memory Cu–Al–Ni alloys // Mater. Letters. 2003. V. 57. P. 1079–1085.
Li Z., Pan Z.Y., Tang N., Jiang Y.B., Liu N., Fang M., Zheng F. Cu–Al–Ni–Mn shape memory alloy processed by mechanical alloying and powder metallurgy // Mater. Sci. Eng. A. 2006. V. 417. P. 225–229.
Suresh N., Ramamurty U. Aging response and its effect on the functional properties of Cu–Al–Ni shape memory alloys // J. Alloys Compounds. 2008. V. 449. P. 113–118.
Dar R.D., Yan H., Chen Y. Grain boundary engineering of Co–Ni–Al, Cu–Zn–Al, and Cu–Al–Ni shape memory alloys by intergranular precipitation of a ductile solid solution phase // Scripta Mater. 2016. V. 115. P. 113–117.
La Roca P., Isola L., Vermaut Ph., Malarria J. Relationship between grain size and thermal hysteresis of martensitic transformations in Cu-based shape memory alloys // Scripta Mater. 2017. V. 135. P. 5–9.
Zhang X., Zhao X, Wang F, Qingsuo L., Wang Q. Microstructure, mechanical properties and shape memory effect of Cu–Hf–Al–Ni alloys // Mater. Sci. Techn. 2018. V. 34. № 12. P. 1497–1501.
Svirid A.E., Pushin V.G., Kuranova N.N., Luk’yanov A.V., Pushin A.V., Uksusnikov A.N., Ustyugov Y.M. The structure–phase transformations and mechanical properties of the shape memory effect alloys based on the system Cu–Al–Ni // Mater. Today: Proceedings. 2017. V. 4. P. 4758–4762.
Свирид А.Э., Куранова Н.Н., Лукьянов А.В., Макаров В.В., Николаева Н.В., Пушин В.Г., Уксусни-ков А.Н. Влияние термомеханической обработки на структурно-фазовые превращения и механические свойства сплавов Cu–Al–Ni с памятью формы // Известия вузов. Физика. 2018. Т. 61. № 9. С. 114–119.
Свирид А.Э., Лукьянов А.В., Макаров В.В., Пушин В.Г., Уксусников А.Н. Влияние легирования алюминием на структуру, фазовые превращения и свойства сплавов Cu–Al–Ni с эффектом памяти формы // Челябинский физико-мат. журнал. 2019. Т. 4. С. 108–117.
Дополнительные материалы отсутствуют.
Инструменты
Физика металлов и металловедение