Физика металлов и металловедение, 2022, T. 123, № 11, стр. 1195-1202
Сравнительное исследование коррозионно-электрохимических свойств и микроструктуры высокоазотистых сталей
Д. С. Кушнерева a, b, *, О. О. Гавриленко c, Е. В. Галанова c, Е. М. Борисова c, С. М. Решетников a, c, М. Д. Кривилев a, c
a Удмуртский федеральный исследовательский центр УрО РАН
426067 Ижевск, ул. Т. Барамзиной, 34, Россия
b ОАО “Научно-исследовательский институт металлургической технологии”
426010 Ижевск, ул. Азина, 2, Россия
c Удмуртский государственный университет
426034 Ижевск, ул. Университетская, 1, Россия
* E-mail: d.kushnereva@yandex.ru
Поступила в редакцию 30.06.2022
После доработки 08.09.2022
Принята к публикации 03.10.2022
- EDN: RRPAWE
- DOI: 10.31857/S0015323022600800
Аннотация
Нержавеющие стали обладают высокой коррозионной стойкостью в различных средах, в том числе и в кислых. Пассивация таких сталей происходит за счет плотного оксидного слоя шпинельного типа, который самопроизвольно образуется на поверхности. В настоящей статье проведены экспериментальные исследования микроструктуры трех нержавеющих сталей: ВНС53, новой ВНС53-М, легированной ниобием и ванадием и 08Х18Н10Т, выбранной в качестве базовой для сравнения экспериментальных данных. Полученные данные сопоставлены с результатами коррозионно-электрохимических исследований. Показано, что в испытанных электролитах не наблюдается существенного снижения коррозионной стойкости указанных сталей. Данный результат особенно важен для высокоазотистой нержавеющей стали марки ВНС53-М, имеющей сложное легирование, приводящее к формированию карбидных и нитридных фаз в структуре материала.
ВВЕДЕНИЕ
В настоящее время такие отрасли народного хозяйства как судостроение, нефтяная и газовая промышленность, энергетика, строительство, медицина, нуждаются в сталях нового поколения. Они должны превосходить существующие по прочности, коррозионной стойкости, экологическим характеристикам, комплексу функциональных свойств. Одним из наиболее эффективных путей решения данной проблемы является внедрение азота в качестве легирующего элемента в высокопрочные и коррозионностойкие стали. Введение азота способно отчасти заменить никель, марганец и остальные аустенитообразующие элементы за счет способности стабилизовать аустенит [1].
Высокопрочная коррозионностойкая аустенитная сталь ВНС53 (08Х21Г11АН6) отличается высоким содержанием азота (до 0.5%) и обладает пределом прочности 980 МПа. Данная сталь разработана как материал для тонкостенных трубопроводов гидросистем высокого давления летательных аппаратов, работающих во всех климатических условиях в контакте с авиационными жидкостями при температурах от –70 до +300°С. Сталь ВНС53 помимо прочностных характеристик превосходит стали-аналоги по показателям выносливости при сохранении хорошей пластичности и технологичности [2].
В традиционных коррозионностойких низкоуглеродистых сталях легирование азотом приводит к снижению чувствительности к локальным видам коррозии. Последнее качество связано с ослаблением или полным предотвращением процесса образования карбида Cr23C6 на границах зерен [3]. Для повышения сопротивления локальной коррозии и измельчения зерна традиционную нержавеющую сталь легируют титаном или ниобием [4, 5]. Однако для азотсодержащих сталей не применяется легирование титаном, так как он имеет сильное сродство к азоту и не участвует в связывании свободного углерода. Как показано авторами [6], Ti-содержащие нержавеющие стали азотируют строго методом химико-термической обработки (ХТО) – без введения азота в расплав посредством шихтовых материалов, для исключения формирования крупных нитридных включений, снижающих пластичность.
Титан и ниобий связывают углерод, образуя карбиды TiC и NbC и исключают возможность образования карбидов хрома, и как следствие, обеднение хромом аустенита [4]. Преимуществом ниобия по сравнению с титаном является его меньшее сродство к кислороду, что особенно важно при изготовлении сварных конструкций из нержавеющей стали. Кроме того, карбиды ниобия обладают значительно меньшей растворимостью в аустените при высоких температурах, чем карбиды титана [7].
Таким образом, целью работы является сравнительное коррозионно-электрохимическое исследование новой азотсодержащей стали ВНС53-М в нейтральных средах, содержащих депассивирующие ионы (хлориды, сульфаты), а также установление связи со структурно-фазовыми характеристиками. Полученные данные сопоставлены с данными для известных марок сталей 08Х18Н10Т и ВНС53, также исследованными в данной работе.
ЭКСПЕРИМЕНТАЛЬНАЯ ЧАСТЬ
Были исследованы три марки стали: стандартная нержавеющая сталь 08Х18Н10Т, азотсодержащая аустенитная сталь ВНС53 и сталь ВНС53-М, модифицированная ниобием и ванадием. Стали были получены на предприятии ОАО “Научно-исследовательский институт металлургической технологии” методом индукционной выплавки, в дальнейшем были подвержены электрошлаковому переплаву (ЭШП). Для получения электродов ЭШП слитки индукционной выплавки подвергали ковке. Предварительную ковку слитков осуществляли в интервале температур 1200–1000°С, окончательную – в интервале 1200–950°С. Полученные слитки ЭШП были откованы в круг ∅80 мм. Температурный интервал ковки составлял 1200–950°С для сталей ВНС53 и ВНС53-М, и 1200–900°С для стали 08Х18Н10Т. Химический состав сталей представлен в табл. 1.
Таблица 1.
Химический состав исследованных образцов
Марка стали | Химический состав, вес. % | |||||||||||
---|---|---|---|---|---|---|---|---|---|---|---|---|
C | Mn | Si | P | S | Cr | Ni | Cu | V | Ti | Nb | N | |
ВНС53 | 0.08 | 10.65 | 0.50 | 0.016 | 0.005 | 21.13 | 5.59 | 0.11 | 0.17 | 0.02 | 0.01 | 0.499 |
ВНС53-М | 0.07 | 11.00 | 0.22 | 0.014 | 0.005 | 20.48 | 5.50 | 0.09 | 0.29 | 0.01 | 0.29 | 0.491 |
08Х18Н10Т | 0.07 | 0.90 | 0.68 | 0.030 | 0.008 | 17.07 | 9.48 | 0.35 | 0.16 | 0.59 | – | – |
Образцы для металлографического анализа и исследования коррозионных свойств были изготовлены из образцов для испытаний на ударную вязкость при отрицательных температурах. Металлографические шлифы изготавливали для образцов каждого типа стали. Шлифование проводили на шлифовально-полировальном станке до 13 класса чистоты поверхности. К образцам для исследования коррозионных свойств методом лазерной сварки приваривали проволоку, которая в дальнейшем служила токосъемником при коррозионно-электрохимических исследованиях. Обезжиренная поверхность металлографического шлифа являлась рабочей, остальные поверхности изолировали лаком.
Электрохимические свойства образцов исследовали путем снятия анодных потенциодинамических кривых в боратном буферном растворе (ББР) с pH 7.4, а также в ББР с добавлением 0.01 M NaCl и 0.01 M Na2SO4 при естественной аэрации. Использовали потенциостат EcoLab 2A-100. Растворы готовили на дистиллированной воде, температура растворов составляла 23 ± 2°C. Использована стандартная электрохимическая ячейка ЯСЭ-2. Электродные потенциалы E, мВ приведены относительно электрода сравнения – насыщенного хлорид-серебряного. Скорость сканирования потенциала 1 мВ/с. Плотность тока I, мкА/см2 на рисунках и в тексте приведена в расчете на видимую геометрическую поверхность электрода.
Металлографический анализ был проведен на инвертированном металлографическом микроскопе Альтами МЕТ-1 и автоматизированном анализаторе микроструктуры SIAMS 800.
Топографию анализируемых образцов исследовали методом атомно-силовой микроскопии на исследовательском комплексе Centaur U HR, в состав которого входит сканирующий зондовый микроскоп Certus. Съемку вели при сканировании в полуконтактном режиме на воздухе при комнатной температуре. В результате были получены изображения поверхности с размером скана 20 × 20 мкм разрешением 400 × 400 точек при скорости сканирования 0.8 Гц. Компьютерную обработку изображений проводили в программе ПО Gwiddion.
Электронно-микроскопические исследования проводили на растровом электронном микроскопе FEI Inspect S50. Съемку осуществляли в режиме высокого вакуума при ускоряющем напряжении 20 кВ и геометрических увеличениях 5000×, постоянная времени 7.68 мкс, рабочее расстояние 10 мм. Время накопления варьировали: 100, 200 и 500 с. Детектирование поверхности осуществляли в режиме вторичных электронов (ETD). Рентгеноспектральный микроанализ образцов проводили после обдува поверхности воздухом. Количественный анализ проводили точечно по дефектам структуры образцов.
РЕЗУЛЬТАТЫ И ОБСУЖДЕНИЕ
Потенциодинамические исследования. Для всех исследованных образцов и сред характерна широкая область перехода образцов в пассивное состояние. В качестве характеристики пассивного состояния могут быть выбраны: потенциал перепассивации, ширина пассивной области. Кроме того, при различных потенциалах, где металл находится в пассивном состоянии, могут быть определены анодные токи при фиксированных значениях потенциала, которые также являются количественной мерой скорости анодного растворения данного образца. Учитывая большую ширину потенциала пассивации, были выбраны три значения потенциалов, при которых определены токи (табл. 2). Это позволяет количественно судить о степени торможения анодного процесса в одинаковых условиях для разных сталей.
Таблица 2.
Анодные токи растворения образцов при двух фиксированных потенциалах в различных средах
Образец | I1, мкА/см2 при Е = 0 мВ |
I2, мкА/см2 при Е = +700 мВ (для Na2SO4) E = +50 мВ (для NaCl) |
Eпп, мВ | ||||||
---|---|---|---|---|---|---|---|---|---|
ББР | ББР + NaСl | ББР + Na2SO4 | ББР | ББР + NaСl | ББР + Na2SO4 | ББР | ББР + NaСl | ББР + Na2SO4 | |
08Х18Н10Т | 8.9 | 8.1 | –0.8 | 18.1 | 5.7 | 6.1 | 1031.3 | 217.6 | 1060.7 |
ВНС53 | 10.4 | –18.2 | –6.6 | 17.9 | –20.4 | 8.4 | 1019.6 | 107.3 | 1067.4 |
ВНС53-М | 7.4 | 1.9 | 1.1 | 14.3 | –1.4 | 7.9 | 1063.9 | 179.8 | 1056.8 |
На рис. 1 представлены анодные поляризационные кривые для широко используемой стали 08Х18Н10Т, выбранной в качестве основы для сравнения, и сталей ВНС53 и ВНС53-М в боратном буферном растворе.
Рис. 1.
Потенциодинамические кривые в боратном буферном растворе: 1 – сталь 08Х18Н10Т; 2 – сталь ВНС53; 3 – сталь ВНС53-М.
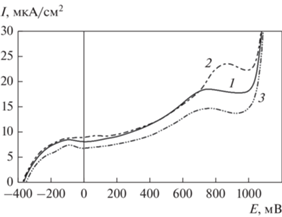
Можно видеть, что ход анодных кривых во многом аналогичен. Низкие токи анодной поляризации в области потенциалов от –400 до 1000 мВ свидетельствуют об устойчивом пассивном состоянии всех образцов. Однако для стали ВНС53-М наблюдаются меньшие значения токов во всех областях пассивации.
Таким образом, сталь ВНС53-М более коррозионно стойкая в испытанном нейтральном растворе. Есть некоторые различия в области перепассивации: резкое возрастание анодного тока при достижении соответствующего потенциала. Можно отметить, что сталь ВНС53-М имеет некоторые преимущества.
На рис. 2 показаны кривые поляризации в сантимолярном растворе хлорида натрия в ББР. Из рисунка видно, что минимальные анодные токи характерны для аустенитной стали ВНС53, которая достигает области перепассивации при значении потенциала Eпп ≈ 110 мВ. Для базовой стали 08Х18Н10Т и стали ВНС53-М эти значения составляют Eпп ≈ 120 и Eпп ≈ 165 мВ соответственно. Таким образом, по устойчивости стали к перепассивации лучшие результаты показывает сталь ВНС53-М. Отметим, что в данном хлоридном растворе образцы стали подвергаются воздействию хлорид-анионов, что стимулирует локализацию их анодного растворения. Об этом свидетельствует фибриляция токов по мере роста потенциалов. Следовательно, сталь ВНС53-М проявляет более высокую коррозионную стойкость также в хлорид-содержащем растворе.
Рис. 2.
Потенциодинамические кривые в боратном буферном растворе с добавлением хлоридов: 1 – сталь 08Х18Н10Т; 2 – сталь ВНС53; 3 – сталь ВНС53-М.
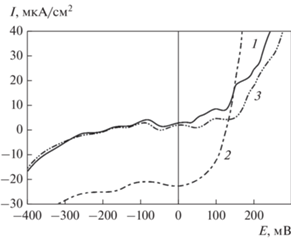
На рис. 3 изображены кривые анодной поляризации для изученных сталей в ББР с добавлением 0.01 M Na2SO4.
Рис. 3.
Потенциодинамические кривые в боратном буферном растворе с добавлением сульфатов: 1 – сталь 08Х18Н10Т; 2 – сталь ВНС53; 3 – сталь ВНС53-М.
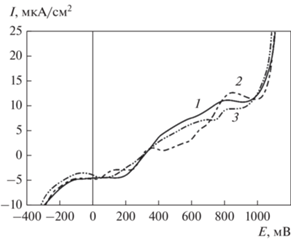
Как уже отмечали, ионы сульфата являются менее сильными стимуляторами растворения легированных сталей, что сказывается в меньшем увеличении анодных токов и увеличении потенциала перепассивации по сравнению с хлоридсодержащим раствором. Отметим, что с ростом потенциала в области пассивности наблюдается устойчивое повышение анодного тока для всех образцов стали, хотя плотность этого тока перед переходом сталей в транспассивное состояние невелика и составляет 10–12 мкА/см2. Для данного раствора можно отметить отсутствие преимуществ сталей ВНС53 и ВНС53-М по сравнению с базовой сталью 08Х18Н10Т. Таким образом, все испытанные в данном растворе стали ведут себя в равной степени аналогично.
В табл. 2 сопоставлены результаты электрохимических испытаний для всех образцов сталей. Выбраны значения потенциалов Е = 0 мВ, Е = = +700 мВ (для Na2SO4), E = +50 мВ (для NaCl), соответствующие устойчивому пассивному состоянию.
Исследование микроструктуры. Исследуемые марки сталей относятся к классу аустенитных. Металлографическое исследование показало, что микроструктура образцов сталей ВНС53 и ВНС53-М представляет собой аустенит. В результате модифицирования ВНС53-М в металле образуются дополнительные центры кристаллизации, способствующие измельчению зерна. Номер зерна аустенита в образцах сталей ВНС53 и ВНС53-М – 6 и 11 соответственно (рис. 4б, 4в).
Рис. 4.
Микроструктура исследуемых образцов сталей: а – 08Х18Н10Т: мартенсит и остаточный аустенит, включения нитридов и карбонитридов титана размерами 2–6 мкм; б – ВНС53: аустенит 6 номера, включения нитридов хрома размерами 3–8 мкм; в – ВНС53-М: аустенит 11 номера, включения нитридов и карбонитридов ниобия размерами 2.5–8 мкм.
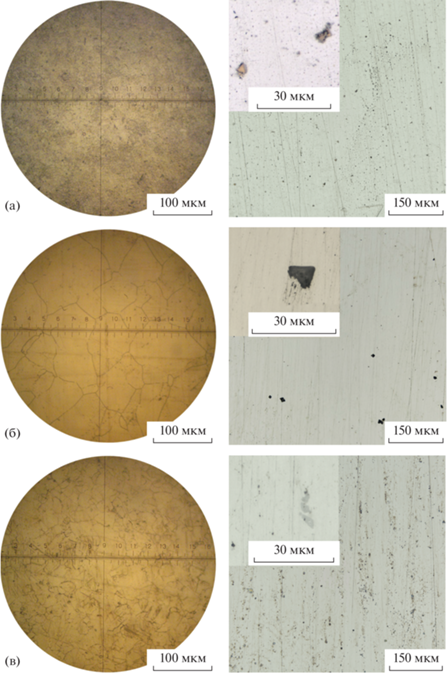
Микроструктура стали 08Х18Н10Т состоит из мелкоигольчатого мартенсита и остаточного аустенита (рис. 4а). В структуре металла образца стали 08Х18Н10Т наблюдаются характерные включения нитридов и карбонитридов титана, а также включения оксидов и сульфидов. В структуре стали ВНС53 наблюдается скопление мелких карбидов преимущественно по границам зерен. В структуре образца стали ВНС53-М, помимо оксидов и сульфидов, присутствуют множественные включения нитридов и карбонитридов ниобия, а также скопление мелких и крупных карбидов как по границам зерен, так и внутри зерна. При этом образец стали ВНС53 является наименее загрязненным неметаллическими включениями: оксидами и сульфидами, по сравнению с образцами из сталей 08Х18Н10Т и ВНС53-М.
Энергодисперсионный анализ включений в стали ВНС53-М подтвердил, что они представляют собой сложные включения на основе ниобия и хрома (рис. 5, табл. 3). Имеются также следы ванадия, но в меньшем процентном содержании. Пики S Kα, появившиеся в EDS-спектре, соответствуют включениям сульфидов, располагающихся вокруг нитридов и карбонитридов, что подтверждено металлографическим анализом.
Таблица 3.
Энергодисперсионный анализ химического состава включений в стали ВНС53-М
Химический элемент | Массовая доля, вес. % | |
---|---|---|
Спектр 1 | Спектр 2 | |
Nb | 40.89 | 7.92 |
Cr | 27.76 | 20.59 |
O | 10.96 | 3.05 |
Fe | 10.19 | 43.04 |
Mn | 3.64 | 17.09 |
N | 3.12 | 0.30 |
V | 1.71 | 0.64 |
C | 0.77 | 0.49 |
Ni | 0.64 | 3.83 |
Si | 0.32 | 0.46 |
S | – | 2.60 |
Среди неметаллических частиц в стали также обнаруживаются включения на основе циркония, который, вероятно, попал в сталь в результате шихтовки.
После проведения коррозионно-электрохимических испытаний образцы исследовали на металлографическом микроскопе и методом АСМ. Снятие поляризационных кривых показало на поверхности следы коррозионных поражений диаметром 100–400 мкм (рис. 6а). В результате электрохимических испытаний в растворе ББР очаги коррозии выявлены для всех трех анализируемых марок стали. При этом следов растворения вокруг включений нитридов и карбонитридов не наблюдается.
Рис. 6.
Участки коррозионного поражения, обнаруженные на образцах стали ВНС53-М: а – в растворе ББР; б – в растворе ББР + 0.01 M NaCl; в – в растворе ББР + 0.01 M Na2SO4.
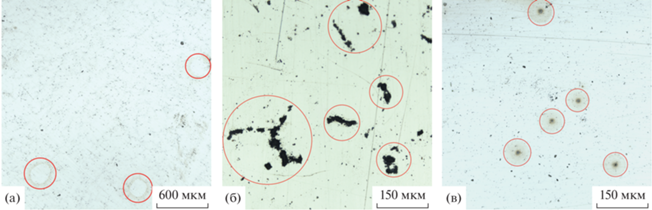
В боратном буфере с добавлением 0.01 M NaCl на поверхности образца стали ВНС53 в оптическом микроскопе наблюдаются коррозионные поражения размерами ~250 мкм. По границам участка коррозии расположены включения карбидов размерами до 8 мкм.
На поверхности образца стали ВНС53-М обнаружен участок коррозионного поражения (рис. 6б), по границам очагов коррозии наблюдаются включения карбидов. Коррозионные поражения вокруг одиночных включений в оптический микроскоп не наблюдаются. Для образца стали 08Х18Н10Т в растворе ББР + 0.01 M NaCl следов коррозии не наблюдается. В растворе ББР + 0.01 M Na2SO4 следы коррозии также обнаружены только на образцах сталей ВНС53 и ВНС53-М. Для стали ВНС53 размер участков коррозионного поражения составляет ~600 мкм. На поверхности образца стали ВНС53-М обнаружены множественные коррозионные поражения размерами ~300 мкм (рис. 6в). При этом следов коррозии вокруг включений для обеих сталей не наблюдается, что крайне важно с точки зрения условий эксплуатации стали в агрессивных средах. Другими словами, формирование локальных включений карбонитридов не приводит к ухудшению коррозионных свойств материала. Действительно, в работе [8] было убедительно показано, что основной вклад в МКК вносят включения карбидов и боридов, при этом нитриды и РЗМ практически не ухудшают коррозионную стойкость.
Сравнительный анализ топографии поверхности образцов, проведенный методом АСМ до и после потенциодинамических исследований, показал наличие пор как на исходной поверхности, так и на поверхности образцов после испытаний в коррозионной среде. На образце стали 08Х18Н10Т поры обнаружены вблизи включений. Для сталей ВНС53 и ВНС53-М выявлено, что обнаруженные поры не связаны с включениями и располагаются отдельно, преимущественно строчками. При этом число пор в исходном образце стали ВНС53-М наименьшее (рис. 7а).
Рис. 7.
АСМ-изображение поверхности образца стали ВНС53-М: а – в исходном состоянии; б – после испытаний в растворе ББР; в – после испытаний в растворе ББР + 0.01 M NaCl; г – после испытаний в растворе ББР + 0.01 M Na2SO4.
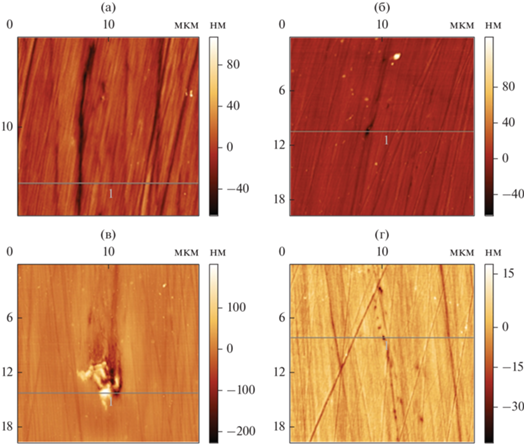
АСМ-изображения и профиль поверхности образцов стали 08Х18Н10Т и ВНС53 после испытаний в растворе ББР показывают наличие пор глубиной до 60 и 40 нм соответственно, расположенных обособленно от включений. Анализ АСМ-изображений и профиля поверхности образца стали ВНС53-М показывает наличие одиночных пор глубиной ~50 нм, расположенных обособленно от включений, и пор, расположенных непосредственно рядом с включением.
После испытаний в растворе ББР + 0.01 M NaCl в образце 08Х18Н10Т обнаружены поры, расположенные на участке поверхности равномерно или строчками. Глубина пор составляет 50–80 нм. На образцах сталей ВНС53 и ВНС53-М методом АСМ также обнаружены поры, причем наибольшая глубина пор обнаружена в стали ВНС53-М и составляет 170 мкм.
На образцах сталей 08Х18Н10Т и ВНС53 после коррозионных испытаний в растворе ББР + 0.01 M Na2SO4 обнаружены одиночные поры, расположенные вблизи включений. Глубина пор в образце ВНС53 ~50 нм, в образце 08Х18Н10Т достигает 100 нм. АСМ изображения поверхности образца стали ВНС53-М выявляют наличие строчек и одиночных пор, расположенных как вблизи включений, так и обособленно. Глубина пор составляет 20–50 нм.
ЗАКЛЮЧЕНИЕ
Проведен анализ микроструктуры и коррозионно-электрохимических свойств в различных средах новой высокоазотистой нержавеющей стали ВНС53-М, перспективной для применения в авиационной технике, в сравнении с высоколегированными сталями 08Х18Н10Т и ВНС53, широко используемыми в машиностроении.
В нейтральном ББР все образцы в условиях анодной поляризации после катодной активации переходят в пассивное состояние. Установлено, что легирование азотистой стали ВНС53-М карбонитридообразующими элементами – ниобием и ванадием – не приводит к ухудшению коррозионно-электрохимических свойств при регистрируемом изменении микроструктуры.
Показано, что добавление в ББР сульфат-ионов несколько ухудшает пассивационные свойства всех образцов стали, что приводит к некоторому снижению их коррозионных характеристик. Одновременно с этим выявлено, что новая сталь ВНС53-М более стойкая, чем другие исследованные образцы. Введение в ББР более агрессивного депассивирующего хлорид-аниона приводит к практически одинаковому снижению коррозионной стойкости указанных сталей.
Исследована взаимосвязь между микроструктурой и коррозионными свойствами сталей. Для всех образцов размер наблюдаемых включений одного порядка и соответствует диапазону 1–10 мкм. Однако плотность их локализации выше для стали ВНС53-М. Включения представлены карбонитридами, сульфидами, оксидами. Обнаружена высокая концентрация ниобия, ванадия, азота, углерода во включениях. Включения имеют высокую степень когерентности с матрицей металла и не являются причиной локального растворения поверхности образца.
Одновременно с этим были обнаружены следы локальной (строчечной) коррозии, не связанные с включениями, что свидетельствует об отсутствии корреляции между наличием включений и началом указанного вида коррозии. Полученные результаты подтверждают литературные данные о том, что включения ниже критического размера не ухудшают пассивационные характеристики поверхности и не приводят к локальной коррозии. Данное свойство крайне важно для легированных нержавеющих сталей, эксплуатируемых при повышенных температурах в агрессивных средах.
Авторы выражают благодарность за финансовую поддержку РНФ, проект № 19-79-20012, а также сотрудникам кафедры физики твердого тела УдГУ А.С. Алалыкину и Р.М. Закировой за содействие в организации и проведении экспериментов.
Список литературы
Явойский В.И., Кряковский Ю.В., Григорьев В.П. Металлургия стали. М.: Металлургия, 1983. 584 с.
Тонышева О.А., Вознесенская Н.М. Перспективные высокопрочные коррозионностойкие стали, легированные азотом (Сравнительный анализ) // Авиационные материалы и технологии. 2014. № 3. С. 27–32.
Банных О.А., Бецофен В.М., Блинов В.М., Ильин А.А. Исследование фазовых превращений в азотосодержащих сталях методом высокотемператуной рентгенографии // Металлы. 2005. № 5. С. 15–22.
Левин Ф.Л., Свистунова Т.В., Сорокина Н.А., Фельдгандлер Э.Г. Тенденции развития коррозионностойких сталей и сплавов // Тематический сборник научных трудов “Металлургия. Проблемы, поиски, решения”, под общ. ред. Н.П. Лякишева. М.: Металлургия, 1989. С. 254–267.
Лахтин Ю.М., Леонтьева В.П. Материаловедение: учебник для высших технических учебных заведений. 3-е изд., перераб. и доп. М.: Машиностроение, 1990. 528 с.
Рогачев С.О., Стомахин А.Я., Никулин С.А., Кадач М.В., Хаткевич В.М. Структура и механические свойства аустенитных Сr–Ni–Ti сталей после высокотемпературного азотирования // Известия вузов. Черная металлургия. 2019. Т. 62. № 5. С. 366–373.
Колотыркин Я.М., Княжева В.М. Свойства карбидных фаз и коррозионная стойкость нержавеющих сталей // Итоги науки и техники. Сер. Коррозия и защита от коррозии 1974. Т. 3. С. 5–82.
Мазничевский А.Н., Гойхенберг Ю.Н., Сприкут Р.В. Электронно-микроскопические исследования выделений избыточных фаз, оказывающих влияние на межкристаллитную коррозию // ФММ. 2021. Т. 122. № 4. С. 388–395.
Дополнительные материалы отсутствуют.
Инструменты
Физика металлов и металловедение