Физика металлов и металловедение, 2022, T. 123, № 10, стр. 1046-1053
Рост зерна при отжиге железа, деформированного при 250°С методом сдвига под давлением
К. Е. Шугаев a, М. В. Дегтярев a, Л. М. Воронова a, *, Т. И. Чащухина a
a Институт физики металлов УрО РАН
620108 Екатеринбург, ул. С. Ковалевской, 18, Россия
* E-mail: highpress@imp.uran.ru
Поступила в редакцию 24.06.2022
После доработки 20.07.2022
Принята к публикации 29.07.2022
- EDN: TAOJBW
- DOI: 10.31857/S0015323022600757
Аннотация
Методами сканирующей электронной микроскопии и дюрометрии исследована рекристаллизация чистого железа, деформированного при 250°С сдвигом под давлением. Полнота протекания динамической рекристаллизации оказывает влияние на последующую статическую рекристаллизацию: в структуре смешанного типа (образованной дислокационными ячейками и отдельными рекристаллизованными зернами) заметный рост зерна начинается при температуре на 100°С ниже, чем в субмикрокристаллической (СМК) структуре (состоящей из зерен, полученных в результате динамической рекристаллизации). Неоднородность структуры, созданной в условиях динамической рекристаллизации, обусловливает ее низкую термическую стабильность. В СМК структуре выявлена склонность к вторичной рекристаллизации.
ВВЕДЕНИЕ
Термическую стабильность структуры можно охарактеризовать температурой начала быстрого роста зерна и скоростью роста зерна при нагреве. Благодаря высокой запасенной энергии, ультрадисперсная структура деформационного происхождения в однофазных чистых металлах имеет достаточно низкую температуру рекристаллизации [1]. Но рекристаллизация может развиваться путем быстрого роста отдельных центров [2–5] либо путем совершенствования границ и формы кристаллитов в условиях низкой скорости их роста [6]. В первом случае можно говорить о низкой, а во-втором – о высокой термической стабильности ультрадисперсной структуры. Характер роста рекристаллизованного зерна зависит как от самого материала, так и от типа созданной в нем деформационной ультрадисперсной структуры, обусловленной релаксационными процессами, доминирующими при деформационно-термической обработке.
Например, в железе при деформации сдвигом под давлением при комнатной температуре может быть получена субмикрокристаллическая (СМК) структура, характеризующаяся однородным распределением дефектов и отсутствием преимущественной ориентировки микрокристаллитов и обладающая наиболее высокой термической стабильностью в сравнении со структурами других типов, которые можно получить, применив пластическую деформацию при комнатной температуре [7]. Ряд исследователей, например [8], считают, что СМК-структура формируется по механизму непрерывной динамической рекристаллизации (ДР), независимо от температуры деформации, и при отжиге такой структуры происходит непрерывная статическая рекристаллизация, приводящая к совершенствованию структуры без значительного укрупнения зерна. Другие, например [9], полагают, что механизм непрерывной ДР реализуется при температуре ниже 0.5Тпл, а при более высокой температуре – прерывистой ДР.
Большая пластическая деформация при повышенной температуре в сравнении с холодной деформацией должна приводить к формированию более совершенной зеренной структуры, образованию тройных стыков зерен, которые сдерживают рост зерна. Последнему способствует также меньшая запасенная энергия деформации. Поэтому можно ожидать достаточно высокой термической стабильности ультрадисперсной структуры железа, полученной при температуре деформации ниже 0.5Тпл. Публикации показывают интерес исследователей к большой деформации железа и низкоуглеродистых сталей при повышенной температуре [10–15]. Однако нам неизвестны результаты исследования термической стабильности такой структуры.
Целью настоящей работы явилось исследование термической стабильности при отжиге ультрадисперсной структуры чистого железа, созданной путем большой деформации сдвигом под давлением при температуре 0.3Тпл (250°С).
МЕТОДИКА ЭКСПЕРИМЕНТА
Чистое железо (99.97% Fe) деформировали при 250°С методом сдвига под высоким давлением в наковальнях Бриджмена. Подробно эксперимент описан в работе [16]. Образцы до деформации имели диаметр 5 мм и толщину 0.3 мм. Деформацию осуществляли под давлением 8 ГПа, со скоростью 0.3 об./мин. Угол поворота наковальни составил 45° и 2 × 360° (2 оборота). Истинную деформацию (е) рассчитывали с учетом угла поворота наковальни, расстояния от центра образца (оси вращения) и осадки, которая также зависела от расстояния до центра образца [7]. На расстоянии 1 мм от центра расчетные значения истинной деформации составили при угле поворота 45° – 2.2, а после 2 оборотов – 6.9. Результаты исследования сравнивали с результатами, полученными при деформации Fe того же состава сдвигом под давлением при 20°С с углом поворота наковальни 60° и 5 оборотов [7]. После поворота наковальни на 60° истинная деформация на расстояние от оси вращения 1.5 мм составила 4, а после 5 оборотов е = 7.8 [7]. Погрешность, связанная с разбросом значений толщины образцов на одинаковом расстоянии от центра, во всех случаях не превышала ∆е = ±0.2.
Деформированные образцы отжигали в вакуумной печи (10–5 Па) при температурах от 350 до 650°С с шагом 100°С. Продолжительность изотермической выдержки составляла 1 ч.
Твердость измеряли на твердомере МЕТОЛАБ 502 при нагрузке 0.5 Н по двум взаимно перпендикулярным диаметрам с шагом 0.25 мм. Значения твердости, измеренные на одинаковом расстоянии от центра образца, усредняли. Погрешность определения твердости не превышала 5%.
Структурные исследования осуществляли в плоскости сдвига с использованием сканирующего электронного микроскопа (СЭМ) QUANTA_200 Philips с приставкой EDAX/TSL для анализа дифракции обратно рассеянных электронов (EBSD) при ускоряющем напряжении 25 кВ. EBSD-анализ структуры (размеры зерен, их ориентировку, спектр углов разориентировки границ, долю рекристаллизованной структуры и плотность дислокаций) проводили на расстоянии 1.00 ± 0.25 мм от центра образца. В зависимости от размера элементов структуры изменяли шаг сканирования от 0.15 до 5 мкм. Перед EBSD-исследованием образцы подвергали шлифовке и электролитической полировке. Из рассмотрения были исключены точки с индексом конфиденциальности (CI) ниже 0.1 [17] и зерна, содержащие менее 2 пикселей. Границы с углом разориентировки меньше 15° относили к малоугловым (МУГ), а больше 15° – к большеугловым (БУГ) [18]. Средний размер зерна оценивали по методу секущих. Долю рекристаллизованной структуры определяли по данным о разбросе ориентировки в пределах зерна (GOS), к рекристаллизованным относили зерна с GOS < < 2.5° [17]. Плотность геометрически необходимых дислокаций определяли по формуле из [19]: ρGND = αθКАМ/(bx), где α – постоянная (для ОЦК α = 2), b – вектор Бюргерса (для железа 0.25 нм [20]), x – шаг сканирования, θКАМ – средняя кернел-разориентация, определенная как средний угол разориентировки между выбранной точкой (пикселем) и всеми соседними пикселями во второй координационной сфере (в рад.).
РЕЗУЛЬТАТЫ И ИХ ОБСУЖДЕНИЕ
Рис. 1.
Характеристика исходной структуры железа, деформированного при 250°С с углом поворота наковальни 45°: ориентационная карта с нанесенными БУГ (а), гистограммы распределения зерен по размерам (б) и границ по углам разориентировки (в) (СЭМ).
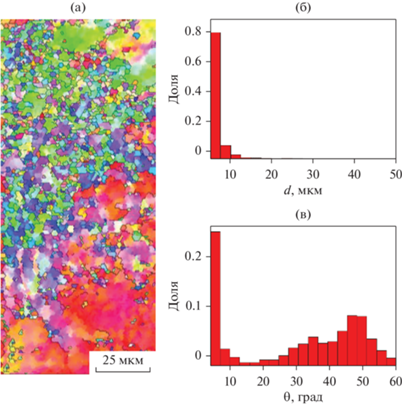
Рис. 2.
Характеристика исходной структуры железа, деформированного при 250°С на 2 оборота наковальни: а – тонкая структура (ПЭМ); б – ориентационная карта; в, г – гистограммы распределения зерен по размерам и границ по углам разориентировки соответственно (СЭМ).
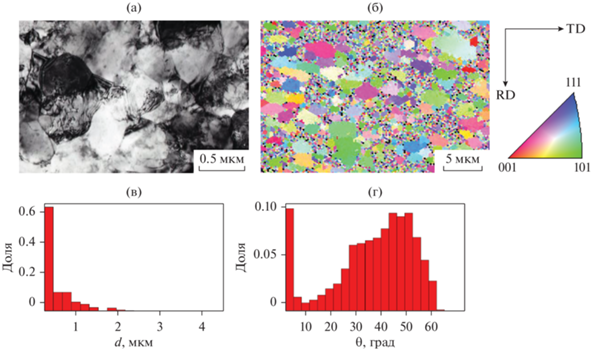
Характеристика структуры, полученной в результате деформации при повышенной температуре, представлена на рис. 1, 2. После деформации с углом поворота 45° структура очень неоднородна (рис. 1). Присутствуют области слабо-разориентированной структуры, в которой ориентировка меняется постепенно. Поскольку материал перед деформацией имел крупнозернистую структуру (средний размер зерна 200 мкм), без преимущественной ориентировки, области слаборазориентированной структуры также ориентированы произвольно. Протяженность таких областей достигает десятков микрометров (нижняя часть рис. 1а и 1б). Кроме того, наблюдаются дисперсные динамически рекристаллизованные зерна с БУГ. На гистограмме распределения элементов структуры по размерам пик в области малых размеров (около 2 мкм на рис. 1б) соответствует этим зернам. На распределении границ по углам разориентировки (рис. 1в) наблюдаются два пика: один высокий в области МУГ, соответствующий областям слабо разориентированной структуры, и второй низкий, в области больших углов, соответствующий динамически рекристаллизованным зернам. Средний угол разориентировки составляет 29°. Такую структуру смешанного типа будем в дальнейшем называть смешанной структурой, аналогично структуре, полученной в результате деформации при комнатной температуре с поворотом наковальни 60° и образованной дислокационными ячейками и микрокристаллитами [7].
После деформации на 2 оборота наковальни (е = 6.9) структура полностью состоит из динамически рекристаллизованных зерен (рис. 2а, 2б). Распределение зерен по размерам однородное, средний размер зерна составляет 0.5мкм (рис. 2в). На гистограмме распределения границ по углам разориентировки существенно увеличивается доля БУГ, но при этом пик в области МУГ сохраняется (рис. 2г). Средний угол разориентировки составляет 37°. Следует отметить, что из-за ДР при размерной однородности структуры различается дефектность отдельных зерен: присутствуют как наклепанные зерна, так и чистые зерна без дислокаций (рис. 2а). В дальнейшем эту структуру условно будем называть СМК, подобно состоящей из микрокристаллитов структуре, полученной деформацией при комнатной температуре на 5 оборотов наковальни.
На рис. 3 приведены зависимости твердости от температуры отжига железа с различной исходной структурой, созданной деформацией как при 250°С, так и при 20°С. В первом случае снижение твердости до значений твердости недеформированного железа наблюдается с увеличением температуры отжига в интервале 450–550°С, что свидетельствует о развитии рекристаллизации. При этом снижение твердости СМК-железа происходит медленнее, чем железа со смешанной структурой. В то же время СМК-структура, полученная при 20°С, такого полного разупрочнения не допускает: после отжига при 650°С, 1ч твердость остается выше твердости недеформированного железа.
Рис. 3.
Влияние отжига на твердость железа с различной исходной структурой, полученной в результате
деформации при 250°С: – смешанная (е = 2.4),
– СМК (е = 7.6). Штрихпунктирной линией обозначена твердость недеформированного железа. Для
сравнения приведены данные для железа той же чистоты, деформированного при 20°С: ◇
– смешанная структура (е = 4), ◻ – СМК структура (е = 7.8) [7].

Структурные исследования подтверждают протекание рекристаллизации в ходе отжига железа, деформированного при 250°С. На рис. 4 приведены ориентационные карты с нанесенной схемой БУГ, полученные с железа с разной исходной структурой, позволяющие качественно оценить структурные изменения при отжиге. После отжига при 350°С структура мало меняется. При более высокой температуре наблюдается рост зерна для обоих исходных состояний. После отжига СМК-структуры при максимальной температуре выявляется разнозернистость.
Рис. 4.
Микроструктура железа с разной исходной структурой, полученной в результате деформации при 250°С, после отжига при 350 (а, б), 450 (в, г), 650°С (д, е); смешанная структура (а, в, д) и СМК структура (б, г, е). Ориентационные карты с нанесенными БУГ. (СЭМ).
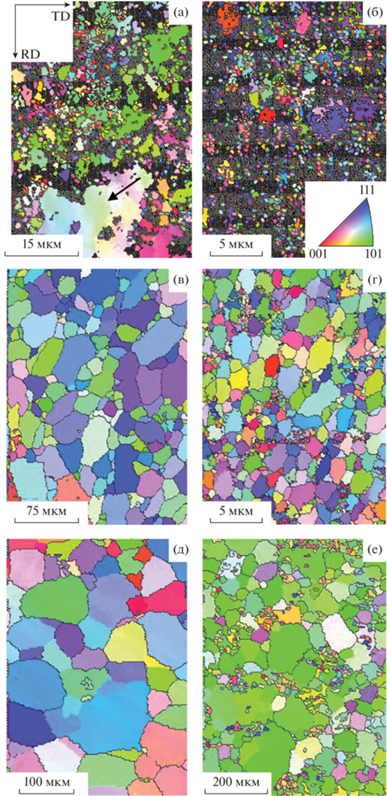
Количественные характеристики структуры приведены в табл. 1. Видно, что в результате отжига при 350°С в исходной смешанной структуре в два раза возрастает доля БУГ (до 85%) и, соответственно, растет средний угол разориентировки зерен (Ɵср). В исходной СМК-структуре доля БУГ изначально больше 90% (рис. 2г, табл. 1). Средний и максимальный размер зерна в обоих случаях уменьшаются. Следовательно, формируются новые мелкие зерна, вероятно, в результате термически активируемого зарождения, т.е. можно говорить о начале статической рекристаллизации при 350°С.
Таблица 1.
Параметры структуры железа после деформации при 250°С с разными углами поворота наковальни и отжига при различных температурах
Параметр | Температура отжига, °С | |||||||||
---|---|---|---|---|---|---|---|---|---|---|
до отжига | 350, 1 ч | 450, 1 ч | 550, 1 ч | 650, 1 ч | ||||||
45° | 2 об. | 45° | 2 об. | 45° | 2 об. | 45° | 2 об. | 45° | 2 об. | |
Доля БУГ, % | 44 | 92 | 88 | 92 | 81 | 89 | 82 | 87 | 80 | 83 |
dср, мкм | 2.5 | 0.5 | 0.6 | 0.2 | 14 | 0.8 | 20 | 9 | 38 | 27 |
Максимальный размер зерна, мкм | 50 | 4 | 19 | 3 | 64 | 4,4 | 82 | 37 | 150 | 175 |
Ɵср, град | 29 | 38 | 37 | 38 | 31 | 37 | 33 | 35 | 34 | 35 |
ρGND, х1013 м–2 | 0.52 | 1.4 | 1.9 | 3.7 | 0.09 | 0.93 | 0.09 | 0.09 | 0.05 | 0.03 |
Доля рекристаллизованной структуры, % | 38 | 49 | 43 | 49 | 93 | 98 | 96 | 97 | 100 | 96 |
Доля площади, занятой зернами размером >5dср, % | 0 | 0 | 0 | 0 | 0 | 0 | 0 | 0 | 0 | 8 |
При этой температуре нерекристаллизованная структура сохраняется (отмечена стрелкой на рис. 4а). Доля рекристаллизованной структуры, определенная по данным GOS-анализа, по сравнению с исходным состоянием (деформация при 250°С) мало меняется после такого отжига и составляет около 40 и 50% в исходно смешанной и СМК-структурах соответственно (табл. 1). При этом средний размер рекристаллизованного зерна достигает соответственно 0.6 и 0.2 мкм. Следует отметить, что формирование новых зерен сопровождается повышением плотности геометрически необходимых дислокаций (табл. 1). Завершение рекристаллизации наблюдается после отжига при 450°С, 1 ч (рис. 4в, 4г, табл. 1), когда по данным GOS-анализа доля рекристаллизованной структуры превышает 90%, а плотность дислокаций резко снижается. Однако в структуре сохраняются МУГ (рис. 5), средний угол разориентировки зерен не достигает значения, характерного для случайного ансамбля зерен (40° [18]). Вид гистограмм распределения границ по углам разориентировки (рис. 5а, 5г) после отжига при 350°С для обеих исходных структур железа близок к виду распределения, свойственному случайному ансамблю зерен, но на них присутствует одиночный пик в области малых углов до 5°. С увеличением температуры отжига в железе со смешанной структурой доля МУГ снижается, и на гистограмме распределения после отжига при 650°С наблюдаются два пика в области 15° и 40° (рис. 5в). В СМК-железе с повышением температуры отжига гистограммы все больше отклоняются от вида, свойственного случайному ансамблю зерен: снижается доля границ с углами разориентировки больше 30°, и распределение “размывается”. Это может быть связано с развитием текстуры рекристаллизации. Формирование преимущественной ориентировки видно и на рис. 4е – большинство зерен на ориентационной карте имеют одинаковый цвет.
Рис. 5.
Гистограммы распределения границ по углам разориентировки после отжига железа, деформированного при 250°С; тип исходной структуры: а–в – смешанная, г–е – СМК; а, г – 350, б – 450, в, д – 550, е – 650°С.
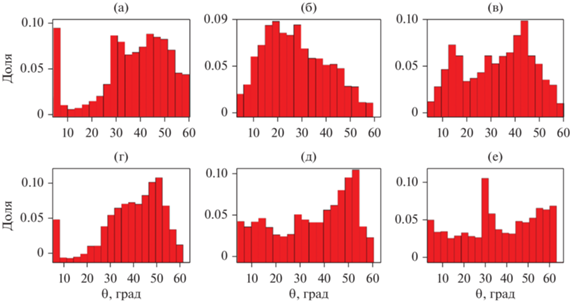
Изменение при отжиге среднего размера рекристаллизованного зерна приведено на рис. 6. Видно, что предшествующая деформация оказывает значительное влияние как на температуру начала роста зерна, так и на конечный размер зерна после отжига. В образцах железа со смешанной структурой заметное укрупнение зерна наблюдается после отжига при температуре 450°С, а в образцах СМК-железа – только после 550°С. При отжиге СМК-железа во всем исследованном интервале температур формируется более мелкое зерно, чем при отжиге железа со структурой смешанного типа.
Рис. 6.
Изменение при отжиге среднего размера зерна железа с различной исходной структурой,
полученной в результате деформации при 250°С, по данным СЭМ исследований. – смешанная (е = 2.2),
– СМК (е = 6.9). Для сравнения приведены данные для железа той же чистоты, деформированного
при 20°С: ◇ – смешанная структура (е = 4), ◻ – СМК структура (е = 7.8) [7].
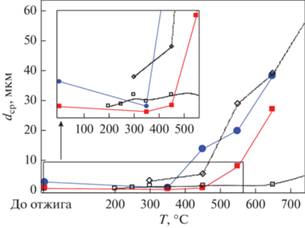
Однако в ходе отжига СМК-железа при 650°С происходит резкий рост отдельных зерен, и их максимальный размер даже превышает соответствующую характеристику для железа с исходно смешанной структурой (табл. 1). В этом случае доля площади, занятой зернами с размером >5dcp составляет 8%, что свидетельствует о склонности данной структуры к вторичной рекристаллизации. Остальные режимы отжигов не приводят к появлению зародышей вторичной рекристаллизации (табл. 1).
СМК-структура железа, сформированная деформацией при комнатной температуре, обладает значительно большей термической стабильностью (меньшей склонностью к росту зерна при нагреве), чем структура смешанного типа, полученная в тех же температурных условиях (рис. 6). Повышение температуры деформации до 250°С нивелирует различие в поведении таких структур при последующем отжиге: различие в размере рекристаллизованного зерна при отжиге в одинаковых условиях существенно меньше.
Более того, СМК-структура, полученная при повышенной температуре, проявляет склонность ко вторичной рекристаллизации, что говорит о ее низкой термической стабильности.
ВЫВОДЫ
1. В железе СМК-структура, полученная в результате деформации при 250°С, обладает низкой термической стабильностью по сравнению с СМК-структурой, полученной при комнатной температуре. Это обусловлено неоднородностью структуры, созданной в условиях динамической рекристаллизации. В СМК структуре, сформированной при 250°С, выявлена склонность к вторичной рекристаллизации.
2. Полнота протекания динамической рекристаллизации при деформации сдвигом под давлением оказывает влияние на статическую рекристаллизацию: в смешанной структуре заметный рост зерна начинается на 100°С ниже, чем в СМК-структуре.
3. Тип структуры, полученной в результате деформации при 250°С, не влияет на температуру начала статической рекристаллизации. При 350°С наблюдается появление термически активируемых центров рекристаллизации, что, приводит к уменьшению среднего размера зерна и повышению плотности геометрически необходимых дислокаций. Кроме того, в структуре смешанного типа доля БУГ увеличивается до 90%.
Работа выполнена в рамках государственного задания МИНОБРНАУКИ России (теме “Давление” № 122021000032-5). Работа выполнена с использованием оборудования ЦКП “Испытательный центр нанотехнологий и перспективных материалов” ИФМ УрО РАН. Авторы благодарят Н.В. Николаеву и В.П. Пилюгина за помощь в проведении эксперимента.
Список литературы
Yang Cao, Song Ni, Xiaozhou Liao, Min Song, Yuntian Zhu. Structural evolutions of metallic materials processed by severe plastic deformation // Mater. Sci. Eng.: R. 2018. V. 133. P. 1–59.
Маркушев М.В., Мурашкин М.Ю. Структура и механическое поведение алюминиевого сплава АМг6 после интенсивной пластической деформации и отжига. I. Особенности зеренной структуры и текстуры // ФММ. 2001. Т. 91. № 5. С. 97–102.
Чувильдеев В.Н., Копылов В.И., Нохрин А.В., Макаров И.М., Малашенко Л.М., Кукареко В.А. Рекристаллизация в микрокристаллической меди и никеле, полученных методами РКУ прессования. I. Структурные исследования. Эффект аномального роста // ФММ. 2003. Т. 96. Вып. 5. С. 51–60.
Ghosh P., Renk O., Pippan R. Microtexture analysis of restoration mechanisms during high pressure torsion of pure nickel // Mater. Sci. Eng. A. 2017. V. 684. P. 101–109.
Fuping Yuan, Ping Jiang, Xiaolei Wu. Annealing and strain rate effects on the mechanical behavior of ultrafine-grained iron produced by SPD. // Theoret. Appl. Mechan. Letters. 2011. V. 2. P. 021002.
Дегтярев М.В., Воронова Л.М., Губернаторов В.В., Чащухина Т.И. О термической стабильности микрокристаллической структуры в однофазных металлических материалах // ДАН. 2002. Т. 386. № 2. С. 180–183.
Воронова Л.М., Дегтярев М.В., Чащухина Т.И. Рекристаллизация ультрадисперсной структуры чистого железа, сформированной на разных стадиях деформационного наклепа // ФММ. 2007. Т. 104. № 3. С. 275–286.
Sakai T., Belyakov A., Kaibyshev R., Miura H., Jonas J.J. Dynamic and post-dynamic recrystallization under hot, cold and severe plastic deformation conditions // Progress in Mater. Sci. 2014. V. 60. P. 130–207.
Huang K., Logé R.E. A review of dynamic recrystallization phenomena in metallic materials // Mater. Design. 2016. V. 111. P. 548–574.
Vorhauer A., Pippan R. On the Onset of a Steady State in Body-Centered Cubic Iron during Severe Plastic Deformation at Low Homologous Temperatures // Metall. and Mater. Trans. A. 2008. V. 39. P. 417–429.
Aleshin A.N., Arsenkin A.M., Dobatkin S.V. Study of Grain Growth Kinetics in Submicrocrystalline Armco-Iron // Mater. Sci. Forum. 2007. V. 550. P. 465–470.
Добаткин С.В., Шагалина С.В., Слепцов О.И., Красильников Н.А. Влияние исходного состояния низкоуглеродистых сталей на формирование наноразмерной структуры при пластической деформации кручением с большими степенями и давлением // Металлы. 2006. № 5. С. 95–104.
Jiang-li Ning, Courtois-Manara E., Kurmanaeva L., Ganeev A.V., Valiev R.Z., Kübel C., Ivanisenko Y. Tensile properties and work hardening behaviors of ultrafine grained carbon steel and pure iron processed by warm high pressure torsion // Mater. Sci. Eng. A. 2013. V. 581. P. 8–15.
Muñoz J.A., Higuera O.F., Benito J.A., Bradai Dj., Khelfa T., Bolmaro R.E., J.Jr A.M., Cabrera J.M. Analysis of the micro and substructural evolution during severe plastic deformation of ARMCO iron and consequences in mechanical properties // Mater. Sci. Eng. A. 2019. V. 740–741. P. 108–120.
Narayana Murty S.V.S., Torizuka S., Nagai K., Koseki N., Kogo Y. Classification of microstructural evolution during large strain high Z deformation of a 0.15 carbon steel // Scripta Mater. 2005. V. 52. P. 713–718.
Дегтярев М.В., Пилюгин В.П., Чащухина Т.И., Воронова Л.М. Структура железа, деформированного кручением под давлением при 250°С // ФММ. 2019. Т. 120. С. 1292–1298.
Bernardi H.H., Sandim H.R.Z., Zilnyk K.D., Verlinden B., Raabe D. Microstructural Stability of a Niobium Single Crystal Deformed by Equal Channel Angular Pressing // Materials Research. 2017. V. 20. P. 1238–1247.
Humphreys F.J. Review grain and subgraincharacterisation by electron backscatter diffraction // J. Mater. Sci. 2001. V. 36. P. 3833–3854.
Moussa C., Bernacki M., Besnard R., Bozzolo N. About quantitative EBSD analysis of deformation and recovery substructures in pure Tantalum// IOP Conf. Series: Mater. Sci. and Eng. 2015. V. 89. P. 012038.
Duan J., Wen H., Zhou C., Islamgaliev R., Li X. Evolution of microstructure and texture during annealing in a high-pressure torsion processed Fe–9Cr alloy // Materialia. 2019. V. 6. P. 100349.
Дополнительные материалы отсутствуют.
Инструменты
Физика металлов и металловедение